3D Printed Fluid Line Clamps
Оглавление
Введение
In the demanding realm of aerospace engineering, every component plays a pivotal role in ensuring the safety, efficiency, and performance of aircraft and spacecraft. Among these critical elements are fluid line clamps, seemingly simple yet indispensable devices responsible for securing vital fuel lines, hydraulic conduits, coolant systems, and other fluid transfer networks. These clamps must withstand extreme temperatures, high pressures, and significant vibrations while maintaining structural integrity and preventing leaks. Traditionally, these components have been manufactured using conventional methods like machining or casting. However, the landscape of aerospace manufacturing is rapidly evolving, with металл 3D-печать услуги emerging as a transformative force. This advanced manufacturing technique, also known as additive manufacturing, offers unprecedented opportunities to optimize the design, material selection, and production of aerospace fluid line clamps, paving the way for lighter, stronger, and more efficient aircraft and spacecraft. As the aerospace industry continues to push the boundaries of innovation, the adoption of аддитивное производство металлов for critical components like fluid line clamps is poised to accelerate, offering solutions that were previously unattainable with traditional manufacturing processes. Companies like Metal3DP are at the forefront of this revolution, providing cutting-edge metal 3D printing equipment and high-performance металлические порошки tailored for demanding aerospace applications.
What are 3D Printed Fluid Line Clamps Used For?
Aerospace fluid line clamps, whether produced through traditional methods or advanced металлическая 3D-печать, serve a fundamental purpose: to securely fasten and support fluid-carrying lines within aircraft and spacecraft. Their role is critical for maintaining the integrity and functionality of various essential systems. Here’s a more detailed breakdown of their applications:
- Fuel Lines: Ensuring the safe and reliable transport of fuel to the aircraft engines is paramount. Fluid line clamps securely hold these lines in place, preventing movement, vibration-induced wear, and potential leaks that could have catastrophic consequences. The lightweighting potential offered by аддитивное производство can be particularly beneficial here, contributing to overall fuel efficiency.
- Hydraulic Systems: Aircraft rely heavily on hydraulic systems for controlling flight surfaces, landing gear, brakes, and other critical functions. Robust fluid line clamps are essential for securing the high-pressure hydraulic lines, ensuring the integrity of the system under demanding operational conditions. The ability to create complex geometries with металлическая 3D-печать allows for optimized clamp designs that can better withstand these pressures.
- Coolant Lines: Managing temperature within aircraft systems is crucial for the performance and longevity of electronic components and engines. Fluid line clamps secure the lines that circulate coolants, preventing disconnections or damage due to vibration or thermal expansion.
- Environmental Control Systems (ECS): These systems regulate cabin pressure, temperature, and air quality. Fluid lines within the ECS need to be securely fastened to ensure proper operation and prevent leaks of conditioned air or other fluids.
- Lubrication Systems: Ensuring proper lubrication of moving parts is vital for the longevity and reliability of mechanical systems in aircraft. Fluid line clamps hold the lubrication lines in place, preventing disruptions in the flow of lubricants.
- Spacecraft Applications: In spacecraft, the demands on fluid line clamps are even more extreme, with exposure to vacuum, radiation, and significant temperature variations. 3D-печать по металлу allows for the creation of highly specialized clamps with optimized material properties to withstand these harsh environments.
The specific design and material requirements for these clamps vary depending on the application, the type of fluid being transported, the operating pressures and temperatures, and the vibration environment. 3D-печать по металлу offers the flexibility to tailor the clamp design and material selection to meet these specific requirements, providing significant advantages over traditional, more standardized solutions. Aerospace engineers and procurement managers are increasingly recognizing the value of аддитивное производство металлов in producing these critical components.
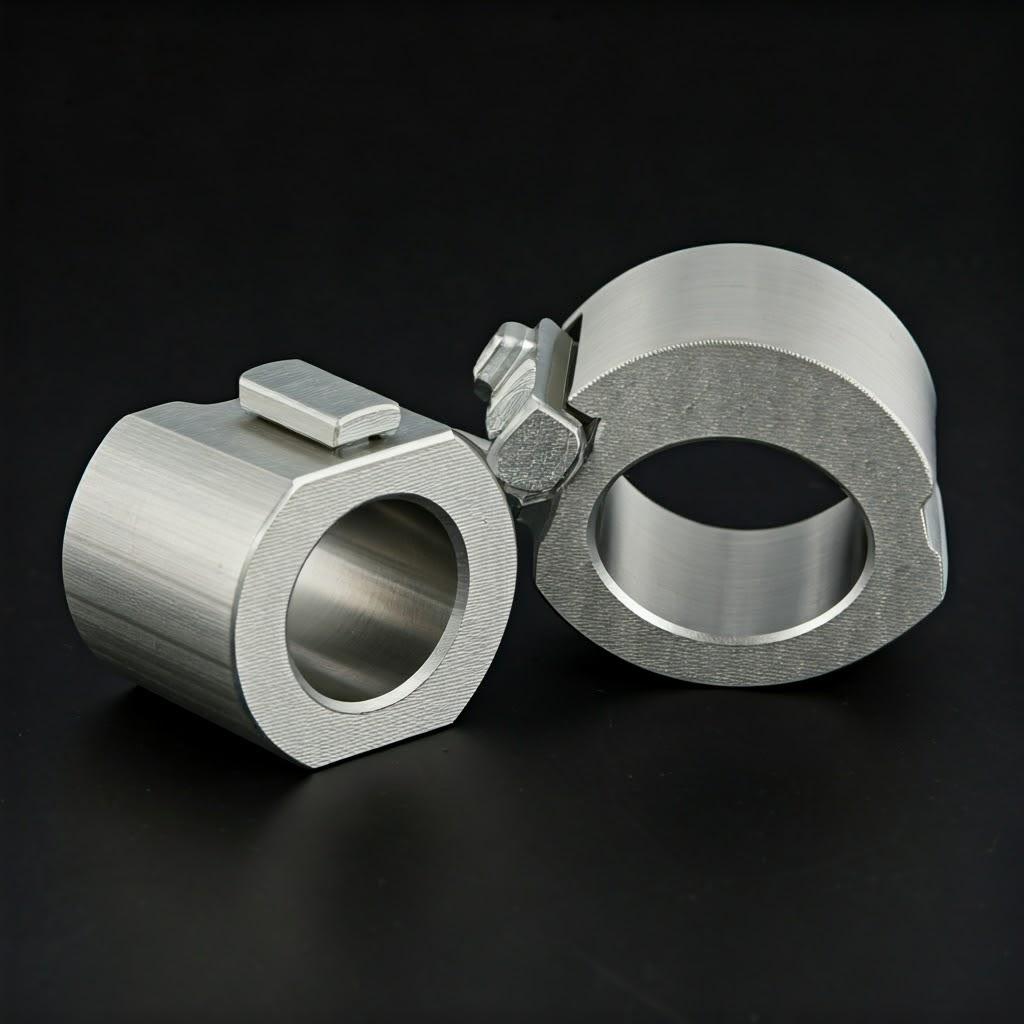
Why Use Metal 3D Printing for Aerospace Fluid Line Clamps?
Принятие металлическая 3D-печать for the production of aerospace fluid line clamps is driven by a multitude of compelling advantages over traditional manufacturing methods. These benefits directly address the critical needs of the aerospace industry for lighter, stronger, and more efficient components:
- Снижение веса: In aerospace, every gram counts. Аддитивное производство enables the creation of complex geometries, including internal lattice structures and topology-optimized designs, which can significantly reduce the weight of fluid line clamps without compromising their structural integrity. This weight reduction translates directly into improved fuel efficiency and reduced emissions – key priorities in modern aerospace. Metal3DP’s expertise in высокоэффективные металлические порошки like AlSi10Mg and Ti-6Al-4V further enhances the potential for lightweighting while maintaining strength.
- Design Flexibility and Optimization: Traditional manufacturing methods often impose limitations on the complexity of part designs. 3D-печать по металлу liberates engineers to create highly optimized clamp geometries that precisely fit the contours of the fluid lines and the surrounding structures. This can lead to improved clamping force distribution, reduced stress concentrations, and enhanced overall performance.
- On-Demand Manufacturing and Reduced Lead Times: Traditional manufacturing processes for specialized aerospace components can involve lengthy lead times for tooling and production. 3D-печать по металлу offers the potential for on-demand manufacturing, producing parts directly from digital designs. This can significantly reduce lead times, accelerate development cycles, and facilitate rapid prototyping and part replacement.
- Эффективность материала: Subtractive manufacturing methods like machining often result in significant material waste. Аддитивное производство, as the name suggests, builds parts layer by layer, using only the material needed for the component. This can lead to substantial cost savings, especially when working with expensive aerospace-grade alloys. Metal3DP’s advanced система изготовления порошка ensures efficient use of materials.
- Customization and Part Consolidation: 3D-печать по металлу allows for easy customization of clamp designs to accommodate specific requirements. Furthermore, it offers the possibility of part consolidation, where multiple components can be integrated into a single 3D-printed part. This reduces the number of fasteners and assembly steps, leading to simplified designs and improved reliability.
- Повышенная производительность: By tailoring the material and design through металлическая 3D-печать, it’s possible to create fluid line clamps with enhanced performance characteristics, such as improved vibration damping, increased resistance to fatigue, and better thermal management. Metal3DP provides comprehensive solutions, including SEBM-принтеры, that can achieve these high-performance results.
- Supply Chain Optimization: 3D-печать по металлу can enable a more distributed manufacturing model, potentially reducing reliance on complex global supply chains and mitigating risks associated with geopolitical instability or logistical disruptions.
The ability to achieve these benefits makes металлическая 3D-печать an increasingly attractive option for aerospace engineers and procurement managers seeking to enhance the performance, efficiency, and cost-effectiveness of their fluid line systems. Exploring the capabilities of a trusted metal 3D printing service provider like Metal3DP can be a crucial step in realizing these advantages.
Recommended Materials and Why They Matter
The selection of the appropriate metal powder is paramount in achieving the desired performance characteristics for 3D printed aerospace fluid line clamps. Two materials stand out as particularly well-suited for this application: AlSi10Mg and Ti-6Al-4V. Metal3DP specializes in providing высококачественные металлические порошки, including these alloys, optimized for additive manufacturing processes. Let’s delve into why these materials are recommended:
1. AlSi10Mg (Aluminum Silicon Magnesium)
- Свойства: AlSi10Mg is an aluminum alloy known for its excellent strength-to-weight ratio, good thermal conductivity, and high ductility. It exhibits good corrosion resistance and is readily printable using Laser Powder Bed Fusion (LPBF) techniques.
- Why it Matters for Fluid Line Clamps:
- Облегчение: Its low density makes it ideal for aerospace applications where weight reduction is critical. Lighter fluid line clamps contribute to overall aircraft fuel efficiency.
- Good Strength: Despite its low weight, AlSi10Mg offers sufficient strength to securely hold fluid lines under typical operating conditions.
- Тепловое управление: The good thermal conductivity of this alloy can be beneficial in applications where heat dissipation from the fluid lines is a concern.
- Эффективность затрат: Compared to titanium alloys, AlSi10Mg is generally more cost-effective, making it a viable option for a larger range of applications.
- Приложения: Suitable for fluid line clamps in areas where weight is a primary concern and operating temperatures and pressures are within the alloy’s capabilities.
2. Ti-6Al-4V (Titanium 6 Aluminum 4 Vanadium)
- Свойства: Ti-6Al-4V is the most widely used titanium alloy, renowned for its exceptional strength-to-weight ratio, excellent corrosion resistance (even in harsh environments), high fatigue strength, and biocompatibility. It can be processed using both Laser Powder Bed Fusion (LPBF) and Electron Beam Melting (EBM) techniques, including Metal3DP’s advanced SEBM-принтеры.
- Why it Matters for Fluid Line Clamps:
- Superior Strength-to-Weight Ratio: Ti-6Al-4V offers significantly higher strength than aluminum alloys while still being relatively lightweight, making it ideal for demanding aerospace applications.
- Отличная коррозионная стойкость: Aerospace components are often exposed to corrosive environments. Ti-6Al-4V’s superior corrosion resistance ensures the long-term reliability of the fluid line clamps.
- High Fatigue Strength: Fluid lines and their clamps are subjected to vibrations and cyclic loads during flight. The high fatigue strength of Ti-6Al-4V ensures the longevity and reliability of the clamps under these conditions.
- Высокотемпературные характеристики: Ti-6Al-4V retains its mechanical properties at higher temperatures compared to aluminum alloys, making it suitable for applications near engines or other heat-generating components.
- Приложения: Ideal for critical fluid line clamps that require high strength, excellent corrosion resistance, and the ability to withstand demanding operating conditions, such as those found in high-performance aircraft and spacecraft. Metal3DP’s высококачественные металлические порошки of Ti-6Al-4V are specifically designed for such demanding applications.
The choice between AlSi10Mg and Ti-6Al-4V will depend on the specific requirements of the application, including the operating environment, the loads the clamps need to withstand, and the weight targets for the aircraft or spacecraft. Consulting with a metal 3D printing service provider like Metal3DP, which has extensive experience with these materials, can help engineers and procurement managers make the optimal material selection for their aerospace fluid line clamp applications.
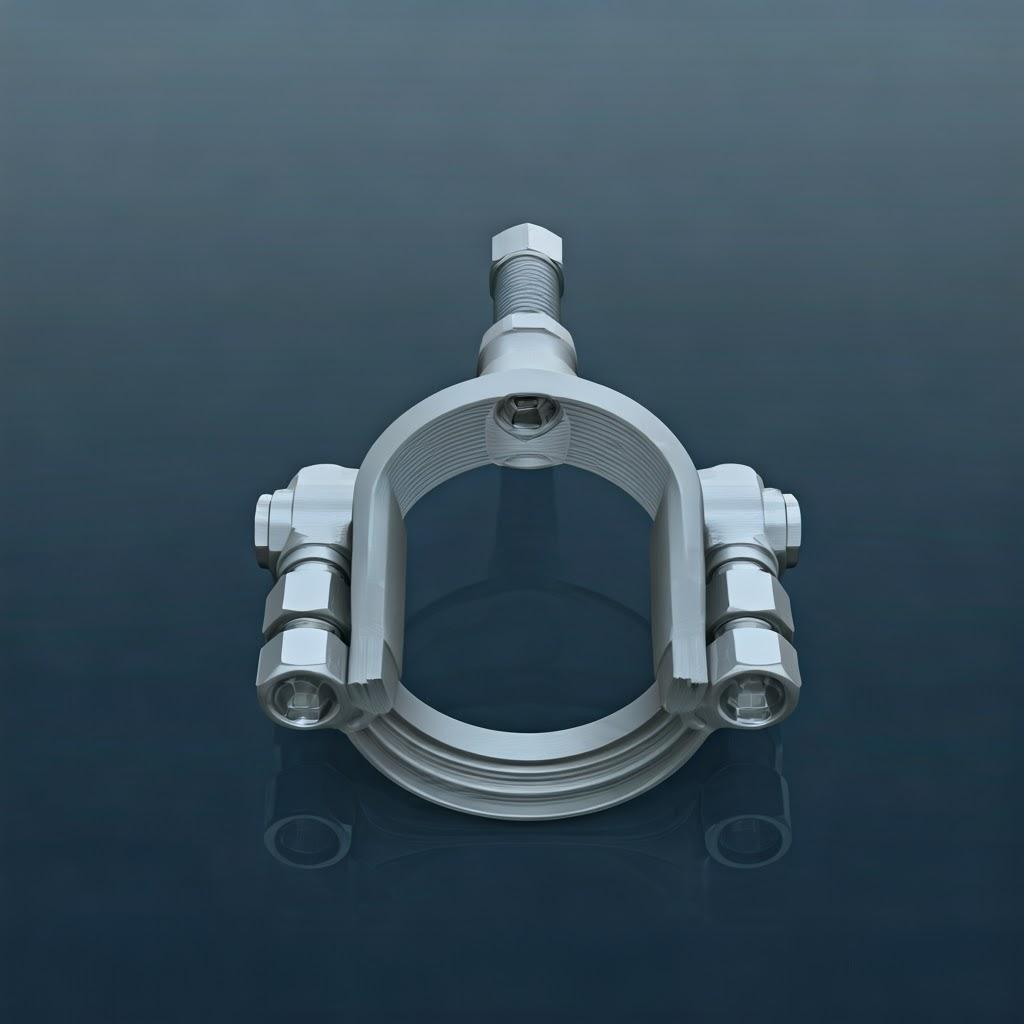
Design Considerations for Additive Manufacturing
Designing aerospace fluid line clamps for металлическая 3D-печать requires a different mindset compared to designing for traditional manufacturing methods. To fully leverage the capabilities of аддитивное производство, engineers need to consider specific design principles and optimization techniques. Here are some key considerations:
- Topology Optimization: This computational method allows for the removal of material from low-stress areas of the clamp while maintaining its structural integrity. By defining the load cases and constraints, engineers can generate highly efficient and lightweight designs that would be difficult or impossible to achieve with conventional manufacturing. 3D-печать по металлу excels at producing these complex, organic shapes.
- Решетчатые структуры: Incorporating lattice structures within the clamp design can significantly reduce weight without sacrificing stiffness or strength. These intricate, repeating patterns provide excellent structural support while using minimal material. Different lattice geometries (e.g., gyroid, diamond, cubic) can be chosen based on the specific load requirements and desired stiffness.
- Объединение частей: Аддитивное производство offers the opportunity to integrate multiple components of a traditional clamp assembly into a single 3D-printed part. This reduces the number of fasteners required, simplifies assembly, and can improve the overall reliability of the system. Consider integrating features like mounting bosses or alignment tabs directly into the clamp design.
- Orientation and Support Structures: The orientation of the part during the printing process can significantly impact surface finish, dimensional accuracy, and the need for support structures. Careful consideration of the build orientation is crucial to minimize support material, which requires post-processing removal and can leave surface blemishes. Design features that minimize overhangs and self-supporting angles are beneficial.
- Wall Thickness and Ribs: Optimizing wall thickness is essential for balancing weight and strength. In areas subjected to high stress, increasing wall thickness or incorporating reinforcing ribs can enhance structural integrity without adding excessive weight to the overall part.
- Fillets and Radii: Sharp corners can be stress concentration points. Incorporating fillets and radii in the design can help distribute stress more evenly and improve the fatigue life of the clamp. 3D-печать по металлу allows for the creation of smooth, continuous curves.
- Tolerances and Interfaces: When designing mating surfaces or interfaces with other components, it’s crucial to consider the achievable tolerances with the chosen металлическая 3D-печать process. Designing appropriate clearances or interference fits is essential for proper assembly and functionality.
- Material Considerations: The chosen металлический порошок (e.g., AlSi10Mg or Ti-6Al-4V from Metal3DP) will influence the design possibilities. Understanding the material’s mechanical properties, such as its modulus of elasticity and yield strength, is crucial for effective design optimization.
By carefully considering these design principles specific to аддитивное производство, aerospace engineers can create fluid line clamps that are lighter, stronger, and more efficient than those produced using traditional methods. Leveraging the expertise of a metal 3D printing service provider with experience in aerospace applications is highly recommended to optimize designs for manufacturability and performance.
Tolerance, Surface Finish, and Dimensional Accuracy
In the aerospace industry, precision is paramount. The tolerance, surface finish, and dimensional accuracy of fluid line clamps directly impact their functionality, reliability, and safety. 3D-печать по металлу has made significant strides in achieving tight tolerances and good surface finishes, but understanding the capabilities and limitations of the technology is crucial for successful implementation.
- Achievable Tolerances: The achievable tolerances in металлическая 3D-печать depend on several factors, including the printing technology (e.g., LPBF, EBM), the material used, the part geometry, and the build parameters. Generally, tolerances in the range of ±0.1 to ±0.05 mm can be achieved for critical dimensions. However, tighter tolerances may require post-processing, such as CNC machining. When working with a metal 3D printing service provider, it’s essential to discuss the specific tolerance requirements for the fluid line clamps and understand what is achievable with their equipment and processes.
- Отделка поверхности: The as-printed surface finish in металлическая 3D-печать typically has a certain degree of roughness due to the layer-by-layer build process and the partially melted powder particles on the surface. The surface roughness (Ra value) can range from 5 to 20 µm depending on the printing parameters and material. For applications requiring smoother surfaces, post-processing techniques like media blasting, polishing, or machining can be employed. The choice of post-processing will depend on the specific requirements of the fluid line clamp.
- Точность размеров: Dimensional accuracy refers to the ability of the 3D-printed part to match the intended CAD model dimensions. Factors affecting dimensional accuracy include material shrinkage during solidification, thermal gradients during the build process, and the accuracy of the printing equipment. Calibration of the 3D printer and optimization of build parameters are crucial for achieving high dimensional accuracy. Utilizing advanced metal 3D printing equipment like those offered by Metal3DP, known for their accuracy and reliability, can significantly improve dimensional accuracy.
- Impact on Functionality: For fluid line clamps, dimensional accuracy is critical for ensuring a proper fit around the fluid lines and a secure connection. Tight tolerances on the inner diameter of the clamp are essential to maintain the correct clamping force without damaging the lines. Surface finish can also play a role, particularly in sealing applications or where smooth contact surfaces are required to prevent wear or abrasion.
- Quality Control and Inspection: Rigorous quality control and inspection procedures are essential to verify that 3D-printed aerospace fluid line clamps meet the required tolerances, surface finish, and dimensional accuracy. Techniques such as coordinate measuring machines (CMM), laser scanning, and non-destructive testing (NDT) methods are commonly used for this purpose. Suppliers with AS9100 certification demonstrate a commitment to stringent quality management systems relevant to the aerospace industry.
Understanding the achievable tolerances, surface finish, and dimensional accuracy with металлическая 3D-печать and implementing appropriate design considerations and post-processing techniques are crucial for producing high-quality aerospace fluid line clamps that meet the stringent requirements of the industry.
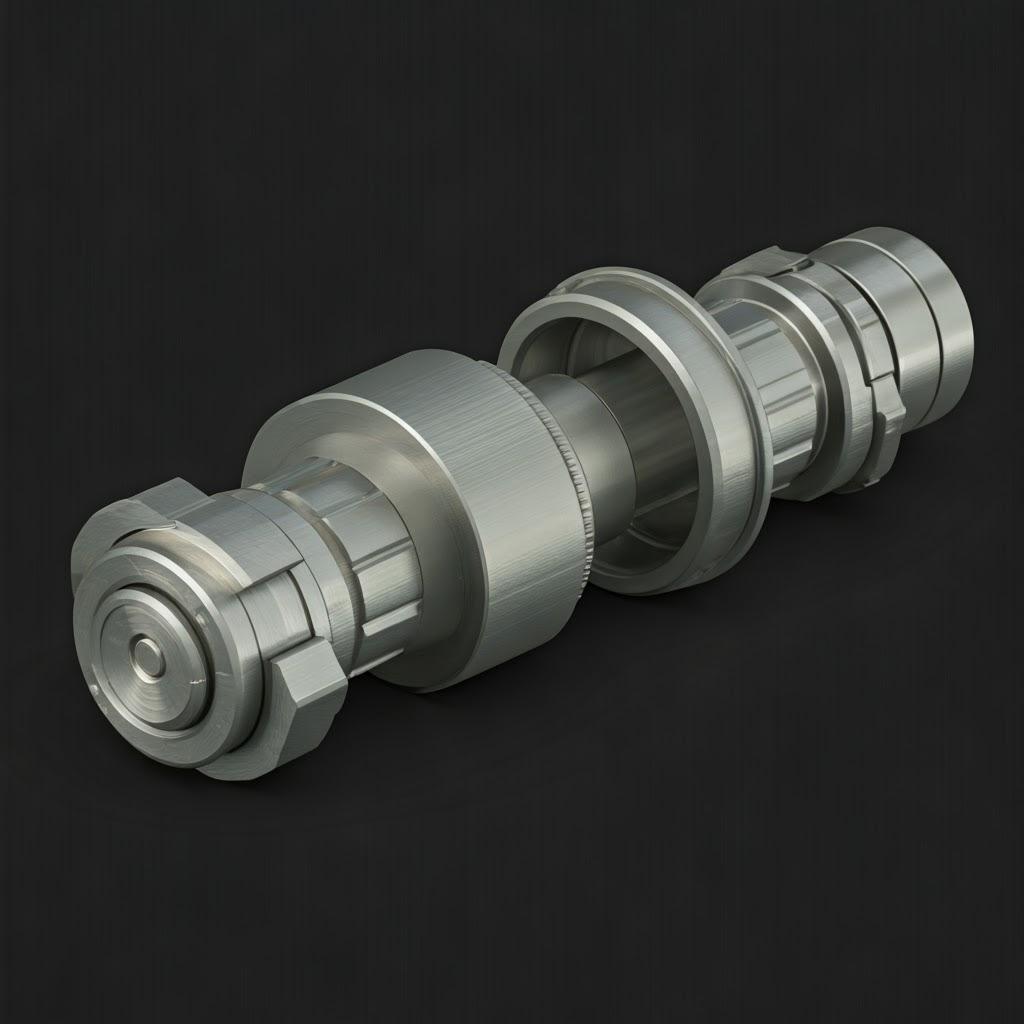
Требования к постобработке
В то время как металлическая 3D-печать offers significant advantages in creating complex geometries, most 3D-printed metal parts, including aerospace fluid line clamps, require some form of post-processing to achieve the desired final properties, surface finish, and dimensional accuracy. Here are some common post-processing requirements:
- Удаление порошка: After the printing process, loose metal powder remains within the internal channels and on the surface of the part. This powder needs to be carefully removed using techniques such as compressed air, vacuuming, or ultrasonic cleaning, especially for complex geometries with internal features.
- Демонтаж опорной конструкции: Support structures are often necessary during the printing process to prevent part deformation and support overhangs. These supports need to be removed after printing, typically through manual breaking, cutting, or machining. The design of the part should aim to minimize the need for extensive support structures to reduce post-processing time and potential surface damage.
- Stress Relief Heat Treatment: Metal parts produced by 3D-печать often contain residual stresses due to the rapid heating and cooling cycles during the build process. Stress relief heat treatment is performed to reduce these internal stresses, which can improve the dimensional stability and mechanical properties of the component. The specific heat treatment cycle depends on the material used.
- Горячее изостатическое прессование (HIP): HIP is a process that involves subjecting the 3D-printed part to high pressure and temperature in an inert gas environment. This process helps to eliminate internal porosity, increase the density, and improve the mechanical properties, particularly the fatigue strength, of the material. HIP is often a critical step for aerospace components.
- Отделка поверхности: As mentioned earlier, the as-printed surface finish may not be suitable for all applications. Various surface finishing techniques can be employed to achieve smoother surfaces, including:
- Media Blasting: Using abrasive media to remove partially sintered powder and improve surface uniformity.
- Grinding and Polishing: Mechanical processes to achieve very smooth and precise surfaces.
- Chemical Etching: Using chemical solutions to remove surface layers and reduce roughness.
- CNC Machining: For critical dimensions and tight tolerances that cannot be achieved directly through 3D-печать, CNC machining may be required as a secondary process. This can include features like precise holes, threads, or mating surfaces.
- Inspection and Quality Control: After post-processing, thorough inspection is necessary to ensure that the fluid line clamps meet the required dimensional accuracy, surface finish, and material properties. Techniques like CMM measurements, non-destructive testing (NDT), and material testing are used.
- Surface Treatments and Coatings: Depending on the application environment, surface treatments like anodizing (for aluminum alloys) or coatings (e.g., for corrosion protection or wear resistance) may be applied to the 3D-printed fluid line clamps.
The specific post-processing steps required will depend on the material, the application requirements, and the capabilities of the metal 3D printing service provider. It’s crucial to discuss these requirements upfront to ensure that the final parts meet the necessary specifications for aerospace applications. Metal3DP offers comprehensive solutions that include not only advanced metal 3D printing equipment и высококачественные металлические порошки but also expertise in the necessary post-processing techniques.
Common Challenges and How to Avoid Them
В то время как металлическая 3D-печать offers numerous advantages for producing aerospace fluid line clamps, there are also potential challenges that engineers and procurement managers should be aware of. Understanding these challenges and implementing appropriate strategies to avoid them is crucial for successful adoption of this technology.
- Warping and Distortion: Thermal stresses during the printing process can lead to warping or distortion of the part, especially for complex geometries or large parts.
- How to Avoid: Optimize part orientation, use appropriate support structures, and carefully control the build parameters. Stress relief heat treatment after printing is often essential. Simulation software can also help predict and mitigate potential distortion.
- Пористость: Internal voids or porosity within the 3D-printed part can compromise its mechanical strength and fatigue life.
- How to Avoid: Optimize printing parameters such as laser power, scan speed, and layer thickness. Using high-quality металлические порошки with good flowability, like those offered by Metal3DP, and employing processes like Hot Isostatic Pressing (HIP) can significantly reduce porosity.
- Шероховатость поверхности: The as-printed surface can be rough, which may not be suitable for all applications and can affect fatigue performance.
- How to Avoid: Optimize printing parameters to minimize surface roughness. Implement appropriate post-processing techniques like media blasting, polishing, or machining to achieve the desired surface finish.
- Support Structure Removal Damage: Removing support structures can sometimes leave surface blemishes or damage the part, especially for delicate features.
- How to Avoid: Design parts with self-supporting geometries whenever possible. Optimize support structure design for easy removal. Use appropriate removal techniques and consider machining for critical surfaces.
- Dimensional Inaccuracy: Achieving tight tolerances can be challenging, especially for complex geometries or large parts.
- How to Avoid: Calibrate the 3D printer regularly and optimize build parameters. Consider the material’s shrinkage behavior. For critical dimensions, plan for post-processing machining.
- Material Property Variability: The mechanical properties of 3D-printed metal parts can sometimes vary depending on the build orientation and process parameters.
- How to Avoid: Establish robust process control and quality assurance procedures. Perform material testing to verify that the parts meet the required specifications. Work with experienced Поставщики услуг 3D-печати по металлу who have expertise in material characterization.
- Стоимостные оценки: В то время как металлическая 3D-печать can be cost-effective for certain applications, the initial investment in equipment or the cost of outsourcing to a service provider can be significant.
- How to Avoid: Carefully evaluate the total cost of ownership or the cost per part, considering design optimization, material usage, and post-processing requirements. For lower volumes or specialized parts, partnering with a reliable metal 3D printing service provider like Metal3DP can be a cost-effective solution.
- Масштабируемость: Scaling up production of 3D-printed metal parts to meet high-volume demands can present challenges.
- How to Avoid: For high-volume production, consider hybrid manufacturing approaches that combine 3D-печать for complex features with traditional manufacturing for simpler geometries. Work with service providers that have the capacity and infrastructure for larger production runs.
By understanding these potential challenges and implementing appropriate mitigation strategies, aerospace engineers and procurement managers can effectively leverage the benefits of металлическая 3D-печать for the production of high-quality and reliable fluid line clamps. Collaborating with a knowledgeable metal 3D printing service provider is key to navigating these challenges successfully.
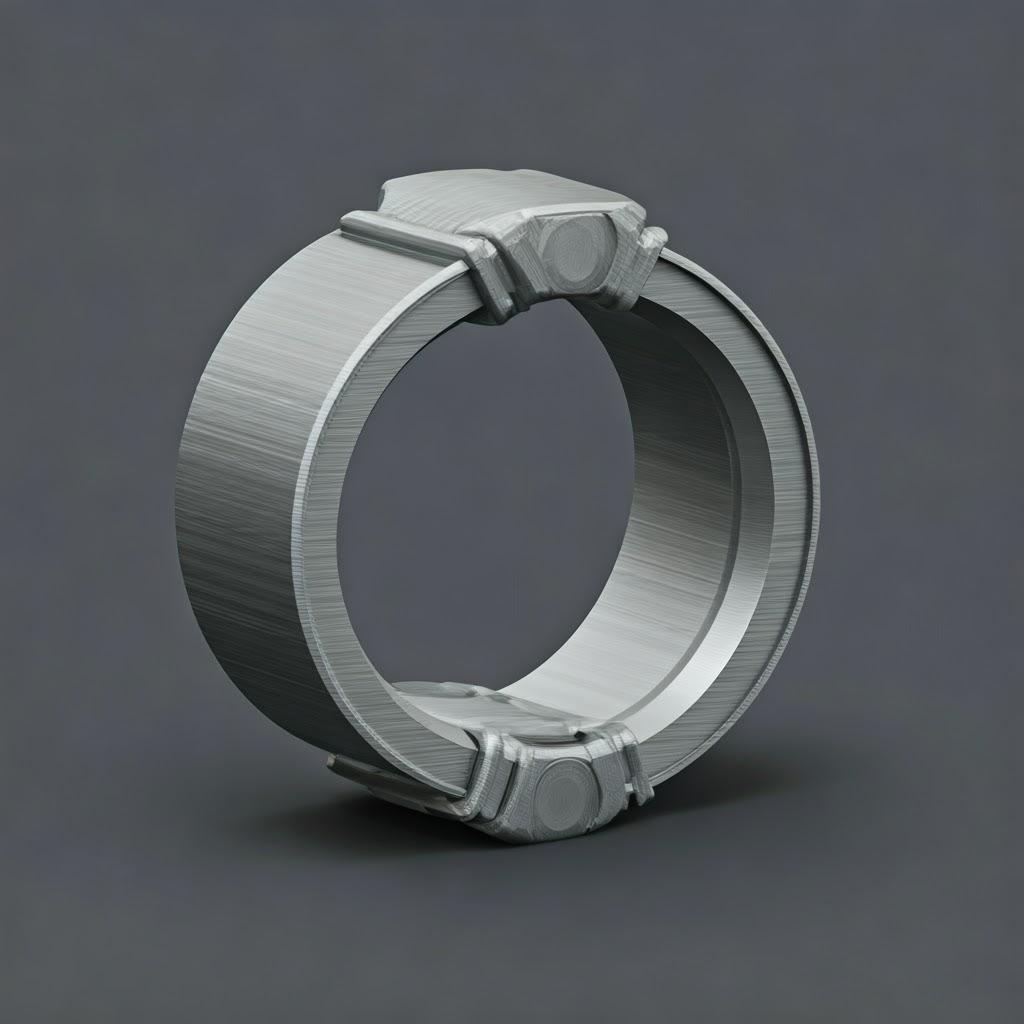
How to Choose the Right Metal 3D Printing Service Provider
Выбор правильного metal 3D printing service provider is a critical decision that can significantly impact the success of your aerospace fluid line clamp project. Given the stringent requirements of the aerospace industry, it’s essential to partner with a provider that possesses the necessary expertise, certifications, and capabilities. Here are key factors to consider when making your choice:
- Aerospace Experience and Certifications: Look for a provider with a proven track record in serving the aerospace industry and relevant certifications such as AS9100. This certification demonstrates a commitment to quality management systems specific to aerospace requirements for design, development, production, installation, and servicing.
- Экспертиза материалов: Ensure the provider has extensive experience working with the recommended металлические порошки for aerospace fluid line clamps, specifically AlSi10Mg and Ti-6Al-4V. They should understand the nuances of processing these materials to achieve the desired mechanical properties and performance. Metal3DP’s specialization in высокоэффективные металлические порошки makes them a strong contender in this regard.
- Printing Technology and Equipment: Inquire about the types of metal 3D printing equipment the provider uses (e.g., LPBF, EBM). The choice of technology can influence the achievable tolerances, surface finish, and build volume. Providers with advanced and well-maintained equipment are more likely to deliver high-quality parts. Metal3DP’s industry-leading print volume, accuracy, and reliability are key differentiators.
- Design for Additive Manufacturing (DfAM) Support: A good service provider will offer expertise in DfAM, helping you optimize your fluid line clamp designs for металлическая 3D-печать to maximize performance, reduce weight, and minimize material usage and post-processing.
- Post-Processing Capabilities: Understand the provider’s in-house post-processing capabilities, including powder removal, support removal, heat treatment (like stress relief and HIP), surface finishing, and CNC machining. A provider offering a comprehensive suite of services can streamline the production process.
- Quality Control and Inspection Procedures: Robust quality control processes are essential for aerospace components. Inquire about the provider’s inspection methods, including dimensional measurement, non-destructive testing (NDT), and material testing. They should be able to provide detailed inspection reports.
- Lead Times and Production Capacity: Discuss your project timelines and volume requirements to ensure the provider can meet your needs. Understand their typical lead times for similar projects and their production capacity.
- Communication and Customer Support: Effective communication and responsive customer support are crucial for a smooth and successful project. Choose a provider that is proactive, transparent, and willing to collaborate closely with your team.
- Cost Structure: Understand the provider’s pricing model, including material costs, printing costs, and post-processing charges. Request a detailed quote and compare it with other providers, considering the overall value and quality offered.
- References and Case Studies: Ask for references or case studies of similar aerospace projects they have completed. This can provide valuable insights into their capabilities and customer satisfaction.
By carefully evaluating potential Поставщики услуг 3D-печати по металлу based on these criteria, you can select a partner that aligns with your project goals and ensures the production of high-quality, reliable aerospace fluid line clamps. Considering a provider like Metal3DP, with their expertise in аддитивное производство металлов, современные металлические порошки, and comprehensive solutions, could be a significant advantage. You can learn more about their capabilities on their Страница "О нас.
Cost Factors and Lead Time
Understanding the cost factors and lead time associated with металлическая 3D-печать of aerospace fluid line clamps is crucial for budgeting and project planning. These aspects can vary significantly depending on several factors:
Факторы стоимости:
- Материальные затраты: The cost of the металлический порошок (e.g., AlSi10Mg or Ti-6Al-4V) is a significant factor. Titanium alloys are generally more expensive than aluminum alloys. The quantity of material used, which is influenced by the part design and the need for support structures, also impacts the cost.
- Время печати: The duration of the 3D printing process is a key cost driver. Longer print times, influenced by part size, complexity, and build volume, translate to higher machine usage costs.
- Расходы на постобработку: The extent of post-processing required (e.g., powder removal, support removal, heat treatment, surface finishing, machining) significantly affects the overall cost. More complex post-processing steps will increase the final price.
- Design Optimization Costs: If significant design optimization for аддитивное производство is required, including topology optimization or lattice structure design, this engineering effort will contribute to the overall cost.
- Equipment and Overhead Costs: Metal 3D printing service providers factor in their equipment costs, maintenance, energy consumption, and operational overhead into their pricing. Providers with more advanced equipment or specialized certifications may have higher overheads.
- Quality Control and Inspection Costs: Stringent quality control procedures, including material testing and dimensional inspection, add to the overall cost but are essential for aerospace applications.
Время выполнения:
- Design and Engineering: The initial design phase, including optimization for металлическая 3D-печать, can take varying amounts of time depending on the complexity of the part and the level of customization required.
- Время сборки: The actual 3D printing process duration depends on the part size, complexity, and the number of parts being printed in a single build. Larger or more intricate parts will require longer build times.
- Post-Processing Time: The time required for post-processing steps can vary significantly. Simple powder and support removal may take a few hours, while complex heat treatments or machining operations can take days or even weeks.
- Quality Control and Inspection: Thorough inspection processes also contribute to the overall lead time.
- Shipping and Logistics: The time required for shipping the finished parts to their final destination needs to be considered.
Strategies for Managing Cost and Lead Time:
- Оптимизация дизайна: Designing parts specifically for аддитивное производство can minimize material usage, reduce build time, and simplify post-processing.
- Выбор материала: Choosing the most appropriate material for the application, considering both performance requirements and cost, is crucial.
- Build Planning: Optimizing part orientation and nesting within the build volume can maximize efficiency and reduce print time per part.
- Post-Processing Efficiency: Selecting designs and materials that minimize the need for extensive post-processing can reduce both cost and lead time.
- Working with Experienced Providers: Partnering with a reputable metal 3D printing service provider like Metal3DP, with efficient processes and expertise in aerospace applications, can help optimize both cost and lead time. You can explore their способы печати on their website: Услуги 3D-печати по металлу.
By carefully considering these cost factors and lead time elements, and by working strategically with a knowledgeable service provider, aerospace companies can effectively leverage металлическая 3D-печать for their fluid line clamp needs while staying within budget and meeting project timelines.
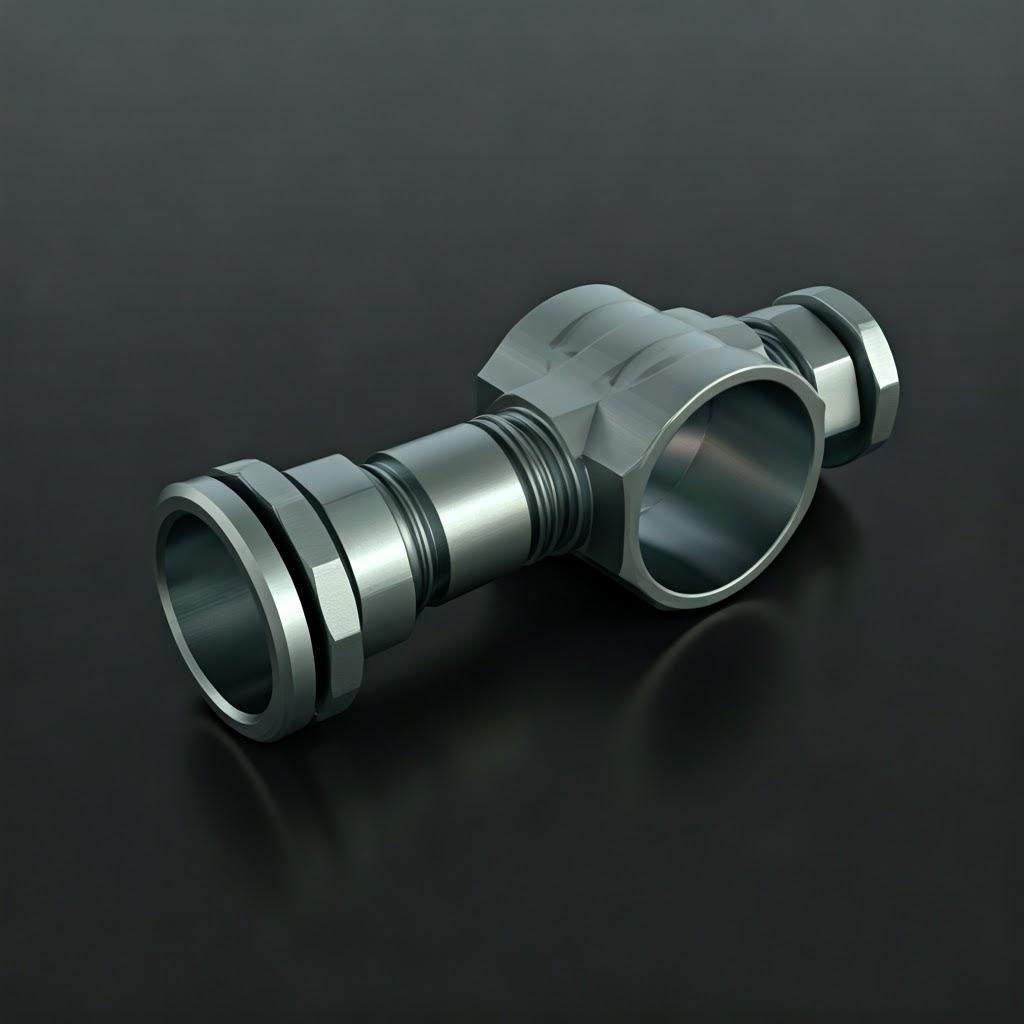
Часто задаваемые вопросы (FAQ)
Here are some frequently asked questions about using металлическая 3D-печать for aerospace fluid line clamps:
- Q: Are 3D printed metal fluid line clamps strong enough for aerospace applications?
- A: Yes, when the appropriate металлический порошок (e.g., Ti-6Al-4V), design optimization for аддитивное производство, and proper post-processing (including heat treatment and HIP) are employed, 3D-printed metal fluid line clamps can meet or exceed the strength and durability requirements of aerospace applications. Rigorous testing and quality control are essential to verify performance. Metal3DP’s высококачественные металлические порошки are designed to achieve superior mechanical properties.
- Q: Can metal 3D printing achieve the tight tolerances required for fluid line connections?
- A: 3D-печать по металлу can achieve tolerances in the range of ±0.1 to ±0.05 mm. For applications requiring tighter tolerances, post-processing techniques like precision CNC machining can be used to achieve the necessary accuracy on critical dimensions. It’s crucial to discuss tolerance requirements with your metal 3D printing service provider.
- Q: What are the typical lead times for 3D printed aerospace fluid line clamps?
- A: Lead times can vary depending on the complexity of the design, the material selected, the required post-processing, and the service provider’s workload. For prototypes or small batches, lead times can range from a few days to a few weeks. Larger production runs will require longer lead times. Discuss your specific timeline requirements with your chosen provider.
- Q: Is metal 3D printing cost-effective for aerospace fluid line clamps?
- A: The cost-effectiveness of металлическая 3D-печать depends on factors such as the volume of parts, the complexity of the design, and the material used. For low to medium volumes of complex, customized parts, металлическая 3D-печать can be more cost-effective than traditional manufacturing methods due to reduced tooling costs and material waste. For high-volume production of simpler designs, traditional methods may still be more economical. A thorough cost analysis should be performed for each specific application. You can explore Metal3DP’s product offerings здесь.
- Q: What kind of post-processing is typically required for 3D printed aerospace fluid line clamps?
- A: Common post-processing steps include powder removal, support structure removal, stress relief heat treatment, and potentially Hot Isostatic Pressing (HIP) to improve density and mechanical properties. Surface finishing techniques like media blasting or polishing may also be required depending on the application. For critical dimensions, CNC machining may be necessary.
- Q: How do I ensure the quality and reliability of 3D printed aerospace fluid line clamps?
- A: Ensure you are working with a metal 3D printing service provider that has experience in the aerospace industry and relevant certifications like AS9100. They should have robust quality control procedures in place, including material testing, dimensional inspection, and non-destructive testing if required. Thorough documentation and traceability are also essential.
Заключение
The integration of металлическая 3D-печать into the manufacturing of aerospace fluid line clamps represents a significant leap forward in terms of design freedom, material efficiency, and performance optimization. By leveraging the unique capabilities of аддитивное производство, engineers can create lighter, stronger, and more customized components tailored to the specific demands of aerospace applications. The use of advanced металлические порошки like AlSi10Mg and Ti-6Al-4V, processed on high-precision metal 3D printing equipment, enables the production of fluid line clamps with exceptional properties.
While challenges exist, such as achieving tight tolerances and managing post-processing requirements, choosing the right metal 3D printing service provider with aerospace expertise is paramount. A partner like Metal3DP, with their comprehensive understanding of аддитивное производство металлов, their range of высококачественные металлические порошки, and their commitment to quality, can guide aerospace companies through the entire process, from design optimization to final production.
As the aerospace industry continues to innovate and push the boundaries of what’s possible, металлическая 3D-печать will undoubtedly play an increasingly vital role in the creation of critical components like fluid line clamps, paving the way for more efficient, safer, and higher-performing aircraft and spacecraft. Contact Metal3DP to explore how their capabilities can power your organization’s additive manufacturing goals. You can find more information on their website: Metal3DP Technology.
Поделиться
MET3DP Technology Co., LTD - ведущий поставщик решений для аддитивного производства со штаб-квартирой в Циндао, Китай. Наша компания специализируется на производстве оборудования для 3D-печати и высокопроизводительных металлических порошков для промышленного применения.
Сделайте запрос, чтобы получить лучшую цену и индивидуальное решение для вашего бизнеса!
Похожие статьи
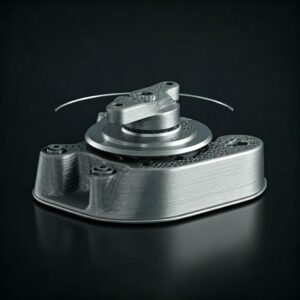
3D-печатные крепления для автомобильных радарных датчиков: Точность и производительность
Читать далее "О компании Met3DP
Последние обновления
Наш продукт
CONTACT US
Есть вопросы? Отправьте нам сообщение прямо сейчас! После получения Вашего сообщения мы всей командой выполним Ваш запрос.
Получите информацию о Metal3DP
Брошюра о продукции
Получить последние продукты и прайс-лист