Custom Cutting Tools with Metal 3D Printing
Оглавление
In the relentless pursuit of efficiency and precision, manufacturing industries worldwide are constantly seeking innovative solutions to enhance their processes. At the forefront of this revolution lies metal additive manufacturing, more commonly known as metal 3D printing. This transformative technology is reshaping how complex components are designed and produced, and one area where its impact is particularly profound is in the creation of custom cutting tools. From intricate geometries that optimize material removal to the precise application of advanced alloys, metal 3D-печать offers unprecedented flexibility and performance advantages for manufacturers in aerospace, automotive, medical, and industrial sectors.
Imagine a cutting tool tailored precisely to the unique contours of a complex workpiece, or a drill bit engineered with internal cooling channels that extend its lifespan and improve cutting speed. This is the power of custom metal 3D printed cutting tools. By leveraging advanced design software and high-performance metal powders, manufacturers can now produce tools with optimized geometries, enhanced material properties, and features that were previously impossible or cost-prohibitive with traditional manufacturing methods. As a leading provider of additive manufacturing solutions, Metal3DP is at the forefront of this innovation, empowering businesses to achieve new levels of precision and efficiency in their machining operations.
What are Custom Cutting Tools Used For? – Applications Across Aerospace, Automotive, Medical, and Industrial Sectors
Custom cutting tools play a critical role across a diverse range of industries, each with its unique demands for precision, material compatibility, and performance. Understanding these applications highlights the versatility and importance of tailored tooling solutions.
- Аэрокосмическая промышленность: In the aerospace industry, the machining of high-performance alloys like titanium and Inconel is commonplace. Custom cutting tools are essential for manufacturing complex engine components, structural parts, and airframe elements with stringent tolerance requirements. These tools can be designed for specific operations such as blisk machining, turbine blade profiling, and the creation of intricate cooling channels. The ability to produce lightweight yet robust components is paramount, and custom 3D printed tools contribute significantly to achieving these goals.
- Автомобили: The automotive sector relies heavily on efficient and precise machining for the mass production of engine parts, transmission components, chassis elements, and molds for plastic injection molding. Custom cutting tools in this industry are often designed for high-speed machining, extended tool life, and the ability to work with a variety of materials, including aluminum alloys, steel, and composites. The demand for complex geometries, such as those found in cylinder heads or intricate mold designs, makes metal 3D printing an invaluable tool for creating optimized cutting solutions.
- Медицина: The medical device industry requires cutting tools for manufacturing surgical instruments, orthopedic implants, and customized patient-specific devices. Precision and biocompatibility are critical in this sector. Metal 3D printing enables the creation of intricate tool geometries for minimally invasive procedures and the use of biocompatible materials like titanium alloys and stainless steels. Customization allows for the production of tools that meet the exact specifications of a surgical procedure or the unique anatomy of a patient.
- Industrial Manufacturing: Across general industrial manufacturing, custom cutting tools are used in a vast array of applications, including the production of machinery parts, consumer goods, electronics, and energy equipment. These tools can be tailored for specific materials like hardened steels, plastics, and composites, and for operations ranging from heavy material removal to fine finishing. The ability to optimize tool geometry for specific tasks leads to improved efficiency, reduced material waste, and higher quality end products.
The demand for specialized cutting tools that can handle increasingly complex materials and geometries is constantly growing. Metal 3D printing, with its ability to create intricate designs and utilize high-performance materials, provides a powerful solution for meeting these evolving needs across various industries. Learn more about the applications of metal 3D printing.
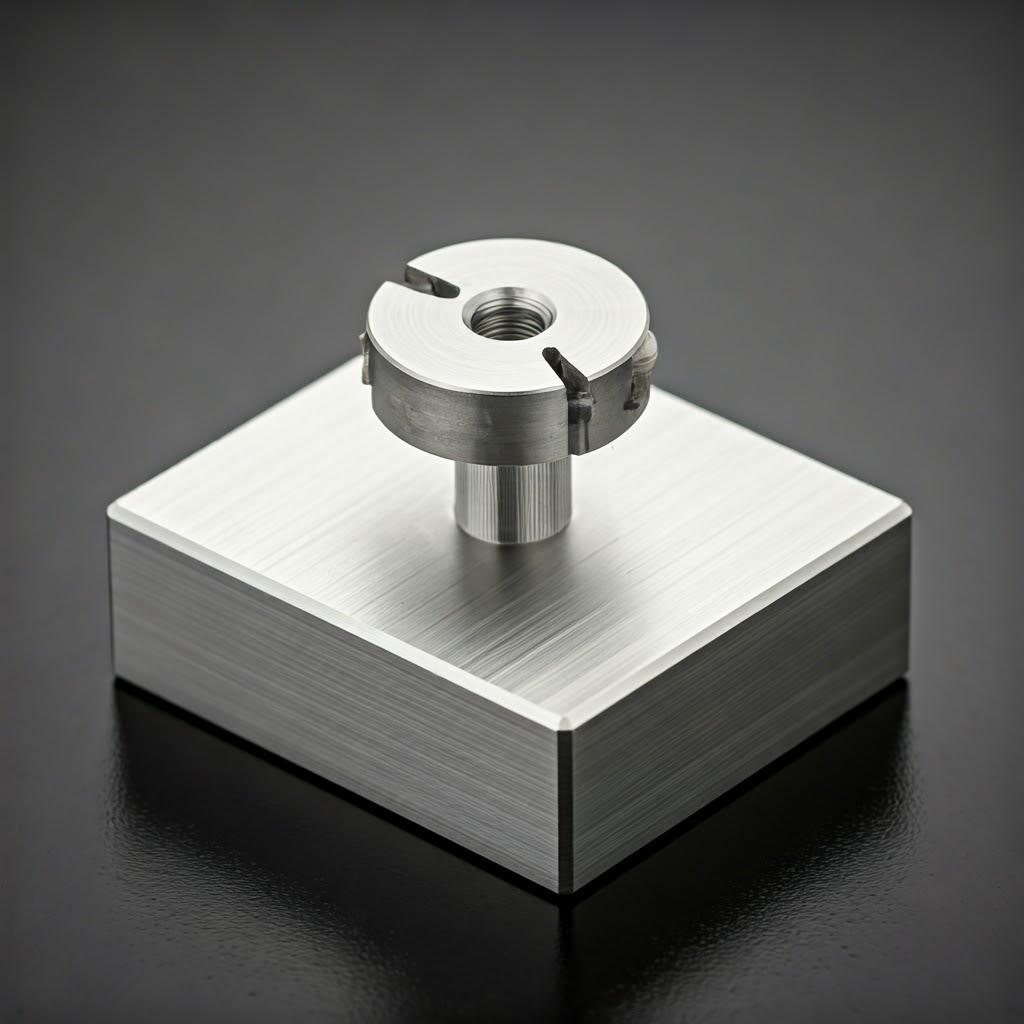
Why Use Metal 3D Printing for Custom Cutting Tools? – Advantages Over Traditional Manufacturing Methods
The adoption of metal 3D printing for the production of custom cutting tools is driven by a multitude of advantages it offers over traditional manufacturing methods such as subtractive machining (CNC milling, turning) and conventional tooling processes. These benefits translate to improved performance, reduced costs, and enhanced design freedom.
- Design Flexibility and Complexity: Metal 3D printing allows for the creation of tool geometries that are simply not achievable with traditional methods. This includes:
- Internal Cooling Channels: Conformal cooling channels can be integrated directly into the tool body, allowing for more efficient heat dissipation, extended tool life, and improved cutting performance.
- Optimized Chip Evacuation: Complex flute designs and chip breakers can be incorporated to enhance chip removal, reduce cutting forces, and improve surface finish.
- Облегчение: Internal lattice structures can be used to reduce the weight of larger tools without compromising stiffness.
- Custom Contours: Tools can be precisely matched to the complex geometries of the workpiece, ensuring optimal engagement and reducing the need for multiple machining passes.
- Оптимизация материалов: Metal 3D printing offers the ability to use advanced metal powders tailored for specific applications. This includes:
- Multi-Material Tools: While still an evolving area, the potential to combine different materials within a single tool to optimize wear resistance and toughness exists.
- Gradient Materials: Controlled variations in material composition can be achieved to create tools with specific properties in different areas.
- High-Performance Alloys: Materials like H13 and M300, offered by Metal3DP, provide exceptional hardness, wear resistance, and high-temperature performance, crucial for demanding cutting applications.
- Reduced Lead Times and Costs for Small Batches: Traditional tooling often involves lengthy lead times and significant upfront costs for mold creation or complex fixturing. Metal 3D printing can produce custom tools on demand, significantly reducing lead times, especially for small to medium production volumes and prototypes. This agility is particularly beneficial for rapid product development and specialized applications.
- Сокращение отходов: Unlike subtractive manufacturing, which generates significant material waste in the form of chips, metal 3D printing adds material layer by layer, resulting in significantly less waste. This is particularly important when working with expensive specialty alloys.
- Tool Integration and Multifunctionality: Metal 3D printing allows for the integration of multiple functions into a single tool. For example, a cutting tool could incorporate features for measuring cutting forces or monitoring tool wear in-situ.
By overcoming the limitations of traditional manufacturing, metal 3D printing empowers manufacturers to create custom cutting tools with enhanced performance, extended lifespan, and optimized efficiency, ultimately leading to improved productivity and reduced operational costs.
Recommended Materials and Why They Matter – Exploring H13 and M300 Metal Powders for Superior Performance
The selection of the right metal powder is paramount in achieving the desired properties and performance characteristics of a 3D printed custom cutting tool. Metal3DP offers a range of high-quality metal powders, including H13 and M300, which are particularly well-suited for demanding cutting applications. Understanding the unique properties of these materials is crucial for engineers and procurement managers.
H13 Tool Steel:
H13 is a chromium-molybdenum hot work tool steel known for its exceptional toughness, high strength at elevated temperatures, and excellent wear resistance. These properties make it an ideal choice for cutting tools used in demanding applications.
Недвижимость | Типовое значение | Significance for Cutting Tools |
---|---|---|
Твердость | 42-52 HRC (depending on heat treatment) | Provides excellent resistance to wear and deformation under cutting forces. |
Прочность на разрыв | Up to 1860 MPa | Ensures the tool can withstand high cutting forces without fracturing. |
Жесткость | Высокая | Resists chipping and cracking, especially important for interrupted cuts and high feed rates. |
Red Hardness | Хороший | Maintains hardness and cutting ability at elevated temperatures generated during high-speed machining. |
Сопротивление термической усталости | Отличный | Withstands repeated heating and cooling cycles without cracking, crucial for applications involving intermittent cutting. |
Износостойкость | Хороший | Provides a long tool life, reducing the frequency of tool changes and downtime. |
Приложения | Hot forging dies, extrusion dies, die casting tools, plastic molds, high-performance cutting tools (taps, milling cutters, broaches) | Particularly suitable for machining tough materials and operating at high speeds and temperatures. Offers a good balance of hardness and toughness. |
Export to Sheets
M300 High-Speed Steel:
M300 is a cobalt-enhanced high-speed steel that offers superior hardness, wear resistance, and red hardness compared to conventional high-speed steels. The addition of cobalt contributes to its exceptional performance in demanding cutting operations.
Недвижимость | Типовое значение | Significance for Cutting Tools |
---|---|---|
Твердость | 64-67 HRC (depending on heat treatment) | Provides exceptional resistance to wear, abrasion, and indentation, leading to extended tool life and improved surface finish. |
Прочность на разрыв | Up to 2500 MPa | Offers high strength to withstand significant cutting forces, allowing for higher feed rates and depths of cut. |
Жесткость | Умеренный | Provides a good balance of strength and resistance to chipping, suitable for a wide range of machining operations. |
Red Hardness | Отличный | Retains its hardness and cutting efficiency at very high temperatures, making it ideal for high-speed machining of difficult-to-cut materials. |
Износостойкость | Отличный | Offers superior resistance to abrasive and adhesive wear, significantly extending tool life, especially when machining hard and abrasive materials. |
Приложения | High-performance drills, taps, end mills, reamers, broaches for machining hardened steels, superalloys, and abrasive materials | Ideal for applications requiring high cutting speeds, aggressive feed rates, and superior wear resistance. Excels in machining challenging materials in aerospace, automotive, and die/mold industries. |
Export to Sheets
By offering these high-performance metal powders, Metal3DP enables manufacturers to 3D print custom cutting tools with the specific properties required for their unique applications, leading to enhanced productivity, improved part quality, and reduced operational costs.
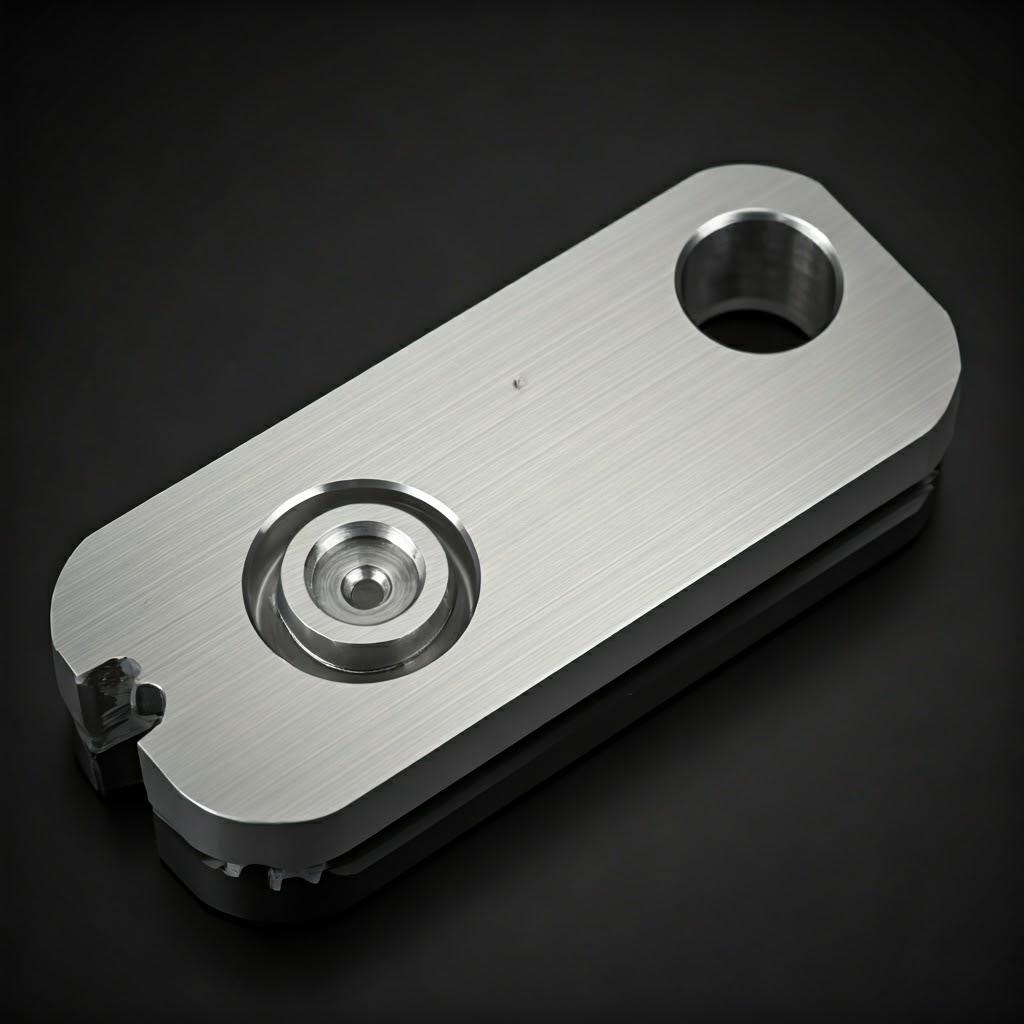
Design Considerations for Additive Manufacturing of Cutting Tools – Optimizing Geometry, Cooling Channels, and Chip Evacuation
Designing custom cutting tools for metal 3D printing requires a different mindset compared to traditional manufacturing. The layer-by-layer additive process opens up new possibilities for optimizing tool geometry and incorporating features that enhance performance and longevity.
- Optimizing Tool Geometry:
- Complex Contours: Metal 3D printing allows for the creation of intricate external shapes that precisely match the workpiece geometry. This can lead to improved material removal rates, reduced vibration, and better surface finishes. For example, a custom form tool can be designed to create a complex profile in a single pass, reducing cycle time.
- Variable Pitch and Helix Angles: The ability to vary the pitch and helix angles along the cutting edge can optimize chip formation and evacuation for specific materials and cutting conditions. This can lead to reduced cutting forces and improved tool life.
- Customized Rake and Relief Angles: Additive manufacturing enables precise control over rake and relief angles, which are critical for cutting efficiency and surface quality. These angles can be tailored to the specific material being machined.
- Integrating Internal Cooling Channels: One of the most significant advantages of 3D printing for cutting tools is the ability to incorporate conformal cooling channels directly within the tool body.
- Conformal Cooling: Unlike traditional drilled cooling channels, conformal channels follow the contours of the cutting edges, providing more efficient and uniform cooling. This reduces thermal stress, minimizes tool wear, and allows for higher cutting speeds and feed rates.
- Complex Channel Networks: 3D printing allows for the creation of complex internal channel networks that maximize coolant flow to critical areas of the cutting edge. This can significantly improve tool life, especially when machining difficult-to-cut materials.
- Optimized Coolant Outlet Placement: The location and orientation of coolant outlets can be precisely designed to ensure effective chip evacuation and cooling at the cutting zone.
- Enhancing Chip Evacuation: Efficient chip removal is crucial for preventing chip clogging, reducing cutting forces, and improving surface finish. Metal 3D printing enables the design of optimized chip evacuation features:
- Custom Flute Designs: The shape and size of flutes can be tailored to the specific material being machined and the type of chip produced. Wider flutes can improve chip flow for ductile materials, while narrower flutes may be better for brittle materials.
- Chip Breakers and Diverters: Integrated chip breakers and diverters can be designed to break long, stringy chips into smaller, more manageable pieces, preventing them from interfering with the cutting process.
- Surface Texturing: Applying specific surface textures to the flutes can further enhance chip evacuation by reducing friction between the chip and the tool surface.
By carefully considering these design aspects, engineers can leverage the unique capabilities of metal 3D printing to create custom cutting tools with significantly enhanced performance and longevity. Explore the possibilities of custom metal 3D printing.
Tolerance, Surface Finish, and Dimensional Accuracy in 3D Printed Tools – Achieving High Precision for Demanding Applications
Achieving the required tolerance, surface finish, and dimensional accuracy is paramount for the functionality and performance of custom cutting tools. Metal 3D printing technologies have advanced significantly in their ability to produce parts with tight specifications. However, understanding the capabilities and limitations of the chosen printing process and post-processing techniques is crucial.
- Tolerance Capabilities: The achievable tolerance in metal 3D printing depends on several factors, including the printing technology (e.g., Laser Powder Bed Fusion (LPBF) or Electron Beam Powder Bed Fusion (EBPBF)), the material used, part geometry, and build orientation.
- Типичные допуски: With optimized parameters and careful process control, LPBF can typically achieve tolerances in the range of ±0.05 to ±0.1 mm for critical dimensions. EBPBF may have slightly wider tolerances but is often preferred for larger parts and certain materials.
- Factors Affecting Tolerance: Thermal stresses during the printing process, material shrinkage upon solidification, and the layer thickness can all influence the final dimensional accuracy. Proper build orientation and support structure design are essential for minimizing these effects.
- Design for Tolerance: Designing parts with consideration for the inherent tolerances of the 3D printing process is crucial. This may involve incorporating features that allow for post-machining of critical surfaces if extremely tight tolerances are required.
- Surface Finish Characteristics: The surface finish of a 3D printed metal part is typically rougher than that achieved by traditional machining processes. The layer-by-layer build process results in a stepped surface texture.
- Typical Surface Roughness: As-printed surface roughness (Ra) can range from 5 to 20 µm, depending on the printing parameters and material.
- Impact on Cutting Tool Performance: A rough surface finish on a cutting tool can increase friction, leading to higher cutting forces, increased heat generation, and reduced tool life. It can also negatively impact the surface finish of the machined part.
- Улучшение качества поверхности: Post-processing techniques such as abrasive blasting, polishing, vibratory finishing, and CNC machining are commonly employed to improve the surface finish of 3D printed cutting tools to the required levels.
- Dimensional Accuracy Considerations: Dimensional accuracy refers to the degree to which the printed part matches the intended design dimensions.
- Calibration and Process Control: Accurate calibration of the 3D printer and precise control of the printing parameters are essential for achieving high dimensional accuracy.
- Material Shrinkage Compensation: Software tools can be used to compensate for material shrinkage during the printing process by slightly scaling the CAD model.
- Демонтаж опорной конструкции: The removal of support structures can sometimes affect the dimensional accuracy of the part, especially for complex geometries. Careful design of support structures is crucial to minimize this impact.
- Inspection and Verification: Post-printing inspection using coordinate measuring machines (CMMs) or other metrology equipment is essential to verify the dimensional accuracy of the 3D printed cutting tools.
While metal 3D printing offers significant advantages in terms of design freedom, achieving the required tolerance, surface finish, and dimensional accuracy for high-performance cutting tools often necessitates a combination of optimized printing parameters, careful design considerations, and appropriate post-processing techniques. Metal3DP’s advanced printing technology and expertise ensure the production of tools that meet stringent quality standards.
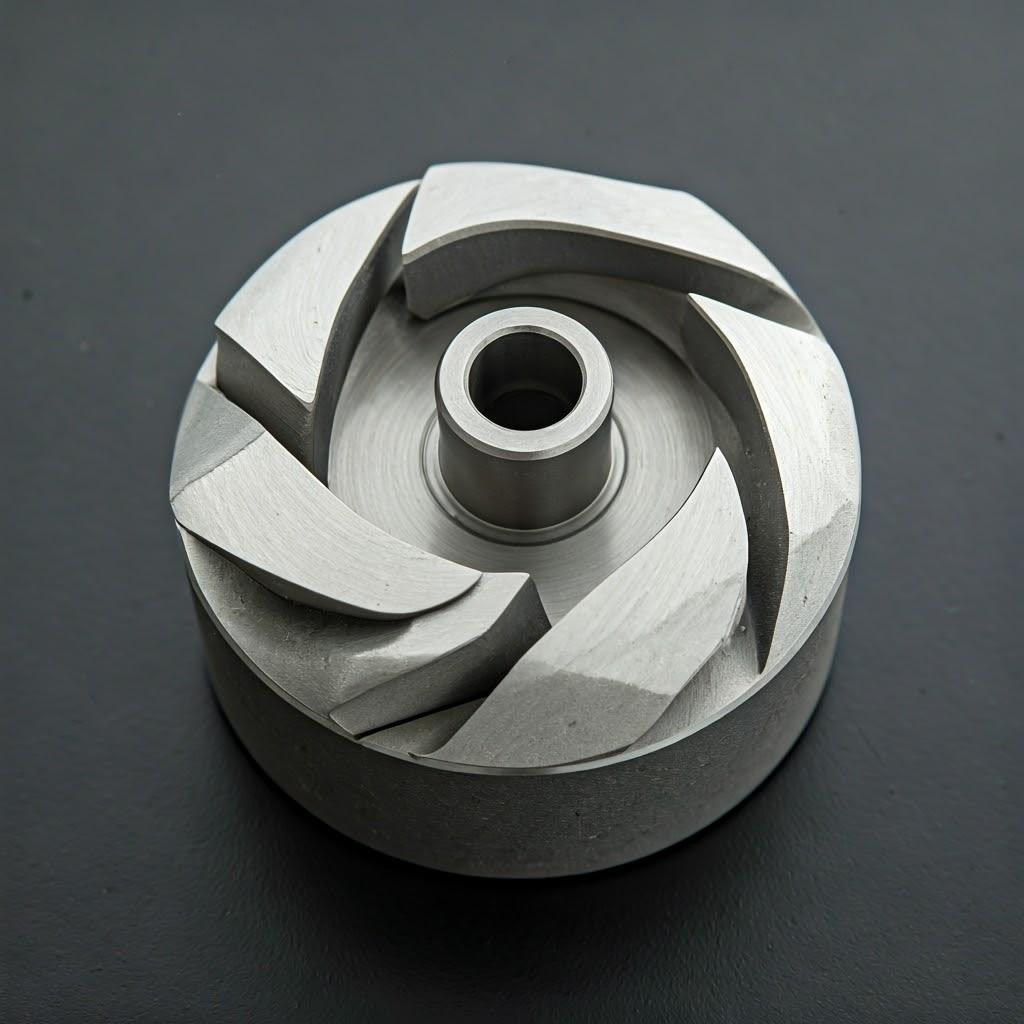
Post-Processing Requirements for Metal 3D Printed Cutting Tools – Heat Treatment, Coating, and Sharpening Techniques
While the metal 3D printing process creates the near-net-shape of the cutting tool, post-processing steps are often necessary to achieve the final desired properties, surface finish, and cutting edge geometry. These steps are crucial for optimizing the tool’s performance and extending its lifespan.
- Термообработка: Heat treatment is a critical post-processing step for metal 3D printed cutting tools, as it significantly influences the material’s microstructure, hardness, strength, and toughness.
- Снятие стресса: This process is often performed to reduce internal stresses that may have built up during the printing process, preventing warping or cracking.
- Hardening and Tempering: Depending on the material (e.g., H13 or M300), specific hardening and tempering cycles are applied to achieve the optimal balance of hardness and toughness required for cutting applications. For H13, this typically involves austenitizing followed by quenching and multiple tempering cycles. For M300, a similar process with potentially higher austenitizing temperatures and different tempering parameters is used to maximize hardness and red hardness.
- Vacuum Heat Treatment: To prevent oxidation and decarburization, heat treatment is often performed in a vacuum furnace, ensuring the integrity of the material’s surface.
- Покрытие поверхности: Applying a surface coating to 3D printed cutting tools can significantly enhance their wear resistance, reduce friction, and improve cutting performance, especially when machining difficult materials.
- PVD (Physical Vapor Deposition) Coatings: Coatings such as TiN (Titanium Nitride), TiAlN (Titanium Aluminum Nitride), and DLC (Diamond-like Carbon) are commonly applied using PVD techniques. These coatings offer high hardness, low friction coefficients, and excellent adhesion to the substrate material.
- CVD (Chemical Vapor Deposition) Coatings: CVD coatings, such as diamond coatings, can be used for specialized applications requiring extreme hardness and wear resistance, particularly when machining non-ferrous materials.
- Coating Selection: The choice of coating depends on the workpiece material, cutting speed, feed rate, and other machining parameters. Consulting with coating specialists is often recommended to select the most appropriate coating for a specific application.
- Sharpening and Edge Preparation: Achieving the precise cutting edge geometry is essential for the performance of any cutting tool. While 3D printing can create the near-net-shape, final sharpening and edge preparation are typically required.
- Измельчение: Precision grinding is used to create the final rake and relief angles, as well as the desired cutting edge sharpness. CNC grinding machines ensure high accuracy and repeatability.
- Honing: Honing is a micro-finishing process used to create a controlled radius or chamfer on the cutting edge. This improves edge strength, reduces chipping, and enhances tool life.
- Edge Rounding: In some cases, controlled edge rounding can be beneficial, especially for interrupted cuts or when machining abrasive materials.
The specific post-processing steps required for a 3D printed custom cutting tool will depend on the material, the intended application, and the desired performance characteristics. Collaboration with experienced metal 3D printing service providers like Metal3DP ensures that the appropriate post-processing techniques are applied to achieve optimal results.
Common Challenges and How to Avoid Them in 3D Printing Cutting Tools – Warping, Breakage, and Material Porosity Solutions
While metal 3D printing offers numerous advantages, there are also potential challenges that need to be addressed to ensure the successful production of high-quality custom cutting tools. Understanding these challenges and implementing appropriate mitigation strategies is crucial.
- Warping and Distortion: Thermal stresses that develop during the layer-by-layer printing process can lead to warping or distortion of the part, especially for complex geometries or large parts.
- Optimization of Build Orientation: Orienting the part strategically on the build platform can minimize the build-up of thermal stresses and reduce the likelihood of warping.
- Support Structure Design: Properly designed support structures can help to anchor the part and prevent distortion during printing. However, the supports themselves can also introduce stresses, so careful consideration of their placement and removal is necessary.
- Оптимизация параметров процесса: Adjusting printing parameters such as laser power, scan speed, and layer thickness can influence the thermal gradient and reduce internal stresses.
- Stress Relieving Heat Treatment: As mentioned earlier, a stress-relieving heat treatment after printing can effectively reduce residual stresses and minimize warping.
- Breakage and Low Toughness: If the material lacks sufficient toughness or if there are internal defects, the cutting tool may be prone to breakage under cutting forces.
- Выбор материала: Choosing the right metal powder with adequate toughness for the intended application is crucial. Both H13 and M300 offer good toughness, but the specific requirements of the application should be considered.
- Optimization of Heat Treatment: Proper heat treatment cycles are essential for achieving the optimal balance of hardness and toughness. Incorrect heat treatment can lead to a brittle material that is susceptible to fracture.
- Minimizing Internal Defects: Porosity and inclusions within the printed part can weaken it and increase the risk of breakage. Optimizing printing parameters and ensuring the quality of the metal powder are essential for minimizing these defects. Metal3DP’s high-quality metal powders are produced with advanced techniques to ensure high density and purity.
- Material Porosity: Porosity, or the presence of voids within the printed part, can negatively impact its strength, fatigue resistance, and cutting performance.
- Optimization of Printing Parameters: Achieving high density requires careful optimization of laser power, scan speed, powder layer thickness, and other printing parameters.
- Inert Build Atmosphere: Printing in an inert atmosphere (e.g., argon) minimizes oxidation and can improve the density of the printed part.
- Качество порошка: Using high-quality, spherical metal powders with good flowability, such as those offered by Metal3DP, is essential for achieving dense and homogeneous parts.
- Горячее изостатическое прессование (HIP): For critical applications requiring maximum density, Hot Isostatic Pressing (HIP) can be used as a post-processing step to eliminate internal porosity by applying high pressure and temperature.
By understanding these common challenges and implementing appropriate strategies for design, material selection, process optimization, and post-processing, manufacturers can effectively leverage metal 3D printing to produce high-performance custom cutting tools that meet their specific needs.
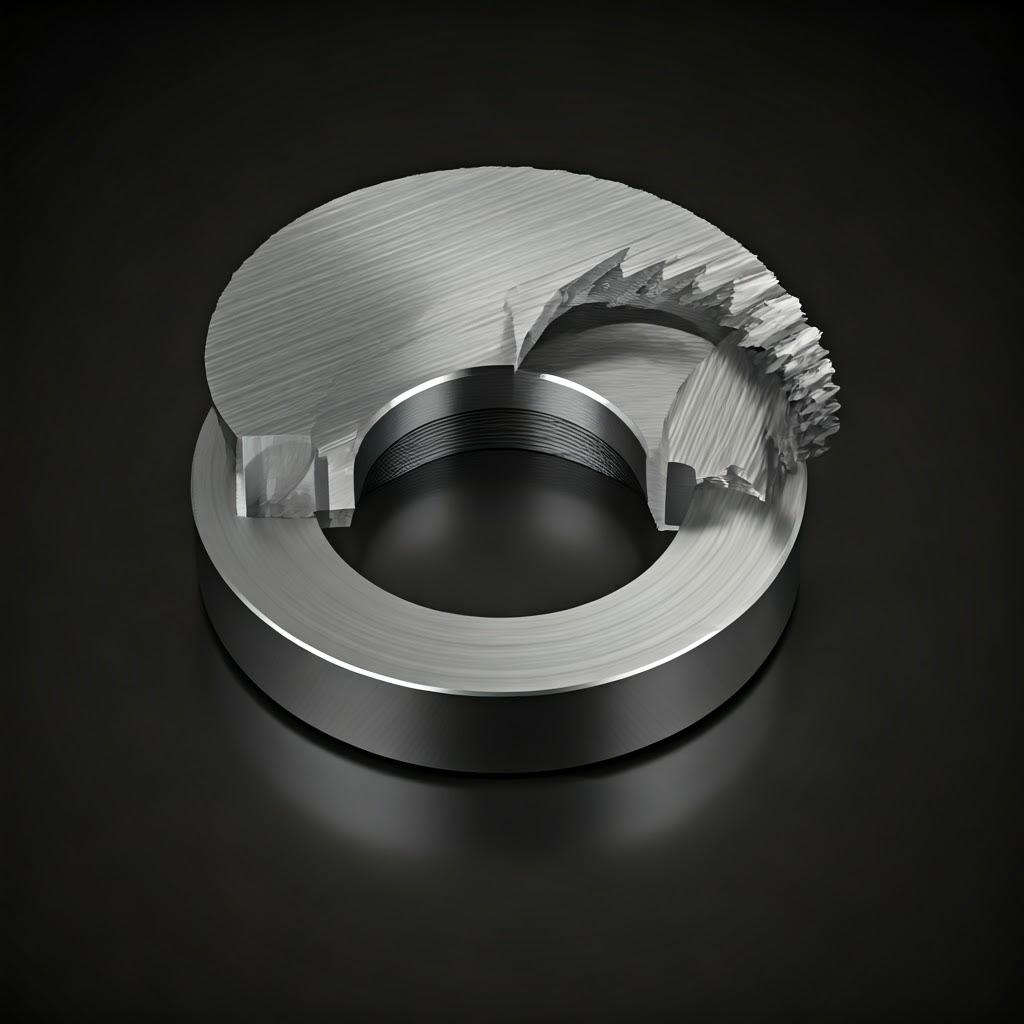
How to Choose the Right Metal 3D Printing Service Provider for Custom Tools – Key Considerations for Partner Selection
Selecting the right metal 3D printing service provider is crucial for obtaining high-quality custom cutting tools that meet your specific requirements. Consider the following key factors when evaluating potential partners:
- Material Capabilities: Ensure the service provider offers the specific metal powders required for your application, such as H13 and M300. Verify the quality and traceability of their materials. A provider like Metal3DP, which manufactures its own high-quality powders, can offer greater control over material properties and consistency.
- Printing Technology and Equipment: Understand the types of metal 3D printing technologies the provider utilizes (e.g., LPBF, EBPBF). Different technologies have varying strengths in terms of accuracy, build volume, and material compatibility. Inquire about the specifications and maintenance of their equipment to ensure reliable and high-quality printing. Metal3DP’s industry-leading printers are designed for accuracy and reliability.
- Design and Engineering Expertise: A good service provider should offer design consultation and engineering support to optimize your cutting tool designs for additive manufacturing. This includes guidance on geometry optimization, support structure design, and material selection. Their expertise can help you leverage the full potential of metal 3D printing.
- Post-Processing Capabilities: Inquire about the in-house post-processing services offered, such as heat treatment, surface finishing, and coating. A provider with comprehensive post-processing capabilities can streamline the production process and ensure the final tool meets your specifications.
- Quality Assurance and Certifications: Verify if the service provider has robust quality control procedures and relevant certifications (e.g., ISO 9001, AS9100 for aerospace). This ensures that the printed parts meet stringent quality standards and are suitable for demanding applications.
- Experience and Industry Focus: Look for a service provider with experience in producing cutting tools or serving similar industries (aerospace, automotive, medical, industrial manufacturing). Their understanding of industry-specific requirements and challenges can be invaluable.
- Lead Times and Production Capacity: Discuss lead times for design, printing, and post-processing. Ensure the provider has the production capacity to meet your volume requirements and delivery schedules.
- Cost Structure and Transparency: Obtain a clear breakdown of the costs involved, including design, material, printing, post-processing, and shipping. Understand their pricing model and ensure transparency in their quotes.
- Communication and Customer Support: Effective communication and responsive customer support are essential for a smooth and successful collaboration. Evaluate the provider’s responsiveness and willingness to address your questions and concerns.
By carefully considering these factors, you can choose a metal 3D printing service provider that can deliver high-performance custom cutting tools tailored to your specific needs.
Cost Factors and Lead Time for 3D Printed Custom Cutting Tools – Understanding Pricing and Production Efficiency
Understanding the factors that influence the cost and lead time for 3D printed custom cutting tools is essential for budgeting and project planning.
- Факторы стоимости:
- Материальные затраты: The cost of the metal powder is a significant factor. Advanced alloys like H13 and M300 can be more expensive than standard steels. The quantity of material used for each tool also impacts the overall cost.
- Design and Engineering Fees: If you require design optimization or engineering support from the service provider, these services will be factored into the cost.
- Время печати: The build time on the 3D printer is a key cost driver. Longer print times, influenced by part size, complexity, and build volume utilization, will increase the cost.
- Расходы на постобработку: Heat treatment, surface finishing, coating, and sharpening all add to the final cost. The complexity and number of post-processing steps will influence these costs.
- Machine and Labor Costs: The service provider’s operational costs, including machine depreciation, maintenance, and labor, are factored into their pricing.
- Quantity and Volume: While 3D printing can be cost-effective for low to medium volumes, economies of scale may favor traditional manufacturing for very high production runs of simpler tools. However, for complex custom tools, 3D printing can remain competitive even at higher volumes due to the elimination of tooling costs.
- Lead Time Factors:
- Design and Engineering Time: The time required for design optimization and preparation for 3D printing.
- Время печати: The duration of the 3D printing process, which depends on the size and complexity of the tool and the number of parts being printed simultaneously.
- Post-Processing Time: The time required for heat treatment, surface finishing, coating, and sharpening. Each of these steps can add several days to the overall lead time.
- Quality Control and Inspection: Time for thorough inspection and quality checks.
- Shipping Time: The time taken for the finished tools to be shipped to your location.
Metal 3D printing can offer faster lead times compared to traditional tooling for custom or low-volume production, as it eliminates the need for mold creation or complex fixturing. However, for very simple tools produced in high volumes, traditional methods might still be faster. It’s crucial to discuss lead times and production schedules with your chosen service provider to align with your project timelines. Связаться с Metal3DP to discuss your specific requirements and obtain a detailed cost and lead time estimate.
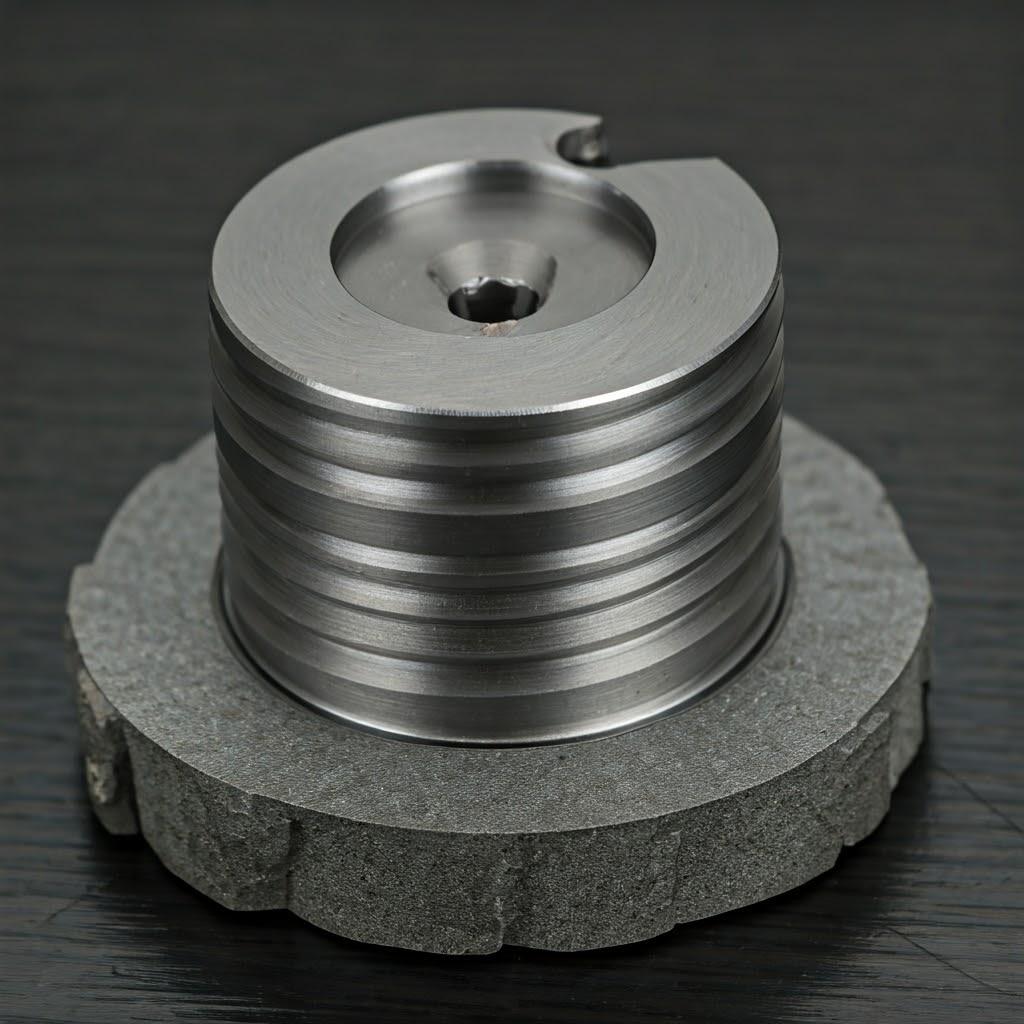
Frequently Asked Questions (FAQ) – Addressing Common Inquiries About Metal 3D Printed Cutting Tools
- Can metal 3D printed cutting tools achieve the same hardness and wear resistance as conventionally manufactured tools? Yes, with the right material selection (like H13 or M300 from Metal3DP) and appropriate post-processing, including heat treatment and coatings, metal 3D printed cutting tools can achieve and even exceed the hardness and wear resistance of conventionally manufactured tools. The ability to optimize the tool design and incorporate features like conformal cooling can further enhance their performance and lifespan.
- What are the typical applications where custom metal 3D printed cutting tools offer the most significant advantages? Custom metal 3D printed cutting tools are particularly advantageous for machining complex geometries, difficult-to-cut materials, and in applications requiring integrated features like conformal cooling channels. They are also beneficial for low to medium volume production, rapid prototyping, and creating tools tailored to very specific workpiece requirements in industries like aerospace, automotive, and medical.
- Is metal 3D printing cost-effective for producing custom cutting tools? The cost-effectiveness of metal 3D printing for custom cutting tools depends on factors such as the complexity of the tool, the material used, the production volume, and the required post-processing. For highly complex tools or low to medium production volumes, metal 3D printing can be very cost-competitive compared to traditional methods that may require expensive tooling. As volumes increase for simpler designs, traditional methods might become more economical. However, the added performance benefits and design flexibility often justify the cost of 3D printed custom tools.
Conclusion – Unleashing Innovation: The Future of Custom Cutting Tools with Metal 3D Printing
Metal 3D printing is revolutionizing the manufacturing of custom cutting tools, offering unprecedented design freedom, material optimization, and the potential for enhanced performance. By leveraging advanced materials like H13 and M300, and embracing innovative design principles such as conformal cooling and optimized chip evacuation, manufacturers can achieve new levels of efficiency and precision in their machining operations.
Такие компании, как Metal3DP, with their expertise in metal additive manufacturing equipment and high-quality metal powders, are empowering industries across aerospace, automotive, medical, and industrial manufacturing to unlock the full potential of this transformative technology. As metal 3D printing continues to advance, we can expect to see even more innovative and high-performance custom cutting tool solutions that drive manufacturing forward. Contact Metal3DP today to explore how their capabilities can power your organization’s additive manufacturing goals and redefine the future of your cutting tool applications.
Поделиться
MET3DP Technology Co., LTD - ведущий поставщик решений для аддитивного производства со штаб-квартирой в Циндао, Китай. Наша компания специализируется на производстве оборудования для 3D-печати и высокопроизводительных металлических порошков для промышленного применения.
Сделайте запрос, чтобы получить лучшую цену и индивидуальное решение для вашего бизнеса!
Похожие статьи
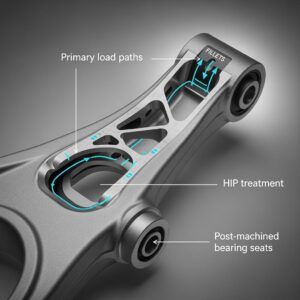
Metal 3D Printing for U.S. Automotive Lightweight Structural Brackets and Suspension Components
Читать далее "О компании Met3DP
Последние обновления
Наш продукт
CONTACT US
Есть вопросы? Отправьте нам сообщение прямо сейчас! После получения Вашего сообщения мы всей командой выполним Ваш запрос.
Получите информацию о Metal3DP
Брошюра о продукции
Получить последние продукты и прайс-лист