3D Printed Avionics Mounts for Vibration and Weight Reduction
Оглавление
Introduction: The Critical Role of Avionics Mounts and the Additive Manufacturing Advantage
In the demanding realm of aerospace engineering, every component matters, but few carry the dual burden of structural integrity and delicate protection quite like avionics mounts. These critical pieces of hardware are the unsung heroes securing the sophisticated electronic systems – the brains and senses of modern aircraft, spacecraft, and unmanned aerial vehicles (UAVs). Avionics systems, encompassing communication, navigation, monitoring, and control functions, rely absolutely on their mounts to perform reliably under extreme conditions. From withstanding punishing G-forces during takeoff and maneuvers to isolating sensitive circuits from engine vibrations and aerodynamic flutter, the role of an avionics mount is far more complex than simply holding a box in place. They are essential for flight safety, mission success, and the longevity of high-value electronic assets.
Traditionally, manufacturing these mounts involved significant challenges. Engineers often relied on subtractive manufacturing techniques, machining brackets and enclosures from solid blocks of metal, typically aluminum or titanium alloys. While effective, this approach inherently leads to substantial material waste (poor buy-to-fly ratios) and limitations in design complexity. Achieving optimal shapes for weight reduction or intricate features for vibration damping often required complex assemblies involving multiple machined parts, fasteners, and specialized damping materials. This not only increased weight – a primary adversary in aerospace design – but also introduced potential points of failure, increased assembly time, and drove up overall costs. Procurement managers faced hurdles in sourcing custom-designed mounts with long lead times associated with tooling and complex machining setups, especially for low-volume, high-specialization parts common in aerospace and defense sectors.
Enter metal 3D-печать, or more broadly, Additive Manufacturing (AM). This suite of technologies is fundamentally changing how engineers approach the design and production of aerospace components, and avionics mounts are prime candidates for this revolution. Instead of carving away material, AM builds parts layer by intricate layer directly from digital designs using high-performance metal powders. This process unlocks unprecedented design freedom, allowing for the creation of highly optimized, lightweight structures that were previously impossible or prohibitively expensive to manufacture. AM enables:
- Massive Weight Reduction: Utilizing topology optimization algorithms, engineers can design mounts with material only where structurally necessary, significantly reducing component weight without compromising strength or stiffness. This translates directly to improved fuel efficiency, increased payload capacity, or enhanced performance envelopes for aircraft and spacecraft.
- Консолидация частей: Complex assemblies, previously made of multiple brackets, fasteners, and plates, can often be redesigned and printed as a single, monolithic component. This drastically reduces part count, simplifies assembly, minimizes potential failure points associated with joints and fasteners, and streamlines the supply chain.
- Расширенная функциональность: AM allows for the integration of complex internal features directly into the mount design. This could include optimized channels for convective cooling of heat-generating electronics, intricate lattice structures designed for specific vibration damping frequencies, or integrated pathways for wiring and connectors.
- Быстрое создание прототипов и итерации: New mount designs can be printed and tested in days or weeks, rather than months, accelerating the development cycle for new avionics systems or aircraft platforms. This agility is crucial in the fast-paced aerospace and defense industries.
For industries like aerospace, defense, and aviation manufacturing, where performance, reliability, and weight are paramount, metal additive manufacturing isn’t just an alternative; it’s rapidly becoming a strategic necessity. Companies specializing in advanced manufacturing solutions, such as Met3dp, are at forefront, providing the technology, materials, and expertise needed to leverage AM for critical components like avionics mounts. As we delve deeper, we’ll explore the specific functions, the compelling reasons to adopt AM, and the best materials for creating next-generation avionics mounting solutions.
Avionics Mounts Decoded: Core Functions, Applications, and Stringent Industry Requirements
To fully appreciate the impact of additive manufacturing, it’s crucial to understand the multifaceted roles avionics mounts play and the harsh conditions they endure. These are not simple brackets; they are engineered components designed to perform several critical functions simultaneously within the tightly constrained environments of aircraft, satellites, missiles, and other aerospace platforms.
Core Functions of Avionics Mounts:
- Structural Support and Securement: The primary function is to securely hold sensitive and often heavy avionics units (often referred to as Line Replaceable Units or LRUs) in place. This prevents movement during high-G maneuvers, turbulence, landing impacts, or launch vibrations, ensuring the physical integrity of the equipment and its connections. The mount must interface precisely with both the airframe structure and the avionics unit, often adhering to standardized form factors like ARINC specifications.
- Vibration Isolation and Damping: Aerospace platforms are inherently vibration-rich environments, stemming from engines, rotors, aerodynamic forces, and structural resonances. These vibrations can be detrimental to the delicate internal components of electronics, leading to fretting corrosion on connectors, fatigue failure of solder joints, and inaccurate sensor readings. Avionics mounts are often designed with features or incorporate materials (sometimes integrated via AM) to isolate the LRU from the most damaging frequencies and dissipate vibrational energy.
- Тепловое управление: Avionics equipment generates significant heat during operation. Mounts can play a role in the thermal management strategy, acting as a heat sink to draw heat away from the LRU and dissipate it into the surrounding structure or airflow. AM allows for the integration of highly efficient cooling channels or optimized conductive pathways directly within the mount structure, improving thermal performance without adding separate cooling hardware.
- Environmental Protection and Interface: Mounts contribute to protecting avionics from factors like moisture, dust, and electromagnetic interference (EMI). They provide a stable platform for electrical connectors, grounding points, and data interfaces, ensuring reliable signal transmission. Design considerations often include features for sealing or shielding integration.
- Crashworthiness and Safety: In crewed aircraft and critical systems, mounts must often meet stringent crashworthiness requirements, ensuring that heavy avionics units do not detach and become dangerous projectiles during survivability scenarios.
Diverse Applications:
The application scope for avionics mounts is vast, covering nearly every electronic system onboard:
- Cockpit Systems: Mounting for primary flight displays (PFDs), multi-function displays (MFDs), control panels, and flight management systems (FMS).
- Communication & Navigation: Securement for radios (VHF, UHF, SATCOM), GPS receivers, transponders, VOR/ILS receivers, and inertial navigation systems (INS).
- Sensors & Monitoring: Brackets for radar equipment, infrared sensors, air data computers (ADCs), gyroscopes, accelerometers, and engine monitoring units.
- Mission Systems (Defense): Mounts for electronic warfare (EW) suites, targeting pods, secure communication gear, and specialized reconnaissance equipment.
- Utility & Control Systems: Housing for flight control computers, power distribution units, lighting controls, and cabin management systems.
- Data Recorders: Secure mounting for cockpit voice recorders (CVRs) and flight data recorders (FDRs), often requiring high survivability designs.
- Satellites & Spacecraft: Lightweight, high-stiffness mounts for sensitive instruments, processors, communication payloads, and power systems, designed to withstand launch loads and operate in the vacuum of space.
Stringent Industry Requirements:
The aerospace industry imposes some of the most rigorous requirements on component design, manufacturing, and qualification. Avionics mounts are no exception:
- Environmental Extremes: Must operate reliably across wide temperature ranges (e.g., -55°C to +85°C or higher), varying altitudes (pressure changes), and humidity levels. Resistance to fluids like hydraulic oil, jet fuel, and de-icing agents is often necessary.
- Mechanical Loads: Must withstand static loads from maneuvering (up to 9G or more), high levels of random and sinusoidal vibration (specified by standards like RTCA DO-160, MIL-STD-810), acoustic noise, and shock loads from landing or pyrotechnic events.
- Ограничения по весу: Mass is always critical. Every gram saved contributes to fuel efficiency or payload capacity. Mounts are prime targets for lightweighting initiatives.
- Совместимость материалов: Materials must be compatible with the airframe structure (preventing galvanic corrosion), the avionics housing, and meet stringent outgassing requirements for space applications.
- Соответствие нормативным требованиям: Parts must meet airworthiness standards set by regulatory bodies like the Federal Aviation Administration (FAA) in the US, the European Union Aviation Safety Agency (EASA), and equivalent military authorities. This involves rigorous testing, documentation, and process control. Traceability of materials and manufacturing processes is paramount.
- Reliability & Longevity: Mounts are expected to perform flawlessly for the entire service life of the aircraft or system, which can span decades and tens of thousands of flight hours.
Meeting these demanding requirements necessitates advanced engineering, precise manufacturing, and robust quality assurance. Aerospace engineering teams and procurement specialists involved in component sourcing must ensure their chosen suppliers can consistently deliver parts that meet these non-negotiable standards. This is where the capabilities of specialized additive manufacturing providers become highly valuable.
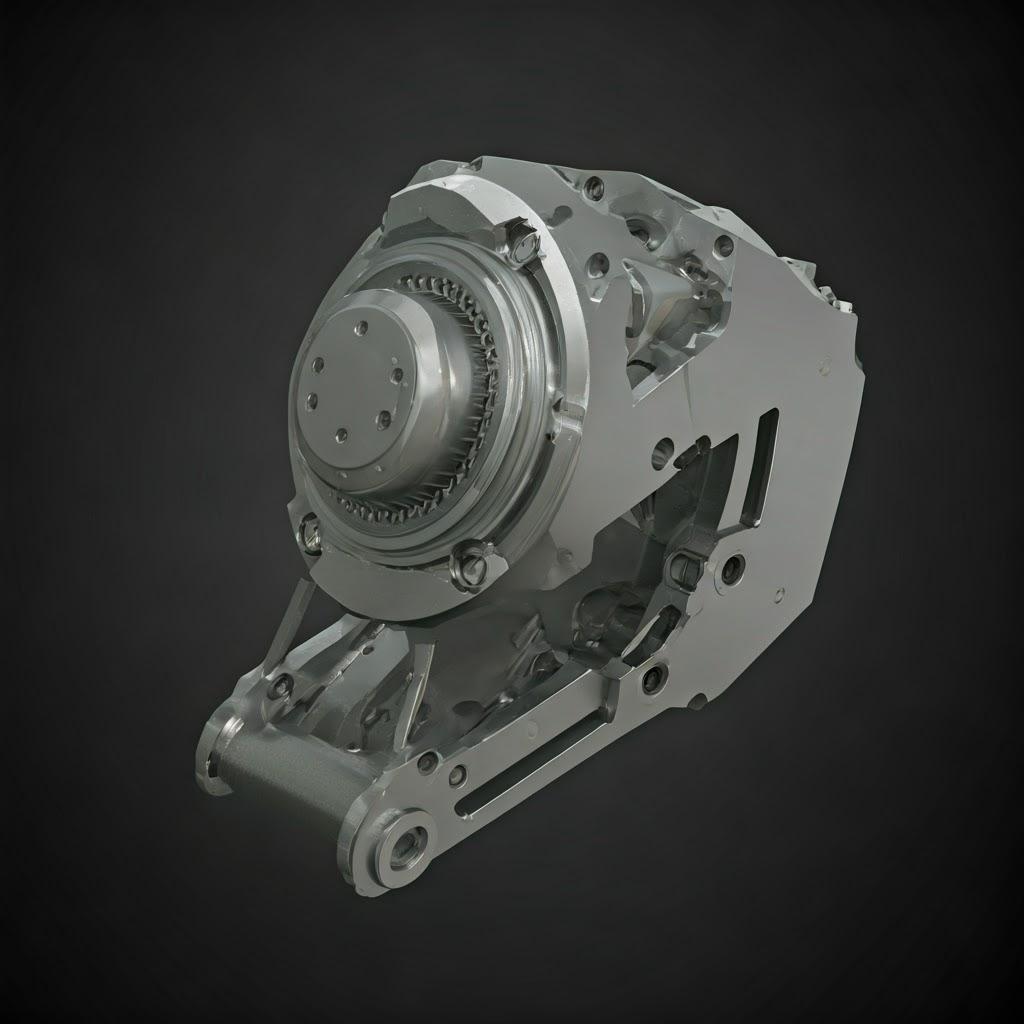
Why Choose Metal 3D Printing for Aerospace Avionics Mounts? Unlocking Performance Gains
The inherent limitations of traditional manufacturing methods often force compromises in avionics mount design, particularly when balancing strength, weight, functionality, and cost. Metal additive manufacturing fundamentally shifts this paradigm, offering engineers powerful tools to overcome these limitations and unlock significant performance improvements. The advantages of using metal 3D printing for these critical aerospace components are compelling and address key industry drivers.
1. Unprecedented Weight Reduction: This is arguably the most significant benefit AM brings to aerospace. Using techniques like Topology Optimization, engineers can computationally determine the most efficient load paths within a design envelope. Software algorithms iteratively remove material from areas experiencing low stress, leaving behind an organic, often skeletal-looking structure that meets all structural requirements with the minimum possible mass.
- How it Works: Define keep-out zones (interfaces, mounting points), apply expected loads (G-forces, vibrations), set performance targets (stiffness, stress limits), and let the software sculpt the optimal shape.
- The Result: Weight savings of 30-60% or even more compared to traditionally machined mounts are commonly achievable. This directly impacts fuel burn, range, emissions, and payload capacity – critical metrics for any aircraft or spacecraft program. AM allows these optimized, complex shapes to be manufactured directly, whereas machining them would be impractical or impossible.
2. Radical Part Consolidation: Traditional mounts often consist of multiple machined pieces (brackets, plates, ribs, standoffs) fastened together. Each fastener adds weight, requires assembly time, and represents a potential failure point (loosening under vibration, stress concentration). Metal AM enables the consolidation of these multiple elements into a single, monolithic printed part.
- Преимущества:
- Reduced Part Count: Simplifies inventory management, procurement, and logistics. Fewer part numbers to track.
- Elimination of Fasteners: Reduces weight and removes potential failure modes associated with bolts, rivets, or screws.
- Simplified Assembly: Reduces labor time and complexity on the production line.
- Improved Structural Integrity: Monolithic parts often exhibit better load distribution and fatigue resistance compared to bolted assemblies.
- Example: A 5-piece bolted assembly could be redesigned as a single, topologically optimized 3D printed component, saving weight and assembly steps.
3. Geometric Complexity for Enhanced Functionality: AM builds parts layer by layer, freeing designers from the constraints imposed by machining access or casting molds. This allows for the creation of intricate internal and external features that enhance performance.
- Integrated Cooling: Complex internal channels can be designed directly into the mount structure to allow for airflow or liquid cooling, efficiently managing heat generated by the avionics unit without separate heat sinks.
- Optimized Vibration Damping: Lattice structures or specific geometric configurations, designed using simulation tools, can be incorporated to dampen specific vibration frequencies, better protecting the sensitive electronics.
- Conformal Designs: Mounts can be designed to conform precisely to complex airframe structures or oddly shaped avionics units, optimizing space utilization within crowded avionics bays.
- Integrated Features: Wiring channels, connector housings, grounding points, or even antenna elements can potentially be integrated directly into the mount’s design.
4. Accelerated Development Cycles via Rapid Prototyping: In the fast-paced world of aerospace R&D, speed matters. AM allows design teams to move from a digital model to a physical metal prototype in a matter of days or weeks.
- Faster Iteration: Engineers can quickly print and test multiple design variations, validating performance (fit, form, basic function) much earlier in the development cycle.
- Reduced Tooling Costs: Prototyping via AM eliminates the need for expensive and time-consuming tooling associated with casting or complex machining setups.
- Risk Reduction: Potential design flaws can be identified and corrected early, reducing the risk of costly changes later in the program. Companies offering услуги быстрого прототипирования using production-grade materials provide invaluable support here.
5. Improved Buy-to-Fly Ratio: Subtractive manufacturing inherently involves removing large amounts of material from a starting block or forging, resulting in significant waste (material that is bought but does not fly). Additive manufacturing, being an additive process, uses only the material needed to build the part and its necessary supports.
- Sustainability & Cost: While high-performance metal powders are expensive, reducing waste significantly improves the buy-to-fly ratio, leading to better material utilization and potentially lower overall costs, especially for complex parts or expensive materials like titanium or high-strength nickel alloys (though aluminum alloys like AlSi10Mg and Scalmalloy® are common for mounts).
6. Customization and On-Demand Manufacturing: AM is ideal for the low-to-medium volume, high-variation nature of many aerospace components.
- Tailored Solutions: Mounts can be easily customized for specific aircraft variants, mission requirements, or updated avionics packages without requiring new tooling.
- Obsolete Part Replacement: AM can be used to manufacture replacements for mounts where original tooling no longer exists or suppliers are gone.
- Distributed Manufacturing: Potential for parts to be printed closer to the point of need, reducing logistical footprints (requires robust qualification and process control).
Choosing AM for avionics mounts is a strategic decision for aerospace manufacturers and B2B manufacturing solutions providers looking to enhance performance, reduce costs, and accelerate innovation. It requires a shift in design thinking (DfAM) and collaboration with capable AM partners, but the potential rewards in terms of weight savings, functional integration, and streamlined production are transforming aerospace component manufacturing.
Material Selection Spotlight: AlSi10Mg and Scalmalloy® for High-Performance Mounts
Choosing the right material is fundamental to the success of any aerospace component, and 3D printed avionics mounts are no different. The selection process involves balancing mechanical properties (strength, stiffness, fatigue life), thermal performance, weight, environmental resistance, manufacturability via AM, and cost. For aluminum alloy mounts, two materials stand out in the additive manufacturing world: the workhorse AlSi10Mg and the high-performance Scalmalloy®. Understanding their respective strengths helps engineers and procurement managers make informed decisions based on specific application requirements.
AlSi10Mg: The Reliable Workhorse
AlSi10Mg is one of the most widely used aluminum alloys in metal additive manufacturing, particularly via Laser Powder Bed Fusion (L-PBF). It’s essentially an aluminum casting alloy adapted for AM processes.
- Key Properties & Advantages:
- Хорошее соотношение прочности и веса: Offers respectable mechanical properties suitable for many structural applications, including moderately loaded mounts.
- Отличная теплопроводность: Beneficial for mounts that play a role in heat dissipation from avionics units.
- Хорошая коррозионная стойкость: Suitable for typical aerospace operating environments.
- Well-Understood Processability: Extensive research and established print parameters exist, leading to reliable and repeatable results from experienced suppliers.
- Эффективность затрат: Generally more economical than higher-performance aerospace alloys like Scalmalloy® or titanium, making it attractive for less demanding applications or cost-sensitive projects.
- Доступность: Widely available from numerous поставщики металлических порошков.
- Typical Aerospace Applications: Ideal for static or moderately loaded mounts, brackets, housings, and components where extreme strength or fatigue performance is not the primary driver. Suitable for UAVs, general aviation, and some commercial aerospace applications where its properties meet design requirements after appropriate heat treatment (typically a T6 cycle for optimal strength).
- Соображения: While strong, its mechanical properties (especially fatigue strength and performance at elevated temperatures) are lower than specialized aerospace alloys. It may not be suitable for highly stressed components or applications requiring exceptional fatigue life.
Scalmalloy®: High-Performance Aluminum for Demanding Applications
Developed specifically for additive manufacturing by APWORKS (an Airbus subsidiary), Scalmalloy® is a patented high-strength aluminum-magnesium-scandium alloy (AlMgSc) designed to push the performance boundaries of printed aluminum.
- Key Properties & Advantages:
- Исключительная прочность: Offers mechanical properties (yield strength, ultimate tensile strength) significantly higher than AlSi10Mg, approaching or even exceeding those of some traditional high-strength 7xxx series aluminum alloys, especially after heat treatment.
- Excellent Fatigue Resistance: Scandium addition creates fine grain structures, leading to superior fatigue life, crucial for components subjected to cyclic loading and vibration.
- Good Ductility & Weldability: Retains good ductility compared to other high-strength aluminum alloys, making it less brittle. It’s also readily weldable, which can be useful for post-processing or assembly if needed.
- High Specific Strength: Combines high strength with low density, resulting in an outstanding specific strength (strength-to-weight ratio), perfect for aerospace lightweighting.
- Хорошая коррозионная стойкость: Similar or better corrosion performance compared to other Al-Mg alloys.
- Elevated Temperature Performance: Maintains good mechanical properties at moderately elevated temperatures better than AlSi10Mg.
- Typical Aerospace Applications: Ideally suited for highly loaded structural components, performance-critical mounts experiencing significant vibration or cyclic stress, safety-critical parts, and applications where maximizing weight savings is paramount. Used in Formula 1, motorsport, high-performance drones, satellites, and increasingly in certified aircraft components.
- Соображения: Scalmalloy® powder is typically more expensive than AlSi10Mg due to the scandium content and licensing. Processing requires optimized parameters and expertise to achieve its full potential.
Comparison Table:
Характеристика | AlSi10Mg | Scalmalloy® | Примечания |
---|---|---|---|
Primary Elements | Al, Si, Mg | Al, Mg, Sc, Zr | Scandium (Sc) is key to Scalmalloy®’s performance. |
Предел текучести | Good (e.g., ~230-280 MPa after T6) | Excellent (e.g., ~450-500 MPa after heat treatment) | Scalmalloy® strength is significantly higher. |
Ultimate Strength | Good (e.g., ~350-450 MPa after T6) | Excellent (e.g., ~500-540 MPa after heat treatment) | Values depend heavily on print parameters and heat treatment. |
Усталостная прочность | Умеренный | Отличный | Critical advantage for vibration-prone avionics mounts. |
Удельная прочность | Хороший | Выдающийся | Enables maximum lightweighting potential. |
Теплопроводность | Отличный | Хороший | AlSi10Mg slightly better for pure thermal conduction. |
Технологичность | Well-established, easier to process | Requires optimized parameters, more sensitive | Expertise needed for consistent Scalmalloy® results. |
Стоимость | Нижний | Выше | Scandium content and licensing increase Scalmalloy® cost. |
Лучший вариант использования | General purpose, moderately loaded mounts | High-load, high-fatigue, weight-critical mounts | Match material to performance requirements. |
Export to Sheets
The Importance of Powder Quality and Supplier Expertise
Regardless of the chosen alloy, the quality of the metal powder is critical for achieving the desired material properties and part integrity in AM. Factors like particle size distribution (PSD), sphericity, flowability, and chemical purity directly impact the density, microstructure, and mechanical performance of the final printed part.
This is where partnering with a knowledgeable поставщик металлического порошка and AM service provider like Met3dp becomes crucial. Met3dp utilizes industry-leading powder manufacturing technologies, including advanced Gas Atomization (employing unique nozzle and gas flow designs) and Plasma Rotating Electrode Process (PREP), to produce high-quality spherical metal powders with high sphericity and excellent flowability – essential for dense, reliable prints. While specializing in innovative alloys like TiNi, TiTa, TiAl, TiNbZr, and CoCrMo, Met3dp’s commitment to quality extends across its product portfolio, ensuring customers receive materials optimized for demanding applications. Their decades of collective expertise in metal AM mean they understand the nuances of processing different alloys, including high-performance aluminum like AlSi10Mg and potentially Scalmalloy® (or equivalent high-strength options), ensuring that the chosen material delivers its promised performance in the final avionics mount. Sourcing high-quality, aerospace-grade powder is the foundation upon which reliable, high-performance 3D printed components are built.
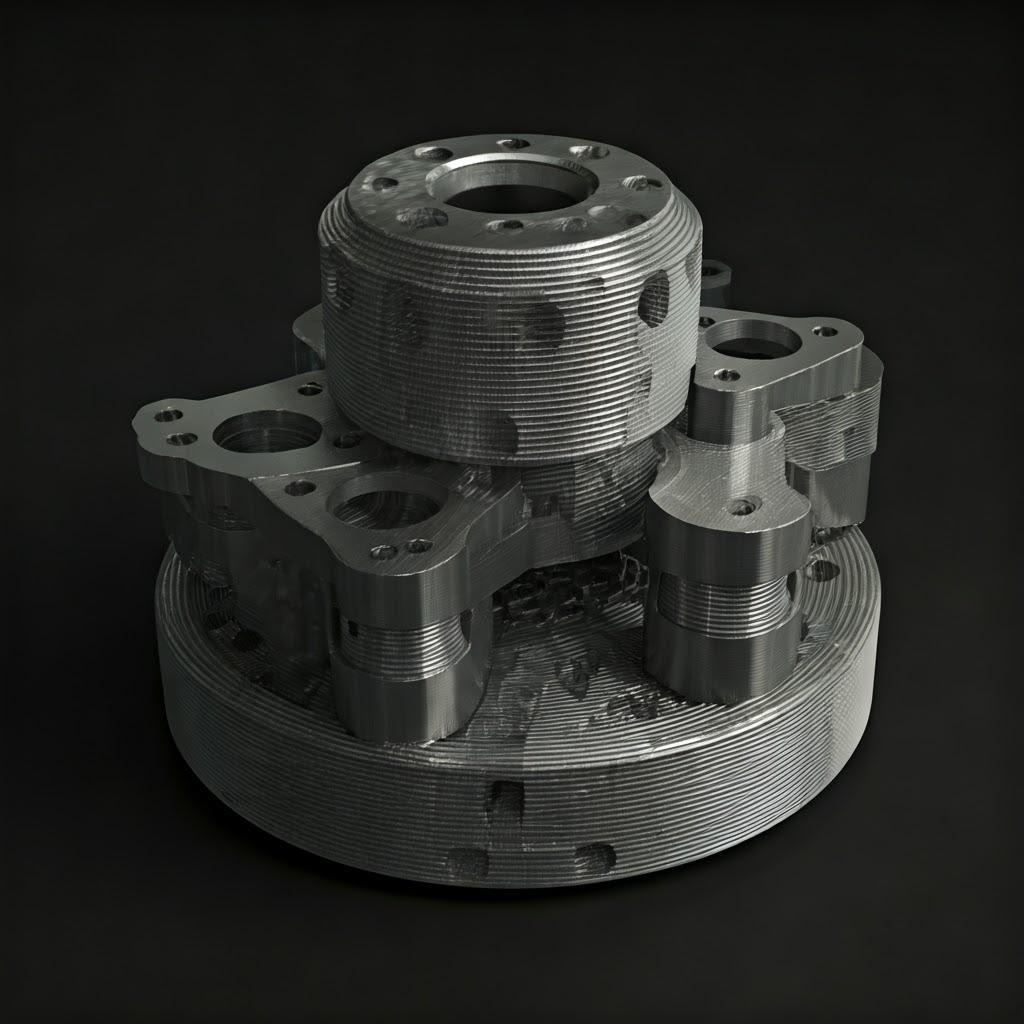
Designing for Success: DfAM Principles for Optimized 3D Printed Avionics Mounts
Simply replicating a design intended for machining or casting using additive manufacturing rarely unlocks the full potential of the technology. To truly leverage the benefits of metal 3D printing – particularly the dramatic weight savings and functional integration possible for avionics mounts – engineers must embrace Проектирование для аддитивного производства (DfAM). DfAM is not just a suggestion; it’s a fundamental shift in mindset, considering the unique capabilities and constraints of the layer-by-layer building process right from the initial concept stage. Applying DfAM principles is crucial for creating optimized, efficient, and reliable 3D printed avionics mounts.
Here are key DfAM considerations specific to designing these components:
1. Leverage Topology Optimization and Generative Design: As mentioned earlier, these computational tools are central to achieving significant weight reduction.
- Процесс: Define the design space (maximum allowable volume), specify fixed points (mounting interfaces with airframe and LRU), define keep-out zones (for connectors, access, etc.), apply realistic load cases (static, dynamic, vibration), and set performance goals (stiffness, stress limits, factor of safety).
- Outcome: The software generates an organic, load-path-optimized structure, often looking skeletal, placing material only where it’s needed. This directly translates to lighter mounts without sacrificing performance. Procurement teams benefit from sourcing components with significantly improved buy-to-fly ratios.
- Tools: Various CAD and CAE software packages now integrate topology optimization and generative design modules (e.g., Altair Inspire, Autodesk Fusion 360, Siemens NX, Dassault Systèmes CATIA). Collaborating with engineering design services experienced in these tools can accelerate the optimization process.
2. Strategize Support Structures: Most metal Powder Bed Fusion (PBF) processes, like Laser PBF (L-PBF or SLM) commonly used for aluminum alloys, require support structures for overhanging features (typically below 45 degrees from the horizontal) and to anchor the part to the build plate, managing thermal stresses.
- Minimize Supports: Design with self-supporting angles (greater than 45 degrees) wherever possible. Orient the part strategically on the build plate to reduce the volume of supports needed.
- Design for Removal: Consider how supports will be removed. Ensure accessibility for tools (manual or CNC). Avoid placing supports on critical functional surfaces or intricate internal channels where removal is difficult or impossible. Design supports that break away easily or are optimized for machining removal.
- Влияние: Reducing support volume saves material cost, print time, and post-processing labor, directly impacting the final component cost and lead time.
3. Optimize Wall Thickness and Feature Size: AM processes have limitations on minimum feature size and wall thickness they can reliably produce.
- Minimum Walls: For L-PBF with AlSi10Mg or Scalmalloy®, minimum printable wall thickness is typically around 0.4-0.8 mm, but designing slightly thicker (e.g., 1 mm or more) is often recommended for robustness and to avoid print failures or distortion, especially for larger structural elements.
- Consistent Thickness: Avoid abrupt changes in wall thickness, which can lead to thermal stress concentrations and potential warping or cracking during the print or cool-down phase.
- Small Features: Holes, pins, and bosses have minimum achievable sizes depending on the machine resolution and process parameters. Ensure critical features are designed within these limits or plan for post-machining.
4. Integrate Functionality Directly: DfAM encourages thinking beyond simple structure. How can the mount do more?
- Internal Channels: Design complex, conformal cooling channels directly within the mount body to dissipate heat from the avionics unit more effectively than a solid block.
- Решетчатые структуры: Incorporate internal lattice structures optimized for vibration damping at specific frequencies, potentially reducing the need for external viscoelastic dampers. These complex geometries are uniquely enabled by AM.
- Wiring Pathways: Create internal conduits or integrated clips/guides for routing cables, simplifying wiring harness installation and protection.
- Consolidated Assemblies: Actively look for opportunities to combine adjacent brackets, fixtures, or thermal components into a single printed part.
5. Plan the Build Orientation: The orientation of the part on the build plate significantly impacts several factors:
- Support Needs: As discussed, orientation affects the amount and location of supports.
- Отделка поверхности: Downward-facing (supported) surfaces generally have a rougher finish than upward-facing or vertical surfaces. Orient critical surfaces accordingly or plan for post-processing.
- Механические свойства: Anisotropy (directional variation in properties) can exist in AM parts, although it’s generally less pronounced in metals compared to polymers. Orientation might be considered for optimizing properties in the primary load direction, though proper parameters and heat treatment often minimize this.
- Print Time & Cost: Taller builds generally take longer. Packing multiple parts efficiently on the build plate impacts overall throughput and cost for wholesale 3D printing заказы.
Effective DfAM requires close collaboration between the design engineers and the AM manufacturing partner, like Met3dp. Leveraging the partner’s expertise on specific machine capabilities, material characteristics, and post-processing considerations early in the design cycle is key to avoiding pitfalls and maximizing the benefits of additive manufacturing for high-performance avionics mounts.
Achieving Precision: Understanding Tolerance, Surface Finish, and Dimensional Accuracy in AM Mounts
While additive manufacturing offers incredible design freedom, it’s crucial for aerospace engineers and procurement managers to understand the levels of precision achievable directly from the printer versus what might require secondary operations. Avionics mounts often have critical interface dimensions, mounting hole patterns, and surface requirements that demand specific tolerances and finishes. Managing expectations and planning necessary post-processing are vital for successful implementation.
Typical As-Printed Tolerances:
Metal L-PBF processes, commonly used for AlSi10Mg and Scalmalloy®, offer good dimensional accuracy, but it’s not equivalent to high-precision machining out-of-the-box.
- General Tolerances: Typical achievable tolerances for well-controlled L-PBF processes are often in the range of ±0.1 mm to ±0.2 mm for smaller dimensions (e.g., up to 100 mm), plus a percentage (e.g., ±0.1% to ±0.2%) for larger dimensions. However, this is highly dependent on the specific machine, part geometry, material, process parameters, and calibration.
- Factors Influencing Accuracy: Thermal shrinkage and potential warping during the build, layer thickness used, laser spot size, scanning strategy, and powder quality all play a role. Residual stress built up during printing can also cause minor distortions after the part is removed from the build plate.
- Supplier Capability: Experienced AM providers like Met3dp, focused on точное производство for mission-critical parts, invest heavily in process control, machine calibration, and thermal simulation to minimize deviations and achieve the best possible as-printed accuracy. Their industry-leading equipment contributes significantly to reliable and accurate outcomes.
As-Printed Surface Finish (Roughness):
The surface finish of an AM part is inherently rougher than a machined surface due to the layer-by-layer construction and the partially melted powder particles adhering to the surface.
- Typical Values: As-printed surface roughness (Ra) for L-PBF aluminum alloys often ranges from 6 µm to 20 µm (approximately 240 to 800 microinches), varying significantly depending on the surface orientation relative to the build direction.
- Upward-facing & Vertical Surfaces: Generally smoother.
- Downward-facing (Supported) Surfaces: Rougher due to contact with support structures. Removing supports also impacts the local surface finish.
- Internal Channels: Can be difficult to finish post-print and will retain a rougher surface unless specifically designed for flow finishing processes.
- Влияние: For non-critical surfaces, the as-printed finish may be acceptable. However, for mating interfaces, sealing surfaces, or areas requiring specific aerodynamic or fatigue performance, post-processing is usually required.
Achieving Tighter Tolerances and Improved Finishes:
For dimensions and surfaces requiring higher precision than achievable in the as-printed state, post-processing is essential.
- CNC Machining: The most common method for achieving tight tolerances (e.g., ±0.01 mm to ±0.05 mm or better) on critical features like mounting holes, interface planes, connector bores, and mating surfaces. Parts are often designed with extra material (machining allowance) in these specific areas.
- Обработка поверхности: Processes like bead blasting, sandblasting, or tumbling can improve the overall surface finish, remove loose powder, and create a uniform aesthetic, although they don’t typically improve dimensional accuracy significantly. Polishing can achieve much smoother surfaces (Ra < 1 µm) where required.
- Inspection & Metrology: High-precision CMM (Coordinate Measuring Machines) and 3D scanning are used to verify dimensional accuracy against the CAD model and engineering drawings throughout the process (as-printed and after post-processing).
Met3dp’s Commitment to Accuracy:
A key factor in achieving reliable precision is the manufacturing partner’s commitment to quality. Met3dp emphasizes industry-leading accuracy and reliability, crucial for mission-critical aerospace components. This stems from:
- Advanced Equipment: Utilizing high-precision printing systems.
- Управление процессом: Implementing rigorous control over printing parameters and environment.
- Powder Quality Management: Ensuring consistent, high-quality metal powders optimized for their systems. You can learn more about their various способы печати and quality focus.
- Экспертиза: Decades of collective experience in metal AM allow for optimized build strategies and troubleshooting.
Understanding the interplay between as-printed capabilities and necessary post-processing allows engineers to design effectively and procurement managers to accurately scope manufacturing requirements when sourcing 3D printed avionics mounts.
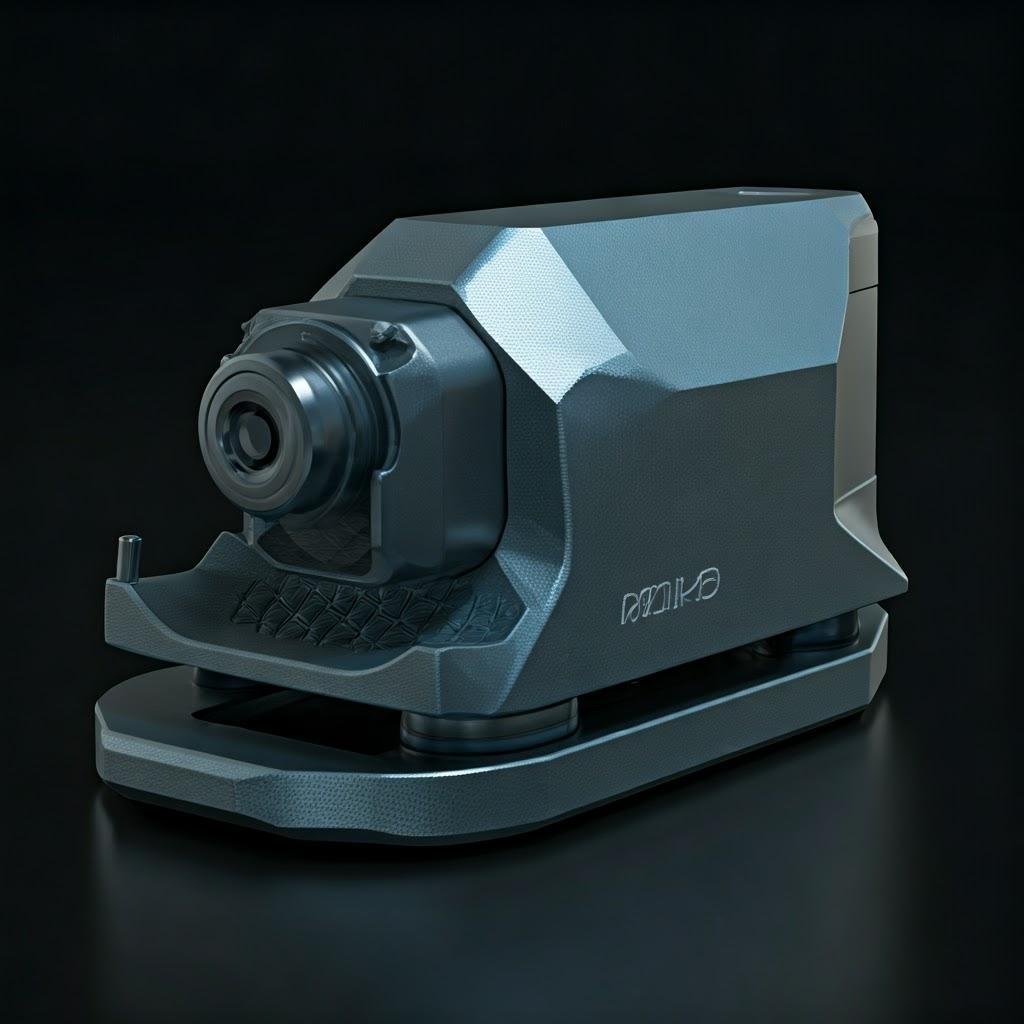
Beyond the Print: Essential Post-Processing Steps for Aerospace-Grade Avionics Mounts
The journey of a 3D printed metal avionics mount doesn’t end when the printer stops. Achieving the final desired mechanical properties, dimensional accuracy, surface characteristics, and overall quality required for demanding aerospace applications necessitates a series of crucial post-processing steps. These steps transform the raw printed part into a flight-ready component. Omitting or improperly executing these stages can compromise performance and reliability.
Here’s a typical workflow for post-processing 3D printed AlSi10Mg or Scalmalloy® avionics mounts:
- Powder Removal (Depowdering):
- Цель: Remove as much unfused metal powder as possible from the part and the build chamber, especially from internal channels or complex features.
- Методы: Typically involves manual brushing, vacuuming, and compressed air blow-off within a controlled environment to safely handle the fine metal powder. Automated depowdering stations are also used. Careful design (DfAM) can facilitate easier powder removal.
- Stress Relief / Heat Treatment:
- Цель: This is arguably one of the most critical steps for metal AM parts, especially aluminum alloys. The rapid heating and cooling cycles during printing induce significant residual stresses within the part. Heat treatment relieves these stresses, preventing distortion during subsequent steps (like removal from the build plate or machining) and significantly improves mechanical properties (strength, ductility, fatigue life).
- Методы: Parts are typically heat-treated while still attached to the build plate to minimize warping. Specific cycles (temperature, time, atmosphere) depend on the alloy:
- AlSi10Mg: Often undergoes a solution treatment followed by artificial aging (e.g., T6 condition) to achieve optimal strength and hardness.
- Scalmalloy®: Requires specific aging treatments tailored to achieve its peak strength and fatigue properties.
- Importance: Skipping or using incorrect heat treatment parameters will result in parts with suboptimal and potentially inconsistent mechanical properties, unsuitable for demanding applications. This is a core competency for any qualified aerospace supplier.
- Removal from Build Plate & Support Removal:
- Цель: Separate the printed part(s) from the metal build plate and remove the temporary support structures generated during the print.
- Методы:
- Plate Removal: Often done using wire EDM (Electrical Discharge Machining) or a bandsaw.
- Удаление опоры: Can involve manual break-off (for well-designed supports), cutting tools (e.g., Dremel), or CNC machining for more integrated or difficult-to-reach supports. DfAM plays a huge role in making this step efficient.
- CNC Machining:
- Цель: Achieve final dimensional accuracy and surface finish on critical features that exceed the as-printed capabilities.
- Приложения: Machining mounting holes to precise diameters and positional tolerances, creating flat and smooth mating surfaces, threading holes, machining O-ring grooves, or bringing any critical dimension within specification.
- Соображения: Requires careful fixture design to hold the often complex AM part geometries securely without distortion. Machining allowances must be included in the DfAM phase.
- Surface Finishing & Cleaning:
- Цель: Improve surface roughness, remove residual support marks, achieve a uniform appearance, and prepare the surface for subsequent coatings or inspections.
- Методы:
- Blasting: Sandblasting, bead blasting, or shot peening using various media (glass beads, aluminum oxide) to clean and texturize the surface. Peening can also improve fatigue life by inducing compressive stresses.
- Tumbling/Vibratory Finishing: Using ceramic or plastic media in a vibratory bowl or tumbler to deburr edges and smooth surfaces, particularly for batches of smaller parts.
- Полировка: Manual or automated polishing for achieving very smooth, mirror-like finishes if required.
- Cleaning: Thorough cleaning to remove any machining fluids, blasting media, or contaminants.
- Inspection & Quality Control (QC):
- Цель: Verify that the finished part meets all dimensional, material, and structural integrity requirements specified in the engineering drawings and quality standards.
- Методы:
- Проверка размеров: Using CMM, 3D scanning, calipers, gauges.
- Неразрушающий контроль (NDT): Crucial for aerospace. Common methods include:
- Computed Tomography (CT Scanning): Provides detailed 3D visualization of internal structures to detect voids, porosity, or inclusions.
- Fluorescent Penetrant Inspection (FPI): Detects surface-breaking cracks or defects.
- Radiographic Testing (X-ray): Detects internal defects.
- Material Property Verification: Sometimes involves testing witness coupons printed alongside the parts to verify tensile strength, hardness, and microstructure after heat treatment.
- Surface Treatments & Coatings (Optional):
- Цель: Enhance corrosion resistance, improve wear resistance, provide electrical insulation or conductivity, or prime for painting.
- Methods for Aluminum:
- Anodizing (Type II or Type III Hardcoat): Creates a hard, corrosion-resistant oxide layer. Can be dyed various colors.
- Chemical Conversion Coating (Chem Film / Alodine): Provides corrosion resistance and a good base for paint adhesion (e.g., MIL-DTL-5541).
Providing turnkey AM solutions often involves managing this entire post-processing chain. Working with a supplier who has robust in-house capabilities or well-managed partnerships for these steps ensures seamless production and guarantees the final avionics mount meets all aerospace specifications.
Navigating Potential Pitfalls: Common Challenges in 3D Printing Avionics Mounts and Mitigation Strategies
While metal additive manufacturing offers tremendous advantages for producing advanced avionics mounts, it’s not without its challenges. Awareness of potential issues and proactive mitigation strategies, often rooted in strong DfAM principles and rigorous process control, are essential for successful outcomes, particularly in the zero-failure tolerance environment of aerospace. Procurement managers and engineers should understand these challenges when evaluating suppliers and project feasibility.
1. Warping and Distortion (Residual Stress):
- Вызов: The intense, localized heating and rapid cooling inherent in L-PBF builds significant residual stresses within the metal part. If not managed, these stresses can cause the part to warp during printing, distort after removal from the build plate, or even crack. Aluminum alloys are particularly susceptible due to their high thermal conductivity and coefficient of thermal expansion.
- Mitigation Strategies:
- Optimized Build Strategy: Careful selection of laser parameters (power, speed, scan strategy) and part orientation. Thermal simulation software can predict stress buildup.
- Robust Support Structures: Well-designed supports anchor the part effectively and help conduct heat away.
- Stress Relief Heat Treatment: Performing a stress relief cycle (often while still on the build plate) is crucial before further processing.
- DfAM: Avoiding large variations in cross-sectional area and designing for thermal management.
2. Porosity:
- Вызов: Small voids or pores can form within the printed material due to incomplete melting, gas entrapment (e.g., from moisture in the powder or insufficient shielding gas), or keyholing (vapor depression instability) during laser melting. Excessive porosity can degrade mechanical properties, particularly fatigue strength.
- Mitigation Strategies:
- High-Quality Powder: Using powder with controlled particle size distribution, high sphericity, good flowability, and low moisture/gas content. Proper powder handling and storage are vital. Met3dp’s advanced powder production systems are designed to ensure optimal powder characteristics.
- Optimized Process Parameters: Fine-tuning laser power, scan speed, layer thickness, and shielding gas flow to ensure complete melting and stable melt pool dynamics.
- Process Monitoring: In-situ monitoring tools (melt pool monitoring, thermal imaging) can help detect process instabilities that might lead to porosity.
- Горячее изостатическое прессование (HIP): A post-processing step involving high temperature and pressure that can close internal pores (adds cost and lead time, but may be required for critical applications).
3. Cracking:
- Вызов: Can occur during printing (hot cracking) or during cool-down/heat treatment (cold cracking), often linked to high residual stresses, alloy composition (some alloys are more susceptible), or inappropriate thermal gradients.
- Mitigation Strategies:
- Alloy Selection: Using alloys known for good printability (AlSi10Mg and Scalmalloy® are generally considered weldable/printable).
- Parameter Optimization & Scan Strategy: Tailoring parameters to minimize thermal stress build-up.
- Pre-heating: Some systems use build plate heating to reduce thermal gradients.
- Appropriate Heat Treatment: Correct stress relief and aging cycles are critical.
4. Support Removal Difficulties:
- Вызов: Supports in hard-to-reach areas, especially internal channels, can be extremely difficult or impossible to remove completely. Support removal can also damage the part surface if not done carefully.
- Mitigation Strategies:
- DfAM: Designing for minimal support needs, using self-supporting angles, providing clear access for support removal tools, and designing supports that detach cleanly.
- Orientation Strategy: Choosing an orientation that minimizes supports on critical surfaces or in inaccessible areas.
- Soluble Supports (Less Common in Metals): Research is ongoing, but currently less common for major metal AM processes.
- Обработка: Planning to machine away supports in critical areas.
5. Achieving Consistent Material Properties:
- Вызов: Ensuring that the mechanical properties (strength, ductility, fatigue life) are consistent throughout the part and from build to build can be challenging, as they are highly sensitive to powder quality, process parameters, and post-processing.
- Mitigation Strategies:
- Rigorous Process Control: Strict adherence to validated process parameters, machine calibration, and environmental controls.
- Powder Management: Stringent quality control, testing, storage, and traceability of metal powders.
- Standardized Heat Treatment: Using precisely controlled and validated heat treatment cycles.
- Qualification & Testing: Implementing robust part qualification plans, including material testing of witness coupons printed with each build. AM quality assurance protocols are paramount.
6. Cost and Lead Time:
- Вызов: While offering long-term benefits, the initial cost per part for AM can be higher than traditional methods, especially for simpler geometries or very large production runs. Lead times involve printing plus extensive post-processing.
- Mitigation Strategies:
- DfAM for Cost: Optimizing designs not just for weight but also for reduced print time (e.g., minimizing height) and easier post-processing (minimal supports).
- Nesting: Printing multiple parts simultaneously on the build plate increases efficiency for bulk additive manufacturing.
- Supplier Partnership: Working with an experienced supplier who can optimize the entire workflow. Evaluating the total cost of ownership, including assembly simplification and operational benefits (weight savings).
Successfully navigating these challenges requires deep expertise in materials science, process engineering, DfAM, and quality control. This underscores the importance of selecting a manufacturing partner, like Met3dp, with proven experience and expert AM support. Their comprehensive understanding, from powder creation to final part qualification, provides the foundation needed to reliably produce high-quality, aerospace-grade 3D printed avionics mounts. Exploring their background and capabilities on the О нас page can offer insights into their commitment to overcoming these industry challenges.
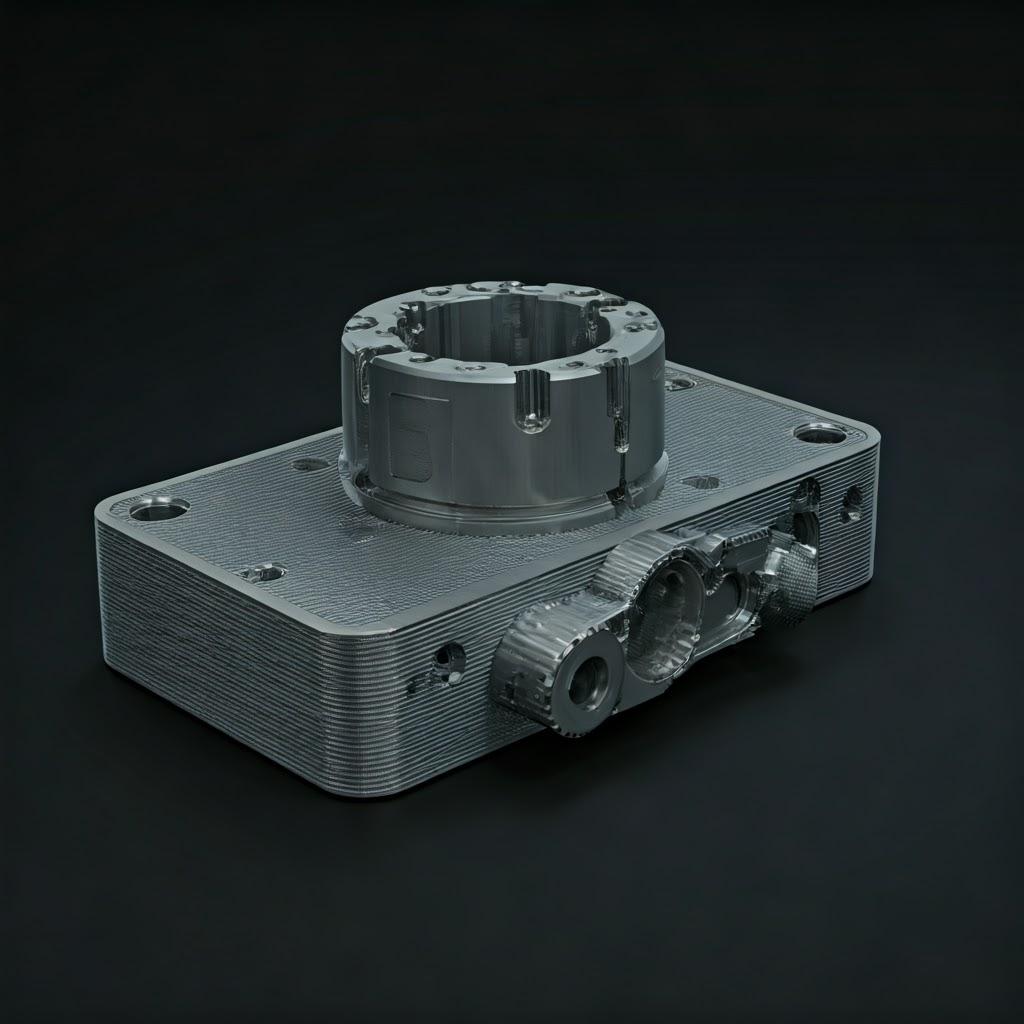
Selecting Your Manufacturing Partner: How to Evaluate Metal 3D Printing Service Providers for Aerospace Components
Choosing the right manufacturing partner is as critical as the design and material selection for producing aerospace-grade 3D printed avionics mounts. The stakes are incredibly high; component failure is not an option. Therefore, aerospace engineers and procurement B2B specialists must conduct rigorous evaluations when sourcing additive manufacturing services. The ideal partner isn’t just a print shop; they are a technology expert, a quality gatekeeper, and a collaborative problem-solver.
Here are key criteria for evaluating potential metal AM service providers for aerospace components:
- Aerospace Certifications and Quality Management System (QMS):
- Requirement: Look for internationally recognized aerospace quality certifications, primarily AS9100 (or equivalent, like EN 9100). This demonstrates a robust QMS tailored to the stringent requirements of the aviation, space, and defense industries, covering aspects like traceability, configuration management, risk management, and process control.
- Why it Matters: Certification provides assurance that the supplier has established and maintains processes capable of consistently producing parts that meet demanding aerospace standards.
- Material Expertise and Traceable Sourcing:
- Requirement: Deep expertise in processing the specific alloys required (e.g., AlSi10Mg, Scalmalloy®). This includes validated parameter sets, understanding of heat treatment responses, and material characterization capabilities. Crucially, they must demonstrate full material traceability from the powder batch back to the source, with certifications (e.g., Certificates of Conformance) for every batch used.
- Why it Matters: Guarantees that the correct, high-quality material is used and that its properties meet specifications. Suppliers who manufacture their own powders, like Met3dp, offer an added layer of control and traceability. Met3dp’s use of advanced Gas Atomization and PREP technologies ensures high sphericity, flowability, and purity – critical for aerospace-grade powders.
- Technology, Equipment, and Process Control:
- Requirement: State-of-the-art, industrial-grade metal AM systems (e.g., L-PBF machines from reputable OEMs) suitable for the chosen materials. Evidence of rigorous machine calibration, maintenance schedules, and environmental controls (temperature, humidity, oxygen levels in the build chamber). In-process monitoring capabilities are a plus.
- Why it Matters: Ensures consistency, repeatability, and the ability to produce dense parts with optimal microstructure. Met3dp prides itself on printers delivering industry-leading print volume, accuracy, and reliability, essential for mission-critical components.
- Engineering and DfAM Support:
- Requirement: The supplier should have experienced application engineers who understand DfAM principles and can collaborate with your design team to optimize the avionics mount for additive manufacturing, weight reduction, support minimization, and functionality.
- Why it Matters: This collaborative approach maximizes the benefits of AM and helps avoid costly print failures or suboptimal designs. Met3dp’s decades of collective expertise in metal AM underpins their ability to provide valuable application development services.
- Comprehensive Post-Processing Capabilities:
- Requirement: Assess their in-house capabilities or rigorously vetted partnerships for all necessary post-processing steps: stress relief/heat treatment (with certified furnaces), support removal, high-precision CNC machining, surface finishing, NDT inspection (CT, FPI, etc.), and surface treatments (anodizing, chem film).
- Why it Matters: A single source or tightly managed supply chain for all steps simplifies logistics, ensures accountability, and maintains quality control throughout the entire manufacturing process. This turnkey AM solution approach reduces risk for the buyer.
- Proven Track Record and Aerospace Experience:
- Requirement: Look for evidence of successful projects within the aerospace industry. Case studies, references, and examples of similar components (brackets, mounts, housings) they have produced are valuable indicators of capability and experience.
- Why it Matters: Aerospace has unique requirements; a supplier familiar with the standards, documentation needs, and performance expectations is better equipped to deliver conforming parts. Met3dp’s focus spans aerospace, medical, and automotive – all demanding fields requiring high precision and reliability.
- Capacity, Lead Times, and Scalability:
- Requirement: Ensure the supplier has the machine capacity and operational efficiency to meet your project timelines, from prototypes to potential wholesale 3D printing or production volumes. Evaluate their ability to scale production if needed.
- Why it Matters: Meeting program schedules is critical in aerospace. Understand their quoting process, typical lead times, and how they manage production scheduling.
- Location and Logistics:
- Requirement: While global sourcing is common, consider the implications of location on shipping times, costs, communication (time zones), and potential site visits or audits.
- Why it Matters: Efficient logistics and clear communication channels are essential for smooth project execution. Met3dp, headquartered in Qingdao, China, serves a global clientele, leveraging its position as a leader in metal AM equipment and materials.
Why Met3dp Stands Out:
Met3dp emerges as a compelling partner when evaluated against these criteria. As a leading provider of additive manufacturing solutions specializing in both 3D printing equipment and high-performance metal powders, they offer a unique synergy:
- Integrated Expertise: From powder production using advanced atomization techniques to printing on systems designed for accuracy and reliability, Met3dp controls key aspects of the value chain.
- Material Focus: Their portfolio includes innovative aerospace-relevant alloys, demonstrating a deep understanding of materials science in AM.
- Comprehensive Solutions: Offering SEBM printers (though L-PBF is typical for Al/Scalmalloy, their broader expertise is relevant), advanced metal powders, and application development services, they position themselves as a true partner in adopting AM.
- Commitment to Quality: Their focus on mission-critical parts for demanding industries underscores their commitment to meeting stringent quality requirements.
Выбор qualified aerospace supplier like Met3dp provides confidence that your 3D printed avionics mounts will be manufactured to the highest standards, leveraging cutting-edge technology and deep domain expertise.
Understanding the Investment: Key Cost Drivers and Lead Time Considerations for 3D Printed Mounts
While the performance benefits of 3D printed avionics mounts are clear, understanding the associated costs and timelines is crucial for project planning and budgeting. Procurement managers need insight into what drives the price and delivery schedule for these advanced components. The metal 3D printing cost is influenced by a combination of factors:
Key Cost Drivers:
- Part Volume & Size: Larger parts consume more material and require longer print times, directly increasing costs. The overall bounding box size impacts how many parts can fit on a single build plate.
- Part Complexity & Design: Highly complex geometries, especially those requiring extensive support structures or intricate internal features, increase print time and post-processing effort (support removal, finishing). However, complexity achieved through part consolidation can offset costs by reducing assembly labor later.
- Material Choice: The raw material powder is a significant cost component. High-performance alloys like Scalmalloy® are inherently more expensive than standard AlSi10Mg due to alloying elements (scandium) and licensing/production costs. The amount of material used (part volume + support volume) is critical.
- Support Structure Volume: Supports consume material and require significant labor or machining time to remove. DfAM practices aimed at minimizing supports directly reduce costs.
- Order Quantity (Volume): Like most manufacturing processes, economies of scale apply. Wholesale 3D printing or larger batch orders generally result in a lower cost per part compared to single prototypes, due to setup time amortization, optimized build plate utilization (nesting), and potentially volume discounts on powder.
- Требования к постобработке: Each additional step (heat treatment, extensive CNC machining, specific surface finishes, coatings, rigorous NDT) adds cost due to labor, machine time, and specialized equipment usage. Machining often becomes a significant cost driver for achieving tight tolerances.
- Quality Assurance & Inspection: The level of inspection required (e.g., basic dimensional checks vs. full CT scanning and FPI) impacts cost. Aerospace components typically demand higher levels of NDT, contributing to the final price. Documentation packages also add overhead.
Lead Time Considerations:
Lead time is the total time from order placement to part delivery. For 3D printed avionics mounts, it typically includes:
- Pre-Processing: File preparation, build simulation, scheduling (can take 1-3 days).
- Print Time: Highly variable based on part size, complexity, nesting efficiency, and layer thickness used. Can range from 12 hours to several days for a single build plate.
- Post-Processing Queue & Execution: This is often the largest variable. Includes cool-down time, heat treatment cycles (can take a full day or more), depowdering, support removal, CNC machining setup and runtime, finishing, inspection, and coating application times. Queue times at each step depend on the supplier’s workload. Total post-processing can range from a few days to several weeks depending on complexity.
- Перевозки: Dependent on the supplier’s location and the chosen shipping method.
Typical Ranges (Subject to Variation):
- Прототипы: Often 1-3 weeks, depending on complexity and post-processing needs.
- Production Batches: Can range from 3 weeks to several months, depending on quantity, part complexity, required qualification level, and supplier capacity.
Engaging with potential suppliers like Met3dp early to get detailed quotes based on finalized designs is crucial. Their integrated approach and expertise can help optimize the entire workflow, potentially streamlining lead times compared to managing multiple disparate vendors for printing, heat treatment, machining, and inspection. Accurate production cost analysis requires considering the entire process chain.
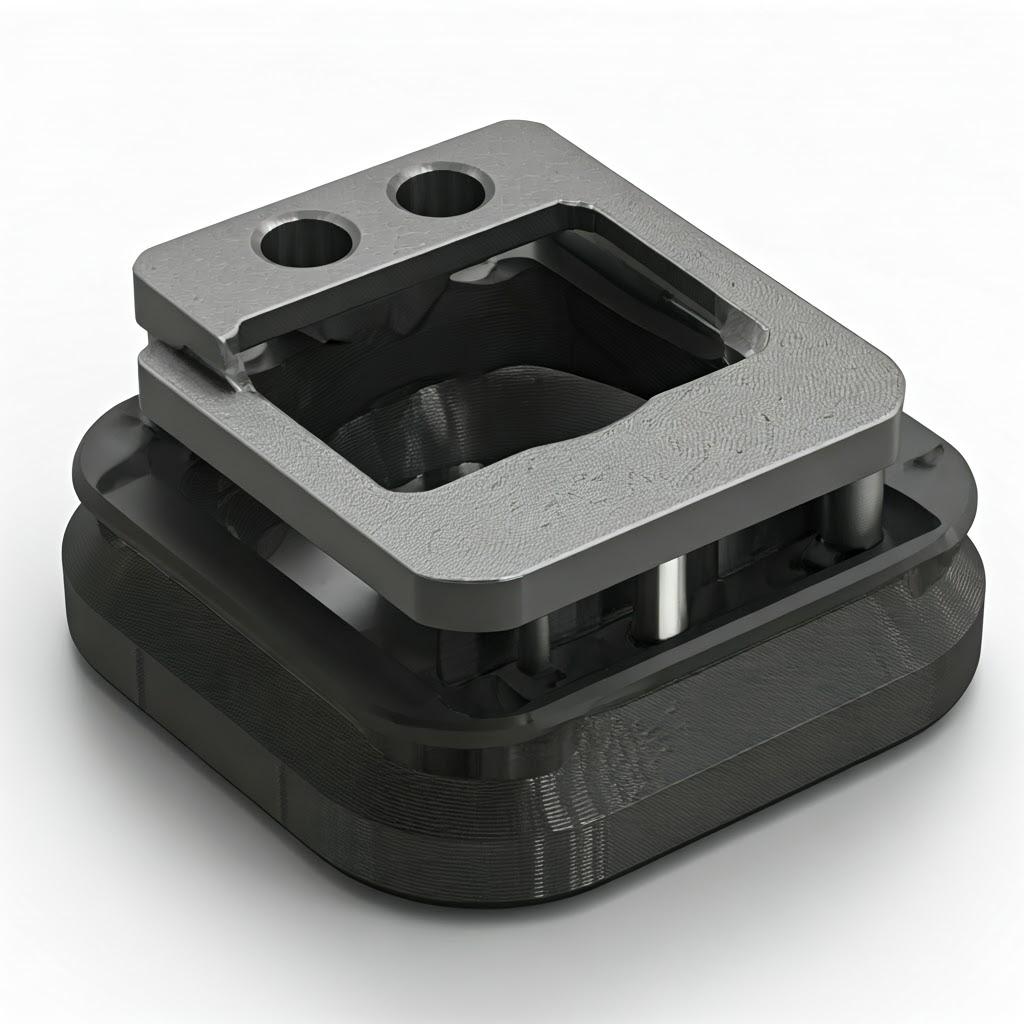
Frequently Asked Questions (FAQ): Addressing Common Queries from Aerospace Engineers and Procurement Teams
When adopting a relatively new technology like metal AM for critical components, questions inevitably arise. Here are answers to some common queries regarding 3D printed avionics mounts:
Q1: What are the main advantages of using Scalmalloy® over AlSi10Mg for avionics mounts?
- A: The primary advantages of Scalmalloy® are its significantly higher yield strength, ultimate tensile strength, and fatigue strength compared to AlSi10Mg, especially after appropriate heat treatment. This makes it ideal for mounts subjected to high static loads, significant vibration, or cyclic stresses where long fatigue life is critical. Its excellent specific strength (strength-to-weight ratio) also allows for potentially greater weight savings in performance-critical applications. Choose Scalmalloy® when AlSi10Mg’s properties are insufficient for the load requirements or when maximizing performance and durability is paramount.
Q2: How does the fatigue life of 3D printed aluminum mounts compare to traditionally machined parts?
- A: This is a complex question highly dependent on the specific alloy, print quality (porosity, defects), surface finish, and post-processing. For standard alloys like AlSi10Mg, the fatigue performance of as-printed parts might be lower than wrought equivalents due to microstructure and surface roughness, but it can be significantly improved with optimized parameters, HIP (Hot Isostatic Pressing), and surface treatments (like shot peening). High-performance AM alloys like Scalmalloy® are specifically designed for excellent fatigue resistance and can meet or even exceed the fatigue performance of some traditional wrought aluminum alloys when processed correctly. Rigorous testing and qualification are essential to validate fatigue life for any specific application.
Q3: What level of traceability and quality documentation can I expect from a supplier like Met3dp for aerospace parts?
- A: A qualified aerospace supplier like Met3dp, especially one aiming for or holding AS9100 certification, should provide comprehensive documentation. This typically includes:
- Material Traceability: Certificates of Conformance for the powder batch used, linking it back to the original powder production lot and its chemical/physical analysis.
- Process Records: Documentation of the specific build parameters used, machine identification, operator logs, and build report (potentially including in-process monitoring data).
- Post-Processing Records: Confirmation and parameters for heat treatment cycles, machining reports, finishing processes applied.
- Inspection Reports: Dimensional inspection data (e.g., CMM reports), NDT reports (CT scan analysis, FPI results), and final inspection certificate.
- Certificate of Conformance (CoC): A final document stating that the part conforms to all specified requirements (drawing, specifications).
Q4: Can 3D printed mounts meet the vibration and shock requirements for aerospace applications (e.g., RTCA DO-160, MIL-STD-810)?
- A: Yes, absolutely. Properly designed and manufactured 3D printed metal mounts using appropriate materials (like AlSi10Mg or Scalmalloy®) and post-processing can meet stringent aerospace vibration and shock requirements. The key lies in:
- Accurate Simulation: Using Finite Element Analysis (FEA) during the design phase to predict response to vibration and shock loads.
- DfAM for Dynamics: Potentially incorporating features like optimized lattice structures for damping or ensuring sufficient stiffness through topology optimization.
- Свойства материала: Leveraging the high strength and fatigue resistance of alloys like Scalmalloy®.
- Qualification Testing: Performing physical vibration and shock testing on the final component or assembly according to relevant standards (e.g., DO-160) to validate performance.
Q5: What is the typical lead time for procuring prototype vs. production batches of 3D printed avionics mounts?
- A: As mentioned previously, lead times vary greatly. Прототипы might take 1-3 недели if complexity and post-processing are moderate. Production batches involve more extensive planning, potentially tooling for machining fixtures, batch processing for heat treatment and finishing, and comprehensive QC, leading to lead times ranging from 3 weeks to several months depending on the quantity, complexity, and qualification requirements. Always request specific lead time estimates from your supplier based on the final part data and quantity.
Conclusion: Elevating Aerospace Performance with Met3dp’s Advanced Additive Manufacturing for Avionics Mounts
The aerospace industry’s relentless pursuit of higher performance, lower weight, and increased efficiency demands innovative manufacturing solutions. Metal additive manufacturing has unequivocally emerged as a powerful enabler, particularly for complex and critical components like avionics mounts. By moving beyond the constraints of traditional methods, AM unlocks the potential for significant снижение веса through topology optimization, enhances functionality via сложные геометрии и объединение частей, and accelerates development cycles through быстрое прототипирование.
Materials like the reliable AlSi10Mg and the high-performance Scalmalloy® provide engineers with options tailored to diverse operational demands, from standard applications to the most challenging, fatigue-critical scenarios. However, realizing these benefits hinges on embracing Проектирование для аддитивного производства (DfAM) principles and navigating essential постобработка steps to achieve aerospace-grade quality, precision, and reliability.
Crucially, the success of implementing 3D printed avionics mounts depends heavily on selecting the right manufacturing partner. The ideal supplier must possess not only state-of-the-art equipment but also deep expertise in materials science, process control, aerospace quality standards (AS9100), and collaborative DfAM support.
Met3dp stands as a leader in this field, offering a comprehensive ecosystem for metal additive manufacturing. With their foundation in producing высококачественные металлические порошки using advanced atomization techniques, operating industry-leading printing systems focused on accuracy and reliability, and providing decades of collective expertise in AM applications, Met3dp is uniquely positioned to support aerospace companies in their digital manufacturing transformations. They provide comprehensive solutions spanning printers, advanced materials, and application development, partnering with organizations to turn innovative designs into flight-ready realities.
Whether you are developing next-generation aircraft, optimizing satellite payloads, or seeking replacements for legacy components, leveraging metal AM for avionics mounts offers a distinct competitive advantage. We invite you to explore how Met3dp’s cutting-edge systems, advanced materials, and expert services can power your organization’s additive manufacturing goals.
Ready to revolutionize your avionics components? Contact Met3dp today to discuss your project requirements and discover the possibilities of advanced metal 3D printing. Visit our website at https://met3dp.com/ to learn more about our capabilities and solutions.
Поделиться
MET3DP Technology Co., LTD - ведущий поставщик решений для аддитивного производства со штаб-квартирой в Циндао, Китай. Наша компания специализируется на производстве оборудования для 3D-печати и высокопроизводительных металлических порошков для промышленного применения.
Сделайте запрос, чтобы получить лучшую цену и индивидуальное решение для вашего бизнеса!
Похожие статьи
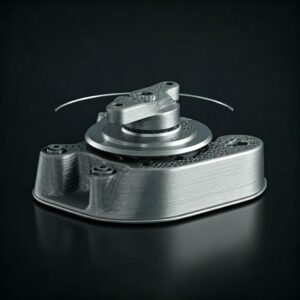
3D-печатные крепления для автомобильных радарных датчиков: Точность и производительность
Читать далее "О компании Met3DP
Последние обновления
Наш продукт
CONTACT US
Есть вопросы? Отправьте нам сообщение прямо сейчас! После получения Вашего сообщения мы всей командой выполним Ваш запрос.
Получите информацию о Metal3DP
Брошюра о продукции
Получить последние продукты и прайс-лист
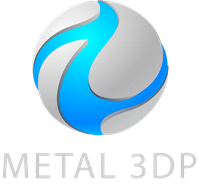
Металлические порошки для 3D-печати и аддитивного производства