Custom 3D Printed Phone & Laptop Cases from Aluminum
Оглавление
Introduction: Revolutionizing Consumer Electronics with Custom Aluminum 3D Printed Cases
In today’s hyper-competitive consumer electronics landscape, differentiation is paramount. Consumers and enterprise users alike demand devices that are not only powerful and feature-rich but also durable, personalized, and aesthetically pleasing. While plastics have long dominated the casing market due to cost-effectiveness in mass production, a new wave of innovation is being driven by аддитивное производство металлов (AM), commonly known as metal 3D-печать. This technology is unlocking unprecedented possibilities for creating custom electronics enclosuresв частности bespoke phone cases and high-performance laptop shells, using advanced materials like aluminum alloys.
Imagine a phone case not merely as a protective afterthought but as an integral part of the device’s design language – lightweight yet incredibly strong, potentially incorporating intricate cooling channels or unique, un-machinable textures. Picture a laptop shell designed with topology optimization for maximum rigidity at minimal weight, perfectly complementing the high-performance components within. This is the reality enabled by metal 3D printing. By building parts layer by layer directly from digital designs, AM bypasses the constraints of traditional manufacturing methods like injection molding (high tooling costs, design limitations) and CNC machining (material waste, difficulty with complex internal features).
Aluminum, specifically alloys like AlSi10Mg and AlSi7Mg, stands out as a prime candidate for these applications. Renowned for its excellent strength-to-weight ratio, good thermal conductivity, and natural corrosion resistance, aluminum offers a significant upgrade over plastics and even standard metals in terms of performance and premium feel. Алюминиевая 3D-печать allows engineers and designers to leverage these properties fully, creating lightweight device protection that doesn’t compromise on strength or thermal management.
This shift towards premium tech accessories and functionally superior enclosures presents a significant opportunity for businesses targeting niche markets, high-performance computing, ruggedized applications, or simply seeking a unique value proposition. However, harnessing the full potential of metal AM requires specialized expertise, high-quality materials, and advanced printing technology.
This is where Met3dp enters the picture. As a leading provider of additive manufacturing solutions, headquartered in Qingdao, China, Met3dp specializes in both state-of-the-art 3D printing equipment and the high-performance metal powders essential for industrial applications. With industry-leading print volume, accuracy, and reliability, Met3dp’s Selective Electron Beam Melting (SEBM) and Laser Powder Bed Fusion (LPBF) systems are engineered for mission-critical parts across demanding sectors. Our deep understanding of material science, coupled with advanced powder manufacturing techniques like gas atomization and Plasma Rotating Electrode Process (PREP), ensures the highest quality aluminum powders (including AlSi10Mg and AlSi7Mg) optimized for dense, high-performance printed components. Whether you are an engineer designing the next generation of rugged tablets or a procurement manager sourcing unique, high-value enclosures, understanding the capabilities of aluminum 3D printing is crucial. Explore the Met3dp website to learn more about our comprehensive additive manufacturing solutions.
This post will delve into the world of custom 3D printed aluminum phone and laptop cases, exploring their applications, the distinct advantages of using metal AM, the critical role of material selection, design considerations, post-processing requirements, and how to partner with the right service provider like Met3dp to bring your innovative designs to life.
Applications Unveiled: Where Aluminum 3D Printed Cases Shine in B2B and Niche Markets
While the idea of a 3D printed aluminum case might initially evoke images of bespoke luxury accessories, the applications extend far beyond mere aesthetics, particularly into demanding B2B and specialized industrial sectors. The unique combination of design freedom, material properties, and low-to-mid volume production feasibility offered by metal AM opens doors for innovative solutions where traditional manufacturing falls short. Procurement managers and engineers seeking advanced solutions should consider these key application areas:
- Ruggedized Device Protection:
- Target Users: Military personnel, first responders, field engineers, construction workers, outdoor adventurers.
- Requirements: Extreme durability, impact resistance, environmental sealing (dust/water), secure mounting points.
- AM Advantage: Aluminum alloys like AlSi10Mg provide superior impact resistance compared to plastics. AM allows for integrated shock-absorbing structures (e.g., internal lattice geometries), reinforced corners, and custom-fit seals, often consolidated into a single printed part. Companies acting as rugged phone case suppliers или industrial device housing manufacturers can leverage AM for low-volume, high-performance custom orders.
- Met3dp Edge: Met3dp’s high-accuracy printers ensure precise fits for sealing and component mounting, critical for ruggedized performance. Our quality-controlled powders guarantee consistent material properties for reliable impact protection.
- High-Performance Laptop and Tablet Shells:
- Target Users: Gamers, creative professionals (video editing, CAD), engineers running simulations, users of high-power mobile workstations.
- Requirements: Efficient heat dissipation, lightweight construction, high rigidity, premium feel.
- AM Advantage: Aluminum’s inherent thermal conductivity is a major benefit. 3D printing allows for the design of integrated heat sinks, complex airflow channels, and optimized vent patterns directly into the laptop shell, impossible or prohibitively expensive with CNC machining. Topology optimization can significantly reduce weight while maintaining structural integrity. Performance laptop shell manufacturers can use AM to create superior thermal management solutions for cutting-edge hardware.
- Met3dp Edge: Met3dp’s expertise in printing complex geometries and our range of high-performance powders enable the creation of highly optimized, lightweight, and thermally efficient shells.
- Custom Medical Device Casings:
- Target Users: Hospitals, clinics, diagnostic labs, medical device manufacturers.
- Requirements: Biocompatibility (potentially requiring specific coatings or alloys), sterilizability, custom shapes for specific diagnostic tools or wearable monitors, EMI shielding.
- AM Advantage: Metal AM allows for patient-specific or device-specific enclosures. Aluminum can be easily post-processed (e.g., anodized, coated) to meet specific surface requirements. Complex internal features for mounting sensors or electronics can be integrated directly. AM enables rapid prototyping and iteration of custom medical device casings during the development cycle.
- Met3dp Edge: While AlSi10Mg/AlSi7Mg aren’t typically primary choices for direct biocompatibility (unlike Titanium alloys, which Met3dp also supplies), they are excellent for external casings. Met3dp’s process control ensures the cleanability and dimensional accuracy required in medical applications.
- Luxury and Bespoke Accessories:
- Target Users: High-end consumers, corporate gifting, limited edition product designers.
- Requirements: Unique aesthetics, intricate designs, personalization (monograms, logos), premium materials, exclusivity.
- AM Advantage: The ultimate platform for unique designs. Intricate patterns, non-traditional shapes, and personalized elements can be easily incorporated without tooling limitations. The inherent quality of metal provides a premium feel unattainable with plastic. This allows brands to offer truly bespoke phone cases or limited-run accessories.
- Met3dp Edge: Our high-resolution printing capabilities can capture fine details, enabling intricate aesthetic features on luxury goods.
- Rapid Prototyping and Bridge Production (B2B):
- Target Users: Product designers, R&D departments, startups developing new electronic devices.
- Requirements: Fast turnaround for functional prototypes, testing form/fit/function with production-intent materials, low-volume initial runs before mass production tooling.
- AM Advantage: Metal AM is significantly faster than creating injection mold tools or complex multi-axis CNC setups for initial prototypes. Prototype metal cases B2B allow engineers to quickly validate designs using durable, functional aluminum parts that accurately mimic final product properties. It can also serve as “bridge production” – fulfilling initial low-volume orders while mass production methods are being established.
- Met3dp Edge: Met3dp offers comprehensive services, supporting clients from prototyping through to potential low-volume production runs, ensuring a smooth transition and leveraging our efficient металлическая 3D-печать процессы.
Table: Key Applications & AM Benefits for Aluminum Cases
Область применения | Key Requirements | Primary AM Advantages | Target B2B Keywords |
---|---|---|---|
Ruggedized Devices | Durability, Impact Resistance, Sealing | Integrated complex structures, High strength-to-weight, Custom fits | Rugged phone case supplier, Industrial device housing |
Performance Laptops/Tablets | Heat Dissipation, Lightweight, Rigidity | Integrated cooling channels, Topology optimization, Premium feel | Performance laptop shell manufacturer, Thermal solutions |
Custom Medical Devices | Specific shapes, Sterilizability, Potential Shielding | Patient/Device-specific designs, Rapid prototyping, Feature integration | Custom medical device casing, Medical prototyping |
Luxury/Bespoke Goods | Unique Aesthetics, Personalization, Exclusivity | Extreme design freedom, Intricate details, Premium material feel | Bespoke phone cases, Limited edition accessories |
Prototyping & Bridge Prod. | Speed, Functional Testing, Low-Volume Viability | Fast turnaround, Production-intent material testing, Tooling avoidance, On-demand runs | Prototype metal cases B2B, Low-volume manufacturing |
Export to Sheets
Универсальность aluminum enclosure applications via 3D printing extends further into areas like custom drone bodies, specialized camera housings, casings for scientific instruments, and protective enclosures for IoT devices in industrial settings. For procurement managers and engineers evaluating manufacturing methods for bulk electronics enclosures or specialized casings, metal AM offers a compelling, flexible, and increasingly cost-effective alternative, especially when complexity, customization, or speed are key drivers.
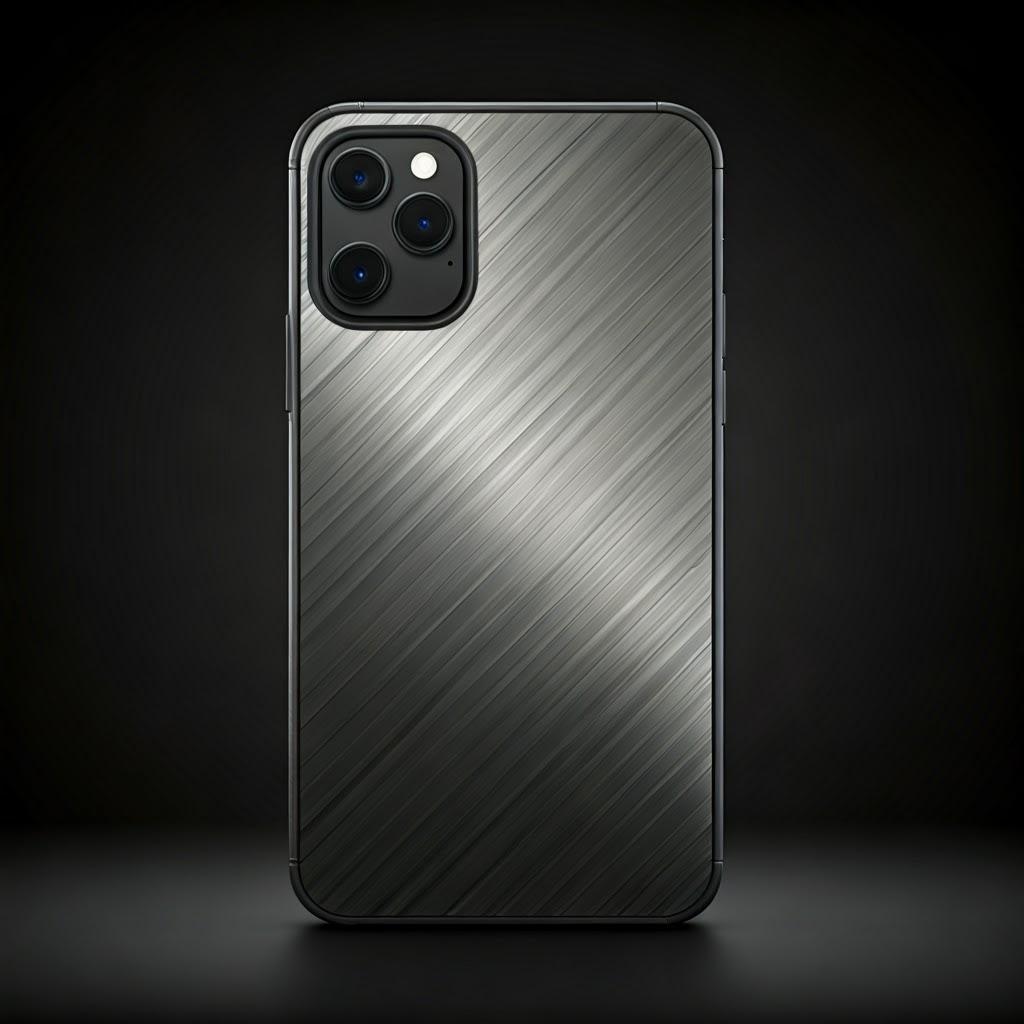
The Additive Advantage: Why Metal 3D Printing Outperforms Traditional Methods for Custom Cases
When considering the production of custom phone cases, laptop shells, or specialized electronic enclosures, particularly from metals like aluminum, engineers and procurement specialists traditionally weigh options like CNC machining, die casting, or potentially sheet metal fabrication. However, аддитивное производство металлов (AM) introduces a paradigm shift, offering distinct advantages, especially when dealing with complexity, customization, and low-to-mid volume production runs. Understanding the benefits of metal AM vs. CNC or molding is crucial for making informed manufacturing decisions and calculating the true metal 3D printing ROI.
1. Unmatched Design Freedom & Complexity:
- AM: Builds parts layer-by-layer, allowing for highly complex internal and external geometries that are impossible or prohibitively expensive to create with traditional methods. Think internal cooling channels for laptops, integrated snap-fits, complex lattice structures for weight reduction and shock absorption, or intricate artistic patterns. Additive manufacturing design freedom is perhaps its most significant advantage.
- CNC Machining: A subtractive process that removes material from a solid block. Internal features are difficult and require specific tooling and multi-axis machines. Complex curves and undercuts increase machining time and cost significantly. Material waste can also be substantial.
- Injection Molding/Casting: Requires expensive molds or dies. While excellent for high volumes of simpler parts, the tooling cost makes it uneconomical for custom or low-volume runs. Design changes require costly mold modifications. Complexity is limited by the ability to create and demold the part.
2. Rapid Prototyping & Accelerated Iteration:
- AM: Allows designers to go directly from a CAD file to a physical metal part, often within days. This drastically speeds up the design validation process. Multiple iterations can be printed and tested quickly, enabling faster product development cycles for rapid prototyping aluminum parts.
- Traditional: Creating molds or complex CNC programs takes weeks or even months, significantly slowing down prototyping and iteration.
3. Ideal for Customization & Low-Volume Production:
- AM: Excels where mass production falters – personalization and low-volume metal production. Each print can be unique without any tooling changes. This is ideal for bespoke luxury items, patient-specific medical devices, or fulfilling small batch orders for niche markets. The cost per part is less dependent on volume compared to molding.
- Traditional: High setup costs (tooling, programming) make traditional methods cost-prohibitive for producing small quantities of custom parts.
4. Part Consolidation & Weight Reduction:
- AM: Enables the redesign of assemblies into single, complex components. This reduces part count, assembly time, and potential points of failure. Furthermore, AM allows for lightweighting strategies like topology optimization and lattice structures, removing material from non-critical areas while maintaining strength, crucial for portable electronics cases.
- Traditional: Limited ability to consolidate complex parts. Weight reduction often relies on using thinner materials (potentially compromising strength) or extensive, costly machining.
5. Material Efficiency:
- AM (Powder Bed Fusion): Uses only the material necessary to build the part and its supports, significantly reducing waste compared to subtractive methods, especially for complex geometries (buy-to-fly ratio). While unused powder needs careful handling and recycling, the initial material usage is often more efficient.
- CNC Machining: Can generate significant waste (chips) as material is cut away from a larger block.
6. On-Demand Manufacturing & Digital Inventory:
- AM: Enables a shift towards digital inventories. Designs can be stored digitally and printed on demand when needed, reducing physical inventory costs and warehousing needs. This is particularly beneficial for spare parts or fulfilling infrequent orders.
Table: Metal AM vs. Traditional Methods for Custom Aluminum Cases
Характеристика | Metal Additive Manufacturing (LPBF/SEBM) | Обработка с ЧПУ | Injection Molding/Casting (Metal) |
---|---|---|---|
Сложность конструкции | Very High (Internal channels, lattices, organic shapes) | Moderate to High (Limited internal features) | Moderate (Limited by demolding/tooling) |
Персонализация | Excellent (Each part can be unique) | Possible but costly reprogramming | Very Expensive (Requires new molds/dies) |
Lead Time (Proto) | Fast (Days) | Moderate (Days to Weeks, depends on complexity) | Slow (Weeks to Months due to tooling) |
Стоимость оснастки | Никто | Low (Fixturing) to Moderate (Complex setups) | Очень высокий |
Ideal Volume | Prototypes, Low-to-Mid Volume, Custom | Prototypes, Low-to-High Volume (Simpler parts) | High to Very High Volume |
Материальные отходы | Low to Moderate (Support structures, powder reuse) | Moderate to High (Chips) | Low (Runners/gates) |
Консолидация частей | Отличный | Limited | Limited |
Облегчение | Excellent (Topology optimization, lattices) | Possible but often less efficient | Limited |
Export to Sheets
While traditional methods remain the most cost-effective solution for mass-producing millions of identical, relatively simple cases, металлическая 3D-печать clearly offers superior flexibility, speed, and design capability for complex geometry manufacturing, custom runs, and rapid development cycles. For businesses looking to innovate in the electronics enclosure space, partnering with an expert provider like Met3dp, equipped with advanced способы печати and materials, unlocks these powerful advantages, enabling the creation of truly differentiated products.
Material Matters: Choosing AlSi10Mg & AlSi7Mg Aluminum Powders for Optimal Performance
The success of any metal 3D printing project hinges critically on selecting the right material. For custom phone and laptop cases, where a balance of lightweight strength, durability, thermal performance, and aesthetics is required, specific aluminum alloys stand out. AlSi10Mg и AlSi7Mg are two of the most widely used aluminum alloys in additive manufacturing, particularly via Laser Powder Bed Fusion (LPBF), also known as Selective Laser Melting (SLM). Understanding their properties and why they are suitable is essential for engineers and designers.
Aluminum Silicon Magnesium Alloys (Al-Si-Mg): An Overview
These alloys belong to the 4xxx series (based on casting alloy classifications) and are known for their excellent casting characteristics, which translate well into good printability in AM processes.
- Кремний (Si): Primarily added to improve fluidity in the molten state and reduce solidification shrinkage. This enhances weldability (crucial in layer-by-layer fusion) and printability, allowing for the creation of complex geometries with finer details and reducing the risk of cracking during the rapid heating and cooling cycles of AM.
- Магний (Mg): Allows the alloy to be precipitation-hardened through heat treatment (like T6). This process significantly increases the strength and hardness of the final part compared to its as-printed state.
AlSi10Mg:
- Состав: Typically contains 9-11% Silicon and 0.2-0.45% Magnesium.
- Характеристики: Offers a good balance of strength, hardness, thermal properties, and dynamic loads resistance. It’s often considered the workhorse aluminum alloy for AM. It exhibits excellent printability due to the relatively high silicon content.
- Приложения: Widely used in automotive (heat exchangers, engine parts), aerospace (ducts, housings), and general engineering components. Its properties make it highly suitable for protective casings and enclosures requiring good mechanical performance.
AlSi7Mg:
- Состав: Contains 6.5-7.5% Silicon and 0.25-0.45% Magnesium.
- Характеристики: Compared to AlSi10Mg, AlSi7Mg generally offers slightly better ductility (elongation) and potentially higher strength after appropriate heat treatment. It might be chosen when slightly improved toughness or specific strength characteristics after heat treatment are desired. Its printability is still very good, though perhaps marginally more challenging than AlSi10Mg due to the lower Si content.
- Приложения: Also used in aerospace and automotive, sometimes preferred where ductility is a key design consideration alongside strength. It can be a good choice for cases that might experience flexing or require higher fracture toughness.
Why AlSi10Mg & AlSi7Mg for Electronics Cases?
- Легкий вес: Aluminum alloys have a low density (approx. 2.67 g/cm³), crucial for portable devices like phones and laptops where minimizing weight is paramount.
- Хорошее соотношение прочности и веса: Especially after heat treatment, these alloys provide significant strength, offering robust protection against drops, impacts, and bending without adding excessive bulk.
- Отличная теплопроводность: Aluminum naturally dissipates heat well (around 130-150 W/m·K for these alloys). This is a major advantage for laptop shells or cases housing powerful processors, helping to prevent overheating and maintain performance. AM allows designers to enhance this further with integrated cooling features.
- Коррозионная стойкость: Aluminum forms a passive oxide layer, providing good resistance to atmospheric corrosion. This can be further enhanced with post-processing like anodizing.
- Возможность печати: As mentioned, the silicon content ensures good processing characteristics in LPBF systems, enabling the production of complex and detailed case designs reliably.
- Параметры постобработки: These alloys readily accept various post-processing steps critical for final parts: heat treatment (T6 aging for peak strength), surface finishing (bead blasting, polishing), machining (for critical tolerances), and coating/anodizing (for enhanced durability and aesthetics/color).
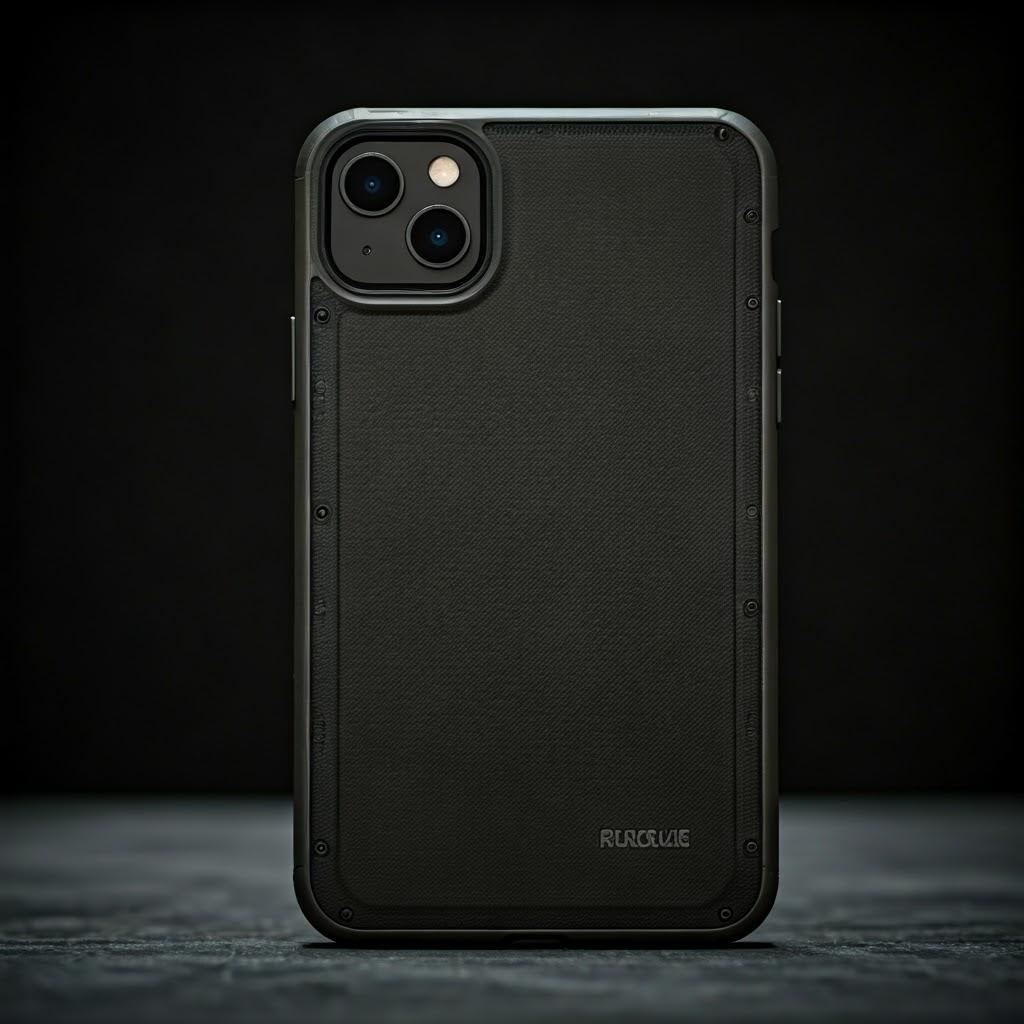
Table: Typical Properties of 3D Printed AlSi10Mg & AlSi7Mg (LPBF, Heat Treated – T6)
Недвижимость | Единица | AlSi10Mg (Typical T6) | AlSi7Mg (Typical T6) | Significance for Cases |
---|---|---|---|---|
Плотность | г/см³ | ~2.67 | ~2.67 | Lightweight construction |
Предельная прочность на разрыв | MPa | 330 – 430 | 350 – 450 | Resistance to breaking under tension (e.g., bending) |
Предел текучести (0,2%) | MPa | 230 – 350 | 250 – 370 | Resistance to permanent deformation (dents) |
Удлинение при разрыве | % | 3 – 10 | 5 – 12 | Ductility, resistance to fracture (toughness indicator) |
Твердость | HBW | 90 – 125 | 100 – 130 | Resistance to scratching and surface wear |
Теплопроводность | Вт/(м-К) | ~130 | ~140 | Efficient heat dissipation |
Модуль упругости | ГПа | ~70 | ~70 | Stiffness, resistance to flexing |
Export to Sheets
(Note: Exact properties depend heavily on print parameters, machine used, build orientation, and specific heat treatment cycles. These are representative values.)
The Critical Role of High-Quality Metal Powders – The Met3dp Advantage
The final properties and quality of a 3D printed aluminum case are not just dependent on the alloy choice but profoundly influenced by the quality of the металлический порошок itself. Inferior powders can lead to defects like porosity, poor surface finish, inconsistent mechanical properties, and even print failures.
Met3dp places immense emphasis on powder quality. We utilize Ведущие в отрасли технологии газового распыления и PREP to produce highly spherical aluminum powder with excellent flowability, minimal satellite particles, and controlled particle size distribution (PSD).
- Газовая атомизация: Our unique nozzle and gas flow designs create highly spherical particles, which pack densely and flow uniformly in the printer’s recoater system. This is crucial for achieving fully dense parts (>99.5%) with predictable mechanical properties.
- PREP (Plasma Rotating Electrode Process): Used for specific reactive or high-purity alloys, ensuring ultra-low oxygen and satellite content for demanding applications.
- Контроль качества: Rigorous testing ensures chemical composition accuracy, consistent PSD, high sphericity, and good flowability batch after batch.
By using premium Met3dp powders, manufacturers sourcing aluminum alloys for 3D printing can be confident in achieving:
- High Density & Low Porosity: Leading to superior strength and fatigue life.
- Consistent Mechanical Properties: Ensuring reliable performance across multiple builds.
- Good Surface Finish: Reducing the need for extensive post-processing.
- Improved Printability: Reducing the risk of build failures and ensuring feature accuracy.
Choosing the right material is the foundation, but choosing a поставщик металлического порошка like Met3dp, committed to the highest quality standards through advanced manufacturing like gas atomization, ensures that the full potential of AlSi10Mg and AlSi7Mg can be realized in your custom electronic cases. Explore our diverse range of high-performance metal powders on our product page. Sources and related content
Designing for Durability & Functionality: DfAM for Aluminum Electronics Cases
Successfully leveraging metal additive manufacturing for custom aluminum phone and laptop cases isn’t just about choosing the right material and printer; it hinges on adopting a Проектирование для аддитивного производства (DfAM) mindset. DfAM involves optimizing a part’s design specifically for the layer-by-layer build process, maximizing its benefits while mitigating potential challenges. For engineers and designers creating optimized aluminum cases, applying DfAM principles is crucial for achieving desired durability, functionality, aesthetics, and cost-effectiveness. These principles go beyond simple geometry creation and influence everything from printability to final performance.
Key DfAM Guidelines for Metal AM Cases:
- Strategic Build Orientation:
- Влияние: Orientation affects surface finish (stair-stepping on shallow angles), support requirements (overhangs), print time (Z-height), and potentially anisotropic mechanical properties (though less pronounced in metals than polymers).
- Considerations for Cases:
- Prioritize critical cosmetic surfaces: Orient the part so key visual surfaces (e.g., the outer face of a phone case) are vertical or upward-facing for better finish.
- Minimize supports: Angled orientations can reduce the need for supports on overhangs (typically angles > 45° from horizontal are self-supporting). However, this might compromise surface finish on those angled faces.
- Optimize for Z-Height: Taller prints take longer. Orienting a flat case horizontally minimizes print time but maximizes support needs for the first layer off the build plate.
- Thermal Management: Orientation can influence heat dissipation during the print, impacting residual stress.
- Met3dp Approach: Our application engineers work with clients to determine the optimal orientation based on design priorities – balancing surface finish, support minimization, dimensional accuracy, and print efficiency.
- Intelligent Support Structure Design:
- Necessity: In Powder Bed Fusion (LPBF/SEBM), supports are vital. They anchor the part to the build plate, prevent warping due to thermal stress, support overhanging features, and help conduct heat away from the melt pool.
- Design Implications: Supports consume material, add print time, require removal (post-processing), and leave witness marks on the surface.
- DfAM Strategies:
- Minimize Overhangs: Design with self-supporting angles (>45°) wherever possible. Use chamfers or fillets instead of sharp horizontal overhangs.
- Design for Accessibility: Ensure support structures are easily reachable for removal tools (manual or CNC). Avoid trapping supports in inaccessible internal cavities unless absolutely necessary and designed for powder removal.
- Optimize Support Type: Use appropriate support structures (e.g., block, line, cone, tree) depending on the location and function. Software tools and experienced providers like Met3dp optimize support generation.
- Integrate Supports: Sometimes, features intended for support can be integrated into the functional design itself.
- Wall Thickness and Feature Size:
- Minimums: There’s a limit to how thin a wall or feature can be reliably printed (often around 0.4-0.8 mm, depending on machine, material, and feature height). Designing below this can lead to incomplete features or warping.
- Равномерность: While AM allows variable thickness, overly abrupt changes can induce stress. Aim for smooth transitions where thickness changes are necessary. Uniform thickness generally promotes better thermal stability during the print.
- Case Design: Ensure case walls provide adequate rigidity and protection without being unnecessarily thick, adding weight and cost. Ribbing or internal structures can add stiffness to thin walls.
- Holes, Channels, and Cavities:
- Hole Design: Vertical holes generally print more accurately than horizontal ones. Small horizontal holes might print slightly elliptical and may require support depending on size and orientation. Consider designing teardrop shapes for self-supporting horizontal holes.
- Internal Channels: Crucial for thermal management design (airflow, liquid cooling integration) or housing internal components. Ensure channels are self-supporting or designed with access for support/powder removal. Escape holes are essential for clearing trapped powder.
- Minimum Size: Very small holes or channels (< 0.5mm) can be challenging to print reliably and clear of powder.
- Lightweighting Strategies:
- Topology Optimization: Use FEA-driven software to remove material from areas experiencing low stress, creating organic-looking, highly efficient structures optimized for specific load cases. Ideal for minimizing weight in laptop shells or protective frames while maintaining stiffness.
- Решетчатые структуры: Incorporate internal lattice structures (e.g., gyroid, honeycomb, diamond) to significantly reduce weight and material usage while providing good structural support, energy absorption (impact resistance), or increased surface area for heat dissipation. Lightweighting strategies AM are a key benefit for portable electronics.
- Integrated Features:
- Консолидация частей: Redesign assemblies into a single printed part. For cases, this could mean integrating mounting bosses, cable clips, battery holders, or even spring features directly into the case body. This reduces assembly time, part count, and potential failure points.
- Threads: Small threads can sometimes be printed directly but often lack the strength and precision of machined threads. It’s usually better to print pilot holes and tap them afterwards, or design for threaded inserts.
- Snap-Fits: Can be printed, but material properties (ductility, fatigue) must be considered. Design requires careful attention to clearances and stress concentrations.
Table: DfAM Principles for Aluminum Cases
DfAM Principle | Рассмотрение | Benefit for Cases | Keywords |
---|---|---|---|
Orientation | Surface finish, supports, time, stress | Optimize aesthetics, reduce post-processing, cost | Design for metal 3D printing |
Support Design | Minimization, accessibility, type | Reduce cost/time, improve surface, ensure print success | Support structure optimization |
Толщина стенки | Minimums, uniformity, transitions | Ensure printability, structural integrity, manage stress | Optimizing aluminum cases |
Holes/Channels | Size, orientation, powder removal | Enable ports, vents, cooling, component integration | Thermal management design |
Облегчение | Topology optimization, lattice structures | Reduce weight, material cost, improve performance | Lightweighting strategies AM |
Feature Integration | Part consolidation, threads, snap-fits, bosses | Reduce assembly, improve reliability, add functionality | Integrated features 3D printing, part consolidation |
Export to Sheets
By embracing these DfAM guidelines, designers can fully exploit the capabilities of metal 3D printing, moving beyond simply replicating traditionally manufactured designs to creating truly innovative, high-performance, and optimized aluminum cases for consumer electronics. Collaborating with experienced partners like Met3dp ensures these principles are applied effectively, leveraging advanced software tools and process knowledge.
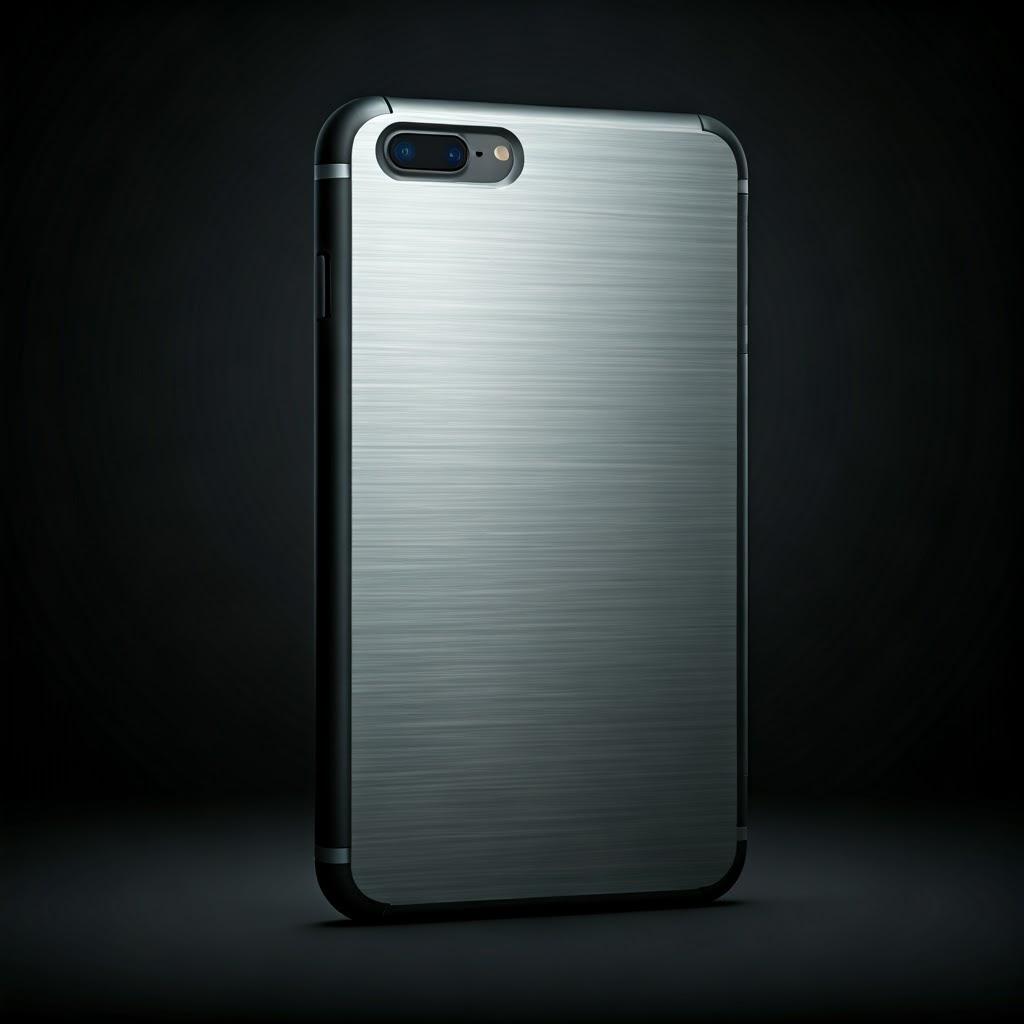
Precision and Aesthetics: Achieving Tight Tolerances, Superior Surface Finish, and Dimensional Accuracy
For products like phone cases and laptop shells, where fit, feel, and finish are paramount, understanding the achievable levels of precision and aesthetics with metal 3D printing is crucial. While AM offers incredible design freedom, it has inherent characteristics regarding tolerances, surface finish, and dimensional accuracy that engineers and procurement managers must consider. Partnering with a capable provider like Met3dp, utilizing high-end equipment and robust process controls, maximizes the potential for creating high-precision enclosures.
Точность размеров:
- Typical Expectations: For processes like LPBF using aluminum alloys, typical dimensional accuracy is often cited in the range of ±0.1 mm to ±0.2 mm, or ±0.1% to ±0.2% of the nominal dimension, whichever is greater. However, this is a general guideline.
- Factors Influencing Accuracy:
- Калибровка машины: Regular calibration and maintenance of the 3D printer are fundamental.
- Параметры процесса: Laser power, scan speed, layer thickness, and hatching strategy all influence the melt pool size and stability, affecting accuracy.
- Thermal Effects: Residual stress build-up and potential warping during the print or after removal from the build plate can impact final dimensions. Effective thermal management and stress relief are key.
- Part Geometry & Size: Larger parts and complex geometries are more prone to deviation due to accumulated thermal stress.
- Постобработка: Steps like heat treatment can sometimes cause minor dimensional changes (shrinkage/growth). Support removal can also affect local accuracy.
- Met3dp’s Commitment: Met3dp utilizes industry-leading printers known for their accuracy and reliability. Our stringent process controls, material quality assurance, and optimized parameters aim to achieve the best possible dimensional accuracy additive manufacturing offers, consistently meeting client specifications.
Surface Finish (Roughness – Ra):
- As-Printed Reality: Metal AM parts inherently have a rougher surface finish compared to machined or molded parts. The surface finish aluminum parts Ra (average roughness) typically ranges from 5 µm to 20 µm, depending heavily on:
- Orientation: Vertical walls tend to have a better finish than top-facing (up-skin) or bottom-facing (down-skin) surfaces. Shallow angled surfaces exhibit noticeable “stair-stepping” effects.
- Parameters: Layer thickness, powder particle size, and energy input influence the surface texture. Finer powders and thinner layers generally yield smoother finishes but increase print time.
- Support Interface: Surfaces where support structures were attached will be rougher and show witness marks after removal, requiring further finishing.
- Achieving Desired Aesthetics: For consumer electronics cases, the as-printed finish is often insufficient for cosmetic requirements. Post-processing is usually necessary.
- Matte Finish: Achieved through bead blasting or sandblasting. This provides a uniform, non-reflective texture, effective at hiding layer lines and minor imperfections.
- Satin/Brushed Finish: Can be achieved through controlled abrasive processes or light machining/brushing.
- Polished Finish: Requires multi-step grinding, sanding, and buffing processes. Achievable on aluminum AM parts but can be labor-intensive, especially on complex geometries.
- Met3dp Solutions: We offer various cosmetic finishing metal AM options and advise clients on the most suitable and cost-effective methods to achieve their desired aesthetic outcome, balancing finish requirements with budget and lead time.
Tolerances:
- General AM Tolerances: The dimensional accuracy mentioned above (±0.1 to ±0.2 mm) defines the general tolerances achievable directly from the printing process for non-critical features.
- Critical Tolerances: For features requiring tighter control (e.g., interfaces with screens, ports connecting to other components, bearing fits), the standard AM tolerances may not suffice.
- Solution – Hybrid Approach: The most common solution is a hybrid manufacturing approach. Design the part for AM, print it near-net-shape, and then use CNC machining as a post-processing step to achieve tight tolerances (potentially down to ±0.01 mm or better) on specific critical features. This combines the design freedom of AM with the precision of subtractive machining.
- Design Consideration: When planning for post-machining, ensure sufficient material allowance is added to the relevant surfaces in the CAD model before printing (e.g., add 0.5-1.0 mm stock).
Table: Precision & Aesthetics Overview for Aluminum AM Cases
Аспект | Typical As-Printed State (AlSi10Mg/AlSi7Mg) | Key Influencing Factors | Enhancement Methods / Solutions | Keywords |
---|---|---|---|---|
Точность размеров | ±0.1 to ±0.2 mm or ±0.1-0.2% | Machine, Parameters, Thermal, Geometry | Process control, Calibration, Post-machining critical features | Dimensional accuracy additive manufacturing |
Surface Finish (Ra) | 5 – 20 µm | Orientation, Parameters, Supports | Bead blasting, Polishing, Tumbling, Coating | Surface finish aluminum parts Ra |
General Tolerances | Matches Dimensional Accuracy | See Accuracy Factors | Process optimization, Design for AM | Metal 3D printing tolerances |
Critical Tolerances | Often insufficient | Feature function, Mating requirements | Post-process CNC machining, Design with machining stock | High-precision enclosures, CNC machining 3D prints |
Эстетика | Often requires improvement | Surface finish, Uniformity, Defects | Blasting, Polishing, Anodizing, Painting | Cosmetic finishing metal AM |
Export to Sheets
By understanding these characteristics and leveraging the capabilities of experienced providers like Met3dp, companies can confidently utilize aluminum 3D printing to produce electronics cases that meet demanding requirements for fit, form, function, and the premium aesthetic expected in today’s market.
Beyond the Print: Essential Post-Processing Techniques for Aluminum Cases
Producing a custom aluminum case using metal 3D printing rarely ends when the printer stops. The “as-printed” part, while geometrically complete, requires several crucial post-processing metal 3D prints steps to achieve the desired mechanical properties, dimensional accuracy, surface finish, and overall quality. These steps are integral to the manufacturing workflow and significantly impact the final product’s performance and appearance. Understanding this workflow is vital for procurement managers and engineers planning AM projects.
Typical Post-Processing Workflow for Aluminum (AlSi10Mg/AlSi7Mg) Cases:
- Stress Relief Heat Treatment:
- Цель: Absolutely essential for parts made via LPBF. The rapid heating and cooling cycles during printing induce significant internal stresses. Without stress relief, the part could warp or distort upon removal from the build plate.
- Процесс: The entire build plate with the printed part(s) still attached is heated in a controlled atmosphere furnace (typically argon or nitrogen to prevent oxidation) to a specific temperature (e.g., ~300°C for AlSi alloys), held for a period (e.g., 2 hours), and then slowly cooled.
- Importance: Stabilizes the part’s dimensions and microstructure before further processing.
- Part Removal from Build Plate:
- Method: Once cooled after stress relief, the part needs to be separated from the metal build plate it was printed on. Common methods include:
- Wire Electrical Discharge Machining (Wire EDM): Precise, minimal force, good for complex or delicate parts.
- Bandsaw: Faster and lower cost for simpler geometries, but less precise and requires a sufficiently rigid part.
- Consideration: The removal method can influence the finish of the part’s base surface.
- Method: Once cooled after stress relief, the part needs to be separated from the metal build plate it was printed on. Common methods include:
- Демонтаж опорной конструкции:
- Necessity: Supports must be removed to reveal the final part geometry.
- Методы:
- Manual Removal: Supports are often designed with weakened connection points and can sometimes be broken off by hand or with simple tools. Requires careful handling to avoid damaging the part.
- Machining: CNC milling or grinding can be used to remove supports, especially block supports or those in less accessible areas. This often provides a cleaner surface finish at the interface.
- Wire EDM / Grinding: Also used for precise removal.
- Вызов: Can be labor-intensive and time-consuming, especially for complex parts with extensive internal supports. DfAM plays a crucial role in simplifying this step.
- Solutionizing & Aging Heat Treatment (e.g., T6 Temper):
- Цель: To significantly enhance the mechanical properties (strength, hardness) of AlSi10Mg and AlSi7Mg alloys. As-printed aluminum often has moderate strength but good ductility. Heat treatment AlSi10Mg / AlSi7Mg unlocks their full potential.
- Process (T6 Example):
- Растворение: Heating the part to a high temperature (e.g., ~515-535°C) to dissolve alloying elements (Mg, Si) into the aluminum matrix, followed by rapid quenching (e.g., in water) to trap them in a supersaturated solid solution.
- Artificial Aging: Reheating the part to a lower temperature (e.g., ~160-175°C) for several hours, allowing controlled precipitation of fine hardening phases (Mg₂Si) within the aluminum matrix.
- Result: A significant increase in yield strength, tensile strength, and hardness, making the case much more durable.
- Surface Finishing & Smoothing:
- Цель: To improve aesthetics, remove layer lines, smooth support witness marks, and prepare the surface for subsequent coatings.
- Common Techniques for Aluminum AM:
- Bead Blasting / Sand Blasting: Propels abrasive media (glass beads, aluminum oxide) at the surface, creating a uniform, matte finish. Very effective for surface finishing aluminum AM части.
- Tumbling / Vibratory Finishing: Parts are placed in a tub with media that vibrates or tumbles, causing friction that deburrs edges and smooths surfaces. Good for batch processing.
- Grinding / Polishing: Manual or automated processes using progressively finer abrasives to achieve smoother, brighter, or even mirror-like finishes. Can be targeted to specific areas.
- CNC Machining (Optional but often necessary):
- Цель: To achieve tight tolerances on critical features (mating surfaces, port openings, threaded holes), improve surface finish on specific areas, or create features not easily formed during printing.
- Применение: Frequently used for interfaces, ensuring precise fit and function of the electronic components housed within the case. CNC machining 3D prints is a key part of the hybrid approach.
- Cleaning:
- Цель: To remove any residual powder, machining fluids, or contaminants from previous steps.
- Методы: Ultrasonic cleaning, solvent washing, compressed air.
- Coating / Surface Treatment (Optional):
- Цель: To enhance corrosion resistance, improve wear resistance, add color, or provide specific functional properties (e.g., electrical insulation, EMI shielding).
- Options for Aluminum:
- Anodizing: An electrochemical process that grows a durable, corrosion-resistant oxide layer on the surface. Can be dyed in various colors. Anodizing 3D printed aluminum is very common for aesthetic and protective reasons.
- Painting / Powder Coating: Application of organic coatings for color and protection.
- Chemical Conversion Coating (e.g., Chromate/Non-Chromate): Improves corrosion resistance and paint adhesion.
- Plating (e.g., Nickel, Gold): For conductivity, shielding, or wear resistance.
- Inspection & Quality Assurance (QA):
- Цель: To verify that the final part meets all specifications.
- Методы: Dimensional inspection (calipers, CMM, 3D scanning), visual inspection, surface roughness measurement, material testing (if required), NDT (e.g., CT scanning to check for internal porosity in critical applications).
- Met3dp Commitment: Quality is paramount. Met3dp integrates quality assurance metal AM checks throughout the process, from powder analysis to final part inspection, ensuring parts meet the stringent requirements of industries like aerospace, medical, and high-performance electronics. Our comprehensive approach is detailed further when you learn О нас.
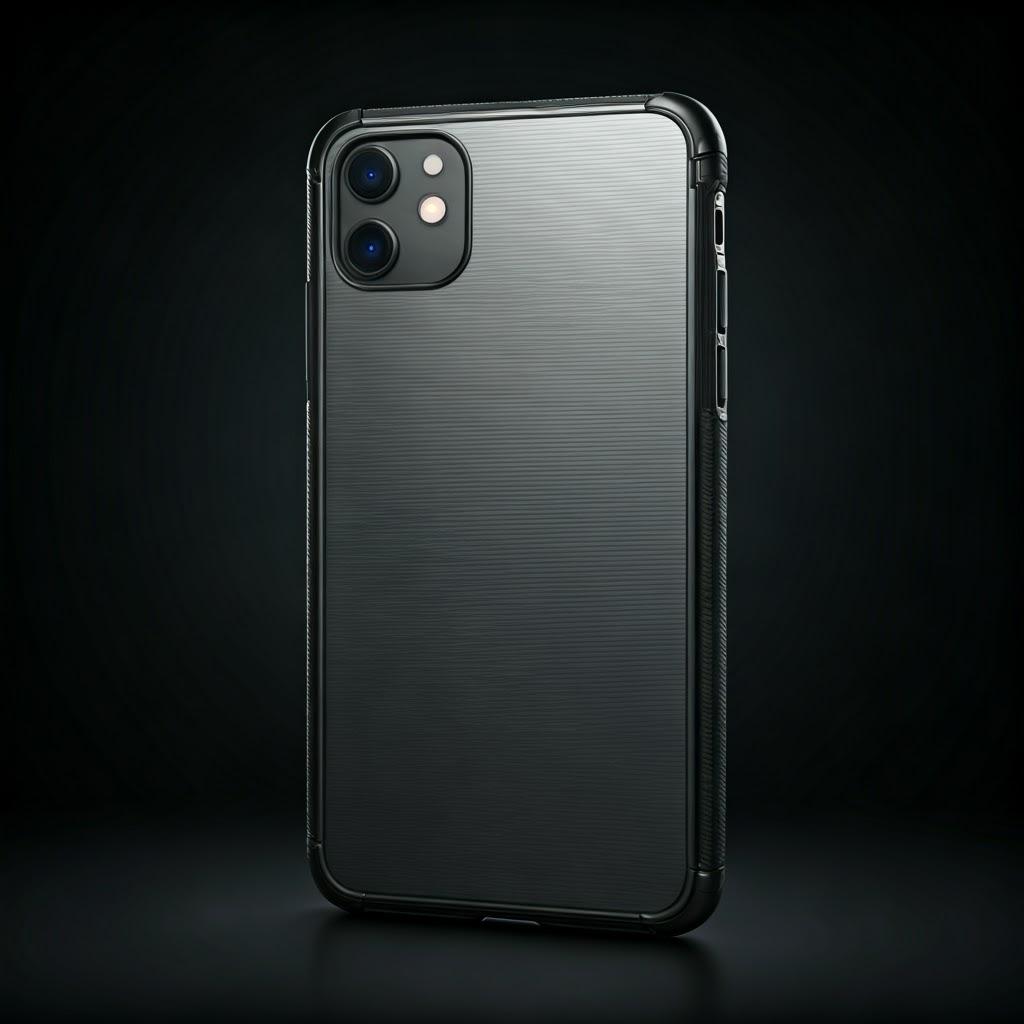
Table: Post-Processing Steps & Their Purpose for Aluminum Cases
Post-Processing Step | Primary Purpose | Typical Method(s) for Aluminum | Impact on Case Properties |
---|---|---|---|
Снятие стресса | Prevent warping/distortion | Furnace heating (inert atm.) | Стабильность размеров |
Part Removal | Separate part from build plate | Wire EDM, Bandsaw | Enables further processing |
Удаление опоры | Reveal final geometry | Manual breaking, Machining, Grinding | Final shape, Surface at interface |
Hardening Heat Treat (T6) | Increase strength & hardness | Solutionizing + Quenching + Aging | Enhanced durability, Mechanical performance |
Обработка поверхности | Improve aesthetics, Smoothness | Blasting, Tumbling, Polishing | Look & feel, Preparation for coating |
Обработка с ЧПУ | Achieve tight tolerances, Critical features/finish | Milling, Turning, Drilling, Tapping | Precision fit, Functionality |
Очистка | Remove contaminants | Ultrasonic, Solvent wash | Part cleanliness |
Coating/Surface Treatment | Enhance protection, Add color/functionality | Anodizing, Painting, Plating | Corrosion/wear resistance, Aesthetics |
Inspection & QA | Verify specifications | Dimensional checks, Visual, NDT | Conformance, Reliability |
Export to Sheets
Understanding this comprehensive post-processing chain is essential for accurately estimating costs, lead times, and ensuring the final aluminum case meets all functional and aesthetic requirements. It highlights that metal 3D printing is often the first crucial step in a multi-stage manufacturing process.
Navigating Potential Challenges: Ensuring Success in 3D Printing Aluminum Cases
While metal 3D printing offers transformative capabilities, like any advanced manufacturing process, it presents potential challenges. Awareness of these issues and partnering with an experienced metal printing quality control supplier like Met3dp, which employs robust mitigation strategies, is key to ensuring successful outcomes for your aluminum case projects. Proactively addressing these potential hurdles during design and production planning leads to higher quality parts, reduced costs, and shorter lead times.
Common Challenges in Metal AM (LPBF) and How to Overcome Them:
- Warping and Distortion:
- Cause: Significant temperature gradients between the molten pool and surrounding material create internal stresses that can cause the part to curl or distort, especially thin walls or large flat sections.
- Mitigation Strategies:
- Effective Support Strategy: Well-designed supports anchor the part firmly to the build plate and help manage thermal contraction.
- Optimized Print Parameters: Controlling laser power, scan speed, and strategy minimizes localized overheating and stress buildup.
- Build Plate Heating: Maintaining an elevated temperature on the build plate reduces the thermal gradient.
- Снятие стресса: Performing stress relief heat treatment before removing the part from the build plate is critical for avoiding warping aluminum AM.
- Design Modification: Avoiding large, unsupported flat areas; adding ribs for stiffness.
- Остаточное напряжение:
- Cause: Inherent consequence of the rapid heating/cooling cycles, even if warping is controlled. High residual stress can lead to premature failure, reduced fatigue life, or distortion during post-machining.
- Mitigation Strategies:
- Stress Relief Heat Treatment: The primary method to reduce residual stress to manageable levels.
- Parameter Optimization: Scan strategies (e.g., island scanning) can help distribute stress more evenly.
- Process Simulation: Advanced simulation tools can predict stress accumulation, guiding design and orientation choices.
- Пористость:
- Cause: Small voids within the printed material. Can be caused by gas entrapment (from improperly handled powder or shielding gas issues) or lack-of-fusion (insufficient energy input to fully melt powder). Porosity reduces density, strength, and fatigue resistance.
- Mitigation Strategies:
- High-Quality Powder: Using spherical, gas-atomized powder with low internal porosity and moisture content (like Met3dp’s powders) is crucial. Proper powder handling and storage are essential.
- Optimized Print Parameters: Ensuring sufficient energy density (laser power, speed, layer thickness) to achieve full melting and fusion between layers.
- Inert Atmosphere Control: Maintaining a high-purity argon or nitrogen atmosphere in the build chamber prevents oxidation and reduces gas porosity.
- Met3dp Expertise: Our deep understanding of metallurgy and process control ensures optimized parameters for porosity control additive manufacturing, achieving part densities typically exceeding 99.5%.
- Support Structure Removal Difficulty & Surface Impact:
- Cause: Poorly designed supports (too dense, inaccessible locations), strong bonding between support and part. Removal can be labor-intensive and potentially damage the part or leave significant witness marks.
- Mitigation Strategies:
- DfAM Focus: Designing parts to minimize the need for supports (self-supporting angles, orientation). Designing supports for easier access and removal (optimized interfaces, break-off points).
- Software Tools: Utilizing advanced support generation software with various structure types and optimization algorithms.
- Skilled Technicians: Experienced technicians using appropriate tools and techniques for removal.
- Постобработка: Planning for finishing steps (blasting, machining) to clean up support interface areas. Addressing support structure removal metal prints during the design phase saves time and cost later.
- Surface Finish Inconsistencies:
- Cause: Natural variations due to layer stepping, orientation (up-skin vs. down-skin vs. vertical), and support contact points.
- Mitigation Strategies:
- Strategic Orientation: Prioritizing critical surfaces for optimal orientation.
- Parameter Tuning: Adjusting parameters can influence finish, sometimes at the expense of speed.
- Post-Processing Plan: Accepting the as-printed finish variations and incorporating necessary finishing steps (blasting, polishing) into the production plan to achieve the final desired uniformity.
- Powder Removal from Internal Channels:
- Cause: Unfused powder can become trapped within complex internal geometries designed for cooling or lightweighting.
- Mitigation Strategies:
- DfAM for Drainage: Designing channels with sufficient diameter and incorporating strategically placed drain/access holes for powder evacuation.
- Post-Print Cleaning: Utilizing compressed air, vibration tables, or specialized powder removal systems.
- Design Validation: Considering powder removal limitations during the design phase.
- Achieving Very Fine Features/Details:
- Cause: Limited by factors like laser spot size, powder particle size distribution, and layer thickness. Very sharp edges might be slightly rounded.
- Mitigation Strategies:
- Process Selection: Choosing the right AM process variant and parameters optimized for detail resolution.
- Design Adaptation: Avoiding features smaller than the process capability or designing them to be finished via post-machining.
- Material Choice: Some materials may resolve finer features better than others.
Table: Common Metal AM Challenges & Mitigation Approaches
Испытание | Primary Cause(s) | Key Mitigation Strategy | Relevant Keywords |
---|---|---|---|
Warping / Distortion | Thermal stress, Insufficient support | Support strategy, Stress relief, Parameter tuning | Avoiding warping aluminum AM |
Остаточное напряжение | Rapid heating/cooling cycles | Stress relief heat treatment, Parameter optimization | Metal AM stress management |
Пористость | Gas entrapment, Lack-of-fusion, Poor powder | Quality powder, Optimized parameters, Atm. control | Porosity control additive manufacturing |
Support Removal Difficulty | Poor DfAM, Strong bonding | DfAM, Smart supports, Skilled labor, Post-proc. | Support structure removal metal prints |
Surface Finish Inconsistency | Layering effects, Orientation, Supports | Orientation, Post-processing plan, Parameters | Metal AM surface quality |
Trapped Powder | Complex internal channels, Lack of drain holes | DfAM (drainage), Post-print cleaning | Powder removal AM |
Fine Feature Resolution | Process limits (laser/powder/layer) | Process selection, Post-machining, Design adapt | High-resolution metal printing |
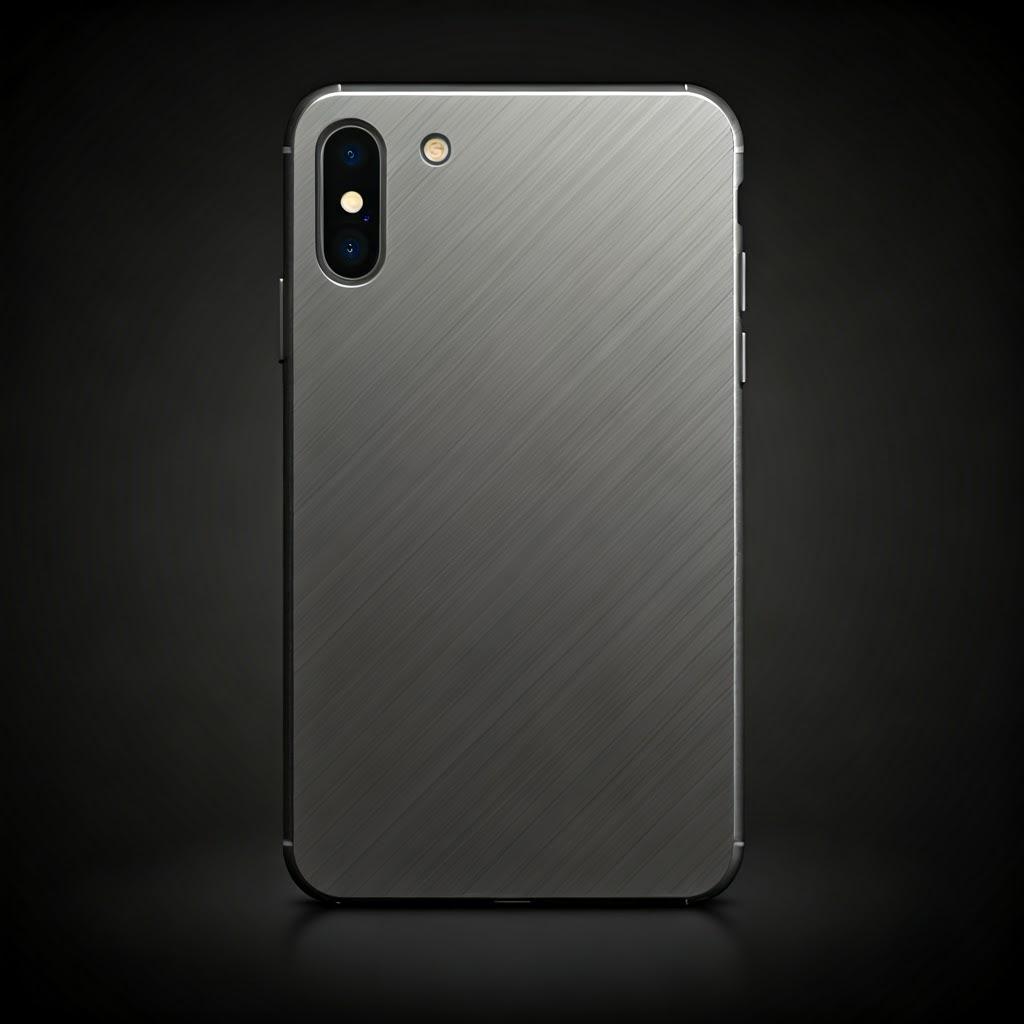
Export to Sheets
Overcoming these challenges requires a combination of robust machine technology, high-quality materials, optimized process parameters, adherence to DfAM principles, and skilled engineering and technical expertise. By partnering with a knowledgeable and experienced provider like Met3dp, which proactively addresses these potential issues through rigorous metal printing quality control and process optimization, companies can confidently leverage aluminum 3D printing for demanding applications like custom electronics cases.
Selecting Your Partner: How to Choose the Right Metal 3D Printing Service Provider for Electronic Cases
Choosing the right manufacturing partner is paramount to the success of your custom aluminum electronics case project. The quality, precision, cost, and timely delivery of your components heavily depend on the capabilities and expertise of your chosen metal AM supplier B2B. For engineers and procurement managers navigating the additive manufacturing landscape, evaluating 3D printing services criteria carefully is essential. Not all providers are created equal, especially when dealing with the nuances of aluminum printing for demanding applications. Here’s a checklist to help you select a reliable additive manufacturing partner:
- Proven Expertise in Aluminum Printing:
- Requirement: Look for demonstrable experience specifically with AlSi10Mg, AlSi7Mg, or other relevant aluminum alloys. Ask for case studies or examples of similar projects (e.g., enclosures, heat sinks, complex geometries). Aluminum printing expertise не подлежит обсуждению.
- Met3dp Advantage: Met3dp possesses decades of collective expertise in metal additive manufacturing, including extensive experience with aluminum alloys, backed by our advanced powder production and state-of-the-art printing systems.
- Advanced Technology and Equipment:
- Requirement: Ensure the provider uses well-maintained, industrial-grade LPBF or SEBM machines capable of achieving the required accuracy and build volume. Understand their machine capacity and redundancy.
- Met3dp Advantage: We invest in industry-leading printing technology, offering exceptional print volume, accuracy, and reliability suitable for mission-critical components.
- Material Quality Assurance:
- Requirement: How do they source and qualify their metal powders? Is there traceability? High-quality powder is fundamental to high-quality parts. Providers who manufacture their own powder often have better control.
- Met3dp Advantage: Met3dp manufactures its own high-sphericity, high-flowability metal powders using advanced Gas Atomization and PREP technologies, ensuring consistent quality and optimal printing performance. We maintain full traceability from raw material to final powder batch.
- Robust Quality Management System (QMS) & Certifications:
- Requirement: Look for certifications like ISO 9001 (general quality management). For higher assurance relevant to demanding industries, certifications like AS9100 (aerospace) or ISO 13485 (medical), even if not strictly required for your case, indicate mature processes for control, traceability, and risk management. A certified metal printing provider demonstrates a commitment to quality.
- Met3dp Advantage: Met3dp operates under stringent quality control protocols, ensuring process repeatability and part conformity critical for industrial applications.
- Comprehensive In-House Capabilities (End-to-End Solutions):
- Requirement: Can the provider handle the entire workflow, including DfAM consultation, printing, stress relief, support removal, heat treatment, CNC machining for critical features, surface finishing, and quality inspection? Managing multiple vendors adds complexity and potential delays.
- Met3dp Advantage: Met3dp provides comprehensive solutions spanning SEBM/LPBF printers, advanced metal powders, DfAM support, application development, and post-processing coordination, offering a streamlined path from design to finished part.
- Engineering and DfAM Support:
- Requirement: Does the provider offer technical support to help optimize your design for additive manufacturing? Collaborative DfAM support can significantly improve part performance, reduce cost, and minimize print failures.
- Met3dp Advantage: Our team partners with organizations, providing application development services and DfAM expertise to help clients fully leverage the benefits of AM.
- Capacity and Lead Time:
- Requirement: Assess their current capacity and typical lead times for projects similar to yours. Can they accommodate potential scaling or urgent requests? Transparent communication regarding scheduling is crucial.
- Met3dp Advantage: Our efficient operations and significant machine capacity allow us to offer competitive lead times for both prototyping and low-volume production runs.
- Transparency and Communication:
- Requirement: Look for clear and detailed quotes, responsive communication, and proactive project updates. A good partner acts as an extension of your team.
- Met3dp Advantage: We believe in building strong partnerships through clear communication and technical transparency. Explore our website https://met3dp.com/ to learn more about our company and approach.
Table: Criteria for Evaluating Metal AM Service Providers
Evaluation Criterion | Key Questions to Ask | Why It Matters for Aluminum Cases | Related Keywords |
---|---|---|---|
Aluminum Expertise | What’s your experience with AlSi10Mg/AlSi7Mg? Show examples. | Ensures understanding of material nuances & process optimization. | Aluminum printing expertise |
Технологии и оборудование | What machines do you use? Build volume? Maintenance schedule? | Determines accuracy, reliability, part size capability. | Industrial metal 3D printers |
Качество материала | Where do you source powder? How is quality verified? Traceability? | Directly impacts part density, properties, consistency. | High-quality metal powders, Powder traceability |
QMS & Certifications | Are you ISO 9001 certified? AS9100? ISO 13485? | Indicates process maturity, control, and commitment to quality. | Certified metal printing provider ISO AS9100 |
Внутренние возможности | Do you offer heat treatment, machining, finishing? Or manage subcontractors? | Streamlines workflow, simplifies procurement, ensures accountability. | End-to-end AM solutions |
Инженерная поддержка | Do you provide DfAM consultation? Simulation? | Helps optimize design for performance, cost, and printability. | DfAM services, Additive manufacturing consulting |
Capacity & Lead Time | What are your typical lead times? Can you handle our volume/urgency? | Ensures project timelines can be met. | Metal AM lead time, Production capacity |
Communication & Cost | Is your quoting transparent? How do you manage projects? | Ensures clear expectations and smooth collaboration. | Reliable additive manufacturing partner |
Export to Sheets
Choosing the right provider is a strategic decision. By carefully evaluating 3D printing services criteria and prioritizing partners like Met3dp with proven expertise, robust quality systems, and comprehensive Met3dp capabilities, you significantly increase the likelihood of a successful outcome for your custom aluminum electronics case project.
Understanding Cost Factors and Lead Times for Custom Metal AM Cases
While metal 3D printing offers significant advantages for custom aluminum cases, understanding the factors that drive cost and lead time is crucial for effective budgeting, project planning, and calculating the total cost of ownership (AM). Unlike mass production techniques, AM costs and timelines are influenced by a unique set of variables.
Key Cost Factors in Metal 3D Printing:
- Material Consumption:
- Influence: Direct cost of the aluminum powder used for the part и its support structures. Higher quality powders typically cost more but yield better results.
- Calculation: Based on the total volume of the part + supports (derived from the CAD model and build preparation software). Efficient DfAM (e.g., lightweighting) can reduce material usage.
- Время машин:
- Influence: This is often the most significant cost driver. It depends on:
- Build Height (Z-axis): Printing taller parts takes longer, regardless of how many parts are on the build plate.
- Part Volume/Complexity: More material to melt and complex geometries requiring intricate laser scanning paths increase print time.
- Number of Parts per Build: Maximizing the number of parts nested onto a single build plate amortizes the setup and non-printing time per part.
- Calculation: Based on hourly rates for expensive industrial metal AM machines, incorporating depreciation, maintenance, energy, and inert gas consumption.
- Influence: This is often the most significant cost driver. It depends on:
- Труд:
- Influence: Skilled labor is required for various stages:
- Pre-Processing: CAD file preparation, DfAM analysis, build setup, support generation.
- Machine Operation: Monitoring the print process.
- Постобработка: Part removal, extensive support removal, heat treatments, surface finishing, machining, inspection. Support removal and finishing can be particularly labor-intensive.
- Calculation: Based on time required for each step multiplied by skilled labor rates.
- Influence: Skilled labor is required for various stages:
- Требования к постобработке:
- Influence: Each additional step (stress relief, T6 heat treatment, bead blasting, CNC machining, anodizing, etc.) adds cost due to equipment usage, consumables, and labor. High-precision machining or complex finishing operations can significantly increase the aluminum printing price per part.
- Calculation: Based on the specific steps required, complexity, and time involved.
- Part Complexity & Size:
- Influence: More complex parts may require more intricate support structures (longer print time, more material, difficult removal) and potentially more complex post-processing or inspection. Very large parts occupy machine time and may require specialized handling.
- Quality Assurance & Inspection:
- Influence: Higher quality requirements (tighter tolerances, specific mechanical property verification, NDT like CT scanning) necessitate more rigorous inspection procedures, adding time and cost.
- Order Quantity (Volume):
- Influence: While AM avoids tooling costs, there are still setup costs per build (machine preparation, powder loading/unloading). Printing multiple copies of a part in a single build (or across multiple optimized builds) reduces the setup cost allocated to each individual part. Bulk 3D printing quote factors often include tiered pricing based on quantity.
Typical Lead Time Components:
Additive manufacturing lead time calculation involves summing the time required for each stage:
- Quoting & Order Processing (1-5 days): Includes DfAM review, file check, build simulation, quote generation, and order confirmation.
- Queue Time (Variable: Days to Weeks): Time spent waiting for an available machine slot. Depends on the provider’s capacity and workload.
- Printing Time (Hours to Days): Dependent on build height, volume, complexity, and number of parts. A full build plate might take 1-5 days or longer.
- Post-Processing (Days to Weeks): Often the longest component. Includes:
- Cooling & Stress Relief (typically <1 day)
- Part/Support Removal (hours to days, depending on complexity)
- Heat Treatment Cycles (Solutionizing + Aging can take >1 day including ramp/soak/cool times)
- Machining (variable, depends on complexity)
- Finishing/Coating (variable, depends on process)
- Inspection (variable)
- Shipping (1-5 days domestically, longer internationally): Logistics time.
Total lead times for metal AM parts can range from 1-2 недели for simple prototypes with minimal post-processing to 4-8 weeks or more for complex parts requiring extensive post-processing, multiple machining setups, or specific coatings, especially for production quantities.
Table: Cost & Lead Time Factors Summary
Фактор | Primary Influence on Cost | Primary Influence on Lead Time | Mitigation / Optimization Strategy |
---|---|---|---|
Material Volume | High (Direct cost of powder) | Minor (Related to print volume) | DfAM (Lightweighting), Optimize supports |
Machine Time | Very High (Hourly rate, Z-height, complexity) | High (Dominant factor in print stage) | DfAM (Reduce height/complexity), Nest multiple parts |
Труд | High (Setup, Post-processing) | High (Especially for complex post-processing) | DfAM (Simplify supports/finishing), Automation (where possible) |
Постобработка | Variable to Very High (Depends on steps needed) | Variable to Very High (Can be longest component) | DfAM (Minimize requirements), Efficient process selection |
Complexity / Size | От умеренного до высокого | От умеренного до высокого | DfAM (Simplification where possible) |
Quality Needs | Moderate to High (Inspection/testing costs) | Moderate (Inspection time) | Clearly define critical requirements |
Количество заказов | High (Setup amortization reduces cost/part) | Moderate (Build plate optimization, queue time) | Consolidate orders, Discuss bulk pricing |
Export to Sheets
Engaging with your AM provider early in the design process allows for accurate metal 3D printing cost estimation and realistic additive manufacturing lead time calculation. Met3dp works transparently with clients to provide detailed quotes and project timelines based on optimized manufacturing plans.
Frequently Asked Questions (FAQ) about 3D Printed Aluminum Cases
Here are answers to some common questions regarding custom 3D printed aluminum phone and laptop cases:
- How strong and durable are 3D printed aluminum cases compared to traditional options?
- Ответ: Significantly more durable than typical plastic cases. When using alloys like AlSi10Mg or AlSi7Mg and applying appropriate post-print heat treatment (e.g., T6), the mechanical properties (strength, hardness) can be comparable to bulk aluminum alloys used in CNC machining. Compared to machined cases, 3D printing allows for optimized designs (like internal lattices) that can enhance stiffness and impact absorption relative to weight. The 3D printed case durability comparison strongly favors AM aluminum over plastics and positions it competitively with traditionally manufactured metal cases, especially when custom, complex designs are needed.
- Can intricate logos, patterns, or textures be printed directly onto the case?
- Ответ: Yes, one of the key advantages of metal 3D printing is its ability to create complex surface geometries. Embossed or debossed logos, intricate patterns, and unique textures can often be incorporated directly into the CAD model and printed as part of the case. The level of detail achievable depends on the printer’s resolution, layer thickness, and powder size. Very sharp edges might be slightly rounded. For extremely fine or sharp details, post-process engraving or machining might be considered.
- What is the typical minimum order quantity (MOQ) for custom aluminum cases?
- Ответ: Unlike injection molding which requires high MOQs due to tooling costs, metal 3D printing is economically viable for producing single prototypes or very small batches. There is often no strict minimum order quantity metal AM. However, be aware that setup costs (machine preparation, file setup) are amortized over the number of parts in a build. Therefore, the cost per part will be significantly higher for a single unit than for a small batch (e.g., 10 or 50 units) printed together. Discuss your volume needs with the provider for optimized pricing.
- Are other aluminum alloys or different metals available besides AlSi10Mg/AlSi7Mg?
- Ответ: Yes, depending on the service provider’s capabilities. Other printable aluminum alloys exist, potentially offering higher strength or different characteristics. Beyond aluminum, other metals commonly used in AM include Titanium alloys (Ti6Al4V) for extreme lightweight/strength and biocompatibility, Stainless Steels (like 316L or 17-4PH) for corrosion resistance and strength, and various Tool Steels or Superalloys (like Inconel) for specialized high-temperature or high-wear applications, though these would be less common for typical consumer electronics cases unless specific properties are needed. Met3dp offers a broad portfolio including Titanium alloys, CoCrMo, stainless steels, and more, showcasing our wide-ranging material expertise. Finding the best aluminum alloy for electronics depends on balancing cost, printability, strength, weight, and thermal needs.
- How does the cost of a 3D printed aluminum case compare to a mass-produced plastic or standard metal case?
- Ответ: A custom 3D printed aluminum case will almost always be significantly more expensive per unit than a mass-produced plastic case due to higher material costs, expensive machinery, longer processing times, and necessary post-processing. It will also generally be more expensive than a mass-produced, simple die-cast or stamped metal case. The value proposition of AM lies not in competing on cost for high volumes of simple parts, but in enabling:
- Customization & Personalization: Unique designs not possible otherwise.
- Сложные геометрии: Integrated features, advanced thermal management.
- Высокая производительность: Superior strength-to-weight ratio, durability.
- Быстрое прототипирование: Quick turnaround for functional metal prototypes.
- Low-Volume Viability: Economical production of small batches where tooling is prohibitive.
- Понимание custom aluminum case cost factors reveals that AM is a premium manufacturing method suited for applications where its unique benefits justify the higher per-part price.
- Ответ: A custom 3D printed aluminum case will almost always be significantly more expensive per unit than a mass-produced plastic case due to higher material costs, expensive machinery, longer processing times, and necessary post-processing. It will also generally be more expensive than a mass-produced, simple die-cast or stamped metal case. The value proposition of AM lies not in competing on cost for high volumes of simple parts, but in enabling:
Conclusion: Elevate Your Electronics with Met3dp’s Custom Aluminum AM Solutions
In the rapidly evolving world of consumer and industrial electronics, standing out requires innovation in both performance and design. Custom 3D printed aluminum cases, leveraging alloys like AlSi10Mg and AlSi7Mg, offer a compelling pathway to achieve this differentiation. Moving beyond the limitations of traditional manufacturing, metal additive manufacturing unlocks unparalleled design freedom, enabling the creation of premium aluminum cases that are lightweight, exceptionally durable, thermally efficient, and aesthetically unique.
From ruggedized enclosures demanding extreme resilience to sleek laptop shells with integrated thermal management, the applications are diverse and growing. The ability to rapidly prototype, iterate designs quickly, and produce complex geometries economically in low-to-mid volumes makes metal AM an invaluable tool for engineers and product developers. Key advantages like part consolidation, topology optimization for weight reduction, and the creation of intricate internal structures provide tangible performance benefits.
However, realizing the full potential of this technology requires navigating its complexities – from mastering DfAM principles and understanding material nuances to implementing meticulous post-processing and quality control. This journey necessitates collaboration with a knowledgeable and capable partner.
Met3dp stands as a leading custom electronics solutions provider in the additive manufacturing space. Our comprehensive capabilities make us an ideal advanced additive manufacturing partner:
- Integrated Solutions: We offer end-to-end services, from producing our own high-quality metal powders via advanced atomization techniques to operating state-of-the-art Met3dp metal 3D printing services (LPBF/SEBM), managing essential post-processing, and providing expert engineering support.
- Uncompromising Quality: Our commitment to quality is embedded in every step, ensuring consistent, reliable, high-performance components that meet stringent industry standards.
- Collaborative Approach: We partner with our clients, offering DfAM expertise and application development support to transform innovative concepts into tangible, market-leading products.
Whether you are developing the next generation of high-performance laptops, rugged field devices, bespoke luxury accessories, or specialized medical equipment, Met3dp has the technology, materials, and expertise to help you leverage the power of metal additive manufacturing. Embrace the future of custom electronics and elevate your products with the strength, precision, and design freedom of 3D printed aluminum.
Contact Met3dp today to discuss your project requirements and discover how our advanced additive manufacturing solutions can bring your vision to life.
Поделиться
MET3DP Technology Co., LTD - ведущий поставщик решений для аддитивного производства со штаб-квартирой в Циндао, Китай. Наша компания специализируется на производстве оборудования для 3D-печати и высокопроизводительных металлических порошков для промышленного применения.
Сделайте запрос, чтобы получить лучшую цену и индивидуальное решение для вашего бизнеса!
Похожие статьи
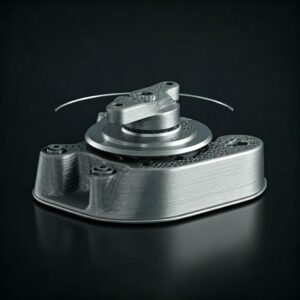
3D-печатные крепления для автомобильных радарных датчиков: Точность и производительность
Читать далее "О компании Met3DP
Последние обновления
Наш продукт
CONTACT US
Есть вопросы? Отправьте нам сообщение прямо сейчас! После получения Вашего сообщения мы всей командой выполним Ваш запрос.
Получите информацию о Metal3DP
Брошюра о продукции
Получить последние продукты и прайс-лист
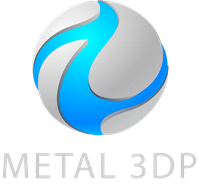
Металлические порошки для 3D-печати и аддитивного производства