Custom Impellers via 3D Printing for Harsh Environments
Оглавление
Introduction: Revolutionizing Pump Performance with 3D Printed Custom Impellers
The heart of any centrifugal pump, the impeller, plays a mission-critical role in energy transfer and fluid movement. Its intricate design dictates the pump’s efficiency, head, flow rate, and overall operational reliability. In numerous industrial sectors – from chemical processing plants handling aggressive media to offshore platforms battling corrosive seawater, and power generation facilities demanding unwavering performance – impellers face relentless challenges. Harsh environments characterized by extreme temperatures, high pressures, abrasive particles, and corrosive fluids constantly threaten impeller integrity, leading to reduced performance, costly downtime, and potential system failure.
Traditionally, manufacturing impellers, especially those with complex geometries or requiring specialized alloys, has relied on casting followed by extensive machining, or direct machining from billet. While effective for mass production of standard designs, these methods present significant limitations when dealing with:
- Сложные геометрии: Achieving optimal hydraulic efficiency often requires intricate blade curvatures, varying thicknesses, and potentially internal channels that are difficult or impossible to cast or machine.
- Specialized Materials: Casting certain high-performance alloys like nickel-based superalloys or specific copper-nickel grades can be challenging and expensive, limiting material choices.
- Lead Times and Tooling Costs: Creating molds for casting involves significant upfront investment and long lead times, making it uneconomical for low-volume, custom, or prototype impellers. Machining complex shapes from exotic materials is time-consuming and generates substantial material waste.
- Design Iteration: Modifying a design requires new tooling or extensive reprogramming, hindering rapid prototyping and optimization cycles.
Входить 3D-печать по металлу, also known as Additive Manufacturing (AM). This transformative technology builds components layer by layer directly from digital models using high-performance metal powders. For pump impellers operating in harsh environments, metal AM offers a paradigm shift, enabling the production of highly customized, performance-optimized components from advanced materials previously difficult to work with. It bypasses the constraints of traditional manufacturing, unlocking new possibilities in pump design, efficiency, and reliability.
Такие компании, как Met3dp, a leader in additive manufacturing solutions, are at the forefront of this revolution. Specializing in advanced metal 3D-печать systems and high-performance spherical metal powders, Met3dp empowers industries to leverage AM for demanding applications, including the production of robust, custom impellers designed to conquer the toughest operational conditions. This technology isn’t just about replacing old methods; it’s about fundamentally rethinking how critical components like impellers are designed, manufactured, and deployed.
What Are 3D Printed Pump Impellers Used For? Key Applications and Industries
The versatility and advantages of metal additive manufacturing allow 3D printed impellers to deliver significant value across a diverse range of demanding industries and applications. The ability to create complex geometries from specialized, high-performance alloys makes them ideal solutions where standard off-the-shelf impellers fall short or where customization offers a distinct performance or longevity advantage. Procurement managers and engineers in these sectors are increasingly turning to metal AM suppliers for custom impeller manufacturing and wholesale pump parts solutions.
Here’s a breakdown of key applications and industries benefiting from 3D printed pump impellers:
1. Chemical Processing:
- Вызов: Handling highly corrosive acids, bases, solvents, and volatile organic compounds (VOCs) at various temperatures and pressures. Material compatibility is paramount to prevent leaching, contamination, and rapid degradation.
- AM Solution: 3D printing enables the use of highly corrosion-resistant alloys like Nickel Alloy IN625, Hastelloys, or specialized stainless steels. Complex impeller designs optimized for specific fluid viscosities or mixing requirements can be realized, improving process efficiency and safety. Custom designs can minimize shear for sensitive fluids or maximize turbulence for effective mixing.
- Примеры: Reactors, mixers, transfer pumps for aggressive chemicals.
2. Marine and Offshore:
- Вызов: Constant exposure to corrosive saltwater, potential for biofouling, and demanding operational requirements for propulsion, ballast, cooling, and fire suppression systems. Reliability in remote offshore locations is critical.
- AM Solution: Copper-nickel alloys like CuNi30Mn1Fe, known for excellent resistance to seawater corrosion and biofouling, can be effectively processed using AM. Optimized impeller designs can enhance propulsion efficiency or pump performance in confined spaces. Rapid production of replacement impellers minimizes downtime for critical vessel or platform systems.
- Примеры: Seawater lift pumps, cooling water pumps, fire pumps, thruster components, ballast pumps.
3. Oil and Gas (Upstream, Midstream, Downstream):
- Вызов: Handling abrasive slurries (sand, rock particles), corrosive sour gas (H2S), high temperatures, high pressures, and varying fluid compositions. Erosion, corrosion, and wear are major concerns.
- Вызов: Handling abrasive slurries (sand, rock particles), corrosive sour gas (H₂S), high temperatures, high pressures, and varying fluid compositions. Erosion, corrosion, and wear are major concerns.
- AM Solution: Wear-resistant materials and hard-facing alloys can be utilized. Complex geometries tailored to specific flow conditions (e.g., multiphase flow) can improve efficiency and reduce erosion. Topology optimization can create stronger, lighter impellers for demanding downhole or subsea applications. On-demand printing facilitates rapid replacement of worn components in remote or critical operations.
- Примеры: Multistage centrifugal pumps for artificial lift, pipeline booster pumps, slurry pumps, process pumps in refineries, subsea pumping systems.
4. Power Generation:
- Вызов: Ensuring high efficiency and extreme reliability in boiler feedwater pumps, cooling water systems, and condensate extraction pumps, often operating at high temperatures and pressures. Minimizing cavitation and maximizing hydraulic performance are crucial for overall plant efficiency.
- AM Solution: AM allows for fine-tuning impeller designs (blade angles, surface finish) to achieve peak hydraulic efficiency. High-temperature and creep-resistant alloys can be used for demanding applications. Complex internal cooling or recirculation channels can be integrated to manage temperature or prevent cavitation, designs often impossible with casting.
- Примеры: Boiler feedwater pumps, condensate extraction pumps, auxiliary cooling pumps, flue gas desulfurization (FGD) slurry pumps.
5. Water and Wastewater Treatment:
- Вызов: Handling large volumes of water, often containing suspended solids, abrasive grit, and potentially corrosive treatment chemicals. Energy efficiency is a major operational cost factor.
- AM Solution: Customized impeller designs can be optimized for specific flow rates and head requirements, maximizing energy efficiency. Abrasion-resistant materials extend impeller life when dealing with grit or sludge. Rapid prototyping allows for testing different designs to find the most efficient solution for a particular treatment stage.
- Примеры: Influent/effluent pumps, sludge pumps, backwash pumps, chemical dosing pumps.
6. Aerospace and Defense:
- Вызов: Stringent requirements for lightweight components, high performance, extreme operating temperatures (cryogenic fuels, hot gas), and material traceability. Applications include fuel pumps, hydraulic systems, and thermal management.
- AM Solution: Topology optimization enabled by AM creates lightweight yet strong impeller designs crucial for aerospace. Advanced materials like titanium alloys and nickel superalloys can be processed. Complex, highly efficient micro-impeller designs for specialized fluid systems can be manufactured. Part consolidation reduces component count and potential failure points.
- Примеры: Rocket engine turbopumps, aircraft fuel pumps, hydraulic system pumps, coolant circulation pumps.
7. Industrial Manufacturing & General Engineering:
- Вызов: Wide variety of pumping needs, from machine tool cooling to process fluid transfer and hydraulic power packs. Need for reliable, often customized solutions, sometimes in low volumes for specialized machinery.
- AM Solution: Provides a cost-effective route for producing custom or obsolete impellers without high tooling costs. Enables rapid prototyping for new machine designs. Allows tailoring impeller performance to specific process requirements, enhancing overall system efficiency for B2B clients needing specialized equipment.
- Примеры: Coolant pumps, hydraulic pumps, process pumps for food/pharma (requiring specific materials/finish), specialized test rig pumps.
Table: Industry Challenges & AM Impeller Solutions
Промышленность | Common Challenges | How 3D Printed Impellers Help | Potential Materials (Examples) |
---|---|---|---|
Химическая обработка | Extreme Corrosion, Specific Mixing Needs | Use of resistant alloys (IN625, Hastelloy), complex geometries for tailored flow, improved safety through material integrity. | IN625, Stainless Steels (316L) |
Marine & Offshore | Saltwater Corrosion, Biofouling, Reliability | Excellent marine alloys (CuNi), optimized designs for efficiency, rapid spares production. | CuNi30Mn1Fe, Duplex SS |
Нефть и газ | Abrasion, Corrosion (H₂S), High Pressure/Temp | Wear-resistant materials, designs optimized for multiphase flow/erosion resistance, topology optimization for strength. | IN625, Tool Steels, Ti6Al4V |
Производство электроэнергии | High Efficiency, Reliability, High Temp/Pressure | Fine-tuned hydraulics, high-temp alloys, complex internal features (cooling channels) for performance/longevity. | Stainless Steels, IN625, IN718 |
Water & Wastewater | Abrasion, Volume Throughput, Energy Efficiency | Abrasion-resistant materials, custom designs optimized for efficiency, rapid prototyping for performance testing. | Stainless Steels, Duplex SS |
Аэрокосмическая и оборонная промышленность | Lightweighting, High Performance, Extreme Temps | Topology optimization, advanced alloys (Ti, Ni-superalloys), complex micro-designs, part consolidation. | Ti6Al4V, IN718, AlSi10Mg |
Industrial/General | Customization Needs, Low Volume, Obsolete Parts | Tooling-free production, rapid prototyping, cost-effective custom solutions, reverse engineering support. | Various (SS, Tool Steel, etc.) |
Export to Sheets
By leveraging metal AM, companies can procure impellers specifically engineered for their unique operating environment, moving beyond the limitations of standard parts and achieving superior performance, longevity, and overall system value.
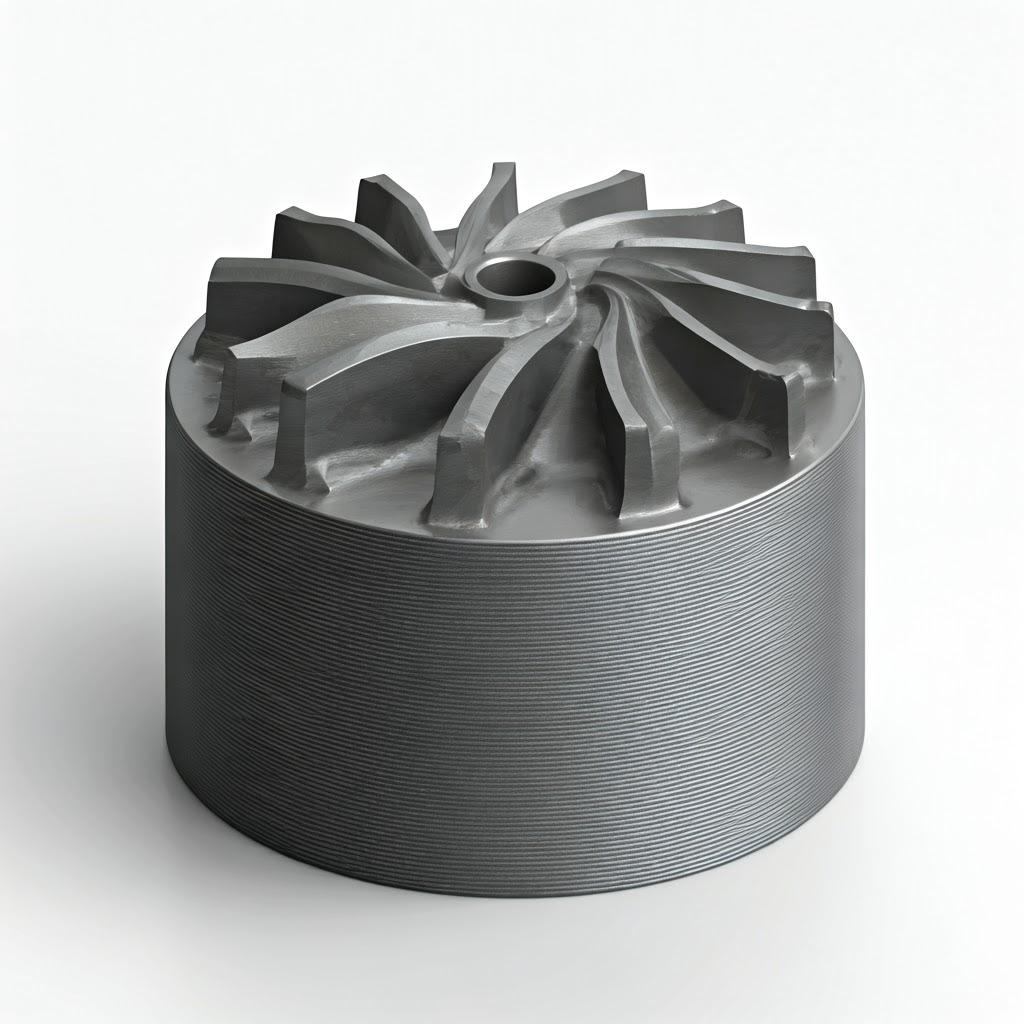
Why Use Metal 3D Printing for Custom Impellers? Unlocking Design Freedom and Performance
While traditional manufacturing methods like casting and machining have served the pump industry for decades, they inherently carry limitations, particularly when faced with the increasing demands for higher efficiency, material performance, and customization in harsh environments. Metal additive manufacturing fundamentally disrupts these constraints, offering compelling advantages for engineers and procurement managers seeking superior impeller solutions. The decision to utilize metal AM for custom impellers often stems from its ability to deliver on aspects where conventional methods falter:
1. Unparalleled Design Freedom:
- Сложные геометрии: AM excels at creating intricate shapes that are difficult or impossible to achieve through casting or machining. This includes:
- Optimized Blade Profiles: Highly complex, continuously varying curvatures and twisted blade designs for maximum hydraulic efficiency and specific performance curves (e.g., low NPSHr).
- Thin Walls & Fine Features: Precisely controlled wall thicknesses and sharp trailing edges minimize flow resistance.
- Internal Channels: Integration of internal cooling channels (for high-temperature applications), recirculation pathways (to mitigate cavitation), or hollow structures (for weight reduction) directly into the impeller body.
- Topology Optimization: Software algorithms can optimize material distribution within a defined design space, removing unnecessary material while maintaining or increasing strength and stiffness. This leads to lighter-weight impellers, reducing rotational mass, bearing load, and potentially vibration, which is crucial in high-speed or aerospace applications.
- Консолидация частей: Complex assemblies, potentially consisting of multiple traditionally manufactured components (e.g., impeller body, separate inducer, wear rings), can sometimes be redesigned and printed as a single, monolithic part. This reduces assembly time, eliminates potential leak paths or failure points at joints, and simplifies inventory management.
2. Material Flexibility and Performance:
- Access to Advanced Alloys: Metal AM processes, particularly powder bed fusion techniques like Selective Laser Melting (SLM), Direct Metal Laser Sintering (DMLS), and Electron Beam Melting (EBM, such as Met3dp’s SEBM systems), can effectively process a wider range of high-performance alloys compared to casting. This includes:
- Nickel-based superalloys (e.g., IN625, IN718) for high temperature and corrosion resistance.
- Copper-nickel alloys (e.g., CuNi30Mn1Fe) for marine environments.
- Titanium alloys for high strength-to-weight ratio and corrosion resistance.
- Tool steels for exceptional wear resistance.
- Specialized stainless steels (Duplex, Super Austenitic).
- Optimized Microstructures: The rapid solidification inherent in many AM processes can lead to fine-grained microstructures, potentially offering enhanced mechanical properties compared to conventionally cast parts, provided process parameters are correctly controlled and appropriate post-processing (like heat treatment or HIP) is applied.
3. Speed and Agility:
- Быстрое прототипирование: Producing functional impeller prototypes directly from CAD data can take days instead of the weeks or months required for tooling and casting. This allows engineering teams to quickly test multiple design iterations, perform hydraulic testing, and arrive at an optimized solution much faster.
- Reduced Lead Times for Low Volumes: For small production runs or one-off custom impellers, AM eliminates the need for expensive and time-consuming tooling setup. Manufacturing can begin almost immediately after design finalization, drastically reducing lead times compared to casting. This is critical for urgent replacements or specialized equipment orders.
- On-Demand Manufacturing & Digital Inventory: Impeller designs can be stored digitally and printed as needed. This facilitates an “on-demand” spare parts strategy, reducing physical inventory holding costs and warehousing space, particularly valuable for obsolete or infrequently needed impellers.
4. Economic Advantages (in specific scenarios):
- Elimination of Tooling Costs: The significant upfront investment in molds or dies required for casting is completely avoided. This makes AM highly cost-effective for prototyping, custom designs, and low-volume production series where tooling amortization is not feasible.
- Сокращение отходов материалов: Unlike subtractive machining, which starts with a solid block and removes material, AM builds parts layer by layer, using only the material required for the part and its support structures. While some powder is non-recyclable or requires conditioning, waste is generally much lower than machining complex shapes from expensive billets.
- Cost-Effective Complexity: In traditional manufacturing, complexity often equates to significantly higher costs (more machining steps, complex molds). In AM, the cost is driven more by part volume and build time rather than geometric complexity. Therefore, intricate, highly optimized designs can often be produced more economically via AM than through extensive multi-axis machining.
Comparison Table: Metal AM vs. Traditional Manufacturing for Impellers
Характеристика | Аддитивное производство металлов (AM) | Традиционное литье | Traditional Machining (from Billet) |
---|---|---|---|
Сложность конструкции | Very High (Complex curves, internal channels, topology opt.) | Moderate (Limited by mold-making/withdrawal) | High (but internal features difficult/costly) |
Варианты материалов | Wide range (incl. difficult-to-cast/machine alloys) | Moderate (Limited by castability) | Wide range (but limited by machinability) |
Стоимость оснастки | Никто | High (Molds/Dies) | Low (Fixtures, standard tools) |
Lead Time (Prototype) | Very Fast (Days) | Slow (Weeks/Months for tooling) | Moderate-Slow (Depending on complexity) |
Lead Time (Low Vol.) | Быстрый | Slow (Tooling + Production) | Moderate-Slow |
Материальные отходы | Low (Powder recycling possible) | Moderate (Gates, risers) | High (Chips) |
Консолидация частей | Excellent potential | Limited | Limited |
Cost Driver | Part Volume, Build Time, Material | Tooling, Material, Labor | Material, Machine Time, Complexity |
Best Fit | Prototypes, Custom Designs, Low-Mid Volume, Complex Parts, Adv. Mat. | High Volume, Standard Designs, Castable Mat. | High Precision Features, Simpler Geometries |
Export to Sheets
By carefully considering these advantages, engineers and procurement specialists can identify applications where leveraging metal 3D printing provides a clear technical and commercial advantage for producing high-performance, custom impellers suited for the most demanding operational environments. Partnering with knowledgeable AM service providers like Met3dp, who possess expertise in both advanced printing technologies and material science, is key to unlocking this potential.
Recommended Materials for Harsh Environments: IN625 and CuNi30Mn1Fe Explored
Selecting the right material is arguably the most critical decision when designing pump impellers for harsh environments. The material must withstand the specific combination of corrosive media, temperature, pressure, and potential wear mechanisms present in the application. Metal additive manufacturing opens the door to using high-performance alloys that might be challenging or cost-prohibitive to form using traditional methods. For demanding applications frequently encountered in chemical processing, marine, and oil & gas sectors, two standout candidates readily processable via AM are Nickel Alloy 625 (IN625) и Copper-Nickel Alloy CuNi30Mn1Fe (often referenced by UNS C96800 or similar marine grades).
Leading metal powder suppliers, such as Met3dp, utilize advanced manufacturing techniques like vacuum induction melting gas atomization (VIGA) and Plasma Rotating Electrode Process (PREP). These methods produce highly spherical metal powders with excellent flowability, controlled particle size distribution, and high purity – characteristics essential for achieving dense, defect-free components with consistent properties in powder bed fusion AM processes. The quality of the input powder directly impacts the final part’s mechanical integrity and performance.
Let’s delve into why IN625 and CuNi30Mn1Fe are excellent choices for 3D printed impellers in harsh environments:
1. Nickel Alloy 625 (IN625 / UNS N06625)
IN625 is a non-magnetic, corrosion- and oxidation-resistant, nickel-based superalloy. Its outstanding strength and toughness from cryogenic temperatures up to approximately 816°C (1500°F) are derived primarily from the solid solution strengthening effects of niobium and molybdenum in the nickel-chromium matrix.
- Key Properties & Benefits for Impellers:
- Исключительная коррозионная стойкость: IN625 exhibits outstanding resistance to a wide range of corrosive environments, including:
- Pitting and crevice corrosion in chloride-containing media (e.g., seawater, brines).
- Sour gas environments (H₂S, CO₂, chlorides) found in oil and gas production.
- Acids, both oxidizing (nitric acid) and reducing (sulfuric, phosphoric, hydrochloric).
- Alkalies.
- Its high PREN (Pitting Resistance Equivalent Number, typically > 30) quantifies its excellent resistance to localized corrosion.
- Высокая прочность и выносливость: Maintains significant strength and toughness across a broad temperature range, resisting deformation and fracture under high pressure or stress.
- Excellent Fatigue Strength: Resists cyclical loading, important for rotating components like impellers.
- Good Weldability/Printability: Generally considered readily processable by laser and electron beam powder bed fusion methods, allowing complex impeller geometries to be built successfully.
- Resistance to Chloride-Ion Stress Corrosion Cracking: Crucial in marine and chemical processing applications.
- Исключительная коррозионная стойкость: IN625 exhibits outstanding resistance to a wide range of corrosive environments, including:
- Typical Applications for 3D Printed IN625 Impellers:
- Chemical processing pumps handling aggressive acids or chloride solutions.
- Oil and gas components exposed to sour gas or high-temperature corrosive fluids.
- High-performance marine pumps requiring superior corrosion resistance and strength.
- Aerospace fuel and hydraulic pumps operating at elevated temperatures.
- Power generation components in corrosive flue gas or high-purity water systems.
Table: Typical Properties of Additively Manufactured IN625 (Heat Treated)
Недвижимость | Typical Value Range | Significance for Impellers |
---|---|---|
Chemical Composition (%) | ||
Никель (Ni) | 58,0 мин | Base element, provides toughness and corrosion resistance |
Хром (Cr) | 20.0 – 23.0 | Critical for oxidation and general corrosion resistance |
Молибден (Mo) | 8.0 – 10.0 | Enhances pitting/crevice corrosion resistance, solid solution strength |
Niobium (Nb) (+Ta) | 3.15 – 4.15 | Primary strengthening element, improves creep resistance |
Железо (Fe) | 5.0 макс. | Often present as balance |
Mechanical Properties (RT) | ||
Предельная прочность на разрыв | 830 – 1050 MPa (120 – 152 ksi) | Resistance to breaking under tensile load |
Предел текучести (смещение 0,2%) | 415 – 700 MPa (60 – 102 ksi) | Stress required to cause permanent deformation |
Удлинение при разрыве | 30 – 50% | Ductility, ability to deform before fracture |
Твердость | ~20-30 HRC / ~220-300 HV | Resistance to indentation and scratching (can influence wear) |
Физические свойства | ||
Плотность | ~8.44 g/cm³ (0.305 lb/in³) | Affects rotational mass and inertia |
Max Operating Temp (approx.) | ~816°C (1500°F) | Suitability for high-temperature fluid handling |
Export to Sheets
(Note: Properties are approximate and depend heavily on AM process parameters, build orientation, heat treatment, and whether HIP is applied. Always consult specific material datasheets from suppliers like Met3dp for guaranteed minimums).
2. Copper-Nickel Alloy CuNi30Mn1Fe (e.g., UNS C96800 / CN107 Similar)
Copper-nickel alloys, particularly the 70/30 (CuNi 70/30) and 90/10 (CuNi 90/10) grades, are widely used in marine applications due to their exceptional resistance to seawater corrosion and biofouling. The CuNi30Mn1Fe composition (approximately 70% Copper, 30% Nickel, with Manganese and Iron additions) offers a great balance of strength and corrosion resistance.
- Key Properties & Benefits for Impellers:
- Excellent Seawater Corrosion Resistance: Forms a stable, protective surface film in seawater, offering very low general corrosion rates and good resistance to localized attack, even in polluted or high-velocity waters.
- Inherent Biofouling Resistance: Copper ions released from the surface inhibit the settlement and growth of marine organisms (algae, barnacles), maintaining hydraulic efficiency and reducing the need for cleaning or coatings.
- Good Strength and Ductility: Offers adequate mechanical properties for many pump impeller applications, particularly where extreme strength is less critical than corrosion/biofouling resistance.
- Good Fabricability/Printability: Can be processed using metal AM, although parameter optimization is crucial due to copper’s high thermal conductivity and reflectivity (especially for laser-based systems). Electron Beam Melting (EBM/SEBM) can offer advantages here.
- Resistance to Stress Corrosion Cracking: Generally resistant to SCC in marine environments.
- Typical Applications for 3D Printed CuNi30Mn1Fe Impellers:
- Seawater lift pumps on ships and offshore platforms.
- Cooling water circulation pumps using seawater.
- Firewater systems in marine environments.
- Ballast water pumps.
- Bilge pumps.
- Heat exchanger components operating with seawater.
Table: Typical Properties of Additively Manufactured CuNi30Mn1Fe (Approximate)
Недвижимость | Typical Value Range (As-Built/Stress Relieved) | Significance for Impellers |
---|---|---|
Chemical Composition (%) | ||
Медь (Cu) | Balance (~65-70) | Base element, contributes to biofouling resistance |
Никель (Ni) | 29.0 – 33.0 | Primary alloying element for seawater corrosion resistance & strength |
Марганец (Mn) | 0.5 – 1.5 | Improves castability/printability, deoxidizer, adds strength |
Железо (Fe) | 0.4 – 1.0 | Enhances erosion resistance in flowing seawater |
Mechanical Properties (RT) | ||
Предельная прочность на разрыв | 380 – 500 MPa (55 – 73 ksi) | Resistance to breaking under tensile load |
Предел текучести (смещение 0,2%) | 170 – 250 MPa (25 – 36 ksi) | Stress required to cause permanent deformation |
Удлинение при разрыве | 25 – 40% | Ductility, ability to deform before fracture |
Твердость | ~80-120 HB / ~75-110 HV | Resistance to indentation (lower than IN625) |
Физические свойства | ||
Плотность | ~8.94 g/cm³ (0.323 lb/in³) | Similar to steel/nickel alloys |
Устойчивость к биообрастанию | Отличный | Key advantage for maintaining hydraulic performance in marine systems |
Max Operating Temp (general) | ~300°C (572°F) | Lower temperature limit than IN625 |
Export to Sheets
(Note: Properties are approximate and heavily influenced by the specific AM process and parameters. Copper alloys can be more challenging to print than nickel alloys or steels. Consultation with experienced providers like Met3dp is essential).
Choosing Between IN625 and CuNi30Mn1Fe:
- Выберите IN625 when the primary challenges are extreme corrosion (acids, sour gas), high temperatures (> 300°C), high mechanical stress, or a combination thereof. It’s a versatile “go-to” for many severe chemical and O&G applications.
- Выберите CuNi30Mn1Fe when the primary challenge is seawater corrosion and biofouling is a significant concern. It offers a cost-effective and highly reliable solution specifically for marine environments where extreme temperatures or stresses are not present.
By selecting the appropriate high-performance alloy and partnering with a capable metal AM provider like Met3dp, companies can procure custom 3D printed impellers that not only survive but thrive in the most demanding harsh environments, leading to improved reliability, efficiency, and reduced life cycle costs.
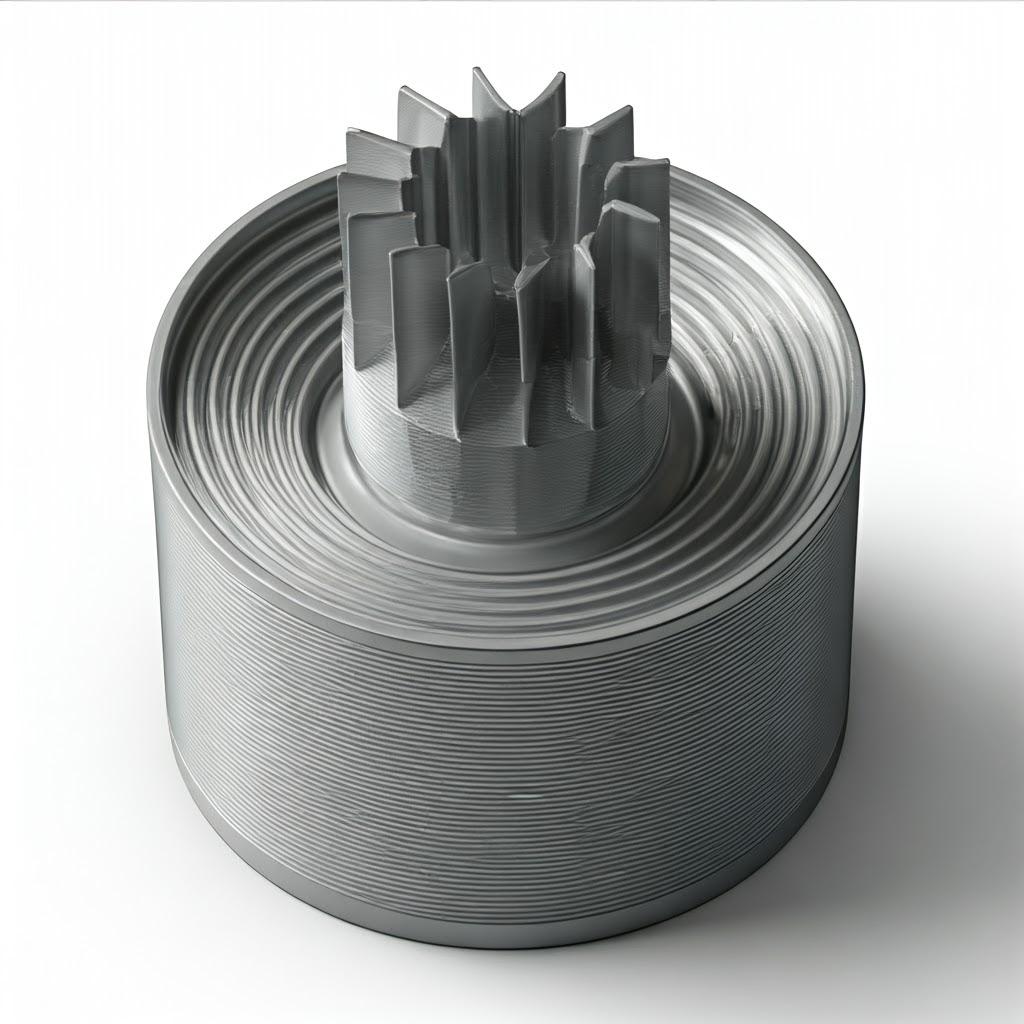
Design Considerations for Additive Manufacturing of Pump Impellers
Transitioning from designing impellers for traditional manufacturing (casting, machining) to designing for Additive Manufacturing (DfAM) requires a shift in mindset. While AM removes many constraints, it introduces new ones and offers unique opportunities that must be considered early in the design phase to maximize the benefits. Simply taking a design intended for casting and sending it to a 3D printer will likely yield suboptimal results and potentially higher costs. Effective DfAM for pump impellers involves optimizing for both functional performance and the specific nuances of the chosen AM printing process, such as Powder Bed Fusion (PBF).
Here are key DfAM considerations for engineers developing custom impellers for harsh environments:
1. Embrace Geometric Freedom for Hydraulic Performance:
- Complex Blade Geometries: Leverage AM’s ability to create highly complex 3D blade shapes (e.g., varying angles of attack, non-linear curvatures, optimized inlet/outlet angles) tailored precisely to the desired flow rate, head, and efficiency targets. Integrate Computational Fluid Dynamics (CFD) simulations early and often to iterate on designs that minimize recirculation, cavitation (low NPSHr), and flow separation.
- Optimized Shroud and Hub Profiles: Design smooth, blended transitions between blades, hub, and shrouds (for closed impellers) to reduce hydraulic losses. Vary wall thicknesses strategically – thicker where structurally needed, thinner elsewhere to save weight and material, which is easily achieved in AM.
- Leading and Trailing Edge Definition: AM allows for much sharper and thinner trailing edges compared to casting, reducing wake losses. However, consider minimum printable feature size and potential stress concentrations. Leading edges can be optimized for specific inflow conditions.
2. Design for the AM Process (PBF Specifics):
- Build Orientation: This is a critical decision impacting:
- Поддерживающие структуры: Orient the impeller to minimize the need for supports, especially on complex blade undersides or internal passages. Overhanging features typically require support beyond a certain angle (often ~45 degrees from horizontal).
- Отделка поверхности: Upward-facing and vertical surfaces generally have better as-printed finish than downward-facing surfaces supported by structures. Critical flow paths should ideally be oriented for optimal finish or easy post-processing access.
- Механические свойства: Anisotropy (direction-dependent properties) can exist in AM parts; orientation might be chosen to align maximum strength with critical stress directions.
- Build Time & Cost: Taller builds generally take longer. Packing multiple impellers efficiently in a build chamber is also a consideration.
- Support Structure Strategy: Where supports are unavoidable, design them for:
- Effectiveness: Must adequately anchor the part and conduct heat to prevent warping.
- Minimization: Use only where necessary to save material and removal time.
- Accessibility & Removability: Ensure supports can be reached and removed without damaging the impeller, especially intricate blade details. Consider break-away points or structures designed for easier machining removal.
- Self-Supporting Angles: Design overhangs and internal channels to be below the critical angle requiring support whenever possible. Chamfers or fillets can sometimes replace sharp overhangs.
- Minimum Feature Size & Wall Thickness: Understand the resolution limits of the chosen AM machine and material. Avoid features thinner than the minimum printable thickness (often ~0.3-0.5 mm, but varies). Ensure sufficient wall thickness for structural integrity, especially under pressure.
- Удаление порошка: For closed or shrouded impellers, design effective escape holes or internal pathways to allow unfused powder to be removed after printing. These holes must be strategically placed and potentially sealed later if necessary. Trapped powder adds weight and can compromise performance or cleanliness.
3. Leverage Advanced DfAM Techniques:
- Topology Optimization: Use software to automatically generate the most efficient material layout for given load cases, boundary conditions, and performance objectives (e.g., minimize mass, maximize stiffness). This can lead to organic-looking, highly efficient, lightweight impeller designs, particularly valuable in aerospace or high-speed applications.
- Решетчатые структуры: Incorporate internal lattice structures within thicker sections or shrouds to reduce weight and material consumption while maintaining structural integrity. This requires careful analysis and is typically used where external geometry is fixed, but internal optimization is possible.
- Консолидация частей: Analyze if adjacent components (e.g., an impeller and an inducer stage, or integrated wear rings) can be redesigned and printed as a single, monolithic part. This eliminates assembly steps, fasteners, potential leak paths, and simplifies the supply chain.
4. Collaborate with AM Experts:
- Engage with experienced AM service providers like Met3dp early in the design process. Their application engineers understand the intricacies of different AM processes (SLM, SEBM) and materials (IN625, CuNi30Mn1Fe). They can provide crucial feedback on printability, orientation strategy, support requirements, and potential cost implications, helping to optimize the design for successful and efficient manufacturing. This collaboration ensures the design is not only functionally sound but also manufacturable via AM.
By incorporating these DfAM principles, engineers can fully exploit the potential of metal 3D printing to create custom impellers that offer superior performance, durability, and value, especially when tackling the challenges of harsh operating environments.
Achievable Tolerance, Surface Finish, and Dimensional Accuracy in 3D Printed Impellers
While metal additive manufacturing offers incredible design freedom, it’s crucial for engineers and procurement managers to have realistic expectations regarding the achievable tolerances, surface finish, and overall dimensional accuracy of 3D printed impellers, particularly in the as-printed state. Post-processing steps are almost always required to meet the tight specifications typical for high-performance turbomachinery components.
1. Dimensional Tolerances:
- As-Printed Tolerances: Powder Bed Fusion processes like SLM and SEBM can typically achieve dimensional tolerances in the range of:
- ± 0.1 mm to ± 0.2 mm (± 0.004″ to ± 0.008″) for smaller features (e.g., up to 50-100 mm).
- ± 0.1% to ± 0.2% of the nominal dimension for larger parts.
- Факторы, влияющие на толерантность:
- Калибровка машины: Accuracy of the laser/electron beam positioning, scanning strategy, layer thickness control.
- Свойства материала: Thermal expansion/contraction characteristics of the alloy (e.g., IN625 vs. CuNi).
- Part Geometry & Size: Larger parts or complex geometries with varying cross-sections are more prone to thermal distortion.
- Build Orientation: Can affect how thermal stresses accumulate.
- Поддерживающие структуры: Placement and effectiveness influence stability during the build.
- Тепловое управление: How effectively heat is controlled and dissipated during the build.
- Post-Processing for Tight Tolerances: Features requiring high precision, such as the shaft bore diameter and fit, keyways, sealing surfaces, and overall impeller balancing dimensions, will typically need final machining after printing and heat treatment. CNC machining can achieve tolerances of ± 0.01 mm to ± 0.05 mm (± 0.0004″ to ± 0.002″) or better, depending on the requirement.
- Стандарты: Referencing standards like ISO/ASTM F3303 or ISO 17296-3 can provide frameworks for tolerance specification in AM.
2. Surface Finish (Roughness):
- As-Printed Surface Finish: The surface roughness (Ra) of as-printed metal AM parts is significantly higher than machined surfaces. Typical Ra values range from:
- 5 µm to 20 µm (200 µin to 800 µin), sometimes higher.
- Factors Influencing As-Printed Ra:
- Толщина слоя: Thicker layers generally result in rougher surfaces.
- Powder Particle Size: Finer powders can lead to smoother finishes but may have flowability challenges.
- Surface Orientation:
- Vertical Walls: Tend to show layer lines.
- Upward-Facing Surfaces: Generally smoother, influenced by powder melting characteristics.
- Downward-Facing Surfaces (Supported): Tend to be the roughest due to contact with support structures and partial melting/sintering.
- Параметры процесса: Laser/beam power, scan speed, hatch spacing.
- Impact on Impellers: High surface roughness on impeller blades and flow passages increases friction losses, reduces hydraulic efficiency, and can potentially provide initiation sites for corrosion or cavitation.
- Post-Processing for Improved Finish: Achieving the smooth surfaces required for optimal hydraulic performance (often Ra < 1.6 µm or even < 0.8 µm on critical flow paths) necessitates post-processing. Common methods include:
- CNC Machining: For accessible surfaces requiring precise dimensions and finish.
- Abrasive Flow Machining (AFM): Pushing abrasive media through channels.
- Electropolishing: Electrochemical process to smooth surfaces, particularly effective on complex shapes and certain alloys.
- Manual Polishing/Grinding: Labor-intensive but effective for specific areas.
- Mass Finishing (Tumbling): For overall surface smoothing, less precise.
Table: Surface Finish Comparison
Finishing State | Typical Ra Range (µm) | Typical Ra Range (µin) | Примечания |
---|---|---|---|
As-Printed (PBF) | 5 – 20+ | 200 – 800+ | Varies greatly with orientation, material, parameters. |
Support Interface | 15 – 30+ | 600 – 1200+ | Downward-facing surfaces contacting supports are typically roughest. |
Machined | 0.8 – 6.3 | 32 – 250 | Standard machining finishes. Tighter finishes possible with grinding etc. |
Polished | < 0.8 | < 32 | Achieved through grinding, lapping, polishing, electropolishing. |
HIPed Surface | Similar to As-Printed | Similar to As-Printed | HIP improves internal density but doesn’t significantly smooth the outer surface. |
Export to Sheets
3. Dimensional Accuracy & Stability:
- Achieving Accuracy: This involves not just hitting tolerances but ensuring the part maintains its shape throughout manufacturing and service.
- Снятие стресса: Residual stresses build up during the layer-by-layer heating and cooling cycles of AM. A proper stress relief heat treatment immediately after printing (often while still on the build plate) is crucial to prevent distortion during support removal or subsequent machining.
- Термообработка: Further heat treatments (solution annealing, aging, etc., depending on the alloy like IN625) are needed to achieve the desired final microstructure and mechanical properties. These cycles must be carefully controlled to minimize warping.
- Контроль качества: Experienced AM providers like Met3dp implement rigorous quality control measures, including precise machine calibration, in-process monitoring (where available), and post-build inspection using tools like CMMs (Coordinate Measuring Machines) and 3D scanners to verify dimensional accuracy against the original CAD model and engineering drawings.
Engineers specifying 3D printed impellers must clearly define the required tolerances and surface finishes on critical features in their drawings and technical specifications, understanding that these will likely be achieved through a combination of the AM process and subsequent post-processing steps.
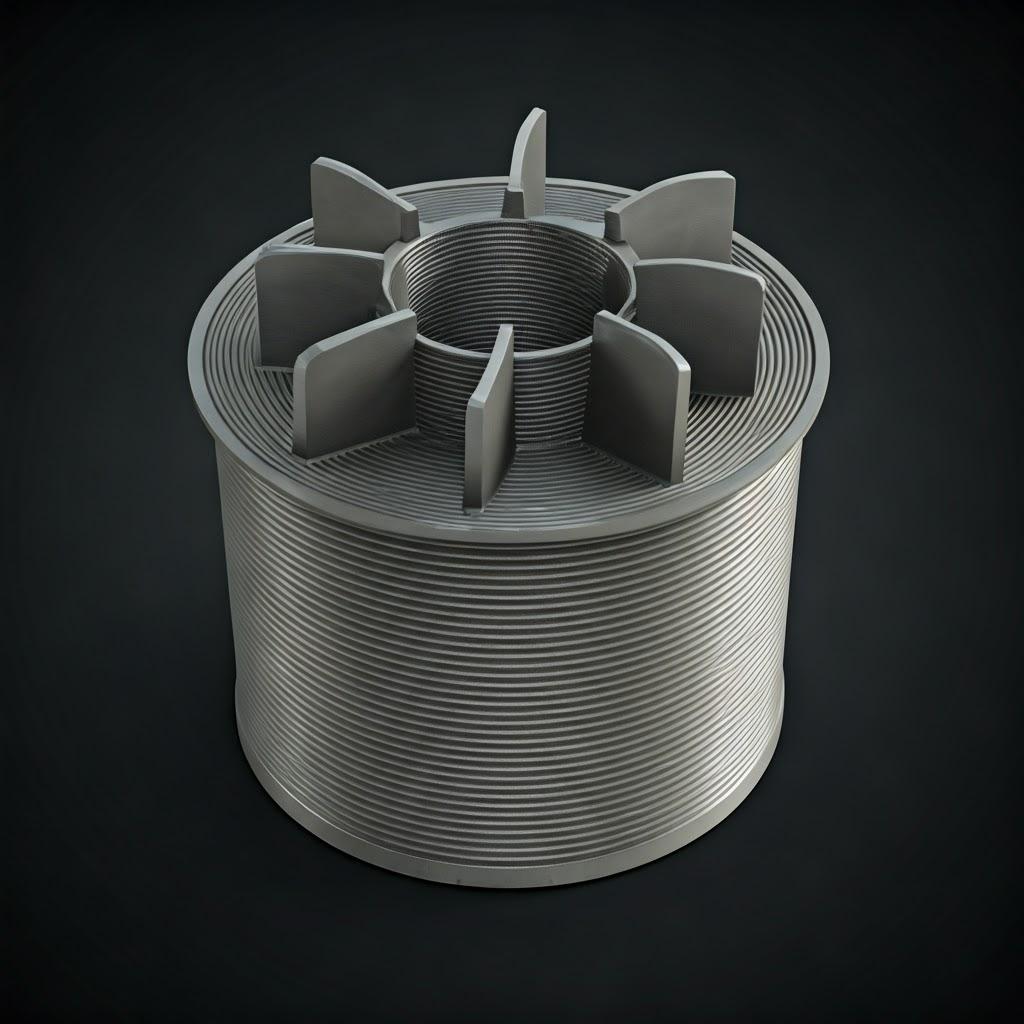
Essential Post-Processing Requirements for 3D Printed Metal Impellers
Additive manufacturing is rarely the final step in producing a functional, high-performance metal impeller. A series of crucial post-processing steps are typically required to transform the as-printed part into a finished component ready for assembly and operation in harsh environments. These steps are essential for achieving the required dimensional accuracy, surface finish, mechanical properties, and overall reliability. Procurement managers should ensure their chosen AM service provider has the capability to perform or manage these critical operations.
Key post-processing requirements include:
1. Stress Relief Heat Treatment:
- Цель: To relax internal residual stresses built up during the rapid heating and cooling cycles of the AM process. These stresses can cause distortion, cracking, or premature failure if not relieved.
- Процедура: Performed soon after the build finishes, often while the impeller is still attached to the build plate. Involves heating the part to a specific temperature (below transformation temperatures) and holding it for a set duration, followed by controlled cooling. Parameters vary significantly depending on the alloy (e.g., IN625 requires different cycles than CuNi alloys or steels).
- Importance: Absolutely critical for dimensional stability during subsequent steps (support removal, machining) and for long-term performance.
2. Part Removal from Build Plate & Support Structure Removal:
- Цель: To separate the printed impeller(s) from the base plate they were built upon and remove the temporary support structures used during the build.
- Методы:
- Plate Removal: Often done using wire EDM (Electrical Discharge Machining) or sawing.
- Удаление опоры: Can involve manual breaking/cutting (for well-designed, accessible supports), CNC machining, grinding, or sometimes specialized electrochemical methods.
- Задачи: Support removal can be labor-intensive and risks damaging delicate impeller features if not done carefully. DfAM plays a huge role in designing easily removable supports.
3. Hot Isostatic Pressing (HIP):
- Цель: To eliminate internal microscopic pores (porosity) that can sometimes remain after the AM process, and to further homogenize the microstructure.
- Процедура: The impeller is subjected to high inert gas pressure (typically 100-200 MPa / 15,000-30,000 psi) at an elevated temperature (below melting point) for several hours. The combination of heat and pressure collapses internal voids.
- Преимущества: Significantly improves:
- Плотность: Achieving near 100% theoretical density.
- Ductility & Elongation: Increases resistance to fracture.
- Fatigue Life: Crucial for rotating components subject to cyclic loading.
- Вязкость разрушения: Resistance to crack propagation.
- Recommendation: Highly recommended, often mandatory, for critical impellers used in demanding applications (aerospace, high-pressure systems, critical chemical processes) where fatigue life and material integrity are paramount. Often combined with solution heat treatment cycles.
4. Final Heat Treatment (Solution Annealing, Aging, etc.):
- Цель: To achieve the final desired microstructure and optimal mechanical properties (strength, hardness, corrosion resistance) for the specific alloy (e.g., solution treating and aging IN625).
- Процедура: Involves carefully controlled heating and cooling cycles tailored to the material specification. HIP cycles are often designed to incorporate solution treatment.
- Importance: Essential for meeting the material performance requirements specified in the design. Incorrect heat treatment can compromise the impeller’s strength and corrosion resistance.
5. Machining of Critical Features:
- Цель: To achieve tight dimensional tolerances, specific surface finishes, and precise geometric features that cannot be consistently produced by the as-printed AM process.
- Typical Machined Areas:
- Shaft Bore: Precise diameter and concentricity for proper fit and alignment.
- Keyway(s): Accurate dimensions for torque transmission.
- Sealing Surfaces: Smooth, flat, or precisely profiled surfaces where the impeller interfaces with casing or seals.
- Wear Ring Surfaces: If applicable.
- Balancing Features: Material removal might be needed for dynamic balancing.
- Flange Faces: If the impeller includes integrated flanges.
- Method: Typically CNC milling or turning. Requires careful fixture design to hold the complex impeller geometry accurately.
6. Surface Finishing & Polishing:
- Цель: To reduce surface roughness on hydraulic passages (blades, shrouds) to improve efficiency, reduce friction losses, and minimize sites for corrosion initiation or cavitation inception.
- Методы: As mentioned previously (Machining, AFM, Electropolishing, Manual Polishing, Mass Finishing), chosen based on the required finish level, accessibility, and cost-effectiveness.
7. Cleaning & Inspection:
- Цель: To remove any residual powder, machining fluids, or contaminants, and to verify the impeller meets all specifications.
- Методы:
- Cleaning: Ultrasonic cleaning, solvent washing, compressed air blow-off.
- Проверка размеров: CMM, 3D scanning.
- Неразрушающий контроль (NDT):
- Visual Inspection: For surface defects.
- Dye Penetrant Inspection (DPI): To detect surface-breaking cracks.
- X-ray or CT Scanning: To detect internal defects (porosity, inclusions) and verify internal channel integrity (critical after HIP).
- Material Certification & Traceability: Verifying powder batches, process logs, heat treatment records.
8. Balancing:
- Цель: To ensure the mass distribution is uniform around the axis of rotation, minimizing vibration during operation.
- Процедура: Static and/or dynamic balancing may be required, involving measuring imbalance and removing small amounts of material from specific locations (often pre-designed balancing lands).
A comprehensive AM service provider should offer a clear plan outlining which post-processing steps are included, performed in-house, or managed through qualified partners, ensuring a seamless workflow from digital file to finished, validated impeller.
Common Challenges in 3D Printing Impellers and How to Overcome Them
While metal 3D printing offers significant advantages for producing custom impellers, the process is complex and not without potential challenges. Awareness of these issues and partnering with an experienced provider like Met3dp – a company built on decades of collective expertise in metal additive manufacturing (learn more О нас) – is key to mitigating risks and ensuring successful outcomes.
Here are some common challenges and strategies to overcome them:
1. Warping and Distortion:
- Вызов: Uneven heating and cooling during the layer-by-layer build process create internal stresses. If these stresses exceed the material’s yield strength or the anchoring force of supports, the impeller can warp or distort, deviating from the intended geometry. This is particularly prevalent in large parts or those with significant changes in cross-section.
- Solutions:
- Process Simulation: Advanced software can simulate the build process to predict thermal stresses and distortion, allowing for pre-compensation in the build file or optimization of orientation/supports.
- Optimized Build Orientation: Positioning the impeller to minimize large, flat surfaces parallel to the build plate and reduce thermal gradients.
- Robust Support Strategy: Well-designed supports anchor the part securely and help conduct heat away effectively.
- Optimized Process Parameters: Fine-tuning laser/beam power, scan speed, and scan strategy to manage heat input.
- Immediate Stress Relief: Performing stress relief heat treatment before removing the part from the build plate is crucial.
2. Support Structure Removal Difficulties:
- Вызов: Supports, while necessary, can be difficult and time-consuming to remove, especially from intricate internal passages or delicate blade features. Aggressive removal can damage the impeller surface or geometry.
- Solutions:
- DfAM for Supports: Designing parts with self-supporting angles where possible. Optimizing support types (e.g., thin-contact points, lattice supports) and placement for accessibility and easier break-off or machining.
- Specialized Removal Tools/Techniques: Using appropriate cutting tools, grinders, or sometimes wire EDM or electrochemical methods.
- Skilled Technicians: Experienced personnel are vital for careful and efficient support removal.
3. Residual Stress Management:
- Вызов: Even if significant warping doesn’t occur during the build, high residual stresses can remain within the part. These can lead to delayed cracking, reduced fatigue life, or distortion during subsequent machining operations.
- Solutions:
- Effective Stress Relief Cycles: Implementing scientifically validated heat treatment protocols specific to the alloy.
- Горячее изостатическое прессование (HIP): HIP not only closes pores but also helps to relieve residual stresses through creep mechanisms at high temperatures.
- Оптимизация параметров процесса: Controlling heat input and cooling rates during the build.
4. Porosity Control:
- Вызов: Microscopic voids or pores can form within the printed material due to incomplete melting, gas entrapment (from powder or shielding gas), or keyholing effects (vapor depression instability). Porosity reduces density and can significantly degrade mechanical properties, particularly fatigue strength and ductility.
- Solutions:
- Optimized Process Parameters: Precise control over laser/beam power density, scan speed, layer thickness, and powder characteristics is essential to achieve full melting and stable melt pool behavior.
- High-Quality Powder: Using spherical, gas-atomized powders (like those produced by Met3dp) with controlled particle size distribution and low internal gas porosity ensures consistent melting and packing. Regular powder quality checks are vital.
- Inert Atmosphere Control: Maintaining a high-purity inert gas atmosphere (Argon or Nitrogen) in the build chamber minimizes oxidation and gas pickup.
- Горячее изостатическое прессование (HIP): The most effective method to eliminate any remaining internal porosity after printing.
5. Achieving Desired Surface Finish:
- Вызов: The inherent layer-by-layer nature and powder particle size result in a relatively rough as-printed surface finish compared to machined parts, which can negatively impact hydraulic efficiency. Achieving a smooth finish, especially on complex internal surfaces, can be difficult.
- Solutions:
- Orientation & Parameter Optimization: Choosing build orientations and parameters that favor smoother finishes on critical surfaces where possible.
- Appropriate Post-Processing: Selecting and effectively applying the right surface finishing techniques (machining, polishing, AFM, electropolishing) based on the specific requirements and geometry.
6. Powder Handling and Quality Management:
- Вызов: Metal powders, especially reactive ones like Titanium or Aluminum, require careful handling to prevent contamination (oxygen, moisture) and ensure safety (flammability/explosion risk). Maintaining powder quality through sieving, storage, and controlled recycling is critical for consistent part properties.
- Solutions:
- Strict Procedures: Implementing robust protocols for powder handling, storage in inert environments, sieving, and traceability.
- Контроль качества: Regularly testing powder characteristics (chemistry, particle size distribution, flowability, morphology).
- Надежность поставщика: Partnering with reputable powder manufacturers like Met3dp ensures high-quality, consistent starting material produced using advanced atomization techniques.
7. Ensuring Consistency and Repeatability:
- Вызов: Achieving the same high quality across multiple builds and multiple parts requires rigorous process control. Variations in machine calibration, powder batches, or ambient conditions can potentially affect outcomes.
- Solutions:
- Robust Quality Management System (QMS): Implementing ISO 9001 or industry-specific standards (e.g., AS9100 for aerospace).
- Process Monitoring & Control: Utilizing sensors and data logging to monitor critical parameters during the build.
- Standardized Procedures: Following defined workflows for build setup, execution, post-processing, and inspection.
- Experienced Provider: Working with an established AM service provider with a proven track record and deep process knowledge significantly reduces variability.
By understanding these potential challenges and working with a knowledgeable and well-equipped partner, businesses can confidently leverage metal 3D printing to produce high-quality, reliable custom impellers that meet the stringent demands of harsh industrial environments.
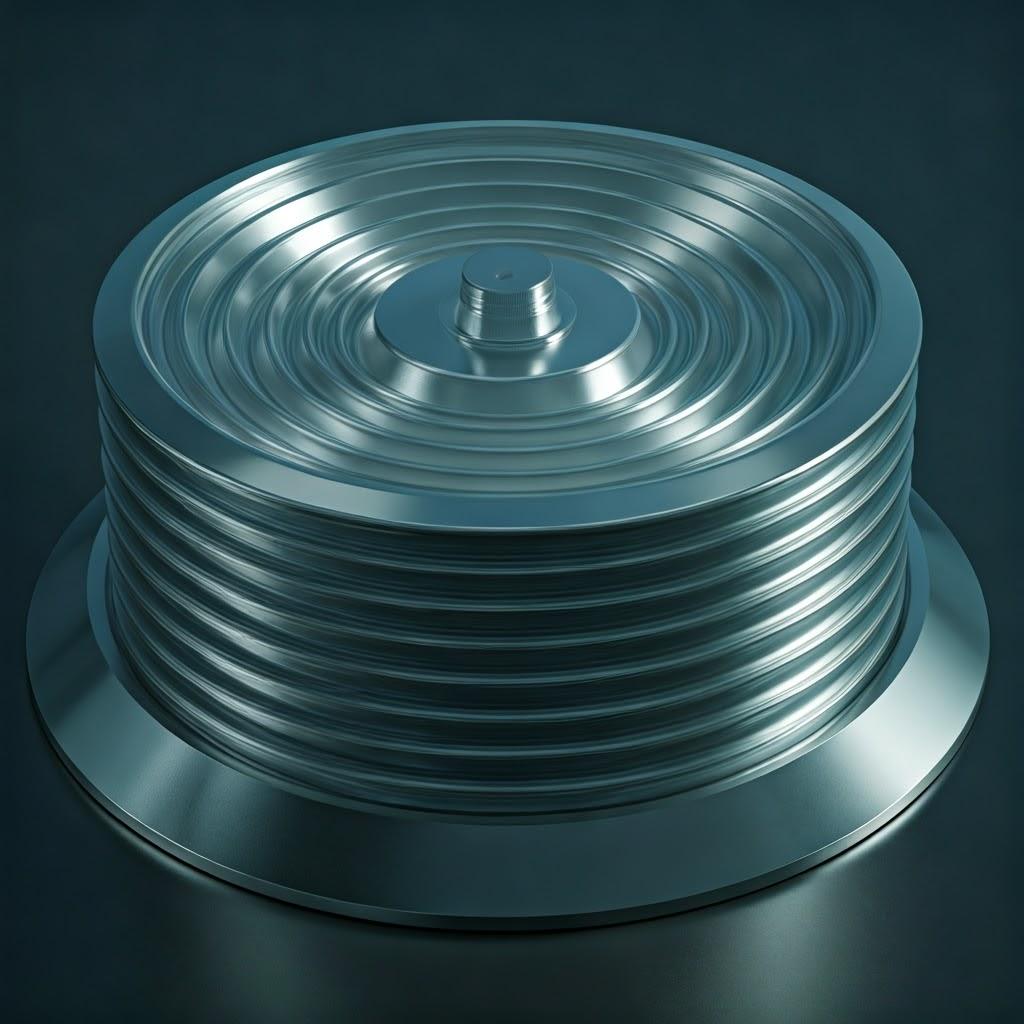
How to Choose the Right Metal 3D Printing Service Provider for Custom Impellers
Selecting the appropriate metal additive manufacturing partner is as critical as choosing the right material or optimizing the design. The success of your 3D printed impeller project – achieving the desired performance, quality, and timely delivery – hinges on the capabilities and expertise of your chosen service provider. For procurement managers and engineers navigating the landscape of metal AM suppliers, especially for demanding applications like custom impellers in harsh environments, a structured evaluation process is essential.
Here are key criteria to consider when selecting a metal 3D printing service provider:
1. Proven Expertise and Experience:
- Application-Specific Knowledge: Does the provider have demonstrable experience printing impellers, turbomachinery components, or parts with similar geometric complexity and functional requirements? Ask for case studies or examples related to fluid handling applications.
- Material Specialization: Expertise in processing the specific alloys you require (e.g., IN625, CuNi30Mn1Fe) is non-negotiable. This includes understanding optimal printing parameters, necessary heat treatments, and potential challenges associated with the material. Providers like Met3dp, with their deep roots in both advanced metal powder manufacturing and printing systems, possess this fundamental material science understanding.
- Опыт работы в отрасли: Familiarity with the quality standards and operational demands of your industry (e.g., aerospace, chemical processing, marine, oil & gas) is a significant advantage.
2. Technological Capabilities:
- Appropriate Printing Technology: Do they operate the right type of Powder Bed Fusion (PBF) system for your needs? While Laser PBF (SLM/DMLS) is common, Electron Beam PBF (SEBM), like the systems developed by Met3dp, can offer advantages for certain materials (e.g., titanium alloys, crack-sensitive materials, potentially copper alloys due to better energy absorption) and can sometimes result in lower residual stress. Ensure their machine build volumes accommodate your impeller size.
- Machine Fleet and Capacity: Consider the number and type of machines they operate. A larger, well-maintained fleet suggests better capacity, redundancy, and potentially shorter lead times. Assess the age and upkeep of their equipment.
- Powder Handling and Management: Stringent controls over powder storage, handling, sieving, and recycling are crucial for consistent part quality. Inquire about their powder management protocols. Met3dp’s own production of high-sphericity, high-flowability powders underscores their commitment to material quality from the source.
3. Comprehensive Post-Processing Capabilities:
- In-House vs. Managed Services: As discussed previously, post-processing is essential for impellers. Does the provider offer critical steps like heat treatment (stress relief, HIP), CNC machining, support removal, and surface finishing in-house? If not, do they have a robust, qualified network of partners and manage the entire process seamlessly? Integrated services often streamline the workflow and ensure accountability.
- Quality Control & Inspection: What Non-Destructive Testing (NDT) methods do they offer (e.g., CT scanning, dye penetrant, ultrasonic testing)? Do they have Coordinate Measuring Machines (CMM) for dimensional verification? Ensure their inspection capabilities align with your part’s criticality.
4. Robust Quality Management System (QMS):
- Сертификаты: Look for relevant certifications as indicators of mature processes and commitment to quality. ISO 9001 is a fundamental requirement for industrial suppliers. Depending on the industry, certifications like AS9100 (Aerospace) or ISO 13485 (Medical) might be necessary or indicative of a higher level of process control.
- Traceability: Can they provide full material and process traceability, linking the final part back to the specific powder batch, machine used, build parameters, and post-processing steps? This is vital for critical components.
5. Engineering and Technical Support:
- Design for Additive Manufacturing (DfAM) Support: Does the provider offer expert guidance on optimizing your impeller design for AM? Collaborative DfAM support can significantly improve printability, performance, and cost-effectiveness. Met3dp, for instance, leverages its collective expertise in metal AM to partner with organizations on application development.
- Problem Solving: How do they handle potential issues during production? A proactive, transparent communication style and strong engineering support are crucial for resolving challenges effectively.
6. Communication, Transparency, and Business Practices:
- Quoting Process: Is their quoting clear, detailed, and timely? Does it break down costs associated with printing, materials, and post-processing?
- Lead Time Communication: Do they provide realistic lead time estimates and proactively communicate any potential delays?
- Обслуживание клиентов: Responsiveness and accessibility of their sales and technical teams are important indicators of a good B2B partnership.
Evaluation Checklist for Potential Suppliers:
Критерии | Questions to Ask | Ideal Response / What to Look For |
---|---|---|
Опыт работы | Show examples of similar parts (impellers). Detail experience with [Material X]. Which industries do you serve? | Relevant case studies, demonstrated success with IN625/CuNi, familiarity with industry standards. |
Технология | Which AM process (SLM, SEBM)? Machine specs (build size)? Powder handling procedures? | Technology suited to material/part, adequate capacity, strict powder quality control (like Met3dp). |
Постобработка | Which steps in-house (Heat Treat, HIP, CNC, Finish)? How are external processes managed? | Comprehensive in-house capabilities preferred, or well-managed, qualified partner network. |
Качество | ISO 9001 certified? Other certs (AS9100)? NDT methods offered? CMM capability? Traceability system? | Relevant certifications, required NDT/inspection methods, robust traceability. |
Support & Engineering | DfAM support available? Who is the technical point of contact? How are issues resolved? | Accessible application engineers, collaborative approach, proactive problem-solving. |
Business & Communication | Quote turnaround time? Quote clarity? Lead time estimation process? Communication channels? | Transparent pricing, realistic lead times, responsive communication. |
Export to Sheets
By systematically evaluating potential suppliers against these criteria, companies can confidently select a metal 3D printing partner like Met3dp, who not only possesses the advanced technology and material expertise but also operates with a commitment to quality, collaboration, and customer success, ensuring your custom impeller project achieves its objectives.
Understanding Cost Factors and Lead Time for 3D Printed Impellers
One of the primary considerations for adopting any manufacturing technology is understanding the associated costs and production timelines. Metal additive manufacturing, while offering significant technical advantages, has a different cost structure compared to traditional methods. Providing accurate B2B quotes requires careful consideration of several factors that influence the final price and lead time of a 3D printed impeller.
Key Cost Drivers for Metal AM Impellers:
- Part Volume & Bounding Box: This is often the most significant cost factor. The amount of material used (calculated from the part’s volume) directly impacts cost. Additionally, the overall size (bounding box) dictates how much space the part occupies in the build chamber and influences the printing time. Larger parts generally cost more.
- Тип материала: High-performance alloys like IN625 are inherently more expensive raw materials than standard stainless steels or aluminum alloys. Copper-nickel alloys also carry a premium. The cost per kilogram (/kg) or cubic centimeter (/cm3) of the chosen powder is a major input. Powder suppliers like Met3dp focus on producing high-quality, spherical powders suitable for AM, which represents significant value but also factors into the cost.
- Время машин: This encompasses the actual time the AM machine spends building the part and its supports, layer by layer.
- Build Height: Taller parts take longer to print.
- Сложность: While AM handles complexity well, very intricate features or large cross-sectional areas per layer can sometimes influence print parameters and time.
- Number of Parts per Build: Printing multiple parts simultaneously can optimize machine utilization and potentially reduce the cost per part compared to printing a single unit.
- Поддерживающие структуры: Most complex metal AM parts require support structures to anchor them to the build plate, manage thermal stresses, and support overhanging features.
- Volume of Supports: Supports consume material and machine time, adding to the cost. Efficient DfAM aims to minimize support needs.
- Support Removal Effort: Removing supports (manually, via machining, or EDM) requires labor and potentially specialized equipment, contributing significantly to post-processing costs. Complex internal supports can be particularly challenging and costly to remove.
- Post-Processing Intensity: As detailed earlier, the required post-processing steps heavily influence the final cost.
- Heat Treatment (Stress Relief, Annealing, HIP): Furnace time and specialized equipment (like HIP units) add cost. HIP is a significant cost adder but often necessary for critical applications.
- Обработка: Achieving tight tolerances on bores, keyways, sealing surfaces, or blade profiles requires CNC machining, adding substantial cost based on complexity and time.
- Отделка поверхности: Manual polishing, bead blasting, or other finishing methods require labor and consumables.
- Quality Assurance & Inspection: The level of inspection required (visual, dimensional via CMM, NDT like CT scanning or dye penetrant) adds cost based on the time, equipment, and expertise involved. More stringent requirements mean higher costs.
- Объем заказа: While AM eliminates tooling costs (making low volumes viable), there are still setup costs (build preparation, machine setup). Higher volumes can allow for better machine utilization and potentially small per-part cost reductions, but the cost curve doesn’t drop as steeply as with mass production methods like casting after tooling amortization.
- Engineering & Setup: Initial design review, DfAM consultation, build file preparation, and machine setup contribute to the overall project cost, often amortized over the number of parts produced.
Typical Lead Time Components:
Lead time is the total duration from order placement to part delivery. It’s crucial to understand the contributing factors:
- Quotation & Design Review: Initial communication, quote generation, design finalization, and DfAM checks. (1-5 days)
- Order Confirmation & Scheduling: Placing the part into the production queue. Queue times can vary significantly based on the service provider’s backlog. (1 day – 2 weeks)
- Build Preparation: Preparing the build file, setting up the machine, loading powder. (0.5 – 1 day)
- Время печати: Actual machine runtime, which can range from hours for small impellers to several days for large, complex ones. (1 – 7+ days)
- Cool Down & Depowdering: Allowing the build chamber to cool, removing the part(s), and cleaning off excess powder. (0.5 – 1 day)
- Постобработка: This is often the longest and most variable part of the lead time.
- Stress Relief/Heat Treatment: 1-3 days (including furnace time and handling)
- Support Removal & Basic Finishing: 1-3 days
- HIP: Can add 3-7 days (including shipping to/from HIP facility if not in-house)
- CNC Machining: Highly variable, 2 days to 2+ weeks depending on complexity.
- Advanced Surface Finishing: 1-5 days
- Проверка качества: Dimensional checks, NDT. (1-3 days)
- Packing & Shipping: (1-5 days depending on destination and method)
Estimated Total Lead Times (Ballpark):
- Prototypes (minimal post-processing): 1 – 3 недели
- Functional Parts (standard post-processing, no HIP/complex machining): 3 – 6 weeks
- Critical Parts (extensive post-processing, HIP, complex machining, NDT): 6 – 10+ weeks
Transparency is Key: Reputable metal AM service providers like Met3dp will provide detailed quotes outlining cost components and realistic lead time estimates based on your specific impeller design, material, post-processing needs, and current capacity. Understanding these factors allows for better project planning and budgeting when incorporating metal AM into your supply chain.
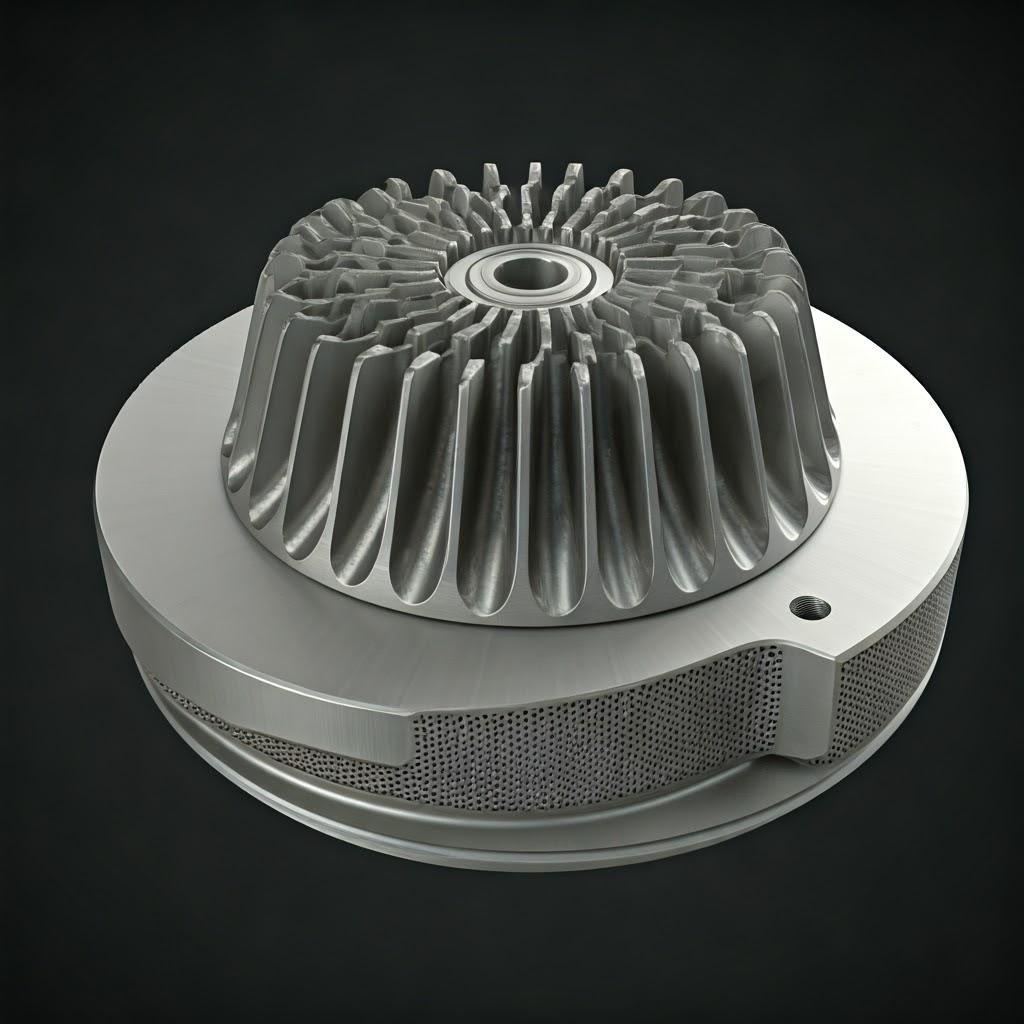
Frequently Asked Questions (FAQ) about 3D Printed Pump Impellers
As metal additive manufacturing becomes more prevalent for producing critical components like pump impellers, engineers and procurement managers often have questions about the technology’s capabilities, limitations, and comparison to traditional methods. Here are answers to some common questions:
1. How does the strength and durability of a 3D printed metal impeller compare to a cast or machined one?
The mechanical properties (strength, durability, fatigue life) of a 3D printed metal impeller can be comparable, and sometimes superior, to those manufactured by traditional methods, provided that several conditions are met:
- Оптимизация процессов: The AM process parameters must be meticulously optimized for the specific material to achieve high density (typically >99.5%, often >99.9% post-HIP).
- Appropriate Post-Processing: Heat treatments (like stress relief, solution annealing, aging) are crucial to achieve the desired microstructure and mechanical properties for the alloy. Hot Isostatic Pressing (HIP) is often recommended, especially for fatigue-critical applications, as it helps close internal microporosity, significantly improving fatigue life and ductility, bringing properties closer to or exceeding wrought material standards.
- Качество материала: High-quality, AM-specific metal powder (like those produced by Met3dp) is essential for consistent results.
- Дизайн: While AM allows complex shapes, proper DfAM must be followed to avoid stress concentrations.
In summary, a well-designed, properly printed, and correctly post-processed AM impeller using high-quality materials can meet or exceed the performance of cast counterparts and approach the properties of components machined from wrought billet, especially after HIP.
2. Is 3D printing cost-effective for impellers compared to traditional methods (casting, machining)?
Cost-effectiveness depends heavily on several factors:
- Объем: For high-volume production (thousands of identical parts), casting is typically more cost-effective due to the amortization of tooling costs.
- Сложность: For highly complex impeller geometries that would require intricate molds or extensive multi-axis machining, AM can be more cost-effective, even at lower volumes, because complexity doesn’t add cost in the same way.
- Customization & Prototyping: AM is almost always more cost-effective for one-off prototypes, highly customized designs, or very low volume production runs, as it completely eliminates tooling costs and allows for rapid iteration.
- Материал: If the required material is very difficult or expensive to cast or machine, AM might offer a more viable manufacturing route.
- Lead Time Urgency: If rapid delivery is critical (e.g., emergency replacement), the speed advantage of AM (bypassing tooling) can provide significant value, potentially offsetting a higher per-part cost.
The breakeven point varies, but generally, AM is most competitive for complex, customized, low-to-mid volume impellers, or where rapid prototyping/delivery is essential.
3. What is the typical surface finish of a 3D printed impeller before and after post-processing?
- As-Printed: The surface roughness (Ra) of parts produced by Powder Bed Fusion processes typically ranges from 10 to 25 micrometers (µm) or roughly 400-1000 microinches (µin). The finish depends on factors like layer thickness, particle size, material, orientation, and process parameters. Upward-facing surfaces are generally smoother than downward-facing or sharply angled surfaces influenced by support structures. This finish is often too rough for optimal hydraulic performance on impeller blades.
- After Post-Processing: Significant improvements are possible:
- Bead Blasting/Tumbling: Can achieve Ra values of 5-10 µm.
- CNC Machining: Can achieve very smooth finishes (Ra < 1 µm) on specific critical surfaces (bores, sealing faces, potentially blade profiles if required).
- Polishing (Manual or Automated): Can achieve mirror-like finishes (Ra << 1 µm) but is labor-intensive and typically reserved for specific areas or applications demanding extremely low friction.
Achieving the required surface finish, particularly on the complex curved surfaces of impeller blades, is a key consideration in post-processing planning and cost.
4. Can complex internal cooling channels be integrated into 3D printed impellers?
Yes, absolutely. This is one of the significant advantages of metal additive manufacturing. AM allows for the design and creation of intricate internal channels and conformal cooling passages directly within the impeller body during the printing process. These channels can be optimized for:
- Targeted Cooling: Directing coolant flow precisely to high-temperature zones, crucial for impellers handling very hot fluids or in high-speed applications.
- Повышенная эффективность: Conformal channels follow the part’s contours, providing more effective and uniform cooling compared to traditionally drilled straight holes.
- Recirculation/Flow Management: Internal passages can be designed to manage fluid recirculation within the pump casing or mitigate cavitation effects.
Designing these channels requires careful consideration of DfAM principles, such as ensuring channels are self-supporting where possible or designing appropriate access points for powder removal after printing.
5. What certifications should I look for in a metal 3D printing service provider for industrial impellers?
The required certifications depend on the end-use application and industry standards:
- ISO 9001: This is the foundational standard for Quality Management Systems and should be considered a minimum requirement for any reputable industrial supplier. It demonstrates that the provider has established processes for quality control, documentation, continuous improvement, and customer satisfaction.
- AS9100: If the impeller is for aerospace or defense applications, AS9100 certification is often mandatory. It includes all ISO 9001 requirements plus additional stringent controls specific to the aerospace industry (e.g., traceability, configuration management, risk management).
- ISO 13485: For medical pump applications, this certification specific to medical device quality management systems would be relevant.
- Material Certifications: Ensure the provider can supply material test certificates (confirming chemical composition and sometimes basic mechanical properties of the powder batch) and certificates of conformity for the final parts.
Look for providers like Met3dp who emphasize their commitment to quality and possess the necessary systems and potentially certifications relevant to demanding industrial sectors.
Conclusion: Driving Innovation in Fluid Handling with Custom Metal 3D Printed Impellers
The challenges posed by harsh operating environments – demanding extreme corrosion resistance, high-temperature stability, and wear resilience – necessitate advanced solutions for critical pump components. Custom impellers, specifically tailored to the unique demands of applications in chemical processing, marine, oil and gas, power generation, and beyond, are crucial for achieving optimal performance, efficiency, and reliability.
Metal additive manufacturing has emerged as a powerful enabler, transcending the limitations of traditional casting and machining. By leveraging metal 3D printing, companies gain access to:
- Беспрецедентная свобода дизайна: Crafting highly complex, optimized impeller geometries previously unattainable, leading to significant improvements in hydraulic efficiency and performance.
- Advanced Material Capabilities: Utilizing high-performance alloys like IN625 and CuNi30Mn1Fe, specifically chosen for their exceptional resistance to corrosion, temperature, and wear in demanding environments.
- Accelerated Innovation Cycles: Rapidly prototyping and iterating on designs to achieve optimal performance much faster than traditional methods allow.
- On-Demand, Customized Production: Manufacturing impellers cost-effectively in low-to-mid volumes without the prohibitive expense and lead time of tooling, enabling customized solutions and efficient spare parts management.
However, realizing the full potential of metal AM requires more than just access to a printer; it demands expertise in materials science, DfAM principles, process control, and comprehensive post-processing. Partnering with the right service provider is paramount.
Met3dp stands as a leader in the field, offering a synergistic combination of cutting-edge metal AM systems (including industry-leading SEBM technology), high-quality spherical metal powders manufactured in-house using advanced atomization techniques, and decades of collective expertise in additive manufacturing applications. Our commitment extends beyond simply printing parts; we partner with organizations to develop comprehensive solutions, providing the engineering support and process rigor needed to tackle challenging components like custom impellers for harsh environments.
Whether you are seeking enhanced corrosion resistance with IN625, superior biofouling and seawater resistance with CuNi30Mn1Fe, or exploring other advanced alloys for your fluid handling systems, metal AM offers a pathway to significant improvements.
Ready to revolutionize your pump performance? Explore the possibilities of custom metal 3D printed impellers. Contact Met3dp today to discuss your specific application requirements and learn how our advanced additive manufacturing solutions can power your organization’s innovation goals.
Поделиться
MET3DP Technology Co., LTD - ведущий поставщик решений для аддитивного производства со штаб-квартирой в Циндао, Китай. Наша компания специализируется на производстве оборудования для 3D-печати и высокопроизводительных металлических порошков для промышленного применения.
Сделайте запрос, чтобы получить лучшую цену и индивидуальное решение для вашего бизнеса!
Похожие статьи
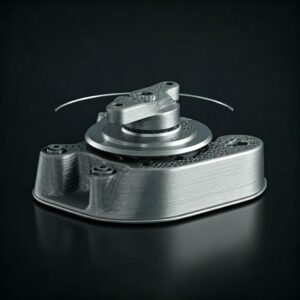
3D-печатные крепления для автомобильных радарных датчиков: Точность и производительность
Читать далее "О компании Met3DP
Последние обновления
Наш продукт
CONTACT US
Есть вопросы? Отправьте нам сообщение прямо сейчас! После получения Вашего сообщения мы всей командой выполним Ваш запрос.
Получите информацию о Metal3DP
Брошюра о продукции
Получить последние продукты и прайс-лист
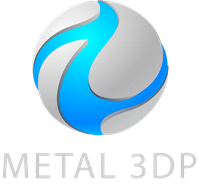
Металлические порошки для 3D-печати и аддитивного производства