Wire Routing Channels for Aerospace via Additive Manufacturing
Оглавление
Introduction: Revolutionizing Aerospace Wiring with 3D Printed Metal Channels
In the demanding world of aerospace engineering, every component matters. From the largest structural elements to the smallest connectors, reliability, weight, and performance are paramount. Among the critical systems ensuring the safe and efficient operation of aircraft, spacecraft, and satellites are the intricate networks of wiring harnesses. These harnesses, responsible for transmitting power and data, require robust protection and organization. This is where aerospace wiring channels, also known as wire routing channels or conduits, play a vital role. Traditionally manufactured using methods like CNC machining, sheet metal fabrication, or injection molding for polymer variants, these components face increasing challenges in meeting modern aerospace demands for complexity, customization, and weight reduction.
Входить аддитивное производство металлов (AM), или 3D-печать. This transformative technology is rapidly changing how aerospace components, including wiring channels, are designed and produced. By building parts layer by layer directly from digital models using high-performance metal powders, AM offers unprecedented design freedom, enables significant weight savings through optimized geometries, and allows for the consolidation of multiple parts into a single, complex component. For engineers and procurement managers in aerospace, leveraging metal AM for wiring channels means accessing solutions that are lighter, potentially stronger, customizable on-demand, and capable of integrating complex routing paths impossible to achieve with conventional methods.
The need for advanced manufacturing solutions is particularly acute in applications ranging from commercial airliners and defense aircraft to satellites and unmanned aerial vehicles (UAVs). Wiring channels in these environments must not only securely route and protect cables from abrasion, vibration, electromagnetic interference (EMI), and harsh environmental factors but also contribute to the overall goals of fuel efficiency and performance enhancement through minimal weight and optimized space utilization. Metal AM directly addresses these needs, offering materials like lightweight aluminum alloys (e.g., AlSi10Mg) and robust stainless steels (e.g., 316L) that meet stringent aerospace requirements.
As a pioneer in metal additive manufacturing solutions, Met3dp is at the forefront of this technological shift. Headquartered in Qingdao, China, Met3dp specializes in providing industry-leading metal 3D printing equipment, particularly Selective Electron Beam Melting (SEBM) systems, and high-performance metal powders tailored for critical industrial applications. Our expertise in powder metallurgy, employing advanced gas atomization and Plasma Rotating Electrode Process (PREP) technologies, ensures the production of highly spherical metal powders with excellent flowability and consistency – crucial factors for printing dense, high-quality aerospace components. With decades of collective experience, we partner with aerospace organizations to implement AM strategies, accelerating their journey towards next-generation manufacturing. This article explores the significant advantages and practical considerations of using metal 3D printing for aerospace wiring channels, highlighting why this technology is becoming indispensable for modern aerospace design and manufacturing.
Critical Applications: Where are 3D Printed Wiring Channels Used in Aerospace?
The adoption of metal additive manufacturing for wiring channels is driven by the unique demands of various aerospace applications. The ability to create highly customized, complex, and lightweight components makes 3D printed metal channels suitable for environments where traditional solutions fall short. These components are crucial for organizing, protecting, and managing the extensive electrical wiring systems found throughout aerospace vehicles.
Key Application Areas:
- Aircraft Cabins and Fuselage:
- Function: Routing power, data, and communication cables for lighting, in-flight entertainment systems, passenger service units (PSUs), and cabin management systems.
- AM Benefit: Custom-designed channels can perfectly follow the complex contours of the fuselage or cabin interior structures, maximizing space utilization and minimizing intrusion into passenger or cargo areas. Lightweight materials like AlSi10Mg significantly reduce overall aircraft weight, contributing to fuel efficiency. Design consolidation can integrate mounting points or connection features directly into the channel, reducing part count and assembly time.
- B2B Focus: Aerospace interior suppliers, aircraft manufacturers, and MRO (Maintenance, Repair, Overhaul) providers seeking optimized, lightweight cabin solutions.
- Avionics Bays and Equipment Racks:
- Function: Organizing dense bundles of wiring connecting various avionics systems (navigation, communication, flight control). Protection against EMI and vibration is critical.
- AM Benefit: Metal AM allows for the creation of intricate channel geometries with integrated shielding features. The inherent rigidity of printed metal parts provides excellent vibration damping. Complex layouts can be accommodated precisely, simplifying installation and maintenance access. Materials like 316L offer durability and shielding properties.
- B2B Focus: Avionics system integrators, defense contractors, and aircraft manufacturers requiring high-density, reliable wiring solutions for mission-critical systems.
- Engine Compartments and Nacelles:
- Function: Protecting wiring from extreme temperatures, fluids (fuel, oil, hydraulic fluid), and intense vibration near the engine.
- AM Benefit: High-performance metal alloys, printable via AM, offer superior heat resistance and chemical inertness compared to polymers. 316L stainless steel, for instance, provides excellent corrosion resistance and durability in harsh engine environments. Complex routing paths can navigate around engine components effectively.
- B2B Focus: Engine manufacturers, nacelle producers, and aerospace suppliers needing robust, heat-resistant wiring management solutions.
- Спутники и космические аппараты:
- Function: Managing wiring for power distribution, telemetry, command systems, and payloads within extremely tight space and weight constraints. Components must withstand launch stresses (vibration, G-forces) and the space environment (radiation, thermal cycling).
- AM Benefit: Weight reduction is paramount for launch cost savings. Metal AM enables topology optimization to create ultra-lightweight yet strong channel structures. Custom shapes can integrate seamlessly with satellite bus structures. Materials are selected for space-grade properties, including low outgassing. Part consolidation simplifies assembly, crucial for complex satellite builds.
- B2B Focus: Satellite manufacturers, space agencies, payload developers, and subsystem suppliers looking for mass-optimized, highly reliable components.
- Unmanned Aerial Vehicles (UAVs) / Drones:
- Function: Routing power and data cables for sensors, actuators, communication links, and flight controllers within compact airframes. Weight and durability are key considerations.
- AM Benefit: Rapid prototyping and production of custom channels tailored to specific UAV designs. Lightweighting is critical for endurance and payload capacity. AM allows for integrated features and complex shapes necessary for small, densely packed airframes.
- B2B Focus: UAV manufacturers, drone component suppliers, and defense contractors developing bespoke aerial platforms.
- Landing Gear Systems:
- Function: Protecting hydraulic lines and sensor wiring within the landing gear bays and struts, areas subjected to high impact loads, vibration, and potential debris.
- AM Benefit: High-strength metal alloys can provide robust protection. Complex channel designs can follow the intricate geometry of landing gear mechanisms, ensuring secure routing and preventing chafing or damage during operation and retraction/deployment cycles.
- B2B Focus: Landing gear manufacturers, hydraulic system suppliers, and aircraft MRO providers.
Table: Application Areas and AM Benefits for Wiring Channels
Область применения | Ключевые вызовы | Metal AM Advantages | Target B2B Audience |
---|---|---|---|
Aircraft Cabins/Fuselage | Weight, Space Optimization, Customization | Lightweighting (AlSi10Mg), Complex Contours, Part Consolidation, Rapid Customization | Aircraft OEMs, Interior Suppliers, MRO Providers |
Avionics Bays | Density, EMI Shielding, Vibration, Reliability | Intricate Geometries, Integrated Shielding, Rigidity, Custom Layouts | Avionics Integrators, Defense Contractors, OEMs |
Engine Compartments | High Temperature, Fluids, Vibration | Heat Resistance (316L, Superalloys), Chemical Inertness, Durability, Complex Routing | Engine/Nacelle Manufacturers, Aerospace Suppliers |
Satellites/Spacecraft | Extreme Weight Constraints, Space, Reliability | Topology Optimization (Ultra-Lightweight), Custom Integration, Part Consolidation, Space-Grade Materials | Satellite Manufacturers, Space Agencies, Payload Developers |
UAVs/Drones | Weight, Compactness, Durability, Customization | Rapid Prototyping/Production, Lightweighting, Integrated Features, Complex Shapes | UAV Manufacturers, Component Suppliers, Defense Contractors |
Системы шасси | Impact Loads, Vibration, Debris, Complex Geometry | High Strength, Robust Protection, Custom Routing along Mechanisms, Durability | Landing Gear Manufacturers, Hydraulic Suppliers, MRO |
Export to Sheets
By understanding these diverse applications, aerospace engineers and procurement managers can identify opportunities where metal 3D printed wiring channels offer tangible benefits over conventional counterparts, driving innovation and efficiency in aerospace design and manufacturing. Partnering with an experienced металлическая 3D-печать provider like Met3dp ensures access to the right materials, processes, and expertise to realize these advantages.
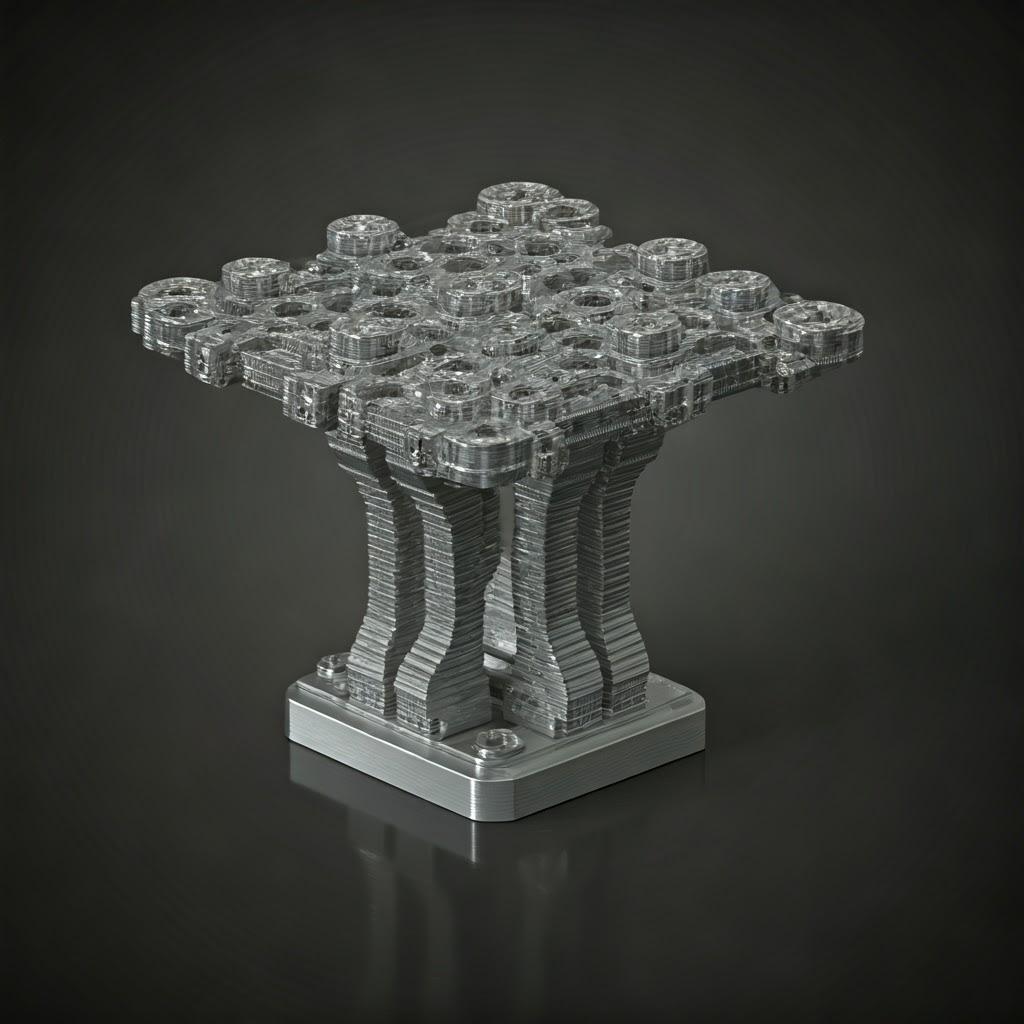
The Additive Advantage: Why Choose Metal 3D Printing for Wiring Channels?
While traditional manufacturing methods like CNC machining from billet, sheet metal bending, or extrusion have long served the aerospace industry for creating wiring channels, they often come with limitations, particularly when faced with the increasing complexity and performance demands of modern aerospace platforms. Metal additive manufacturing presents a compelling alternative, offering a suite of advantages that directly address these limitations and unlock new possibilities in design and production.
1. Unmatched Design Freedom and Complexity:
- Traditional Limits: Machining is subtractive, making intricate internal features or complex curves difficult and costly. Sheet metal forming is limited in the shapes it can produce, often requiring multiple parts and fasteners.
- AM Advantage: AM builds parts layer-by-layer, enabling the creation of highly complex geometries, including internal channels, organic curves, and varying wall thicknesses within a single, monolithic part. Wiring channels can be designed to follow the most efficient paths, perfectly conforming to surrounding structures, even in tightly packed areas like avionics bays or engine nacelles. This freedom allows engineers to route wiring more effectively, reduce stress points on cables, and optimize for space.
2. Significant Weight Reduction through Optimization:
- Traditional Limits: Components are often designed with uniform thickness or are limited by subtractive process constraints, leading to over-engineered, heavier parts.
- AM Advantage: AM facilitates advanced design techniques like оптимизация топологии и generative design. Software algorithms can determine the most efficient distribution of material to meet specific load requirements, removing unnecessary mass while maintaining structural integrity. This can lead to wiring channels that are significantly lighter (often 20-50% or more) than their traditionally manufactured counterparts, directly contributing to fuel savings or increased payload capacity – critical metrics in aerospace. Lightweight alloys like AlSi10Mg are ideal candidates for this approach.
3. Part Consolidation and Reduced Assembly Time:
- Traditional Limits: Complex channel assemblies often require multiple individual components (brackets, sections, fasteners) to be manufactured and then assembled, increasing complexity, potential points of failure, and labor costs.
- AM Advantage: The design freedom of AM allows engineers to consolidate multiple functional elements into a single printed part. For example, mounting brackets, connector housings, or access points can be integrated directly into the wiring channel structure. This drastically reduces part count, simplifies the supply chain, minimizes assembly time and effort, and enhances the overall reliability by eliminating joints and fasteners.
4. Rapid Prototyping and Iteration:
- Traditional Limits: Creating prototypes using traditional methods often requires expensive tooling (molds, dies) or significant machining time, making design iterations slow and costly.
- AM Advantage: AM is a tool-less process. Designs can be sent directly from CAD software to the printer, allowing for the creation of functional prototypes in metal within days, not weeks or months. This accelerates the design validation cycle, enabling engineers to test multiple iterations quickly and affordably, leading to a more optimized final product. Met3dp’s capabilities allow for swift production of prototypes for fit and function checks.
5. On-Demand Production and Reduced Inventory:
- Traditional Limits: Economies of scale often necessitate large production runs, leading to significant inventory holding costs, especially for spares or low-volume custom parts. Tooling must be stored and maintained.
- AM Advantage: AM enables economically viable production of small batches or even single, unique parts. Wiring channels can be printed on-demand, directly from digital files. This “digital inventory” approach minimizes warehousing costs, reduces lead times for replacement parts (digital spares), and allows for easy customization for specific aircraft configurations or repair scenarios. This is ideal for MRO providers and manufacturers dealing with diverse fleets.
6. Material Versatility:
- Traditional Limits: Material choice might be constrained by the manufacturing process (e.g., formability for sheet metal, machinability for CNC).
- AM Advantage: Metal AM processes, such as Selective Laser Melting (SLM) / Laser Powder Bed Fusion (LPBF) and Selective Electron Beam Melting (SEBM), can work with a growing range of high-performance aerospace alloys, including lightweight aluminum (AlSi10Mg), corrosion-resistant stainless steels (316L), high-strength titanium alloys, and heat-resistant superalloys. This allows engineers to select the optimal material for the specific application requirements (e.g., temperature, strength, weight). Met3dp offers a diverse portfolio of металлические порошки suitable for these demanding applications.
Table: Metal AM vs. Traditional Manufacturing for Aerospace Wiring Channels
Характеристика | Аддитивное производство металлов (AM) | Traditional Methods (CNC Machining, Sheet Metal) | Aerospace Impact |
---|---|---|---|
Сложность конструкции | High; complex internal features, organic shapes, conformal designs | Moderate to Low; limited by tool access, forming constraints | Optimized routing, space utilization, integration with complex structures |
Снижение веса | High potential via topology optimization, lightweight alloys (AlSi10Mg) | Limited; often uniform thickness, subtractive constraints | Significant fuel savings, increased payload capacity |
Консолидация частей | Excellent; integration of brackets, fasteners, features | Low; often requires multiple parts and assembly | Reduced part count, assembly time, weight, and potential failure points |
Prototyping Speed | Fast (days); tool-less process | Slow (weeks/months); requires tooling or extensive machining setup | Accelerated design validation, faster time-to-market |
Объем производства | Ideal for low-to-medium volume, customization, on-demand | Efficient for high volume, less economical for small batches/custom parts | Reduced inventory, digital spares, support for diverse/aging fleets, customization |
Выбор материала | Growing range of aerospace alloys (Al, Ti, SS, Ni-based) | Dependent on specific process (machinability, formability) | Optimal material selection for specific performance requirements |
Lead Time (Low Vol) | Короче | Longer (due to setup/tooling) | Faster access to spares and prototypes |
Export to Sheets
Choosing metal AM for aerospace wiring channels is not just about adopting a new manufacturing technique; it’s about embracing a paradigm shift towards more efficient, optimized, and capable aerospace systems. Companies like Met3dp provide the necessary technology and expertise to harness these advantages effectively.
Recommended Materials and Why They Matter: AlSi10Mg and 316L for Optimal Performance
Selecting the right material is fundamental to the success of any aerospace component, and 3D printed wiring channels are no exception. The material dictates the part’s mechanical properties, weight, environmental resistance, and ultimately, its suitability for the demanding conditions of flight. While metal AM offers a broadening spectrum of alloys, two materials stand out as particularly well-suited and commonly used for aerospace wiring channels: AlSi10Mg (an aluminum alloy) и 316L (a stainless steel). Understanding their properties is key for engineers and procurement specialists making material decisions.
1. AlSi10Mg (Aluminum-Silicon-Magnesium Alloy): The Lightweight Champion
- Аннотация: AlSi10Mg is a widely used cast aluminum alloy that has become a staple in metal additive manufacturing, particularly via Laser Powder Bed Fusion (LPBF/SLM). It’s known for its excellent combination of low density, good mechanical properties (strength and hardness), weldability, and thermal conductivity.
- Key Properties & Benefits for Wiring Channels:
- Low Density (approx. 2.67 g/cm³): This is arguably its most significant advantage in aerospace. Using AlSi10Mg dramatically reduces the weight of wiring channels compared to steel or even titanium alloys, directly contributing to fuel efficiency or increased payload capacity.
- Хорошее соотношение прочности и веса: While not as strong as steel or titanium, its strength is sufficient for many structural and semi-structural applications like wiring channels, especially when designs are optimized using DfAM principles.
- Отличная теплопроводность: Helps dissipate heat generated by electrical wiring or from the surrounding environment, which can be beneficial in certain applications.
- Хорошая коррозионная стойкость: Offers adequate resistance to atmospheric corrosion, although surface treatments (like anodizing) might be applied for enhanced protection in specific environments.
- Возможность печати: It processes well with LPBF, allowing for fine details and relatively good surface finishes as-printed.
- Typical Aerospace Applications: Ideal for weight-critical applications such as cabin interiors, fuselage structures, satellite components, and UAV airframes where extreme temperatures or corrosion are not the primary concerns.
- Met3dp Context: Sourcing high-quality AlSi10Mg powder with consistent particle size distribution and sphericity is crucial for achieving reliable mechanical properties and defect-free prints. Met3dp’s advanced powder production technologies ensure powders meet these stringent aerospace quality requirements.
2. 316L Stainless Steel: The Robust Workhorse
- Аннотация: 316L is an austenitic chromium-nickel stainless steel containing molybdenum. It is renowned for its outstanding corrosion resistance, good strength and ductility (even at cryogenic temperatures), and excellent weldability and formability. It’s a common choice in demanding environments.
- Key Properties & Benefits for Wiring Channels:
- Отличная коррозионная стойкость: Superior resistance to a wide range of corrosive media, including atmospheric corrosion, moisture, de-icing salts, and various chemicals. This makes it ideal for channels exposed to harsh conditions, such as those near galleys, lavatories, cargo bays, or external environments.
- Good Strength and Durability: Offers higher strength and toughness compared to AlSi10Mg, providing robust protection for wiring against impact and vibration. Maintains good mechanical properties over a reasonably wide temperature range.
- Biocompatibility (for ‘L’ grade): While less relevant for wiring channels, the ‘L’ denotes low carbon content, improving resistance to sensitization during welding or thermal treatments and contributing to its biocompatibility profile in medical applications (demonstrating material quality).
- Возможность печати: 316L is readily processable using both LPBF and SEBM techniques, yielding dense parts with good mechanical properties.
- Typical Aerospace Applications: Suitable for engine compartments (moderate temperatures), landing gear bays, areas exposed to moisture or corrosive fluids, external conduits, and applications requiring higher strength or durability than aluminum can provide.
- Met3dp Context: Met3dp manufactures high-quality 316L powders optimized for additive manufacturing processes like SEBM and LPBF. Our advanced powder making system guarantees the high sphericity and flowability needed for producing dense, reliable 316L components suitable for demanding aerospace use cases. We also offer expertise in processing parameters to achieve optimal material properties.
Table: Comparison of AlSi10Mg vs. 316L for Aerospace Wiring Channels
Недвижимость | AlSi10Mg (алюминиевый сплав) | Нержавеющая сталь 316L | Key Consideration for Wiring Channels |
---|---|---|---|
Плотность | Low (~2.67 g/cm³) | High (~8.0 g/cm³) | Вес: AlSi10Mg offers significant weight savings. |
Прочность | Умеренный | Good to High | Долговечность: 316L provides higher strength and impact resistance. |
Прочность к весу | Очень хорошо | Умеренный | Эффективность: AlSi10Mg excels where weight is the primary driver. |
Коррозионная стойкость | Good (Atmospheric) | Excellent (Wide range, including chlorides) | Окружающая среда: 316L is superior for harsh or corrosive conditions. |
Температурная стойкость | Moderate (Strength decreases above ~120°C) | Good (Up to ~500°C+, depending on specific criteria) | High Temp Zones: 316L is better suited for engine proximity (within limits). |
Теплопроводность | Высокая | Низкий | Heat Dissipation: AlSi10Mg dissipates heat more effectively. |
Cost (Powder) | Generally Lower | Generally Higher | Бюджет: AlSi10Mg can be more cost-effective from a raw material perspective. |
Printability (LPBF) | Отличный | Хороший | Both are well-established AM materials. |
Printability (SEBM) | Not Typically Used | Хороший | SEBM often preferred for specific applications needing reduced residual stress. |
Основная выгода | Легкий | Corrosion Resistance & Durability | Match benefit to primary application requirement. |
Export to Sheets
Making the Choice:
The selection between AlSi10Mg and 316L (or potentially other aerospace alloys like Ti6Al4V for extreme requirements) depends heavily on the specific application:
- Выберите AlSi10Mg когда weight saving is the absolute priority, and the operating environment is relatively benign (e.g., cabin interiors, protected fuselage areas, satellites).
- Выберите 316L когда corrosion resistance, durability, or operation in harsher environments (moisture, chemicals, moderate heat) are key requirements, and the higher weight is acceptable (e.g., landing gear bays, engine areas, galleys).
Consulting with material specialists and experienced AM service providers like Met3dp is crucial. We can help evaluate the application requirements, advise on the optimal material choice, and ensure the selected high-performance metal powder meets the stringent quality standards demanded by the aerospace industry. Our comprehensive solutions span advanced printers and premium powders to application development support.
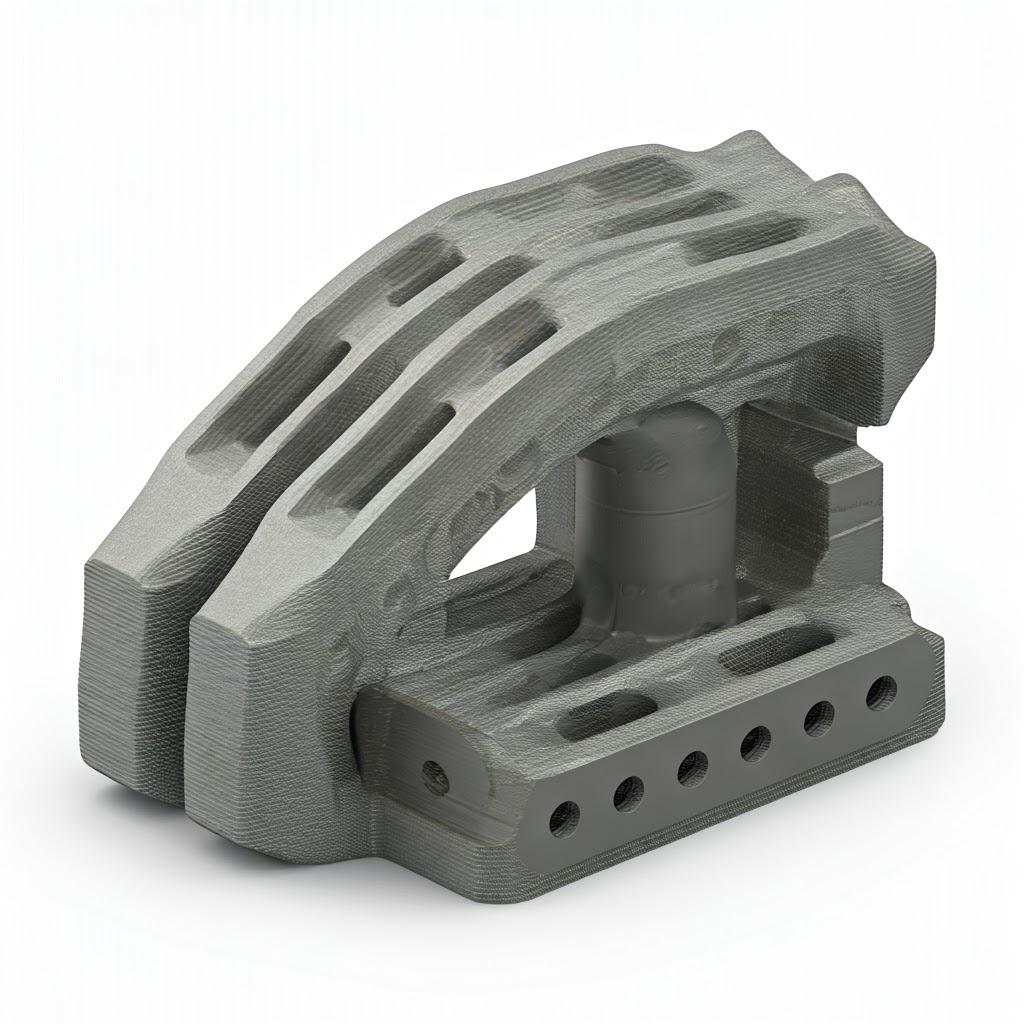
Design for Additive Manufacturing (DfAM): Optimizing Wiring Channel Geometry
Transitioning from traditional manufacturing to metal additive manufacturing (AM) for aerospace wiring channels isn’t just about swapping production methods; it requires a fundamental shift in design philosophy. Designing для Additive Manufacturing (DfAM) is crucial to fully leverage the technology’s benefits – particularly complexity, lightweighting, and consolidation – while ensuring manufacturability and performance. Simply printing a design intended for CNC machining will likely be suboptimal and may even fail. Optimizing wiring channel geometry for AM involves considering the unique layer-by-layer build process.
Key DfAM Principles for Metal AM Wiring Channels:
- Optimize Channel Paths and Geometry:
- Freedom: Leverage AM’s ability to create smooth, organic curves and complex paths. Route channels to follow the most direct or space-efficient path, conforming precisely to aircraft structures or avoiding obstacles.
- Avoid Sharp Corners: Design internal channel paths with generous radii instead of sharp 90-degree bends. This improves flow for wiring installation, reduces stress concentrations in the part, and aids in powder removal after printing.
- Variable Cross-Sections: Unlike extrusion, AM allows channel cross-sections to vary along the length, adapting to different wiring bundle sizes or space constraints.
- Minimum Wall Thickness and Feature Size:
- Process Limits: AM processes have limitations on the minimum printable wall thickness and feature size (dependent on material, machine, parameters). Typically, for robustness, wall thicknesses for channels might range from 0.8mm to 1.5mm, but thinner sections (down to ~0.4-0.5mm) may be achievable for non-structural elements.
- Design Consideration: Ensure walls are thick enough for structural integrity, handling, and to prevent warping during printing and heat treatment. Consult with your AM provider, like Met3dp, for specific guidelines based on their equipment (e.g., SEBM or LPBF) and materials (AlSi10Mg, 316L).
- Self-Supporting Angles and Overhangs:
- Поддерживающие структуры: Metal AM requires support structures for overhanging features typically below a certain angle (often around 45 degrees from the horizontal plane). These supports prevent collapse during printing but must be removed afterward, adding cost and potentially affecting surface finish.
- Design Strategy: Design channels and features with self-supporting angles (greater than 45 degrees) wherever possible. Orient the part strategically on the build plate to minimize the need for supports, especially in hard-to-reach internal channel areas. Consider diamond or teardrop shapes for horizontal internal passages instead of circles to make them self-supporting.
- Integration of Functional Features:
- Консолидация частей: This is a major AM advantage. Design mounting points (bosses, flanges, holes), cable tie/clamp features, connector interfaces, or even small brackets directly into the channel structure.
- Преимущества: Reduces part count, eliminates fasteners, simplifies assembly, lowers weight, and improves overall system reliability. Ensure integrated features are also designed with AM principles (e.g., avoiding unsupported overhangs).
- Topology Optimization and Lightweighting:
- Structural Efficiency: For channels that bear some load or require high stiffness, use topology optimization software. This software removes material from non-critical areas, leaving behind an organic, load-bearing structure that is significantly lighter but meets performance requirements.
- Решетчатые структуры: Incorporate internal lattice or honeycomb structures within thicker sections of the channel walls for lightweighting while maintaining stiffness and strength. This is particularly effective with materials like AlSi10Mg.
- Design for Powder Removal:
- Critical Consideration: Trapped powder inside long, narrow, or complex internal channels is a significant challenge in AM. It adds weight and can be a source of contamination or failure.
- Design Strategies:
- Include strategically placed drain/access holes (which can potentially be plugged or integrated into the design later).
- Design channels with smooth internal surfaces and gradual bends.
- Consider designing channels in sections that are printed separately and joined later (e.g., laser welding), although this negates some consolidation benefits.
- Ensure internal passages are large enough for effective cleaning procedures (e.g., compressed air, vibration).
- Orientation and Anisotropy:
- Build Direction: The orientation of the part on the build plate affects surface finish, the need for supports, and potentially mechanical properties (anisotropy).
- Collaboration: Work with your AM service provider to determine the optimal build orientation considering trade-offs between surface finish on critical features, support minimization, and desired material properties in specific directions. Understanding different способы печати like SEBM and LPBF is key here, as they can have different implications.
Met3dp’s Role: Applying DfAM principles effectively requires expertise. Met3dp provides comprehensive solutions, including application development services. Our engineers can collaborate with your team to optimize wiring channel designs specifically for our advanced SEBM and LPBF systems, ensuring manufacturability, performance, and cost-effectiveness using our high-quality AlSi10Mg and 316L powders.
Table: DfAM Considerations for Wiring Channels
DfAM Principle | Design Action | Выгода | Challenge Mitigation |
---|---|---|---|
Optimized Paths | Use smooth curves, conformal routing, varying cross-sections | Efficient space use, reduced wire stress, optimized flow | N/A (Leveraging AM strength) |
Толщина стенки | Maintain minimum viable thickness (e.g., >0.8mm), consult provider | Structural integrity, printability, weight optimization | Avoid warping, ensure handling robustness |
Self-Supporting Angles | Design overhangs >45°, use teardrop/diamond internal shapes, strategic orientation | Minimize support needs, reduce post-processing cost & time | Easier cleaning, better internal surface finish |
Feature Integration | Combine mounts, clamps, connectors into single part design | Part count reduction, simplified assembly, lower weight, reliability | Ensure integrated features are AM-friendly |
Topology Optimization | Use software to remove non-essential material, incorporate lattices | Significant weight reduction, high stiffness-to-weight ratio | Requires FEA expertise, potentially complex geometry |
Удаление порошка | Include access holes, smooth internal paths, consider sectioning | Ensure complete powder evacuation, prevent contamination, reduce weight | Critical for functional internal channels |
Orientation Strategy | Collaborate with AM provider based on critical features & properties | Balance surface finish, support needs, mechanical properties | Manage anisotropy, optimize build time/cost |
Export to Sheets
By embracing DfAM, aerospace companies can unlock the full potential of metal 3D printing for creating next-generation wiring channels that are lighter, more integrated, and better performing than ever before.
Precision Matters: Achieving Tight Tolerances and Surface Finish in AM Wiring Channels
While metal additive manufacturing offers incredible design freedom, understanding its capabilities regarding dimensional accuracy, tolerances, and surface finish is crucial for producing functional aerospace components like wiring channels. Engineers and procurement managers need realistic expectations about what can be achieved directly from the printer and what might require secondary post-processing steps.
Dimensional Accuracy and Tolerances:
- General Capabilities: Metal AM processes like Laser Powder Bed Fusion (LPBF) and Selective Electron Beam Melting (SEBM) can achieve reasonably good dimensional accuracy. As a general guideline, typical tolerances for as-printed metal parts often fall within:
- ±0.1 mm to ±0.3 mm for smaller features (e.g., up to 50-100 mm).
- ±0.1% to ±0.3% of the nominal dimension for larger parts.
- This often aligns with ISO 2768 – class m (medium) or sometimes class f (fine) for general tolerances.
- Factors Influencing Accuracy:
- Printer Calibration: Well-maintained and precisely calibrated machines, like the industry-leading systems offered by Met3dp, are fundamental.
- Параметры процесса: Laser/electron beam power, scan speed, layer thickness, and gas flow (LPBF) significantly impact accuracy.
- Материал: Different materials (e.g., AlSi10Mg vs. 316L) exhibit different shrinkage and thermal behavior.
- Thermal Stress: Residual stresses built up during printing can cause warping and distortion, affecting final dimensions. Stress relief heat treatment is often required.
- Геометрия и ориентация деталей: Complex shapes and build orientation influence heat buildup and potential distortion.
- Achieving Tighter Tolerances: For critical interfaces, mounting points, or connector fits requiring tolerances tighter than the standard AM process capability (e.g., < ±0.1 mm), post-process CNC machining is typically employed. Specific features identified in the design phase can be printed with extra stock material (‘machining allowance’) and then machined to final, precise dimensions.
Обработка поверхности (шероховатость):
- As-Printed Surface: The surface finish of as-printed metal AM parts is inherently rougher than machined surfaces due to the layer-by-layer process and partially melted powder particles adhering to the surface.
- Typical as-printed surface roughness (Ra) values range from 6 µm to 25 µm (240 µin to 1000 µin), depending on the material, process (SEBM often yields slightly rougher surfaces than LPBF), parameters, and surface orientation (upward-facing surfaces are generally smoother than downward-facing or vertical walls).
- Internal Channels: Achieving a smooth surface finish inside complex wiring channels can be particularly challenging due to limited access for post-processing. This is a key DfAM consideration – design channels for accessibility if internal smoothness is critical.
- Улучшение качества поверхности: Various post-processing techniques can significantly improve the surface finish:
- Bead Blasting / Sand Blasting: Provides a uniform matte finish, removing loose powder. Typical Ra: 5-10 µm.
- Tumbling / Vibratory Finishing: Uses abrasive media to smooth surfaces, especially effective for external features. Ra can be improved significantly depending on media and time.
- Electropolishing: An electrochemical process that removes a thin layer of material, resulting in a very smooth, bright, and clean surface. Excellent for 316L. Can achieve Ra < 1 µm.
- Abrasive Flow Machining (AFM): Pushes an abrasive putty through internal channels to smooth them. Effective but specialized.
- Manual Polishing: For achieving mirror finishes on specific external areas, but labor-intensive.
- Specification: Surface finish requirements should be clearly defined on engineering drawings, specifying the Ra value and the areas where it applies (e.g., external surfaces, critical internal paths).
Table: Tolerances and Surface Finish in Metal AM (AlSi10Mg & 316L)
Параметр | As-Printed Capability | Post-Processing Potential | Key Considerations for Wiring Channels |
---|---|---|---|
Tolerance (General) | ±0.1 to ±0.3 mm (ISO 2768-m/f typical) | < ±0.05 mm (via CNC Machining) | Identify critical interfaces requiring tighter tolerances early in design. |
Surface Finish (Ra) | 6 – 25 µm (LPBF generally smoother) | < 1 µm – 10 µm (Polishing, Blasting, etc.) | Specify required Ra for external/internal surfaces; design for access. |
Internal Channels | Rougher finish, harder to process | Challenging; AFM or Electropolishing possible | Design for powder removal and flow; consider if internal Ra is critical. |
Влияющие факторы | Machine, Material, Parameters, Thermal | Method, Media, Time | Collaborate with AM provider (like Met3dp) for realistic expectations. |
Export to Sheets
Achieving the required precision and surface finish for aerospace wiring channels is a combination of leveraging the inherent capabilities of advanced AM systems and implementing appropriate DfAM strategies and post-processing steps. Met3dp’s focus on industry-leading print accuracy and reliability, combined with our material expertise, provides a solid foundation for manufacturing high-quality aerospace components.
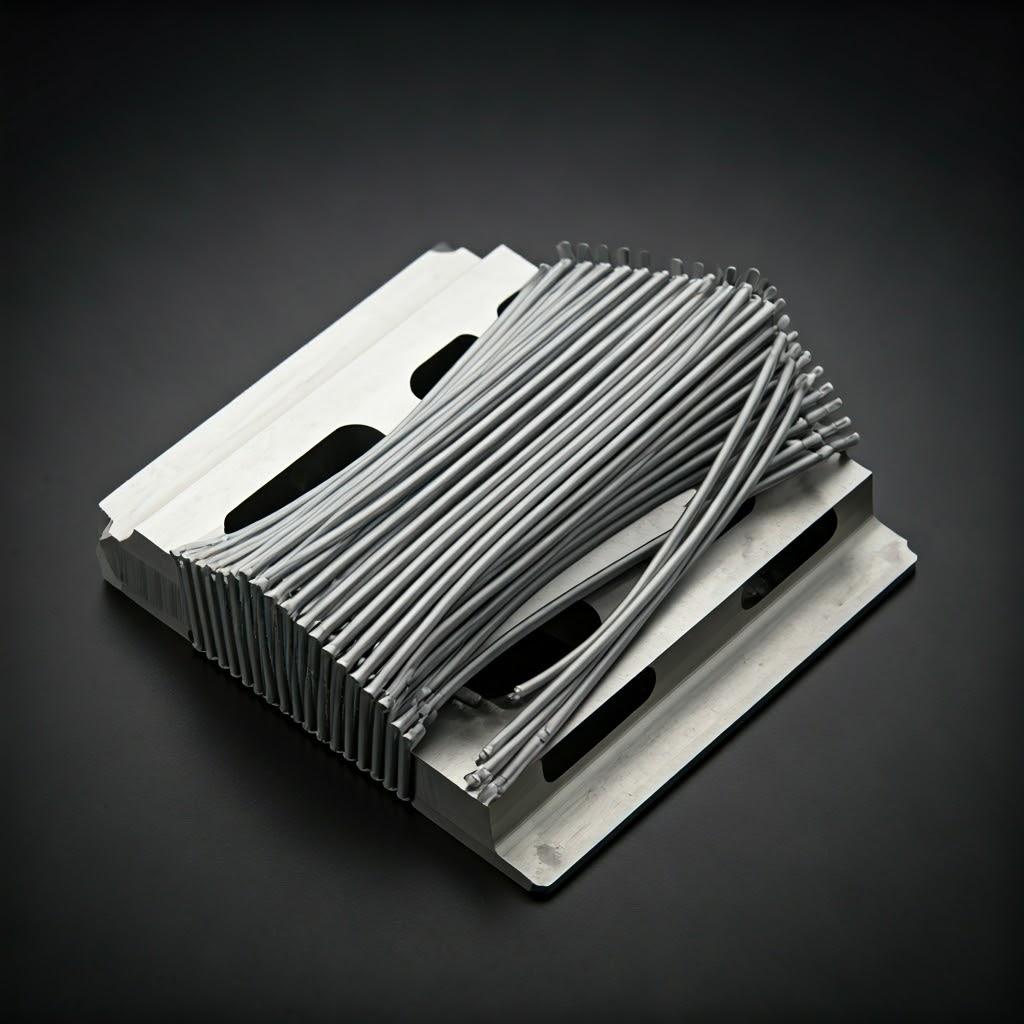
Beyond the Print: Essential Post-Processing for Aerospace Wiring Channels
Creating a metal wiring channel using additive manufacturing doesn’t end when the printer stops. The “green” part, fresh off the build plate, requires several crucial post-processing steps to transform it into a functional, flight-ready aerospace component. These steps are essential for achieving the desired mechanical properties, dimensional accuracy, surface finish, and overall quality required for aerospace applications. Understanding these processes is vital for project planning, costing, and lead time estimation.
Common Post-Processing Stages for AM Metal Parts:
- Stress Relief / Heat Treatment:
- Цель: The rapid heating and cooling cycles during AM build up internal stresses within the part. Heat treatment (typically performed in a vacuum or inert atmosphere furnace) at specific temperatures relieves these stresses, preventing distortion or cracking later and stabilizing the material’s microstructure. Specific cycles depend on the material (AlSi10Mg and 316L have different requirements). For some materials and applications, further heat treatments (like aging for AlSi10Mg or solution annealing/aging for other alloys) may be needed to achieve final desired mechanical properties (e.g., increased strength or ductility).
- Necessity: Almost always required for aerospace metal AM parts to ensure dimensional stability and performance.
- Удаление порошка:
- Цель: Removing all unfused metal powder from the part, especially from internal channels and complex geometries. Trapped powder adds weight, can be a source of contamination, and may sinter during heat treatment, blocking channels.
- Методы: Compressed air blow-off, vibration, ultrasonic cleaning, bead blasting. Access holes designed during the DfAM phase are critical here. Requires meticulous inspection.
- Necessity: Absolutely critical, especially for internal passages of wiring channels.
- Part Removal from Build Plate:
- Цель: Separating the printed part(s) from the base plate they were built upon. Parts are often strongly bonded or welded to the plate.
- Методы: Wire Electrical Discharge Machining (Wire EDM) or band sawing are common methods. Care must be taken not to damage the part.
- Necessity: Required for all AM processes using build plates.
- Демонтаж опорной конструкции:
- Цель: Removing the temporary structures printed to support overhanging features during the build.
- Методы: Supports are typically designed with weaker connection points. They can often be removed manually (pliers, cutters) or require machining (milling, grinding, EDM). Careful removal is needed to avoid damaging the part surface.
- Necessity: Required for any part printed with support structures. DfAM aims to minimize this.
- Hot Isostatic Pressing (HIPing) – Optional but Recommended for Critical Parts:
- Цель: HIPing involves subjecting the part to high temperature and high inert gas pressure simultaneously. This process closes any residual internal micro-porosity, improving fatigue life, ductility, and overall material integrity.
- Necessity: Often mandated for critical aerospace components, especially rotating parts or those subjected to high fatigue cycles. It significantly enhances material properties and consistency, providing an extra layer of quality assurance. Recommended for high-performance wiring channels.
- CNC Machining:
- Цель: To achieve tight tolerances on critical features (mating surfaces, interfaces, hole diameters) that exceed the as-printed accuracy. Also used to improve surface finish on specific areas or remove support witnesses.
- Методы: Milling, turning, drilling, tapping. Requires careful setup and potentially custom fixtures.
- Necessity: Frequently required for functional interfaces and achieving final dimensional specifications on drawings.
- Отделка поверхности:
- Цель: To achieve the desired surface roughness (Ra), cosmetic appearance, or prepare the surface for subsequent coatings.
- Методы: As discussed previously: bead blasting (common for a uniform matte finish), tumbling, electropolishing (excellent for 316L smoothness and cleanability), manual polishing, micro-machining, etc.
- Necessity: Depends on application requirements – cosmetic, functional (e.g., reducing friction for wire pulling), or pre-treatment for coating.
- Cleaning and Inspection:
- Цель: Final cleaning to remove any residues from machining or finishing processes. Rigorous inspection ensures the part meets all specifications.
- Методы: Visual inspection, dimensional checks (CMM – Coordinate Measuring Machine), Non-Destructive Testing (NDT) like CT scanning (especially valuable for checking internal channel clearance and integrity), penetrant testing, or radiographic testing may be required depending on criticality.
- Necessity: Mandatory for all aerospace components to ensure quality and safety.
- Surface Treatments / Coatings (Optional):
- Цель: Enhance specific properties like corrosion resistance, wear resistance, or electrical insulation.
- Методы: Anodizing (common for AlSi10Mg corrosion/wear resistance), passivation (for 316L to enhance corrosion resistance), painting, powder coating, or specialized aerospace coatings.
- Necessity: Application-specific based on environmental exposure and functional requirements.
Workflow Integration: These steps are often performed sequentially, and the specific workflow will depend on the part complexity, material, and final requirements. Efficiently managing this post-processing chain is key to controlling overall lead time and cost. Working with a full-service provider like Met3dp, who understands the entire металлическая 3D-печать workflow from powder to finished part, simplifies this process.
Navigating Challenges: Avoiding Pitfalls in Metal AM for Wiring Channels
While metal additive manufacturing offers transformative potential for aerospace wiring channels, it’s not without its challenges. Awareness of these potential issues allows engineers and manufacturers to implement mitigation strategies early in the design and production planning stages, ensuring successful outcomes.
Common Challenges and Mitigation Strategies:
- Warping and Distortion:
- Cause: Uneven heating and cooling during the layer-by-layer process induce thermal stresses, which can cause the part to warp or distort, especially for large or thin-walled geometries.
- Mitigation:
- Optimized Support Structures: Well-designed supports anchor the part to the build plate and manage thermal gradients.
- Build Orientation: Strategic orientation can minimize stress accumulation in critical areas.
- Параметры процесса: Fine-tuning laser/beam parameters can reduce thermal input.
- Thermal Simulation: Advanced simulation software can predict stress and distortion, allowing for design compensation or optimized support strategies.
- Снятие стресса: Prompt and proper post-print heat treatment is crucial.
- SEBM Advantage: Processes like SEBM operate at elevated temperatures, which inherently reduces residual stress compared to LPBF, potentially minimizing distortion for certain geometries. Met3dp’s expertise in SEBM can be beneficial here.
- Остаточное напряжение:
- Cause: Similar to warping, thermal gradients cause internal stresses even if visible distortion is controlled. High residual stress can reduce fatigue life and lead to premature failure.
- Mitigation:
- Stress Relief Heat Treatment: Essential for reducing internal stresses to acceptable levels.
- Управление процессом: Optimized parameters and scanning strategies (e.g., island scanning in LPBF).
- Дизайн: Avoiding large, bulky sections adjacent to thin walls can help manage stress distribution.
- HIPing: Can help further relieve stress and improve microstructure.
- Support Removal Difficulties (Especially Internally):
- Cause: Supports are necessary but can be difficult and time-consuming to remove, particularly from complex internal channels or intricate external features. Removal can also damage part surfaces.
- Mitigation:
- DfAM for Support Reduction: Designing with self-supporting angles and optimizing orientation are the primary strategies.
- Optimized Support Design: Using specialized software to create supports that are strong where needed but have easily breakable connection points or structures that minimize surface contact.
- Access Planning: Designing access points for tools if manual support removal is anticipated.
- Техники постобработки: Utilizing methods like CNC machining or EDM for precise support removal in critical areas.
- Powder Removal from Internal Channels:
- Cause: Unfused powder gets trapped inside narrow, long, or complex internal passages. It can be very difficult to fully evacuate.
- Mitigation:
- DfAM for Flow: Designing smooth internal paths, larger radii, and dedicated drain/access holes.
- Process Planning: Incorporating vibration, controlled airflow, and potentially ultrasonic cleaning during post-processing.
- Inspection: Using methods like CT scanning or borescope inspection to verify complete powder removal, especially for critical flight hardware.
- Модульная конструкция: For extremely complex internal networks, consider printing in sections and joining, though this adds complexity.
- Achieving Internal Surface Finish:
- Cause: As-printed surfaces inside channels are inherently rough, and access for traditional polishing methods is limited. Roughness can impede wire installation or potentially cause chafing over time.
- Mitigation:
- Оптимизация процессов: Some parameter sets can yield slightly smoother internal surfaces.
- Specialized Finishing: Techniques like Abrasive Flow Machining (AFM) or chemical etching/polishing can smooth internal passages but add cost and complexity.
- Дизайн: Increase channel diameter slightly if possible to ease installation even with some roughness. Specify internal finish requirements only where functionally necessary.
- Пористость:
- Cause: Tiny voids or pores can form within the printed material due to incomplete melting, gas entrapment, or keyholing (vapor depressions). Porosity can degrade mechanical properties, particularly fatigue life.
- Mitigation:
- High-Quality Powder: Using powder with consistent sphericity, size distribution, and low internal gas content, like those produced by Met3dp’s advanced atomization processes, is crucial.
- Optimized Process Parameters: Developing robust parameter sets specific to the material and machine.
- Process Monitoring: In-situ monitoring systems can help detect process anomalies.
- HIPing: Highly effective at closing internal pores and achieving near-full theoretical density.
- Material Property Consistency:
- Cause: Variations in the printing process (e.g., local overheating, gas flow variations) can potentially lead to minor inconsistencies in the material’s microstructure and mechanical properties throughout the part.
- Mitigation:
- Robust Process Control: Strict adherence to qualified printing procedures and machine calibration.
- Material Testing: Regular testing of material properties using witness coupons printed alongside parts.
- Heat Treatment & HIPing: Homogenize microstructure and ensure consistent properties.
- Supplier Expertise: Partnering with experienced providers like Met3dp who have deep material science knowledge and process control ensures greater reliability.
Table: Common Metal AM Challenges & Solutions for Wiring Channels
Испытание | Primary Cause(s) | Key Mitigation Strategies | Met3dp Advantage |
---|---|---|---|
Warping/Distortion | Тепловой стресс | Optimized Supports, Orientation, Parameters, Simulation, Stress Relief, SEBM option | Expertise in SEBM and LPBF, simulation capabilities |
Остаточное напряжение | Thermal Gradients | Stress Relief Heat Treatment, Process Control, Design, HIPing | Controlled processes, post-processing expertise |
Support Removal (Internal) | Overhangs, Limited Access | DfAM (Self-Supporting), Optimized Support Design, Access Planning, Machining/EDM | DfAM support, advanced support generation software |
Powder Removal (Internal) | Complex Geometry, Trapped Powder | DfAM (Drain Holes, Smooth Paths), Cleaning Procedures (Vibration, Air), Inspection (CT) | Design guidance, established cleaning protocols |
Internal Surface Finish | Layering Process, Access Limits | Process Optimization, Specialized Finishing (AFM, Electro), Design Allowance | Guidance on achievable finishes, finishing partners |
Пористость | Process Instability, Powder | High-Quality Powder, Optimized Parameters, Process Monitoring, HIPing | Premium powder quality (Gas Atomization/PREP), HIPing access |
Property Consistency | Process Variations | Process Control, Material Testing, Heat Treatment/HIPing, Supplier Expertise | Deep material science knowledge, rigorous QA |
Export to Sheets
Successfully implementing metal AM for aerospace wiring channels requires navigating these challenges proactively. By combining robust DfAM practices, careful process control, appropriate post-processing, and partnering with knowledgeable suppliers like Met3dp, aerospace companies can confidently adopt this technology to produce superior wiring management solutions.
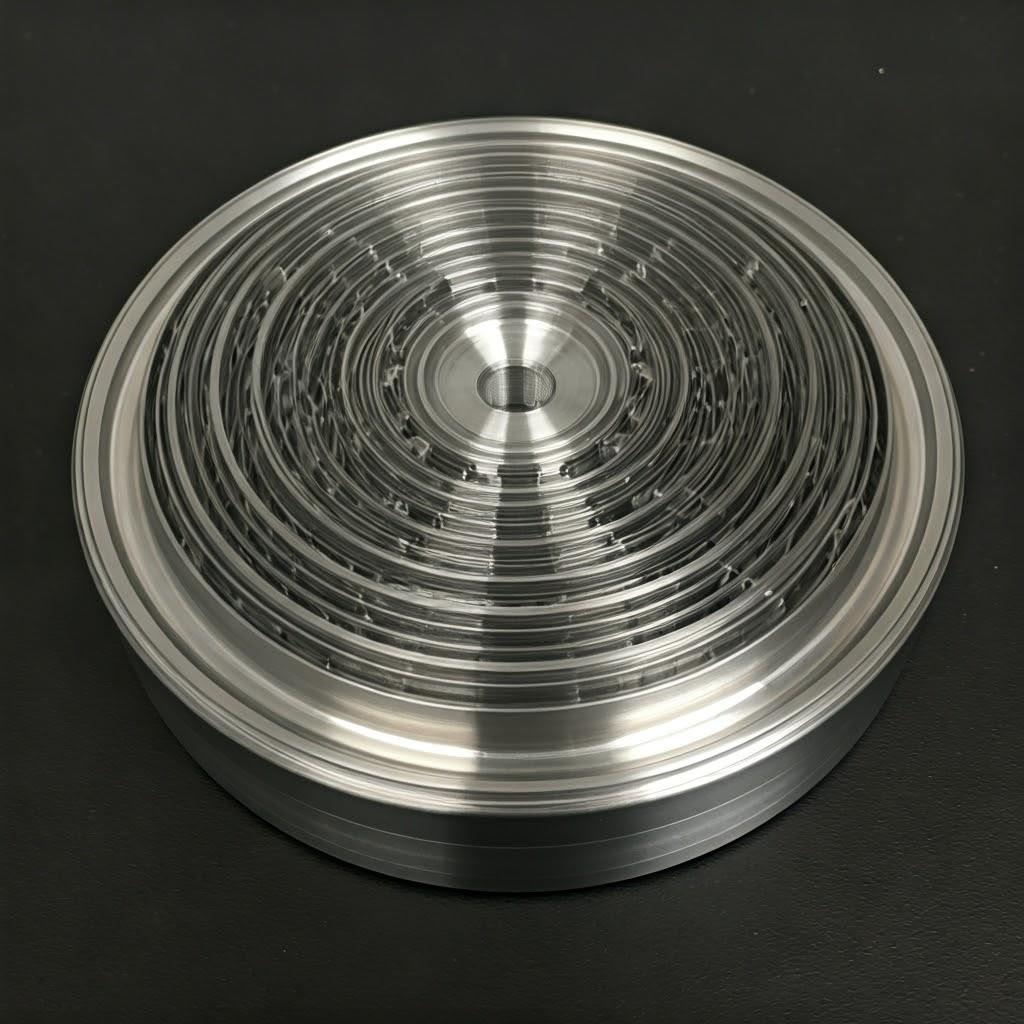
Supplier Selection: Choosing the Right Metal AM Partner for Aerospace Components
Selecting the right additive manufacturing partner is as critical as the technology itself, especially within the stringent requirements of the aerospace industry. The quality, reliability, and airworthiness of 3D printed wiring channels depend heavily on the expertise, processes, and quality systems of your chosen supplier. For engineers and procurement managers, evaluating potential partners requires looking beyond just printing capabilities.
Key Criteria for Evaluating Metal AM Suppliers for Aerospace:
- Aerospace Certifications and Compliance:
- AS9100 Certification: This is the standard Quality Management System (QMS) requirement for the aviation, space, and defense industries. Ensure the supplier holds a current AS9100 certification (or equivalent, like EN 9100), demonstrating their commitment to aerospace quality standards, traceability, and process control.
- ITAR/EAR Compliance: If working on defense-related projects, ensure the supplier complies with International Traffic in Arms Regulations (ITAR) or Export Administration Regulations (EAR) as applicable.
- Proven Aerospace Experience:
- Track Record: Look for suppliers with demonstrable experience in producing metal AM parts for aerospace applications. Ask for case studies, references, or examples of similar components they have manufactured.
- Understanding Requirements: An experienced partner will understand the nuances of aerospace documentation, qualification processes (First Article Inspection – FAI), and material specifications.
- Material Expertise and Portfolio:
- Specific Alloys: Confirm the supplier has extensive experience processing the specific alloys required for your wiring channels (e.g., AlSi10Mg, 316L) and potentially others like Titanium alloys (Ti6Al4V) or Nickel superalloys if needed for demanding applications.
- Powder Quality Control: Inquire about their powder sourcing, testing, handling, and traceability procedures. High-quality, aerospace-grade powder is fundamental. Suppliers like Met3dp, who manufacture their own high-performance metal powders using advanced techniques like gas atomization and PREP, offer significant advantages in quality control and material consistency.
- Technological Capabilities:
- Appropriate Technology: Do they offer the right AM process (LPBF, SEBM) for your specific material and application needs? SEBM, for instance, might be preferred for certain alloys or geometries prone to residual stress.
- Machine Fleet: Assess the range, capacity, and maintenance status of their printers. Redundancy can be important for meeting deadlines. Met3dp provides industry-leading SEBM printers known for their large build volume, accuracy, and reliability.
- Программное обеспечение: Ensure they use up-to-date software for build preparation, simulation, and support generation.
- In-House Post-Processing Capabilities:
- Integrated Workflow: Suppliers with comprehensive in-house capabilities for critical post-processing steps (heat treatment, basic machining, surface finishing, inspection) can often offer better control, streamlined workflows, and potentially faster lead times.
- Qualified Network: If certain processes (e.g., HIPing, advanced NDT, specialized coatings) are outsourced, ensure they have a network of qualified and approved vendors who also meet aerospace standards.
- Quality Management System (QMS) and Inspection:
- Robust QMS: Beyond AS9100, evaluate their overall QMS documentation, process control measures, and change management procedures.
- Inspection Capabilities: Assess their metrology equipment (CMMs, scanners) and NDT capabilities (CT scanning is highly valuable for internal channel verification). Ensure they can provide detailed inspection reports.
- Engineering and DfAM Support:
- Collaboration: A valuable partner will offer engineering support to help optimize your design for additive manufacturing (DfAM), suggest improvements, and ensure manufacturability. Met3dp’s application development services exemplify this collaborative approach.
- Project Management and Communication:
- Clear Communication: Look for responsive communication, clear project timelines, and a dedicated point of contact.
- Прозрачность: Ensure transparency regarding process steps, potential challenges, and quality documentation.
Why Partner with Met3dp?
Met3dp stands out as a comprehensive solutions provider in metal additive manufacturing.
- Dual Expertise: We not only manufacture industry-leading SEBM printers known for accuracy and reliability but also produce our own high-quality spherical metal powders (including aerospace grades) using proprietary gas atomization and PREP technologies.
- Quality Focus: Our commitment to quality is embedded in both our equipment design and powder manufacturing processes.
- Comprehensive Solutions: We offer solutions spanning printers, advanced powders, and application development services, partnering with organizations to implement AM effectively.
- Опыт работы: With decades of collective expertise, we understand the demands of industrial applications, including aerospace.
Choosing a partner like Met3dp ensures access to cutting-edge technology, premium materials, and deep expertise, de-risking your adoption of metal AM for critical components like wiring channels.
Understanding Costs and Timelines: Factors Influencing Production
While metal AM offers long-term value through performance gains and design efficiencies, understanding the cost structure and typical lead times is essential for budgeting and project planning. The cost of a 3D printed metal wiring channel is influenced by a combination of factors related to design, material, processing, and quality requirements.
Key Cost Drivers:
- Part Design Complexity and Volume:
- Material Volume: The sheer amount of metal powder required is a primary cost factor. Larger or denser parts naturally cost more. Topology optimization, while adding design effort, significantly reduces material volume and thus cost.
- Build Height (Z-Height): Print time is heavily influenced by the number of layers (height). Taller parts take longer to print.
- Сложность: While AM handles complexity well, extremely intricate designs might require more support structures or longer print times due to intricate scanning paths.
- Тип материала:
- Стоимость порошка: The raw material cost varies significantly between alloys. Standard alloys like 316L or AlSi10Mg are generally less expensive than titanium alloys or specialized superalloys. Met3dp’s efficient powder production aims to provide high-quality materials cost-effectively.
- Возможность печати: Some materials are trickier or slower to print reliably, impacting machine time.
- Machine Time (Printing):
- Hourly Rate: AM machines represent significant capital investment, and their operating time is a major cost component.
- Скорость печати: Determined by layer thickness, scanning strategy, and material.
- Nesting/Build Density: Printing multiple parts simultaneously in one build job optimizes machine utilization and reduces cost per part, especially beneficial for wholesale buyers or series production.
- Поддерживающие структуры:
- Объем: Supports consume material and print time.
- Removal Effort: Complex or internal supports require significant manual labor or machining time for removal, adding cost. Designing for minimal support (DfAM) is crucial for cost savings.
- Требования к постобработке:
- Термообработка: Standard stress relief is typically included, but complex cycles or HIPing add cost.
- Обработка: The extent of CNC machining required for tolerances or features directly impacts cost.
- Отделка поверхности: Basic bead blasting is common, but extensive polishing, electropolishing, or AFM adds considerable cost.
- Труд: Manual tasks like support removal and finishing are labor-intensive.
- Quality Assurance and Inspection:
- Level of Inspection: Basic dimensional checks are standard. Comprehensive NDT (CT scanning, FAI reports) required for aerospace significantly increases costs but ensures compliance and safety.
- Объем заказа:
- Экономия на масштабе: While AM is good for low volumes, costs per part decrease with larger batch sizes due to setup amortization and optimized build nesting. This is relevant for distributors and wholesale B2B orders.
Typical Lead Times:
Lead times for metal AM parts encompass the entire workflow: data preparation, scheduling, printing, cooling, post-processing, and inspection.
- Прототипы: For simple to moderately complex parts like wiring channels, prototypes can often be produced in 1 to 3 weeks, depending on machine availability and post-processing needs.
- Production Batches: For small-to-medium production runs, lead times might range from 3 to 8 weeks, heavily influenced by the batch size, part complexity, and the extent of post-processing and QA required.
- Accelerating Factors: DfAM optimization, clear specification, and partnering with a responsive supplier like Met3dp can help streamline the process.
Table: Cost & Lead Time Considerations
Фактор | Влияние на стоимость | Impact on Lead Time | Mitigation / Optimization Strategy |
---|---|---|---|
Part Volume/Complexity | High (Material, Print Time) | High (Print Time) | Topology Optimization, DfAM, Nesting |
Тип материала | Moderate to High (Powder Price) | Minor | Select appropriate material for function, not over-specify |
Machine Time | High (Operating Cost) | High (Primary Driver) | Optimize Orientation, Nesting, Select Efficient Process (LPBF vs SEBM) |
Вспомогательные структуры | Moderate (Material, Removal Labor) | Moderate (Removal Time) | DfAM for self-supporting features |
Постобработка | Moderate to Very High (Machining, Finishing) | Moderate to High (Multiple Steps) | Specify only necessary finishing/tolerances, Automate where possible |
Обеспечение качества | Moderate to High (NDT, Documentation) | Moderate (Inspection Time) | Clearly define QA requirements early, Leverage supplier QMS |
Объем заказа | Lower Cost/Part at Higher Volume | Longer Total Time for Large Batches | Plan production runs, explore batch optimization with supplier |
Export to Sheets
Engaging with an AM provider early in the design phase allows for accurate cost estimation and realistic timeline planning, ensuring projects stay on budget and schedule.
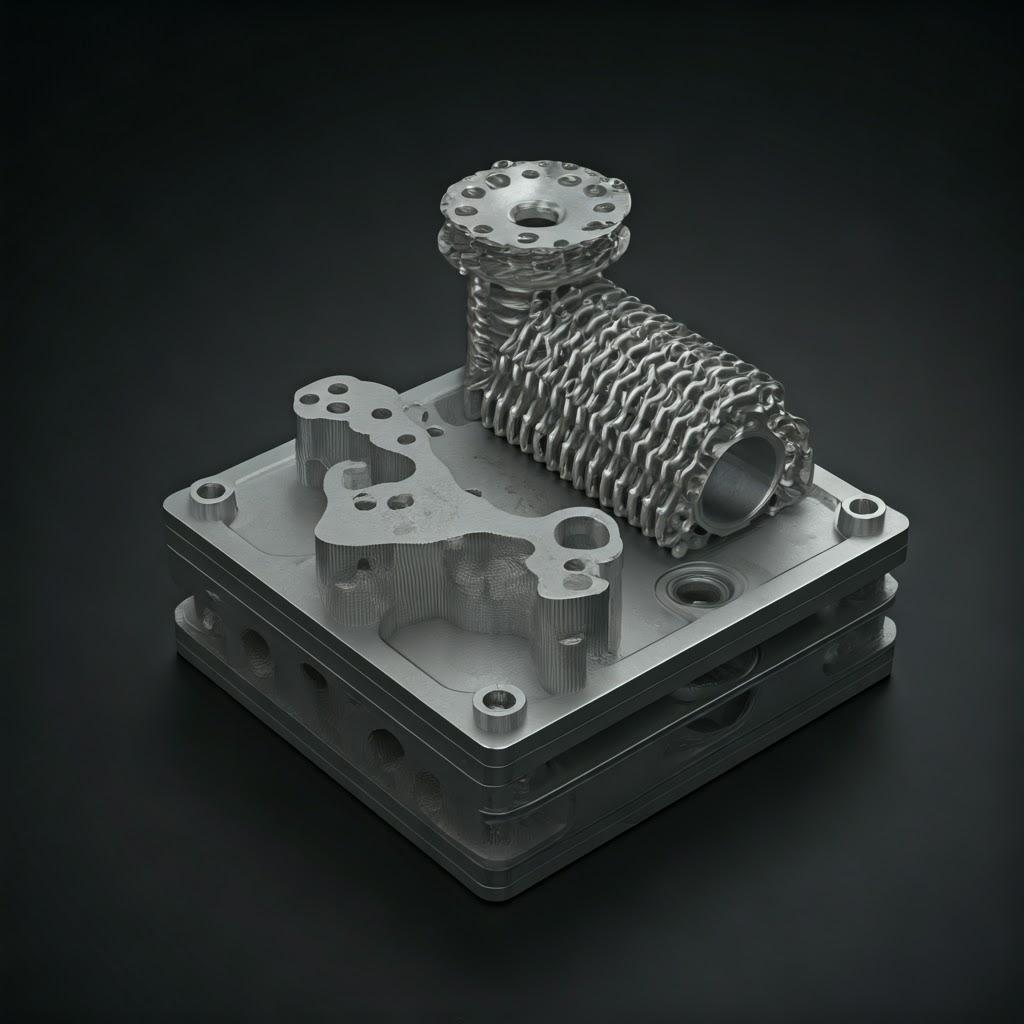
Frequently Asked Questions (FAQ) about 3D Printed Aerospace Wiring Channels
Here are answers to some common questions engineers and procurement managers have about using metal AM for aerospace wiring channels:
- What are the typical weight savings achievable with AM wiring channels compared to traditional methods?
- Weight savings can be significant, often ranging from 20% to 50% or even more compared to parts traditionally manufactured via CNC machining or sheet metal fabrication. The exact savings depend heavily on the original design, the chosen AM material (e.g., AlSi10Mg offers substantial savings over steel), and the effective application of DfAM principles like topology optimization and part consolidation. Integrating brackets and mounts directly into the channel design further contributes to system-level weight reduction.
- Are 3D printed metal wiring channels certified for flight? How does certification work?
- Individual 3D printed parts themselves aren’t automatically “certified.” Flight certification applies to the aircraft or system as a whole. However, the процесс used to create the parts must meet stringent aerospace standards. This involves:
- Supplier Certification: The manufacturer (AM service provider) must typically hold AS9100 certification.
- Квалификация процесса: The specific combination of machine, material (qualified powder batch), and parameters must be rigorously qualified and proven to produce parts with consistent, repeatable mechanical properties that meet design specifications.
- Material Allowables: Utilizing materials with established aerospace design allowables (e.g., through MMPDS).
- Part-Specific Qualification: Each part design usually requires qualification, often including FAI (First Article Inspection) and potentially destructive/non-destructive testing to verify it meets all performance and safety requirements.
- Working with an experienced aerospace AM provider like Met3dp, who understands these qualification pathways, is crucial.
- Individual 3D printed parts themselves aren’t automatically “certified.” Flight certification applies to the aircraft or system as a whole. However, the процесс used to create the parts must meet stringent aerospace standards. This involves:
- How does the cost of metal AM compare to traditional CNC machining for complex wiring channels?
- For simple channel geometries: CNC machining from stock material is often more cost-effective, especially at higher volumes.
- For complex geometries: When wiring channels involve intricate curves, internal features, integrated mounts, or require significant lightweighting (topology optimization), metal AM becomes increasingly competitive and often more cost-effective. This is because AM handles complexity with little added cost, whereas machining complexity dramatically increases programming and machining time (e.g., 5-axis machining).
- Объединение частей via AM also reduces downstream assembly costs, shifting the cost comparison in AM’s favor for integrated components.
- Создание прототипов: AM is almost always faster and cheaper for producing initial prototypes and design iterations due to the lack of tooling.
- Can we just take our existing wiring channel design (made for sheet metal or CNC) and directly 3D print it?
- While technically possible, it’s highly discouraged. Designs created for traditional methods are not optimized for AM. Directly printing them often results in:
- Excessive weight (no lightweighting applied).
- Increased need for support structures (higher cost, longer lead time).
- Potential printability issues (e.g., thin walls, sharp corners).
- Missed opportunities for part consolidation and performance improvements.
- To realize the true benefits of metal AM, redesigning the part using Проектирование для аддитивного производства (DfAM) principles is essential. Collaboration with AM experts is recommended to optimize the design effectively.
- While technically possible, it’s highly discouraged. Designs created for traditional methods are not optimized for AM. Directly printing them often results in:
Conclusion: Elevating Aerospace Design with Additively Manufactured Wiring Solutions
The aerospace industry operates at the cutting edge of engineering, demanding components that are lighter, stronger, more complex, and delivered faster than ever before. For managing the critical nervous system of aircraft and spacecraft – the electrical wiring – traditional manufacturing methods for creating wiring channels are increasingly hitting limitations. Metal additive manufacturing offers a powerful solution, enabling a paradigm shift in how these essential components are designed and produced.
As we’ve explored, leveraging metal AM for aerospace wiring channels provides tangible benefits:
- Беспрецедентная свобода дизайна: Creating complex, conformal routing paths optimized for space and function.
- Significant Weight Reduction: Employing topology optimization and lightweight alloys like AlSi10Mg to enhance fuel efficiency and payload capacity.
- Консолидация частей: Integrating brackets, mounts, and other features to reduce part count, assembly time, and potential failure points.
- Характеристики материала: Utilizing robust materials like 316L stainless steel for durability and corrosion resistance in demanding environments.
- Agile Manufacturing: Enabling rapid prototyping, on-demand production, and reduced lead times for custom or spare parts.
Successfully implementing this technology requires careful consideration of DfAM principles, material selection, precision requirements, post-processing steps, and potential challenges. Critically, it demands partnership with a knowledgeable and capable supplier equipped with the right technology, robust quality systems, and deep expertise in aerospace applications.
Met3dp is uniquely positioned to be that partner. With our industry-leading SEBM additive manufacturing systems, advanced metal powder production capabilities (Gas Atomization & PREP), and comprehensive application support, we provide end-to-end solutions tailored for the demanding aerospace sector. We empower engineers and manufacturers to harness the full potential of metal 3D printing, transforming component design and accelerating the future of flight.
Ready to explore how metal additive manufacturing can revolutionize your aerospace wiring solutions?
Contact Met3dp today to discuss your specific application needs, learn more about our advanced SEBM printers and high-performance metal powders, and discover how our expertise can elevate your next project. Visit our website at https://met3dp.com/ чтобы узнать больше.
Поделиться
MET3DP Technology Co., LTD - ведущий поставщик решений для аддитивного производства со штаб-квартирой в Циндао, Китай. Наша компания специализируется на производстве оборудования для 3D-печати и высокопроизводительных металлических порошков для промышленного применения.
Сделайте запрос, чтобы получить лучшую цену и индивидуальное решение для вашего бизнеса!
Похожие статьи
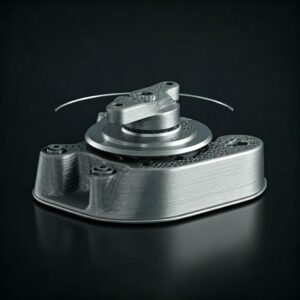
3D-печатные крепления для автомобильных радарных датчиков: Точность и производительность
Читать далее "О компании Met3DP
Последние обновления
Наш продукт
CONTACT US
Есть вопросы? Отправьте нам сообщение прямо сейчас! После получения Вашего сообщения мы всей командой выполним Ваш запрос.
Получите информацию о Metal3DP
Брошюра о продукции
Получить последние продукты и прайс-лист
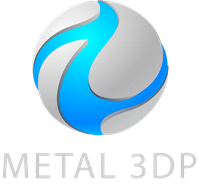
Металлические порошки для 3D-печати и аддитивного производства