Lightweight Instrument Panels via Additive Manufacturing
Оглавление
Introduction: Revolutionizing Aerospace Cockpits with Metal AM
The aerospace instrument panel, often referred to as the flight deck or cockpit dashboard, serves as the nerve center of any aircraft. It’s the critical interface between the pilot, the machine, and the environment, housing essential flight instruments, navigation displays, control switches, and warning systems. The clarity, reliability, and functionality of this panel are paramount to flight safety and mission success. For decades, the design and manufacture of these crucial components have relied on traditional methods like CNC machining of aluminum plates, sheet metal fabrication, and intricate assembly processes involving numerous fasteners, brackets, and individual components. While reliable, these conventional approaches often face significant limitations in the face of evolving aerospace demands.
The relentless drive for greater fuel efficiency, increased payload capacity, enhanced performance, and reduced environmental impact forces aerospace engineers and procurement managers to seek innovative solutions. Weight reduction is a primary objective, as every kilogram saved translates directly into lower operating costs and improved capabilities. Traditional manufacturing methods often result in panels that are heavier than necessary, constrained by the limitations of subtractive processes and the need for bulky assemblies. Furthermore, the complexity of modern avionics requires intricate panel designs to accommodate sophisticated electronic systems, wiring harnesses, and cooling requirements, often pushing traditional fabrication techniques to their limits in terms of design freedom and integration possibilities. Lead times associated with tooling, setup, and multi-stage assembly can also hinder rapid development cycles and customization efforts.
Входить аддитивное производство металлов (AM), also known as metal 3D-печать. This transformative technology is rapidly moving beyond prototyping into the realm of functional end-use parts, particularly within the demanding aerospace sector. Metal AM builds components layer by layer directly from digital models using high-performance metal powders. This approach fundamentally changes the design and manufacturing paradigm, offering unprecedented opportunities to overcome the limitations of traditional methods. For aerospace instrument panels, metal AM enables the creation of highly optimized, lightweight structures with complex geometries and integrated functionalities that were previously unattainable. It represents a significant leap forward, promising to revolutionize cockpit design and contribute substantially to the next generation of aircraft performance and efficiency. Companies specializing in металлическая 3D-печать are at the forefront of this revolution, providing the technology and expertise needed to realize these advanced designs.
Core Applications: Where Metal AM Instrument Panels Excel
The application of metal additive manufacturing for instrument panels extends across the entire spectrum of aerospace, offering tailored benefits for various platforms and missions. The ability to customize designs, reduce weight, and integrate complex features makes AM particularly valuable where performance and efficiency are critical.
Key Application Areas:
- Commercial Aviation: In commercial airliners, weight reduction is paramount for fuel efficiency. Metal AM allows airlines and OEMs (Original Equipment Manufacturers) to replace traditionally heavier panel assemblies with lighter, topologically optimized versions. This contributes directly to lower fuel burn over the aircraft’s lifespan. Furthermore, the design freedom allows for improved ergonomics, better integration of large-format displays, and potentially simplified maintenance access through consolidated designs. Procurement managers benefit from potentially shorter lead times for customized cockpit configurations or replacement parts compared to traditional supply chains reliant on extensive tooling.
- Defense Aircraft (Fighter Jets, Military Transport, Helicopters): Military platforms demand high performance, structural integrity, and resilience under extreme conditions. Metal AM enables the production of instrument panels that are not only lightweight but also exceptionally strong and durable, often using high-strength alloys like Scalmalloy®. The ability to integrate features like embedded cooling channels for heat-generating avionics or internal structural reinforcements optimized for specific load paths is crucial. Part consolidation reduces potential failure points and simplifies logistics in demanding operational environments. B2B suppliers specializing in defense manufacturing find AM a powerful tool for meeting stringent military specifications (Mil-Spec) and delivering mission-critical components.
- Space Exploration Vehicles (Satellites, Launch Vehicles, Landers, Habitats): In space applications, mass is arguably the most critical constraint. Every gram launched into orbit costs thousands of dollars. Metal AM provides an unparalleled advantage in creating ultra-lightweight yet robust instrument panels and control interfaces for spacecraft. The technology allows for intricate designs optimized for minimal mass while maintaining structural integrity during launch vibrations and operation in harsh space environments (radiation, thermal cycling). Companies supplying components for space systems leverage AM for producing highly specialized, low-volume parts without the prohibitive costs of traditional tooling. Examples include control panels for rovers, mounting structures for sensors within satellites, and interfaces within crewed capsules.
- Unmanned Aerial Vehicles (UAVs / Drones): The rapidly growing UAV market, from small surveillance drones to large autonomous cargo carriers, benefits immensely from lightweight components. AM-produced instrument panels or control system housings contribute to longer flight times, increased payload capacity, and enhanced maneuverability. The ability to rapidly prototype and iterate designs is also crucial in this fast-evolving sector. B2B suppliers providing UAV components can utilize metal AM to offer customized, high-performance solutions to drone manufacturers.
Specific Functions Enhanced by AM:
- Structural Support: Moving beyond simple plates, AM allows panels to be designed as complex space frames or shells, providing structural support for displays and switches while minimizing material usage.
- Housing Electronics: Panels can be designed with integrated mounting bosses, snap-fits, and enclosures specifically contoured to house complex avionics packages securely and efficiently.
- Integrated Cooling: Complex internal channels can be designed and printed directly into the panel structure to provide air or liquid cooling paths for heat-sensitive electronics, eliminating the need for separate cooling plates and assemblies.
- Ergonomic Designs: AM enables the creation of curved and organically shaped panels that improve pilot comfort, visibility, and interaction with controls, which is difficult and costly to achieve with traditional machining.
- Vibration Dampening: Lattice structures, specifically designed using AM, can be incorporated into the panel’s internal structure to help dampen vibrations, protecting sensitive instruments and improving readability.
By leveraging metal AM, aerospace manufacturers and their B2B suppliers can produce instrument panels that are lighter, stronger, more functional, and often faster to develop, meeting the exacting demands of modern aerospace applications.
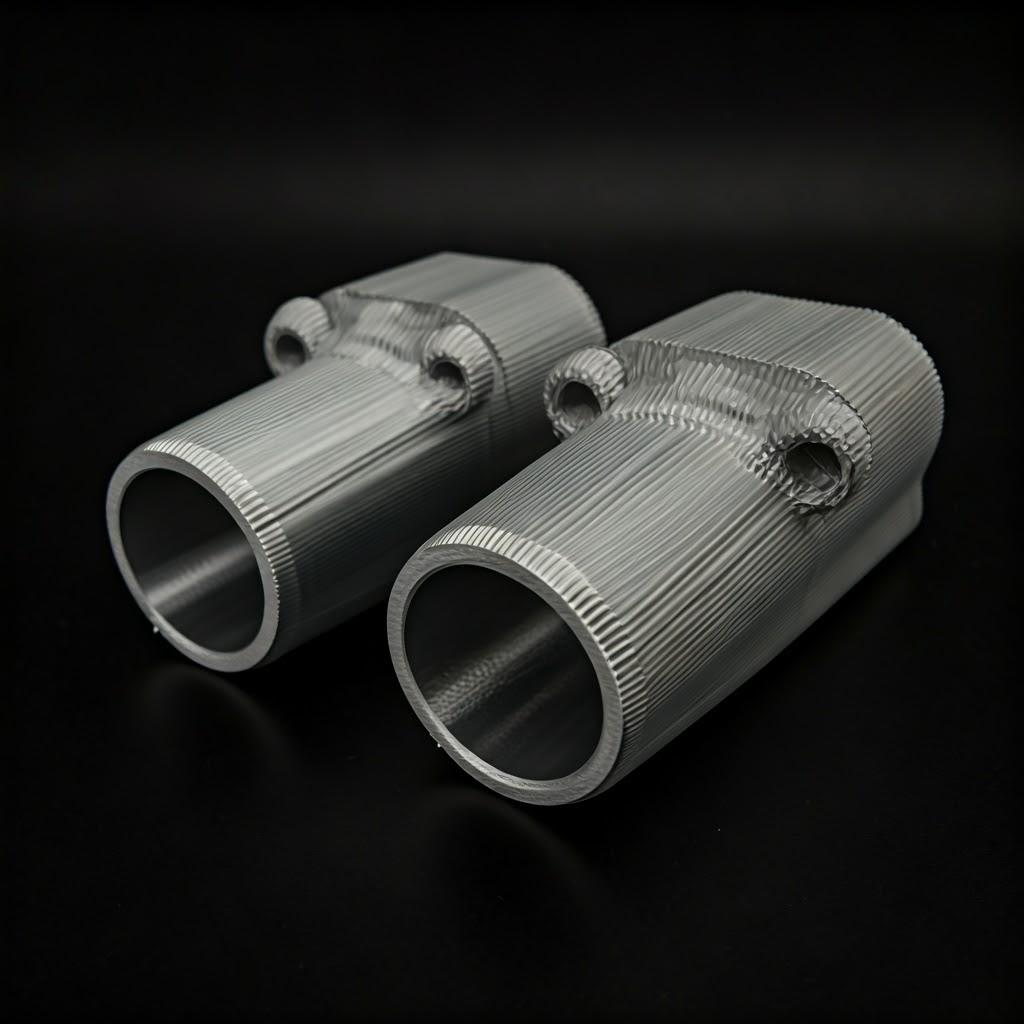
The Additive Advantage: Why Choose Metal 3D Printing for Instrument Panels?
Opting for metal additive manufacturing over traditional techniques like CNC machining or sheet metal fabrication for aerospace instrument panels isn’t just a novel approach; it offers tangible engineering and business advantages that directly address key industry challenges. Procurement managers, design engineers, and aerospace manufacturers are increasingly turning to metal AM due to its compelling value proposition:
- Significant Weight Reduction: This is often the primary driver. Metal AM enables advanced design techniques like:
- Topology Optimization: Software algorithms identify where material is structurally necessary to withstand specific loads, removing excess material from non-critical areas. This results in organic-looking, highly efficient structures.
- Решетчатые структуры: Internal lattices (honeycomb, gyroid, stochastic foams) can replace solid sections, dramatically reducing weight while maintaining desired stiffness and structural integrity.
- Result: Weight savings of 30-60% or even more are often achievable compared to traditionally manufactured counterparts, leading to significant fuel savings or increased payload capacity over the aircraft’s lifecycle.
- Консолидация частей: Complex assemblies involving multiple components (panels, brackets, supports, fasteners) can often be redesigned and printed as a single, monolithic part.
- Преимущества: Reduces assembly time and labor costs, eliminates potential failure points at joints and interfaces, simplifies inventory management and supply chain logistics, and inherently improves structural integrity.
- Беспрецедентная свобода дизайна: AM builds parts layer by layer, freeing designers from many constraints imposed by traditional methods (e.g., tool access for CNC, draw limitations in stamping).
- Capabilities: Enables highly complex geometries, internal channels (for cooling, wiring), conformal shapes matching aircraft contours, negative draft angles, and intricate surface details. This allows for greater functional integration and optimized packaging of electronics and controls.
- Быстрое создание прототипов и итерации: Creating prototypes of instrument panels using traditional methods often requires significant time and investment in tooling or complex machining setups.
- AM Speed: Metal AM allows engineers to quickly produce functional prototypes directly from CAD models, test them, identify improvements, and iterate designs in days or weeks rather than months. This accelerates the development cycle and facilitates design optimization early in the process.
- Сокращение отходов материалов: Subtractive manufacturing, like CNC machining, starts with a solid block of material and removes large amounts to achieve the final shape, generating significant scrap (often >80-90% for complex aerospace parts).
- Additive Efficiency: Powder Bed Fusion (PBF) processes, a common metal AM technique, use only the material necessary to build the part and its supports. While some powder is used for supports and cannot be fully recycled indefinitely, the overall material utilization is significantly higher, reducing waste and associated costs, aligning with sustainability goals.
- Tooling Elimination: Traditional manufacturing often requires expensive and time-consuming tooling (molds, dies, jigs, fixtures).
- AM Advantage: Metal AM is a toolless process. Parts are built directly from digital files, eliminating tooling costs and lead times. This makes it economically viable for low-to-mid volume production runs and highly customized designs, which are common in aerospace.
- Supply Chain Simplification & On-Demand Production: AM enables distributed manufacturing and on-demand production. Digital part files can be sent electronically to certified AM service providers globally for local production.
- Влияние: Reduces reliance on complex, geographically concentrated supply chains, shortens lead times for replacement parts (digital inventory), and enhances supply chain resilience against disruptions.
Comparison: AM vs. Traditional Methods for Instrument Panels
Характеристика | Аддитивное производство металлов (AM) | Traditional (CNC Machining / Fabrication) |
---|---|---|
Вес | Optimized for minimum weight (Topology Opt., Lattices) | Often heavier due to process limitations |
Комплексность | High geometric complexity achievable (Internal channels) | Limited by tool access, forming constraints |
Консолидация частей | Excellent; multiple parts printable as one | Requires assembly of multiple components |
Lead Time (Proto) | Fast (Days/Weeks) | Slower (Weeks/Months due to setup/tooling) |
Lead Time (Prod) | Competitive for low-mid volume, toolless | Efficient for high volume, tooling req. |
Материальные отходы | Low (Additive process) | High (Subtractive process) |
Стоимость оснастки | Никто | Significant investment required |
Персонализация | High flexibility, economical for unique parts | Costly for customization, requires rework |
Свобода дизайна | Очень высокий | От умеренного до низкого |
Export to Sheets
By embracing metal AM, aerospace companies can design and produce instrument panels that are superior in performance, faster to develop, and contribute significantly to overall aircraft efficiency and capability.
Material Matters: Selecting AlSi10Mg and Scalmalloy® for Performance
Choosing the right material is fundamental to the success of any engineering application, and this holds especially true for critical aerospace components like instrument panels produced via additive manufacturing. The selection process involves balancing performance requirements (strength, stiffness, weight, temperature resistance, fatigue life) with processability and cost. For lightweight, high-performance aerospace panels, two aluminum alloys stand out in the metal AM landscape: AlSi10Mg и Scalmalloy®.
AlSi10Mg:
- Аннотация: AlSi10Mg is a well-established aluminum alloy, essentially a cast-grade aluminum with silicon and magnesium additions. It’s one of the most commonly used materials in metal AM, particularly Laser Powder Bed Fusion (LPBF), due to its excellent processability, good strength-to-weight ratio, and favorable thermal properties.
- Основные свойства:
- Good weldability and printability, leading to relatively high-density parts.
- Moderate strength and hardness, suitable for many structural and thermal applications.
- Good corrosion resistance.
- Excellent thermal conductivity, making it suitable for applications requiring heat dissipation.
- Can be readily post-processed (heat treated, machined, finished).
- Aerospace Relevance: Ideal for instrument panel components where moderate strength is sufficient, but lightweighting and thermal management are important. It’s often used for housings, brackets, and less structurally critical panel sections. Its widespread availability and lower cost compared to specialty alloys make it attractive for cost-sensitive applications.
Scalmalloy®:
- Аннотация: Scalmalloy® is a patented high-performance aluminum-magnesium-scandium alloy specifically developed for additive manufacturing by APWORKS. It offers significantly higher mechanical properties compared to standard aluminum alloys like AlSi10Mg.
- Основные свойства:
- Very High Strength: Possesses tensile strength significantly higher than AlSi10Mg, approaching that of some titanium alloys, particularly after appropriate heat treatment.
- Excellent Ductility and Fatigue Strength: Exhibits good elongation and exceptional resistance to fatigue failure, crucial for components subjected to vibrations and cyclic loading common in aerospace environments.
- Низкая плотность: Maintains the low density characteristic of aluminum alloys, providing an outstanding strength-to-weight ratio.
- Good Processability: Designed for AM, it demonstrates good printability with optimized parameter sets.
- Коррозионная стойкость: Offers good resistance to corrosion.
- Aerospace Relevance: Scalmalloy® is the preferred choice for highly loaded structural components within the instrument panel assembly or for panels requiring maximum weight savings without compromising strength and fatigue life. Its superior properties make it suitable for demanding applications in defense, space, and high-performance aviation where component failure is not an option. While typically more expensive than AlSi10Mg, the performance benefits often justify the cost for critical applications.
Material Property Comparison (Typical Values after Heat Treatment):
Недвижимость | AlSi10Mg (LPBF, Heat Treated) | Scalmalloy® (LPBF, Heat Treated) | Единица | Примечания |
---|---|---|---|---|
Плотность | ~ 2.67 | ~ 2.66 | г/см³ | Both are lightweight aluminum alloys |
Предельная прочность на разрыв | 330 – 430 | 500 – 540 | MPa | Scalmalloy® offers significantly higher strength |
Yield Strength (Rp0.2) | 230 – 300 | 460 – 500 | MPa | Scalmalloy® shows much higher yield strength |
Удлинение при разрыве | 6 – 10 | 10 – 16 | % | Scalmalloy® generally offers better ductility |
Твердость | 100 – 120 | 140 – 160 | ВН | Scalmalloy® is harder |
Fatigue Strength (R=-1) | ~ 100 – 130 | ~ 180 – 250 | MPa (at 10⁷ cycles) | Scalmalloy® exhibits superior fatigue life |
Теплопроводность | ~ 130 – 150 | ~ 120 – 140 | Вт/(м-К) | Both offer good thermal conductivity |
Export to Sheets
(Note: Properties can vary significantly based on specific AM process parameters, build orientation, heat treatment cycles, and testing conditions. These are representative values.)
Met3dp’s Role in Material Excellence:
The performance of the final printed part is critically dependent on the quality of the metal powder used. Inferior powder characteristics (e.g., inconsistent particle size distribution, poor sphericity, high satellite content, impurities, oxygen content) can lead to printing defects, suboptimal mechanical properties, and inconsistent results.
Met3dp Technology Co., LTD recognizes this critical link and specializes in the research, development, and production of высококачественные металлические порошки optimized for additive manufacturing. Leveraging industry-leading technologies like advanced gas atomization (employing unique nozzle and gas flow designs) and Plasma Rotating Electrode Process (PREP), Met3dp produces metallic powders, including aluminum alloys crucial for aerospace applications, with:
- Высокая сферичность: Ensures excellent powder flowability and uniform spreading during the printing process.
- Optimized Particle Size Distribution (PSD): Tailored PSD for specific AM processes (like LPBF or SEBM) leads to high packing density and fully dense parts.
- Low Oxygen and Impurity Content: Minimizes defects and ensures optimal material properties in the final component.
- Последовательность: Rigorous quality control ensures batch-to-batch consistency, vital for repeatable manufacturing in aerospace.
By utilizing premium powders like those developed and manufactured by Met3dp, potentially including optimized AlSi10Mg or exploring custom high-performance aluminum alloys, aerospace companies can have higher confidence in achieving the desired material properties and performance for their lightweight AM instrument panels built with AlSi10Mg or the high-strength Scalmalloy®. Partnering with a provider knowledgeable in both advanced powder production and printing processes is key to maximizing the benefits of these exceptional materials.
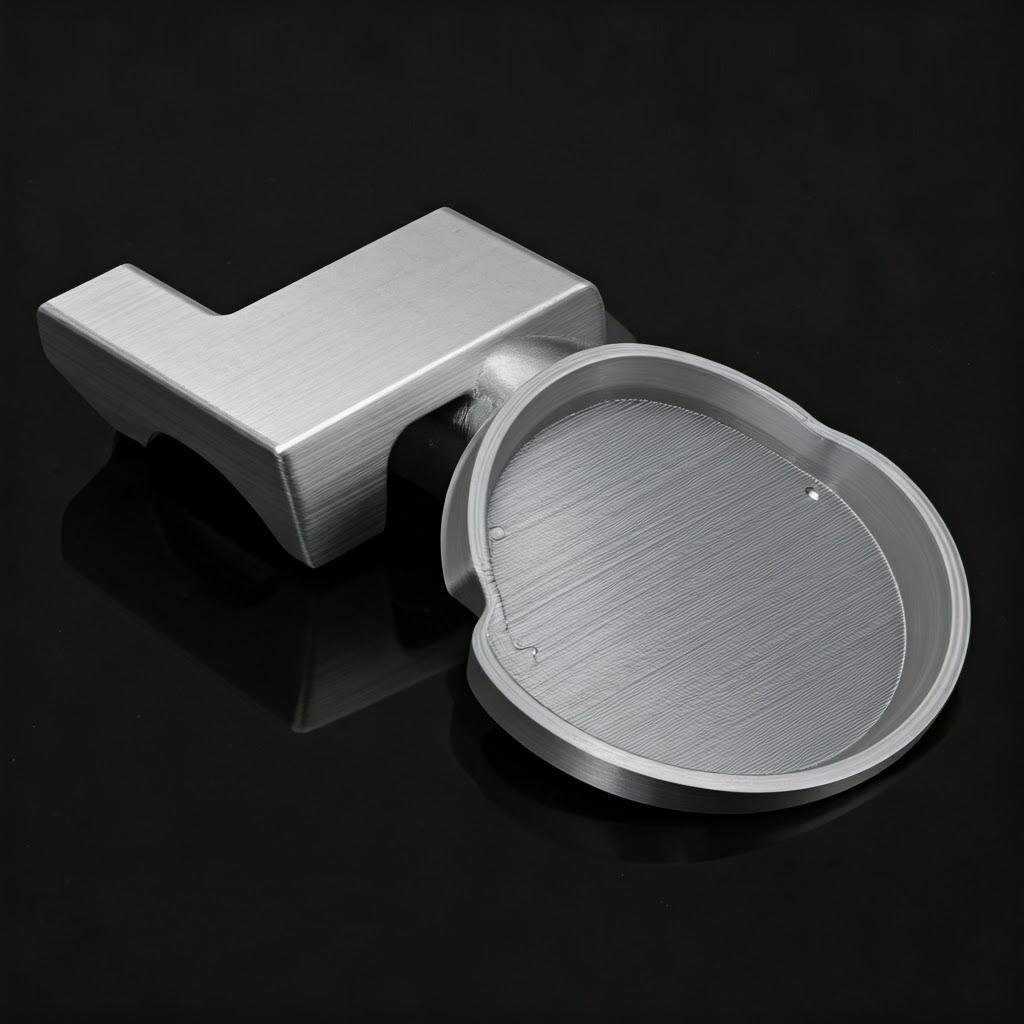
Design for Additive Manufacturing (DfAM): Optimizing Instrument Panels
Simply replicating a design intended for traditional manufacturing using metal additive manufacturing rarely unlocks the full potential of the technology. To truly leverage the benefits of weight reduction, part consolidation, and functional integration for aerospace instrument panels, engineers must embrace Проектирование для аддитивного производства (DfAM). DfAM is a methodology that involves rethinking the design process to specifically suit the capabilities and constraints of AM technologies like Laser Powder Bed Fusion (LPBF) or Electron Beam Melting (EBM), often available through comprehensive service providers like Met3dp.
Adopting DfAM principles early in the design cycle is crucial for maximizing performance gains and ensuring manufacturability. Key DfAM strategies for aerospace instrument panels include:
- Topology Optimization: This is a powerful computational tool used extensively in aerospace DfAM.
- Процесс: Engineers define the design space (the maximum allowable volume for the part), specify load cases (forces, pressures, vibrations the panel must withstand), define constraints (mounting points, keep-out zones for electronics), and set objectives (e.g., minimize mass, maximize stiffness).
- Outcome: Sophisticated software algorithms then iteratively remove material from areas where it doesn’t contribute significantly to structural performance, leaving behind an optimized, often organic-looking structure that efficiently carries the specified loads with minimum weight. This is ideal for creating lightweight yet strong panel frames and support structures.
- Benefit: Achieves maximum theoretical weight savings while ensuring structural integrity based on defined performance requirements.
- Generative Design: Taking optimization a step further, generative design algorithms explore numerous design possibilities autonomously based on a set of high-level functional requirements, materials, manufacturing methods (including AM constraints), and performance criteria. It can yield multiple innovative, often non-intuitive design solutions that meet the objectives, providing engineers with a range of optimized options to choose from.
- Lattice Structures and Infill: Instead of solid material, internal sections of the instrument panel can be filled with engineered lattice structures.
- Типы: These can range from simple strut-based lattices (like honeycomb or tetrahedral) to more complex, curved structures known as Triply Periodic Minimal Surfaces (TPMS) like gyroids or Schwarzites.
- Приложения:
- Облегчение: Replacing solid volumes with porous lattices drastically reduces mass while maintaining significant structural rigidity.
- Vibration Damping/Energy Absorption: Specific lattice geometries can be designed to absorb shock and dampen vibrations, protecting sensitive instruments.
- Тепловое управление: Open-cell lattice structures can facilitate airflow or coolant flow if integrated with cooling channels, enhancing heat dissipation from avionics.
- Tools: Specialized modules in CAD or standalone software are used to define, grade (vary density), and integrate these complex structures into the part design.
- Support Structure Minimization and Optimization: Metal AM processes typically require support structures for overhangs (usually features angled less than 45 degrees from the horizontal plane) and to anchor the part to the build plate, managing thermal stresses. However, supports add material cost, increase build time, and require significant post-processing effort for removal, potentially marring surfaces.
- DfAM Strategies:
- Orientation: Choosing the optimal build orientation can significantly reduce the need for supports on critical features or surfaces.
- Self-Supporting Angles: Designing overhangs with angles greater than 45 degrees where possible.
- Feature Modification: Incorporating chamfers or fillets instead of sharp horizontal overhangs.
- Internal Channels: Designing channels with diamond, teardrop, or circular cross-sections that are often self-supporting.
- Breakaway Supports: Designing support structures that are easier to remove manually or via machining.
- DfAM Strategies:
- Feature Integration and Part Consolidation: This is a cornerstone of DfAM’s value proposition. Engineers should look for opportunities to:
- Integrate brackets, mounting bosses, hinges, and fasteners directly into the main panel structure.
- Design integrated conduits or channels for wiring harnesses, reducing clutter and assembly complexity.
- Combine multiple smaller components of a traditional assembly into a single, complex AM part.
- Преимущества: Reduces part count, assembly labor, weight associated with fasteners, potential failure points, and simplifies inventory management.
- Minimum Wall Thickness and Feature Size: AM processes have limitations on the minimum size of features and walls they can reliably produce. For LPBF, this is often in the range of 0.3mm to 0.5mm. Designers must ensure that walls and features are thick enough to be manufacturable, robust, and meet functional requirements. Thin walls are also more susceptible to warping during the build.
- Collaboration with AM Experts: Successfully implementing DfAM, especially for complex aerospace components, often requires close collaboration between the design engineers and the AM service provider. Experts at companies like Met3dp possess deep knowledge of the specific способы печати, material behaviors, and process limitations. They can provide invaluable feedback on design manufacturability, suggest DfAM optimizations, advise on optimal orientation, and help develop effective support strategies, ensuring a successful outcome.
By adopting these DfAM principles, engineers can move beyond merely substituting manufacturing methods and truly harness additive manufacturing to create next-generation aerospace instrument panels that are lighter, stronger, more functional, and optimized for performance.
Precision and Finish: Achieving Aerospace Tolerances and Quality
While metal additive manufacturing offers significant design freedom, aerospace applications demand stringent adherence to dimensional accuracy, tolerances, and surface finish requirements. Engineers and procurement managers need to understand the capabilities and limitations of AM processes like Laser Powder Bed Fusion (LPBF) concerning these critical quality aspects.
Dimensional Accuracy and Tolerances:
- Typical Capabilities: For well-calibrated industrial LPBF systems printing aluminum alloys like AlSi10Mg or Scalmalloy®, typical achievable dimensional accuracy is often cited as:
- +/- 0.1 mm to +/- 0.2 mm for smaller features (e.g., up to 100 mm).
- +/- 0.1% to +/- 0.2% for larger dimensions.
- Influencing Factors: Achieving these tolerances consistently depends on several factors:
- Калибровка машины: Regular calibration of the laser system, scanners, and motion control is essential.
- Параметры процесса: Laser power, scan speed, layer thickness, and hatching strategy significantly impact accuracy.
- Тепловое управление: Internal stresses developed during printing can cause warping and distortion, affecting final dimensions. Effective support strategies and stress relief post-processing are crucial.
- Part Geometry and Size: Larger parts and complex geometries are generally more challenging to print with very tight tolerances due to cumulative thermal effects.
- Build Orientation: The orientation of the part on the build plate affects accuracy due to factors like layer stepping on curved surfaces and anisotropic shrinkage.
- Постобработка: Machining operations are often required to achieve tighter tolerances on critical features than possible with the as-built AM process.
- Met3dp’s Commitment: Reputable service providers like Met3dp invest in high-end, well-maintained equipment and employ rigorous process control methodologies to maximize achievable accuracy and repeatability for demanding aerospace clients.
Обработка поверхности (шероховатость):
- Состояние после строительства: The surface finish of metal AM parts directly after printing is inherently rougher than machined surfaces due to the layer-by-layer fusion of powder particles.
- Typical Ra Values (LPBF): Surface roughness (Ra) typically ranges from 5 µm to 20 µm.
- Orientation Dependence: Surface finish varies significantly depending on the surface’s orientation relative to the build direction:
- Up-skin surfaces (upward-facing) tend to be smoother.
- Down-skin surfaces (downward-facing, supported) are typically rougher due to support contact and heat accumulation.
- Vertical walls often show layer lines and have intermediate roughness.
- Поддерживаемые свесы exhibit the roughest surfaces where support structures have been removed.
- Post-Processed Finish: For many applications, especially those involving fluid flow, sealing surfaces, or aesthetic requirements, the as-built finish is insufficient. Post-processing steps are employed to improve surface finish:
- Bead Blasting/Shot Peening: Creates a uniform matte finish, removes loose powder (Ra typically 5-10 µm). Can also impart beneficial compressive stress.
- Tumbling/Vibratory Finishing: Smoothes surfaces and deburrs edges using abrasive media (Ra can reach ~1-5 µm).
- CNC Machining: Provides smooth, highly accurate surfaces for critical features (Ra < 1 µm possible).
- Полировка: Manual or automated polishing can achieve mirror-like finishes (Ra << 1 µm) for specific applications.
Achievable Surface Roughness (Ra) Comparison:
Surface Type | Typical As-Built Ra (LPBF) | Typical Post-Processed Ra | Примечания |
---|---|---|---|
Vertical Walls | 8 – 15 µm | < 1 µm (Machined) | Layer lines visible in as-built state |
Up-skin Surfaces (Top) | 5 – 10 µm | < 3 µm (Blasted/Tumbled) | Generally the smoothest as-built surfaces |
Down-skin Surfaces (Bottom) | 12 – 25 µm | < 5 µm (Blasted/Tumbled) | Rougher due to support interaction/removal |
CNC Machined Feature | Н/Д | < 1 µm | Required for tight tolerances/sealing |
Polished Surface | Н/Д | < 0.1 µm | For optical or very low friction needs |
Export to Sheets
Meeting Aerospace Quality Standards:
Achieving the required precision and finish for flight-worthy components necessitates a robust quality management system (QMS). Aerospace suppliers often require certifications like AS9100. Key quality control aspects include:
- Powder Management: Strict control over powder quality, storage, handling, and traceability.
- Process Monitoring: Real-time monitoring of critical parameters during the build (e.g., laser power, melt pool characteristics, oxygen levels).
- Проверка размеров: Using CMM (Coordinate Measuring Machines), 3D scanning, or traditional metrology tools to verify dimensional accuracy.
- Material Testing: Conducting tensile tests, density measurements, and microstructural analysis on witness coupons built alongside the parts.
- Неразрушающий контроль (NDT): Techniques like CT scanning (Computed Tomography) may be used to detect internal defects like porosity or cracks in critical components.
By understanding the inherent capabilities and limitations of metal AM regarding precision and finish, and by partnering with quality-focused service providers who implement rigorous process controls and offer necessary post-processing, engineers can confidently specify and procure metal AM instrument panels that meet demanding aerospace requirements.
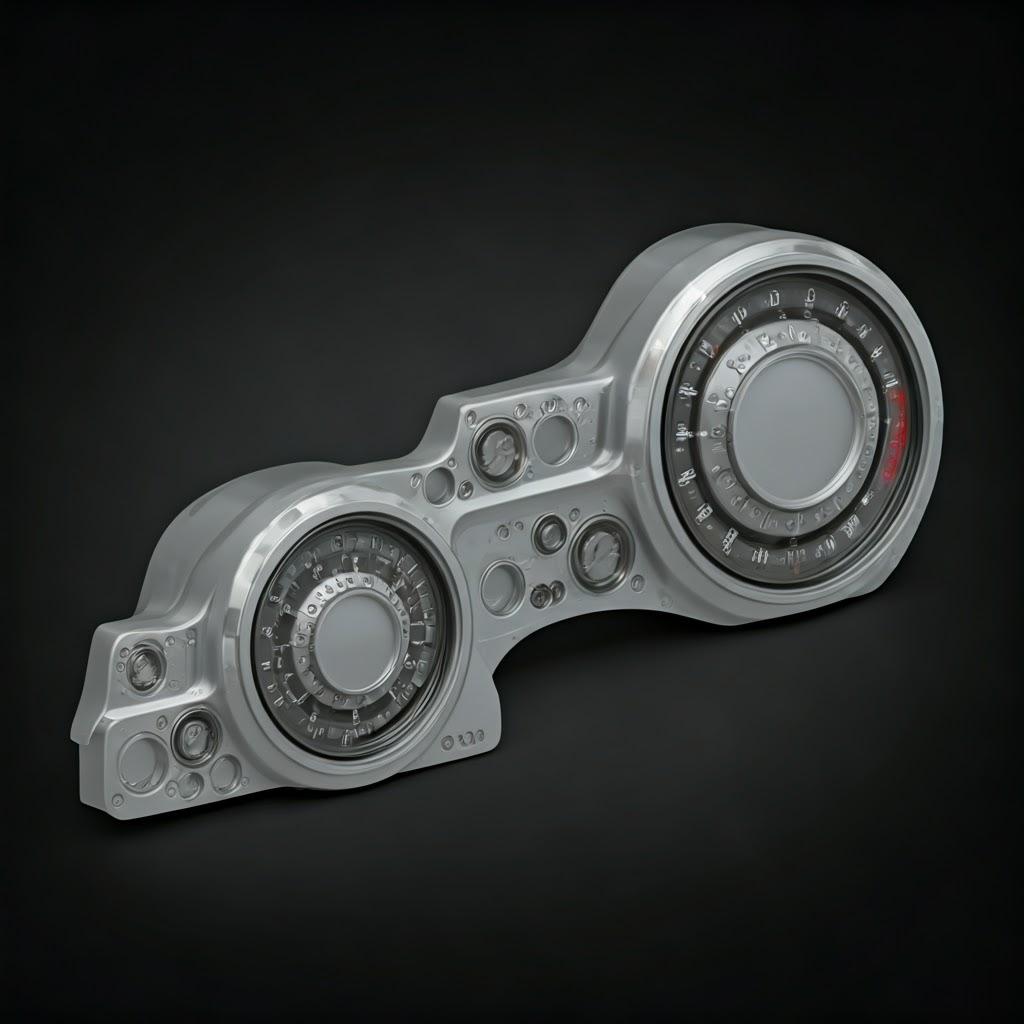
Beyond the Print: Essential Post-Processing Steps
The journey of a metal 3D printed aerospace instrument panel doesn’t end when it comes off the build plate. In almost all cases, a series of crucial post-processing steps are required to transform the as-built part into a functional, flight-ready component. These steps are essential for achieving the desired mechanical properties, dimensional accuracy, surface finish, and overall integrity required for aerospace applications. Planning for post-processing from the initial design phase is critical, as it significantly impacts final part cost and lead time.
Common post-processing steps for AM aluminum alloy (AlSi10Mg, Scalmalloy®) instrument panels include:
- Stress Relief Heat Treatment:
- Цель: The rapid heating and cooling cycles inherent in LPBF create significant internal stresses within the printed part. If not relieved, these stresses can cause distortion or cracking during support removal, subsequent machining, or service life.
- Процесс: Parts (often while still attached to the build plate) are subjected to a controlled heating and cooling cycle in an furnace. Typical cycles for aluminum alloys involve heating to around 250-350°C for several hours, followed by slow cooling. Specific parameters depend on the alloy and part geometry.
- Importance: Mandatory for most functional metal AM parts, especially those requiring tight tolerances or subject to fatigue loading.
- Part Removal from Build Plate:
- Процесс: After stress relief, the part needs to be separated from the metal build plate it was printed on. This is typically done using:
- Wire EDM (Electrical Discharge Machining): Precise, minimal force, good for complex or delicate parts.
- Band Sawing: Faster, more economical for simpler geometries, but less precise.
- Machining: Milling the part off the plate.
- Consideration: The removal method can influence subsequent machining needs for the base surface.
- Процесс: After stress relief, the part needs to be separated from the metal build plate it was printed on. This is typically done using:
- Демонтаж опорной конструкции:
- Цель: Removing the temporary support structures required during the build process.
- Методы: Can range from simple manual breaking (for well-designed, accessible supports) to more involved methods like CNC machining, grinding, or using hand tools. Accessing and removing supports from complex internal channels can be particularly challenging.
- Задачи: Can leave witness marks or rough surfaces requiring further finishing; risk of damaging the part if not done carefully. Efficient support removal heavily relies on smart DfAM strategies.
- Hot Isostatic Pressing (HIP) – Optional but Recommended for Critical Parts:
- Цель: To eliminate internal microporosity that can sometimes remain after the AM process, even with optimized parameters. Porosity can act as a stress concentrator and degrade mechanical properties, particularly fatigue life.
- Процесс: Parts are subjected to high temperature (below melting point) and high isostatic pressure (typically 100-200 MPa) in an inert gas atmosphere (e.g., Argon) for several hours. The combination of heat and pressure causes internal voids to collapse and metallurgically bond, increasing density closer to 100%.
- Преимущества: Significantly improves ductility, fatigue strength, fracture toughness, and overall material consistency. Often required for flight-critical aerospace components.
- Consideration: Adds cost and lead time; parts may require re-machining of critical dimensions as HIP can cause slight, predictable shrinkage.
- Solution Annealing and Age Hardening Heat Treatment (for specific property enhancement):
- Цель: Beyond stress relief, specific heat treatment cycles (like T6 for aluminum alloys) are used to optimize the final mechanical properties (strength, hardness, ductility) by controlling the material’s microstructure (dissolving precipitates and then aging to re-precipitate them optimally).
- Процесс: Involves heating to a higher temperature (solutionizing), quenching rapidly, and then aging at a lower temperature for a specific duration. Parameters are alloy-specific (e.g., different for AlSi10Mg vs. Scalmalloy®).
- Importance: Crucial for achieving the peak performance potential of alloys like Scalmalloy®.
- CNC Machining:
- Цель: To achieve tighter tolerances on critical features (e.g., mating surfaces, bearing interfaces, precise hole diameters) than possible with as-built AM; to create specific surface finishes; to machine away support witness marks or rough base surfaces.
- Процесс: Using multi-axis CNC mills or lathes to selectively machine specific areas of the AM part. Fixturing complex AM geometries can require custom solutions.
- Importance: Often essential for ensuring proper fit, assembly, and function within the larger cockpit environment.
- Отделка поверхности:
- Цель: To achieve the desired surface texture, appearance, and protective properties.
- Методы:
- Bead Blasting / Shot Peening: Uniform matte finish, cleaning.
- Tumbling / Vibratory Finishing: Deburring, edge rounding, smoothing.
- Sanding / Grinding / Polishing: Achieving smoother finishes, up to mirror polish if needed.
- Anodizing (Aluminum): Improves corrosion resistance, wear resistance, and allows dyeing for color coding.
- Painting / Powder Coating: For aesthetics, branding, and additional environmental protection.
Integrating Post-Processing into the Workflow:
It’s vital for procurement managers and engineers to recognize that post-processing is not an afterthought but an integral part of the AM workflow. It significantly influences the final cost, lead time, and properties of the component. Collaborating with a service provider like Met3dp, who understands the entire end-to-end process – from powder quality and printing parameters through to the intricacies of post-processing requirements for aerospace alloys – is key to a successful project outcome.
Navigating Challenges: Ensuring Successful AM Implementation
While metal additive manufacturing offers transformative potential for aerospace instrument panels, it’s not without its challenges. Understanding these potential hurdles and implementing mitigation strategies is crucial for successful adoption and achieving reliable, high-quality results. Partnering with experienced AM service providers who possess deep process knowledge is often the best way to navigate these complexities.
Common Challenges and Mitigation Strategies:
- Warping and Residual Stress:
- Вызов: The intense, localized heating and rapid cooling during layer fusion generate significant thermal gradients, leading to internal stresses. These stresses can cause the part to warp during the build, detach from supports, or distort after removal from the build plate. Aluminum alloys are particularly susceptible due to their high thermal conductivity and expansion coefficient.
- Mitigation:
- Thermal Simulation: Using FEA software to predict stress accumulation and distortion before printing, allowing for design or orientation adjustments.
- Optimized Build Orientation: Orienting the part to minimize large flat surfaces parallel to the build plate and manage heat distribution.
- Robust Support Structures: Designing effective supports not only for overhangs but also to anchor the part securely and act as heat sinks.
- Optimized Scan Strategies: Using specific laser scanning patterns (e.g., island scanning) to manage heat input locally.
- Mandatory Stress Relief: Performing appropriate heat treatment immediately after printing, often before support removal.
- Support Removal Difficulty:
- Вызов: Supports, while necessary, can be difficult and time-consuming to remove, especially from complex internal geometries (like cooling channels) or delicate features. Removal can leave undesirable witness marks or damage the part surface.
- Mitigation:
- DfAM Focus: Designing parts to be self-supporting where possible (using >45° angles, specific channel shapes). Designing supports for easier access and breakaway.
- Process Selection: Considering processes or materials that might allow for soluble or chemically etched supports (less common for these aluminum alloys).
- Specialized Tools: Utilizing appropriate tools (manual, CNC, EDM) for careful removal.
- Skilled Labor: Relying on experienced technicians for manual support removal.
- Achieving Consistent Material Properties:
- Вызов: Ensuring that the mechanical properties (strength, ductility, density, fatigue life) are consistent throughout the part and from build to build, meeting strict aerospace specifications. Variations can arise from powder inconsistencies, parameter fluctuations, or incomplete fusion.
- Mitigation:
- Powder Quality Control: Using high-quality, certified powder with consistent characteristics (PSD, morphology, chemistry). Implementing strict powder handling, storage, and recycling protocols (Met3dp’s expertise in powder production is a key advantage here).
- Process Parameter Optimization & Control: Developing and locking down validated process parameters for specific material/machine combinations.
- Мониторинг в процессе работы: Utilizing sensors to monitor melt pool conditions, temperature, oxygen levels, etc., during the build for real-time quality assurance.
- Post-Build Testing: Performing destructive testing (tensile tests) on witness coupons printed alongside the parts for batch verification.
- HIP Treatment: Using Hot Isostatic Pressing to heal internal defects and homogenize the microstructure for improved consistency, especially for fatigue-critical parts.
- Porosity Concerns:
- Вызов: Small internal voids or pores can form during printing due to factors like insufficient energy density (incomplete melting), trapped gas within the powder or shield gas, or keyholing (vapor depression instability) at excessive energy densities. Porosity degrades mechanical properties.
- Mitigation:
- Parameter Optimization: Fine-tuning laser power, scan speed, and layer thickness to ensure complete melting and stable melt pool behavior.
- High-Quality Powder: Using powder with low internal gas porosity and good flowability.
- Atmosphere Control: Maintaining a high-purity inert gas atmosphere in the build chamber.
- HIP Treatment: Effectively closes gas porosity, significantly increasing part density.
- Неразрушающий контроль (NDT): Using CT scanning to detect and quantify internal porosity in critical components.
- Cost Management:
- Вызов: Metal AM can have higher per-part costs than traditional methods, especially for simpler designs or very high volumes, due to expensive machines, materials, and extensive post-processing.
- Mitigation:
- Leverage DfAM: Maximize benefits like lightweighting and part consolidation, which provide value offsetting the print cost. Optimize designs for minimal material usage and support structures.
- Application Selection: Focus AM on applications where its unique benefits (complexity, weight, lead time) provide the most value. Ideal for low-to-mid volume production where tooling costs for traditional methods are prohibitive.
- Выбор материала: Choose the most cost-effective material that meets performance requirements (e.g., AlSi10Mg vs. Scalmalloy® if extreme strength isn’t needed).
- Nesting & Build Optimization: Printing multiple parts simultaneously in a single build to maximize machine utilization.
- B2B Volume Considerations: Discussing potential volume discounts with suppliers for larger batch orders or recurring production.
Successfully implementing metal AM for aerospace instrument panels requires a proactive approach to addressing these challenges. Working closely with knowledgeable and experienced AM service providers like Met3dp, who understand the intricacies of materials, DfAM, process control, and post-processing, is paramount to mitigating risks and achieving the desired outcomes for demanding aerospace applications.

Supplier Selection: Choosing Your Metal AM Partner for Aerospace Panels
Selecting the right additive manufacturing service provider is a critical decision for aerospace companies looking to leverage metal AM for instrument panels. The quality, reliability, and performance of the final component depend heavily on the supplier’s capabilities, expertise, and adherence to stringent industry standards. Procurement managers and engineers should conduct thorough due diligence when evaluating potential B2B partners.
Key Criteria for Evaluating Metal AM Service Providers:
- Aerospace Certifications (AS9100): This is paramount. AS9100 certification indicates the supplier operates a Quality Management System (QMS) specifically tailored to the rigorous demands of the aerospace industry, covering aspects like traceability, process control, risk management, and configuration management. While ISO 9001 is a good foundation, AS9100 is the aerospace standard.
- Material Expertise (AlSi10Mg & Scalmalloy®): Look for demonstrated experience and validated processes specifically for the chosen aluminum alloy(s). This includes:
- Proven, optimized parameter sets for high-density, high-quality printing.
- Deep understanding of powder handling, storage, and recycling protocols for these materials.
- Expertise in the required heat treatment cycles (stress relief, T6 aging) to achieve specified properties.
- Experience qualifying parts made from these materials for aerospace applications.
- Technology and Capacity:
- Оборудование: Does the supplier operate industrial-grade LPBF machines known for reliability and consistency? Are they well-maintained and calibrated?
- Capacity: Can they accommodate your project timeline for both prototypes and potential low-to-mid volume production runs? Do they have sufficient machine availability?
- Redundancy: Multiple machines can mitigate risks associated with equipment downtime.
- Powder Quality Control: Given the critical link between powder quality and part integrity, inquire about the supplier’s powder management processes:
- Sourcing: Do they source powder from reputable suppliers with clear specifications, or do they, like Met3dp, possess in-house powder production capabilities ensuring ultimate quality control?
- Тестирование: Do they perform incoming powder inspection (chemistry, PSD, morphology)?
- Handling & Traceability: What are their protocols for storage, handling, sieving, and tracking powder batches throughout the process?
- Engineering and DfAM Support: A valuable partner offers more than just printing services. Look for:
- DfAM Expertise: Ability to review designs and provide actionable feedback for AM optimization (weight reduction, support minimization, feature integration).
- Simulation Capabilities: Use of software for build simulation (predicting stress, distortion) and topology optimization.
- Collaborative Approach: Willingness to work closely with your engineering team throughout the project.
- End-to-End Post-Processing Capabilities: Does the supplier offer a comprehensive suite of in-house post-processing services (stress relief, HIP coordination, CNC machining, finishing), or do they manage a network of qualified subcontractors? An integrated approach simplifies the supply chain and ensures accountability.
- Quality Management and Inspection:
- Process Monitoring: Use of in-situ monitoring tools during the build.
- Inspection Equipment: Availability of CMMs, 3D scanners, and other metrology tools for dimensional verification.
- NDT Capabilities: Access to CT scanning or other NDT methods if required for critical part inspection.
- Documentation: Ability to provide comprehensive quality documentation (see FAQ).
- Track Record and Experience:
- Have they successfully completed similar projects for other aerospace clients?
- Can they provide relevant case studies or references?
- What is their experience level with parts of similar complexity and size?
Questions to Ask Potential Suppliers:
- Are you AS9100 certified? Can you provide your certificate?
- Describe your experience printing AlSi10Mg and/or Scalmalloy® for aerospace applications.
- What specific LPBF machines do you operate? What is their build volume and typical accuracy?
- How do you manage and control powder quality (sourcing, testing, handling, traceability)?
- What DfAM support and build simulation services do you offer?
- What post-processing capabilities do you have in-house versus outsourced?
- Describe your quality inspection process and available equipment (CMM, NDT).
- What standard quality documentation package do you provide with parts?
- What are your typical lead times for prototypes and production batches of this complexity?
- Can you provide references from other aerospace customers?
Choosing a partner like Met3dp, with its strong foundation in both advanced metal powder manufacturing and sophisticated 3D printing solutions, provides a distinct advantage. Their integrated understanding of the entire process chain, from raw material to finished part, positions them as a knowledgeable and reliable supplier capable of meeting the high standards of the aerospace industry.
Cost Analysis and Lead Time: Planning Your AM Project
Effectively planning an aerospace instrument panel project using metal AM requires a clear understanding of the factors driving costs and typical manufacturing timelines. While AM eliminates tooling costs, making it attractive for low-to-mid volumes and customization, other factors significantly influence the final price and delivery schedule.
Factors Influencing Metal AM Costs:
- Part Design Complexity: Highly complex geometries with intricate features or internal channels may require longer design optimization, more extensive support structures, and more complex post-processing (especially support removal), increasing overall cost.
- Part Size and Volume: Larger parts consume more material and require significantly longer machine build times, which is often the primary cost driver. The bounding box volume also influences how many parts can fit in a single build.
- Material Choice: High-performance alloys like Scalmalloy® typically have a higher raw material cost per kilogram compared to more standard alloys like AlSi10Mg. Material density also plays a role in the final weight and thus material consumption.
- Поддерживающие структуры: While minimized through DfAM, necessary supports consume material (which may not be fully recyclable) and require significant labor or machining time for removal, adding to the cost.
- Время машин: Calculated based on the total time required to print the part(s), heavily influenced by the part height (number of layers) and the volume/area to be scanned per layer. Machine depreciation, operation costs, and labor are factored into hourly rates.
- Post-Processing Intensity: Each required step adds cost:
- Stress relief heat treatment (furnace time, energy).
- Support removal (labor, machining time).
- HIP treatment (specialized equipment, cycle time).
- CNC machining (programming, setup, machine time).
- Surface finishing (labor, materials, equipment time).
- Quality Assurance Requirements: The level of inspection and documentation required impacts cost. Basic dimensional checks are standard, but extensive CMM reports, material testing per batch, NDT (like CT scanning), and detailed traceability documentation add to the final price.
- Order Quantity (B2B Volume): While AM avoids traditional tooling amortization, there are still setup costs (build preparation, programming). Larger batch sizes allow these costs to be spread over more parts. Suppliers may offer volume discounts for wholesale or recurring production orders.
Understanding Lead Times:
Lead time is the total duration from order placement to part delivery. It comprises several stages:
- Quoting & Order Confirmation: Includes engineering review of the design (DfAM check), quote generation, and order processing (typically 1-5 business days).
- Build Preparation & Queue Time: Preparing the build file, scheduling the job on an available machine. Queue times can vary significantly based on supplier workload (can range from days to weeks).
- Printing (Build Time): The actual time the part spends printing in the machine. Primarily dependent on part height, but also volume and number of parts nested in the build. Can range from hours for small parts to many days for large/tall components.
- Постобработка: Often the longest and most variable part of the lead time. Includes cooling time, stress relief, removal from plate, support removal, potential HIP cycles (which can take 1-2 days plus shipping to/from a HIP provider if outsourced), CNC machining, and finishing. Can easily add 1-2 weeks or more depending on complexity.
- Проверка качества: Time required for dimensional checks, NDT, and documentation preparation (typically 1-3 days).
- Перевозки: Transit time to the customer’s location.
Typical Indicative Lead Times:
- Прототипы: Often prioritized, potentially 1-3 weeks depending on complexity and post-processing.
- Малосерийное производство: Can range from 3-8 weeks depending on quantity, complexity, post-processing, and supplier capacity.
Planning and Procurement:
For accurate planning, it is essential to provide potential suppliers with a complete technical data package (CAD models, 2D drawings with tolerances, material specifications, post-processing requirements, quality standards) when requesting a quote (RFQ). Discussing long-term B2B supply agreements can help secure capacity and potentially optimize pricing for recurring needs.
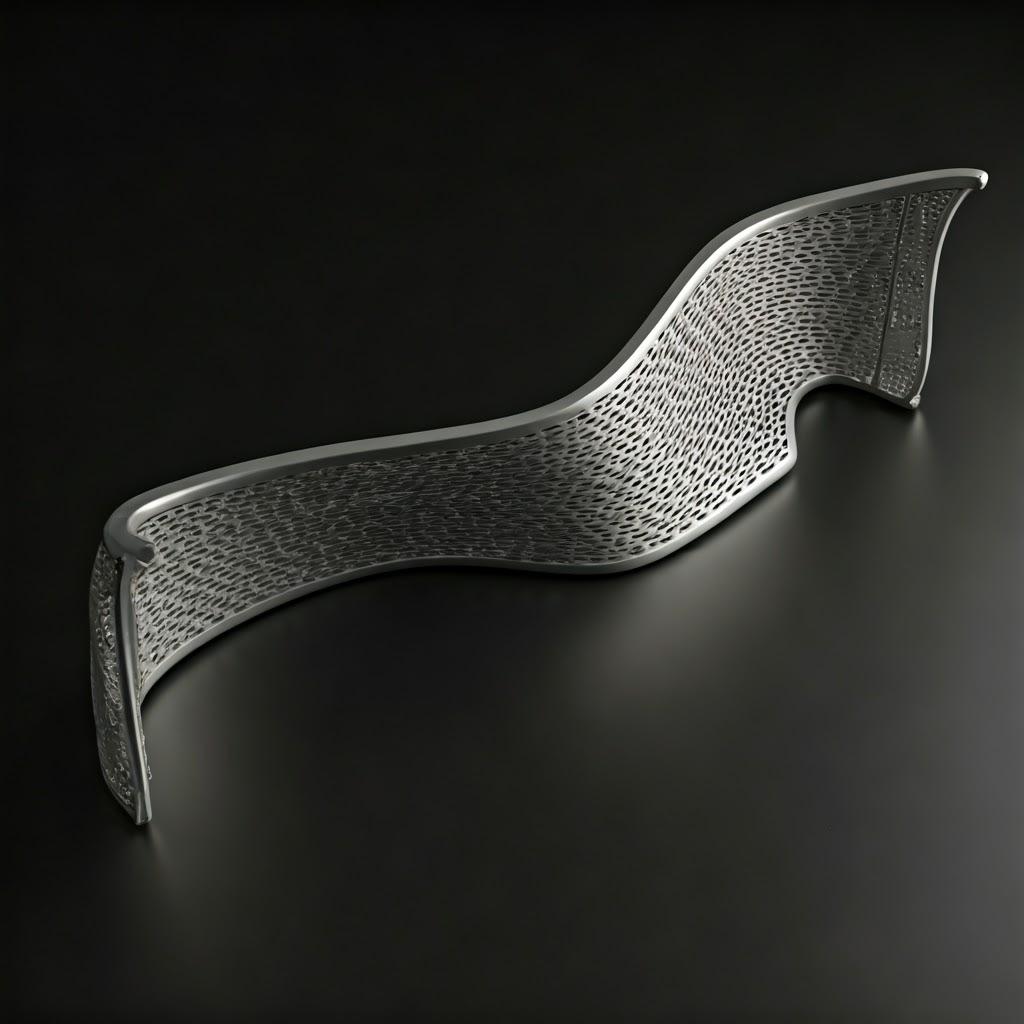
Часто задаваемые вопросы (FAQ)
Q1: What is the typical weight saving achievable with AM for aerospace instrument panels?
A: Significant weight savings are a primary benefit. Depending on the original design, the chosen AM material (AlSi10Mg, Scalmalloy®), and the extent to which DfAM principles like topology optimization and lattice structures are applied, weight reductions typically range from 30% to 60% compared to traditionally manufactured panels (e.g., machined from billet or assembled from sheet metal). However, the exact savings are highly dependent on the specific part geometry and functional requirements.
Q2: Are 3D printed metal panels flight-certified? What is the qualification process?
A: Individual 3D printed parts are not “certified” off the machine. Instead, the процесс производства used to produce the parts must be rigorously qualified and statistically controlled to ensure repeatability and meet aerospace specifications. Qualification typically involves:
- Квалификация материала: Extensive testing of the specific powder batch and printed material properties (tensile, fatigue, density, microstructure) to ensure they meet standards (e.g., MMPDS data).
- Process Validation: Demonstrating that the specific AM machine, parameters, and post-processing steps consistently produce parts meeting all requirements (dimensional, material properties, defect levels). This often involves building and testing multiple samples.
- Part-Specific Qualification: Testing the final component under representative load conditions to verify it meets all performance requirements outlined in the part specification.
- Supplier QMS: The supplier must operate under a certified QMS like AS9100. Achieving flight readiness requires close collaboration between the design authority, the manufacturer, and regulatory bodies (e.g., FAA, EASA).
Q3: How does the cost of AM panels compare to traditionally manufactured ones, especially for low-to-mid volume production?
A: The cost comparison depends heavily on volume and complexity.
- Low Volumes (Prototypes, 1-100 parts): AM is often более рентабельно because it eliminates the need for expensive tooling (molds, dies, jigs) associated with methods like casting or injection molding, and avoids extensive setup for complex CNC machining.
- Mid Volumes (Hundreds of parts): AM can remain competitive, especially if part consolidation significantly reduces assembly costs or if the design complexity makes traditional methods very difficult.
- High Volumes (Thousands of parts): Traditional methods like casting or stamping typically become more economical due to lower per-part costs once tooling is amortized. However, a simple per-part cost comparison isn’t sufficient. Consider the Общая стоимость владения, including benefits like reduced weight (fuel savings), reduced assembly time, simplified supply chain, and faster time-to-market enabled by AM.
Q4: Can complex internal features like cooling channels or integrated wiring conduits be printed directly into the panel?
A: Да, this is one of the major advantages of metal AM. Processes like LPBF can create intricate internal geometries, such as conformal cooling channels following the heat sources or integrated conduits for routing wiring harnesses. This allows for highly efficient thermal management and packaging density. However, designing these features requires careful consideration of DfAM principles to ensure they are self-supporting or that support structures, if needed, can be effectively removed through access ports designed into the part. Powder removal from internal channels also needs to be addressed during post-processing.
Q5: What quality documentation can be expected from a reputable metal AM service provider like Met3dp?
A: For aerospace components, a comprehensive documentation package is usually required to ensure traceability and compliance. This typically includes:
- Certificate of Conformance (CoC): Stating the parts conform to the purchase order, drawings, and specifications.
- Сертификация материала: Traceability to the specific metal powder batch used, often including the powder manufacturer’s certificate of analysis (chemistry, PSD).
- Build Report: Details about the specific build job, including machine used, parameters (if permissible), part orientation, and any anomalies noted during the build.
- Heat Treatment Records: Certification showing the parameters used for stress relief, HIP, and/or aging cycles and confirmation of compliance.
- Dimensional Inspection Report: Measurement results for critical dimensions specified on the drawing (e.g., CMM report, 3D scan report).
- Non-Destructive Testing (NDT) Report: Results from tests like CT scanning, if required by the specification. The exact documentation package should be clearly defined in the purchase order or quality agreement.
Conclusion: Elevating Aerospace Design with Lightweight AM Panels
Metal additive manufacturing represents a paradigm shift in the design and production of aerospace instrument panels. By moving beyond the constraints of traditional manufacturing, AM empowers engineers to create components that are significantly lighter, structurally optimized, and functionally integrated in ways previously unimaginable. The ability to leverage advanced materials like the versatile AlSi10Mg and the high-strength Scalmalloy®, combined with powerful DfAM techniques like topology optimization and lattice structures, directly addresses the aerospace industry’s critical needs for weight reduction, improved performance, and enhanced efficiency.
While the path to successful implementation involves careful consideration of design principles (DfAM), precision requirements, essential post-processing steps, and potential challenges, the benefits are compelling. Part consolidation simplifies assemblies, rapid prototyping accelerates development, and the freedom of design enables novel solutions for thermal management, ergonomics, and systems integration within the cockpit.
Choosing the right manufacturing partner – one with proven expertise in aerospace standards, specific material knowledge, robust process controls, and comprehensive capabilities like Met3dp – is crucial for navigating the complexities and realizing the full potential of this transformative technology.
Metal AM is no longer just a future possibility; it is a present-day reality enabling the creation of next-generation aerospace components. For engineers and procurement managers seeking to push the boundaries of aircraft design and performance, exploring lightweight instrument panels via additive manufacturing offers a clear trajectory towards innovation and competitive advantage. Contact an experienced AM provider today to discuss how this technology can elevate your specific aerospace applications.
Поделиться
MET3DP Technology Co., LTD - ведущий поставщик решений для аддитивного производства со штаб-квартирой в Циндао, Китай. Наша компания специализируется на производстве оборудования для 3D-печати и высокопроизводительных металлических порошков для промышленного применения.
Сделайте запрос, чтобы получить лучшую цену и индивидуальное решение для вашего бизнеса!
Похожие статьи
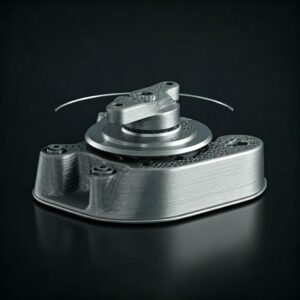
3D-печатные крепления для автомобильных радарных датчиков: Точность и производительность
Читать далее "О компании Met3DP
Последние обновления
Наш продукт
CONTACT US
Есть вопросы? Отправьте нам сообщение прямо сейчас! После получения Вашего сообщения мы всей командой выполним Ваш запрос.
Получите информацию о Metal3DP
Брошюра о продукции
Получить последние продукты и прайс-лист
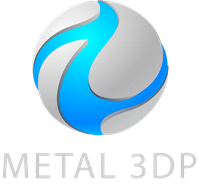
Металлические порошки для 3D-печати и аддитивного производства