Custom Bone Plates: Revolutionizing Orthopedic Implants with Metal 3D Printing
Оглавление
Introduction – The Paradigm Shift in Orthopedic Care with Custom Bone Plates
The field of orthopedic surgery is continually evolving, with advancements in materials science and manufacturing techniques paving the way for more personalized and effective patient care. Among these innovations, the advent of metal 3D-печать, also known as metal additive manufacturing, stands out as a transformative technology. This groundbreaking approach is revolutionizing the creation of custom bone plates, offering unprecedented levels of design freedom, material optimization, and patient-specific fit. Imagine a future where every bone plate is meticulously crafted to the unique anatomy of the individual, leading to improved surgical outcomes, faster healing times, and enhanced patient comfort. This future is rapidly becoming a reality, driven by the precision and versatility of metal 3D printing. At the forefront of this revolution is Metal3DP Technology Co., LTD, a leading provider of additive manufacturing solutions headquartered in Qingdao, China. With their industry-leading print volume, accuracy, and reliability, Metal3DP is empowering medical professionals and device manufacturers to explore the vast potential of custom 3D-printed bone plates for a wide range of orthopedic applications. Their commitment to innovation and quality positions them as a trusted partner in this rapidly advancing field. To learn more about Metal3DP and their capabilities, visit their О нас страница.
What are Load-Bearing Bone Plates Used For? Applications Across Medical Fields
Load-bearing bone plates are essential medical devices designed to provide stability and support to fractured or surgically reconstructed bones. Their primary function is to bear physiological loads, facilitate proper alignment, and promote the healing process. These plates are meticulously engineered to withstand the stresses and strains exerted on the skeletal system during movement and weight-bearing activities. The applications of load-bearing bone plates span a wide spectrum of orthopedic procedures, addressing various traumatic injuries, degenerative conditions, and reconstructive surgeries.
Key Applications of Load-Bearing Bone Plates:
- Fracture Fixation: This is perhaps the most common application, where bone plates are used to stabilize and join the fragments of broken bones, ensuring proper alignment for healing. They are crucial in treating complex fractures, non-unions (fractures that fail to heal), and malunions (fractures that heal in an incorrect position).
- Spinal Fusion: In spinal surgery, bone plates are used to stabilize the vertebrae and promote fusion, a process where two or more vertebrae grow together. This is often necessary to treat spinal instability, deformities, or degenerative conditions.
- Joint Reconstruction: Bone plates play a vital role in reconstructive surgeries involving joints, such as osteotomies (bone reshaping procedures) and arthrodesis (joint fusion). They provide the necessary support and fixation for the altered bone structures.
- Травматологическая хирургия: In high-energy trauma cases involving multiple fractures or significant bone damage, robust load-bearing plates are essential for stabilizing the skeletal system and facilitating the patient’s recovery.
- Corrective Osteotomies: These procedures involve cutting and reshaping bones to correct deformities or misalignments. Bone plates are used to maintain the corrected position during the healing process.
- Tumor Resection: Following the surgical removal of bone tumors, load-bearing plates can be used to bridge gaps and provide structural support to the affected area.
The ability to customize the design of these bone plates through metal 3D printing opens up new possibilities for addressing complex anatomical variations and specific patient needs, potentially leading to improved outcomes and reduced complications. Metal3DP‘s advanced 3D-печать по металлу services are well-suited for producing these intricate and patient-specific implants.
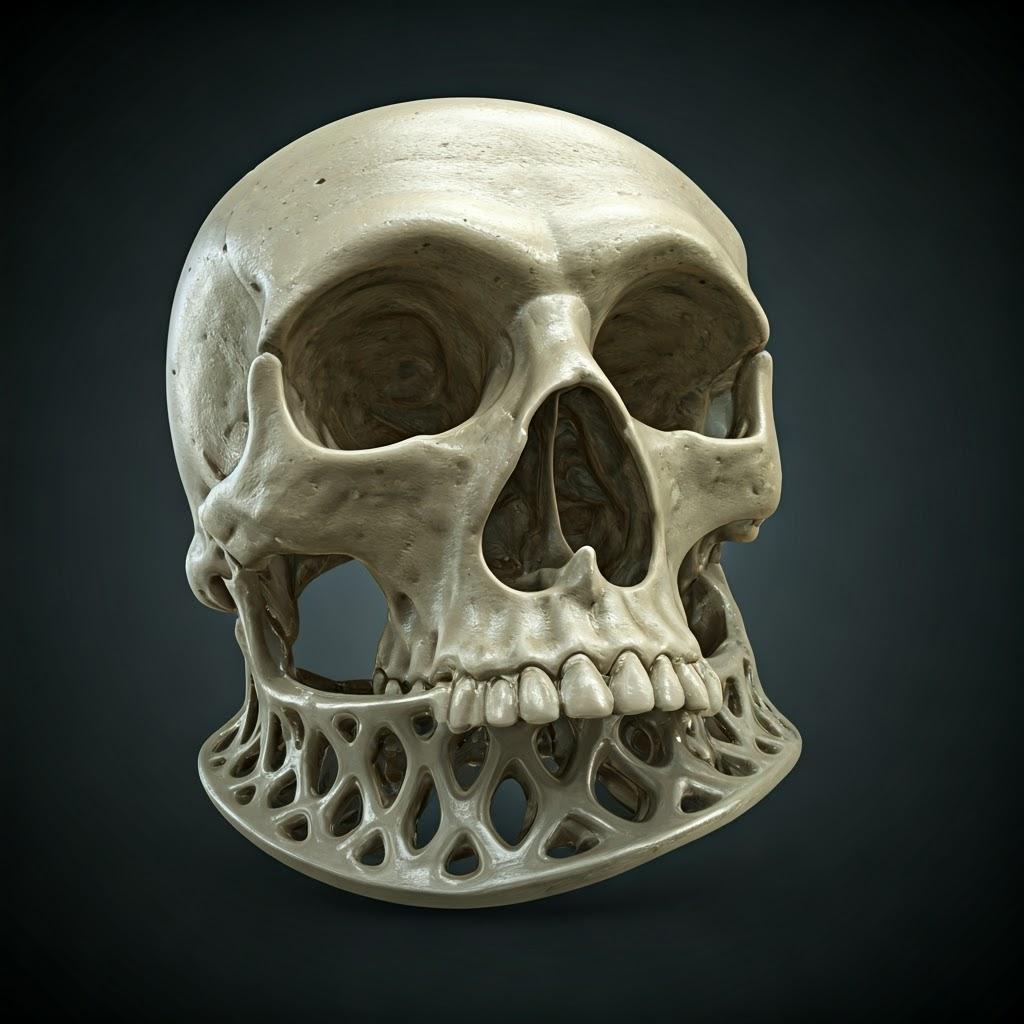
Why Choose Metal 3D Printing for Custom Bone Plates? Advantages Over Traditional Manufacturing
Traditional manufacturing methods for bone plates, such as machining and casting, often involve standardized designs that may not perfectly match the unique anatomical contours of each patient. This can lead to challenges in achieving optimal fit, potentially increasing surgical complexity, recovery time, and the risk of complications. Metal 3D printing offers a paradigm shift, providing numerous advantages for the creation of custom bone plates:
Advantages of Metal 3D Printing for Bone Plates:
- Индивидуальная настройка под конкретного пациента: Metal 3D printing allows for the creation of bone plates that are precisely tailored to the individual patient’s anatomy, derived from medical imaging data such as CT scans or MRI. This ensures an optimal fit, potentially leading to better load distribution, reduced stress on the implant and surrounding bone, and improved surgical outcomes.
- Complex Geometries and Design Freedom: Additive manufacturing enables the fabrication of intricate geometries and features that are difficult or impossible to achieve with traditional methods. This includes porous structures for enhanced osseointegration (bone ingrowth), complex curvature to match bone contours, and integrated screw holes at precise angles.
- Быстрое создание прототипов и итерации: Metal 3D printing facilitates rapid prototyping, allowing surgeons and engineers to quickly iterate on designs based on pre-operative planning and intra-operative feedback. This agile approach can lead to optimized implant designs and reduced development time.
- Оптимизация материалов: Metal 3D printing allows for precise control over material distribution, enabling the creation of lightweight yet strong implants. Furthermore, techniques like lattice structures can be incorporated to reduce weight while maintaining structural integrity and promoting bone ingrowth. Metal3DP offers a range of high-quality metal powders, including the biocompatible Ti-6Al-4V ELI, specifically optimized for these applications.
- Сокращение отходов материалов: Compared to subtractive manufacturing processes like machining, additive manufacturing typically generates less material waste as material is only deposited where needed. This can lead to cost savings and a more sustainable manufacturing process.
- Производство по требованию: Metal 3D printing enables on-demand manufacturing, producing implants as needed rather than relying on large production runs and inventory management. This can be particularly beneficial for custom implants required for specific patient cases.
Metal3DP‘s expertise in Методы печати, including Selective Electron Beam Melting (SEBM), ensures the production of high-density, high-quality metal parts suitable for demanding medical applications like load-bearing bone plates.
Ti-6Al-4V ELI: The Ideal Material for High-Performance Bone Plates
The selection of the appropriate material is paramount in the design and manufacturing of load-bearing bone plates, as it directly impacts the implant’s biocompatibility, mechanical strength, corrosion resistance, and long-term performance within the human body. Titanium alloy Ti-6Al-4V ELI (Extra-Low Interstitial) stands out as an exceptionally well-suited material for these critical medical implants.
Key Properties and Benefits of Ti-6Al-4V ELI for Bone Plates:
- Superior Biocompatibility: Titanium and its alloys are renowned for their excellent biocompatibility, meaning they are well-tolerated by the human body and promote osseointegration – the direct structural and functional connection between living bone and the surface of an artificial implant. The ELI grade of Ti-6Al-4V has lower levels of interstitial elements (oxygen, nitrogen, carbon, and hydrogen), further enhancing its biocompatibility and corrosion resistance compared to standard Ti-6Al-4V.
- Высокое соотношение прочности и веса: Ti-6Al-4V ELI offers an exceptional combination of high tensile strength and low density. This is crucial for load-bearing implants as it allows for the creation of strong and durable plates that are also lightweight, reducing stress on the surrounding tissues and improving patient comfort.
- Отличная коррозионная стойкость: The human body is a corrosive environment, and implant materials must be able to withstand degradation over time. Titanium alloys possess a natural oxide layer that provides excellent resistance to corrosion, ensuring the long-term integrity and functionality of the bone plate.
- Osseointegration Promotion: The surface properties of titanium alloys, particularly when processed through additive manufacturing techniques that can create porous structures, promote the ingrowth of bone tissue. This osseointegration is essential for the long-term stability and fixation of the bone plate.
- Усталостная прочность: Load-bearing bone plates are subjected to cyclic loading during patient movement. Ti-6Al-4V ELI exhibits high fatigue strength, meaning it can withstand repeated stress without fracturing, ensuring the long-term reliability of the implant.
- Radiolucency Considerations: While titanium is not radiolucent (transparent to X-rays), its biocompatibility and mechanical properties often outweigh this consideration in load-bearing applications where clear visualization of the healing bone may be achieved through other imaging modalities or the implant’s design.
Metal3DP recognizes the critical importance of material selection in medical device manufacturing. Their advanced powder making system ensures the production of high-quality Ti-6Al-4V ELI powder with high sphericity and good flowability, optimized for additive manufacturing processes to yield dense, high-performance bone plates with superior mechanical properties. You can explore Metal3DP‘s range of Продукция and their commitment to providing high-quality metal powders for demanding applications.
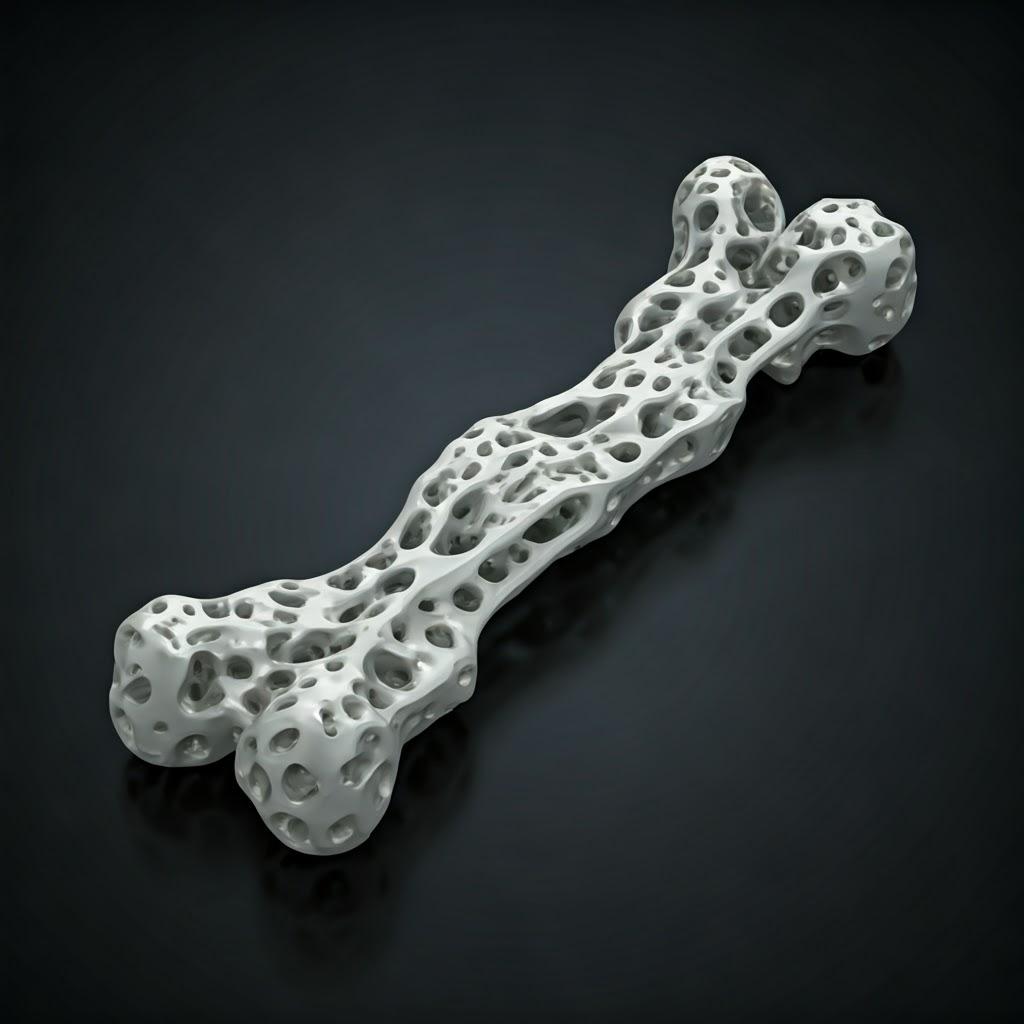
Design Considerations for 3D-Printed Bone Plates: Optimizing for Functionality and Osseointegration
Designing bone plates for additive manufacturing requires a different mindset compared to traditional methods. The layer-by-layer fabrication process allows for intricate geometries and customized features that can significantly enhance the functionality and osseointegration of the implant. Careful consideration of design parameters is crucial for achieving optimal clinical outcomes.
Key Design Considerations for 3D-Printed Bone Plates:
- Patient-Specific Geometry: The primary advantage of 3D printing is the ability to create bone plates that precisely match the patient’s unique anatomy. This requires accurate conversion of medical imaging data (CT or MRI scans) into a 3D model. The plate should contour perfectly to the bone surface to ensure optimal fit, load distribution, and reduced stress concentrations.
- Screw Hole Placement and Orientation: The placement and angulation of screw holes are critical for secure fixation of the bone plate. With 3D printing, screw holes can be precisely positioned and oriented to align with the underlying bone structure, maximizing screw purchase and stability. Consideration should be given to self-tapping features or threads that can be directly incorporated into the design.
- Porous Structures for Osseointegration: Incorporating porous regions or lattice structures within the bone plate design can significantly enhance osseointegration. These interconnected pores allow bone tissue to grow into the implant, promoting long-term stability and integration. The pore size, shape, and interconnectivity are crucial factors to optimize for effective bone ingrowth.
- Surface Texture: The surface finish of the bone plate plays a vital role in osseointegration. 3D printing allows for the creation of controlled surface textures, such as micro-roughness, which has been shown to promote cell adhesion and bone formation. Techniques like post-processing or direct printing of textured surfaces can be employed.
- Load Distribution and Stress Shielding: The design of the bone plate should aim to distribute the physiological loads effectively across the fracture site while minimizing stress shielding – a phenomenon where the rigid implant bears too much load, leading to bone resorption (loss of bone density) beneath the plate. Finite element analysis (FEA) can be used to optimize the plate’s geometry and thickness for appropriate load transfer.
- Minimally Invasive Surgery Considerations: The design should also consider the surgical approach. For minimally invasive procedures, the plate might need to be smaller or have specific features that facilitate insertion through smaller incisions.
- Integration of Drug Delivery Systems: Advanced designs can even incorporate channels or reservoirs for localized drug delivery, such as antibiotics or bone growth factors, further enhancing the healing process and reducing the risk of infection.
By leveraging the design freedom offered by metal 3D printing, in collaboration with a knowledgeable partner like Metal3DP, engineers and surgeons can create bone plates that are not just fixation devices but active participants in the healing process.
Achieving Precision: Tolerance, Surface Finish, and Dimensional Accuracy in 3D-Printed Implants
In the realm of medical implants, particularly load-bearing bone plates, precision is paramount. The dimensional accuracy, tolerance, and surface finish of the implant directly impact its fit, stability, and interaction with the surrounding tissues. Metal 3D printing technologies, when properly controlled and validated, can achieve remarkable levels of precision suitable for these critical applications.
Key Aspects of Precision in 3D-Printed Bone Plates:
- Точность размеров: This refers to the degree to which the printed part matches the intended design dimensions. Factors influencing dimensional accuracy in metal 3D printing include the printer’s calibration, material properties, process parameters (laser power, scan speed, layer thickness), and part orientation during printing.
- Tolerance: Tolerance defines the allowable variation in the dimensions of the printed part. Medical implants often have tight tolerance requirements to ensure proper fit and function. Advanced metal 3D printing systems, like those utilized by Metal3DP, are capable of achieving tight tolerances, minimizing the need for extensive post-machining.
- Отделка поверхности: The surface roughness of a bone plate can influence osseointegration and the risk of bacterial adhesion. Metal 3D-printed parts typically have a rougher surface finish compared to machined parts. However, this roughness can be controlled to some extent through process parameters and can even be beneficial for promoting bone ingrowth. Post-processing techniques like polishing or chemical etching can be employed to achieve specific surface finish requirements.
- Repeatability and Reproducibility: It is crucial that the 3D printing process can consistently produce parts with the desired level of accuracy and surface finish. This requires robust process control, validated parameters, and quality assurance measures. Metal3DP‘s commitment to accuracy and reliability ensures consistent production of high-quality implants.
- Metrology and Quality Control: Rigorous metrology and quality control procedures are essential to verify the dimensional accuracy and surface finish of 3D-printed bone plates. Techniques such as coordinate measuring machines (CMM), optical scanners, and surface profilometers are used to ensure that the implants meet the required specifications.
By carefully controlling the metal 3D printing process and implementing thorough quality control measures, it is possible to achieve the high levels of precision required for load-bearing bone plates, ensuring their safe and effective performance.
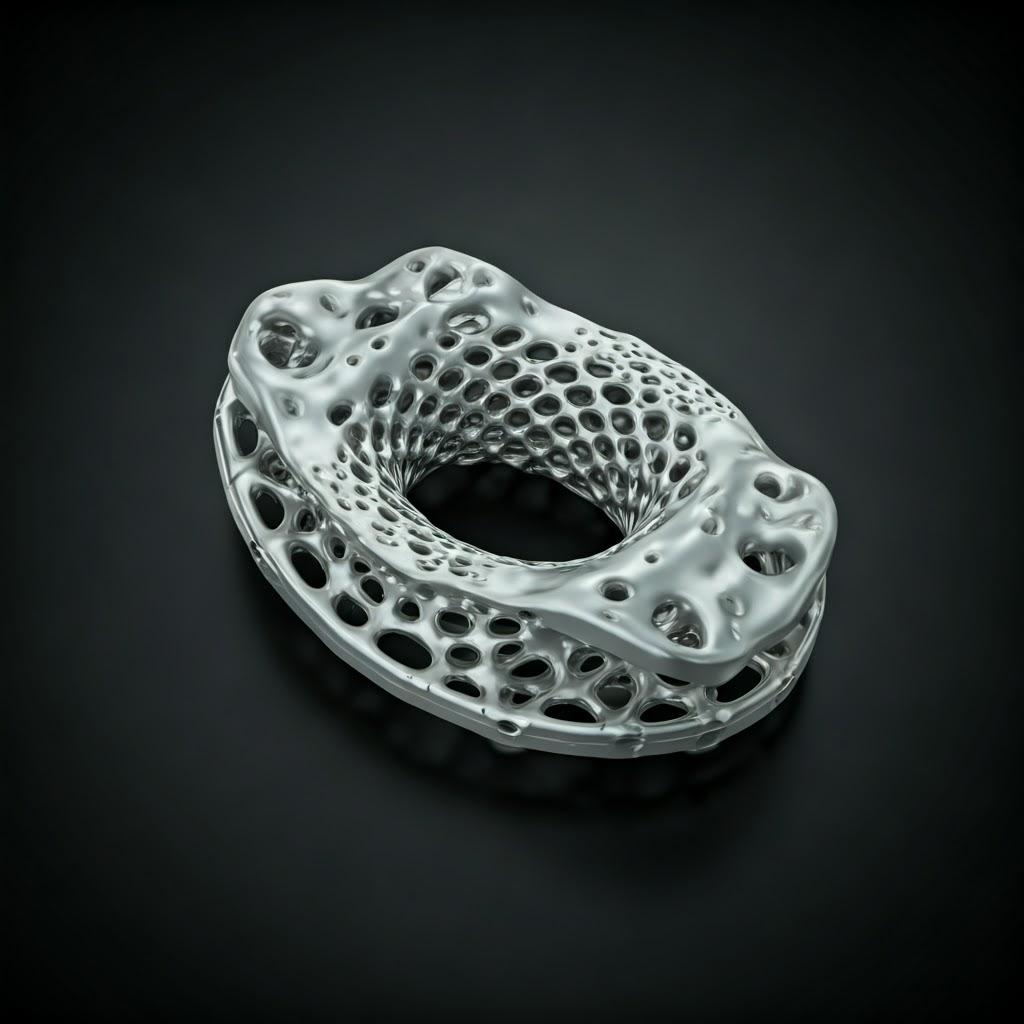
Streamlining Post-Processing for Bone Plates: Ensuring Biocompatibility and Longevity
While metal 3D printing offers significant advantages in creating complex geometries, post-processing steps are often necessary to achieve the final desired properties, surface finish, and biocompatibility of bone plates. Streamlining these processes is crucial for efficient and cost-effective manufacturing.
Common Post-Processing Requirements for 3D-Printed Bone Plates:
- Удаление порошка: After the printing process, residual metal powder needs to be carefully removed from the part’s surface and any internal channels or porous structures. Techniques such as brushing, vacuuming, and ultrasonic cleaning are commonly used.
- Stress Relief Heat Treatment: Metal 3D-printed parts can have residual stresses due to the rapid heating and cooling cycles during the build process. Stress relief heat treatment is often performed to reduce these stresses, improving the mechanical properties and preventing warping or cracking.
- Демонтаж опорной конструкции: Support structures are often necessary during metal 3D printing to prevent distortion and support overhanging features. These supports need to be carefully removed, typically through machining, grinding, or wire electrical discharge machining (EDM). The design of the supports should aim to minimize the effort required for removal and avoid damage to the part’s surface.
- Отделка поверхности: Depending on the application and design requirements, additional surface finishing steps may be necessary. This can include polishing, grinding, blasting, or chemical etching to achieve the desired surface roughness for osseointegration or to improve aesthetics.
- Cleaning and Sterilization: Before implantation, bone plates must undergo thorough cleaning and sterilization to remove any contaminants and ensure biocompatibility. Validated sterilization procedures, such as autoclaving or gamma irradiation, are employed.
- Покрытие (опционально): In some cases, coatings may be applied to the bone plate surface to enhance osseointegration (e.g., hydroxyapatite) or provide antimicrobial properties.
- Проверка качества: Final quality inspection, including dimensional verification and surface finish analysis, is crucial to ensure that the bone plate meets all specifications before it is approved for use.
Metal3DP understands the importance of efficient post-processing and can provide guidance and solutions to streamline these steps, ensuring the delivery of high-quality, biocompatible bone plates. Their expertise in the entire additive manufacturing workflow, from powder selection to post-processing considerations, makes them a valuable partner in the medical device industry.
Overcoming Challenges in 3D Printing Bone Plates: Ensuring Structural Integrity and Patient Safety
While metal 3D printing offers tremendous potential for creating custom bone plates, several challenges need to be addressed to ensure the structural integrity, biocompatibility, and patient safety of these critical medical devices.
Common Challenges and Mitigation Strategies in 3D Printing Bone Plates:
- Porosity and Density: Achieving fully dense parts with minimal porosity is crucial for load-bearing applications. Inadequate process parameters can lead to internal voids that weaken the implant. Optimization of printing parameters, such as laser power, scan speed, and powder bed density, is essential. Metal3DP‘s advanced SEBM technology is known for producing high-density parts.
- Warping and Distortion: Residual stresses during the printing process can cause warping or distortion of the bone plate, affecting its dimensional accuracy and fit. Optimizing part orientation, using support structures effectively, and implementing stress relief heat treatment can mitigate these issues.
- Surface Roughness and Finish: Achieving the desired surface finish for osseointegration and minimizing bacterial adhesion can be challenging with direct metal 3D printing. Careful selection of process parameters and the implementation of appropriate post-processing techniques are necessary.
- Biocompatibility Concerns: Ensuring the biocompatibility of the 3D-printed bone plate is paramount. This involves using biocompatible materials like Ti-6Al-4V ELI from reputable suppliers like Metal3DP, proper post-processing cleaning and sterilization, and potentially biocompatible coatings.
- Mechanical Property Variability: Variations in the printing process can lead to inconsistencies in the mechanical properties of the final part. Robust process control, validated parameters, and thorough testing are essential to ensure consistent and predictable performance.
- Соответствие нормативным требованиям: Medical devices are subject to stringent regulatory requirements. Manufacturers of 3D-printed bone plates must adhere to these regulations, including material traceability, process validation, and quality management systems. Partnering with experienced providers like Metal3DP, who understand these requirements, is crucial.
- Cost and Scalability: While the cost of metal 3D printing is decreasing, it can still be higher than traditional manufacturing methods for large production volumes. Optimizing designs for efficient printing and streamlining post-processing can help improve cost-effectiveness. Scalability for widespread clinical adoption is also an ongoing consideration.
By proactively addressing these challenges through careful design, optimized printing processes, rigorous quality control, and collaboration with experienced partners like Metal3DP, the full potential of metal 3D printing for custom bone plates can be realized, ultimately benefiting patients.
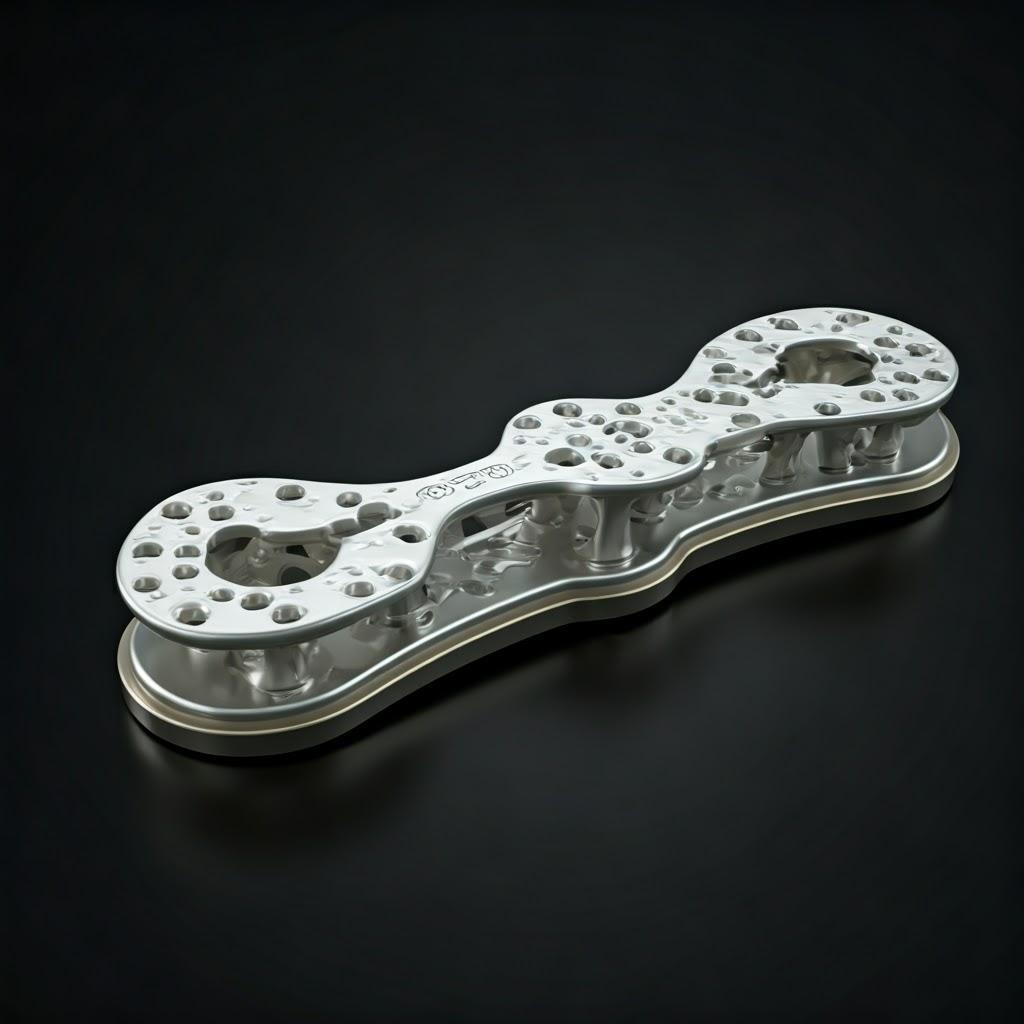
Selecting a Trusted Metal 3D Printing Partner for Medical Implants
Choosing the right metal 3D printing service provider is a critical decision for companies venturing into the production of custom bone plates. The partner’s expertise, capabilities, and commitment to quality will significantly impact the success and safety of the final medical device.
Key Factors to Consider When Selecting a Metal 3D Printing Partner:
- Industry Experience and Certifications: Look for a partner with a proven track record in manufacturing medical devices or similar high-precision components. Relevant certifications, such as ISO 13485 (Quality Management System for Medical Devices), are essential indicators of their commitment to quality and regulatory compliance. Metal3DP‘s decades of collective expertise in metal additive manufacturing make them a reliable choice.
- Material Capabilities: Ensure the partner has experience working with biocompatible materials suitable for bone plates, such as Ti-6Al-4V ELI. They should have robust processes for material handling, traceability, and quality control. Metal3DP manufactures a wide range of high-quality metal powders optimized for medical applications.
- Printing Technology and Equipment: The type of metal 3D printing technology used (e.g., SLM, DMLS, EBM) can influence the accuracy, density, and surface finish of the printed parts. The partner should possess advanced and well-maintained equipment capable of meeting the specific requirements of bone plate manufacturing. Metal3DP utilizes industry-leading SEBM printers known for their accuracy and reliability.
- Design Optimization Support: An experienced partner can offer valuable insights into designing bone plates specifically for additive manufacturing, optimizing for functionality, osseointegration, and cost-effectiveness. Collaboration during the design phase can lead to improved implant performance.
- Post-Processing Capabilities: Understand the partner’s in-house post-processing capabilities, including powder removal, heat treatment, surface finishing, cleaning, and sterilization. A comprehensive suite of services can streamline the manufacturing process.
- Quality Control and Metrology: Inquire about the partner’s quality control procedures, including dimensional inspection, material testing, and documentation. Robust quality assurance is crucial for medical implants.
- Regulatory Understanding: The partner should have a strong understanding of the regulatory landscape for medical devices in your target markets (e.g., FDA, CE marking). They should be able to provide the necessary documentation and support for regulatory submissions.
- Scalability and Production Capacity: Consider the partner’s ability to scale up production as your needs evolve. Ensure they have the capacity to meet your current and future demands.
- Communication and Collaboration: Effective communication and a collaborative approach are essential for a successful partnership. 1 Choose a partner who is responsive, transparent, and willing to work closely with you throughout the 2 project. 1. medium.com medium.com 2. remmed.com remmed.com
By carefully evaluating potential metal 3D printing partners based on these factors, you can select a provider like Metal3DP who can reliably produce high-quality, custom bone plates that meet the stringent demands of medical applications.
Understanding the Economics and Timelines of Custom 3D-Printed Bone Plates
The cost and lead time associated with manufacturing custom 3D-printed bone plates are important considerations for medical device companies and healthcare providers. While the initial investment might seem higher than off-the-shelf solutions, the long-term benefits and the potential for improved patient outcomes can provide significant value.
Key Factors Influencing Cost and Lead Time:
- Design Complexity and Customization: Highly complex and patient-specific designs may require more design effort and longer printing times, impacting the overall cost. However, the added clinical value of a perfectly tailored implant can outweigh these costs.
- Материальные затраты: The cost of the metal powder, such as Ti-6Al-4V ELI, is a significant factor. Material prices can vary depending on the grade, purity, and supplier. Metal3DP‘s in-house powder manufacturing capabilities may offer cost advantages.
- Время печати: The build time for a bone plate depends on its size, complexity, and the chosen printing technology. Larger or more intricate parts will typically take longer to print, affecting the lead time and potentially the cost.
- Требования к постобработке: The extent of post-processing required (e.g., support removal, heat treatment, surface finishing) will influence both the cost and the overall lead time. Streamlined post-processing workflows can help optimize these factors.
- Объем производства: The cost per part generally decreases as the production volume increases. For custom, patient-specific implants, the focus is often on the value of the individual device rather than mass production economics.
- Контроль качества и испытания: Rigorous quality control procedures and testing add to the overall cost but are essential for ensuring the safety and efficacy of medical implants.
- Regulatory Compliance Costs: Meeting regulatory requirements, including documentation and validation, can contribute to the overall cost. Partnering with a knowledgeable provider like Metal3DP can help navigate these complexities efficiently.
- Shipping and Logistics: The costs and timelines associated with shipping the final implants to the healthcare provider need to be considered.
While the upfront cost of a custom 3D-printed bone plate might be higher than a standard implant, the benefits of improved fit, potentially faster healing, and reduced complications can lead to long-term cost savings for the healthcare system and improved patient well-being. The lead time will depend on the complexity of the case and the efficiency of the manufacturing process. Collaborating closely with a partner like Metal3DP from the design stage can help optimize both the cost and the turnaround time for custom bone plates.
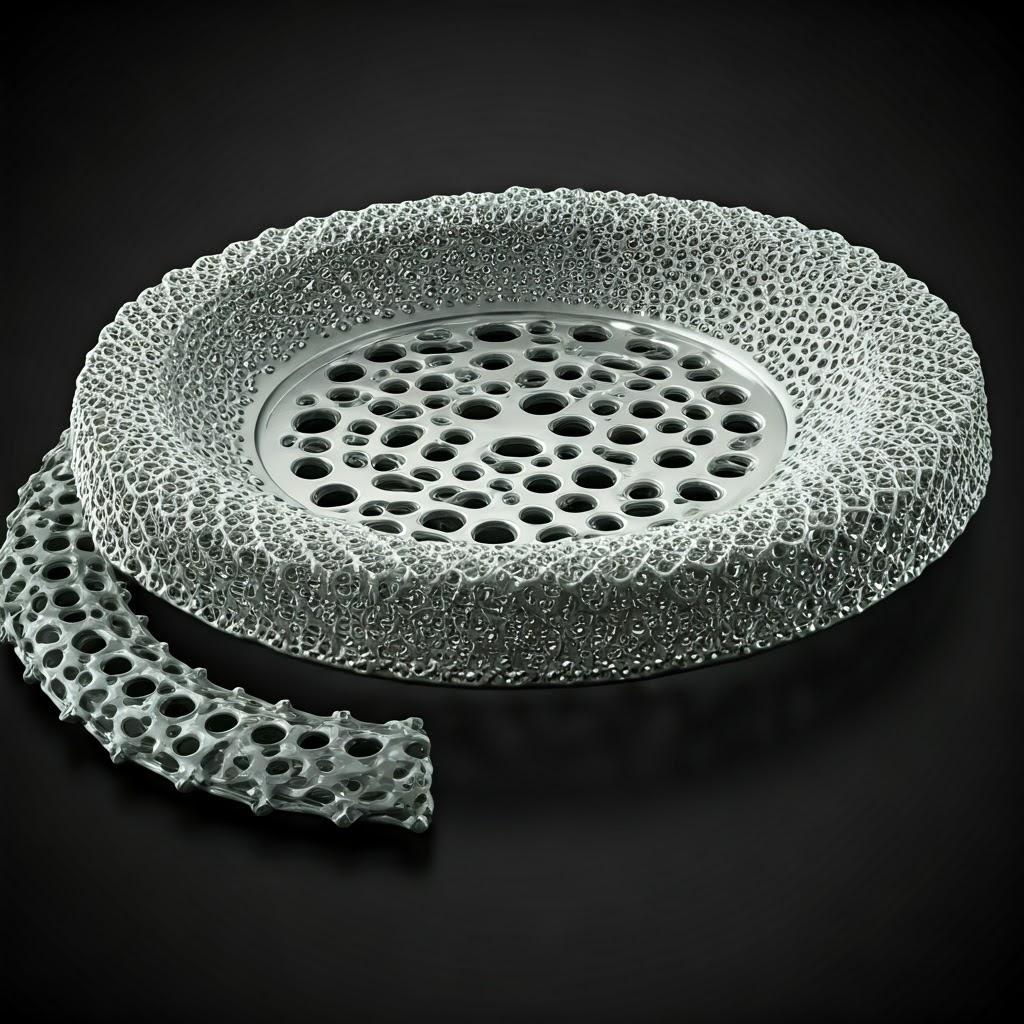
Часто задаваемые вопросы (FAQ)
- What is the typical lifespan of a 3D-printed titanium bone plate?
- When manufactured using high-quality materials like Ti-6Al-4V ELI and adhering to proper design and post-processing procedures, 3D-printed titanium bone plates are designed for long-term implantation. Titanium’s excellent biocompatibility and corrosion resistance contribute to the implant’s longevity, often lasting the lifetime of the patient, provided there are no unusual mechanical stresses or complications.
- Can 3D-printed bone plates be customized for pediatric patients?
- Absolutely. One of the significant advantages of metal 3D printing is the ability to create highly customized implants tailored to the unique anatomy of each patient, including pediatric cases. This is particularly beneficial in pediatric orthopedics where bone geometries are still developing and standard-sized implants may not be suitable. Imaging data from the child can be used to design and print a bone plate that precisely fits their specific needs.
- How does the cost of a custom 3D-printed bone plate compare to a standard off-the-shelf plate?
- The initial cost of a custom 3D-printed bone plate may be higher than a standard off-the-shelf plate due to the personalized design and manufacturing process. However, the potential benefits of a better fit, improved surgical outcomes, reduced risk of complications, and potentially faster healing times can provide significant long-term value and cost savings for the healthcare system. The specific cost will depend on the complexity of the design, the material used, and the post-processing requirements.
Conclusion – The Future of Orthopedics with Additive Manufacturing and Custom Implants
Metal 3D printing is heralding a new era in orthopedic care, offering the ability to create custom load-bearing bone plates that are precisely tailored to individual patient anatomy. This technology, combined with biocompatible materials like Ti-6Al-4V ELI and the expertise of companies like Metal3DP, holds the promise of revolutionizing fracture fixation, joint reconstruction, and other orthopedic procedures.
The advantages of patient-specific design, complex geometries, and enhanced osseointegration offered by metal 3D printing can lead to improved surgical precision, reduced recovery times, and better long-term outcomes for patients. As the technology continues to advance and become more accessible, we can expect to see an increasing adoption of custom 3D-printed implants in orthopedic practice.
Metal3DP is at the forefront of this transformative shift, providing cutting-edge metal additive manufacturing solutions, including advanced SEBM printers and high-quality metal powders, to empower medical device manufacturers and healthcare professionals. By embracing the possibilities of metal 3D printing, we can unlock a future where orthopedic implants are as unique as the patients they serve, ultimately leading to enhanced quality of life and improved healthcare outcomes. Contact Metal3DP today to explore how their capabilities can power your organization’s additive manufacturing goals in the medical field. You can also learn more about their comprehensive solutions on their домашняя страница.
Поделиться
MET3DP Technology Co., LTD - ведущий поставщик решений для аддитивного производства со штаб-квартирой в Циндао, Китай. Наша компания специализируется на производстве оборудования для 3D-печати и высокопроизводительных металлических порошков для промышленного применения.
Сделайте запрос, чтобы получить лучшую цену и индивидуальное решение для вашего бизнеса!
Похожие статьи
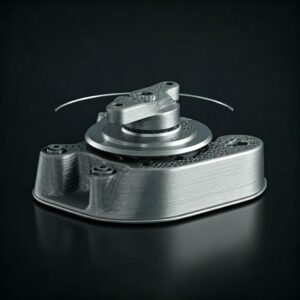
3D-печатные крепления для автомобильных радарных датчиков: Точность и производительность
Читать далее "О компании Met3DP
Последние обновления
Наш продукт
CONTACT US
Есть вопросы? Отправьте нам сообщение прямо сейчас! После получения Вашего сообщения мы всей командой выполним Ваш запрос.
Получите информацию о Metal3DP
Брошюра о продукции
Получить последние продукты и прайс-лист