3D Printed Heat Dissipation Sinks for UAV Electronics
Оглавление
Introduction: The Critical Role of Thermal Management in Modern UAVs
Unmanned Aerial Vehicles (UAVs), commonly known as drones, have transitioned from niche applications to indispensable tools across a multitude of sectors, including defense, surveillance, logistics, agriculture, and infrastructure inspection. This proliferation is driven by continuous advancements in miniaturization, sensor technology, battery life, and autonomous capabilities. However, as UAVs become more powerful, compact, and mission-critical, they face a significant engineering challenge: managing the heat generated by their increasingly dense and high-performance electronic components. Effective thermal management is no longer just an optimization parameter; it is a fundamental requirement for ensuring operational reliability, maximizing performance, extending mission endurance, and guaranteeing the safety of the aircraft and its surroundings.
At the heart of UAV operations lie sophisticated electronic systems. Central processing units (CPUs) and graphics processing units (GPUs) handle complex flight control algorithms, sensor data fusion, image processing, and communication protocols. Power electronics, including Electronic Speed Controllers (ESCs) and voltage regulators, manage the flow of energy from the battery to the motors and onboard systems, often operating at high currents and switching frequencies. High-resolution cameras, LiDAR sensors, communication modules, and specialized payloads all contribute to the overall heat load within the confined space of the UAV airframe. Without adequate cooling, these components can quickly exceed their optimal operating temperature ranges.
The consequences of inadequate thermal management in UAVs are severe and multifaceted:
- Performance Degradation: Electronic components exhibit reduced processing speeds and efficiency when overheated. CPUs may throttle down, reducing computational power needed for navigation or data analysis. Sensor accuracy can drift, compromising mission objectives.
- Reduced Reliability: Sustained high temperatures accelerate the degradation of electronic components, leading to premature failures. Solder joints can weaken, capacitors can dry out, and semiconductor junctions can fail, potentially causing catastrophic system malfunction during flight.
- Shorter Mission Endurance: Higher temperatures can lead to increased power consumption, draining batteries faster. Furthermore, systems may need to operate at reduced power levels to prevent overheating, limiting the UAV’s operational capabilities and flight time.
- Safety Risks: Failure of critical components like flight controllers or power systems due to overheating can lead to loss of control, posing significant safety risks, especially in populated areas or complex operational environments.
- Component Damage: Extreme overheating can cause permanent physical damage to sensitive electronics, requiring costly repairs and replacements.
Traditionally, thermal management in electronics has relied on heat sinks – passive components designed to absorb heat from a source (like a CPU) and dissipate it into the surrounding air or fluid. These are typically made from thermally conductive materials like aluminum or copper and feature fins or other extended surfaces to maximize the area available for heat transfer, primarily through convection. However, conventional manufacturing methods like CNC machining or extrusion, while effective for simpler designs, face limitations when applied to the unique constraints of UAVs:
- Вес: Every gram matters in aerospace. Traditional heat sinks, often machined from solid blocks, can add significant weight, reducing payload capacity and flight time.
- Space Constraints: UAV airframes are tightly packed. Standard heat sink designs may not fit optimally within the available, often irregular, internal spaces.
- Сложность дизайна: Achieving optimal airflow and heat dissipation often requires complex geometries (e.g., curved fins, non-uniform fin spacing, integrated ducting) that are difficult or impossible to produce efficiently with subtractive manufacturing.
This is where аддитивное производство металлов (AM), или 3D-печать, emerges as a transformative technology. By building parts layer by layer directly from digital models, metal AM enables the creation of highly complex, lightweight, and customized heat sinks specifically optimized for the demanding thermal and geometric constraints of UAV applications. Companies like Met3dp, specializing in advanced metal powders and printing systems, are at forefront of providing these innovative thermal management solutions. This capability allows engineers to reimagine heat sink design, moving beyond the limitations of traditional methods to unlock new levels of performance and reliability for next-generation UAV platforms. This article delves into the specifics of using metal 3D printing for UAV heat sinks, exploring applications, benefits, materials, design considerations, and how to partner with the right AM service provider.
What are 3D Printed UAV Heat Sinks Used For? Applications and Industries
The application of 3D printed metal heat sinks in UAVs is driven by the need for highly efficient and customized cooling solutions for specific heat-generating components housed within tightly constrained spaces. The unique capabilities of additive manufacturing allow designers to tailor thermal solutions precisely to the component’s heat load, the available airflow (or lack thereof), and the specific geometric limitations of the surrounding environment within the drone. These custom heat sinks are finding critical use cases across various components and are enabling advancements in several key industries reliant on high-performance UAVs.
Key UAV Components Benefiting from 3D Printed Heat Sinks:
- Central Processing Units (CPUs) & Graphics Processing Units (GPUs): These are the brains of the UAV, handling intensive tasks like real-time flight control, autonomous navigation (SLAM), sensor fusion, AI-powered image recognition, and complex data processing. High clock speeds and multi-core architectures generate substantial heat loads, often concentrated in small areas. 3D printed heat sinks can be designed with optimized fin structures, microchannels, or even integrated heat pipes (using hybrid manufacturing approaches) to efficiently draw heat away from these critical processors, preventing thermal throttling and ensuring consistent performance. Topology optimization algorithms can be used to place material only where it’s needed for thermal transfer and structural integrity, minimizing weight.
- Power Electronics (ESCs, Voltage Regulators, Power Distribution Units): Electronic Speed Controllers (ESCs) regulate the power delivered to the UAV’s motors, involving high currents and rapid switching, leading to significant resistive and switching losses manifesting as heat. Voltage regulators and power distribution boards also generate considerable heat. The compact nature of these components, often distributed throughout the airframe, demands custom-shaped heat sinks that can conform to available surfaces and potentially integrate with airflow paths. Metal AM allows for the creation of complex, conformal heat sinks with high surface areas, ensuring these power components operate reliably under demanding flight conditions.
- High-Power Sensors (LiDAR, High-Resolution Cameras, Radar): Advanced sensor payloads generate significant heat. For example, the laser diodes and detectors in LiDAR systems, the processing chips in high-resolution cameras, or the transmitters/receivers in compact radar units can all require dedicated cooling. 3D printed heat sinks can be designed to directly interface with these specific sensor modules, maximizing thermal contact and providing localized cooling, ensuring data accuracy and sensor longevity. The design freedom allows integration of cooling features directly into sensor housings or mounts.
- Communication Modules (High-Bandwidth Data Links, SATCOM): Transmitting and receiving large amounts of data, especially over long ranges or via satellite communication (SATCOM) terminals, requires powerful RF amplifiers and processing hardware that generate substantial heat. Ensuring the thermal stability of these communication systems is vital for maintaining reliable command and control links, as well as data transmission. Custom 3D printed heat sinks, potentially incorporating optimized airflow channels or liquid cooling integration points, can effectively manage the heat from these high-power modules.
- FPGA (Field-Programmable Gate Arrays) Boards: FPGAs are often used for specialized, high-speed processing tasks in UAVs. Their power consumption and heat generation can vary significantly depending on the programmed logic. Custom-designed 3D printed heat sinks provide a flexible solution to cool these versatile chips effectively, accommodating different board layouts and thermal profiles.
- Integrated Electronics Enclosures: Beyond individual components, metal AM can be used to print entire electronics enclosures that incorporate heat sinking features directly into the structure. This part consolidation reduces assembly complexity, saves weight, and ensures optimal thermal pathways from multiple heat sources to the exterior of the enclosure. Such integrated designs are exceptionally difficult to achieve using traditional methods.
Industries Leveraging 3D Printed UAV Heat Sinks:
- Оборона и безопасность: Military and surveillance drones often operate in harsh environments and carry sophisticated, high-power sensor suites and communication equipment. Reliability is paramount. 3D printed heat sinks enable compact, lightweight, and highly effective thermal management solutions crucial for mission success and stealth (e.g., optimizing for low thermal signature). The ability to rapidly prototype and produce custom designs for specific mission requirements is a significant advantage. Demand for UAV heat sink manufacturers specializing in defense applications is growing.
- Aerospace and Exploration: Whether for atmospheric research, planetary exploration (e.g., Mars helicopters), or high-altitude platforms, aerospace applications demand extreme weight savings and reliability. 3D printed heat sinks made from aerospace-grade materials like AlSi10Mg offer significant advantages in achieving these goals. The technology supports the development of more capable and longer-endurance aerial platforms.
- Logistics and Delivery: Delivery drones, especially those designed for heavier payloads or longer ranges, require efficient power systems. Optimizing the cooling of ESCs and power distribution units using lightweight 3D printed heat sinks helps maximize flight time and payload capacity, crucial for the economic viability of drone delivery services. Wholesale 3D printed parts suppliers can cater to the scaling needs of this industry.
- Agriculture and Environmental Monitoring: Drones equipped with multispectral cameras, thermal sensors, and other instruments for precision agriculture or environmental monitoring benefit from reliable electronics cooling. 3D printed heat sinks ensure sensor accuracy and operational longevity during extended flights over large areas, often in hot or humid conditions.
- Infrastructure Inspection: UAVs inspecting bridges, power lines, wind turbines, and pipelines rely on high-resolution cameras and sensors. Effective thermal management ensures these tools operate correctly throughout potentially long inspection missions, preventing data loss or component failure. Custom 3D printed electronics enclosure solutions with integrated cooling are particularly relevant here.
- Медицинские приложения: While less common currently, specialized UAVs for emergency medical supply delivery might carry temperature-sensitive payloads or require highly reliable operation, benefiting from optimized thermal management.
In essence, any application demanding high performance, reliability, miniaturization, and weight optimization in UAVs can benefit significantly from the tailored thermal solutions offered by 3D printed metal heat sinks. The ability to create application-specific, performance-driven designs makes AM a key enabler for pushing the boundaries of UAV capabilities across diverse industries. Procurement managers seeking поставщики аддитивного производства should look for partners with expertise in thermal design and experience with relevant aerospace or electronics applications.
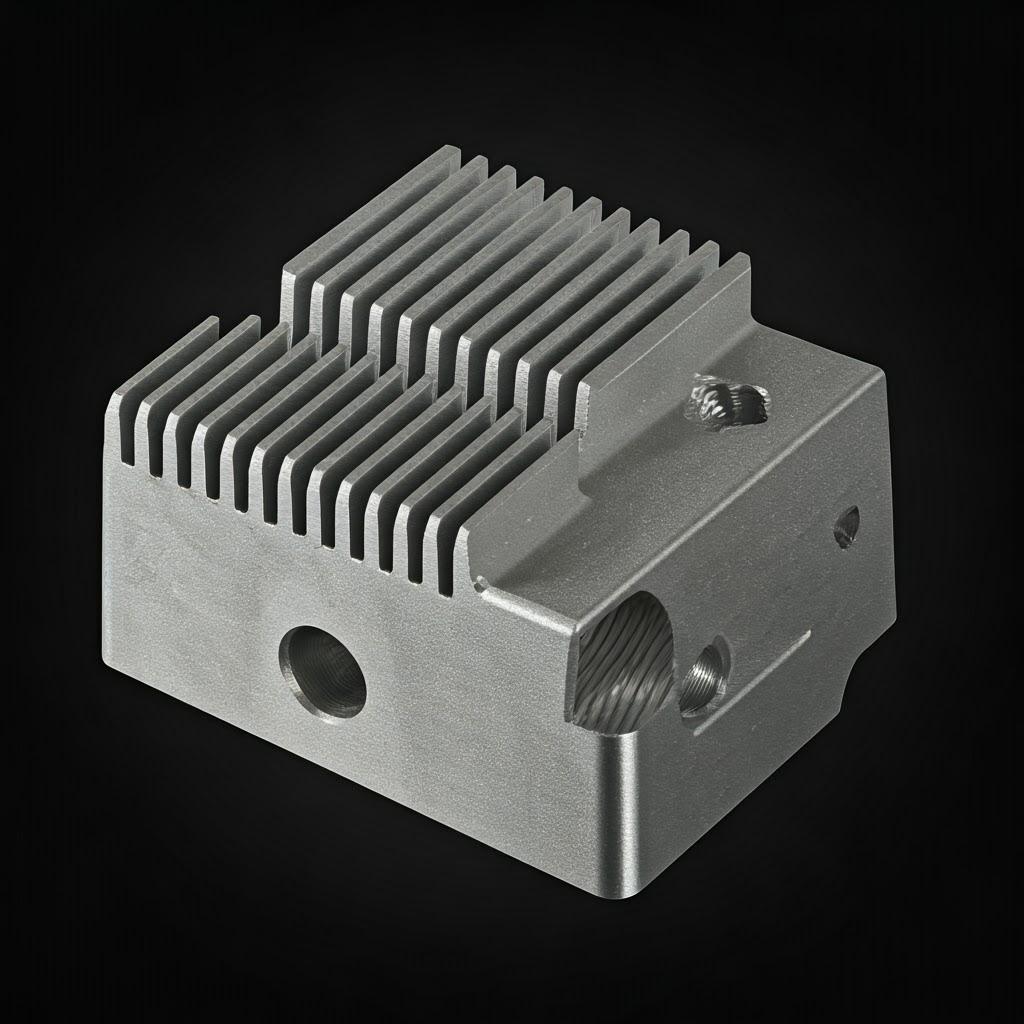
Why Use Metal 3D Printing for UAV Heat Sinks? Unlocking Performance Gains
The decision to adopt metal additive manufacturing for producing UAV heat sinks stems from a confluence of compelling advantages that directly address the limitations of traditional manufacturing methods and align perfectly with the demanding requirements of aerospace applications. While CNC machining, casting, or extrusion can produce functional heat sinks, metal AM offers unique capabilities that unlock significant performance gains, design freedom, and operational efficiencies, particularly crucial for UAVs where weight, space, and performance are critically intertwined. The transition towards AM represents a shift from designing for manufacturability (within traditional constraints) to manufacturing for optimal performance.
Let’s explore the key reasons why металлическая 3D-печать is rapidly becoming the preferred method for high-performance UAV heat sinks:
1. Unprecedented Design Freedom & Complexity:
- Topology Optimization: This is perhaps the most significant advantage. Engineers can use Finite Element Analysis (FEA) and topology optimization software to define thermal loads, boundary conditions, and design spaces. The software then iteratively removes material from areas where it doesn’t contribute significantly to thermal transfer or structural integrity, leaving behind an organic, highly efficient structure. This often results in complex, lattice-like or biomimetic designs that are impossible to machine or cast but offer superior heat dissipation-to-weight ratios. The resulting heat sinks are inherently lightweight and tailored precisely to the thermal task.
- Сложные геометрии: AM can create intricate internal channels, non-uniform fin shapes and densities, curved surfaces, and integrated features (like mounting points or flow guides) in a single piece. This allows designers to:
- Maximize surface area within a given volume.
- Optimize airflow paths for forced or natural convection.
- Create conformal heat sinks that perfectly match the contours of curved electronic components or internal airframe structures.
- Integrate functionalities, potentially combining a structural bracket with heat dissipation features.
- Решетчатые структуры: AM enables the incorporation of periodic or stochastic lattice structures within the heat sink body. These structures can dramatically increase the surface area for heat exchange while minimizing material usage and weight. Different lattice cell types (e.g., gyroids, octet-truss) can be selected based on desired thermal conductivity, permeability to airflow, and structural properties.
2. Significant Weight Reduction:
- Topology Optimization: As mentioned, this process inherently removes unnecessary material, leading to substantial weight savings compared to subtractively manufactured parts designed with traditional constraints. Weight reductions of 30-60% or even more are often achievable for complex components like heat sinks, directly translating to improved UAV flight time, payload capacity, or maneuverability.
- Эффективность материала: AM is an additive process, meaning material is only placed where needed. Unlike CNC machining, which starts with a solid block and removes material (creating waste), AM minimizes material consumption, which can be cost-effective, especially with expensive aerospace alloys.
- Lightweight Materials: AM processes are well-suited for lightweight, high-performance alloys like Aluminum Silicon Magnesium (AlSi10Mg), offering excellent thermal conductivity combined with low density.
3. Part Consolidation:
- AM allows multiple components of a thermal management assembly to be combined into a single, monolithic part. For instance, a heat sink, its mounting bracket, and potentially even part of the electronics enclosure could be printed as one unit.
- Преимущества:
- Reduces assembly time and labor costs.
- Eliminates fasteners and interfaces, reducing potential points of failure.
- Improves structural integrity.
- Can further reduce overall weight and volume.
- Simplifies supply chain management (fewer parts to source).
4. Rapid Prototyping and Iteration:
- AM enables designers to move quickly from a digital CAD model to a physical metal prototype. This accelerates the design-test-iterate cycle significantly compared to the long lead times often associated with tooling for casting or complex multi-axis CNC programming.
- Engineers can print multiple design variations simultaneously or in quick succession, physically test their thermal performance, and rapidly refine the design based on empirical data. This agility is crucial for optimizing thermal solutions in the fast-evolving field of UAV technology. Companies seeking услуги быстрого прототипирования find AM particularly attractive.
5. Customization and On-Demand Production:
- AM is ideal for producing highly customized or low-volume batches of heat sinks without the prohibitive tooling costs associated with traditional methods. Each print run can potentially produce unique designs tailored to specific UAV models, mission profiles, or component variations.
- This facilitates on-demand manufacturing, reducing the need for large inventories and allowing for design updates to be implemented quickly. Custom heat sink design becomes economically viable even for specialized applications.
6. Enhanced Thermal Performance:
- The ability to create complex geometries and maximize surface area directly translates to more efficient heat dissipation. Optimized airflow channels and fin designs enabled by AM can significantly lower component operating temperatures compared to standard, off-the-shelf heat sinks constrained by traditional manufacturing limitations.
- AM allows for thin walls and fine features, enabling designs with higher fin densities where appropriate, further boosting convective heat transfer.
Comparison: Metal AM vs. Traditional Methods for UAV Heat Sinks
Характеристика | Аддитивное производство металлов (AM) | Обработка с ЧПУ | Extrusion / Casting |
---|---|---|---|
Сложность конструкции | Very High (Topology optimization, lattices, complex channels) | Moderate to High (Limited by tool access, axes) | Low to Moderate (Uniform cross-sections, draft angles) |
Weight Efficiency | Excellent (Optimized structures, lightweight materials) | Good (Material removal, but often over-engineered) | Moderate (Often solid, less optimized shapes) |
Консолидация частей | High potential | Low potential | Low potential |
Lead Time (Prototype) | Fast (Days) | Moderate (Days to Weeks) | Slow (Weeks to Months – requires tooling) |
Стоимость оснастки | Никто | Low (Fixturing) | High (Molds, Dies) |
Материальные отходы | Low (Additive process) | High (Subtractive process) | Moderate (Gates, runners) |
Персонализация | High (Economical for low volume / unique parts) | Moderate (Requires reprogramming) | Low (Requires new tooling for changes) |
Ideal Volume | Low to Medium, High Complexity | Low to High, Moderate Complexity | Medium to Very High, Low Complexity |
Тепловые характеристики | Potentially Superior (Optimized shapes, max surface area) | Good (Standard fin designs) | Good (Standard fin designs) |
Export to Sheets
While traditional methods remain suitable for simple, high-volume heat sinks, metal AM provides a clear advantage for the demanding, weight-sensitive, and geometrically complex thermal challenges found in modern UAVs. By embracing additive manufacturing vs CNC or casting, engineers can design and produce heat sinks that are lighter, more efficient, and perfectly integrated into the UAV system, ultimately contributing to superior overall performance and reliability. Partnering with an experienced поставщик аддитивного производства like Met3dp, which possesses both advanced printing technology and materials expertise, is key to realizing these benefits.
Recommended Materials for Optimal Thermal Performance: AlSi10Mg and CuCrZr
Selecting the right material is paramount when designing and manufacturing 3D printed heat sinks, especially for demanding UAV applications where thermal performance, weight, and mechanical integrity are critical. The choice of material directly impacts the heat sink’s ability to conduct heat away from the source, its overall weight contribution to the UAV, its structural robustness, and its compatibility with the operating environment. For metal additive manufacturing of UAV heat sinks, two alloys stand out due to their favorable combination of properties: Aluminum Silicon Magnesium (AlSi10Mg) and Copper Chromium Zirconium (CuCrZr). Understanding their characteristics is essential for making informed design and manufacturing decisions.
1. Aluminum Silicon Magnesium (AlSi10Mg): The Lightweight All-Rounder
AlSi10Mg is one of the most widely used aluminum alloys in additive manufacturing, particularly Laser Powder Bed Fusion (L-PBF). It’s essentially a casting alloy adapted for AM processes, known for its excellent combination of low density, good thermal conductivity, good mechanical properties (especially after heat treatment), and relatively straightforward printability.
- Основные свойства:
- Плотность: Approximately 2.67g/cm3. This low density is a primary driver for its use in aerospace applications, directly contributing to weight savings in the UAV.
- Теплопроводность: Typically ranges from 130−180W/(m⋅K) depending on the print parameters, post-processing (heat treatment significantly improves it), and microstructure. While not as high as pure aluminum or copper alloys, it’s sufficient for many electronic cooling applications and significantly better than polymers or stainless steels.
- Механическая прочность: Offers good strength-to-weight ratio. As-printed parts have decent strength, but appropriate heat treatments (like T6) can significantly increase tensile strength, yield strength, and hardness, making the heat sink structurally robust.
- Возможность печати: Generally considered to have good processability with L-PBF systems, allowing for fine features and complex geometries.
- Коррозионная стойкость: Exhibits good corrosion resistance, suitable for typical operating environments.
- Стоимость: Relatively cost-effective compared to copper alloys or titanium.
- Why it Matters for UAV Heat Sinks:
- Weight Savings: The primary advantage. Its low density allows for the creation of lightweight yet effective heat sinks, maximizing UAV endurance and payload capacity. Even complex, topology-optimized designs remain significantly lighter than comparable copper parts.
- Good Thermal Performance: Provides effective heat dissipation for many common UAV electronic components like CPUs, FPGAs, and lower-power modules.
- Structural Integration: Its good mechanical properties (post-heat treatment) allow the heat sink to potentially serve a secondary structural role, supporting components or contributing to the rigidity of the electronics enclosure, enabling part consolidation.
- Manufacturability: Its widespread use means many AM service providers have well-established parameters and expertise in printing AlSi10Mg, leading to reliable production.
- Соображения:
- Requires post-print heat treatment (stress relief and aging, e.g., T6 cycle) to achieve optimal mechanical properties and thermal conductivity. This adds a step and cost to the process.
- Thermal conductivity is good, but lower than copper alloys. For extremely high heat flux applications, it might be insufficient.
2. Copper Chromium Zirconium (CuCrZr): High Conductivity Champion
CuCrZr (typically UNS C18150) is a high-performance copper alloy specifically designed to offer a compelling combination of high thermal and electrical conductivity, good mechanical strength, and excellent resistance to softening at elevated temperatures. It’s increasingly being adopted in additive manufacturing for applications demanding superior heat transfer capabilities.
- Основные свойства:
- Плотность: Approximately 8.89g/cm3. Significantly denser than AlSi10Mg, making weight a critical design consideration.
- Теплопроводность: Excellent, typically exceeding 300W/(m⋅K), often reaching over 320W/(m⋅K) after appropriate heat treatments. This is more than double the conductivity of AlSi10Mg, allowing for much more efficient heat transfer.
- Электропроводность: Very high (typically >80% IACS – International Annealed Copper Standard), which can be relevant if the heat sink also needs to serve as an electrical ground plane or conductor.
- Механическая прочность: Good strength, especially for a copper alloy, and notably retains its strength well at moderately elevated temperatures where pure copper would soften significantly. Precipitation hardening heat treatments are used to achieve optimal strength.
- Возможность печати: More challenging to print via L-PBF than AlSi10Mg due to copper’s high reflectivity and thermal conductivity, which affects laser absorption and melt pool stability. Requires optimized high-power lasers (often green lasers) and carefully controlled parameters. Less commonly processed via SEBM.
- Стоимость: Copper powders are generally more expensive than aluminum powders, and the challenging printing process can add to the overall cost.
- Why it Matters for UAV Heat Sinks:
- Superior Heat Dissipation: Its outstanding thermal conductivity makes it the ideal choice for cooling components with very high heat fluxes, such as high-power RF amplifiers, densely packed power electronics (ESCs), or high-performance processing units pushed to their limits. It can manage thermal loads that are simply too demanding for aluminum alloys.
- Compact Designs: Because it transfers heat so efficiently, a CuCrZr heat sink can often be designed to be smaller or have less surface area than an AlSi10Mg equivalent for the same cooling performance, which can be beneficial in space-constrained UAVs, partially offsetting the weight penalty.
- Высокотемпературная стабильность: Maintains mechanical properties better than aluminum alloys at higher operating temperatures, improving reliability for components that run hot.
- Соображения:
- Weight is a major drawback due to its high density. Designs must leverage topology optimization aggressively to minimize mass.
- Higher material and processing costs compared to AlSi10Mg.
- More challenging to print reliably, requiring specialized equipment (e.g., green laser PBF systems) and expertise. Fewer service providers may offer reliable CuCrZr printing.
Material Properties Comparison:
Недвижимость | AlSi10Mg (Post T6 Heat Treatment) | CuCrZr (Post Heat Treatment) | Единицы | Significance for UAV Heat Sinks |
---|---|---|---|---|
Плотность | ~2.67 | ~8.89 | g/cm3 | Lower is better for weight savings (Advantage: AlSi10Mg) |
Теплопроводность | ~150 – 180 | ~300 – 320+ | W/(m⋅K) | Higher is better for heat dissipation (Advantage: CuCrZr) |
Прочность на разрыв | ~300 – 350 | ~450 – 550 | MPa | Higher indicates better structural integrity |
Предел текучести | ~230 – 280 | ~350 – 450 | MPa | Resistance to permanent deformation |
Рабочая температура | Good up to ~150°C | Good up to ~400-500°C (retains strength better) | °C | CuCrZr offers better high-temp stability |
Print Difficulty (L-PBF) | Умеренный | High (Requires specific parameters/lasers) | – | Impacts availability, cost, and quality control needs |
Относительная стоимость | Нижний | Выше | – | Impacts overall component and UAV cost |
Export to Sheets
Met3dp’s Role in Material Quality:
The performance of the final 3D printed heat sink is heavily dependent on the quality of the metal powder used. Companies like Met3dp play a crucial role by leveraging advanced powder production techniques to ensure optimal material characteristics.
- Advanced Powder Making System: Met3dp utilizes industry-leading распыление газа and Plasma Rotating Electrode Process (PREP) technologies. Gas atomization, in particular, employs unique nozzle and gas flow designs optimized to produce metallic powders with:
- Высокая сферичность: Spherical powder particles flow more easily and pack more densely in the powder bed, leading to more uniform layers and reduced porosity in the final part. This is critical for consistent thermal conductivity and mechanical integrity.
- Good Flowability: Consistent powder flow ensures reliable recoating of the build plate during the printing process, preventing defects and ensuring dimensional accuracy.
- Controlled Particle Size Distribution (PSD): An optimized PSD contributes to high packing density and predictable melting behavior.
- Low Impurity Levels: High purity powders ensure the desired alloy properties are achieved without detrimental effects from contaminants.
- Высококачественные металлические порошки: Met3dp manufactures a wide range of высококачественные металлические порошки optimized for laser (L-PBF) and electron beam (SEBM – Selective Electron Beam Melting) powder bed fusion processes. While their portfolio includes innovative alloys like TiNi, TiTa, TiAl, etc., their capabilities extend to producing high-grade AlSi10Mg and potentially CuCrZr suitable for demanding applications like UAV heat sinks. Accessing powders directly from a reputable metal powder supplier China like Met3dp, which controls the production process, provides assurance of quality and consistency, essential for mission-critical aerospace components. You can explore their offerings further via their страница продукта.
Conclusion on Materials:
The choice between AlSi10Mg and CuCrZr for a 3D printed UAV heat sink depends on a careful trade-off analysis:
- Выберите AlSi10Mg когда weight saving is the absolute top priority, and the thermal load is within its dissipation capabilities. It offers a well-rounded, cost-effective solution with good manufacturability.
- Выберите CuCrZr когда maximum thermal performance is required for very high heat loads or extremely compact designs, and the associated weight penalty and higher cost can be justified.
In both cases, leveraging high-quality powders and advanced additive manufacturing processes, like those offered by Met3dp, is key to achieving the desired performance and reliability for these critical UAV components. Sources and related content
Design Considerations for Additively Manufactured UAV Heat Sinks
Additive Manufacturing (AM) liberates designers from many constraints imposed by traditional manufacturing, but it introduces its own set of rules and considerations. To fully exploit the potential of metal 3D printing for creating high-performance, lightweight UAV heat sinks, engineers must embrace Design for Additive Manufacturing (DfAM) principles. DfAM is not merely about making a traditionally designed part printable; it’s about fundamentally rethinking the design process to leverage AM’s unique capabilities for creating optimized geometries that maximize thermal performance, minimize weight, and ensure manufacturability. Ignoring DfAM can lead to suboptimal performance, print failures, excessive post-processing, and higher costs.
Here are critical design considerations specifically tailored for additively manufactured UAV heat sinks:
1. Leverage Simulation-Driven Design (Topology Optimization & CFD):
- Topology Optimization: As introduced earlier, this is a cornerstone of lightweighting and performance optimization in AM. For heat sinks, the process starts by defining the design space (maximum allowable volume), load cases (thermal load from the component, structural loads if any), constraints (mounting points, keep-out zones), and objectives (maximize stiffness, minimize mass, maximize heat dissipation). The software then algorithmically determines the most efficient material distribution.
- Применение: Creates organic, load-path-optimized structures that efficiently transfer heat while using the minimum necessary material. Essential for achieving significant weight savings crucial for UAVs. Requires careful setup of thermal boundary conditions.
- Computational Fluid Dynamics (CFD): Before committing to a print, simulating airflow (natural or forced convection) around and through the proposed heat sink design is crucial. CFD analysis helps:
- Identify areas of stagnant flow or recirculation zones that hinder heat transfer.
- Optimize fin spacing, shape, and orientation for the specific airflow conditions within the UAV (which are often complex and constrained).
- Validate the effectiveness of different lattice structures or internal channel designs.
- Predict pressure drop, especially important for ducted or forced-air cooling systems.
- Применение: Используйте thermal simulation UAV results to iteratively refine the geometry (e.g., adjust fin pitch, incorporate turbulence promoters, reshape channels) until optimal thermal performance is predicted.
2. Design for Print Orientation and Support Minimization:
- Build Orientation: The orientation in which the heat sink is printed significantly impacts print time, support structure requirements, surface finish, and potentially mechanical properties (due to anisotropy).
- Соображения:
- Minimize the amount of support needed, especially on complex fin structures or internal channels where removal is difficult or impossible.
- Orient critical surfaces (e.g., the base contacting the heat source) to achieve the best possible surface finish and dimensional accuracy, often facing upwards or downwards with minimal support contact.
- Consider thermal stresses during printing; orientation can influence distortion.
- Aim for self-supporting angles (typically >45 degrees from the horizontal, depending on the material and machine) wherever possible to avoid supports altogether.
- Соображения:
- Поддерживающие структуры: While minimized, supports are often unavoidable for overhangs and bridges. Design considerations include:
- Ensuring supports are accessible for removal post-printing. Avoid designing features that create trapped volumes needing support.
- Using easily removable support types (e.g., block, cone, tree supports) where appropriate. Software often provides options.
- Understanding that support contact points will leave “witness marks” on the surface, potentially requiring post-processing. Minimize supports on functionally critical or aesthetically important surfaces. Support structure minimization is a key DfAM goal.
3. Incorporate Advanced Geometries:
- Решетчатые структуры: AM excels at creating complex internal lattices. For heat sinks, lattices offer:
- Massive Surface Area Increase: Triply Periodic Minimal Surfaces (TPMS) like Gyroids or Schwarz-P structures provide very high surface area-to-volume ratios, enhancing convective heat transfer.
- Снижение веса: They are inherently porous, significantly reducing weight compared to solid material.
- Tailored Flow: Different lattice types have varying permeability and can be designed to guide airflow or liquid coolant flow.
- Применение: Replace solid sections of the heat sink body or fins with thermally conductive lattices. Requires careful selection of lattice type, cell size, and strut thickness based on thermal/fluid/structural analysis. Lattice structure design is a specialized DfAM skill.
- Optimized Fins: Move beyond simple straight fins. AM allows for:
- Curved or Airfoil-Shaped Fins: Optimize aerodynamic performance and reduce pressure drop in forced convection.
- Variable Fin Density/Thickness: Thicker fins near the heat source, thinner fins further away; denser fin packing where airflow is strongest.
- Pin Fins and Other Complex Shapes: Explore various geometries proven to enhance turbulence and heat transfer.
- Конформные охлаждающие каналы: For liquid cooling or integration with heat pipes, AM can create complex, conformal channels that follow the shape of the heat source or fit within constrained spaces, impossible with drilling or machining.
4. Wall Thickness and Feature Size:
- Minimum Wall Thickness: There’s a limit to how thin features can be reliably printed. This depends on the AM process (L-PBF typically allows finer features than SEBM), material, and machine calibration. Typical minimum printable wall thickness might be 0.3−0.5mm. Fins need sufficient thickness for structural integrity and thermal conduction.
- Aspect Ratio: Very tall, thin features (like fins) can be prone to distortion or damage during printing or handling. Design fins with a reasonable aspect ratio (height vs. thickness).
- Small Holes/Channels: Minimum printable hole diameter is also limited. Very small channels may trap powder that is difficult to remove.
5. Stress Reduction Features:
- Fillets and Radii: Sharp internal corners are stress concentrators, both mechanically and thermally (during printing). Generous fillets and radii should be added at junctions (e.g., where fins meet the base) to distribute stress, reduce the risk of cracking during printing or in service, and improve fatigue life.
- Thermal Stress Management: Design choices can influence thermal stress build-up during printing. Avoid large, flat sections parallel to the build plate where possible. Consider features that allow for some compliance. Build process simulation tools can help predict and mitigate high-stress areas through design modifications or optimized support strategies.
6. Design for Post-Processing:
- Support Access: Ensure clear line-of-sight and tool access for support removal, especially for internal features.
- Machining Allowances: If critical surfaces require high precision or specific flatness/smoothness (e.g., the base contacting the CPU/GPU), add extra “machining stock” material (0.5−1.0mm typically) to the design in those areas, which will be precisely removed via CNC machining later.
- Inspection Access: Ensure features allow for dimensional inspection and potentially Non-Destructive Testing (NDT) if required for quality assurance.
DfAM Guidelines Summary for UAV Heat Sinks:
DfAM Principle | Application / Consideration for UAV Heat Sinks | Выгода |
---|---|---|
Simulation-Driven Design | Use Topology Optimization for lightweighting; Use CFD for airflow/thermal analysis | Optimized performance (thermal & weight), Reduced iterations |
Orientation Strategy | Minimize supports, optimize surface finish on critical faces, manage stress | Reduced post-processing, Improved quality, Higher success rate |
Support Minimization | Design self-supporting angles (>45°), strategically place unavoidable supports | Less material waste, Faster post-processing, Fewer surface defects |
Leverage Complexity | Use lattices (TPMS), optimized fin shapes, conformal channels | Enhanced thermal performance, Weight reduction, Compact design |
Feature Size Limits | Adhere to minimum wall thickness, hole size; Manage aspect ratios | Printability, Structural integrity, Powder removal feasibility |
Stress Reduction | Add fillets/radii at junctions, consider thermal compliance | Reduced cracking risk (print & service), Improved durability |
Design for Post-Pro | Ensure access for support removal, Add machining stock where needed | Feasible finishing, Achievement of tight tolerances |
Export to Sheets
By integrating these DfAM heat sink considerations early in the design phase, engineers can fully harness the power of metal additive manufacturing to create truly optimized thermal management solutions for demanding UAV applications, pushing the boundaries of performance and efficiency. Collaborating with an experienced AM service provider like Met3dp, who understands these principles and can offer design guidance, is highly recommended.
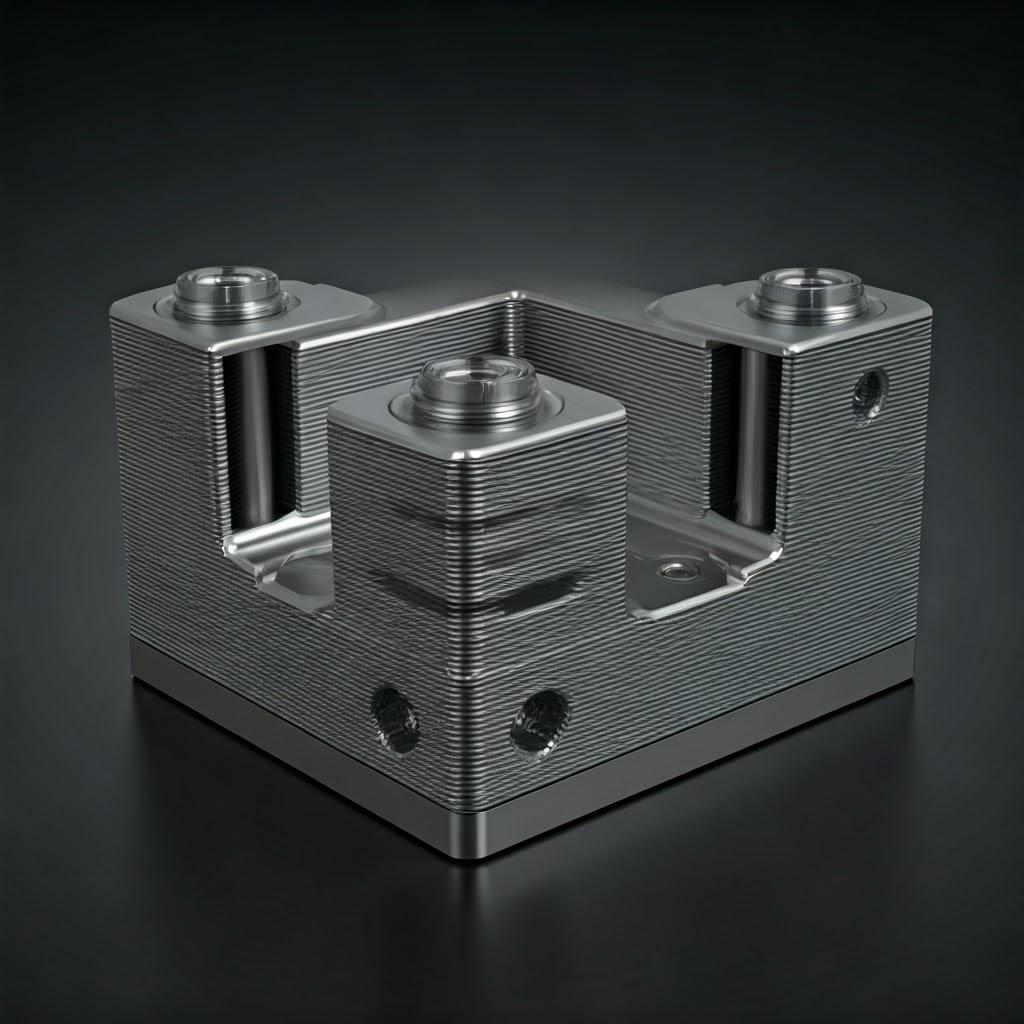
Achievable Tolerance, Surface Finish, and Dimensional Accuracy
While metal additive manufacturing unlocks unprecedented design freedom, it’s crucial for engineers and procurement managers to understand the levels of precision, surface quality, and dimensional accuracy typically achievable with these processes. These factors directly impact the heat sink’s assembly fit, its thermal performance (especially contact resistance), and potentially its aerodynamic properties if exposed to external airflow. The achievable specifications depend on several factors, including the chosen AM technology (e.g., L-PBF vs. SEBM), the material being printed, the machine’s calibration and condition, the part’s geometry and orientation, and the post-processing steps applied.
Dimensional Accuracy and Tolerances:
- General Tolerances: Metal AM processes like Laser Powder Bed Fusion (L-PBF) and Selective Electron Beam Melting (SEBM) offer good dimensional accuracy, but typically not as tight as precision CNC machining out-of-the-box. General achievable tolerances often fall within:
- ISO 2768-m (medium) or sometimes ISO 2768-f (fine) for smaller dimensions.
- A common rule of thumb for L-PBF is around ±0.1mm to ±0.2mm for the first 25mm, plus an additional ±0.005mm to ±0.01mm for each subsequent mm, although this varies significantly.
- SEBM, often operating at higher temperatures with less residual stress in some materials, can sometimes offer slightly different accuracy profiles, but generally in a similar range for many applications. Met3dp’s expertise spans both L-PBF optimized powders and SEBM-принтеры, offering flexibility depending on application needs. You can learn more about different способы печати and their characteristics.
- Factors Influencing Accuracy:
- Калибровка машины: Regular, precise calibration of the laser/electron beam scanning system is critical.
- Thermal Effects: Shrinkage during cooling, warping due to thermal gradients, and residual stress can all affect final dimensions. Build process simulation can help predict and compensate for some distortion.
- Part Geometry & Size: Large or complex parts are generally harder to hold tight tolerances on due to accumulated thermal effects.
- Orientation: Part placement and orientation on the build plate influence thermal history and support needs, affecting accuracy.
- Качество порошка: Consistent particle size and morphology contribute to stable melting and solidification.
- Толщина слоя: Thinner layers generally allow for finer detail and potentially better accuracy in the build direction (Z-axis).
- Achieving Tighter Tolerances: For critical dimensions, such as mounting holes, mating surfaces, or the base of the heat sink that contacts the electronic component, standard AM tolerances may not be sufficient. In these cases, the design should incorporate extra material (machining stock), and Обработка на станках с ЧПУ is employed as a post-processing step to achieve tolerances down to ±0.01mm or even tighter, meeting typical aerospace quality standards.
Обработка поверхности (шероховатость):
- As-Built Surface Roughness: The nature of layer-by-layer manufacturing results in surfaces that are inherently rougher than machined surfaces. The roughness depends heavily on:
- Surface Orientation: Upward-facing surfaces (looking up away from the build plate) tend to be smoother than downward-facing surfaces (which require support structures and are affected by gravity during melting) and vertical walls (which show layer lines).
- Толщина слоя: Thinner layers generally result in a smoother finish, particularly on sloped surfaces.
- Параметры процесса: Laser/beam power, scan speed, and powder characteristics influence melt pool dynamics and surface texture.
- Процесс AM: L-PBF typically produces finer surface finishes than SEBM as-built, due to smaller powder particle sizes and lower energy input per layer.
- Typical Ra Values (As-Built):
- L-PBF: Ra values often range from 6μm to 20μm (240μin to 800μin), depending heavily on orientation and parameters.
- SEBM: Ra values are generally rougher, potentially 20μm to 50μm (800μin to 2000μin) or more.
- Impact on Heat Sinks:
- Thermal Contact Resistance: A rough surface on the heat sink base increases thermal contact resistance between the heat sink and the heat-generating component, reducing cooling efficiency. This is often the most critical aspect of surface finish for a heat sink.
- Airflow: Rough surfaces on fins can slightly increase turbulence, which might marginally enhance heat transfer in some convective scenarios but can also increase pressure drop in ducted systems.
- Post-Processing for Improved Finish: Various secondary processes can significantly improve the surface finish additive manufacturing parts:
- Abrasive Blasting (Sand/Bead Blasting): Creates a uniform, matte finish, removing loose powder particles. Ra values might improve slightly or become more uniform, perhaps in the 5−15μm range.
- Tumbling/Vibratory Finishing: Uses media to smooth surfaces and edges, effective for batches of smaller parts. Can achieve Ra values down to 1−5μm.
- Micro-Machining/Polishing: Can achieve very smooth finishes (Ra < 0.8μm or even < 0.1μm) on specific surfaces, essential for minimizing thermal contact resistance at the base.
- Electropolishing: An electrochemical process that removes material, smoothing surfaces and potentially achieving very low Ra values, especially on certain alloys like stainless steels (less common for Al or Cu alloys).
Summary Table: Tolerances & Surface Finish
Параметр | As-Built (Typical L-PBF) | As-Built (Typical SEBM) | Post-Processed (Machined/Polished) | Единица | Примечания |
---|---|---|---|---|---|
General Tolerance | ±0.1−0.2 (initial) + slope | ±0.2−0.4 (initial) + slope | ±0.01−0.05 (or tighter) | mm | Highly dependent on size, geometry, material. Requires machining for high precision. |
Шероховатость поверхности (Ra) | 6−20 | 20−50+ | <0.1−5 (method dependent) | мкм | Varies greatly with orientation. Requires finishing for smooth surfaces. |
Export to Sheets
Conclusion on Precision:
Engineers designing 3D printed UAV heat sinks must be aware of the inherent metal 3D printing tolerances and surface characteristics. While AM provides geometric freedom, achieving high precision and smooth surfaces, especially for critical interfaces like the thermal contact area, typically requires incorporating secondary постобработка steps like CNC machining and polishing. Partnering with a knowledgeable metal 3D printing service provider like Met3dp, equipped with precise machinery and robust quality control processes, is essential to ensure the final heat sink meets the required dimensional and surface finish specifications for optimal assembly and thermal performance in demanding UAV applications.
Essential Post-Processing Requirements for 3D Printed Heat Sinks
Producing a metal part via additive manufacturing is often only the midpoint of the manufacturing journey. The “as-built” part straight out of the printer rarely possesses the final desired properties, tolerances, or surface finish required for demanding applications like UAV heat sinks. A series of carefully planned and executed post-processing steps are almost always necessary to transform the printed component into a functional, reliable end-use part. Understanding these requirements is crucial for project planning, cost estimation, and ensuring the final heat sink performs as intended.
Key post-processing steps for 3D printed metal heat sinks (AlSi10Mg and CuCrZr) include:
1. Stress Relief / Heat Treatment:
- Why it’s needed: The rapid heating and cooling cycles inherent in powder bed fusion processes (especially L-PBF) induce significant residual stresses within the printed part. These stresses can cause distortion during or after printing (especially once removed from the build plate), reduce fatigue life, and negatively impact mechanical properties. Additionally, the as-built microstructure may not be optimal for thermal conductivity or strength.
- Процесс:
- Снятие стресса: Typically performed while the part is still attached to the build plate (for L-PBF) in an inert atmosphere furnace. Involves heating the part to a specific temperature below the aging or annealing temperature, holding it for a period, and then slowly cooling it. This allows internal stresses to relax without significantly altering the microstructure.
- Heat Treatment (Solutionizing & Aging): Required to achieve optimal mechanical properties and often improves thermal conductivity.
- AlSi10Mg: Often undergoes a T6 heat treatment. This involves solutionizing at a high temperature (e.g., ~530∘C) to dissolve precipitates, quenching rapidly, and then artificially aging at a lower temperature (e.g., ~160∘C) to form fine precipitates that significantly increase strength and hardness. The T6 cycle also helps homogenize the microstructure, improving thermal conductivity compared to the as-built state. Heat treatment AlSi10Mg is standard practice for structural or performance-critical parts.
- CuCrZr: Typically requires solution annealing followed by aging (precipitation hardening) at temperatures around 450−500∘C to form Cr and Zr precipitates, which provide high strength while largely maintaining the copper matrix’s high thermal and electrical conductivity.
- Соображения: Heat treatment parameters (temperature, time, atmosphere, cooling rates) must be precisely controlled and tailored to the specific alloy and desired final properties. Distortion can sometimes occur during heat treatment itself, which needs consideration during the design (e.g., adding fixtures or allowances).
2. Part Removal from Build Plate:
- Why it’s needed: Parts are printed on a thick metal build plate. They need to be separated for subsequent processing.
- Процесс: Commonly done using Wire Electrical Discharge Machining (Wire EDM) or a bandsaw. Wire EDM provides a cleaner, more precise cut with minimal mechanical stress but is slower. Bandsawing is faster but less precise and can induce some stress.
- Соображения: The removal process needs to be planned to avoid damaging the part. For complex or delicate heat sinks, wire EDM is often preferred near the part interface.
3. Support Structure Removal:
- Why it’s needed: Support structures, used to anchor the part and support overhanging features during printing, must be removed.
- Процесс: This can be one of the most labor-intensive steps. Methods include:
- Удаление вручную: Breaking or cutting supports away using hand tools (pliers, cutters, grinders). Requires skill to avoid damaging the part surface.
- CNC Machining: Milling or grinding away support structures, especially for large or difficult-to-access supports. More controlled but adds cost.
- Wire EDM: Can sometimes be used for precise removal of intricate supports.
- Соображения: Access for tools is a key DfAM consideration. Support removal invariably leaves witness marks or rougher areas on the part surface where the supports were attached. These areas often require further finishing. Support removal metal AM complexity heavily influences overall cost.
4. CNC Machining:
- Why it’s needed: To achieve tight tolerances, specific flatness/parallelism, or smooth surface finishes on critical features that cannot be met by the AM process alone.
- Процесс: Using milling machines, lathes, or grinders to precisely remove material from specific areas. Common applications for heat sinks include:
- Machining the base flat and smooth for optimal thermal contact with the electronic component.
- Machining mounting holes to precise diameters and locations.
- Creating threaded holes.
- Machining sealing surfaces or interfaces.
- Соображения: Requires accurate fixturing of the complex AM part. Design must include necessary machining stock. CNC machining 3D prints adds cost and lead time but is often essential for functionality.
5. Surface Finishing:
- Why it’s needed: To improve surface quality (smoothness, uniformity), remove loose powder, clean witness marks, or prepare for coatings.
- Процесс:
- Abrasive Blasting (Bead/Sand Blasting): Most common method for achieving a uniform matte finish and cleaning surfaces. Different media (glass beads, aluminum oxide) produce different textures.
- Tumbling/Vibratory Finishing: Smooths surfaces and deburrs edges using abrasive media in a tumbling barrel or vibratory bowl. Good for batches but less controlled for specific surface requirements.
- Manual Grinding/Polishing: Used locally to smooth specific areas, especially support witness marks or achieve mirror finishes on contact surfaces.
- Electropolishing/Chemical Polishing: Can achieve very smooth surfaces but depends heavily on the alloy and part geometry.
- Соображения: Choice depends on the required final finish (aesthetic or functional) and cost. Aggressive methods can remove material and affect dimensions.
6. Cleaning and Inspection:
- Why it’s needed: To remove residual powder (especially from internal channels or complex features), machining fluids, or blasting media. To verify dimensional accuracy, surface finish, and integrity.
- Процесс:
- Cleaning: Ultrasonic cleaning baths, solvent wiping, compressed air blow-off. Critical for ensuring no loose powder remains, which could cause issues later.
- Inspection: Dimensional checks (CMM, scanners), surface roughness measurements, visual inspection, potentially NDT (e.g., CT scanning for internal defects/porosity, FPI for surface cracks) depending on criticality.
- Соображения: Thorough cleaning is vital. Inspection level depends on application requirements (e.g., aerospace components require rigorous NDT).
7. Coating (Optional):
- Why it’s needed: To enhance corrosion resistance, improve wear resistance, alter surface emissivity, or provide electrical insulation.
- Процесс:
- Anodizing (for Aluminum): Creates a hard, corrosion-resistant oxide layer. Can be dyed for color. May slightly impact thermal performance.
- Plating (e.g., Nickel, Gold): Can improve conductivity, solderability, or corrosion resistance.
- Painting/Powder Coating: For environmental protection or aesthetics.
- Соображения: Coating adds cost and requires surface preparation. Ensure the coating is compatible with the operating environment and thermal requirements.
Конкретный post-processing additive manufacturing workflow will vary based on the heat sink’s design complexity, material choice (AlSi10Mg vs. CuCrZr require different heat treatments), and application requirements. It’s essential to factor these steps into the overall production plan and budget. Working with a vertically integrated service provider that offers both printing and comprehensive post-processing capabilities can streamline the process and ensure quality control throughout.
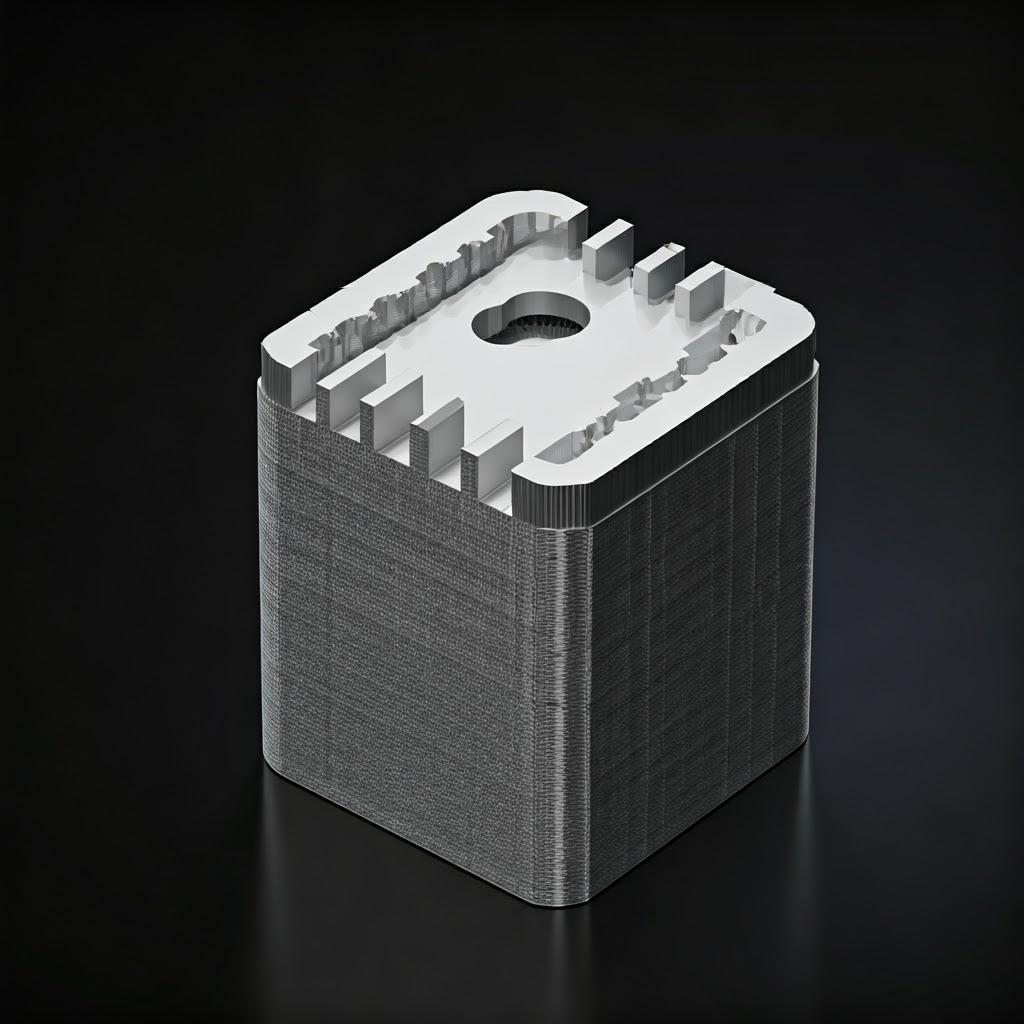
Common Challenges in 3D Printing UAV Heat Sinks and Mitigation Strategies
While metal additive manufacturing offers remarkable advantages for creating complex UAV heat sinks, the process is not without its challenges. Successfully printing intricate geometries with demanding materials like AlSi10Mg and especially CuCrZr requires careful control, process expertise, and often iterative refinement. Understanding these potential hurdles and their mitigation strategies is key for engineers and procurement managers to set realistic expectations and partner effectively with AM service providers.
1. Warping and Distortion:
- Вызов: The intense localized heating from the laser or electron beam followed by rapid cooling creates significant thermal gradients within the part and between the part and the build plate. This induces internal stresses that can cause the part (especially large, flat sections or thin, tall features like fins) to warp, distort, or even detach from the build plate during printing.
- Mitigation Strategies:
- Моделирование процесса сборки: Specialized software can predict thermal gradients and resulting stresses/distortions based on the part geometry, orientation, and material properties. This allows for adjustments before printing.
- Optimized Orientation: Orienting the part to minimize large flat areas parallel to the build plate and reduce internal stresses.
- Effective Support Structures: Well-designed supports anchor the part securely to the build plate, resist warping forces, and help conduct heat away. Support strategy is critical.
- Оптимизация параметров процесса: Fine-tuning laser/beam power, scan speed, layer thickness, and scan strategy (e.g., using an island scanning pattern) can minimize residual stress accumulation.
- Build Plate Heating: Pre-heating the build plate (common in L-PBF, inherent in SEBM operating in vacuum at high temp) reduces thermal gradients between the part and the plate.
- Design Modifications: Adding sacrificial ribs or features to stiffen prone areas during printing, which are removed later. 3D printing warping prevention is a major focus of process development.
2. Support Structure Design and Removal:
- Вызов: Heat sinks often feature delicate fins, overhangs, and potentially internal channels that require support structures. Designing supports that are effective during the build but also easily and cleanly removable without damaging the part is difficult. Access for removal tools can be limited in complex geometries, and removal can be time-consuming and leave undesirable witness marks. Internal supports are often impossible to remove.
- Mitigation Strategies:
- DfAM Principles: Design for minimum support (using self-supporting angles, optimizing orientation). Avoid internal features requiring non-removable supports unless powder can be fully evacuated.
- Advanced Support Generation Software: Use software tools that offer optimized support types (e.g., tree supports, thin block supports with small contact points) designed for easier removal.
- Process Parameter Tuning for Supports: Using different print parameters for support structures to make them weaker or more brittle than the main part.
- Post-Processing Planning: Select appropriate removal techniques (manual, machining, EDM) based on access and required surface finish. Factor removal time into cost/lead time. Address support structure challenges during the design phase.
3. Residual Stress Management:
- Вызов: Even if catastrophic warping doesn’t occur, significant residual stress can remain locked within the as-built part. This can lead to dimensional instability over time, reduced fatigue life, and increased susceptibility to cracking, especially under operational loads or vibrations common in UAVs.
- Mitigation Strategies:
- Stress Relief Heat Treatment: The primary method. Performing a proper stress relief cycle (often while still on the build plate) significantly reduces internal stresses.
- Parameter & Scan Strategy Optimization: As mentioned for warping, careful control over the melting process helps minimize stress build-up.
- Моделирование процесса сборки: Predict high-stress areas and potentially modify the design or support strategy. Understanding and managing residual stress metal AM is critical for part performance.
4. Porosity Control:
- Вызов: Porosity (small voids within the printed material) can compromise mechanical properties (especially fatigue strength) and potentially reduce the bulk thermal conductivity of the heat sink. Pores can arise from two main sources:
- Gas Porosity: Trapped gas (often argon used as a shield gas in L-PBF, or dissolved gases in the powder) forming bubbles that get locked in during solidification.
- Lack-of-Fusion Porosity: Insufficient melting and fusion between adjacent melt tracks or layers, leaving voids. Often caused by incorrect parameters (too fast scan speed, too low power) or powder issues.
- Mitigation Strategies:
- High-Quality Powder: Using powder with high sphericity, good flowability, controlled particle size distribution, and low internal gas content is crucial. Gas atomized metal powder production methods, like those employed by Met3dp, are designed to minimize gas entrapment and ensure consistent powder characteristics.
- Optimized Process Parameters: Developing and using validated parameter sets (power, speed, hatch spacing, layer thickness) that ensure complete melting and fusion for the specific material and machine.
- Proper Machine Maintenance & Calibration: Ensuring consistent energy delivery and powder layering.
- Горячее изостатическое прессование (HIP): A post-processing step involving high temperature and high pressure (using an inert gas like Argon). HIP can effectively close internal pores (both gas and lack-of-fusion), significantly improving density and mechanical properties. Often required for critical aerospace components but adds significant cost. Porosity control additive manufacturing relies on a combination of powder quality, process control, and potentially HIP.
5. Ensuring Thermal Contact Integrity:
- Вызов: The primary function of the heat sink base is to efficiently draw heat from the electronic component. As-printed surface roughness can create microscopic air gaps at the interface, significantly increasing thermal contact resistance and hindering performance. Achieving a consistently flat and smooth contact surface can be difficult directly from the printer.
- Mitigation Strategies:
- Post-Process Machining/Lapping/Polishing: The most reliable method is to machine or lap the critical contact surface to achieve the required flatness and smoothness (low Ra value).
- Thermal Interface Materials (TIMs): Using appropriate TIMs (thermal paste, pads, or phase change materials) between the component and the heat sink helps fill microscopic gaps and improve heat transfer, but the underlying surface quality still matters.
- Design for Machining: Ensure the design includes machining stock on the contact surface.
6. Material-Specific Challenges (e.g., CuCrZr):
- Вызов: Materials like copper alloys (CuCrZr) are inherently difficult to process with standard infrared lasers used in many L-PBF systems due to their high reflectivity and thermal conductivity. This can lead to unstable melt pools, increased porosity, and poor surface finish.
- Mitigation Strategies:
- Specialized Equipment: Using L-PBF machines equipped with higher power lasers or, more effectively, green lasers (which have much better absorption by copper).
- Expert Parameter Development: Requires significant expertise to develop stable and reliable printing parameters for these challenging materials.
- Alternative Processes: Exploring processes like SEBM or Binder Jetting (followed by sintering) might be alternatives, although L-PBF is currently more common for intricate heat sinks.
Overcoming these challenges requires a combination of robust DfAM practices, careful material selection and quality control, advanced processing equipment, optimized parameters, appropriate post-processing, and deep process expertise. Partnering with an experienced additive manufacturing service provider like Met3dp, which possesses strong capabilities in materials science (especially with their advanced powder making system), process control across different способы печати, and post-processing, significantly mitigates these risks and increases the likelihood of successfully producing high-performance, reliable UAV heat sinks.
How to Choose the Right Metal 3D Printing Service Provider for UAV Components
Selecting the right manufacturing partner is as critical as the design itself when implementing metal additive manufacturing for mission-critical components like UAV heat sinks. The quality, reliability, and performance of the final part depend heavily on the service provider’s capabilities, expertise, and quality control processes. For engineers and procurement managers navigating the landscape of поставщики аддитивного производства, making an informed choice requires evaluating potential partners against a stringent set of criteria, especially when dealing with aerospace applications.
Here’s a comprehensive guide on what to look for when choosing a metal 3D printing service provider for UAV components:
1. Proven Technical Expertise and Experience:
- Application-Specific Knowledge: Does the provider have demonstrable experience with thermal management applications, particularly heat sinks? Do they understand the unique challenges of UAV components (weight, vibration, environmental factors)?
- Materials Expertise: Look for deep knowledge of the specific alloys you intend to use (AlSi10Mg, CuCrZr). This includes understanding their metallurgy, optimal processing parameters, required heat treatments, and performance characteristics. Providers who manufacture their own powders, like Met3dp, often possess deeper material science insights.
- DfAM Support: Can they offer Design for Additive Manufacturing guidance? An ideal partner collaborates with your design team to optimize the heat sink for printability, performance, and cost-effectiveness, leveraging techniques like topology optimization and lattice structures.
- Problem-Solving Skills: Metal AM can present unexpected challenges. An experienced provider will have the troubleshooting skills, developed through years of practice, to overcome issues related to printability, distortion, or quality.
2. Advanced Equipment and Technology:
- Relevant AM Processes: Do they operate the appropriate technology (primarily L-PBF for intricate heat sinks, possibly SEBM for specific materials/applications)? Met3dp’s capabilities include both L-PBF-optimized powders and SEBM-принтеры, offering versatility.
- Machine Quality and Features: Are their machines well-maintained and calibrated? Do they possess specific features beneficial for your project (e.g., sufficient build volume for your part size, high-power or green lasers for copper alloys, inert atmosphere control, in-situ monitoring)? Met3dp emphasizes its printers’ industry-leading print volume, accuracy, and reliability.
- Capacity: Can they meet your volume requirements, whether for prototypes or low-to-medium series production (wholesale 3D printed parts)? Assess their machine park size and utilization.
3. Material Quality, Range, and Traceability:
- Powder Quality Control: This is paramount. Inquire about their powder sourcing and quality control procedures. Do they test incoming powder batches for chemical composition, particle size distribution (PSD), morphology, and flowability? Providers like Met3dp, employing advanced powder making systems (Gas Atomization, PREP) for in-house production, offer greater control and consistency.
- Портфель материалов: Do they offer the specific alloys you need (AlSi10Mg, CuCrZr) validated on their machines? A broader portfolio indicates wider expertise. Met3dp manufactures a diverse range including titanium alloys, superalloys, and custom compositions alongside standards like AlSi10Mg.
- Traceability: For aerospace components, full material traceability from powder batch to final part is often mandatory. Ensure the provider has systems in place to track material history and provide necessary certifications.
4. Robust Quality Management System (QMS) and Certifications:
- Сертификаты: AS9100 certification is the gold standard for aerospace suppliers, indicating a rigorous QMS tailored to the industry’s safety and reliability demands. ISO 9001 is a fundamental requirement. Ask for proof of current certifications.
- Управление процессом: Do they have documented procedures for every step, from order entry and file preparation to printing, post-processing, and inspection? Consistency is key.
- Inspection Capabilities: What metrology and inspection tools do they possess? This should include Coordinate Measuring Machines (CMMs) for dimensional verification, surface profilometers, and potentially Non-Destructive Testing (NDT) methods like CT scanning (for internal defects) or Fluorescent Penetrant Inspection (FPI) for surface flaws, especially if required by your specifications. Quality control metal AM must be rigorous.
5. Comprehensive Post-Processing Capabilities:
- In-House Services: Does the provider offer the necessary post-processing steps (stress relief/heat treatment, support removal, CNC machining, surface finishing, cleaning) in-house? A vertically integrated provider often offers better control, streamlined workflow, and potentially faster lead times compared to managing multiple subcontractors.
- Expertise in Finishing: Do they have experience finishing complex AM parts, including support removal from intricate areas and achieving tight tolerances on machined surfaces?
6. Communication, Lead Times, and Logistics:
- Responsiveness: How quickly and clearly do they respond to inquiries and technical questions? Good communication is vital throughout the project.
- Quoted Lead Times: Are their lead times competitive and realistic for prototyping and production? Understand the breakdown of lead time estimation AM.
- Logistics: Consider the provider’s location and shipping capabilities, especially for international suppliers. Met3dp, headquartered in Qingdao, China, serves a global market and understands international logistics.
7. Reputation, Case Studies, and References:
- Track Record: Look for evidence of successful projects, particularly in aerospace, defense, or demanding industrial sectors. Ask for relevant case studies or customer references.
- Company Stability and Vision: Assess the provider’s history, stability, and commitment to advancing AM technology. Learning about Met3dp reveals decades of collective expertise and a focus on comprehensive solutions.
8. Cost vs. Overall Value:
- Transparent Pricing: Ensure quotes are detailed and clearly break down costs (material, print time, labor, post-processing).
- Value Proposition: Don’t choose based solely on the lowest price. Consider the provider’s expertise, quality, reliability, and support – factors that contribute to the overall value and reduce risks associated with producing critical UAV components. Choosing AM partner is a strategic decision.
Evaluation Checklist Summary:
Критерии | Основные вопросы | Why It Matters for UAV Heat Sinks |
---|---|---|
Техническая экспертиза | Experience with thermal/UAV apps? Material knowledge? DfAM support? | Ensures optimal design, print success, functional performance |
Equipment & Technology | Right process (L-PBF/SEBM)? Machine quality/features (laser type, volume)? Capacity? | Determines feasibility, part quality, production capability |
Material Control | Powder source & QC? Validated alloys (AlSi10Mg, CuCrZr)? Traceability? | Guarantees material properties, consistency, compliance |
Quality System (QMS) | AS9100 / ISO 9001 certified? Documented process control? Inspection tools (CMM, NDT)? | Ensures reliability, safety, repeatability, meets aerospace standards |
Постобработка | In-house capabilities (heat treat, CNC, finishing)? Expertise? | Streamlines production, ensures final specs are met |
Service & Logistics | Communication responsiveness? Realistic lead times? Shipping expertise? | Facilitates smooth project execution, on-time delivery |
Reputation & References | Proven track record (aerospace)? Case studies? | Builds confidence in capability and reliability |
Cost vs. Value | Transparent pricing? Balance of cost vs. quality, expertise, risk reduction? | Ensures best long-term outcome beyond just initial price |
Export to Sheets
By systematically evaluating potential suppliers against these criteria, you can select a metal 3D printing service provider that is not just a vendor but a true strategic partner, capable of reliably delivering high-performance, flight-ready heat sinks for your UAV applications.
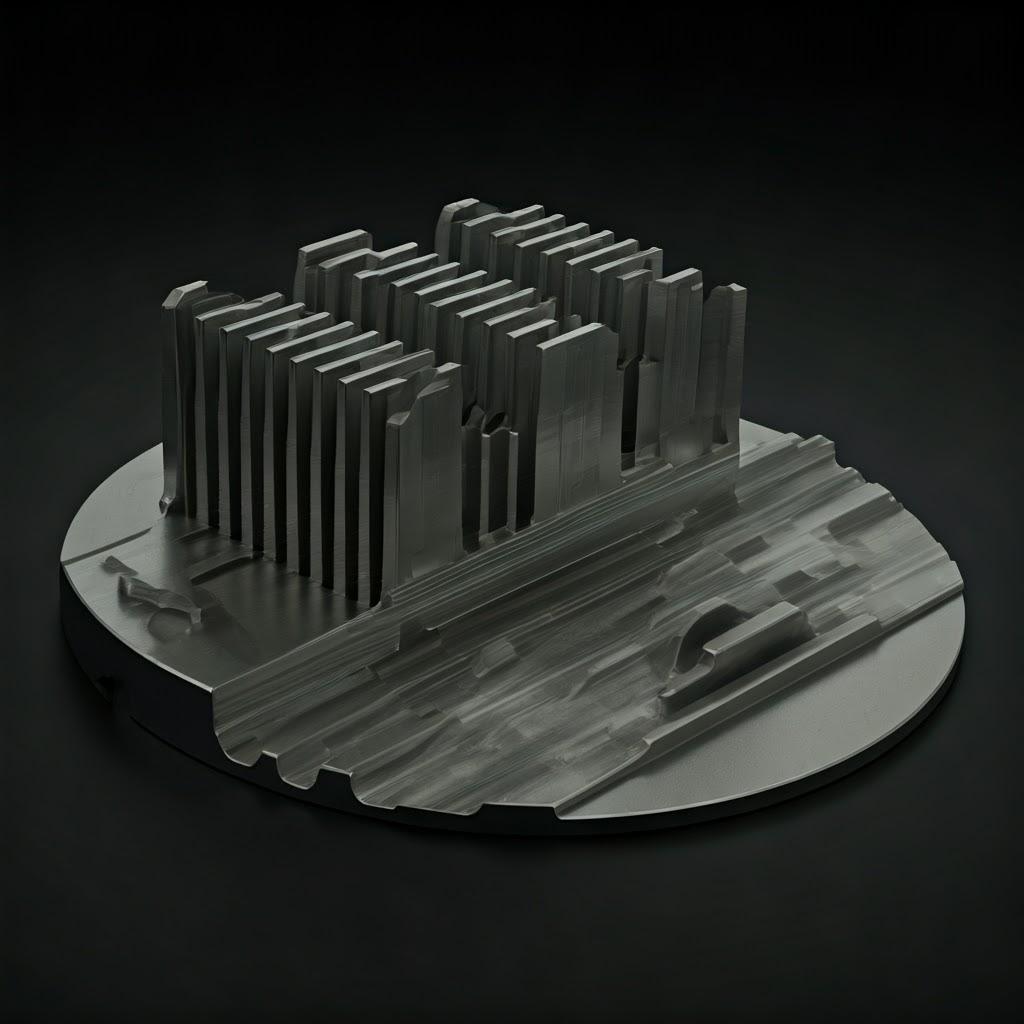
Understanding Cost Factors and Lead Times for Production
One of the primary considerations for adopting any manufacturing technology is understanding its cost structure and typical production timelines. Metal additive manufacturing, while offering significant performance benefits, involves different cost drivers compared to traditional methods like CNC machining or casting. A clear understanding of these factors helps in budgeting, design optimization (designing for cost), and managing project schedules effectively.
Key Cost Factors in Metal 3D Printing:
- Стоимость материала:
- Powder Price: The cost per kilogram of the metal powder is a direct input. Prices vary significantly by alloy:
- AlSi10Mg: Relatively common and cost-effective among AM metals.
- CuCrZr: Significantly more expensive than aluminum alloys due to raw material costs and specialized atomization requirements.
- Other alloys (e.g., Titanium, Nickel superalloys): Can be even more expensive.
- Material Usage: The total volume of the part, including any necessary support structures, determines the amount of powder consumed. Topology optimization and DfAM play a crucial role here in minimizing material use while maintaining performance. Efficient nesting of multiple parts on a build plate can also reduce relative material cost per part.
- Переработка порошка: The ability to safely recycle unfused powder impacts overall material efficiency and cost. Service providers should have robust powder handling and recycling protocols.
- Powder Price: The cost per kilogram of the metal powder is a direct input. Prices vary significantly by alloy:
- AM Machine Time:
- Hourly Rate: Metal AM machines represent significant capital investment and have operational costs (power, inert gas, maintenance). Service providers typically charge an hourly rate for machine usage.
- Время сборки: This is often the largest cost driver, especially for complex or large parts. Build time is influenced by:
- Part Volume: The total volume of material being fused.
- Part Height (Z-height): Each layer adds time; taller parts take longer.
- Толщина слоя: Thinner layers improve resolution but significantly increase the number of layers and thus print time.
- Scan Strategy & Parameters: Optimized parameters balance speed and quality.
- Machine Technology: Different machines/processes have varying build rates.
- Nesting Efficiency: Printing multiple parts simultaneously reduces the effective machine time per part by sharing setup and recoating time.
- Расходы на оплату труда:
- Pre-Processing: CAD file preparation, build simulation, slicing, build layout planning, and machine setup require skilled technician/engineer time.
- Постобработка: This can be a significant labor component, including:
- Part Removal from the build plate.
- Демонтаж опорной конструкции (often manual and intricate).
- Basic Finishing (e.g., bead blasting).
- Инспекция (visual, basic dimensional checks).
- Post-Processing Costs (Beyond Basic Labor):
- Термообработка: Furnace time, energy consumption, controlled atmosphere costs.
- CNC Machining: Machine time (milling, turning, EDM), tooling, programming, and skilled machinist labor required for achieving tight tolerances or specific features.
- Advanced Surface Finishing: Costs associated with specialized processes like polishing, tumbling, electropolishing, or coating.
- Inspection & QA: Costs for advanced metrology (CMM programming/operation), NDT (equipment, certified inspectors), and detailed documentation/certification packages (e.g., for AS9100).
- Сложность дизайна:
- While AM handles complexity well, extremely intricate designs might require more extensive support structures (increasing print time, material use, and removal labor) or more challenging post-processing steps, indirectly increasing costs. However, complexity that leads to part consolidation can reduce overall system cost.
- Order Volume (Economies of Scale):
- Setup Amortization: Initial setup costs (file prep, machine setup) are amortized over the number of parts in a batch. Higher volumes lead to lower per-part setup costs.
- Nesting: Printing multiple parts in a single build significantly improves machine time efficiency.
- Dedicated Resources: For larger volume orders (wholesale 3D printed parts pricing), providers may optimize workflows or dedicate resources, potentially lowering costs.
- Powder Utilization: Larger runs can improve powder recycling efficiency.
Typical Lead Times:
Lead time is the total time from order placement to receiving the finished parts. It comprises several stages:
- Order Processing & File Preparation: (Hours to Days) Includes quote finalization, technical review, file checks/repairs, build layout planning, and slicing.
- Machine Queue Time: (Days to Weeks) Depending on the service provider’s backlog and machine availability.
- Время печати: (Hours to Days) As discussed under cost factors, dependent on part size, complexity, and quantity. A build might run continuously for several days.
- Cooling & Depowdering: (Hours) Allowing the build chamber and parts to cool before safely removing loose powder.
- Постобработка: (Days to Weeks) This often takes longer than the printing itself, involving potentially multiple steps:
- Stress Relief/Heat Treatment (can take 1-3 days including furnace cycles).
- Part Removal & Support Removal (highly variable based on complexity).
- Machining (depends on complexity and machine shop scheduling).
- Finishing & Cleaning.
- Inspection & QA.
- Перевозки: (Days) Depending on location and shipping method.
Overall Lead Time: For prototypes or small batches of complex metal AM parts like UAV heat sinks, typical lead times can range from 1 to 4 weeks. Larger volumes or parts requiring extensive post-processing or rigorous QA might extend this further. Lead time estimation AM should always account for all steps, not just the print time.
Cost vs. Lead Time Trade-offs:
- Expedited services are often available at a premium cost (reducing queue time, potentially dedicating resources).
- Design choices impact both cost and lead time (e.g., minimizing supports reduces post-processing time).
- Choosing standard layer thicknesses might be faster (and cheaper) than using ultra-fine layers for slightly better resolution.
Understanding these metal 3D printing cost analysis factors and lead time components allows for better planning, cost management, and communication with your additive manufacturing pricing factors from your service provider.
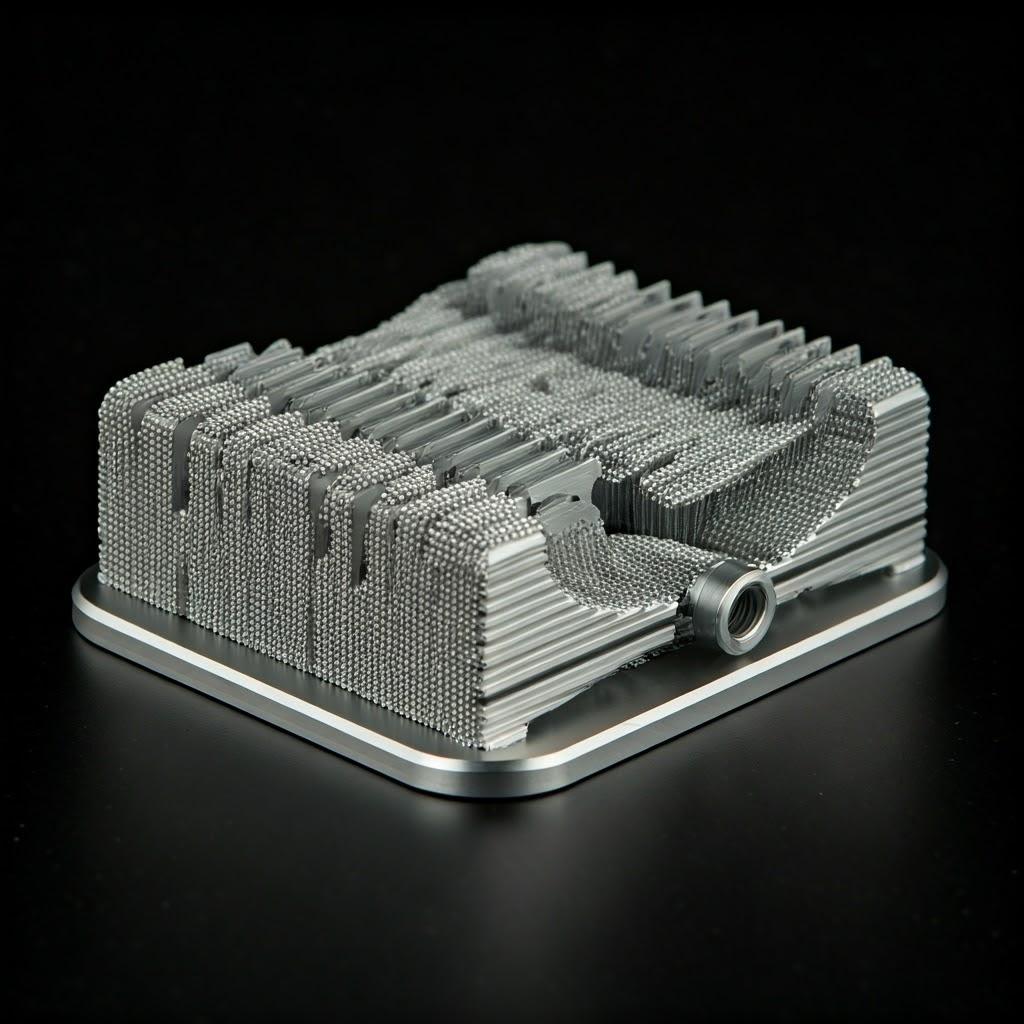
Frequently Asked Questions (FAQ) about 3D Printed UAV Heat Sinks
Here are answers to some common questions regarding the use of metal additive manufacturing for UAV heat sinks:
1. How does the thermal performance of a 3D printed heat sink compare to a traditionally machined one?
A well-designed 3D printed heat sink, particularly one utilizing topology optimization and complex geometries (like lattices or optimized fins), can significantly outperform a conventionally machined heat sink of the same weight or volume. AM allows for maximizing surface area and optimizing airflow in ways machining cannot easily replicate. However, comparing a simple AM design to a well-designed machined part made from the same material might show similar performance if the design constraints for AM are not fully leveraged. The key advantage lies in AM’s ability to create optimized shapes that are lighter и perform better. 3D printed heat sink performance hinges on leveraging DfAM.
2. What are the typical weight savings achievable with 3D printed heat sinks?
Significant weight savings are a primary driver for using AM in UAVs. Compared to a traditionally designed and machined heat sink performing the same function, topology-optimized 3D printed versions in AlSi10Mg can often achieve weight reductions of 30% to 60%, sometimes even more. This is achieved by placing material only where structurally or thermally necessary. The exact savings depend heavily on the initial design, the applied optimization, and the performance requirements.
3. Can complex internal cooling channels be printed for liquid cooling applications?
Yes, this is a major strength of metal AM. Processes like L-PBF can create highly complex, conformal internal channels within the heat sink structure, allowing for efficient liquid cooling designs that would be impossible to manufacture otherwise. However, design considerations are crucial: channels must be self-supporting during the build or designed for powder removal (minimum channel diameter, smooth paths, access points for cleaning). Thorough cleaning and inspection (potentially CT scanning) are necessary to ensure channels are clear and free of obstructions.
4. Is post-machining always necessary for 3D printed heat sinks?
Not always, but often yes for critical features. If the heat sink requires very tight dimensional tolerances for mounting, specific flatness and surface finish for the thermal interface (contact with the CPU/GPU/etc.), or threaded holes, then post-machining AM parts in those specific areas is typically required. As-printed tolerances and surface finish are often insufficient for direct, high-performance thermal contact. If the design requirements are less stringent, a well-printed part with appropriate finishing (like bead blasting) might suffice.
5. What are the typical size limitations for 3D printed metal heat sinks?
Size is limited by the build volume of the AM machine. Typical L-PBF machines have build envelopes ranging from around 250×250×300mm to 400×400×400mm. Larger systems exist (up to 800mm or more in X/Y), but are less common. SEBM machines often offer generous build volumes as well. For most UAV electronic components, these build volumes are more than sufficient. For very large thermal management structures, the design might need to be broken into segments and joined after printing, or a provider with large format metal 3D printing capabilities must be sought. Met3dp highlights its printers’ industry-leading print volume as a key advantage.
6. Are materials other than AlSi10Mg and CuCrZr used for 3D printed heat sinks?
While AlSi10Mg and CuCrZr are primary choices balancing weight/performance and high conductivity respectively, other materials could be considered:
- Pure Copper (Cu): Offers slightly higher thermal conductivity than CuCrZr but is very soft and loses strength rapidly at elevated temperatures. Difficult to print reliably via L-PBF.
- Other Aluminum Alloys: Research is ongoing into higher-performance aluminum alloys specifically designed for AM, potentially offering better strength or higher temperature resistance than AlSi10Mg.
- Aluminum Matrix Composites (AMCs): Experimental work involves reinforcing aluminum with ceramic particles (e.g., Silicon Carbide) via AM to enhance stiffness and potentially tailor thermal properties, though printability can be challenging. The choice typically comes down to the optimal balance of thermal conductivity, weight, strength, printability, and cost for the specific UAV application.
Conclusion: Elevating UAV Performance with Additively Manufactured Heat Sinks
The relentless drive for higher performance, longer endurance, and increased capabilities in Unmanned Aerial Vehicles necessitates innovative solutions for managing the heat generated by sophisticated onboard electronics. As we’ve explored, metal additive manufacturing offers a powerful pathway to creating advanced thermal solutions that directly address the critical challenges of weight reduction, space constraints, and complex thermal loads inherent in UAV design.
By moving beyond the limitations of traditional manufacturing, metal 3D printing empowers engineers to:
- Design for Performance: Leverage topology optimization, intricate lattice structures, and complex geometries to create heat sinks with superior thermal dissipation capabilities.
- Achieve Significant Weight Savings: Utilize lightweight materials like AlSi10Mg and optimized structures to drastically reduce component weight, directly improving flight time and payload capacity.
- Enable Customization and Integration: Produce highly customized heat sinks tailored to specific components and available spaces, even integrating thermal management features directly into structural elements through part consolidation.
- Accelerate Development: Rapidly prototype and iterate designs, speeding up the validation and deployment of effective thermal management solutions.
The recommended materials, AlSi10Mg for its excellent balance of low weight and good thermal performance, and CuCrZr for applications demanding the highest possible thermal conductivity, provide robust options for tackling diverse cooling needs. However, unlocking the full potential of these materials and the AM process requires careful consideration of DfAM principles, achievable tolerances, essential post-processing steps, and potential manufacturing challenges.
Successfully navigating this advanced manufacturing landscape necessitates partnering with a knowledgeable and capable metal 3D printing service provider. Такие компании, как Met3dp stand out by offering comprehensive Met3dp solutions that span the entire value chain. With their decades of collective expertise, vertically integrated capabilities including advanced powder making systems ensuring high-quality AlSi10Mg and other alloys, state-of-the-art SEBM-принтеры alongside L-PBF expertise, and a commitment to quality control, they serve as a strategic partner enabling the future of UAV cooling.
Embracing metal additive manufacturing for UAV heat sinks is more than just adopting a new production technique; it’s a step towards a digital manufacturing transformation, enabling the creation of lighter, more efficient, and more reliable aerial platforms. Whether you are an engineer designing next-generation drones or a procurement manager seeking reliable aerospace additive manufacturing suppliers, the advantages offered by 3D printed metal heat sinks are compelling and increasingly crucial for maintaining a competitive edge.
To explore how Met3dp‘s cutting-edge systems, advanced metal powders, and application development services can power your organization’s additive manufacturing goals for UAV components and beyond, contact their team today.
Поделиться
MET3DP Technology Co., LTD - ведущий поставщик решений для аддитивного производства со штаб-квартирой в Циндао, Китай. Наша компания специализируется на производстве оборудования для 3D-печати и высокопроизводительных металлических порошков для промышленного применения.
Сделайте запрос, чтобы получить лучшую цену и индивидуальное решение для вашего бизнеса!
Похожие статьи
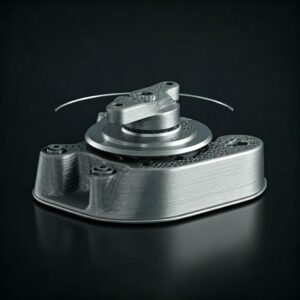
3D-печатные крепления для автомобильных радарных датчиков: Точность и производительность
Читать далее "О компании Met3DP
Последние обновления
Наш продукт
CONTACT US
Есть вопросы? Отправьте нам сообщение прямо сейчас! После получения Вашего сообщения мы всей командой выполним Ваш запрос.
Получите информацию о Metal3DP
Брошюра о продукции
Получить последние продукты и прайс-лист
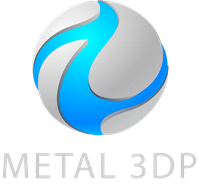
Металлические порошки для 3D-печати и аддитивного производства