3D Printed Support Rings for Jet Engine Components
Оглавление
Introduction: The Critical Role of Support Rings in Modern Jet Engines
Jet engines represent the pinnacle of complex engineering, operating under extreme conditions to generate the immense thrust required for modern flight. Within this intricate assembly of high-performance machinery, numerous components play vital roles, often unseen but absolutely critical. Among these are jet engine support rings. These are not mere static fixtures; they are essential structural elements designed to maintain the precise architecture and operational integrity of the engine throughout its demanding life cycle.
What exactly are support rings? In essence, they are annular components, typically metallic, strategically positioned within various sections of a gas turbine engine. Their primary functions include:
- Structural Support: Providing rigidity and maintaining the precise circularity and alignment of casings and other rotating or stationary components under significant aerodynamic and thermal loads.
- Load Distribution: Transferring and distributing mechanical loads between different engine modules or sections, preventing stress concentrations and ensuring structural stability.
- Component Alignment: Ensuring the accurate positioning and concentricity of adjacent components, such as compressor stages, turbine stages, and bearing assemblies, which is critical for efficiency and preventing damaging contact.
- Sealing Interfaces: Often forming part of complex sealing systems to manage airflow, prevent leakage between stages, and maintain pressure differentials, directly impacting engine performance and efficiency.
The environment within a jet engine is incredibly hostile. Support rings must withstand:
- Экстремальные температуры: Fluctuating from cryogenic temperatures on engine start-up at altitude to scorching highs exceeding 1000∘C (1832∘F) near the combustor and turbine sections.
- High Mechanical Stresses: Including tensile, compressive, and shear stresses from rotating components, pressure differentials, and vibrational loads.
- Vibrational Fatigue: Constant exposure to high-frequency vibrations inherent in engine operation.
- Corrosive Atmospheres: Potential exposure to oxidation and hot corrosion from combustion byproducts and ingested atmospheric contaminants.
Traditionally, manufacturing these critical components involved processes like forging, casting, and extensive machining from wrought materials or castings. While effective, these methods often entail long lead times, significant material waste (high buy-to-fly ratios), and limitations in geometric complexity.
This is where аддитивное производство металлов (AM), или 3D-печать, enters the picture as a transformative technology. By building parts layer by layer directly from metal powder, AM offers unprecedented opportunities to reimagine the design and production of components like support rings. This technology enables the creation of optimized, lightweight structures with enhanced performance characteristics, often using high-performance никелевые суперсплавы perfectly suited to the demanding aerospace environment. For procurement managers and engineers in the aerospace sector seeking innovative aerospace manufacturing solutions, understanding the potential of AM for producing critical компоненты реактивных двигателей like support rings is paramount.
Applications & Demands: Where are 3D Printed Support Rings Utilized?
Support rings are integral to nearly every major section of a modern turbofan or turbojet engine. Their specific design and material requirements vary depending on their location and function, but the need for reliability under extreme conditions is universal. Understanding these specific аэрокосмические приложения highlights why advanced manufacturing techniques and materials are crucial.
Here are key areas where support rings are utilized within a jet engine:
- Fan Section: While operating at lower temperatures than the core, support rings here maintain the structure around the large fan blades and initial compressor stages, ensuring alignment and managing loads from bird strikes or blade-out events.
- Compressor Section:
- Compressor Case Rings: These rings provide structural rigidity to the compressor casing, maintaining tight clearances between blade tips and the casing wall for optimal compression efficiency. They must withstand significant pressure differentials and mechanical loads.
- Stator Vane Support Rings: Locate and secure rows of stationary stator vanes that direct airflow between rotating compressor stages. Precise alignment is crucial for aerodynamic performance.
- Combustor Section:
- Combustor Casing Supports: Rings in this area must endure extremely high temperatures radiating from the combustion process while maintaining the structural integrity of the combustor liner and outer casing. Thermal management and resistance to thermal fatigue are critical.
- Fuel Nozzle Guides/Supports: Rings may be used to precisely locate and support fuel nozzle assemblies, ensuring proper fuel delivery and mixing.
- Turbine Section: This is arguably the most demanding environment.
- Turbine Frame/Case Rings: These support rings form the backbone of the turbine section, bearing significant structural loads and operating at very high temperatures. They must resist creep deformation under sustained stress and heat.
- Nozzle Guide Vane (NGV) Support Rings: Similar to stator vane supports in the compressor, these rings locate the NGVs that direct the hot gas flow onto the turbine blades. They face the highest temperatures in the engine and require materials with exceptional high-temperature strength and oxidation resistance.
- Bearing Support Rings: Critical rings that locate and support the main shaft bearings (e.g., roller and ball bearings). They must maintain precise dimensions and alignment under heavy loads and high rotational speeds across a wide temperature range. Misalignment here can lead to catastrophic engine failure.
- Exhaust Section: Support rings maintain the structure of the exhaust nozzle and related components, facing high temperatures and vibrational loads.
Key Demands on Jet Engine Support Rings:
Demand Category | Specific Challenges | Why AM is Relevant |
---|---|---|
Терморегулирование | Extreme temperature gradients, thermal cycling fatigue, creep at high temperatures. | AM allows integration of complex cooling channels or heat-dissipating geometries not possible with traditional methods. |
Structural Integrity | High mechanical loads (tensile, compressive), pressure differentials, vibration. | Topology optimization via AM can create stiffer, stronger structures for the same weight, or significantly lighter ones. |
Устойчивость размеров | Maintaining precise tolerances and circularity across wide temperature ranges. | AM processes, combined with post-process machining, can achieve tight tolerances. Material choice is critical. |
Сопротивление усталости | High-cycle fatigue from vibration, low-cycle fatigue from thermal cycles. | AM allows optimized designs minimizing stress concentrations. High-quality AM materials (like IN718/IN625) offer excellent fatigue life. |
Коррозионная стойкость | Oxidation and hot corrosion from combustion gases and environment. | Nickel superalloys like IN718 and IN625 offer inherent resistance, crucial for longevity in harsh engine environments. |
Снижение веса | Constant drive to reduce overall engine weight for fuel efficiency (thrust-to-weight ratio). | AM enables lightweight lattice structures and optimized geometries, significantly reducing component weight. |
Export to Sheets
Meeting these multifaceted demands requires not only advanced materials but also manufacturing processes capable of producing complex, reliable parts. Procurement managers involved in aerospace parts procurement must consider suppliers who can reliably meet these stringent requirements, making advanced Услуги 3D-печати по металлу an increasingly attractive option.
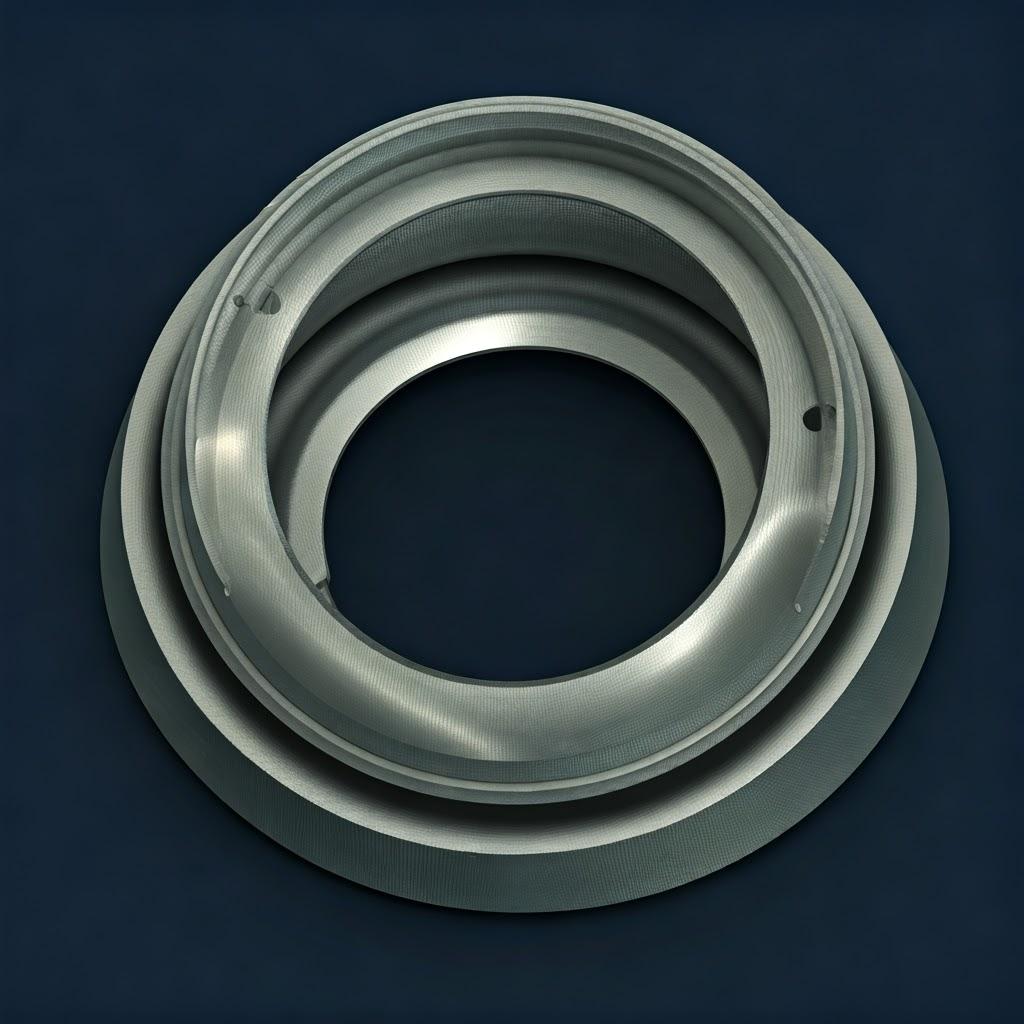
Additive Advantage: Why Choose Metal 3D Printing for Jet Engine Support Rings?
While traditional manufacturing methods have served the aerospace industry well for decades, аддитивное производство металлов offers a compelling suite of advantages, particularly for complex, high-value components like jet engine support rings. Opting for AM isn’t just about adopting a new technology; it’s about unlocking tangible benefits in performance, cost, and supply chain efficiency. Key metal 3D printing benefits for these components include:
- Design Freedom & Optimization: This is perhaps the most significant advantage. AM liberates designers from the constraints of traditional manufacturing (e.g., draft angles for casting, tool access for machining).
- Topology Optimization: Algorithms can determine the most efficient material distribution to withstand specific load paths, resulting in organically shaped, highly optimized structures that are significantly lighter yet meet or exceed stiffness requirements.
- Сложные геометрии: Intricate internal channels for cooling or fluid flow, complex mounting interfaces, and fine features can be built directly into the part.
- Консолидация частей: Multiple components previously manufactured separately and then assembled (via welding or fasteners) can often be redesigned and printed as a single, monolithic part. This reduces part count, assembly time, potential leak paths, and failure points.
- Облегчение: Weight reduction is a primary driver in aerospace. By enabling topology optimization and the use of internal lattice structures, AM can produce support rings that are 10-50% lighter than their traditionally manufactured counterparts without compromising structural integrity. This directly translates to improved fuel efficiency and increased payload capacity.
- Сокращение сроков изготовления: Traditional manufacturing often involves long lead times associated with tooling (e.g., creating molds or forging dies), complex machining setups, and assembly processes.
- Tooling Elimination: AM builds parts directly from a CAD file, eliminating the time and cost associated with tool production.
- Faster Prototyping & Iteration: Design modifications can be implemented quickly by simply changing the digital file, allowing for rapid iteration and testing cycles.
- Производство по требованию: Parts can be produced closer to the point of need, reducing inventory requirements and enabling faster response to demand fluctuations or AOG (Aircraft on Ground) situations.
- Эффективность материала: AM processes, particularly Powder Bed Fusion (PBF) techniques like Selective Laser Melting (SLM) and Selective Electron Beam Melting (SEBM), are near-net-shape processes.
- Reduced Buy-to-Fly Ratio: Significantly less raw material is used compared to subtractive machining, where much of the initial billet or forging becomes scrap. While some support material is needed in AM, the overall material utilization is often much higher.
- High-Value Material Savings: This is particularly impactful when working with expensive nickel superalloys like IN718 and IN625.
- Supply Chain Optimization: AM enables a more agile and resilient supply chain.
- Digital Inventory: Designs can be stored digitally and printed on demand, reducing physical inventory needs.
- Distributed Manufacturing: Parts can potentially be printed at certified facilities closer to the point of assembly or maintenance, reducing shipping costs and times.
Такие компании, как Met3dp are at the forefront of leveraging these advantages for critical industrial applications. Specializing in both advanced металлическая 3D-печать equipment (including industry-leading SEBM printers known for accuracy and reliability) and high-performance metal powders, Met3dp provides comprehensive solutions tailored for demanding sectors like aerospace. Their focus on producing mission-critical parts underscores the maturity and capability of AM technology for applications like jet engine support rings. Choosing an experienced aerospace components supplier proficient in AM, like Met3dp, can unlock significant performance and economic benefits.
Comparison: AM vs. Traditional Manufacturing for Support Rings
Характеристика | Metal Additive Manufacturing (e.g., SEBM/SLM) | Traditional Manufacturing (e.g., Forging + Machining) | Advantage of AM |
---|---|---|---|
Сложность конструкции | High (internal channels, topology optimization, lattices) | Moderate to Low (limited by tooling & machining access) | Enables optimized performance, lightweighting, part consolidation. |
Время выполнения заказа | Short to Moderate (no hard tooling, faster iteration) | Long (tooling design & production, long machining cycles) | Faster time-to-market, rapid prototyping, supply chain agility. |
Материальные отходы | Low (near-net shape, powder recyclability) | High (significant material removal during machining) | Reduced raw material cost, better sustainability (especially for expensive alloys). |
Консолидация частей | High potential (combining multiple parts into one) | Low potential (requires assembly steps) | Reduced assembly time/cost, fewer joints/failure points, potential weight savings. |
Первоначальная стоимость оснастки | Никто | High (forging dies, casting molds) | Economical for low-to-mid volume production and complex parts. |
Облегчение | Excellent potential via optimized design | Limited potential (primarily through material choice) | Significant improvements in fuel efficiency and performance. |
Export to Sheets
While AM offers numerous benefits, it’s important to note that post-processing (like heat treatment and finish machining) is often still required to meet the final stringent aerospace specifications for tolerances and surface finish. However, the overall advantages in design, speed, and material utilization make AM a compelling choice for manufacturing the next generation of jet engine support rings.
Material Focus: IN718 & IN625 Nickel Superalloys for Demanding Aerospace Needs
The selection of the right material is absolutely critical for components operating within the extreme environment of a jet engine. For support rings, which must maintain structural integrity under intense heat, stress, and potential corrosion, суперсплавы на основе никеля are the materials of choice. Among the most widely used and proven superalloys in aerospace additive manufacturing are Inconel® 718 (IN718) и Inconel® 625 (IN625).
These alloys are renowned for their exceptional combination of properties, making them ideal candidates for 3D printing demanding parts like support rings:
- High Temperature Strength: They retain significant mechanical strength and resist creep deformation even at elevated temperatures commonly found in the turbine and combustor sections.
- Отличная коррозионная стойкость: The high chromium and nickel content provides outstanding resistance to oxidation and various forms of corrosion encountered in combustion environments.
- Good Fatigue Life: They exhibit excellent resistance to both high-cycle and low-cycle fatigue, crucial for durability under the vibrational and thermal cycling loads in an engine.
- Weldability/Printability: Both alloys, particularly IN718, generally exhibit good processability in laser and electron beam powder bed fusion systems, allowing for the production of dense, defect-free parts.
Let’s compare some key properties relevant for IN718 3D printing и IN625 aerospace applications:
Comparison of IN718 and IN625 Properties (Typical Values for AM Parts after Heat Treatment)
Недвижимость | Инконель 718 (IN718) | Инконель 625 (IN625) | Significance for Support Rings |
---|---|---|---|
Первичные легирующие элементы | Ni, Cr, Fe, Nb+Ta, Mo, Ti, Al | Ni, Cr, Mo, Nb+Ta, Fe | Determine phase structure, strengthening mechanisms, and corrosion resistance. |
Strengthening Mechanism | Precipitation Hardening (γ′, γ′′ phases) | Укрепление твердых растворов | IN718 generally offers higher strength, especially after appropriate heat treatment. |
Max Operating Temp. | ~ 650−700∘C (1200−1300∘F) | ~ 815∘C (1500∘F), higher in some conditions | IN625 typically preferred for hotter sections due to better high-temp strength & creep resistance. |
Tensile Strength (RT) | ~ 1200−1400MPa (175−200ksi) | ~ 830−1000MPa (120−145ksi) | High strength needed to handle mechanical loads. IN718 stronger at lower temps. |
Tensile Strength (650°C) | ~ 1000−1150MPa (145−165ksi) | ~ 700−850MPa (100−125ksi) | Critical for maintaining integrity at operating temperatures. IN718 retains strength well. |
Сопротивление ползучести | Хороший | Отличный | Resistance to deformation under sustained load/heat. IN625 often excels here. |
Коррозионная стойкость | Очень хорошо | Excellent (especially pitting/crevice corrosion) | Protects against oxidation and harsh chemical environments within the engine. |
Возможность печати | Generally Good | Good (can be slightly more prone to cracking if parameters aren’t optimized) | Determines ease of processing and quality achievable via AM. |
Термообработка | Required (Solution + Precipitation Hardening) | Typically Stress Relief (or Solution Anneal) | IN718 requires complex heat treatment for full properties; IN625 is simpler. |
Export to Sheets
Why these Properties Matter for Support Rings:
- Соотношение прочности и веса: While dense materials, their high strength allows for optimized, lighter designs compared to using steels or titanium alloys in high-temperature zones.
- Сопротивление ползучести: Prevents the ring from slowly deforming over time under load at high temperatures, which could lead to loss of clearance control or component misalignment. IN625’s advantage here makes it suitable for the hottest sections near the turbine inlet.
- Fatigue Life: Ensures the ring can withstand millions of stress cycles from vibration and thermal expansion/contraction without failing.
- Устойчивость к окислению: Prevents material degradation and thinning due to high-temperature reactions with oxygen, ensuring the ring maintains its structural integrity throughout the engine’s service life.
The Importance of Powder Quality:
The final properties and reliability of an AM support ring are heavily dependent on the quality of the metal powder used. Met3dp understands this critical link and employs industry-leading powder production technologies, including Vacuum Induction Melting Gas Atomization (VIGA) и Плазменный вращающийся электродный процесс (PREP). These advanced methods allow Met3dp to manufacture высококачественные металлические порошки, including IN718 and IN625, characterized by:
- Высокая сферичность: Ensures excellent powder flowability, leading to uniform powder bed layers during printing.
- Low Porosity: Minimizes internal voids within the powder particles.
- Controlled Particle Size Distribution (PSD): Optimized PSD for specific AM processes (like SEBM or L-PBF) ensures high packing density and stable melting behavior.
- Высокая чистота: Low levels of impurities (like oxygen and nitrogen) prevent defects in the final part and ensure optimal mechanical properties.
By utilizing premium Met3dp metal powders, manufacturers can achieve denser, stronger, and more reliable 3D printed support rings, meeting the stringent demands of the aerospace industry. Partnering with a supplier like Met3dp, who controls both the advanced powder manufacturing and the способы печати, provides a vertically integrated solution ensuring quality from raw material to final component.
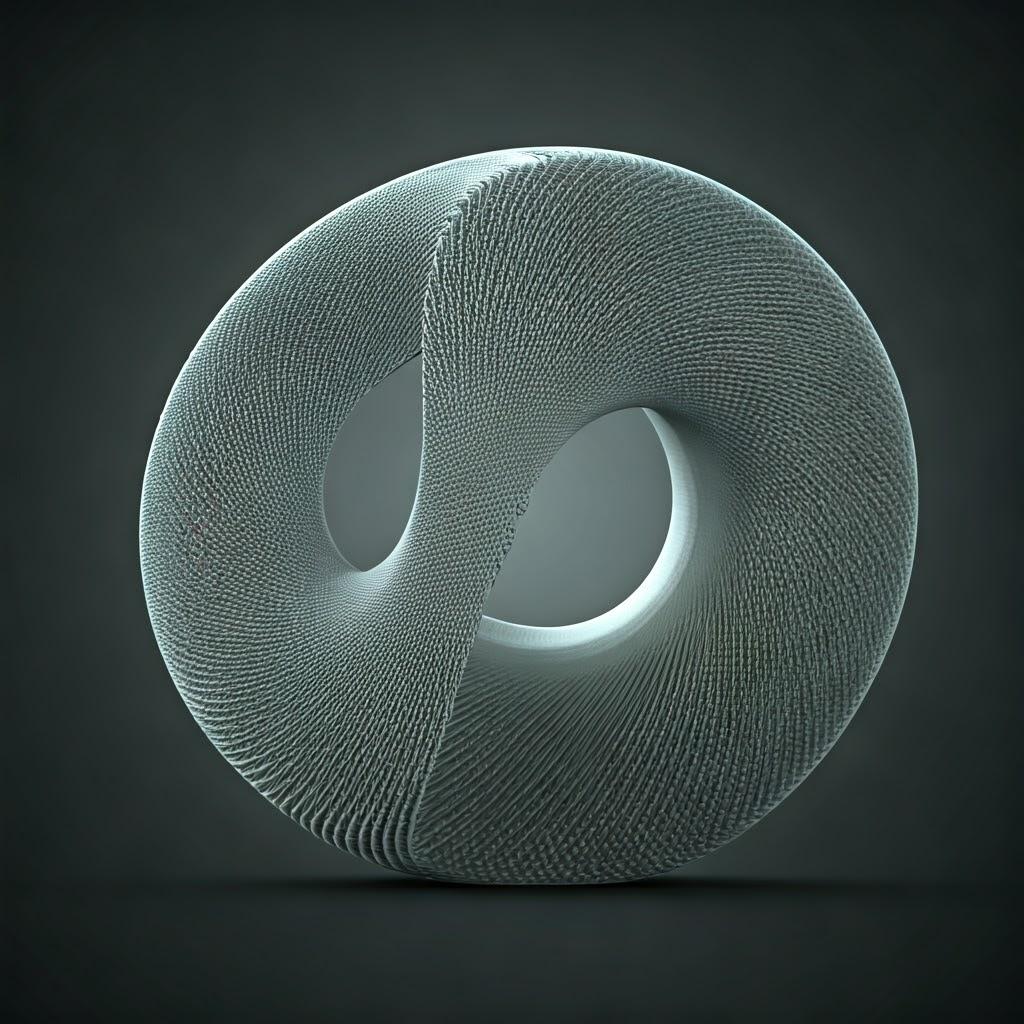
Design for Additive Manufacturing (DfAM): Optimizing Support Rings for 3D Printing
Successfully leveraging metal additive manufacturing for components like jet engine support rings requires more than simply converting an existing CAD file designed for traditional methods. To truly unlock the benefits of AM – particularly lightweighting, performance enhancement, and cost efficiency – engineers must embrace Проектирование для аддитивного производства (DfAM) principles. DfAM is a mindset shift, moving from subtractive constraints (what material can be removed) to additive possibilities (where material needs to be placed). Applying DfAM aerospace strategies is crucial for optimizing support ring design.
Key DfAM considerations for 3D printed support rings include:
- Build Orientation Strategy: How the part is oriented on the build plate significantly impacts:
- Поддерживающие структуры: Affects the amount and location of required supports. Vertical walls generally need fewer supports than horizontal overhangs.
- Отделка поверхности: Up-facing and down-facing surfaces often have different roughness values. Critical surfaces might dictate orientation.
- Время сборки: Taller builds generally take longer.
- Механические свойства: AM parts can exhibit some degree of anisotropy (properties varying with direction). Orientation should align critical stress paths with the strongest build direction if possible, although heat treatment often mitigates this significantly for IN718/IN625.
- Тепловое управление: Orientation affects heat distribution and dissipation during the build, influencing residual stress.
- Self-Supporting Angles & Overhangs: Most metal PBF processes can build overhangs reliably up to a certain angle from the horizontal (typically around 45 degrees) without supports. Designing features like chamfers instead of sharp horizontal edges can drastically reduce the need for support structure design AM.
- Support Minimization & Accessibility: While sometimes necessary, support structures add material cost, print time, and significant post-processing effort for removal.
- Clever design choices can minimize reliance on supports.
- Where supports are unavoidable, ensure they are accessible for easy removal without damaging the part’s functional surfaces. Avoid designing features that require extensive internal supports that are difficult or impossible to reach.
- Topology Optimization & Generative Design: These computational tools are powerful allies in DfAM.
- Topology Optimization: Starts with a design space and load conditions, then algorithmically removes material where it’s not needed, resulting in highly efficient, often organic-looking structures optimized for stiffness-to-weight. This is ideal for lightweighting support rings.
- Generative Design: Explores multiple design solutions based on defined constraints (loads, materials, manufacturing methods, cost), offering engineers various optimized options.
- Lattice Structures & Infill: For non-critical sections or to achieve specific stiffness or vibration damping properties, internal lattice structures can replace solid material, significantly reducing weight and material consumption.
- Feature Consolidation: Integrate brackets, mounting bosses, sensor housings, or fluidic channels directly into the support ring design. This reduces part count, eliminates assembly steps (like welding or fastening), minimizes potential leak paths, and often improves overall structural integrity.
- Thermal Management Features: If the support ring operates in an extremely hot zone or requires active cooling, AM allows for the seamless integration of complex internal cooling channels or conformal cooling passages that would be impossible or prohibitively expensive to machine conventionally.
- Designing for Post-Processing: DfAM isn’t just about the printing process; it must consider downstream steps.
- Machining Allowances: Add extra material (e.g., 0.5-2mm) to surfaces requiring tight tolerances or specific finishes, which will be achieved via final CNC machining.
- Inspection Access: Ensure critical features are accessible for measurement (CMM probes) and non-destructive testing (e.g., FPI access to surfaces).
- Handling Features: Consider adding temporary features to aid in handling the part during post-processing, which can be removed later.
By thoughtfully applying these DfAM principles, engineers can design support rings that are not only manufacturable via AM but are also lighter, stronger, and potentially more functional than their traditional counterparts. Collaborating with an experienced AM provider like Met3dp early in the design phase can provide valuable insights into optimizing parts for their specific AM processes (like SEBM) and materials (IN718/IN625).
Achieving Precision: Tolerances, Surface Finish, and Dimensional Accuracy in AM Support Rings
For critical aerospace components like jet engine support rings, meeting stringent dimensional requirements is non-negotiable. Engineers and procurement managers often raise valid questions about the precision achievable with metal additive manufacturing. Understanding the capabilities and limitations regarding metal 3D printing tolerances, surface finish, and overall dimensional accuracy aerospace standards is key.
Tolerances:
- As-Printed Tolerances: Metal AM processes like L-PBF and SEBM typically achieve dimensional tolerances in the range of ±0.1 mm to ±0.3 mm (±0.004” to ±0.012”) for smaller features, potentially widening slightly for larger dimensions due to thermal effects. SEBM, operating at higher temperatures, often exhibits lower residual stress but might have slightly looser as-printed tolerances than L-PBF initially.
- Factors Influencing Tolerances: Machine calibration, laser/electron beam spot size, layer thickness, powder characteristics, scan strategy, thermal stresses during the build, and part geometry all play a role.
- Post-Machined Tolerances: For critical interfaces, diameters, and sealing surfaces requiring tighter control, post-print CNC machining is standard practice. Tolerances achievable after machining are comparable to traditional methods, often reaching ±0.01 mm to ±0.05 mm (±0.0004” to ±0.002”) or better, depending on the specific requirements. DfAM principles should incorporate necessary machining allowances on these critical features.
Обработка поверхности (шероховатость):
- As-Printed Surface Finish (Ra): The surface roughness of as-printed metal AM parts is generally higher than machined surfaces.
- L-PBF: Typically produces Ra values ranging from 6 µm to 15 µm (240 µin to 590 µin).
- SEBM: Often results in a rougher finish, potentially Ra 20 µm to 35 µm (790 µin to 1380 µin), due to larger powder particles and higher energy input, although process advancements are improving this.
- Factors Influencing Surface Finish: Layer thickness (thinner layers = smoother finish), particle size distribution of the powder, energy input, and surface orientation (up-facing, down-facing, and vertical walls have different roughness characteristics). Down-facing surfaces relying on supports tend to be the roughest.
- Achieving Smoother Finishes: When smoother surfaces are required (e.g., for aerodynamic reasons, sealing faces, fatigue-critical areas), post-processing steps like machining, grinding, polishing, abrasive flow machining (AFM), or electro-chemical polishing are employed. Shot peening can also be used, which improves fatigue life even if it doesn’t drastically reduce Ra.
Dimensional Accuracy & Stability:
- Warpage and Shrinkage: The rapid heating and cooling inherent in AM processes create thermal gradients, leading to internal stresses. If not properly managed, these stresses can cause warping during the build or distortion after removal from the build plate. Material shrinkage upon cooling also needs to be compensated for.
- Mitigation Strategies:
- Process Simulation: Software tools predict thermal behavior and distortion, allowing for adjustments to orientation or support strategies before printing.
- Optimized Scan Strategies: Specific patterns for melting the powder (e.g., island scanning) help distribute heat more evenly.
- Build Plate Heating: Maintaining an elevated temperature (especially in SEBM) reduces thermal gradients.
- Stress Relief Heat Treatment: Performed before removing the part from the build plate, this crucial step reduces internal stresses.
- Robust Support Structures: Well-designed supports anchor the part firmly during printing.
- Verification: Ensuring the final part meets specifications requires meticulous inspection using tools like Coordinate Measuring Machines (CMM) and 3D laser scanning.
Achieving consistent precision relies heavily on the quality and calibration of the AM equipment and the expertise of the service provider. Met3dp, for instance, emphasizes the industry-leading print volume, accuracy and reliability of their SEBM printers, developed through decades of collective expertise in metal additive manufacturing. This focus on reliable equipment and process control is fundamental to producing aerospace support rings that meet demanding dimensional requirements.
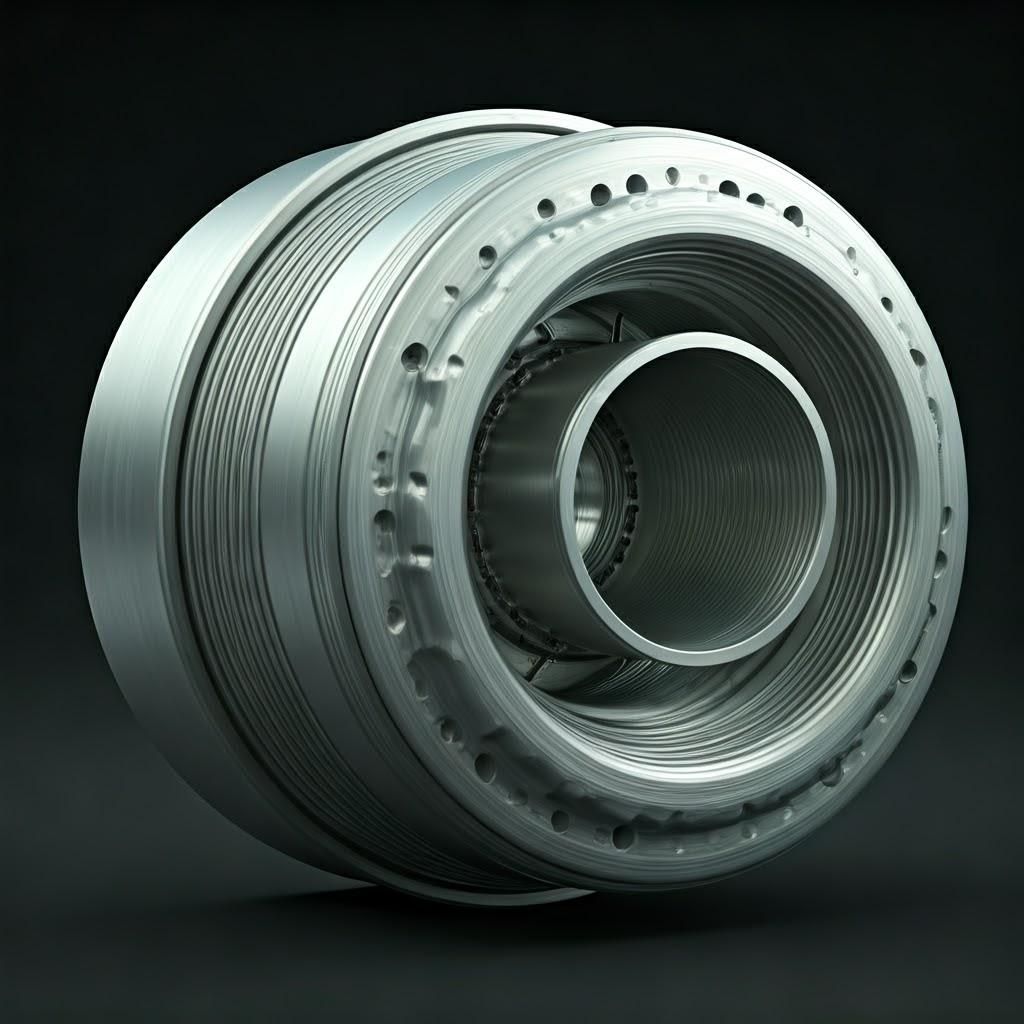
Beyond the Print: Essential Post-Processing Steps for Aerospace Support Rings
A common misconception about metal 3D printing is that parts come out of the machine ready to use. For demanding applications, especially in aerospace, the printing process is just one step in a comprehensive workflow. Metal AM post-processing is critical to achieving the required material properties, dimensional accuracy, surface finish, and overall integrity for components like jet engine support rings. Expect a multi-stage process managed by experienced technicians and potentially specialized aerospace parts finishing suppliers.
The typical post-processing workflow for an AM IN718 or IN625 support ring includes:
- Снятие стресса:
- Цель: To reduce the internal stresses built up during the rapid heating and cooling cycles of the printing process, minimizing the risk of distortion or cracking when the part is removed from the build plate.
- Процесс: Typically performed while the part is still attached to the build plate in a vacuum or inert atmosphere furnace. Temperatures and times depend on the alloy and part geometry (e.g., for IN718, ~ 1065∘C for 1 hour might be used, but varies).
- Part Removal from Build Plate:
- Цель: To separate the printed component(s) from the base plate they were built upon.
- Процесс: Commonly done using wire Electrical Discharge Machining (EDM) or a bandsaw. Care must be taken to avoid damaging the part.
- Демонтаж опорной конструкции:
- Цель: To remove the temporary structures used to anchor the part and support overhangs during printing.
- Процесс: This can be labor-intensive. Methods include manual breaking/cutting (for accessible supports), CNC machining, grinding, or sometimes specialized electrochemical or abrasive flow methods for internal or hard-to-reach supports. Ease of removal is heavily influenced by DfAM.
- Термообработка:
- Цель: Crucial for developing the final, desired microstructure and mechanical properties (strength, hardness, creep resistance) of the superalloy.
- Процесс: Specific cycles depend on the alloy and desired properties.
- IN718: Typically requires a multi-step process involving solution treatment followed by a two-stage precipitation hardening (aging) cycle (e.g., Solution at ~980∘C, Age 1 at ~720∘C, Age 2 at ~620∘C). This develops the strengthening gamma prime (γ′) and gamma double prime (γ′′) phases. AMS standards dictate specific cycles.
- IN625: Often used after a solution anneal or simply requires stress relief, as it’s primarily solid-solution strengthened. Specific heat treatments can optimize certain properties if needed.
- Окружающая среда: Heat treatments are performed in precisely controlled vacuum or inert atmosphere furnaces to prevent oxidation.
- Hot Isostatic Pressing (HIP) – Optional but Common for Critical Parts:
- Цель: To close any residual internal microporosity that might remain after printing, improving fatigue life, ductility, and overall material integrity. Often mandated for critical rotating or structurally significant aerospace parts.
- Процесс: Subjects the part to high temperature (below melting point) and high isostatic pressure (using an inert gas like Argon) simultaneously in a specialized vessel.
- Final Machining / Finishing:
- Цель: To achieve tight tolerances on critical dimensions (mating faces, diameters, sealing surfaces) and specified surface finishes.
- Процесс: Utilizes conventional CNC machining (milling, turning), grinding, or other precision finishing techniques. Requires careful setup to handle potentially complex AM geometries.
- Обработка поверхности:
- Цель: To enhance surface properties like wear resistance, fatigue life, or smoothness.
- Процесс: May include shot peening (induces compressive residual stresses, improving fatigue life), polishing, abrasive blasting, or specialized coatings depending on the application requirements.
- Cleaning & Inspection:
- Цель: To ensure the part is clean and meets all specifications.
- Процесс: Thorough cleaning to remove any machining fluids, debris, or residual powder. Final inspection includes dimensional verification (CMM, scanning) and Non-Destructive Testing (NDT) like Fluorescent Penetrant Inspection (FPI) for surface defects, X-ray or CT scanning for internal defects.
Understanding this comprehensive post-processing chain is vital for procurement managers and engineers when planning projects and evaluating suppliers. Lead times and costs associated with these steps must be factored into the overall production plan.
Navigating Challenges: Overcoming Hurdles in 3D Printing Support Rings
While metal additive manufacturing offers significant advantages, producing high-integrity aerospace components like support rings is not without its challenges. Awareness of these potential metal AM challenges and the strategies employed by experienced providers to overcome them is crucial for ensuring successful outcomes.
Common hurdles and mitigation strategies include:
- Residual Stress and Warpage:
- Вызов: High thermal gradients during printing can lead to significant internal stresses, potentially causing the part to warp on the build plate or distort after removal.
- Mitigation:
- Thermal Simulation: Predicting stress accumulation before printing.
- Optimized Scan Strategies: Using techniques like island scanning or rotating scan vectors to manage heat input.
- Build Plate Heating: Maintaining elevated temperatures (inherent in SEBM, controllable in L-PBF) reduces gradients.
- Effective Support Structures: Anchoring the part securely.
- Post-Build Stress Relief: Essential step before part removal.
- Контроль пористости:
- Вызов: Small voids or pores can form within the printed material due to trapped gas, incomplete fusion between layers, or powder quality issues. Porosity degrades mechanical properties, particularly fatigue life.
- Mitigation:
- Оптимизация параметров процесса: Dialing in laser/electron beam power, scan speed, layer thickness, and hatching parameters for the specific material and machine.
- High-Quality Powder: Using powder with low internal gas porosity, controlled PSD, and high flowability (like the powders produced by Met3dp using advanced atomization).
- Inert Atmosphere Control: Maintaining a high-purity inert gas environment (Argon or Nitrogen) in the build chamber to minimize oxidation and contamination.
- Горячее изостатическое прессование (HIP): Effectively closes internal pores post-print.
- Демонтаж опорной конструкции:
- Вызов: Supports, especially internal or intricate ones, can be very difficult and time-consuming to remove without damaging the part surface.
- Mitigation:
- DfAM: Designing parts to be self-supporting where possible or ensuring supports are placed in accessible locations.
- Optimized Support Design: Using support types (e.g., thin-walled, easily breakable) that are easier to remove.
- Specialized Removal Techniques: Employing appropriate mechanical, machining, or chemical methods.
- Отделка поверхности:
- Вызов: As-printed surfaces are relatively rough compared to machined finishes, which may not be acceptable for certain aerodynamic or sealing applications.
- Mitigation:
- Parameter Optimization: Fine-tuning parameters can improve finish to some extent.
- Orientation Planning: Positioning critical surfaces optimally during build setup.
- Постобработка: Incorporating steps like CNC machining, polishing, or abrasive flow machining for critical surfaces.
- Анизотропия:
- Вызов: Mechanical properties can sometimes vary depending on the direction relative to the build layers (X, Y vs. Z).
- Mitigation:
- Оптимизация процессов: Achieving near-fully dense parts minimizes anisotropy.
- Термообработка: Appropriate heat treatment cycles for alloys like IN718 significantly homogenize the microstructure, reducing directional property variations.
- Design Consideration: Aligning the most critical stress directions with favorable build orientations if significant anisotropy is expected.
- Quality Assurance and Consistency:
- Вызов: Ensuring that every part produced meets the same stringent aerospace standards requires rigorous process control and monitoring. Quality assurance aerospace AM имеет первостепенное значение.
- Mitigation:
- Robust Quality Management System (QMS): Implementing systems compliant with aerospace standards like AS9100.
- Material Traceability: Tracking powder batches from source to final part.
- Мониторинг в процессе работы: Using sensors to monitor melt pool characteristics, temperature, oxygen levels, etc.
- Regular Machine Calibration & Maintenance: Ensuring equipment performs consistently.
- Comprehensive NDT and Metrology: Verifying part integrity and dimensional accuracy.
Successfully navigating these challenges requires deep expertise in materials science, AM process physics, and aerospace quality requirements. Partnering with a knowledgeable and well-equipped service provider is key. Companies like Met3dp, detailed further on their О нас page, invest heavily in technology and expertise to address these challenges, offering reliable additive manufacturing solutions for demanding applications. Their range of capabilities can be explored further via their страница продукта.
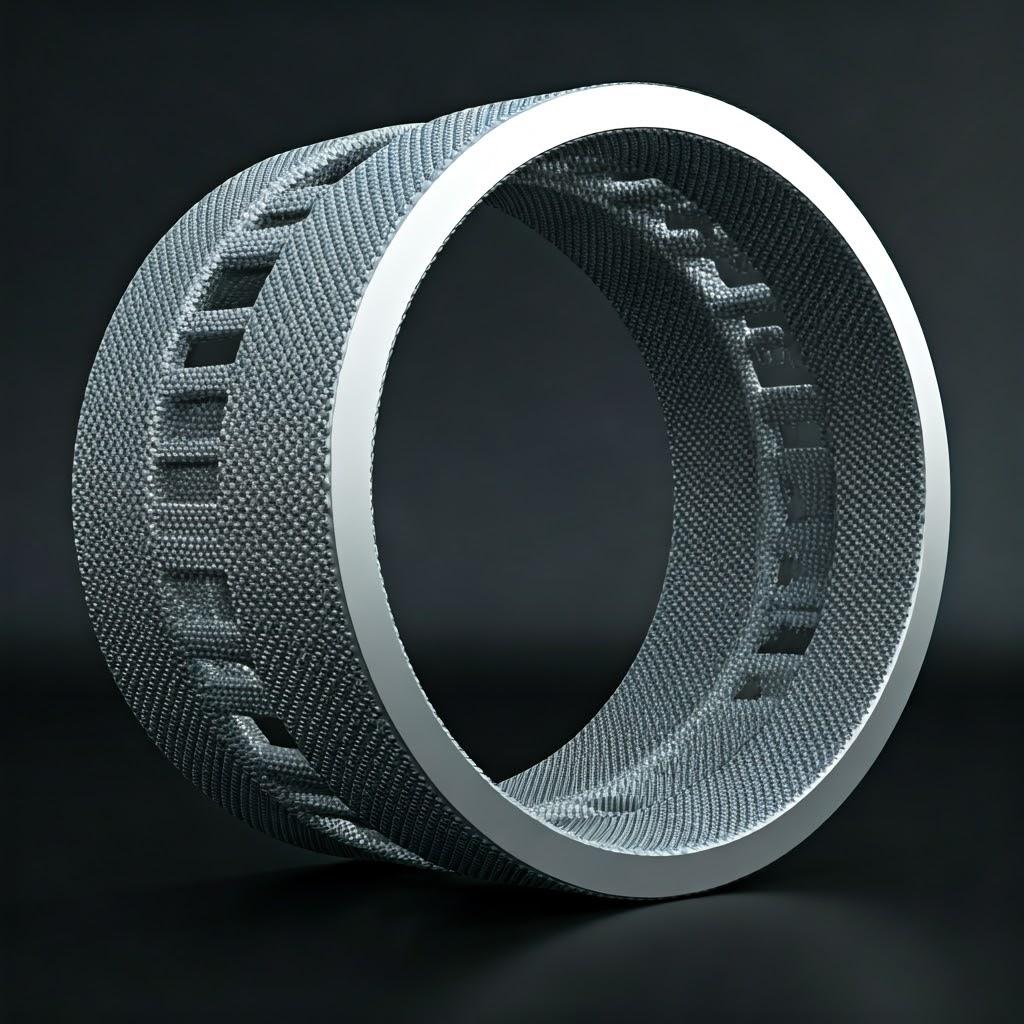
Supplier Selection: Choosing the Right Metal AM Partner for Aerospace Components
The success of implementing 3D printed support rings hinges significantly on the capabilities and reliability of your additive manufacturing partner. Selecting the right metal 3D printing services aerospace provider is a critical decision for engineers and procurement managers. Given the stringent requirements of the aerospace industry, the vetting process must be thorough. Look beyond simple printing capabilities and evaluate potential suppliers based on a comprehensive set of criteria:
- Aerospace Certifications: This is non-negotiable for flight-critical components.
- AS9100: This is the internationally recognized Quality Management System (QMS) standard for the aerospace industry. Certification demonstrates a supplier’s commitment to quality, traceability, and continuous improvement specific to aerospace requirements. Ensure the supplier’s certification scope covers additive manufacturing processes.
- Nadcap: While AS9100 covers the overall QMS, Nadcap accreditation may be required for specific special processes the supplier performs internally (e.g., heat treatment, non-destructive testing, materials testing). Verify if these are needed and if the supplier holds the relevant accreditations.
- Proven Aerospace Experience: Look for a certified aerospace supplier with a demonstrated track record in manufacturing aerospace components, particularly those involving similar complexities, materials (IN718, IN625), and operating environments. Ask for case studies, references, or examples of previous work relevant to jet engine applications.
- Экспертиза материалов: Deep knowledge of the specific superalloys is crucial. The supplier should understand:
- Optimal AM process parameters for IN718 and IN625 to achieve dense, defect-free parts.
- Powder handling and recycling protocols to maintain material integrity and traceability.
- Required post-processing, especially the intricacies of heat treatment cycles for IN718 precipitation hardening.
- Material testing and characterization capabilities. Suppliers like Met3dp, who manufacture their own high-quality aerospace-grade powders, possess inherent material expertise.
- Equipment Capability and Capacity:
- Технология: Do they operate the right type of machines (e.g., SEBM, L-PBF) for your specific needs? SEBM, offered by Met3dp, is often favored for nickel superalloys due to its heated build environment reducing residual stress.
- Объем сборки: Can their machines accommodate the size of your support rings?
- Machine Condition & Calibration: Are the machines well-maintained and regularly calibrated for accuracy and consistency?
- Capacity: Do they have sufficient machine availability to meet your required lead times and potential production volumes?
- Robust Quality Management System (QMS): Beyond certification, assess the practical implementation of their QMS. This includes documented procedures for every step, rigorous process controls, in-process monitoring, meticulous record-keeping, and full material traceability from powder batch to final shipped part.
- Comprehensive Post-Processing Capabilities: Determine if they handle critical post-processing steps (stress relief, heat treatment, HIP, final machining, NDT) in-house or through a network of qualified and approved subcontractors. Seamless management of this entire workflow is essential.
- Engineering and Application Support: Valuable partners offer more than just printing. Look for engineering support, including:
- DfAM Expertise: Ability to review designs and suggest optimizations for additive manufacturing.
- Process Simulation: Capabilities to predict and mitigate potential issues like distortion.
- Application Development: Experience in translating requirements into successful AM components. Met3dp, for example, provides comprehensive solutions spanning printers, powders, and услуги по разработке приложений.
- Transparency and Communication: Choose a partner who communicates clearly and proactively regarding project status, potential challenges, and quality documentation.
Choosing a supplier is establishing a partnership, especially for critical aerospace components. A thorough audit and clear technical discussions are essential before committing to a metal AM provider.
Understanding Investment: Cost Factors and Lead Times for AM Support Rings
While additive manufacturing offers long-term value through performance gains and design optimization, understanding the direct metal 3D printing cost and associated AM production timeline is crucial for project planning and budgeting. Several factors influence the final price and delivery schedule for 3D printed jet engine support rings:
Факторы стоимости:
Cost Driver | Пояснение | Impact Level |
---|---|---|
Стоимость материала | Nickel superalloy powders (IN718, IN625) are inherently expensive. The primary driver is the volume/weight of the final part plus supports. | Высокая |
Machine Time | Calculated based on the build height (number of layers) and the area to be scanned per layer. Includes machine depreciation and operational costs. | Высокая |
Labor Costs | Includes machine setup, build monitoring, part removal, extensive post-processing (support removal, finishing), and quality inspection. | Средний и высокий |
Сложность деталей | Highly complex geometries may require more intricate support structures (longer print time, difficult removal) or more setup time. | Средний |
Post-Processing Intensity | Heat treatment cycles, HIP (if required), extent of CNC machining for tight tolerances, specific surface treatments all add significant cost. | Средний и высокий |
Обеспечение качества | Rigorous NDT (X-ray, CT, FPI), detailed dimensional inspection (CMM), and comprehensive documentation required for aerospace add overhead. | Средний |
Объем заказа | Economies of scale can apply. Setup costs are amortized over more parts. Discuss potential for wholesale aerospace parts pricing for larger batches. | Средний |
Повторное использование порошка | Efficient powder recycling and rejuvenation processes by the supplier can help mitigate raw material costs. | Низкий-средний |
Export to Sheets
Lead Time Factors:
- Design & Preparation: Finalizing the design (including DfAM optimization), programming the build layout, and performing simulations. (Days)
- Время печати: Highly dependent on part height and volume. Can range from 12 hours to several days or even a week for large/complex rings. (Hours to Days)
- Cooling & Stress Relief: Allowing the build to cool properly and performing the initial heat treatment cycle. (Hours to 1 Day)
- Part & Support Removal: Cutting from the build plate and removing support structures. Can be quick or take significant time depending on complexity. (Hours to Days)
- Heat Treatment & HIP: Furnace cycles take time (including heating, soaking, cooling). HIP adds another cycle. (Days)
- Machining & Finishing: Setup and machining time depend on the number and complexity of features requiring tight tolerances. (Days)
- Inspection & QA: Thorough NDT and dimensional verification. (Days)
- Supplier Queue: Existing workload and machine availability at the supplier significantly impact start time. (Variable: Days to Weeks)
Typical Lead Time Range: For a prototype or small batch of aerospace support rings, expect lead times ranging from 2 to 6 weeks, depending heavily on the factors above. Production orders will require careful scheduling based on volume and required delivery cadence. Clear communication with the supplier is essential to establish realistic timelines.
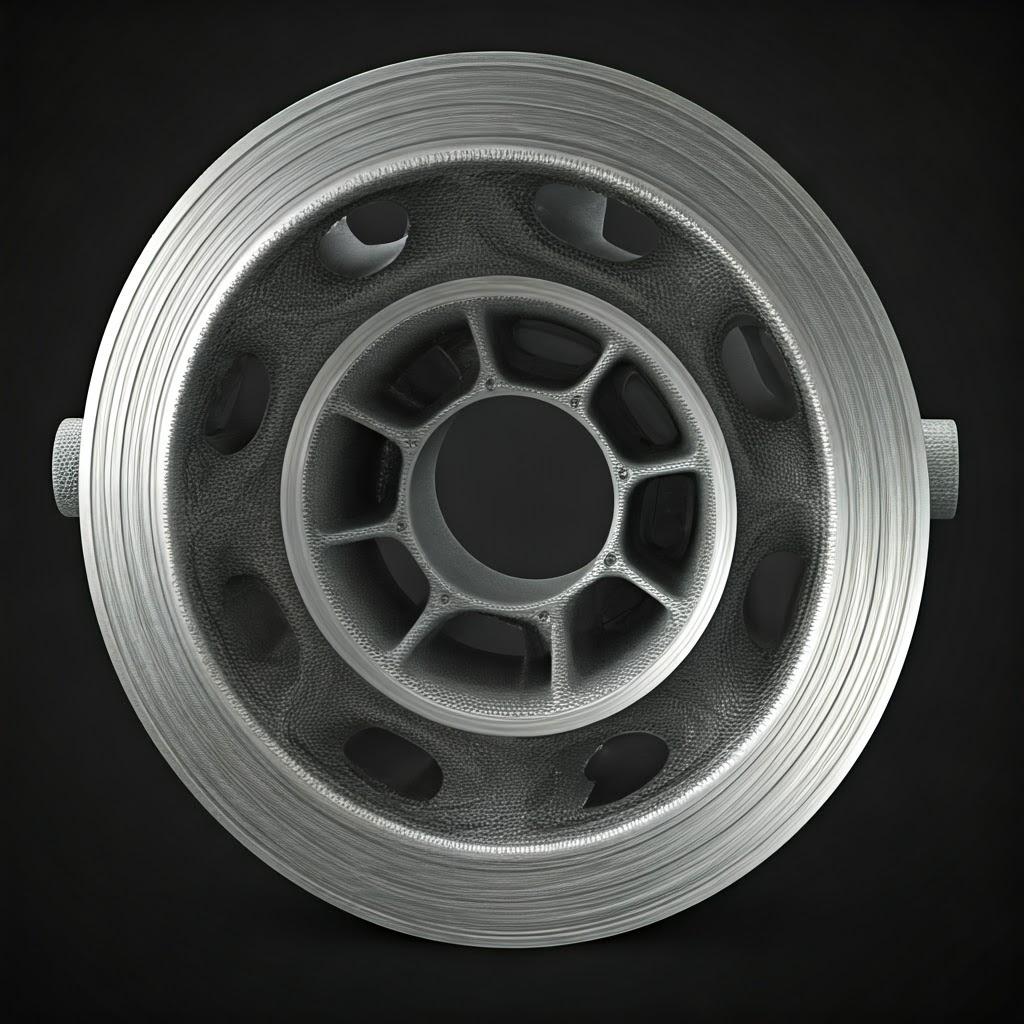
FAQ: Answering Your Questions on 3D Printed Jet Engine Support Rings
Here are answers to some frequently asked questions about using metal additive manufacturing for jet engine support rings:
1. How do the mechanical properties of AM IN718/IN625 compare to wrought counterparts?
After appropriate post-processing (especially heat treatment and potentially HIP), the mechanical properties of AM IN718 and IN625 can be highly comparable to, and sometimes even exceed certain properties of, their traditionally forged or wrought counterparts. Tensile strength, yield strength, and creep resistance are often similar. Fatigue properties, particularly with HIP treatment to close porosity, can be excellent. There might be slight variations in ductility or direction-dependent properties (anisotropy), but rigorous process control and heat treatment minimize these differences, making AM materials suitable for demanding aerospace applications.
2. What certifications are essential for an AM supplier providing aerospace parts like support rings?
The most critical certification is AS9100, which defines the Quality Management System requirements for aviation, space, and defense organizations. This ensures robust processes for traceability, configuration management, risk management, and quality control specific to the industry. Additionally, if the supplier performs special processes like heat treatment or NDT in-house, Nadcap accreditation for those specific processes may be required by the end customer.
3. Can existing support ring designs originally made for forging/machining be directly 3D printed?
While technically possible to print from an existing CAD file, it’s generally not recommended without a Design for Additive Manufacturing (DfAM) review. Designs optimized for traditional methods often contain features (like uniform wall thicknesses or specific draft angles) that are unnecessary or suboptimal for AM. Directly printing them might lead to longer print times, excessive support material, higher costs, and missed opportunities for lightweighting or performance enhancement through AM-specific features like topology optimization or internal lattices. A DfAM review is crucial to adapt or redesign the part to leverage AM’s benefits effectively.
4. What is the typical surface finish of an as-printed support ring, and is it sufficient?
The as-printed surface finish (roughness, Ra) typically ranges from 6-15 µm for Laser Powder Bed Fusion (L-PBF) and 20-35 µm for Selective Electron Beam Melting (SEBM). This finish is generally rougher than machined surfaces. Whether it’s sufficient depends entirely on the specific requirements of the ring’s surfaces. Mating faces, sealing surfaces, or areas critical for fatigue life will almost always require post-process machining or polishing to achieve a smoother finish and tighter tolerances. Non-critical surfaces might be acceptable as-printed.
5. How does Met3dp ensure the quality and reliability of its 3D printed aerospace components?
Met3dp ensures quality through a comprehensive approach that leverages its vertical integration and expertise. This includes:
- Передовое производство порошков: Utilizing industry-leading Gas Atomization and PREP technologies to create high-sphericity, high-purity IN718, IN625, and other metal powders optimized for AM.
- Reliable Printing Systems: Employing their own SEBM printers known for industry-leading accuracy and reliability, specifically designed for mission-critical parts.
- Управление процессом: Leveraging decades of collective expertise in metal AM to develop and implement optimized printing parameters and robust process controls.
- Comprehensive Solutions: Offering support throughout the process, from material selection and DfAM consultation through printing and guidance on post-processing and qualification, as highlighted on theirО насстраница.
- Focus on Industrial Applications: Specializing in demanding sectors like aerospace, medical, and automotive, understanding the critical quality requirements involved.
Conclusion: Elevating Jet Engine Performance with Additive Manufacturing
The adoption of metal additive manufacturing for critical components like jet engine support rings represents a significant leap forward in aerospace engineering and production. By leveraging the unique capabilities of AM, particularly with high-performance nickel superalloys like IN718 and IN625, engineers can design and produce parts that were previously impossible or impractical to manufacture.
The key advantages are clear:
- Беспрецедентная свобода дизайна: Enabling topology optimization for substantial lightweighting, integration of complex features like cooling channels, and part consolidation for reduced assembly complexity.
- Повышенная производительность: Creating stronger, stiffer, and potentially more durable components tailored precisely to their operational demands.
- Эффективность материала: Minimizing waste, especially important when using expensive superalloys.
- Agile Manufacturing: Reducing reliance on traditional tooling, enabling faster prototyping, iteration, and potentially shorter lead times for complex geometries.
However, realizing these benefits requires a holistic approach. Success depends on embracing Проектирование для аддитивного производства (DfAM) principles, understanding the necessity of meticulous постобработка (including heat treatment, machining, and inspection), and implementing rigorous обеспечение качества protocols compliant with aerospace standards.
Furthermore, choosing the right manufacturing partner is paramount. Look for suppliers with proven aerospace certifications (AS9100), deep material and process expertise, robust quality systems, and comprehensive capabilities spanning the entire production workflow.
Met3dp stands as a leader in this field, providing not only cutting-edge SEBM printers and advanced metal powders but also the crucial application development support needed to navigate the complexities of aerospace AM. Their vertically integrated approach, from powder creation to finished part guidance, ensures a foundation of quality and reliability. To explore how Met3dp’s capabilities can power your organization’s additive manufacturing goals for demanding applications like jet engine support rings and other critical components, visit their website at https://met3dp.com/ or learn more about their comprehensive solutions on their О нас page. Partnering with experts like Met3dp can help unlock the full potential of additive manufacturing to build the next generation of more efficient, higher-performing jet engines.
Поделиться
MET3DP Technology Co., LTD - ведущий поставщик решений для аддитивного производства со штаб-квартирой в Циндао, Китай. Наша компания специализируется на производстве оборудования для 3D-печати и высокопроизводительных металлических порошков для промышленного применения.
Сделайте запрос, чтобы получить лучшую цену и индивидуальное решение для вашего бизнеса!
Похожие статьи
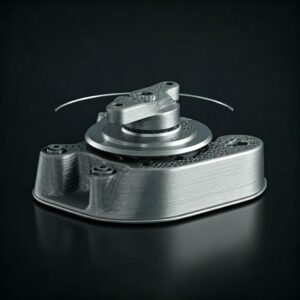
3D-печатные крепления для автомобильных радарных датчиков: Точность и производительность
Читать далее "О компании Met3DP
Последние обновления
Наш продукт
CONTACT US
Есть вопросы? Отправьте нам сообщение прямо сейчас! После получения Вашего сообщения мы всей командой выполним Ваш запрос.
Получите информацию о Metal3DP
Брошюра о продукции
Получить последние продукты и прайс-лист
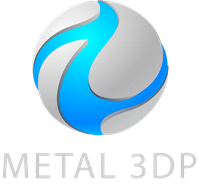
Металлические порошки для 3D-печати и аддитивного производства