Custom Pipe Brackets for Aerospace Systems via 3D Printing
Оглавление
Introduction: Revolutionizing Aerospace Componentry with 3D Printed Pipe Brackets
The aerospace industry stands at the forefront of technological adoption, constantly seeking materials and manufacturing processes that deliver unparalleled performance, reliability, and efficiency. In this pursuit, metal additive manufacturing (AM), commonly known as 3D-печать, has emerged as a transformative force, reshaping how complex components are designed, produced, and integrated into aircraft, spacecraft, and satellite systems. Among the myriad of parts benefiting from this revolution are pipe brackets – seemingly simple, yet structurally critical components responsible for securing fluid lines, conduits, and wiring harnesses throughout aerospace platforms. Traditionally manufactured through methods like CNC machining, casting, or sheet metal fabrication, these brackets often present design limitations, weight penalties, and lengthy production cycles. Metal 3D printing offers a compelling alternative, enabling the creation of custom pipe brackets for aerospace systems with optimized geometries, reduced weight, consolidated assemblies, and accelerated timelines, directly addressing the stringent demands of the sector.
Pipe brackets in aerospace are ubiquitous, found in engines, fuselages, landing gear assemblies, environmental control systems (ECS), and hydraulic systems. Their primary function is to secure pipes and conduits, preventing vibration-induced fatigue, ensuring proper routing, and maintaining system integrity under extreme operating conditions, including significant temperature fluctuations, high pressures, and intense G-forces. Failure of a bracket can lead to pipe damage, fluid leaks, system malfunctions, or even catastrophic failure, underscoring their importance in flight safety and mission success.
The limitations of conventional manufacturing often force engineers to compromise on bracket design. Machining complex shapes from billet material can be wasteful and time-consuming, while casting may not achieve the required strength-to-weight ratios or intricate features. Sheet metal forming has limitations in terms of geometric complexity and load-bearing capacity for certain applications. This is where the power of metal additive manufacturing aerospace solutions comes into play. By building parts layer-by-layer directly from metal powder feedstock using technologies like Selective Laser Melting (SLM) or Selective Electron Beam Melting (SEBM), 3D printing unshackles designers from traditional constraints. It allows for:
- Беспрецедентная свобода дизайна: Engineers can create highly complex, topology-optimized bracket geometries that precisely conform to surrounding structures, minimize material usage while maximizing strength, and integrate features like cable guides or mounting points directly into the part. This leads to significant weight savings – a paramount concern in aerospace where every gram saved translates to fuel efficiency or increased payload capacity.
- Консолидация частей: Multiple individual components that previously made up a bracket assembly can often be redesigned and printed as a single, monolithic part. This reduces part count, eliminates assembly steps, minimizes potential failure points (like fasteners), and simplifies supply chain logistics.
- Быстрое создание прототипов и итерации: New bracket designs can be prototyped and tested much faster than with traditional tooling-based methods. Design modifications can be implemented quickly based on test results, accelerating the development cycle for new aircraft or system upgrades.
- Производство по требованию: Spare or replacement brackets can be produced on-demand, reducing the need for large physical inventories and minimizing downtime during maintenance, repair, and overhaul (MRO) operations. This is particularly valuable for legacy aircraft where original tooling may no longer exist.
- Универсальность материала: Metal AM processes can utilize a wide range of high-performance aerospace-grade alloys, including titanium alloys (like Ti-6Al-4V) and stainless steels (like 316L), ensuring the brackets meet demanding strength, temperature resistance, and corrosion resistance requirements.
Companies seeking reliable Решения для 3D-печати for critical components like pipe brackets require partners with deep expertise in materials science, process control, and quality assurance. Met3dp, headquartered in Qingdao, China, is a leading provider of comprehensive additive manufacturing solutions, specializing in high-performance metal powders and industrial-grade 3D printing equipment. Leveraging decades of collective expertise, Met3dp partners with aerospace manufacturers and suppliers to implement cutting-edge AM technologies, delivering components that meet the industry’s exacting standards. Their focus on producing high-quality spherical metal powders using advanced techniques like gas atomization ensures the feedstock consistency crucial for reliable, high-density aerospace parts. As we delve deeper into the applications, advantages, and considerations for 3D printed aerospace pipe brackets, the value of partnering with experienced aerospace component suppliers like Met3dp becomes increasingly clear. This technology is not just an alternative; it’s a fundamental shift towards more efficient, capable, and resilient aerospace systems.
Applications: Where are 3D Printed Pipe Brackets Utilized in Aerospace?
The versatility and advantages of metal additive manufacturing have led to the adoption of 3D printed pipe brackets across a diverse range of aerospace applications. Their ability to be customized, lightweighted, and produced on-demand makes them suitable for virtually any system requiring secure routing and support of pipes, tubes, conduits, or wiring harnesses. Procurement managers and engineers in the aerospace sector are increasingly specifying metal AM for these components, recognizing the value proposition it offers over conventional methods, especially in demanding environments and for complex configurations. The applications span commercial aviation, defense aircraft, space launch vehicles, satellites, and even unmanned aerial vehicles (UAVs).
Key application areas include:
- Fluid Conveyance Systems (Fuel, Hydraulic, Coolant):
- Function: Securely routing fuel lines, hydraulic tubes, and coolant pipes throughout the aircraft, from tanks and pumps to engines and actuators.
- Why 3D Printing? These systems often involve complex routing through tight spaces with numerous bends and connections. 3D printing allows for brackets perfectly contoured to the specific pipe layout and surrounding structures, minimizing stress concentrations and vibration. The ability to use materials like Ti-6Al-4V aerospace grade titanium provides excellent strength-to-weight ratios and corrosion resistance, crucial for handling potentially aggressive fluids like hydraulic oil or jet fuel. Part consolidation can reduce potential leak points associated with multi-part bracket assemblies.
- B2B Relevance: Suppliers specializing in aerospace fluid systems components are prime candidates for adopting metal AM to offer lighter, more integrated bracket solutions to Tier 1 and OEM customers.
- Environmental Control Systems (ECS):
- Function: Supporting the ducting and piping associated with cabin air conditioning, pressurization, and temperature regulation systems.
- Why 3D Printing? ECS ducting can be complex and voluminous. Lightweighting is critical here to minimize the overall system’s impact on aircraft performance. Topology optimization enabled by AM can create brackets that provide robust support with minimal material usage. Materials like 316L stainless steel or aluminum alloys (printable via AM) offer good corrosion resistance and moderate temperature capabilities suitable for ECS applications.
- B2B Relevance: Manufacturers of ECS modules and авиационные компоненты can leverage 3D printing for faster design iteration and production of customized brackets tailored to specific aircraft models.
- Engine and Nacelle Components:
- Function: Supporting various pipes (oil, fuel, pneumatic) and wiring harnesses within the harsh environment of the engine nacelle and pylon.
- Why 3D Printing? This area demands high strength, fatigue resistance, and tolerance to extreme temperatures and vibrations. High-performance materials like Ti-6Al-4V or nickel-based superalloys (also printable via AM) are often required. 3D printing enables complex bracket shapes that can withstand these conditions while optimizing weight and potentially integrating heat shielding features.
- B2B Relevance: Engine manufacturers and their Tier suppliers can utilize AM for producing highly specialized, performance-critical brackets, often benefiting from on-demand aerospace parts capability for MRO.
- Wiring Harness and Conduit Support:
- Function: Organizing and securing electrical wiring harnesses and protective conduits throughout the airframe, avionics bays, and other areas.
- Why 3D Printing? While often less structurally demanding than fluid pipe brackets, wire harness brackets still benefit from customization and weight reduction. AM allows for integrated features like snap-fits, cable tie mounts, or specific channel geometries to neatly manage complex wiring bundles. Using materials like 316L or even specialized polymers (via different AM processes) can be effective.
- B2B Relevance: Avionics integrators and aerospace component distributors can offer customized 3D printed bracket solutions for efficient wiring installation and maintenance.
- Space Launch Vehicles and Satellites:
- Function: Securing propellant lines, hydraulic tubes, pressurization lines, and data cables in rockets and satellites, where weight is absolutely critical and operating conditions are extreme (cryogenic temperatures, vacuum, high G-forces during launch).
- Why 3D Printing? The extreme lightweighting potential offered by topology optimization and materials like Ti-6Al-4V is paramount for space applications. Every kilogram saved translates directly into higher payload capacity or mission delta-v. The ability to create highly complex, bespoke brackets for densely packed satellite interiors is invaluable. Детали спутника manufacturers heavily rely on the design freedom of AM.
- B2B Relevance: Specialist suppliers to the space industry utilize metal AM extensively for producing flight-critical легкие конструкции, including brackets.
- Aerospace Maintenance, Repair, and Overhaul (MRO):
- Function: Replacing damaged or obsolete brackets on existing aircraft, often where original parts or tooling are unavailable.
- Why 3D Printing? AM allows for the reverse engineering and on-demand production of replacement brackets without needing legacy tooling. This significantly reduces lead times for repairs, getting aircraft back into service faster. Digital inventories of bracket designs can be maintained, allowing parts to be printed anywhere globally with certified equipment and processes.
- B2B Relevance: Aerospace MRO providers can gain a competitive advantage by integrating metal 3D printing capabilities for rapid, certified part replacement, improving aircraft availability for operators.
The breadth of these applications highlights why custom pipe brackets for aerospace systems are increasingly being realized through metal 3D printing. The technology provides tailored solutions across diverse platforms and systems, meeting specific performance requirements while offering significant advantages in weight, lead time, and design complexity compared to traditional manufacturing approaches. Companies like Met3dp, with their focus on high-quality metal powders and advanced printing systems, are crucial enablers for the successful implementation of AM in these critical aerospace applications. Their commitment to providing reliable металлическая 3D-печать solutions ensures that manufacturers and suppliers can confidently adopt this technology for demanding components.
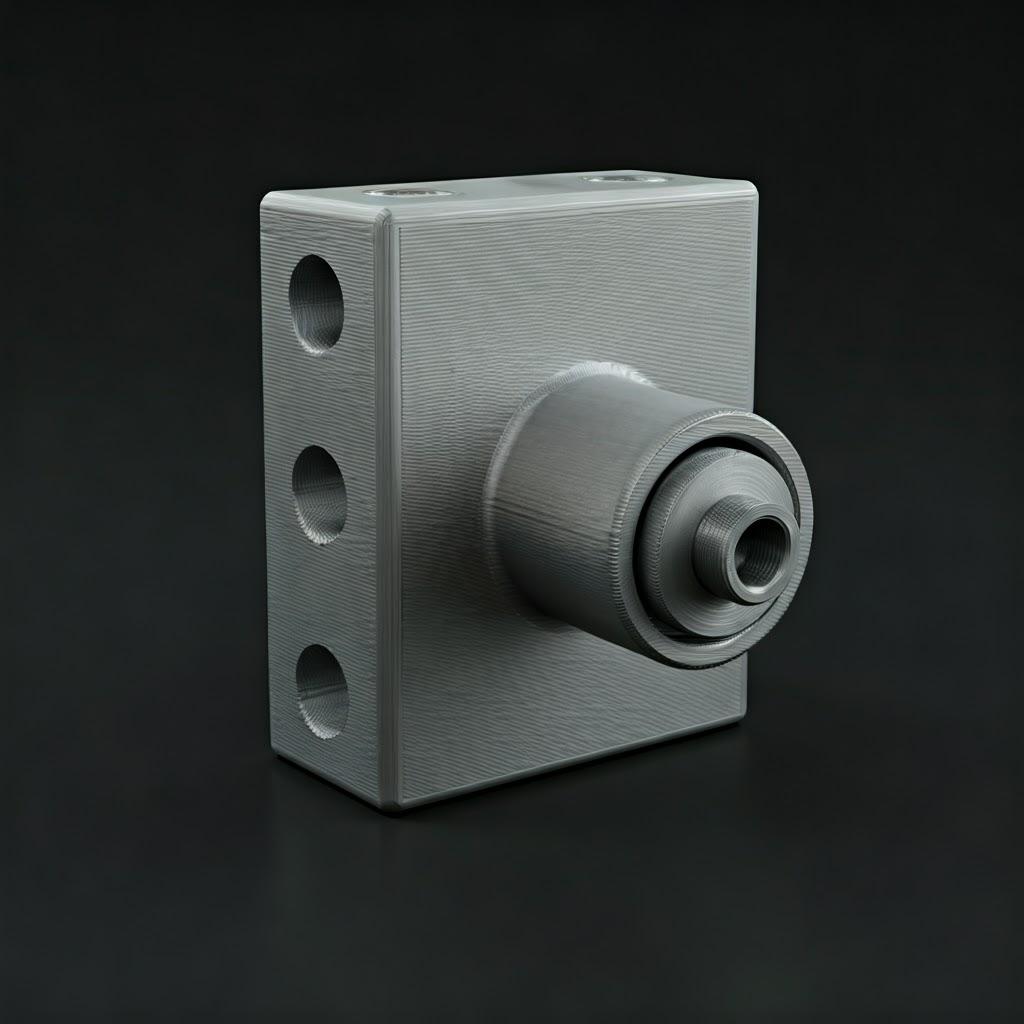
Advantages: Why Choose Metal 3D Printing for Aerospace Pipe Brackets?
The shift towards utilizing metal additive manufacturing for aerospace pipe brackets isn’t merely a trend; it’s driven by a convergence of tangible engineering, manufacturing, and operational benefits that directly address the core challenges faced by the aerospace industry. Compared to traditional methods like machining, casting, or forming, metal 3D printing offers a unique combination of advantages that make it particularly well-suited for producing these critical support components. Engineers, designers, and procurement managers evaluating manufacturing options should consider the compelling reasons why metal AM stands out.
Ключевые преимущества:
- Significant Weight Reduction (Lightweighting):
- Mechanism: Metal AM enables advanced design techniques like topology optimization and generative design. Algorithms determine the most efficient material distribution to withstand specific loads, removing unnecessary mass while maintaining structural integrity. This results in organic, often complex-looking brackets that are significantly lighter than their traditionally manufactured counterparts designed with subtractive constraints in mind. Lattice structures can also be incorporated internally to reduce density further.
- Влияние: In aerospace, weight is a primary driver of operational cost (fuel burn) and performance (payload capacity, range, maneuverability). Even small weight savings per bracket, when multiplied by the hundreds or thousands of brackets on an aircraft, accumulate into substantial overall weight reduction. This pursuit of lightweighting aerospace structures is a major factor driving AM adoption.
- B2B Value: Suppliers offering topology-optimized 3D printed brackets provide direct value to airframe manufacturers (OEMs) and airlines by contributing to fuel efficiency and performance goals.
- Unmatched Design Freedom & Complexity:
- Mechanism: Layer-by-layer construction removes many of the geometric constraints imposed by traditional methods. Features like internal channels, complex curves, conformal shapes, varying wall thicknesses, and integrated functionalities (e.g., mounting points, vibration damping features) can be created directly during the printing process without the need for complex tooling, multi-axis machining setups, or assembly steps.
- Влияние: Engineers can design brackets that are perfectly optimized for their specific location and function, fitting precisely within tight envelopes, conforming to adjacent components, and performing multiple roles. This capability allows for more integrated and efficient system designs overall. The ability to manufacture complex geometry manufacturing challenges is a hallmark of AM.
- B2B Value: Design consultancies and engineering service providers can leverage AM to offer innovative bracket solutions that were previously impossible or impractical to manufacture.
- Консолидация частей:
- Mechanism: Assemblies previously consisting of multiple machined, formed, or cast parts held together by fasteners can often be redesigned and printed as a single, monolithic component.
- Влияние: Reduces part count, simplifies inventory management and logistics, eliminates assembly labor and associated costs, reduces potential points of failure (fastener loosening, joint fatigue), and often contributes to weight reduction by eliminating overlaps and fasteners.
- B2B Value: Component suppliers can offer more integrated, reliable, and potentially cost-effective solutions by consolidating assemblies into single 3D printed parts, streamlining the supply chain for their customers.
- Rapid Prototyping and Accelerated Development Cycles:
- Mechanism: Metal AM is a direct digital manufacturing process. Designs can go from CAD model to physical metal prototype in days, rather than the weeks or months often required for traditional tooling and setup. Design iterations can be implemented and tested quickly.
- Влияние: Significantly speeds up the product development process for new aircraft programs or system upgrades. Allows engineers to physically validate designs and perform functional testing much earlier, reducing development risks and costs. This capability for rapid prototyping aerospace components is invaluable.
- B2B Value: Service bureaus and OEMs with in-house AM capabilities can offer significantly faster turnaround times for prototype brackets, enabling quicker design freeze and program progression.
- On-Demand Production and MRO Support:
- Mechanism: Once a bracket design is digitized and the printing process is qualified, parts can be produced as needed without dedicated tooling. Digital inventories replace physical stockpiles.
- Влияние: Reduces warehousing costs and eliminates inventory obsolescence. Crucially for aerospace MRO, it enables the rapid production of spare parts, especially for older aircraft where original suppliers or tooling may no longer exist. Minimizes aircraft downtime (Aircraft on Ground – AOG situations).
- B2B Value: MRO providers and parts distributors equipped with certified metal AM capabilities can offer on-demand aerospace parts, providing a highly responsive and cost-effective solution for airline maintenance needs, improving supply chain resilience.
- Эффективность материала:
- Mechanism: Additive processes typically use only the material needed to build the part and its support structures, unlike subtractive machining which starts with a larger block and removes material, generating significant waste (swarf). While some powder recycling is necessary, the overall “buy-to-fly” ratio (the ratio of raw material purchased to the weight of the final part) can often be improved.
- Влияние: Reduces raw material consumption, particularly important for expensive aerospace alloys like titanium. Lowers the environmental footprint associated with material waste.
- B2B Value: Cost savings associated with reduced material waste can make 3D printed brackets more competitive, especially for complex geometries or expensive materials.
- Customization and Bespoke Solutions:
- Mechanism: Each part printed can potentially be unique without significant tooling changes. This allows for brackets tailored to specific installation points or minor variations between individual aircraft.
- Влияние: Enables highly optimized installations and potentially accommodates modifications or retrofits more easily.
- B2B Value: Suppliers can offer highly customized bracket solutions tailored to individual customer requirements or specific platform needs, moving beyond standard off-the-shelf parts.
In summary, the benefits additive manufacturing brings to aerospace pipe bracket production are multi-faceted, addressing critical industry drivers like weight reduction, performance optimization, cost efficiency, and supply chain agility. While challenges exist (discussed later), the compelling advantages make metal 3D printing an increasingly indispensable tool for aerospace engineers and manufacturers striving to build the next generation of aircraft and spacecraft. Providers like Met3dp, with their robust equipment and high-quality powder portfolio, are essential partners in realizing these benefits reliably and repeatably.
Material Focus: Selecting Optimal Powders like 316L & Ti-6Al-4V
The performance, reliability, and suitability of a 3D printed aerospace pipe bracket are fundamentally dictated by the material chosen. Additive manufacturing processes like Selective Laser Melting (SLM) and Selective Electron Beam Melting (SEBM) utilize fine metal powders as feedstock. Selecting the right powder is critical and depends heavily on the specific application requirements, including operating temperature, structural loads, corrosive environment, weight constraints, and certification requirements. For aerospace pipe brackets, two materials stand out as frequently recommended choices: 316L Stainless Steel and Ti-6Al-4V Titanium alloy. Understanding their properties and why they are favored is crucial for engineers and procurement managers.
Why Material Selection Matters in Aerospace AM:
- Производительность: The material must meet or exceed the mechanical property requirements (strength, fatigue life, stiffness, fracture toughness) under operational loads and environmental conditions.
- Вес: Strength-to-weight ratio is paramount in aerospace. Lighter materials that still meet performance criteria are highly desirable.
- Environmental Resistance: Resistance to corrosion (from fluids, atmosphere, de-icing agents), oxidation (at high temperatures), and stress corrosion cracking is vital for longevity and safety.
- Temperature Capability: Brackets near engines or in high-speed aircraft experience significant temperature variations. The material must maintain its properties across the required temperature range.
- Возможность печати: Not all alloys are easily processed via AM. The chosen material must be compatible with the specific AM process (SLM, SEBM) and capable of producing dense, defect-free parts.
- Certifiability: Aerospace components often require stringent certification (e.g., FAA, EASA). Materials must have well-characterized properties and established process specifications to meet these requirements.
- Стоимость: Material cost significantly impacts the final part price. Balancing performance needs with budget constraints is always a consideration.
Recommended Powders for Aerospace Pipe Brackets:
1. Нержавеющая сталь 316L:
- Состав: An austenitic stainless steel containing chromium, nickel, and molybdenum. The “L” denotes low carbon content (typically < 0.03%), which improves weldability and reduces sensitization (chromium carbide precipitation) during thermal cycles like those encountered in AM and post-processing heat treatments.
- Основные свойства:
- Отличная коррозионная стойкость: Highly resistant to a wide range of corrosive environments, including atmospheric corrosion, various chemicals, and saltwater. Molybdenum content enhances resistance to pitting and crevice corrosion.
- Good Strength and Ductility: Offers a good balance of tensile strength, yield strength, and elongation, making it tough and resistant to fracture.
- Good Weldability & Printability: Generally considered one of the easier metals to process reliably using Powder Bed Fusion (PBF) techniques like SLM.
- Moderate Temperature Capability: Suitable for applications generally below 400-500°C, depending on load and environment.
- Эффективность затрат: Relatively lower cost compared to titanium or nickel superalloys.
- Биосовместимость: Often used in medical applications, indicating good general material safety.
- Why Use for Brackets? 316L is an excellent choice for brackets in less demanding temperature zones (e.g., cabin interiors, cargo bays, some ECS applications) where excellent corrosion resistance and good mechanical properties are required, and weight is not the absolute primary driver, or where cost is a significant factor. Its robustness and ease of printing make it a reliable workhorse material.
- Met3dp Relevance: As a provider of high-quality поставщик металлического порошка, Met3dp offers optimized 316L powders suitable for demanding industrial applications, ensuring consistency and quality for reliable bracket production. Their advanced gas atomization techniques produce powders with high sphericity and good flowability, critical for achieving dense parts in the AM process.
Table: Typical Properties of AM 316L (Varies with Process & Post-Processing)
Недвижимость | Typical Value Range | Единица | Примечания |
---|---|---|---|
Предельная прочность на разрыв | 500 – 650 | MPa | Can be higher depending on build orientation |
Предел текучести (0,2%) | 400 – 550 | MPa | |
Удлинение при разрыве | 30 – 50 | % | Indicates good ductility |
Плотность | ~7.9 – 8.0 | г/см³ | |
Твердость | ~150 – 200 | ВН | |
Max Operating Temp. | ~425 (long term exposure) | °C | Dependent on load and environment |
Коррозионная стойкость | Отличный | Qualitative | Especially in chloride environments |
Export to Sheets
2. Ti-6Al-4V (Grade 5 Titanium):
- Состав: An alpha-beta titanium alloy containing approximately 6% aluminum and 4% vanadium. It is the most widely used titanium alloy across many industries, especially aerospace.
- Основные свойства:
- Исключительное соотношение прочности и веса: Offers high strength comparable to many steels but at nearly half the density. This is its most significant advantage for aerospace.
- Отличная коррозионная стойкость: Forms a stable, passive oxide layer providing outstanding resistance to corrosion in seawater, oxidizing acids, and many industrial chemicals.
- High Temperature Capability: Can operate continuously up to around 400°C (750°F) and withstand short-term excursions higher. Specific grades (like ELI – Extra Low Interstitial) maintain good toughness at cryogenic temperatures.
- Good Fatigue Strength: Performs well under cyclic loading conditions common in aerospace structures.
- Биосовместимость: Widely used for medical implants.
- Хорошая печать: While more challenging to print than 316L (requiring careful atmosphere control due to reactivity), Ti-6Al-4V is well-established for both SLM and SEBM processes. SEBM, often preferred for titanium, uses a vacuum environment which minimizes contamination.
- Why Use for Brackets? Ti-6Al-4V aerospace applications are numerous. It’s the go-to material when weight reduction is critical, and/or when operating temperatures exceed the limits of stainless steel or aluminum alloys (e.g., near engines, in high-performance aircraft structures, space applications). Its combination of high strength, low density, and excellent corrosion resistance makes it ideal for performance-critical brackets.
- Met3dp Relevance: Met3dp’s portfolio includes high-performance alloys like Ti-6Al-4V, produced using advanced powder manufacturing systems. Their expertise extends to processing challenging materials, ensuring customers can leverage the benefits of titanium for demanding aerospace grade materials requirements. They offer comprehensive solutions, including optimized powders and SEBM printers, which are particularly adept at processing reactive materials like titanium.
Table: Typical Properties of AM Ti-6Al-4V (Varies with Process & Post-Processing, e.g., Heat Treatment)
Недвижимость | Typical Value Range (Annealed) | Единица | Примечания |
---|---|---|---|
Предельная прочность на разрыв | 900 – 1150 | MPa | Significantly stronger than 316L |
Предел текучести (0,2%) | 800 – 1050 | MPa | |
Удлинение при разрыве | 6 – 15 | % | Lower ductility than 316L |
Плотность | ~4.43 | г/см³ | ~45% lighter than steel |
Твердость | ~300 – 350 | ВН | |
Max Operating Temp. | ~400 | °C | Continuous service limit |
Коррозионная стойкость | Отличный | Qualitative | Especially in oxidizing/chloride media |
Export to Sheets
Choosing Between 316L and Ti-6Al-4V:
The choice often comes down to a trade-off analysis:
- Weight Critical? -> Ti-6Al-4V is strongly favored.
- High Operating Temperature (>300-400°C)? -> Ti-6Al-4V or potentially other high-temperature alloys (e.g., Inconel, also printable) are necessary.
- Corrosion Resistance Paramount? -> Both are excellent, but Ti-6Al-4V may have an edge in specific environments. 316L is very robust in general atmospheric and fluid conditions.
- Budget Conscious & Lower Performance Demands? -> 316L is often the more economical choice.
- Ductility/Toughness Critical? -> 316L generally offers higher ductility. Post-processing (like HIPing and heat treatments) can significantly influence the final properties of both materials.
Ultimately, careful analysis of the specific bracket’s operating environment, structural requirements, and cost targets, guided by material datasheets and potentially expert consultation from высокоэффективные сплавы providers like Met3dp, will lead to the optimal material selection for successful aerospace application. The quality of the initial powder feedstock is paramount, influencing the final part’s density, mechanical properties, and overall reliability. Sources and related content
Design for Additive Manufacturing (DfAM): Optimizing Pipe Bracket Geometry
Simply replicating a traditionally designed pipe bracket using 3D printing often fails to capture the full potential of additive manufacturing. To truly leverage the benefits of weight reduction, part consolidation, and enhanced performance, engineers must embrace Design for Additive Manufacturing (DfAM). DfAM is a design philosophy and set of principles that considers the unique capabilities and constraints of AM processes right from the conceptual stage. Applying DfAM aerospace principles to pipe brackets allows for the creation of highly optimized, efficient, and manufacturable components tailored specifically for layer-by-layer fabrication. Procurement managers should also be aware of these principles, as they influence part cost, lead time, and ultimately, performance – factors critical when evaluating quotes from metal AM service providers.
Key DfAM Principles for Aerospace Pipe Brackets:
- Topology Optimization:
- Concept: This is perhaps the most transformative DfAM technique for structural components like brackets. Using specialized software, engineers define the design space (maximum allowable volume), load cases (forces, pressures, vibrations the bracket must withstand), constraints (mounting points, keep-out zones), and optimization goals (typically minimizing mass while meeting stiffness or stress targets). The software then iteratively removes material from non-critical areas, leaving behind an optimized load path – often resulting in organic, bone-like structures.
- Application to Brackets: Topology optimization can drastically reduce the weight of pipe brackets compared to conventional designs, directly contributing to aircraft fuel efficiency or increased payload. The resulting geometries are often complex and non-intuitive, perfectly suited for AM’s ability to create freeform shapes.
- Соображения: Optimized designs require careful validation through Finite Element Analysis (FEA) to ensure structural integrity. Manufacturability constraints (e.g., minimum feature size, overhang angles) must be incorporated into the optimization process.
- Support Structure Strategy:
- Concept: Most Powder Bed Fusion (PBF) processes (like SLM and SEBM) require support structures for overhanging features (typically surfaces angled less than 45 degrees from the build plate) and to anchor the part to the build plate, preventing warping due to thermal stresses. Designing с supports in mind is crucial.
- Application to Brackets: Engineers should orient the bracket in the build chamber to minimize the need for supports, especially on critical functional surfaces or hard-to-reach internal areas. Where supports are necessary, they should be designed for easy and clean removal without damaging the part surface. Sometimes, the bracket geometry itself can be altered slightly (e.g., changing fillet radii, adding self-supporting angles) to reduce support requirements. Effective support structure design is key to cost-effective and high-quality printing.
- Соображения: Support removal adds time and cost to post-processing. Poorly designed supports can leave witness marks or damage surfaces. Minimizing supports through clever design and orientation is a primary DfAM goal.
- Part Orientation:
- Concept: The orientation of the bracket on the build plate significantly impacts several factors:
- Support Needs: As mentioned above.
- Отделка поверхности: Upward-facing and vertical surfaces generally have better finish than downward-facing surfaces influenced by supports.
- Точность размеров: Thermal expansion/contraction effects can vary with orientation.
- Механические свойства: Anisotropy (direction-dependent properties) can occur in AM parts, although typically less pronounced in metals compared to polymers. Orientation might be chosen to align the strongest direction with the primary load path.
- Build Time & Cost: Taller builds generally take longer. Packing multiple brackets efficiently on a build plate depends on their orientation.
- Application to Brackets: Choosing the optimal orientation involves balancing these factors. For a bracket, orienting critical bores or mating surfaces vertically might yield better accuracy and finish, but could increase support needs or build height. Simulation tools and process expertise are used to determine the best compromise.
- Concept: The orientation of the bracket on the build plate significantly impacts several factors:
- Minimum Feature Sizes and Wall Thickness:
- Concept: AM processes have limitations on the minimum size of features (e.g., holes, pins, ribs) and the minimum thickness of walls they can reliably produce. These limits depend on the machine, material, and process parameters.
- Application to Brackets: Designs must respect these minimums. Very thin walls (<0.5mm, for example, depending on the process) might warp, fail to resolve fully, or be too fragile. Small features need to be designed large enough to be accurately formed by the laser or electron beam and the powder particle size. Wall thickness AM considerations are vital for structural integrity and printability.
- Соображения: Designing below minimum feature size leads to print failures or non-conforming parts. Consulting the AM provider’s design guidelines is essential.
- Консолидация частей:
- Concept: Actively look for opportunities to redesign assemblies of multiple simple parts into a single, more complex AM component.
- Application to Brackets: A bracket assembly might consist of a main body, separate clamps, and fasteners. DfAM encourages redesigning this into one monolithic bracket with integrated clamping features. This eliminates fasteners (potential failure points), reduces assembly time, simplifies inventory, and often saves weight.
- Соображения: Consolidated designs can be more complex to analyze and require careful thought about accessibility for installation and inspection. However, the benefits often outweigh these challenges.
- Generative Design:
- Concept: Similar to topology optimization but often broader, generative design aerospace tools allow engineers to input high-level requirements (loads, constraints, material, manufacturing method), and the software automatically generates multiple potential design solutions that meet the criteria. The engineer then selects the most suitable option based on performance, cost, or other factors.
- Application to Brackets: Can rapidly explore diverse, high-performing bracket design possibilities that a human designer might not conceive, pushing the boundaries of lightweighting and functional integration.
- Designing for Post-Processing:
- Concept: Consider how the part will be handled after printing. Will it require machining on specific surfaces? How will supports be removed from internal channels? Is access needed for inspection tools?
- Application to Brackets: Add extra stock material (machining allowance) on surfaces requiring high precision or specific finishes achievable only through CNC machining. Ensure internal channels are large enough for powder removal and potentially surface treatment. Design features that facilitate handling and inspection.
By applying these DfAM principles, aerospace engineers can move beyond simply substituting a traditionally manufactured bracket with a 3D printed one. They can create superior components – lighter, stronger, more integrated, and produced more efficiently – fully realizing the transformative potential of additive manufacturing for critical applications like custom pipe brackets for aerospace systems. Collaborating with AM experts, like the team at Met3dp who understand the nuances of different способы печати and material behaviors, is crucial for effective DfAM implementation.
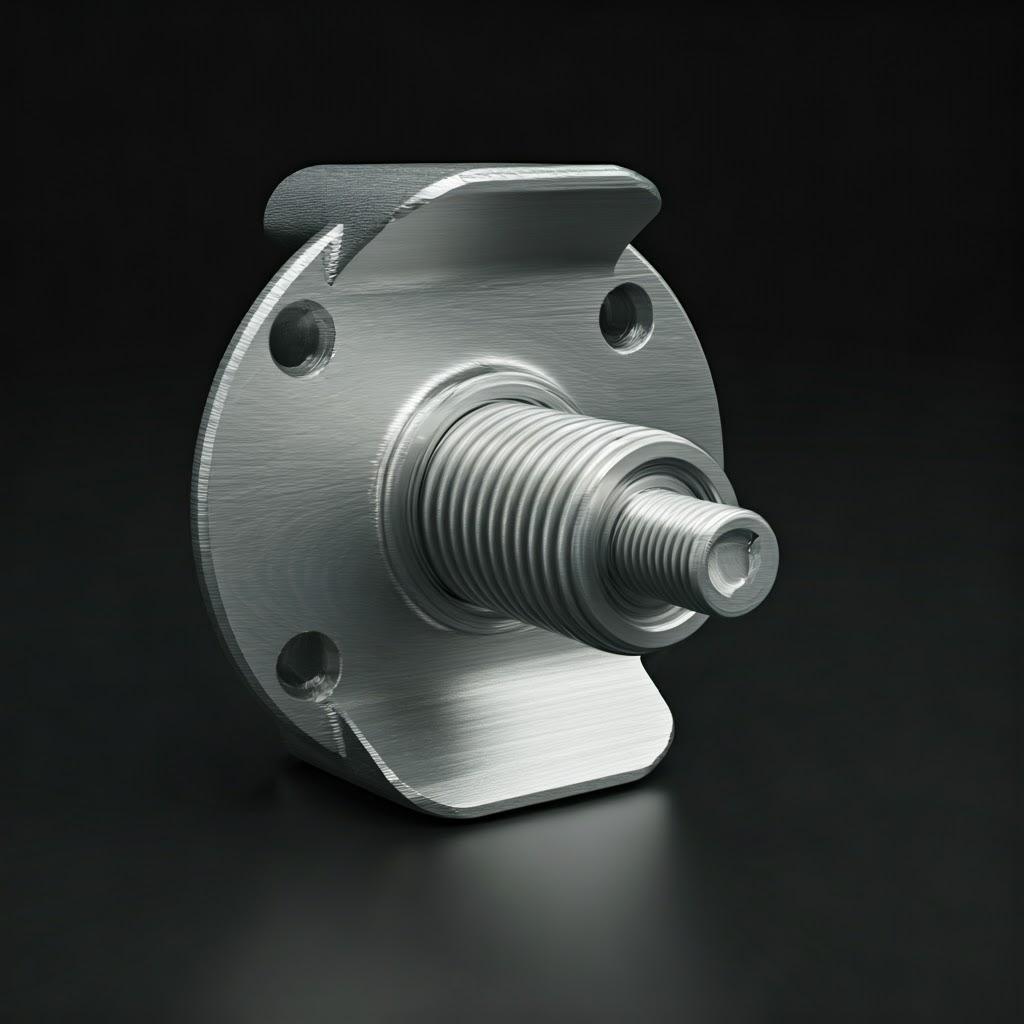
Achieving Precision: Tolerance, Surface Finish, and Accuracy in 3D Printed Brackets
While metal 3D printing offers incredible design freedom, a common question from engineers and procurement managers concerns the achievable precision: what level of tolerance, surface finish, and dimensional accuracy can be expected for components like aerospace pipe brackets? Understanding the capabilities and limitations of current metal AM technologies (primarily Laser Powder Bed Fusion – L-PBF/SLM and Electron Beam Powder Bed Fusion – EB-PBF/SEBM) is crucial for setting realistic expectations and determining necessary post-processing steps. Achieving the tight aerospace tolerances often required necessitates careful process control and often, secondary finishing operations.
Точность размеров:
- Определение: How closely the dimensions of the printed part match the nominal dimensions specified in the CAD model.
- Achievable Levels: Typical dimensional accuracy for metal PBF processes is often cited in the range of ±0.1 mm to ±0.2 mm for smaller features (e.g., up to 100 mm), or ±0.1% to ±0.2% of the nominal dimension for larger parts. However, this is a general guideline and can be influenced by:
- Part Size and Geometry: Larger parts and complex geometries are more susceptible to thermal distortion and deviation.
- Материал: Different materials have varying thermal expansion coefficients and shrinkage rates. Ti-6Al-4V, for instance, can be prone to residual stress and distortion if not managed properly.
- Калибровка машины: Printer accuracy and calibration play a significant role.
- Параметры процесса: Laser/beam power, scan speed, layer thickness, etc., affect melt pool stability and solidification, influencing accuracy.
- Part Orientation: As discussed in DfAM, orientation affects thermal gradients and potential warpage.
- Тепловое управление: Build plate heating, chamber atmosphere control, and scan strategies are employed to minimize distortion.
- Соображения: For critical dimensions requiring tighter tolerances than typically achievable “as-built” (e.g., bearing interfaces, precise mating surfaces), secondary CNC machining is usually required. Designating these critical features and adding machining allowance during the DfAM phase is essential. Achieving high dimensional accuracy 3D printing requires a holistic approach encompassing design, simulation, process control, and post-processing.
Обработка поверхности (шероховатость):
- Определение: The measure of the fine-scale irregularities on a part’s surface, often quantified by Ra (average roughness).
- As-Built Surface Finish: The surface finish of a metal AM part directly after printing and removal from the build plate (before support removal or other finishing).
- Характеристики: Generally rougher than machined surfaces. The roughness depends heavily on:
- Размер частиц: Finer powders can lead to smoother surfaces but may pose other challenges.
- Толщина слоя: Thinner layers typically result in smoother surfaces, especially on angled or curved faces (“stair-stepping” effect).
- Orientation: Vertical walls tend to be smoother than angled or horizontal surfaces. Downward-facing surfaces impacted by support structures are typically the roughest and show support witness marks.
- Параметры процесса: Energy density and melt pool characteristics influence surface texture. SEBM often produces slightly rougher surfaces than SLM due to powder sintering effects but can sometimes achieve better results on overhangs without support.
- Typical Values: As-built Ra values for metal PBF often range from 6 µm to 25 µm (240 µin to 1000 µin), but this can vary significantly.
- Характеристики: Generally rougher than machined surfaces. The roughness depends heavily on:
- Post-Processed Surface Finish: Various techniques can dramatically improve the surface finish metal AM parts:
- Abrasive Blasting (Bead/Sand Blasting): Provides a uniform matte finish, removes semi-sintered particles, but doesn’t significantly improve dimensional accuracy. Ra values might improve to 3-10 µm.
- Tumbling/Vibratory Finishing: Uses abrasive media in a tumbling barrel or vibratory bowl to smooth surfaces and deburr edges. Effective for batches of smaller parts. Can achieve Ra values down to 1-5 µm.
- CNC Machining: Offers the highest level of precision and surface finish on specific features. Can achieve Ra < 1 µm.
- Polishing (Manual or Automated): Can achieve mirror-like finishes (Ra < 0.1 µm) but is labor-intensive and typically reserved for specific requirements.
- Electropolishing: An electrochemical process that removes a thin layer of material, smoothing surfaces and improving corrosion resistance, particularly effective for stainless steels like 316L.
- Соображения: The required surface finish depends on the bracket’s function. Fluid-contact surfaces might need smoothness to reduce turbulence or prevent deposit buildup. Fatigue-critical areas benefit from smoother finishes to eliminate stress risers. Aesthetic requirements might also dictate a certain finish level. Specifying the required finish on drawings and discussing achievable levels with the AM provider is crucial.
Table: Typical Precision Capabilities of Metal PBF (Guideline Values)
Параметр | As-Built Capability | Post-Processed Capability (Method Dependent) | Примечания |
---|---|---|---|
Допуск на размеры | ±0.1 to ±0.2 mm or ±0.2% | < ±0.025 mm (via CNC Machining) | Highly dependent on size, geometry, material, process control |
Шероховатость поверхности (Ra) | 6 – 25 µm | < 1 µm (Machining), < 0.1 µm (Polishing) | Varies significantly with orientation, supports, and finishing method |
Минимальный размер элемента | ~0.3 – 0.5 mm | N/A (Determined by print process) | Machine and parameter dependent |
Минимальная толщина стенки | ~0.4 – 1.0 mm | N/A (Determined by print process) | Must be sufficient for structural integrity and printability |
Export to Sheets
Achieving Precision in Practice:
For demanding aerospace applications, achieving the required precision often involves a combination of:
- Process Simulation: Predicting thermal distortion and optimizing build layout/parameters before printing.
- Rigorous Process Control: Utilizing high-quality, consistent metal powders (like those produced by Met3dp using advanced atomization), maintaining precise machine calibration, and monitoring the build environment (atmosphere, temperature).
- Targeted Post-Processing: Applying machining, grinding, or other finishing techniques specifically to critical features and surfaces where tight tolerances or smooth finishes are mandated.
- Metrology and Inspection: Using advanced measurement techniques (CMM, 3D scanning) to verify dimensional accuracy and surface finish against specifications.
By understanding these factors, engineers can design brackets that are manufacturable within AM capabilities, and procurement managers can specify realistic aerospace tolerances and finishing requirements, ensuring the final 3D printed pipe brackets meet all functional and quality standards.
Post-Processing Pathways: Finishing Touches for Aerospace Brackets
Producing a metal pipe bracket layer-by-layer using additive manufacturing is only the first step in the manufacturing workflow. The “green” part, fresh off the build plate, almost always requires a series of post-processing steps to transform it into a flight-ready component that meets the stringent quality, performance, and safety standards of the aerospace industry. These steps are critical for relieving internal stresses, removing support structures, achieving required dimensional tolerances and surface finishes, and ensuring material integrity. Understanding the common требования к постобработке is essential for accurately estimating costs, lead times, and the final properties of 3D printed aerospace brackets.
Common Post-Processing Steps for Metal AM Aerospace Components:
- Stress Relief Heat Treatment:
- Цель: The rapid heating and cooling cycles inherent in PBF processes create significant residual stresses within the printed part. These stresses can cause distortion (especially after removal from the build plate) and negatively impact mechanical properties, particularly fatigue life. Stress relief involves heating the part (often while still attached to the build plate) to a specific temperature below the material’s transformation point, holding it for a set duration, and then cooling it slowly.
- Timing: Typically performed immediately after printing, before removing the part from the build plate, to prevent warping during removal.
- Соображения: The exact temperature and time depend heavily on the material (e.g., different cycles for 316L vs. Ti-6Al-4V) and part geometry. Controlled atmosphere furnaces (vacuum or inert gas) are often required, especially for reactive materials like titanium, to prevent oxidation.
- Снятие со строительной плиты:
- Method: Parts are typically separated from the build plate using wire electrical discharge machining (Wire EDM) or a bandsaw.
- Соображения: Care must be taken to avoid damaging the part. The separation method may leave a rough surface that requires subsequent finishing.
- Демонтаж опорной конструкции:
- Цель: Removing the temporary structures used to support overhangs and anchor the part during printing.
- Методы: Can range from simple manual breaking (for easily accessible, lightly sintered supports) to more involved mechanical removal using hand tools, pliers, CNC machining, or sometimes specialized chemical etching (less common for these materials).
- Соображения: This can be one of the most labor-intensive and potentially damaging steps if not planned carefully during the DfAM stage. Supports in internal channels or complex geometries can be particularly challenging to remove completely. Witness marks where supports contacted the part surface are common and may require blending or machining.
- Горячее изостатическое прессование (HIP):
- Цель: To eliminate internal microporosity (small voids) that can sometimes remain after the AM process. HIP subjects the part to high temperature (below melting point) and high isostatic pressure (using an inert gas like Argon) simultaneously. This pressure collapses internal voids, leading to a fully dense part (approaching 100% theoretical density).
- Преимущества: Significantly improves mechanical properties, particularly fatigue strength, fracture toughness, and ductility – often critical for аэрокосмические детали. Reduces variability in properties.
- Соображения: HIP is an additional process step adding cost and time. It’s often required for critical aerospace components, especially those made from fatigue-sensitive materials like Ti-6Al-4V. Part geometry must be able to withstand the pressure without distortion (minor dimensional changes can occur).
- Solution Annealing / Aging Heat Treatments (Material Specific):
- Цель: Beyond stress relief, further heat treatments may be required to achieve the desired final microstructure and mechanical properties (e.g., strength, hardness, ductility) specified for the alloy. For example, Ti-6Al-4V often undergoes solution treatment followed by aging to optimize its strength. 316L might be annealed to maximize corrosion resistance and ductility.
- Соображения: Конкретный heat treatment aerospace parts cycles depend entirely on the alloy and the target properties, following established aerospace material specifications (e.g., AMS standards). Requires calibrated furnaces with precise temperature control and often controlled atmospheres.
- CNC Machining:
- Цель: To achieve tight dimensional tolerances, precise geometric features (e.g., flat mating surfaces, accurately sized bores), and smooth surface finishes on specific critical areas that cannot be achieved by the as-built AM process.
- Применение: Commonly used for interfaces, mounting holes, sealing surfaces, and any dimension requiring tolerance tighter than ~ ±0.1 mm. CNC machining 3D prints requires careful fixture design to hold potentially complex AM geometries securely.
- Соображения: Requires adding machining allowance (extra material) to the relevant surfaces in the DfAM phase. Increases cost and lead time.
- Surface Finishing Techniques:
- Цель: To achieve the desired surface roughness, appearance, or to prepare the surface for subsequent coatings.
- Методы: As discussed previously, includes bead blasting, tumbling, polishing, electropolishing, etc. The choice depends on the required Ra value, part geometry, material, and cost constraints. Various surface finishing techniques offer different trade-offs.
- Соображения: Some finishing methods (e.g., tumbling) are better suited for batch processing, while others (machining, polishing) are feature-specific.
- Cleaning and Inspection:
- Цель: Removing any residual powder, cutting fluids, or debris. Verifying dimensional accuracy (e.g., CMM), surface finish, and internal integrity (e.g., CT scanning for porosity check, especially if HIP is not performed or for critical part validation). Non-destructive testing (NDT) methods are crucial.
- Соображения: Aerospace components require rigorous quality assurance (QA) and documentation. Inspection methods must be capable of assessing complex AM geometries.
Workflow Integration:
The specific sequence and combination of these post-processing steps depend heavily on the bracket’s design, material, and application requirements. A typical workflow might look like: Print -> Stress Relief -> Remove from Plate -> Support Removal -> (Optional HIP) -> Solution Anneal/Age -> Machining -> Surface Finishing -> Cleaning -> Final Inspection.
Partnering with a knowledgeable metal AM service provider who has established, certified processes for these post-processing steps is critical for ensuring that 3D printed aerospace pipe brackets meet all necessary specifications. Companies like Met3dp, focusing on integrated solutions from powder to finished part, understand the importance of this entire workflow for delivering reliable, high-quality aerospace components. Their expertise ensures that the potential unlocked during design is fully realized in the final, processed part.
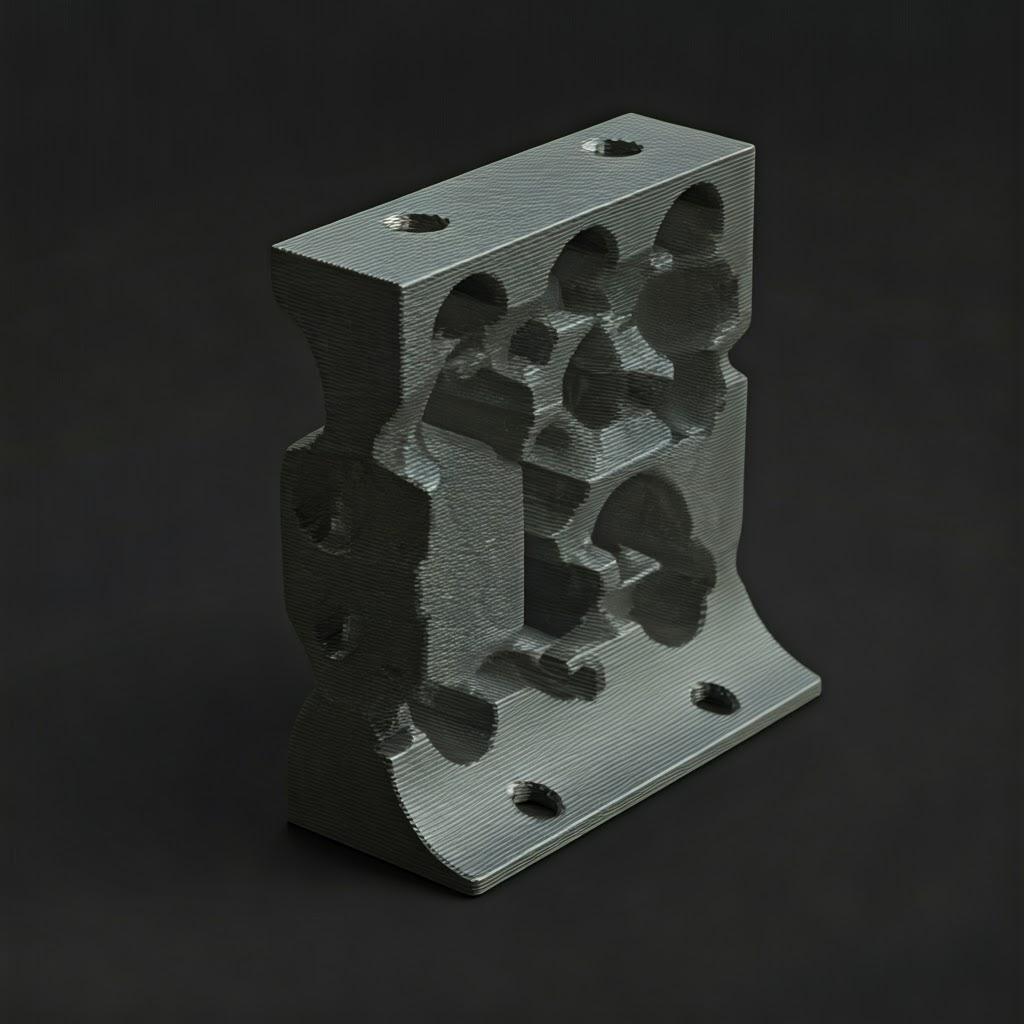
Overcoming Challenges: Mitigating Risks in Metal AM for Brackets
While metal additive manufacturing offers significant advantages for producing aerospace pipe brackets, the technology is not without its challenges. Understanding these potential pitfalls and the strategies used to mitigate them is crucial for successful implementation. Engineers designing parts and procurement managers selecting suppliers must be aware of these factors to ensure reliable, high-quality outcomes that meet stringent aerospace standards. Effective quality assurance AM protocols are paramount throughout the process.
Common Challenges and Mitigation Strategies:
- Warping and Distortion (Residual Stress):
- Вызов: The rapid, localized heating and cooling during PBF induces thermal gradients, leading to internal stresses. As these stresses build up, they can cause the part to warp or distort, especially thin sections or large flat areas, potentially pulling away from supports or the build plate. Warping metal 3D printing является первоочередной задачей.
- Mitigation Strategies:
- Thermal Simulation: Using software to predict stress accumulation and distortion based on geometry and scan strategy, allowing for adjustments before printing.
- Optimized Scan Strategies: Employing specific patterns (e.g., island scanning, alternating directions) to distribute heat more evenly and reduce localized stress buildup.
- Build Plate Heating: Maintaining an elevated temperature reduces the thermal gradient between the molten material and the surrounding part/plate.
- Effective Support Structures: Robustly designed supports anchor the part securely and help conduct heat away.
- Stress Relief Heat Treatment: Performing this step (often before plate removal) is critical to relax accumulated stresses.
- DfAM: Designing parts with features less prone to warping (e.g., avoiding large, unsupported flat areas, using gradual thickness transitions).
- Пористость:
- Вызов: Small voids or pores can form within the printed material due to incomplete fusion between layers (Lack of Fusion – LoF), gas becoming trapped in the melt pool (gas porosity), or material evaporation (keyholing). Porosity acts as stress concentrators, significantly degrading mechanical properties, especially fatigue life – a critical concern for aerospace.
- Mitigation Strategies:
- Optimized Process Parameters: Developing and strictly controlling parameters (laser/beam power, scan speed, hatch spacing, layer thickness) validated for the specific material and machine to ensure complete melting and fusion.
- High-Quality Powder: Using spherical, gas-free powder with consistent particle size distribution and flowability (a focus for powder manufacturers like Met3dp) is essential. Powder quality directly impacts melt pool stability and density.
- Controlled Atmosphere: Maintaining a high-purity inert gas environment (Argon or Nitrogen) in SLM or a high vacuum in SEBM minimizes oxidation and gas pickup by the melt pool.
- Горячее изостатическое прессование (HIP): As mentioned, HIP is highly effective at closing internal pores and achieving near-full density, often mandated for critical parts. Porosity control AM is a key function of HIP.
- Неразрушающий контроль (NDT): Using CT scanning or other NDT methods to detect and quantify internal porosity in finished parts.
- Support Removal Difficulties:
- Вызов: Supports, while necessary, can be difficult, time-consuming, and costly to remove, especially from complex internal geometries or delicate features. Improper removal can damage the part surface or leave behind residual material (stubs).
- Mitigation Strategies:
- DfAM for Support Reduction: Designing parts with self-supporting angles (>45°) where possible, using fillets, and orienting the part to minimize overhangs.
- Optimized Support Design: Using support types (e.g., tree supports, block supports with specific densities and perforation patterns) designed for easier breakaway or machining access. Software tools often automate optimized support generation.
- Process Parameter Control: Adjusting parameters at the interface between the support and the part to create a weaker connection for easier removal.
- Техники постобработки: Utilizing appropriate tools (manual, CNC, sometimes electrochemical methods) suited for the support type and location. Budgeting adequate time and resources for support removal.
- Surface Finish Limitations:
- Вызов: As-built surface roughness may not meet requirements for fluid dynamics, fatigue resistance, or mating interfaces. Downward-facing surfaces and areas affected by supports are particularly rough.
- Mitigation Strategies:
- Orientation and Parameter Optimization: Choosing build orientation and parameters (e.g., thinner layers) that favor better finish on critical surfaces.
- Targeted Post-Processing: Employing bead blasting, tumbling, machining, polishing, or electropolishing as needed to achieve the specified Ra value on functional surfaces (see previous section).
- DfAM: Designing critical surfaces in orientations (e.g., vertical) that naturally produce better finishes.
- Material Contamination and Powder Handling:
- Вызов: Metal powders, especially reactive ones like Ti-6Al-4V, can be contaminated by oxygen, nitrogen, or moisture if not handled properly. Cross-contamination between different alloy types in a shared machine can occur if cleaning procedures are inadequate. Powder degradation through repeated recycling can affect print quality.
- Mitigation Strategies:
- Strict Powder Handling Protocols: Storing powders in sealed containers with controlled humidity, using dedicated equipment for different material types, and employing closed-loop powder management systems.
- Atmosphere Control: Ensuring high purity of the inert gas or vacuum environment during printing.
- Powder Quality Management: Regularly testing and characterizing virgin and recycled powder (e.g., chemistry, particle size distribution, flowability) to ensure it remains within specification. Following supplier recommendations for powder reuse limits.
- Rigorous Machine Cleaning: Implementing thorough cleaning procedures when changing materials.
- Cost and Lead Time:
- Вызов: While offering long-term benefits, the initial cost per part for AM can sometimes be higher than traditional methods, especially for simpler brackets or very high volumes. Lead times include not just printing but also extensive post-processing.
- Mitigation Strategies:
- DfAM for Cost Reduction: Utilizing topology optimization to reduce material usage, minimizing support structures, and consolidating parts.
- Эффективность процесса: Optimizing build layouts to print multiple parts simultaneously (nesting), using appropriate layer thicknesses, and streamlining post-processing workflows.
- Strategic Application: Focusing AM on applications where its benefits (complexity, lightweighting, consolidation, rapid prototyping) provide the most value, justifying the cost (e.g., high-performance or custom brackets).
- Partnering with Experienced Suppliers: Working with providers who have optimized workflows and economies of scale can help manage costs.
Successfully implementing metal AM for aerospace pipe brackets requires a proactive approach to identifying and mitigating these challenges. It relies on a combination of smart design (DfAM), robust process control, diligent post-processing, and rigorous quality assurance. Partnering with experienced providers like Met3dp, who possess deep knowledge of materials, processes, and quality systems, significantly de-risks the adoption of this powerful technology for demanding aerospace applications.
Supplier Selection: Choosing the Right Metal 3D Printing Partner
Selecting the right manufacturing partner is paramount when sourcing critical components like aerospace pipe brackets produced via metal additive manufacturing. The unique complexities of AM processes, combined with the stringent requirements of the aerospace industry (safety, reliability, traceability), demand a supplier with specialized expertise, robust quality systems, and proven capabilities. For procurement managers, engineers, and supply chain professionals, evaluating potential metal AM service providers goes beyond just comparing quotes; it requires a thorough assessment of their technical proficiency, operational maturity, and commitment to quality. Making the right choice ensures access to high-quality parts, reliable delivery, and valuable technical support throughout the component lifecycle.
Key Criteria for Evaluating Aerospace 3D Printing Suppliers:
- Aerospace Certifications (AS9100):
- Importance: This is often a non-negotiable requirement. AS9100 is the internationally recognized Quality Management System (QMS) standard for the aviation, space, and defense industries. Certification demonstrates that the supplier has implemented rigorous processes for traceability, configuration management, risk management, process control, and continuous improvement, specifically tailored to aerospace demands.
- Action: Verify the supplier’s current AS9100 certification status and scope. Ask about their experience with specific customer or regulatory audits (e.g., FAA, EASA).
- Technical Expertise and Experience:
- Importance: Metal AM involves complex interplay between materials science, process physics, and design engineering. An experienced partner can provide valuable DfAM guidance, optimize build parameters, troubleshoot potential issues, and ensure process repeatability.
- Assessment:
- Engineering Support: Do they offer DfAM consultation? Can they assist with topology optimization or build simulation?
- Process Knowledge: How deep is their understanding of the specific AM processes they offer (SLM, SEBM, etc.) and the materials they process?
- Track Record: Do they have demonstrable experience producing similar aerospace components? Can they provide case studies or references (within confidentiality limits)?
- Team Credentials: What is the experience level of their engineers, metallurgists, and machine operators?
- Material Capabilities and Quality:
- Importance: The supplier must be proficient in processing the specific aerospace-grade alloys required for your bracket (e.g., Ti-6Al-4V aerospace, 316L, Inconel). Crucially, they must have robust procedures for ensuring the quality and consistency of the metal powder feedstock.
- Assessment:
- Портфель материалов: Do they offer the required alloys? Are these materials certified to relevant aerospace specifications (e.g., AMS standards)?
- Powder Sourcing & Management: Where do they source their powders? Do they have internal powder production or stringent incoming quality checks? How do they handle, store, and recycle powders to prevent contamination and ensure traceability? (Suppliers like Met3dp, who emphasize their advanced powder manufacturing systems like gas atomization and PREP, demonstrate a strong commitment to foundational material quality).
- Material Characterization: Do they have capabilities for testing material properties (tensile, fatigue, chemistry) of printed samples?
- Equipment and Facilities:
- Importance: The quality, calibration, and maintenance of the AM machines directly impact part quality and consistency. The overall facility layout should support efficient workflow and prevent contamination.
- Assessment:
- Machine Fleet: What specific types and models of metal AM machines do they operate (e.g., SLM, SEBM)? Are these industrial-grade machines known for reliability? What is the build volume capability? (Knowing if a supplier uses industry-leading equipment, potentially including systems like those developed by Met3dp, can indicate a commitment to state-of-the-art production).
- Machine Maintenance & Calibration: What are their procedures for regular maintenance and calibration to ensure accuracy and repeatability?
- Facility Controls: Are environmental conditions (temperature, humidity) controlled? Are procedures in place to prevent cross-contamination between materials?
- Post-Processing Capabilities:
- Importance: As discussed, post-processing is critical. An ideal supplier either has comprehensive in-house capabilities (heat treatment, machining, finishing, inspection) or well-managed relationships with certified external partners.
- Assessment:
- In-House vs. Outsourced: What post-processing steps can they perform in-house? Which are outsourced, and how do they manage the quality and traceability of outsourced processes?
- Specific Capabilities: Do they possess the necessary equipment (e.g., vacuum furnaces for heat treatment, multi-axis CNC machines, NDT equipment)?
- Управление процессом: Are post-processing steps governed by documented procedures and quality controls?
- Quality Management System (QMS) and Traceability:
- Importance: Beyond AS9100, the supplier’s overall QMS must ensure end-to-end traceability – from raw powder batch to finished, inspected part. This is critical for aerospace compliance and root cause analysis if issues arise.
- Assessment:
- Documentation: Review their quality manual and standard operating procedures (SOPs).
- Traceability: How do they track material batches, machine usage, process parameters, post-processing steps, and inspection results for each part produced?
- Non-Conformance Handling: What are their procedures for identifying, documenting, and addressing non-conforming parts?
- Lead Time, Capacity, and Communication:
- Importance: The supplier must be able to meet required lead times and have sufficient capacity for production volumes. Clear and responsive communication is vital for managing projects effectively. Lead time evaluation имеет решающее значение.
- Assessment:
- Quoted Lead Times: Are their quoted lead times realistic, considering printing and all post-processing steps?
- Производственная мощность: Can they handle potential fluctuations in demand or scale up for larger orders?
- Communication: Who are the primary points of contact? How responsive are they to inquiries and technical questions?
Table: Supplier Evaluation Checklist Summary
Критерии | Основные вопросы | Ideal Supplier Attributes |
---|---|---|
Сертификаты | AS9100 certified? Scope relevant? Experience with audits? | Current AS9100 certification; proven audit success. |
Техническая экспертиза | DfAM support? Process/material knowledge? Aerospace track record? Team experience? | Strong engineering team; documented experience; offers DfAM consultation. |
Материальные возможности | Required alloys offered/certified? Powder sourcing/QA procedures? Powder handling/recycling protocols? Material testing capability? | Certified aerospace materials; stringent powder quality control (potentially in-house production); robust handling/recycling; material test data. |
Equipment & Facilities | Industrial-grade machines? Relevant build volume? Calibration/maintenance program? Facility controls (environment, contamination)? | Well-maintained, calibrated industrial printers; controlled environment; clear material segregation. |
Постобработка | In-house vs. outsourced capabilities (heat treat, machining, NDT)? Equipment suitability? Process control? | Comprehensive in-house or tightly controlled/certified external capabilities; documented procedures. |
QMS & Traceability | Documented QMS? End-to-end traceability system (powder to part)? Non-conformance process? | Robust QMS; digital or rigorous manual traceability; clear NCR process. |
Commercials & Logistics | Realistic lead times? Sufficient capacity? Responsive communication? Geographic location factors? | Reliable lead time quoting; scalable capacity; clear communication channels. |
Export to Sheets
Choosing a partner like Met3dp, which emphasizes its position as a leading provider of comprehensive additive manufacturing solutions including high-performance powders and advanced printing systems, aligns well with these criteria. Their focus on industry-leading technology and collective expertise positions them as a capable aerospace 3D printing supplier. Ultimately, a thorough evaluation using these criteria will help identify a metal AM service provider who can reliably deliver high-quality, compliant 3D printed aerospace pipe brackets, fostering a successful long-term partnership.
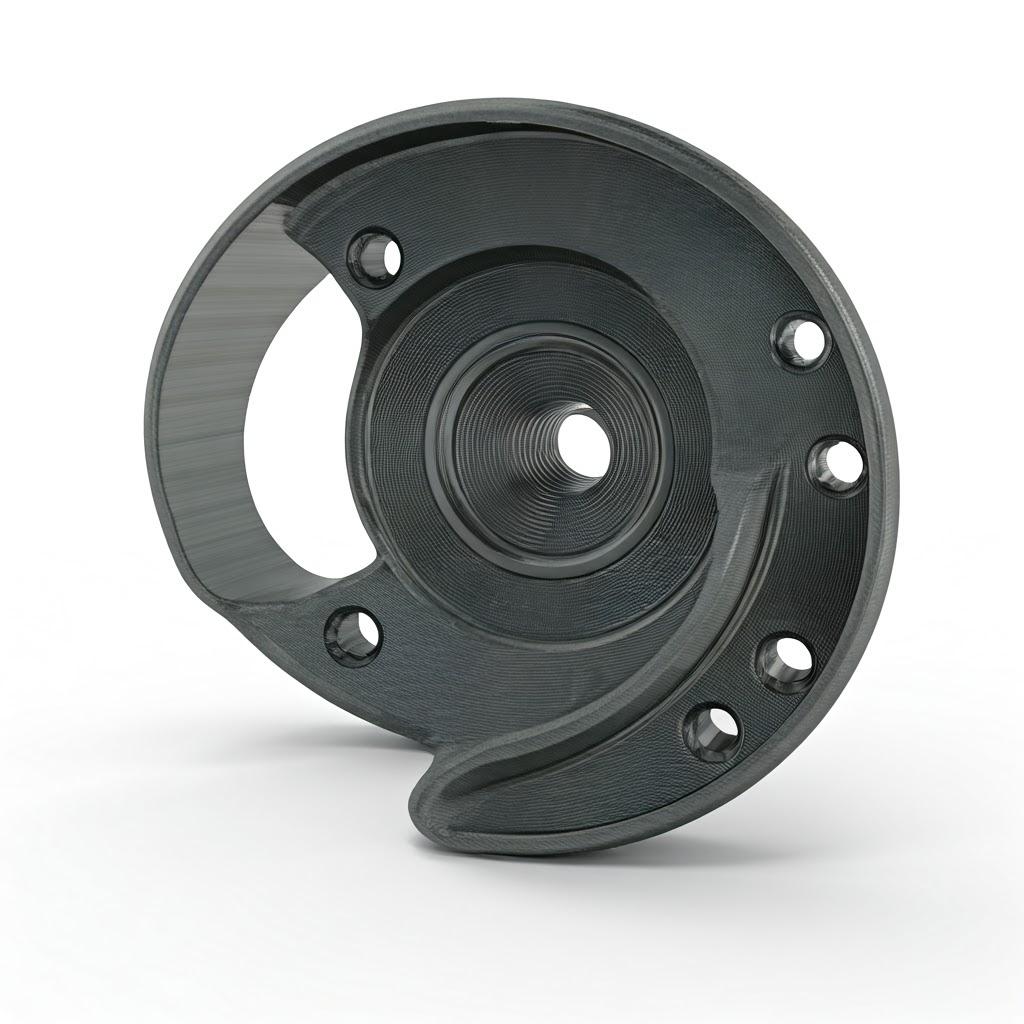
Cost Dynamics & Lead Times: Budgeting for 3D Printed Aerospace Brackets
Understanding the factors that influence the cost and lead time of 3D printed metal aerospace pipe brackets is essential for accurate budgeting, project planning, and evaluating the economic feasibility of using AM compared to traditional methods. While AM offers compelling technical advantages, procurement managers and engineers need a clear picture of the metal 3D printing cost factors and typical production timelines. The cost is not solely based on material weight; it’s a complex interplay of design, process, material, and post-processing requirements.
Factors Influencing Cost:
- Material Type and Consumption:
- Стоимость материала: High-performance aerospace alloys like Ti-6Al-4V or nickel superalloys are inherently more expensive than materials like 316L stainless steel. The raw powder cost is a significant input.
- Part Volume & Weight: Larger or heavier brackets naturally consume more material, directly increasing cost. However, thanks to topology optimization, AM can often significantly reduce the volume compared to machined parts, partially offsetting higher material costs per kilogram.
- Support Structure Volume: Material used for support structures also adds to the cost. Minimizing supports through DfAM is crucial for cost efficiency.
- Powder Recycling Efficiency: The supplier’s ability to safely and effectively recycle unused powder impacts overall material cost efficiency.
- Part Complexity and Design:
- Geometric Complexity: While AM excels at complexity, extremely intricate designs might require more complex support structures or longer print times, potentially increasing cost slightly. However, the primary benefit is enabling complexity that would be prohibitively expensive or impossible with traditional methods.
- Minimum Feature Size & Wall Thickness: Designing features close to the process limits may require slower print speeds or specialized parameters, potentially impacting cost.
- Topology Optimization: While the goal is weight reduction, the initial software and engineering effort for optimization might be factored into the cost for bespoke designs.
- Print Time (Machine Utilization):
- Build Height: Taller parts generally take longer to print as more layers are required.
- Part Volume: Larger volume parts take longer to scan and fuse.
- Number of Parts per Build (Nesting): Printing multiple brackets simultaneously on a single build plate utilizes the machine more efficiently, reducing the cost per part compared to printing individually. Efficient nesting is key for production runs.
- Layer Thickness & Parameters: Thinner layers improve resolution but increase print time. Optimized parameters balance speed and quality.
- Support Structure Requirements:
- Volume & Complexity: As mentioned, supports consume material and machine time.
- Removal Effort: Complex or extensive supports require significant manual labor or machining time for removal, adding considerably to post-processing costs. DfAM focusing on support minimization directly reduces this cost component.
- Требования к постобработке:
- Heat Treatments: Stress relief, HIP, annealing/aging all require specialized furnaces, energy, and time, adding significant cost, especially HIP.
- Обработка: CNC machining specific features requires machine time, tooling, programming, and labor. The extent of machining needed is a major cost driver.
- Отделка поверхности: Techniques like blasting, tumbling, or polishing add labor and consumables costs. High-end finishes (e.g., mirror polishing) can be very expensive.
- Труд: Many post-processing steps (support removal, manual finishing) are labor-intensive.
- Quality Assurance and Inspection:
- NDT Requirements: Non-destructive testing like CT scanning or FPI (Fluorescent Penetrant Inspection) adds equipment/service costs and time. The level of inspection mandated by aerospace standards influences the final price.
- Documentation: Creating the extensive documentation package required for aerospace traceability (material certs, build logs, inspection reports) involves administrative overhead.
- Объем заказа:
- Экономия на масштабе: As with most manufacturing, higher volumes generally lead to lower cost per part analysis due to setup cost amortization, optimized nesting, and streamlined workflows. However, AM’s advantage lies in its cost-effectiveness even at lower volumes compared to tooling-intensive traditional methods.
Factors Influencing Lead Time:
Lead time for a 3D printed aerospace bracket encompasses the entire workflow, not just the printing itself. AM production lead time can vary significantly based on complexity and requirements.
- Design & Preparation: File preparation, build simulation, support generation. (Typically 1-3 days)
- Queue Time: Waiting for machine availability, especially for specialized machines or materials. (Highly variable: days to weeks)
- Печать: Actual time on the machine. (Hours to several days, depending on size, height, quantity).
- Cool Down: Allowing the build chamber and part to cool before removal. (Several hours)
- Постобработка: This often constitutes the majority of the total lead time.
- Stress Relief/Heat Treatments: Furnace time, including ramp-up, soak, and cool-down. (1-3 days per cycle)
- Removal from Plate & Support Removal: (Hours to days, depending on complexity)
- HIP: Requires specialized facilities, batching often needed. (Can add 3-7 days)
- CNC Machining: Dependent on complexity and machine availability. (Days)
- Surface Finishing: (Hours to days)
- Inspection & QA: (1-3 days)
- Перевозки: Transit time to the customer.
Typical Lead Times:
- Prototypes (minimal post-processing): 1-2 недели
- Functional Parts (standard post-processing, no HIP): 2-4 недели
- Production Parts (including HIP, extensive machining, full QA): 4-8 weeks or longer
Table: Cost & Lead Time Driver Summary
Фактор | Влияние на стоимость | Impact on Lead Time | Mitigation/Optimization Strategy |
---|---|---|---|
Материал | High (esp. Ti, Ni alloys) | Низкий | Select appropriate material; optimize design for volume reduction. |
Part Volume/Complexity | Moderate (material use); Low (complexity enabling) | Moderate (print time) | Topology optimization; DfAM for printability. |
Print Time | High (machine amortization) | Moderate-High (direct impact) | Optimize nesting; balance layer thickness & speed. |
Вспомогательные структуры | Moderate (material); High (removal labor) | Moderate (removal time) | DfAM to minimize supports; optimize support design. |
Post-Processing (General) | Very High (multiple steps, labor, equipment) | Very High (often the longest phase) | Specify only necessary steps; optimize workflow; DfAM for finishing. |
HIP | High (specialized process) | Moderate (batching, cycle time) | Use only when required for material properties (e.g., fatigue). |
Обработка с ЧПУ | High (if extensive) | Умеренно-высокий | DfAM to minimize machining needs; add machining allowance. |
QA & Inspection | Умеренно-высокий | Умеренный | Specify appropriate NDT level; streamline documentation. |
Объем | Lower per part at higher volumes | Setup time amortized; potential for longer total run | Batch production runs; long-term agreements. |
Export to Sheets
By understanding these dynamics, stakeholders can have informed discussions with suppliers like Met3dp about aerospace component pricing and delivery schedules. Providing clear specifications, leveraging DfAM, and collaborating closely with the manufacturing partner are key to managing costs and achieving predictable lead times for 3D printed aerospace components. Exploring the range of продукты and solutions offered by experienced providers can also help in assessing capabilities relevant to specific cost and timeline requirements.
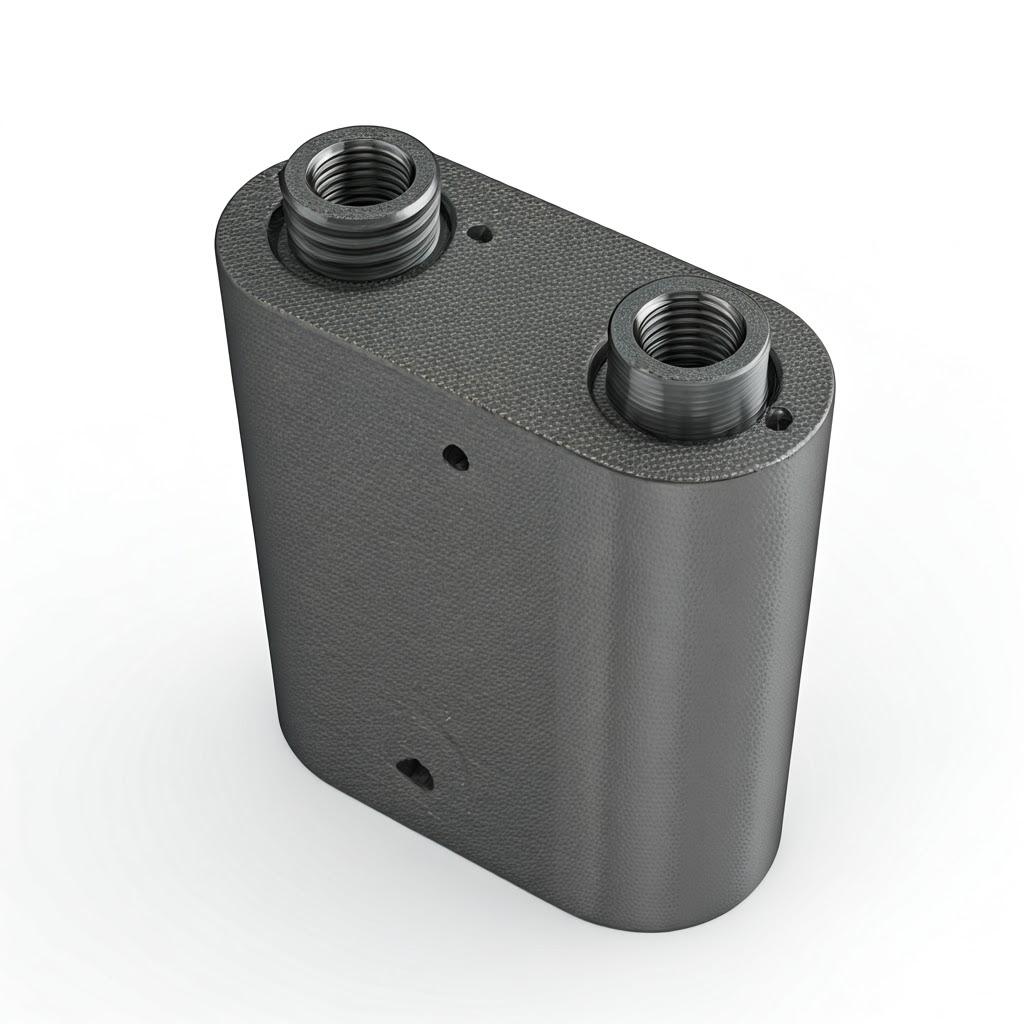
Frequently Asked Questions (FAQ) about 3D Printed Aerospace Pipe Brackets
Here are some common questions engineers, designers, and procurement managers have when considering metal additive manufacturing for aerospace pipe brackets:
- Can 3D printed metal brackets be certified for flight like traditionally manufactured parts?
- Ответ: Yes, absolutely. Achieving flight certification for 3D printed components involves a rigorous process focused on demonstrating equivalence or superiority to existing certified parts. This requires:
- Mature Process Control: Using qualified machines, validated process parameters, and consistent, high-quality feedstock (like certified Ti-6Al-4V or 316L powders).
- Material Characterization: Extensive testing to establish a statistically significant database of mechanical properties (tensile, fatigue, fracture toughness) for the specific material and AM process combination, often adhering to standards like MMPDS (Metallic Materials Properties Development and Standardization).
- Robust Quality Management: Adherence to aerospace standards like AS9100, ensuring full traceability from powder batch to final part.
- Process Specification: Having a locked-down, documented manufacturing process, including all printing and post-processing steps.
- Неразрушающий контроль (NDT): Rigorous inspection (e.g., CT scanning) to verify internal integrity and absence of critical defects.
- Part-Specific Qualification: Often involves testing final parts under representative load conditions. Many 3D printed components, including brackets, are already flying on commercial and military aircraft, as well as spacecraft, having successfully passed certification requirements set by bodies like the FAA and EASA. Partnering with an experienced aerospace 3D printing supplier with a strong QMS is crucial for navigating the certification pathway.
- Ответ: Yes, absolutely. Achieving flight certification for 3D printed components involves a rigorous process focused on demonstrating equivalence or superiority to existing certified parts. This requires:
- When should I choose Ti-6Al-4V versus 316L Stainless Steel for my pipe bracket?
- Ответ: The choice primarily depends on the specific application requirements, balancing performance and cost:
- Choose Ti-6Al-4V if:
- Weight saving is critical: Titanium’s high strength-to-weight ratio is its main advantage (~45% lighter than steel for similar strength).
- Operating temperatures are high: Ti-6Al-4V generally performs well up to ~400°C.
- Specific corrosion environments demand it: While both are corrosion-resistant, titanium excels in certain conditions (e.g., seawater).
- High fatigue strength is essential in a weight-sensitive design.
- Choose 316L Stainless Steel if:
- Cost is a major driver: 316L powder and processing are typically less expensive than Ti-6Al-4V.
- Operating temperatures are moderate: Generally suitable below ~400-500°C.
- Exceptional ductility is needed: 316L is typically more ductile than Ti-6Al-4V.
- Weight is less critical for the specific application.
- Good general corrosion resistance is sufficient. Consulting material datasheets for parts produced via AM (as properties can differ from wrought materials) and discussing the operating environment with a material expert or AM provider is recommended for making the final selection. Ti-6Al-4V printing questions often revolve around managing its reactivity and post-processing needs compared to the more forgiving 316L.
- Choose Ti-6Al-4V if:
- Ответ: The choice primarily depends on the specific application requirements, balancing performance and cost:
- Is 3D printing always the best option for aerospace brackets? When does traditional manufacturing still make sense?
- Ответ: Metal 3D printing is a powerful tool, but not always the optimal solution. Consider the following:
- Choose 3D Printing (AM) when:
- High geometric complexity is required (e.g., topology optimized shapes, internal channels, conformal designs).
- Significant weight reduction is a primary goal.
- Объединение частей (reducing assembly complexity) offers significant benefits.
- Быстрое прототипирование and fast design iteration are needed.
- Low to medium production volumes are anticipated (avoids high tooling costs).
- Производство по требованию for MRO or spare parts is valuable.
- Персонализация is required for specific installations.
- Traditional Manufacturing (e.g., CNC Machining, Sheet Metal Forming) may still be better when:
- The bracket design is very simple and can be easily machined from stock or formed from sheet.
- Extremely high production volumes are required (where tooling costs can be amortized effectively).
- The lowest possible cost is the absolute priority for a simple, non-weight-critical part.
- Existing tooling and processes are already established and highly efficient for a legacy part (unless AM offers clear performance/weight benefits).
- Materials not easily processed by AM are required (though the range of AM materials is constantly expanding). A careful cost-benefit analysis, considering design complexity, performance requirements (especially weight), volume, lead time, and the total cost of ownership (including assembly and potential downstream benefits), should guide the decision between AM and traditional methods for any given custom bracket inquiry.
- Choose 3D Printing (AM) when:
- Ответ: Metal 3D printing is a powerful tool, but not always the optimal solution. Consider the following:
Conclusion: The Future of Aerospace Component Manufacturing is Additive
The journey through the design, material selection, manufacturing, and qualification of custom pipe brackets for aerospace systems via 3D printing highlights the transformative impact of additive manufacturing on the aerospace industry. Metal AM is no longer an experimental technology but a mature, viable, and increasingly preferred solution for producing complex, high-performance components where weight reduction, design optimization, and accelerated innovation are paramount. Pipe brackets, though seemingly simple, exemplify the advantages AM brings: enabling topology-optimized, lightweight structures; consolidating multi-part assemblies into single, robust units; and facilitating on-demand production for both new platforms and critical MRO operations.
Leveraging advanced materials like the workhorse 316L нержавеющая сталь for its robustness and corrosion resistance, or the high-performance Ti-6Al-4V for its exceptional strength-to-weight ratio, allows engineers to tailor bracket solutions precisely to the demanding environments found within aircraft and spacecraft. The key to success lies in embracing Design for Additive Manufacturing (DfAM) principles, understanding the nuances of precision and surface finish achievable, navigating the necessary post-processing pathways, and proactively mitigating potential manufacturing challenges through rigorous process control and quality assurance.
Choosing the right manufacturing partner – one with proven aerospace credentials (like AS9100 certification), deep technical expertise, high-quality equipment, robust material controls, and comprehensive post-processing capabilities – is critical. Companies like Met3dp, which position themselves as leaders in both advanced metal powders and industrial AM systems, represent the integrated approach needed to reliably deliver flight-ready components. Their commitment to industry-leading technologies, from powder production to printing equipment, underpins the quality and reliability essential for digital manufacturing aerospace решения.
While cost and lead time require careful consideration, the strategic application of metal AM for components like pipe brackets often yields significant benefits that outweigh the initial investment, contributing to more fuel-efficient aircraft, higher payload capacities for launch vehicles, and more responsive aerospace supply chains. The future additive manufacturing holds for aerospace is one of greater design freedom, enhanced performance, increased operational efficiency, and continued innovation. As the technology evolves and adoption grows, 3D printed components will become increasingly integral to the structures taking flight, pushing the boundaries of what’s possible in aerospace engineering. Partnering with forward-thinking solution providers is key to unlocking this potential and shaping the future of flight.
Поделиться
MET3DP Technology Co., LTD - ведущий поставщик решений для аддитивного производства со штаб-квартирой в Циндао, Китай. Наша компания специализируется на производстве оборудования для 3D-печати и высокопроизводительных металлических порошков для промышленного применения.
Сделайте запрос, чтобы получить лучшую цену и индивидуальное решение для вашего бизнеса!
Похожие статьи
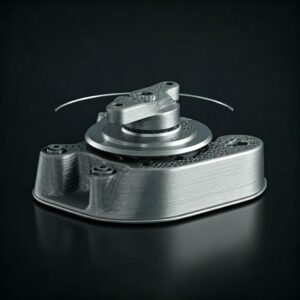
3D-печатные крепления для автомобильных радарных датчиков: Точность и производительность
Читать далее "О компании Met3DP
Последние обновления
Наш продукт
CONTACT US
Есть вопросы? Отправьте нам сообщение прямо сейчас! После получения Вашего сообщения мы всей командой выполним Ваш запрос.
Получите информацию о Metal3DP
Брошюра о продукции
Получить последние продукты и прайс-лист
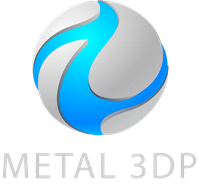
Металлические порошки для 3D-печати и аддитивного производства