Structural Latches for Fairing Attachment via 3D Printing
Оглавление
Introduction: The Critical Role of Fairing Attachment Latches in Aerospace
The aerospace industry stands at the pinnacle of engineering achievement, demanding components that meet extraordinary standards of performance, reliability, and safety. Within the intricate assembly of an aircraft or spacecraft, every single part, no matter how seemingly small, plays a vital role. Among these crucial components are aerospace fairings – smooth, streamlined coverings designed to reduce aerodynamic drag on objects or junctions that would otherwise disrupt airflow. They are essential for fuel efficiency, stability, and overall flight performance, encasing everything from engine pylons and wing-root junctions to landing gear mechanisms and sensitive equipment bays. However, these fairings are not merely static shells; they often need to be opened or removed for inspection, maintenance, repair, and overhaul (MRO). This necessity introduces another critical component: the aerospace fairing attachment latch.
A fairing attachment latch is far more than a simple fastener. It is a precisely engineered structural mechanism designed to securely fasten fairings to the airframe while allowing for reliable and often rapid release when access is required. These latches must withstand significant aerodynamic loads, constant vibration, extreme temperature fluctuations ranging from cryogenic lows in space or high altitude to scorching highs near engines, and potential exposure to corrosive environments (hydraulic fluids, de-icing agents, saltwater spray). Their failure can have catastrophic consequences, ranging from in-flight detachment of a fairing – causing severe aerodynamic disruption and potential damage to engines or control surfaces – to compromising the structural integrity of the aircraft. Therefore, the design, material selection, and manufacturing process for these latches are subject to the most rigorous scrutiny and demanding specifications within the aerospace sector. Procurement managers and B2B buyers in aerospace prioritize suppliers who can guarantee absolute reliability and compliance.
Traditionally, manufacturing these complex, high-strength, lightweight latches has relied heavily on subtractive methods like CNC machining from billet stock or, for some components, investment casting followed by extensive machining. While these methods are mature and well-understood, they face inherent challenges, particularly when dealing with the complex geometries often required for modern latch mechanisms designed for optimal performance and minimal weight.
- Complexity Limitations: Machining intricate internal features, optimized load paths, or highly organic shapes can be difficult, time-consuming, and expensive, often requiring multiple setups and specialized tooling. This limits the potential for design innovation.
- Отходы материалов: Subtractive manufacturing, especially CNC machining, starts with a larger block of material and removes the excess. For expensive aerospace alloys like titanium, this results in significant, costly material waste (buy-to-fly ratio).
- Weight Penalties: Achieving complex shapes often involves compromises that leave excess material, adding unnecessary weight – a critical penalty in aerospace where every gram saved translates to fuel efficiency or increased payload capacity. Part consolidation opportunities are often missed.
- Long Lead Times: Tooling creation, multiple machining steps, and complex assembly processes can lead to extended lead times, hindering rapid prototyping, design iteration, and flexible responses to MRO needs. Sourcing these parts through traditional aerospace supply chains can be slow.
- Assembly Complexity: Latch mechanisms often consist of multiple individual components that need to be manufactured separately and then assembled, introducing potential failure points, tolerance stack-up issues, and increased labor costs.
It is against this backdrop that Аддитивное производство металлов (AM), commonly known as metal 3D-печать, emerges as a truly transformative technology for the production of aerospace fairing attachment latches and other critical structural components. Metal AM builds parts layer by layer directly from a digital model, typically using high-energy sources like lasers or electron beams to fuse fine metal powders. This additive approach fundamentally changes the manufacturing paradigm, offering compelling solutions to the limitations of traditional methods.
The key benefits of leveraging metal AM for aerospace components, particularly structural latches, are manifold and directly address the core needs of aerospace engineers, designers, and procurement professionals:
- Unprecedented Lightweighting: AM enables the creation of complex, topology-optimized geometries that place material only where it is structurally necessary. This facilitates the design of latches with significantly reduced mass but equivalent or even superior strength and stiffness compared to their traditionally manufactured counterparts. This is a major driver for B2B aerospace manufacturing seeking efficiency gains.
- Консолидация частей: The layer-by-layer building process allows multiple functional components of a latch mechanism to be integrated into a single, monolithic printed part. This drastically reduces part count, eliminates complex assembly steps, minimizes potential failure points associated with fasteners or joints, simplifies inventory management for wholesale buyers, and streamlines the supply chain.
- Enhanced Design Freedom: Engineers are liberated from many of the constraints imposed by traditional manufacturing. Intricate internal channels for lubrication or cooling, complex locking features, biomimetic structures, and highly customized designs tailored to specific load cases or spatial constraints become feasible. This opens doors for innovation in latch functionality and performance.
- Быстрое создание прототипов и итерации: Metal AM allows for the quick production of functional prototypes directly from CAD data. Designs can be tested, evaluated, and refined much faster than with traditional methods that require tooling or extensive machining setups. This accelerates the development cycle for new aircraft programs or modifications.
- Улучшенное использование материалов: Additive manufacturing is inherently more resource-efficient, using only the material needed to build the part and its supports. This significantly reduces the buy-to-fly ratio, especially crucial when working with high-cost aerospace alloys like Titanium, offering cost savings sought by procurement teams.
For engineers pushing the boundaries of aerospace design and procurement managers seeking more efficient, reliable, and innovative sourcing solutions, metal AM presents a powerful toolkit. Companies specializing in high-performance металлическая 3D-печать, such as Met3dp, offer the advanced technologies, materials expertise, and process control necessary to realize the full potential of AM for demanding applications like aerospace fairing attachment latches. Understanding the specific applications, the advantages AM brings, and the crucial material choices is the first step towards leveraging this technology effectively.
Applications and Functions: Where are 3D Printed Fairing Latches Utilized?
The versatility and performance advantages of metal 3D printed fairing attachment latches make them suitable for a wide array of applications across the diverse landscape of the aerospace industry. Their ability to combine strength, low weight, complex functionality, and environmental resistance allows them to replace traditionally manufactured counterparts in numerous critical locations, offering tangible benefits for manufacturers, operators, and MRO providers. B2B suppliers focusing on aerospace structural components find significant opportunities in this growing market segment.
Use Cases Across Aircraft Types:
- Commercial Airliners (e.g., Boeing, Airbus): On large commercial jets, fairings are ubiquitous, covering wing-to-body junctions, flap track mechanisms, engine pylons, and landing gear bays. Latches securing these large, load-bearing fairings must be exceptionally reliable and often require features for quick access during routine maintenance checks performed on tight schedules. Metal AM allows for the creation of robust yet lightweight latches, contributing to overall fuel efficiency targets. Furthermore, the ability to consolidate parts simplifies maintenance procedures and reduces the inventory of spare parts needed by airlines and MRO facilities.
- Business Jets: Similar to commercial airliners but often with even tighter integration and aesthetic requirements, business jets utilize numerous fairings. AM enables the production of highly customized latches that fit perfectly within constrained spaces and contribute to the aircraft’s sleek aerodynamic profile, while still ensuring secure fastening and easy access for maintenance crews.
- Military Aircraft (Fighters, Transports, Helicopters): Military applications impose extreme performance demands. Latches on fighter jets, for example, must withstand high G-forces, extreme vibrations, and rapid temperature changes, while potentially needing features for low observability (stealth). Transport aircraft require robust latches for large cargo bay doors and equipment fairings. Helicopters utilize numerous access panels and cowlings secured by latches that must endure intense vibrational environments. Metal AM, particularly using high-strength materials like Ti-6Al-4V, can produce latches meeting these stringent military specifications (Mil-Spec), offering enhanced durability and potentially reduced weight compared to legacy designs. The ability for on-demand printing also supports rapid deployment and field repairs.
- Spacecraft (Launch Vehicles, Satellites): In space applications, weight is paramount, and components must function flawlessly in vacuum and extreme temperatures. Latches used on payload fairings of launch vehicles must withstand the immense forces of ascent and then release reliably for satellite deployment. On satellites themselves, latches might secure deployable structures like solar arrays or antennas. Metal AM allows for extreme lightweighting through topology optimization and the use of space-grade materials, making it an ideal choice for these mass-critical applications. Distributors specializing in space-qualified hardware are increasingly looking towards AM solutions.
- Unmanned Aerial Vehicles (UAVs / Drones): From large surveillance drones to smaller tactical UAVs, weight reduction and component integration are key design drivers. AM enables the production of miniature, complex, lightweight latches for securing payload bays, battery compartments, and sensor housings, maximizing flight endurance and payload capacity.
Specific Locations and Functional Requirements:
Regardless of the aircraft type, fairing attachment latches are commonly found in several key areas, each with specific functional demands:
- Engine Cowlings/Nacelles: These large fairings enclose the engines and require frequent access for inspection and maintenance. Latches here must withstand high temperatures, significant vibration, and aerodynamic loads. They often feature quick-release mechanisms (e.g., hook latches, pressure relief door latches) and must fail-safe. Reliability is absolutely critical.
- Landing Gear Doors: Fairings covering the landing gear wells must be securely latched during flight to maintain aerodynamics but open reliably during gear extension and retraction. These latches experience significant dynamic loads during operation.
- Access Panels: Numerous smaller panels providing access to avionics bays, hydraulic systems, fuel tanks, and structural inspection points are secured by various types of latches (e.g., flush latches, adjustable latches, tool-operated latches). Security, ease of operation, and often flushness with the surrounding skin are key requirements.
- Aerodynamic Fairings: Wing-to-body fairings, flap track fairings, pylon fairings, tail cone fairings – these smooth aerodynamic shapes are crucial for performance. Latches must provide high clamping force to prevent movement or vibration, ensuring the fairing maintains its precise aerodynamic contour under load.
Key Functional Requirements Met by AM Latches:
- Load-Bearing Capacity: Latches must safely handle aerodynamic pressure loads, inertial loads (during maneuvers), and operational loads (clamping force). Metal AM allows tailoring the internal structure and using high-strength alloys (like Ti-6Al-4V supplied by quality-focused producers like Met3dp) to meet specific load requirements efficiently.
- Vibration Resistance: Aircraft environments are characterized by constant vibration from engines and airflow. Latches must remain securely fastened and resist fatigue failure under these conditions. AM parts, especially after processes like HIPing, exhibit excellent fatigue properties. Design features enabled by AM can also incorporate anti-vibration mechanisms.
- Environmental Resilience: Latches must function across a wide temperature range (-55°C to potentially >150°C near engines), resist corrosion from fluids and atmospheric conditions, and withstand UV exposure. Material selection (Ti-6Al-4V’s excellent corrosion resistance, AlSi10Mg with appropriate coating) is key, and AM allows complex shapes that might incorporate sealing features.
- Reliability and Durability: Aerospace components demand long service life and predictable performance. Well-designed and properly processed metal AM latches, manufactured using high-quality powders and qualified processes, meet these demands. Stringent quality control, often exceeding industry standards, is a hallmark of reputable AM service providers targeting the aerospace B2B market.
- Ease of Operation & Maintenance: Latches must be easily operable by maintenance crews, often in tight spaces or adverse conditions. AM allows for ergonomic design features and integration of tool interfaces. Part consolidation reduces the number of potential maintenance issues.
Meeting the stringent aerospace standards and certifications (e.g., AS9100 for quality management, specific OEM requirements, FAA/EASA regulations) is non-negotiable. Additive Manufacturing processes for critical components are undergoing rigorous qualification efforts globally. Partnering with an experienced aerospace AM supplier who understands these requirements and has robust quality systems in place is essential for procurement managers and engineers looking to adopt 3D printed latches. The integration of these advanced latches into the surrounding airframe structures requires careful design consideration, ensuring proper fit, load transfer, and compatibility with existing or concurrently designed components, reinforcing the need for collaboration between designers and AM specialists.
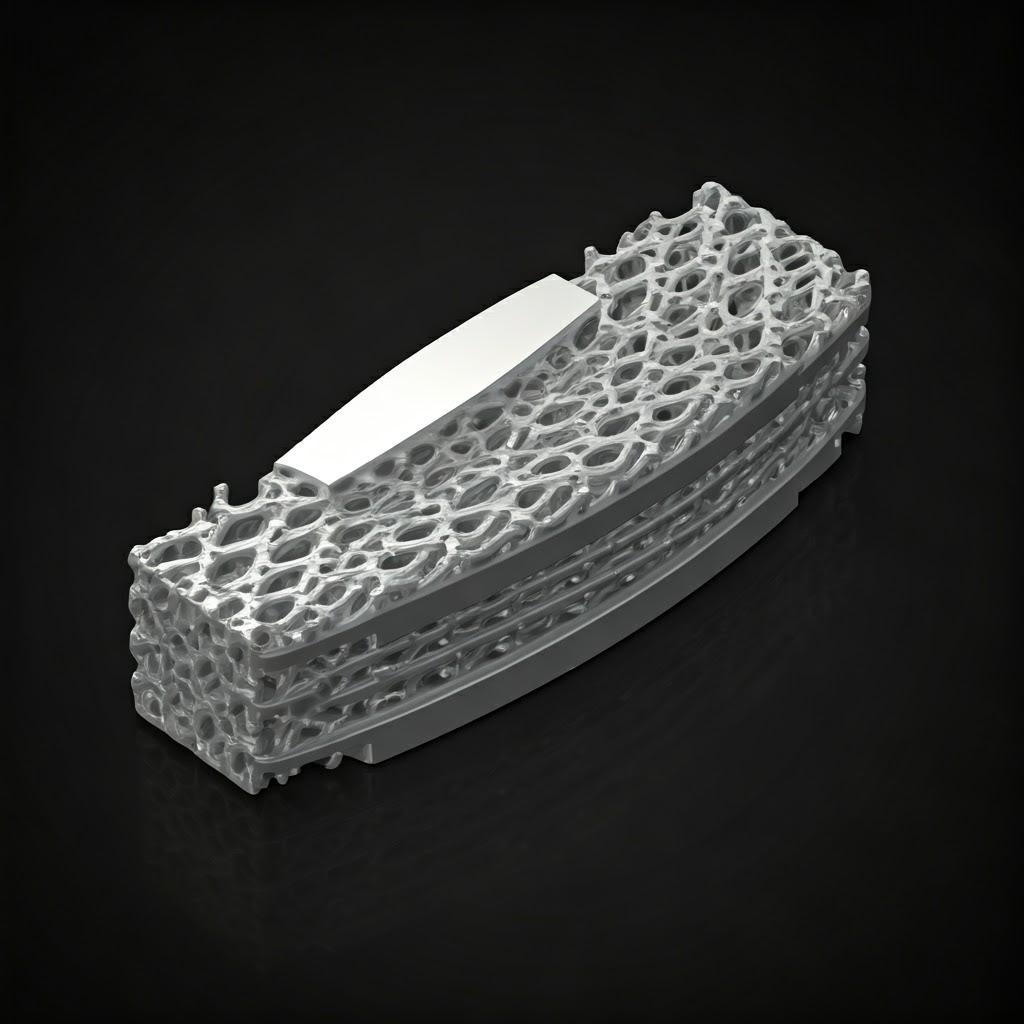
Why Choose Metal 3D Printing for Aerospace Fairing Latches?
The decision to adopt metal additive manufacturing for critical components like aerospace fairing attachment latches is driven by a convergence of compelling technical and economic advantages over established traditional methods like CNC machining or casting. For aerospace engineers striving for optimal performance and procurement managers seeking value, efficiency, and supply chain resilience, metal AM offers a paradigm shift. Let’s delve deeper into the specific reasons why this technology is rapidly gaining traction in the demanding aerospace sector, particularly for complex structural and mechanical parts like latches.
1. Unprecedented Weight Reduction: In aerospace, weight is a primary design constraint directly impacting fuel consumption, payload capacity, range, and overall operational cost. Every kilogram saved can translate into significant lifetime savings for an aircraft. Metal AM excels at lightweighting through several mechanisms: * Topology Optimization: This computational design technique allows engineers to define load cases, constraints, and design spaces, and the software algorithmically removes material from areas where it’s not structurally required. The result is highly organic, load-path-optimized structures that are significantly lighter (often 20-60% weight reduction) than traditionally designed parts, while maintaining or even exceeding the required strength and stiffness. Creating these complex, skeletal structures is often impossible or prohibitively expensive with machining. * Решетчатые структуры: AM enables the incorporation of internal lattice or cellular structures within solid components. These structures drastically reduce mass while providing tailored stiffness, energy absorption, or thermal management properties – potentially useful within the body of a larger latch mechanism. * Material Choice: AM processes efficiently utilize high strength-to-weight ratio materials like Титановые сплавы (Ti-6Al-4V) и Алюминиевые сплавы (AlSi10Mg). While these materials can be machined, AM minimizes the waste associated with subtractive processes, making their use more economically viable, especially for Titanium. Reputable suppliers like Met3dp provide high-quality, aerospace-certified powders of these materials, ensuring optimal performance.
2. Part Consolidation: Traditional latch mechanisms often comprise numerous individual components – levers, springs, housings, pins, fasteners – each manufactured separately and then painstakingly assembled. This complexity introduces several drawbacks: increased weight from fasteners, potential tolerance stack-up issues affecting performance, multiple points of potential failure (joints, fasteners), longer assembly times, and complex inventory management for B2B buyers and MRO providers. Metal AM fundamentally changes this by enabling объединение частей. Designers can integrate multiple functional elements into a single, monolithic printed part. For example, a latch housing, lever, and spring anchor point could potentially be printed as one unit. This offers substantial benefits: * Reduced Assembly Time and Labor Costs: Eliminating assembly steps saves significant time and cost. * Improved Reliability: Fewer joints and fasteners mean fewer potential failure points. * Weight Savings: Eliminating fasteners and simplifying geometry reduces overall weight. * Simplified Supply Chain: Fewer individual part numbers to procure, track, and stock, easing the burden on aerospace procurement teams and wholesale distributors.
3. Design Freedom and Complexity: Perhaps the most transformative aspect of AM is the vastly expanded design freedom it offers. Engineers are no longer constrained by the limitations of traditional manufacturing processes (e.g., tool access for machining, draft angles for casting). This liberation enables: * Highly Complex Geometries: Manufacturing intricate internal channels (e.g., for lubrication delivery within the latch mechanism), complex curved surfaces, negative draft angles, and interlocking features becomes feasible. * Оптимизированная функциональность: Latch mechanisms can be designed with novel kinematics, integrated damping features, or precisely tailored engagement surfaces that would be impossible to machine or cast as a single piece. * Персонализация: AM allows for easy customization of latch designs for specific applications or interfaces without the need for expensive tooling changes.
4. Rapid Prototyping and Accelerated Iteration: Developing and qualifying aerospace components is a lengthy and expensive process. Metal AM significantly accelerates the prototyping phase. * Скорость: Functional metal prototypes can often be produced in days directly from CAD data, compared to weeks or months required for traditional tooling and machining setups. * Cost-Effective Iteration: Design changes can be implemented digitally and new prototypes printed quickly and relatively inexpensively. This allows engineers to test multiple design variations, optimize performance, and identify potential issues much earlier in the development cycle. This agility is invaluable in fast-paced aerospace programs.
5. On-Demand Manufacturing and Supply Chain Enhancement: Traditional manufacturing often relies on large production runs to achieve economies of scale, leading to warehousing costs and potential obsolescence. Metal AM enables a more flexible, on-demand manufacturing model. * Уменьшенный инвентарь: Parts like specialized latches can be printed as needed, minimizing the need for large physical inventories, particularly beneficial for MRO operations and managing spare parts for older aircraft fleets. Wholesale suppliers can adopt more agile stocking strategies. * Supply Chain Resilience: AM can help mitigate supply chain disruptions caused by geopolitical issues, natural disasters, or supplier problems. The ability to print parts closer to the point of need (distributed manufacturing) enhances resilience. * Legacy Part Replacement: Digital scan data from legacy parts can be used to create CAD models and print replacements for obsolete components where original tooling no longer exists.
6. Superior Material Performance and Quality: When executed correctly using high-quality materials and validated processes, metal AM can produce parts with mechanical properties that are equivalent or even superior to those of wrought or cast materials. * Fine Microstructure: The rapid solidification inherent in processes like L-PBF and EBM often results in a fine-grained microstructure, which can enhance strength and fatigue properties. * Высокая плотность: Processes like Hot Isostatic Pressing (HIP) are commonly applied to aerospace AM parts to eliminate any residual internal porosity, achieving full theoretical density and maximizing mechanical performance, especially fatigue life. * Чистота материала: Starting with high-purity, spherical metal powders, such as those produced using advanced gas atomization or PREP technologies by specialists like Met3dp, is crucial. Met3dp’s commitment to powder quality directly translates to the integrity and reliability of the final printed latch. Their expertise spans not just Ti-6Al-4V and AlSi10Mg but also other high-performance alloys relevant to aerospace.
Comparison: Metal AM vs. Traditional Manufacturing for Latches
Характеристика | Аддитивное производство металлов (AM) | Traditional Machining (CNC) | Инвестиционное литье |
---|---|---|---|
Свобода дизайна | Very High (complex geometries, internal features, topology opt.) | Moderate (limited by tool access) | High (complex shapes possible) |
Снижение веса | Excellent (topology opt., lattices) | Good (pocketing, material removal) | Moderate (near-net shape) |
Консолидация частей | Excellent (integrating multiple parts) | Poor (requires assembly) | Poor (requires assembly, some integration) |
Материальные отходы | Low (additive process, support material minimal) | High (subtractive process, significant chips) | Moderate (gates, runners) |
Lead Time (Proto) | Very Fast (days) | Moderate (weeks, depends on complexity) | Slow (weeks/months for tooling & process) |
Lead Time (Prod.) | Moderate (depends on volume, post-processing) | Fast (for established processes) | Moderate (tooling amortized over volume) |
Стоимость оснастки | None / Minimal | Low (fixtures, standard tools) | High (wax injection molds, ceramic shells) |
Cost (Low Volume) | Конкурентоспособный | High (setup, programming, material waste) | Very High (tooling dominates) |
Cost (High Volume) | Can be higher (machine time, powder cost) | Competitive / Lower | Competitive / Lower |
Выбор материала | Growing range (Ti, Al, Ni-alloys, Steels) | Широкий диапазон | Широкий диапазон |
Постобработка | Often Required (support removal, heat treat, machining, HIP) | Often Required (deburring, finishing) | Often Required (gate removal, machining) |
Export to Sheets
In summary, while traditional methods remain viable, particularly for very high-volume production of simpler designs, metal 3D printing offers a compelling suite of advantages for aerospace fairing attachment latches, especially where complexity, weight reduction, part consolidation, and development speed are critical drivers. For B2B sourcing, AM provides flexibility and performance benefits that are increasingly difficult to ignore.
Recommended Materials (Ti-6Al-4V & AlSi10Mg) and Their Significance
The performance, reliability, and longevity of an aerospace fairing attachment latch are fundamentally dependent on the material from which it is constructed. Metal additive manufacturing processes can work with a growing range of alloys, but for structural aerospace applications like latches, two materials stand out due to their well-understood properties, processing characteristics in AM, and established track record: Titanium alloy Ti-6Al-4V и Aluminum alloy AlSi10Mg. The choice between them hinges on a careful balance of performance requirements, weight targets, operating environment, and cost considerations, directly impacting decisions made by aerospace engineers and procurement specialists. Sourcing these materials as high-quality powders optimized for AM is paramount, a specialty of providers like Met3dp.
Titanium Alloy (Ti-6Al-4V): The Aerospace Workhorse
Ti-6Al-4V (Grade 5 Titanium) is arguably the most widely used titanium alloy in the aerospace industry, and for good reason. Its combination of properties makes it exceptionally well-suited for demanding structural applications, including fairing latches operating under significant stress and in challenging environments.
- Detailed Properties:
- Высокое соотношение прочности и веса: This is Ti-6Al-4V’s defining characteristic. It offers strength comparable to many steels but at roughly 56% of the density. This allows for significantly lighter components without compromising structural integrity – a critical factor for latches contributing to overall aircraft weight.
- Отличная коррозионная стойкость: Titanium naturally forms a stable, passive oxide layer that protects it from corrosion in a wide range of aggressive environments, including saltwater, hydraulic fluids, and atmospheric conditions. This ensures long service life and reliability, even for externally mounted latches.
- Высокотемпературные характеристики: Ti-6Al-4V retains good strength and creep resistance at elevated temperatures (up to around 315°C or 600°F), making it suitable for latches located near engines or other heat sources.
- Усталостная прочность: It exhibits excellent resistance to fatigue crack initiation and propagation, crucial for components subjected to cyclic loading and vibration, as latches invariably are. Post-processing like HIP further enhances fatigue life.
- Биосовместимость: While not directly relevant for latches, its biocompatibility has driven its widespread use in medical implants, further attesting to its material integrity.
- Why it’s the Aerospace Standard: Decades of use in airframes, engines, landing gear, and fasteners have resulted in a deep understanding of its behavior, extensive material property databases, and established qualification protocols. Regulators (FAA, EASA) and major OEMs (Boeing, Airbus) have well-defined specifications for Ti-6Al-4V components, providing confidence for its use in critical applications like structural latches.
- Processing Considerations in Metal AM: Ti-6Al-4V is readily processable using both major powder bed fusion technologies:
- Laser Powder Bed Fusion (L-PBF): Offers high resolution and good surface finish but can induce higher residual stresses requiring careful thermal management and post-process stress relief.
- Electron Beam Melting (EBM / SEBM): EBM, such as the Selective Electron Beam Melting (SEBM) technology utilized by Met3dp, operates at higher build chamber temperatures. This in-situ heat treatment significantly reduces residual stresses, often minimizing the need for extensive post-build stress relief cycles. EBM typically builds faster for bulk geometries but may have a rougher surface finish than L-PBF. It’s particularly well-suited for reactive materials like titanium.
- Постобработка: Regardless of the AM process, stress relief heat treatment is typically required. Hot Isostatic Pressing (HIP) is often specified for critical aerospace parts to close any internal voids and maximize fatigue properties. Machining may be needed for tight tolerance interfaces or specific surface finish requirements.
- Приложения: Ti-6Al-4V is the preferred choice for fairing latches where maximum strength, low weight, high temperatures, or extreme reliability are paramount. This includes latches for engine cowlings, highly loaded access panels, critical structural fairings, and applications on military aircraft and spacecraft. Sourcing certified Ti-6Al-4V powder specifically qualified for aerospace AM processes is essential for B2B procurement.
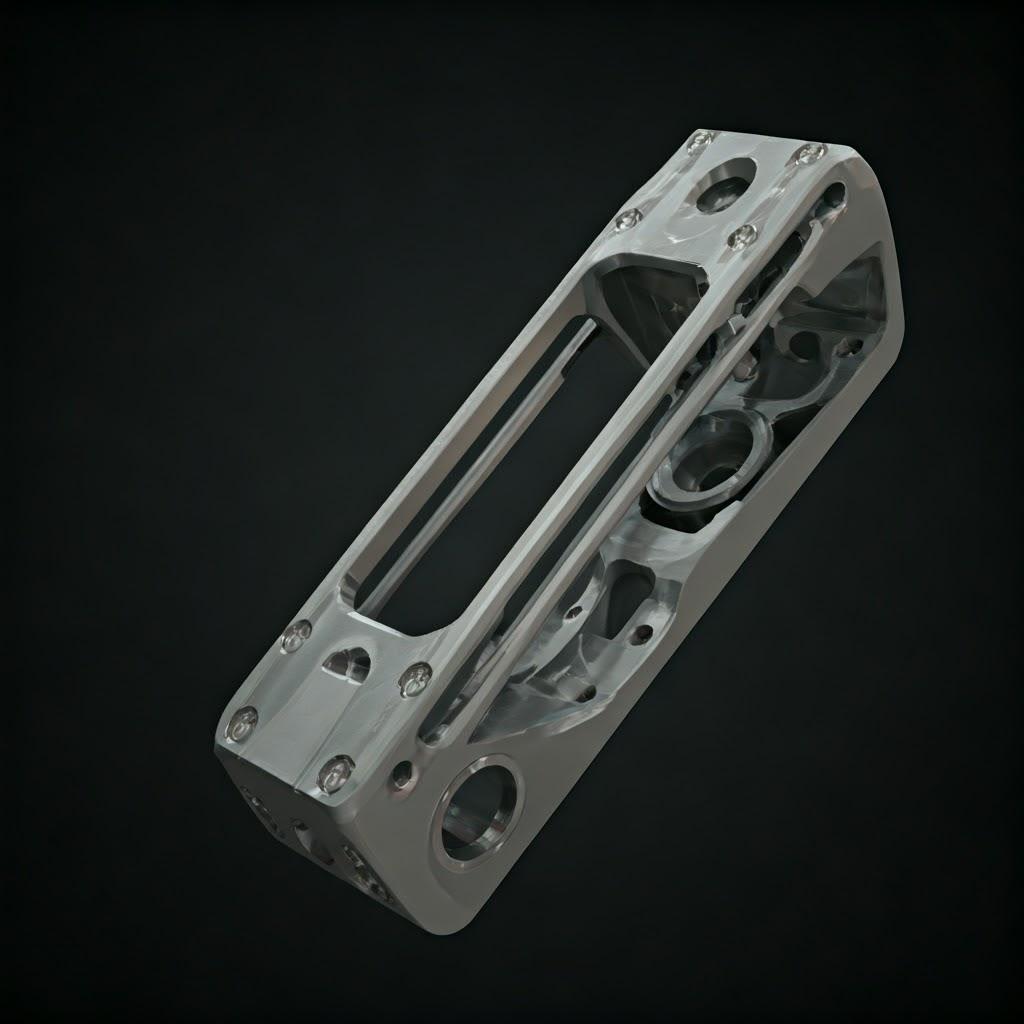
Aluminum Alloy (AlSi10Mg): The Lightweight and Printable Option
AlSi10Mg is an aluminum alloy containing silicon and magnesium, traditionally used for casting parts with good strength and thermal properties. It has become one of the most popular materials for metal AM due to its excellent printability and favorable balance of properties for many applications.
- Detailed Properties:
- Very Low Density: Aluminum alloys are significantly lighter than titanium and steel (approx. 2.68 g/cm³ for AlSi10Mg vs. 4.43 g/cm³ for Ti-6Al-4V). This makes it highly attractive for weight-sensitive applications where the absolute strength of titanium is not required.
- Хорошее соотношение прочности и веса: While not as strong as Ti-6Al-4V, AlSi10Mg offers a very respectable strength-to-weight ratio, significantly better than many non-heat-treatable aluminum alloys or plastics. Heat treatment after printing can further enhance its strength.
- Отличная пригодность для печати: It melts and solidifies well under laser PBF conditions, allowing for the creation of fine features and complex geometries with relative ease and speed compared to some other alloys.
- Good Thermal Conductivity: Useful if the latch needs to dissipate heat, although less common for this specific application.
- Коррозионная стойкость: Generally good, but less resistant than titanium, especially in saltwater environments. Anodizing or other coatings are often applied for enhanced protection.
- Эффективность затрат: Aluminum powders are generally less expensive than titanium powders, and the printing process can sometimes be faster, potentially leading to lower overall part costs. This makes AlSi10Mg an attractive option for less critical latches or when cost is a major driver, a key consideration for wholesale buyers.
- Suitable Applications: AlSi10Mg is ideal for fairing latches on access panels for avionics or non-critical systems, secondary structural fairings, UAV components, or prototypes where the extreme strength or temperature resistance of titanium is not necessary. It provides significant weight savings over steel or even heavier aluminum alloys used in traditional designs.
- Processing Considerations in Metal AM: AlSi10Mg is primarily processed using L-PBF. It requires careful parameter control to achieve dense parts. Post-print heat treatment (typically a T6 cycle involving solutionizing and artificial aging) is essential to achieve optimal mechanical properties (strength and ductility). Surface finishing and coating (e.g., anodizing) are common post-processing steps.
The Paramount Importance of Powder Quality
Regardless of the alloy chosen, the quality of the metal powder used in the AM process is absolutely critical to the final part’s integrity and performance – especially for demanding aerospace applications. Key powder characteristics include:
- Сферичность: Highly spherical powder particles flow uniformly and pack densely in the powder bed, leading to consistent melting and minimizing porosity in the final part.
- Текучесть: Good flow ensures uniform spreading of powder layers during the printing process, preventing defects.
- Чистота: Contaminants (like oxygen, nitrogen, carbon) can degrade mechanical properties. Strict control over powder chemistry is essential.
- Распределение частиц по размерам (PSD): A controlled PSD ensures predictable melting behavior and good packing density. Fines can cause issues, while overly large particles may not melt completely.
Такие компании, как Met3dp invest heavily in advanced powder manufacturing techniques like Vacuum Induction Melting Gas Atomization (VIGA) и Плазменный вращающийся электродный процесс (PREP). These methods, combined with rigorous quality control, produce metal powders (including Ti-6Al-4V, AlSi10Mg, and a wide range of other alloys like Nickel-based superalloys, stainless steels, CoCrMo, and even specialized Titanium alloys like TiNi and TiTa used in other demanding fields) with the high sphericity, controlled PSD, purity, and flowability required for aerospace-quality additive manufacturing. Their product portfolio reflects this commitment to high-performance materials. Sourcing powder from a reputable B2B supplier with transparent quality documentation is non-negotiable for aerospace applications.
Material Selection Guide (Simplified)
Требование | Recommended Primary Choice | Secondary Choice / Considerations |
---|---|---|
Highest Strength/Wt | Ti-6Al-4V | Topology Optimized AlSi10Mg |
High Temperature | Ti-6Al-4V | (Other Ni-based superalloys if temp > 315°C) |
Extreme Corrosion Res. | Ti-6Al-4V | Coated AlSi10Mg |
Lowest Weight | AlSi10Mg | Highly Optimized Ti-6Al-4V |
Lowest Cost | AlSi10Mg | Consider design simplification for Ti-6Al-4V |
Maximum Reliability | Ti-6Al-4V (with HIP) | AlSi10Mg (with T6 & thorough NDT) |
Быстрое прототипирование | AlSi10Mg (often faster) | Ti-6Al-4V (EBM/SEBM can be fast) |
Export to Sheets
Ultimately, the material selection process requires close collaboration between design engineers, materials specialists, and the AM service provider to ensure the chosen alloy, combined with the appropriate AM process and post-processing steps, meets all functional, performance, and certification requirements for the specific aerospace fairing attachment latch application.
Design Considerations for Additively Manufactured Fairing Latches
Successfully leveraging metal additive manufacturing (AM) for complex, critical components like aerospace fairing attachment latches requires more than simply feeding an existing CAD model designed for machining into a 3D printer. It demands a fundamental shift in design thinking, embracing the principles of Проектирование для аддитивного производства (DfAM). DfAM is not just about accommodating the AM process; it’s about actively exploiting its unique capabilities to achieve superior performance, reduced weight, and enhanced functionality that would be unattainable with traditional methods. For engineers designing latches and procurement managers sourcing them, understanding DfAM is crucial for unlocking the true potential of metal 3D printing and collaborating effectively with B2B manufacturing partners.
Embracing the Additive Mindset:
The core principle of DfAM is moving away from the constraints of subtractive manufacturing (what material can be removed easily?) towards the possibilities of additive construction (where does material нужно to be placed?). This involves:
- Thinking Functionally, Not Geometrically: Instead of starting with a block shape, designers define the functional requirements, load paths, interfaces, and spatial constraints. The geometry then evolves to meet these needs in the most efficient way possible, often leading to organic, biomimetic forms.
- Leveraging Complexity: AM thrives on complexity that often doesn’t add significant cost, unlike machining. Designers should actively look for opportunities to integrate multiple parts, create intricate internal features, and optimize forms without being unduly limited by manufacturability concerns of the past.
- Designing for the Process: Understanding the nuances of the chosen AM process – whether Laser Powder Bed Fusion (L-PBF) or Electron Beam Melting (EBM/SEBM) – is vital. Factors like minimum feature size, support structure requirements, build orientation effects, and achievable tolerances must inform the design from the outset.
Key DfAM Strategies for Fairing Latches:
- Topology Optimization (TopOpt):
- What it is: A powerful computational tool that optimizes material layout within a defined design space based on specific load conditions, boundary constraints, and performance objectives (e.g., minimize mass, maximize stiffness).
- Application to Latches: For a load-bearing latch component, engineers define where it mounts, where loads are applied (aerodynamic, clamping forces), and any keep-out zones. The TopOpt software then generates a highly efficient, often skeletal or truss-like structure that meets the strength requirements with minimum material usage.
- Преимущества: Significant weight reduction (often 20-60%), improved structural efficiency, and unique aesthetics. The resulting organic shapes are ideal for AM production.
- Tools: Software like Altair OptiStruct, Dassault Systèmes TOSCA, Ansys Mechanical. Requires careful setup of load cases and constraints for accurate results.
- Lattice Structures and Infill:
- Concept: Replacing solid material volumes with internal lattice or cellular structures (e.g., cubic, octet-truss, gyroid).
- Latch Applications: While the primary load-bearing elements might remain solid or topology-optimized, internal sections of a latch body or non-critical features could potentially incorporate lattices to further reduce weight without sacrificing necessary stiffness or strength in specific directions. Lattices can also be designed for vibration damping.
- Соображения: Requires specialized software for generation and analysis. Powder removal from very fine internal lattices can be challenging, influencing design choices.
- Designing for Minimal Support Structures:
- The Need for Supports: In powder bed fusion processes, overhangs and features below a certain angle relative to the build plate (typically < 45 degrees) require support structures to anchor them to the plate or lower layers, preventing collapse and managing thermal stress.
- Why Minimize Them: Supports consume extra material, add to build time, require labor-intensive and potentially damaging removal processes, and can negatively impact the surface finish where they attach.
- DfAM Techniques:
- Self-Supporting Angles: Designing overhangs to be steeper than the critical angle (e.g., > 45 degrees).
- Chamfers and Fillets: Using chamfers instead of sharp horizontal overhangs on downward-facing edges.
- Teardrop Shapes for Holes: Orienting holes horizontally often requires supports. Designing them with a “teardrop” or diamond shape can make them self-supporting.
- Sacrificial Features: Designing thin ribs or features specifically intended to support a critical area, which are then easily machined away later.
- Build Orientation: Strategically choosing the orientation of the latch on the build plate to minimize the total area requiring support.
- Minimum Feature Size and Wall Thickness:
- Process Limitations: Each процесс аддитивного производства (L-PBF, EBM/SEBM) has limitations on the smallest features (e.g., pins, thin walls) it can reliably produce. This is influenced by beam spot size, layer thickness, and powder particle size.
- Typical Values: L-PBF generally offers finer feature resolution (e.g., walls down to ~0.3-0.5 mm) compared to EBM (e.g., ~0.5-1.0 mm), though this varies by machine and material.
- Design Rule: Engineers must ensure all critical features in the latch design (e.g., small pins, locking tabs, thin housing walls) exceed the minimum producible size for the chosen process and material combination. Designing walls too thin can lead to incomplete formation or warping.
- Part Consolidation Strategy:
- Goal: Reduce the number of individual components in the latch assembly.
- How: Identify adjacent parts that can be combined into a single AM component without compromising function. Look for opportunities to integrate brackets, levers, spring seats, or housings.
- Example: A traditional latch might have a separate housing, lever, pivot pin, and mounting bracket. DfAM could potentially integrate the housing and bracket, and perhaps design the lever pivot directly into the housing (using AM’s ability to create complex internal geometries), eliminating the pin.
- Преимущества: Reduced assembly time/cost, fewer failure points, simplified procurement and inventory for B2B supply chains.
- Designing Functional Elements for AM:
- Compliant Mechanisms: Leveraging material flexibility and AM’s geometric freedom to design features that act like springs or hinges without separate components (e.g., a flexible tab that acts as a detent).
- Integrated Channels: Designing internal channels for lubrication, cooling, or routing small wires/sensors within the latch body.
- Optimized Interfaces: Designing mating surfaces, locking features, and clearances specifically considering the achievable tolerances and surface finish of the AM process.
- Build Orientation Planning:
- Влияние: The orientation in which the latch is placed on the build platform significantly affects:
- Поддерживающие структуры: Amount and location.
- Время сборки: Primarily driven by the height (number of layers).
- Отделка поверхности: Upward-facing and vertical surfaces are generally smoother than downward-facing surfaces that required support.
- Анизотропия: Mechanical properties can vary slightly depending on the build direction relative to the loading direction.
- Strategy: Often involves a trade-off analysis. Simulation tools can help predict outcomes for different orientations. Collaboration with the AM service provider (like Met3dp, who understand their SEBM process nuances) is crucial to determine the optimal orientation for quality, cost, and performance.
- Влияние: The orientation in which the latch is placed on the build platform significantly affects:
- Designing for Post-Processing:
- Доступность: Ensure support structures are physically accessible for removal tools without damaging the part. Avoid complex internal supports where possible.
- Machining Allowances: If specific surfaces require tight tolerances or fine finishes achievable only by machining, add extra “stock” material (e.g., 0.5-1.0 mm) to those areas in the design to be machined away later.
- HIP Considerations: Ensure the design doesn’t have features that might be compromised by the high pressure/temperature of HIP. Design features that allow for effective cleaning before HIP.
- Inspection Access: Consider how critical features will be measured and inspected (e.g., line-of-sight for CMM probes, access for NDT methods).
Effective DfAM is an iterative process, often requiring collaboration between the design engineer and the AM manufacturing partner. Leading B2B additive manufacturing suppliers offer DfAM consultation services to help clients optimize their designs, ensuring components like fairing latches are not just printable, but truly enhanced by the additive process.
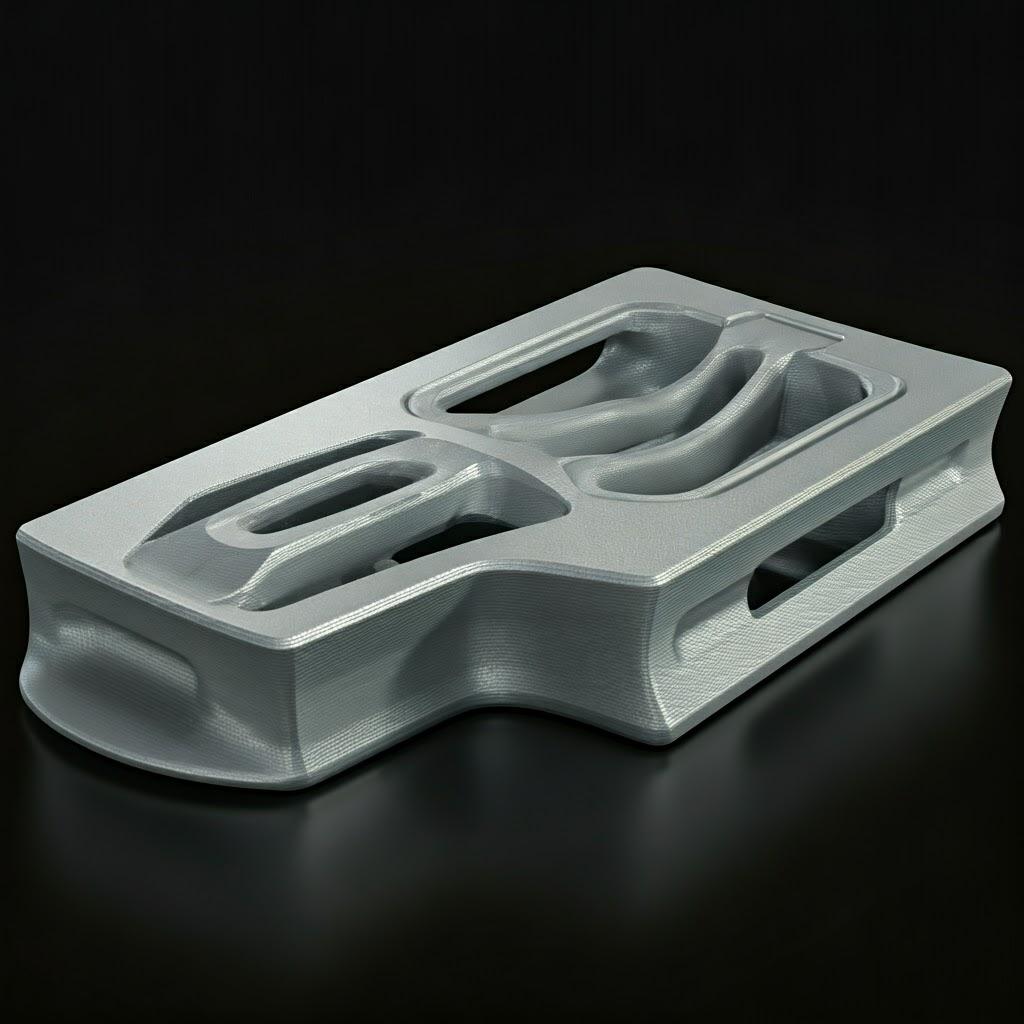
Achievable Tolerances, Surface Finish, and Dimensional Accuracy
While metal additive manufacturing offers incredible geometric freedom, it’s crucial for engineers and procurement managers to have realistic expectations regarding the achievable dimensional tolerances and surface finish directly from the printer (as-built state). These factors directly influence the part’s fit, function, aerodynamic performance, and the need for subsequent post-processing steps. Understanding the typical capabilities and limitations of different AM processes is essential for designing mating parts, defining drawing specifications, and evaluating potential B2B manufacturing suppliers.
Dimensional Tolerances:
Dimensional tolerance refers to the permissible variation in a part’s dimensions from its nominal specification in the CAD model. In metal AM, several factors influence the final tolerances:
- Процесс AM: L-PBF generally offers tighter as-built tolerances than EBM/SEBM due to its finer layer thickness, smaller melt pool, and lower processing temperatures, resulting in less thermal distortion.
- Материал: Different materials exhibit varying shrinkage rates and thermal behavior during processing.
- Part Geometry & Size: Larger parts and complex geometries with significant thermal mass variations are more prone to distortion and deviation.
- Build Parameters: Layer thickness, scan strategy, and energy input affect accuracy.
- Machine Calibration & Condition: Regular calibration and maintenance are critical for consistent accuracy.
- Постобработка: Stress relief heat treatments can cause minor dimensional changes that need to be accounted for.
Typical As-Built Tolerances:
Процесс | General Tolerance (Smaller Features < 100mm) | General Tolerance (Larger Features > 100mm) | Примечания |
---|---|---|---|
L-PBF | ± 0.1 mm to ± 0.2 mm | ± 0.1% to ± 0.2% of dimension | Can achieve tighter tolerances on specific features with optimization. |
EBM / SEBM | ± 0.2 mm to ± 0.4 mm | ± 0.2% to ± 0.4% of dimension | Higher process temperature reduces stress but can increase distortion. |
Export to Sheets
Disclaimer: These are general guidelines. Specific machine capabilities, optimized parameters, and part geometry heavily influence actual results. Always consult with the AM service provider.
Implications for Fairing Latches:
- Critical Interfaces: For latch components that need precise fits (e.g., mating surfaces, pivot points, locking features), the as-built tolerances of AM might not be sufficient. These features often require secondary CNC machining to achieve aerospace-level precision (e.g., tolerances of ± 0.025 mm to ± 0.05 mm).
- DfAM: Designers must account for these typical tolerances. Features requiring high precision should be designed with machining stock included. Non-critical dimensions can often accept as-built tolerances, saving post-processing costs.
- Procurement Specifications: Drawings for AM parts should clearly distinguish between dimensions requiring tight, machined tolerances and those acceptable in the as-built or post-processed (e.g., after HIP/heat treat) state. This clarity is vital for accurate quoting by B2B suppliers.
Обработка поверхности (шероховатость):
Surface finish, typically quantified by average roughness (Ra), describes the texture of a part’s surface. In AM, the layer-by-layer process inherently creates a rougher surface compared to traditional machining or polishing.
- Factors Influencing Ra:
- Толщина слоя: Thicker layers generally result in rougher surfaces.
- Powder Particle Size: Larger powder particles contribute to roughness.
- Build Angle: Surfaces built at an angle (“stair-stepping effect”) and downward-facing surfaces requiring support structures are typically rougher than vertical walls or upward-facing surfaces. EBM/SEBM often produces rougher surfaces than L-PBF due to larger powder size and melt pool dynamics.
- Параметры процесса: Laser/electron beam power, scan speed.
Typical As-Built Surface Roughness (Ra):
Процесс | Vertical Walls / Up-Skin | Down-Skin / Supported Surfaces | Примечания |
---|---|---|---|
L-PBF | 5 – 15 µm (micrometers) | 15 – 30 µm+ | Highly dependent on parameters and material. |
EBM / SEBM | 20 – 40 µm | 35 – 50 µm+ | Generally rougher than L-PBF. |
Export to Sheets
Disclaimer: Values are indicative. Post-processing can significantly improve surface finish.
Implications for Fairing Latches:
- Aerodynamics: For external fairing surfaces or latch components exposed to airflow, a smooth finish is often required to minimize drag. As-built AM surfaces are rarely smooth enough for external aerodynamic applications without significant finishing.
- Mating Surfaces & Wear: Rough surfaces can cause friction and wear in moving latch components or where the latch contacts the fairing/structure. These surfaces typically require machining or polishing.
- Fatigue Life: Surface roughness can act as initiation points for fatigue cracks. Finishing processes like polishing or shot peening are often employed to improve fatigue performance of critical latch components.
- Эстетика: While less critical for internal components, visible latches may require finishing for aesthetic reasons.
Achieving Precision and Smoothness:
Where as-built tolerances and surface finish are insufficient, post-processing is essential:
- CNC Machining: The most common method to achieve tight tolerances (±0.025 mm or better) and smooth finishes (Ra < 1.6 µm or better) on specific features or entire surfaces.
- Grinding/Polishing: Used for achieving very fine surface finishes (Ra < 0.8 µm or even mirror finishes) on critical sealing or bearing surfaces.
- Mass Finishing: Processes like tumbling or vibratory finishing can improve surface finish and deburr edges on multiple parts simultaneously, though they offer less dimensional control than machining.
- Shot Peening / Bead Blasting: Primarily used to improve fatigue life by inducing compressive stress, but also provides a uniform matte finish.
Metrology and Inspection:
Verifying dimensional accuracy and surface finish is critical in aerospace. Common methods include:
- Coordinate Measuring Machines (CMMs): High-accuracy probing for dimensional verification against the CAD model.
- 3D Laser Scanning / Structured Light Scanning: Capturing the full geometry of the part for comparison with CAD, useful for complex shapes and first article inspection (FAI).
- Surface Profilometers: Measuring surface roughness (Ra).
- Computed Tomography (CT) Scanning: Non-destructive inspection of internal features and detection of internal defects (porosity).
Reliable AM providers like Met3dp emphasize process control and machine calibration to achieve the best possible as-built accuracy and consistency from their systems (e.g., SEBM printers known for reliability). However, they also work closely with clients to define and execute the necessary post-processing and metrology steps to meet stringent aerospace drawing specifications and quality standards demanded by procurement departments.
Post-Processing Requirements for 3D Printed Latches
A common misconception about metal additive manufacturing is that parts come out of the printer ready to use. In reality, particularly for demanding aerospace applications like fairing attachment latches, the printing process is often just the first step. A series of crucial post-processing steps are typically required to transform the as-built component into a flight-worthy, functional part that meets all engineering specifications and airworthiness requirements. Understanding this workflow is essential for accurate cost estimation, lead time planning, and selecting a capable B2B manufacturing partner with comprehensive capabilities.
The specific post-processing steps depend heavily on the AM process used (L-PBF vs. EBM/SEBM), the material (Ti-6Al-4V vs. AlSi10Mg), the design complexity, and the specific performance requirements of the latch. Common steps include:
- Part Removal and De-Powdering:
- Процесс: Once the build is complete and cooled, the build platform containing the printed latch(es) is removed from the machine. Excess metal powder surrounding the parts must be carefully removed, often using vacuum systems and brushes within a controlled environment to allow powder recovery and recycling. This step is critical to prevent loose powder from interfering with subsequent processes or becoming trapped in internal features.
- Задачи: Removing powder from intricate internal channels or tightly packed lattice structures designed using DfAM can be difficult and requires careful planning and execution.
- Демонтаж опорной конструкции:
- Цель: Removing the temporary structures that anchored the part during the build.
- Методы: This is often a manual process using hand tools (pliers, cutters), band saws, or electrical discharge machining (EDM) for delicate or hard-to-reach supports. CNC machining can also be used for precise support removal integrated with feature machining.
- Задачи: Can be time-consuming and labor-intensive. Risk of damaging the part surface if not done carefully. DfAM plays a huge role here – minimizing supports through smart design significantly reduces this effort. Residual support “nubs” often require grinding or machining for a smooth finish.
- Stress Relief / Heat Treatment:
- Цель: The rapid heating and cooling cycles inherent in AM, especially L-PBF, induce significant residual stresses within the part. These stresses can cause distortion and negatively impact mechanical properties, particularly fatigue life. Heat treatment relieves these stresses and can also optimize the material’s microstructure for desired properties (strength, ductility, hardness).
- Процесс: Parts are heated in a furnace (often vacuum or inert atmosphere for reactive materials like Titanium) to a specific temperature, held for a period, and then cooled at a controlled rate.
- Ти-6Ал-4В: Typically requires stress relief at intermediate temperatures (e.g., 650-800°C) followed by controlled cooling. Solution Treatment and Aging (STA) may be used for higher strength.
- AlSi10Mg: Typically undergoes a T6 heat treatment (solutionizing followed by artificial aging) to achieve optimal strength.
- Importance: This is a critical step for almost all structural aerospace AM parts to ensure dimensional stability and mechanical integrity. Must be performed by certified facilities (e.g., NADCAP accredited) for flight hardware.
- Горячее изостатическое прессование (HIP):
- Цель: To eliminate residual internal porosity (microscopic voids) that can sometimes remain after the AM process, even with optimized parameters. Porosity acts as stress concentrators and severely degrades fatigue life.
- Процесс: Parts are subjected to high temperature (below melting point) and high isostatic pressure (using an inert gas like Argon) simultaneously within a specialized HIP vessel. The pressure collapses internal voids, diffusion bonding the material across the void interfaces.
- Importance: Существенный for most fatigue-critical or fracture-critical aerospace components, including many structural latches. HIPing results in parts with near 100% density, improved ductility, significantly enhanced fatigue life, and reduced variability in mechanical properties. Often mandated by aerospace prime contractors and certification authorities. Requires specialized, certified providers.
- Отделка поверхности:
- Цель: To achieve the required surface roughness (Ra), improve aesthetics, prepare for coatings, or remove minor imperfections.
- Методы:
- Machining (CNC): For achieving tight tolerances and smooth finishes on specific features (mating surfaces, interfaces).
- Grinding/Polishing: For very smooth, low-Ra finishes on sealing or bearing surfaces.
- Mass Finishing (Tumbling, Vibratory): Cost-effective way to deburr edges and provide a uniform finish on multiple parts, especially smaller latch components.
- Bead Blasting / Shot Peening: Creates a uniform matte finish and, importantly, induces compressive residual stress on the surface, which significantly improves fatigue resistance. Often used on Ti-6Al-4V components.
- Coatings and Surface Treatments:
- Цель: To enhance corrosion resistance, improve wear resistance, provide thermal barrier properties, or meet specific surface property requirements.
- Common Treatments for Latches:
- Anodizing (for Aluminum): Creates a hard, corrosion-resistant oxide layer. Can also be dyed for color-coding.
- Passivation (for Titanium): Enhances the natural protective oxide layer.
- Dry Film Lubricants / DLC Coatings: Applied to moving parts within the latch mechanism to reduce friction and wear.
- Paint/Primer: For environmental protection and matching aircraft livery.
- Chemical Conversion Coatings: Improve corrosion resistance and paint adhesion.
- Inspection and Testing (Quality Assurance):
- Цель: To verify that the final latch meets all dimensional, material, and performance specifications.
- Методы:
- Проверка размеров: CMM, 3D scanning (as discussed previously).
- Неразрушающий контроль (NDT): Crucial for finding internal and surface defects without damaging the part. Common NDT methods for AM aerospace parts include:
- Computed Tomography (CT): X-ray based method to visualize internal structure and detect porosity or inclusions.
- Fluorescent Penetrant Inspection (FPI): Detects surface-breaking cracks.
- Magnetic Particle Inspection (MPI): Detects surface and near-surface flaws in ferromagnetic materials (not Ti or Al).
- Ultrasonic Testing (UT): Detects internal flaws.
- Destructive Testing: Performed on representative test coupons built alongside the parts or sometimes on sacrificial parts to verify material properties (tensile strength, yield strength, elongation, fatigue life).
- Documentation: Thorough documentation of all post-processing steps and inspection results is mandatory for aerospace traceability and certification.
Workflow Integration for B2B Manufacturing:
A key differentiator for high-capability B2B additive manufacturing suppliers is their ability to manage this entire post-processing workflow efficiently, either through in-house capabilities or a network of qualified and certified partners (e.g., NADCAP accredited for heat treatment, HIP, NDT). Procurement managers should evaluate potential suppliers not just on their printing capabilities but also on their demonstrated expertise and infrastructure for handling these critical downstream processes reliably and with full traceability. Companies like Met3dp, with their focus on industrial applications and comprehensive solutions, understand the importance of this integrated approach for delivering flight-ready components.
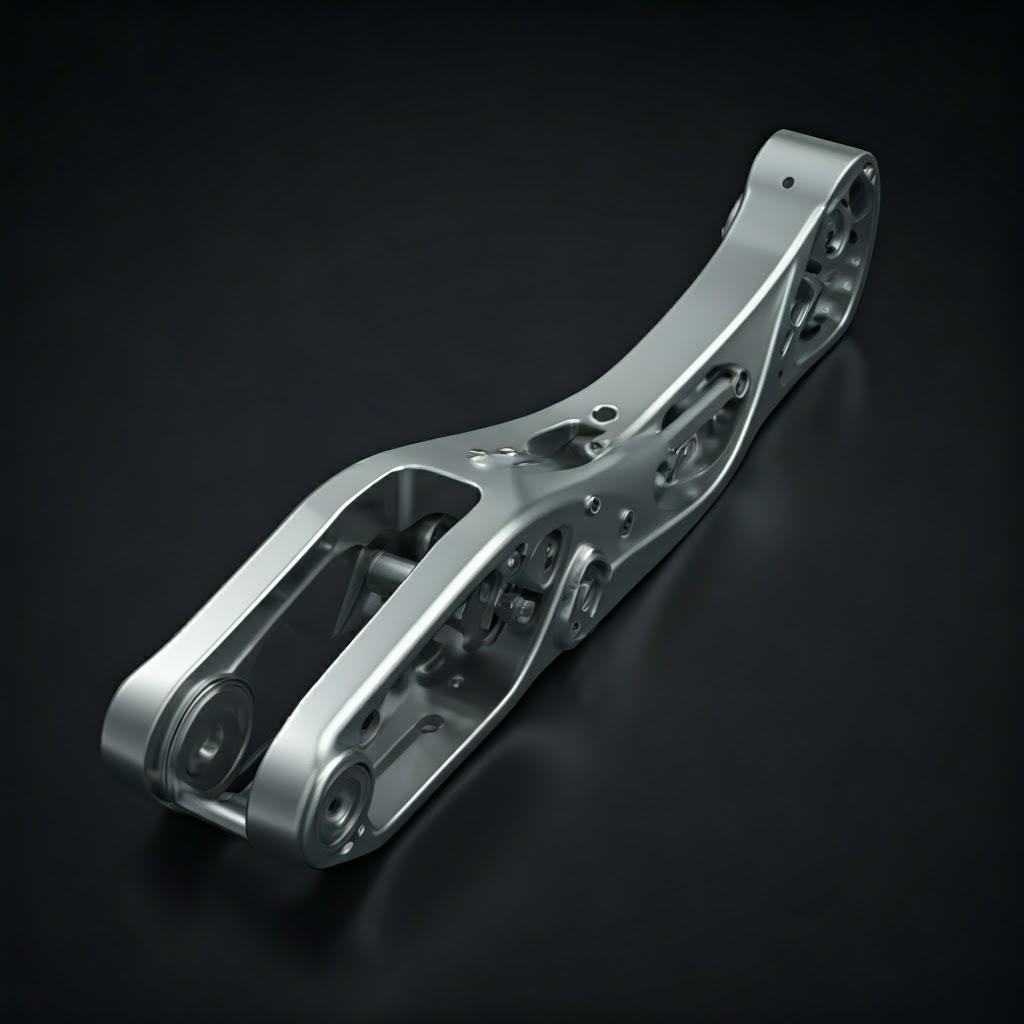
Common Challenges in 3D Printing Aerospace Latches and Mitigation Strategies
While metal additive manufacturing offers significant advantages for producing aerospace fairing latches, the technology is not without its challenges. Achieving the stringent quality, reliability, and consistency demanded by the aerospace industry requires careful control over the entire process chain, from design and powder handling to printing and post-processing. Awareness of potential issues and effective mitigation strategies is crucial for both designers and manufacturers, ensuring successful adoption of AM for these critical components. Partnering with an experienced AM service provider like Met3dp, who possess deep process knowledge and robust quality systems, is a key mitigation strategy in itself.
1. Residual Stress and Warpage:
- Вызов: The rapid, localized melting and solidification during powder bed fusion creates steep thermal gradients. As layers cool and contract, residual stresses build up within the part and at the interface with the build plate. Excessive stress can lead to:
- Warpage/Distortion: The part deforms during or after the build, failing to meet dimensional tolerances.
- Build Plate Detachment: The part may partially or fully detach from the build plate during the print, causing build failure.
- Cracking: In susceptible materials or geometries, high stress can lead to cracking during the build or cooling.
- Mitigation Strategies:
- Simulation: Using process simulation software (e.g., Ansys Additive Suite, Simufact Additive) to predict thermal behavior and residual stress distribution before printing. Allows optimization of build orientation and support strategy.
- Optimized Build Strategy: Careful selection of build orientation to minimize stress concentration; using appropriate scan strategies (e.g., island scanning, checkerboard patterns) to manage heat input.
- Тепловое управление: Preheating the build plate (standard in L-PBF) or maintaining an elevated build chamber temperature (a key feature of EBM/SEBM systems like those from Met3dp, significantly reducing stress in-situ).
- Robust Support Structures: Designing supports not just for gravity but also to anchor the part firmly and conduct heat away effectively.
- Prompt Post-Build Stress Relief: Performing heat treatment as soon as possible after the build is crucial, especially for L-PBF parts, to relax residual stresses before they cause further distortion (e.g., during removal from the build plate).
2. Support Removal Difficulty and Part Damage:
- Вызов: Support structures, while necessary, must be removed. This can be difficult, costly, and potentially damaging, especially for:
- Complex Internal Geometries: Supports inside channels or intricate features can be very hard to access.
- Delicate Features: Applying force to remove supports can break or bend thin walls or small pins on the latch.
- Прочные материалы: Removing well-fused supports from strong materials like Ti-6Al-4V requires significant effort.
- Mitigation Strategies:
- DfAM is Key: The primary mitigation is designing the latch to minimize the need for supports (self-supporting angles, optimal orientation).
- Breakaway/Optimized Supports: Using specialized support structure designs (e.g., tapered interfaces, perforated structures) generated by build preparation software to facilitate easier removal.
- Careful Manual Removal: Requires skilled technicians using appropriate tools.
- Non-Contact Removal: Using methods like wire EDM for precise cutting in difficult areas, though this adds cost and time.
- Accessibility Planning: Ensuring the design allows physical access for support removal tools.
3. Porosity:
- Вызов: The presence of microscopic voids or pores within the printed material. Porosity severely degrades mechanical properties, particularly fatigue strength, and is unacceptable for critical aerospace components. Types include:
- Lack of Fusion: Insufficient energy input leaves unmelted powder particles between layers or scan tracks.
- Keyhole Porosity: Excessive energy input creates instability in the melt pool, trapping gas.
- Gas Porosity: Gas trapped within the powder particles (e.g., Argon used in atomization) or introduced during printing expands upon melting.
- Mitigation Strategies:
- Optimized Process Parameters: Rigorous development and validation of printing parameters (laser/beam power, speed, layer thickness, scan strategy) specific to the material and machine.
- High-Quality Powder: Using powders with high sphericity, controlled PSD, low internal gas content, and proper handling to avoid moisture absorption is critical. This underscores the importance of sourcing from quality-focused suppliers like Met3dp, whose advanced atomization (VIGA, PREP) and quality control minimize inherent powder defects.
- Process Monitoring: Advanced machines may incorporate in-situ monitoring (e.g., melt pool monitoring) to detect process anomalies that could lead to porosity.
- Горячее изостатическое прессование (HIP): The most effective way to eliminate any remaining internal porosity, ensuring maximum density and performance. Essential for most aerospace latches.
4. Anisotropy:
- Вызов: Mechanical properties (e.g., strength, ductility) of AM parts can vary depending on the direction relative to the build layers (X, Y vs. Z direction). This is due to the columnar grain growth aligned with the thermal gradient during solidification and potential layer boundary effects. Designers must account for this potential directionality.
- Mitigation Strategies:
- Understanding Material Behavior: Using material property data that accounts for build orientation (Z vs. XY properties). Datasheets from reputable material/service providers should specify this.
- Strategic Build Orientation: Orienting the part so that critical stresses are applied in the direction of optimal material properties (often parallel to the build plate, XY).
- Термообработка: Specific heat treatments can sometimes homogenize the microstructure and reduce the degree of anisotropy.
- Conservative Design: Applying appropriate safety factors to account for potential directional variations if orientation cannot be fully optimized.
5. Surface Roughness:
- Вызов: As-built surfaces are inherently rougher than machined surfaces, which can impact aerodynamics, wear, fatigue, and aesthetics. Downward-facing surfaces and those built at shallow angles are particularly rough due to support interaction and the stair-stepping effect.
- Mitigation Strategies:
- Optimized Orientation & Parameters: Building critical surfaces vertically or as upward-facing features where possible; fine-tuning parameters for specific surface finish goals (often a trade-off with build speed).
- Extensive Post-Processing: Implementing necessary machining, grinding, polishing, or mass finishing steps to achieve the required Ra values on critical surfaces. This must be factored into cost and lead time.
- Обработка поверхности: Shot peening can improve fatigue life despite some inherent roughness.
6. Meeting Stringent Aerospace Qualification & Certification:
- Вызов: The aerospace industry requires extremely high levels of process control, repeatability, material traceability, documentation, and part qualification. Achieving this with relatively newer AM processes requires significant investment and expertise. Variability in powder batches, machine performance, or operator skill can impact part quality.
- Mitigation Strategies:
- Robust Quality Management System (QMS): Partnering with suppliers who have mature QMS certified to aerospace standards (AS9100).
- Process Validation & Control: Rigorous validation of machine parameters (IQ/OQ/PQ), continuous process monitoring, and statistical process control (SPC).
- Material Traceability: Strict tracking of powder batches from sourcing through production to the final part.
- Comprehensive Testing & Documentation: Performing required NDT and destructive testing, and maintaining detailed records for full traceability and airworthiness certification support.
- Experienced Partnerships: Collaborating with AM service providers and engineering teams who have a proven track record in qualifying aerospace components.
Successfully navigating these challenges requires a deep understanding of materials science, AM process physics, DfAM principles, and rigorous quality control methodologies. It highlights the importance for aerospace companies and their procurement teams to select B2B additive manufacturing partners who demonstrate not only advanced technological capabilities but also the process maturity and quality focus needed to deliver reliable, flight-worthy fairing attachment latches.
How to Choose the Right Metal 3D Printing Service Provider for Aerospace Components
Selecting the right manufacturing partner is arguably one of the most critical decisions when adopting metal additive manufacturing for aerospace components like fairing attachment latches. The unique demands of the aerospace industry – uncompromising safety standards, stringent quality requirements, complex qualification processes, and the need for absolute reliability – mean that not all AM service providers are created equal. Choosing an unsuitable partner can lead to costly delays, quality issues, failed certifications, and potentially unsafe components. Therefore, aerospace engineers and procurement managers must conduct thorough due diligence, evaluating potential B2B suppliers against a rigorous set of criteria that go far beyond just quoting the lowest price.
Here’s a detailed breakdown of key factors to consider when evaluating and selecting a metal AM service provider for producing aerospace-grade fairing latches:
- Demonstrated Aerospace Expertise and Experience:
- Track Record: Look for providers with a proven history of successfully manufacturing components, preferably structural or mechanical parts, for the aerospace industry. Ask for case studies, examples of similar parts produced (respecting NDAs), and client references within aerospace.
- Understanding Requirements: Do they understand aerospace materials specifications (AMS, Mil-Spec), quality clauses (e.g., from Boeing, Airbus, Lockheed Martin), regulatory frameworks (FAA, EASA), and the nuances of aerospace qualification processes? Their team should include engineers and quality personnel familiar with the sector’s demands.
- Problem Solving: Can they discuss challenges encountered on previous aerospace projects and how they were overcome? This indicates practical experience beyond just operating the machines.
- Relevant Certifications:
- AS9100: This is the internationally recognized Quality Management System (QMS) standard specifically for the Aviation, Space, and Defense industries. Certification to AS9100 (currently AS9100D) is often a minimum requirement for suppliers of flight hardware. It demonstrates robust processes for configuration management, risk management, traceability, process control, and continuous improvement tailored to aerospace needs. Verify the certificate’s validity and scope.
- ISO 9001: While AS9100 incorporates ISO 9001, the latter is a more general QMS standard. It’s a good baseline but generally insufficient on its own for critical aerospace work.
- NADCAP Accreditation: The National Aerospace and Defense Contractors Accreditation Program provides independent certification for specific ‘special processes’. While AM itself is still evolving within NADCAP, crucial post-processing steps often require it. Ask if the provider (or their key subcontractors) holds NADCAP accreditation for:
- Heat Treating
- Non-Destructive Testing (NDT – FPI, MPI, UT, CT)
- Materials Testing Laboratories
- Welding (sometimes relevant for post-processing repairs or assemblies)
- Chemical Processing (e.g., Anodizing, Passivation)
- Material Certifications: Ensure the provider sources powders from reputable suppliers who provide full material certifications documenting chemistry, PSD, and compliance with relevant AMS or OEM specifications.
- Material Capabilities and Quality Control:
- Relevant Alloy Portfolio: Do they offer the specific aerospace-grade alloys required for your latch (e.g., Ti-6Al-4V, AlSi10Mg, Inconel 718/625)? What is their experience level with processing these materials?
- Powder Quality Management: This is critical. Enquire about their procedures for:
- Powder Sourcing: Do they use approved aerospace powder suppliers?
- Incoming Inspection: How do they verify the quality of incoming powder batches (e.g., chemistry, PSD analysis)?
- Handling and Storage: Procedures to prevent contamination and moisture absorption (e.g., controlled atmosphere storage, sieving).
- Traceability: Lot tracking of powder from receipt through production to the final part.
- Recycling Strategy: If they recycle powder (common practice), what are their procedures for monitoring powder chemistry and morphology over multiple uses to ensure continued quality? Reputable providers like Met3dp, with their own advanced powder production capabilities (VIGA, PREP), often have an inherent advantage in understanding and controlling powder quality from the source.
- Equipment, Technology, and Capacity:
- Appropriate AM Technology: Do they have the right type of machine (L-PBF, EBM/SEBM) for your specific latch design, material, and requirements? (e.g., Met3dp’s SEBM technology is often favored for stress-sensitive Ti-6Al-4V parts).
- Machine Condition and Calibration: Are the machines well-maintained and regularly calibrated to ensure accuracy and consistency?
- Capacity and Redundancy: Do they have sufficient machine capacity to meet your lead time requirements, including potential fluctuations in demand for B2B wholesale orders? Do they have multiple machines to provide redundancy in case of downtime?
- Post-Processing Capabilities: Evaluate their in-house capabilities for essential post-processing steps (stress relief, support removal, basic finishing). If they outsource critical processes like HIP, machining, NDT, or coating, assess their network of approved, certified subcontractors and how they manage that supply chain. An integrated offering simplifies project management.
- Robust Quality Management System (QMS) in Practice:
- Beyond Certification: Look for evidence that their QMS is actively used and effective, not just a certificate on the wall. This includes:
- Process Control Documentation: Detailed work instructions, process parameters, and control plans for each step.
- Traceability: Ability to trace materials, processes, operators, and inspection results back to a specific part or batch (often via serial numbers).
- Configuration Management: Controlling changes to designs, processes, and materials.
- Non-Conformance Management: Procedures for identifying, documenting, segregating, and dispositioning non-conforming parts.
- Corrective and Preventive Actions (CAPA): A system for addressing root causes of problems and preventing recurrence.
- Personnel Training and Qualification: Ensuring operators and inspectors are properly trained and qualified.
- Beyond Certification: Look for evidence that their QMS is actively used and effective, not just a certificate on the wall. This includes:
- Engineering and Technical Support:
- DfAM Expertise: Can they provide knowledgeable support in optimizing the latch design for additive manufacturing (DfAM)? Can they advise on topology optimization, support minimization, and feature design?
- Simulation Capabilities: Do they offer process simulation to predict and mitigate issues like distortion or residual stress?
- Collaborative Approach: Are they willing to work closely with your engineering team throughout the design, prototyping, and qualification process? A true partner adds value beyond just printing. Companies like Met3dp, positioning themselves as providers of comprehensive solutions, often excel here. You can learn more about a potential service provider by reviewing their company information and technical resources.
- Lead Time and Responsiveness:
- Realistic Quoting: Do they provide clear, realistic lead time estimates that account for all process steps (printing, post-processing queues, inspection)?
- Production Scalability: Can they support your needs from initial prototypes through to potential low-rate initial production (LRIP) or series production for wholesale/B2B volumes?
- Communication: Are they responsive to inquiries and proactive in communicating project status?
- Cost Structure and Transparency:
- Detailed Quotes: Do they provide transparent quotes that break down the costs associated with materials, machine time, labor, post-processing, and QA? Beware of quotes that seem too low – they may be omitting necessary steps or compromising on quality.
- Value Proposition: Evaluate the total value offered, considering quality, reliability, engineering support, and lead time, not just the per-part price. The cost of failure in aerospace is extremely high.
- Security and Compliance:
- Data Security: Procedures for handling sensitive CAD data and technical information (NDAs).
- ITAR/Export Controls: If applicable (especially for military projects), ensure the provider understands and complies with relevant regulations like ITAR (International Traffic in Arms Regulations). Note: Met3dp is based in China, so US ITAR projects would require specific consideration.
Choosing the right metal AM partner is an investment in quality and reliability. Taking the time to rigorously evaluate potential suppliers against these criteria will significantly increase the probability of successfully implementing 3D printed fairing attachment latches that meet the demanding standards of the aerospace industry.
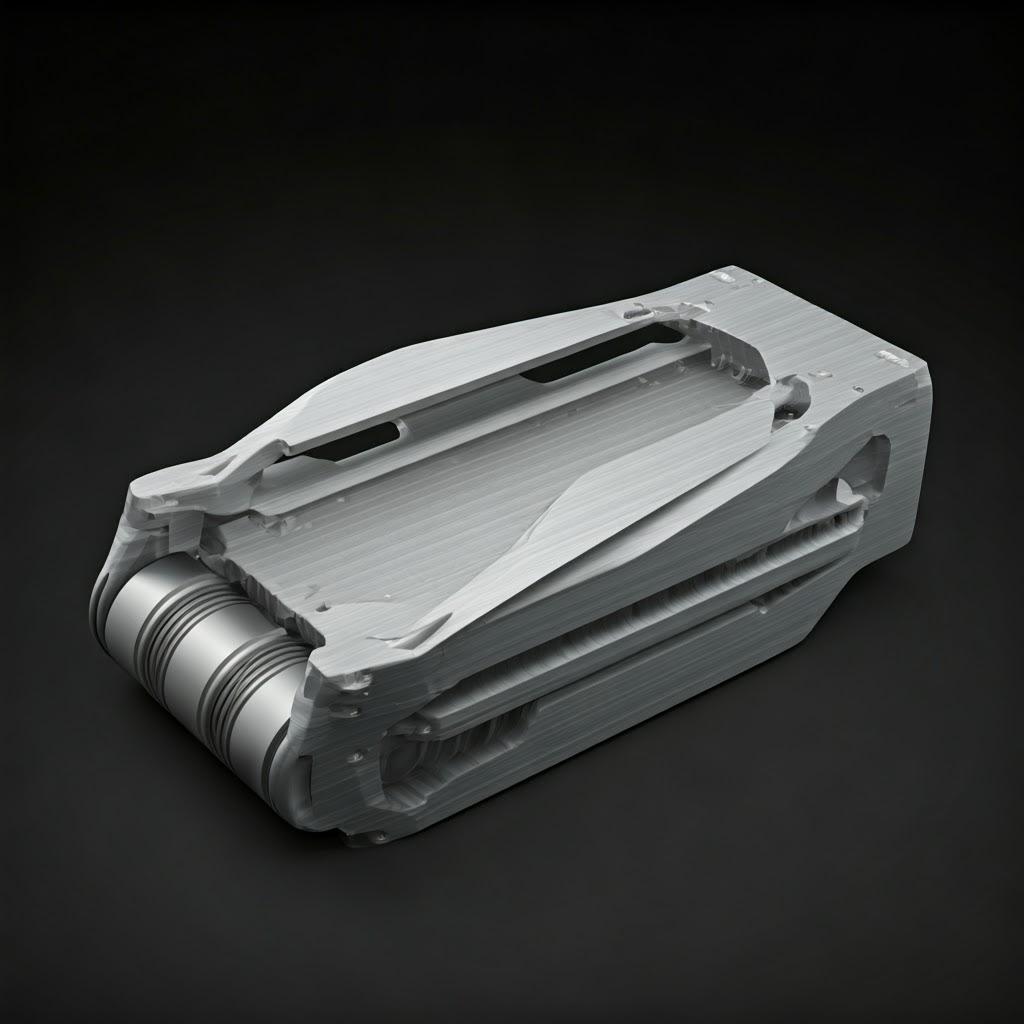
Cost Factors and Lead Time Estimation for 3D Printed Latches
While metal additive manufacturing unlocks significant performance and design benefits for aerospace components like fairing latches, understanding the associated cost structure and typical lead times is crucial for project planning, budgeting, and managing expectations within engineering and procurement departments. Unlike traditional mass production methods where tooling costs dominate low volumes, AM costs are driven by different factors, primarily related to material consumption, machine time, and extensive post-processing.
Breakdown of Cost Factors:
- Материальные затраты:
- Powder Price: This is a significant driver. Aerospace-grade metal powders are expensive, with Ti-6Al-4V typically being several times more costly per kilogram than AlSi10Mg or stainless steels. Costs can range from ~$50-$150/kg for Aluminum/Steel up to ~$200-$500+/kg for Titanium alloys, depending on quality, certification, and supplier. Bulk pricing for wholesale B2B orders can offer some reduction.
- Material Consumed: This includes the volume of the final part plus the volume of support structures plus any material needed for process control witnesses or destructive test coupons printed alongside the part. Efficient DfAM (topology optimization, support minimization) directly reduces material consumption.
- Powder Refresh/Recycling: While powder is recycled, there’s often a need to blend used powder with virgin powder (refresh rate) to maintain quality, which factors into the effective material cost.
- Machine Time Costs:
- Hourly Rate: AM machines represent significant capital investment, and providers charge an hourly rate for their use. Rates vary based on machine type (L-PBF vs. EBM/SEBM), size, and capabilities ($50 – $200+/hour is a rough range).
- Время сборки: This is determined by:
- Part Height (Z-axis): The primary driver, as printing is layer by layer. Taller parts take longer.
- Part Volume/Area per Layer: More volume or larger cross-sectional areas per layer require more scanning time.
- Number of Parts per Build: Nesting multiple latches efficiently on a single build plate maximizes machine utilization and reduces cost per part.
- Layer Thickness & Parameters: Thicker layers build faster but may compromise resolution and surface finish.
- Setup/Teardown Time: Labor time for preparing the machine, loading the build file, unloading the completed build, and initial cleaning.
- Расходы на оплату труда:
- Pre-Processing: Engineering time for DfAM consultation, CAD preparation, build simulation, and generating support structures.
- Machine Operation: Skilled technicians monitoring the build process.
- Post-Processing Labor: This can be substantial and includes:
- De-powdering
- Manual support removal (often time-consuming)
- Basic finishing (e.g., grinding support nubs)
- Part handling and preparation for external processes (heat treat, HIP, machining)
- Inspection labor (visual, dimensional)
- Post-Processing Costs (Specific Processes):
- Stress Relief / Heat Treatment: Cost based on furnace time, batch size, and required atmosphere (vacuum/inert gas is more expensive). NADCAP certified heat treatment commands a premium.
- Горячее изостатическое прессование (HIP): Significant cost factor due to specialized equipment and long cycle times. Costs depend on vessel size, cycle parameters, and batching efficiency. Often charged per cycle or per kilogram.
- CNC Machining: Charged based on programming time, machine setup time, machining time (complexity-dependent), tooling, and required tolerances/finishes.
- Surface Finishing/Coating: Costs vary widely depending on the method (tumbling, polishing, anodizing, painting) and specifications.
- Неразрушающий контроль (NDT): Costs depend on the method (FPI is relatively inexpensive, CT scanning can be costly), part size/complexity, and required inspection coverage.
- Quality Assurance and Certification Costs:
- Costs associated with maintaining AS9100/ISO 9001 systems, performing required material and process qualifications, generating documentation packages (FAI reports, Certificates of Conformance), and managing certified suppliers. These are often factored into overheads or charged separately.
- Overhead and Profit:
- Standard business costs including facilities, administration, engineering overhead, and the service provider’s profit margin.
Factors Influencing Lead Time:
Lead time for a 3D printed aerospace latch is the total time from order placement to part delivery and can vary significantly. It’s crucial for procurement to understand the contributing factors:
- Design Finalization & Quoting: Initial back-and-forth, DfAM review, quote generation (can take days).
- Доступность материала: Ensuring the correct certified powder batch is in stock or ordering it if necessary (can add days/weeks).
- Machine Scheduling & Queue: The provider’s backlog dictates when the build can start. Complex builds requiring specific machines might have longer queues (days to weeks).
- Actual Print Time: Can range from hours for small, single parts to multiple days for large or complex builds with many parts.
- Cooling & De-Powdering: Typically takes several hours to a day.
- Post-Processing Queue & Time:Often the biggest variable and potential bottleneck.
- Stress Relief/Heat Treat: Requires furnace scheduling, cycle time (hours to days), and cooling.
- HIP: Long cycles (often >12 hours) plus scheduling at specialized HIP facilities (can add days to weeks).
- Support Removal & Basic Finishing: Labor-dependent (hours to days).
- Machining: Depends on complexity and machine shop availability (days to weeks).
- NDT & Inspection: Scheduling and performing tests (days).
- Shipping & Logistics: Transportation time (days).
Typical Lead Time Ranges:
- Simple Prototypes (minimal post-processing): 5 – 15 working days
- Functional Prototypes (with heat treat, basic machining): 2 – 5 weeks
- Fully Qualified Production Parts (all steps including HIP, full NDT, FAI): 6 – 12+ weeks
Managing Costs and Lead Times:
- Optimize Design (DfAM): Minimizing volume and supports reduces material and print time. Designing for easier post-processing saves labor.
- Консолидация частей: Can reduce overall manufacturing and assembly time/cost, even if the AM part itself is complex.
- Nesting: Printing multiple parts per build significantly reduces per-part machine time cost. Planning for B2B batch production helps.
- Clear Specifications: Providing complete and unambiguous drawings and specifications upfront avoids delays and quoting errors. Specify only necessary tolerances and finishes.
- Partner Communication: Maintain open communication with the AM provider regarding scheduling, potential bottlenecks, and expectations.
- Realistic Planning: Build realistic timelines into project plans, especially accounting for post-processing queues.
By understanding these cost drivers and lead time components, aerospace companies can make informed decisions about adopting metal AM for fairing latches and work effectively with their chosen B2B manufacturing partners to manage budgets and schedules.
Frequently Asked Questions (FAQ) about 3D Printed Aerospace Latches
As metal additive manufacturing becomes increasingly adopted for aerospace applications, engineers, designers, and procurement professionals often have specific questions regarding the capabilities, reliability, and implementation of 3D printed components like fairing attachment latches. Here are answers to some frequently asked questions:
Q1: Are 3D printed metal latches as strong and reliable as traditionally manufactured ones (e.g., machined from billet)?
A: Yes, when designed, manufactured, and post-processed correctly, metal AM parts can meet or even exceed the mechanical properties (like tensile strength, yield strength, fatigue life) of equivalent parts made by traditional methods like machining or casting. Key factors ensuring strength and reliability include: * Material Equivalence: Starting with high-quality, certified aerospace-grade powders (e.g., Ti-6Al-4V, AlSi10Mg) ensures the base material meets specifications. * Оптимизация процессов: Using validated and tightly controlled printing parameters to achieve high density (>99.5% typical, near 100% after HIP) and sound metallurgical bonding between layers. * Microstructure Control: Appropriate heat treatments (stress relief, annealing, aging) are critical to achieving the desired microstructure and optimizing properties like strength, ductility, and fatigue resistance. * Porosity Elimination: Hot Isostatic Pressing (HIP) is often mandatory for critical aerospace AM parts, as it eliminates internal voids that could compromise fatigue life and overall integrity. * Rigorous Testing: Non-destructive testing (NDT) like CT scanning verifies internal soundness, while destructive testing of sample coupons validates material properties for each build or batch. * DfAM: Designing the part specifically for the loads it will encounter, leveraging topology optimization, ensures structural efficiency. With these measures, 3D printed latches can offer comparable or superior reliability, often with the added benefit of reduced weight and consolidated design. Partnering with an experienced aerospace AM provider with robust quality control is paramount.
Q2: What certifications are necessary for using 3D printed latches on aircraft?
A: Using any component, especially a structural one like a fairing latch, on a certified aircraft requires demonstrating compliance with stringent airworthiness regulations (e.g., FAA Part 23/25, EASA CS-23/25). This involves several layers of certification and qualification: * Supplier Quality System: The manufacturer should ideally be certified to AS9100. * Special Process Accreditation: Key post-processing steps like heat treatment and NDT usually require NADCAP accreditation for the facility performing them. * Material Specification: The powder used must meet relevant material standards (e.g., AMS specs for Ti-6Al-4V or AlSi10Mg) and be fully traceable. * Process Specification: The entire manufacturing process (printing parameters, post-processing steps) must be defined, documented, controlled, and often approved by the aircraft OEM or certification authority through a process specification. * Частичная квалификация: The specific latch design must undergo rigorous testing (static strength, fatigue, environmental testing) to demonstrate it meets all performance requirements defined by the aircraft integrator or MRO provider. This often involves a “First Article Inspection” (FAI) report and potentially specific OEM approvals. * Airworthiness Certification: Ultimately, the aircraft integrator is responsible for showing the regulatory authority (FAA/EASA) that the installed latch meets all applicable airworthiness requirements as part of the overall aircraft certification. Simply printing a part is not sufficient; a comprehensive qualification and certification package involving the designer, manufacturer, and aircraft integrator is required.
Q3: Can metal 3D printing be used for replacement or MRO (Maintenance, Repair, Overhaul) of existing latch designs?
A: Yes, metal AM holds significant promise for MRO and replacing legacy parts, but it comes with specific challenges and considerations: * Scan-to-Print: If original drawings are unavailable, existing latches can be 3D scanned to create a CAD model. However, scanning may not capture internal features perfectly, and tolerances need careful verification. Reverse engineering may be required. * Material Equivalence: The replacement part must typically be made from the same material or a certified equivalent approved for the application. If the original material is obsolete or unknown, significant engineering analysis and testing are needed to qualify a replacement AM material. * Certification Pathway: Introducing an AM part as a replacement requires a clear certification path. This might involve demonstrating equivalence to the original part (“form, fit, and function” replacement) or pursuing a Supplemental Type Certificate (STC) or other approved repair/alteration procedure. Regulatory bodies are actively developing clearer guidelines for AM parts in MRO. * Economic Viability: For low-demand legacy parts where original tooling is lost or suppliers no longer exist, AM can be highly cost-effective compared to re-tooling for traditional manufacture. * Преимущества: AM allows on-demand production of spare parts, reducing inventory holding and potentially shortening MRO turnaround times.
Q4: How does the cost of 3D printed latches compare to machined latches, especially for low-volume production?
A: The cost comparison is nuanced and depends heavily on part complexity, material, volume, and required post-processing: * Low Volume (Prototypes, 1-100 units): Metal AM is often более рентабельно than machining. This is because AM avoids the high upfront costs of custom tooling, fixtures, and complex CNC programming associated with machining intricate shapes from billet, especially with expensive materials like Titanium where machining generates significant waste. * High Volume (1000s of units): Traditional CNC machining or casting typically becomes более рентабельно as tooling costs are amortized over many parts, and machining cycle times per part can be faster than AM build times for simpler geometries. * Complexity Factor: For highly complex latches or those benefiting significantly from объединение частей, AM can remain competitive even at higher volumes because it eliminates assembly labor and simplifies the supply chain. The value of weight savings achieved through AM’s topology optimization over the aircraft’s lifetime (fuel savings) can also shift the economic balance in favor of AM, even if the initial part cost is higher (Total Cost of Ownership analysis). * Отходы материалов: AM’s lower buy-to-fly ratio is a significant cost advantage for expensive materials like Ti-6Al-4V compared to subtractive machining. In summary: AM excels for complex, low-volume, or highly optimized parts, while traditional methods are often better for simpler, high-volume parts. A detailed cost analysis based on the specific latch design and production scenario is always recommended.
Q5: What information is needed to get an accurate quote for 3D printing an aerospace fairing latch?
A: To provide an accurate quote and lead time estimate, a metal AM service provider typically needs the following information: * CAD Model: A 3D model in a standard format (e.g., STEP, IGES, STL – though STEP is preferred for manufacturing data). * Technical Drawing: A 2D drawing specifying critical dimensions, tolerances (clearly indicating as-built vs. machined tolerances), surface finish requirements (Ra values for specific surfaces), GD&T (Geometric Dimensioning and Tolerancing), and any specific inspection requirements. * Material Specification: The exact alloy required (e.g., Ti-6Al-4V Grade 5) and any required material standard (e.g., AMS 4928). * Требования к постобработке: Clearly state all required steps: stress relief/heat treatment cycle, HIP requirement, specific machining operations, surface finishing, coating specifications. * Testing & Inspection: Detail any required NDT (specify method and coverage), destructive testing requirements (e.g., tensile coupons), and documentation needs (e.g., FAI report, Certificate of Conformance, material certs). * Количество: Number of parts required (specify if prototype or production volume, allows for quoting batch production). * Required Delivery Date/Timeline: Desired lead time to assess feasibility against current capacity. * Certification Requirements: Specify required quality system (AS9100) and any special process certifications (NADCAP). Providing comprehensive information upfront enables the AM provider to give a precise quote and avoids delays caused by missing information.
Conclusion: Embracing Additive Manufacturing for Advanced Aerospace Latching Systems
The journey through the intricacies of utilizing metal additive manufacturing for aerospace fairing attachment latches reveals a technology poised to redefine how these critical components are designed, produced, and utilized. Moving beyond the constraints of traditional subtractive methods, metal AM offers a compelling suite of advantages uniquely suited to the demanding environment of aerospace. The ability to create highly complex, topology-optimized geometries allows for significant снижение веса without compromising structural integrity – a paramount goal in aircraft design translating directly to fuel efficiency and performance gains. Furthermore, the power of объединение частей, integrating multiple functions into a single printed component, not only reduces weight further but also simplifies assembly, enhances reliability by eliminating joints and fasteners, and streamlines B2B procurement and MRO logistics.
The adoption of advanced, aerospace-proven materials like Ti-6Al-4V for high-strength, high-temperature applications and AlSi10Mg for lightweight, cost-effective solutions, combined with the geometric freedom offered by AM, empowers engineers to design latches that are truly optimized for their specific function and operating environment. Realizing this potential, however, hinges on embracing Проектирование для аддитивного производства (DfAM) principles and understanding the nuances of the AM process, from build orientation strategies to post-processing requirements like heat treatment, HIP, and precision finishing.
Navigating the challenges inherent in AM – managing residual stress, ensuring thorough powder removal, achieving tight tolerances, and mitigating porosity – requires meticulous process control, advanced simulation tools, and rigorous quality assurance protocols. This underscores the absolute necessity of partnering with the right metal 3D printing service provider. The ideal partner possesses not only state-of-the-art equipment (such as Met3dp’s advanced SEBM printers and VIGA/PREP powder systems) but also deep aerospace expertise, robust quality certifications (AS9100, NADCAP for relevant processes), proven DfAM capabilities, and a commitment to transparency and collaboration.
As the technology matures, qualification processes become more standardized, and material portfolios expand, the adoption of metal AM for structural aerospace components like fairing latches will undoubtedly accelerate. It represents a key enabler for next-generation aircraft designs, offering enhanced performance, greater design flexibility, more resilient supply chains, and new possibilities for efficient MRO strategies.
For aerospace engineers and procurement managers seeking innovative solutions to complex challenges, metal additive manufacturing is no longer a futuristic concept but a tangible, powerful tool. If you are exploring the potential of 3D printing for your aerospace latching systems or other critical components, we encourage you to engage with experts in the field.
Contact Met3dp today to discuss your specific project requirements, learn more about our comprehensive additive manufacturing solutions, including industry-leading SEBM printers and high-quality metal powders, and discover how we can partner with you to accelerate your journey into the future of aerospace manufacturing. Visit our website at https://met3dp.com/ to explore our capabilities further.
Поделиться
MET3DP Technology Co., LTD - ведущий поставщик решений для аддитивного производства со штаб-квартирой в Циндао, Китай. Наша компания специализируется на производстве оборудования для 3D-печати и высокопроизводительных металлических порошков для промышленного применения.
Сделайте запрос, чтобы получить лучшую цену и индивидуальное решение для вашего бизнеса!
Похожие статьи
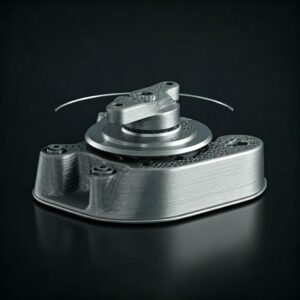
3D-печатные крепления для автомобильных радарных датчиков: Точность и производительность
Читать далее "О компании Met3DP
Последние обновления
Наш продукт
CONTACT US
Есть вопросы? Отправьте нам сообщение прямо сейчас! После получения Вашего сообщения мы всей командой выполним Ваш запрос.
Получите информацию о Metal3DP
Брошюра о продукции
Получить последние продукты и прайс-лист
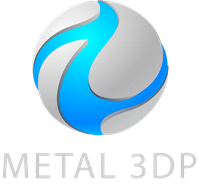
Металлические порошки для 3D-печати и аддитивного производства