Введение в механическое легирование для 3D-печати металлическим порошком
Оглавление
Мир Металлический порошок для 3D-печати continues to evolve at an astonishing pace, pushing the boundaries of what’s possible in terms of design, complexity, and material selection. Metal additive manufacturing, specifically, has opened doors to creating intricate and functional objects directly from digital models. But have you ever wondered how the metal powder used in these printers is even produced? Enter mechanical alloying, a fascinating technology that plays a crucial role in creating high-performance Металлический порошок для 3D-печати.
the basic principles of mechanical alloying
Imagine you have a cocktail shaker filled with different colored candies. Shaking vigorously blends the candies, creating a seemingly uniform mix. This, in essence, is the basic principle behind mechanical alloying. It’s a solid-state powder processing technique that utilizes high-energy ball milling to intimately mix and blend multiple metal powders together at an atomic level.
Here’s a more detailed breakdown of the process:
- Выбор порошка: The first step involves carefully choosing the desired metal powders based on the final material properties and application requirements. This could involve individual elements, pre-alloyed powders, or even combinations of both.
- Milling Process: The selected powders are then loaded into a high-energy ball mill, which essentially acts like a giant shaker. Inside the mill, numerous balls made of a harder material (often steel or ceramic) collide with the powder particles at high speeds. This intense mechanical force fractures, deforms, and welds the powder particles together, promoting intimate mixing and creating a new, homogenized powder material с уникальными свойствами.
- Powder Collection and Processing: After a predetermined milling time, the resulting powder is collected and undergoes further processing steps like sieving and classification to achieve the desired particle size distribution and morphology.
Подумайте об этом так: Imagine trying to mix chocolate chips and flour by hand. You might end up with a somewhat blended mixture, but there will still be distinct pockets of each ingredient. Mechanical alloying, on the other hand, is like putting these ingredients in a powerful blender, achieving a much more uniform and consistent mixture at the individual particle level.
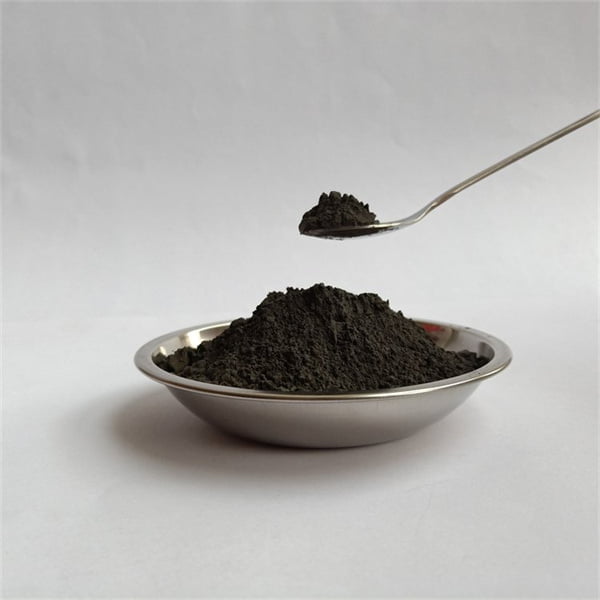
How to apply Mechanical Alloying to the production of 3D printed metal powders
Mechanical alloying offers a versatile approach to producing metal powders specifically tailored for 3D printing applications. Here’s how it plays a key role:
- Creating New Alloys: By mixing different elemental powders, mechanical alloying allows the creation of novel alloys with specific properties not readily available in conventional forms. This opens doors to customizing material properties like strength, corrosion resistance, and thermal behavior for specific 3D printing applications.
- Improving Powder Properties: Mechanical alloying can also enhance the flowability, packing density, and overall printability of existing metal powders. By refining the particle size and morphology, the powder becomes more suitable for various 3D printing processes like laser powder bed fusion (LPBF) and electron beam melting (EBM).
- Enabling Composite Powders: This technique also paves the way for the development of metal matrix composites (MMCs) for 3D printing. By incorporating ceramic or other reinforcing particles into the metal matrix through mechanical alloying, the resulting powder offers improved mechanical properties like wear resistance and high-temperature performance.
In essence, mechanical alloying acts as a powerful tool for unlocking the potential of 3D printing metals by enabling the creation of novel materials with precisely tailored properties to meet the demands of diverse applications.
The advantages of mechanical alloying in Металлические порошки для 3D-печати
Compared to traditional powder production methods like atomization, mechanical alloying offers several distinct advantages for 3D printing:
- Greater compositional control: It allows for the creation of precise and uniform alloys with specific compositions, not limited to readily available pre-alloyed powders.
- Enhanced powder properties: The process refines the powder particles, improving their flowability, packing density, and printability, leading to better performance in 3D printing processes.
- Разработка новых материалов: It opens doors to the creation of unique alloys and metal matrix composites with properties not achievable through conventional methods, expanding the possibilities for 3D printing applications.
- Масштабируемость: Mechanical alloying can be adapted to produce small or large batches of powder, making it suitable for both research and industrial-scale production.
However, it’s important to acknowledge that mechanical alloying also comes with certain limitations:
- Время обработки: The milling process can be time-consuming and energy-intensive, especially for harder or more complex material combinations.
- Contamination potential: Careful selection of milling media and process control are crucial to minimize contamination from the milling balls or environment.
- Соображения, связанные с затратами: Setting up and maintaining high-
Specific Metal Powder Models for 3D Printing using Mechanical Alloying
While the core functionalities remain consistent, specific metal powder models produced via mechanical alloying cater to diverse 3D printing applications and performance demands. Here are 10 noteworthy examples:
1. Inconel 625: This nickel-chromium-based superalloy powder boasts exceptional high-temperature strength, oxidation resistance, and creep resistance. It’s particularly suited for demanding applications like aerospace components, gas turbine parts, and heat exchangers in the 3D printing realm.
2. Ti-6Al-4V: This workhorse titanium alloy powder offers an excellent balance of strength, weight, and biocompatibility. It’s widely used in the medical and aerospace industries for applications like orthopedic implants, aircraft components, and custom prosthetics due to its favorable properties when produced via mechanical alloying.
3. AlSi10Mg: This aluminum-silicon-magnesium alloy powder is known for its good castability, weldability, and corrosion resistance. It finds applications in various sectors, including automotive, aerospace, and consumer goods, due to its combination of printability and mechanical properties achievable through mechanical alloying.
4. Cu-Sn10: This copper-tin alloy powder offers superior electrical conductivity and wear resistance. It’s often utilized in the production of electrical components like heat sinks, bus bars, and connectors, where its properties, enhanced through mechanical alloying, are crucial for performance.
5. CoCrMo: This cobalt-chromium-molybdenum alloy powder is renowned for its high biocompatibility, wear resistance, and corrosion resistance. It’s a popular choice for the 3D printing of medical implants like hip and knee replacements, where the biocompatibility and mechanical properties achieved through mechanical alloying are paramount.
7. Inconel 718: This nickel-chromium-based superalloy powder is known for its exceptional strength at high temperatures, good oxidation resistance, and excellent creep resistance. It’s often used in demanding applications like turbine blades, rocket engine components, and other high-performance parts, where the properties achievable through mechanical alloying are essential.
8. Maraging Steel 300: This high-strength, low-carbon steel powder offers superior strength and toughness after heat treatment. It’s used in various applications requiring high strength-to-weight ratios, like aerospace components, tooling, and defense equipment, where the properties obtained through mechanical alloying are crucial.
9. Nickel Aluminum Bronze (NAB): This copper-aluminum-nickel alloy powder delivers excellent corrosion resistance, wear resistance, and good mechanical properties. It finds applications in marine components, bearings, and wear parts, where its printability and properties, enhanced by mechanical alloying, are advantageous.
10. Hastelloy C-276: This nickel-chromium-molybdenum alloy powder is known for its exceptional corrosion resistance in a wide range of aggressive environments. It’s used in chemical processing equipment, pollution control systems, and other applications requiring superior resistance to harsh chemicals, where the properties achieved through mechanical alloying are vital.
It’s important to remember that these are just a few examples, and the possibilities with mechanically alloyed powders are constantly expanding. As the technology advances, we can expect to see even more innovative and specialized metal powders tailored to meet the specific needs of various 3D printing applications.
Comparison of Metal Powder Models for 3D Printing
When choosing a metal powder model for your 3D printing project, several factors need to be considered:
- Желаемые свойства: Identify the crucial properties your finished part needs, such as strength, weight, corrosion resistance, biocompatibility, or electrical conductivity.
- Требования к заявке: Consider the specific application and the environmental conditions the part will be subjected to.
- 3D printing process: Match the powder characteristics like particle size and flowability to the specific 3D printing process you’ll be using (e.g., LPBF, EBM).
Here’s a brief comparison of some key properties for the mentioned metal powder models:
Модель металлического порошка | Прочность (МПа) | Плотность (г/см³) | Температура плавления (°C) | Приложения |
---|---|---|---|---|
Инконель 625 | Boasts exceptional high-temperature strength, making it ideal for demanding applications like aerospace components and heat exchangers. | Possesses a high density of 8.44 g/cm³, contributing to its robust nature. | Offers a melting point of 1455°C, allowing it to withstand extreme temperatures. | Widely used in aerospace, gas turbines, and heat exchangers due to its combination of strength, high-temperature resistance, and good printability. |
Ti-6Al-4V | Strikes an excellent balance between strength, weight, and biocompatibility, making it suitable for applications like orthopedic implants and prosthetics. | Exhibits a moderate density of 4.43 g/cm³, offering a good balance between weight and strength. | Melts at a temperature of approximately 1600°C, showcasing its ability to withstand high temperatures. | A popular choice in the medical and aerospace industries due to its biocompatibility, favorable strength-to-weight ratio, and good printability. |
AlSi10Mg | Known for its good castability, weldability, and corrosion resistance, making it versatile for various applications. | Possesses a lower density of around 2.7 g/cm³, contributing to its lightweight properties. | Melts at a relatively lower temperature compared to others, around 577°C, offering easier processing in some cases. | Commonly used in the automotive, aerospace, and consumer goods sectors due to its printability, favorable mechanical properties, and good castability. |
Cu-Sn10 | Delivers superior electrical conductivity and wear resistance, making it valuable for applications like electrical components and heat sinks. | Exhibits a moderate density of approximately 8.9 g/cm³, balancing electrical conductivity with weight considerations. | Melts at a temperature of around 830°C, offering good workability and printability. | Frequently utilized in the production of electrical components like heat sinks and bus bars due to its exceptional electrical conductivity and wear resistance. |
CoCrMo | Renowned for its high biocompatibility, wear resistance, and corrosion resistance, making it a top choice for medical implants. | Possesses a high density of around 8.3 g/cm³, contributing to its durability and wear resistance. | Melts at a temperature of approximately 1350°C, showcasing its ability to withstand high temperatures during various processes. | Extensively used in the medical field for applications like hip and knee replacements due to its excellent biocompatibility, good printability, and wear resistance. |
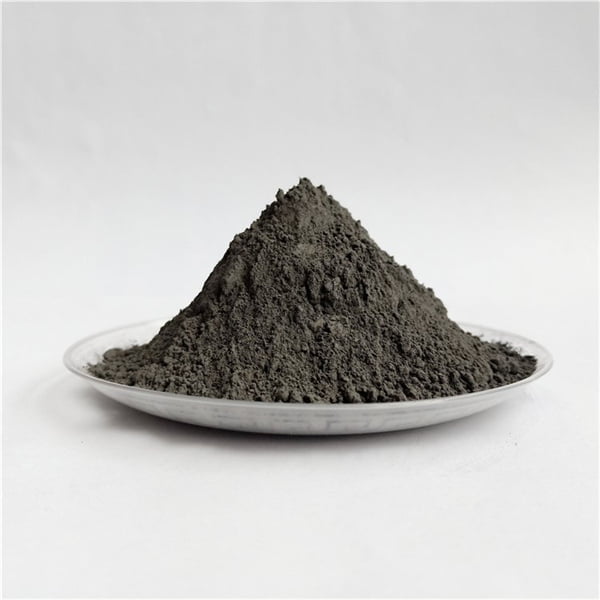
Additional Considerations and Future Outlook of Mechanical Alloying in 3D Printing
While mechanical alloying offers numerous advantages for Металлические порошки для 3D-печати, it’s essential to consider some additional factors:
- Стоимость: Процесс может быть дороже compared to traditional powder production methods like atomization, especially for larger quantities.
- Управление процессом: Strict control over milling parameters and equipment is crucial to ensure consistent powder quality and minimize contamination risks.
- Воздействие на окружающую среду: The energy consumption associated with the milling process necessitates consideration of sustainability and potential environmental impact.
Despite these considerations, the future of mechanical alloying in 3D printing appears bright. Here are some exciting possibilities to look forward to:
- Разработка новых сплавов: The technology will continue to pave the way for the creation of novel alloys with unique properties, pushing the boundaries of what’s achievable in 3D printing.
- Повышение эффективности процесса: Advancements in milling technology and process optimization can lead to increased efficiency and reduced costs, making it more accessible for various applications.
- Nanocomposite powders: The future might see the development of nanocomposite powders with exceptional properties, further expanding the potential of 3D printing for advanced applications.
In conclusion, mechanical alloying stands as a powerful tool for unlocking the potential of 3D printing metals. By enabling the creation of novel materials with tailored properties and fostering advancements in the field, this technology paves the way for the creation of innovative, high-performing, and functional objects across diverse industries. As research and development continue, we can expect to see even more exciting possibilities emerge, shaping the future of 3D printing metals.
ЧАСТО ЗАДАВАЕМЫЕ ВОПРОСЫ
В: Каковы преимущества использования механически легированных порошков в 3D-печати?
A: Several advantages exist, including:
- Greater control over composition: Allows creation of precise and uniform alloys with specific compositions.
- Enhanced powder properties: Improves flowability, packing density, and printability for better performance in 3D printing processes.
- Разработка новых материалов: Enables the creation of unique alloys and metal matrix composites with properties not achievable through conventional methods.
- Масштабируемость: Adaptable to produce small or large batches of powder for both research and industrial-scale production.
Q: What are some limitations of using mechanically alloyed powders?
A: Potential limitations include:
- Время обработки: The milling process can be time-consuming and energy-intensive, especially for complex material combinations.
- Contamination potential: Careful selection of milling media and process control are crucial to minimize contamination.
- Соображения, связанные с затратами: Setting up and maintaining high-energy milling equipment can be expensive.
Q: What are some factors to consider when choosing a metal powder model for 3D printing?
A: Key factors include:
- Желаемые свойства: Identify the crucial properties your finished part needs (strength, weight, corrosion resistance, etc.).
- Требования к заявке: Consider the specific application and environmental conditions the part will face.
- 3D printing process: Match the powder characteristics (particle size, flowability) to the specific 3D printing process you’ll be using.
Q: What is the future outlook for mechanical alloying in 3D printing?
A: The future looks promising, with potential for:
- Разработка новых сплавов: Creation of novel alloys with unique properties, expanding the possibilities of 3D printing.
- Повышение эффективности процесса: Advancements in milling technology and process optimization can lead to increased efficiency and reduced costs.
- Nanocomposite powders: Development of nanocomposite powders with exceptional properties, further expanding the potential of 3D printing for advanced applications.
By understanding the potential and limitations of mechanical alloying, we can leverage this technology to create innovative and functional 3D printed objects, shaping the future of various industries.
Поделиться
MET3DP Technology Co., LTD - ведущий поставщик решений для аддитивного производства со штаб-квартирой в Циндао, Китай. Наша компания специализируется на производстве оборудования для 3D-печати и высокопроизводительных металлических порошков для промышленного применения.
Сделайте запрос, чтобы получить лучшую цену и индивидуальное решение для вашего бизнеса!
Похожие статьи
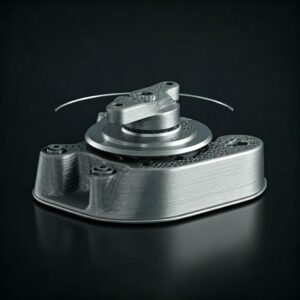
3D-печатные крепления для автомобильных радарных датчиков: Точность и производительность
Читать далее "О компании Met3DP
Последние обновления
Наш продукт
CONTACT US
Есть вопросы? Отправьте нам сообщение прямо сейчас! После получения Вашего сообщения мы всей командой выполним Ваш запрос.
Получите информацию о Metal3DP
Брошюра о продукции
Получить последние продукты и прайс-лист
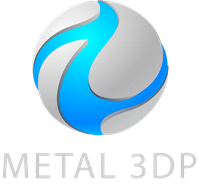
Металлические порошки для 3D-печати и аддитивного производства