порошок сплава для спекания
Оглавление
Представьте себе мир, в котором вы можете создавать сложные металлические компоненты с исключительной прочностью, одновременно оптимизируя производственный процесс. В этом и заключается магия порошков для спекания-закалки. Эти крошечные металлические чудеса революционизируют способ производства деталей для бесчисленных применений. Но прежде чем углубиться в их мир, давайте немного отмотаем назад.
Функция порошка для спекания-закалки
Представьте себе спекание как «дай пять» на атомном уровне. Вот суть:
- Порошковая сила: Металлические порошки, тщательно изготовленные из различных сплавов, образуют основу.
- Уплотнение — это ключ: Эти порошки прессуются под огромным давлением, создавая «зеленую» деталь желаемой формы.
- Жара нарастает: Затем зеленая деталь подвергается воздействию высоких температур (но ниже температуры плавления металла) в печи. Именно здесь происходит волшебство.
- Атомная связь: Во время спекания частицы металла соединяются друг с другом на своих атомных границах, образуя твердую и прочную структуру.
Спекание-закалка: Вывод прочности на новый уровень
Теперь давайте добавим изюминку в эту историю. При спекании-закалке решающую роль играет стадия охлаждения после спекания. Быстрое охлаждение детали приводит к металлургическому преобразованию. Вот суть:
- Преобразование: Быстрое охлаждение захватывает определенные элементы внутри кристаллической структуры металла, образуя более твердую и прочную фазу, называемую мартенситом. Это как поймать мимолетный момент в атомном танце металла, зафиксировав его прочность.
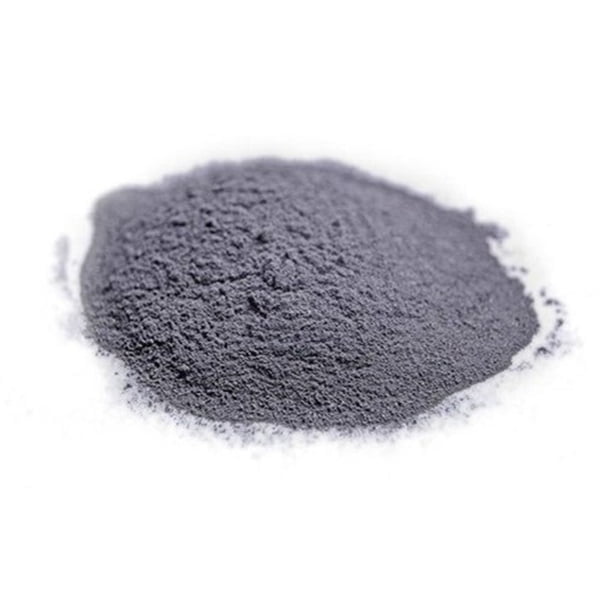
Вселенная металлических порошков: раскрываем 10 главных претендентов
С такой мощной техникой неудивительно, что для спекания-закалки используется разнообразный ассортимент металлических порошков. Вот 10 самых популярных претендентов, каждый со своими уникальными сильными сторонами:
Металлический порошок | Описание |
---|---|
Distaloy AE | Железоуглеродистый сплав, обеспечивающий баланс твердости, обрабатываемости и экономической эффективности. |
Astaloy Mo | Исключительно износостойкий благодаря содержанию молибдена, идеально подходит для шестерен, кулачков и втулок. |
Flamet 4800 | Высокопроизводительный вариант с превосходной прочностью и ударной вязкостью благодаря высокому содержанию никеля, подходит для шатунов и звездочек. |
Ancorsteel 85HP | Никель-хром-молибденовый сплав, превосходящий по прочности и коррозионной стойкости, идеально подходит для клапанов, насосов и крепежных деталей. |
Hoeganaes DM | Предварительно легированный железный порошок, отвечающий определенным магнитным свойствам, используемый в электромагнитных компонентах и датчиках. |
Astaloy CrM | Хром-молибденовый сплав, сохраняющий исключительную стабильность размеров при спекании, идеально подходит для сложных геометрий. |
FC-0205 | Экономичный железо-углеродистый сплав, предлагающий баланс доступности и приличной прочности, подходит для некритичных применений. |
Astaloy CrB | Хром-борный сплав, образующий защитный слой для превосходной коррозионной стойкости. |
AMPCOLOY 94M | Молибденсодержащий сплав, сохраняющий прочность при повышенных температурах, идеально подходит для компонентов, подверженных нагреву. |
Порошки из нержавеющей стали | Различные марки (например, 316L), обеспечивающие коррозионную стойкость наряду с приличной прочностью, идеально подходят для медицинских или пищевых применений. |
Применение порошок сплава для спекания
Порошки для спекания с упрочнением не являются просто одноразовым решением. Они предлагают убедительное сочетание преимуществ, которые делают их предпочтительным выбором для многих применений. Давайте углубимся в эти преимущества:
- Превосходная прочность: По сравнению с традиционным спеканием, процесс быстрого охлаждения при спекании с упрочнением создает более твердую и прочную микроструктуру. Это означает, что детали могут выдерживать более высокие нагрузки и напряжения. Представьте себе замену громоздких компонентов более легкими, упрочненными при спекании альтернативами без ущерба для прочности.
- Повышенная износостойкость: Определенные легирующие элементы, такие как молибден, превосходно борются с трением и износом. Это делает упрочненные при спекании детали идеальными для компонентов, которые испытывают постоянное движение и контакт, таких как шестерни и втулки. Они могут значительно продлить срок службы этих деталей, снижая затраты на техническое обслуживание и время простоя.
- Точность размеров: Контролируемое уплотнение и процесс спекания позволяют создавать детали с жесткими допусками и стабильными размерами. Это исключает необходимость в обширной последующей обработке, экономя время и ресурсы. Подумайте о сложных геометриях, производимых с замечательной точностью.
- Эффективность затрат: Хотя первоначальная стоимость металлических порошков может показаться выше, спекание с упрочнением предлагает несколько преимуществ с точки зрения экономии средств. Процесс часто исключает необходимость в дополнительных этапах термической обработки, экономя потребление энергии и время обработки. Кроме того, высокоточный характер процесса сводит к минимуму отходы материала.
- Гибкость конструкции: В отличие от традиционных методов обработки, ограниченных геометрией инструмента, спекание с закалкой позволяет создавать сложные формы и изделия, близкие к конечной форме. Это открывает двери для инновационных и сложных конструкций компонентов, которые ранее были невозможны.
- Универсальность материала: Как мы видели на примере 10 лучших претендентов, для спекания с закалкой доступна широкая гамма составов металлических порошков. Это позволяет адаптировать свойства материала к конкретным потребностям применения. Нужна исключительная коррозионная стойкость? Есть порошок для этого. Высокотемпературная прочность? Вы ее получите.
Недостатки Порошки сплавов, упрочняющиеся спеканием
Хотя спекание с закалкой имеет ряд преимуществ, важно знать о его ограничениях:
- Материальные ограничения: Не все металлы подходят для спекания с закалкой. Процесс лучше всего работает со сплавами, которые легко образуют мартенсит при быстром охлаждении. Это может ограничить выбор материалов для определенных применений.
- Ограничения по размеру деталей: Из-за трудностей в достижении равномерной скорости охлаждения по всей поверхности больших деталей, спекание с закалкой, как правило, лучше подходит для небольших компонентов. Очень большие детали могут не достичь желаемого уровня твердости по всему объему.
- Соображения по пористости: Спекание по своей природе оставляет некоторую пористость в готовом изделии. Хотя спекание с закалкой может уплотнить структуру по сравнению с обычным спеканием, некоторая пористость все же может присутствовать. Это может быть проблемой для применений, требующих полной газо- или жидконепроницаемости.
- Важность контроля процесса: Успех спекания с закалкой зависит от точного контроля всего процесса, включая выбор порошка, давление уплотнения, температуру спекания и скорость охлаждения. Любые отклонения от этих параметров могут негативно повлиять на конечные свойства детали.
Области применения порошков сплавов для спекания
Мы уже рассмотрели, как спекание с закалкой проявляет себя в автомобильной промышленности и производстве бытовой техники. Но его охват выходит далеко за пределы этих секторов. Вот более широкий взгляд на его разнообразные применения:
Промышленность | Приложения |
---|---|
Аэрокосмическая промышленность: Шестерни, компоненты шасси, легкие конструкционные детали | |
Медицина: Хирургические инструменты, зубные имплантаты, каркасы для восстановления костей | |
Огнестрельное оружие: Детали оружия, компоненты спускового механизма | |
Оборудование: Инструменты, крепежные детали, компоненты замков | |
Электроника: Разъемы, радиаторы, электромагнитные компоненты | |
Электроинструменты: Шестерни, компоненты двигателей, детали трансмиссии |
Выбор подходящего порошка для спекания с закалкой
С таким огромным количеством доступных металлических порошков выбор подходящего для вашего применения может показаться сложной задачей. Вот несколько ключевых факторов, которые следует учитывать:
- Желаемые свойства: Определите наиболее важные свойства для вашей детали, такие как прочность, износостойкость, коррозионная стойкость или точность размеров.
- Требования к заявке: Учитывайте конкретные требования вашего применения, включая условия нагрузки, рабочую температуру и воздействие окружающей среды.
- Стоимостные оценки: Взвесьте первоначальную стоимость порошка с потенциальной экономией за счет таких факторов, как сокращение этапов обработки и увеличение срока службы детали.
- Геометрия детали: Сложность геометрии вашей детали может повлиять на выбор порошка. Некоторые порошки обеспечивают лучшую стабильность размеров при спекании, что делает их идеальными для сложных форм.
Поставщики Порошки сплавов, упрочняющиеся спеканием
Успех вашего проекта по спеканию с закалкой зависит от приобретения высококачественных металлических порошков и сотрудничества с надежным поставщиком. Вот несколько ключевых моментов, которые следует учитывать при поиске поставщика:
- Репутация и опыт: Ищите поставщика с проверенной репутацией в отрасли и опытом работы с порошками для спекания с закалкой. Он должен быть в состоянии предоставить технические рекомендации и поддержку на протяжении всего процесса выбора.
- Разнообразие материалов: Поставщик с разнообразным портфелем металлических порошков позволяет вам изучить различные варианты и найти идеальное решение для ваших конкретных потребностей.
- Меры контроля качества: Строгие процедуры контроля качества имеют первостепенное значение. Убедитесь, что поставщик придерживается отраслевых стандартов и может гарантировать однородность и чистоту своих металлических порошков.
- Техническая поддержка: Доступ к знающему техническому персоналу поставщика неоценим. Они могут ответить на ваши вопросы, помочь с выбором материала и предложить помощь в устранении неполадок при необходимости.
- Конкурентные цены: Хотя стоимость не должна быть единственным решающим фактором, все же важно получить расценки от нескольких поставщиков, чтобы убедиться, что вы получаете справедливую цену.
Спецификации, размеры и марки порошков для спекания с закалкой
Мир порошков для спекания с закалкой огромен, с вариациями в спецификациях, размерах и марках. Вот разбивка, которая поможет вам сориентироваться в этом ландшафте:
Недвижимость | Описание |
---|---|
Химический состав | Это относится к конкретным элементам и их процентному содержанию по весу в металлическом порошке. Различные составы предлагают различные свойства. |
Кажущаяся плотность | Это указывает на вес порошка на единицу объема в его рыхлом, неуплотненном состоянии. |
Скорость потока | Это измеряет, насколько легко порошок течет, влияя на его пригодность для автоматизированных процессов заполнения. |
Распределение частиц по размерам | Распределение размеров частиц в порошке может влиять на плотность упаковки и свойства конечной детали. |
Атмосфера спекания | Некоторые порошки требуют определенной атмосферы (например, инертного газа) во время процесса спекания. |
Степень порошкообразности | Порошки можно разделить по различным маркам, часто обозначаемым буквенной или цифровой системой. Эти марки обозначают различия в составе, размере частиц и других свойствах. |
Доступные размеры | Металлические порошки обычно доступны в различных стандартных диапазонах размеров частиц, измеряемых в микронах (мкм). |
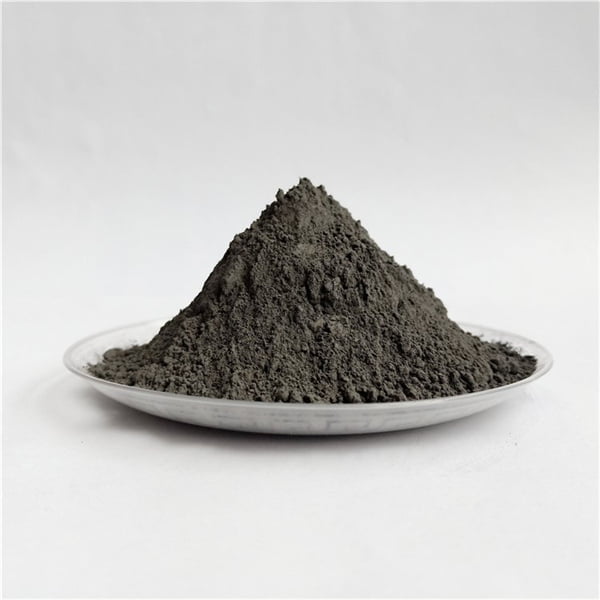
Ценообразование Порошки сплавов, упрочняющиеся спеканием
Стоимость порошков для спекания с закалкой может варьироваться в зависимости от нескольких факторов, в том числе:
- Состав материала: Экзотические сплавы с редкоземельными элементами, как правило, будут дороже, чем обычные железо-углеродистые сплавы.
- Порошок: Более чистые марки с более строгим контролем размера частиц часто стоят дороже.
- Объем: Покупка больших объемов порошка иногда может привести к скидкам от поставщиков.
- Рыночные колебания: Мировые цены на металлы могут влиять на стоимость сырья, используемого в процессе производства порошка.
Вот общий диапазон, чтобы предоставить отправную точку (ожидайте значительные отклонения в зависимости от вышеупомянутых факторов):
- Порошки железо-углеродистых сплавов: 2–5 долларов США за килограмм
- Порошки из низколегированной стали: 3–7 долларов США за килограмм
- Порошки никелевых сплавов: 5–10 долларов США за килограмм
- Порошки из нержавеющей стали: 7–15 долларов США за килограмм
ЧАСТО ЗАДАВАЕМЫЕ ВОПРОСЫ
В: Каковы преимущества спекания с закалкой по сравнению с традиционным спеканием?
О: Спекание с закалкой обеспечивает превосходную прочность, повышенную износостойкость и улучшенную точность размеров по сравнению с традиционным спеканием. Оно также может быть более экономичным благодаря сокращению технологических операций и минимизации отходов материала.
В: Существуют ли какие-либо ограничения на использование порошков сплавов для спекания с закалкой?
О: Не все металлы подходят для спекания с закалкой, и существуют ограничения по размеру деталей. Кроме того, может оставаться определенный уровень пористости, и решающее значение имеет точный контроль процесса для достижения успеха.
В: Каковы некоторые распространенные области применения порошков сплавов для спекания с закалкой?
О: Они широко используются в автомобильной, приборостроительной, аэрокосмической, медицинской, оружейной, аппаратной, электронной и электроинструментальной промышленности для различных компонентов.
В: Как мне выбрать подходящий порошок сплава для спекания с закалкой для моего применения?
О: Учитывайте желаемые свойства, требования к применению, стоимость и геометрию детали. Проконсультируйтесь с авторитетным поставщиком для получения экспертных рекомендаций.
Поделиться
MET3DP Technology Co., LTD - ведущий поставщик решений для аддитивного производства со штаб-квартирой в Циндао, Китай. Наша компания специализируется на производстве оборудования для 3D-печати и высокопроизводительных металлических порошков для промышленного применения.
Сделайте запрос, чтобы получить лучшую цену и индивидуальное решение для вашего бизнеса!
Похожие статьи
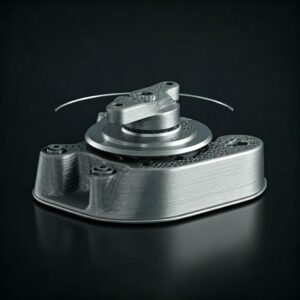
3D-печатные крепления для автомобильных радарных датчиков: Точность и производительность
Читать далее "О компании Met3DP
Последние обновления
Наш продукт
CONTACT US
Есть вопросы? Отправьте нам сообщение прямо сейчас! После получения Вашего сообщения мы всей командой выполним Ваш запрос.
Получите информацию о Metal3DP
Брошюра о продукции
Получить последние продукты и прайс-лист
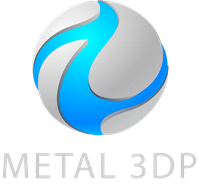
Металлические порошки для 3D-печати и аддитивного производства