Порошковая кровать Fusion
Оглавление
Обзор
Сплавление порошкового слоя - это процесс аддитивного производства, в котором используется тепловая энергия для выборочного послойного сплавления участков порошкового слоя с целью создания деталей. Сегодня это одна из наиболее распространенных технологий 3D-печати металлов для производства.
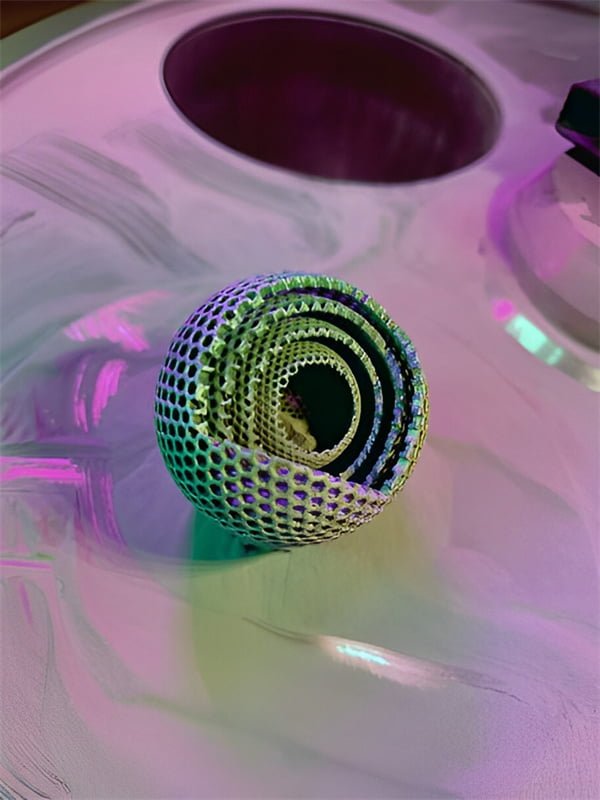
Некоторые ключевые детали порошковой плавки:
- Он относится к семейству аддитивных производств, основанных на чановой фотополимеризации.
- Источник тепловой энергии, например лазер или электронный луч, используется для расплавления и сплавления порошка материала.
- В качестве порошков обычно используются металлы, такие как нержавеющая сталь, титан, алюминий, никелевые сплавы и кобальт-хром. В некоторых процессах также могут использоваться полимеры и керамика.
- Порошковая плавка позволяет создавать полностью плотные металлические детали с механическими свойствами, сравнимыми с традиционным производством.
- Она позволяет создавать сложные геометрические фигуры, недоступные при использовании обычных субтрактивных технологий.
- Область применения - аэрокосмическая, медицинская, стоматологическая, автомобильная и общепромышленная.
- К популярным технологиям порошкового слоя относятся селективное лазерное плавление (SLM), прямое лазерное спекание металлов (DMLS), электронно-лучевое плавление (EBM) и струйное нанесение связующего.
Процессы плавления в порошковом слое
Существует несколько различных технологий порошковой плавки. Основными из них являются:
Процесс | Описание |
---|---|
Селективное лазерное плавление (SLM) | Используется мощный лазер для полного расплавления и сплавления металлического порошка в станине. |
Прямое лазерное спекание металлов (DMLS) | Аналогична SLM, но направлена на спекание порошков, а не на их полное плавление. |
Электронно-лучевое плавление (ЭЛП) | В качестве источника энергии для расплавления порошка используется электронный луч. Выполняется в вакууме. |
Многоструйный синтез (MJF) | Струйная печать плавкого агента на слое полимерного порошка перед спеканием с помощью источника энергии. |
Струйная обработка вяжущего | Жидкий связующий агент, избирательно наносимый для связывания порошкового материала с последующим спеканием. |
Селективное лазерное плавление (SLM) это наиболее распространенная технология плавления в порошковом слое, используемая в настоящее время. Мощный лазер (например, волоконный, CO2, YAG) фокусируется на слое порошка, чтобы создать лужи расплава и сплавить материал. После каждого слоя порошковый слой опускается, и на него насыпается новый порошок. SLM использует полное плавление, поэтому можно создавать детали с высокой плотностью. Обычно используются такие материалы, как нержавеющая сталь, титан, алюминий, инконель.
Прямое лазерное спекание металлов (DMLS) Работает аналогично, но направлена на частичное расплавление порошка с образованием зазоров между частицами для получения цельной детали. DMLS имеет более низкие требования к мощности лазера по сравнению с SLM.
Электронно-лучевое плавление (ЭЛП) В качестве источника энергии используется электронный луч, сфокусированный в вакууме для послойного расплавления металлических порошков. EBM обеспечивает более высокую скорость сборки по сравнению с лазерными процессами, поскольку луч может сканировать быстрее. EBM в основном используется с титановыми сплавами в аэрокосмической промышленности.
Многоструйный синтез (MJF) Использует струйные печатающие головки для выборочного нанесения плавкого агента на слой полимерного порошка, который затем спекается под воздействием источника энергии. MJF обеспечивает высокоскоростное спекание термопластов.
Струйная обработка вяжущего Сначала на выбранные участки наносится жидкое связующее вещество, чтобы связать порошковый материал, а затем происходит спекание для придания детали плотности. Этот метод можно использовать с металлами, керамикой и полимерами.
Материалы для порошкового наплавления
В аддитивном производстве с применением порошкового напыления может использоваться целый ряд материалов. Наиболее распространенными являются:
Материал | Процессы | Приложения |
---|---|---|
Нержавеющая сталь | SLM, DMLS, струйная обработка связующего | Медицинские имплантаты, оснастка, общее машиностроение |
Титановые сплавы | SLM, EBM | Аэрокосмические и медицинские имплантаты |
Алюминиевые сплавы | SLM, EBM | Облегчение автомобильной и аэрокосмической техники |
Никелевые суперсплавы | SLM, EBM | Лопасти турбин, сопла ракет для экстремальных условий эксплуатации |
Кобальт-хром | SLM, DMLS | Зубные имплантаты и протезирование |
Полимеры | MJF, струйное нанесение вяжущего | Прототипирование и конечные пластиковые детали |
Керамика | Струйная обработка вяжущего | Медицинские имплантаты, аэрокосмическая промышленность |
Наиболее широко используются нержавеющие сталикоторые обладают хорошей коррозионной стойкостью и механическими свойствами. Титановые сплавы Такие сплавы, как Ti6Al4V, популярны в аэрокосмической отрасли благодаря снижению веса по сравнению со сталью и никелевыми сплавами. Алюминиевые сплавы позволяют создавать легкие детали для автомобильной и аэрокосмической промышленности.
Никелевые суперсплавы такие как инконель, используются для изготовления высокотемпературных лопаток турбин и сопел ракет. Кобальтохромовые сплавы являются биосовместимыми и широко используются для изготовления зубных протезов. Полимеры Такие материалы, как нейлон, полиэфирэфиркетон и полиамиды, могут быть спечены для изготовления пластиковых деталей. Керамика Такие материалы, как диоксид циркония и глинозем, находят применение в медицинских имплантатах.
Гранулометрический состав, текучесть, плотность упаковки и температура плавления - ключевые свойства порошкового материала, которые определяют технологичность и свойства конечной детали.
Применение порошкового наплавления
Аддитивное производство с использованием порошкового наплавления применяется в аэрокосмической, медицинской, стоматологической, автомобильной и машиностроительной отраслях. Типичные области применения включают:
Промышленность | Приложения |
---|---|
Аэрокосмическая промышленность | Лопасти турбин, сопла ракет, аэродинамические профили, спутники, беспилотники |
Медицина | Ортопедические и зубные имплантаты, протезы, хирургические инструменты |
Автомобильная промышленность | Облегчение прототипов, изготовление оснастки на заказ |
Промышленность | Металлическая оснастка, горное оборудование, обработка жидкостей |
Архитектура | Декоративные элементы, фасады, освещение, мебель |
В аэрокосмическая промышленностьСплавление в порошковом слое идеально подходит для изготовления разовых деталей, таких как спутники и беспилотные летательные аппараты. Она используется для изготовления легких деталей из титана и никелевых сплавов, включая турбины, сопла, каркасы самолетов.
Для медицинскийВ качестве основной области применения титановых и кобальт-хромовых имплантатов и протезов, изготовленных по индивидуальному заказу. Это также позволяет создавать персонализированные хирургические инструменты.
В автомобильная промышленностьПорошковая станина используется для изготовления легких прототипов и нестандартных инструментов и приспособлений, например, оснастки. Для промышленный Оборудование позволяет изготавливать специализированные инструменты, оснастку и конечные металлические детали.
В архитектураПорошковое напыление позволяет создавать уникальные геометрические формы для декоративных и функциональных элементов зданий и мебели.
Преимущества порошкового наплавления
Среди основных преимуществ технологий порошковой плавки можно назвать следующие:
- Сложная геометрия - Возможны замысловатые внутренние элементы и решетки.
- Персонализация - Детали могут быть подобраны в соответствии с индивидуальными требованиями.
- Облегчение - снижение веса компонентов за счет оптимизации конструкции.
- Укрепление - объединение узлов в отдельные детали.
- Высокая прочность - полностью плотные металлы, сопоставимые по прочности с деформируемыми материалами.
- Более короткие сроки выполнения - Быстрый переход от цифрового файла к детали.
- Массовая кастомизация - Сочетание экономии на масштабе с индивидуальным подходом к деталям.
- Устойчивое развитие - меньше отходов по сравнению с субтрактивными процессами.
Способность производить плотные металлические детали со сложной геометрией по индивидуальному заказу делает порошковое наплавление идеальным решением для изготовления легких и высокоэффективных компонентов в различных отраслях промышленности. Технология позволяет объединять узлы в отдельные детали, снижая производственные и складские расходы. Использование аддитивного производства также приводит к значительно меньшему количеству отходов материала по сравнению с традиционными субтрактивными методами, такими как обработка с ЧПУ.
Ограничения порошкового наплавления
Некоторые существующие ограничения включают:
- Ограничения по размеру - Объемы строительства обычно не превышают 1 кубического метра.
- Обработка поверхности - эффект лестницы, требующий постобработки.
- Скорость сборки - медленнее, чем методы крупносерийного производства.
- Анизотропные свойства - направленные изменения свойств материала.
- Стандарты - отсутствие кодов и спецификаций для квалификационных деталей.
- Программное обеспечение - правила оформления и сложности подготовки файлов.
- Затраты - стоимость оборудования и материалов остается относительно высокой.
Максимальный размер компонентов ограничен объемом сборки машин, который растет, но все еще обычно не превышает 1 кубического метра. Послойный процесс может привести к плохой обработке поверхности, требующей сглаживания и полировки.
Общая скорость сборки ниже по сравнению с технологиями крупносерийного производства, такими как литье под давлением. Кроме того, детали могут проявлять анизотропные свойства в зависимости от ориентации сборки. Отсутствие стандартов и спецификаций для квалификации напечатанных деталей также является ограничением в таких жестко регулируемых отраслях, как аэрокосмическая и медицинская. Проектирование оптимальных деталей и предварительная обработка файлов требуют специальных знаний в области программного обеспечения.
Стоимость системы и материалов все еще относительно высока по сравнению с традиционным производством. Однако с ростом внедрения стоимость снижается, и многие приложения могут оправдать затраты за счет производительности деталей, индивидуальности и гибкости конструкции.
Постобработка
Под постобработкой понимаются действия, необходимые после процесса сборки для получения готовой детали:
- Удаление порошка - Детали отделяются от нерасплавленного порошка с помощью щеток.
- Поддержка удаления - Опорные конструкции срезаются и очищаются.
- Обработка поверхности - Шлифовка, шлифовка, дробеструйная обработка для улучшения
Параметры процесса
Существует несколько ключевых параметров процесса, которые могут быть настроены для оптимизации свойств, характеристик и производительности при плавке в порошковом слое:
Параметр | Типовой диапазон | Эффект |
---|---|---|
Мощность лазера | 50-500W | Скорость плавления, размер бассейна расплава, глубина проникновения |
Скорость сканирования | 100-10 000 мм/с | Скорость затвердевания, скорость охлаждения, микроструктура |
Расстояние между люками | 50-200 мкм | Перекрытие дорожек, плотность, прочность соединения |
Толщина слоя | 20-100 мкм | Разрешение, шероховатость поверхности, время сборки |
Стратегия сканирования | Острова, полосы, шахматная доска | Остаточные напряжения, деформация, анизотропия |
Атмосфера процесса | Вакуум, инертный газ | Окисление, загрязнение, пористость |
Мощность лазера влияет на потребляемую энергию, скорость плавления, размеры бассейна расплава и глубину проникновения. Скорость сканирования контролирует скорость затвердевания и скорость охлаждения, что влияет на морфологию зерна и образование дефектов.
Расстояние между люками задает расстояние между дорожками сканирования и влияет на перекрытие, уплотнение и склеивание слоев. Толщина слоя определяет разрешение, шероховатость поверхности и общее время сборки.
Стратегия сканирования (шаблоны сканирования) влияет на остаточные напряжения, искажения и анизотропные свойства в зависимости от направления печати. Атмосфера процесса определяет уровень окисления и загрязнения.
Переработка порошков
- Нерасплавленный порошок можно собрать и просеять для удаления крупных частиц
- Обычно используется до 20 циклов
- Значительное снижение затрат на порошок
- Свежий порошок добавляется для пополнения и поддержания химического состава
- Свойства, контролируемые на предмет пороговых значений повторного использования
В процессе плавления в порошковом слое нерасплавленный порошок используется повторно для изготовления новых изделий. После обезжиривания сыпучий порошок собирается, просеивается для удаления крупных частиц и смешивается со свежим порошком перед повторным использованием.
Типичная частота повторного использования составляет до 20 циклов в зависимости от материала, изменения размера частиц и уровня загрязнения. Такая переработка значительно повышает эффективность использования материала и снижает общую стоимость деталей. Для определения коэффициента обновления контролируется соотношение и свойства повторно используемого порошка.
Контроль качества
Некоторые ключевые меры контроля качества, используемые при плавке в порошковом слое, включают:
- Химический анализ порошков
- Анализ распределения частиц по размерам
- Отслеживание повторного использования порошка
- Контроль бассейна расплава
- Контроль геометрии деталей
- Испытание механических свойств
- Неразрушающий контроль (например, рентгеновский)
- Компьютерная томография для выявления внутренних дефектов
- Измерение шероховатости поверхности
Для обеспечения высокого качества анализируются химический состав и гранулометрический состав исходного порошка. Отслеживается скорость обновления порошка. Системы контроля в процессе производства, такие как мониторинг бассейна расплава, выявляют дефекты во время сборки.
Печатные детали измеряются на предмет геометрических допусков. Механические испытания оценивают свойства в зависимости от параметров процесса и ориентации сборки. Неразрушающее и компьютерное сканирование выявляет внутренние дефекты. Оценивается качество обработки поверхности. Все данные анализируются для калибровки и оптимизации процессов.
Анализ затрат
Типичная стоимость деталей, изготовленных методом порошкового наплавления, зависит от:
- Амортизация оборудования
- Материальные затраты
- Трудозатраты на предварительную и последующую обработку
- Время строительства и потребление энергии
- Количество многоразового порошка
- Соотношение покупки и полета
Затраты на оборудование амортизируются в течение ожидаемого срока службы в зависимости от его использования. Затраты на материалы рассчитываются исходя из объема деталей и соотношения "покупка - полет". Трудозатраты включают подготовку файлов, настройку, удаление остатков и финишную обработку.
Расход энергии зависит от времени сборки и уровня мощности. Многоразовый порошок снижает общие затраты на материалы. Соотношение "покупка - полет" от 3:1 до 20:1 является обычным для дорогостоящих деталей.
Поставщики
Среди основных поставщиков систем порошкового наплавления можно назвать следующих:
Поставщик | Ключевая технология |
---|---|
EOS | DMLS (прямое лазерное спекание металлов) |
3D Systems | DMP (прямая печать по металлу) |
GE Additive | DMLM (прямое лазерное плавление металла) |
Трампф | Металлические 3D-принтеры TruPrint |
Sisma | Системы лазерного сплавления металлов |
AddUp | Металлические 3D-принтеры FormUp |
EOS и 3D Systems были первопроходцами в области порошкового термоядерного синтеза и остаются лидерами по сей день. GE Additive приобрела компании Concept Laser и Arcam EBM, чтобы предлагать лазерные и электронно-лучевые технологии. Трампф и Sisma также поставляет промышленные системы SLM. AddUp это совместное предприятие Michelin и Fives, специализирующееся на аддитивном производстве металлов.
Существует также множество поставщиков материалов для порошкового плавления, включая Carpenter, Sandvik, Praxair, LPW Technology и AP&C.
Сравнение стоимости
Процесс | Стоимость оборудования | Стоимость материала | Скорость |
---|---|---|---|
Сплавление порошкового слоя | $100K - $1M+ | $100-500/кг | 5-100 см3/час |
Обработка на станках с ЧПУ | $50K - $500K | 1ТП4Т5-50/кг | 50-500 см3/час |
Литье под давлением | $100K - $1M+ | $2-5/кг | 100-1000 см3/час |
Системы с порошковым слоем имеют высокую стоимость оборудования - от $100 000 для промышленных принтеров до более $1 миллиона для крупных производственных систем. Стоимость материалов варьируется от $100-500/кг. Скорость производства варьируется от 5-100 см3/час в зависимости от технологии.
Обработка с ЧПУ имеет более низкую стоимость оборудования - от $50 000. Стоимость металлических материалов дешевле - $5-50/кг. Скорость обработки составляет 50-500 см3/час.
Системы литья под давлением также стоят более $100 000. Но пластик очень дешев - $2-5/кг. Скорость составляет 100-1000 см3/час.
Таким образом, плавка в порошковом слое экономически эффективна только при изготовлении металлических деталей небольшого объема и высокой стоимости, когда производительность оправдывает более высокие затраты.
Сплавление порошкового слоя по сравнению со струйной обработкой связующего
Порошковая кровать Fusion | Струйная обработка вяжущего | |
---|---|---|
Материалы | Металлы, полимеры, керамика | Металлы, полимеры, керамика |
Плотность | Полностью плотные детали | Пористые части, необходима инфильтрация |
Точность | Средний, ±0,1% с постобработкой | Средняя, ±0,2% |
Отделка поверхности | Умеренная, требует отделки | Остается справедливая, многослойная текстура. |
Скорость | Медленно, зависит от источника энергии | Быстро, независимо от источника энергии |
Приложения | Металлические детали конечного использования | Инструментальная оснастка, модели для литья, прототипы |
- Сплавление порошкового слоя позволяет получать полностью плотные детали, в то время как детали, полученные методом струйной обработки связующего, являются пористыми и требуют инфильтрации.
- Точность струйного нанесения связующего умеренная, в то время как сплавление в порошковом слое может достигать более высокой точности при последующей обработке.
- Поверхность, полученная методом порошкового наплавления, требует финишной обработки, в то время как струйное нанесение связующего имеет многослойную, текстурированную поверхность.
- Скорость создания струи связующего намного выше, чем при использовании порошкового слоя, ограниченного источником энергии.
- Порошковый слой чаще используется для изготовления деталей конечного потребления, в то время как струйная обработка связующим лучше подходит для изготовления оснастки, литья и концептуальных моделей.
Порошковое напыление против направленного энергетического осаждения
Порошковая кровать Fusion | DED | |
---|---|---|
Материалы | Преимущественно металлы | Металлы, полимеры |
Геометрия | Обеспечение сложности | Средняя сложность |
Точность | Средний и высокий уровень | Средний |
Отделка поверхности | Умеренная, требует отделки | Грубая, более тщательная отделка |
Масштабируемость | Мелкие и средние детали | Средние и крупные детали |
Скорость осаждения | Низкая, зависит от скорости сканирования | Высокая, увеличивается при использовании более крупных насадок |
- Порошковая плавка в основном используется для металлов, в то время как DED может использовать металлы и полимеры.
- Сплавление в порошковом слое обеспечивает более высокую сложность, чем DED, которая имеет некоторые геометрические ограничения.
- Точность выше при плавке в порошковом слое. Точность DED средняя.
- DED создает шероховатые поверхности, требующие более тщательной обработки за счет присадок.
- Сплавление в порошковом слое позволяет создавать небольшие детали, а DED - средние и большие формы, близкие к сетчатым.
- DED имеет гораздо более высокую скорость осаждения благодаря методу выдувания порошка.
Таким образом, сплавление в порошковом слое обычно позволяет получать небольшие сложные геометрические формы на умеренных скоростях. DED позволяет получать большие простые формы гораздо быстрее, но с большим объемом отделочных работ.
Будущее порошкового наплавления
Некоторые области будущего развития порошковой плавки включают в себя:
- Большие объемы строительства до нескольких кубических метров
- Более быстрые методы сканирования для увеличения скорости сборки
- Расширяющиеся материалы, такие как высокотемпературные сплавы, ГМК, полимеры
- Гибридное производство, объединяющее порошковое наплавление и ЧПУ
- Автоматизированная очистка и постобработка
- Расширенный мониторинг и управление в режиме реального времени
- Более строгие процедуры квалификации и сертификации
Более крупные платформы для сборки позволяют изготавливать более крупные детали или увеличивать производительность. Новые технологии более быстрого сканирования могут значительно увеличить скорость сборки. Возможности выбора материалов будут продолжать расширяться, особенно за счет высокоэффективных сплавов.
Поделиться
MET3DP Technology Co., LTD - ведущий поставщик решений для аддитивного производства со штаб-квартирой в Циндао, Китай. Наша компания специализируется на производстве оборудования для 3D-печати и высокопроизводительных металлических порошков для промышленного применения.
Сделайте запрос, чтобы получить лучшую цену и индивидуальное решение для вашего бизнеса!
Похожие статьи
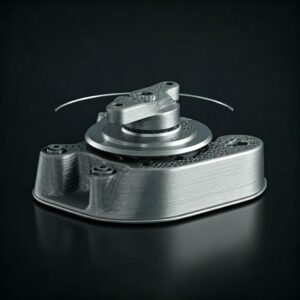
3D-печатные крепления для автомобильных радарных датчиков: Точность и производительность
Читать далее "О компании Met3DP
Последние обновления
Наш продукт
CONTACT US
Есть вопросы? Отправьте нам сообщение прямо сейчас! После получения Вашего сообщения мы всей командой выполним Ваш запрос.
Получите информацию о Metal3DP
Брошюра о продукции
Получить последние продукты и прайс-лист
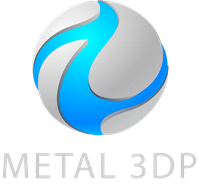
Металлические порошки для 3D-печати и аддитивного производства