Internal Cooling Structures
Оглавление
Introduction – The Critical Role of Advanced Cooling in Aerospace Applications
The relentless pursuit of enhanced performance, increased efficiency, and miniaturization in the aerospace industry has placed unprecedented demands on thermal management systems. From the extreme heat generated within turbine engines and combustion chambers to the critical need to dissipate heat from sensitive avionics and hydraulic systems, effective cooling is no longer a secondary consideration but a fundamental requirement for operational safety and mission success. As aerospace components become more complex and operate under increasingly demanding conditions, traditional manufacturing methods often fall short in providing the intricate cooling solutions necessary to maintain optimal operating temperatures. This is where the transformative power of metal additive manufacturing, specifically for producing internal cooling manifolds, emerges as a game-changer. These meticulously designed internal channels, integrated directly into the component structure, offer unparalleled efficiency in heat dissipation, contributing to enhanced system reliability, prolonged component lifespan, and ultimately, safer and more capable aircraft and spacecraft. Metal3DP Technology Co., LTD, headquartered in Qingdao, China, stands at the forefront of this revolution, providing industry-leading additive manufacturing solutions tailored to the stringent demands of the aerospace sector. With a comprehensive portfolio encompassing advanced 3D-печать equipment and high-performance metal powders, Metal3DP empowers aerospace engineers and procurement managers to unlock the full potential of metal additive manufacturing for their most critical applications. Our commitment to industry-leading print volume, accuracy, and reliability ensures that mission-critical aerospace parts can be produced with the utmost confidence. Explore our range of advanced 3D printing solutions at 3D-печать по металлу.
What are Aerospace Cooling Manifolds Used For?
Aerospace cooling manifolds are integral components designed to regulate the temperature of various critical systems and subsystems within aircraft and spacecraft. Their primary function is to efficiently transfer heat away from sensitive areas, ensuring optimal performance and preventing thermal damage that could lead to catastrophic failures. The applications of these sophisticated cooling structures are diverse and span across numerous domains within the aerospace industry:
- Лопасти и лопатки турбины: In the hot sections of gas turbine engines, turbine blades and vanes are subjected to extremely high temperatures and stresses. Internal cooling channels within these components, often with intricate serpentine or lattice designs, allow for the circulation of cooling air, maintaining material integrity and extending service life. The complex geometries required for effective cooling are ideally achieved through metal 3D printing.
- Combustion Chambers: The combustion process in rocket engines and gas turbines generates immense heat. Cooling manifolds integrated into the walls of combustion chambers help to dissipate this heat, preventing material burnout and ensuring the structural integrity of the engine. Conformal cooling channels, precisely tailored to the heat flux distribution, are a significant advantage offered by additive manufacturing.
- Electronic Systems and Avionics: Modern aircraft and spacecraft are equipped with increasingly sophisticated electronic systems that generate significant heat. Cooling manifolds are used to manage the thermal environment of these components, ensuring reliable operation of critical avionics, control systems, and communication equipment. Lightweight and efficient cooling solutions are paramount in this domain.
- Hydraulic Systems: Aerospace hydraulic systems operate under high pressures and can generate substantial heat. Cooling manifolds integrated into hydraulic actuators and other components help to maintain optimal fluid temperatures, ensuring consistent performance and preventing system failures.
- Теплообменники: While often considered separate components, complex internal channels within 3D printed heat exchangers can be viewed as specialized cooling manifolds. These are used in various aerospace applications to transfer heat between fluids, playing a crucial role in thermal management.
By providing tailored cooling solutions for these diverse applications, aerospace cooling manifolds contribute directly to enhanced system reliability, improved performance, increased fuel efficiency, and extended component lifespan. The ability to design and manufacture these intricate structures with unprecedented freedom is a key driver for the adoption of metal 3D printing in the aerospace sector. Learn more about the versatility of metal 3D printing applications at Портфолио продуктов.
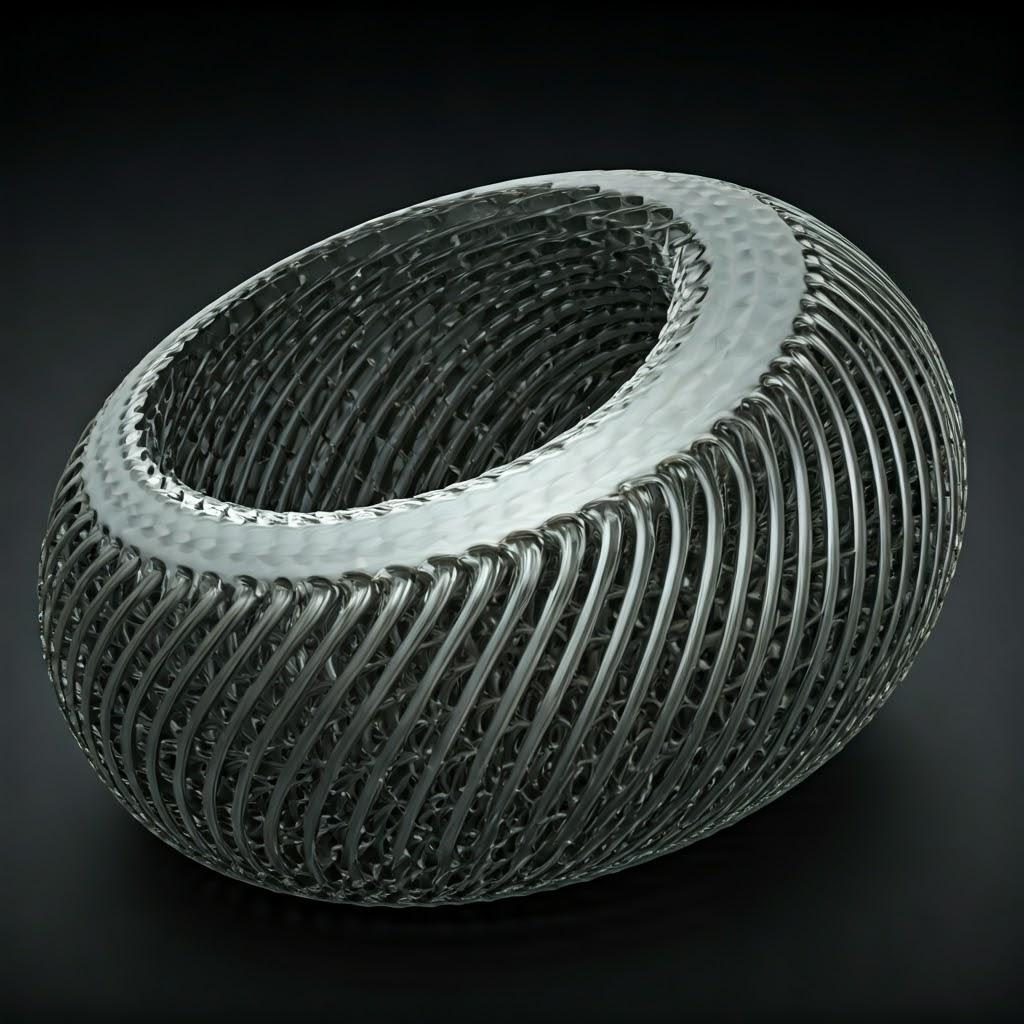
Why Use Metal 3D Printing for Aerospace Cooling Manifolds?
The adoption of metal 3D printing for the production of aerospace cooling manifolds offers a multitude of compelling advantages over traditional manufacturing methods such as casting, machining, or brazing. These benefits are particularly significant in the demanding environment of the aerospace industry, where performance, weight, and reliability are paramount:
- Свобода и сложность дизайна: Metal additive manufacturing allows for the creation of highly complex internal geometries that are simply impossible or prohibitively expensive to achieve with conventional techniques. This design freedom enables the optimization of cooling channel layouts for maximum heat transfer efficiency, including conformal cooling channels that follow the exact contours of the hot component.
- Material Optimization and Lightweighting: 3D printing facilitates the creation of intricate lattice structures and thin-walled designs, significantly reducing the weight of cooling manifolds without compromising structural integrity or cooling performance. This is crucial in aerospace, where every kilogram saved translates to increased fuel efficiency and payload capacity. Metal3DP’s expertise in high-performance metal powders ensures that these lightweight designs maintain the necessary strength and durability.
- Reduced Assembly and Part Count: Additive manufacturing enables the consolidation of multiple parts into a single, complex component. This reduces the need for assembly processes like brazing or welding, minimizing potential failure points and improving overall reliability. Internal cooling channels can be directly integrated into the main component structure during the printing process.
- Faster Prototyping and Iteration: The speed and flexibility of 3D printing allow for rapid prototyping and design iteration. Aerospace engineers can quickly test different cooling channel designs and optimize performance before committing to mass production, significantly reducing development timelines and costs.
- Кастомизация и производство по требованию: Metal 3D printing is ideal for producing customized cooling solutions tailored to specific aerospace applications and low-volume production runs. This eliminates the need for expensive tooling and large minimum order quantities associated with traditional manufacturing.
- Enhanced Performance and Efficiency: The ability to create optimized internal cooling channels leads to more efficient heat dissipation, resulting in lower operating temperatures, improved performance of critical aerospace components, and extended service life.
Metal3DP’s advanced metal 3D printing capabilities are specifically geared towards meeting the stringent requirements of the aerospace industry. Our industry-leading print volume, accuracy, and reliability ensure the production of high-performance cooling manifolds that meet the demanding specifications of aerospace applications. Explore the various Методы печати we offer to achieve these complex geometries.
Recommended Materials and Why They Matter
The selection of the appropriate metal powder is crucial for the performance and reliability of 3D printed aerospace cooling manifolds. The extreme operating conditions encountered in aerospace applications necessitate materials with exceptional high-temperature strength, corrosion resistance, and thermal conductivity. Metal3DP offers a range of high-quality metal powders optimized for laser and electron beam powder bed fusion, including two standout materials for aerospace cooling manifolds: IN625 and AlSi10Mg.
IN625 (Inconel 625)
IN625 is a nickel-chromium-molybdenum superalloy renowned for its exceptional combination of properties, making it an ideal choice for demanding aerospace environments:
- Excellent High-Temperature Strength: IN625 retains its strength and creep resistance at elevated temperatures, crucial for components operating in the hot sections of engines or exposed to significant thermal loads.
- Превосходная коррозионная стойкость: This alloy exhibits outstanding resistance to a wide range of corrosive environments, including oxidation and aggressive chemical attack, which is vital for ensuring the long-term durability of cooling manifolds in aerospace applications.
- High Fatigue Strength: Aerospace components are often subjected to cyclic loading and vibrations. IN625 possesses high fatigue strength, ensuring the structural integrity of cooling manifolds under these demanding conditions.
- Good Weldability and Fabricability: While traditionally challenging to machine, IN625 is well-suited for additive manufacturing, allowing for the creation of complex geometries with excellent material properties.
Metal3DP’s high-quality IN625 powder is specifically processed using advanced gas atomization technology to ensure high sphericity and good flowability, essential for achieving dense, high-quality 3D printed parts with superior mechanical properties.
AlSi10Mg (Aluminum Silicon Magnesium Alloy)
AlSi10Mg is a lightweight aluminum alloy with good thermal conductivity, making it suitable for aerospace cooling applications where weight reduction and efficient heat transfer are critical:
- Легкий вес: Aluminum alloys offer a significant weight advantage over nickel-based superalloys, contributing to improved fuel efficiency and payload capacity in aircraft and spacecraft.
- Good Thermal Conductivity: AlSi10Mg exhibits excellent thermal conductivity, facilitating efficient heat transfer away from critical components.
- Хорошее соотношение прочности и веса: Despite its low density, AlSi10Mg offers a good balance of strength and stiffness, making it suitable for various structural cooling applications.
- Excellent Processability with Additive Manufacturing: AlSi10Mg is well-established for powder bed fusion processes, yielding parts with good density and mechanical properties.
Metal3DP manufactures high-quality AlSi10Mg powder optimized for additive manufacturing, ensuring consistent and reliable printing of complex cooling manifold designs.
Comparative Table:
Недвижимость | IN625 (Inconel 625) | AlSi10Mg (Aluminum Silicon Magnesium) |
---|---|---|
Плотность | Высокая | Низкий |
Высокотемпературная прочность | Отличный | Умеренный |
Коррозионная стойкость | Superior | Хороший |
Теплопроводность | Умеренный | Хороший |
Weight Sensitivity | Less suitable for extreme lightweighting | Highly suitable for lightweighting |
Типовые применения | High-temperature, corrosive environments | Weight-sensitive applications with good thermal management |
Export to Sheets
The choice between IN625 and AlSi10Mg depends on the specific requirements of the aerospace cooling application, considering factors such as operating temperature, corrosive environment, and weight constraints. Metal3DP’s expertise in both these and other advanced metal powders ensures that our customers can select the optimal material for their unique needs. Learn more about our comprehensive range of высококачественные металлические порошки.
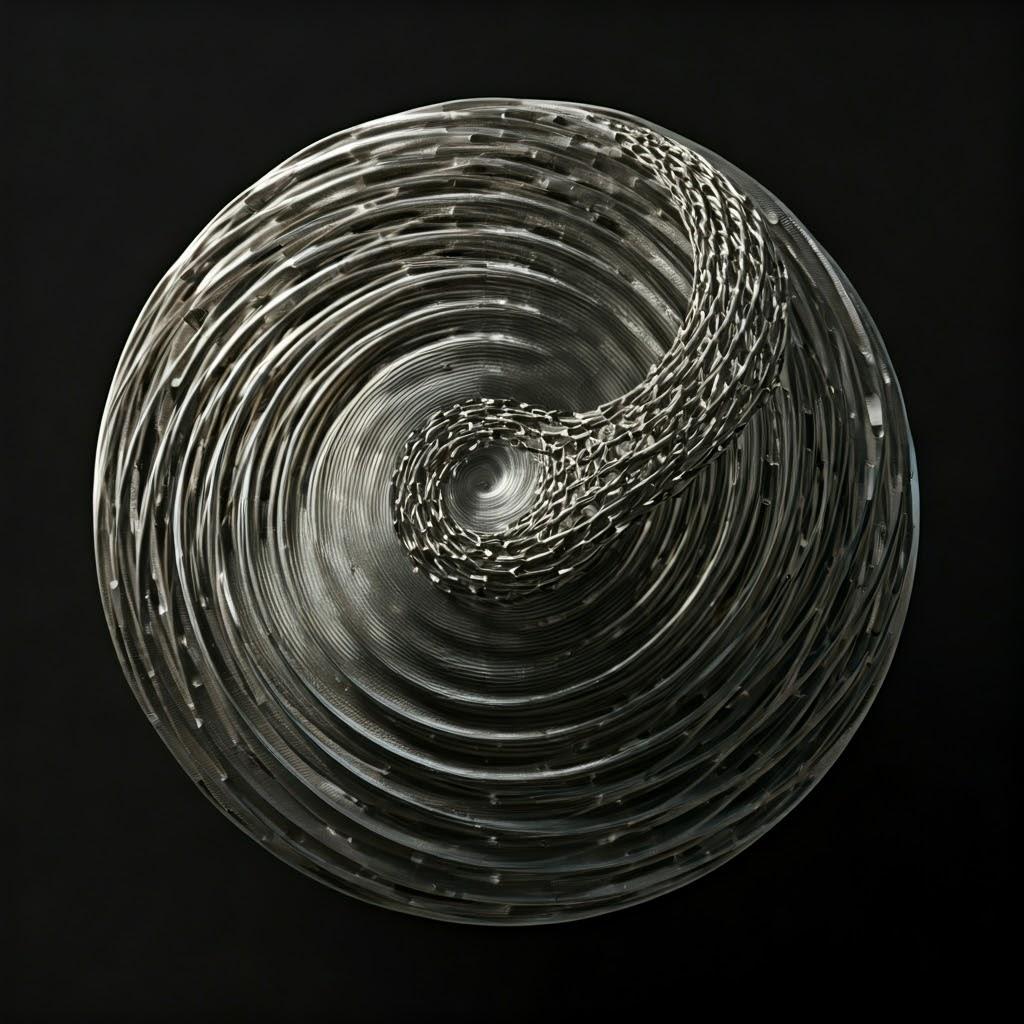
Design Considerations for Additive Manufacturing of Cooling Manifolds
Designing aerospace cooling manifolds for metal additive manufacturing requires a different mindset compared to traditional methods. The unique capabilities and limitations of 3D printing open up new possibilities for optimizing performance and functionality. Here are key design considerations to keep in mind:
- Internal Channel Design:
- Shape and Size: Optimize the shape and cross-sectional area of internal cooling channels to ensure efficient fluid flow and maximize heat transfer surface area. Consider using non-circular channels or incorporating turbulators to enhance convective heat transfer.
- Layout and Conformity: Design channels that conform closely to the heat-generating surfaces. Conformal cooling, a significant advantage of 3D printing, allows for uniform cooling and eliminates hot spots more effectively than traditional straight channels.
- Network Complexity: Metal 3D printing enables the creation of complex internal networks with branching channels and intricate pathways to target specific areas requiring cooling.
- Support Structure Minimization:
- Self-Supporting Angles: Design the manifold with self-supporting angles (typically 45 degrees or greater relative to the build plate) to minimize the need for support structures within internal channels, which can be difficult to remove post-printing.
- Orientation Optimization: Strategically orient the part on the build platform to reduce the number and volume of necessary supports, improving surface finish and reducing material waste.
- Smart Support Design: When supports are unavoidable, design them with easy removal in mind, using breakaway points or thin connections to the part.
- Wall Thickness and Feature Size:
- Minimum Wall Thickness: Adhere to the minimum wall thickness specifications recommended for the chosen metal powder and printing process to ensure structural integrity and successful printing.
- Feature Resolution: Be mindful of the minimum feature size achievable with the selected technology when designing small channels, intricate details, and sharp corners.
- Lattice Structures and Weight Reduction:
- Internal Lattices: Explore the use of internal lattice structures within the manifold walls to reduce weight while maintaining stiffness and facilitating heat transfer through increased surface area.
- Topology Optimization: Employ topology optimization software to identify areas where material can be removed without compromising structural performance, leading to lightweight designs with optimized cooling channels.
- Powder Removal Considerations:
- Access Ports: Design access ports or strategically placed openings to facilitate the removal of un-sintered powder from internal channels after printing.
- Channel Connectivity: Ensure that internal channels are interconnected or have sufficient openings to allow for effective powder evacuation.
By carefully considering these design principles, engineers can leverage the unique capabilities of metal 3D printing to create aerospace cooling manifolds with enhanced performance, reduced weight, and improved manufacturability. Metal3DP’s expertise in design for additive manufacturing (DfAM) can assist in optimizing your designs for our advanced printing processes.
Tolerance, Surface Finish, and Dimensional Accuracy of 3D Printed Cooling Manifolds
Achieving the required tolerance, surface finish, and dimensional accuracy is paramount for aerospace components, including cooling manifolds. Metal 3D printing technologies have advanced significantly in their ability to produce parts with tight specifications. Here’s what users can typically expect from Metal3DP’s advanced processes:
- Tolerance:
- Typical Range: Depending on the geometry, material, and specific printing technology (e.g., DMLS, SLM, EBM), typical achievable tolerances for metal 3D printed parts range from ±0.05 mm to ±0.2 mm. Critical functional surfaces may require post-machining to achieve tighter tolerances.
- Факторы, влияющие на толерантность: Part size, orientation on the build plate, material shrinkage during solidification, and the calibration of the 3D printer all influence the final dimensional accuracy. Metal3DP employs rigorous calibration and process control measures to minimize deviations.
- Отделка поверхности:
- As-Built Surface Roughness: The as-built surface finish of metal 3D printed parts is typically rougher compared to machined surfaces, with Ra (average roughness) values ranging from 5 to 20 µm. This surface roughness is influenced by the powder particle size and the layer thickness used during printing.
- Post-Processing for Improved Surface Finish: Various post-processing techniques can be employed to improve the surface finish of 3D printed cooling manifolds, including:
- Media Blasting: To remove partially sintered powder and achieve a more uniform surface.
- Полировка: Mechanical or chemical polishing can significantly reduce surface roughness for improved fluid flow and reduced friction within cooling channels.
- CNC Machining: For critical external surfaces requiring very smooth finishes and tight tolerances.
- Точность размеров:
- Факторы, влияющие на точность: Similar to tolerances, dimensional accuracy is influenced by the printing process, material properties, and part geometry. Complex geometries with significant overhangs or thin features can be more challenging to print with high accuracy.
- Metal3DP’s Commitment to Accuracy: Metal3DP’s state-of-the-art printing equipment and optimized process parameters are designed to maximize dimensional accuracy. We work closely with our clients to understand their specific requirements and implement appropriate strategies to achieve the desired precision. This may include pre-build simulation and analysis to predict and compensate for potential distortions.
- Inspection and Quality Control: Rigorous inspection processes, including coordinate measuring machines (CMM) and non-destructive testing (NDT), are employed to verify the dimensional accuracy and integrity of the printed cooling manifolds.
Understanding the achievable tolerances and surface finishes in metal 3D printing is crucial for designing functional aerospace cooling manifolds. Metal3DP provides comprehensive information on the capabilities of our equipment and offers various post-processing options to meet stringent aerospace specifications.
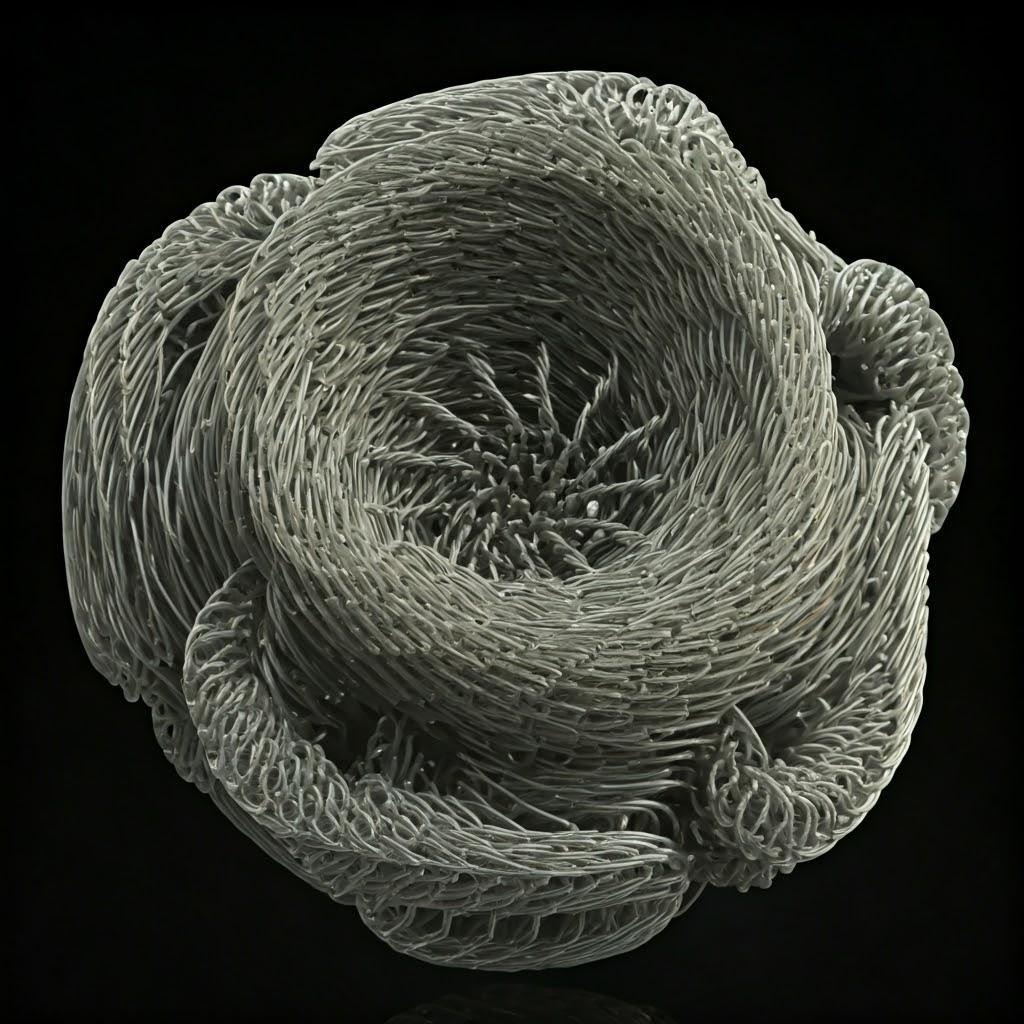
Post-Processing Requirements for Aerospace Cooling Manifolds
While metal 3D printing offers significant advantages in creating complex geometries, post-processing is often necessary to achieve the final desired properties, surface finish, and dimensional accuracy for aerospace cooling manifolds. Common post-processing steps include:
- Удаление опоры:
- Удаление вручную: Supports are often manually broken away or cut off using specialized tools.
- Обработка: For more intricate supports or those in difficult-to-reach areas, CNC machining or wire EDM (Electrical Discharge Machining) may be required.
- Solvent Dissolution: For certain materials and support types, chemical dissolution in a solvent bath can be used.
- Powder Removal from Internal Channels:
- Air Blasting: High-pressure air or inert gas is used to blow out loose, un-sintered powder from internal cooling channels.
- Vibration and Agitation: Vibratory tables or ultrasonic cleaning baths can help dislodge trapped powder.
- Водоструйная обработка: High-pressure water jets can be effective in removing powder, especially for complex internal geometries.
- Термообработка:
- Снятие стресса: To reduce internal stresses that may have built up during the printing process.
- Annealing: To soften the material and improve ductility.
- Solution Annealing and Aging: Specific heat treatment cycles are used for certain alloys like IN625 to optimize their mechanical properties, such as strength and hardness.
- Горячее изостатическое прессование (HIP): Applying high pressure and temperature simultaneously to eliminate internal porosity and improve the density and mechanical properties of the printed part. This is particularly important for critical aerospace components.
- Отделка поверхности:
- Media Blasting: To achieve a uniform surface texture and remove partially sintered particles.
- Grinding and Polishing: To reduce surface roughness and achieve smoother finishes for improved fluid flow or aesthetic requirements.
- CNC Machining: For achieving very tight tolerances and smooth surface finishes on critical external features.
- Покрытия: Applying protective coatings, such as anti-corrosion or thermal barrier coatings, to enhance the performance and durability of the cooling manifold in specific aerospace environments. Examples include ceramic coatings or specialized metallic coatings.
- Inspection and Quality Control:
- Измерение размеров: Using CMMs or other precision measurement tools to verify that the part meets the specified dimensional tolerances.
- Неразрушающий контроль (NDT): Techniques like dye penetrant inspection, ultrasonic testing, or X-ray radiography may be used to detect any internal flaws or defects.
The specific post-processing requirements for an aerospace cooling manifold will depend on the material, the intended application, and the required performance characteristics. Metal3DP offers a comprehensive suite of post-processing services to ensure that our 3D printed parts meet the stringent quality standards of the aerospace industry.
Common Challenges and How to Avoid Them in 3D Printing Cooling Manifolds
While metal 3D printing offers numerous advantages, there are also potential challenges that need to be addressed to ensure the successful fabrication of high-quality aerospace cooling manifolds:
- Warping and Distortion:
- Вызов: Thermal stresses during the printing process can lead to warping or distortion of the part, especially for large or complex geometries with significant variations in cross-section.
- Avoidance:
- Optimized Part Orientation: Orienting the part strategically on the build plate can minimize thermal gradients and reduce the likelihood of warping.
- Support Structure Design: Properly designed support structures can help anchor the part and prevent distortion.
- Оптимизация параметров процесса: Fine-tuning laser power, scan speed, and layer thickness can minimize residual stresses.
- Pre-Build Simulation: Using simulation software to predict and compensate for potential distortions in the design phase.
- Support Removal from Internal Channels:
- Вызов: Removing support structures from intricate internal cooling channels can be difficult and time-consuming, potentially damaging the delicate features.
- Avoidance:
- Self-Supporting Designs: Design channels with angles that minimize the need for internal supports.
- Water-Soluble Supports: For certain materials, using water-soluble support materials can simplify removal.
- Strategic Access Ports: Incorporating access ports in the design to facilitate the removal of supports and un-sintered powder.
- Porosity and Density Issues:
- Вызов: Insufficient laser power or improper process parameters can lead to lack of fusion and the formation of porosity within the printed part, compromising its mechanical properties and potentially causing leaks in cooling channels.
- Avoidance:
- Optimized Process Parameters: Utilizing well-established and optimized print parameters for the chosen material.
- High-Quality Powder: Using high-quality metal powders with good flowability and consistent particle size distribution, such as those offered by Metal3DP.
- Inert Atmosphere: Printing in a controlled inert atmosphere to prevent oxidation and ensure proper melting.
- Горячее изостатическое прессование (HIP): Post-processing with HIP can effectively eliminate internal porosity and achieve near-full density.
- Surface Roughness Affecting Fluid Flow:
- Вызов: The inherent surface roughness of as-built 3D printed parts can increase friction and reduce the efficiency of fluid flow within cooling channels.
- Avoidance:
- Optimized Print Parameters: Using finer layer thicknesses and optimized laser parameters can improve surface finish.
- Постобработка: Employing surface finishing techniques like polishing or chemical etching to reduce roughness.
- Ensuring Leak-Proof Designs:
- Вызов: Achieving perfectly leak-proof internal channels is critical for cooling manifolds. Porosity or micro-cracks can lead to leakage.
- Avoidance:
- Dense Printing: Optimizing process parameters and using HIP to minimize porosity.
- Thorough Inspection: Employing NDT methods to detect any internal flaws.
- Pressure Testing: Conducting pressure tests after printing and post-processing to verify the integrity of the cooling channels.
By understanding these potential challenges and implementing appropriate design strategies and process controls, it is possible to consistently produce high-quality, reliable metal 3D printed cooling manifolds for demanding aerospace applications. Metal3DP’s extensive experience and expertise in metal additive manufacturing enable us to help our clients navigate these challenges effectively.
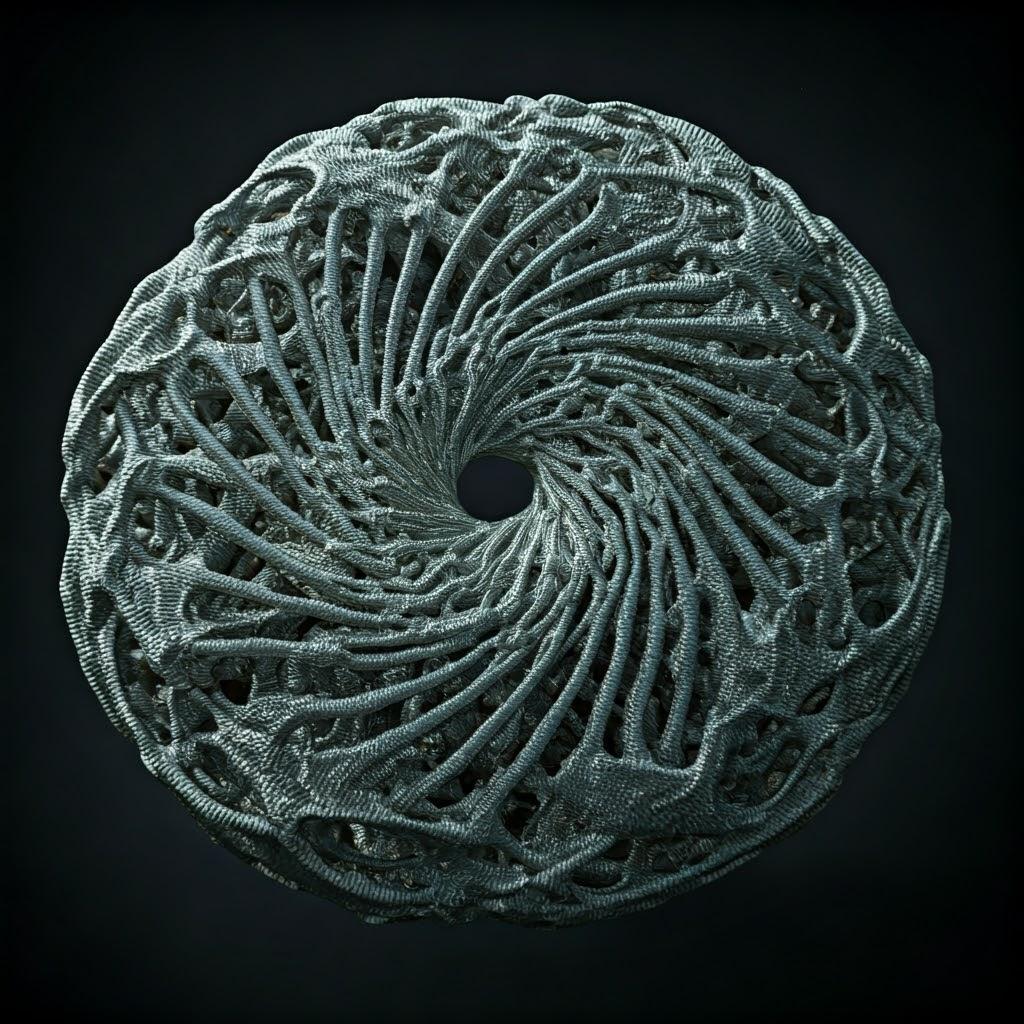
How to Choose the Right Metal 3D Printing Service Provider for Aerospace Cooling Manifolds
Selecting the appropriate metal 3D printing service provider is a critical decision for aerospace companies seeking to leverage the benefits of additive manufacturing for their cooling manifold needs. The stringent requirements of the aerospace industry demand a partner with specific expertise, certifications, and capabilities. Here are key factors to consider when evaluating potential providers:
- Aerospace Certifications and Standards:
- AS9100 Certification: Ensure the provider holds AS9100 certification, the internationally recognized quality management system standard specific to the aerospace industry. This demonstrates their commitment to quality, reliability, and safety. Metal3DP adheres to rigorous quality standards relevant to the aerospace sector.
- NADCAP Accreditation: Accreditation from the National Aerospace and Defense Contractors Accreditation Program (NADCAP) for processes like heat treating or non-destructive testing can be a significant indicator of a provider’s competence.
- Material Expertise and Range:
- Experience with Aerospace Alloys: The provider should have extensive experience working with aerospace-grade metal powders such as IN625 and AlSi10Mg, as well as a deep understanding of their specific processing requirements and properties. Metal3DP specializes in a wide range of high-performance metal powders optimized for aerospace applications.
- Material Characterization and Testing: Inquire about the provider’s material characterization and testing capabilities to ensure the quality and consistency of the printed parts.
- Technology and Equipment:
- Advanced Metal 3D Printing Technologies: The provider should possess state-of-the-art metal 3D printing equipment, such as Direct Metal Laser Sintering (DMLS), Selective Laser Melting (SLM), or Electron Beam Melting (EBM), capable of producing the required complexity and precision. Metal3DP utilizes industry-leading SEBM printers known for their accuracy and reliability.
- Build Volume and Capacity: Ensure the provider has sufficient build volume and production capacity to meet your project requirements, especially for larger cooling manifolds or serial production.
- Design for Additive Manufacturing (DfAM) Support:
- Expertise in Optimizing Designs: The provider should offer expertise in DfAM, helping you optimize your cooling manifold designs for the specific constraints and opportunities of metal 3D printing. Metal3DP provides comprehensive application development services to assist with design optimization.
- Simulation and Analysis Capabilities: The ability to perform pre-build simulations to predict and mitigate potential issues like warping or residual stresses is a valuable asset.
- Post-Processing Capabilities:
- Comprehensive Services: The provider should offer a range of in-house or readily accessible post-processing services critical for aerospace applications, including support removal, powder removal, heat treatment (including HIP), surface finishing, and specialized coatings.
- Quality Control and Inspection:
- Rigorous Quality Systems: A robust quality management system with thorough inspection processes, including dimensional measurement and non-destructive testing, is essential to ensure the integrity and reliability of the printed cooling manifolds.
- Communication and Collaboration:
- Transparent Communication: The provider should maintain clear and transparent communication throughout the project lifecycle, from design to delivery.
- Willingness to Collaborate: A collaborative approach, where the provider works closely with your engineering team, is crucial for successful outcomes.
- Lead Times and Scalability:
- Realistic Lead Times: Understand the provider’s typical lead times for similar projects and ensure they align with your project schedule.
- Scalability for Future Needs: Consider the provider’s ability to scale up production if your requirements increase in the future.
By carefully evaluating potential metal 3D printing service providers based on these criteria, aerospace companies can identify a trusted partner like Metal3DP to deliver high-performance, reliable cooling manifolds that meet the demanding standards of the industry. Contact Metal3DP to explore how our capabilities can power your organization’s additive manufacturing goals.
Cost Factors and Lead Time for 3D Printed Aerospace Cooling Manifolds
Understanding the cost drivers and typical lead times associated with metal 3D printing of aerospace cooling manifolds is essential for effective project planning and budgeting. Here’s a breakdown of the key factors:
Факторы стоимости:
- Материальные затраты: The cost of the metal powder is a significant factor. Aerospace-grade alloys like IN625 are typically more expensive than standard metals like aluminum alloys. The quantity of material used, which is influenced by part size and design optimization, also impacts the overall cost. Metal3DP offers competitive pricing on a wide range of high-quality metal powders.
- Сложность дизайна: Intricate designs with complex internal channels, thin walls, and lattice structures may require more sophisticated printing strategies and longer build times, thus increasing costs. Design optimization for manufacturability can help mitigate these costs.
- Время сборки: The duration of the printing process directly affects the machine utilization cost. Factors influencing build time include part size, complexity, layer height, and the number of parts being printed simultaneously on the build platform. Metal3DP’s industry-leading print volume allows for efficient nesting and potentially lower per-part costs for batch production.
- Расходы на постобработку: The extent of post-processing required (e.g., support removal, powder removal, heat treatment, surface finishing, coatings) significantly impacts the final cost. Complex geometries with difficult-to-access internal channels may require more labor-intensive post-processing.
- Расходы на оплату труда: This includes the expertise required for design optimization, print setup, machine operation, post-processing, and quality control. Experienced providers with specialized knowledge in aerospace applications may have higher labor rates.
- Equipment and Overhead Costs: The cost of maintaining and operating advanced metal 3D printing equipment, as well as general overhead costs, are factored into the pricing.
- Quality Assurance and Inspection: Rigorous quality control procedures and non-destructive testing, which are crucial for aerospace components, add to the overall cost.
Время выполнения:
Lead times for metal 3D printed aerospace cooling manifolds can vary depending on several factors:
- Design Complexity and Optimization: Initial design and optimization for additive manufacturing may take time, especially for intricate internal cooling structures.
- Доступность материала: The availability of the specific aerospace-grade metal powder required can influence lead times. Metal3DP maintains a stock of a wide range of high-quality metal powders to minimize delays.
- Время печати: The actual printing duration depends on the part size, complexity, and the number of parts being processed.
- Post-Processing Time: The time required for support removal, powder removal, heat treatment cycles, surface finishing, and any specialized coatings can add to the overall lead time.
- Quality Inspection and Testing: Thorough quality checks and testing procedures are essential and contribute to the overall lead time.
- Scheduling and Production Queue: The current workload and production schedule of the service provider can also affect lead times. Metal3DP strives for efficient scheduling to minimize turnaround times.
While metal 3D printing can offer faster prototyping compared to traditional methods, the overall lead time for production parts depends on the complexity and the required post-processing and quality assurance steps. It’s crucial to discuss lead time expectations clearly with your chosen service provider early in the project.
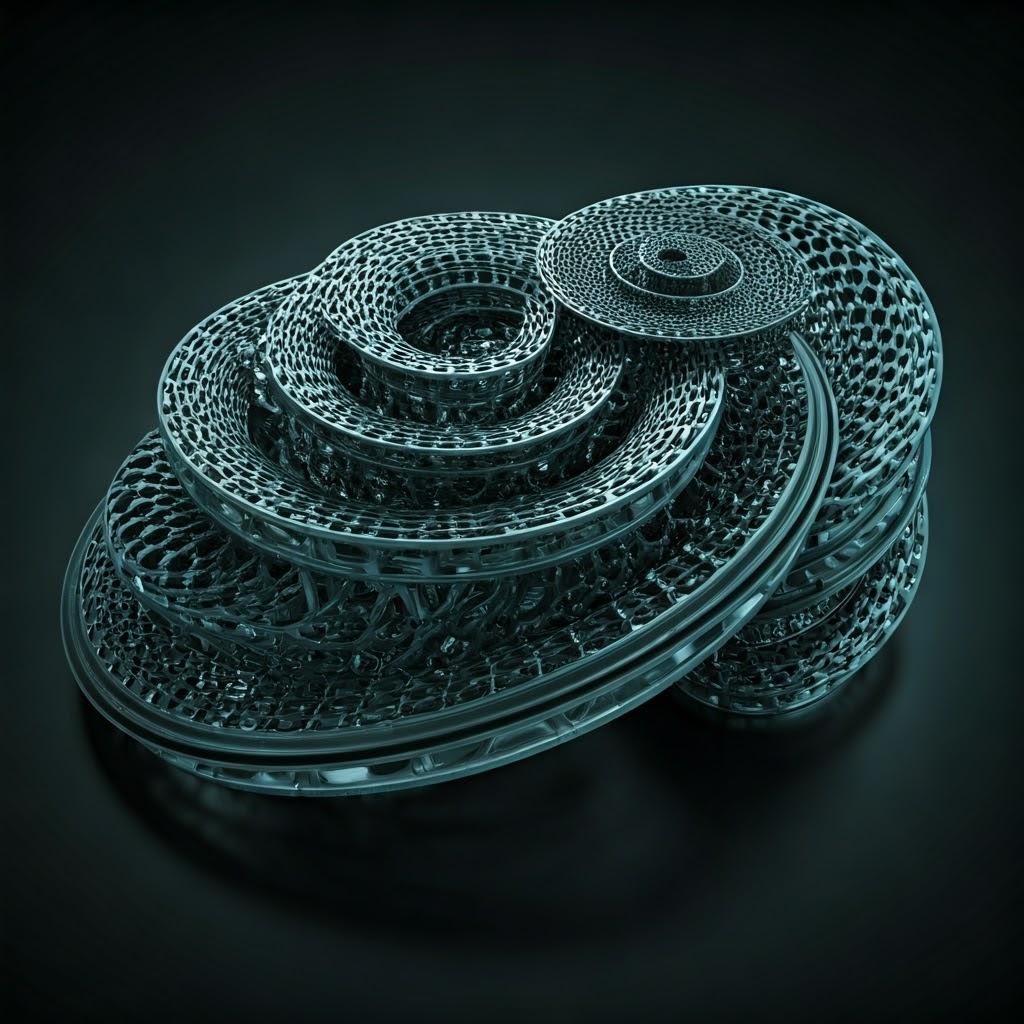
Часто задаваемые вопросы (FAQ)
- Q: Can metal 3D printing produce cooling channels with complex internal geometries suitable for aerospace applications?
- A: Absolutely. Metal 3D printing, particularly technologies like DMLS, SLM, and EBM, excels at creating intricate internal geometries, including conformal cooling channels tailored to the specific thermal management needs of aerospace components. This design freedom allows for optimized heat transfer and improved performance compared to traditional manufacturing methods. Metal3DP’s advanced printing systems are well-suited for producing such complex internal structures.
- Q: What are the key advantages of using IN625 for 3D printed aerospace cooling manifolds operating in high-temperature environments?
- A: IN625 (Inconel 625) offers exceptional high-temperature strength, superior corrosion resistance, and high fatigue strength, making it an ideal material for demanding aerospace environments where cooling manifolds are exposed to extreme heat and potential corrosive agents. Metal3DP provides high-quality IN625 powder specifically optimized for additive manufacturing to ensure excellent performance in these conditions.
- Q: How does metal 3D printing contribute to weight reduction in aerospace cooling systems?
- A: Metal 3D printing enables the creation of optimized designs with intricate lattice structures, thin walls, and hollow features, significantly reducing the weight of cooling manifolds compared to conventionally manufactured parts. This weight reduction is crucial in aerospace for improving fuel efficiency and increasing payload capacity. Techniques like topology optimization, facilitated by the design freedom of 3D printing, further enhance lightweighting possibilities.
Conclusion – Embracing the Future of Aerospace Cooling with Metal 3D Printing
The aerospace industry stands at the cusp of a new era in thermal management, driven by the transformative capabilities of metal 3D printing. The ability to design and manufacture intricate internal cooling manifolds with optimized geometries, using high-performance materials like IN625 and lightweight alloys like AlSi10Mg, offers unprecedented opportunities for enhancing the performance, reliability, and efficiency of critical aerospace components.
Metal3DP Technology Co., LTD is proud to be a leading provider of comprehensive metal additive manufacturing solutions, empowering aerospace engineers and procurement managers to realize the full potential of this groundbreaking technology. From our industry-leading SEBM printers that deliver exceptional accuracy and reliability to our portfolio of advanced metal powders engineered for demanding applications, we are committed to enabling the next generation of aerospace manufacturing.
By partnering with Metal3DP, aerospace companies gain access to not only cutting-edge equipment and materials but also decades of collective expertise in metal additive manufacturing. Our application development services, coupled with our commitment to stringent quality standards, ensure that our clients can confidently adopt metal 3D printing to revolutionize their cooling system designs and manufacturing processes.
We invite you to explore the possibilities of metal 3D printing with Metal3DP and discover how our advanced capabilities can power your organization’s additive manufacturing goals in the aerospace sector and beyond. Visit our website at 3D-печать по металлу to learn more and contact us to discuss your specific requirements.
Поделиться
MET3DP Technology Co., LTD - ведущий поставщик решений для аддитивного производства со штаб-квартирой в Циндао, Китай. Наша компания специализируется на производстве оборудования для 3D-печати и высокопроизводительных металлических порошков для промышленного применения.
Сделайте запрос, чтобы получить лучшую цену и индивидуальное решение для вашего бизнеса!
Похожие статьи
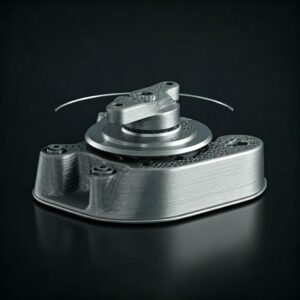
3D-печатные крепления для автомобильных радарных датчиков: Точность и производительность
Читать далее "О компании Met3DP
Последние обновления
Наш продукт
CONTACT US
Есть вопросы? Отправьте нам сообщение прямо сейчас! После получения Вашего сообщения мы всей командой выполним Ваш запрос.
Получите информацию о Metal3DP
Брошюра о продукции
Получить последние продукты и прайс-лист