3D Printed Exhaust Tips in Heat-Resistant Alloys
Оглавление
Revolutionizing Automotive Aesthetics and Performance: 3D Printed Exhaust Tips in Heat-Resistant Alloys
Subtitle: Enhancing vehicle appeal and durability with advanced metal additive manufacturing for custom exhaust components.
The automotive industry thrives on innovation, constantly seeking ways to enhance vehicle performance, aesthetics, and manufacturing efficiency. One area undergoing a significant transformation is the design and production of exhaust components, particularly the exhaust tip – the final, visible flourish of a vehicle’s exhaust system. Traditionally manufactured through methods like casting, stamping, or CNC machining, exhaust tips are now entering a new era thanks to the power of metal additive manufacturing (AM), commonly known as metal 3D-печать. This technology is not just changing how exhaust tips are made; it’s redefining что возможно. By utilizing advanced, heat-resistant alloys like Inconel 625 (IN625) and 17-4PH stainless steel, металлическая 3D-печать enables the creation of exhaust tips with unparalleled design complexity, optimized performance characteristics, and exceptional durability, perfectly suited to the demanding environment at the tail end of an exhaust system.
For engineers and procurement managers in the automotive sector – from original equipment manufacturers (OEMs) striving for brand differentiation to aftermarket suppliers catering to customization demands and performance tuning specialists pushing the boundaries of speed and sound – metal AM offers a compelling value proposition. Imagine exhaust tips with intricate internal geometries designed to fine-tune exhaust notes, lightweight structures that contribute to overall vehicle efficiency, or unique, brand-specific designs that are simply impossible or prohibitively expensive to create using conventional methods. This is the reality that metal 3D printing delivers. The ability to work with high-performance superalloys like IN625 ensures that these components can withstand the extreme temperatures and corrosive gases inherent in exhaust systems, significantly outlasting traditional materials in many applications. Similarly, the robust properties of 17-4PH stainless steel provide an excellent balance of strength, corrosion resistance, and manufacturability, making it a popular choice for a wide range of automotive applications. This blog post delves into the world of 3D printed exhaust tips, exploring their applications, the distinct advantages offered by additive manufacturing, the critical role of material selection (focusing on IN625 and 17-4PH), and the key considerations for successfully implementing this technology. We aim to provide valuable insights for B2B decision-makers, including wholesale buyers, automotive component suppliers, and distributors looking to leverage cutting-edge manufacturing solutions.
Defining the Role: What are Automotive Exhaust Tips Used For?
While often perceived primarily as a cosmetic enhancement, the exhaust tip plays a multifaceted role in a vehicle’s exhaust system and overall appeal. Understanding its functions is crucial before exploring the benefits of advanced manufacturing techniques like 3D printing.
Core Functions and Applications:
- Directing Exhaust Gases: The most fundamental function is to safely direct hot, corrosive exhaust gases away from the vehicle’s undercarriage and rear fascia. This prevents heat damage, staining, and the potential ingress of harmful fumes into the cabin or surrounding components. The shape and angle of the tip influence the direction and dispersion of the exhaust plume.
- Aesthetic Enhancement: Exhaust tips are a key styling element, significantly impacting a vehicle’s rear profile and perceived value. Manufacturers and consumers use them to:
- Signal Performance: Larger diameter, polished, or uniquely shaped tips (e.g., dual, quad, trapezoidal) often signify a higher-performance model or trim level.
- Customize Appearance: The aftermarket thrives on custom exhaust tips, allowing owners to personalize their vehicles with different finishes (chrome, black ceramic, carbon fiber overlays), shapes, and sizes.
- Brand Identity: OEMs often incorporate specific exhaust tip designs as part of their brand language, making vehicles instantly recognizable.
- Sound Modulation (Subtle Influence): While the primary components responsible for exhaust sound are the muffler, resonator, and engine itself, the exhaust tip can have a subtle influence on the final perceived sound. Its shape, diameter, and internal structure (if any) can slightly alter the resonance and exit characteristics of the exhaust note, contributing to the overall auditory experience. Some advanced, 3D printed designs intentionally incorporate internal features specifically for sound tuning.
- Protecting the Bumper/Fascia: By extending slightly beyond the main exhaust pipe, the tip can help protect the painted or plastic bumper area from direct exposure to hot gases and soot, reducing discoloration and potential heat damage over time.
Industry Use Cases:
The application of exhaust tips spans the entire automotive landscape:
- Original Equipment Manufacturers (OEMs): Integrate exhaust tips as standard or optional equipment across their vehicle lines, balancing cost, durability, and brand aesthetics. Increasingly exploring AM for high-end models or performance variants to achieve unique designs and material properties.
- Aftermarket Suppliers & Distributors: Offer a vast array of replacement and upgrade exhaust tips catering to customization trends and replacement needs. This sector presents significant opportunities for B2B suppliers offering innovative, 3D printed options with unique designs or superior materials. Wholesale buyers are constantly seeking differentiated products.
- Performance Tuning Shops & Motorsport: Demand high-performance, often lightweight, and extremely heat-resistant exhaust tips. Customization is paramount, and materials like IN625 are highly valued for their ability to withstand extreme temperatures found in racing and high-output tuned engines. AM allows for bespoke solutions tailored to specific performance requirements.
- Реставрация классических автомобилей: Sometimes requires the recreation of obsolete or hard-to-find exhaust tip designs. Metal 3D printing offers a viable solution for producing small batches or even one-off replicas with accuracy.
In essence, the exhaust tip is far more than just a tailpipe trim. It’s a functional component, a critical design element, and a symbol of a vehicle’s character and performance intent. The demand for greater customization, enhanced durability, and unique designs makes it an ideal candidate for the disruptive capabilities of metal additive manufacturing. Procurement managers seeking reliable automotive exhaust system component suppliers или wholesale performance exhaust parts should increasingly consider partners proficient in AM technologies.
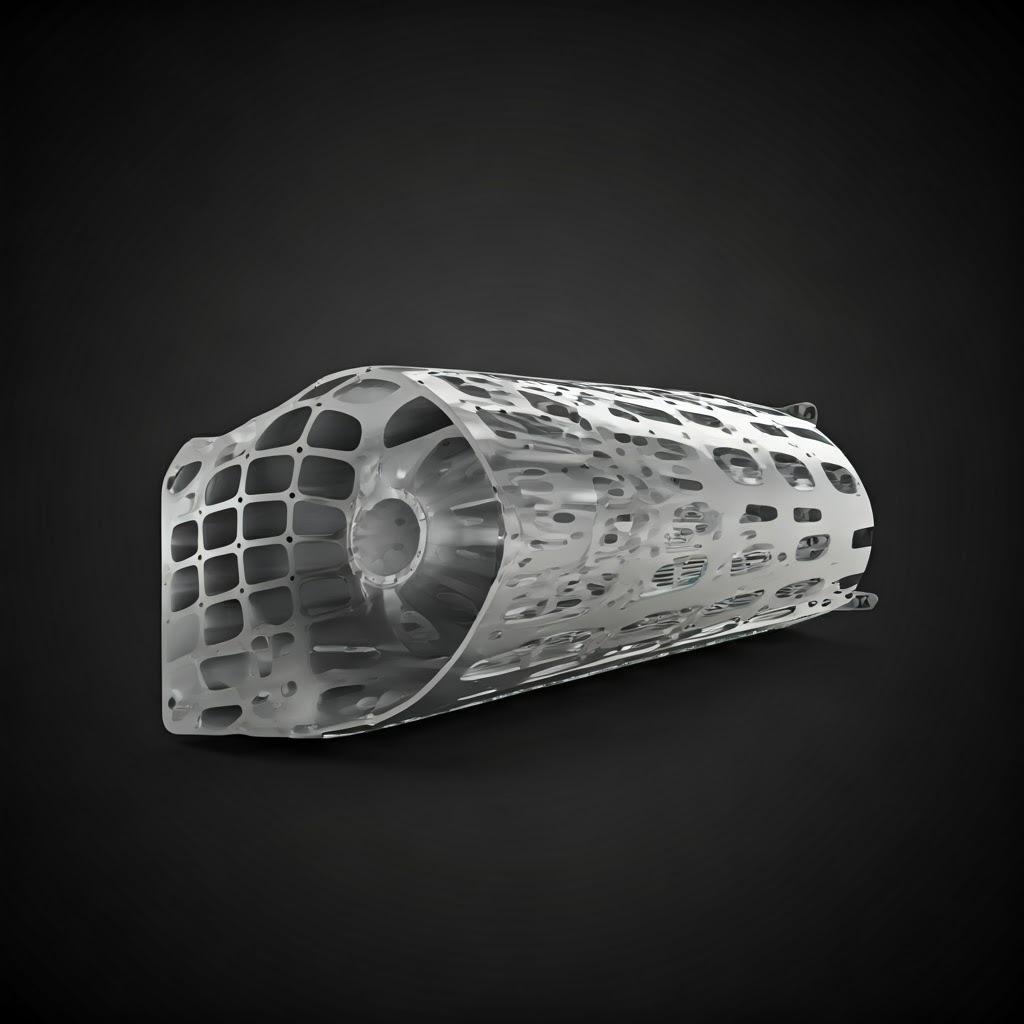
The Additive Advantage: Why Use Metal 3D Printing for Exhaust Tips?
Traditional manufacturing methods for exhaust tips, such as tube bending, hydroforming, CNC machining, casting, and welding/fabrication, have served the industry well. However, they often come with limitations, particularly regarding design complexity, tooling costs, lead times for custom parts, and material waste. Metal additive manufacturing overcomes many of these hurdles, offering compelling advantages for producing exhaust tips, especially when targeting complex designs or high-performance applications.
Key Advantages of Metal AM for Exhaust Tips:
- Unmatched Design Freedom & Complexity: This is arguably the most significant advantage. AM builds parts layer by layer directly from a 3D CAD model, enabling the creation of geometries that are difficult, impossible, or prohibitively expensive to produce conventionally.
- Intricate Internal Structures: Design internal baffles, meshes, or flow channels within the tip for specific acoustic tuning or flow management.
- Organic and Complex Shapes: Create highly stylized, non-linear, or topology-optimized shapes that enhance aesthetics or performance without the constraints of traditional tooling.
- Integrated Features: Combine multiple components into a single printed part, potentially reducing assembly steps and weight (e.g., integrating mounting brackets or internal diffusers).
- Custom Logos/Texturing: Easily incorporate intricate logos, brand names, or surface textures directly into the design.
- Быстрое создание прототипов и итерации: AM allows designers and engineers to quickly produce physical prototypes of new exhaust tip designs. They can test fitment, aesthetics, and even perform preliminary performance assessments much faster and more cost-effectively than waiting for traditional tooling. This accelerates the design cycle and allows for rapid iteration based on feedback. Need a slight angle change or a different internal structure? A revised design can often be printed overnight or within days.
- Mass Customization and Bespoke Designs: For aftermarket suppliers, tuning shops, or even OEMs offering personalization programs, AM enables cost-effective production of unique or low-volume custom exhaust tips. Each tip can potentially be different without the need for dedicated molds or tooling setups, catering directly to individual customer preferences or specific vehicle requirements. This capability is invaluable for businesses targeting the bespoke exhaust tip design market.
- Tooling Elimination: Traditional methods often require significant investment in molds (casting), dies (stamping/hydroforming), or complex fixtures (CNC machining). AM eliminates this requirement, drastically reducing upfront costs and lead times, particularly for low-to-medium volume production runs or highly complex parts. This makes it economically viable to explore designs that would otherwise be too costly.
- Потенциал облегчения: While exhaust tips are not typically primary targets for aggressive lightweighting compared to structural components, AM allows for material placement only where needed. Through topology optimization and the creation of internal lattice structures, weight can be reduced compared to solid, conventionally machined tips without compromising strength, contributing marginally to overall vehicle efficiency and performance dynamics.
- Material Flexibility and High-Performance Alloys: AM processes, particularly Powder Bed Fusion (PBF) techniques like Selective Laser Melting (SLM) / Laser Powder Bed Fusion (L-PBF) and Selective Electron Beam Melting (SEBM), can effectively process a wide range of metals, including challenging high-temperature superalloys like IN625. These materials offer superior heat and corrosion resistance compared to standard stainless steels often used in conventional tips, leading to significantly longer component life, especially in high-performance or demanding environments. Access to these advanced materials is a key enabler for premium heat-resistant alloy automotive components.
- Сокращение отходов материалов: Unlike subtractive manufacturing (like CNC machining) which starts with a solid block and removes material, AM is an additive process, using only the material necessary to build the part (plus support structures). This results in significantly less material waste, which is particularly beneficial when working with expensive alloys like IN625.
Comparison: AM vs. Traditional Methods for Exhaust Tips
Характеристика | Аддитивное производство металлов (AM) | Traditional Methods (CNC, Casting, Fabrication) |
---|---|---|
Сложность конструкции | Very High (Internal channels, organic shapes) | Moderate to Low (Limited by tooling/process) |
Персонализация | High (Economical for low volumes/unique parts) | Low (Requires specific tooling per design) |
Стоимость оснастки | None / Minimal | High (Molds, dies, fixtures) |
Prototyping Speed | Fast (Hours/Days) | Slow (Weeks/Months for tooling) |
Варианты материалов | Wide range, including superalloys (e.g., IN625) | More limited by process (e.g., castability) |
Облегчение | Good potential (Topology optimization, lattices) | Limited potential (Typically solid) |
Материальные отходы | Low (Additive process) | High (Subtractive processes like CNC) |
Unit Cost (Low Vol) | Potentially Lower (No tooling amortization) | High (Tooling cost dominates) |
Unit Cost (High Vol) | Potentially Higher (Slower build speed) | Lower (Economy of scale) |
Lead Time (New Design) | Короткий | Длинный |
Export to Sheets
While AM might have higher per-part costs in high-volume scenarios compared to established methods like stamping, its advantages in design freedom, customization, speed for new designs, and ability to process high-performance materials make it an increasingly attractive option for automotive exhaust tips, particularly in the premium, performance, and aftermarket segments. Companies seeking metal additive manufacturing automotive solutions can gain a significant competitive edge.
Material Matters: Recommended Heat-Resistant Alloys (IN625 & 17-4PH) for 3D Printed Exhaust Tips
Selecting the right material is paramount for ensuring the longevity, performance, and aesthetic integrity of an exhaust tip, especially given the harsh operating conditions it endures. Extreme temperatures, corrosive exhaust gases, moisture, road salts, and vibrations demand materials with exceptional properties. Metal 3D printing opens the door to using high-performance alloys that might be difficult or costly to process conventionally. For demanding exhaust tip applications, two materials stand out: Inconel 625 (IN625) and 17-4PH Stainless Steel.
Leveraging advanced powder manufacturing techniques, such as the gas atomization and Plasma Rotating Electrode Process (PREP) employed by specialists like Met3dp, ensures the availability of high-quality, spherical metal powders crucial for successful additive manufacturing. Met3dp’s commitment to producing powders with high sphericity and good flowability translates directly into denser, higher-quality printed parts with superior mechanical properties – essential for components like exhaust tips.
Inconel 625 (IN625): The High-Performance Choice
Inconel 625 is a nickel-chromium-molybdenum-niobium superalloy renowned for its outstanding combination of high strength, excellent fabricability, and exceptional corrosion resistance across a wide temperature range.
- Key Properties & Benefits for Exhaust Tips:
- Исключительная высокотемпературная прочность: Maintains significant strength and structural integrity at elevated temperatures (up to ~980°C / 1800°F), far exceeding the capabilities of most stainless steels. This prevents deformation or failure under prolonged exposure to hot exhaust gases, crucial for performance vehicles.
- Outstanding Corrosion Resistance: Highly resistant to a wide range of corrosive environments, including oxidation, acidic condensates found in exhaust streams, and pitting/crevice corrosion from road salts and moisture. This ensures a long service life and maintains aesthetic appearance.
- Excellent Fatigue Strength: Withstands the cyclic heating/cooling and vibrations inherent in an exhaust system without cracking.
- Weldability/Printability: While requiring careful parameter control, IN625 is readily processable using Laser Powder Bed Fusion (L-PBF) and Electron Beam Melting (EBM) techniques, allowing complex geometries to be realized.
- Why Choose IN625? Ideal for motorsport applications, high-performance tuned vehicles, luxury cars where longevity and performance are paramount, and designs involving thin walls or intricate features operating under extreme heat. It’s the go-to choice when standard stainless steels may not suffice. B2B buyers looking for IN625 3D printing powder или high-temperature metal printing services will find this alloy indispensable for demanding applications.
17-4PH Stainless Steel: The Versatile Workhorse
17-4 Precipitation Hardening (PH) stainless steel is a chromium-nickel-copper alloy known for its excellent combination of high strength, good corrosion resistance, good toughness, and ease of heat treatment.
- Key Properties & Benefits for Exhaust Tips:
- Высокая прочность и твердость: Achieves high strength levels through a simple, low-temperature heat treatment (aging) after printing. This provides good resistance to dents, scratches, and wear.
- Хорошая коррозионная стойкость: Offers significantly better corrosion resistance than standard 300-series stainless steels (like 304 or 316), suitable for most OEM and aftermarket exhaust tip applications. While not as resistant as IN625 at extreme temperatures, it’s sufficient for many scenarios.
- Good Toughness: Resists cracking and fracture under typical road conditions and vibrations.
- Эффективность затрат: Generally less expensive than nickel-based superalloys like IN625, providing a good balance of performance and cost.
- Отличная пригодность для печати: Well-understood and widely processed using L-PBF, allowing for reliable and repeatable production.
- Why Choose 17-4PH? A strong contender for a wide range of automotive exhaust tips, including OEM applications, aftermarket upgrades, and moderately tuned vehicles. It offers a significant performance step-up from basic stainless steels without the higher cost of IN625. Its heat treatability allows properties to be tailored. Procurement managers sourcing 17-4PH stainless steel additive manufacturing services will find it suitable for durable and aesthetically pleasing exhaust components.
Material Comparison Table:
Недвижимость | Инконель 625 (IN625) | 17-4PH Stainless Steel (Heat Treated) | Typical 304/316 Stainless Steel |
---|---|---|---|
Primary Elements | Ni, Cr, Mo, Nb | Fe, Cr, Ni, Cu | Fe, Cr, Ni |
Max Use Temp. | ~980°C (1800°F) | ~315°C (600°F) continuous | ~260-300°C (500-570°F) |
Коррозионная стойкость | Исключительный | Good to Very Good | Moderate to Good |
Strength (High Temp) | Отличный | Умеренный | Низкий |
Strength (Room Temp) | Высокая | Very High (Post Heat Treat) | Умеренный |
Printability (PBF) | Good (Requires expertise) | Отличный | Хороший |
Относительная стоимость | Высокая | Средний | Низкий |
Идеальное применение | Extreme Heat, Performance, Motorsport | OEM, Aftermarket, Moderate Performance | Basic OEM/Aftermarket |
Export to Sheets
Conclusion on Materials:
The choice between IN625 and 17-4PH depends heavily on the specific application requirements, particularly the operating temperature and budget. IN625 provides ultimate performance and longevity in extreme conditions, while 17-4PH offers a robust and cost-effective solution for a broader range of applications. Both materials are readily available as high-quality powders optimized for additive manufacturing from specialized suppliers like Met3dp, enabling automotive companies to leverage metal 3D printing for superior exhaust tip solutions. Consulting with experienced поставщики металлических порошков and AM service providers is crucial to making the optimal material selection for your specific exhaust tip project.
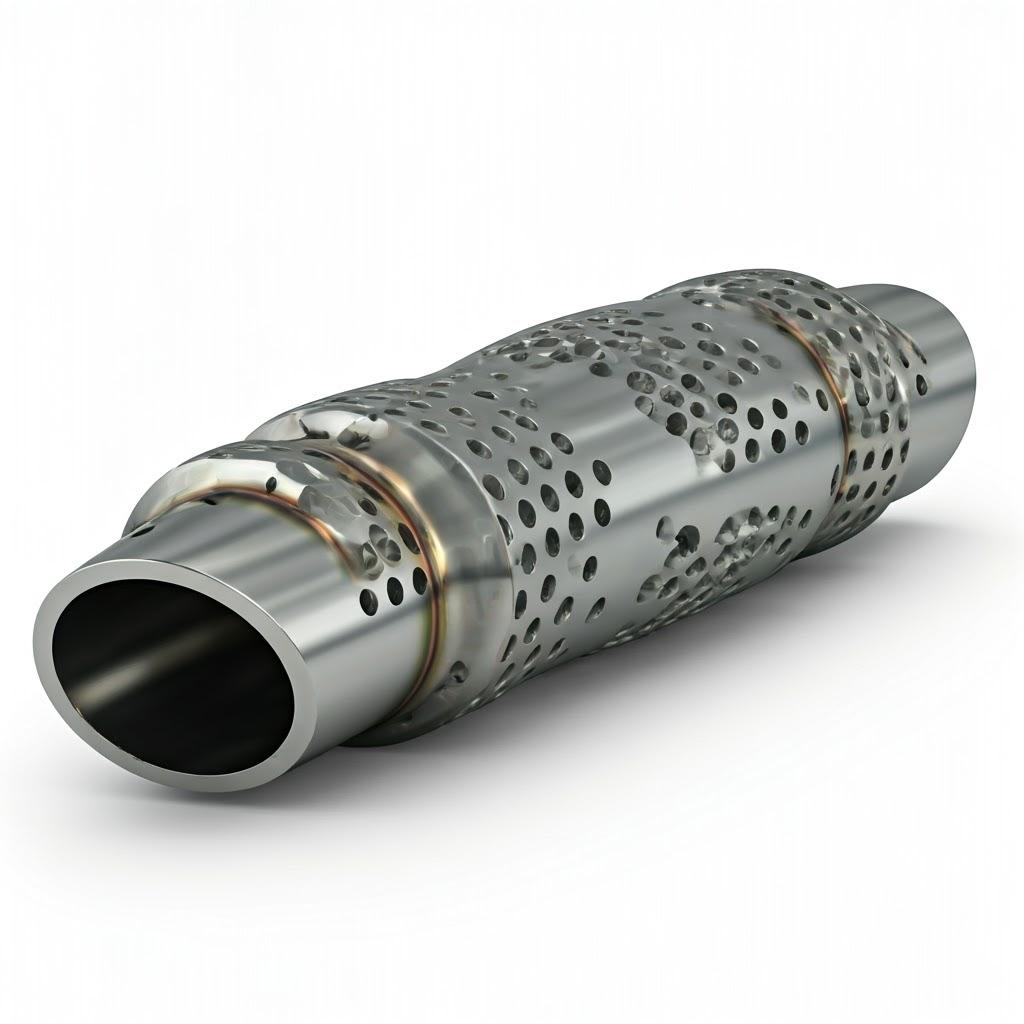
Designing for Durability: Key Considerations for Additively Manufactured Exhaust Tips
Successfully leveraging metal additive manufacturing for exhaust tips goes beyond simply choosing the right material; it requires adopting a Design for Additive Manufacturing (DfAM) approach. DfAM principles help engineers optimize designs not just for end-use performance (like heat resistance and aesthetics) but also for the nuances of the layer-by-layer printing process itself. This ensures better printability, reduces the likelihood of defects, minimizes post-processing efforts, and ultimately leads to a more cost-effective and reliable component. For automotive engineers designing the next generation of performance or custom exhaust tips, incorporating these considerations early in the design phase is critical.
Key DfAM Principles for 3D Printed Exhaust Tips:
- Optimize Geometry for Printability & Self-Support:
- Overhangs and Angles: Powder Bed Fusion processes (L-PBF, SEBM) can typically print overhangs up to a certain angle (often around 45 degrees from the horizontal) without support structures. Designing features like outlets, internal baffles, or mounting points to stay within these self-supporting angles minimizes the need for supports, which saves material, reduces print time, and simplifies post-processing. Consider using chamfers or fillets instead of sharp horizontal overhangs.
- Hole Orientation: Horizontal holes are more challenging to print accurately than vertical holes. Orienting critical bores vertically or designing them with teardrop shapes can improve roundness and reduce the need for internal supports.
- Bridging: Avoid long, unsupported horizontal spans (bridges). If unavoidable, design them as arches or minimize their length.
- Wall Thickness Management:
- Minimum Wall Thickness: There’s a minimum printable wall thickness determined by the AM process, machine, and material (often around 0.4-0.8 mm for L-PBF). Ensure all features meet this requirement to prevent print failures.
- Uniformity vs. Variation: While AM allows varying wall thickness, abrupt changes can lead to differential cooling rates and increased thermal stress, potentially causing warping or cracking, especially with high-temperature alloys like IN625. Aim for gradual transitions in thickness where possible.
- Heat Dissipation: Thicker sections retain heat longer. Consider how wall thickness variations might impact thermal management during printing and in the final application. Thin, intricate features might be desirable aesthetically but need sufficient thickness for durability and heat resistance.
- Internal Structures and Channels:
- Удаление порошка: One of AM’s strengths is creating complex internal features (e.g., for sound tuning or flow control). However, you must design access points or strategically placed drainage holes to allow unfused metal powder to be removed after printing. Trapped powder adds weight and can sinter during heat treatment, becoming permanently fixed.
- Support for Internals: Complex internal overhangs may require internal support structures. These can be extremely difficult or impossible to remove manually. Consider designing internal features to be self-supporting or explore soluble or easily breakable support strategies if offered by the service provider. Alternatively, advanced multi-axis deposition techniques might mitigate some internal support needs.
- Stress Concentration Mitigation:
- Fillets and Radii: Sharp internal corners act as stress concentrators, which can be initiation points for fatigue cracks under thermal cycling and vibration – conditions common for exhaust tips. Incorporate generous fillets and radii, especially at junctions between thin and thick sections or at mounting points.
- Плавные переходы: Ensure smooth transitions between different geometric features to distribute stress more evenly.
- Support Structure Strategy (Collaboration with Provider):
- Minimize Need: As mentioned, designing for self-support is ideal.
- Доступность: Where supports are necessary (e.g., for low-angle overhangs, large bridges, or ensuring flatness of critical surfaces), design the part so that support structures are easily accessible for removal during post-processing without damaging the part surface.
- Contact Points: Discuss with your AM service provider, like Met3dp, how support contact points might affect surface finish and if critical surfaces should be oriented to avoid supports altogether. Met3dp’s expertise in both L-PBF and SEBM способы печати allows them to advise on the best orientation and support strategy for specific designs and materials.
- Консолидация частей:
- Explore opportunities to combine multiple components of an exhaust tip assembly (e.g., the tip itself, an internal diffuser, mounting flange) into a single printed part. This reduces assembly time, potential leak paths, and part count, aligning with efficient manufacturing principles often sought by automotive component suppliers.
By embracing DfAM, engineers can unlock the full potential of metal 3D printing for exhaust tips, creating components that are not only visually striking and performant but also efficiently manufacturable. Close collaboration with experienced AM service providers who understand the nuances of DfAM for automotive components is highly recommended during the design process.
Precision and Finish: Understanding Tolerance, Surface Quality, and Accuracy in 3D Printed Exhaust Tips
For automotive components, particularly those visible like an exhaust tip or requiring precise fitment, understanding the achievable levels of precision, surface finish, and overall dimensional accuracy is crucial. Metal additive manufacturing technologies, while incredibly capable, have inherent characteristics regarding these aspects that differ from traditional methods like CNC machining. Setting realistic expectations and knowing when post-processing is necessary are key for engineers and procurement managers.
Dimensional Tolerances:
- Typical Achievable Tolerances (As-Printed): The tolerances achievable directly from the AM process depend heavily on the specific technology (L-PBF generally offers finer tolerances than SEBM, though SEBM excels in reducing residual stress), the machine calibration, part size, geometry, orientation in the build chamber, and the material being printed.
- L-PBF: Often achieves tolerances in the range of ±0.1 mm to ±0.2 mm for smaller features, potentially increasing slightly for larger dimensions (e.g., ±0.1-0.2% of the overall dimension).
- SEBM: May have slightly looser tolerances initially compared to L-PBF but benefits from reduced thermal stress, potentially leading to better overall part stability for certain geometries.
- Факторы, влияющие на толерантность: Thermal expansion/contraction during printing and cooling, slight variations in layer thickness, laser/electron beam spot size, and powder characteristics all play a role. Residual stress can also lead to minor distortions after the part is removed from the build plate.
- Critical Dimensions: For interfaces requiring tight tolerances (e.g., mating surfaces with the exhaust pipe or mounting points), it’s common practice to design the part slightly oversized in these areas and utilize post-process CNC machining to achieve the final required precision (often down to ±0.025 mm or tighter).
Обработка поверхности (шероховатость):
- As-Printed Surface Roughness (Ra): Metal AM parts inherently have a rougher surface finish compared to machined parts. The roughness depends on:
- Толщина слоя: Thicker layers generally result in rougher surfaces.
- Powder Particle Size: Finer powders can lead to smoother finishes.
- Orientation: Surfaces parallel to the build plate (up-facing) are typically smoother than vertical walls, which are smoother than down-facing surfaces or those requiring support structures. Support contact points leave witness marks that need removal.
- Процесс: L-PBF often produces finer surface finishes (Ra 6-15 µm) compared to SEBM (Ra 20-35 µm) in the as-printed state.
- Aesthetic vs. Functional Surfaces: For an exhaust tip, the visible external surfaces often require a much smoother finish for aesthetic appeal than internal surfaces or non-critical mounting areas.
- Achieving Smoother Finishes: Significant improvements in surface finish require post-processing steps like bead blasting, tumbling, polishing, or electro-chemical polishing (see next section). Achieving a mirror polish typically involves manual or automated polishing steps after initial smoothing.
Точность размеров:
- Overall Accuracy: This refers to how closely the final part conforms to the original CAD model across its entire geometry. It’s influenced by tolerances, surface roughness, and potential distortions.
- Warping and Distortion: Residual stresses built up during the rapid heating and cooling cycles of the AM process can cause parts to warp or distort, particularly large, flat sections or designs with significant variations in thickness. Techniques like stress relief heat treatments (often performed while the part is still on the build plate) and careful build orientation planning are crucial to minimize distortion. Met3dp’s expertise, detailed further on our О нас page, includes managing these thermal challenges through process control and post-processing knowledge.
- Контроль качества: Reputable AM service providers utilize 3D scanning and CMM (Coordinate Measuring Machine) inspection to verify dimensional accuracy against the CAD model and ensure parts meet specified tolerances.
Expectation Management:
It’s vital for procurement managers sourcing high-accuracy automotive parts via AM to understand that achieving the tightest tolerances or finest finishes often requires secondary operations. Communicating critical dimensions, required surface finishes for specific areas (e.g., visible surfaces vs. mating surfaces), and overall accuracy requirements clearly to the AM provider is essential for obtaining quotes that include necessary post-processing and ensuring the final part meets expectations. Relying on partners with industry-leading equipment and robust quality management systems, like Met3dp, provides confidence in achieving consistent and accurate results for mission-critical components like performance exhaust tips.
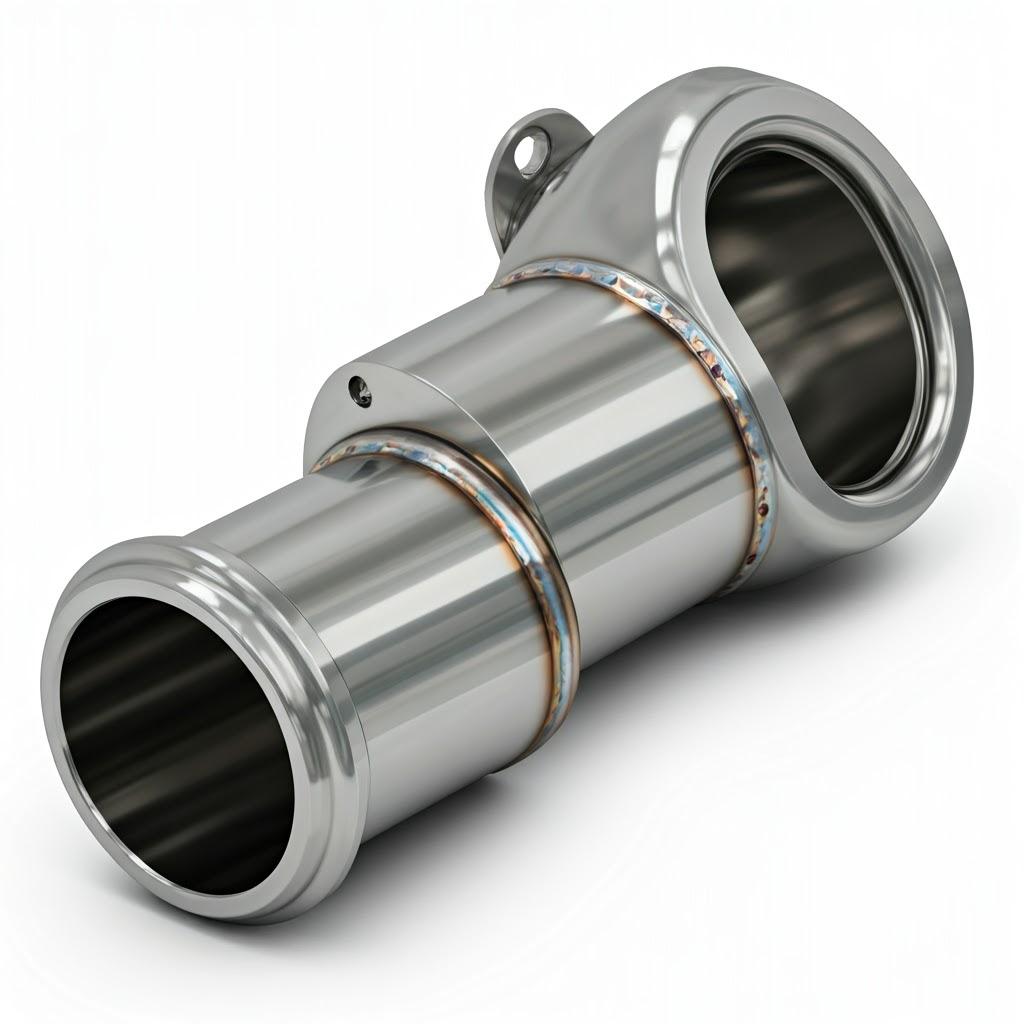
Beyond the Print: Essential Post-Processing for Functional Exhaust Tips
The journey of a 3D printed metal exhaust tip doesn’t end when the printer stops. A series of crucial post-processing steps are typically required to transform the raw printed part into a functional, durable, and aesthetically pleasing final component. These steps are essential for achieving the desired mechanical properties, dimensional accuracy, surface finish, and overall quality. Understanding these requirements is vital for estimating total cost and lead time.
Common Post-Processing Steps for AM Exhaust Tips:
- De-Powdering: The first step after the build finishes and cools is removing the part(s) from the build chamber and extracting them from the bed of unfused metal powder. Thorough removal of all loose powder, especially from internal channels or complex geometries, is critical. Automated de-powdering stations and manual cleaning with compressed air are often used. Any trapped powder can negatively impact performance or sinter during subsequent heat treatment.
- Stress Relief / Heat Treatment: This is arguably one of the most critical steps, especially for parts like exhaust tips made from alloys like IN625 or 17-4PH that experience significant thermal stress during printing and operation.
- Снятие стресса: Often performed while the part is still attached to the build plate, this involves heating the part in a controlled atmosphere furnace to a specific temperature below the material’s critical transformation point. This relieves internal stresses built up during printing, significantly reducing the risk of distortion or cracking when the part is removed from the plate or during its service life.
- Aging/Hardening (for PH Steels like 17-4PH): For precipitation-hardening steels, a specific heat treatment cycle (solution annealing followed by aging at a precise temperature) is required to achieve the desired final hardness, strength, and toughness.
- Annealing/Solution Treatment (Optional): Depending on the alloy and application, other heat treatments might be needed to optimize microstructure, ductility, or corrosion resistance.
- Importance: Skipping or improperly performing heat treatment can lead to premature component failure.
- Part Removal from Build Plate: Parts are typically printed on a thick metal build plate. They need to be separated, usually using wire EDM (Electrical Discharge Machining) or band sawing. This step requires care to avoid damaging the part.
- Демонтаж опорной конструкции: Any support structures necessary during the printing process must be removed. This can be done manually (using pliers, grinders, or hand tools) or sometimes through CNC machining or EDM, depending on the support complexity and location. This step can be labor-intensive and requires skill to avoid marring the part surface. Designing for minimal support (DfAM) significantly simplifies this stage.
- Отделка поверхности: As-printed surfaces are typically too rough for the final visible parts of an exhaust tip. Several methods can be employed, often in combination:
- Bead Blasting / Sand Blasting: Propels media (glass beads, ceramic grit, etc.) against the surface to create a uniform, matte finish and remove minor imperfections. It’s effective for general cleaning and improving cosmetic appearance.
- Tumbling / Vibratory Finishing: Places parts in a machine with media that vibrates or tumbles, gradually smoothing surfaces and edges. Effective for batch processing but less controlled for specific features.
- Manual Grinding/Polishing: Skilled technicians use various tools to grind down support witnesses, smooth surfaces, and achieve high-gloss or brushed finishes. Essential for achieving mirror polishes on premium exhaust tips.
- Electrochemical Polishing: An electrochemical process that removes a small layer of material, resulting in a very smooth, bright finish, particularly effective on complex shapes and internal surfaces.
- CNC Machining: Used not only for tolerances (see below) but can also create specific surface finishes (e.g., machined grooves, precise chamfers).
- CNC Machining for Critical Tolerances: As mentioned previously, if specific features require tolerances tighter than achievable by the AM process itself (e.g., the inlet diameter for connection to the exhaust pipe, mounting holes), precision CNC machining is employed to achieve the final dimensions.
- Покрытие (опционально): For enhanced aesthetics or additional protection, coatings can be applied:
- Ceramic Coating: High-temperature ceramic coatings (often black, titanium, or other colors) are popular for performance exhaust components, providing thermal barrier properties and a durable, corrosion-resistant finish.
- Powder Coating / Painting: For primarily aesthetic purposes, though heat resistance needs to be considered.
- Plating: Chrome or other plating types can be applied for a specific look, though adhesion to AM surfaces requires proper preparation.
- Проверка качества: Throughout the post-processing chain, quality checks are essential. This includes visual inspection, dimensional verification (using calipers, CMM, or 3D scanning), and potentially material testing or non-destructive testing (NDT) like X-ray for critical applications to ensure internal integrity (e.g., detecting porosity).
The extent and combination of these post-processing metal 3D prints steps depend entirely on the design complexity, material choice, and the final requirements for the exhaust tip. It’s crucial for procurement teams sourcing услуги по обработке металлов AM to factor these steps into the overall cost and lead time calculations. Partnering with a full-service provider like Met3dp, capable of managing the entire workflow from printing through complex post-processing and quality assurance, simplifies the supply chain.
Navigating Challenges: Overcoming Potential Issues in 3D Printing Exhaust Tips
While metal 3D printing offers tremendous advantages for producing exhaust tips, it’s not without its challenges. Understanding these potential hurdles and knowing how experienced providers like Met3dp address them is key to successful implementation. Proactive planning and process control can mitigate most issues.
Common Challenges and Mitigation Strategies:
- Warping and Distortion:
- Issue: Uneven heating and cooling during the layer-by-layer process builds internal stresses, which can cause the part to warp or distort, especially after removal from the build plate. This is more pronounced in large, flat parts or designs with varying thicknesses, particularly with high-thermal-expansion alloys.
- Mitigation:
- Optimized Build Orientation: Orienting the part strategically on the build plate can minimize stress accumulation in critical areas.
- Robust Support Structures: Properly designed supports anchor the part securely and help dissipate heat.
- Оптимизация параметров процесса: Fine-tuning laser/electron beam power, scan speed, and hatching strategies minimizes localized overheating.
- Thermal Simulation: Advanced simulation software can predict stress buildup and guide design/orientation adjustments.
- Stress Relief Heat Treatment: Performing a stress relief cycle before removing the part from the build plate is crucial for dimensional stability.
- Support Removal Difficulties:
- Issue: Support structures, while necessary, can be difficult and time-consuming to remove, especially from internal channels or intricate external features. Removal can leave witness marks or potentially damage the part surface if not done carefully.
- Mitigation:
- DfAM for Self-Support: Designing parts with overhang angles less than ~45 degrees and minimizing features requiring support is the best approach.
- Optimized Support Design: Using easily breakable support structures (e.g., conical or thin-walled supports) where possible. Designing supports for accessibility.
- Specialized Removal Techniques: Utilizing wire EDM or precise grinding for delicate areas.
- Process Selection: In some cases, binder jetting (followed by sintering) might offer support-free advantages for certain geometries, though mechanical properties might differ.
- Achieving Desired Surface Finish:
- Issue: As-printed surfaces are inherently rougher than machined surfaces. Achieving a smooth, aesthetically pleasing finish (like polished or uniformly matte) requires significant post-processing effort.
- Mitigation:
- Orientation Planning: Printing critical aesthetic surfaces facing upwards or vertically generally yields better initial finishes.
- Parameter Optimization: Using finer layer heights and optimized scanning strategies can improve as-printed roughness, though often at the cost of longer print times.
- Effective Post-Processing: Selecting the right combination of bead blasting, tumbling, polishing, or electro-polishing based on the desired finish and material. Budgeting adequately for these steps.
- Material Integrity and Porosity:
- Issue: Incomplete melting or gas entrapment during printing can lead to internal voids or porosity within the material. Excessive porosity can compromise mechanical properties (strength, fatigue life) and corrosion resistance.
- Mitigation:
- High-Quality Powder: Using powders with controlled particle size distribution, high sphericity, and low internal porosity (like those produced using advanced atomization by Met3dp) is fundamental. Powder handling to prevent moisture contamination is also key.
- Optimized Print Parameters: Ensuring sufficient energy density (laser/e-beam power, speed) to fully melt the powder particles. Using protective inert gas atmospheres (Argon, Nitrogen) to prevent oxidation.
- Горячее изостатическое прессование (HIP): For critical applications demanding maximum density (near 100%), HIP involves applying high temperature and isostatic gas pressure after printing to close internal pores. Often used for aerospace and medical, but potentially applicable for very high-performance exhaust tips.
- Контроль качества: Non-destructive testing (NDT) like micro-CT scanning or X-ray can detect internal porosity.
- Cost Management:
- Issue: Metal AM can be perceived as expensive, especially due to material costs (e.g., IN625 powder), machine time, and extensive post-processing requirements.
- Mitigation:
- DfAM for Efficiency: Optimizing designs to reduce print volume, minimize supports, and simplify post-processing.
- Nesting: Printing multiple parts simultaneously in a single build maximizes machine utilization.
- Выбор материала: Choosing the most cost-effective material that meets requirements (e.g., 17-4PH instead of IN625 if appropriate).
- Volume Considerations: Discussing potential wholesale 3D printed parts pricing or bulk discounts with suppliers for larger quantities.
- Holistic Cost View: Considering the total cost of ownership, including reduced tooling, faster development, and potential performance gains, not just the per-part print cost.
By partnering with an experienced AM service provider like Met3dp, who proactively addresses these metal AM porosity control и preventing warping additive manufacturing challenges through rigorous process control, advanced equipment, and material science expertise, automotive companies can confidently adopt 3D printing for demanding applications like heat-resistant exhaust tips. Explore the range of materials and продукты offered to see how these challenges are overcome in practice.
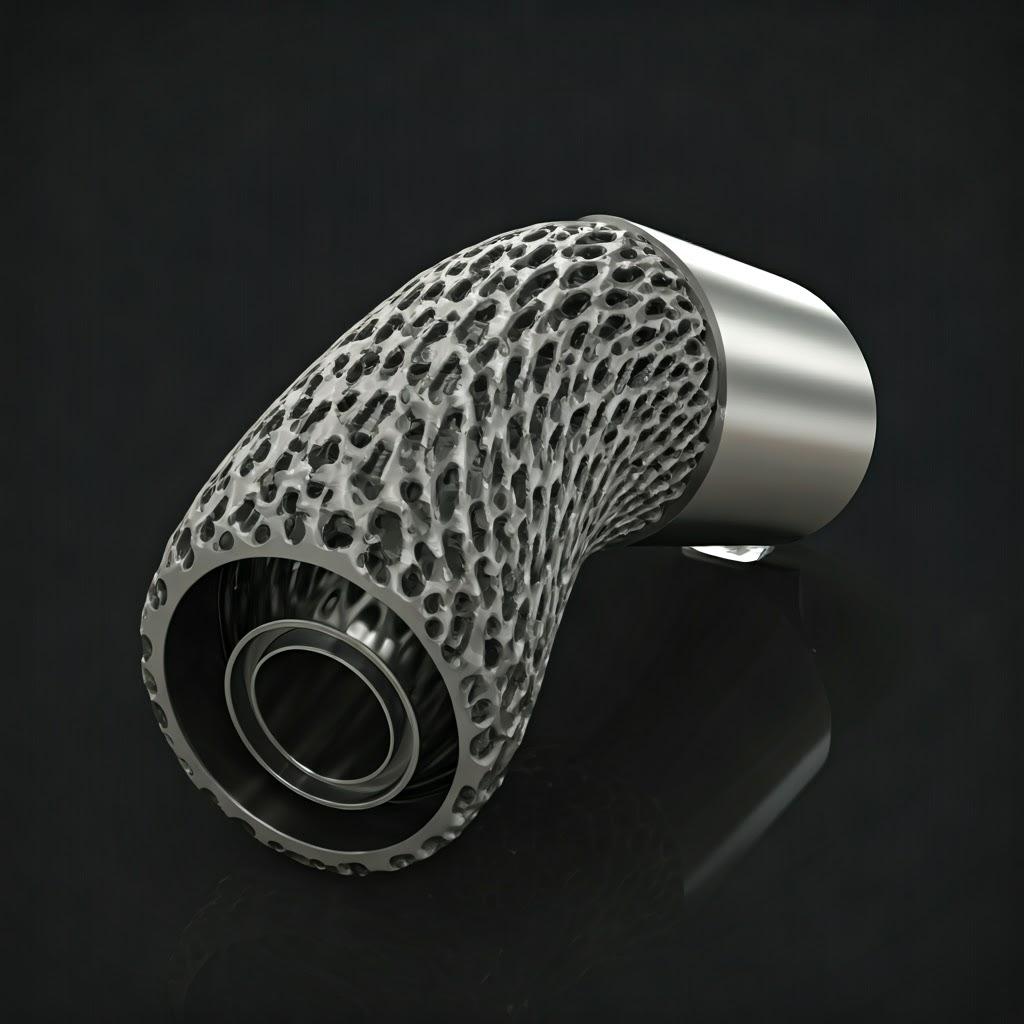
Sourcing Success: How to Choose the Right Metal 3D Printing Service Provider for Automotive Components
Selecting the right additive manufacturing partner is as crucial as perfecting the design or choosing the correct material. The quality, consistency, and reliability of your 3D printed exhaust tips depend heavily on the capabilities and expertise of your chosen service provider. For automotive engineers and procurement managers navigating the landscape of metal 3D printing service providers for automotive, establishing clear selection criteria is essential for a successful sourcing outcome.
Key Criteria for Evaluating AM Service Providers:
- Material Expertise and Portfolio:
- Specific Alloy Experience: Ensure the provider has demonstrable experience printing the specific alloys you require, such as IN625 and 17-4PH stainless steel. Ask for case studies or sample parts.
- Powder Quality and Sourcing: Inquire about their metal powder sourcing and quality control processes. Providers like Met3dp, who manufacture their own high-quality spherical powders using advanced techniques like gas atomization and PREP, offer greater control over material consistency and performance.
- Range of Materials: While you may need specific alloys now, a provider with a broader portfolio indicates deeper materials science knowledge and potential flexibility for future projects.
- Technological Capability:
- Relevant AM Processes: Verify they operate the appropriate technologies (e.g., L-PBF for fine features and finish, SEBM for reduced stress in certain alloys/geometries). Understand the specific machines they use and their capabilities (build volume, laser/beam power, control systems). Met3dp’s offering of both SEBM printers and L-PBF capabilities provides flexibility.
- Объем сборки: Ensure their machines can accommodate the size of your exhaust tip design, including potential nesting for small production runs.
- Software and Workflow: Assess their use of simulation software for optimizing builds, process monitoring capabilities, and digital traceability throughout the manufacturing process.
- Quality Management and Certifications:
- Quality Management System (QMS): Look for certifications like ISO 9001, which demonstrates a commitment to consistent quality processes.
- Industry-Specific Certifications (A Plus): While less common for exhaust tips than critical powertrain or structural components, experience with automotive standards like IATF 16949 (even if not fully certified for AM) indicates an understanding of automotive quality expectations.
- Inspection Capabilities: Ensure they have robust inspection capabilities, including CMM, 3D scanning, and potentially NDT methods, to verify parts meet specifications.
- Post-Processing Capabilities:
- In-House vs. Outsourced: Determine which post-processing steps (heat treatment, support removal, machining, finishing) they perform in-house versus outsourcing. In-house capabilities generally offer better control over the entire workflow, lead times, and quality.
- Экспертиза: Verify their expertise in the specific post-processing required for your chosen material and finish requirements (e.g., experience heat treating IN625 correctly).
- Industry Experience and Application Knowledge:
- Automotive Portfolio: Have they produced parts for the automotive industry before? Understanding the specific demands and context of automotive applications is invaluable.
- Техническая поддержка: Do they offer DfAM support and consultation? A good partner collaborates with you to optimize designs for manufacturing. Met3dp prides itself on partnering with organizations, leveraging decades of collective expertise in metal AM to provide comprehensive solutions.
- Lead Times and Capacity:
- Quoted Lead Times: Get realistic lead time estimates that include printing и all necessary post-processing steps.
- Capacity: Ensure they have sufficient capacity to meet your volume requirements, whether for prototypes or small series production. Inquire about their ability to handle bulk additive manufacturing orders if applicable.
- Communication and Customer Service:
- Responsiveness: Evaluate their responsiveness during the quoting and inquiry process.
- Project Management: Do they assign a dedicated point of contact for your project? Clear and consistent communication is key.
- Конкурентоспособность по цене:
- Transparent Pricing: Ensure quotes clearly break down costs (material, print time, post-processing, NDT, etc.).
- Value Proposition: Don’t choose solely on the lowest price. Consider the value offered in terms of expertise, quality, reliability, and support.
By carefully evaluating potential additive manufacturing partners against these criteria, automotive companies can build relationships with suppliers like Met3dp, who possess the necessary equipment, materials expertise, and commitment to quality required for producing high-performance, heat-resistant 3D printed exhaust tips.
Understanding Investment: Cost Factors and Lead Times for 3D Printed Exhaust Tips
One of the primary considerations for adopting any new manufacturing technology is understanding the associated costs and production timelines. Metal additive manufacturing for exhaust tips presents a different cost structure compared to traditional methods, influenced by a unique set of factors. Clear communication with your AM provider is essential to manage expectations.
Key Factors Influencing Cost:
- Material Type and Consumption:
- Стоимость порошка: The raw material cost varies significantly between alloys. Nickel-based superalloys like IN625 are considerably more expensive than stainless steels like 17-4PH.
- Part Volume & Weight: Larger or heavier parts consume more powder, directly increasing material costs.
- Support Structure Volume: Material used for support structures also adds to the cost, reinforcing the importance of DfAM to minimize supports.
- Переработка порошка: Efficient powder handling and recycling by the service provider can help mitigate costs, but some material degradation occurs over multiple uses.
- Machine Time (Print Time):
- Part Volume & Height: The larger the volume and taller the part (in the build orientation), the longer it takes to print, directly impacting machine utilization costs.
- Сложность: Highly intricate designs with many features or thin walls can sometimes increase print time due to complex scanning strategies required.
- Толщина слоя: Using thinner layers for finer detail or surface finish increases the number of layers and thus the print time.
- Nesting/Machine Utilization: Printing multiple parts simultaneously (nesting) spreads the machine setup and operation costs across more units, reducing the per-part cost. This is key for wholesale 3D printed parts production.
- Требования к постобработке:
- Complexity and Extent: This is often a significant cost driver. Extensive support removal, multi-step heat treatments (essential for IN625/17-4PH), precision CNC machining for tolerances, and high-end surface finishes (e.g., manual polishing) all add labor and machine time.
- Labor Intensity: Manual processes like support removal and polishing are labor-intensive and contribute significantly to the final cost.
- Design Complexity (Indirect Costs):
- While AM enables complexity, overly complex designs might require more intricate support structures, longer print times, and more challenging post-processing, indirectly increasing costs. DfAM helps balance complexity with manufacturability.
- Quality Assurance and Inspection:
- The level of inspection required (e.g., basic dimensional checks vs. CMM reports vs. NDT) impacts the cost. Higher assurance levels require more time and specialized equipment.
- Объем заказа:
- Prototypes vs. Production: One-off prototypes will have a higher per-part cost than small batch production runs due to setup costs being amortized over fewer parts.
- Скидки за объем: For larger quantities, discuss potential volume discounts or bulk additive manufacturing pricing structures with your supplier.
Typical Lead Times:
Lead times for 3D printed metal exhaust tips can vary significantly based on the factors above, particularly complexity and post-processing.
- Создание прототипов: For a single, moderately complex exhaust tip, lead times might range from 1 to 3 weeks. This includes printing, standard stress relief/heat treatment, basic support removal, and minimal finishing (e.g., bead blast).
- Small Batch Production (e.g., 10-50 units): Lead times could range from От 3 до 6 недель, depending on nesting efficiency, machine availability, and the extent of post-processing required for all units.
- Complex Finishing/Machining: If extensive manual polishing or multi-axis CNC machining is required, add several days to potentially 1-2 weeks to the lead time.
Lead Time Breakdown:
- Quoting & Setup: 1-3 дня
- Печать: 1-5 days (highly dependent on size, complexity, nesting)
- Cooling & De-powdering: 0.5-1 day
- Термообработка: 1-3 days (including furnace cycles)
- Support Removal & Basic Finishing: 1-3 дня
- Advanced Machining/Polishing: 2-10 days (if required)
- Quality Inspection & Shipping: 1-2 дня
It’s crucial to get specific lead time estimates from your provider based on your final design, material, quantity, and finishing requirements. Understanding the metal 3D printing cost automotive factors and realistic timelines allows for better project planning and budgeting.
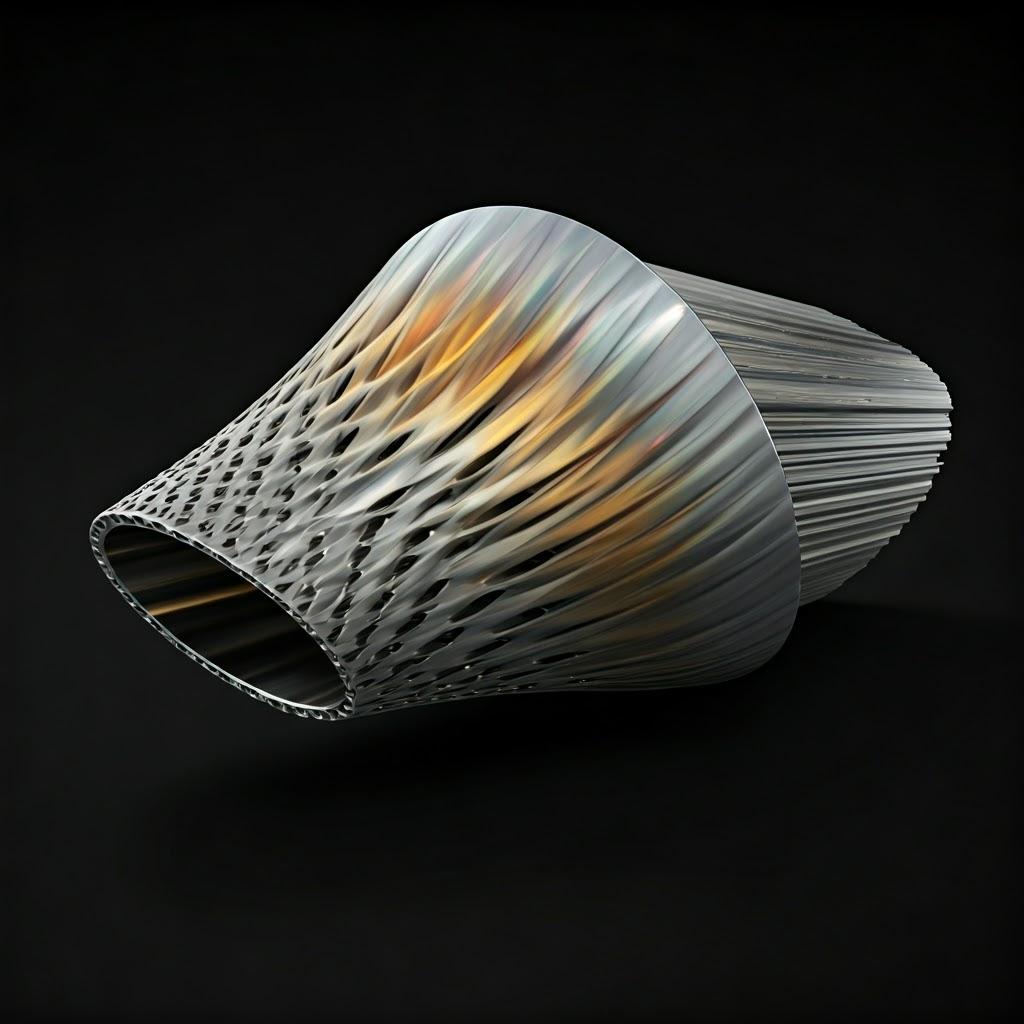
Frequently Asked Questions (FAQ) about 3D Printed Exhaust Tips
Here are answers to some common questions regarding the use of metal additive manufacturing for automotive exhaust tips:
Q1: How durable are 3D printed exhaust tips compared to traditional ones (e.g., CNC machined or cast)?
- A: When printed with appropriate materials like IN625 or 17-4PH and properly post-processed (especially heat treatment), 3D printed exhaust tips can be equally or even more durable than traditional counterparts, particularly in demanding high-temperature or corrosive environments. IN625, often used in AM, offers superior heat and corrosion resistance compared to commonly used standard stainless steels in conventional tips. The layer-by-layer fusion process creates fully dense parts with mechanical properties often meeting or exceeding cast or wrought equivalents, especially after treatments like HIP (if required). The key lies in correct material selection, process control during printing, and thorough post-processing, especially stress relief and aging heat treatments.
Q2: Can I get custom logos, intricate patterns, or complex internal structures 3D printed on exhaust tips?
- A:Абсолютно. This is one of the primary advantages of metal 3D printing. The technology excels at creating complex geometries that are difficult or impossible with traditional methods.
- Logos/Patterns: Custom logos, lettering, and complex surface textures can be directly incorporated into the CAD model and printed as part of the tip.
- Internal Structures: Intricate internal features, such as baffles for sound tuning, flow straighteners, or mesh structures, can be designed and printed within the exhaust tip, offering functional benefits beyond aesthetics.
- Свобода дизайна: This allows for truly unique, bespoke exhaust tip designs catering to specific branding, aesthetic, or performance goals. Remember to consider DfAM principles like powder removal for internal cavities.
Q3: What is the typical cost difference between 3D printing and CNC machining for a custom, complex exhaust tip?
- A: The cost comparison depends heavily on complexity and volume:
- Low Volume / High Complexity: For one-off prototypes or very small batches (e.g., 1-10 units) of a очень сложный exhaust tip design (e.g., with internal channels, organic shapes), 3D printing is often more cost-effective. This is because AM avoids the significant upfront costs of complex CNC programming, specialized fixtures, and potentially multiple setups required for machining intricate geometries from a solid block. Material waste is also lower with AM.
- Higher Volume / Simpler Geometry: Для simpler exhaust tip designs produced in larger quantities (e.g., hundreds or thousands), CNC machining or traditional fabrication/casting methods typically become more cost-effective due to economies of scale and faster cycle times per part once tooling/programming is established.
- Hybrid Approach: Often, a hybrid approach is optimal: 3D printing the main complex shape and then using CNC machining for critical interface dimensions and specific surface finishes offers a balance of design freedom and precision.
- Rule of Thumb: If the design complexity is high and volume is low, AM likely wins on cost and speed for the initial parts. If complexity is low and volume is high, traditional methods are usually cheaper per part. Always get quotes for both methods if feasible for your specific case.
Conclusion: Driving Forward with Additively Manufactured Exhaust Tips
Metal additive manufacturing is no longer a futuristic concept but a tangible, powerful tool transforming how automotive components like exhaust tips are designed, developed, and produced. By leveraging the capabilities of processes like L-PBF and SEBM, combined with advanced heat-resistant alloys such as Inconel 625 and 17-4PH stainless steel, the automotive industry can unlock unprecedented levels of design freedom, customization, and performance.
We’ve explored the journey from understanding the functional and aesthetic role of exhaust tips to recognizing the compelling advantages AM offers over traditional methods – namely, the ability to create complex geometries, facilitate rapid prototyping and customization, eliminate tooling costs, and utilize superior materials tailored for harsh exhaust environments. We’ve delved into the critical importance of Design for Additive Manufacturing (DfAM), the nuances of achievable tolerances and surface finishes, the essential nature of post-processing steps like heat treatment, and strategies for overcoming potential manufacturing challenges.
For OEMs seeking differentiation through unique styling and enhanced durability, for aftermarket suppliers aiming to provide cutting-edge customization options, and for performance tuning shops demanding the utmost in heat resistance and bespoke design, 3D printed exhaust tips represent a significant value proposition. The ability to craft lightweight, intricate, and highly durable components from materials perfectly suited to the application opens new avenues for innovation in vehicle aesthetics and performance signaling.
Choosing the right manufacturing partner is paramount to realizing these benefits. Look for providers with proven expertise in materials like IN625 and 17-4PH, robust quality systems, comprehensive post-processing capabilities, and a collaborative approach to design optimization.
Met3dp, headquartered in Qingdao, China, stands as a leading provider of comprehensive metal additive manufacturing solutions. Specializing in industry-leading 3D printing equipment, advanced powder manufacturing using gas atomization and PREP technologies, and application development services, Met3dp delivers high-quality metal powders (including TiNi, TiTa, TiAl, TiNbZr, CoCrMo, stainless steels, superalloys like IN625, and more) and cutting-edge systems. Our expertise enables the production of dense, high-quality metal parts with superior mechanical properties for demanding industries like automotive, aerospace, and medical.
Ready to explore how metal 3D printing can revolutionize your exhaust tip designs or other automotive components? Visit our website at https://met3dp.com/ to learn more about our capabilities, or contact our team today to discuss your specific project requirements and discover how Met3dp can power your organization’s additive manufacturing goals. Embrace the future of automotive component manufacturing with 3D printed exhaust tips.
Поделиться
MET3DP Technology Co., LTD - ведущий поставщик решений для аддитивного производства со штаб-квартирой в Циндао, Китай. Наша компания специализируется на производстве оборудования для 3D-печати и высокопроизводительных металлических порошков для промышленного применения.
Сделайте запрос, чтобы получить лучшую цену и индивидуальное решение для вашего бизнеса!
Похожие статьи
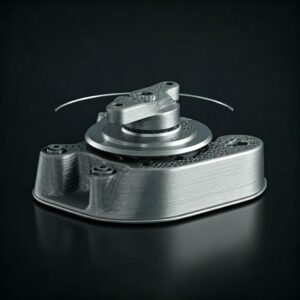
3D-печатные крепления для автомобильных радарных датчиков: Точность и производительность
Читать далее "О компании Met3DP
Последние обновления
Наш продукт
CONTACT US
Есть вопросы? Отправьте нам сообщение прямо сейчас! После получения Вашего сообщения мы всей командой выполним Ваш запрос.
Получите информацию о Metal3DP
Брошюра о продукции
Получить последние продукты и прайс-лист
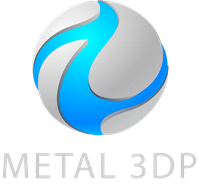
Металлические порошки для 3D-печати и аддитивного производства