High-Efficiency Cooling Channel Inserts for Industrial Applications
Оглавление
Введение
In demanding industrial environments, maintaining optimal operating temperatures is paramount for the longevity, efficiency, and reliability of critical machinery and tooling. Cooling channel inserts play a vital role in thermal management, facilitating the transfer of heat away from sensitive components. Traditionally manufactured cooling solutions often present limitations in terms of design complexity and material selection, hindering the achievement of peak performance. Metal 3D-печать, also known as metal additive manufacturing, offers a transformative approach to producing high-efficiency cooling channel inserts, enabling intricate geometries and tailored material properties that were previously unattainable. This blog post explores the advantages of utilizing metal 3D printing for creating these crucial components, the recommended materials, design considerations, and how partnering with a trusted supplier like Metal3DP can optimize your industrial cooling solutions.
What are Industrial Cooling Channel Inserts Used For?
Industrial cooling channel inserts are integral components designed to manage heat in a wide array of applications across various sectors. Their primary function is to facilitate the circulation of coolant fluids within machinery, molds, and other industrial equipment to dissipate heat generated during operation. This prevents overheating, which can lead to reduced efficiency, material degradation, and ultimately, equipment failure.
Here are some key use cases and industries where industrial cooling channel inserts are essential:
- Литье под давлением: In plastic and metal injection molding, cooling channels within the mold are critical for solidifying the injected material quickly and uniformly, reducing cycle times and improving part quality. Conformal cooling channels, achievable through metal 3D printing, follow the complex contours of the mold cavity more closely than conventionally drilled channels, leading to more efficient heat extraction.
- Литье под давлением: Similar to injection molding, die casting processes generate significant heat. Efficient cooling channel inserts are necessary to maintain the die temperature, ensuring consistent casting quality and extending die life.
- Machining Tools: High-speed machining operations generate substantial frictional heat. Integrating cooling channels directly into cutting tools or tool holders via metal 3D printing allows for precise temperature control at the cutting interface, enhancing tool life, improving surface finish, and increasing material removal rates.
- Power Electronics: Electronic components, particularly high-power devices, generate considerable heat. Custom-designed cooling channel inserts made through metal 3D printing can provide tailored cooling solutions for complex heat sink geometries, ensuring reliable operation and preventing thermal runaway.
- Aerospace and Automotive: In these industries, lightweighting and high performance are critical. Metal 3D printed cooling channel inserts can be optimized for both thermal efficiency and weight reduction in applications such as engine components, heat exchangers, and electronic control units.
- Медицинское оборудование: Certain medical devices and diagnostic equipment require precise temperature control. Metal 3D printing enables the creation of intricate cooling channels within these devices, ensuring accurate and reliable operation.
By effectively managing heat, industrial cooling channel inserts contribute significantly to increased productivity, improved product quality, reduced downtime, and extended equipment lifespan across a multitude of industrial processes.
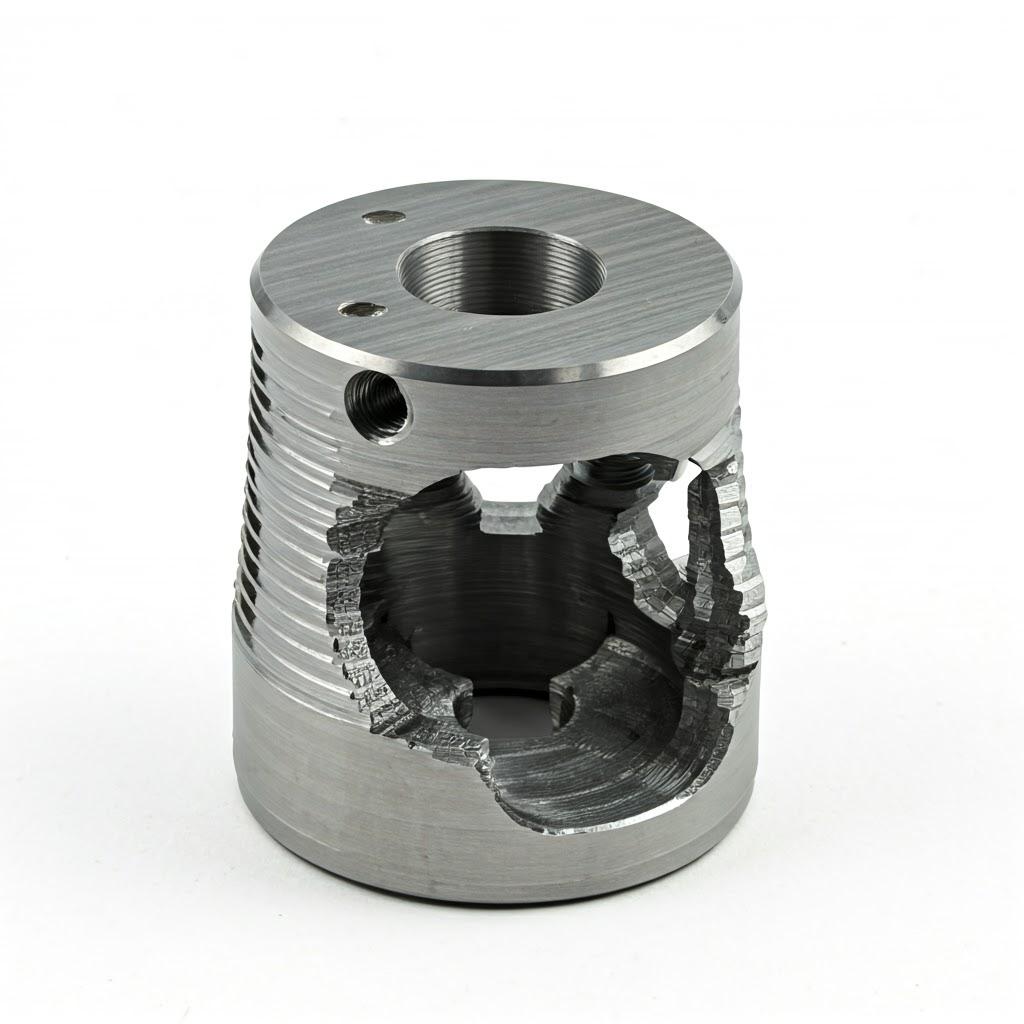
Why Use Metal 3D Printing for Industrial Cooling Channel Inserts?
Opting for metal 3D printing to manufacture industrial cooling channel inserts offers a compelling array of advantages over traditional manufacturing methods such as drilling, machining, or casting. These benefits directly address the critical performance requirements and design complexities often encountered in industrial thermal management.
- Свобода и сложность дизайна: Metal 3D printing allows for the creation of highly complex internal geometries, including conformal cooling channels that closely follow the contours of the part. This is virtually impossible to achieve with conventional methods. Conformal cooling ensures more uniform and efficient heat extraction, leading to faster cycle times and improved part quality, particularly in molding and casting applications.
- Оптимизация материалов: Metal 3D printing provides the flexibility to utilize advanced materials tailored for specific thermal conductivity and strength requirements. Alloys like CuCrZr offer excellent thermal conductivity and high strength, while AlSi10Mg provides a good balance of thermal properties and lightweighting potential. This material selection can be optimized for the specific application demands.
- Быстрое создание прототипов и итерации: Additive manufacturing significantly accelerates the design and development process. Engineers can quickly iterate on cooling channel designs, print prototypes, and test their performance, leading to faster optimization and reduced time-to-market. This agility is crucial in rapidly evolving industrial sectors.
- Кастомизация и производство по требованию: Metal 3D printing enables the production of customized cooling channel inserts tailored to specific equipment or application needs without the need for expensive tooling. This is particularly advantageous for low-volume production, spare parts, or highly specialized machinery.
- Integration of Features: Metal 3D printing allows for the integration of multiple functionalities into a single component. For example, cooling channels can be combined with internal support structures or mounting features, reducing the number of parts and assembly steps.
- Weight Optimization: For applications where weight is a critical factor, such as in aerospace and automotive, metal 3D printing enables the creation of lightweight cooling channel inserts with optimized internal lattices or thin-walled structures while maintaining structural integrity and thermal performance.
- Сокращение отходов материалов: Compared to subtractive manufacturing processes like machining, metal 3D printing generates significantly less material waste as material is only deposited where needed. This leads to cost savings and a more sustainable manufacturing approach.
- Enhanced Performance and Efficiency: The ability to create complex, conformal cooling channels and utilize optimized materials directly translates to improved thermal management efficiency, leading to increased productivity, better product quality, and extended equipment lifespan.
By leveraging the capabilities of metal 3D printing, businesses can overcome the limitations of traditional manufacturing and achieve superior performance in their industrial cooling solutions. Companies like Metal3DP are at the forefront of this technology, offering advanced printing equipment and high-performance metal powders to enable the production of these critical components.
Recommended Materials and Why They Matter
The selection of the appropriate metal powder is crucial for achieving the desired performance characteristics of industrial cooling channel inserts. Factors such as thermal conductivity, strength, corrosion resistance, and biocompatibility (for medical applications) must be carefully considered based on the specific application requirements. Metal3DP offers a range of high-quality metal powders optimized for additive manufacturing, including the following recommended materials for cooling channel inserts:
CuCrZr (Copper-Chromium-Zirconium)
- Основные свойства: CuCrZr is a copper alloy renowned for its exceptional thermal conductivity (typically around 350-400 W/m·K), high strength, excellent wear resistance, and good corrosion resistance. The addition of chromium and zirconium enhances its strength and hardness without significantly compromising its thermal conductivity.
- Why it Matters for Cooling Channel Inserts: The superior thermal conductivity of CuCrZr allows for rapid and efficient heat transfer, making it ideal for applications where effective cooling is paramount, such as in high-cycle injection molds and critical components in power electronics. Its high strength ensures the durability of the cooling channels under demanding operating conditions.
- Приложения: Injection molding tools, die casting molds, heat sinks for high-power electronics, welding electrodes.
- Metal3DP Advantage: Metal3DP’s advanced powder making system ensures the production of high-sphericity CuCrZr powder with excellent flowability, crucial for achieving dense and homogeneous parts with optimal thermal performance in our industry-leading print volume and accuracy printers.
AlSi10Mg (Aluminum-Silicon-Magnesium)
- Основные свойства: AlSi10Mg is a widely used aluminum alloy in additive manufacturing known for its good thermal conductivity (around 120-160 W/m·K), high strength-to-weight ratio, and good corrosion resistance. It offers a significant weight reduction compared to copper alloys while still providing effective heat dissipation.
- Why it Matters for Cooling Channel Inserts: For applications where lightweighting is critical, such as in aerospace and automotive components, AlSi10Mg provides a viable alternative to copper alloys. Its good thermal conductivity and mechanical properties make it suitable for cooling channels in applications where weight savings contribute to overall efficiency.
- Приложения: Automotive cooling systems, aerospace heat exchangers, lightweight structural components with integrated cooling, housings for electronic devices.
- Metal3DP Advantage: Metal3DP’s high-quality AlSi10Mg powder is optimized for laser powder bed fusion (LPBF) processes, delivering dense, high-quality metal parts with superior mechanical properties. Our expertise in application development services can help customers leverage the benefits of AlSi10Mg for their specific cooling channel insert requirements.
The choice between CuCrZr and AlSi10Mg will depend on the specific demands of the application. For maximum thermal transfer efficiency, CuCrZr is the preferred choice. However, if weight is a critical constraint, AlSi10Mg offers a compelling alternative with good thermal performance. Metal3DP’s comprehensive solutions, spanning advanced metal powders and application development services, empower customers to select and utilize the optimal material for their industrial cooling channel insert needs, accelerating digital manufacturing transformations. Sources and related content
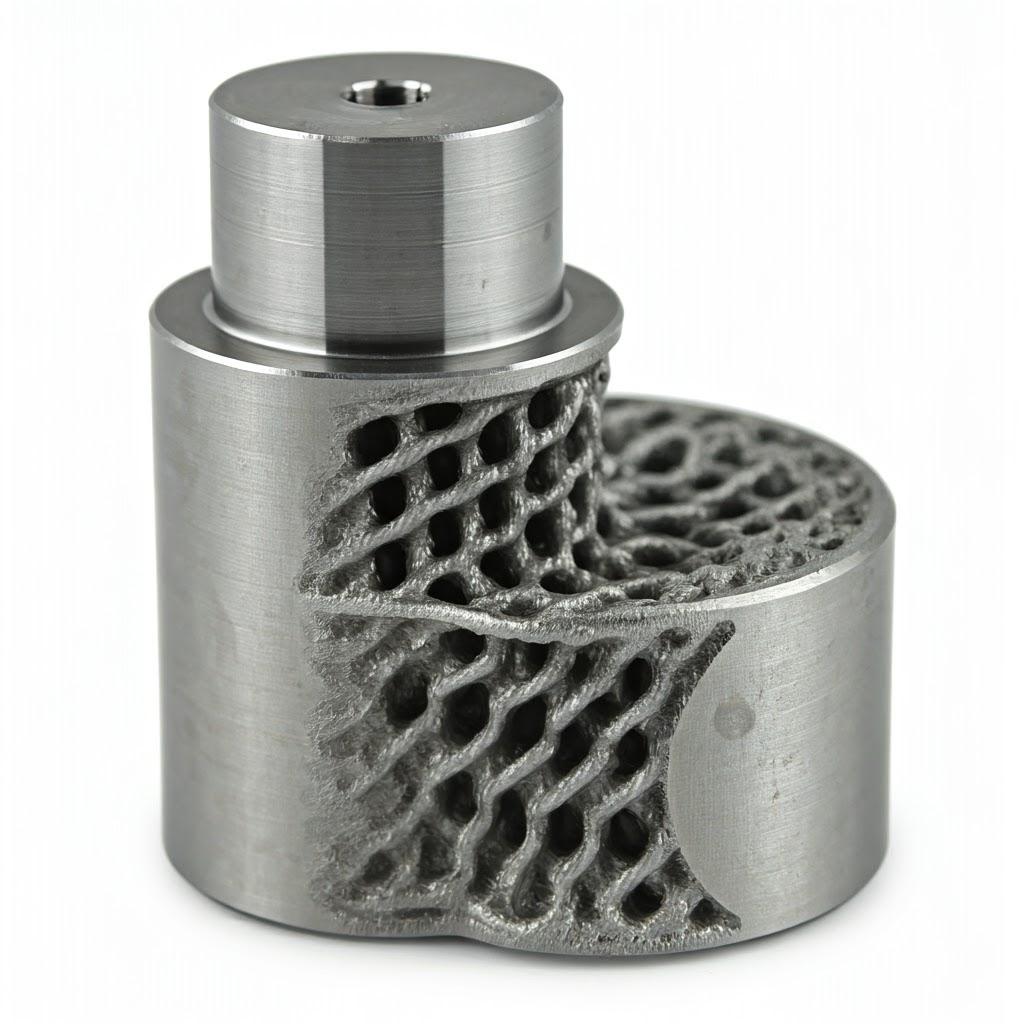
Design Considerations for Additive Manufacturing of Cooling Channel Inserts
Designing industrial cooling channel inserts for metal 3D printing requires a different mindset compared to designing for traditional manufacturing methods. To fully leverage the capabilities of additive manufacturing and achieve optimal performance, several key design considerations must be taken into account:
- Conformal Cooling Channel Design: One of the primary advantages of metal 3D printing is the ability to create conformal cooling channels that closely follow the contours of the part. This ensures more uniform heat extraction compared to straight, drilled channels. When designing conformal channels, consider:
- Distance from Heat Source: Maintain a consistent and optimal distance between the cooling channel and the heat-generating areas for efficient heat transfer.
- Channel Shape and Size: Optimize the cross-sectional shape and size of the channels to maximize coolant flow and heat exchange surface area while considering pressure drop. Complex shapes like teardrop or oval channels can offer advantages over circular channels in certain applications.
- Плавные переходы: Design smooth bends and transitions in the cooling channels to minimize flow resistance and prevent turbulence, which can reduce cooling efficiency.
- Толщина стенок: The wall thickness of the cooling channels is critical for both thermal transfer and structural integrity.
- Теплопроводность: Thinner walls generally facilitate better heat transfer. However, there needs to be a balance to ensure sufficient strength to withstand coolant pressure and operational stresses.
- Minimum Printable Thickness: Consider the minimum feature size and wall thickness achievable with the chosen metal 3D printing process and material. Metal3DP’s printers deliver industry-leading accuracy, enabling the creation of fine features and thin walls with high precision.
- Поддерживающие структуры: Depending on the complexity of the cooling channel design and the build orientation, support structures may be necessary during the printing process to prevent collapse or distortion.
- Minimize Support: Design parts with self-supporting angles whenever possible to reduce the need for support structures, which can add to post-processing time and material waste.
- Strategic Support Placement: If supports are required, strategically place them in areas that will have minimal impact on the functional surfaces and are easily removable.
- Surface Finish of Internal Channels: The surface finish of the internal cooling channels can affect coolant flow and heat transfer efficiency.
- Optimize Build Orientation: Orient the part during printing to minimize the step effect on critical internal surfaces.
- Постобработка: Consider post-processing techniques like chemical etching or abrasive flow machining to improve the surface finish of internal channels if required for demanding applications.
- Integration of Inlet and Outlet Ports: Design the inlet and outlet ports for the coolant to ensure proper connection and flow.
- Threaded Connections: Integrate threads directly into the design for secure and leak-proof connections.
- Manifold Design: For complex cooling systems, consider designing integrated manifolds to distribute coolant flow efficiently to multiple channels.
- Topology Optimization: For applications where weight is a significant concern, topology optimization techniques can be employed to identify the most efficient material distribution for both structural integrity and thermal performance. This can lead to lightweight cooling channel inserts with optimized heat transfer capabilities.
- Consideration of the Build Process: Understanding the specific characteristics of the chosen metal 3D printing process, such as Selective Electron Beam Melting (SEBM) or Laser Powder Bed Fusion (LPBF), is crucial for designing printable parts. Metal3DP offers both SEBM printers and a wide range of high-quality metal powders optimized for these processes.
By carefully considering these design factors, engineers can leverage the unique capabilities of metal 3D printing to create high-efficiency cooling channel inserts that outperform conventionally manufactured components. Metal3DP’s expertise in metal additive manufacturing can provide valuable guidance in optimizing designs for manufacturability and performance.
Tolerance, Surface Finish, and Dimensional Accuracy of 3D Printed Cooling Channel Inserts
Achieving the required tolerance, surface finish, and dimensional accuracy is critical for the proper functioning and integration of industrial cooling channel inserts. Metal 3D printing technologies have advanced significantly in recent years, offering increasingly precise and reliable manufacturing capabilities. However, it’s important to understand the factors that influence these aspects and what can be realistically achieved.
- Точность размеров: The dimensional accuracy achievable with metal 3D printing depends on several factors, including the chosen printing technology (e.g., LPBF, SEBM), the material being used, the part geometry, and the build parameters.
- Machine Accuracy: Metal3DP’s printers are engineered to deliver industry-leading accuracy, ensuring that printed parts closely match the intended design dimensions.
- Material Shrinkage: During the solidification process, metal powders undergo shrinkage. The extent of shrinkage varies depending on the material and process. Experienced service providers like Metal3DP account for this shrinkage in the design and build preparation stages.
- Build Orientation: The orientation of the part during printing can influence dimensional accuracy, particularly for features oriented in the Z-axis (build direction).
- Tolerance: Tolerances specify the allowable variation in a dimension. The achievable tolerances in metal 3D printing are generally tighter than those of traditional casting methods but may not always match the precision of CNC machining without post-processing.
- Standard Tolerances: Typical tolerances for metal 3D printed parts range from ±0.1 to ±0.5 mm, depending on the size and complexity of the feature. Tighter tolerances can be achieved in specific areas through careful process control and post-processing.
- Critical Dimensions: Identify critical dimensions that require tighter tolerances for proper fit and function of the cooling channel inserts. These areas may necessitate post-machining.
- Отделка поверхности: The surface finish of metal 3D printed parts is typically rougher than that achieved by machining or polishing. It is characterized by the partially melted powder particles on the surface.
- Параметры процесса: The laser or electron beam power, scan speed, and layer thickness in the printing process influence the surface roughness. Metal3DP optimizes these parameters to achieve the best possible as-built surface finish.
- Build Orientation: Surfaces oriented at an angle to the build platform tend to have a rougher surface finish due to the stepped nature of the layer-by-layer printing process.
- Post-Processing for Surface Finish Improvement: Several post-processing techniques can be employed to improve the surface finish of 3D printed cooling channel inserts:
- Media Blasting: Removes loosely adhered powder particles and can provide a more uniform surface texture.
- Полировка: Mechanical or chemical polishing can significantly reduce surface roughness for applications requiring smooth internal channels to minimize flow resistance or external surfaces for better sealing.
- Chemical Etching: Can selectively remove surface layers to improve smoothness and reveal the underlying material microstructure.
- Abrasive Flow Machining (AFM): Involves forcing an abrasive-laden fluid through the cooling channels to smooth internal surfaces, which is particularly important for optimizing coolant flow.
Understanding the inherent tolerances and surface finish characteristics of metal 3D printing is crucial for designing functional industrial cooling channel inserts. For applications requiring very tight tolerances or smooth surface finishes, incorporating post-processing steps into the manufacturing workflow is often necessary. Metal3DP’s comprehensive service offerings include access to various post-processing techniques to meet specific application requirements.
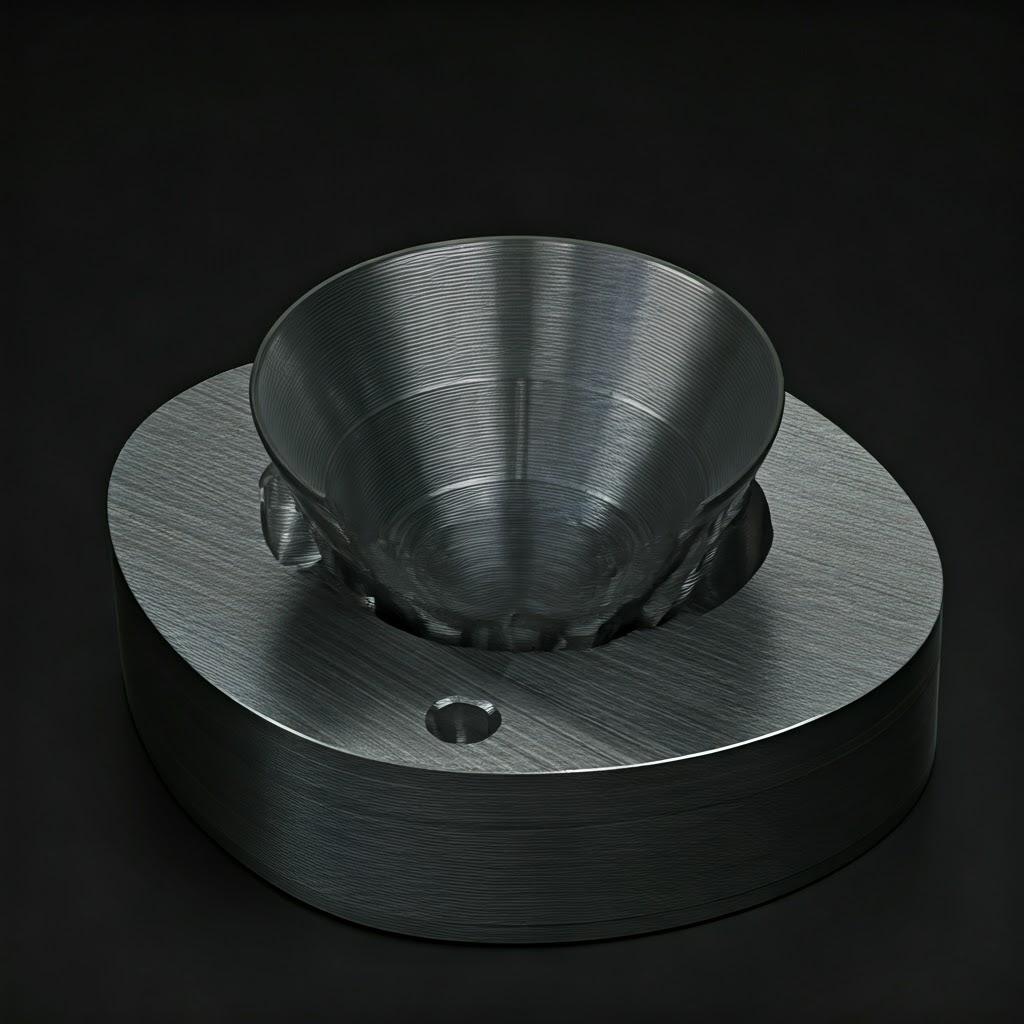
Post-Processing Requirements for Metal 3D Printed Cooling Channel Inserts
While metal 3D printing offers significant advantages in creating complex geometries for industrial cooling channel inserts, post-processing steps are often required to achieve the final desired properties, surface finish, and dimensional accuracy. The specific post-processing needs will depend on the application requirements and the chosen printing process and material.
- Удаление порошка: After the printing process is complete, unbound metal powder needs to be carefully removed from the build chamber and, more importantly, from the internal cooling channels.
- Brushing and Blowing: External powder can typically be removed with brushes and compressed air.
- Vibration and Ultrasonic Cleaning: For more intricate internal channels, vibration tables and ultrasonic cleaning baths can be used to dislodge trapped powder.
- Specialized Tools: For complex internal geometries, specialized tools and techniques may be required to ensure complete powder removal, which is crucial for proper coolant flow.
- Удаление опоры: If support structures were used during the printing process, they need to be removed.
- Удаление вручную: Supports can often be manually broken off or cut away using hand tools.
- Обработка: For more robust supports or when a clean break is required, CNC machining or wire EDM (Electrical Discharge Machining) may be necessary.
- Soluble Supports: Some metal 3D printing processes utilize soluble support materials that can be dissolved in a chemical bath, simplifying removal, especially for complex internal features.
- Термообработка: Heat treatment is often a critical step to achieve the desired mechanical properties of the 3D printed metal part.
- Снятие стресса: Reduces internal stresses that may have built up during the printing process.
- Annealing: Softens the material and improves ductility.
- Hardening and Tempering: Increases the strength and hardness of the material.
- HIP (Hot Isostatic Pressing): Involves applying high pressure and temperature simultaneously to reduce porosity and improve the density and mechanical properties of the printed part. Metal3DP leverages its expertise to determine the optimal heat treatment cycles for various metal powders to ensure superior mechanical performance.
- Отделка поверхности: As discussed earlier, post-processing techniques can be employed to improve the surface finish of the cooling channel inserts.
- Media Blasting: Provides a uniform matte finish and removes residual powder.
- Polishing (Mechanical and Chemical): Reduces surface roughness for improved aesthetics, sealing, or fluid flow.
- Abrasive Flow Machining (AFM): Specifically targets the internal surfaces of cooling channels to improve smoothness and optimize coolant flow.
- CNC Machining: For critical dimensions and tight tolerances that cannot be achieved directly through 3D printing, CNC machining can be used as a secondary operation. This is particularly relevant for interface surfaces, mounting features, or sealing areas.
- Покрытие: Depending on the application environment, coatings may be applied to enhance corrosion resistance, wear resistance, or other specific properties.
- PVD (Physical Vapor Deposition) and CVD (Chemical Vapor Deposition): Thin-film coatings for wear and corrosion protection.
- Гальваническое покрытие: Applying a layer of another metal for improved corrosion resistance or conductivity.
Understanding the necessary post-processing steps and having access to the required equipment and expertise are crucial for realizing the full potential of metal 3D printed industrial cooling channel inserts. Metal3DP offers comprehensive solutions that include not only advanced printing capabilities but also a range of post-processing services to meet diverse industrial needs. Our application development services can guide you through the entire process, from design optimization to final part finishing.
Common Challenges and How to Avoid Them in Metal 3D Printing of Cooling Channel Inserts
While metal 3D printing offers numerous advantages for creating industrial cooling channel inserts, certain challenges can arise during the design and manufacturing process. Understanding these potential issues and implementing preventative measures is crucial for achieving high-quality, functional parts.
- Warping and Distortion: Thermal stresses during the printing process can lead to warping or distortion of the part, particularly for complex geometries or thin-walled structures.
- Optimization of Build Orientation: Orienting the part strategically on the build platform can minimize the build-up of thermal stresses in critical areas.
- Support Structure Design: Properly designed support structures can help anchor the part and prevent distortion during printing.
- Оптимизация параметров процесса: Fine-tuning printing parameters such as laser power, scan speed, and layer thickness can reduce thermal gradients and minimize warping. Metal3DP’s expertise in process parameter optimization is crucial in mitigating these issues.
- Пористость: Internal voids or pores within the printed part can compromise its mechanical strength, thermal conductivity, and leak tightness, which is particularly critical for cooling channels.
- Material Selection and Preparation: Using high-quality metal powders with good flowability and packing density is essential. Metal3DP’s advanced powder making system ensures the production of such powders.
- Оптимизация параметров процесса: Optimizing laser or electron beam power and scan strategies helps to fully melt the powder particles and minimize porosity.
- Inert Atmosphere Control: Maintaining a pure inert atmosphere during printing prevents oxidation and contamination, which can contribute to porosity.
- HIP (Hot Isostatic Pressing): As mentioned earlier, HIP is a post-processing step that effectively reduces porosity and enhances the density of 3D printed metal parts.
- Support Removal Challenges: Removing support structures from intricate internal cooling channels can be difficult and may damage the part if not done carefully.
- Design for Minimal Supports: Designing self-supporting geometries whenever possible reduces the need for extensive support structures.
- Strategic Support Placement: Placing supports in easily accessible areas minimizes removal challenges.
- Soluble Supports: Utilizing soluble support materials simplifies the removal process for complex internal features.
- Surface Roughness of Internal Channels: A rough internal surface finish can impede coolant flow and reduce heat transfer efficiency.
- Build Orientation Optimization: Orienting the part to minimize stepped surfaces within the channels can help.
- Abrasive Flow Machining (AFM): Employing AFM as a post-processing step is highly effective in smoothing internal channel surfaces.
- Dimensional Inaccuracies: Deviations from the intended design dimensions can lead to fitment issues and compromised performance.
- Accurate Machine Calibration: Ensuring that the 3D printer is properly calibrated is crucial for dimensional accuracy. Metal3DP’s printers undergo rigorous calibration procedures.
- Material Shrinkage Compensation: Accounting for material shrinkage during the design and build preparation stages is essential.
- Post-Machining for Critical Dimensions: For features requiring very tight tolerances, incorporating CNC machining as a secondary operation may be necessary.
- Leakage in Cooling Channels: Porosity or cracks in the walls of the cooling channels can lead to coolant leakage, compromising the functionality of the insert.
- Optimized Printing Parameters: Ensuring complete melting and fusion of powder particles through optimized printing parameters minimizes the risk of porosity and cracks.
- Неразрушающий контроль (NDT): Techniques like pressure testing or dye penetrant inspection can be used to identify leaks in the printed parts.
By understanding these common challenges and implementing appropriate design strategies, process controls, and post-processing techniques, it is possible to consistently produce high-quality industrial cooling channel inserts using metal 3D printing. Partnering with an experienced provider like Metal3DP, which possesses deep expertise in metal additive manufacturing and offers comprehensive solutions, can significantly mitigate these risks and ensure successful outcomes.
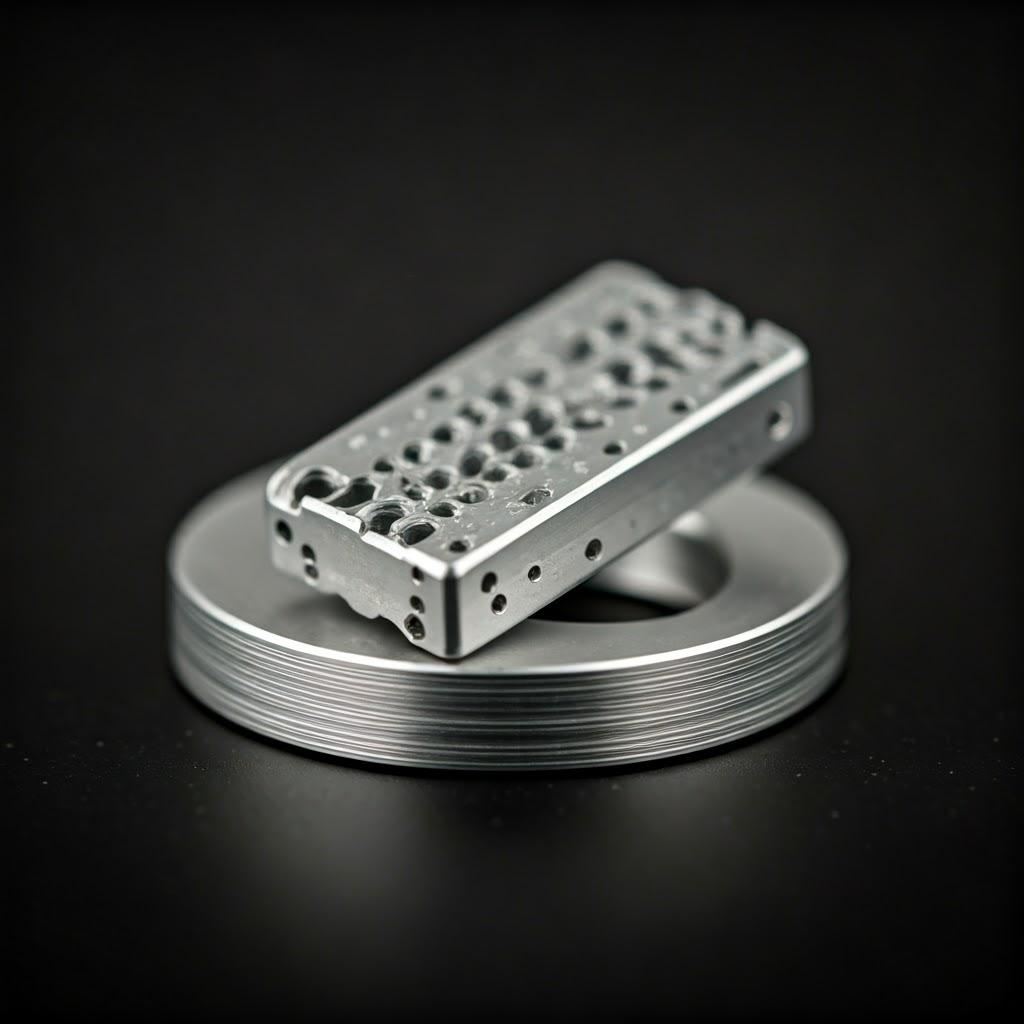
How to Choose the Right Metal 3D Printing Service Provider for Cooling Channel Inserts
Selecting the right metal 3D printing service provider is crucial for obtaining high-quality industrial cooling channel inserts that meet your specific application requirements. Consider the following factors when evaluating potential suppliers:
- Material Capabilities: Ensure the provider offers the recommended metal powders, such as CuCrZr and AlSi10Mg, and has experience processing these materials for thermal management applications. Metal3DP manufactures a wide range of high-quality metal powders optimized for laser and electron beam powder bed fusion, including innovative alloys.
- Printing Technology and Equipment: Inquire about the types of metal 3D printing technologies they utilize (e.g., LPBF, SEBM) and the capabilities of their equipment in terms of build volume, accuracy, and resolution. Metal3DP’s printers deliver industry-leading print volume, accuracy, and reliability.
- Design Optimization Expertise: A good service provider should offer support in optimizing your cooling channel insert designs for additive manufacturing, taking into account factors like conformal cooling, support structures, and material selection. Metal3DP provides comprehensive solutions spanning SEBM printers, advanced metal powders, and application development services. 1 1. About Us – Metal3DP – 3D Printing Metal Powder Hub met3dp.sg
- Post-Processing Services: Determine if the provider offers the necessary post-processing services to meet your requirements, such as powder removal, support removal, heat treatment, surface finishing (including AFM for internal channels), and CNC machining.
- Quality Control and Certifications: Ask about their quality control procedures and any relevant certifications they hold (e.g., ISO 9001, AS9100 for aerospace). Robust quality management systems ensure consistent and reliable part quality.
- Industry Experience and Expertise: Look for a provider with a proven track record in manufacturing parts for your specific industry (e.g., aerospace, automotive, medical). Experience indicates a deeper understanding of industry-specific requirements and challenges. With decades of collective expertise in metal additive manufacturing, Metal3DP partners with organizations to implement 3D printing and accelerate digital manufacturing transformations.
- Lead Times and Production Capacity: Discuss their typical lead times for similar projects and their production capacity to ensure they can meet your volume requirements.
- Communication and Customer Support: A responsive and communicative provider who understands your needs and offers excellent customer support is essential for a smooth and successful collaboration. Contact Metal3DP to explore how its capabilities can power your organization’s additive manufacturing goals.
- Pricing and Value: While cost is a factor, focus on the overall value proposition, including the quality of the parts, the expertise of the provider, and the range of services offered.
- References and Case Studies: Request references or case studies of similar projects they have completed to assess their capabilities and customer satisfaction.
By carefully evaluating potential metal 3D printing service providers based on these criteria, you can choose a partner that will deliver high-quality industrial cooling channel inserts tailored to your specific needs, ensuring optimal performance and efficiency for your industrial applications.
Cost Factors and Lead Time for Metal 3D Printed Cooling Channel Inserts
Understanding the cost drivers and typical lead times associated with metal 3D printing of industrial cooling channel inserts is essential for project planning and budgeting. These factors can vary depending on several parameters:
- Стоимость материала: The cost of the metal powder is a significant factor. Alloys like CuCrZr can be more expensive than AlSi10Mg. The quantity of material used for the part and any support structures will also influence the overall material cost. Metal3DP manufactures a wide range of high-quality metal powders, offering cost-effective solutions for various applications.
- Время сборки: The time it takes to print the cooling channel inserts depends on factors such as the part volume, complexity, layer height, and the number of parts being printed simultaneously in a single build. Longer build times translate to higher machine operating costs.
- Machine Operating Costs: These costs include energy consumption, maintenance, and depreciation of the 3D printing equipment.
- Расходы на постобработку: The extent of post-processing required will significantly impact the overall
post-processing costs. Simple powder and support removal will be less expensive than extensive machining, polishing, or specialized treatments like HIP or AFM.
- Расходы на оплату труда: This includes the time and expertise of engineers, technicians, and machinists involved in design optimization, print setup, operation, post-processing, and quality control.
- Complexity of Design: More intricate designs with complex internal channels or thin walls may require more sophisticated printing strategies and post-processing, leading to higher costs.
- Объем производства: While metal 3D printing is advantageous for low-to-medium volume production and customization, higher volumes may benefit from economies of scale. However, unlike traditional manufacturing, there are typically no tooling costs associated with metal 3D printing, which can be a significant advantage for smaller production runs.
- Quality Assurance Costs: Stringent quality control procedures and testing can add to the overall cost but are essential for ensuring the reliability and performance of critical components like cooling channel inserts.
Typical Lead Times:
Lead times for metal 3D printed industrial cooling channel inserts can vary depending on the complexity of the part, the chosen material, the required post-processing, and the service provider’s current workload. Generally, the process involves the following stages:
- Design and Optimization (1-5 days): This includes finalizing the 3D model and optimizing it for metal 3D printing. Collaboration with experienced providers like Metal3DP can help expedite this stage.
- Build Preparation and Printing (1-10 days): This involves preparing the build file, setting up the printer, and the actual printing time, which depends on the part size and complexity.
- Post-Processing (1-14 days): This can include powder removal, support removal, heat treatment (which can take several days), surface finishing, and machining. The duration depends on the specific requirements.
- Quality Control and Inspection (1-3 days): Thorough inspection to ensure the parts meet the required specifications.
- Shipping (1-5 days): Depending on the location and shipping method.
Therefore, the total lead time for metal 3D printed cooling channel inserts can range from a few days to several weeks. It’s crucial to discuss lead times in detail with your chosen service provider, such as Metal3DP, to ensure they align with your project timelines. Factors like expedited printing or specific post-processing requirements can influence the final lead time and cost. Metal3DP is committed to providing efficient and timely services while maintaining the highest standards of quality for your metal 3D printing needs.
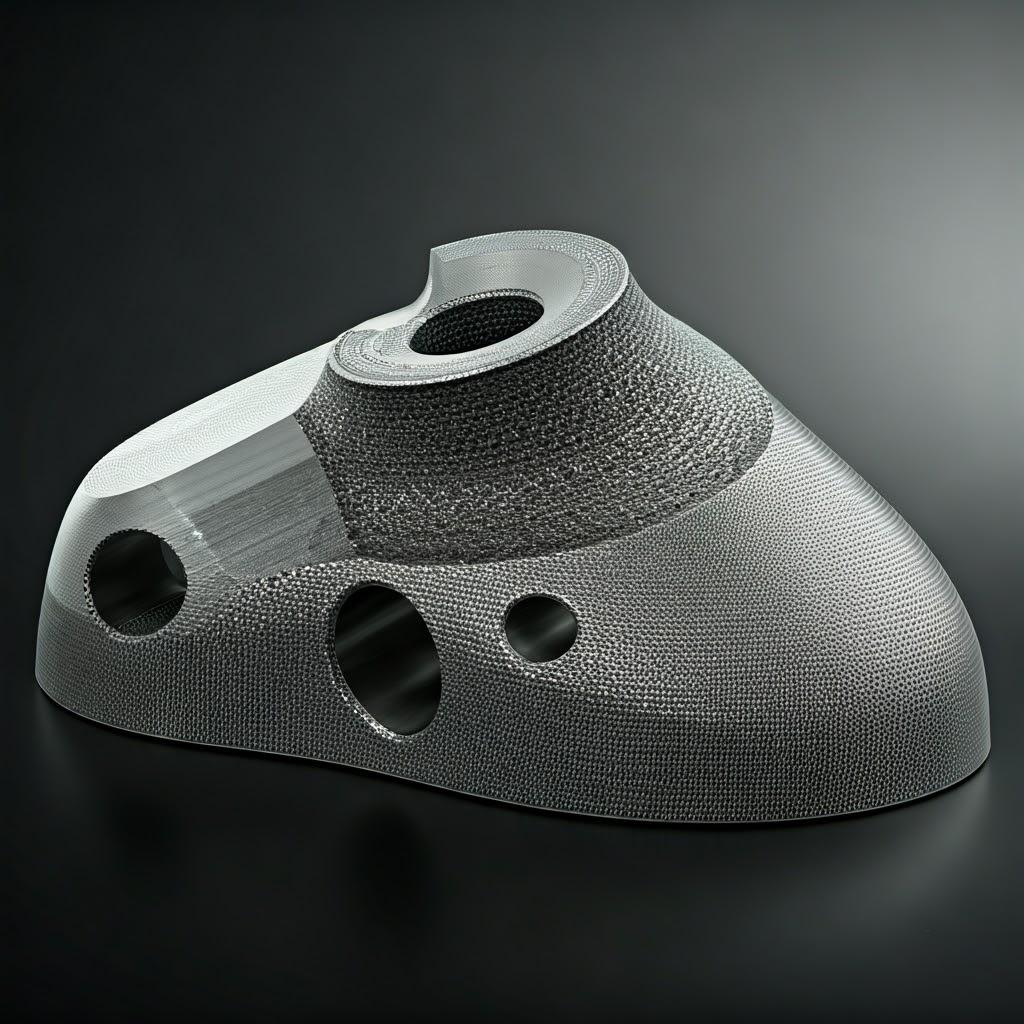
Часто задаваемые вопросы (FAQ)
- What are the main benefits of using metal 3D printing for cooling channel inserts compared to traditional methods? Metal 3D printing enables the creation of complex, conformal cooling channels for more efficient heat transfer, allows for material optimization (e.g., using CuCrZr for high thermal conductivity), facilitates rapid prototyping and customization, and can integrate multiple features into a single part. Traditional methods like drilling are limited in the complexity of channel designs.
- Which metal powder is best for my cooling channel insert application? The optimal material depends on the specific requirements. CuCrZr offers excellent thermal conductivity and high strength, ideal for demanding applications like injection molding. AlSi10Mg provides a good balance of thermal properties and lightweighting potential for applications like aerospace and automotive. Metal3DP offers a range of high-quality metal powders and can help you select the best material for your needs.
- What level of dimensional accuracy and surface finish can I expect from metal 3D printed cooling channel inserts? Dimensional accuracy typically ranges from ±0.1 to ±0.5 mm, depending on the geometry and printing process. Surface finish is generally rougher than machined surfaces but can be improved through post-processing techniques like polishing and abrasive flow machining (AFM) for internal channels. Metal3DP’s industry-leading print accuracy and post-processing capabilities ensure high-quality results.
Заключение
Metal 3D printing has revolutionized the manufacturing of industrial cooling channel inserts, offering unprecedented design freedom, material flexibility, and performance enhancements compared to traditional methods. The ability to create conformal cooling channels using materials like CuCrZr and AlSi10Mg allows for optimized thermal management in critical industrial applications across aerospace, automotive, medical, and industrial manufacturing. While design considerations, post-processing requirements, and potential challenges need careful attention, partnering with an experienced and reliable metal 3D printing service provider like Metal3DP can ensure the successful production of high-quality, efficient cooling solutions tailored to your specific needs. By embracing metal additive manufacturing, businesses can achieve superior performance, reduce cycle times, improve product quality, and accelerate their digital manufacturing transformations. Contact Metal3DP today to explore how our cutting-edge systems and high-performance metal powders can empower your organization’s additive manufacturing goals.
Поделиться
MET3DP Technology Co., LTD - ведущий поставщик решений для аддитивного производства со штаб-квартирой в Циндао, Китай. Наша компания специализируется на производстве оборудования для 3D-печати и высокопроизводительных металлических порошков для промышленного применения.
Сделайте запрос, чтобы получить лучшую цену и индивидуальное решение для вашего бизнеса!
Похожие статьи
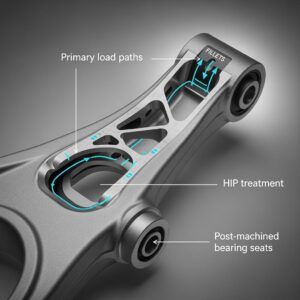
Metal 3D Printing for U.S. Automotive Lightweight Structural Brackets and Suspension Components
Читать далее "О компании Met3DP
Последние обновления
Наш продукт
CONTACT US
Есть вопросы? Отправьте нам сообщение прямо сейчас! После получения Вашего сообщения мы всей командой выполним Ваш запрос.
Получите информацию о Metal3DP
Брошюра о продукции
Получить последние продукты и прайс-лист