3D Printing Fuel Injectors for Aerospace Engines
Оглавление
Introduction: Revolutionizing Aerospace Propulsion with Additive Manufacturing for Fuel Injectors
The relentless pursuit of higher performance, greater efficiency, and reduced environmental impact defines the modern aerospace industry. At the heart of propulsion systems, whether powering commercial airliners across continents, launching satellites into orbit, or enabling advanced military aircraft capabilities, lies a critical component: the fuel injector. This intricate device governs the precise delivery and preparation of fuel for combustion, directly influencing engine thrust, fuel consumption, emissions, and overall reliability. For decades, manufacturing these complex components has pushed the boundaries of traditional techniques like casting, machining, and brazing. However, the intricate internal geometries, demanding material requirements, and tight tolerances inherent to advanced injector designs often present significant manufacturing challenges, leading to long lead times, high costs, and limitations on design innovation.
Enter Metal Additive Manufacturing (AM), more commonly known as 3D-печать по металлу. This suite of technologies is not merely an alternative manufacturing method; it represents a fundamental paradigm shift in how complex, high-value components like aerospace fuel injectors are designed, developed, and produced. By building parts layer by layer directly from digital models using high-performance metal powders, AM unlocks unprecedented design freedom. Engineers are no longer constrained by the limitations of subtractive machining or the mold requirements of casting. They can now create fuel injectors with incredibly complex internal passages, optimized spray patterns for superior atomization and mixing, integrated cooling channels, and consolidated features, often combining multiple previously separate parts into a single, lighter, and more robust unit.
This transformative potential is particularly relevant for aerospace propulsion. 3D printed fuel injectors can lead to tangible improvements in engine performance metrics: better fuel atomization enhances combustion efficiency, reducing specific fuel consumption (SFC); optimized internal cooling passages allow for higher operating temperatures, boosting thermal efficiency and thrust; and integrated designs reduce part count, minimizing potential leak paths and improving overall system reliability. Furthermore, AM significantly accelerates the development cycle. Prototypes can be produced in days or weeks, rather than months, allowing for rapid design iteration and validation. This agility is crucial in an industry where innovation and speed-to-market are key competitive advantages.
This article is intended for aerospace engineers grappling with the challenges of fuel injector design and optimization, procurement specialists seeking reliable and innovative manufacturing solutions, engine manufacturers aiming to push performance boundaries, and Maintenance, Repair, and Overhaul (MRO) providers looking for advanced component sourcing options. We will delve into the critical role of fuel injectors, explore why metal AM is uniquely suited for their production, examine the recommended high-performance materials like Inconel 718 (IN718), Inconel 625 (IN625), and Hastelloy X, and discuss the essential considerations for leveraging this technology successfully. We aim to provide a comprehensive overview for technical and procurement professionals evaluating additive manufacturing suppliers and technologies for demanding aerospace applications, highlighting how partners like Met3dp, with their deep expertise in AM processes and high-quality metal powders, are enabling this revolution in propulsion technology.
The Critical Role of Fuel Injectors in Modern Aerospace Engines
Fuel injectors are far more than simple nozzles; they are highly engineered, precision instruments operating under extreme conditions within the heart of gas turbine and rocket engines. Their primary function is multifaceted: to accurately meter the flow of fuel, atomize it into a fine spray, and distribute this spray uniformly into the combustor, where it mixes intimately with compressed air (or oxidizer in rockets) for efficient and stable combustion. The effectiveness of these processes profoundly impacts nearly every critical performance parameter of an aerospace engine.
Core Functions Explained:
- Fuel Metering: Injectors receive fuel from the engine’s fuel control system and must deliver it at a precise flow rate corresponding to the engine’s operating conditions (e.g., idle, takeoff, cruise, acceleration). Inaccuracies can lead to incorrect fuel-air ratios, resulting in inefficient combustion, flame instability, or excessive emissions.
- Распыление: This is arguably the most crucial function. Liquid fuel does not burn efficiently; it must be broken down into microscopic droplets, vastly increasing the surface area available for rapid vaporization and mixing with air/oxidizer. The quality of atomization (droplet size distribution, spray angle, penetration) is paramount. Finer droplets vaporize faster, leading to more complete combustion, reduced soot formation (visible smoke), and lower emissions of pollutants like unburned hydrocarbons (UHC) and carbon monoxide (CO). Poor atomization results in larger droplets that may not burn completely within the combustor, leading to inefficiency, potential coking (carbon deposits), and increased emissions.
- Mixing and Distribution: The atomized fuel spray must be precisely directed and distributed within the combustor liner to mix thoroughly with the incoming compressed air. The injector’s design, often in conjunction with combustor swirlers, creates specific flow patterns to achieve a stable flame front, uniform temperature distribution (avoiding hot spots that can damage turbine blades), and optimal fuel-air ratios across different zones within the combustor.
Applications Across Aerospace:
The importance of fuel injectors spans the entire spectrum of aerospace propulsion:
- Commercial Jet Engines (Turbofans): Powering the vast majority of commercial aircraft, these engines demand exceptional fuel efficiency to minimize operating costs and environmental impact. Advanced injector designs contribute significantly to achieving low specific fuel consumption (SFC) and meeting stringent emissions regulations (e.g., NOx, CO, UHC, smoke). Reliability and long service life are also paramount for airline economics.
- Military Jet Engines (Turbojets/Turbofans): While efficiency is important, military applications often prioritize high thrust-to-weight ratios, rapid throttle response, and robust performance across a wide flight envelope, including supersonic speeds and high-G maneuvers. Injectors must perform reliably under extreme temperatures, pressures, and vibrations, sometimes incorporating features for afterburner fuel injection.
- Rocket Engines (Liquid Propellant): In spacecraft launch vehicles and upper stages, injectors handle cryogenic fuels (like liquid hydrogen, LH2) and oxidizers (like liquid oxygen, LOX) or hypergolic propellants. They operate at extremely high pressures and flow rates, and injector design is critical for achieving stable combustion, maximizing specific impulse (Isp – a measure of rocket engine efficiency), and preventing catastrophic combustion instabilities. Coaxial swirl injectors and pintle injectors are common types, often featuring incredibly complex internal geometries.
- Auxiliary Power Units (APUs): These smaller gas turbines provide electrical power and bleed air while the aircraft is on the ground or as backup power in flight. While operating conditions are less severe than main engines, efficient and reliable fuel injection is still crucial for starting reliability and power generation efficiency.
- Helicopter Turboshaft Engines: These engines prioritize power density, reliability, and control response. Fuel injectors play a vital role in maintaining stable power delivery to the rotors under varying load conditions.
Key Performance Metrics Influenced by Injector Design:
- Fuel Efficiency (SFC): Better atomization and mixing lead to more complete combustion, extracting more energy from the fuel.
- Emissions (NOx, CO, UHC, Soot/Smoke): Optimized fuel-air mixing and spray patterns minimize the formation of pollutants, helping manufacturers meet strict environmental regulations.
- Thrust and Power Output: Efficient combustion directly translates to higher energy release and thus greater thrust or power.
- Combustion Stability: Precise fuel delivery prevents flameouts or damaging pressure oscillations within the combustor.
- Engine Lifespan and Durability: Uniform temperature distribution resulting from good fuel-air mixing reduces thermal stress on downstream components like turbine blades, preventing premature wear or failure. Injector durability itself is critical, preventing clogging or erosion.
- Starting Reliability and Altitude Relight Capability: Injectors must perform reliably during engine start sequences and be capable of reigniting the engine at high altitudes if necessary.
Industry Demands Driving Injector Innovation:
The aerospace industry continuously pushes for higher performance, placing immense demands on fuel injector technology:
- Higher Operating Temperatures and Pressures: Modern engine designs aim for higher overall pressure ratios (OPR) and turbine entry temperatures (TET) to increase thermal efficiency. Fuel injectors must withstand these increasingly harsh conditions.
- Complex Fuel Paths and Functionality: Designs often incorporate intricate internal passages for fuel swirling, air-assist atomization, internal cooling, and multiple fuel staging circuits (for different operating modes).
- Alternative Fuels: The move towards Sustainable Aviation Fuels (SAFs) requires injectors compatible with different fuel properties (viscosity, density, composition).
- Stringent Reliability and Safety Mandates: As flight-critical components, fuel injectors are subject to rigorous certification requirements and must demonstrate exceptional reliability over thousands of flight hours.
Traditional manufacturing methods struggle to meet these evolving demands, particularly regarding the fabrication of complex internal features and the use of advanced high-temperature materials. This is precisely where metal additive manufacturing offers a compelling solution, enabling the production of next-generation fuel injectors that were previously impossible or prohibitively expensive to manufacture. Aerospace component manufacturing requires suppliers who understand these stringent demands and can deliver parts meeting the highest quality and performance standards.
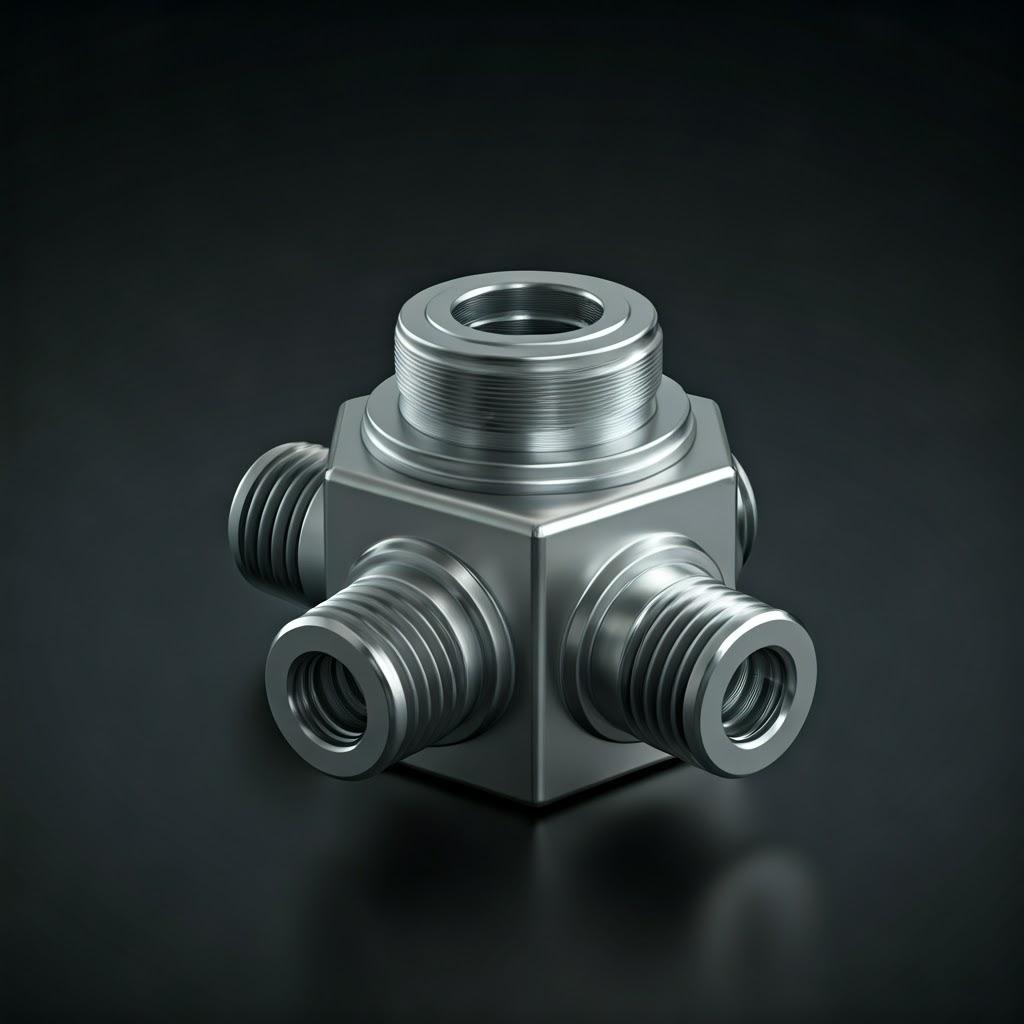
Why Use Metal 3D Printing for Aerospace Fuel Injector Production?
The decision to adopt metal additive manufacturing for producing critical components like aerospace fuel injectors is driven by a confluence of compelling advantages that directly address the limitations of conventional manufacturing techniques. While traditional methods like CNC machining, investment casting, and complex multi-part brazed assemblies have served the industry well for decades, they face increasing challenges when confronted with the demands for higher performance, intricate designs, and faster development cycles characteristic of modern aerospace engineering. Metal AM, particularly laser powder bed fusion (LPBF, also known as SLM) and electron beam melting (EBM), offers a transformative approach.
Comparison: Additive Manufacturing vs. Traditional Methods
Характеристика | Traditional Methods (Machining, Casting, Brazing) | Metal Additive Manufacturing (LPBF/EBM) | Advantage for Fuel Injectors |
---|---|---|---|
Свобода дизайна | Limited by tool access (machining), mold complexity (casting), joint accessibility (brazing). Internal features are very difficult or impossible. | Highly flexible. Complex internal channels, organic shapes, lattice structures feasible. | Enables optimized internal flow paths, swirl generators, cooling channels, improved atomization. |
Консолидация частей | Often requires multiple individual parts joined together (e.g., brazing, welding). | Can print multiple components as a single monolithic part. | Reduces part count, weight, assembly time, and potential leak paths/failure points. |
Снижение веса | Limited optimization potential; often solid parts or basic hollow structures. | Enables topology optimization and internal lattice structures for maximum stiffness-to-weight ratio. | Lower engine weight improves fuel efficiency and payload capacity. |
Материальные отходы | High waste, especially in subtractive machining (up to 80-90% for complex parts). Casting has runners/gates. | Significantly less waste; unused powder is largely recyclable. | More sustainable and cost-effective use of expensive aerospace superalloys. |
Lead Time (New Design) | Long: Requires tooling (casting molds, machining fixtures), extensive process planning, multi-step assembly. Months to years. | Short: Direct manufacturing from CAD data. No part-specific tooling needed. Days to weeks for prototypes. | Accelerates R&D, enables rapid design iteration and faster time-to-market for new engines. |
Complexity Cost | Cost increases significantly with geometric complexity. | Cost is less dependent on complexity, more on volume/build time. | Makes highly complex, performance-enhancing designs economically viable. |
Внутренние особенности | Extremely difficult/costly to create complex internal passages. | Relatively easy to incorporate intricate internal cooling channels, fuel paths, mixing features. | Critical for advanced injector functionality (cooling, atomization, mixing). |
Export to Sheets
Key Advantages of AM for Fuel Injectors:
- Беспрецедентная свобода дизайна: This is the cornerstone advantage. AM liberates designers from traditional manufacturing constraints. For fuel injectors, this means:
- Complex Internal Geometries: Creating optimized swirl chambers, converging-diverging nozzle sections, and precisely shaped orifices for superior atomization and spray patterning.
- Integrated Cooling Channels: Incorporating conformal cooling channels that follow the injector’s contours, allowing for more effective thermal management, enabling higher operating temperatures, and extending component life.
- Functionally Graded Materials (Potential): Future capability to vary material composition within a single part, although challenging for current superalloys.
- Biomimicry: Designing flow paths inspired by natural forms for optimal fluid dynamics.
- Significant Part Consolidation: Traditionally, complex fuel injectors were often assemblies of 10-20 or even more individual pieces meticulously machined and then joined, typically through brazing. Each joint represents a potential leak path, a point of mechanical weakness, and adds considerable manufacturing complexity and inspection requirements. AM allows designers to consolidate these multi-part assemblies into a single, monolithic component. GE Aviation’s famous LEAP engine fuel nozzle, for instance, consolidated 20 parts into one 3D-печать unit. This dramatically simplifies the supply chain, reduces assembly time and cost, improves structural integrity, and eliminates potential failure points associated with joints. Procurement managers benefit from sourcing a single complex part rather than managing multiple suppliers and assembly steps.
- Accelerated Development and Lead Time Reduction: Creating tooling for traditional methods, especially investment casting molds, is time-consuming and expensive. Any design modification requires new tooling, delaying development. With AM, designs go directly from CAD software to the printer. Prototypes can be produced and tested within days or weeks. This rapid iteration capability allows engineers to explore multiple design variations quickly, optimize performance through empirical testing, and significantly shorten the overall development cycle for new engine programs. For MRO or low-volume production scenarios, AM offers on-demand manufacturing without the need for maintaining expensive tooling inventory.
- Снижение веса: While fuel injectors themselves are relatively small, weight savings are critical in aerospace where every gram counts. AM enables techniques like:
- Topology Optimization: Using software algorithms to remove material from non-load-bearing areas while maintaining structural integrity, resulting in organic-looking, highly efficient structures.
- Internal Lattice Structures: Incorporating lightweight but strong internal lattices where solid material is not required.
- Консолидация частей: Eliminating fasteners, flanges, and joint material inherently reduces weight. GE’s LEAP nozzle achieved a 25% weight reduction through AM and design optimization.
- Enhanced Performance and Durability: The design freedom offered by AM directly translates to improved injector performance. Optimized internal flow paths and nozzle geometries lead to better fuel atomization and mixing, boosting combustion efficiency and reducing emissions. Integrated cooling channels allow the injector tip to withstand higher temperatures, improving engine thermal efficiency and component longevity. The monolithic nature of consolidated parts also enhances structural integrity and fatigue life compared to brazed assemblies, particularly under high-pressure, high-vibration conditions. The ability to use advanced superalloys like those offered by Met3dp further enhances durability in extreme engine environments.
- Эффективность материала: Subtractive manufacturing, especially CNC machining of complex parts from billet, generates substantial material waste (chips). While casting is more efficient, it still involves runners, gates, and sprues that become scrap. AM, being an additive process, uses material only where needed. While some support structures are required, the overall material utilization is significantly higher, especially for expensive aerospace superalloys like IN718, IN625, and Hastelloy X. Unused powder can typically be sieved and reused multiple times, further improving material economy and sustainability – a key consideration for wholesale powder procurement and cost management.
While AM presents numerous advantages, it’s crucial to approach it with a Design for Additive Manufacturing (DfAM) mindset. Simply taking a design intended for traditional manufacturing and printing it often fails to leverage AM’s full potential and may even introduce new challenges. Successful adoption requires understanding the specific capabilities and constraints of AM processes, materials, and post-processing requirements, topics we will explore in subsequent sections. Engaging with experienced additive manufacturing partners who provide comprehensive solutions, from powder supply to printing and application development support, is key to realizing these benefits for complex aerospace components.
Recommended Materials for 3D Printed Fuel Injectors: IN718, IN625, Hastelloy X
The selection of materials for aerospace fuel injectors is critically important, dictated by the extreme operating environment within a gas turbine or rocket engine combustor. These components face a brutal combination of extremely high temperatures (often exceeding 1000∘C or 1832∘F), high pressures, corrosive combustion byproducts, oxidizing atmospheres, and significant thermal cycling. Only a select group of materials can withstand these conditions while maintaining structural integrity and performing reliably over thousands of hours or multiple mission cycles. Nickel-based superalloys are the workhorse materials for these demanding applications, and three stand out as particularly well-suited for additive manufacturing of fuel injectors: Inconel 718 (IN718), Inconel 625 (IN625), and Hastelloy X.
These alloys possess an exceptional combination of high-temperature strength, creep resistance, fatigue life, oxidation resistance, and corrosion resistance. Importantly, they have also been extensively characterized and optimized for metal AM processes like Laser Powder Bed Fusion (LPBF/SLM), allowing for the production of dense, high-performance parts. Sourcing high-quality, spherical metal powders with controlled chemistry and particle size distribution is paramount for successful AM, an area where specialized suppliers like Met3dp excel, utilizing advanced production techniques like Vacuum Induction Melting Gas Atomization (VIGA) and Plasma Rotating Electrode Process (PREP) to ensure powder consistency and purity. Procuring certified aerospace grade metal powders from reliable поставщики металлических порошков is a critical first step for any manufacturer or service bureau.
Let’s examine each recommended alloy in detail:
1. Inconel 718 (IN718 / Alloy 718 / UNS N07718)
- Аннотация: IN718 is arguably the most widely used nickel-based superalloy in the aerospace industry, accounting for a significant percentage of the weight of modern jet engines. It’s a precipitation-hardenable alloy, meaning its exceptional strength is derived from the controlled formation of fine secondary phases (γ′ and γ′′) within the metal matrix during heat treatment.
- Основные свойства:
- Высокая прочность: Excellent tensile, yield, creep, and rupture strength at temperatures up to about 700∘C (1300∘F).
- Хорошая коррозионная стойкость: Resists oxidation and corrosion in various environments, although IN625 and Hastelloy X offer superior performance in certain highly corrosive or oxidizing conditions.
- Отличная свариваемость: Compared to other precipitation-hardenable superalloys, IN718 exhibits good weldability, which translates favorably to its processability in fusion-based AM processes like LPBF. It is less susceptible to strain-age cracking during post-weld or post-build heat treatment.
- Good Fatigue Life: Maintains strength under cyclic loading conditions.
- Availability and Cost: Relatively widely available and often more cost-effective than some other superalloys.
- Aerospace Applications: Turbine disks, compressor blades and vanes, shafts, fasteners, engine casings, and critically, fuel system components including injector bodies and internal elements where high strength up to moderate superalloy temperatures is required.
- AM Considerations: IN718 is one of the most mature materials for metal AM. Process parameters for LPBF are well-established, enabling the production of parts with densities exceeding 99.9%. Post-processing typically involves stress relief followed by a full solution and double-aging heat treatment to develop the required microstructure and mechanical properties. Hot Isostatic Pressing (HIP) is often specified for critical aerospace parts to close any residual internal porosity and further enhance fatigue properties.
2. Inconel 625 (IN625 / Alloy 625 / UNS N06625)
- Аннотация: IN625 is a solid-solution strengthened nickel-chromium-molybdenum-niobium alloy. Unlike IN718, it doesn’t rely on precipitation hardening for its strength; instead, the alloying elements distort the nickel-chromium matrix, providing high strength and toughness from cryogenic temperatures up to elevated temperatures (around 800−900∘C or 1470−1650∘F).
- Основные свойства:
- Outstanding Corrosion Resistance: Exhibits exceptional resistance to a wide range of corrosive media, including pitting, crevice corrosion, and intergranular attack. Particularly effective against acids and chloride-ion stress-corrosion cracking. Excellent oxidation resistance at high temperatures.
- Высокая прочность и выносливость: Maintains good strength and excellent toughness over a broad temperature range.
- Excellent Fabricability: Known for its ease of fabrication using traditional methods, which also translates well to AM processability.
- High Fatigue Strength: Resists fatigue failure under demanding cyclic conditions.
- Aerospace Applications: Exhaust systems, thrust reversers, engine ducting, heat exchangers, bellows, honeycomb structures, and fuel system components exposed to corrosive fuels or combustion byproducts, or where excellent oxidation resistance at higher temperatures than IN718 is needed. Often used for injector shrouds or components near the combustion zone.
- AM Considerations: IN625 is also well-established in metal AM. Its solid-solution nature simplifies heat treatment compared to IN718; typically, only stress relief or annealing is required, although HIP may still be used for critical applications. It generally prints well using LPBF, achieving high densities. Its superior corrosion and oxidation resistance make it attractive for long-life fuel injector components.
3. Hastelloy X (Alloy X / UNS N06002)
- Аннотация: Hastelloy X is another solid-solution strengthened nickel-chromium-iron-molybdenum superalloy. It is renowned for its combination of excellent high-temperature strength and outstanding oxidation resistance up to very high temperatures (up to 1200∘C or 2200∘F).
- Основные свойства:
- Исключительная высокотемпературная прочность: Maintains good strength and creep resistance at temperatures significantly higher than IN718 or IN625 can typically handle long-term.
- Выдающаяся стойкость к окислению: Forms a protective, adherent oxide scale that resists spalling during thermal cycling, crucial for components directly exposed to hot combustion gases.
- Very Good Fabricability and Weldability: Can be readily formed and welded, contributing to its good performance in AM.
- Good Resistance to Stress-Corrosion Cracking: Resists cracking in chloride-bearing environments and furnace atmospheres.
- Aerospace Applications: Combustor cans and liners, turbine exhaust components, afterburner components, tailpipes, cabin heaters, and critically, fuel injector nozzles or tips directly exposed to the highest temperatures and most aggressive combustion environment.
- AM Considerations: While perhaps slightly less common in AM than IN718 or IN625, Hastelloy X is increasingly processed via LPBF. Its high-temperature capabilities make it ideal for the “hot end” parts of the fuel injector assembly. Similar to IN625, post-processing typically involves stress relief or annealing, with HIP as an option for enhancing properties for the most demanding applications. Achieving optimal parameters might require more specific expertise compared to the more ubiquitous IN718.
Comparative Table of Key Properties (Typical Values, Vary with Processing & Temp):
Недвижимость | IN718 (Aged) | IN625 (Annealed) | Hastelloy X (Annealed) | Единица | Примечания |
---|---|---|---|---|---|
Max Operating Temp (Strength) | ~700 | ~850 | ~1000+ | ∘C | Approximate continuous use limit based on strength/creep. |
Max Operating Temp (Oxid.) | ~980 | ~1000 | ~1200 | ∘C | Approximate limit based on oxidation resistance. |
Tensile Strength (RT) | 1240−1400 | 830−1000 | 760−900 | MPa | Room Temperature values. |
Yield Strength (RT) | 1030−1200 | 410−600 | 345−500 | MPa | Room Temperature values. |
Плотность | 8.19 | 8.44 | 8.22 | g/cm3 | |
Коррозионная стойкость | Хороший | Отличный | Очень хорошо | – | General rating; specific environments vary. |
Устойчивость к окислению | Хороший | Отличный | Выдающийся | – | Especially important at high temperatures. |
AM Processability | Отличный | Отличный | Good to Excellent | – | Maturity and ease of parameter development. |
Относительная стоимость | Умеренный | Выше | Высокая | – | General indication; market prices fluctuate. |
Export to Sheets
Why Powder Quality Matters (Met3dp’s Advantage):
The performance of the final 3D printed fuel injector is inextricably linked to the quality of the metal powder used. Key powder characteristics influencing part quality include:
- Сферичность: Highly spherical powders ensure good flowability within the AM machine’s recoating system, leading to uniform powder layers and consistent melting. Irregular powders can cause voids and inconsistencies.
- Распределение частиц по размерам (PSD): A controlled PSD is crucial for achieving high packing density in the powder bed, minimizing porosity, and ensuring good surface finish. Too many fine particles can impede flowability and pose safety hazards, while too many large particles can lead to poor resolution and surface roughness.
- Chemical Purity: Contaminants or deviations from the specified alloy chemistry can negatively impact the mechanical properties and corrosion resistance of the final part. Low levels of interstitial elements like oxygen and nitrogen are particularly important.
- Internal Porosity: Powder particles produced via some methods can contain internal gas pores. These can translate into porosity in the final part, degrading mechanical properties, especially fatigue life.
Met3dp’s commitment to utilizing advanced powder manufacturing techniques like Газовая атомизация (employing unique nozzle and gas flow designs) and Плазменный вращающийся электродный процесс (PREP) allows for the production of metal powders (including IN718, IN625, Hastelloy X, and other specialized alloys like TiNi, TiTa, TiAl, TiNbZr, CoCrMo) with:
- Высокая сферичность: Ensuring excellent powder flow and uniform layer deposition.
- Optimized PSD: Tailored distributions for specific AM processes (LPBF, EBM) and applications.
- Высокая чистота: Strict control over raw materials and atomization processes minimizes contamination.
- Низкая внутренняя пористость: PREP, in particular, is known for producing highly dense powders with minimal internal gas porosity.
By leveraging these high-quality powders, manufacturers and service providers using Met3dp materials can achieve greater consistency, higher density, superior mechanical properties, and better overall reliability in their 3D printed aerospace components, including mission-critical fuel injectors. Selecting the right alloy and ensuring the quality of the powder feedstock are fundamental prerequisites for success in additive manufacturing for demanding aerospace applications.
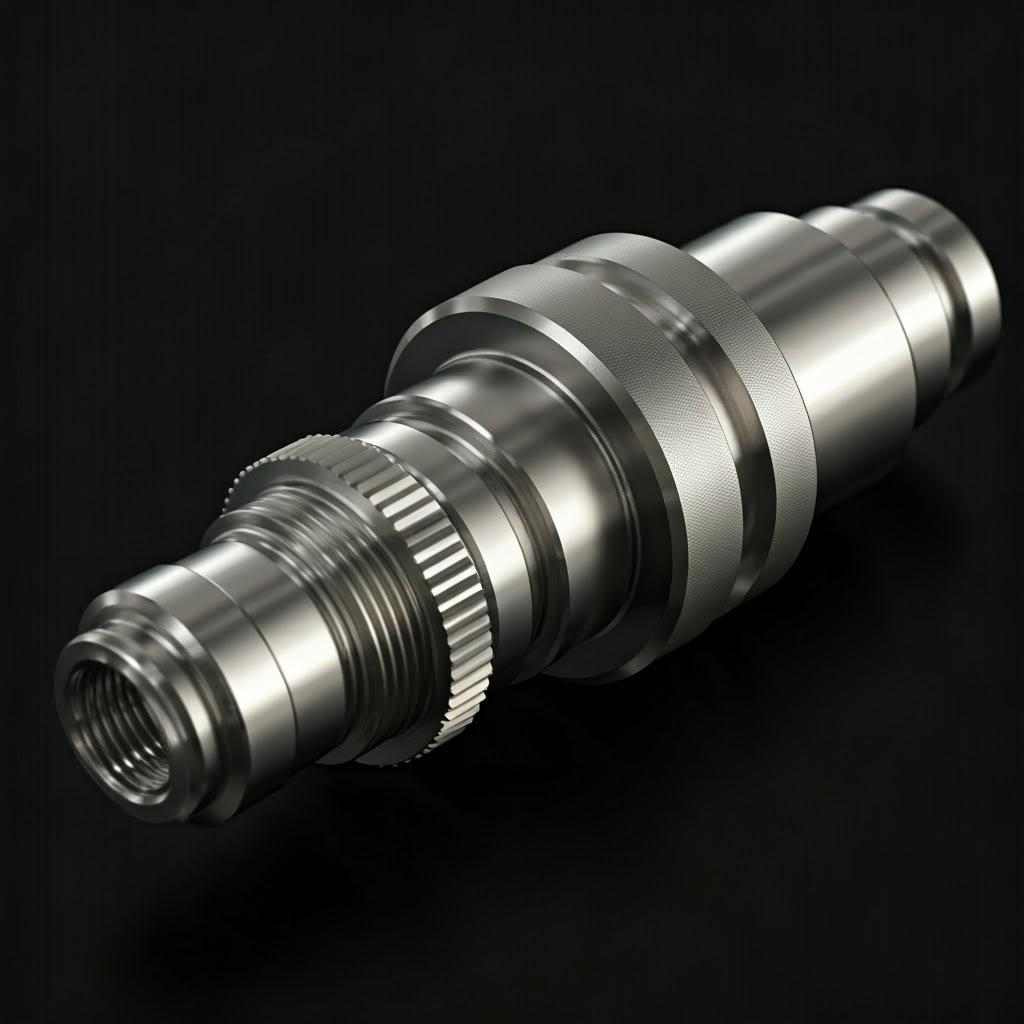
Design for Additive Manufacturing (DfAM) Principles for Fuel Injectors
Simply possessing a 3D model of a fuel injector designed for traditional manufacturing is insufficient to guarantee success with metal additive manufacturing. To truly unlock the benefits of AM – complexity for free, part consolidation, weight reduction, and enhanced performance – engineers must embrace Проектирование для аддитивного производства (DfAM) principles. DfAM is a methodology that involves designing parts specifically tailored to the capabilities and constraints of AM processes, such as Laser Powder Bed Fusion (LPBF/SLM) or Electron Beam Melting (EBM). Applying DfAM from the outset is critical for producing high-quality, functional, and cost-effective 3D printed fuel injectors. It requires a shift in thinking, moving beyond the limitations of machining or casting and leveraging the layer-by-layer build process. Procurement specialists should also be aware of DfAM, as it impacts manufacturability, cost, and the feasibility of achieving desired performance goals when evaluating AM suppliers.
Key DfAM Considerations for Fuel Injectors:
- Optimizing Internal Geometries for Flow and Printability:
- Self-Supporting Angles: One of the most fundamental DfAM rules relates to overhangs. Surfaces built at angles less than approximately 45 degrees relative to the build plate typically require support structures to prevent collapse or distortion during printing. For the complex internal channels within a fuel injector (swirl passages, mixing chambers, fuel conduits), designing these features with self-supporting angles (greater than 45 degrees) wherever possible is paramount. This drastically reduces the need for internal supports, which are often extremely difficult or impossible to remove completely without damaging the part or compromising internal surface finish.
- Smooth Transitions and Filleting: Sharp internal corners can create stress concentrations and impede smooth fluid flow. Incorporating generous fillets and smooth transitions between different channel sections improves structural integrity, reduces pressure drops, and enhances the injector’s hydraulic efficiency. Smooth transitions also tend to print more reliably.
- Minimum Feature Size and Wall Thickness: AM processes have limitations on the minimum size of features (holes, slots) and walls they can accurately produce. This is influenced by laser beam spot size (LPBF), layer thickness, and powder particle size. Designers must ensure that critical orifices, thin walls separating passages, and fine details meet the minimum printable dimensions for the chosen process and material (e.g., typically >0.2-0.4 mm for fine features in LPBF). Minimum wall thickness must also consider pressure containment requirements and thermal conductivity needs.
- Teardrop Shapes for Horizontal Holes: Small horizontal holes or channels often print more accurately if designed with a “teardrop” or “diamond” shape at the top, making the roof self-supporting and avoiding the need for internal supports that would block the passage.
- Support Structure Strategy and Optimization:
- Minimizing Supports: While sometimes unavoidable, support structures add cost (material usage, build time, removal labor) and can negatively impact the surface finish where they attach. DfAM aims to minimize their necessity through clever design orientation and self-supporting geometry.
- Designing for Removability: Where supports are necessary, especially externally or in accessible internal areas, they should be designed for easy removal. This might involve using specific support types (e.g., lattice supports, conical supports) with minimal contact points, ensuring adequate clearance for tools, or designing break-away points. The difficulty of removing supports from deep, tortuous internal passages in fuel injectors is a major challenge, reinforcing the need to design them out whenever feasible.
- Тепловое управление: Supports also play a crucial role in conducting heat away from the part during the build process, particularly for overhangs and isolated features. Insufficient support can lead to overheating, warping, and poor feature definition. Support strategy must balance ease of removal with thermal requirements.
- Sacrificial Features: In some cases, features might be added purely to aid the build process (e.g., providing a stable base, facilitating support removal) and are machined off during post-processing.
- Консолидация частей:
- Identifying Opportunities: Analyze existing multi-part injector assemblies to identify components that can be integrated into a single printed part. This often includes bodies, swirlers, internal vanes, mounting flanges, and nozzle tips.
- Redesigning Interfaces: When consolidating parts, the interfaces disappear. The design needs to be re-evaluated as a single entity, optimizing flow paths and structural load paths that now exist within one monolithic component. This often requires computational fluid dynamics (CFD) and finite element analysis (FEA) simulations.
- Преимущества: Reduced part count, elimination of joints (brazed, welded), lower assembly labor, reduced potential leak paths, improved structural integrity, and often significant weight savings. This simplifies the supply chain for aerospace manufacturers and procurement teams.
- Topology Optimization and Lightweighting:
- Load Path Analysis: Using FEA software to understand how stresses are distributed through the injector body under operating pressures and temperatures.
- Material Removal: Employing topology optimization algorithms to remove material from areas experiencing low stress, while retaining material along critical load paths. This results in organic, load-bearing structures that are significantly lighter than their conventionally designed counterparts.
- Решетчатые структуры: Incorporating internal lattice or cellular structures in areas where solid material is not required for strength or function. These can provide structural support with minimal weight, and potentially enhance thermal management or vibration damping characteristics. Lattice design must consider printability and powder removal.
- Considering the AM Process (Selective Laser Melting/Powder Bed Fusion, Electron Beam Melting):
- LPBF vs. EBM: While both are powder bed fusion processes, they have differences. LPBF generally offers better surface finish and accuracy for fine features, making it common for intricate injectors. EBM operates at higher temperatures in a vacuum, reducing residual stress (less need for supports) and making it suitable for crack-prone alloys, but often results in rougher surfaces. Design choices (e.g., support strategy, minimum feature size) may be influenced by the specific process selected.
- Build Orientation: The orientation of the part on the build plate significantly affects support requirements, surface finish on different facets, build time, and potentially anisotropic material properties. Injectors should be oriented to minimize supports in critical internal channels, prioritize accuracy on key functional features, and manage thermal stresses effectively. Simulation tools can help determine the optimal orientation.
- Проектирование на основе моделирования:
- CFD Analysis: Simulating fuel flow, atomization, and mixing within the designed internal passages to verify performance against requirements before printing. This allows for iterative optimization of channel shapes, swirl angles, and orifice designs.
- Thermal Analysis: Modeling heat distribution and thermal stresses during operation and during the AM build process itself. This informs cooling channel design and helps predict potential warping or distortion during printing, allowing for compensation strategies (e.g., pre-deformation, optimized supports).
- Process Simulation: Specialized AM simulation software can predict residual stresses, potential distortion, and optimal support strategies based on the chosen material, process parameters, and part geometry.
By thoughtfully applying these DfAM principles, engineers can move beyond merely replicating existing designs and instead create next-generation aerospace fuel injectors that fully leverage the unique capabilities of additive manufacturing, resulting in superior performance, reduced weight, and improved reliability. Collaborating with an AM service provider experienced in DfAM for aerospace components is crucial for success.
Achieving Precision: Tolerance, Surface Finish, and Dimensional Accuracy in AM Fuel Injectors
While metal AM offers incredible design freedom, achieving the tight tolerances, specific surface finishes, and high dimensional accuracy demanded by aerospace fuel injectors requires careful process control, appropriate post-processing, and a thorough understanding of the factors influencing precision. Fuel injectors contain critical features – such as orifices controlling flow rate, sealing surfaces preventing leaks, and internal passages governing fluid dynamics – where even minor deviations can impact engine performance and reliability. Aerospace procurement standards mandate verifiable precision and quality.
Typical Tolerances and Influencing Factors:
- General Tolerances: As-built parts produced using high-resolution Laser Powder Bed Fusion (LPBF) systems typically achieve dimensional tolerances in the range of ±0.1 to ±0.2 mm (±0.004 to ±0.008 inches) for smaller features, with potentially larger deviations (e.g., ±0.1% to ±0.2% of feature size) for larger dimensions. Electron Beam Melting (EBM) generally has slightly looser tolerances due to higher processing temperatures and powder characteristics.
- Factors Influencing Accuracy: Achieving these tolerances consistently requires meticulous control over numerous variables:
- Калибровка машины: Precise calibration of the laser/electron beam scanning system, optical components, and Z-axis movement is fundamental. Regular calibration checks are essential. Companies like Met3dp emphasize the accuracy and reliability of their printing equipment, which is foundational for producing mission-critical parts.
- Параметры процесса: Laser/beam power, scan speed, layer thickness, hatch spacing, scan strategy, and gas flow (LPBF) all impact the melt pool size and stability, influencing dimensional accuracy and surface finish. Optimized parameter sets specific to the material (IN718, IN625, Hastelloy X) are crucial.
- Тепловые нагрузки: The rapid heating and cooling inherent in AM create internal stresses that can cause warping and distortion, particularly in complex geometries or large parts. Build plate heating (LPBF), higher chamber temperatures (EBM), optimized scan strategies, and robust support structures help mitigate this.
- Качество порошка: Consistent powder characteristics (sphericity, PSD) contribute to uniform powder bed density and predictable melting behavior, aiding accuracy.
- Part Geometry and Orientation: Complex shapes, large overhangs, and tall, thin features are more prone to deviation. Build orientation impacts thermal history and support needs, affecting final dimensions.
- Постобработка: Stress relief heat treatments can cause minor dimensional changes. Support removal and subsequent machining or finishing steps significantly influence the final tolerances of specific features.
Обработка поверхности (шероховатость):
- As-Built Surfaces: The surface finish of as-built metal AM parts is inherently rougher than machined surfaces. Typical Ra (average roughness) values for LPBF parts are often in the range of 5 to 20μm (200 to 800μin), depending on material, parameters, and surface orientation (upward-facing, downward-facing, vertical walls). EBM parts are typically rougher.
- Up-facing surfaces tend to be smoother.
- Vertical walls show layer lines.
- Down-facing (overhang) surfaces are generally the roughest due to the attachment points of support structures or the nature of forming over loose powder.
- Internal Channels: Achieving a smooth surface finish inside the intricate internal passages of a fuel injector is particularly challenging but critical. Rough internal surfaces can:
- Increase pressure drop, reducing hydraulic efficiency.
- Alter flow patterns and negatively impact atomization quality.
- Create sites for carbon deposition (coking) or fuel residue buildup.
- Impede heat transfer if they are cooling channels. While DfAM aims to minimize internal roughness (e.g., smooth transitions, avoiding sharp corners), specific post-processing techniques (discussed next) are often required to meet stringent internal surface finish requirements.
- Achieving Smoother Finishes: Where smoother surfaces are required (e.g., sealing faces, aerodynamic surfaces, critical flow paths), post-processing techniques like CNC machining, polishing, abrasive flow machining (AFM), or electro-chemical polishing (ECP) are employed. These can achieve Ra values well below 1μm.
Metrology and Inspection:
Verifying that a 3D printed fuel injector meets all dimensional and surface finish specifications is non-negotiable in aerospace. Given the complexity and often inaccessible internal features, advanced metrology techniques are essential:
- Coordinate Measuring Machines (CMM): Used to measure external dimensions, geometric dimensioning and tolerancing (GD&T) features, and accessible internal features with high accuracy.
- Structured Light / Laser Scanning: Provide high-resolution 3D scans of the part’s external geometry, allowing comparison to the original CAD model to identify deviations.
- Industrial Computed Tomography (CT) Scanning: This is often the only way to non-destructively inspect and measure complex internal channels, wall thicknesses, and detect internal defects (like porosity) within a monolithic AM part. It provides a full 3D density map of the component.
- Измерение шероховатости поверхности: Profilometers or optical surface scanners are used to quantify surface finish (Ra, Rz) on critical external and, where accessible, internal surfaces. Borescopes may be used for visual inspection of internal channels.
Achieving the required precision for aerospace fuel injectors using AM is a holistic process. It starts with DfAM, relies on high-precision printing systems (like those developed by Met3dp known for industry-leading accuracy), requires carefully controlled processes and high-quality materials, necessitates appropriate post-processing, and culminates in rigorous metrology and inspection to ensure every part meets stringent aerospace quality standards.
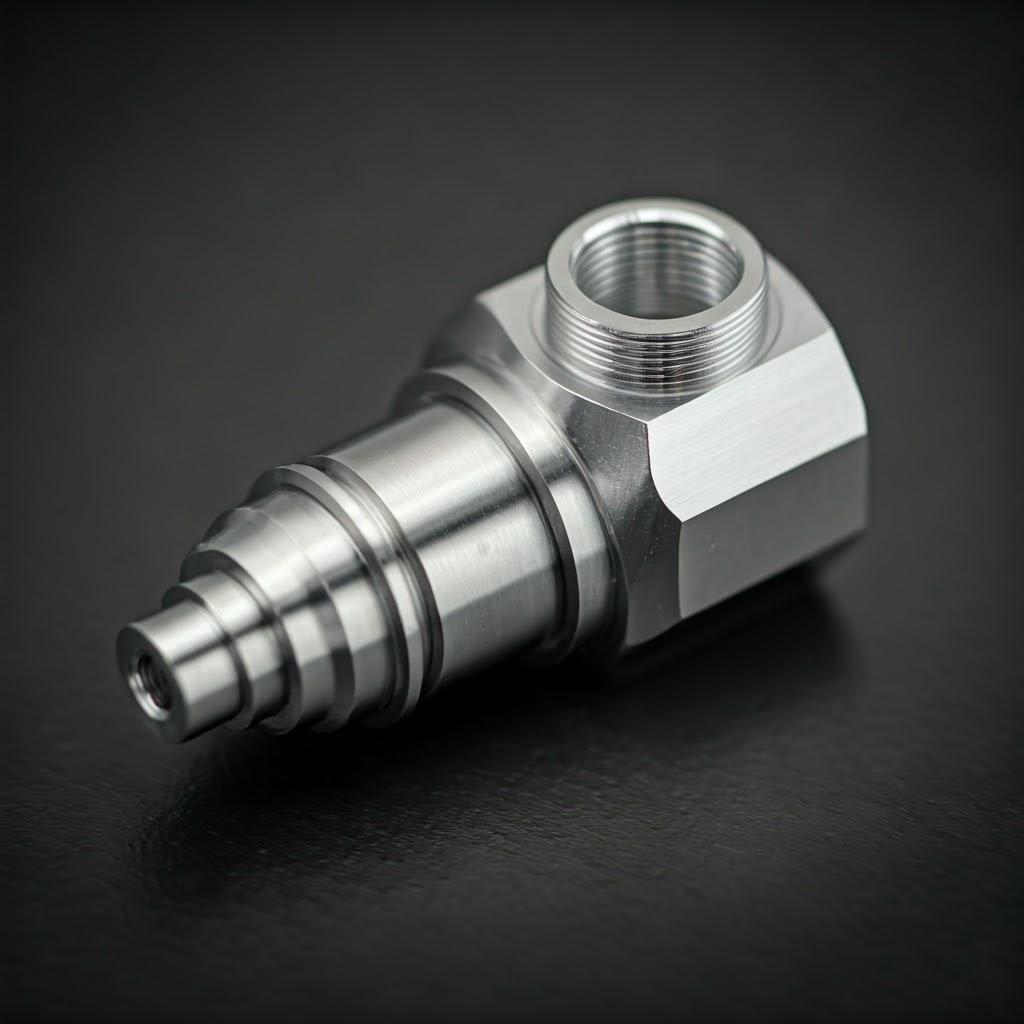
Essential Post-Processing Steps for 3D Printed Aerospace Fuel Injectors
An aerospace fuel injector emerging from a metal 3D printer is rarely ready for engine integration. While the additive process creates the complex geometry, a series of crucial post-processing steps are required to transform the as-built part into a functional, reliable, and flight-worthy component. These steps are essential to relieve internal stresses, achieve the desired material microstructure and mechanical properties, remove support structures, attain critical tolerances and surface finishes, and ensure cleanliness. The specific sequence and intensity of post-processing depend on the chosen AM process (LPBF/EBM), the material (IN718, IN625, Hastelloy X), the complexity of the part, and the stringent requirements of the aerospace application. Understanding these steps is vital for engineers designing the parts and for procurement managers sourcing AM services, as post-processing significantly impacts final part cost and lead time.
Common Post-Processing Workflow:
- Удаление порошка: The first step after the build finishes is removing the component from the build plate and meticulously cleaning off all residual loose powder, especially from internal channels and cavities. This typically involves brushing, vacuuming, and using compressed air jets in a controlled environment to reclaim unused powder safely. Incomplete powder removal can lead to issues in subsequent heat treatment or blockages in the final part.
- Stress Relief Heat Treatment: Due to the rapid heating and cooling cycles during layer-by-layer fusion, significant residual stresses build up within the as-built part. These stresses can cause distortion or cracking during subsequent handling, support removal, or machining, and can negatively impact mechanical performance. A stress relief heat treatment, performed while the part may still be attached to the build plate (depending on geometry and support strategy), is crucial. The specific temperature and time depend on the alloy (e.g., typically 850−1050∘C for nickel superalloys, followed by controlled cooling) but are generally below the full solutioning temperature. This step relaxes internal stresses without significantly altering the microstructure.
- Removal from Build Plate & Support Structure Removal: Once stress-relieved (if done on the plate), the part is separated from the build plate, usually using wire EDM, sawing, or machining. Support structures are then removed. This can be a labor-intensive process, depending on the complexity and accessibility of the supports. Techniques include:
- Удаление вручную: Using hand tools (pliers, cutters, grinders) for easily accessible supports.
- Обработка: Milling or turning away support structures, often used for external supports or large contact areas.
- Wire EDM: Precisely cutting supports close to the part surface. Removing internal supports from fuel injector channels is a major challenge, often requiring specialized techniques or careful DfAM to avoid them entirely.
- Горячее изостатическое прессование (HIP): This is a critical step frequently mandated for aerospace components, especially those subject to fatigue loading or requiring maximum material integrity. HIP involves subjecting the part to high temperature (typically just below the solutioning temperature) and high isostatic pressure (using an inert gas like Argon, often 100 MPa or more) simultaneously in a specialized furnace.
- Преимущества: HIP effectively closes residual internal porosity (microporosity from printing or gas porosity) that could act as crack initiation sites, leading to near 100% density. It also helps to homogenize the microstructure and can improve ductility, fatigue life, and creep resistance.
- Соображения: HIP is an additional cost and time step. Parts must be designed to withstand the process without distortion (e.g., sealed internal cavities require venting or careful design).
- Solution Annealing and Aging Heat Treatment (Especially for IN718): For precipitation-hardenable alloys like IN718, a full heat treatment cycle after HIP (or after stress relief if HIP is not used) is required to develop the desired microstructure and optimal mechanical properties. This typically involves:
- Отжиг раствора: Heating to a high temperature (e.g., ~950−1050∘C for IN718) to dissolve secondary phases and homogenize the alloy.
- Aging (Precipitation Hardening): A subsequent lower-temperature, multi-step heat treatment (e.g., 720∘C followed by 620∘C for IN718) causes the controlled precipitation of strengthening phases (γ′ and γ′′). Solid-solution strengthened alloys like IN625 and Hastelloy X typically only require annealing or stress relief, simplifying the heat treatment process. Accurate furnace control and atmosphere (vacuum or inert gas) are critical for all heat treatments to prevent oxidation and achieve the target properties.
- Отделка поверхности: As-built AM surfaces are often too rough for critical fuel injector applications. Various techniques are used to achieve the required surface finish (Ra):
- Tumbling/Vibratory Finishing: Using abrasive media in a rotating or vibrating bowl to smooth external surfaces and break sharp edges. Effective for general smoothing but less controlled.
- Abrasive Flow Machining (AFM): Pumping a putty-like abrasive media back and forth through the part, including internal channels. Effective for smoothing complex internal passages and inaccessible areas, crucial for fuel injectors.
- Electro-Chemical Polishing (ECP) / Chemical Milling: Using electrochemical processes or chemical etchants to remove material and smooth surfaces. Can provide very smooth finishes, including internally, but requires careful control.
- Micro-Machining/Polishing: Manual or automated polishing for specific critical surfaces requiring very low Ra values.
- Final Machining (CNC): While AM creates the near-net shape, critical interfaces, sealing surfaces, mounting points, threads, and features requiring tolerances tighter than AM can achieve as-built often require final CNC machining (milling, turning, grinding). This ensures precise mating with other engine components and guarantees dimensional accuracy for functional features like orifice diameters.
- Cleaning and Final Inspection: After all processing steps, the fuel injectors undergo rigorous cleaning procedures to remove any machining fluids, polishing compounds, or residual contaminants. Final inspection, including CMM, visual inspection, potentially CT scanning (if required post-machining), and flow testing, verifies that the part meets all specifications before being certified for use.
The extensive nature of post-processing highlights that additive manufacturing is often just the first step in producing a flight-ready aerospace component. Partnering with a supplier, or developing internal capabilities, that includes expertise and facilities for these critical downstream processes is essential for successfully implementing AM for fuel injectors. Met3dp offers comprehensive solutions that span the AM lifecycle, understanding the importance of these integrated steps.
Common Challenges in 3D Printing Fuel Injectors and Mitigation Strategies
While metal additive manufacturing offers transformative potential for aerospace fuel injectors, it is not without its challenges. Successfully printing these complex components from demanding superalloys requires overcoming several potential hurdles related to the physics of the process, material behavior, and geometric complexity. Awareness of these challenges and implementing proactive mitigation strategies, often rooted in DfAM, process control, and material quality, is key to achieving consistent, high-quality results.
1. Warping and Distortion:
- Вызов: The extreme temperature gradients during LPBF/EBM (rapid localized melting followed by rapid solidification) generate significant residual stresses within the part and between the part and the build plate. These stresses can accumulate layer by layer, leading to warping, curling at edges, or overall distortion, compromising dimensional accuracy. Complex geometries and large, flat sections are particularly susceptible.
- Mitigation Strategies:
- Optimized Build Orientation: Orienting the part to minimize large cross-sectional areas parallel to the build plate and reduce unsupported overhangs.
- Robust Support Structures: Designing effective support structures that anchor the part firmly to the build plate, resist contractile forces, and help conduct heat away efficiently.
- Thermal Engineering: Utilizing build plate heating (common in LPBF), higher ambient chamber temperatures (inherent in EBM), or optimized scan strategies (e.g., island scanning, varying parameters) to reduce thermal gradients.
- Process Simulation: Using software to predict stress accumulation and distortion, allowing for geometry compensation (pre-deformation) or optimized support placement before printing.
- Stress Relief Cycles: Incorporating intermediate stress relief cycles during very long builds (less common but possible).
2. Residual Stress Management:
- Вызов: Even if macroscopic warping is controlled, significant residual stresses remain locked within the as-built component. These stresses can reduce fatigue life, cause delayed cracking (especially during post-processing), and lead to unpredictable distortion when the part is removed from the build plate or during machining.
- Mitigation Strategies:
- Mandatory Stress Relief: Performing a proper stress relief heat treatment immediately after the build (often before support removal) is the primary mitigation method.
- Оптимизация процессов: Fine-tuning scan strategies and parameters to minimize thermal gradients during the build.
- EBM Process: EBM operates at higher temperatures, which inherently results in lower residual stress compared to LPBF, making it advantageous for highly complex or crack-sensitive parts, albeit often with a trade-off in surface finish.
- Конструкторские соображения: Avoiding abrupt changes in cross-section and incorporating generous radii can help distribute stress more evenly.
3. Porosity:
- Вызов: The presence of internal voids or pores within the printed material can significantly degrade mechanical properties, particularly fatigue strength, fracture toughness, and ductility. Porosity can arise from several sources:
- Lack-of-Fusion Porosity: Insufficient energy input (laser/beam power too low, scan speed too high) leads to incomplete melting and fusion between adjacent scan tracks or layers, leaving irregular voids.
- Keyhole Porosity: Excessive energy input can create an unstable, deep melt pool (keyholing) that traps process gas, resulting in small, spherical gas pores upon solidification.
- Powder-Related Porosity: Gas pores trapped within the original powder particles (especially in gas-atomized powders if not properly controlled) can transfer to the final part. Contaminated powder can also outgas during melting.
- Mitigation Strategies:
- Optimized Process Parameters: Rigorous development and control of process parameters (power, speed, layer thickness, hatch strategy) specific to the material (IN718, IN625, Hastelloy X) and machine are crucial to ensure stable melting and full fusion. This often involves extensive empirical testing and characterization.
- High-Quality Powder: Using powders with high sphericity, controlled PSD, low internal gas porosity, and high purity is essential. Advanced powder production methods like those used by Met3dp (PREP, optimized Gas Atomization) minimize powder-related defects. Rigorous powder handling and recycling protocols are also necessary to prevent contamination.
- Горячее изостатическое прессование (HIP): As mentioned earlier, HIP is highly effective at closing most types of porosity (especially lack-of-fusion and powder-related gas pores), densifying the material to near 100%. It is often a mandatory step for critical aerospace components.
- Process Monitoring: Advanced AM systems incorporate in-situ monitoring (e.g., melt pool monitoring) to detect anomalies during the build that could lead to porosity.
4. Support Removal Difficulties (Internal Channels):
- Вызов: While DfAM aims to minimize internal supports in fuel injectors, some complex designs may still require them within deep, narrow, or tortuous passages. Removing these supports mechanically or manually without damaging the internal surfaces or leaving remnants that could obstruct flow is extremely difficult, often impossible.
- Mitigation Strategies:
- Prioritize DfAM: The most effective strategy is to design internal channels to be self-supporting (e.g., angles >45 degrees, teardrop shapes for horizontal ceilings). This often requires close collaboration between design engineers and AM specialists.
- Advanced Support Design: If unavoidable, using specialized support types (e.g., easily crushable lattices, minimal contact points) may help, but effectiveness is limited in highly constrained spaces.
- Chemical Etching/Milling: In some cases, specific chemical processes might be developed to selectively dissolve support material without significantly attacking the base alloy, but this is complex and material-specific.
- Abrasive Flow Machining (AFM): While primarily a finishing process, AFM can sometimes help erode or dislodge small internal support remnants, but it’s not a primary removal method for substantial structures.
- Redesign: Often, the most practical solution is to redesign the injector to eliminate the need for non-removable internal supports, even if it requires deviating slightly from the “ideal” performance design.
5. Ensuring Consistent Material Properties:
- Вызов: Achieving consistent, predictable mechanical properties (strength, ductility, fatigue life) that meet aerospace specifications throughout the part and from build to build requires tight control over the entire AM ecosystem. Variations in powder batches, machine calibration drift, minor parameter fluctuations, or inconsistencies in post-processing can lead to variability in microstructure and properties.
- Mitigation Strategies:
- Strict Process Control: Implementing robust quality management systems (e.g., AS9100) covering machine calibration, parameter control, environmental conditions (oxygen levels, humidity), and operator training.
- Powder Management: Rigorous testing and qualification of incoming powder batches, controlled storage, careful sieving and recycling protocols to maintain powder quality and traceability. Partnering with reputable powder suppliers with strong quality control, like Met3dp, is crucial.
- Standardized Post-Processing: Ensuring that heat treatment cycles (temperature, time, atmosphere), HIP parameters, and machining processes are precisely controlled and consistently applied.
- Testing and Qualification: Implementing a regime of material testing (e.g., tensile tests, microstructure analysis on witness coupons built alongside parts) for each build or batch to verify that properties meet requirements. Part-specific qualification processes are standard for aerospace components.
Addressing these challenges requires a combination of design expertise (DfAM), materials science knowledge, meticulous process control, advanced equipment, and rigorous quality assurance. It underscores the importance of selecting an additive manufacturing partner with proven experience and capabilities in handling high-complexity, high-consequence parts for the aerospace industry.
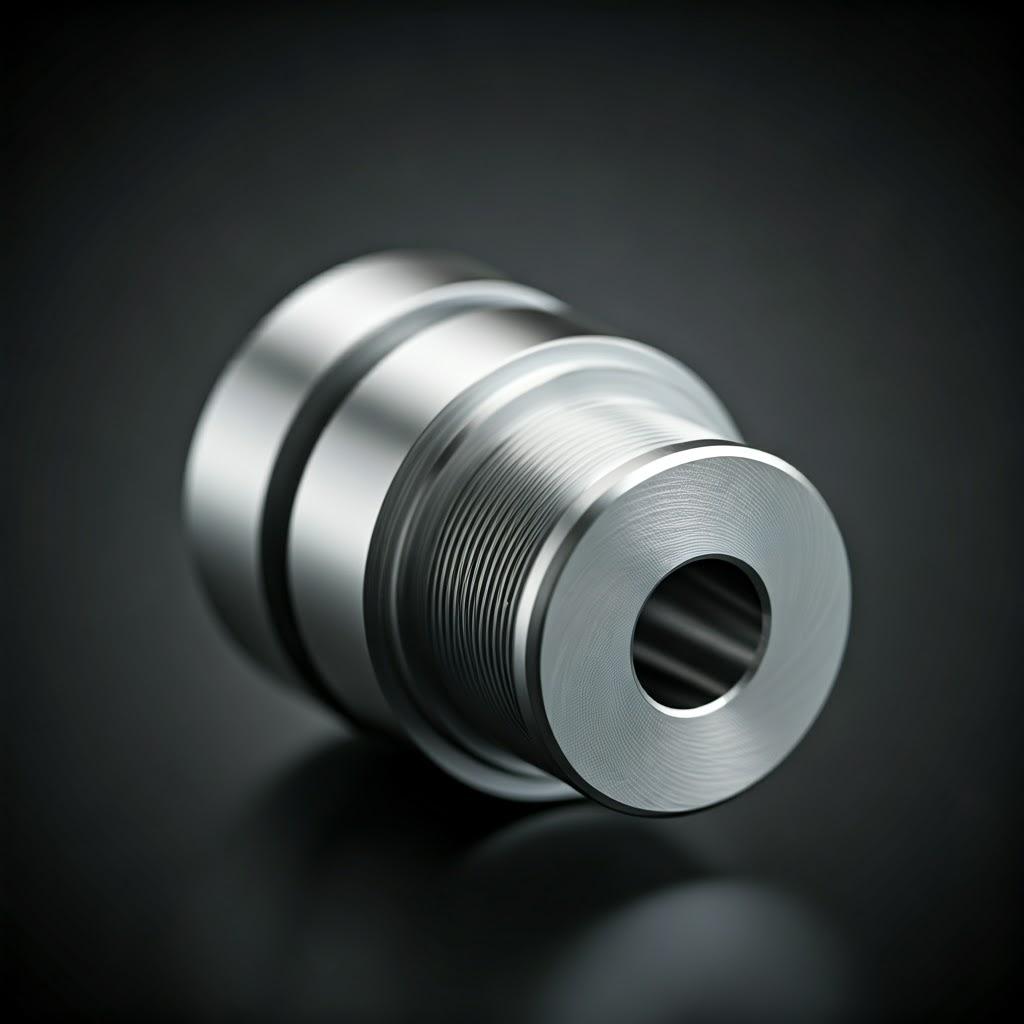
Selecting the Right Metal Additive Manufacturing Partner for Aerospace Components
Choosing the right additive manufacturing partner is arguably as critical as the technology itself, especially when dealing with flight-critical components like aerospace fuel injectors. The complexity of the parts, the demanding nature of the materials (IN718, IN625, Hastelloy X), the stringent quality requirements of the aerospace industry (e.g., AS9100), and the need for deep technical collaboration necessitate a rigorous supplier evaluation process. Procurement managers and engineering teams must look beyond mere printing capabilities and assess potential partners holistically. Selecting an inappropriate supplier can lead to project delays, cost overruns, subpar part quality, and even safety risks. This decision involves evaluating a potential partner’s technical prowess, quality systems, material expertise, production capacity, and collaborative approach.
Key Criteria for Evaluating Metal AM Suppliers:
- Technical Expertise and Experience:
- Process Knowledge: Deep understanding of the nuances of the chosen AM process (LPBF/EBM), including parameter development, optimization for specific alloys, and limitations.
- Materials Science: Expertise in metallurgy, particularly concerning nickel-based superalloys – understanding their behavior during printing, heat treatment response, and final mechanical properties.
- DfAM Capability: Proven ability to work collaboratively on Design for Additive Manufacturing, helping optimize injector designs for printability, performance, and cost-effectiveness. Do they offer design consultation services?
- Post-Processing Know-How: In-house or tightly managed external capabilities for all necessary post-processing steps (stress relief, HIP, heat treatment specific to superalloys, support removal, surface finishing like AFM/ECP, precision machining). Understanding how these steps impact final properties and tolerances is crucial.
- Aerospace Focus: Demonstrated experience specifically with aerospace components, ideally including propulsion systems, fuel systems, or parts with similar complexity and material requirements. Ask for case studies or references relevant to aerospace fuel injector manufacturing solutions.
- Machine Capabilities and Technology:
- Appropriate Technology: Access to industrial-grade LPBF or EBM machines suitable for processing reactive superalloys consistently and reliably.
- Объем сборки: Sufficient build envelope size to accommodate the required injector dimensions or batch production layouts. Met3dp, for example, highlights its industry-leading print volume, accuracy, and reliability, which are key factors for both prototype and production runs.
- Accuracy and Resolution: Machines capable of achieving the required dimensional accuracy and feature resolution for intricate injector details.
- Process Monitoring: Availability of in-situ monitoring capabilities (melt pool monitoring, thermal imaging) can provide valuable data for quality assurance and process consistency.
- Maintenance and Calibration: Robust procedures for machine maintenance and regular calibration to ensure consistent performance over time.
- Material Quality, Handling, and Traceability:
- Powder Sourcing and Quality Control: Use of high-quality, aerospace-grade metal powders (like IN718, IN625, Hastelloy X) from reputable sources or produced in-house with stringent quality control. Ask about their powder specification, testing procedures (chemistry, PSD, flowability, morphology), and how they ensure batch-to-batch consistency. Met3dp’s focus on advanced powder production (Gas Atomization, PREP) directly addresses this need for superior powder quality.
- Обработка порошка: Strict protocols for powder storage (controlled environment), handling, sieving, blending, and recycling to prevent contamination (especially cross-contamination between alloys) and degradation.
- Traceability: Ability to provide full material traceability from the initial powder batch through printing and post-processing to the final certified part, often a requirement for aerospace components.
- Quality Management System (QMS) and Certifications:
- AS9100 Certification: This is the standard QMS requirement for organizations designing, developing, or providing aviation, space, and defense products and services. Certification to AS9100 (or equivalent, like ISO 9001 with aerospace sector specifics) demonstrates a commitment to quality, process control, risk management, and continuous improvement relevant to the industry’s demands.
- Process Control Documentation: Well-documented procedures for all stages of the manufacturing process, from order review and build preparation to post-processing and final inspection.
- Inspection Capabilities: In-house or certified third-party access to necessary metrology equipment (CMM, scanners, CT scanning) and non-destructive testing (NDT) methods appropriate for validating AM parts.
- Configuration Management: Procedures to manage design revisions and ensure the correct version is manufactured.
- Capacity, Lead Times, and Scalability:
- Prototyping vs. Production: Does the supplier have the capacity and workflow management to handle both rapid prototyping needs and potential series production volumes?
- Quoted Lead Times: Realistic and reliable lead time estimates that account for build preparation, printing, queuing, full post-processing, and inspection. Verify their track record for on-time delivery.
- Масштабируемость: Can the supplier scale production up or down to meet fluctuating demand? Do they have multiple machines or established partnerships to handle overflow?
- Partnership Approach and Communication:
- Collaboration: Willingness to work closely with your engineering team on DfAM, material selection, process optimization, and qualification efforts.
- Прозрачность: Open communication regarding process capabilities, potential challenges, and project status.
- Support: Providing technical support and consultation throughout the project lifecycle. Companies offering comprehensive solutions, like Met3dp, which spans printers, powders, and application development, often excel in this partnership approach.
- Intellectual Property (IP) Protection: Clear policies and procedures for safeguarding sensitive design information.
Supplier Evaluation Checklist (Simplified):
Criterion | Основные вопросы | Importance (High/Med/Low) | Примечания |
---|---|---|---|
Техническая экспертиза | Aerospace experience? DfAM support? Superalloy knowledge? Post-processing mastery? | Высокая | Critical for complex injector parts. |
Machine Capability | Suitable AM process? Build volume? Accuracy? Process monitoring? Calibration procedures? | Высокая | Foundation for part quality. |
Качество материала | Powder sourcing/QC? Handling protocols? Traceability system? | Высокая | Directly impacts final part properties. |
Quality System (QMS) | AS9100 certified? Documented processes? Inspection capabilities (incl. CT)? Configuration management? | Высокая | Non-negotiable for aerospace. |
Capacity & Lead Time | Prototyping/Production? Realistic lead times? Scalability? On-time delivery record? | Med-High | Impacts project schedule & cost. |
Partnership & Communication | Collaborative approach? Transparency? Technical support? IP protection? | Med | Important for complex projects. |
Стоимость и ценность | Competitive pricing? Clear cost breakdown? Value beyond price (expertise, quality, reliability)? | Med | Consider Total Cost of Ownership (TCO). |
Export to Sheets
Selecting the right AM partner is a strategic decision. It requires thorough due diligence, site visits or audits (if feasible), technical discussions, and careful evaluation against these criteria. A strong partner becomes an extension of your team, enabling you to successfully leverage additive manufacturing for producing next-generation aerospace fuel injectors.
Understanding Cost Drivers and Lead Times for AM Fuel Injectors
While additive manufacturing enables complex designs and faster development, understanding the factors that influence the cost and lead time of 3D printed fuel injectors is crucial for project budgeting, scheduling, and making informed comparisons with traditional manufacturing methods. Both engineers designing the parts and procurement managers sourcing AM services need insight into these drivers. The cost is not solely determined by the weight of the part; it’s a complex interplay of material, machine time, labor, and downstream processing.
Key Cost Drivers:
- Material Type and Consumption:
- Alloy Cost: Nickel-based superalloys like IN718, IN625, and Hastelloy X are inherently expensive raw materials compared to standard steels or aluminum alloys. Hastelloy X is typically more costly than IN625, which is often more costly than IN718. The market price of nickel and other alloying elements (Cr, Mo, Nb, Co) significantly impacts powder cost. Wholesale powder procurement strategies can offer some cost advantages for larger volumes.
- Part Volume & Support Volume: The total amount of powder melted to create the part and its necessary support structures directly contributes to the cost. Larger, denser parts consume more material. Efficient DfAM that minimizes support structures helps reduce material consumption.
- Powder Reuse/Recycling: While unused powder can be recycled, there are costs associated with sieving, testing, and potentially refreshing the powder over multiple cycles. The number of times powder can be effectively reused impacts overall material cost efficiency.
- Machine Utilization (Build Time):
- Part Complexity & Height: Build time is primarily driven by the number of layers required (part height in the build orientation) and the area that needs to be scanned per layer. Complex internal features or intricate lattices can increase scan time per layer.
- Build Layout Efficiency: Printing multiple parts simultaneously in a single build (nesting) maximizes machine utilization and reduces cost per part, especially for smaller components. The efficiency of packing the build volume is key.
- Machine Hourly Rate: AM machines represent significant capital investment, and operational costs (energy, inert gas, maintenance) contribute to an hourly rate charged for machine time. High-performance machines capable of processing superalloys reliably command higher rates.
- Labor and Engineering:
- Build Preparation: Setting up the build file, optimizing orientation, generating support structures, and preparing the machine requires skilled technician or engineer time.
- Post-Processing Labor: Significant labor is often involved in powder removal, part removal from the plate, manual support removal, surface finishing, and inspection. The more complex the part and supports, the higher the labor cost.
- Engineering Support: DfAM consultation, process simulation, and qualification activities also contribute to the overall project cost.
- Post-Processing Intensity:
- Heat Treatments (Stress Relief, HIP, Aging): These require specialized furnaces and add significant time and cost, particularly HIP, which uses expensive equipment and long cycles. The specific cycles required depend on the alloy and aerospace specifications.
- Удаление опоры: As mentioned, difficult support removal drives up labor costs.
- Отделка поверхности: Techniques like AFM or ECP add cost based on the complexity and required finish level.
- CNC Machining: Final machining of critical features adds cost based on the number of features, required tolerances, and machining time.
- Quality Assurance and Inspection:
- Metrology: Time and resources for CMM measurements, 3D scanning, or CT scanning (which can be particularly costly but often necessary for internal validation).
- NDT: Non-destructive testing (e.g., fluorescent penetrant inspection – FPI) adds cost.
- Documentation: Creating comprehensive quality documentation and certification packages requires time and resources.
- Объем заказа:
- Прототипы: One-off prototypes typically have a higher cost per part due to setup costs being amortized over a single unit.
- Series Production: Costs per part generally decrease with larger batch sizes due to efficiencies in build layout, setup, and potentially negotiated material pricing (bulk powder procurement).
Estimating Lead Times:
Lead time is the total time from order placement to part delivery. It encompasses several stages:
- Order Review & Planning: (1-3 days) Confirming requirements, finalizing design for AM, planning build layout.
- Build Preparation & Queuing: (1-5 days) Preparing the build file, machine setup, waiting for machine availability.
- Время печати: (1-10+ days) Highly variable based on part height, volume, complexity, and number of parts per build. Complex injectors can take several days to print.
- Cooling & Powder Removal: (0.5-1 day) Allowing the build chamber to cool, carefully removing parts and powder.
- Постобработка: (3-15+ days) This is often the longest phase, encompassing stress relief, build plate removal, support removal, HIP (can take several days including logistics if outsourced), heat treatment cycles, machining, and surface finishing. Each step adds time.
- Inspection & Shipping: (1-3 days) Final QA checks, documentation, packaging, and shipping.
Total typical lead times for a complex AM fuel injector prototype can range from 2 to 6 weeks, depending heavily on complexity, post-processing requirements, and supplier backlog. This is still significantly faster than the months or even years often required for traditional manufacturing involving complex tooling.
Total Cost of Ownership (TCO) Perspective:
When comparing AM to traditional methods, it’s essential to consider the TCO. While the per-part cost of an AM fuel injector might sometimes be higher than a mass-produced cast/machined equivalent (especially at very high volumes), AM offers potential savings in other areas:
- Reduced Development Time/Cost: Faster prototyping accelerates innovation.
- Lower Tooling Costs: No expensive molds or fixtures needed.
- Reduced Assembly Costs: Part consolidation eliminates assembly steps.
- Улучшенная производительность: Enhanced fuel efficiency or longer component life provides downstream value.
- Снижение веса: Lower fuel burn over the aircraft’s lifetime.
- Supply Chain Simplification: Sourcing one complex part instead of managing multiple components and assembly processes.
Understanding these cost and lead time dynamics allows organizations to make strategic decisions about adopting AM for fuel injectors and effectively budget for these advanced manufacturing projects.
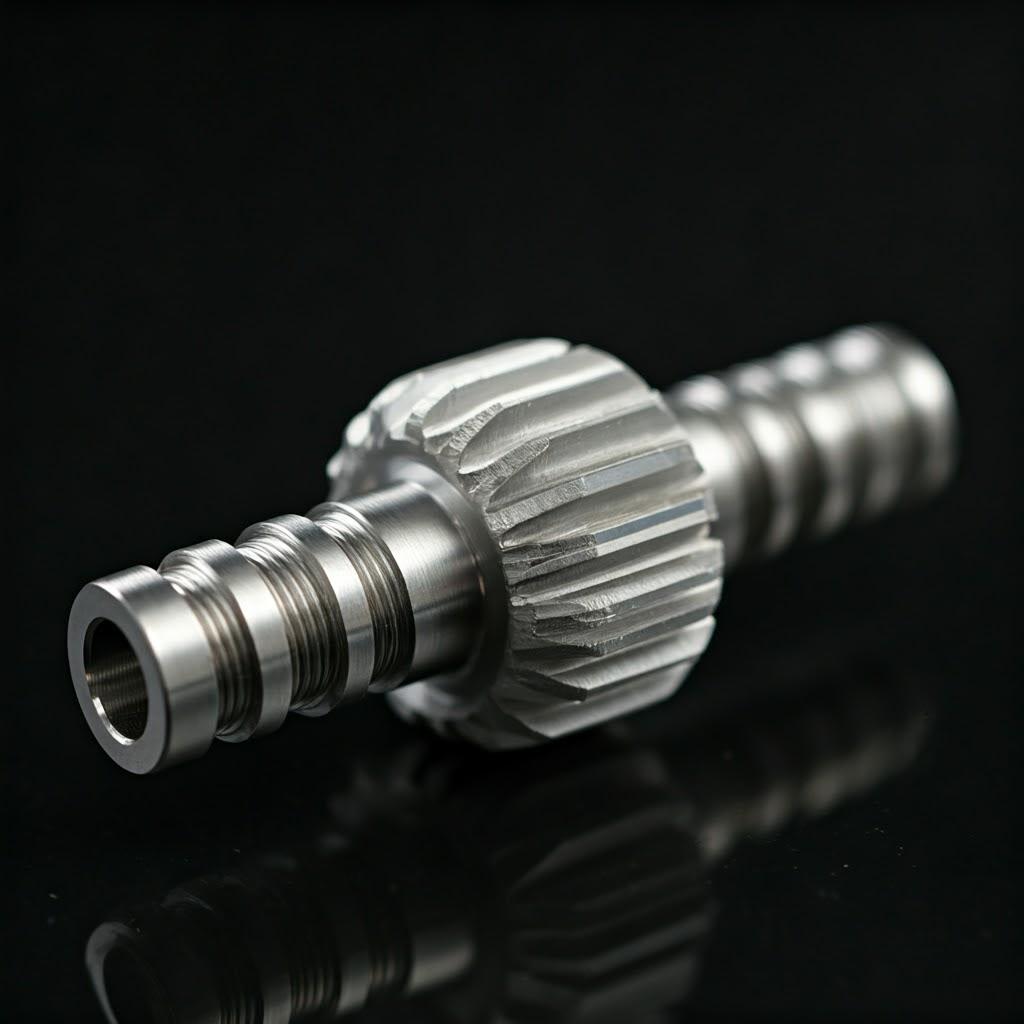
Frequently Asked Questions (FAQ) about 3D Printing Aerospace Fuel Injectors
As metal additive manufacturing gains traction for critical aerospace components, engineers, designers, and procurement professionals often have specific questions about its capabilities and implications for parts like fuel injectors. Here are answers to some frequently asked questions:
Q1: Can 3D printed fuel injectors meet or exceed the performance requirements of traditional ones?
A: Yes, absolutely. In many cases, 3D printed fuel injectors can exceed the performance of their traditionally manufactured counterparts. The primary reason is the design freedom offered by AM. Engineers can create highly optimized internal geometries for fuel swirling, atomization, and mixing that are simply impossible to produce using casting or machining. This can lead to finer fuel sprays, better fuel-air mixing, more complete combustion, reduced emissions (NOx, soot), and improved combustion stability. Furthermore, AM enables the integration of conformal cooling channels, allowing injectors to operate reliably at higher temperatures, which contributes to overall engine thermal efficiency. Part consolidation also enhances reliability by eliminating potential leak paths from brazed or welded joints. However, achieving this superior performance requires leveraging DfAM principles and rigorous process control.
Q2: What certifications are typically necessary for 3D printed aerospace parts like fuel injectors?
A: Certifying flight-critical AM components involves multiple layers. Firstly, the manufacturing supplier should ideally hold an aerospace-specific Quality Management System certification, most commonly AS9100. This demonstrates that the supplier has robust processes for design (if applicable), production, quality control, traceability, and risk management tailored to the aerospace industry. Secondly, the Процесс AM itself (specific machine, material, parameter set, post-processing route) needs to be qualified and statistically controlled to ensure repeatability. Thirdly, and most importantly, the specific part (e.g., the fuel injector design) must undergo a rigorous qualification process defined by the engine manufacturer (OEM) and aviation regulatory authorities (like the FAA or EASA). This involves extensive testing (material properties, dimensional checks, flow tests, fatigue tests, engine tests) to demonstrate that the AM part meets or exceeds all performance, safety, and reliability requirements established for that component. There isn’t a single “AM part” certification; it’s a combination of supplier QMS, process control, and part-specific performance validation.
Q3: How does the surface finish of internal channels affect injector performance, and what can be done about it?
A: The surface finish inside the intricate passages of a fuel injector is critical. As-built AM surfaces are relatively rough compared to machined finishes (Ra often 5-20 µm). This internal roughness can:
- Increase Friction: Leading to higher pressure drops and reduced hydraulic efficiency.
- Alter Flow Dynamics: Affecting swirl patterns, spray cone angles, and atomization quality.
- Promote Coking: Rough surfaces provide nucleation sites for carbon deposits (coke) to form from fuel breakdown at high temperatures, potentially blocking passages over time.
- Reduce Heat Transfer: If the channels are for cooling, roughness can slightly impede convective heat transfer. Therefore, achieving a controlled, smoother internal surface finish is often required. Mitigation strategies include:
- DfAM: Designing smoother transitions and avoiding sharp corners.
- Оптимизация процессов: Fine-tuning AM parameters can influence surface roughness to some extent.
- Постобработка: Techniques like Abrasive Flow Machining (AFM) или Electro-Chemical Polishing (ECP) are specifically used to smooth internal passages, significantly reducing Ra values and improving flow characteristics. The choice depends on the geometry, material, and required finish level.
Q4: Is Hot Isostatic Pressing (HIP) always required for AM fuel injectors?
A: While not universally mandated for every single AM part, HIP is very frequently required for flight-critical aerospace components like fuel injectors, especially those made from nickel-based superalloys like IN718, IN625, and Hastelloy X. The primary reason is reliability. AM processes can sometimes leave microscopic internal pores (due to incomplete fusion or trapped gas). While often small, these pores can act as initiation sites for cracks, significantly reducing fatigue life – a critical property for components experiencing thermal and pressure cycling in an engine. HIP uses high pressure and temperature to effectively close these internal voids, resulting in a fully dense (approaching 100% theoretical density) material with improved fatigue strength, ductility, and creep resistance. Given the safety-critical nature of fuel injectors, OEMs and regulatory bodies often specify HIP as a necessary post-processing step to ensure maximum material integrity and predictable performance.
Q5: What is the typical lead time difference between AM and traditional manufacturing for a new fuel injector design?
A: Additive Manufacturing offers a dramatic reduction in lead time, particularly for new designs, prototypes, and low-volume production.
- Traditional: Developing a new fuel injector via traditional methods (e.g., investment casting + machining + brazing) often involves designing and fabricating complex tooling (molds, dies, fixtures) which can take months to well over a year. Each design iteration requires new or modified tooling, further extending the timeline.
- Аддитивное производство: With AM, the design goes directly from a CAD file to the printer. A functional prototype can often be produced, post-processed, and ready for initial testing within 2 to 6 weeks. Design iterations are much faster, requiring only CAD modifications and a new print run, enabling rapid optimization cycles. While the per-part print time for AM might be longer than the cycle time of an established high-volume traditional process, the elimination of tooling lead time makes AM significantly faster for development and initial production phases. For very high-volume series production, mature traditional methods might eventually achieve lower per-part costs and faster cycle times once tooling is established, but AM maintains an advantage for customization, complexity, and speed in early product lifecycle stages.
Conclusion: The Future of Aerospace Propulsion is Additively Manufactured
The journey through the intricacies of 3D printing aerospace fuel injectors reveals a technology that is not just viable, but transformative. Metal additive manufacturing, leveraging high-performance superalloys like Inconel 718, Inconel 625, and Hastelloy X, offers unprecedented advantages that directly address the evolving demands of modern aerospace propulsion. The ability to create highly complex internal geometries, consolidate multiple parts into a single monolithic component, significantly reduce weight, and drastically shorten development cycles represents a paradigm shift from the constraints of traditional manufacturing.
We’ve seen how AM enables the design of fuel injectors with optimized atomization and mixing for enhanced combustion efficiency and reduced emissions. We’ve explored how integrated cooling channels and the inherent strength of consolidated designs contribute to greater durability and allow engines to operate under more demanding conditions. The benefits extend beyond pure performance; faster iteration cycles fuel innovation, while simplified supply chains and reduced assembly requirements offer logistical and economic advantages.
However, realizing this potential requires a sophisticated approach. Success hinges on embracing Design for Additive Manufacturing (DfAM) principles, meticulously controlling the printing process to achieve required tolerances and surface finishes, implementing essential post-processing steps like heat treatment and HIP, and diligently managing potential challenges like residual stress and porosity.
Critically, the journey relies on strong partnerships. Selecting an additive manufacturing supplier with deep technical expertise in aerospace applications, robust quality systems (like AS9100 certification), proven capabilities with demanding materials, and advanced manufacturing technology is paramount. Companies like Met3dp, specializing in both high-performance metal powders produced via cutting-edge techniques and industry-leading printing equipment, exemplify the type of comprehensive solution provider needed to navigate the complexities of AM for critical components. Their focus on powder quality, printer accuracy, and application development support helps ensure that the theoretical benefits of AM translate into tangible, reliable results.
The adoption of 3D printed fuel injectors, like GE’s LEAP nozzle, is not a futuristic concept; it’s a current reality demonstrating the power of AM to revolutionize critical engine components. As the technology continues to mature and adoption grows, additive manufacturing is set to play an increasingly vital role in shaping the future of more efficient, capable, and sustainable aerospace propulsion.
Ready to explore how metal additive manufacturing can elevate your aerospace fuel injector projects or other demanding applications? Contact the experts at Met3dp today to discuss your requirements and discover how our advanced metal powders, state-of-the-art printing solutions, and comprehensive expertise can power your organization’s additive manufacturing goals. Visit https://met3dp.com/ чтобы узнать больше.
Поделиться
MET3DP Technology Co., LTD - ведущий поставщик решений для аддитивного производства со штаб-квартирой в Циндао, Китай. Наша компания специализируется на производстве оборудования для 3D-печати и высокопроизводительных металлических порошков для промышленного применения.
Сделайте запрос, чтобы получить лучшую цену и индивидуальное решение для вашего бизнеса!
Похожие статьи
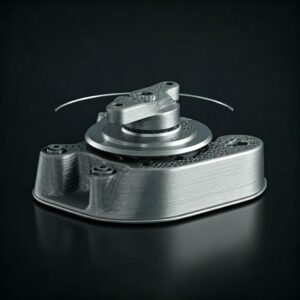
3D-печатные крепления для автомобильных радарных датчиков: Точность и производительность
Читать далее "О компании Met3DP
Последние обновления
Наш продукт
CONTACT US
Есть вопросы? Отправьте нам сообщение прямо сейчас! После получения Вашего сообщения мы всей командой выполним Ваш запрос.
Получите информацию о Metal3DP
Брошюра о продукции
Получить последние продукты и прайс-лист
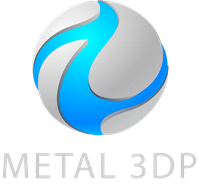
Металлические порошки для 3D-печати и аддитивного производства