Порошок для литья под давлением
Оглавление
Порошок для литья под давлением относится к типу исходного материала, используемого в порошковом литье под давлением - промышленном производственном процессе для изготовления сложных и высокоточных металлических деталей. Этот порошок представляет собой смесь мелкодисперсных металлических порошков и полимерных связующих, которые могут быть отлиты под давлением в сложные детали сетчатой формы в большом объеме.
Преимущества использования порошка для литья под давлением
Преимущество | Описание | Выгода |
---|---|---|
Сложные геометрии: IMP позволяет создавать сложные формы с тонкими элементами, которые трудно или невозможно получить с помощью традиционных методов литья под давлением. Такая свобода дизайна открывает двери для создания инновационных компонентов в различных отраслях промышленности. | В отличие от традиционных формовочных материалов, таких как расплавленные пластмассы, в IMP используется связующая система, которая удерживает частицы порошка вместе в процессе формования. Это позволяет создавать детали с внутренними каналами, вырезами и другими сложными геометрическими формами. | |
Эффективность материала: IMP способствует изготовлению изделий практически чистой формы, минимизируя отходы материала по сравнению с субтрактивными методами, такими как механическая обработка. Это особенно полезно для дорогих или высокопроизводительных материалов. | Точный контроль над распределением порошка при литье под давлением сводит к минимуму избыточный расход материала. Кроме того, в отличие от традиционных процессов, в ходе которых при пробных испытаниях образуются бракованные детали, IMP позволяет ускорить итерации конструкции при минимальных отходах материала. | |
Широкий выбор материалов: IMP предлагает более широкий выбор материалов по сравнению с традиционным литьем под давлением. Такая универсальность позволяет создавать детали с особыми свойствами, соответствующими конкретным условиям применения. | Помимо стандартных полимеров, используемых при литье под давлением, в IMP могут применяться металлические порошки, керамика и даже композитные материалы. Это открывает возможности для создания деталей с уникальными сочетаниями прочности, электропроводности или биосовместимости. | |
Высокопроизводительные детали: Возможность использования металлических и керамических порошков в IMP позволяет производить высокопроизводительные детали с исключительной прочностью, жаростойкостью или износостойкостью. | Металлические детали, изготовленные методом литья под давлением (MIM), могут достигать механических свойств, сравнимых с деформируемыми (объемными) металлами, что делает их пригодными для применения в сложных условиях. Аналогичным образом, керамические детали IMP обеспечивают превосходную износостойкость и высокотемпературные характеристики. | |
Потенциал массового производства: Изначально технология IMP использовалась для создания прототипов, но с развитием технологии стало возможным экономически эффективное массовое производство сложных деталей. | Высокая степень автоматизации процессов IMP позволяет эффективно производить большое количество деталей с неизменным качеством. Это делает его оптимальным вариантом для крупносерийного производства. | |
Улучшенная отделка поверхности: По сравнению с традиционными методами литья металлов, IMP иногда позволяет добиться более гладкой поверхности готовых деталей. | Использование мелкодисперсных порошков и контролируемый процесс формования позволяют свести к минимуму дефекты поверхности, что потенциально снижает потребность в тщательной последующей обработке, например, полировке. |
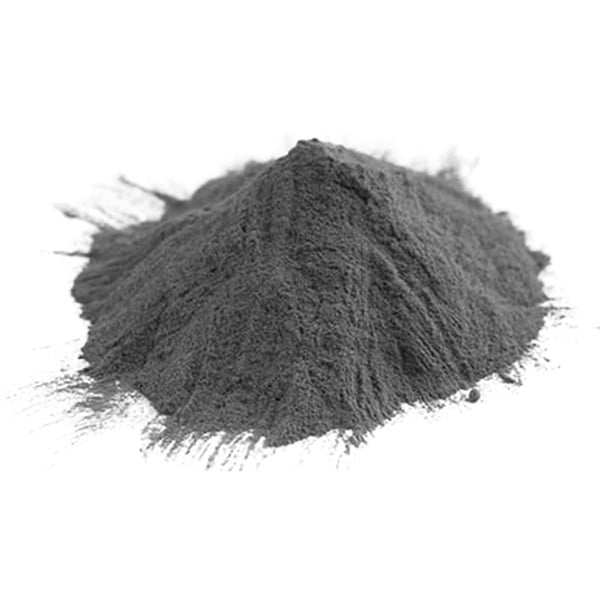
Состав порошка для литья под давлением
Компонент | Описание | Функция |
---|---|---|
Базовые порошки | Они представляют собой основной функциональный материал конечной детали и могут быть разделены на три основных типа: Металлические порошки: Мелкодисперсные металлические частицы из различных сплавов, таких как нержавеющая сталь, инструментальная сталь или суперсплавы. Керамические порошки: Керамические материалы, такие как глинозем, диоксид циркония или нитрид кремния, в виде порошка. Полимерные порошки: Термопластичные полимеры, обычно используемые для литья под давлением, такие как нейлон или полипропилен. | Выбор базового порошка определяет конечные свойства формованной детали, такие как прочность, износостойкость или тепловые характеристики. |
Система скоросшивателей | Это важный компонент, который действует как временный клей, удерживая частицы основного порошка вместе в процессе формования. Связующая система обычно состоит из: Термопластичный полимер: Термопластичная смола, которая плавится на этапе литья под давлением, обеспечивая текучесть и адгезию с базовым порошком. * Воски или добавки: Они могут улучшать текучесть, повышать эффективность разрыхления или способствовать диспергированию порошка в связующем. | Благодаря связующей системе порошок ведет себя как сырье для формования при впрыске и позволяет создавать сложные формы. |
Формирователи пор | Это необязательные добавки, которые создают временные поры в формованной детали. Они могут быть: * Органические материалы: Они выгорают во время дебридинга, оставляя после себя сеть пор, которые облегчают удаление связующего. * Химические выщелачивающие агенты: Они растворяются в специальном растворителе на этапе последующей обработки, создавая контролируемую структуру пор. | Формирователи пор позволяют создавать пористые структуры в конечной детали, что может быть полезно для таких применений, как фильтры или костные имплантаты. |
Характеристики используемых металлических порошков
Характеристика | Описание | Важность в MIM |
---|---|---|
Размер и распределение частиц | Размер и распределение частиц металлического порошка существенно влияют на следующие аспекты MIM: Заполнение формы и прочность зелени: Более мелкие порошки обычно обеспечивают лучшую плотность упаковки и могут улучшить заполнение формы при впрыске. Однако слишком мелкие частицы могут препятствовать текучести и вызывать проблемы при обработке. Узкий гранулометрический состав обеспечивает равномерную упаковку и минимизирует пустоты в литой детали, способствуя хорошей зеленой прочности (прочности детали до спекания). Поведение при спекании и конечные свойства: Размер частиц влияет на процесс спекания, в ходе которого частицы соединяются друг с другом, образуя твердую структуру. Порошки с более широким распределением частиц по размерам могут привести к неоднородному спеканию и потенциально повлиять на конечные механические свойства детали. | Тщательный выбор размера и распределения частиц имеет решающее значение для достижения хорошего заполнения формы, зеленой прочности и оптимальных характеристик конечного спеченного компонента. |
Морфология частиц | Это относится к форме частиц металлического порошка. В идеале в процессах MIM предпочтение отдается порошкам со сферической или близкой к сферической морфологией. | Сферические частицы легче текут, улучшая заполнение формы и плотность упаковки. Частицы неправильной формы могут создавать пустоты и препятствовать текучести, что может привести к дефектам в формованной детали. |
Кажущаяся и таповая плотность | Эти свойства отражают насыпную плотность порошка при различных условиях. Кажущаяся плотность: Это плотность порошка в состоянии покоя с учетом промежутков между частицами. Плотность отвода: Это отражает более плотное состояние, достигнутое благодаря стандартизированному процессу отвода. | Высокая плотность ленты обычно желательна в MIM для эффективного использования материала и хорошей точности размеров конечной детали. Она также способствует улучшению упаковки при формовке и минимизирует усадку при спекании. |
Химический состав | Конкретные элементы или сплавы, используемые в металлическом порошке, определяют конечные свойства спеченной детали. | Выбор состава металлического порошка позволяет изменять такие свойства, как прочность, коррозионная стойкость или износостойкость, в соответствии с конкретными требованиями приложения. В MIM могут использоваться различные металлические сплавы, включая нержавеющую сталь, инструментальную сталь и даже высокопроизводительные сплавы, такие как инконель. |
Текучесть | Это означает легкость, с которой порошок течет под действием силы тяжести или приложенных усилий. | Хорошая текучесть необходима для равномерного распределения порошка при литье под давлением. Порошки с плохой текучестью могут привести к несоответствию плотности упаковки и потенциальным дефектам в готовой детали. |
Стандарты на металлические порошки
Используемые металлические порошки должны соответствовать стандартам по составу и зернистости:
Стандартное тело | Стандарт | Описание | Важность в IMP |
---|---|---|---|
ASTM International (ASTM) | ASTM B930 - Стандартное руководство по определению характеристик порошков для литья металлов под давлением (MIM) | В настоящем стандарте изложены различные методы испытаний для определения свойств металлических порошков, используемых в MIM. | Обеспечивает основу для оценки таких факторов, как гранулометрический состав, морфология, текучесть и кажущаяся плотность. Это обеспечивает постоянство и контроль качества металлических порошков, используемых в IMP. |
** | ** | * ASTM B783 - Стандартная спецификация на порошки из нержавеющей стали для литья металлов под давлением (MIM) | Настоящий стандарт устанавливает специальные требования к химическому составу, гранулометрическому составу и текучести порошков из нержавеющей стали, используемых в MIM. |
** | ** | * ASTM D4000 - Стандартная система классификации для определения пластиковых материалов | Хотя этот стандарт не относится исключительно к IMP, в нем представлена система классификации различных типов пластиковых материалов, включая те, которые потенциально могут использоваться в качестве связующих в сырье IMP. |
Международная организация по стандартизации (ISO) | * ISO 3095 - Металлические порошки - Определение расхода с помощью расходомера Холла | Настоящий стандарт устанавливает метод измерения текучести металлических порошков с помощью расходомера Холла. | Обеспечивает стандартизированный подход к оценке текучести, критической характеристики для достижения хорошего заполнения формы и стабильного качества деталей в IMP. |
** | ** | * ISO 4497 - Пластмассы - Определение скорости течения расплава (MFR) и объемной скорости течения расплава (MVR) термопластов | Настоящий стандарт устанавливает метод измерения скорости течения расплава (MFR) термопластичных материалов, который может быть применим к связующему компоненту в сырье IMP. |
Этапы производственного процесса
Процесс производства состоит из следующих основных этапов:
Шаг | Описание | Важность |
---|---|---|
1. Подготовка и смешивание порошка | Порошок-основа (металлический, керамический или полимерный) тщательно отбирается и проходит предварительную обработку в зависимости от желаемых конечных свойств. В состав могут быть включены такие добавки, как порообразователи или смазочные материалы. Затем порошок точно взвешивается и смешивается со связующей системой для получения однородного сырья. | На этом этапе закладывается основа свойств конечной детали. Тщательный выбор и точное смешивание обеспечивают стабильное поведение материала в процессе обработки. |
2. Литье под давлением | Подготовленное сырье IMP нагревается до полурасплавленного состояния и впрыскивается в закрытую полость пресс-формы под высоким давлением. Форма повторяет желаемую форму конечной детали. | На этом этапе определяется геометрия детали. Постоянный поток и давление во время впрыска имеют решающее значение для достижения точных размеров детали и минимальных дефектов. |
3. Дебиндинг | Отформованная деталь, также называемая "зеленой деталью", проходит процесс дебридинга для удаления связующей системы. Это может быть достигнуто путем: * Растворитель для связывания: Деталь погружается в растворитель, который растворяет связующее вещество, оставляя после себя порошковую структуру. * Термическое скрепление: Деталь подвергается контролируемому циклу нагрева, в ходе которого связующее термически разлагается и выходит в виде газа. | Эффективное обезжиривание имеет решающее значение для достижения окончательной желаемой формы и пористости без повреждения хрупкой структуры порошка. |
4. Спекание | Отшлифованная деталь подвергается воздействию высоких температур в контролируемой атмосфере (часто в вакууме или инертном газе). Этот процесс способствует диффузии и сцеплению между частицами порошка, в результате чего получается твердая деталь, близкая к сетчатой форме. | Спекание определяет конечные механические свойства детали, такие как прочность, плотность и стабильность размеров. Точный контроль температуры и управление атмосферой очень важны. |
5. Постобработка | В зависимости от требований применения спеченная деталь может проходить дополнительные этапы отделки, такие как: * Обработка или шлифовка: Для достижения точных допусков размеров или отделки поверхности. * Термообработка: Для улучшения определенных механических свойств, таких как прочность или твердость. * Покрытие или инфильтрация: Для улучшения свойств поверхности, таких как износостойкость или коррозионная стойкость. | Постобработка может еще больше повысить функциональность и эстетику конечной детали IMP. |
Области применения деталей, изготовленных методом литья под давлением
Порошок для литья под давлением может использоваться для производства различных сложных и высокоточных деталей в различных отраслях промышленности:
Промышленность | Примеры применения | Преимущества литья под давлением |
---|---|---|
Автомобильная промышленность | Компоненты интерьера (приборные панели, дверные панели, консоли) Подкапотные детали (кожухи вентиляторов, впускные коллекторы) Функциональные компоненты (шестерни, звездочки) | Крупносерийное производство сложных форм с точными характеристиками. Облегченные детали для повышения топливной экономичности. Широкий выбор материалов для различных эксплуатационных требований (долговечность, термостойкость). |
Потребительская электроника | Корпуса для электроники (телефоны, ноутбуки, планшеты) Разъемы и кнопки Внутренние компоненты (кронштейны, шестерни) | Массовое производство сложных деталей с высокой точностью размеров. Гладкая поверхность обеспечивает эстетику и комфорт для пользователя. Разнообразие цветов и фактур достигается благодаря выбору материала и технике формовки. |
Медицинские приборы | Хирургические инструменты (ручки, рукоятки) Протезные компоненты (коленные суставы, зубные имплантаты) Одноразовые медицинские компоненты (шприцы, флаконы) | Стерилизуемые материалы для гигиены и безопасности. Биосовместимые материалы для использования в человеческом организме (некоторые полимеры и металлические сплавы). Сложные геометрические формы для точной функциональности в медицинских приложениях. |
Аэрокосмическая и оборонная промышленность | Авиационные компоненты (воздуховоды, детали шасси) Спутниковые компоненты (кронштейны, корпуса) Оборонное снаряжение (шлемы, компоненты оружия) | Легкие и высокопрочные материалы для снижения веса в аэрокосмической отрасли. Огнестойкие или термостойкие материалы для особых требований. Долговечные детали для жестких условий эксплуатации. |
Потребительские товары | Игрушки и игры Приборы (корпуса, ручки, циферблаты) Спортивные товары (шлемы, запчасти для велосипедов) | Экономически эффективное производство крупносерийных потребительских товаров. Широкий выбор цветов и отделок для визуальной привлекательности. Прочные и функциональные детали для повседневного использования. |
Преимущества литья под давлением для изготовления деталей
Преимущество | Описание | Выгода |
---|---|---|
Крупносерийное производство: Литье под давлением позволяет эффективно производить большое количество одинаковых деталей. Возможности автоматизации и быстрое время цикла обеспечивают экономически эффективное массовое производство. | Это особенно выгодно для изделий, требующих миллионных тиражей, таких как бытовая электроника или автомобильные компоненты. Неизменное качество и повторяемость обеспечиваются на протяжении всего производственного цикла. | |
Гибкость конструкции: Литье под давлением позволяет создавать широкий диапазон геометрических сложностей, включая сложные формы, тонкие стенки и внутренние элементы. Такая свобода проектирования позволяет создавать функциональные и инновационные детали. | В отличие от некоторых субтрактивных методов производства, литье под давлением не ограничено геометрией инструмента. Подрезы, каналы и другие сложные элементы могут быть непосредственно впрессованы в деталь. | |
Точность и повторяемость размеров: Точный контроль над конструкцией пресс-формы и параметрами впрыска позволяет добиться постоянства и точности размеров деталей при больших объемах производства. | Это сводит к минимуму необходимость последующей обработки для коррекции размеров и обеспечивает взаимозаменяемость деталей при сборке. Повторяемость имеет решающее значение для поддержания стабильного качества и функциональности продукции. | |
Широкий выбор материалов: При литье под давлением может использоваться огромное количество материалов, включая термопласты, термореактивные материалы, эластомеры и даже некоторые металлические сплавы (при литье металлов под давлением - MIM). | Такая универсальность позволяет выбрать оптимальный материал в зависимости от желаемых свойств, таких как прочность, термостойкость, химическая стойкость или гибкость. | |
Отделка поверхности и эстетика: Литье под давлением позволяет получать детали с гладкой и высококачественной поверхностью, что часто избавляет от необходимости проводить обширную последующую обработку, например полировку. Кроме того, в процессе формования можно вводить различные красители и текстуры. | Это способствует визуальной привлекательности и функциональности конечного продукта. Гладкие поверхности могут быть важны для обеспечения гигиены в медицинских приборах или для легкой очистки в потребительских товарах. | |
Эффективность материала: Литье под давлением способствует изготовлению изделий практически чистой формы, что сводит к минимуму отходы материала по сравнению с субтрактивными методами, такими как механическая обработка. Излишки материала, называемые литниковой массой и бегунками, часто могут быть переработаны и повторно использованы в последующих партиях продукции. | Это выгодно с точки зрения стоимости и экологичности. Минимизация отходов также снижает воздействие производственного процесса на окружающую среду. | |
Потенциал автоматизации: Процесс литья под давлением может быть в значительной степени автоматизирован, при этом вмешательство человека в процесс минимально. Это позволяет добиться стабильного качества продукции и снизить трудозатраты. | Автоматизация особенно выгодна при крупносерийном производстве и обеспечивает стабильное качество продукции независимо от уровня квалификации оператора. |
Ограничения производственного процесса
Есть и некоторые ограничения:
- Вес детали не превышает < 400 г
- Толщина стенок > 0,4 мм
- Сборки, необходимые для сложных геометрических форм
- Дорогостоящая оснастка для пресс-форм
- Размерные изменения во время спекания
Мировые поставщики исходного сырья
Многие международные компании поставляют готовый исходный материал для литья под давлением:
Компания | Расположение | Материалы |
---|---|---|
BASF | Германия | Нержавеющая сталь 316L, титановые сплавы |
Sandvik | Швеция | Нержавеющие стали, инструментальные стали |
GKN | ВЕЛИКОБРИТАНИЯ | Алюминиевые и магниевые сплавы |
Rio Tinto | Австралия | Металлические и керамические инъекционные смеси |
Ориентировочное ценообразование
Материал | Диапазон цен |
---|---|
Нержавеющая сталь | $50-70 за кг |
Инструментальная сталь | $45-65 за кг |
Вольфрам тяжелый сплав | $130-170 за кг |
Ценообразование зависит от объема заказа, потребностей в персонализации и экономических факторов.
Плюсы и минусы использования Порошки для литья под давлением
Преимущества | Недостатки |
---|---|
Замысловатые и сложные формы | Ограниченные размеры и вес |
Более строгие допуски | Дорогие инструменты и оборудование |
Тонкая обработка поверхности | Размерные изменения во время спекания |
Ассортимент материалов | Часто требуется постобработка |
Высокая производительность, низкая стоимость одной детали | Хрупкие материалы склонны к растрескиванию |
Сокращение отходов | Ограничивает выбор материала |
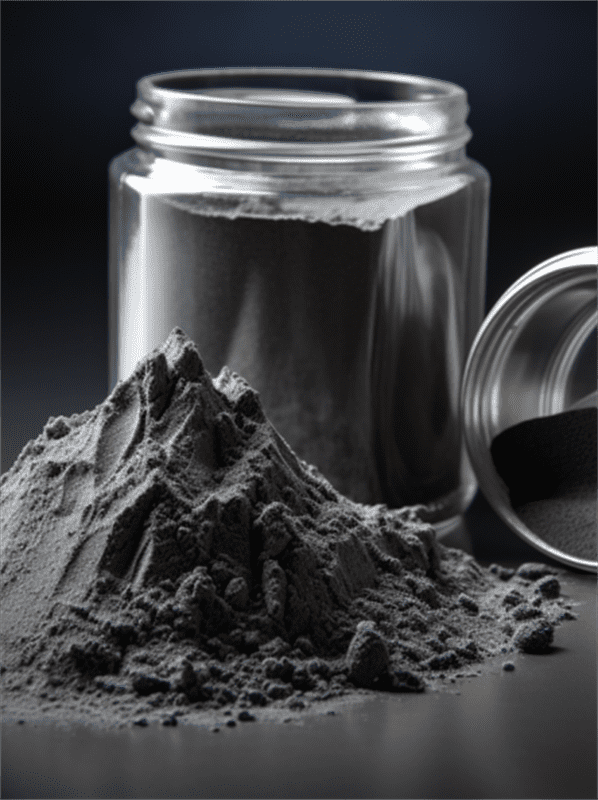
ЧАСТО ЗАДАВАЕМЫЕ ВОПРОСЫ
В: Каков типичный состав порошков для литья под давлением?
О: Они содержат 80-90% металлического порошка, 8-20% связующего вещества и 1-2% смазочных материалов по весу. Обычными связующими являются воск, полипропилен, полиэтилен и полиэтиленгликоль.
В: Какой диапазон размеров порошков используется?
О: Используются порошки в диапазоне 1-20 микрон. Более мелкий порошок повышает плотность, но может быть склонен к агломерации.
Вопрос: Какова степень усадки при спекании?
О: В процессе жидкофазного спекания происходит линейная усадка деталей до 20%. При проектировании инструмента необходимо предусмотреть соответствующие поправки.
Вопрос: Что вызывает трещины в литых деталях из спеченного металла?
О: Неравномерный нагрев в печах, использование быстрого охлаждения после спекания, плохое перемешивание порошка и выбор хрупких сплавов.
В: Какие существуют варианты материалов для литьевых порошков?
О: Нержавеющие стали, инструментальные стали, тяжелые сплавы вольфрама, медные сплавы, титан и титановые сплавы и др.
Поделиться
MET3DP Technology Co., LTD - ведущий поставщик решений для аддитивного производства со штаб-квартирой в Циндао, Китай. Наша компания специализируется на производстве оборудования для 3D-печати и высокопроизводительных металлических порошков для промышленного применения.
Сделайте запрос, чтобы получить лучшую цену и индивидуальное решение для вашего бизнеса!
Похожие статьи
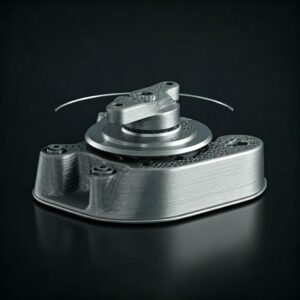
3D-печатные крепления для автомобильных радарных датчиков: Точность и производительность
Читать далее "О компании Met3DP
Последние обновления
Наш продукт
CONTACT US
Есть вопросы? Отправьте нам сообщение прямо сейчас! После получения Вашего сообщения мы всей командой выполним Ваш запрос.
Получите информацию о Metal3DP
Брошюра о продукции
Получить последние продукты и прайс-лист
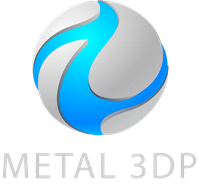
Металлические порошки для 3D-печати и аддитивного производства