Corrosion-Resistant Pipe Connectors: The Future of Fluid Handling
Оглавление
In industries where the integrity of fluid transfer systems is paramount, such as aerospace, chemical processing, marine, and medical, the choice of pipe connectors can significantly impact operational efficiency, safety, and longevity. Traditionally manufactured pipe connectors often face limitations in terms of material selection, complex geometries, and customization. However, the advent of metal 3D printing, also known as metal additive manufacturing, offers a transformative approach to producing high-performance, corrosion-resistant pipe connectors tailored to specific application requirements. This blog post will explore the advantages of using metal 3D-печать for creating these critical components, the recommended materials, design considerations, and what to look for in a metal 3D printing service provider like Metal3DP.
What are Corrosion-Resistant Pipe Connectors Used For?
Corrosion-resistant pipe connectors play a vital role in a multitude of industries, ensuring the secure and leak-proof joining of pipes and tubes that convey various fluids and gases. Their primary function is to create a reliable connection capable of withstanding harsh operating environments, including exposure to corrosive substances, high pressures, and extreme temperatures. Here’s a breakdown of their key applications across different sectors:
- Химическая обработка: In chemical plants, these connectors are essential for transporting aggressive chemicals, acids, and alkalis. Materials like 316L and 254SMO are particularly valuable here due to their exceptional resistance to chemical attack.
- Marine and Offshore: The marine environment poses significant corrosion challenges due to saltwater exposure. Corrosion-resistant connectors are crucial in shipbuilding, offshore oil and gas platforms, and desalination plants to ensure the longevity and safety of piping systems.
- Медицинская промышленность: In medical applications, the purity and sterility of conveyed fluids are critical. Corrosion-resistant connectors made from biocompatible materials are used in pharmaceutical manufacturing, medical device fabrication, and within healthcare facilities for fluid management systems.
- Аэрокосмическая промышленность: Aircraft and spacecraft rely on robust and lightweight fluid transfer systems for fuel, hydraulics, and coolant. Corrosion-resistant connectors ensure the reliability and safety of these critical systems under demanding conditions.
- Автомобили: While perhaps less extreme than other industries, certain automotive applications, such as exhaust systems or fluid lines exposed to road salts, benefit from corrosion-resistant connectors.
- Industrial Manufacturing: Across a wide range of manufacturing processes, these connectors are used in cooling systems, hydraulic lines, and the transport of various industrial fluids, contributing to operational efficiency and preventing costly downtime due to corrosion-related failures.
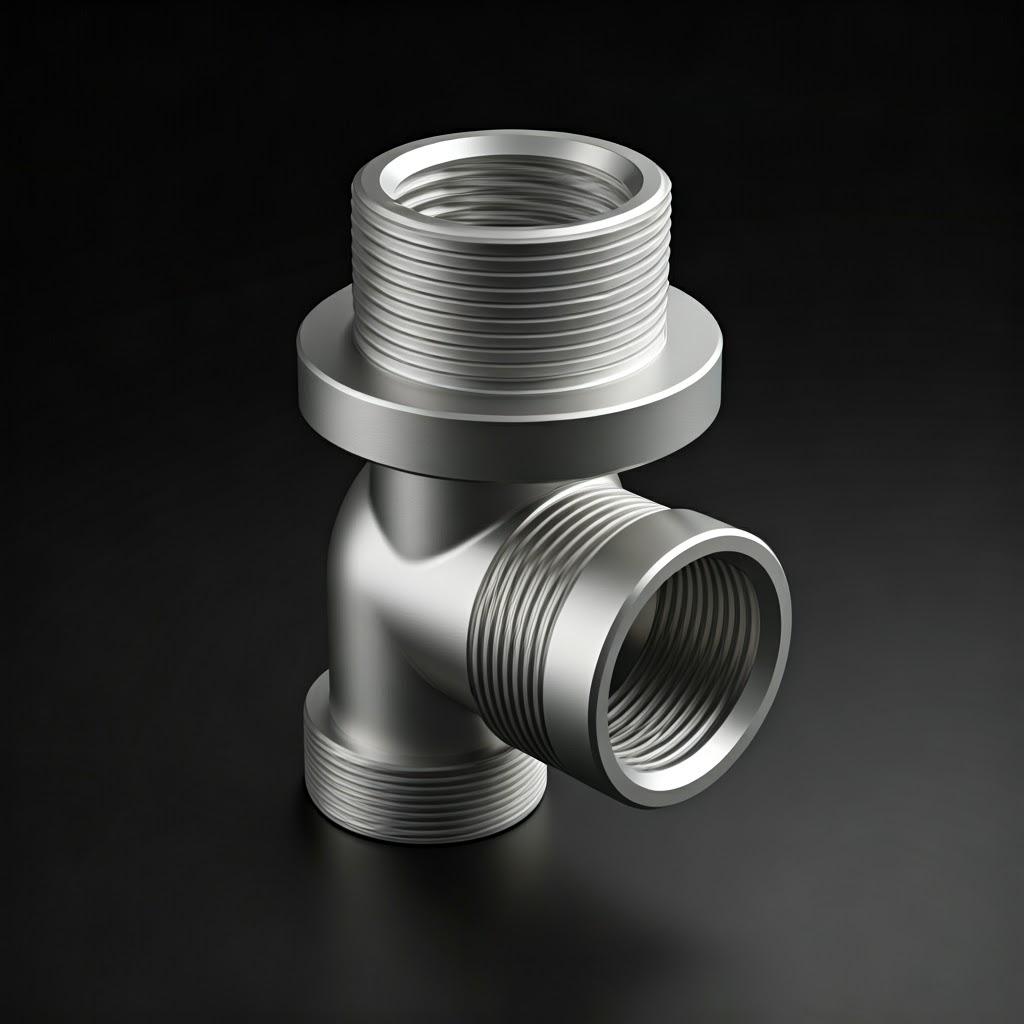
Why Use Metal 3D Printing for Corrosion-Resistant Pipe Connectors?
Opting for metal 3D printing for the production of corrosion-resistant pipe connectors offers several compelling advantages over traditional manufacturing methods such as machining, casting, or forging. These benefits are particularly attractive to engineers and procurement managers seeking enhanced performance, customization, and efficiency.
- Enhanced Design Freedom and Complexity: Additive manufacturing allows for the creation of intricate geometries that are difficult or impossible to achieve with conventional methods. This includes internal channels for improved flow, complex bracketry integration, and optimized shapes for reduced weight and material usage. Engineers can design connectors tailored precisely to their application needs, leading to improved system performance.
- Оптимизация материалов: Metal 3D printing enables the use of high-performance, corrosion-resistant alloys like 316L and 254SMO, which might be challenging or costly to machine. Furthermore, techniques like lattice structures can be employed to reduce weight while maintaining structural integrity. Metal3DP’s advanced powder making system ensures the availability of high-quality metal powders optimized for these applications.
- Кастомизация и производство по требованию: Unlike traditional mass production, metal 3D printing allows for the creation of custom connectors in small to medium volumes without the need for expensive tooling. This is particularly beneficial for specialized applications, prototypes, or replacement parts with unique specifications.
- Сокращение отходов материалов: Additive manufacturing processes typically involve building parts layer by layer, using only the necessary material. This significantly reduces material waste compared to subtractive methods like machining, where a substantial portion of the raw material is removed.
- Faster Prototyping and Iteration: Metal 3D printing accelerates the design and development cycle. Engineers can quickly iterate on designs and produce functional prototypes for testing, leading to faster time-to-market for new products or system upgrades.
- Integration of Multiple Components: Metal 3D printing can consolidate multiple parts into a single, integrated component. For pipe connectors, this could mean incorporating features like mounting flanges or sensor housings directly into the connector design, reducing assembly time and potential leak points. Metal3DP’s expertise in application development can help organizations leverage this capability.
Recommended Materials and Why They Matter
The selection of the appropriate metal powder is crucial for achieving the desired corrosion resistance and mechanical properties in 3D-printed pipe connectors. Metal3DP производит широкий ассортимент высококачественных металлических порошков., and for corrosion-resistant applications, 316L stainless steel and 254SMO stainless steel are excellent choices.
Нержавеющая сталь 316L:
- Состав: An austenitic stainless steel alloy containing chromium (16-18%), nickel (10-14%), and molybdenum (2-3%). The “L” designation indicates a low carbon content (maximum 0.03%), which enhances weldability and reduces the risk of carbide precipitation, a form of corrosion that can occur at grain boundaries.
- Коррозионная стойкость: 316L offers superior corrosion resistance compared to 304 stainless steel, particularly in environments containing chlorides and other aggressive substances. The addition of molybdenum significantly improves its resistance to pitting and crevice corrosion.
- Механические свойства: It exhibits good tensile strength, ductility, and toughness, making it suitable for a wide range of applications involving pressure and mechanical stress.
- Приложения: Widely used in chemical processing equipment, medical implants, marine hardware, food processing, and pharmaceutical industries due to its excellent corrosion resistance and biocompatibility.
254SMO Stainless Steel (UNS S31254):
- Состав: A high-alloy austenitic stainless steel containing chromium (19-21%), nickel (17.5-18.5%), molybdenum (6-6.5%), and copper (0.5-1.0%).
- Коррозионная стойкость: 254SMO offers exceptional resistance to pitting, crevice corrosion, and stress corrosion cracking, particularly in chloride-rich environments such as seawater and highly concentrated chemical solutions. Its PREN (Pitting Resistance Equivalent Number) is significantly higher than that of 316L, indicating superior resistance to localized corrosion.
- Механические свойства: It possesses high strength and ductility, often exceeding that of standard austenitic stainless steels.
- Приложения: Ideal for demanding applications in the chemical processing industry (especially handling halogenated acids and bleaches), offshore oil and gas, marine environments, flue gas desulfurization systems, and pulp and paper processing where resistance to severe corrosion is critical.
By leveraging Metal3DP’s expertise in metal powders and 3D printing technologies, engineers and procurement managers can obtain high-performance, corrosion-resistant pipe connectors tailored to their specific industrial needs. The choice between 316L and 254SMO will depend on the specific corrosive environment, mechanical load requirements, and budget considerations. Sources and related content
Design Considerations for Additive Manufacturing of Pipe Connectors
Optimizing the design of pipe connectors for metal 3D printing is crucial to fully leverage the advantages of additive manufacturing and ensure the final part meets the required performance specifications. Unlike traditional manufacturing methods with their inherent design constraints, 3D printing offers greater freedom but also necessitates a different approach to design. Here are key considerations:
- Topology Optimization: This computational method can be employed to identify the most efficient material distribution for a given set of loads and constraints. For pipe connectors, topology optimization can lead to lightweight designs with enhanced structural integrity by removing unnecessary material while ensuring sufficient strength in critical areas.
- Решетчатые структуры: Incorporating lattice or cellular structures within the connector body can significantly reduce weight without compromising stiffness. These internal geometries can be tailored to specific load-bearing requirements and can also enhance heat dissipation if the application involves elevated temperatures.
- Consolidation of Assemblies: Metal 3D printing allows for the integration of multiple components into a single part. For pipe connectors, this could involve combining the connecting element with features like mounting flanges, support structures, or even integrated sensors. Reducing the number of individual parts simplifies assembly, minimizes potential leak points, and can improve overall reliability.
- Internal Channels and Complex Geometries: Additive manufacturing excels at creating intricate internal features, such as optimized flow channels with smooth curves to minimize pressure drop or complex internal cooling passages. For specialized pipe connectors, this design freedom can lead to significant performance enhancements.
- Surface Finish Considerations: The as-printed surface finish in metal 3D printing can vary depending on the printing technology and material. For pipe connectors requiring smooth sealing surfaces, post-processing steps like machining or polishing might be necessary. Designing the part with easily accessible surfaces for post-processing is an important consideration.
- Orientation and Support Structures: The orientation of the part during the printing process and the design of support structures are critical for minimizing material usage, ensuring dimensional accuracy, and preventing warping. Careful consideration of these factors during the design phase can significantly impact the success and cost-effectiveness of the printing process. Metal3DP’s expertise in printing methods can provide valuable insights into optimizing part orientation and support design.
- Wall Thickness and Feature Size: While 3D printing offers flexibility, there are still limitations regarding minimum wall thicknesses and the size of intricate features. Designers need to be aware of the capabilities and limitations of the chosen printing process and material to ensure manufacturability and structural integrity.
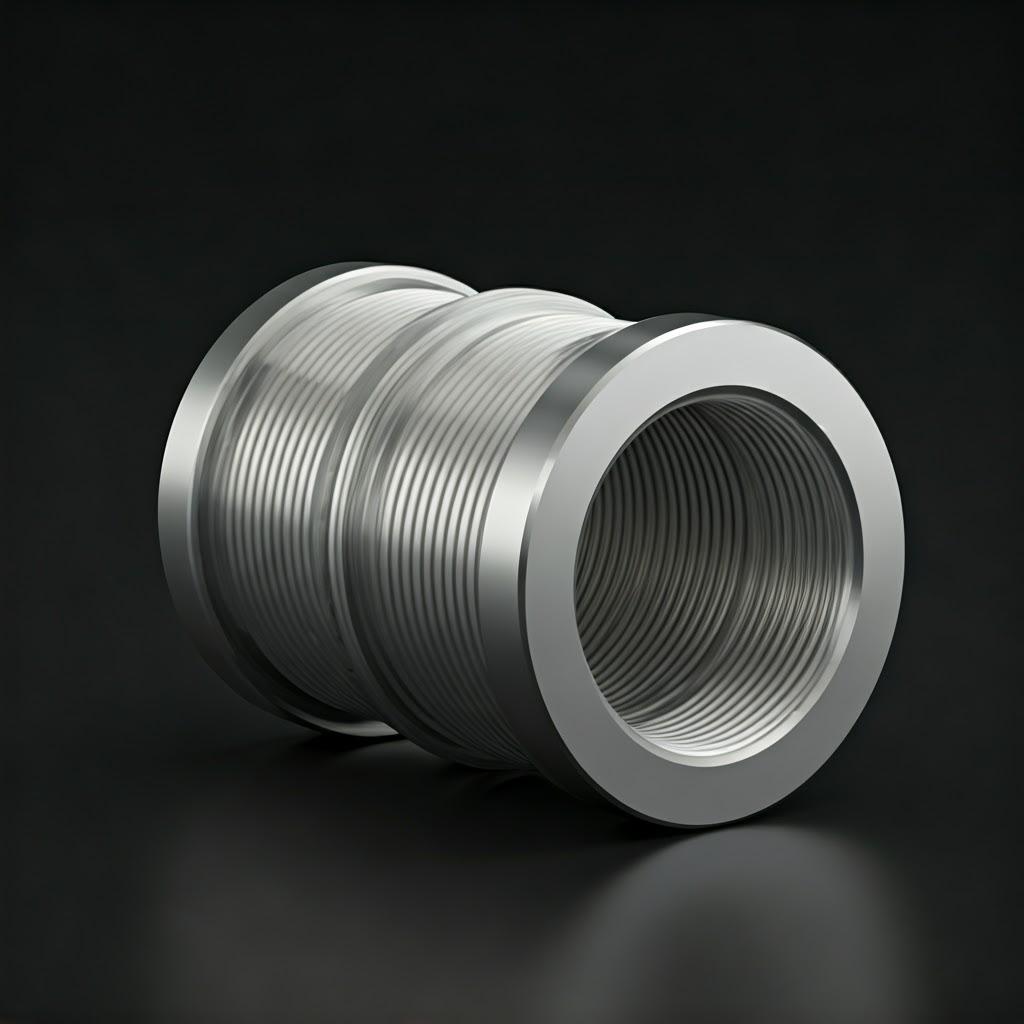
Tolerance, Surface Finish, and Dimensional Accuracy of 3D-Printed Pipe Connectors
Understanding the achievable tolerance, surface finish, and dimensional accuracy of metal 3D-printed pipe connectors is crucial for engineers to determine if the technology meets the requirements of their specific applications. These factors can influence the sealing performance, fit, and overall functionality of the connectors.
- Tolerance: Metal 3D printing technologies have made significant advancements in achieving tighter tolerances. However, the achievable tolerance can vary depending on the printing process (e.g., Selective Laser Melting (SLM), Electron Beam Melting (EBM)), the material used, and the size and geometry of the part. Typically, tolerances in the range of ±0.1 to ±0.05 mm can be achieved for critical dimensions. It’s essential to consult with the chosen metal 3D printing service provider, like Metal3DP, to understand the specific tolerances achievable for a given material and part geometry.
- Отделка поверхности: The as-printed surface finish in metal 3D printing is generally rougher compared to machined surfaces. The surface roughness (Ra value) can range from 5 to 20 µm, depending on the printing parameters and powder particle size. For applications requiring smooth sealing surfaces, post-processing techniques such as machining, polishing, or surface coating are typically employed. Designing critical sealing surfaces with allowances for these post-processing steps is important.
- Точность размеров: Dimensional accuracy refers to the ability of the 3D-printed part to match the intended design dimensions. Factors affecting dimensional accuracy include material shrinkage during solidification, thermal gradients during the printing process, and the calibration of the 3D printer. With careful process control and optimized printing parameters, high levels of dimensional accuracy can be achieved. However, it’s crucial to work with a reputable service provider like Metal3DP that has experience in producing dimensionally accurate metal parts.
- Factors Influencing Precision: Several factors can influence the precision of metal 3D-printed parts, including:
- Технология печати: Different metal 3D printing technologies have varying levels of inherent accuracy.
- Свойства материала: The thermal conductivity and solidification behavior of the metal powder can affect shrinkage and warpage.
- Build Orientation: The orientation of the part on the build platform can influence dimensional accuracy in different directions.
- Поддерживающие структуры: The design and removal of support structures can impact surface finish and dimensional accuracy.
- Постобработка: Heat treatment can relieve internal stresses and improve dimensional stability, while machining can achieve tighter tolerances and smoother surface finishes.
Post-Processing Requirements for Metal 3D-Printed Pipe Connectors
While metal 3D printing offers significant advantages in creating complex geometries, post-processing steps are often necessary to achieve the final desired properties, surface finish, and dimensional accuracy for pipe connectors. Common post-processing requirements include:
- Удаление опоры: Support structures are often required during the printing process to prevent part deformation and ensure build integrity. These supports need to be carefully removed after printing, which can involve manual breaking, cutting, or machining. The design of the supports and the part geometry can influence the ease of removal and the potential for surface damage.
- Термообработка: Heat treatment is a crucial step for many metal 3D-printed parts, including pipe connectors. It helps to relieve internal stresses that can build up during the rapid heating and cooling cycles of the printing process. Heat treatment can also improve the mechanical properties of the material, such as strength, hardness, and ductility. The specific heat treatment cycle depends on the material and the desired final properties.
- Отделка поверхности: As mentioned earlier, the as-printed surface finish may not be suitable for all applications, especially sealing surfaces. Various surface finishing techniques can be employed, including:
- Machining (CNC): Precision machining can achieve tight tolerances and smooth surface finishes on critical areas of the connector.
- Полировка: Mechanical or chemical polishing can further improve surface smoothness and corrosion resistance.
- Blasting: Techniques like shot peening or abrasive blasting can improve surface hardness and fatigue resistance.
- Leak Testing: For pipe connectors, ensuring leak-proof performance is paramount. Post-processing often includes pressure testing or other leak detection methods to verify the integrity of the printed part.
- Покрытие: In some applications, surface coatings may be required to further enhance corrosion resistance, wear resistance, or provide specific functional properties. Common coatings include electroplating, powder coating, or specialized chemical coatings.
- Проверка качества: Thorough quality inspection using techniques like coordinate measuring machines (CMM), non-destructive testing (NDT), and visual inspection is essential to ensure that the final pipe connectors meet the required dimensional accuracy, surface finish, and material integrity standards.
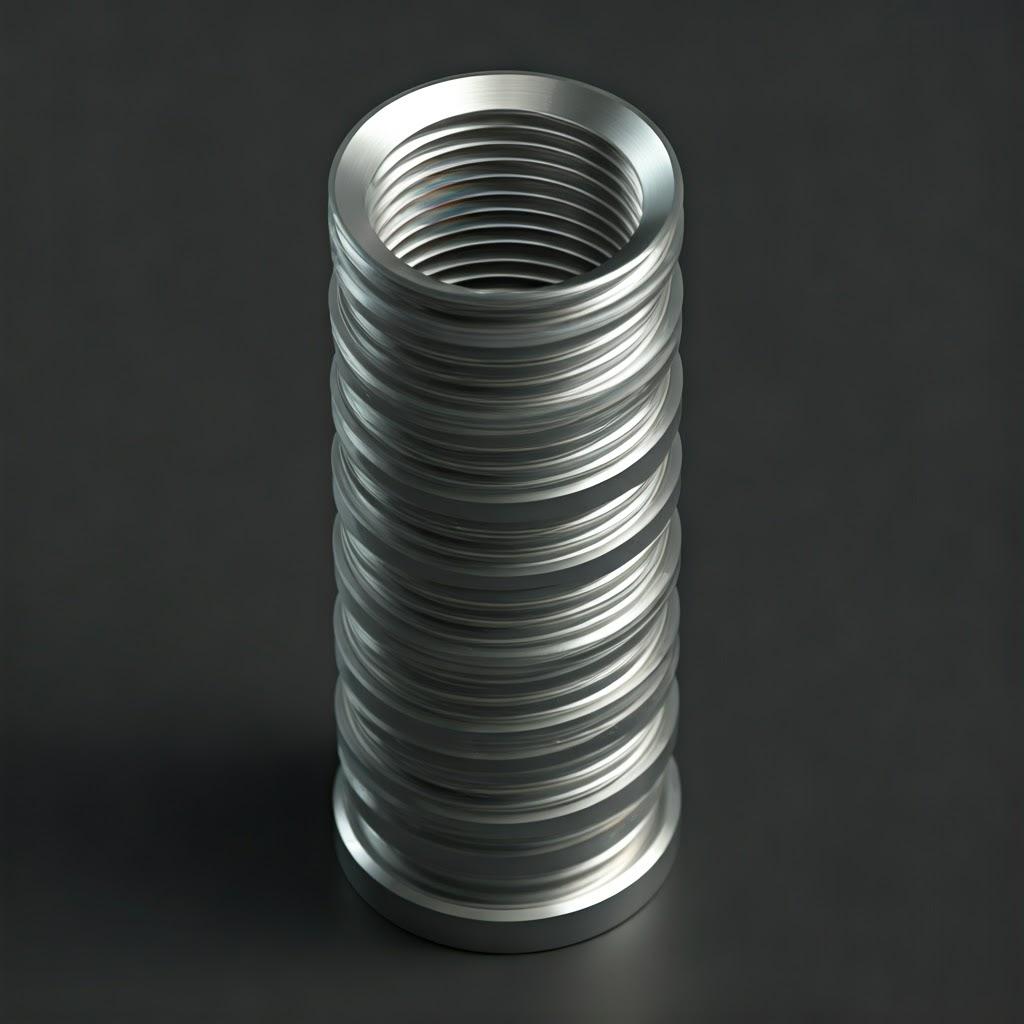
Common Challenges and How to Avoid Them in Metal 3D Printing of Pipe Connectors
While metal 3D printing offers numerous benefits, several challenges can arise during the process. Understanding these potential issues and implementing appropriate strategies can help ensure the successful fabrication of high-quality, corrosion-resistant pipe connectors.
- Warping and Distortion: Thermal stresses during the printing process can lead to warping or distortion of the part, especially for complex geometries or large parts. To mitigate this:
- Optimize part orientation on the build platform.
- Employ effective support structures to anchor the part.
- Carefully control the printing parameters and build chamber temperature.
- Utilize stress-relieving heat treatments post-printing.
- Пористость: Internal voids or pores within the printed part can compromise its mechanical strength and corrosion resistance. To minimize porosity:
- Optimize the powder bed density and laser/electron beam parameters.
- Ensure the use of high-quality, spherical metal powders with good flowability, such as those offered by Metal3DP.
- Employ appropriate shielding gas to prevent oxidation.
- Support Removal Damage: Improper support design or removal techniques can lead to surface damage or dimensional inaccuracies. To avoid this:
- Design support structures that are easy to remove without damaging the part.
- Use appropriate tools and techniques for support removal.
- Consider using breakaway supports or dissolvable support materials where applicable.
- Шероховатость поверхности: As mentioned earlier, the as-printed surface can be rough. For applications requiring smooth surfaces:
- Optimize printing parameters to minimize surface roughness.
- Incorporate post-processing steps like machining or polishing.
- Design critical surfaces with allowances for post-processing.
- Material Property Variability: Achieving consistent and predictable material properties throughout the printed part is crucial. Factors affecting this include:
- Consistent powder quality and handling.
- Stable and well-calibrated printing equipment.
- Optimized and consistent printing parameters.
- Appropriate post-processing heat treatments.
- Стоимостные оценки: Metal 3D printing can be more expensive than traditional manufacturing methods for high-volume production. To manage costs:
- Optimize part design for efficient printing and minimal material usage.
- Consolidate multiple parts into single printed components.
- Carefully evaluate the cost-effectiveness of metal 3D printing for the specific application and production volume.
By being aware of these potential challenges and implementing appropriate design and process optimization strategies, engineers and procurement managers can effectively leverage metal 3D printing for the production of high-performance, corrosion-resistant pipe connectors.
How to Choose the Right Metal 3D Printing Service Provider for Pipe Connectors
Selecting the right metal 3D printing service provider is a critical decision that can significantly impact the quality, cost, and lead time of your corrosion-resistant pipe connectors. Here are key factors to consider when evaluating potential suppliers:
- Material Capabilities: Ensure the provider has experience working with the recommended corrosion-resistant alloys like 316L and 254SMO. Verify the quality and traceability of their metal powders. A provider like Metal3DP that manufactures its own high-quality metal powders can offer greater control over material properties and consistency.
- Printing Technology and Equipment: Different metal 3D printing technologies (e.g., SLM, DMLS, EBM) have varying strengths and limitations in terms of achievable accuracy, surface finish, and material compatibility. Understand the technologies the provider utilizes and whether they are suitable for your specific application requirements. Metal3DP specializes in SEBM printers, which are known for their ability to produce dense, high-quality metal parts.
- Quality Assurance and Certifications: Inquire about the provider’s quality management systems and certifications (e.g., ISO 9001, AS9100 for aerospace). Robust quality control processes, including material testing, dimensional inspection, and non-destructive testing, are essential to ensure the reliability and performance of the printed pipe connectors.
- Design and Engineering Support: A good service provider should offer design and engineering support to help optimize your pipe connector design for additive manufacturing. This includes guidance on material selection, topology optimization, support structure design, and post-processing considerations. Metal3DP provides comprehensive solutions spanning equipment, materials, and application development services.
- Post-Processing Capabilities: Determine if the provider offers the necessary post-processing services, such as support removal, heat treatment, CNC machining, polishing, and surface coating. An in-house or well-established network of post-processing partners can streamline the manufacturing process and ensure consistent quality.
- Experience and Expertise: Look for a provider with a proven track record in metal 3D printing, ideally with experience in producing parts for your specific industry (e.g., aerospace, medical, automotive). Review case studies or testimonials to assess their expertise and customer satisfaction.
- Communication and Customer Service: Effective communication and responsive customer service are crucial for a smooth and successful project. Evaluate the provider’s responsiveness, technical support, and willingness to collaborate.
- Cost and Lead Time: Obtain detailed quotes that clearly outline the costs associated with printing, materials, and post-processing. Understand the estimated lead time for production and delivery. While cost is a factor, prioritize quality and reliability, especially for critical applications.
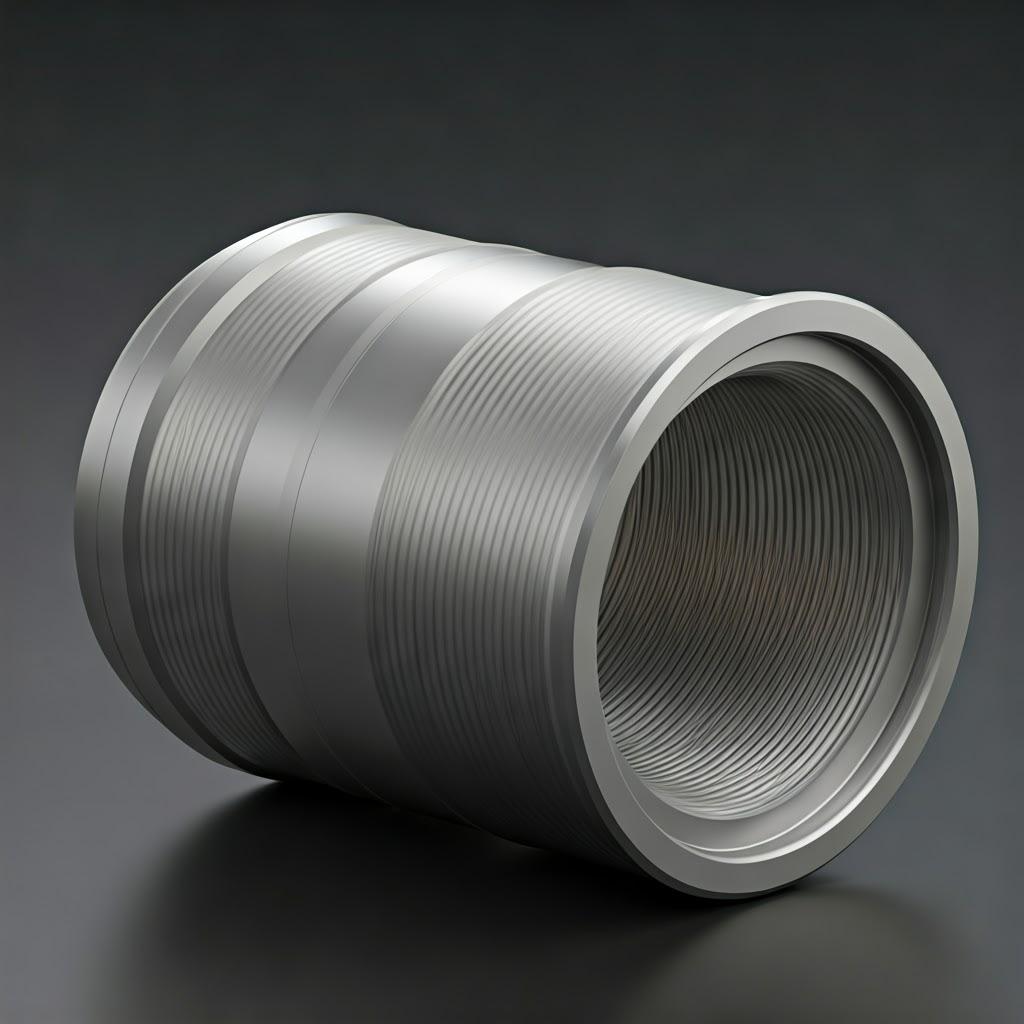
Cost Factors and Lead Time for Metal 3D-Printed Pipe Connectors
The cost and lead time for producing metal 3D-printed pipe connectors can vary significantly depending on several factors. Understanding these factors will help you budget effectively and plan your project timelines.
Факторы стоимости:
- Материальные затраты: The cost of the metal powder (e.g., 316L, 254SMO) is a significant contributor to the overall cost. Specialized alloys like 254SMO are generally more expensive than standard stainless steels like 316L. The quantity of material required for the part also plays a crucial role.
- Время печати: The build time on the 3D printer is a major cost driver. Factors affecting print time include the part’s volume, complexity, layer height, and the number of parts being printed simultaneously on the build platform.
- Machine Operation Costs: This includes the cost of running and maintaining the 3D printer, such as energy consumption, consumables (e.g., shielding gas), and machine depreciation.
- Расходы на постобработку: The cost of post-processing steps like support removal, heat treatment, machining, polishing, and coating can add significantly to the overall cost. The complexity and extent of these processes will influence the final price.
- Design and Engineering Costs: If you require design optimization or engineering support from the service provider, these services will also factor into the cost.
- Quantity and Volume: While metal 3D printing is advantageous for low to medium volumes and highly customized parts, the cost per part may decrease with larger production runs due to economies of scale in material procurement and setup.
Lead Time Factors:
- Part Complexity and Size: More complex and larger parts generally require longer print times, increasing the overall lead time.
- Доступность материала: The availability of the specific metal powder can impact the start of the printing process. Providers like Metal3DP with in-house powder production may have shorter lead times for certain materials.
- Printing Queue: The current workload and capacity of the 3D printing service provider will influence the lead time.
- Post-Processing Time: The time required for post-processing steps can vary depending on the complexity of the part and the specific processes involved. Heat treatment cycles, machining operations, and coating applications can add significant time to the overall lead time.
- Shipping and Logistics: The time required for shipping the finished parts to your location also needs to be considered.
It’s essential to discuss these cost and lead time factors in detail with your chosen metal 3D printing service provider to get an accurate estimate for your specific pipe connector project.
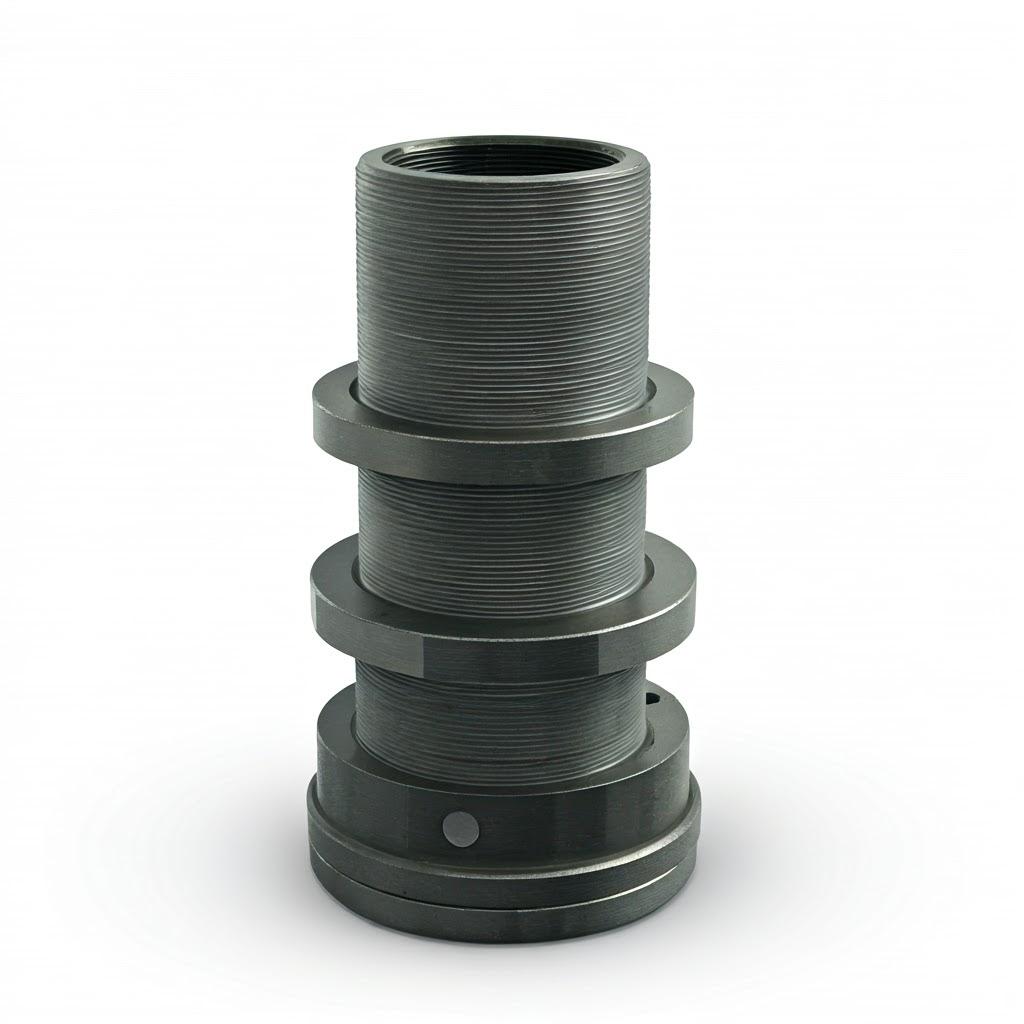
Часто задаваемые вопросы (FAQ)
- Q: Can metal 3D-printed pipe connectors withstand high pressures?
- A: Yes, metal 3D-printed pipe connectors made from materials like 316L and 254SMO can be designed and manufactured to withstand significant pressures, depending on the design, material selection, and post-processing. It’s crucial to work with an experienced provider and conduct thorough testing to validate pressure ratings for specific applications.
- Q: Are metal 3D-printed pipe connectors more expensive than traditionally manufactured ones?
- A: The cost-effectiveness of metal 3D printing for pipe connectors depends on factors such as part complexity, production volume, material choice, and the cost of tooling for traditional methods. For highly customized, low-to-medium volume applications with complex geometries, metal 3D printing can be a cost-competitive and even advantageous solution.
- Q: What is the typical lifespan of a metal 3D-printed corrosion-resistant pipe connector?
- A: The lifespan of a metal 3D-printed corrosion-resistant pipe connector depends on the application environment, the chosen material, and the quality of the manufacturing process. When using appropriate materials like 316L or 254SMO and adhering to proper design and post-processing, these connectors can offer comparable or even superior longevity in corrosive environments compared to traditionally manufactured counterparts.
- Q: Can metal 3D printing be used for large-scale production of pipe connectors?
- A: While metal 3D printing is often associated with prototyping and low-to-medium volume production, advancements in technology and build platform sizes are making it increasingly viable for larger-scale production. However, for very high volumes of simple geometries, traditional manufacturing methods may still be more cost-effective. Metal3DP’s industry-leading print volume capabilities are expanding the possibilities for larger part production.
Заключение
Metal 3D printing offers a powerful and versatile approach to manufacturing high-performance, corrosion-resistant pipe connectors for demanding applications across various industries. The ability to utilize advanced materials like 316L and 254SMO, coupled with the design freedom and customization возможности of additive manufacturing, enables the creation of optimized components with enhanced functionality and longevity. By carefully considering design principles, material selection, post-processing requirements, and choosing a reputable service provider like Metal3DP, engineers and procurement managers can leverage the benefits of metal 3D printing to achieve superior fluid handling solutions. Contact Metal3DP today to explore how their cutting-edge systems and high-quality metal powders can power your organization’s additive manufacturing goals for corrosion-resistant pipe connectors.
Поделиться
MET3DP Technology Co., LTD - ведущий поставщик решений для аддитивного производства со штаб-квартирой в Циндао, Китай. Наша компания специализируется на производстве оборудования для 3D-печати и высокопроизводительных металлических порошков для промышленного применения.
Сделайте запрос, чтобы получить лучшую цену и индивидуальное решение для вашего бизнеса!
Похожие статьи
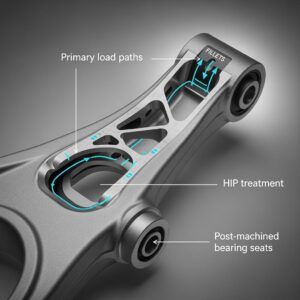
Metal 3D Printing for U.S. Automotive Lightweight Structural Brackets and Suspension Components
Читать далее "О компании Met3DP
Последние обновления
Наш продукт
CONTACT US
Есть вопросы? Отправьте нам сообщение прямо сейчас! После получения Вашего сообщения мы всей командой выполним Ваш запрос.
Получите информацию о Metal3DP
Брошюра о продукции
Получить последние продукты и прайс-лист