Оборудование для распыления металлических порошков
Оглавление
Распыление металлических порошков представляет собой технологию измельчения частиц, используемую для получения тонких металлических порошков с оптимальными характеристиками для промышленного применения. При этом расплавленный металл подается через сопло, в результате чего он распадается на однородные капли, которые быстро затвердевают, превращаясь в частицы порошка.
Распыление позволяет контролировать распределение частиц порошка по размерам, морфологию, чистоту и другие свойства, необходимые для обеспечения высокой производительности при 3D-печати металлов, изготовлении деталей методом порошковой металлургии, нанесении металлических покрытий и т.д. В данной статье представлен полный обзор различных типов оборудования для распыления, принципов работы, конструктивных особенностей, областей применения, преимуществ и ограничений.
Обзор процесса распыления металлических порошков
Распыление металлических порошков позволяет превратить сыпучий жидкий металл в мелкие сферические порошки с регулируемыми характеристиками. Это достигается путем дробления потока расплавленного металла на мелкие капли с помощью газовой или жидкостной струи. При охлаждении капли быстро затвердевают, превращаясь в частицы порошка.
Основными этапами этого процесса являются:
- Плавление металлов - Сырая металлическая шихта расплавляется в индукционной печи, дуговой плавкой или другими методами. К числу распространенных металлов, подвергаемых распылению, относятся алюминий, титан, никель, железо, кобальт, медь и др.
- Поставка расплавленного металла - Жидкий металл поддерживается при оптимальной температуре и направляется в зону распыления с помощью промковшей, тиглей или насосов.
- Распыление - Поток расплавленного металла распадается на капли при взаимодействии с высокоскоростным газом или жидкостью. Применяются различные методы распыления.
- Коллекция порошков - Распыленный металлический порошок охлаждается и собирается для последующих операций. При этом могут использоваться процессы просеивания, магнитной сепарации, отжига.
- Характеристика порошков - Анализируется гранулометрический состав, морфология, плотность, текучесть и микроструктура порошка.
Правильное управление такими параметрами процесса, как состав металла, температура, скорость распыления жидкости, конструкция распылителя, является критически важным для достижения требуемых характеристик порошка.
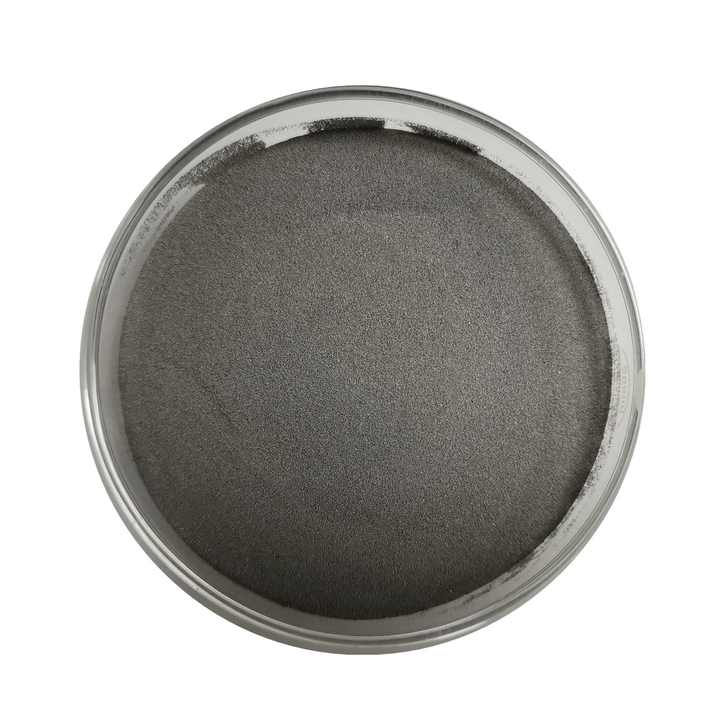
Типы оборудования для распыления
Системы распыления можно классифицировать в зависимости от среды, используемой для дезинтеграции расплавленного металла на капли:
Газовая атомизация
При газовом распылении кинетическая энергия газа высокого давления быстро разгоняет и диспергирует поток жидкого металла на мелкие капли. В зависимости от конструкции подачи газа их можно разделить на:
- Распыление газа под давлением - С помощью близко расположенных сопел сжатый воздух или инертный газ подается сбоку на поток жидкого металла.
- Двухжидкостная форсуночная газовая атомизация - Коаксиальные сопла вводят высокоскоростной распыляемый газ вокруг внутренней металлической трубки подачи.
- Многосопловая газовая атомизация - Используется массив сходящихся-разходящихся сопел для подачи сверхзвуковых газовых струй на поток расплава.
Порошки, распыляемые газом, имеют меньший размер частиц, более однородную морфологию, более высокую чистоту по сравнению с порошками, распыляемыми водой. Однако этот процесс является энергоемким и дорогостоящим.
Распыление воды
При водяном распылении поток расплавленного металла дезинтегрируется под воздействием струй воды высокого давления. При этом образуются капли с более широким распределением по размерам. Водяное распыление имеет более низкие капитальные и эксплуатационные затраты по сравнению с газовым распылением.
В соответствии с конструкцией может использоваться распыление воды:
- Атомизация воды с тесной связью - Струи воды воздействуют непосредственно на жидкий металл, выходящий из промковша.
- Распыление воды при свободном падении - Падающий поток расплавленного металла перехватывается струями воды, расположенными под промковшом.
Порошки, распыляемые водой, имеют более неправильную форму частиц и более широкое распределение, что идеально подходит для прессования и спекания. Однако вода вносит загрязнения.
Центробежное распыление
При центробежном распылении расплавленный металл заливается или закачивается в высокоскоростной вращающийся диск или чашу. Металл образует по периметру тонкую пленку, которая под действием центробежных сил распадается на мелкие капли.
К преимуществам относятся простота конструкции, низкий расход газа, простота масштабирования. Однако диапазон размеров относительно выше, чем при газовом распылении. Используется для получения сферических порошков из металлов с низкой температурой плавления, таких как олово, свинец, цинк и т.д.
Ультразвуковое распыление газа
Сочетает в себе газовое распыление и ультразвуковой генератор, подключенный к соплу. Высокочастотные колебания усиливают дезинтеграцию и диспергирование металла на более мелкие капли, что позволяет получить субмикронный порошок.
Очень эффективен для получения нанокристаллических и аморфных порошковых морфологий. Но дорогостоящий и требующий обслуживания. Используется для специализированных применений.
Искровая эрозия Распыление
В этом методе электрического распыления между расплавленным металлом и наконечником электрода подается импульсный искровой разряд высокого тока, создающий плазму, которая расщепляет металл на ультратонкий сферический порошок.
Позволяет получать очень тонкие металлические порошки с высокой сферичностью. Но при этом низкая производительность и высокая стоимость. В основном используется для драгоценных металлов, таких как золото, платина, палладий.
Компоненты и конструкция атомайзера
Атомайзеры состоят из различных компонентов, предназначенных для расплавления, заливки, распыления, охлаждения и эффективного сбора металлического порошка.
Система плавления и заливки металла
- Индукционная печь - Наиболее часто используется для плавки таких металлов, как сталь. Обеспечивает хороший контроль температуры и низкую загрязненность расплава.
- Крейцкопфы - Огнеупорные керамические горшки, используемые для размещения металлической шихты. Они могут нагреваться в отдельной печи и заливаться вручную или непосредственно включаться в систему распыления.
- Тундиш - Промежуточный резервуар для расплавленного металла, регулирующий скорость заливки в секцию распыления.
- Водосточная труба - Точно направляет поток расплавленного металла в зону распыления. Изготавливается из тугоплавкого металла, например вольфрама, чтобы выдерживать высокие температуры.
- Насосы - Используется для управления подачей расплавленного металла под давлением в некоторых конфигурациях распылителей.
Секция распыления
- Распылительная насадка - Специализированные сопла, устойчивые к высокому давлению и температуре, используются для создания струй газа или воды для распыления.
- Массивы сопел - Несколько специализированных сопел, стратегически расположенных для оптимального формирования капель.
- Компоненты спиннинга - Диски, стаканы, используемые в центробежном распылении, вращаются с очень высокой скоростью - от 10 000 до 50 000 об/мин, приводимые в движение электродвигателем.
- Ультразвуковой генератор - Преобразует электрический сигнал в высокочастотные механические колебания в области сопла. Используется при ультразвуковом распылении.
- Источник питания - Обеспечивает высокий ток для создания электрической дуги при искровом эрозионном распылении.
Система транспортировки порошковых материалов
- Циклоны-сепараторы - Отделение мелкодисперсного порошка от потоков технологического газа или воды с помощью центробежных сил.
- Рукавные фильтры - Собирают очень мелкий порошок, не отделяемый в циклонах. Требуется частая замена.
- Ситовые классификаторы - Классификация порошка по размерам на различные фракции с помощью сетчатых сит.
- Магнитные сепараторы - Удалите из порошка загрязнения в виде бродячих металлов.
- Конвейеры - Транспортирует порошок между оборудованием. Используются винтовые, ленточные, вибрационные конвейеры.
- Хопперы - Хранит порошок для дальнейшей обработки или упаковки.
- Вакуумная очистка - Удаляет просыпавшийся порошок с оборудования и поверхностей. Критически важен для реактивных металлических порошков.
Приборы и средства управления
- Датчики температуры - Очень важно контролировать и регулировать температуру печи/расплава и сопла для оптимального распыления.
- Датчики давления - Контролируйте давление газа и воды в форсунках для поддержания надлежащего распыления.
- Расходомеры - Измерение и контроль расхода жидкости для распыления и расплава.
- Тахометры - Контролирует скорость вращения дисков центробежного распыления.
- Датчики уровня - Поддержание оптимального уровня расплава в основных емкостях. Предотвращает переполнение.
- Аварийный останов - Необходим для быстрой и безопасной остановки оборудования в случае возникновения каких-либо проблем.
- Система управления - Автоматизированное компьютерное управление оптимизирует согласование параметров и повышает повторяемость.
Параметры процесса распыления металлических порошков
Правильный выбор параметров технологического процесса является ключевым фактором для получения порошков с требуемыми характеристиками. В таблице ниже приведены основные переменные и их влияние на свойства порошка:
Параметр | Влияние на свойства порошка |
---|---|
Температура расплавленного металла | Повышение температуры снижает вязкость, улучшает распыление. Но может увеличить окисление, потери при испарении. |
Давление распыляющего газа | Повышение давления газа улучшает гранулометрический состав частиц, снижает средний размер. Но при этом увеличивается расход газа. |
Расход распыляющего газа | Более высокая скорость потока улучшает измельчение частиц. Но при этом увеличивается расход газа. |
Скорость распыления жидкости | Более высокая скорость улучшает измельчение частиц. Зависит от конструкции сопла. |
Конструкция форсунки | Специализированные сопла создают более мелкие капли и порошок. |
Скорость заливки расплава | Более высокие скорости разлива увеличивают производительность при непрерывной работе, но могут привести к уменьшению размера частиц. |
Перегрев расплава | Увеличивается при повышении температуры заливки выше температуры плавления. Улучшает текучесть. |
Фильтрация расплава | Удаляет включения и загрязнения. Повышает чистоту порошка. |
Расстояние распыления | Большее расстояние свободного падения позволяет увеличить время образования капель. Уменьшается образование спутников. |
Состав расплава | Легирующие элементы могут изменять вязкость, поверхностное натяжение, влиять на распыляемость и характеристики порошка. |
Характеристика распыленного металлического порошка
Свойства и качество распыляемого порошка определяют его эффективность в последующих приложениях. Основными оцениваемыми характеристиками являются:
Распределение частиц по размерам
Распределение частиц порошка по различным размерным фракциям, обычно представляемое в виде перцентилей D10, D50 и D90. При газовом распылении можно получить частицы размером менее 20 мкм, в то время как при водяном распылении получается более крупный порошок.
Форма и морфология частиц
Порошок, распыляемый газом, имеет высокосферические частицы, в то время как порошок, распыляемый водой, имеет более неправильную форму. Частицы-спутники свидетельствуют об отсутствии оптимального распыления. Порошок округлой формы обладает лучшей текучестью и плотностью упаковки.
Химический состав
Элементный и фазовый состав по результатам анализов. Определяет марку сплава. Газовая атомизация обеспечивает высокую чистоту, в то время как вода может загрязнять такие реакционноспособные металлы, как титан, алюминий.
Кажущаяся и тангенциальная плотность
Показатель эффективности упаковки порошка. Повышение плотности улучшает свойства изделий при прессовании и спекании. Но может влиять на текучесть порошка. Значения обычно составляют 40-65% от плотности материала.
Характеристики потока
Важны для транспортировки и последующей обработки. Влияют такие факторы, как форма частиц, распределение по размерам, структура поверхности. Улучшается отжигом, обработкой поверхности.
Микроструктура
Внутренняя структура порошка выявляется с помощью микроскопии. Порошок, распыленный газом, имеет мелкие зерна и дефекты, образовавшиеся в результате быстрого затвердевания, а распыленный водой - более крупный. Определяет поведение при спекании.
Области применения распыления металлических порошков
Атомизированные металлические порошки находят широкое применение в современном производстве, повышая качество и эксплуатационные характеристики продукции по сравнению с традиционной обработкой металлов:
Аддитивное производство
- 3D-печать - Атомизированные сферические порошки с контролируемым распределением по размерам идеально подходят для технологий порошкового наплавления. Обычно используются алюминиевые, титановые, никелевые суперсплавы.
- Литье металлов под давлением - Более мелкие порошки нержавеющей стали, титана и алюминия улучшают процесс спекания и плотность деталей.
Порошковая металлургия
- Прессование и спекание - неравномерный, более крупнозернистый порошок железа, распыляемый водой, используется для производства деталей из П/М с хорошими механическими свойствами.
- Мягкие и твердые магниты - мелкокристаллические порошки NdFeB, SmCo позволяют получать высокоэффективные магниты на связке и методом горячего прессования.
- Фрикционные материалы - распыляемый в воде медный порошок повышает эффективность тормозных колодок и накладок сцепления.
Поверхностные покрытия
- Термическое напыление - сферический порошок с контролируемым распределением по размерам важен для получения равномерных, плотных покрытий при плазменном или HVOF-распылении. Используется порошок WC-Co, никелевый сплав.
- Осаждение из паровой фазы - Сверхтонкое порошковое сырье суперсплава, используемое в электронно-лучевом осаждении из паровой фазы для получения покрытий турбин с повышенной защитой.
Другое
- Литье металлов под давлением - Мелкодисперсное порошковое сырье из нержавеющей стали, титана и алюминия позволяет изготавливать небольшие сложные детали.
- Паяльные пасты - распыляемые сплавы серебра, золота, меди, используемые для изготовления высокотемпературных паяных соединений.
- Искровая эрозия - ультратонкий сферический порошок, используемый в качестве диэлектрической среды, повышает точность и скорость электроэрозионной обработки.

Преимущества распыления металлических порошков
По сравнению с традиционными способами обработки металлов основные преимущества использования распыляемых порошков заключаются в следующем:
- Улучшенные механические свойства - Тонкая однородная микроструктура, образующаяся в результате быстрого затвердевания, повышает предел текучести, усталостную прочность и пластичность.
- Точный контроль размеров - Консистентный сферический порошок обеспечивает высокую плотность и точное изготовление сетки. Уменьшает объем механической обработки.
- Более высокая производительность - Серийное производство компонентов с помощью обработки металлических порошков может осуществляться быстрее, чем субтрактивными методами.
- Большая свобода проектирования - Возможно изготовление сложных геометрических форм, невозможных при литье или механической обработке.
- Минимизация отходов - Возможность получения почти чистой формы позволяет снизить потери брака по сравнению с металлургией слитков. Неиспользованный порошок может быть переработан.
- Снижение энергопотребления - Порошковый процесс требует меньшей температуры и энергии, чем производство из сыпучего металла.
- Нестандартные сплавы - С помощью распыления можно получать специальные композиции, которые трудно производить в слитках.
- Высокая чистота - Реактивные элементы, такие как титан, могут распыляться с меньшим загрязнением, чем при традиционных методах.
Ограничения при распылении металлических порошков
- Высокие капитальные вложения в оборудование для распыления и системы обработки порошков по сравнению с обработкой сыпучих металлов.
- Для получения изделий из порошков необходимы дополнительные последующие процессы, такие как уплотнение, спекание и т.д. В целом маршрут производства является сложным.
- Получение сверхтонкого наноразмерного порошка может быть сложным и дорогостоящим процессом при низкой производительности.
- Возможность загрязнения при использовании распыления воды, особенно для реактивных металлов.
- Порошок может адсорбировать кислород и влагу, что требует соблюдения мер предосторожности при хранении и работе с ним.
- Существуют проблемы безопасности, связанные со взрывами пыли, пожароопасностью и токсичностью некоторых порошковых композиций и морфологий.
- Непостоянство свойств конечных деталей по сравнению с деформируемыми изделиями. Дефекты, связанные с порошком, могут проявиться после консолидации.
- Переработка и повторное использование металлического порошка ограничены по сравнению с объемными формами металла. Материал выбрасывается после 1-2 циклов повторного использования.
- Отсутствие отраслевых стандартов на новые металлические порошки по характеристикам, методике испытаний, контролю качества и сертификации создает препятствия для их внедрения.
Выбор системы распыления металлических порошков
Выбор подходящего оборудования для распыления зависит от таких факторов, как:
Объем производства
- Малое производство - распылители лабораторного и опытного масштаба. Центробежные системы или системы распыления газа под давлением.
- Среднее производство - распылители непрерывного действия с производительностью до 3 т/час порошка.
- Высокая производительность - заказные крупномасштабные системы производительностью более 10 тонн/час.
Порошковый материал
- При распылении воды могут использоваться нереактивные металлы, такие как сталь и никелевые сплавы.
- Водочувствительные сплавы, такие как алюминий, титан, нуждаются в распылении в инертных газах.
- Тугоплавкие металлы, такие как вольфрам, требуют специальных распыляющих сред и защиты.
Свойства порошка
- Газовое распыление для получения более тонких порошков размером менее 30 мкм со сферической морфологией.
- Распыление воды для получения более грубого, неравномерного порошка для прессования.
- Специализированное распыление нанокристаллических или аморфных металлических порошков.
Применение продукта
- В аддитивном производстве используется очень мелкий порошок с контролируемым распределением частиц, получаемый в результате газового распыления.
- Для литья под давлением порошковых материалов требуется мелкий сферический порошок с хорошей текучестью.
- Для нанесения покрытий методом термического напыления необходим плотный сферический порошок, который хорошо упаковывается.
Капитальные и эксплуатационные затраты
- Распыление водой имеет более низкую стоимость оборудования и эксплуатационные расходы, но может ухудшить качество порошка.
- Газовое распыление имеет в 10 раз более высокие капитальные затраты, но позволяет получить более качественный порошок. Эксплуатационные расходы также выше.
- Центробежное распыление экономично, но имеет ограничения по размерам и форме.
Интеграция завода
- Требуется достаточная инфраструктура для подготовки расплава, обработки, хранения и транспортировки порошка.
- Системы защиты реактивных металлов в атмосфере инертного газа.
- Автоматизированный контроль и мониторинг данных повышают стабильность процесса.
Ведущие производители распылителей металлических порошков
Несколько компаний предлагают стандартизированные и заказные системы и компоненты для распыления металлических порошков:
Системы газовой атомизации
- Praxair - лидер на рынке оборудования для распыления газов высокого давления. Предлагает системы лабораторного, пилотного и производственного масштаба.
- AP&C - Специализируется на производстве газовых распылителей с близко расположенными соплами для реактивных и тугоплавких металлов. Широко используются для порошков титана и алюминия.
- ALD Vacuum Technologies - разрабатывает многосопловые газовые распылители для средних и высоких производств. Принадлежит компании Oerlikon Metco.
Распыление воды
- Gasbarre - предлагает распыление воды с близким и свободным падением для средних и больших объемов.
- Sheffield Atomising Systems - более 50 лет специализируется на технологии распыления воды свободным падением.
Центробежное распыление
- ABB - Крупнейший мировой поставщик оборудования. Предлагает системы центробежного распыления от лабораторных до полномасштабных серийных.
- Ferrum AG - Ведущий поставщик горизонтальных и вертикальных центробежных распылителей, расположенный в Швейцарии.
Ультразвуковое распыление
- Tekna - предлагает системы ультразвуковых газовых распылителей, основанные на запатентованной технологии двухпроводных индукционных направляющих
- Ultramet - поставляет специализированное оборудование для ультразвукового распыления с технологией высокотемпературного сжижения
Искровая эрозия Распыление
- PyroGenesis - Предлагает систему плазменного распыления (PAS) для получения сверхтонких сферических металлических порошков.
- Plasma Innovations - Поставляет системы искрового эрозионного распыления с вращающимся электродом (REP).
Анализ затрат на распылители металлических порошков
Стоимость распылителя зависит от масштаба, производительности, уровня автоматизации и обрабатываемого порошкового материала. Типовые оценки капитальных затрат:
Газовый распылитель большой производительности | Индивидуальное строительство | 1000 | 10 млн. |
---|---|---|---|
Атомайзер для воды малого производства | Прицепная/контейнерная система | 100 | 750,000 |
Распылитель воды средней производительности | Система укрытий | 500 | 2 млн. |
Крупносерийный распылитель воды | Индивидуальное строительство | 2000 | 5 млн. |
Пилотный центробежный распылитель | Монтаж на салазках | 50 | 400,000 |
Средний центробежный распылитель | Система укрытий | 500 | 1,5 млн. |
Лабораторный ультразвуковой распылитель | Бенчтоп | 5 | 250,000 |
Ультразвуковой распылитель Pilot | Монтаж на салазках | 20 | 1 млн. |
Искровой эрозионный распылитель | Контейнерная система | 10 | 2 млн. |
Операционные расходы
- Основные затраты - энергия, труд, обслуживание, использование инертного газа.
- Расход электроэнергии при газовом распылении составляет ~500-800 кВт-ч на тонну порошка. Расход газа 5-10 м3 на кг порошка.
- Расход электроэнергии при распылении воды ниже - ~200-400 кВт-ч на тонну порошка. Но выше трудоемкость и стоимость обслуживания.
- Расход электроэнергии при центробежном распылении ~300-500 кВт-ч на тонну порошка. Более низкое использование инертных газов.
- Расходные детали, такие как сопла, фильтры-мешки, требуют частой замены.
Возможности снижения затрат
- Увеличение масштабов производства и выпуска порошка снижает капитальные затраты на кг порошка.
- Более высокая степень автоматизации и контроля повышает производительность труда.
- Рециркуляция и повторное использование технологических газов, воды и отработанного тепла снижает эксплуатационные расходы.
- Программы профилактического обслуживания сводят к минимуму время простоя и затраты на обслуживание.
- Местные поставки энергии, газов, воды и вспомогательных услуг снижают логистические расходы.
- Приобретение восстановленных/использованных систем распыления снижает капитальные затраты для мелких производителей.
Оборудование для распыления металлических порошков - часто задаваемые вопросы
Вопрос: Какой типичный диапазон размеров частиц достигается при газовом распылении?
О: Газовое распыление позволяет получать порошки с размером частиц от 1 микрона до более 100 микрон. Типичные значения D50 для большинства сплавов составляют 10-45 мкм. При использовании оптимизированных сопел и высоких скоростей газа возможно получение более тонкого порошка с размером менее 10 мкм.
Вопрос: Какой объем продукции может ежегодно производить небольшая система газовых распылителей?
О: Опытный газовый распылитель производительностью 10 кг/час, работающий 5000 часов в год, может производить ~50 000 кг порошка в год. Небольшая производственная система производительностью 50 кг/час может выпускать ~250 000 кг в год при полном объеме производства.
Вопрос: Какие виды металлов можно распылять в порошок?
О: Большинство коммерческих систем сплавов, включая нержавеющую сталь, инструментальную сталь, никелевые сплавы, титановые сплавы, алюминиевые сплавы, суперсплавы, кобальтовые сплавы и т.д., подвергаются атомизации. Тугоплавкие металлы, такие как вольфрам, молибден, являются сложными и требуют применения специализированных систем распыления.
Вопрос: Какой метод распыления лучше всего подходит для реактивных металлов, таких как титан?
Ответ: Газовое распыление с использованием инертного газа, такого как аргон или азот, предпочтительно для реактивных металлов, таких как титан, алюминий. Это предотвращает окисление и загрязнение по сравнению с распылением воды.
Вопрос: Насколько тонкий размер частиц может быть достигнут при ультразвуковом распылении?
A: Ультразвуковые газовые распылители могут генерировать субмикронные и наноразмерные металлические порошки со средним размером менее 100 нанометров, если их оптимизировать. Однако скорость выхода порошка невелика.
Вопрос: Может ли металлический порошок быть переработан после использования в аддитивном производстве?
О: Да, неиспользованный порошок может быть повторно использован в процессах АМ. Однако до ухудшения свойств порошок можно переработать только 1-2 раза. После этого порошок необходимо повторно атомизировать для дальнейшего использования.
Вопрос: Как лучше всего обращаться с тонким реактивным порошком?
О: Использование коробок с инертными перчатками, герметизация контейнеров с порошком, исключение контакта с воздухом/влагой. Некоторые реактивные материалы могут потребовать обработки поверхности. Алюминиевый порошок, распыляемый водой, обычно покрывают для предотвращения окисления.
Вопрос: Почему для газовой атомизации важен инертный газ высокой чистоты?
О: Высокая степень чистоты сводит к минимуму загрязнение. Влага и кислород могут окислять реактивные сплавы в процессе распыления. Отходящие газы могут попадать в порошок, создавая дефекты в свойствах конечной детали.
Вопрос: Насколько просто обслуживать и ремонтировать газовый распылитель?
О: Текущее обслуживание не требует особых усилий. Однако серьезный ремонт, например замена форсунок, может занять несколько дней и потребовать от персонала специальной подготовки. Для быстрой замены форсунок следует хранить дополнительные форсунки в качестве запасных частей.
Вопрос: Какие проблемы безопасности существуют при производстве металлических порошков?
Ответ: Работа с мелкими порошками всегда сопряжена с опасностью взрыва пыли. Также опасность представляют газы под давлением, электричество под высоким напряжением, повышенные температуры, работа с расплавленным металлом, требующая применения средств защиты и обучения.
Поделиться
MET3DP Technology Co., LTD - ведущий поставщик решений для аддитивного производства со штаб-квартирой в Циндао, Китай. Наша компания специализируется на производстве оборудования для 3D-печати и высокопроизводительных металлических порошков для промышленного применения.
Сделайте запрос, чтобы получить лучшую цену и индивидуальное решение для вашего бизнеса!
Похожие статьи
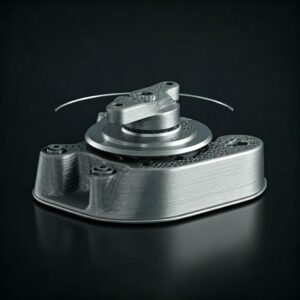
3D-печатные крепления для автомобильных радарных датчиков: Точность и производительность
Читать далее "О компании Met3DP
Последние обновления
Наш продукт
CONTACT US
Есть вопросы? Отправьте нам сообщение прямо сейчас! После получения Вашего сообщения мы всей командой выполним Ваш запрос.
Получите информацию о Metal3DP
Брошюра о продукции
Получить последние продукты и прайс-лист