Custom Engine Pistons via High-Performance Metal 3D Printing
Оглавление
Introduction: Revolutionizing Piston Manufacturing with Metal Additive Manufacturing
The heart of nearly every internal combustion engine (ICE) is the piston. This unassuming component undergoes immense mechanical stress and thermal loads, translating the explosive force of combustion into the rotational power that drives vehicles, powers aircraft, and runs industrial machinery. For decades, the design and manufacture of pistons have relied on established methods like casting, forging, and precision machining. While effective, these traditional techniques often impose limitations, particularly when engineers push the boundaries of performance, efficiency, and customization. Enter metal additive manufacturing (AM), more commonly known as metal 3D-печать – a technology poised to fundamentally reshape how high-performance custom engine pistons are conceived, developed, and produced.
Metal AM is not merely a prototyping tool; it represents a paradigm shift in manufacturing capability. Unlike subtractive methods that carve material away from a solid block, or formative methods that shape material using molds or dies, additive manufacturing builds parts layer by intricate layer directly from digital designs using high-quality metal powders. This layer-wise approach unlocks unprecedented design freedom, enabling the creation of complex internal structures, optimized geometries, and lightweight components that were previously impossible or prohibitively expensive to manufacture. For engineers and procurement managers in demanding sectors like performance automotive, aerospace, and specialized industrial applications, metal AM offers a powerful new avenue to achieve superior engine performance, faster development cycles, and highly tailored solutions.
Imagine pistons with integrated, lattice-based cooling channels that drastically improve heat dissipation, allowing engines to run harder and more efficiently. Picture pistons topology-optimized for maximum strength at minimal weight, reducing reciprocating mass and enabling higher engine speeds. Envision the rapid production of custom piston variants for niche engine applications or performance tuning without the need for expensive tooling. This is the reality that metal 3D printing brings to custom engine piston manufacturing. It moves beyond the constraints of traditional processes, empowering engineers to design for function and performance above all else. Companies seeking a competitive edge, whether through enhanced power output, improved fuel economy, or unique engine configurations, are increasingly turning to metal AM suppliers who possess the expertise and advanced capabilities to deliver these next-generation components. The ability to work with advanced aluminum alloys like AlSi10Mg and high-strength options like A7075 further expands the possibilities, allowing for material selection tailored precisely to the specific thermal and mechanical demands of the application. This introductory exploration sets the stage for understanding how this disruptive technology is not just an alternative but often the superior choice for producing the custom engine pistons that will power the future. Partnering with experienced providers like Met3dp, who combine cutting-edge printing technology with deep materials science knowledge, is crucial for unlocking the full potential of AM in this critical application.
The journey into 3D printed pistons involves understanding the specific applications where it excels, the compelling reasons to adopt it over conventional methods, the critical role of material selection, and the nuances of designing, producing, and validating these advanced components. This guide serves as a comprehensive resource for technical professionals – engineers designing the next generation of engines and procurement managers sourcing the components that will bring those designs to life. We will delve into the technical specifics, explore the practical considerations, and highlight why metal AM is becoming an indispensable tool for achieving peak piston performance and manufacturing agility. The focus is shifting from mass production constraints to mass customization possibilities, driven by the precision and flexibility of additive techniques. For businesses involved in high-performance engine components, understanding and leveraging metal 3D printing is no longer optional; it’s becoming a strategic imperative for innovation and market leadership. Let’s explore how this technology transforms the humble piston into a highly engineered, performance-optimized component.
Applications: Where are 3D Printed Custom Pistons Making an Impact?
The versatility and unique advantages of metal additive manufacturing have opened doors for 3D printed custom pistons across a spectrum of demanding industries and specialized applications. While not yet a replacement for mass-produced pistons in standard passenger vehicles (due to cost at high volumes), metal AM shines where customization, high performance, rapid development, or solutions for unique challenges are paramount. Procurement managers and engineers seeking specialized piston suppliers for low-to-mid volume requirements or performance-critical applications are finding AM to be an increasingly viable and often superior solution.
Key Industries and Use Cases:
- High-Performance Automotive & Motorsports: This is arguably the most prominent field currently leveraging 3D printed pistons.
- Racing Teams (F1, Endurance, Drag Racing, etc.): Teams operate in an environment of constant iteration and optimization. Metal AM allows for rapid design changes and the production of lightweight, highly durable pistons with features like optimized crown shapes for specific combustion characteristics or intricate internal cooling galleries to manage extreme temperatures. The ability to produce small batches quickly without tooling investment is invaluable. B2B suppliers catering to motorsports often need to provide quick-turnaround, high-performance components, making AM an ideal fit.
- Aftermarket Performance Tuning: Tuners and engine builders often require custom pistons tailored to specific engine modifications (e.g., altered bore, stroke, compression ratio, or boost levels). AM enables the creation of bespoke piston designs in low volumes that would be economically unfeasible with forging dies or casting molds. This caters directly to a market demanding unique, high-strength components.
- Hypercars and Limited-Edition Vehicles: For manufacturers producing exclusive vehicles in limited numbers, the tooling costs associated with traditional piston manufacturing can be disproportionately high. Metal 3D printing provides a cost-effective way to produce high-performance pistons specifically designed for these unique powerplants.
- Aerospace and Aviation: Weight reduction and reliability are critical in aerospace.
- Беспилотные летательные аппараты (БПЛА): Drones, especially high-performance or long-endurance models, benefit significantly from weight savings. Topology-optimized 3D printed pistons made from lightweight aluminum alloys (like AlSi10Mg or potentially higher-strength variants like A7075 for specific needs) can reduce reciprocating mass, improving fuel efficiency and payload capacity.
- Specialized Aircraft Engines: This includes applications like auxiliary power units (APUs) or engines for experimental aircraft where unique designs or rapid prototyping are needed. AM allows engineers to explore novel piston concepts to enhance performance or meet specific operational requirements. Aerospace procurement demands rigorous quality control and material traceability, areas where established AM providers excel.
- Component Replacement for Legacy Systems: Sourcing parts for older or out-of-production aircraft engines can be challenging. Metal AM offers a pathway to reverse engineer and manufacture replacement pistons on-demand, ensuring the continued operation of valuable assets.
- Industrial Engines and Machinery:
- Specialized Equipment: Engines used in unique industrial applications (e.g., power generation, heavy machinery operating in extreme environments) may require pistons with specific material properties or design features not available off-the-shelf. AM provides the flexibility to create these custom solutions.
- Prototyping and Development: Before committing to large-scale production methods for a new industrial engine design, AM allows for the creation and testing of functional piston prototypes, accelerating the development cycle and reducing risks. Industrial procurement often involves long-term supply agreements, and AM suppliers capable of consistent quality are highly valued.
- Исследования и разработки:
- Engine Research Institutions: Universities and research labs studying combustion phenomena, alternative fuels, or novel engine architectures use metal AM to rapidly create experimental piston designs with integrated sensors or unique geometries for testing purposes.
Procurement Focus:
For procurement managers and buyers in these sectors, sourcing 3D printed pistons involves identifying suppliers with:
- Экспертиза материалов: Proven capability with relevant alloys like AlSi10Mg and A7075.
- Управление процессом: Robust quality management systems ensuring repeatable results.
- Technological Capability: Access to appropriate AM technologies (primarily Laser Powder Bed Fusion – L-PBF for fine features and good surface finish) and necessary post-processing equipment.
- Engineering Support: Ability to collaborate on design optimization for AM (DfAM).
- Industry Certifications: Relevant quality standards (e.g., ISO 9001, AS9100 for aerospace).
The demand is often for custom piston wholesale или specialized piston manufacturing services rather than off-the-shelf parts. Metal 3D printing service providers act as critical partners, enabling companies to access advanced manufacturing capabilities without direct investment in equipment. They function as high-tech foundries or machine shops, but with the unique advantages inherent in additive processes. Companies like Met3dp, with their focus on high-quality металлические порошки and advanced printing systems, are positioned to serve these demanding B2B markets effectively, offering both the materials and potentially the printing services or equipment necessary for these cutting-edge applications. The impact is clear: metal AM is moving beyond niche prototyping and becoming a vital manufacturing tool for critical, high-value components like custom engine pistons across multiple high-stakes industries.
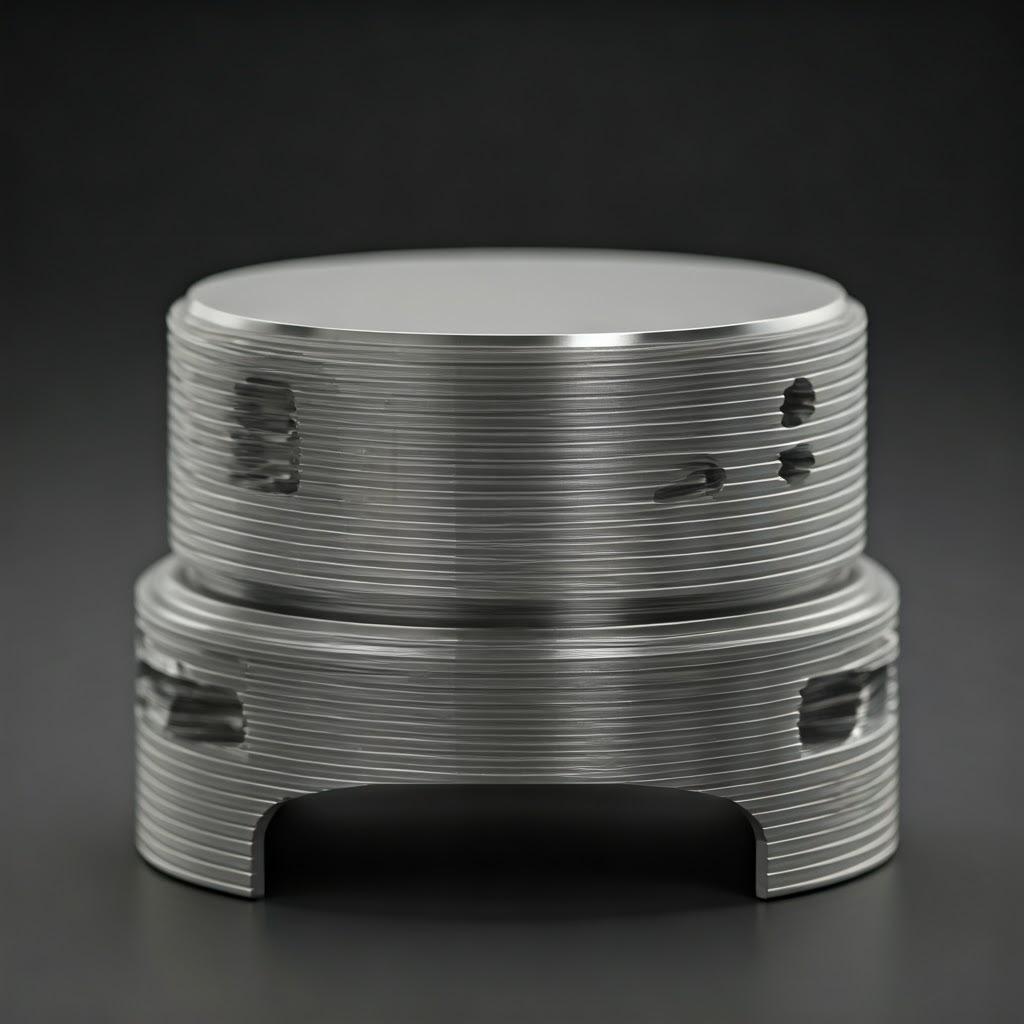
Why Metal 3D Printing for Custom Engine Pistons? Unlocking Performance Advantages
The decision to adopt metal additive manufacturing for custom engine pistons over established methods like forging, casting, or CNC machining is driven by a compelling set of technical and economic advantages, particularly relevant for performance-critical applications and low-to-medium volume production runs. While traditional methods have served the industry well for mass production, metal AM excels in scenarios demanding customization, optimized performance, and design complexity that conventional techniques struggle to achieve efficiently or at all. Engineers seeking maximum performance and procurement managers looking for agile, tooling-free manufacturing solutions find significant value in metal AM.
Comparison with Traditional Methods:
- Ковка: Produces very strong and durable pistons due to the aligned grain structure. However, it requires expensive dies, making it economical only for very high volumes. Design complexity is limited, especially regarding internal features. Lead times for new die creation are long.
- Кастинг: More suitable for complex shapes than forging and less expensive tooling, but generally results in lower strength and fatigue resistance compared to forging. Porosity can be a concern. Still requires molds, limiting design iteration speed and cost-effectiveness for low volumes.
- CNC Machining: Offers high precision and can create complex external shapes from billet material. However, it’s a subtractive process, leading to significant material waste. Creating complex internal features (like cooling channels) is extremely difficult or impossible. Machining time can be substantial for intricate designs.
Key Advantages of Metal 3D Printing (AM):
- Непревзойденная свобода дизайна: This is arguably the most significant advantage. AM builds parts layer by layer, freeing designers from the constraints imposed by molds, dies, or tool access.
- Complex Internal Geometries: Enables the integration of intricate internal cooling channels precisely placed to manage crown temperature and reduce hot spots. This can lead to improved combustion efficiency, increased knock resistance (allowing for higher compression ratios or boost), and enhanced piston durability under extreme loads. Lattice structures or topology-optimized internal ribs can be incorporated to add strength only where needed.
- Optimized External Shapes: Allows for highly customized crown shapes tailored to specific combustion chamber designs, complex skirt profiles to minimize friction, and lightweight wrist pin bosses.
- Significant Weight Reduction: AM facilitates topology optimization and the creation of lightweight lattice structures.
- Topology Optimization: Software algorithms can determine the most efficient material distribution to withstand specific loads, removing unnecessary mass while maintaining or even increasing strength in critical areas. This reduces reciprocating mass, allowing for higher engine speeds, improved throttle response, and reduced vibrations.
- Reduced Inertia: Lighter pistons place less stress on connecting rods, crankshafts, and bearings, potentially improving overall engine reliability or allowing other components to be lightened as well.
- Быстрое создание прототипов и итерации: Designs can go from CAD model to physical metal part in days rather than weeks or months (required for tooling). This allows engineers to quickly test multiple design variations, validate performance improvements, and significantly accelerate the engine development cycle. For racing teams or R&D departments, this speed is a critical competitive advantage.
- Консолидация частей: Complex assemblies can sometimes be redesigned and printed as a single, monolithic part. While less common for pistons themselves, features that might have been separate components could potentially be integrated, reducing assembly time and potential failure points.
- Эффективность материала: While AM isn’t waste-free (support structures, some powder loss), it is generally much less wasteful than subtractive CNC machining, especially for complex parts where a large percentage of the initial billet is removed. Unfused powder can often be recycled and reused, improving sustainability and reducing raw material costs per part, particularly with expensive alloys.
- Tooling Elimination: AM requires no part-specific tooling (dies or molds). This dramatically reduces upfront costs and lead times for custom or low-volume production runs. It makes manufacturing batches as small as a single unit economically viable, enabling true mass customization. Procurement managers benefit from avoiding large capital expenditures on tooling for specialized projects.
- Potential for Improved Thermal Management: Beyond complex cooling channels, the layer-wise process might allow for the future integration of different materials within a single piston (multi-material printing, although still largely developmental for pistons) or precisely controlling material density/microstructure in specific regions to optimize thermal conductivity or insulation.
Addressing B2B Needs:
For wholesale buyers or companies sourcing performance components, metal AM suppliers offer:
- Agility: Ability to respond quickly to custom design requests.
- Scalability (Low-to-Mid Volume): Efficient production without high tooling investment.
- Performance Edge: Access to designs and features not possible with traditional methods.
While the cost per part for AM might be higher than mass-produced forged or cast pistons, the total value proposition – encompassing design freedom, weight savings, performance gains, development speed, and tooling elimination – makes it highly attractive for the target applications. It shifts the manufacturing paradigm from “design for manufacturability” (constrained by traditional process limitations) towards “manufacture the optimal design” (enabled by AM’s flexibility). Leading providers in the металлическая 3D-печать sphere leverage these advantages to deliver components that redefine performance benchmarks.
Recommended Materials: AlSi10Mg and A7075 for High-Performance Pistons
Selecting the right material is fundamental to the success of any engineering component, and this holds especially true for high-performance engine pistons subjected to intense thermal and mechanical cycles. Metal additive manufacturing offers the ability to work with advanced alloys perfectly suited for these demanding conditions. Among the most commonly used and highly recommended metal powders for 3D printing custom pistons are the aluminum alloys AlSi10Mg and A7075, each offering a distinct set of properties tailored to different performance tiers and operating environments. The quality of the metal powder itself – its sphericity, particle size distribution, flowability, and chemical purity – is paramount for achieving dense, defect-free parts with consistent mechanical properties. This is where specialized powder manufacturers like Met3dp, utilizing advanced techniques like gas atomization and Plasma Rotating Electrode Process (PREP), play a crucial role in the supply chain for high-performance AM components.
1. AlSi10Mg: The Versatile Workhorse
AlSi10Mg is one of the most widely used aluminum alloys in metal additive manufacturing, particularly via Laser Powder Bed Fusion (L-PBF). It’s essentially an aluminum-silicon-magnesium casting alloy adapted for AM processes.
- Основные свойства:
- Хорошее соотношение прочности и веса: While not the highest strength aluminum alloy, it offers a good balance of strength and low density, crucial for reducing reciprocating mass.
- Отличная теплопроводность: Essential for dissipating heat away from the piston crown, reducing the risk of detonation and allowing for potentially higher compression ratios or boost levels.
- Хорошая коррозионная стойкость: Generally sufficient for typical engine environments.
- Weldability (Printability): Behaves well during the L-PBF process, exhibiting good fusion characteristics and relatively low tendency for cracking compared to some higher-strength aluminum alloys. This makes it reliable to print complex geometries.
- Поддается термической обработке: Mechanical properties can be significantly enhanced through post-print heat treatments (e.g., T6 solutionizing and aging) to achieve higher strength and hardness.
- Suitability for Pistons:
- Broad Applicability: Ideal for many high-performance automotive applications, aftermarket tuning, motorsports (where regulations allow), and general industrial engine prototyping.
- Cooling Channel Integration: Its good printability allows for the reliable creation of intricate internal cooling channels, leveraging a key advantage of AM.
- Эффективность затрат: Generally more established and potentially less expensive than higher-strength specialty alloys.
- Соображения:
- Its strength ceiling is lower than alloys like A7075, making it less suitable for the most extreme stress applications.
- Mechanical properties, particularly fatigue strength, can degrade more significantly at elevated temperatures compared to some steel or nickel-based alloys (though these are much heavier).
Table: Typical Properties of AM AlSi10Mg (Heat Treated – T6 Condition)
Недвижимость | Typical Value Range | Единица | Significance for Pistons |
---|---|---|---|
Плотность | ~2.67 | г/см³ | Low density reduces reciprocating mass |
Предельная прочность на разрыв | 380 – 450+ | MPa | Resistance to failure under tensile load |
Предел текучести (0,2%) | 240 – 300+ | MPa | Resistance to permanent deformation |
Удлинение при разрыве | 6 – 12+ | % | Ductility, ability to deform before fracturing |
Твердость | 100 – 120+ | ВН | Resistance to wear (especially in ring grooves/pin bore) |
Теплопроводность | 120 – 150 | Вт/(м-К) | Ability to dissipate heat from the combustion chamber |
Модуль упругости | ~70 | ГПа | Stiffness, resistance to elastic deformation |
Max Operating Temp. | ~150 – 200 (for sustained strength) | °C | Temperature limit for retaining significant strength |
Export to Sheets
(Note: Specific properties depend heavily on print parameters, build orientation, powder quality, and heat treatment protocol. These are representative values.)
2. A7075 (Aluminum-Zinc Alloy): The High-Strength Champion
A7075 is a well-known aerospace aluminum alloy, primarily containing zinc, magnesium, and copper. It’s renowned for its exceptionally high strength-to-weight ratio, comparable to some steels, but processing it via AM presents more challenges than AlSi10Mg.
- Основные свойства:
- Very High Strength: Significantly higher tensile and yield strength than AlSi10Mg, especially after appropriate heat treatment.
- Excellent Fatigue Strength: Resists failure under cyclic loading, a critical factor for piston longevity under high stress.
- Good Hardness: Contributes to wear resistance.
- Lower Thermal Conductivity: Compared to AlSi10Mg, its thermal conductivity is significantly lower.
- Проблемы, связанные с возможностью печати: More prone to cracking (hot tearing) during the L-PBF process due to its wide solidification range. Requires carefully controlled parameters, specialized parameter sets, or modified alloy compositions adapted for AM. Often benefits from specific platform heating strategies.
- Поддается термической обработке: Requires specific heat treatment cycles (e.g., T6, T7x) to achieve optimal strength and stress corrosion resistance.
- Suitability for Pistons:
- Extreme Performance: Targeted for applications demanding the absolute highest strength and fatigue resistance, such as top-tier motorsports (F1 potentially, where allowed), aerospace engines, or highly boosted drag racing applications where mechanical loads are paramount.
- Weight-Critical Aerospace: Where minimizing weight is the absolute priority and the high strength allows for thinner sections.
- Соображения:
- The lower thermal conductivity is a significant drawback for pistons, as it hinders heat dissipation from the crown. This disadvantage might be partially offset by AM’s ability to create highly efficient internal cooling channels, but it remains a critical design consideration.
- The increased difficulty in printing reliably means higher manufacturing costs and potentially longer lead times. Requires AM service providers with proven expertise in processing this specific alloy.
- Susceptibility to stress corrosion cracking needs careful management through proper heat treatment and potentially surface treatments.
Table: Typical Properties of AM A7075 (Heat Treated – T6 Condition)
Недвижимость | Typical Value Range | Единица | Significance for Pistons |
---|---|---|---|
Плотность | ~2.81 | г/см³ | Slightly denser than AlSi10Mg, but strength offsets this |
Предельная прочность на разрыв | 520 – 590+ | MPa | Very high resistance to tensile failure |
Предел текучести (0,2%) | 450 – 520+ | MPa | Very high resistance to permanent deformation |
Удлинение при разрыве | 5 – 10+ | % | Lower ductility compared to AlSi10Mg |
Твердость | 150 – 170+ | ВН | High hardness for wear resistance |
Теплопроводность | ~130 (Can vary significantly) | Вт/(м-К) | Lower than AlSi10Mg, potentially hindering heat dissipation |
Модуль упругости | ~72 | ГПа | Similar stiffness to AlSi10Mg |
Max Operating Temp. | ~120 – 150 (for sustained strength) | °C | Lower temperature capability for strength retention than AlSi10Mg |
Export to Sheets
(Note: Properties are highly dependent on AM process optimization for this challenging alloy, powder quality, and precise heat treatment. These are representative values.)
The Importance of Powder Quality (Met3dp’s Role):
Regardless of the chosen alloy, the final part quality begins with the powder. Inconsistent particle size, irregular shapes (low sphericity), poor flowability, internal porosity within powder particles, or impurities can lead to defects in the final printed piston, such as porosity, reduced density, poor surface finish, and inconsistent mechanical properties.
Met3dp addresses this critical need by employing industry-leading powder production technologies:
- Газовая атомизация: Utilizes optimized nozzle and gas flow designs to produce highly spherical metal powders with minimal internal porosity and satellites. Sphericity ensures good powder bed packing density and consistent powder flow during the recoating step in PBF machines.
- Плазменный вращающийся электродный процесс (PREP): Another advanced technique capable of producing exceptionally clean and spherical powders, often preferred for reactive materials or where the highest purity is required.
- Контроль качества: Rigorous testing ensures tight control over particle size distribution (PSD), chemical composition, flowability, apparent density, and morphology.
By providing high-quality, reliable AlSi10Mg, potentially developing optimized A7075 powders for AM, and offering a range of other advanced alloys (like Titanium alloys, CoCrMo, Steels, Superalloys), Met3dp empowers manufacturers and AM service providers to produce custom engine pistons that meet the stringent requirements of high-performance applications. Choosing a supplier who understands the critical link between powder characteristics and final part integrity is essential for B2B customers sourcing these advanced components.
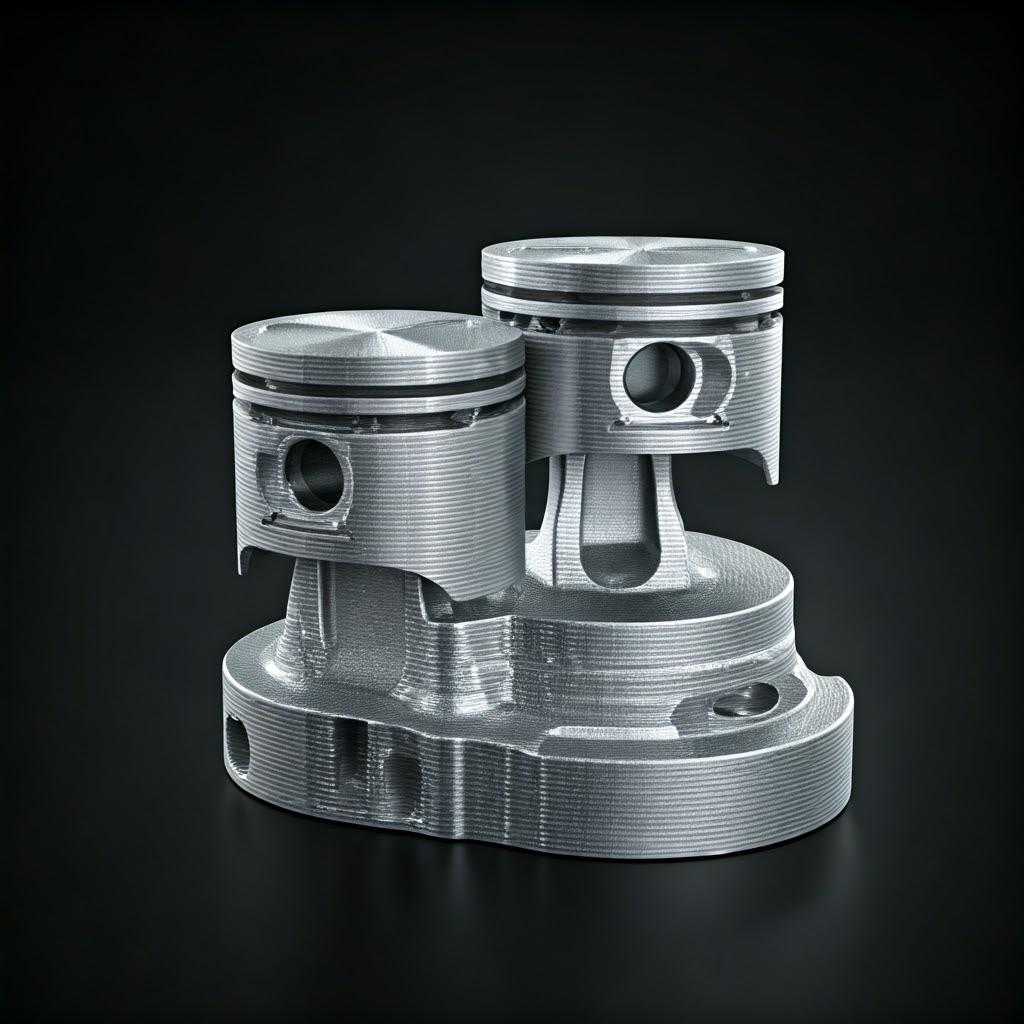
Design Considerations: Optimizing Piston Geometry for Additive Manufacturing
One of the most compelling reasons to utilize metal additive manufacturing for custom engine pistons is the extraordinary level of design freedom it offers. However, simply replicating a conventionally designed piston using AM often fails to leverage the technology’s true potential and can even introduce manufacturing challenges. Designing для Additive Manufacturing (DfAM) is crucial. This involves rethinking piston geometry to maximize performance benefits like weight reduction and improved thermal management while also considering the unique constraints and capabilities of the layer-by-layer building process. Engineers collaborating with AM service providers or utilizing in-house AM capabilities must embrace DfAM principles to create truly optimized pistons.
Leveraging Unprecedented Design Freedom:
- Complex Internal Cooling Channels: This is a standout capability of AM.
- Function: Efficiently extract heat from the hottest part of the piston – the crown and the area behind the ring grooves. This prevents overheating, reduces the likelihood of detonation (knock), allows for potentially higher compression ratios or boost pressures, improves lubricant performance by lowering oil temperatures, and increases piston durability.
- Дизайн: AM allows for channels that follow complex, conformal paths, optimized using Computational Fluid Dynamics (CFD) analysis. They can feature intricate internal turbulators or structures to enhance heat transfer, which are impossible to create via drilling or casting. Channels can be routed precisely where needed, unlike simple drilled holes in conventional pistons. Design variations include gallery cooling (a larger void behind the rings) or intricate networks of smaller channels directly under the crown surface.
- Example: A high-performance turbocharged engine piston could feature a network of 1-2mm diameter channels directly beneath the crown, fed by oil splashed from the crankcase or via dedicated oil jets, significantly lowering crown temperatures compared to a solid piston.
- Topology Optimization for Lightweighting:
- Function: Reduce piston mass while maintaining structural integrity under high combustion pressures and inertial loads. Lower reciprocating mass enables higher engine speeds, improves throttle response, reduces engine vibrations, and decreases stress on the connecting rod and crankshaft.
- Method: Software algorithms analyze the load paths (combustion pressure, inertia forces, thermal stresses) and iteratively remove material from non-critical areas, leaving behind an organic, load-bearing structure.
- Применение: This often results in pistons with highly optimized internal ribbing, thinner skirts in low-stress areas, and intricately shaped pin bosses, achieving weight reductions of 10-20% or more compared to traditional designs without compromising strength. The resulting shapes often resemble bone structures and are impossible to manufacture subtractively or via casting/forging.
- Optimized Crown and Skirt Geometry:
- Crown Shape: AM allows for highly specific crown shapes tailored to the engine’s combustion chamber geometry and fuel injection strategy. This can include complex bowls, valve reliefs with optimized profiles, and features to enhance swirl or tumble for better combustion efficiency.
- Skirt Profile: Skirt shapes can be optimized to minimize friction while maintaining stability within the cylinder bore. AM allows for variable skirt thickness and complex barrel or ovality profiles that might be challenging or time-consuming to machine traditionally. Asymmetric designs, optimized for thrust and anti-thrust sides, are easily realized.
- Integrated Features: While less common, small features like oil drainage holes, sensor mounts (for R&D pistons), or specific surface textures could potentially be integrated directly into the print, reducing post-processing steps.
DfAM Guidelines for Piston Printing:
While AM offers freedom, it has its own set of rules that designers must respect for successful and cost-effective printing:
- Толщина стенок: Minimum achievable wall thickness depends on the machine, material, and orientation (typically ~0.4-0.8mm), but designing slightly thicker walls (e.g., >1mm) where possible improves robustness and printability. Conversely, overly thick sections can accumulate residual stress. Variable thickness, enabled by AM, should be used strategically.
- Overhangs and Support Structures: Features angled less than ~45 degrees relative to the build plate typically require support structures to prevent collapse during printing.
- Design Impact: Supports consume extra material, add print time, require removal in post-processing (potentially leaving witness marks), and can be difficult to remove from internal channels.
- DfAM Strategy: Design to minimize the need for supports where possible. Orient the piston on the build plate strategically (often crown-down or pin-bore horizontal). Use self-supporting angles (>45 degrees) or design features like diamond or teardrop shapes for horizontal holes instead of perfect circles to make them self-supporting. Internal cooling channels must be designed with accessibility for powder removal and potentially support removal in mind, often incorporating specific drain/access holes.
- Residual Stress Management: The rapid heating and cooling inherent in L-PBF can build up internal stresses, potentially causing warping or cracking.
- DfAM Strategy: Avoid large, bulky sections where possible. Use topology optimization to create more skeletal structures. Incorporate smooth transitions between thick and thin sections. Consider stress-relief features if necessary, although careful process control and post-print heat treatment are the primary mitigation methods. Simulation software can predict stress concentrations and inform design modifications.
- Designing for Post-Processing: AM parts, especially pistons, rarely come off the printer ready to use.
- Machining Allowances: Critical surfaces like ring grooves, the pin bore, the top deck surface, and potentially skirt profiles often require final CNC machining for tight tolerances and specific surface finishes. Designers must add extra material (machining stock, e.g., 0.5-1.0mm) to these areas in the CAD model.
- Support Removal Access: Ensure adequate access for tools to remove support structures, especially internal ones.
- Удаление порошка: Unfused powder must be removed from the finished part, particularly from internal channels. Designs must include sufficiently large openings/drainage paths for powder evacuation. Trapped powder can add weight and potentially dislodge during operation.
Software Tools:
Modern CAD and simulation software plays a vital role:
- CAD: Standard CAD software is used for initial design.
- Topology Optimization Software: Tools like Altair Inspire, nTopology, Autodesk Generative Design, or Ansys Discovery analyze loads and generate optimized, lightweight forms.
- Simulation Software: Predicts thermal stresses, distortion, and potential print failures, allowing for design and orientation adjustments before printing (e.g., Ansys Additive Suite, Materialise Magics).
- Build Preparation Software: Used to orient parts, generate support structures, and slice the model into layers for the AM machine.
By embracing these DfAM principles, engineers can move beyond simple substitution and unlock the full performance potential offered by metal AM for custom engine pistons. Collaboration between design engineers and AM manufacturing experts (like those understanding various способы печати) is key to navigating these considerations effectively and achieving optimal results.
Achievable Precision: Tolerance, Surface Finish, and Dimensional Accuracy
A critical consideration for any functional engine component, especially a piston, is the achievable level of precision. Pistons require tight tolerances on several key features – ring grooves, pin bore diameter and location, overall diameter, compression height, and surface finish – to ensure proper sealing, efficient operation, and long-term durability. While metal additive manufacturing technologies like Laser Powder Bed Fusion (L-PBF) offer remarkable capabilities, it’s essential for engineers and procurement managers to understand the typical precision levels achievable “as-built” versus what requires post-processing, and the factors influencing these outcomes.
Typical Tolerances in Metal AM (L-PBF):
- General Dimensional Accuracy: As-built parts typically achieve tolerances in the range of ±0.1mm to ±0.3mm or ±0.1-0.2% of the dimension, whichever is larger. This level of accuracy is often sufficient for many features of the piston body but usually falls short for critical interfaces.
- Feature-Specific Tolerances: Smaller features or holes might achieve tighter tolerances (e.g., approaching ±0.05mm in some cases), but this is highly dependent on feature size, location, orientation, and machine calibration.
- Repeatability: With well-calibrated machines, optimized parameters, and consistent high-quality powder (a focus for suppliers like Met3dp), part-to-part repeatability is generally good, but slight variations can still occur.
Factors Influencing Tolerance and Accuracy:
- Калибровка машины: Regular calibration of the laser scanner system, Z-axis movement, and powder recoating mechanism is crucial.
- Laser Beam Spot Size: Finer laser spots allow for higher resolution but may slow down build speed.
- Толщина слоя: Thinner layers (e.g., 20-30 µm) generally produce better accuracy and surface finish but increase print time compared to thicker layers (e.g., 50-100 µm).
- Свойства материала: Each metal alloy has unique shrinkage characteristics during solidification and cooling, which must be compensated for in the build preparation software. Thermal conductivity also plays a role in heat buildup and potential distortion.
- Part Geometry and Size: Larger parts or parts with significant variations in cross-section are more prone to thermal distortion and deviation from the intended geometry.
- Build Orientation: The orientation of the piston on the build plate significantly impacts accuracy, surface finish on different facets, and the location and amount of support structures needed. Critical dimensions are often oriented parallel or perpendicular to the build plate for better control.
- Поддерживающие структуры: Supports prevent distortion during the build but can slightly affect the accuracy and surface finish of the areas they touch. Their removal can also impact dimensions if not done carefully.
- Тепловое управление: Build plate heating, process parameters (laser power, scan speed), and scan strategy all influence the thermal history of the part and thus its final accuracy and residual stress state.
Обработка поверхности (шероховатость):
- As-Built Surface Finish: The surface roughness (Ra) of as-built L-PBF parts is typically anisotropic and depends heavily on orientation:
- Top Surfaces: Generally smoother (Ra 5-15 µm).
- Vertical Walls: Show layer lines (Ra 8-20 µm).
- Up-facing Angled Surfaces: Relatively smooth.
- Down-facing (Overhang) Surfaces: Tend to be rougher due to the interaction with support structures or the partially melted powder beneath (Ra 15-30+ µm). Internal channels are particularly challenging to achieve a smooth finish in.
- Significance for Pistons: While the general as-built finish might be acceptable for some areas of the piston body, critical surfaces require much smoother finishes:
- Ring Grooves: Need smooth, precise surfaces (typically Ra < 0.8 µm) for proper ring sealing and low wear.
- Pin Bore: Requires a very smooth finish (Ra < 0.4 µm) and precise diameter for the wrist pin fit.
- Skirt:* Often requires a smooth finish (Ra < 1.6 µm, sometimes with specific textures) to minimize friction against the cylinder liner.
- Crown: Surface finish requirements vary; sometimes a slightly rougher surface is acceptable or even desirable for carbon adhesion, while other applications might require polishing.
- Achieving Required Finish: As-built AM surfaces nearly always require post-processing (machining, polishing, micro-machining) to meet the stringent surface finish requirements of critical piston features.
Ensuring Dimensional Accuracy: Metrology and Inspection:
Given the criticality of piston dimensions, rigorous inspection is non-negotiable.
- Coordinate Measuring Machines (CMM): Used for precise measurement of critical dimensions like pin bore diameter and position, ring groove width and depth, compression height, and overall diameter. Touch probes provide high accuracy.
- 3D Scanning: Optical or laser scanners capture the full geometry of the printed (and post-processed) part, allowing comparison to the original CAD model (GD&T – Geometric Dimensioning and Tolerancing). This is useful for verifying complex shapes and identifying overall distortion.
- Surface Roughness Testers (Profilometers): Measure the Ra or Rz values of critical surfaces after machining or polishing.
- Неразрушающий контроль (NDT): Methods like X-ray or CT scanning can be used to inspect internal features (like cooling channels) for blockages or defects and to detect internal porosity within the part structure.
Conclusion on Precision:
Engineers and procurement managers must recognize that metal AM for pistons is typically a near-net-shape process. While it excels at creating complex geometries and lightweight structures, it relies on conventional, high-precision post-processing methods like CNC machining to achieve the final tolerances and surface finishes required for critical features. Therefore, selecting an AM service provider involves not only evaluating their printing capabilities but also their integrated post-processing and metrology expertise. Understanding the achievable precision at each stage is key to setting realistic expectations and ensuring the final 3D printed piston meets all engineering specifications for reliable engine operation.

Post-Processing Pathway: From Printed Part to Performance Piston
A metal 3D printed piston doesn’t simply come off the build plate ready for installation. It represents an intermediate stage in a carefully orchestrated manufacturing workflow. Post-processing is not an optional add-on but an integral and often extensive series of steps required to transform the raw, as-built part into a functional, reliable, high-performance engine component. Understanding this pathway is crucial for estimating realistic lead times, costs, and for selecting manufacturing partners or suppliers with the necessary end-to-end capabilities. The journey involves stress relief, removal from the build plate, support structure removal, precision machining, surface treatments, and rigorous quality inspection.
The Typical Post-Processing Workflow:
- Stress Relief / Heat Treatment: This is often the first step after the build process concludes and the chamber cools, sometimes performed while the part is still attached to the build plate.
- Why: The rapid heating/cooling cycles inherent in L-PBF create significant residual stresses within the printed part. These stresses can cause distortion or cracking during subsequent handling, removal from the build plate, or machining. For aluminum alloys like AlSi10Mg and A7075, specific heat treatments are also essential to achieve the desired final mechanical properties (strength, hardness, ductility).
- Процесс: Involves heating the part(s) in a controlled atmosphere furnace to specific temperatures for defined durations, followed by controlled cooling (e.g., furnace cool, air cool, or quenching depending on the alloy and desired T-state like T6). The exact cycle (temperature, time, atmosphere) is critical and alloy-specific. For A7075, multiple steps including solutionizing, quenching, and aging are required.
- Importance: Failure to perform appropriate stress relief and heat treatment can lead to dimensional instability, premature failure, and parts not meeting mechanical specifications.
- Снятие со строительной плиты:
- Method: Typically done using wire Electrical Discharge Machining (wire EDM) or a bandsaw. Wire EDM provides a cleaner cut with less mechanical stress on the part.
- Consideration: Requires careful handling to avoid damaging the part. The surface where the part was attached to the plate will be rough and usually requires subsequent machining if it’s a functional surface.
- Демонтаж опорной конструкции:
- Why: Supports are necessary scaffolding during the build but must be removed afterward.
- Методы: Can range from manual breaking and cutting (for easily accessible supports) to more precise methods like CNC machining, grinding, or occasionally electrochemical machining for hard-to-reach areas.
- Задачи: Can be labor-intensive and time-consuming, especially for complex internal supports. Care must be taken not to damage the part surface. Support contact points (“witness marks”) often require blending or machining for cosmetic or functional reasons. Designing supports for easier removal (part of DfAM) is crucial.
- CNC Machining: This is arguably the most critical post-processing step for achieving the required precision on functional features.
- Target Areas:
- Ring Grooves: Machined to precise width, depth, and surface finish (Ra < 0.8 µm) for proper ring sealing and function.
- Pin Bore: Machined/honed to the exact diameter, roundness, cylindricity, and surface finish (Ra < 0.4 µm) required for the wrist pin fit. Position relative to the piston crown is also critical.
- Piston Crown/Deck: Often machined flat to achieve the precise compression height dimension. Valve reliefs may also be touched up.
- Skirt: Depending on the design and as-built accuracy/finish, the skirt profile might be precision turned or milled to achieve the required diameter, profile (barrel/ovality), and surface finish.
- Importance: AM alone cannot typically achieve the micron-level tolerances and specific finishes needed for these dynamic interfaces. CNC machining ensures the piston fits and functions correctly within the engine.
- Target Areas:
- Surface Treatments & Finishing: Depending on the application and material, additional treatments may be applied:
- Дробеструйное упрочнение: Introduces compressive residual stresses on the surface, improving fatigue life, particularly beneficial for high-stress applications or alloys like A7075.
- Polishing/Micro-Machining: Used to achieve very smooth surfaces on the skirt or crown if required for friction reduction or specific combustion characteristics.
- Покрытия:
- Износостойкие покрытия: Applied to ring grooves or skirts (e.g., hard anodizing, proprietary low-friction coatings) to enhance durability.
- Thermal Barrier Coatings (TBCs): Ceramic coatings applied to the piston crown to insulate the piston material from extreme combustion temperatures, protecting the aluminum alloy and potentially improving thermal efficiency.
- Dry Film Lubricants: Applied to skirts to reduce friction during break-in and operation.
- Cleaning and Final Inspection:
- Уборка: Thorough cleaning to remove any machining fluids, debris, or residual powder, especially from internal cooling channels.
- Final Inspection: Comprehensive dimensional check (CMM), surface finish verification, visual inspection, and potentially NDT (if required by specification) to ensure the finished piston meets all requirements before shipment or assembly.
Integrating Post-Processing for B2B Suppliers:
Procurement managers sourcing 3D printed pistons should look for suppliers who offer a complete, integrated manufacturing solution. Managing multiple vendors for printing, heat treatment, machining, and coating adds complexity, lead time, and potential points of failure. A vertically integrated supplier or one with strong, established partnerships for these post-processing steps can provide a streamlined workflow, better quality control, and a single point of accountability. The cost and time associated with post-processing are significant and must be factored into the overall project budget and timeline. It’s not uncommon for post-processing to account for 30-60% or even more of the total cost and time required to produce a finished 3D printed piston. Therefore, a clear understanding of this entire pathway is essential for effective project planning and supplier evaluation.
Navigating Challenges: Common Issues in 3D Printing Pistons and Solutions
While metal additive manufacturing unlocks incredible potential for custom engine pistons, the process is not without its challenges. Achieving consistent, high-quality results requires sophisticated equipment, carefully controlled processes, high-quality materials, and deep expertise. Understanding the common pitfalls and their mitigation strategies is crucial for both the engineers designing the pistons and the procurement managers sourcing them. Successfully navigating these challenges ensures the reliability and performance demanded of such critical components.
Common Challenges and Mitigation Strategies:
- Warping and Distortion:
- Cause: Uneven heating and cooling during the layer-wise fusion process induce residual stresses. If these stresses exceed the material’s yield strength at elevated temperature, the part can warp during the build or distort after removal from the build plate. This is particularly relevant for parts with large flat areas or significant changes in cross-section, like pistons.
- Mitigation Strategies:
- Simulation: Use process simulation software to predict areas of high stress and potential distortion before printing. Adjust orientation or support strategy accordingly.
- Build Plate Heating: Maintaining an elevated temperature on the build plate (common in many L-PBF systems) reduces thermal gradients and lowers residual stress.
- Optimized Scan Strategy: Using techniques like island scanning or checkerboard patterns breaks up long, continuous scan vectors, distributing heat more evenly and reducing stress buildup.
- Поддерживающие структуры: Strategically placed supports anchor the part to the build plate, physically restraining it from warping during the build. Robust supports are key.
- DfAM: Design parts with smoother transitions between sections; avoid large, solid blocks where possible (use topology optimization).
- Stress Relief Heat Treatment: Performing this step immediately after printing (ideally before support removal) is critical to relax internal stresses and stabilize the part’s geometry.
- Пористость:
- Cause: Small voids within the printed material. Can be caused by gas trapped within the powder or melt pool (gas porosity) or incomplete fusion between layers or scan tracks (lack-of-fusion porosity). Porosity reduces the density, strength, and fatigue life of the piston.
- Mitigation Strategies:
- Optimized Print Parameters: Laser power, scan speed, hatch spacing, and layer thickness must be carefully tuned for the specific alloy to ensure complete melting and fusion. Developing robust parameter sets is key.
- High-Quality Powder: Using powder with high sphericity, controlled particle size distribution, good flowability, and low internal gas content is crucial. Sourcing powder from reputable suppliers like Met3dp, who utilize advanced atomization processes (Gas Atomization, PREP) and rigorous quality control, significantly minimizes powder-related porosity risks.
- Inert Atmosphere Control: Maintaining a high-purity inert gas environment (Argon or Nitrogen) within the build chamber minimizes oxidation and contamination that can lead to gas porosity. Proper gas flow management is also important.
- Горячее изостатическое прессование (HIP): A post-processing step where the part is subjected to high temperature and high inert gas pressure. This can effectively close internal pores (both gas and lack-of-fusion), significantly improving density and mechanical properties. Often required for critical aerospace or high-fatigue applications.
- Cracking (Hot Tearing):
- Cause: Occurs during solidification in alloys with a wide freezing range (like A7075). Thermal stresses can pull apart the semi-solid structure in the melt pool’s mushy zone, leading to cracks.
- Mitigation Strategies:
- Alloy Selection/Modification: Using alloys known to be more “printable” like AlSi10Mg where requirements allow. Research is ongoing into modified versions of high-strength alloys (like A7075 variants with specific grain refiners) designed for better AM processability.
- Parameter Optimization: Adjusting laser parameters (e.g., using pulsed lasers, specific power modulation) and scan strategies can sometimes mitigate cracking tendencies.
- Build Plate Heating: Higher pre-heating can reduce thermal gradients.
- Управление процессом: Requires extremely careful control over all aspects of the printing process for sensitive alloys. Working with service providers with proven experience printing the specific challenging alloy is vital.
- Difficult Support Removal:
- Cause: Supports are essential but can be challenging to remove completely, especially from complex internal geometries like cooling channels or undercuts. Incomplete removal can leave obstructions or stress risers. Aggressive removal can damage the part surface.
- Mitigation Strategies:
- DfAM for Support Reduction: Design parts to be self-supporting where possible (using angles >45°, optimized orientation).
- Optimized Support Design: Use support generation software to create structures that are strong enough during the build but easier to remove (e.g., perforated supports, specific contact point shapes). Plan access routes for tools.
- Specialized Removal Techniques: Utilize appropriate tools, potentially including micro-machining or electrochemical methods for delicate or internal supports.
- Soluble or Breakaway Supports: Research is ongoing, but less common currently for the metal alloys used in pistons.
- Poor Surface Finish on Internal/Overhanging Features:
- Cause: Down-facing surfaces and internal channels inherently exhibit rougher surfaces in L-PBF due to the interaction with supports or partially sintered powder. This can impede flow in cooling channels or create stress concentrations.
- Mitigation Strategies:
- Orientation: Optimize part orientation to minimize critical surfaces being printed as down-facing overhangs.
- Parameter Tuning: Specific parameters can sometimes slightly improve down-skin finish, but limitations exist.
- Постобработка: Abrasive flow machining (AFM) or chemical polishing can sometimes be used to improve the surface finish of internal channels, though access can be a limitation. Designing channels large enough for effective cleaning and potential finishing is important.
- Acceptance: In some cases, the inherent internal surface roughness must be accepted and accounted for in performance simulations (e.g., adjusting CFD models for cooling channels).
Successfully producing high-performance 3D printed pistons requires a holistic approach that integrates robust design practices (DfAM), high-quality materials, precisely controlled printing processes, effective post-processing, and rigorous quality assurance. Partnering with knowledgeable AM service providers or investing in comprehensive in-house capabilities, including expertise in materials science and process optimization, is key to overcoming these challenges and realizing the full benefits of additive manufacturing for demanding engine applications.
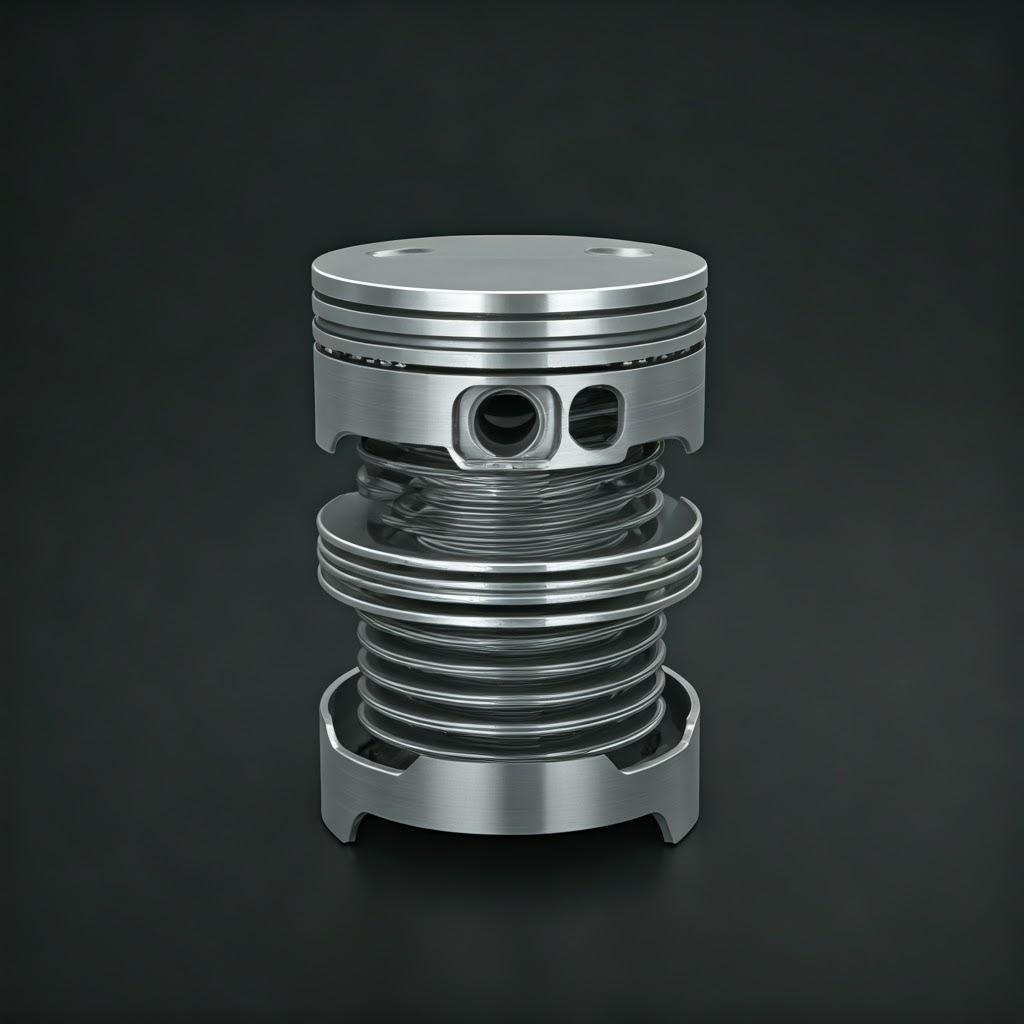
Choosing Your Partner: Selecting the Right Metal 3D Printing Service Provider
Embarking on a project involving metal 3D printed custom engine pistons requires more than just a cutting-edge design; it demands a manufacturing partner with the right expertise, technology, quality systems, and collaborative spirit. Selecting the appropriate metal additive manufacturing service provider or supplier is a critical decision that significantly impacts project success, component quality, cost-effectiveness, and time-to-market. For engineers and procurement managers, especially those operating under B2B frameworks requiring reliable, high-quality component sourcing, a thorough evaluation process is essential. This isn’t just about finding the lowest quote; it’s about establishing a strategic partnership with a supplier capable of meeting demanding technical requirements.
Key Criteria for Evaluating Metal AM Service Providers:
- Materials Expertise and Portfolio:
- Relevant Alloys: Does the provider have proven, documented experience printing the specific aluminum alloys required (e.g., AlSi10Mg, A7075)? Ask for parameter sheets, material test data, and examples of parts printed in these materials.
- Powder Quality Management: How do they source, handle, store, and recycle metal powders? Do they have robust quality control for incoming powder batches? Understanding their powder management protocol is crucial as powder quality directly impacts final part integrity. Providers like Met3dp, who manufacture their own high-quality powders using advanced methods, offer a distinct advantage in controlling this critical input variable.
- Broader Material Range: While you might need aluminum now, does the provider work with other metals (titanium, steel, superalloys)? This indicates broader expertise and potential for future projects.
- Technology and Capacity:
- Appropriate AM Technology: For pistons, Laser Powder Bed Fusion (L-PBF) is typically the most suitable technology due to its ability to produce fine features and good surface finish. Does the provider have well-maintained L-PBF machines from reputable manufacturers? What is the build volume capacity?
- Machine Fleet and Redundancy: How many suitable machines do they operate? Having multiple machines provides capacity for larger orders or faster turnaround and offers redundancy in case of maintenance issues.
- Process Monitoring: Do their machines incorporate in-situ process monitoring (e.g., melt pool monitoring)? This can provide valuable data for quality assurance.
- Quality Management Systems and Certifications:
- Fundamental Certifications: Is the provider ISO 9001 certified? This indicates a baseline commitment to quality management principles.
- Industry-Specific Certifications: Depending on your industry, look for relevant certifications:
- Аэрокосмическая промышленность: AS9100 is often required, demonstrating rigorous quality control processes tailored to aerospace demands.
- Автомобили: IATF 16949 might be relevant for higher-volume production or suppliers integrating into automotive supply chains.
- Медицина: ISO 13485 (less relevant for pistons, but indicates high-quality standards).
- Traceability: Can they provide full material and process traceability from raw powder to finished part? This is crucial for critical components.
- Integrated Post-Processing Capabilities:
- In-House vs. Outsourced: Does the provider perform essential post-processing steps (stress relief/heat treatment, CNC machining, surface finishing) in-house, or do they outsource? In-house capabilities generally offer better control, potentially faster lead times, and streamlined accountability.
- Экспертиза: Do they possess the necessary equipment (furnaces, multi-axis CNC machines, metrology labs) and skilled personnel for high-precision piston finishing? Verify their machining tolerances and surface finish capabilities.
- Engineering and DfAM Support:
- Collaboration: Are they willing and able to collaborate on design optimization for additive manufacturing (DfAM)? Can they provide feedback on printability, support strategy, and feature design based on your initial concepts?
- Expertise Level: Do they have experienced AM application engineers on staff who understand the nuances of designing and printing components like pistons?
- Track Record and Experience:
- Relevant Experience: Have they successfully produced similar components (e.g., other high-performance automotive parts, complex aluminum structures)? Ask for case studies or non-confidential examples.
- References: Can they provide references from satisfied customers in your industry or with similar applications?
- Company Stability and History: Consider the provider’s time in business and market reputation. Learning more about the company’s background, mission, and expertise, often found on their ‘О нас‘ page, can provide valuable context.
- Communication and Project Management:
- Responsiveness: How quickly and clearly do they respond to inquiries and technical questions?
- Project Management: Do they assign a dedicated point of contact for your project? How do they manage timelines and provide updates?
- Cost Structure and Transparency:
- Quoting Process: Is their quoting detailed and transparent, breaking down costs associated with material, printing, post-processing, and QA?
- Value Proposition: Evaluate cost not just in isolation but in the context of quality, capability, support, and lead time. The cheapest option is rarely the best value for critical components.
Table: Evaluation Checklist for AM Piston Supplier
Criterion | Основные вопросы | Важность |
---|---|---|
Материальная экспертиза | Experience with AlSi10Mg/A7075? Powder QA process? Material data available? | Очень высокий |
Technology & Capacity | L-PBF capability? Build volume? Machine maintenance? Process monitoring? Redundancy? | Высокая |
Системы качества | ISO 9001? AS9100/IATF 16949 (if needed)? Traceability procedures? | Очень высокий |
Постобработка | In-house heat treat/CNC? Machining accuracy/finish capability? Inspection equipment (CMM, etc.)? Coating partnerships? | Очень высокий |
Инженерная поддержка | DfAM expertise? Collaborative approach? Application engineers available? | Высокая |
Записи о пройденном пути | Experience with similar parts/industries? Case studies/references? Company stability? | Высокая |
Communication/Management | Responsiveness? Dedicated contact? Project updates? | Средний и высокий |
Стоимость и ценность | Transparent quoting? Competitive pricing relative to capability? Total value proposition? | Высокая |
Location & Logistics | Shipping costs/times? Facility audit possible? | Средний |
Export to Sheets
Choosing the right metal AM service provider is a strategic decision. For demanding applications like custom engine pistons, prioritize technical capability, quality assurance, and collaborative support over solely focusing on price. A strong partner will act as an extension of your engineering team, helping you leverage the full potential of additive manufacturing to achieve superior performance and reliability.
Understanding Investment: Cost Factors and Lead Times for 3D Printed Pistons
While metal 3D printing offers significant technical advantages for custom engine pistons, understanding the associated costs and typical manufacturing timelines is crucial for project planning, budgeting, and effective procurement. The economics of AM differ significantly from traditional manufacturing methods, particularly regarding volume sensitivity and the distribution of cost drivers. Lead times also follow a different pattern, often offering speed advantages for prototypes and low volumes but requiring careful planning for series production.
Primary Cost Drivers for Metal 3D Printed Pistons:
- Стоимость материала:
- Powder Price: High-quality, spherical metal powders optimized for AM (like AlSi10Mg or the more specialized A7075) are significantly more expensive per kilogram than bulk casting alloys or billet material used in machining. Powder cost is influenced by the alloy type, quality level, and purchase volume.
- Material Consumption (Buy-to-Fly Ratio): This includes the material making up the final part plus the material used for support structures plus any powder waste or loss during handling and processing. While unfused powder can often be recycled, there are limits to recyclability and associated costs for testing and requalification. The geometric complexity and need for supports directly impact material consumption. Lightweight, topology-optimized designs can help offset powder cost by using less material.
- Machine Utilization Cost: This is often the largest cost component, especially for complex or tall parts.
- Print Time: Calculated based on the part’s volume and, more significantly, its height (as each layer takes time to recoat and fuse). Complex geometries don’t necessarily increase print time proportionally if the overall volume/height remains similar. Factors include:
- Толщина слоя: Thinner layers = better resolution but much longer print times.
- Laser Scan Speed & Strategy: Optimized parameters balance speed and quality.
- Recoating Time: Time taken for the machine to deposit a new layer of powder.
- Machine Depreciation & Overheads: The high capital cost of industrial metal AM systems, plus maintenance, facility costs, energy consumption, and inert gas (Argon/Nitrogen) usage, are factored into an hourly machine rate.
- Print Time: Calculated based on the part’s volume and, more significantly, its height (as each layer takes time to recoat and fuse). Complex geometries don’t necessarily increase print time proportionally if the overall volume/height remains similar. Factors include:
- Расходы на оплату труда:
- Pre-Processing: CAD file preparation, build layout optimization, support structure generation, and slicing require skilled technicians/engineers.
- Machine Setup & Operation: Loading powder, setting up the build, monitoring the print process.
- Постобработка: This can be highly labor-intensive and includes:
- Part Removal & Cleaning: Removing parts from the build plate, initial powder removal.
- Термообработка: Furnace loading/unloading, monitoring.
- Удаление опоры: Often manual or semi-automated, can be time-consuming for complex parts.
- CNC Machining: Skilled machinists required for high-precision finishing.
- Отделка поверхности: Polishing, coating, etc.
- Inspection & Quality Control: CMM operation, NDT analysis, documentation.
- Quality Assurance & Inspection:
- Metrology: Time and equipment cost for CMM measurements, 3D scanning.
- Неразрушающий контроль (NDT): Costs associated with X-ray or CT scanning if required for internal integrity checks.
- Material Testing: Destructive testing of sample coupons printed alongside the parts (e.g., tensile tests) adds cost but ensures material properties meet specifications.
Cost Comparison: AM vs. Traditional Methods:
- Low Volume (Prototypes, 1-100 parts): AM is often significantly менее дорогой than forging (due to high tooling die costs) or casting (due to mold costs). It can be competitive with or slightly more expensive than CNC machining from billet, but offers far greater geometric freedom.
- Medium Volume (100s – low 1000s parts): The cost comparison becomes more complex. Tooling costs for forging/casting start to amortize, potentially making them cheaper per part. However, if AM enables significant performance gains (e.g., weight reduction leading to fuel savings or higher speeds) or allows for designs impossible otherwise, the total value might still favor AM.
- High Volume (Many 1000s+ parts): Traditional mass production methods like forging and casting are almost always more cost-effective per part due to economies of scale. AM is generally not competitive for standard, high-volume piston production currently.
Table: Cost Driver Summary
Cost Category | Primary Factors | Volume Sensitivity | Примечания |
---|---|---|---|
Материал | Powder cost (€/kg), Part volume, Support volume, Waste/Recycling | Moderate (Powder cost varies) | High-quality powder is expensive but crucial for part integrity. |
Machine Time | Part height, Part volume, Layer thickness, Machine hourly rate (€/hr) | Low (Rate is fixed) | Often the dominant cost factor for AM parts. |
Labor (Pre/Post) | Design complexity (supports), Post-processing needs (machining, finishing) | High (More parts = more labor) | Post-processing labor can be a very significant portion of total cost. |
Обеспечение качества | Level of inspection required (Metrology, NDT, Testing) | Умеренно-высокий | Critical parts require more extensive QA, adding cost. |
Инструментальная оснастка | N/A (Major advantage of AM) | Н/Д | Significant savings compared to forging/casting for low volumes. |
Export to Sheets
Lead Times for 3D Printed Pistons:
Lead time is the total time from order placement to part delivery. For AM pistons, it comprises several stages:
- Order Processing & Preparation (1-3 days): Final design checks, quote confirmation, build file preparation, scheduling machine time.
- Printing (1-5+ days): Highly dependent on piston height, build volume utilization (printing multiple parts simultaneously), and layer thickness. A single complex piston or a small batch might take 24-72 hours or more to print.
- Cooling & Depowdering (0.5-1 day): Allowing the build chamber and parts to cool safely, removing bulk powder.
- Heat Treatment / Stress Relief (1-3 days): Furnace cycle time, including heating, soaking, and controlled cooling.
- Support Removal & Machining (2-7+ days): Can be a bottleneck depending on complexity and required precision. Multiple setups on CNC machines might be needed.
- Surface Finishing / Coating (1-5 days): Dependent on the specific treatments required.
- Inspection & Shipping (1-2 days): Final QA checks, packaging, and transit.
Typical Total Lead Times:
- Prototypes (1-5 units): Often achievable in 1 to 3 weeks, depending on complexity and post-processing needs. The ability to go directly from CAD to part offers a significant speed advantage over tooling-based methods.
- Low Volume Production (10-100 units): Обычно варьируется от 3 to 8 weeks, depending on capacity, batch optimization, and the extent of post-processing and QA required for each part.
Factors Influencing Lead Time:
- Часть сложности: More complex designs may require longer print times and more intricate post-processing.
- Quantity Ordered: Larger batches take longer to print and process.
- Требования к постобработке: Extensive machining, multiple coatings, or rigorous NDT add significant time.
- Supplier Capacity: Current workload and machine availability at the service provider.
- Urgency: Expedited services are often available but come at a premium cost.
Understanding these cost factors and lead time components allows for better budgeting, realistic project scheduling, and informed decisions when comparing AM to traditional manufacturing routes for custom engine pistons. Engaging with potential suppliers early to get detailed quotes and timeline estimates is highly recommended.
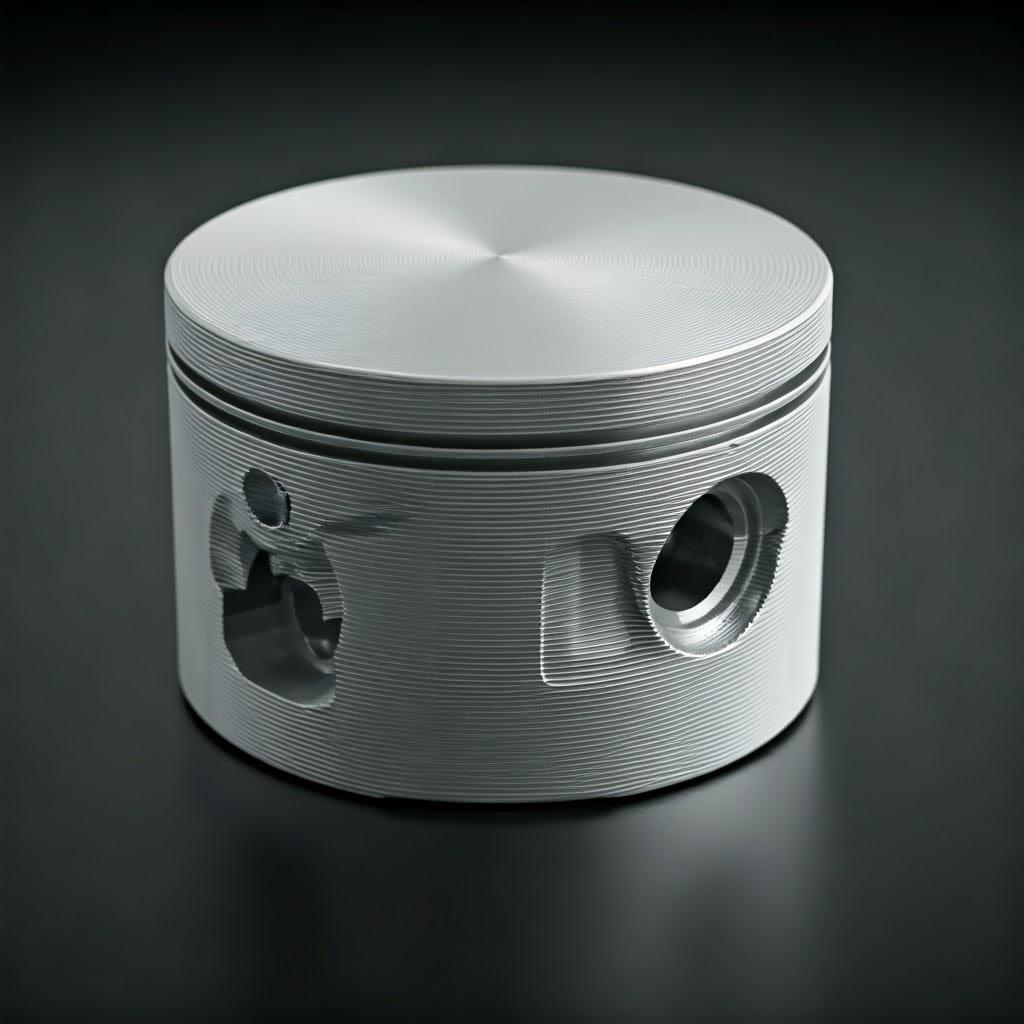
Frequently Asked Questions (FAQ) about 3D Printed Custom Pistons
As metal additive manufacturing gains traction for producing high-performance components like custom pistons, engineers, designers, and procurement managers often have specific questions. Here are answers to some frequently asked questions:
1. How strong are 3D printed aluminum pistons compared to forged ones?
This is a nuanced question.
- Свойства материала: Forged aluminum alloys generally exhibit superior fatigue strength and ductility due to their wrought microstructure with aligned grain flow. As-printed L-PBF aluminum alloys (like AlSi10Mg or even A7075) typically have fine-grained, equiaxed microstructures. After optimal heat treatment, 3D printed AlSi10Mg can achieve tensile and yield strengths comparable to some lower-strength forged alloys, while heat-treated AM A7075 can approach the strength levels of commonly forged piston alloys like 2618 or 4032. However, fatigue properties might still favor the forged counterpart if comparing identical, simple geometries.
- Design Advantages: The key strength of AM lies in оптимизация дизайна. 3D printing allows for topology-optimized designs that place material only where needed, creating lightweight structures with comparable or even superior stiffness and structural integrity under specific load cases compared to a bulkier forged design. Furthermore, the ability to integrate highly efficient internal cooling channels can significantly reduce operating temperatures, lowering thermal stresses and potentially allowing the AM piston (even if made from a slightly less fatigue-resistant base material) to outperform a hotter-running forged piston in terms of detonation resistance and overall durability in demanding applications.
- Постобработка: Processes like Hot Isostatic Pressing (HIP) can be applied to AM pistons to close internal porosity, further improving density and enhancing fatigue properties, bringing them closer to wrought material characteristics.
- Заключение: While a direct material-to-material comparison might show forged alloys having an edge in fatigue, the design freedom offered by AM enables performance gains (cooling, lightweighting) that can result in a 3D printed piston offering superior overall performance and durability in a specific engine application compared to a conventionally designed forged piston. Careful engineering and material selection are key.
2. What is the typical cost difference between a 3D printed custom piston and a traditionally manufactured one?
The cost difference depends heavily on the production volume и сложность конструкции:
- Prototypes & Very Low Volume (e.g., 1-20 units): 3D printing is often significantly дешевле because it eliminates the extremely high upfront costs of forging dies or casting molds (which can run into tens of thousands of dollars/euros). CNC machining from billet might have comparable costs in this range, but AM allows for more complex geometries.
- Low-to-Medium Volume (e.g., 20-500 units): This is the “crossover” zone. As volume increases, the per-part cost of forging/casting decreases as tooling costs are amortized. The per-part cost of AM remains relatively stable (dominated by machine time and labor). In this range, AM might be more expensive per part, but the decision often hinges on factors beyond direct cost: Does AM enable performance-enhancing designs (cooling, lightweighting) not possible otherwise? Is the speed of iteration or ability to customize designs critical? Is the total lifetime value (e.g., fuel savings from lighter weight) considered?
- High Volume (e.g., 1000+ units): Traditional methods (forging, casting) are almost always more cost-effective per part due to established economies of scale. AM is generally not competitive for mass-produced standard pistons.
- Complexity Factor: Highly complex piston designs (e.g., with intricate internal cooling) might be relatively efficient to produce via AM but extremely expensive or impossible via traditional methods, shifting the cost balance even at slightly higher volumes.
- Заключение: AM provides significant cost savings for custom, low-volume pistons by eliminating tooling. For larger volumes, traditional methods are usually cheaper per piece, but AM’s value lies in enabling advanced designs and customization.
3. Can complex internal cooling channels really be printed reliably?
Yes, reliably printing complex internal cooling channels is one of the primary advantages and drivers for using metal AM for high-performance pistons.
- Process Capability: L-PBF technology can create intricate, freeform channels with diameters down to ~1mm or even slightly less, following optimized paths determined by CFD analysis.
- Задачи: Key challenges include ensuring complete powder removal from these channels after printing and managing the surface finish inside the channels (which tends to be rougher than external surfaces). Supports might be needed within larger channels, requiring careful design for removal.
- Solutions: Designing channels with adequate openings for powder drainage and cleaning access is crucial (DfAM). Techniques like abrasive flow machining (AFM) or chemical polishing can sometimes be used to improve internal surface finish if required, though access is key. Robust process control and quality checks (like CT scanning) ensure channels are open and free from defects.
- Преимущества: Despite the challenges, the performance benefits – significantly improved heat dissipation, reduced crown temperatures, increased knock resistance, enhanced durability – make the effort worthwhile for demanding applications. Many successful examples exist in motorsports and aerospace.
4. What quality checks are performed on 3D printed pistons?
Given the critical nature of pistons, rigorous quality assurance is essential. A multi-stage approach is typically used:
- Powder Quality Control: Verifying the chemical composition, particle size distribution, morphology, and flowability of incoming powder batches.
- Process Monitoring: Using in-situ monitoring tools (if available) to track key process parameters during the build (e.g., melt pool temperature, laser power).
- Dimensional Metrology: Precise measurement of critical dimensions using CMM (Coordinate Measuring Machine) after printing and especially after final machining. 3D scanning can be used for comparing overall geometry to CAD.
- Surface Finish Measurement: Using profilometers to verify the roughness (Ra) of critical surfaces like ring grooves, pin bore, and skirts after finishing operations.
- Неразрушающий контроль (NDT):
- Computed Tomography (CT) Scanning / X-Ray: Highly valuable for inspecting internal features (like cooling channels) for blockages or defects, and for detecting internal porosity or inclusions within the piston structure without destroying the part.
- Dye Penetrant or Magnetic Particle Inspection: Can be used to detect surface-breaking cracks, though less common for internal defects.
- Material Property Verification: Printing standardized test specimens (e.g., tensile bars) alongside the actual pistons during the build process. These specimens undergo destructive testing (tensile tests, hardness tests) to verify that the material properties of the build batch meet the required specifications after heat treatment.
- Visual Inspection: Thorough visual checks at various stages for any obvious flaws or inconsistencies.
- Documentation & Traceability: Maintaining comprehensive records linking powder batches, machine parameters, post-processing steps, and inspection results to each specific piston or batch.
This comprehensive suite of checks ensures that the final 3D printed pistons meet the demanding dimensional, material property, and internal integrity requirements for reliable engine performance.
Conclusion: The Future of Piston Performance is Additive
The journey through the world of custom engine pistons manufactured via metal additive manufacturing reveals a technology that is not just viable, but truly transformative. Moving beyond the constraints of traditional forging, casting, and machining, metal 3D printing unlocks a new frontier in piston design and performance, particularly for demanding applications in high-performance automotive, motorsports, aerospace, and specialized industrial sectors.
The ability to create pistons with intricate internal cooling channels tailored for optimal thermal management, topology-optimized structures delivering unprecedented strength-to-weight ratios, and highly customized geometries perfected for specific engine requirements represents a fundamental shift in engineering possibilities. By leveraging advanced aluminum alloys like the versatile AlSi10Mg or the high-strength A7075, combined with rigorous process control and essential post-processing steps, AM delivers components capable of pushing engine performance, efficiency, and durability to new heights.
While challenges related to cost at high volumes, precision limitations requiring post-machining, and the need for specialized expertise exist, the advantages offered by AM for low-to-medium volume custom piston production are undeniable. The elimination of expensive tooling, the speed of iteration for prototyping and development, and the sheer design freedom empower engineers and manufacturers to innovate faster and achieve performance levels previously unattainable.
Choosing the right manufacturing partner – one with deep expertise in materials science, DfAM principles, robust quality systems, and integrated post-processing capabilities – is paramount to harnessing the full potential of this technology. As metal AM processes continue to mature, costs decrease, and material options expand, its role in producing critical engine components like pistons is set to grow significantly.
For engineers striving for the next leap in engine performance and procurement managers seeking agile, cutting-edge manufacturing solutions for specialized components, metal additive manufacturing offers a compelling pathway forward. The future of high-performance custom pistons is intricately linked with the layer-by-layer precision and design freedom of additive manufacturing.
Ready to explore how metal 3D printing can revolutionize your next engine project? Contact the experts at Met3dp today to discuss your custom piston requirements and discover how our comprehensive solutions, from advanced metal powders to potential manufacturing partnerships, can power your innovation.
Поделиться
MET3DP Technology Co., LTD - ведущий поставщик решений для аддитивного производства со штаб-квартирой в Циндао, Китай. Наша компания специализируется на производстве оборудования для 3D-печати и высокопроизводительных металлических порошков для промышленного применения.
Сделайте запрос, чтобы получить лучшую цену и индивидуальное решение для вашего бизнеса!
Похожие статьи
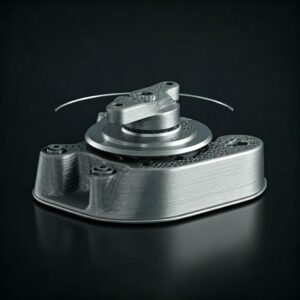
3D-печатные крепления для автомобильных радарных датчиков: Точность и производительность
Читать далее "О компании Met3DP
Последние обновления
Наш продукт
CONTACT US
Есть вопросы? Отправьте нам сообщение прямо сейчас! После получения Вашего сообщения мы всей командой выполним Ваш запрос.
Получите информацию о Metal3DP
Брошюра о продукции
Получить последние продукты и прайс-лист
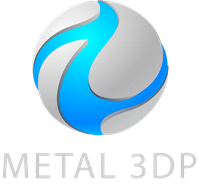
Металлические порошки для 3D-печати и аддитивного производства