MIM-technologie begrijpen
Inhoudsopgave
Overzicht van MIM-technologie
Metaalspuitgieten (MIM), ook bekend als poederspuitgieten (PIM), is een geavanceerd productieproces dat wordt gebruikt om kleine, complexe metalen onderdelen in grote volumes te produceren.
MIM combineert de ontwerpflexibiliteit en precisie van kunststof spuitgieten met de sterkte en prestaties van machinaal bewerkte metalen onderdelen. Het maakt de kosteneffectieve productie mogelijk van ingewikkelde componenten met goede mechanische eigenschappen uit geavanceerde metaallegeringen.
Het MIM-proces begint met een grondstof gemaakt van fijn metaalpoeder gemengd met een bindmiddel. Deze grondstof wordt vervolgens in een mal geïnjecteerd met behulp van kunststofspuitgietapparatuur. Het bindmiddel houdt het metaalpoeder bij elkaar en zorgt voor vloeibaarheid voor het vormen.
Na het vormen wordt het bindmiddel via een ontbindingsproces uit het gevormde groene deel verwijderd. Het losgemaakte deel, het bruine deel genoemd, wordt vervolgens bij hoge temperaturen gesinterd, waardoor de metaaldeeltjes samensmelten tot een massief metalen onderdeel met materiaaleigenschappen die dicht bij die van een gesmeed onderdeel liggen.
MIM is geschikt voor het maken van kleine, complexe onderdelen met behulp van verschillende metalen zoals roestvrij staal, laaggelegeerde staalsoorten, gereedschapsstaal, magnetische legeringen, superlegeringen, titaniumlegeringen en zware wolfraamlegeringen. Het combineert de veelzijdigheid van kunststofspuitgieten met de materiaalflexibiliteit van de poedermetallurgie.
De belangrijkste voordelen van MIM-technologie zijn onder meer:
- Productiecapaciteit voor grote volumes voor complexe, gedetailleerde metalen componenten
- Near-net-shape productie, waardoor afval wordt verminderd en machinale bewerking wordt geminimaliseerd
- Goede mechanische eigenschappen in de buurt van gesmeed materiaal
- Ruime keuze aan metalen waaronder roestvrij staal, gereedschapsstaal, superlegeringen
- Maakt consolidatie van onderdelen in afzonderlijke componenten mogelijk
- Lage eenheidskosten vanwege grote volumes
- Consistentie en herhaalbaarheid van geautomatiseerd proces
MIM-technologie is ideaal voor kleine, complexe onderdelen zoals medische apparaten, onderdelen van vuurwapens, horlogeonderdelen en auto-onderdelen die precisie, sterkte, zuinigheid en massaproductie vereisen.
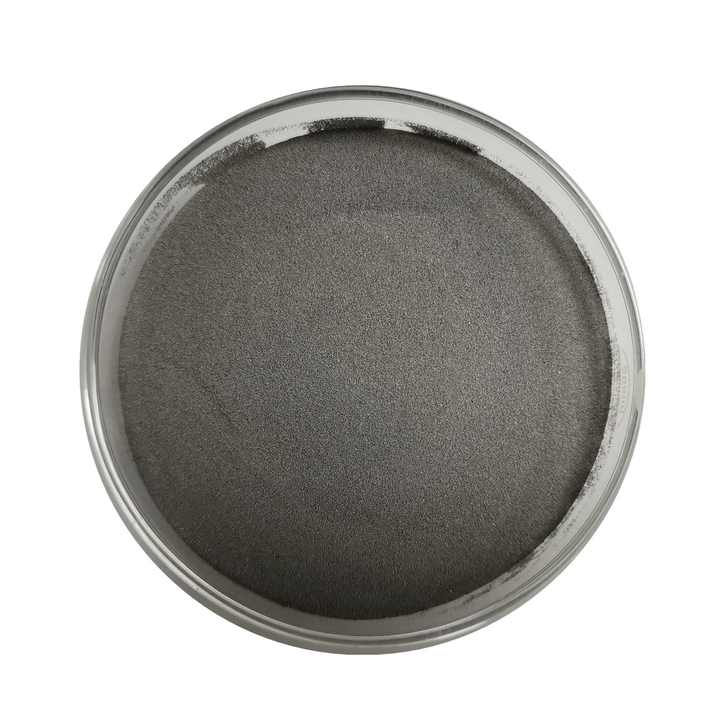
Toepassingen en gebruik van MIM-technologie
MIM-technologie wordt in verschillende industrieën gebruikt om kleine, uiterst nauwkeurige metalen onderdelen efficiënt in grote volumes te vervaardigen. Hier zijn enkele van de belangrijkste toepassingsgebieden en toepassingen van MIM-technologie:
Industrie | Toepassingen en gebruik |
---|---|
Medisch en Tandheelkunde | Chirurgische instrumenten, tandheelkundige implantaten, orthopedische implantaten, katheteronderdelen, naaldcanules, scalpelhandvatten, forceps, klemmen, chirurgische bevestigingsmiddelen, herbruikbare chirurgische instrumenten |
Vuurwapens en defensie | Trekkers, hamers, beveiligingen, uitwerpers, magazijnen, gebruikte omhulsels, projectielen, kernkopcomponenten |
Automobiel | Onderdelen van het brandstofsysteem, oliepomptandwielen, waaiers, kleppen, turbocompressoronderdelen, elektronische onderdelen, stuur-/transmissiecomponenten |
Lucht- en ruimtevaart | Turbinebladen, waaiers, tandwieltanden, bussen, pomponderdelen, motoronderdelen |
Consumentenproducten | Bekijk onderdelen, sieradenbevindingen, bestek, scharen, scheermessen, handgereedschap, ritsonderdelen |
Industriële hardware | Knoppen, fittingen, bevestigingsmiddelen, stopcontacten, connectoren, sprinklers, sproeiers |
Elektronica | Connectoren, schakelaars, micromotoren, microversnellingen, afschermingsmaskers, inductoren, magneetrotoren |
** Voordelen van MIM voor specifieke toepassingen**
- Precisie: Ideaal voor miniatuuronderdelen zoals medische apparaten of horlogecomponenten met ingewikkelde geometrieën.
- Sterkte: Geschikt voor componenten die een hoge sterkte nodig hebben, zoals auto-turbocompressoren en vuurwapentrekkers.
- Slijtvastheid: MIM-onderdelen gemaakt van gereedschapsstaallegeringen hebben een uitstekende slijtvastheid voor een lange levensduur.
- Corrosiebestendigheid: roestvrijstalen MIM-onderdelen zijn bestand tegen corrosie voor herbruikbare chirurgische instrumenten, implantaten, enz.
- Hoge hardheid: MIM kan onderdelen produceren met een hardheid van meer dan 40 HRC, zoals bestek, gereedschap, matrijzen, enz.
- Elektrische eigenschappen: MIM wordt gebruikt om zachtmagnetische componenten te maken, zoals inductoren, motorrotoren, enz.
- Kosteneffectief: Hoge volumes verlagen de onderdeelkosten aanzienlijk in vergelijking met machinaal bewerken.
MIM-apparatuur en gereedschapsgidsen
De belangrijkste apparatuur die in het MIM-proces wordt gebruikt, omvat spuitgietmachines, ontbindings- en sinterovens. Hier is een overzicht:
Apparatuur | Doel | Overwegingen |
---|---|---|
Spuitgietmachine | Om de MIM-grondstof onder hitte en druk in vormholtes te injecteren | Vormklemkracht, injectiesnelheid en drukcapaciteit, precisie en herhaalbaarheid, bedieningselementen en automatiseringsfuncties. |
Oven voor het verwijderen van bindmiddelen | Voor het thermisch of chemisch verwijderen van het bindmiddel uit vormdelen | Temperatuurbereik, atmosfeercontrole, laadvermogen, uniformiteit van het ontbinden. |
Sinteroven | Het verdichten van de losgekomen bruine delen door verhitting tot dichtbij het smeltpunt | Temperatuurbereik, sfeercontrole, uniformiteit van verwarming, batchcapaciteit, volledig geautomatiseerd heeft de voorkeur. |
Mallen en gereedschappen | Gevormde holtes om de MIM-grondstof in de gewenste geometrie te vormen | Bestand tegen vormdrukken en temperaturen, nauwkeurig bewerkt, goede oppervlakteafwerking, maakt snelle verwarming/koeling mogelijk. |
Grondstofapparatuur | Om het metaalpoeder en bindmiddel te mengen tot homogene MIM-grondstof | Mengers, temperatuurregelaars, pelletiseermachines. |
Secundaire verwerking | Extra stappen zoals verspanen, verbinden, oppervlaktebehandeling | Per onderdeelbehoeften zoals CNC-bewerking, lassen, EDM, coating. |
Kwaliteitscontrole | Om de eigenschappen van grondstoffen en gesinterde onderdelen te testen | Poedermorfologie, dichtheid, stroomsnelheid, viscositeitsanalysatoren, mechanische testapparatuur. |
Veiligheids uitrusting | Veilig omgaan met fijne poeders | Handschoenen, ademhalingstoestellen, stofopvangsystemen. |
Ontwerp- en prestatienormen
- ISO 21227 – Poeders voor het spuitgieten van metaal
- ASTM F2885 – Metaalspuitgietproces
- MPIF 35 – Normen voor MIM-grondstoffen
- ASTM E2781 – MIM-trekproefmonsterontwerp
- ISO 2740 – Gesinterde metalen spuitgietonderdelen
Kostenverdeling
De typische kostenverdeling bij MIM-productie is:
- Grondstoffen (poeder + bindmiddel): 50-60%
- Productie (gieten + ontbinden + sinteren): 25-35%
- Secundaire verwerking: 5-10%
- Kwaliteitscontrole: 2-5%
- Techniek (R&D, ontwerp): 2-5%
Leveranciers en prijzen
Hier zijn enkele toonaangevende wereldwijde leveranciers van MIM-apparatuur en hun prijsklassen:
Leverancier | product categorie | Prijsbereik |
---|---|---|
ARBURG | Spuitgietmachines | $100,000 – $500,000 |
Indo-Amerikaanse MIM | MIM-grondstoffen en -diensten | $5 – $50 per kg |
Elnik | Ontbindings- en sinterovens | $50,000 – $1,000,000 |
FijnMIM | End-to-end MIM-productie | $0,5 – $5 per onderdeel |
Parmatech | Metaalpoederverneveling | $250,000 – $1,000,000 |
Meridian-technologieën | Gereedschaps- en matrijsontwerp | $5,000 – $100,000 |
Installatie, bediening en onderhoud
MIM is een geautomatiseerd proces, maar vereist een zorgvuldige installatie, bediening en onderhoud voor optimale prestaties:
Activiteit | Details |
---|---|
Installatie | Precisie-uitlijning van spuitgietmachine en matrijzen. Kalibreer temperatuurregelaars. Proefdraaien met proefbatches. |
Operatie | Zorg voor kwaliteitscontrole van de grondstoffen volgens de normen. Bereik procesparameters zoals injectiedruk, temperatuur en snelheid. |
Onderhoud | Plan preventief onderhoud voor vaten, schroeven en mallen van gietmachines. Handhaaf de atmosfeer van de ontbindingsoven. Kalibreer instrumenten. |
Schoonmaak | Volg de SOP's voor het reinigen van machinevaten na runs. Zorg ervoor dat er zich geen poeder ophoopt in de oven of kanalen. Schimmelreiniging met speciaal ontworpen media. |
Veiligheid | Draag persoonlijke beschermingsmiddelen tijdens het hanteren van fijne poeders. Correcte verwijdering van chemische bindmiddelen. Laat de oven afkoelen vóór onderhoud. |
Opleiding | Train machine- en ovenoperators over de procedures. Verzorgen van opfrissessies over veiligheid en onderhoud. |
Optimalisatie | Pas procesparameters aan totdat de kwaliteit van het onderdeel zich binnen de specificaties stabiliseert. Houd gedetailleerde procesregistraties bij. |
Typische onderhoudsactiviteiten en frequentie
Activiteit | Frequentie |
---|---|
Spuitgietmachine mondstukreiniging | Na elke batch |
Schimmel polijsten | Wekelijks |
Reiniging van machinevaten | Maandelijks |
Ovenatmosfeercontrole voor het verwijderen van bindmiddel | Maandelijks |
Kalibratie van thermokoppels in sinterovens | 6 maanden |
Schimmelstroomstudies | jaarlijks |
Hoe u een MIM-leverancier kiest
Het kiezen van een competente MIM-leverancier is van cruciaal belang om onderdelen van goede kwaliteit op tijd en tegen redelijke kosten te verkrijgen. Hier zijn belangrijke factoren waarmee u rekening moet houden:
Factor | Criteria |
---|---|
Technische capaciteit | Geavanceerde apparatuur, jarenlange ervaring, technische expertise |
Materiaal opties | Bereik van materialen zoals roestvrij staal, gereedschapsstaal, wolfraamlegeringen |
Secundaire verwerking | Eigen bewerkings-, verbindings- en coatingfaciliteiten |
Kwaliteitssystemen | ISO 9001-certificering, kwaliteitscontrole en inspectieprocedures |
Productiecapaciteit | Hoogvolumeproductievermogen voor stabiliteit |
Doorlooptijd | Snelle doorlooptijd van ontwerp tot levering |
Plaats | Geografische nabijheid voor logistieke efficiëntie |
Kosten | Prijsmodel – bij voorkeur een prijs per onderdeel |
Klantenservice | Reactie op vragen, technische ondersteuning, projectmanagement |
Vragen om potentiële MIM-leveranciers te stellen
- Met welke materialen en onderdeelgroottes heeft u ervaring?
- Biedt u secundaire bewerkingen aan, zoals verspanen of coaten?
- Welke kwaliteitscertificeringen en inspectieprocedures worden gevolgd?
- Hoe wordt er omgegaan met gevoelige materialen zoals titaniumlegeringen of wolfraamcarbiden?
- Welke productievolumes kunt u maandelijks betrouwbaar leveren?
- Hoe wordt uitval geminimaliseerd en de opbrengst gemaximaliseerd?
- Wat is de variabiliteit van onderdeel tot onderdeel in afmetingen en eigenschappen?
- Hoe zal ontwerpoptimalisatie voor het MIM-proces worden uitgevoerd?
- Welke kwaliteitsrapporten en controlediagrammen worden verstrekt?
MIM vergelijken met andere processen
Vergelijking tussen MIM en andere metaalproductieprocessen:
Proces | Voordelen | Nadelen |
---|---|---|
MIM | Complexe geometrieën, massaproductie, bijna netvorm, ruime materiaalkeuzes | Investering vooraf in gereedschap, beperkingen qua afmetingen |
CNC-bewerking | Materiaalflexibiliteit, snelle doorlooptijd van prototypes | Beperkte complexiteit, lagere volumes |
Metaal gieten | Lage onderdeelkosten, hoge volumes | Vormbeperkingen, lagere sterkte |
Metaal stampen | Hoge snelheid, hoge volumes, lage kosten | Past alleen bij 2D-geometrieën |
3d printen | Ontwerpvrijheid, snelle prototyping | Lagere sterkte, hogere kosten, beperkte afmetingen en materialen |
Voordelen van MIM ten opzichte van machinale bewerking
- Hoger materiaalgebruik met bijna netvorm
- Geen dure bewerking voor complexe vormen
- Superieure mechanische eigenschappen
- Lagere gereedschapskosten vergeleken met het bewerken van matrijzen
- Geautomatiseerd proces maakt massaproductie mogelijk
- Betere oppervlakteafwerkingen mogelijk
Voordelen van MIM ten opzichte van metaalgieten
- Betere maatnauwkeurigheid en oppervlakteafwerking
- Minder defecten zoals porositeit vergeleken met gegoten onderdelen
- Isotrope eigenschappen in tegenstelling tot directioneel gieten
- Weinig tot geen flits of opening, in tegenstelling tot gietstukken
- Geen smeltgerelateerde reacties of veranderingen in de samenstelling
- Kernen en ondersnijdingen mogelijk in tegenstelling tot gieten
- Brede materiaalopties naast gietbare legeringen
- Consistentie van eigenschappen met poedermetallurgie
Beperkingen van MIM versus CNC-bewerking
- Grootte beperkt door de capaciteit van de spuitgietmachine
- Meer voorbereidingstijd en -kosten voor gereedschap
- Nauwe toleranties +/- 0,5% vs. +/- 0,1% voor CNC-bewerking
- Geometriebeperkingen versus onbeperkte bewerking
- Lagere maximaal haalbare hardheid vergeleken met machinaal bewerken
- Secundaire bewerking is vaak nog nodig om toleranties te bereiken
Wanneer mag u MIM niet gebruiken?
- Zeer grote onderdelen die de capaciteit van de MIM-apparatuur te boven gaan
- Onderdelen die extreem nauwe toleranties onder 0,5% nodig hebben
- Toepassingen waarbij een oppervlaktehardheid van meer dan 50 HRC vereist is
- Producten met zeer lage volumevereisten
- Componenten met extreme aspectverhoudingen die niet geschikt zijn voor gieten
- Als er geen tijd is voor ontwerpoptimalisatie voor het MIM-proces
- Kostengevoelige toepassingen met goedkopere productieopties
Overwegingen bij MIM-ontwerp en -modellering
Een goed onderdeel- en grondstofontwerp is cruciaal voor MIM om de vereiste eigenschappen en prestaties te bereiken. Hier zijn de belangrijkste ontwerpoverwegingen:
Deelontwerpfase
- Optimaliseer de wanddikte voor een uniforme matrijsvulling tijdens het injecteren
- Voeg royale interne radii en filets toe om het vullen te vergemakkelijken
- Vermijd ernstige veranderingen in de dwarsdoorsnede langs het stroompad
- Ontwerp de juiste vormpoorten en geleiders voor geschikte stromingspatronen
- Voeg verstevigende ribben en inzetstukken toe om doorzakken of kromtrekken te voorkomen
- Houd rekening met krimp van het onderdeel tijdens het sinteren in de beginafmetingen
- Ontwikkel prototypematrijzen voor ontwerpvalidatie vóór volledige productie
Ontwikkeling van grondstoffen
- Stem de viscositeit van de grondstof af op de complexiteit van de mal bij giettemperaturen
- Zorg voor voldoende poederlading voor de vereiste gesinterde dichtheid
- Selecteer geschikte bindmiddelcomponenten en poederverhouding voor mengbaarheid
- Optimaliseer de verdeling van de poederdeeltjesgrootte voor de pakkingsdichtheid van het poeder
- Pas de formuleringen van grondstoffen aan voor een foutloze verwijdering van bindmiddel
- Valideer de eigenschappen van grondstoffen door middel van matrijsstroomsimulaties
- Test meerdere grondstofiteraties om volledige vormbaarheid te bereiken
Simulatie en modellering
- Vormstromingsmodellering om poortlocaties en lopers te optimaliseren
- Structurele FEA om kromtrekken te voorspellen en de onderdeelgeometrie te optimaliseren
- CFD-simulaties voor uniforme verwijdering van bindmiddel en sinteren
- Thermische modellering om restspanningen te minimaliseren
- Mechanische modellering om sterkte en prestaties te maximaliseren
- Procesmodelleringssoftware om interacties tussen parameters te bestuderen
- Experimentele validatie van softwarevoorspellingen via prototypematrijzen
Belangrijkste modelleringsuitgangen
- Vultijd van de mal, viscositeit van de grondstof, temperatuur van het stroomfront
- Voorspellingen van laslijnen, luchtbellen en andere vormdefecten
- Ruimtelijk bindmiddelgehalte, temperatuur en oplossingsgradiënten
- Sintersnelheid, dichtheidsgradiënten, krimp, trends in kromtrekken
- Residuele spanningsverdeling, schattingen van hete scheuren en barsten
- Mechanische sterkte, levensduur tegen vermoeiing, analyse van schadetolerantie
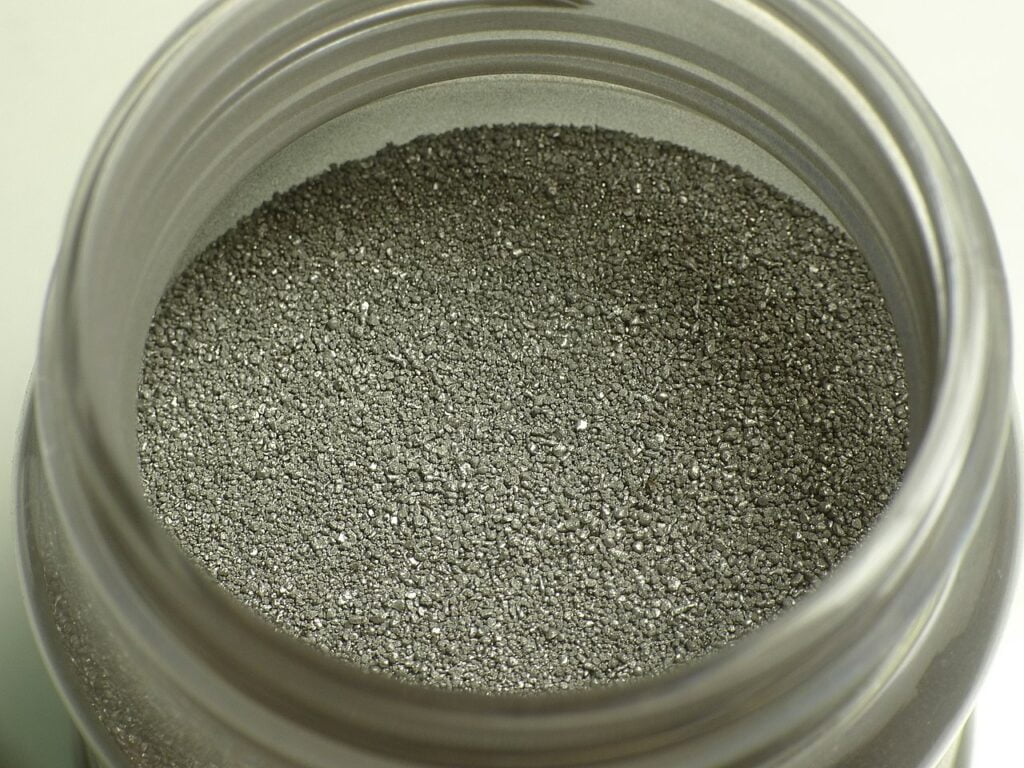
MIM-defecten en mitigatiemethoden
Defecten kunnen optreden in MIM-onderdelen als gevolg van niet-geoptimaliseerde grondstoffen, vormparameters of ovenomstandigheden. Hier volgen veelvoorkomende MIM-defecten en mitigatiemethoden:
Defect | Hoofdoorzaken | Mitigatiemethoden |
---|---|---|
Oppervlaktedefecten | Lage matrijstemperatuur, hoge wrijving, bindmiddelcomponenten | Optimaliseer het polijsten van de mal, gebruik losmiddelen, verlaag de maltemperatuur geleidelijk |
Las lijnen | Ongewenste grondstofstroomfronten | Optimaliseer het ontwerp van poort en runner door middel van modellering om laslijnen te voorkomen |
Kromtrekken | Niet-uniforme verwarming in de oven, restspanningen | Structurele optimalisatie, spanningsverlichting vóór het sinteren, geoptimaliseerde oveninstellingen |
Scheuren | Snel sinteren, hoog bindmiddelgehalte, steile thermische gradiënten | Lagere verwarmingssnelheid, optimaliseren bindmiddelsysteem, structureel herontwerp |
Porositeit | Lage poederbelading in de grondstof, slechte menging | Verhoog het poedergehalte in de grondstof, verbeter het mengproces |
Dimensionale variatie | Inconsistente krimp, schimmelslijtage, dichtheidsgradiënten | Statistische procescontrole, matrijsonderhoud, optimaliseren van ontbinden en sinteren |
Verontreiniging | Slechte bediening, controle van de ovenatmosfeer | Goede PBM's, luchtfilters verbeteren, kruisbesmetting in ovenbatches voorkomen |
Onvolledige vulling | Hoge matrijstemperatuur, hoge viscositeit | Verhoog de temperatuur van de schimmel en de grondstof, gebruik een bindmiddel met een lagere viscositeit |
MIM-industriegegevens en trends
MIM-wereldwijde marktomvang
De mondiale MIM-markt werd in 2022 op 1,5 miljard dollar geschat en zal naar verwachting tegen 2030 3,1 miljard dollar bereiken, met een groei van 8,7% CAGR, gedreven door de vraag uit de gezondheidszorg, de automobielsector en de lucht- en ruimtevaartsector.
Groeifactoren voor de sector
- Lichtgewichttrends in de automobiel-, ruimtevaart- en elektronicasector
- Vraag naar kleine, complexe metalen componenten in medische apparaten
- Levensvatbaarder met een breder scala aan MIM-geschikte materialen
- Automatisering verlaagt de productiekosten
- Groei in de productie van precisiecomponenten
- Verhoogde adoptie in opkomende toepassingen zoals uurwerken
Verwachte CAGR per regio
- Azië-Pacific: 9,3% CAGR
- Europa: 10.2% CAGR
- Noord-Amerika: 7,6% CAGR
- Rest van de wereld: 7,9% CAGR
Aandeel MIM-onderdelen per sector
- Consumentenproducten: 22%
- Automobiel: 21%
- Vuurwapens: 15%
- Medisch: 14%
- Industrieel: 13%
- Lucht- en ruimtevaart: 8%
- Anderen: 7%
MIM-technologieontwikkelingstrends
- Nieuwe bindersystemen om defecten te verminderen en complexe geometrieën mogelijk te maken
- Nieuwe grondstofformuleringen voor betere poederbelading en sintering
- Multi-materiaal MIM combineert verschillende poeders in één component
- Automatisering van nabewerkingen zoals verspanen, verbinden, draadsnijden etc.
- Hybride MIM + Additive Manufacturing-technieken
- Nieuwe verwarmingsmethoden zoals sinteren in de magnetron voor snellere verwerking
- Geïntegreerde simulaties die meerdere fysica- en productiestappen combineren
- Verhoogde adoptie van kwaliteitsmanagementsystemen
Samenvatting
Belangrijkste leerpunten:
- MIM maakt grootschalige productie van ingewikkelde metalen componenten mogelijk door spuitgieten en poedermetallurgie te combineren.
- Geschikt voor kleine, complexe onderdelen met hoge precisie in de medische, vuurwapen-, automobiel-, ruimtevaart- en consumentenindustrie.
- Voordelen zijn onder meer een bijna-netvorm, ruime materiaalkeuze en goede mechanische eigenschappen dichtbij gesmeed materiaal.
- Omvat het vormen van grondstoffen, ontbinden en sinteren met behulp van gespecialiseerde apparatuur.
- Vereist expertise op het gebied van onderdeelontwerp, ontwikkeling van grondstoffen, procesmodellering, defectcontrole en kwaliteitsmanagement.
- Zal naar verwachting wereldwijd groeien met een CAGR van 8,7%, gedreven door de vraag uit verschillende sectoren.
- Voortdurende technologische ontwikkelingen voor snellere verwerking, meer materialen, verhoogde automatisering en verbeterde onderdeelkwaliteit.
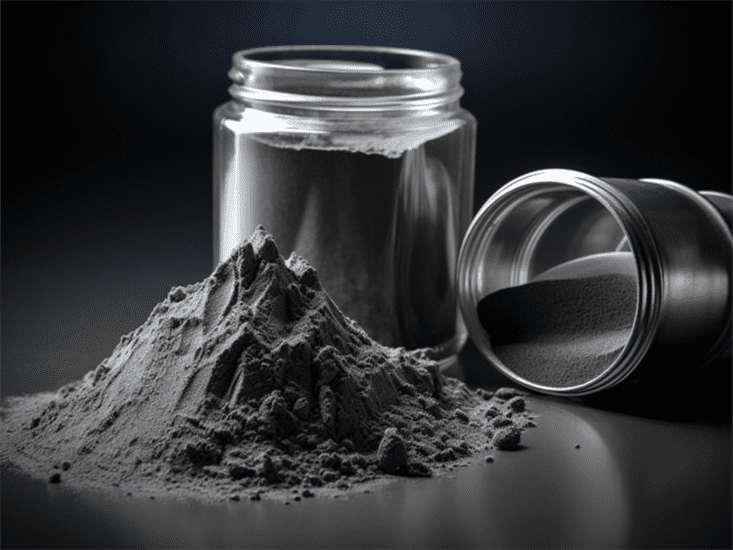
Veelgestelde vragen
Vraag: Wat zijn de belangrijkste voordelen van MIM-technologie?
A: De belangrijkste voordelen van MIM zijn:
- Mogelijkheid om kleine, complexe geometrieën te produceren die niet mogelijk zijn door machinale bewerking of gieten
- Near-net-vormproductie resulteert in
Vraag: Wat is het typische tolerantievermogen van MIM?
A: MIM kan over het algemeen toleranties bereiken van +/- 0,5%, hoewel +/- 0,3% mogelijk is voor sommige geometrieën en bewerking nodig kan zijn voor nauwere toleranties.
Vraag: Welke maat onderdelen kunnen worden geproduceerd met MIM?
A: MIM kan onderdelen produceren van 0,1 gram tot ongeveer 250 gram massa. Grotere onderdelen zijn mogelijk, maar uitdagend vanwege beperkingen in de grootte van de vormmachine.
Vraag: Hoe verhoudt MIM zich tot kunststof spuitgieten?
A: Hoewel beide spuitgietapparatuur gebruiken, kan MIM metalen onderdelen produceren, terwijl kunststoffen een veel lagere sterkte hebben. Maar MIM heeft lagere productiesnelheden en hogere kosten dan kunststofspuitgieten.
Vraag: Welke warmtebehandeling wordt gebruikt in MIM?
A: Het sinterproces in MIM omvat verwarming tot bijna het smeltpunt van het metaalpoeder, dus er is doorgaans geen verdere warmtebehandeling nodig. Indien nodig kunnen aanvullende warmtebehandelingen worden uitgevoerd om de eigenschappen te wijzigen.
Vraag: Welke materialen kunnen in MIM worden gebruikt?
A: Een breed scala aan materialen is geschikt voor MIM, waaronder roestvrij staal, gereedschapsstaal, superlegeringen, titanium, zware wolfraamlegeringen en magnetische legeringen. De ontwikkeling van nieuwe materialen is een belangrijk onderzoeksgebied in MIM.
Vraag: Hoe verhoudt MIM zich tot 3D-printen met metaal?
A: MIM kan grotere volumes produceren met een betere oppervlakteafwerking en mechanische eigenschappen. Maar 3D-printen biedt meer ontwerpvrijheid en een snellere time-to-market voor prototypes of aangepaste onderdelen.
Delen op
MET3DP Technology Co, LTD is een toonaangevende leverancier van additieve productieoplossingen met hoofdkantoor in Qingdao, China. Ons bedrijf is gespecialiseerd in 3D printapparatuur en hoogwaardige metaalpoeders voor industriële toepassingen.
Onderzoek om de beste prijs en een op maat gemaakte oplossing voor uw bedrijf te krijgen!
gerelateerde artikelen
Over Met3DP
Recente update
Ons product
NEEM CONTACT MET ONS OP
Nog vragen? Stuur ons nu een bericht! Na ontvangst van uw bericht behandelen wij uw verzoek met een heel team.