3D Printing Bleed Valves: Revolutionizing Aerospace Fluid Control
Оглавление
Введение
In the demanding realm of aerospace engineering, every component plays a critical role in ensuring safety, efficiency, and performance. Among these vital parts are bleed valves, responsible for controlling the extraction of compressed air from various stages of the aircraft engine or other pneumatic systems. Traditionally manufactured through subtractive methods, these critical components are now being revolutionized by the advent of metal 3D-печать, also known as metal additive manufacturing. This innovative approach offers unprecedented design freedom, material optimization, and streamlined production, presenting significant advantages for aerospace manufacturers and suppliers seeking cutting-edge solutions. Metal3DP Technology Co., LTD, headquartered in Qingdao, China, stands at the forefront of this revolution, providing industry-leading 3D printing equipment and high-performance metal powders tailored for demanding aerospace applications. Our commitment to accuracy and reliability ensures that mission-critical parts like aerospace bleed valves can be produced with the highest quality standards.
What are Aerospace Bleed Valves Used For?
Aerospace bleed valves serve a multitude of essential functions within an aircraft. Primarily, they are used to regulate the flow of high-pressure, high-temperature air bled from the compressor stages of gas turbine engines. This controlled extraction of air is crucial for various subsystems, including:
- Cabin Pressurization and Air Conditioning: Bleed air is cooled and conditioned to maintain a comfortable and safe environment for passengers and crew inside the aircraft cabin.
- Engine Anti-Icing: Hot bleed air is directed to critical engine components like the inlet and fan blades to prevent ice formation, ensuring optimal engine performance and preventing damage.
- Wing and Empennage Anti-Icing: Similar to engine anti-icing, bleed air can be used to heat the leading edges of wings and the tail section (empennage) to prevent ice accumulation, which can severely impact aerodynamic performance.
- Thrust Reverser Actuation: In some aircraft, pneumatic systems powered by bleed air are used to deploy thrust reversers, assisting in deceleration during landing.
- Auxiliary Power Unit (APU) Starting: Bleed air from the APU or the main engines can be used to start the APU, which provides electrical power and air conditioning on the ground.
- Hydraulic System Pressurization: In certain hydraulic systems, bleed air can be used to pressurize reservoirs, ensuring proper hydraulic fluid supply for flight control surfaces and other actuators.
The efficient and reliable operation of these bleed valves is paramount for overall aircraft functionality and safety. As a leading provider of additive manufacturing solutions, Metal3DP understands the critical nature of these components and offers solutions that meet the stringent demands of the aerospace industry. Explore our range of high-performance metal powders suitable for aerospace applications.
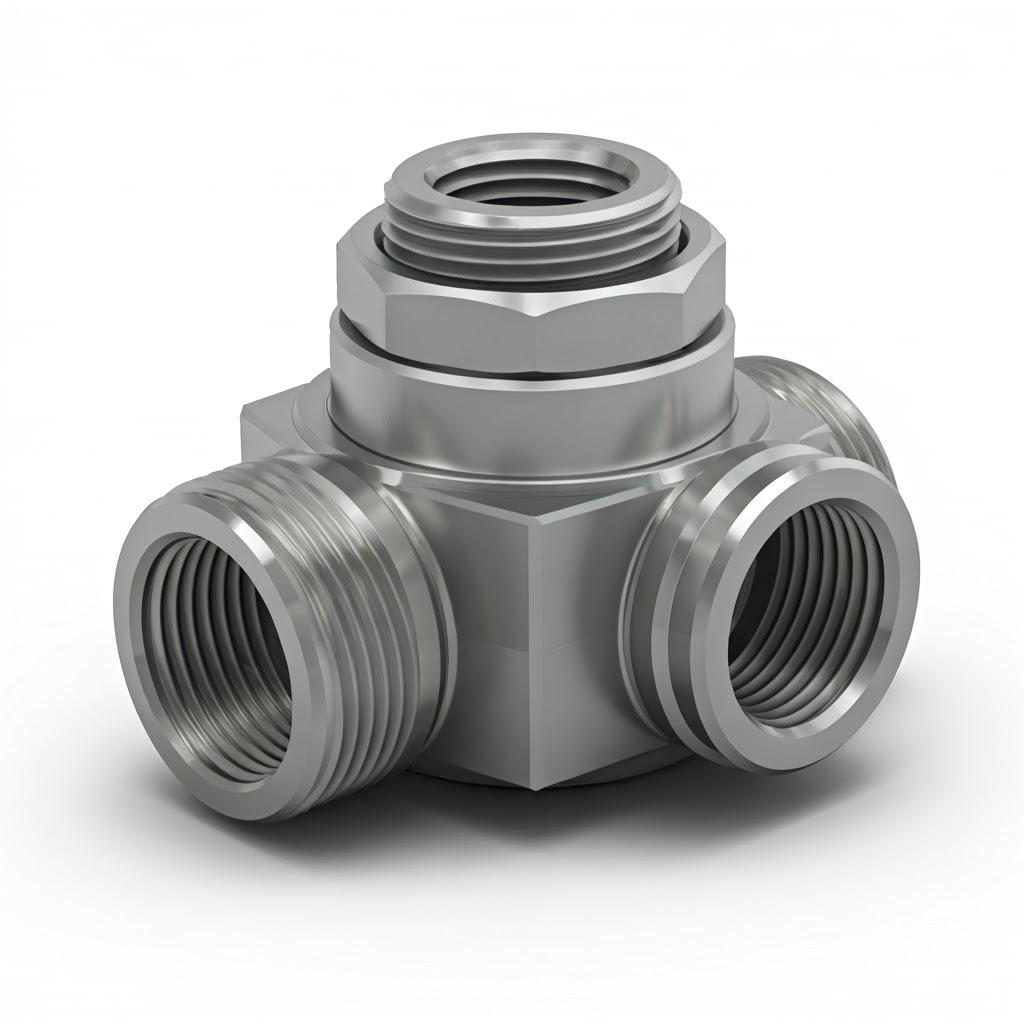
Why Use Metal 3D Printing for Aerospace Bleed Valves?
Adopting metal 3D printing for the production of aerospace bleed valves offers a compelling array of advantages over traditional manufacturing methods like casting, forging, and machining:
- Enhanced Design Freedom: Additive manufacturing allows for the creation of complex geometries that are difficult or impossible to achieve with conventional techniques. This enables engineers to optimize valve designs for improved flow characteristics, reduced weight, and integration of multiple components into a single part, minimizing assembly requirements and potential failure points.
- Облегчение: Aerospace components are under constant pressure to reduce weight, as this directly translates to improved fuel efficiency and performance. Metal 3D printing facilitates the creation of intricate internal structures and lattice designs that maintain structural integrity while significantly reducing material usage and overall weight. Metal3DP’s advanced metal powders are specifically designed to produce dense, lightweight parts without compromising strength.
- Эффективность материала: Subtractive manufacturing processes often result in significant material waste. Metal 3D printing, on the other hand, builds parts layer by layer, using only the necessary material. This reduces waste, lowers material costs, and is particularly beneficial when working with expensive, high-performance alloys commonly used in aerospace.
- Быстрое создание прототипов и итерации: Metal 3D printing drastically reduces lead times for producing prototypes. This allows aerospace engineers to quickly iterate on designs, test different configurations, and accelerate the development cycle for new bleed valve designs. Metal3DP’s industry-leading print volume and accuracy enable rapid production of functional prototypes.
- Customization and Low-Volume Production: Unlike traditional methods that often require significant tooling costs and are best suited for high-volume production, metal 3D printing is economically viable for producing customized bleed valves or smaller batches required for specific aircraft models or aftermarket applications.
- Improved Performance and Reliability: By optimizing the internal flow paths and reducing the number of joints and fasteners, metal 3D printing can contribute to improved performance and reliability of bleed valves. The high density and excellent mechanical properties achievable with Metal3DP’s metal spherical powders further enhance the durability and lifespan of these critical components.
- Supply Chain Optimization: Metal 3D printing offers the potential to decentralize manufacturing, allowing for on-demand production of bleed valves closer to the point of use. This can reduce reliance on complex global supply chains, minimize lead times, and improve responsiveness to maintenance and repair needs.
Recommended Materials and Why They Matter
The selection of the appropriate metal powder is crucial for achieving the desired performance characteristics of 3D printed aerospace bleed valves. Metal3DP offers a range of high-quality metal powders optimized for demanding applications, including:
- Inconel 625 (IN625): This nickel-chromium superalloy is renowned for its exceptional high-temperature strength, corrosion resistance, and oxidation resistance. These properties are essential for bleed valves that operate in the harsh environment of aircraft engines, where they are exposed to high temperatures and corrosive gases.
- Основные свойства:
- Отличная высокотемпературная прочность и сопротивление ползучести
- Superior resistance to oxidation and corrosion, including pitting and crevice corrosion
- Хорошая свариваемость и технологичность
- Высокая усталостная прочность
- Benefits for Bleed Valves: Ensures long-term reliability and performance under extreme operating conditions, resisting degradation from heat and corrosive environments. Metal3DP’s advanced powder making system ensures the high sphericity and flowability of our IN625 powder, leading to dense and high-quality printed parts.
- Основные свойства:
- 17-4 Precipitation Hardening (PH) Stainless Steel: This chromium-nickel-copper precipitation hardening stainless steel offers a high strength-to-weight ratio and good corrosion resistance. It is a versatile material suitable for various aerospace applications where high strength and moderate temperature resistance are required.
- Основные свойства:
- High strength and hardness achievable through heat treatment
- Хорошая коррозионная стойкость
- Excellent fatigue strength
- Relatively good machinability
- Benefits for Bleed Valves: Provides a strong and durable material option with good resistance to corrosion, suitable for less extreme temperature environments within the aircraft pneumatic system. Metal3DP manufactures a wide range of high-quality metal powders, including 17-4 PH, optimized for laser and electron beam powder bed fusion processes.
- Основные свойства:
The choice between IN625 and 17-4 PH will depend on the specific operating conditions, temperature requirements, and cost considerations for the bleed valve application. Metal3DP’s team of experts can provide guidance on selecting the optimal material for your specific needs. Contact Metal3DP to explore how our capabilities can power your organization’s additive manufacturing goals.
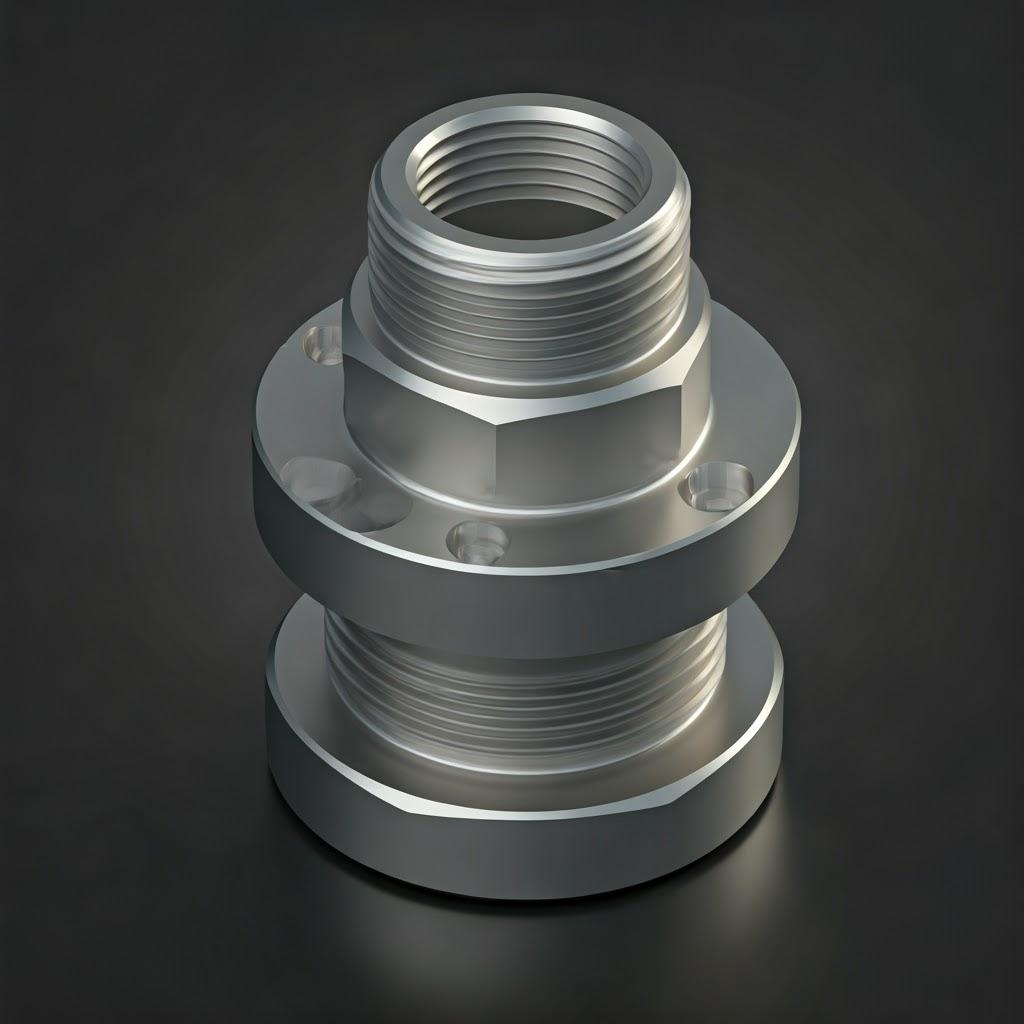
Design Considerations for Additive Manufacturing
Designing aerospace bleed valves for metal 3D printing requires a different mindset compared to traditional manufacturing. To fully leverage the capabilities of additive manufacturing and achieve optimal performance, engineers must consider several key design principles:
- Topology Optimization: This computational method allows for the creation of highly efficient designs by removing material from low-stress areas while maintaining structural integrity. For bleed valves, topology optimization can lead to significant weight reduction and improved flow characteristics by generating organic, free-form geometries.
- Решетчатые структуры: Internal lattice structures can be incorporated into the valve design to further reduce weight without compromising strength or stiffness. These intricate networks of interconnected struts and nodes offer a high strength-to-weight ratio and can be tailored to specific load-bearing requirements.
- Объединение частей: Metal 3D printing enables the integration of multiple components into a single, complex part. For bleed valves, this could mean combining the valve body, flow channels, and mounting features into one piece, reducing assembly time, the number of fasteners, and potential leak paths, ultimately enhancing reliability. This aligns with Metal3DP’s expertise in delivering industry-leading accuracy and reliability for mission-critical parts.
- Optimization of Flow Channels: Additive manufacturing allows for the creation of complex and optimized internal flow channels with smooth curves and varying cross-sections. This can minimize pressure drop and turbulence within the bleed valve, improving its efficiency and performance.
- Self-Supporting Geometries: Designing parts with self-supporting angles minimizes the need for support structures during the printing process. Support removal can be time-consuming and may affect surface finish. Careful design can reduce or eliminate the need for supports, leading to faster printing times and improved part quality.
- Consideration of Build Orientation: The orientation of the part on the build platform can significantly impact surface finish, dimensional accuracy, and the need for support structures. Careful consideration of build orientation is crucial for achieving the desired tolerances and minimizing post-processing requirements.
- Incorporation of Internal Features: Metal 3D printing allows for the creation of internal features such as cooling channels or intricate passageways that would be impossible or very difficult to manufacture using traditional methods. These features can enhance the functionality and performance of bleed valves in specific applications.
By embracing these design considerations, aerospace engineers can unlock the full potential of metal 3D printing to create innovative and high-performance bleed valves. Metal3DP partners with organizations to implement 3D printing and accelerate digital manufacturing transformations, offering expertise in design optimization for additive manufacturing.
Tolerance, Surface Finish, and Dimensional Accuracy
Achieving the required tolerance, surface finish, and dimensional accuracy is paramount for aerospace components like bleed valves, which often interface with other critical systems. Metal 3D printing technologies have made significant advancements in these areas:
- Tolerance Capabilities: Selective Laser Melting (SLM) and Electron Beam Melting (EBM), the primary metal 3D printing processes used by Metal3DP’s equipment, are capable of achieving tight tolerances, typically in the range of ±0.1 to ±0.2 mm for critical dimensions. However, achievable tolerances can be influenced by factors such as part geometry, size, material, and build orientation.
- Отделка поверхности: The as-built surface finish of metal 3D printed parts is generally rougher compared to machined surfaces. The surface roughness is influenced by the powder particle size and the layer thickness used during the printing process. For aerospace bleed valves, post-processing steps like machining, polishing, or surface coating are often employed to achieve the required surface finish for optimal sealing and reduced friction.
- Точность размеров: Metal 3D printing systems from Metal3DP are engineered to deliver high dimensional accuracy. However, factors such as thermal expansion and contraction during the printing process, as well as potential warping or distortion, can affect the final dimensions. Careful process control, optimized build parameters, and support structure design are crucial for minimizing these effects.
- Post-Processing for Precision: To meet the stringent requirements of aerospace applications, post-processing techniques play a vital role in achieving the desired tolerance and surface finish. Precision CNC machining can be used to achieve tight tolerances on critical mating surfaces, while processes like polishing, abrasive flow machining, or chemical etching can improve surface finish for enhanced performance.
Metal3DP’s industry-leading print volume, accuracy, and reliability ensure that our customers can produce aerospace bleed valves with the necessary precision. We also offer guidance on appropriate post-processing techniques to meet specific application requirements.
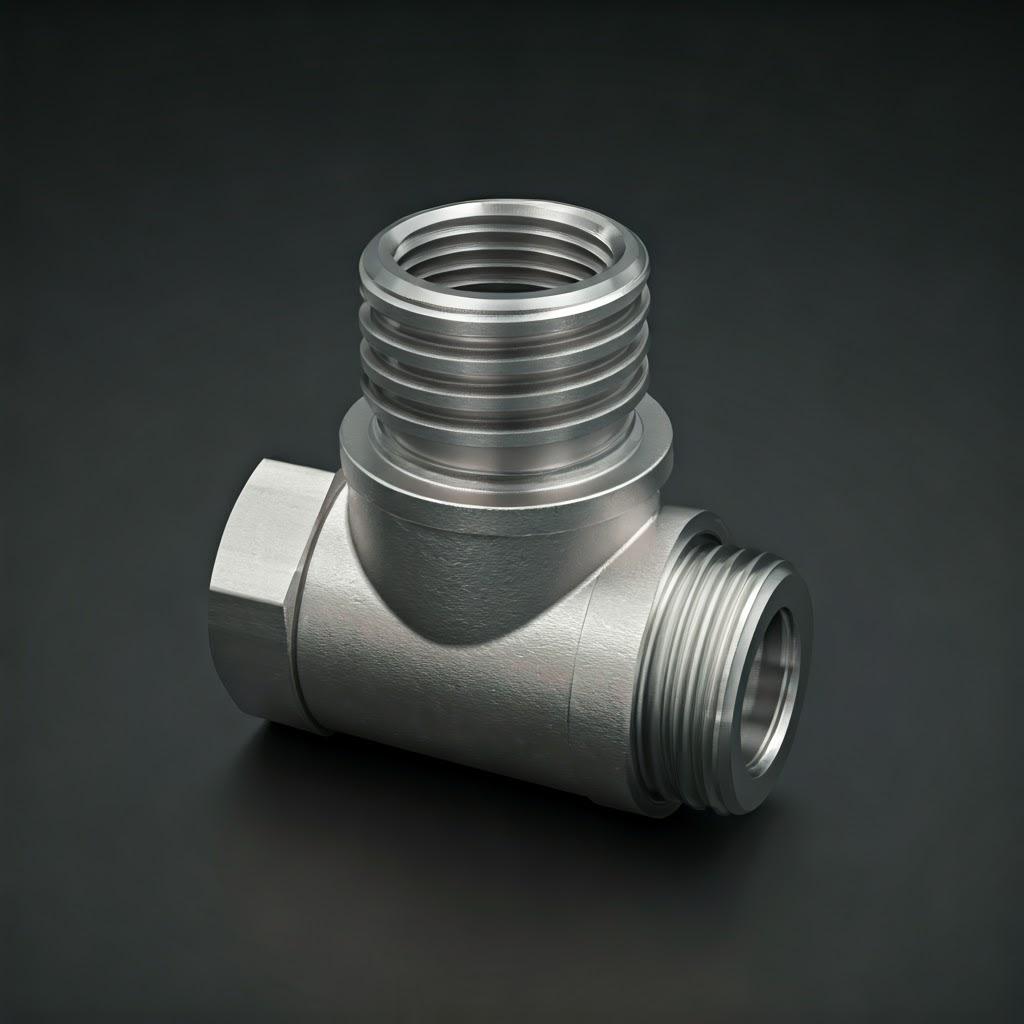
Требования к постобработке
While metal 3D printing offers significant advantages, aerospace bleed valves often require post-processing steps to achieve the final desired properties and functionality:
- Удаление опоры: Support structures are often necessary during the printing process to prevent part deformation and ensure proper overhangs. These supports need to be carefully removed after printing, which can be a manual or automated process depending on the complexity of the part and the type of support used.
- Термообработка: Heat treatment is a crucial step for many metal 3D printed parts, including bleed valves made from materials like 17-4 PH stainless steel. Specific heat treatment cycles are applied to achieve the desired mechanical properties, such as increased strength, hardness, and ductility.
- Снятие стресса: Residual stresses can build up in 3D printed parts during the rapid heating and cooling cycles of the printing process. Stress relief annealing is often performed to reduce these internal stresses, preventing potential cracking or distortion during service.
- Отделка поверхности: As mentioned earlier, post-processing techniques like CNC machining, polishing, abrasive flow machining, or chemical etching are used to improve the surface finish of bleed valves, ensuring proper sealing, reducing friction, and meeting aerodynamic requirements.
- Inspection and Quality Control: Rigorous inspection and quality control procedures are essential for aerospace components. Non-destructive testing methods, such as dye penetrant inspection, magnetic particle inspection, or ultrasonic testing, may be used to detect any internal flaws or surface defects in the 3D printed bleed valves. Dimensional accuracy is verified using coordinate measuring machines (CMMs).
- Покрытие: Depending on the application and the operating environment, bleed valves may require surface coatings to enhance corrosion resistance, wear resistance, or thermal protection.
Metal3DP provides comprehensive solutions spanning SEBM printers, advanced metal powders, and application development services, 1 including guidance on necessary post-processing steps for aerospace components.
Common Challenges and How to Avoid Them
While metal 3D printing offers numerous benefits, there are also potential challenges that need to be addressed to ensure successful production of high-quality aerospace bleed valves:
- Warping and Distortion: Thermal stresses during the printing process can lead to warping or distortion of the part, especially for complex geometries or large parts.
- Mitigation: Optimizing part design for self-supporting structures, carefully controlling build parameters, using appropriate support structures, and employing stress relief heat treatments can minimize warping and distortion.
- Пористость: Internal voids or pores can occur in 3D printed parts, potentially affecting their mechanical properties and fatigue life.
- Mitigation: Using high-quality metal powders like those produced by Metal3DP’s advanced powder making system, optimizing printing parameters (laser power, scan speed, layer thickness), and ensuring proper inert gas atmosphere during printing can minimize porosity.
- Support Removal Damage: Removing support structures can sometimes leave surface blemishes or damage the part, especially for intricate designs.
- Mitigation: Designing parts to minimize the need for supports, using dissolvable support materials (where applicable), and employing careful and controlled support removal techniques can prevent damage.
- Achieving Tight Tolerances: Meeting the tight tolerances required for aerospace components can be challenging with as-built 3D printed parts.
- Mitigation: Incorporating machining allowances in the design and utilizing precision CNC machining as a post-processing step can ensure that critical dimensions meet the required tolerances.
- Material Property Consistency: Ensuring consistent material properties throughout the 3D printed part and from batch to batch is crucial for aerospace applications.
- Mitigation: Using well-characterized and high-quality metal powders from reputable suppliers like Metal3DP, maintaining strict process control during printing, and implementing robust quality control procedures can ensure material property consistency.
- Cost and Lead Time for Complex Parts: While 3D printing can reduce lead times for prototyping and low-volume production, the cost and lead time for complex, high-precision aerospace components can still be significant.
- Mitigation: Optimizing part design for efficient printing, carefully selecting the appropriate printing technology and parameters, and working with experienced metal 3D printing service providers like Metal3DP can help manage costs and lead times effectively.
By understanding these potential challenges and implementing appropriate mitigation strategies, aerospace manufacturers can successfully leverage metal 3D printing to produce high-quality bleed valves.
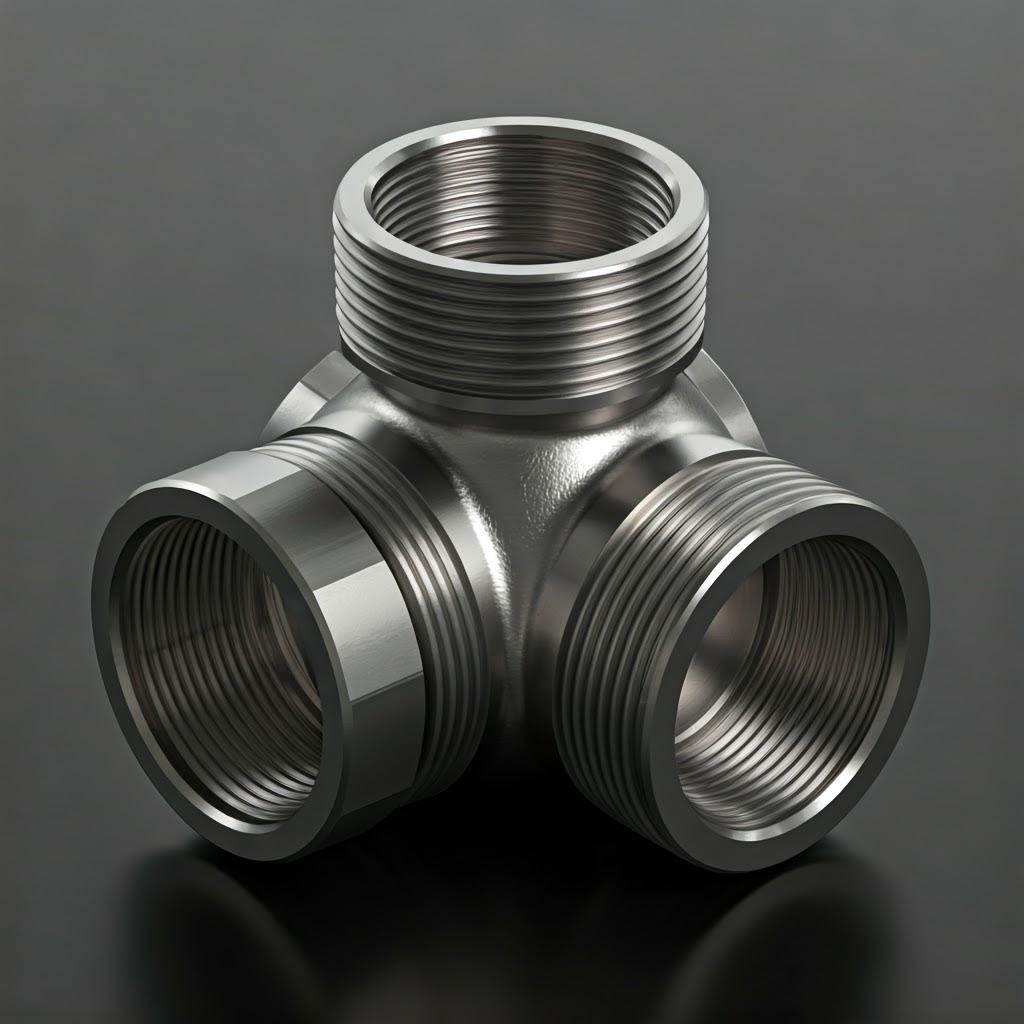
How to Choose the Right Metal 3D Printing Service Provider
Selecting the appropriate metal 3D printing service provider is a critical decision for aerospace companies looking to leverage this advanced manufacturing technology for bleed valves. Here are key factors to consider when evaluating potential suppliers:
- Industry Experience and Certifications: Look for a provider with a proven track record in serving the aerospace industry and relevant certifications such as AS9100D (quality management system for aerospace). Experience with producing flight-critical components is a significant advantage. Metal3DP has decades of collective expertise in metal additive manufacturing and partners with organizations in aerospace and other demanding fields.
- Material Capabilities: Ensure the service provider offers the specific metal powders required for your application, such as IN625 and 17-4 PH. Verify the quality and traceability of their materials. Metal3DP manufactures a wide range of high-quality metal powders optimized for aerospace applications.
- Printing Technology and Equipment: Understand the types of metal 3D printing technologies they employ (e.g., SLM, EBM) and the capabilities of their equipment in terms of build volume, accuracy, and resolution. Metal3DP’s printers deliver industry-leading print volume, accuracy, and reliability.
- Design and Engineering Support: A good service provider should offer design optimization services for additive manufacturing, helping you to tailor your bleed valve designs for optimal performance and printability. Metal3DP provides comprehensive solutions spanning application development services.
- Post-Processing Capabilities: Inquire about their in-house or partnered post-processing capabilities, including support removal, heat treatment, surface finishing, and inspection. A provider offering a comprehensive suite of services can streamline the production process.
- Quality Control and Inspection Procedures: Understand their quality management system and the inspection methods they use to ensure the dimensional accuracy and material integrity of the printed parts. Rigorous quality control is paramount for aerospace components.
- Lead Times and Production Capacity: Discuss their typical lead times for similar projects and their production capacity to ensure they can meet your volume requirements.
- Communication and Customer Support: Evaluate their responsiveness, communication clarity, and willingness to collaborate throughout the project. A strong partnership is essential for successful outcomes.
- Pricing Structure and Transparency: Obtain a clear understanding of their pricing model, including material costs, printing fees, and post-processing charges. Transparency in pricing is crucial for budget planning.
By carefully evaluating these factors, aerospace companies can select a metal 3D printing service provider that aligns with their specific needs and ensures the production of high-quality, reliable bleed valves.
Cost Factors and Lead Time
The cost and lead time for 3D printed aerospace bleed valves are influenced by several factors:
- Материальные затраты: The cost of the metal powder (e.g., IN625, 17-4 PH) is a significant factor. Specialized aerospace-grade alloys can be expensive.
- Part Complexity and Volume: More complex designs and larger volumes typically require longer print times and potentially more post-processing, increasing costs. However, for low to medium volumes, 3D printing can be more cost-effective than traditional methods due to the absence of tooling costs.
- Время сборки: The time it takes to print a bleed valve depends on its size, complexity, and the chosen printing parameters (layer thickness, scan speed, etc.). Longer build times translate to higher machine usage costs.
- Требования к постобработке: The extent of post-processing required (support removal, heat treatment, machining, surface finishing, inspection) significantly impacts both the cost and lead time.
- Оптимизация дизайна: Investing in design optimization for additive manufacturing can potentially reduce material usage, print time, and the need for extensive post-processing, ultimately lowering costs and lead times.
- Service Provider Costs: Different service providers have varying pricing structures based on their equipment, expertise, and overhead costs.
- Время выполнения: Lead times can vary depending on the service provider’s workload, the complexity of the part, and the required post-processing steps. Prototyping lead times with 3D printing are typically much shorter than with traditional manufacturing.
While the initial cost per part for 3D printed aerospace bleed valves might be higher than for mass-produced conventionally manufactured parts, the advantages in terms of design freedom, lightweighting, and rapid prototyping can often outweigh these costs, especially for specialized or low-volume applications. Metal3DP can provide detailed cost breakdowns and lead time estimates based on your specific requirements.
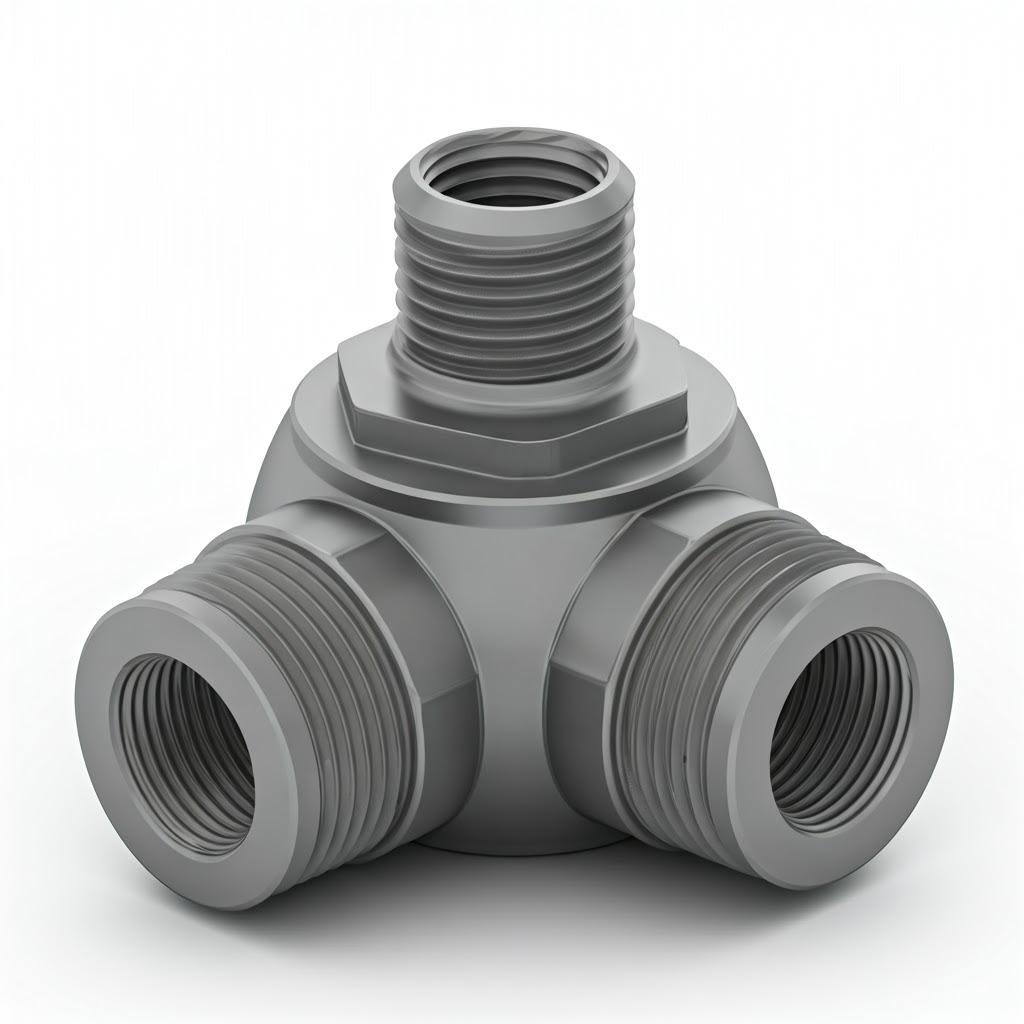
Часто задаваемые вопросы (FAQ)
- Q: Can metal 3D printed bleed valves meet aerospace industry standards?
- A: Yes, when produced using high-quality metal powders, optimized printing parameters, and appropriate post-processing and quality control procedures, metal 3D printed bleed valves can meet stringent aerospace industry standards. Material traceability and process documentation are crucial. Metal3DP adheres to high quality standards to ensure reliable performance of 3D printed parts.
- Q: What are the typical tolerances achievable with metal 3D printing for bleed valves?
- A: Typical tolerances achievable with metal 3D printing (SLM/EBM) range from ±0.1 to ±0.2 mm for critical dimensions. However, tighter tolerances can be achieved through post-processing techniques like precision CNC machining. Metal3DP’s equipment is engineered for high accuracy, and we can advise on achieving specific tolerance requirements.
- Q: Is metal 3D printing cost-effective for producing aerospace bleed valves?
- A: Metal 3D printing can be cost-effective, especially for rapid prototyping, low-to-medium volume production, complex designs, and when considering the benefits of lightweighting and part consolidation. For very high volumes, traditional manufacturing methods may still be more economical. Contact Metal3DP to explore cost-effective solutions for your specific needs.
Заключение
Metal 3D printing is transforming the landscape of aerospace manufacturing, offering compelling advantages for the production of critical components like bleed valves. The ability to create complex, lightweight designs with optimized performance, coupled with rapid prototyping capabilities and material efficiency, makes it an increasingly attractive alternative to traditional manufacturing methods. Companies like Metal3DP Technology Co., LTD are at the forefront of this revolution, providing advanced 3D printing equipment and high-performance metal powders such as IN625 and 17-4 PH that meet the demanding requirements of the aerospace industry. By carefully considering design principles, material selection, post-processing needs, and the choice of a reliable service provider, aerospace engineers and procurement managers can harness the power of metal 3D printing to develop and manufacture next-generation bleed valves that enhance aircraft performance, efficiency, and safety. Explore the possibilities of metal 3D printing for your aerospace applications by visiting our website.
Поделиться
MET3DP Technology Co., LTD - ведущий поставщик решений для аддитивного производства со штаб-квартирой в Циндао, Китай. Наша компания специализируется на производстве оборудования для 3D-печати и высокопроизводительных металлических порошков для промышленного применения.
Сделайте запрос, чтобы получить лучшую цену и индивидуальное решение для вашего бизнеса!
Похожие статьи
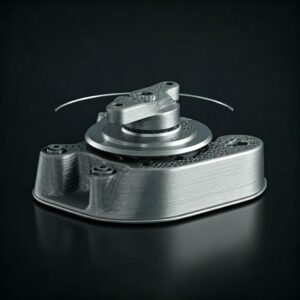
3D-печатные крепления для автомобильных радарных датчиков: Точность и производительность
Читать далее "О компании Met3DP
Последние обновления
Наш продукт
CONTACT US
Есть вопросы? Отправьте нам сообщение прямо сейчас! После получения Вашего сообщения мы всей командой выполним Ваш запрос.
Получите информацию о Metal3DP
Брошюра о продукции
Получить последние продукты и прайс-лист