Custom Aerospace Valve Housings
Оглавление
Introduction to Custom Aerospace Valve Housings via Metal 3D Printing
The aerospace industry constantly demands innovation, pushing the boundaries of engineering and material science to create lighter, stronger, and more efficient components. Among these critical components are valve housings, integral to controlling fluid and gas flow within aircraft and spacecraft systems. Traditionally manufactured through subtractive methods like machining, these housings often face limitations in design complexity, material waste, and lead times. Metal 3D printing, also known as metal additive manufacturing (AM), offers a transformative approach to producing custom aerospace valve housings, unlocking unprecedented design freedom, optimizing material usage, and accelerating production cycles. This blog post delves into the advantages, considerations, and best practices for leveraging metal 3D printing for aerospace valve housings, highlighting how this technology is reshaping the future of aerospace manufacturing. At Metal3DP, we are at the forefront of this revolution, providing advanced 3D-печать equipment and high-performance metal powders to meet the stringent demands of the aerospace sector. Our industry-leading print volume, accuracy, and reliability ensure the production of mission-critical parts that adhere to the highest standards.
Key Applications of 3D Printed Valve Housings in Aerospace
Metal 3D printed valve housings are finding increasing utility across a diverse range of aerospace applications. Their ability to be customized for specific needs makes them invaluable in complex systems where standard components may not suffice. Here are some key areas where 3D printed valve housings are making a significant impact:
- Fuel Systems: Controlling the flow of fuel is paramount in aircraft and spacecraft. 3D printing enables the creation of lightweight and geometrically optimized valve housings for fuel lines, manifolds, and regulators, enhancing fuel efficiency and overall system performance.
- Hydraulic Systems: Aerospace hydraulic systems rely on precise control of fluid power for various functions, including landing gear deployment, flight control surfaces, and braking systems. Metal AM allows for the production of intricate valve housings with integrated channels and features, reducing the number of components and potential leak points.
- Environmental Control Systems (ECS): Maintaining cabin pressure and temperature requires sophisticated air management systems. 3D printed valve housings can be tailored to the specific airflow requirements and spatial constraints of ECS, leading to more efficient and compact designs.
- Системы охлаждения: Effective thermal management is crucial for the performance and longevity of aerospace electronics and engines. Custom-designed valve housings produced via metal 3D printing can optimize the flow of coolant, ensuring efficient heat dissipation in critical areas.
- Satellite Propulsion: In space applications, minimizing weight is critical. 3D printed valve housings for satellite propulsion systems can be designed with complex internal geometries that reduce mass while maintaining structural integrity and performance under extreme conditions.
- Testing and Prototyping: Before mass production, aerospace components undergo rigorous testing. Metal 3D printing allows for the rapid creation of prototype valve housings with design iterations that can be quickly evaluated, significantly accelerating the development process.
Metal3DP understands the unique demands of these applications and offers tailored solutions, including a wide range of high-performance metal powders and advanced printing technologies, to meet the specific requirements of the aerospace industry.
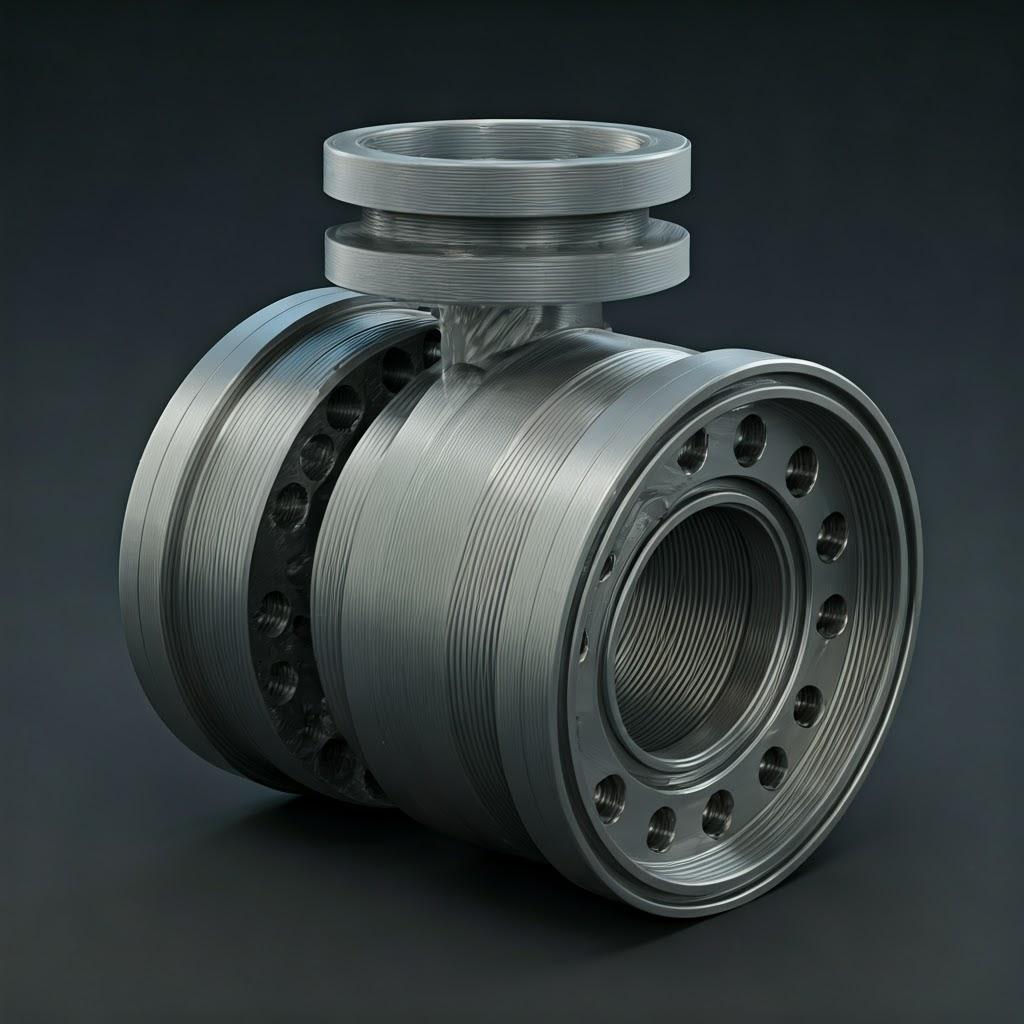
Advantages of Metal Additive Manufacturing for Aerospace Valve Housings
Compared to traditional manufacturing methods, metal 3D printing offers a compelling array of advantages for the production of aerospace valve housings:
- Свобода и сложность дизайна: AM allows for the creation of intricate internal channels, complex geometries, and consolidated parts that are difficult or impossible to achieve with conventional machining. This design flexibility can lead to improved fluid flow, reduced weight, and enhanced functionality.
- Облегчение: The aerospace industry is constantly striving to reduce weight. Metal 3D printing enables the optimization of part designs with features like lattice structures and thin walls, leading to significant weight savings without compromising structural integrity.
- Эффективность материала: Subtractive manufacturing processes often result in significant material waste. Additive manufacturing, as the name suggests, builds parts layer by layer, using only the material needed for the component. This reduces material costs and promotes sustainability.
- Rapid Prototyping and Reduced Lead Times: Metal 3D printing significantly accelerates the prototyping process. Design iterations can be quickly produced and tested, reducing time-to-market. For production, AM can also offer shorter lead times for complex, low-volume parts compared to traditional tooling-dependent methods.
- Кастомизация и производство по требованию: Each aerospace application may have unique requirements. Metal 3D printing allows for the production of highly customized valve housings tailored to specific needs, even in small quantities. This eliminates the need for large production runs and warehousing of standard parts.
- Повышенная производительность: By optimizing the design and material selection, metal 3D printing can lead to valve housings with improved performance characteristics, such as higher strength-to-weight ratios, better fatigue resistance, and enhanced thermal management.
- Консолидация частей: AM can enable the integration of multiple components into a single 3D printed part, reducing the number of joints, fasteners, and assembly steps. This can lead to increased reliability and reduced manufacturing costs.
На сайте Metal3DP, our Selective Electron Beam Melting (SEBM) printers are particularly well-suited for producing complex aerospace components with high accuracy and material integrity, further enhancing these advantages.
Material Selection: Why Ti-6Al-4V and 17-4PH Excel
The choice of material is critical for aerospace valve housings, as they must withstand demanding operating conditions, including high pressures, extreme temperatures, and corrosive environments. Ti-6Al-4V (Titanium Grade 5) and 17-4PH stainless steel are two high-performance alloys frequently used in metal 3D printing for aerospace applications, and for good reason:
Ti-6Al-4V (Titanium Grade 5):
- Высокое соотношение прочности и веса: Titanium alloys are renowned for their exceptional strength relative to their density, making Ti-6Al-4V ideal for weight-sensitive aerospace components.
- Отличная коррозионная стойкость: This alloy exhibits superior resistance to a wide range of corrosive environments, crucial for long-term reliability in aerospace applications.
- Good Fatigue Resistance: Aerospace components are subjected to cyclic loading. Ti-6Al-4V offers excellent fatigue strength, ensuring the longevity of valve housings.
- Биосовместимость: While not always a primary concern for valve housings, the biocompatibility of Ti-6Al-4V makes it suitable for certain specialized aerospace applications.
Нержавеющая сталь 17-4PH:
- Высокая прочность и твердость: 17-4PH is a martensitic precipitation-hardening stainless steel known for its high strength and hardness, achievable through heat treatment.
- Хорошая коррозионная стойкость: This alloy offers good resistance to atmospheric corrosion and many mild environments.
- Универсальность: 17-4PH is readily weldable and machinable in its annealed state, making it a versatile material for various aerospace components.
- Эффективность затрат: Compared to some other aerospace-grade alloys, 17-4PH can be a more cost-effective option for applications where its properties meet the requirements.
Metal3DP offers a comprehensive range of high-quality metal powders, including Ti-6Al-4V and 17-4PH, specifically optimized for laser and electron beam powder bed fusion processes. Our advanced powder making system ensures high sphericity and flowability, critical for producing dense, high-quality metal parts with superior mechanical properties.
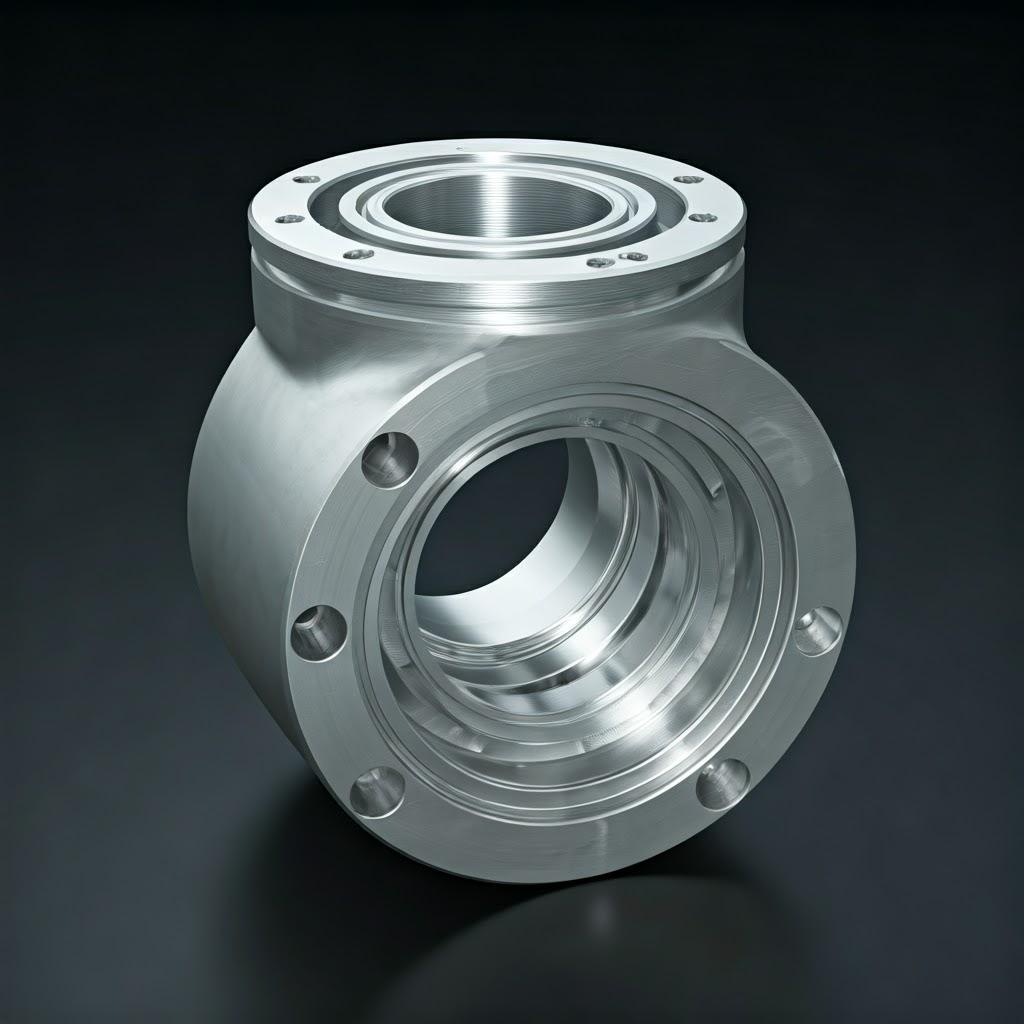
Design Optimization for 3D Printed Aerospace Valve Housings
Designing for metal additive manufacturing requires a different mindset compared to traditional subtractive methods. To fully leverage the capabilities of 3D printing for aerospace valve housings, engineers must consider several key design principles:
- Topology Optimization: This computational method can identify and remove material from low-stress areas of a design, resulting in lightweight yet structurally sound parts. For valve housings, topology optimization can be used to minimize weight while ensuring the component can withstand the required pressures and loads.
- Решетчатые структуры: Incorporating lattice structures within the valve housing design can significantly reduce weight without sacrificing stiffness. These intricate, repeating patterns provide excellent strength-to-weight ratios and can be tailored to specific load-bearing requirements.
- Консолидация частей: As mentioned earlier, AM allows for the integration of multiple components into a single printed part. For valve housings, this could involve incorporating mounting features, fluid channels, or even sensors directly into the design, reducing assembly time and potential failure points.
- Internal Channels and Complex Geometries: One of the key advantages of metal 3D printing is the ability to create complex internal features, such as optimized flow channels within the valve housing. These can be designed to minimize pressure drop and maximize efficiency.
- Self-Supporting Geometries: Designing parts with self-supporting angles can reduce or eliminate the need for support structures during printing. This not only saves material and print time but also simplifies post-processing.
- Consideration of Build Orientation: The orientation of the part during the printing process can affect surface finish, dimensional accuracy, and the need for support structures. Careful consideration of build orientation is crucial for optimizing the final part quality.
- Wall Thickness and Feature Size: While AM offers great design freedom, there are still limitations related to minimum wall thickness and feature size that must be considered to ensure successful printing and structural integrity.
На сайте Metal3DP, our application development services provide expert guidance on designing for metal additive manufacturing, helping aerospace engineers optimize their valve housing designs for performance, weight, and manufacturability using our advanced SEBM technology.
Achieving Precision: Tolerance and Surface Finish in AM Valve Housings
In aerospace applications, precision is paramount. Valve housings must adhere to strict dimensional tolerances and often require specific surface finishes to ensure proper sealing and functionality. Metal 3D printing technologies have made significant strides in achieving these requirements:
- Точность размеров: Modern metal 3D printers, like those offered by Metal3DP, can achieve high levels of dimensional accuracy. However, the achievable tolerance can be influenced by factors such as part geometry, material, build orientation, and post-processing techniques. It’s crucial to discuss tolerance requirements with the chosen service provider early in the design process.
- Отделка поверхности: The as-printed surface finish of metal 3D printed parts is typically rougher than that achieved by machining. The surface roughness depends on the powder particle size, layer thickness, and printing process. For valve housings requiring smooth sealing surfaces, post-processing steps like machining, polishing, or abrasive flow machining are often necessary.
- Controlling Distortion: Thermal stresses during the printing process can lead to distortion in the final part. Design optimization, support structure strategies, and controlled cooling rates are essential to minimize distortion and achieve the required dimensional accuracy.
- Inspection and Quality Control: Rigorous inspection procedures, including coordinate measuring machines (CMMs) and non-destructive testing (NDT) methods, are employed to verify that 3D printed aerospace valve housings meet the specified dimensional tolerances and quality standards.
Metal3DP is committed to delivering high-quality metal 3D printed parts with tight tolerances and controlled surface finishes. Our advanced equipment and expertise in post-processing ensure that aerospace valve housings meet the demanding specifications of the industry.
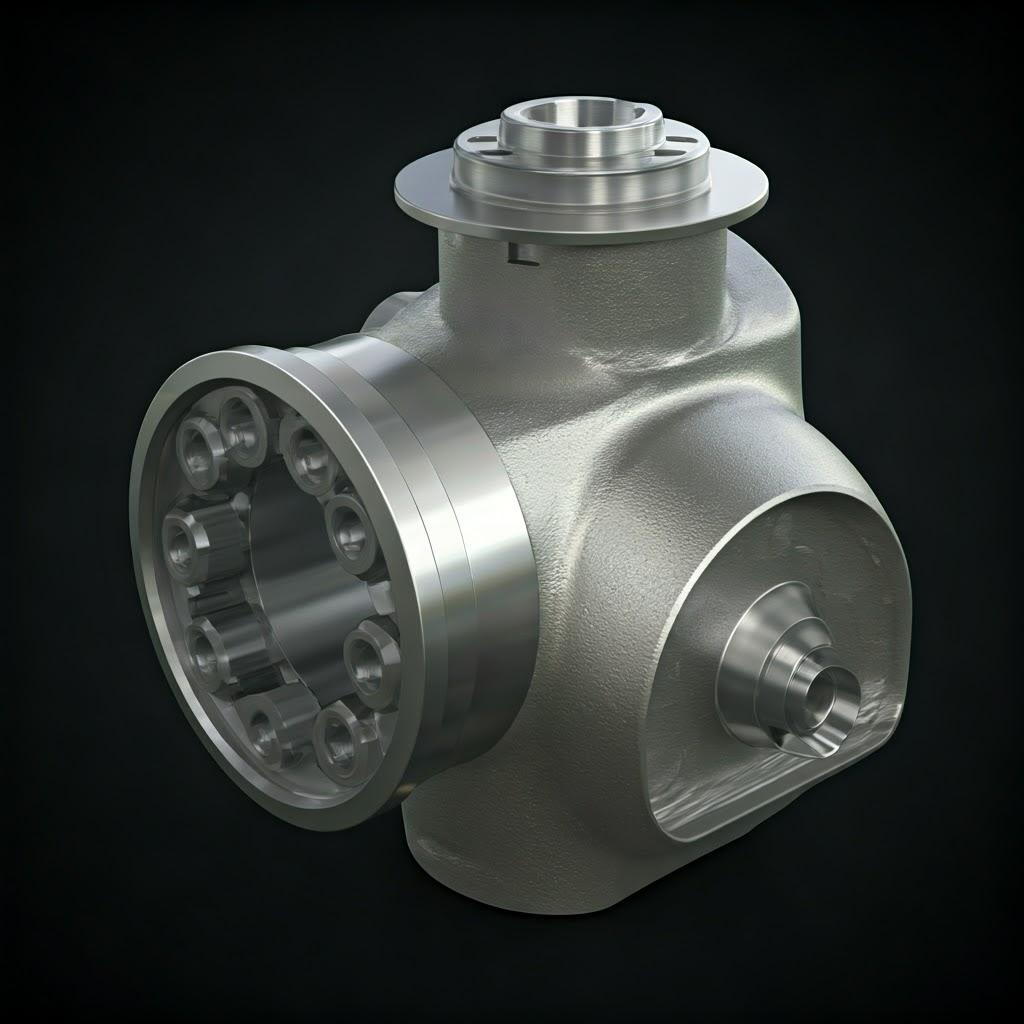
Post-Processing for Aerospace-Grade Valve Housings
While metal 3D printing offers near-net-shape manufacturing, post-processing steps are often required to achieve the final properties and surface finish needed for aerospace valve housings. Common post-processing operations include:
- Удаление опоры: Support structures are often necessary during the printing process to prevent warping and ensure the correct geometry of overhanging features. These supports need to be carefully removed after printing, which can involve manual breaking, cutting, or machining.
- Stress Relief Heat Treatment: To alleviate internal stresses that may have built up during the rapid heating and cooling cycles of the printing process, a stress relief heat treatment is often performed. This improves the dimensional stability and mechanical properties of the part.
- Горячее изостатическое прессование (HIP): HIP is a process that involves subjecting the printed part to high pressure and temperature in an inert atmosphere. This can eliminate internal porosity, increase density, and improve the mechanical properties, particularly fatigue resistance, which is critical for aerospace applications.
- CNC Machining: For critical surfaces requiring very tight tolerances or specific surface finishes, CNC machining may be employed as a secondary operation. This can include operations like drilling, tapping, milling, and turning.
- Отделка поверхности: Depending on the application, various surface finishing techniques may be used, such as polishing, grinding, abrasive flow machining, or coating, to achieve the desired surface roughness and corrosion resistance.
- Неразрушающий контроль (NDT): Techniques like ultrasonic testing, radiographic inspection, and dye penetrant inspection are used to ensure the internal integrity and surface quality of the printed valve housings, verifying that they are free from defects.
Metal3DP offers comprehensive post-processing services to ensure that our 3D printed metal parts meet the stringent requirements of the aerospace industry. We understand the critical nature of these components and employ rigorous quality control measures at every stage of the manufacturing process.
Overcoming Challenges in 3D Printing Aerospace Components
While metal 3D printing offers numerous advantages, there are also challenges that need to be addressed to ensure the successful production of aerospace valve housings:
- Warping and Distortion: As mentioned earlier, thermal stresses during the printing process can lead to warping and distortion. Careful design, optimized build parameters, and effective support strategies are crucial to mitigate these issues.
- Пористость: Internal porosity can compromise the mechanical properties and fatigue resistance of 3D printed parts. Optimizing printing parameters, material selection, and employing post-processing techniques like HIP can minimize porosity.
- Отделка поверхности: Achieving the required surface finish for sealing surfaces often necessitates additional post-processing, which adds to the overall manufacturing time and cost.
- Удаление опоры: Removing support structures from complex geometries can be challenging and may leave surface marks that require further finishing. Designing for minimal support and employing dissolvable support materials can help alleviate this.
- Material Qualification and Certification: Aerospace materials and processes are subject to stringent qualification and certification requirements. Ensuring that the chosen metal powders and printing processes meet these standards is crucial for aerospace applications. Metal3DP is committed to using high-quality, certified materials and adhering to strict quality control procedures.
- Cost and Scalability: While the cost-effectiveness of metal 3D printing for complex, low-volume parts is well-established, achieving cost-effective scalability for high-volume production of smaller, less complex parts can still be a challenge compared to traditional methods.
By understanding these challenges and implementing best practices in design, material selection, printing, and post-processing, it is possible to overcome these hurdles and successfully leverage metal 3D printing for the production of high-performance aerospace valve housings.
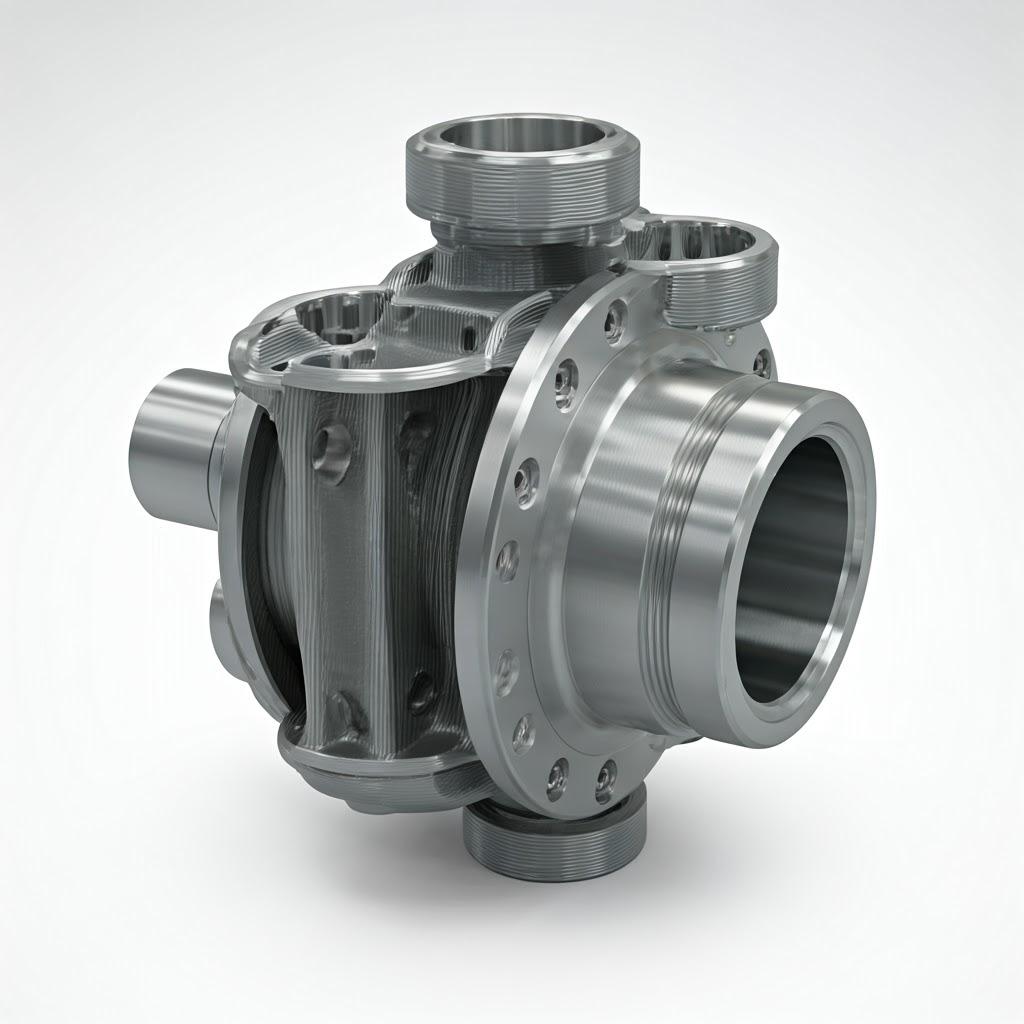
Selecting a Trusted Metal 3D Printing Service Provider
Choosing the right metal 3D printing service provider is crucial for the successful production of aerospace valve housings. Given the critical nature of these components, it’s essential to partner with a provider that has the expertise, experience, and quality systems in place. Here are some key factors to consider when evaluating potential suppliers:
- Industry Experience and Expertise: Look for a provider with a proven track record in serving the aerospace industry. They should have a deep understanding of the specific material requirements, quality standards, and regulatory landscape of the sector. Metal3DP has decades of collective expertise in metal additive manufacturing and partners with organizations in aerospace and other demanding industries.
- Material Capabilities: Ensure the provider offers the specific metal powders required for your application, such as Ti-6Al-4V and 17-4PH. They should have experience processing these materials and be able to provide material certifications and data sheets.
- Printing Technology and Equipment: Understand the types of metal 3D printing technologies the provider utilizes. For high-precision aerospace components, technologies like Selective Electron Beam Melting (SEBM), offered by Metal3DP, are often preferred for their accuracy and material integrity.
- Quality Assurance and Certifications: The provider should have robust quality management systems in place, including certifications relevant to the aerospace industry (e.g., AS9100). They should also have comprehensive inspection and testing capabilities to ensure the parts meet the required specifications.
- Post-Processing Services: Determine if the provider offers the necessary post-processing services, such as support removal, heat treatment, HIP, CNC machining, and surface finishing, to deliver a готовый-to-use component.
- Design and Engineering Support: A good service provider should offer design consultation and engineering support to help optimize your valve housing design for additive manufacturing and ensure it meets the functional requirements. Metal3DP provides comprehensive solutions spanning advanced metal powders and application development services.
- Communication and Customer Service: Effective communication and responsive customer service are essential for a smooth and successful project. Choose a provider that is proactive, transparent, and willing to collaborate closely with you.
- Lead Times and Scalability: Discuss lead times for prototyping and production, as well as the provider’s capacity to scale up production if your needs evolve.
Understanding the Costs and Lead Times for AM Valve Housings
The cost and lead time for metal 3D printed aerospace valve housings can vary depending on several factors:
- Part Complexity and Size: More complex geometries and larger parts typically require longer print times and more post-processing, which can increase costs.
- Выбор материала: The cost of the metal powder itself can vary significantly between different alloys. Aerospace-grade materials like Ti-6Al-4V can be more expensive than standard stainless steels.
- Build Volume and Density: The amount of material used and the build volume occupied on the printer will influence the cost. Denser parts may also require longer print times.
- Требования к постобработке: The extent and type of post-processing required (e.g., support removal, heat treatment, machining, surface finishing) will impact both cost and lead time.
- Объем производства: While metal 3D printing can be cost-effective for low to medium volumes and highly customized parts, the cost per part may decrease with larger production runs due to economies of scale.
- Service Provider’s Pricing Structure: Different service providers may have varying pricing models based on factors like machine time, material usage, and labor costs.
Сроки выполнения:
- Создание прототипов: Metal 3D printing offers significantly faster prototyping lead times compared to traditional tooling-dependent methods. Prototypes can often be produced in days or weeks, allowing for rapid design iteration.
- Производство: Production lead times depend on factors such as part complexity, volume, material availability, and post-processing requirements. While AM can offer shorter lead times for complex, low-volume production, larger volumes may require more time.
It’s crucial to discuss cost and lead time expectations with your chosen metal 3D printing service provider early in the project to ensure they align with your budget and timeline. Metal3DP works closely with its customers to provide transparent cost estimates and realistic lead times based on their specific requirements.
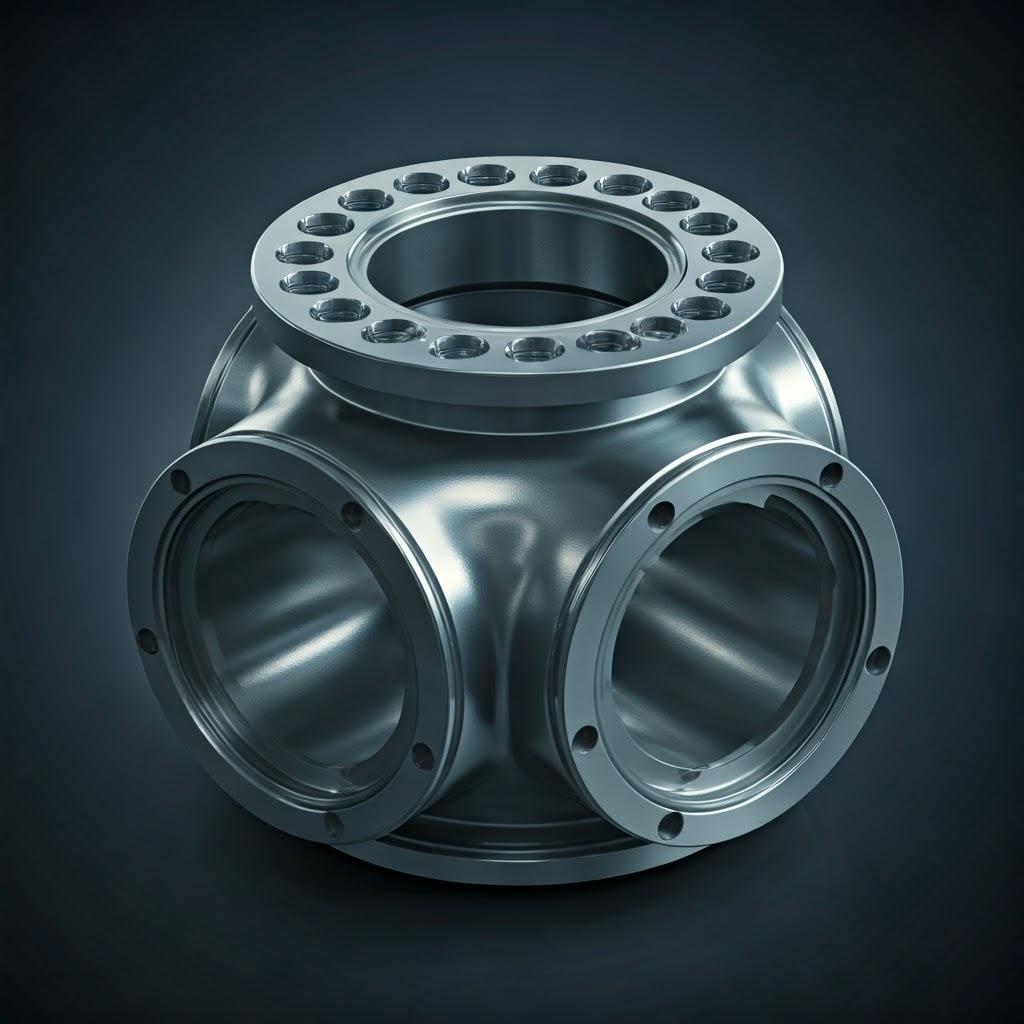
Часто задаваемые вопросы (FAQ)
- What are the typical tolerances achievable with metal 3D printing for aerospace valve housings?
- Achievable tolerances depend on the specific printing technology, material, and part geometry. Generally, tolerances of ±0.1 mm or better can be achieved on critical dimensions with processes like SEBM. However, tighter tolerances may require post-processing like CNC machining.
- Is metal 3D printing cost-effective for producing aerospace valve housings?
- Metal 3D printing can be highly cost-effective for low to medium volumes, complex designs, and customized parts where traditional manufacturing methods may involve significant tooling costs or multiple manufacturing steps. For high-volume production of simpler parts, traditional methods may still be more economical.
- What non-destructive testing methods are used to inspect 3D printed aerospace valve housings?
- Common NDT methods used include ultrasonic testing (UT), radiographic inspection (RT), dye penetrant inspection (PT), and magnetic particle inspection (MT) to ensure the internal integrity and surface quality of the printed parts.
Conclusion: The Future of Aerospace Valve Housings with Metal 3D Printing
Metal 3D printing is revolutionizing the way aerospace valve housings are designed and manufactured. Its ability to enable complex geometries, reduce weight, optimize material usage, and accelerate production cycles offers significant advantages over traditional methods. With advancements in materials like Ti-6Al-4V and 17-4PH, coupled with sophisticated printing technologies and post-processing techniques, metal AM is empowering aerospace engineers to create high-performance, customized valve housings that meet the stringent demands of the industry.
As a leader in metal additive manufacturing, Metal3DP is committed to providing cutting-edge systems, high-quality metal powders, and comprehensive application development services to drive innovation in the aerospace sector. By embracing metal 3D printing, aerospace companies can unlock new possibilities for design, performance, and efficiency in their critical fluid control systems. Contact Metal3DP today to explore how our capabilities can power your organization’s additive manufacturing goals.
Поделиться
MET3DP Technology Co., LTD - ведущий поставщик решений для аддитивного производства со штаб-квартирой в Циндао, Китай. Наша компания специализируется на производстве оборудования для 3D-печати и высокопроизводительных металлических порошков для промышленного применения.
Сделайте запрос, чтобы получить лучшую цену и индивидуальное решение для вашего бизнеса!
Похожие статьи
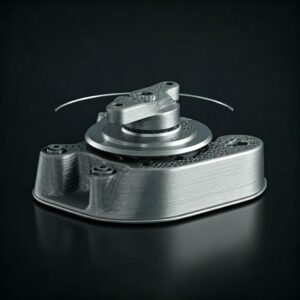
3D-печатные крепления для автомобильных радарных датчиков: Точность и производительность
Читать далее "О компании Met3DP
Последние обновления
Наш продукт
CONTACT US
Есть вопросы? Отправьте нам сообщение прямо сейчас! После получения Вашего сообщения мы всей командой выполним Ваш запрос.
Получите информацию о Metal3DP
Брошюра о продукции
Получить последние продукты и прайс-лист