Lightweight Antenna Bases for Satellites via AM
Оглавление
Introduction: Revolutionizing Satellite Hardware with Lightweight AM Antenna Bases
The aerospace industry, particularly the satellite sector, operates at the vanguard of technological innovation. Driven by the relentless pursuit of reduced launch costs, enhanced payload capacity, and improved mission performance, engineers and procurement specialists are constantly seeking breakthroughs in materials science, design methodologies, and manufacturing processes. One of the most transformative technologies impacting satellite hardware development today is аддитивное производство металлов (AM), commonly known as metal 3D-печать. This process offers unprecedented design freedom, enabling the creation of complex, lightweight, and highly optimized components that were previously impossible or prohibitively expensive to produce using traditional methods like CNC machining or casting.
Among the myriad of satellite components benefiting from this revolution, the antenna base stands out as a prime candidate for AM adoption. These structures, while seemingly simple, are critical for the mounting, alignment, and thermal management of satellite communication antennas. They must provide exceptional structural integrity to withstand the harsh launch environment and maintain precise pointing accuracy throughout the mission’s duration in the vacuum and extreme temperatures of space. Traditionally, antenna bases have often been subtractively machined from solid blocks of metal, leading to significant material waste and design constraints that limit weight optimization potential.
Enter metal AM. By building parts layer-by-layer directly from digital models using high-performance metal powders, manufacturers can achieve significant lightweighting – a paramount objective in satellite design where every gram saved translates directly into lower launch costs or increased payload capability. Additive manufacturing allows for the integration of complex internal lattice structures, topologically optimized geometries, and consolidated part designs, drastically reducing mass without compromising stiffness or strength. This capability is not just an incremental improvement; it represents a paradigm shift in how satellite hardware, including antenna bases, is conceived, designed, and produced. For aerospace engineers designing next-generation communication satellites and procurement managers sourcing aerospace component suppliers, understanding the potential of AM for critical structures like antenna bases is no longer optional; it’s essential for maintaining a competitive edge. Companies specializing in additive manufacturing aerospace solutions, like Met3dp, are at the forefront, providing the advanced materials and printing technologies necessary to realize these lightweight, high-performance designs.
The implications extend beyond mere weight reduction. AM facilitates:
- Быстрое создание прототипов и итерации: Design modifications can be implemented and tested much faster than with traditional tooling-based manufacturing.
- Консолидация частей: Multiple components of an antenna mounting assembly can potentially be combined into a single, complex AM part, reducing assembly time, potential points of failure, and overall system complexity.
- Supply Chain Resilience: On-demand digital manufacturing reduces reliance on complex, geographically dispersed supply chains and extensive tooling inventories.
- Novel Design Features: Integration of features like conformal cooling channels for thermal management or embedded RF structures becomes feasible.
This introductory section sets the stage, highlighting the convergence of satellite technology demands (lightweighting, performance) and the unique capabilities of metal AM. We will delve deeper into the specific functions of antenna bases, the compelling reasons to choose AM, the best materials for the job, and the crucial considerations for successful implementation. The goal is to provide engineers и procurement managers with the insights needed to leverage AM for producing next-generation, lightweight satellite antenna bases.
The Critical Role of Antenna Bases in Satellite Communication Systems
While antennas themselves are the active elements receiving and transmitting radio frequency (RF) signals, the antenna base serves as the critical structural interface between the antenna and the main body of the satellite. Its functions are multifaceted and vital for mission success, extending far beyond simply holding the antenna in place. Understanding these functions clarifies why optimizing the base’s design and manufacturing process is so crucial for overall satellite performance and reliability.
1. Structural Support and Load Bearing: The antenna base must securely anchor the antenna assembly to the satellite structure. This involves withstanding significant loads during various mission phases: * Launch Loads: The most demanding phase, subjecting the satellite to extreme vibrations, acoustic noise, and g-forces. The base must prevent antenna detachment or misalignment under these dynamic conditions. Finite Element Analysis (FEA) is critical in the design phase to simulate these loads and ensure the base’s structural integrity. B2B suppliers must demonstrate robust design validation processes. * Deployment Loads: For deployable antennas, the base often incorporates or interfaces with deployment mechanisms, experiencing stresses during the unfurling process. * On-Orbit Loads: While microgravity dominates, slight torques from station-keeping thrusters or momentum wheels can induce minor stresses that the base must handle over the mission lifetime (often 15+ years).
2. Precise Alignment and Pointing Stability: For most communication antennas (e.g., parabolic dishes, phased arrays), precise pointing accuracy is paramount for maintaining communication links with ground stations or other satellites. The antenna base plays a key role here: * Manufacturing Tolerance: The base must be manufactured to tight dimensional tolerances to ensure the antenna is mounted exactly according to the design specifications. Any deviation can lead to pointing errors. * Термическая стабильность: Satellites experience extreme temperature fluctuations orbiting the Earth, cycling between direct sunlight and shadow. Materials expand and contract with temperature changes (Coefficient of Thermal Expansion – CTE). The antenna base material must have a suitable CTE, and the design must minimize thermally induced distortions that could shift the antenna’s pointing direction. Low-CTE materials or clever thermo-mechanical designs are often required. Metal AM allows for complex geometries that can inherently mitigate some thermal distortion effects. * Long-Term Stability: The base must maintain its dimensional stability over the mission’s lifetime, resisting creep or material degradation due to radiation or thermal cycling.
3. Thermal Management Interface: Antennas, particularly high-power transmitting antennas and associated electronics (like Solid State Power Amplifiers – SSPAs often mounted nearby), generate significant heat. This heat must be efficiently dissipated to prevent overheating, which can degrade RF performance and reduce component lifespan. The antenna base often serves as a crucial part of the thermal path: * Conductive Path: The base provides a conductive path to transfer heat from the antenna or associated electronics to the satellite’s main thermal control system (e.g., heat pipes, radiators). The thermal conductivity of the base material is therefore a critical property. * Integrated Cooling Features: AM allows for the integration of complex internal cooling channels or optimized conductive pathways directly into the base structure, improving thermal management efficiency beyond what’s possible with traditional machining. This is a key area where additive manufacturing aerospace suppliers can offer significant value.
4. RF Considerations (in some designs): While primarily structural, the antenna base’s material and geometry can sometimes influence the antenna’s RF performance, especially at higher frequencies. * Свойства материала: The base material should ideally be non-interfering or have predictable RF properties if it’s close to the antenna’s radiating elements. * Ground Plane: In some configurations, the base might form part of the antenna’s ground plane, requiring specific conductive properties and surface characteristics. * Passive Intermodulation (PIM): For multi-signal communication payloads, PIM generated by junctions or specific material interactions can be a concern. Base design and material choice must consider PIM mitigation.
5. Integration with Other Subsystems: The antenna base must seamlessly integrate with various other satellite subsystems: * Structure: Mounting interfaces (bolts, inserts). * Mechanisms: Interfaces for deployment or pointing mechanisms. * Cabling: Provisions for routing RF and data cables. * Thermal Control: Interfaces with heat straps, pipes, or radiators.
Procurement Perspective: При поиске поставщиков satellite hardware, procurement managers must ensure potential suppliers understand these critical functions. Key considerations include: * Verified Performance: Does the supplier have a track record of producing components meeting stringent aerospace requirements (e.g., AS9100 certification)? * Material Traceability: Can the supplier provide full traceability for space-grade materials? * Testing Capabilities: Does the supplier offer or partner for necessary testing (vibration, thermal vacuum, dimensional verification)? * Design for Manufacturability (DfM/DfAM): Can the supplier collaborate with engineering teams to optimize the base design for the chosen manufacturing process (traditional or AM)?
In summary, the satellite antenna base is a highly engineered component demanding strength, stiffness, precision, thermal stability, and efficient thermal conductivity. Its successful design and fabrication are non-negotiable for reliable satellite communications. The complexity and multi-functional nature of the base make it an ideal candidate for the design freedoms and optimization potential offered by metal additive manufacturing.
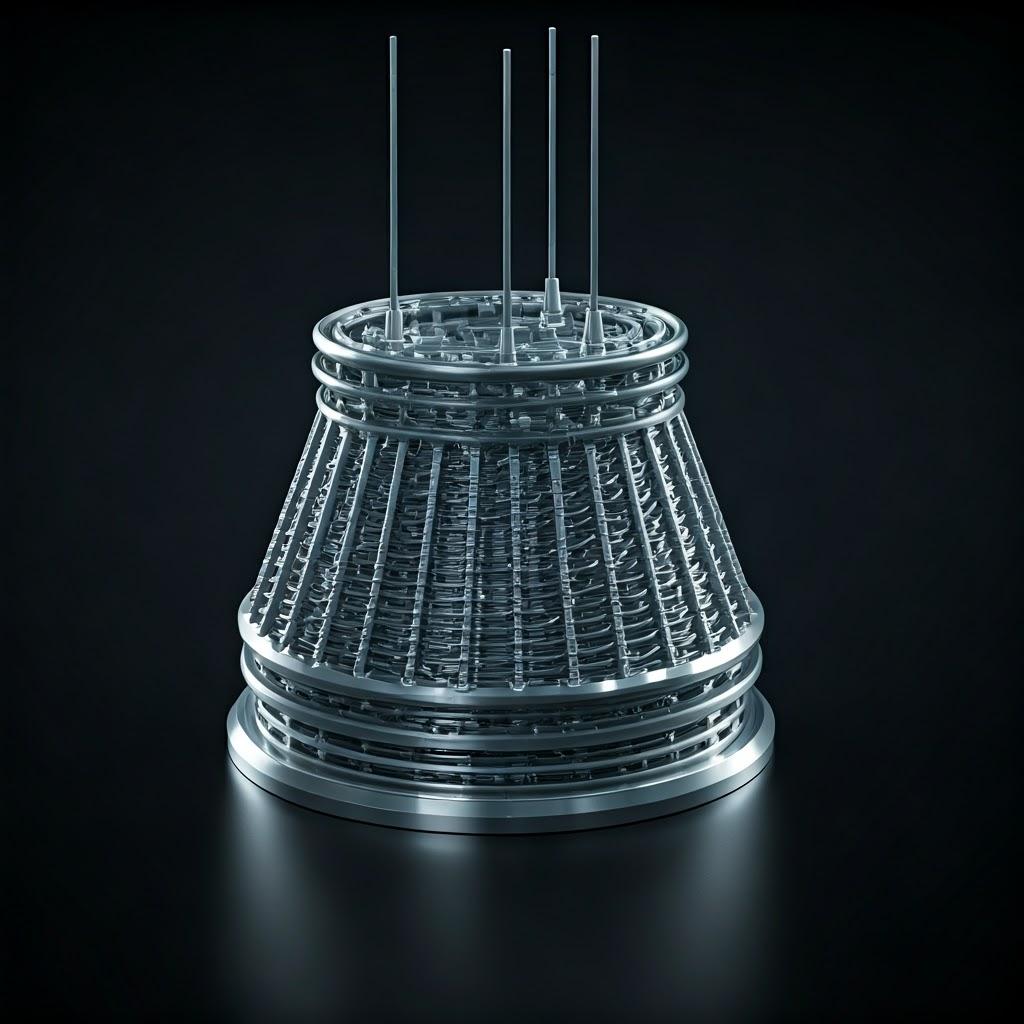
Why Metal Additive Manufacturing is Ideal for Satellite Antenna Bases
The demanding requirements placed on satellite antenna bases – structural robustness, extreme lightweighting, thermal stability, and precise alignment – align remarkably well with the unique capabilities of metal additive manufacturing (AM). While traditional subtractive manufacturing (like CNC machining) has long been the standard, AM offers compelling advantages that are driving its adoption for these critical space hardware components. For aerospace component suppliers and satellite manufacturers, leveraging AM for antenna bases translates into tangible benefits in performance, cost, and lead time.
Let’s explore the key reasons why metal AM is becoming the preferred method:
1. Unparalleled Lightweighting through Design Freedom: This is arguably the most significant driver for AM in aerospace. Launch costs are often calculated per kilogram, making mass reduction paramount. * Topology Optimization: AM enables the use of topology optimization software, which algorithmically removes material from areas where it’s not structurally necessary, leaving behind an organic, highly efficient load-bearing structure. This can achieve weight savings of 30-70% or more compared to traditionally machined parts, while maintaining or even increasing stiffness. Creating these complex, optimized shapes is often impossible with subtractive methods. * Internal Lattice Structures: AM allows the integration of intricate internal lattice structures (e.g., honeycombs, gyroids, stochastic foams) within the solid walls of the antenna base. These lattices provide excellent stiffness-to-weight ratios and can also be tailored for specific vibration damping or thermal properties. * Сокращение отходов материалов: Unlike subtractive machining, which starts with a solid block and removes material (often resulting in >80% waste, known as the buy-to-fly ratio), AM is an additive process, using only the material needed to build the part, plus support structures. This significantly reduces material consumption, especially important for expensive space-grade alloys.
2. Manufacturing Complex Geometries: Antenna bases often require complex shapes to interface with curved satellite panels, integrate mounting points for various antenna types, and incorporate features for thermal management or cable routing. * Объединение частей: AM can combine multiple traditionally separate components (brackets, mounts, thermal straps) into a single, monolithic antenna base structure. This reduces part count, eliminates fasteners (potential failure points), simplifies assembly, shortens supply chains, and often reduces overall weight and envelope. * Integrated Functionality: Features like internal cooling channels following complex paths, optimized mounting interfaces, or integrated waveguides can be built directly into the base structure during the AM process, enhancing performance and reducing assembly complexity.
3. Accelerated Development and Prototyping: The satellite industry faces pressure to reduce development cycles and deploy constellations faster. * Быстрая итерация: AM allows design engineers to quickly produce and test multiple design iterations of an antenna base without the need for expensive tooling or complex machining setups. A new design can be printed within days or weeks, compared to potentially months for traditional methods involving tooling. This rapid feedback loop accelerates the optimization process. * Tool-less Production: AM eliminates the need for custom jigs, fixtures, or molds associated with traditional manufacturing, significantly reducing lead times, especially for low-to-medium volume production typical of satellite programs.
4. Material Flexibility and Advanced Alloys: AM processes can work with a growing range of high-performance metal powders specifically developed or suited for demanding aerospace applications. * Optimized Materials: Materials like Scalmalloy® (a high-strength Aluminum-Magnesium-Scandium alloy) or specialized Titanium alloys (like Ti6Al4V ELI) offer superior specific strength (strength-to-weight ratio) compared to traditional aerospace aluminum grades like 6061 or 7075, especially when optimized through AM processing. * Custom Alloy Development: The powder-based nature of AM potentially allows for the use of custom or novel alloy compositions tailored for specific performance requirements (e.g., extremely low CTE, high thermal conductivity), although qualification for space is rigorous.
5. Potential for Enhanced Performance: The design freedom offered by AM can directly translate into improved functional performance. * Improved Thermal Management: Complex internal channels or optimized conductive paths designed via AM can lead to more efficient heat dissipation from the antenna or associated electronics compared to solid machined bases. * Enhanced Structural Efficiency: Topology optimization ensures that material is placed exactly where it’s needed for stiffness and strength, leading to structurally superior designs for a given weight.
Considerations for Procurement and Engineering: While the benefits are compelling, adopting AM requires careful consideration: * Design for Additive Manufacturing (DfAM): Engineers need to design parts specifically for the AM process, considering factors like build orientation, support structures, residual stress, and achievable tolerances. Partnering with an experienced additive manufacturing aerospace supplier like Met3dp, which offers expertise in DfAM, is crucial. Explore Met3dp’s metal 3D printing capabilities for insights. * Квалификация процесса: Ensuring the repeatability and reliability of the AM process is critical for mission-critical space hardware. This involves rigorous process control, material characterization, and non-destructive testing (NDT). * Постобработка: AM parts typically require post-processing steps like heat treatment, support removal, surface finishing, and machining of critical interfaces to meet final specifications. These steps must be factored into the overall production plan and cost.
In conclusion, the transition towards using metal AM for satellite antenna bases is driven by a powerful combination of weight reduction potential, design complexity enablement, faster development cycles, and the ability to use advanced materials. While challenges exist, the advantages offered by additive manufacturing vs traditional machining for these components are often too significant to ignore for competitive satellite design and procurement satellite hardware strategies.
Material Focus: Scalmalloy® and AlSi10Mg for Space Applications
Selecting the right material is fundamental to the success of any aerospace component, and satellite antenna bases are no exception. The material must meet stringent requirements for mechanical strength, stiffness, low density, thermal properties, and behavior in the space environment (e.g., resistance to radiation, low outgassing). For metal additive manufacturing of antenna bases, two aluminum alloys have emerged as prominent choices: Scalmalloy® и AlSi10Mg. Understanding their respective properties, advantages, and limitations is crucial for engineers making material selection decisions and for procurement managers sourcing поставщики металлических порошков or AM services.
Understanding the Base Materials:
- AlSi10Mg: This is a traditional aluminum casting alloy that has been successfully adapted for additive manufacturing, particularly Laser Powder Bed Fusion (LPBF). It primarily consists of Aluminum (Al), Silicon (Si, ~10%), and Magnesium (Mg, <0.5%). Silicon improves fluidity and castability (beneficial for AM melt pool behavior) and provides moderate strength through precipitation hardening. Magnesium further enhances strength.
- Scalmalloy®: Developed specifically for additive manufacturing by APWorks (an Airbus subsidiary), Scalmalloy® is a high-performance aluminum-magnesium-scandium (Al-Mg-Sc) alloy. The addition of Scandium (Sc) and Zirconium (Zr) creates fine precipitates during heat treatment, leading to significantly higher strength compared to traditional aluminum alloys like AlSi10Mg, particularly at room and moderately elevated temperatures.
Comparative Analysis for Antenna Base Applications:
Недвижимость | AlSi10Mg (As-Built / Stress Relieved) | Scalmalloy® (Heat Treated) | Significance for Antenna Base |
---|---|---|---|
Плотность | ~2.67 g/cm³ | ~2.66 g/cm³ | Both are lightweight aluminum alloys, excellent for mass reduction. Negligible difference. |
Yield Strength (Rp0.2) | ~230-270 MPa | ~480-520 MPa | Critical. Scalmalloy® offers nearly double the yield strength, allowing for more aggressive lightweighting or higher safety factors. |
Ultimate Tensile Strength (Rm) | ~350-450 MPa | ~520-540 MPa | Critical. Higher UTS in Scalmalloy® provides greater resistance to failure under ultimate loads (e.g., launch). |
Удлинение при разрыве | ~6-12% | ~10-15% | Indicates ductility. Scalmalloy® generally offers better ductility alongside its higher strength. |
Specific Strength (UTS/Density) | Умеренно-высокий | Очень высокий | Key Advantage. Scalmalloy®’s high strength-to-weight ratio is ideal for aerospace lightweighting. |
Stiffness (Young’s Modulus) | ~70 GPa | ~75 GPa | Slightly higher stiffness for Scalmalloy®, contributing to better structural rigidity. |
Усталостная прочность | Умеренный | Высокая | Important for components experiencing cyclic loading (vibration during launch). Scalmalloy® excels. |
Теплопроводность | ~120-140 W/(m·K) | ~110-130 W/(m·K) | Both offer good thermal conductivity for aluminum alloys, suitable for thermal management. AlSi10Mg might have a slight edge depending on heat treatment. |
Максимальная температура эксплуатации | ~100-150 °C | ~200-250 °C | Scalmalloy® retains strength better at moderately elevated temperatures relevant in some satellite thermal environments. |
Коррозионная стойкость | Хороший | Очень хорошо (Especially stress corrosion cracking) | Important for ground handling and potentially long-term space exposure. Scalmalloy® generally performs better. |
Свариваемость | Good (relative to other Al alloys) | Хороший | Relevant if welding is required post-AM, though part consolidation aims to minimize this. |
Printability (LPBF) | Отличный (Well-established parameters) | Good (Requires optimized parameters) | AlSi10Mg is often considered easier to print with wider process windows. Scalmalloy® requires careful parameter control for optimal properties. |
Термообработка | Stress Relief / T6 (optional) | Требуется (Solution + Aging) | Scalmalloy® requires specific heat treatment to achieve its high-strength properties. AlSi10Mg can be used as-built/stress-relieved or T6 treated for higher strength. |
Стоимость | Lower (Powder & Processing) | Выше (Powder cost, licensing, heat treatment) | Scalmalloy® powder is significantly more expensive due to scandium content and potential licensing fees. Processing and heat treatment also add cost. |
Доступность | Widely available from many suppliers | More limited suppliers, but growing | AlSi10Mg powder is ubiquitous. Scalmalloy® availability is increasing but still more restricted. |
Export to Sheets
Why Choose Which Material?
- Choose AlSi10Mg when:
- Cost is a primary driver and the absolute highest strength-to-weight ratio is not strictly necessary.
- The design constraints allow for sufficient structural integrity with its moderate strength.
- Established process parameters and wider supplier availability are preferred.
- Slightly better thermal conductivity is advantageous.
- Rapid prototyping where achieving maximum final strength isn’t the initial focus.
- Choose Scalmalloy® when:
- Maximum lightweighting is the top priority, leveraging its superior specific strength.
- The antenna base experiences high structural loads or significant vibration (launch).
- Slightly elevated operating temperatures are expected.
- High fatigue resistance is required.
- The budget accommodates the higher material and processing costs for a significant performance gain.
- Partnering with an AM provider experienced specifically with Scalmalloy® processing and heat treatment is feasible.
Met3dp’s Role in Material Supply and Expertise:
Selecting the right material is only part of the equation; the quality of the metal powder itself is paramount for achieving consistent and reliable results in additive manufacturing. Poor powder quality (e.g., irregular morphology, high satellite content, internal porosity, inconsistent particle size distribution) can lead to defects in the final printed part, compromising its mechanical properties and performance.
This is where specialized поставщики металлических порошков like Met3dp play a critical role. Leveraging advanced powder production techniques such as Vacuum Induction Melting Gas Atomization (VIGA) и Плазменный вращающийся электродный процесс (PREP), Met3dp ensures the production of высококачественные металлические порошки with characteristics essential for demanding aerospace AM applications:
- Высокая сферичность: Smooth, spherical powder particles ensure good flowability in the AM machine’s recoating system, leading to uniform powder bed density and reducing the risk of voids or defects.
- Low Porosity: Minimizing internal gas pores within the powder particles prevents this porosity from transferring to the final part.
- Controlled Particle Size Distribution (PSD): Optimizing the PSD for specific AM processes (like LPBF) ensures efficient packing and melting.
- High Purity & Controlled Chemistry: Strict control over alloy composition and minimizing contaminants are crucial for achieving the desired mechanical properties and ensuring batch-to-batch consistency.
While Met3dp manufactures a wide range of powders including Titanium alloys, superalloys, and stainless steels often used in aerospace, their expertise in powder atomization technology means they are well-positioned to supply high-quality aluminum alloy powders like AlSi10Mg or potentially work with partners or customers on alloys with similar characteristics to Scalmalloy®. Their commitment to quality control ensures that engineers procuring satellite hardware can rely on the consistency and performance of the feedstock material, which is the foundation of a reliable AM component. Consulting with experts at Met3dp can provide valuable insights into material selection and powder specifications tailored for specific satellite antenna base requirements. Their focus on advanced powder making systems directly translates to higher quality inputs for critical space components.
In summary, both AlSi10Mg and Scalmalloy® offer viable paths for producing lightweight satellite antenna bases via AM. AlSi10Mg provides a cost-effective, well-understood solution with good performance, while Scalmalloy® pushes the boundaries of lightweighting and strength for the most demanding applications, albeit at a higher cost. The choice depends on a careful trade-off analysis considering performance requirements, budget constraints, and the manufacturing capabilities of the chosen AM partner. Ensuring high-quality powder feedstock from a reputable supplier like Met3dp is a critical first step in either case.
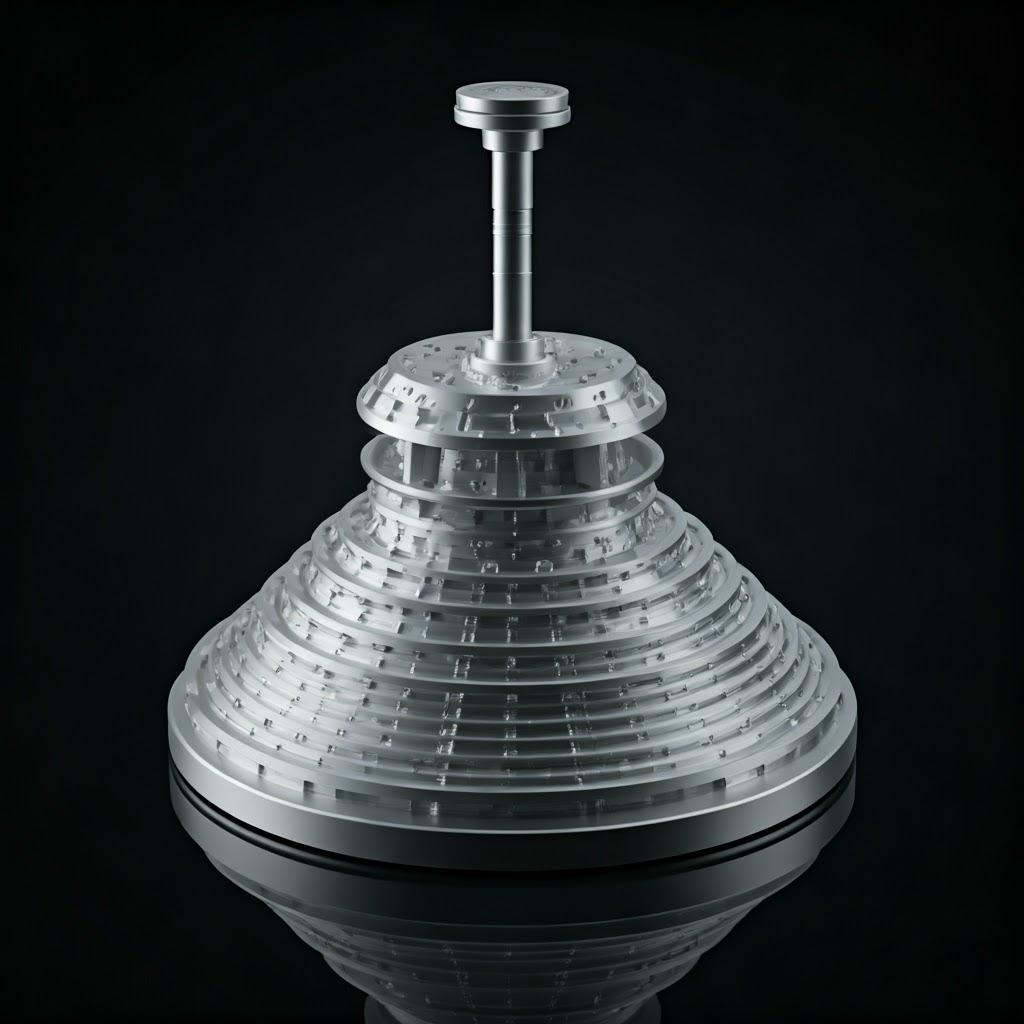
Design Optimization Strategies for AM Satellite Antenna Bases
Simply replicating a traditionally designed antenna base using additive manufacturing often fails to capture the full potential of the technology. To truly harness the benefits of AM, particularly the significant lightweighting and performance enhancements crucial for satellite components, engineers must embrace Проектирование для аддитивного производства (DfAM) principles from the outset. DfAM is not just about ensuring a part можно be printed; it’s about actively leveraging AM’s unique capabilities to create superior components. For satellite antenna bases, DfAM strategies focus on maximizing structural efficiency, integrating functionality, and ensuring manufacturability.
1. Topology Optimization: The Cornerstone of Lightweighting: Topology optimization (TO) is perhaps the most impactful DfAM tool for aerospace lightweighting. It uses mathematical algorithms (often integrated into FEA software) to distribute a limited amount of material within a defined design space, subject to specific load cases, boundary conditions, and performance targets (e.g., maximum stress, minimum stiffness). * Workflow: * Define Design Space: Outline the maximum permissible volume the antenna base can occupy. * Define Non-Design Space: Specify critical areas that must remain solid material (e.g., mounting interfaces, connector points). * Apply Loads & Constraints: Input structural loads (launch vibration, static loads), thermal loads, required stiffness, and manufacturing constraints (e.g., minimum member size). * Run Optimization: The software iteratively removes material from low-stress regions, creating an organic, load-path-optimized structure. * Interpret & Reconstruct: The raw TO result is often jagged and needs interpretation and smoothing into a manufacturable CAD model, often using subdivision modeling or specialized reconstruction tools. * Benefits for Antenna Bases: Achieves maximum stiffness-to-weight ratio, ensuring structural integrity under launch loads with minimum mass. Reduces inertial loads on the satellite structure. * Соображения: Requires expertise in TO software and interpretation. Manufacturing constraints specific to the chosen AM process (e.g., overhang angles, feature resolution) must be incorporated into the optimization setup. Collaboration with AM service providers experienced in aerospace engineering services involving TO is highly recommended.
2. Lattice Structures: Beyond Solid Optimization: Where topology optimization creates efficient solid structures, lattice structures introduce controlled porosity for further lightweighting and functional benefits. AM excels at producing complex internal lattices that are impossible to manufacture subtractively. * Types of Lattices: * Strut-based: Examples include cubic, octet-truss, diamond. Offer high stiffness and strength for their weight. * TPMS (Triply Periodic Minimal Surfaces): Examples include Gyroid, Schwarz P, Diamond. Offer smooth surfaces, good stress distribution, and potentially interesting thermal or fluid flow properties. * Stochastic Foams: Mimic natural foams, offering excellent energy absorption and vibration damping. * Applications in Antenna Bases: * Infill: Replacing solid internal volumes of the base with a lightweight lattice infill. * Vibration Damping: Selecting lattice types known for energy absorption to help dampen launch vibrations. * Тепловое управление: Designing lattices with specific geometries to enhance or impede heat transfer in certain directions. * Design Tools: Specialized software modules or standalone programs are used to generate and integrate these complex lattice geometries into the CAD model. * Соображения: Requires careful analysis (FEA) to predict the mechanical behavior of the lattice. Manufacturability (minimum strut size, powder removal from internal cavities) is crucial. Powder removal from complex internal lattices can be a significant challenge and must be considered during the design phase.
3. Part Consolidation: Simplifying Complexity: AM allows multiple components of an assembly to be redesigned and printed as a single, integrated part. * Example: An antenna base assembly might traditionally consist of a main machined base, several mounting brackets, fasteners, and perhaps a separate thermal interface plate. Using AM, these could potentially be combined into one monolithic component. * Преимущества: Reduced part count, elimination of fasteners (weight saving, reduced failure points), simplified assembly, shorter supply chain, potentially lower overall cost. * Задачи: Requires a holistic redesign approach. The consolidated part becomes more complex, potentially increasing printing challenges (supports, stress). Repairability might be affected.
4. DfAM Principles for Manufacturability: Beyond optimization, practical DfAM rules ensure the antenna base can be printed successfully and reliably. * Build Orientation: Selecting the optimal orientation on the build plate impacts support needs, surface finish, residual stress, and potentially anisotropic material properties. Critical features should ideally be oriented for best accuracy and surface finish. * Overhangs and Support Structures: Metal AM processes like LPBF require support structures for features overhanging beyond a certain angle (typically 45° relative to the build plate). Designs should minimize steep overhangs or incorporate self-supporting angles where possible. Support structures add print time, material cost, and require post-processing for removal, which can be difficult in internal channels. Design for support access and easy removal. * Minimum Feature Size: The laser spot size and powder particle size limit the minimum wall thickness, hole diameter, and feature resolution achievable. Antenna base designs must adhere to these limits (e.g., typical minimum wall thickness might be 0.4-1.0 mm depending on the machine and material). * Thermal Management during Printing: Large flat sections or rapid changes in cross-sectional area can lead to differential cooling, residual stress, and warping. Incorporating fillets/radii, uniform wall thicknesses, and potentially stress-relief features can mitigate these issues. * Удаление порошка: For designs with internal channels or complex cavities (like lattices), ensuring trapped powder can be removed after printing is critical. Design strategically placed drain/access holes.
5. Integrating Functional Requirements: DfAM allows functional features to be built directly into the base. * Thermal Pathways: Designing optimized conductive paths or even conformal cooling channels directly into the base structure for improved heat dissipation from the antenna or nearby electronics. * Mounting Features: Integrating threaded inserts (via post-processing) or designing specific geometries for robust kinematic mounting. * Cable Routing: Incorporating channels or guides for RF and data cables directly into the base design.
Проектирование на основе моделирования: Throughout the DfAM process, simulation plays a vital role. * Structural FEA: Validating the strength and stiffness of the optimized design under operational and launch loads. * Thermal Simulation: Analyzing heat flow and predicting temperature distributions. * Print Process Simulation: Increasingly used to predict residual stress, potential distortion, and optimize build orientation and support strategies before committing to a physical print.
By employing these DfAM satellite parts strategies, engineers can move beyond simple substitution and create antenna bases that are significantly lighter, potentially perform better thermally and structurally, and leverage the full manufacturing advantages offered by metal AM. Partnering with an AM provider like Met3dp, who understands these principles and the nuances of materials like Scalmalloy® and AlSi10Mg, is key to successful implementation.
Achieving Precision: Tolerance, Surface Finish, and Accuracy in AM Antenna Bases
While metal AM offers incredible design freedom, achieving the tight tolerances, specific surface finishes, and high dimensional accuracy required for mission-critical components like satellite antenna bases demands careful process control, understanding the inherent characteristics of AM, and often incorporating targeted post-processing steps. Engineers and procurement managers must have realistic expectations and clearly define the necessary precision levels for different features of the antenna base.
1. Dimensional Accuracy and Tolerances: Dimensional accuracy refers to how closely the final printed part conforms to the nominal dimensions specified in the CAD model. Tolerances define the permissible variation from these nominal dimensions. * Typical As-Built Accuracy (LPBF): For well-controlled processes using materials like AlSi10Mg or Scalmalloy®, typical dimensional accuracy for smaller parts might be in the range of ±0.1 mm to ±0.2 mm, or ±0.1% to ±0.2% of the dimension for larger features. However, this is highly dependent on: * Part Geometry and Size: Larger parts or those with complex features are more prone to thermal distortion during the build, affecting accuracy. * Build Orientation: Dimensions in the Z-axis (build direction) often have different accuracy potential than those in the X-Y plane. * Thermal Stress: Residual stresses built up during the layer-wise heating and cooling can cause warping or distortion, especially after removal from the build plate. * Калибровка машины: Regular and precise calibration of the AM system (laser focus, scanner accuracy, powder deposition) is crucial. * Свойства материала: Different alloys exhibit varying shrinkage and stress behaviors. * Achieving Tighter Tolerances: For critical interfaces, mounting points, or alignment features requiring tolerances tighter than the typical as-built capability (e.g., ±0.025 mm to ±0.05 mm), post-process CNC machining is almost always necessary. These critical features should be designed with extra stock material (machining allowance) added in the AM process. * Geometric Dimensioning and Tolerancing (GD&T): Proper use of GD&T on engineering drawings is essential to communicate precisely which features require high accuracy and what types of geometric controls (e.g., flatness, parallelism, position) are needed.
2. Surface Finish (Roughness): Metal AM parts, particularly from powder bed fusion processes, typically have a characteristic surface roughness resulting from the partially melted powder particles adhering to the surface. * Typical As-Built Surface Roughness (Ra): * Top Surfaces: Generally smoother, often in the range of 5-15 µm Ra. * Vertical Walls (X/Y Plane): Slightly rougher, perhaps 8-20 µm Ra, showing layer lines. * Upward-Facing Slanted Surfaces: Roughness increases as the angle approaches horizontal. * Downward-Facing (Supported) Surfaces: Typically the roughest, often >20 µm Ra, depending heavily on the support strategy and removal process. Surface quality is directly impacted by the support contact points. * Улучшение качества поверхности: * Оптимизация параметров процесса: Fine-tuning parameters like laser power, scan speed, and layer thickness can influence surface finish, but often involves trade-offs with build speed or density. * Постобработка: Various methods can significantly improve surface finish: * Abrasive Blasting (Bead/Sand Blasting): Provides a uniform matte finish, typically improving Ra but not necessarily achieving high smoothness. Effective for removing semi-sintered particles. * Tumbling/Vibratory Finishing: Uses media to smooth surfaces and edges, good for batches of smaller parts. * Micro-Machining/Polishing: Can achieve very smooth surfaces (Ra < 1 µm) on specific areas but is often manual or requires specialized CNC paths. * Electrochemical Polishing: Can smooth complex surfaces but requires specific electrolytes and process control. * Considerations for Antenna Bases: While general surfaces might tolerate the as-built roughness, critical interfaces (mounting pads, thermal contact surfaces) often require smoother finishes achieved through machining or polishing to ensure proper contact, alignment, and thermal transfer. RF performance can also be sensitive to surface roughness at very high frequencies.
3. Quality Control and Metrology: Ensuring that the final antenna base meets the specified dimensional and surface finish requirements necessitates robust quality control and metrology procedures, often aligned with stringent aerospace standards like AS9100. * Мониторинг в процессе работы: Advanced AM systems incorporate some level of in-process monitoring (e.g., melt pool monitoring, thermal imaging) to detect potential anomalies during the build. * Post-Build Metrology: * Coordinate Measuring Machines (CMM): Provide high-accuracy point measurements for verifying critical dimensions and GD&T callouts. Requires careful fixture design. * 3D Laser Scanning/Structured Light Scanning: Capture dense point clouds of the entire part geometry, allowing comparison to the original CAD model (part-to-CAD comparison). Excellent for verifying complex shapes produced by topology optimization but may have lower accuracy than CMM for specific features. * Surface Roughness Testers (Profilometers): Measure Ra or other roughness parameters on specified surfaces. * Неразрушающий контроль (NDT): Crucial for detecting internal defects like porosity or cracks (discussed further in Challenges section). Computed Tomography (CT) scanning is particularly valuable for AM parts.
Met3dp’s Commitment to Precision: Achieving the necessary precision for aerospace components requires not only advanced equipment but also rigorous process control and expertise. Leading providers like Met3dp understand the importance of accuracy and reliability. Their investment in industry-leading print volume, accuracy and reliability is reflected in their equipment capabilities and quality management systems. While post-processing like machining is often required for the tightest tolerances on satellite parts, starting with a dimensionally accurate, high-quality AM build from a reliable partner minimizes the extent and complexity of these finishing steps, ultimately saving time and cost. When discussing potential projects, inquire about the provider’s metrology capabilities and their standard procedures for ensuring dimensional accuracy and surface finish requirements are met. Exploring the range of solutions on the Met3dp product page can give insight into the types of equipment and materials they work with, which underpin their precision capabilities.
In essence, achieving precision in AM antenna bases involves understanding the as-built capabilities and limitations, designing for manufacturability and inspection, strategically employing post-processing where needed, and partnering with an AM provider committed to rigorous quality control and metrology.
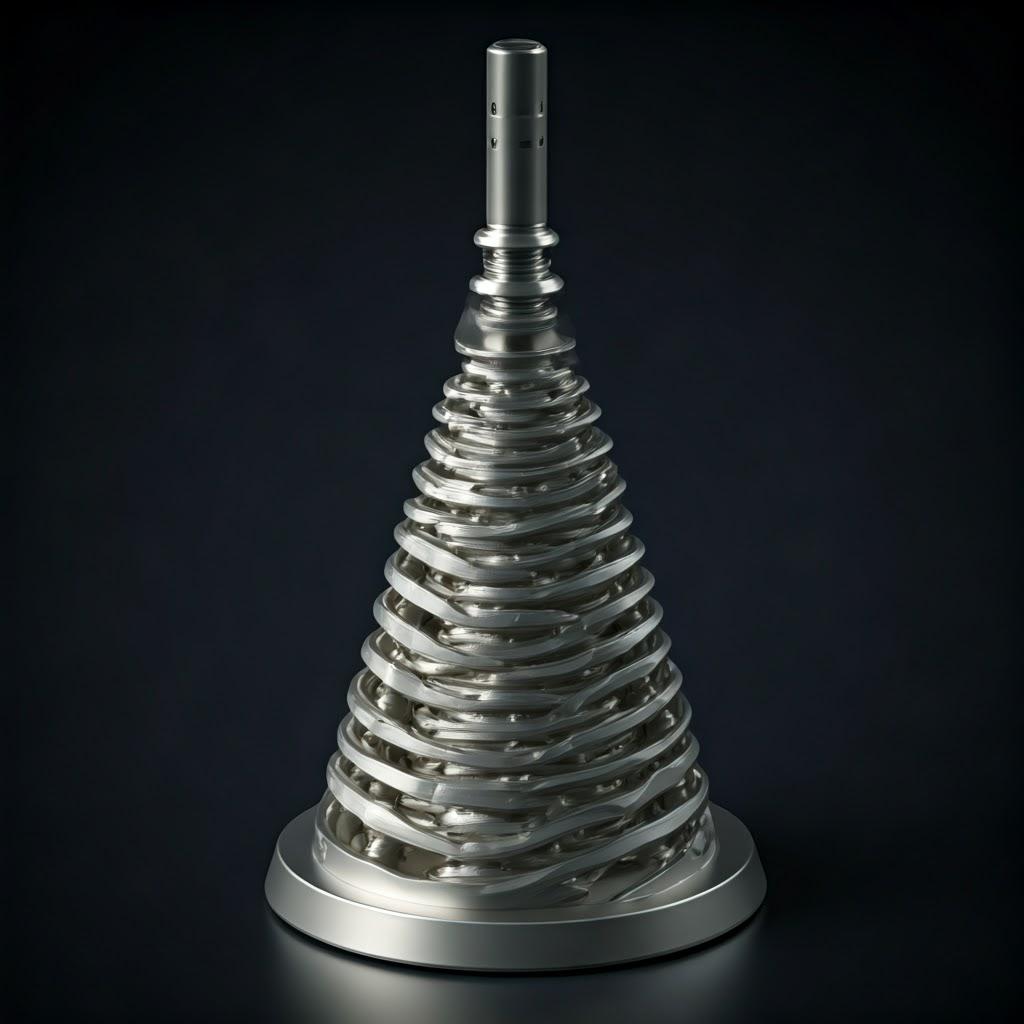
Essential Post-Processing Steps for Mission-Critical Antenna Bases
An additively manufactured metal part, upon removal from the printer, is rarely ready for its final application, especially for demanding aerospace components like satellite antenna bases. A series of crucial post-processing steps are typically required to transform the raw AM part into a functional, reliable, and mission-ready piece of hardware. These steps address residual stresses, remove support structures, achieve required tolerances and surface finishes, and verify internal quality. Planning for these steps is essential for accurately estimating lead times and costs.
1. Stress Relief / Heat Treatment: The rapid heating and cooling cycles inherent in powder bed fusion processes induce significant residual stresses within the printed part. These stresses can cause distortion (especially after removal from the build plate) and potentially compromise the part’s mechanical properties and fatigue life. * Снятие стресса: A low-temperature heat treatment applied while the part may still be attached to the build plate (or immediately after removal). Aims to reduce internal stresses without significantly altering the microstructure or hardness. Often sufficient for AlSi10Mg parts if T6 strengthening is not required. * Solution Annealing and Aging (e.g., T6 for Al): Required for precipitation-hardening alloys like Scalmalloy® to achieve their target high-strength properties. This involves: * Лечение раствором: Heating to a high temperature to dissolve alloying elements into a solid solution. * Закаливание: Rapidly cooling to lock the elements in solution. * Старение: Heating to a lower temperature for a specific duration to allow controlled precipitation of strengthening phases. * Atmosphere Control: Heat treatments for aerospace parts, especially reactive alloys, are typically performed in vacuum or inert gas furnaces to prevent oxidation and contamination. * Importance: Essential for dimensional stability, achieving target mechanical properties (especially for Scalmalloy®), and improving fatigue performance. Process parameters (temperature, time, quench rate) are critical and material-specific.
2. Part Removal from Build Plate: The antenna base is typically printed attached to a solid metal build plate via its support structures or initial layers. * Методы: Usually done using wire EDM (Electrical Discharge Machining) or a band saw. Wire EDM provides a cleaner cut with minimal mechanical stress. * Соображения: Must be done carefully to avoid damaging the part.
3. Support Structure Removal: Support structures are necessary evils in LPBF, enabling the printing of overhangs and complex geometries but requiring removal afterward. * Методы: * Удаление вручную: Breaking or cutting away accessible supports using hand tools. Labor-intensive and can damage part surfaces if not done carefully. * CNC Machining: Milling or grinding away support structures, especially large or difficult-to-access ones. More precise but requires programming and setup. * Wire EDM: Can sometimes be used for intricate support removal. * Design Impact: As mentioned in the DfAM section, designing for support minimization and ease of removal is critical. Internal supports in complex channels or lattice structures can be particularly challenging or impossible to remove completely, potentially trapping powder – this must be avoided for critical applications.
4. Machining of Critical Features: As discussed under ‘Precision’, AM parts rarely achieve the final tolerances required for all features directly from the printer. * Targets: Mounting interfaces, mating surfaces, bearing seats, alignment features, sealing surfaces. * Процесс: Typically involves 3, 4, or 5-axis CNC milling or turning. * Requirements: Requires accurate fixturing of the often complex AM part. Sufficient machining stock must have been included in the AM design.
5. Surface Finishing and Cleaning: These steps aim to achieve the desired surface texture, remove contaminants, and prepare the part for subsequent coatings or inspection. * De-powdering: Thorough removal of loose or semi-sintered powder, especially from internal channels, often using compressed air and vibration. Critical to prevent contamination and ensure accurate weight/density. * Abrasive Blasting (Bead/Sand): Creates a uniform matte finish, removes minor surface imperfections, and can improve fatigue life through compressive stress (shot peening is a more controlled version). * Tumbling/Vibratory Finishing: Smooths surfaces and deburrs edges using abrasive media. * Polishing/Lapping: For achieving very smooth surfaces (Ra < 1 µm) on specific functional areas (e.g., thermal contact pads). * Cleaning: Final cleaning using appropriate solvents or aqueous processes to remove machining fluids, blasting media, fingerprints, etc., before final inspection or coating.
6. Surface Treatment / Coating (Optional but Common in Space): Depending on the application and material, coatings may be applied for various reasons: * Защита от коррозии: Anodizing (for aluminum alloys like AlSi10Mg and Scalmalloy®) or chemical conversion coatings enhance corrosion resistance, important during ground handling and potentially in specific space environments. * Thermal Control: Specialized thermal control coatings (e.g., white paints, black paints, optical solar reflectors – OSRs, Second Surface Mirrors – SSMs) are often applied to satellite surfaces to manage radiative heat transfer. The antenna base may require such coatings depending on its thermal role. * Износостойкость: Hard coatings might be applied to specific wear surfaces if relevant.
7. Final Inspection and Verification: After all processing steps, rigorous final inspection is performed. * Dimensional Verification: CMM or 3D scanning to confirm final dimensions and GD&T compliance. * Surface Finish Measurement: Using profilometers. * Неразрушающий контроль (NDT): * Visual Inspection: Magnified visual checks for surface defects. * Dye Penetrant Inspection (DPI): Detects surface-breaking cracks. * Computed Tomography (CT) Scanning: Provides 3D visualization of the part’s internal structure, detecting voids, porosity, inclusions, and verifying complex internal features or lattice structures. Increasingly vital for qualifying critical AM aerospace parts. * Ultrasonic Testing (UT): Can detect subsurface flaws but is more challenging on complex AM geometries. * Material Property Verification (Coupon Testing): Often, witness coupons are printed alongside the main part and subjected to destructive tensile testing to verify that the material achieved the expected properties after heat treatment.
The necessity and extent of each post-processing step depend heavily on the specific requirements of the satellite antenna base – its material, complexity, criticality, and functional interfaces. Effectively managing this metal AM finishing services workflow is crucial for delivering flight-ready hardware. Procurement managers should ensure potential AM suppliers have demonstrated capabilities and robust quality control throughout these post-processing stages.
Navigating Potential Challenges in 3D Printing Antenna Bases
While metal additive manufacturing offers transformative potential for satellite antenna bases, it’s not without its challenges. Successfully implementing AM for these high-stakes components requires acknowledging potential pitfalls and proactively implementing strategies to mitigate them. Understanding these challenges is crucial for both design engineers and procurement managers evaluating aerospace manufacturing solutions.
1. Residual Stress and Distortion: The layer-by-layer melting and solidification process inherently creates thermal gradients, leading to residual stress build-up. * Проблема: Can cause part distortion during the build, cracking, delamination from the build plate, or warping after the part is removed and stress-relieved. Particularly problematic for large, flat bases or parts with significant variations in cross-section. * Mitigation: * Optimized Build Strategy: Careful selection of build orientation, laser scan patterns (e.g., island scanning), and potentially pre-heating the build platform. * Стратегия поддержки: Robust support structures help anchor the part and dissipate heat but must be balanced against removal difficulty. * DfAM: Designing parts with more uniform wall thicknesses, incorporating fillets, and avoiding large unsupported flat areas. * Process Simulation: Using software to predict stress accumulation and distortion, allowing for geometry compensation or build strategy adjustments. * Effective Heat Treatment: Proper stress relief cycles are critical.
2. Support Structure Design and Removal: Supports are necessary but problematic. * Проблема: Poorly designed supports can fail during the build, leading to part collapse or defects. Dense or internal supports can be extremely difficult or impossible to remove completely, potentially trapping powder and compromising part integrity or cleanliness. Support removal processes (manual or machining) can damage the part surface. * Mitigation: * DfAM: Minimize the need for supports through design (self-supporting angles, topology optimization considering overhang constraints). Design supports for accessibility and ease of removal (e.g., using perforations or specific interface geometries). * Specialized Software: Utilize advanced support generation tools that optimize for minimal contact and easy removal. * Process Selection: Consider AM processes with different support requirements if feasible (though LPBF is dominant for these materials/applications). * Post-Processing Planning: Factor support removal complexity into the overall plan and cost. Consider inspection methods (e.g., borescope, CT scan) to verify removal from internal channels.
3. Porosity Control: Internal voids or pores within the printed material can act as stress concentrators, degrading mechanical properties (especially fatigue life) and potentially causing leak paths. * Sources: Gas entrapment within the powder feedstock, gas porosity formed during melting (due to dissolved gases), lack-of-fusion porosity between layers or scan tracks (due to insufficient energy input). * Mitigation: * High-Quality Powder: Using powder with low internal porosity and controlled chemistry, sourced from reputable поставщики металлических порошков like Met3dp whose advanced powder making systems prioritize powder quality. Consistent powder handling and storage are also essential to avoid moisture pickup. * Optimized Process Parameters: Fine-tuning laser power, scan speed, layer thickness, hatch spacing, and gas flow within the build chamber to ensure complete melting and fusion. Parameter sets are often specific to the material and machine. * Горячее изостатическое прессование (HIP): A post-processing step involving high temperature and high pressure inert gas. HIP can effectively close internal porosity (gas and lack-of-fusion) but adds cost and lead time, and can slightly affect dimensions. Often required for critical aerospace components. * NDT: Using CT scanning to detect and quantify internal porosity.
4. Achieving Consistent Material Properties: Ensuring that the mechanical properties (strength, ductility, fatigue life) are consistent throughout the complex geometry of the antenna base and match the design specifications. * Проблема: Local variations in thermal history during the build can lead to slight microstructural differences. Anisotropy (different properties in different build directions) can also occur. Achieving the full potential of alloys like Scalmalloy® depends critically on precise heat treatment. * Mitigation: * Process Control & Monitoring: Strict control over all AM parameters and environmental conditions. In-process monitoring can help detect anomalies. * Standardized Heat Treatment: Using calibrated furnaces and precisely controlled, validated heat treatment cycles. * Coupon Testing: Printing and testing representative witness coupons alongside the part to verify material properties for each build. * Database Development: Building a database of material properties correlated with specific process parameters and locations within the build volume.
5. Surface Finish and Feature Resolution: As-built surfaces can be rough, and fine features may not be perfectly resolved. * Проблема: Roughness can impact fatigue life, thermal contact resistance, and RF performance. Inability to resolve very fine features limits design possibilities. * Mitigation: * Orientation & Parameter Tuning: Optimizing build orientation and parameters for critical surfaces. * DfAM: Designing features within the known resolution limits of the process. Avoiding knife-edges or extremely thin walls unless necessary and validated. * Targeted Post-Processing: Using machining or polishing for critical surfaces requiring high smoothness or accuracy.
6. Qualification and Certification for Space: Getting any new material or process approved for use in mission-critical space hardware is a rigorous and lengthy process. * Проблема: Requires extensive testing (material characterization, structural testing, environmental testing like thermal vacuum and vibration) and documentation to demonstrate reliability and meet stringent aerospace standards (e.g., NASA-STD, ECSS). Lack of standardized AM qualification processes across the industry can be a hurdle. * Mitigation: * Working with Experienced Partners: Collaborating with AM service providers who have experience qualifying parts for aerospace or space applications. * Leveraging Existing Data: Utilizing publicly available data or data from material suppliers where possible, but often program-specific qualification is needed. * Proto-Qualification Approach: Starting with less critical applications or ground-based prototypes to build confidence and data. * Rigorous NDT and Inspection: Comprehensive inspection is key to demonstrating part integrity.
Navigating these AM process defects and challenges requires a combination of robust DfAM practices, meticulous process control, appropriate post-processing, thorough inspection, and collaboration between designers, manufacturing engineers, and quality assurance teams. Partnering with knowledgeable suppliers who understand the intricacies of additive manufacturing aerospace applications is paramount to successfully overcoming these hurdles and realizing the benefits of AM for satellite antenna bases.
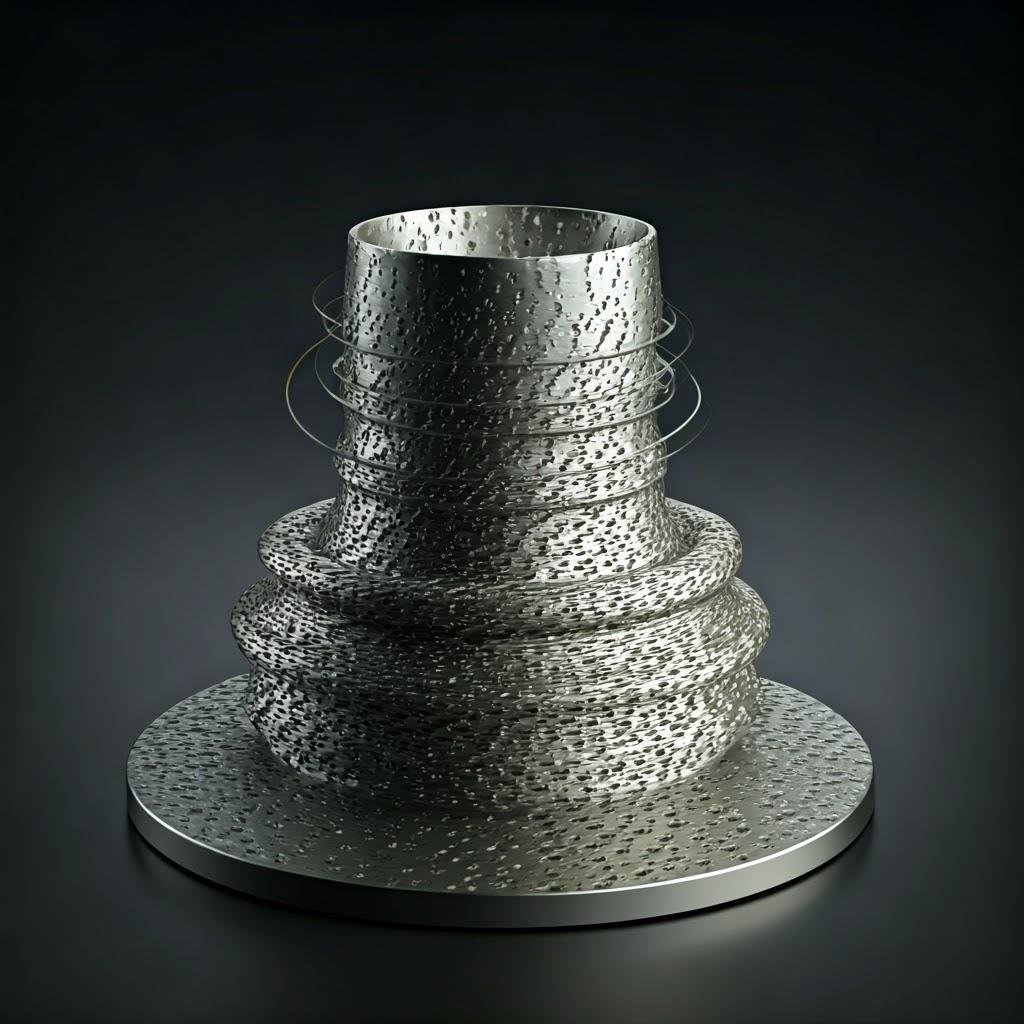
Selecting Your Metal AM Partner for Satellite Component Manufacturing
Choosing the right additive manufacturing service provider is arguably as critical as the design and material selection for producing high-quality, flight-ready satellite antenna bases. The unique demands of the aerospace industry – stringent quality requirements, complex geometries, advanced materials, and mission-critical reliability – necessitate partnering with a supplier that possesses specialized expertise, robust processes, and relevant certifications. For procurement managers and engineering teams navigating the metal AM supplier landscape, evaluating potential partners requires a thorough assessment across several key areas.
1. Aerospace Certifications and Quality Management System (QMS): This is often the first filter for aerospace applications. * AS9100 Certification: This standard builds upon ISO 9001, adding specific requirements for quality and risk management tailored to the aviation, space, and defense industries. Holding AS9100 certification demonstrates a provider’s commitment to rigorous quality control, process traceability, and continuous improvement relevant to aerospace hardware. It is frequently a prerequisite for aerospace component suppliers. * Robust QMS: Even beyond specific certifications, the provider should have a well-documented and implemented QMS covering all aspects from order intake and design review to material handling, process control, post-processing, inspection, and shipping. Ask for details about their QMS documentation and procedures. * ITAR Compliance: If the antenna base design or related information is subject to the U.S. International Traffic in Arms Regulations, ensure the provider is ITAR registered and has procedures in place to handle controlled data securely.
2. Proven Experience and Expertise: Theoretical knowledge isn’t enough; practical experience is crucial. * Aerospace/Space Track Record: Has the provider successfully manufactured components for similar aerospace or, ideally, satellite applications? Can they provide case studies or references (within confidentiality limits)? Experience navigating space qualification processes is invaluable. * Экспертиза материалов: Do they have specific, demonstrable experience printing and post-processing the chosen material (e.g., Scalmalloy®, AlSi10Mg, or relevant Titanium alloys)? This includes validated parameter sets, successful heat treatment protocols, and understanding material-specific challenges. Ask about their material characterization data. * DfAM Support: Does the provider offer Design for Additive Manufacturing support? Can their engineers collaborate with your team to optimize the antenna base design for manufacturability, performance, and cost-effectiveness using AM principles? This collaborative approach often yields the best results.
3. Equipment Capability and Capacity: The right tools for the job are essential. * Machine Fleet: Do they operate modern, well-maintained AM systems suitable for the required material and part size? Consider machine manufacturers known for reliability and accuracy. Inquire about their preventative maintenance and calibration schedules. * Объем сборки: Ensure their machines can accommodate the dimensions of your antenna base. * Technology Alignment: Confirm they utilize the appropriate AM technology (likely Laser Powder Bed Fusion – LPBF for these materials) and have expertise in its specific nuances. Various способы печати exist, ensure their capabilities match your needs. * Capacity and Redundancy: Do they have sufficient machine capacity to meet your required lead times, especially for potential production runs? Do they have multiple machines capable of running your part to provide redundancy?
4. Material Handling and Traceability: Critical for ensuring material integrity and compliance. * Powder Quality Control: What are their procedures for incoming powder inspection, storage (controlling humidity and oxygen exposure), handling, and recycling/rejuvenation? How do they prevent cross-contamination between different alloy types? * Full Traceability: Can they provide complete traceability for the powder batch used for your specific part, linking it back to the original powder manufacturer’s certificate of conformity? This is usually mandatory for flight hardware.
5. Post-Processing Capabilities: AM is rarely the end of the process. * In-House vs. Outsourced: Does the provider have in-house capabilities for essential post-processing steps like heat treatment (in vacuum/inert atmosphere furnaces), CNC machining (multi-axis), surface finishing, and cleaning? If they outsource certain steps, what are their supplier management and quality control processes for these external operations? * Specialized Equipment: Do they possess calibrated furnaces suitable for the specific heat treatment cycles required (especially critical for Scalmalloy®)? Do they have CNC machines capable of achieving the required tolerances on complex AM geometries?
6. Metrology and Non-Destructive Testing (NDT): Verification is non-negotiable. * Inspection Equipment: Do they have calibrated CMMs, 3D scanners, surface profilometers, and other necessary metrology tools? * NDT Capabilities: Crucially, do they offer or have qualified partners for NDT methods suitable for AM aerospace parts, particularly CT scanning for internal defect detection and potentially DPI or UT? Do they have certified NDT personnel?
7. Customer Service and Collaboration: A strong working relationship facilitates success. * Communication: Are they responsive, transparent, and easy to communicate with? * Техническая поддержка: Do they offer accessible technical support throughout the project lifecycle? * Гибкость: Can they accommodate specific project requirements or adapt to changes?
Evaluating Met3dp as a Potential Partner: Такие компании, как Met3dp present a compelling profile for consideration. While evaluation against all the above criteria is necessary, their foundational strengths are highly relevant: * Экспертиза материалов: As a company specializing in developing and manufacturing high-performance metal powders using advanced atomization techniques (Gas Atomization, PREP), Met3dp possesses deep knowledge of material science and powder characteristics crucial for successful AM. This focus ensures high-quality input material. * Integrated Solutions: Offering both advanced metal powders and industrial 3D printers suggests a holistic understanding of the AM ecosystem. Their printers are highlighted for industry-leading print volume, accuracy and reliability, directly addressing key capability requirements. * Comprehensive Approach: Providing comprehensive solutions that span printers, powders, and application development services indicates a capability to support customers beyond just printing, potentially assisting with DfAM and process optimization. You can learn more about Met3dp and their collective expertise.
Making the Choice: Selecting your AM partner is a strategic decision. Issue detailed Requests for Quotation (RFQs) that clearly define all technical requirements, quality standards, and deliverables. Consider conducting site audits (if feasible) and technical interviews. Don’t base the decision solely on price; prioritize proven capability, quality, expertise, and reliability, especially for mission-critical satellite components. A strong partnership with the right supplier is fundamental to leveraging AM effectively for lightweight, high-performance satellite antenna bases.
Understanding Cost Drivers and Lead Times for AM Antenna Bases
While additive manufacturing can offer long-term cost savings through lightweighting (reduced launch costs) and part consolidation (reduced assembly), the direct manufacturing cost and lead time for AM components like satellite antenna bases are influenced by a distinct set of factors compared to traditional methods. Understanding these drivers is essential for accurate budgeting, project planning, and obtaining meaningful quotes (RFQ metal AM).
Key Cost Drivers:
- Стоимость материала:
- Powder Price: This is a significant factor, especially for high-performance alloys. Scalmalloy®, due to its scandium content and potentially licensing fees, is substantially more expensive per kilogram than AlSi10Mg. Titanium alloys are generally more expensive than aluminum alloys.
- Material Usage (Volume): The actual volume of the final part dictates the primary material cost. Topology optimization and lattice structures directly reduce this.
- Support Structure Volume: Material used for supports also adds to the cost. Efficient DfAM aims to minimize support needs.
- Build Plate Occupancy: Powder surrounding the part in the build chamber is often recycled, but the overall volume occupied on the build plate influences how many parts can be nested together, affecting machine time allocation per part.
- Buy-to-Fly Ratio: While much better than subtractive methods, AM still has a buy-to-fly ratio greater than 1 due to supports, test coupons, and potential powder losses during handling and recycling.
- Время машин:
- Время сборки: This is often the largest cost component after materials. It’s primarily driven by the height of the part in the build orientation (more layers = more time) and the том (more area to scan per layer). Complexity (e.g., intricate lattices) can also increase scan time per layer.
- Machine Depreciation & Operating Costs: The cost of owning, operating, and maintaining expensive industrial metal AM systems is factored into the hourly machine rate.
- Setup & Teardown: Time required for preparing the build (loading powder, setting up the file) and removing the completed build from the machine.
- Расходы на оплату труда:
- Design/Engineering (DfAM): While potentially part of the NRE (Non-Recurring Engineering) cost, expert DfAM takes time and skill.
- Build Preparation & Monitoring: Skilled technicians are needed to set up, run, and monitor the AM process.
- Постобработка: This can be very labor-intensive, including:
- De-powdering and cleaning.
- Manual support removal.
- CNC programming and machining setup/operation.
- Manual finishing/polishing.
- Inspection and metrology.
- Расходы на постобработку:
- Термообработка: Furnace time, energy consumption, and potentially the cost of inert gas or vacuum. Specialized cycles for alloys like Scalmalloy® can be more complex and costly.
- Удаление опоры: Labor and potentially machine time (CNC/EDM).
- Обработка: Cost depends heavily on the number of features requiring machining, the complexity of setups, and the required tolerances.
- Отделка поверхности: Costs vary significantly depending on the method (blasting, tumbling, polishing) and the required outcome.
- NDT & Inspection: Costs associated with equipment usage (e.g., CT scanner time) and certified personnel time.
- Qualification & Testing:
- Material Coupon Testing: Destructive testing of witness coupons adds cost.
- Part-Specific Qualification: If extensive functional testing (vibration, thermal vacuum) or qualification documentation is required, this can add significant cost, often treated as NRE.
- Overheads & Profit: Standard business costs and profit margins applied by the AM service provider.
Typical Lead Time Factors:
Lead time refers to the total time from order placement to part delivery. For AM antenna bases, it can range from days/weeks for simple prototypes to several weeks or months for qualified production parts.
- Design & Preparation (if applicable): Time for DfAM optimization, simulation, and build file preparation.
- Queue Time: The service provider’s backlog; how soon can your part get scheduled on a machine? This can vary significantly.
- Время сборки: As described above, primarily driven by part height and volume. Can range from hours to several days for complex or large antenna bases.
- Cool Down & Depowdering: Time required for the build chamber and part to cool before removal and subsequent powder excavation.
- Термообработка: Furnace cycle time (can be many hours or days) plus scheduling/loading time.
- Support Removal & Machining: Can range from hours to days depending on complexity and resource availability. Requires scheduling on different equipment (saws, CNCs).
- Surface Finishing & Cleaning: Time depends on the chosen methods.
- Inspection & NDT: Time required for CMM, scanning, CT scans, etc., plus data analysis and reporting.
- Перевозки: Transit time.
Strategies for Optimization:
- DfAM: Optimize for reduced volume, height, and minimal support structures.
- Nesting: Printing multiple parts (or multiple copies of the same part) in a single build can reduce the per-part machine time cost and setup overhead.
- Material Choice: Balance performance needs with material cost (e.g., use AlSi10Mg if Scalmalloy®’s premium properties aren’t strictly necessary).
- Tolerance Specification: Only specify tight tolerances (requiring machining) where functionally necessary.
- Clear Communication: Provide clear requirements and drawings to the AM provider to avoid delays and rework.
Understanding these metal 3D printing cost factors and lead time components allows for more realistic project planning and helps in evaluating quotes from different suppliers. Always request a detailed quote breakdown to see where the major costs lie for your specific antenna base design.
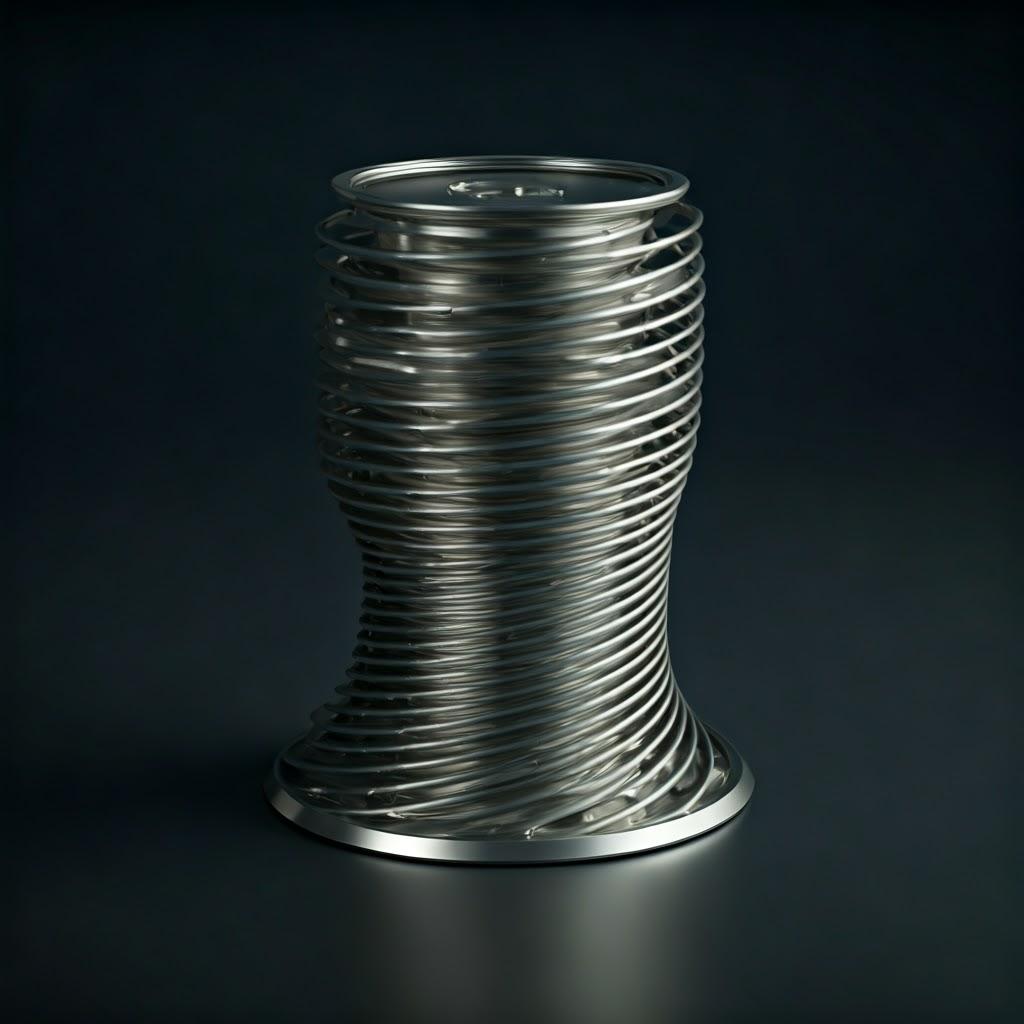
Frequently Asked Questions (FAQ) about AM Satellite Antenna Bases
Here are answers to some common questions engineers and procurement managers have when considering additive manufacturing for satellite antenna bases:
1. Is Scalmalloy® always the best choice over AlSi10Mg for satellite antenna bases?
Not necessarily. While Scalmalloy® offers significantly higher specific strength, fatigue resistance, and better performance at moderately elevated temperatures, it comes at a substantially higher cost (both powder and processing, including mandatory heat treatment).
- Choose Scalmalloy® if: Maximum lightweighting is paramount, the component experiences very high structural or fatigue loads (e.g., during launch), or operates in a thermally challenging environment where AlSi10Mg might soften. The performance benefit must justify the cost premium.
- Choose AlSi10Mg if: The design achieves sufficient structural integrity and stiffness with its moderate strength, cost is a major constraint, established processing parameters are preferred, or slightly better thermal conductivity is beneficial.
The optimal choice requires a trade-off analysis based on specific mission requirements, load cases, thermal environment, and budget constraints. Often, AlSi10Mg provides a “good enough” solution for many applications at a more accessible price point.
2. How is the quality and reliability of AM satellite components verified for space flight?
Verification for space is rigorous and multi-faceted, building upon standard aerospace quality control:
- Material Control: Strict powder quality control (chemistry, PSD, morphology, low porosity) and complete batch traceability.
- Управление процессом: Validated and locked process parameters, environmental monitoring (oxygen levels, temperature), and potentially in-situ monitoring during the build.
- Post-Processing Validation: Precisely controlled and validated heat treatment cycles. Careful support removal and machining processes.
- Extensive NDT: Computed Tomography (CT) scanning is crucial for detecting internal defects (porosity, cracks) and verifying internal features in complex geometries. Dye Penetrant Inspection (DPI) for surface cracks is also common.
- Dimensional Metrology: CMM and/or 3D scanning to ensure conformity to GD&T specifications.
- Mechanical Testing: Tensile testing of witness coupons printed with the part to verify material properties meet specifications after all processing. Fatigue or fracture toughness testing might also be required depending on criticality.
- Proto-Qualification Testing: Often, representative parts undergo qualification-level testing (e.g., vibration testing simulating launch loads, thermal cycling, or thermal vacuum testing) to demonstrate performance under simulated space conditions.
- Documentation: Comprehensive documentation package covering material certs, process logs, NDT reports, metrology data, and test results.
Qualification is often specific to the part, material, machine, and process parameters used.
3. What are the typical lead times for an AM satellite antenna base – prototype vs. qualified production part?
Lead times can vary widely:
- Prototype (Form/Fit Check, non-functional): If minimal post-processing (basic support removal, no heat treatment or machining) is needed, and machine time is available, a prototype might be produced in 1-3 недели.
- Functional Prototype (with heat treatment, basic machining): Requires additional time for furnace cycles and CNC setup/machining. Lead times could be in the 3-6 week range.
- Fully Qualified Production Part: This involves the longest lead times due to the addition of comprehensive NDT, rigorous inspection, potential qualification testing, and thorough documentation generation. Lead times of 6-12 weeks or longer are common, depending heavily on the complexity of the qualification requirements and the supplier’s capacity/backlog.
Factors like part size/complexity, material choice, required post-processing, testing level, and supplier queue significantly impact these estimates. Always get specific lead time quotes based on your detailed requirements.
4. Can we just take our existing antenna base design (made for CNC machining) and print it?
While technically possible, it’s highly discouraged and fails to leverage the key benefits of AM. Directly printing a design optimized for subtractive manufacturing often results in:
- Minimal Lightweighting: The design won’t incorporate topology optimization or internal lattices.
- Potential Printability Issues: Features like sharp internal corners, large flat overhangs, or thin walls designed for machining might be difficult or inefficient to print.
- Unnecessary Support Structures: The design won’t be optimized to minimize supports, increasing print time, material waste, and post-processing effort.
- Более высокая стоимость: Printing a bulky, non-optimized design will consume more material and machine time than a DfAM-optimized equivalent.
To gain the advantages of AM (especially lightweighting), the antenna base should be redesigned or significantly re-evaluated using DfAM principles.
5. What level of lightweighting can realistically be achieved using AM for an antenna base compared to traditional machining?
Significant lightweighting is achievable, but the exact percentage depends heavily on the initial design, the load cases, and how aggressively topology optimization and lattice structures are employed. Realistic expectations, based on various aerospace case studies, often fall in the range of 25% to 60% mass reduction compared to a conventionally machined component designed for the same function. Achieving savings beyond 60-70% becomes increasingly challenging and might require compromises in other areas or highly optimized (and potentially costly) designs and materials like Scalmalloy®.
Conclusion: The Future of Satellite Hardware is Lightweight and Additively Manufactured
The journey through the intricacies of applying metal additive manufacturing to satellite antenna bases reveals a compelling narrative of innovation meeting necessity. In the demanding realm of space exploration and satellite technology, where every gram saved and every performance enhancement matters, AM has transitioned from a novel prototyping tool to a viable and increasingly advantageous manufacturing solution for critical flight hardware.
The ability to produce highly complex, topologically optimized, and lightweight structures using advanced materials like Scalmalloy® and AlSi10Mg directly addresses the core challenges faced by satellite designers: reducing launch costs and maximizing payload capacity. The design freedom inherent in AM unlocks possibilities for part consolidation, integrated thermal management features, and rapid design iteration cycles that are simply unattainable with traditional manufacturing paradigms. We’ve seen how DfAM principles are not just recommendations but necessities for harnessing AM’s full potential, transforming antenna base design from subtractive shaping to additive optimization.
However, the path to flight-ready AM components requires diligence. Careful material selection based on a thorough analysis of performance requirements and cost, meticulous process control, comprehensive post-processing including heat treatment and precision machining, and rigorous NDT and quality verification are all non-negotiable steps. Potential challenges related to residual stress, support structures, porosity, and qualification must be proactively managed through expertise and robust procedures.
Perhaps most critical is the selection of the right manufacturing partner. A supplier like Met3dp, with its deep roots in high-performance metal powder production, advanced printing technology, and a comprehensive understanding of the AM ecosystem, embodies the type of partner needed to navigate the complexities of aerospace additive manufacturing. Their focus on material quality, printer reliability, and providing integrated solutions positions them as a valuable resource for companies looking to implement AM for demanding applications like satellite antenna bases. You can explore their full range of решения для аддитивного производства on their website.
The future of satellite hardware is undeniably intertwined with the trajectory of additive manufacturing. As the technology matures, materials improve, and qualification processes become more standardized, we can expect to see AM playing an even larger role in producing lighter, more capable, and potentially more cost-effective satellite components. For engineers and procurement managers aiming to stay at the forefront of satellite innovation, embracing metal AM for components like antenna bases is not just an option; it’s a strategic imperative. The lightweight, optimized future of space hardware is being built, layer by layer.
Поделиться
MET3DP Technology Co., LTD - ведущий поставщик решений для аддитивного производства со штаб-квартирой в Циндао, Китай. Наша компания специализируется на производстве оборудования для 3D-печати и высокопроизводительных металлических порошков для промышленного применения.
Сделайте запрос, чтобы получить лучшую цену и индивидуальное решение для вашего бизнеса!
Похожие статьи
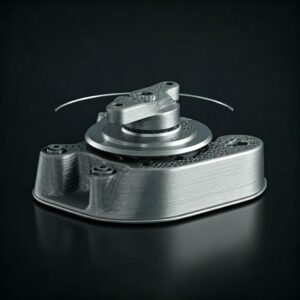
3D-печатные крепления для автомобильных радарных датчиков: Точность и производительность
Читать далее "О компании Met3DP
Последние обновления
Наш продукт
CONTACT US
Есть вопросы? Отправьте нам сообщение прямо сейчас! После получения Вашего сообщения мы всей командой выполним Ваш запрос.
Получите информацию о Metal3DP
Брошюра о продукции
Получить последние продукты и прайс-лист
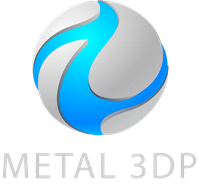
Металлические порошки для 3D-печати и аддитивного производства