Precision Surgical Needle Guides via Metal AM
Оглавление
Introduction: The Critical Role of Precision Needle Guides in Modern Surgery
In the rapidly evolving landscape of modern medicine, precision is paramount. Surgical interventions, whether diagnostic or therapeutic, demand unprecedented levels of accuracy to maximize efficacy while minimizing patient risk. Central to achieving this precision, particularly in minimally invasive surgery (MIS), are surgical needle guides. These seemingly simple instruments play a critical role in ensuring that needles, probes, cannulas, or other instruments reach their intended target within the human body accurately and safely. A surgical needle guide is essentially a targeting device, often custom-designed or procedure-specific, that constrains the path of a surgical instrument, guiding it along a predetermined trajectory towards a specific anatomical location. This guidance is crucial in procedures where direct visualization is limited, relying instead on medical imaging like CT scans, MRI, ultrasound, or fluoroscopy.
The importance of these guides cannot be overstated. They are instrumental in:
- Enhancing Accuracy: By providing a fixed pathway, needle guides drastically reduce the potential for human error in angulation and depth, ensuring instruments reach targets often measured in millimeters. This is vital in delicate procedures like biopsies of small lesions, placement of brachytherapy seeds near sensitive organs, or targeting specific neural pathways in neurosurgery.
- Improving Patient Safety: Precise targeting minimizes damage to surrounding healthy tissues, nerves, and blood vessels. This leads to reduced procedural complications, less post-operative pain, and faster recovery times for patients. In procedures like deep brain stimulation or tumor ablation, errant placement can have devastating consequences, making accurate guidance a non-negotiable requirement.
- Enabling Minimally Invasive Procedures: Needle guides are key enablers for many MIS techniques. By allowing surgeons to accurately access deep-seated targets through small incisions or natural orifices, they reduce surgical trauma, infection risk, and hospital stays compared to traditional open surgeries.
- Standardizing Procedures: Well-designed guides can help standardize complex procedures, making outcomes less dependent on individual surgeon dexterity and experience, leading to more consistent results across different practitioners and institutions.
Historically, surgical guides were often manufactured using traditional methods like CNC machining from metal or polymer blocks, or sometimes casting. While effective for simpler geometries, these methods face limitations when dealing with the increasing complexity demanded by modern surgical approaches. Creating intricate internal channels, patient-specific contoured surfaces matching unique anatomies, or integrating multiple functions into a single device can be challenging, time-consuming, and expensive using subtractive manufacturing. Furthermore, prototyping and iterating designs for optimal performance could be a lengthy process.
This is where аддитивное производство металлов (AM), commonly known as metal 3D-печать, emerges as a transformative technology. Metal AM offers a fundamentally different approach, building parts layer by layer directly from digital models using high-performance metal powders. This technology unlocks unprecedented design freedom and customization capabilities, perfectly suited to the demands of precision surgical instrumentation like needle guides. Companies specializing in металлическая 3D-печать, such as Met3dp, are leveraging advanced processes and materials to produce next-generation surgical tools that were previously impossible or impractical to manufacture. The ability to rapidly create complex, patient-specific, high-strength metal guides is revolutionizing surgical planning and execution, paving the way for safer, more accurate, and less invasive treatments. This blog post will delve into the specifics of using metal AM for surgical needle guides, exploring the applications, benefits, materials, design considerations, and supplier selection process critical for medical device engineers and procurement managers.
Applications & Use Cases: Where are Metal AM Needle Guides Making an Impact?
The versatility and precision offered by metal additive manufacturing have opened doors for needle guides in a diverse range of medical fields and surgical procedures. The ability to create complex geometries, patient-specific designs derived from medical imaging, and utilize biocompatible, high-strength metals makes AM an ideal solution for challenging guidance applications. Procurement managers sourcing surgical instruments and engineers designing new medical devices should be aware of the expanding impact of metal AM needle guides across various specialties:
1. Oncology – Biopsy and Treatment:
- Targeted Biopsies: Metal AM guides are crucial for accurately sampling suspicious lesions identified on CT, MRI, or ultrasound scans. Examples include:
- Prostate Biopsy: Custom guides, often created from MRI data, help target specific regions within the prostate (e.g., PI-RADS 4 or 5 lesions) more reliably than standard template biopsies, improving cancer detection rates and reducing the need for repeat procedures. Guides can be designed for transrectal or transperineal approaches.
- Breast Biopsy: For non-palpable lesions visible only on imaging, AM guides ensure precise needle placement for core needle or vacuum-assisted biopsies, especially for lesions near the chest wall or implants.
- Liver, Kidney, Lung, Pancreas Biopsies: Accessing deep-seated or small lesions in these organs requires extreme precision, often facilitated by patient-specific guides navigating around critical structures.
- Brachytherapy Seed Placement: In cancer treatments like prostate or gynecological brachytherapy, radioactive seeds must be placed with sub-millimeter accuracy. Metal AM allows for the creation of complex, patient-specific templates (often made from Titanium for MRI compatibility during planning/verification) with numerous predefined pathways, ensuring optimal dose distribution to the tumor while sparing surrounding healthy tissue.
- Tumor Ablation: Guiding cryoablation or radiofrequency ablation (RFA) probes accurately into tumors requires stable guidance. Custom AM guides ensure the probe tip is positioned correctly for effective thermal destruction of the target tissue.
2. Neurosurgery:
- Stereotactic Guidance: Procedures like Deep Brain Stimulation (DBS) electrode placement for Parkinson’s disease or epilepsy, or biopsies of brain tumors, require navigating complex neural pathways. Metal AM can produce highly customized stereotactic frames or guides that integrate directly with surgical navigation systems, offering unparalleled accuracy for reaching deep brain targets. Titanium alloys (like Ti-6Al-4V) are often preferred due to their strength, low weight, and MRI compatibility.
- Spinal Procedures: Guiding pedicle screws, performing biopsies, or delivering therapeutics in spinal surgery benefits from patient-specific guides derived from CT scans, improving screw placement accuracy and reducing the risk of nerve root injury.
3. Orthopedic Surgery:
- K-wire and Screw Placement: Patient-specific guides are increasingly used in trauma and reconstructive surgery to ensure accurate placement of Kirschner wires (K-wires) and screws, particularly in complex fractures or osteotomies (e.g., pelvic fractures, corrective osteotomies). This improves fixation stability and surgical outcomes.
- Joint Arthroplasty: While less common for primary needle guidance, custom templates can assist in guiding pins or drills for aligning cutting jigs in knee or hip replacement surgery, contributing to overall component positioning accuracy.
- Access Guides: Creating precise access channels to specific locations within bone or joints for procedures like cartilage repair or bone grafting.
4. Targeted Drug Delivery and Therapeutics:
- Intra-tumoral Injections: Delivering chemotherapy agents or immunotherapies directly into tumors requires precise needle placement. Custom AM guides can ensure the therapeutic agent is deposited accurately within the target volume.
- Gene Therapy & Stem Cell Delivery: Emerging therapies involving targeted delivery to specific tissues (e.g., heart muscle, retina) can benefit from highly accurate guidance systems enabled by AM.
5. Research and Training:
- Preclinical Studies: AM allows researchers to rapidly prototype and test novel guide designs in anatomical models or animal studies.
- Surgical Simulation: Realistic training phantoms incorporating complex anatomy can feature integrated AM needle guides to help surgeons practice challenging procedures.
6. Veterinary Medicine:
- Similar applications exist in veterinary surgery, particularly for specialized procedures in companion animals or livestock, where custom guides can improve outcomes for biopsies, tumor treatments, and orthopedic repairs.
The common thread across these diverse applications is the need for precision, customization, and reliability. Metal AM delivers on these requirements by enabling the translation of detailed digital plans (often derived from patient-specific imaging data) into functional, robust, and biocompatible surgical tools. As imaging technology improves and surgical techniques become more refined, the demand for sophisticated guidance solutions will only grow, positioning metal AM as a key enabling technology for medical device suppliers and manufacturers serving these critical fields. Forward-thinking medical device suppliers и contract manufacturers are increasingly incorporating metal AM into their offerings to meet this demand for custom surgical instruments и patient-specific instrumentation (PSI).
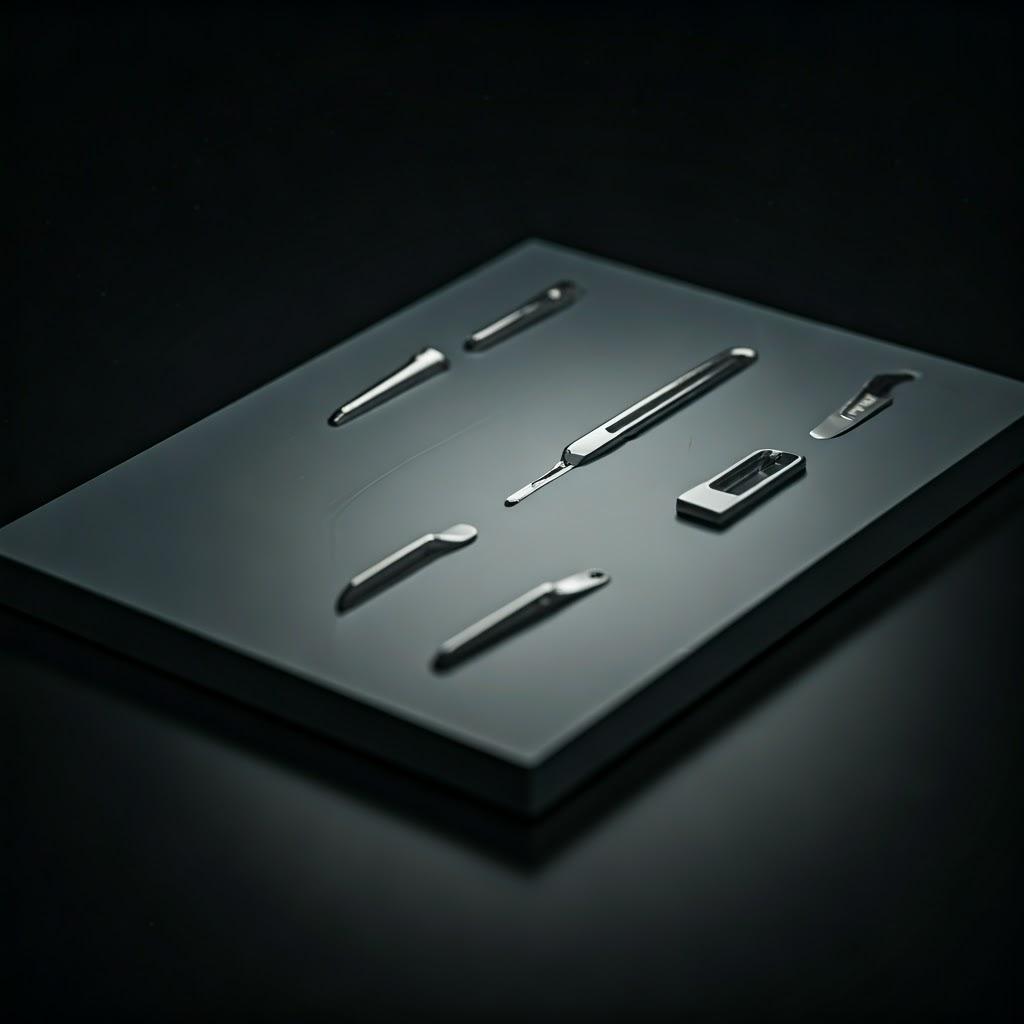
Why Metal Additive Manufacturing for Surgical Needle Guides?
The decision to adopt a new manufacturing technology within the highly regulated medical device industry is never taken lightly. Engineers and procurement specialists must weigh the benefits against established methods, considering factors like cost, quality, scalability, and regulatory compliance. For surgical needle guides, metal additive manufacturing presents a compelling value proposition compared to traditional techniques, primarily CNC machining. While CNC machining remains a vital technology for many surgical instruments, metal AM offers distinct advantages, particularly for complex and customized guides:
1. Unparalleled Design Freedom:
- Сложные геометрии: Traditional machining struggles with creating intricate internal channels, curved pathways, or complex external contours designed to perfectly match patient anatomy. Metal AM builds parts layer-by-layer, making these complex features achievable without the constraints of cutting tool access. This allows for:
- Optimized needle trajectories that navigate around critical structures.
- Guides that conform perfectly to bone or tissue surfaces for stable positioning.
- Integration of multiple guide channels within a single compact device.
- Консолидация частей: Features that might require assembling multiple machined components can often be integrated into a single, monolithic part using AM. This reduces assembly time, potential failure points, and sterilization challenges. Fixation points, fiducial markers for navigation systems, or even ergonomic handling features can be built directly into the guide.
- Облегчение: While not always the primary driver for needle guides (stiffness is often key), techniques like topology optimization can be applied where appropriate to reduce material usage and weight, particularly beneficial for larger or more complex guides made from denser materials, without compromising necessary structural integrity.
2. Rapid Prototyping and Iteration:
- Developing a new surgical guide often involves multiple design iterations to optimize ergonomics, accuracy, and manufacturability. Metal AM allows for rapid prototyping directly in the final intended metal (e.g., 316L or Ti-6Al-4V). Design changes can be implemented digitally and a new prototype printed within days, drastically accelerating the development cycle compared to the weeks or months potentially needed for complex machining setups or modifications. This agility is crucial for innovation in the fast-paced medical device field.
3. Economical Customization and Patient-Specific Solutions:
- Perhaps the most significant advantage for surgical guides is the ability to produce patient-specific instrumentation (PSI) cost-effectively. Using AM, a unique guide can be designed based on a patient’s CT or MRI scan and printed as a “batch of one” without the prohibitive setup costs associated with custom machining jigs or fixtures. This unlocks the potential for truly personalized surgery, tailoring the tools to the individual’s anatomy for optimal accuracy and fit. While the per-part cost might be higher than mass-produced standard guides, the value derived from improved accuracy and potentially avoided complications in complex cases makes PSI highly attractive. This capability provides significant supply chain flexibility for hospitals and surgical centers needing производство по требованию of specialized tools.
4. Material Versatility:
- Metal AM processes, such as Selective Laser Melting (SLM) and Electron Beam Melting (EBM), are compatible with a range of biocompatible metals essential for surgical instruments. As we will discuss in the next section, materials like 316L stainless steel and Ti-6Al-4V titanium alloy offer the required strength, corrosion resistance, and biocompatibility. AM allows these high-performance materials to be formed into shapes that might be difficult or impossible to machine.
5. Speed for Low-to-Medium Volumes:
- For small production runs or instruments needed on relatively short notice, metal AM can often provide shorter lead times than traditional manufacturing, especially if complex machining or tooling is involved. Once the design is finalized and validated, printing can commence relatively quickly, bypassing stages like tool path programming for intricate features or fixture creation.
Comparison with CNC Machining:
Характеристика | Аддитивное производство металлов (AM) | Обработка с ЧПУ | Advantage for Needle Guides |
---|---|---|---|
Сложность конструкции | High (complex internal channels, organic shapes) | Moderate to High (limited by tool access) | AM enables optimized, patient-specific designs |
Персонализация | High (economical for batches of one) | Low (high setup cost for custom parts) | AM excels at Patient-Specific Instrumentation |
Prototyping Speed | Fast (days) | Moderate to Slow (days to weeks for complex parts) | AM accelerates design iteration |
Lead Time (Low Vol) | Potentially Shorter | Can be longer for complex parts | AM offers on-demand potential |
Материальные отходы | Low (powder recycling) | Высокий (субтрактивный процесс) | AM is generally more material-efficient |
Отделка поверхности | Rougher (as-built, requires post-processing) | Smoother (as-machined) | Machining better for innate finish |
Допуски | Good (requires post-processing for critical) | Отличный | Machining better for innate tight tolerances |
Первоначальная стоимость | Can be higher per part (esp. simple designs) | Can be lower per part (esp. simple, high vol) | Cost-benefit depends heavily on complexity |
Export to Sheets
While CNC machining still holds advantages in achieving very tight tolerances and fine surface finishes directly, many critical features on AM parts can be finish-machined during post-processing. For the complex geometries and customization needs inherent in advanced surgical needle guides, the benefits offered by metal AM often outweigh the challenges. Partnering with an experienced metal AM service provider equipped with the right technology and expertise, like Met3dp, allows medical device companies to fully leverage these advantages, transforming surgical possibilities and improving patient outcomes. The shift towards additive manufacturing benefits is clear for companies seeking innovation in complex medical device production.
Biocompatible Material Focus: 316L Stainless Steel and Ti-6Al-4V Titanium for Needle Guides
The choice of material for any medical device, especially one used in surgery, is critical. Surgical needle guides must be fabricated from materials that are not only strong and durable enough to withstand the rigors of the procedure and repeated sterilization cycles but also biocompatible, meaning they do not elicit adverse reactions when in contact with bodily tissues and fluids. Furthermore, properties like corrosion resistance and, in some cases, radiopacity or MRI compatibility, are vital considerations. For metal additive manufacturing of needle guides, two materials stand out as industry standards due to their well-documented properties and successful track record: Нержавеющая сталь 316L и Титановый сплав Ti-6Al-4V.
Understanding the characteristics of these materials is crucial for engineers designing guides and procurement managers sourcing additive manufacturing materials suppliers.
1. 316L Stainless Steel (ASTM F138 / ISO 5832-1):
- Состав: An austenitic stainless steel alloy containing Iron (Fe) as the base, with significant additions of Chromium (Cr, ~16-18%), Nickel (Ni, ~10-14%), and Molybdenum (Mo, ~2-3%). The ‘L’ designation signifies low carbon content (<0.03%), which improves corrosion resistance, particularly after welding or stress relieving relevant in AM post-processing.
- Основные свойства:
- Отличная коррозионная стойкость: The high Chromium content forms a passive oxide layer, protecting the metal from corrosion in bodily fluids and during harsh sterilization processes (like autoclaving). Molybdenum enhances resistance to pitting and crevice corrosion, particularly in chloride environments.
- Good Mechanical Strength and Ductility: 316L offers a good balance of strength, toughness, and ductility, making it resistant to fracture during use. While not as strong as titanium alloys, it’s sufficient for most needle guide applications.
- Proven Biocompatibility: Decades of use in surgical implants and instruments have established 316L as a highly biocompatible material when produced and finished correctly (meeting standards like ISO 10993). Proper cleaning and passivation are essential.
- Sterilizability: Compatible with standard sterilization methods including steam autoclaving, ethylene oxide (EtO), and gamma radiation.
- Эффективность затрат: Generally less expensive than titanium alloys, making it a suitable choice when the higher strength-to-weight ratio or MRI compatibility of titanium is not required.
- AM Considerations: 316L powder is readily available and well-characterized for AM processes like SLM. It prints reliably, achieving high densities (>99.5%). Post-processing typically involves stress relief heat treatment and potentially Hot Isostatic Pressing (HIP) for critical applications to eliminate any residual porosity, followed by surface finishing and passivation.
2. Ti-6Al-4V (Grade 5) Titanium Alloy (ASTM F136 / ISO 5832-3):
- Состав: The most widely used titanium alloy, containing Titanium (Ti) as the base, with approximately 6% Aluminum (Al) and 4% Vanadium (V). The ASTM F136 standard specifies limits for impurities, particularly iron and oxygen, for surgical implant applications (ELI – Extra Low Interstitial variant is often used).
- Основные свойства:
- Отличная биосовместимость: Considered one of the most biocompatible metals, exhibiting superior resistance to corrosion in the body and minimal ion release. Widely used for long-term implants (hips, knees, dental).
- Высокое соотношение прочности и веса: Significantly lighter than stainless steel (density ~4.43 g/cm³ vs. ~8.0 g/cm³ for 316L) but with comparable or higher strength. This is advantageous for larger or more complex guides where surgeon comfort and handling are important.
- Отличная коррозионная стойкость: Forms a very stable and protective titanium dioxide (TiO2) passive layer.
- MRI Compatibility: Non-ferromagnetic, making it safe for use in Magnetic Resonance Imaging (MRI) environments, which is crucial if the guide is needed during intraoperative imaging or for guiding procedures planned with MRI data.
- Good Fatigue Strength: Important for instruments subjected to repeated loading cycles, although less critical for single-use or low-cycle guides.
- AM Considerations: Ti-6Al-4V is also well-suited for metal AM processes (SLM and EBM). However, it requires careful control of the build atmosphere due to titanium’s reactivity with oxygen and nitrogen at elevated temperatures. Inert gas (argon) shielding is critical. Post-processing often includes stress relief and potentially HIPing or solution treatment and aging (STA) heat treatments to achieve desired mechanical properties. Surface finishing is also required.
Material Properties Comparison:
Недвижимость | 316L Stainless Steel (Annealed) | Ti-6Al-4V (Annealed) | Significance for Needle Guides |
---|---|---|---|
Плотность | ~8,0 г/см³ | ~4,43 г/см³ | Ti-6Al-4V offers significant weight savings (lighter handling) |
Предельная прочность на разрыв | ~515 – 690 MPa | ~830 – 950 MPa | Both are strong; Ti-6Al-4V offers higher strength |
Предел текучести | ~205 – 310 MPa | ~760 – 880 MPa | Ti-6Al-4V has significantly higher yield strength (less deformation) |
Модуль упругости | ~193 GPa | ~114 GPa | 316L is stiffer; Ti-6Al-4V is closer to bone modulus (less stress shielding if implant adjacent) |
Коррозионная стойкость | Отличный | Отличный | Both suitable for surgical environment & sterilization |
Biocompatibility (ISO 10993) | Отличный | Отличный | Both widely accepted for medical devices |
MRI Compatibility | No (Paramagnetic) | Yes (Non-magnetic) | Ti-6Al-4V required if MRI is involved during procedure/planning |
Относительная стоимость | Нижний | Выше | Cost factor in material selection |
Export to Sheets
The Critical Role of Powder Quality:
Regardless of the chosen alloy, the quality of the metal powder used in the AM process directly impacts the final part’s integrity, mechanical properties, and biocompatibility. Key powder characteristics include:
- Сферичность и текучесть: Highly spherical powders with good flowability ensure uniform spreading of layers in the powder bed fusion process, leading to consistent melting and high part density.
- Распределение частиц по размерам (PSD): A controlled PSD is crucial for achieving good packing density and influencing the final surface roughness and resolution.
- Purity and Low Contamination: Impurities, particularly interstitial elements like oxygen and nitrogen (especially critical for titanium), can embrittle the final part and compromise its mechanical properties and corrosion resistance. Minimizing satellite particles is also important for density.
This is where partnering with a supplier with deep expertise in powder metallurgy becomes essential. Met3dp, for instance, utilizes industry-leading gas atomization and Plasma Rotating Electrode Process (PREP) technologies to produce high-quality spherical metal powders. Their advanced systems employ unique nozzle and gas flow designs to achieve powders with high sphericity, excellent flowability, and low contamination levels, optimized for laser and electron beam powder bed fusion processes. Met3dp manufactures a wide range of high-performance powders, including the critical 316L and Ti-6Al-4V alloys, ensuring that medical device manufacturers have access to materials that meet the stringent requirements for producing reliable and safe surgical needle guides. Their focus on powder quality translates directly into higher quality printed components with superior mechanical properties and biocompatibility.
Choosing between 316L and Ti-6Al-4V depends on the specific requirements of the needle guide – prioritizing cost-effectiveness (316L) versus lightweighting, ultimate strength, or MRI compatibility (Ti-6Al-4V). Consulting with material experts and an experienced AM service provider is key to making the optimal selection for each unique application.
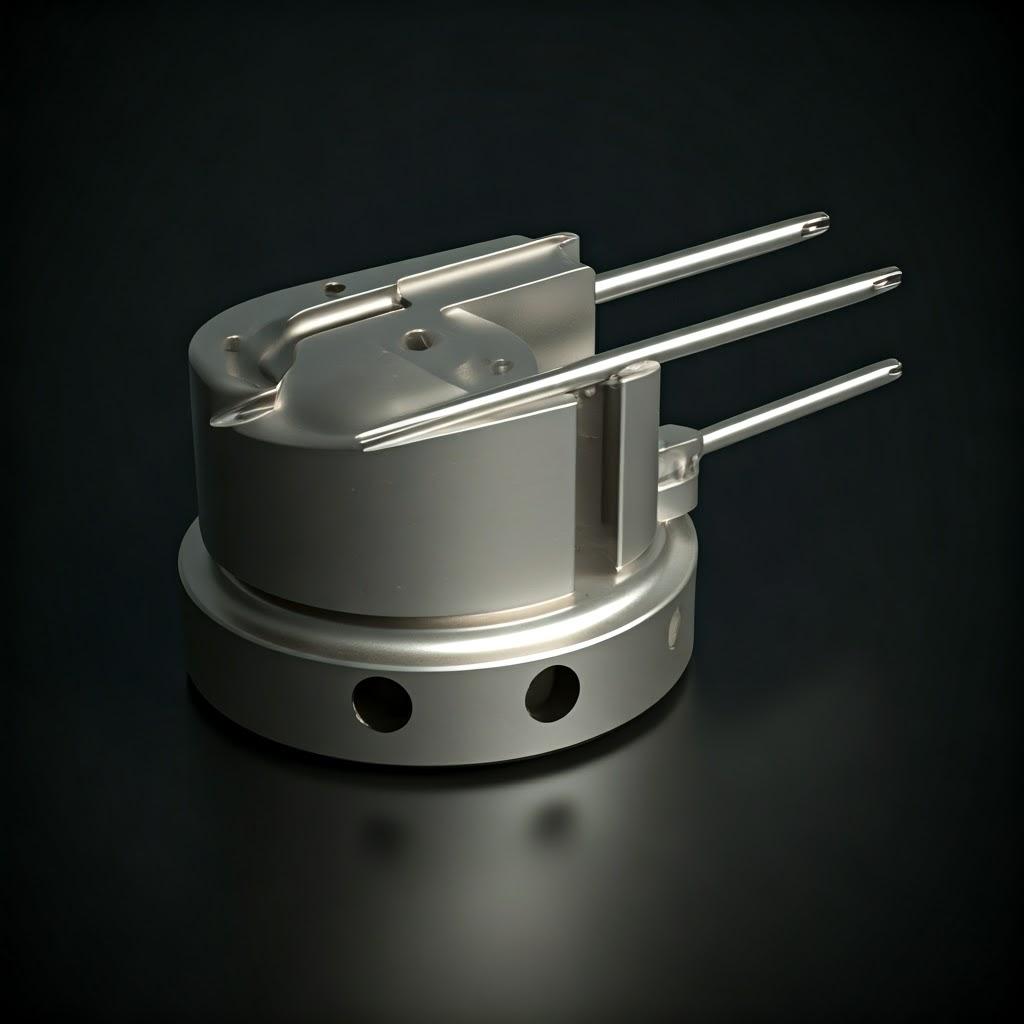
Design for Additive Manufacturing (DfAM): Optimizing Needle Guides for Printing Success
Transitioning from traditional manufacturing paradigms like CNC machining to additive manufacturing requires more than simply converting an existing CAD file. To truly harness the power of metal AM for surgical needle guides, engineers must embrace Проектирование для аддитивного производства (DfAM) principles. DfAM is a design philosophy focused on optimizing a part’s geometry specifically for the layer-by-layer build process, taking into account its capabilities, constraints, and inherent characteristics. Applying DfAM not only enables the creation of complex features impossible with other methods but also improves printability, reduces costs, minimizes post-processing efforts, and enhances the final part’s performance. For engineers designing surgical needle guides, implementing DfAM is crucial for achieving optimal outcomes in terms of accuracy, functionality, and manufacturability.
Here are key DfAM considerations specifically relevant to metal AM surgical needle guides:
1. Internal Channel Design and Optimization:
- Smooth Paths: Needles must glide smoothly without binding. Design internal channels with gradual curves rather than sharp, abrupt angles, which can hinder needle passage and create stress concentrations during printing.
- Minimum Diameter: There’s a practical limit to how small a channel can be reliably printed and, more importantly, effectively cleared of residual powder and potentially surface treated. This minimum diameter depends on the specific AM process (SLM generally offers finer resolution than EBM), machine capabilities, and powder particle size. Typically, diameters below 0.5-1.0 mm become challenging. Consult with your AM provider for specific limits.
- Self-Supporting Shapes: Long, horizontal channel sections require support structures inside, which are extremely difficult to remove. Design internal channels with self-supporting geometries where possible. A “teardrop” or “diamond” cross-section, rather than a perfect circle, allows the upper portion of the channel to be built without supports sagging into the channel below. This is critical for ensuring channel patency.
- Avoid Long Horizontal Runs: Even with self-supporting shapes, very long unsupported horizontal spans can lead to issues. Orient the part or modify the design to minimize these features.
2. Wall Thickness and Rigidity:
- Minimum Wall Thickness: Metal AM processes have limitations on minimum feature size and wall thickness (often around 0.3-0.5 mm, machine/parameter dependent). Ensure walls are thick enough to be reliably printed and provide the necessary structural integrity and rigidity for accurate guidance. Thin walls can be prone to distortion during printing or handling.
- Uniformity and Thermal Management: Avoid abrupt changes in wall thickness or large, bulky sections. Massive sections can accumulate thermal stress, potentially leading to warping or cracking. Gradual transitions are preferred. Consider lattice structures or internal voids (using topology optimization) for thicker sections if lightweighting is desired and structural integrity allows.
3. Strategic Use of Support Structures:
- Minimize Supports: Supports are temporary structures required to anchor overhanging features (typically angles less than 45° from the horizontal) to the build plate or underlying layers, preventing collapse and managing thermal stress. However, supports consume extra material, add print time, and require removal, which can mar surfaces and be difficult in intricate areas. The primary DfAM goal is often to design out the need for supports.
- Orientation for Support Reduction: The orientation of the guide on the build plate significantly impacts support requirements. Analyze different orientations early in the design phase. Orienting critical surfaces (like channel entries/exits or mating faces) vertically or as up-facing surfaces often yields better finish and accuracy, potentially reducing support needs on those features.
- Design for Support Removal: When supports are unavoidable (especially internal supports for complex channel networks if self-supporting designs aren’t feasible), design them for easy access and removal. Use minimally contacting support structures, incorporate features that allow tools to reach supports, or consider designs that can be printed in sections and assembled if internal supports are otherwise impossible to remove. Discuss support strategies thoroughly with your AM service provider.
4. Topology Optimization and Lightweighting:
- Particularly relevant for guides made from denser materials like 316L or for complex Ti-6Al-4V guides used in neurosurgery or orthopedics where handling matters. Topology optimization software uses algorithms (like Finite Element Analysis – FEA) to remove material from non-critical areas while maintaining required stiffness and strength under expected loads. This can result in organic-looking, highly efficient structures that significantly reduce weight without compromising function. However, ensure the resulting geometry is still practical for handling, cleaning, and sterilization.
5. Part Consolidation:
- Examine if multiple components of a traditional guide assembly (e.g., guide block, handle, fixation mechanism) can be combined into a single, monolithic AM part. This eliminates assembly steps, potential weak points at joints, and simplifies inventory and sterilization. Consider integrating features like depth stops, alignment markers, or textured gripping surfaces directly into the AM design.
6. Designing for Post-Processing and Use:
- Sterilizability: Design with cleaning and sterilization in mind. Avoid deep, narrow crevices or complex surface textures where bioburden could potentially become trapped. Ensure internal channels are designed for effective flushing and cleaning. Promote smooth surfaces where possible.
- Identification: Incorporate embedded lettering, logos, or serial numbers directly into the CAD model for permanent part identification, aiding traceability.
7. Collaboration with AM Experts:
- Engage with your metal AM service provider early in the design process. Experienced providers like Met3dp offer DfAM expertise and can provide crucial feedback on printability, optimal orientation, support strategies, and material selection based on their specific equipment and process knowledge. This collaboration ensures the design is not only functional but also efficiently manufacturable via AM.
By thoughtfully applying these DfAM principles, engineers can unlock the full potential of metal additive manufacturing, creating surgical needle guides that are more accurate, functional, patient-specific, and often more efficient to produce than their traditionally manufactured counterparts. This iterative design process, informed by the nuances of the AM process, is key to successful implementation.
Achieving Critical Tolerances, Surface Finish, and Dimensional Accuracy
For a surgical instrument like a needle guide, where precision is paramount, understanding and controlling dimensional accuracy, tolerances, and surface finish are non-negotiable. While metal AM offers incredible design freedom, it inherently produces parts with different characteristics compared to precise machining. Achieving the tight specifications required for medical applications often involves a combination of controlled AM processing and targeted post-processing. Engineers and procurement managers must have realistic expectations and clear communication with their AM supplier regarding these critical quality attributes.
1. Tolerances:
- As-Built Tolerances: Metal Powder Bed Fusion (PBF) processes like Selective Laser Melting (SLM) and Electron Beam Melting (EBM) typically achieve tolerances in the range of ±0.1 mm to ±0.2 mm for smaller features, or sometimes expressed as a percentage of the dimension (e.g., ±0.5% to ±2%) for larger parts. EBM generally has slightly looser tolerances than SLM due to higher processing temperatures and powder characteristics. These tolerances might be sufficient for some features of a needle guide but are often not tight enough for critical dimensions like precise channel diameters or mating interfaces. General tolerance standards like ISO 2768 (medium or fine class) can serve as a starting point for discussion, but specific capabilities depend heavily on the machine, calibration, material, part geometry, and orientation.
- Critical Dimensions: Identify the Critical-To-Quality (CTQ) dimensions on the needle guide early in the design phase. These typically include:
- Internal channel diameter (ensuring smooth needle passage without excessive play).
- Positional accuracy of channel entry and exit points relative to fixation features or anatomical landmarks.
- Overall length and key functional lengths.
- Dimensions of features that mate with other instruments or navigation systems.
- Achieving Tighter Tolerances: For dimensions requiring tolerances tighter than the inherent capability of the AM process, post-process CNC machining is typically employed. Features like channel openings, mating surfaces, or critical interfaces can be designed with extra material (machining stock) in the AM process and then machined to final, tight tolerances (potentially down to ±0.01 mm or better, depending on the feature and machining process).
2. Surface Finish (Roughness):
- As-Built Surface Finish (Ra): The surface roughness of as-built metal AM parts is significantly higher than machined surfaces.
- SLM: Typically produces Ra values between 5 µm and 15 µm.
- EBM: Generally results in rougher surfaces, often Ra 20 µm to 35 µm.
- Factors influencing Ra include layer thickness (thinner layers = smoother finish), powder particle size, beam/laser parameters, and crucially, the orientation of the surface relative to the build direction. Up-facing surfaces tend to be smoother than vertical walls, while down-facing surfaces (supported areas) are typically the roughest.
- Requirements for Surgical Guides: As-built surfaces are generally too rough for surgical instruments. Smooth surfaces are required for:
- Functionality: Ensuring smooth gliding of needles within channels.
- Cleanability & Sterilizability: Rough surfaces have higher surface area and can trap contaminants or bioburden more easily.
- Биосовместимость: Very rough surfaces can sometimes increase tissue irritation or ion release, although the bulk material biocompatibility is primary.
- Handling/Ergonomics: Smooth external surfaces are preferred.
- Улучшение качества поверхности: Various post-processing steps are used:
- Abrasive Blasting: Provides a uniform matte finish but doesn’t drastically reduce Ra.
- Tumbling/Vibratory Finishing: Can significantly improve Ra, especially on external surfaces and edges.
- Manual Polishing: Labor-intensive but can achieve very smooth, mirror-like finishes on accessible surfaces.
- Electropolishing: Highly effective for smoothing complex geometries and internal channels (if electrolyte flow is possible), significantly reducing Ra (often below 1 µm) and improving corrosion resistance. It’s often a preferred method for medical parts.
3. Dimensional Accuracy:
- Overall Accuracy: This refers to how closely the final part conforms to the original CAD model dimensions. It’s influenced by multiple factors throughout the AM workflow:
- Калибровка машины: Regular, precise calibration of the AM system is fundamental.
- Параметры процесса: Optimized parameters (laser power, scan speed, layer thickness, etc.) for the specific material and geometry.
- Тепловые нагрузки: Heating and cooling cycles can cause warping and distortion, affecting final dimensions. This is managed through build strategy (orientation, supports) and stress relief heat treatment.
- Качество порошка: Consistent powder characteristics ensure predictable melting behavior.
- Стратегия поддержки: Supports must adequately constrain the part during build but can sometimes cause minor distortion upon removal.
- Post-Processing Effects: Heat treatments can cause predictable minor shrinkage or growth. Material removal during machining or polishing obviously changes dimensions and must be accounted for.
- Process Control & QMS: Achieving consistent dimensional accuracy requires rigorous process control and a robust Quality Management System (QMS), ideally certified to ISO 13485 for medical devices. This ensures traceability, repeatability, and adherence to validated procedures. Companies like Met3dp emphasize their use of advanced printing systems known for delivering industry-leading print volume, accuracy and reliability, backed by stringent quality control protocols essential for mission-critical medical components.
4. Metrology and Inspection:
- Verifying that the final needle guides meet the specified tolerances and dimensional requirements is crucial. Common metrology techniques include:
- Coordinate Measuring Machines (CMMs): High-accuracy tactile probing for critical dimensions.
- Optical 3D Scanning: Captures overall geometry for comparison to CAD, good for complex shapes.
- Industrial CT Scanning: Increasingly used for non-destructive verification of internal channel dimensions, detection of internal defects (like porosity), and overall geometric accuracy.
- Surface Roughness Testers (Profilometers): Measure Ra values on critical surfaces.
- A clear inspection plan defining CTQs, measurement methods, and acceptance criteria must be established between the customer and the AM supplier.
In summary, while metal AM parts require careful consideration and often post-processing to meet the demanding tolerances and surface finish requirements of surgical needle guides, these specifications are achievable through a combination of DfAM, precise process control, targeted post-machining, appropriate surface finishing techniques, and rigorous quality inspection. Clear communication of requirements and collaboration with a capable AM partner are essential for success.
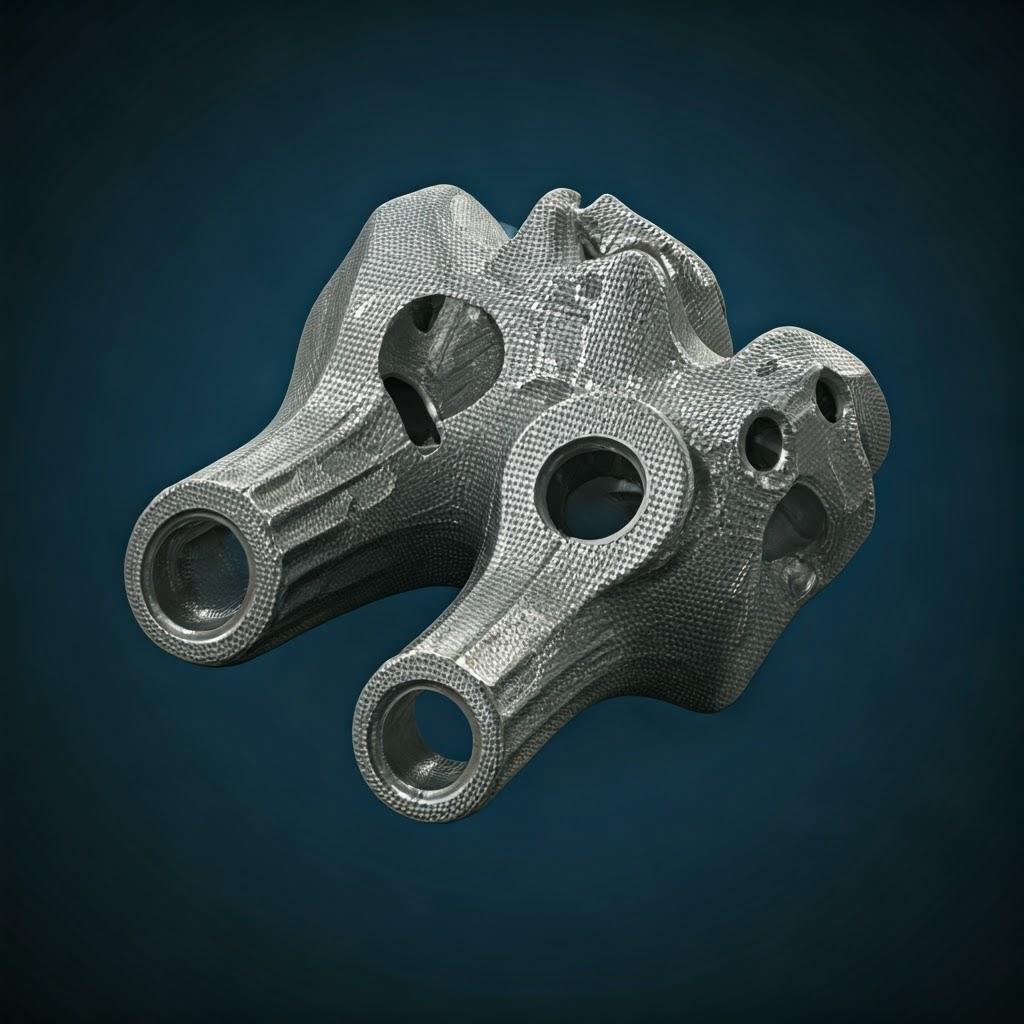
Essential Post-Processing Steps for Functional Surgical Needle Guides
A common misconception about metal additive manufacturing is that parts come off the printer ready for immediate use. In reality, especially for demanding applications like surgical instruments, the printing process is just one stage in a comprehensive workflow. Post-processing steps are absolutely critical to transform an as-built metal AM part into a functional, safe, and reliable surgical needle guide. These steps address residual stresses, remove temporary structures, achieve required surface finishes and tolerances, and ensure cleanliness and biocompatibility. A reputable medical device contract manufacturer specializing in AM will have well-defined, validated procedures for each of these stages:
1. Stress Relief / Heat Treatment:
- Цель: The rapid heating and cooling cycles inherent in PBF processes create significant internal stresses within the printed part. If not relieved, these stresses can cause warping or distortion during or after removal from the build plate, and can negatively impact mechanical properties (especially fatigue life and ductility).
- Процесс: Immediately after the build finishes and before removal from the build plate, the entire platform with the parts is typically subjected to a controlled heat treatment cycle in a vacuum or inert atmosphere furnace. The specific temperature, ramp rates, hold times, and cooling rates depend critically on the material (e.g., different cycles for 316L vs. Ti-6Al-4V) and part geometry. This step is crucial for dimensional stability and optimizing material properties.
2. Part Removal from Build Plate:
- Цель: Separating the printed guides from the metal plate they were built upon.
- Методы: Commonly achieved using wire Electrical Discharge Machining (EDM) for a clean cut with minimal force, or sometimes band sawing or milling. Care must be taken not to damage the parts.
3. Support Structure Removal:
- Цель: Removing the temporary supports required during the build process.
- Методы: This can be one of the most labor-intensive steps, depending on the complexity and location of supports. Methods include:
- Удаление вручную: Breaking or cutting away easily accessible supports using hand tools.
- Machining/Grinding: Milling or grinding away support interfaces.
- Wire EDM: Can be used for precise removal in some cases.
- Задачи: Removing supports from internal channels or delicate features requires extreme care. DfAM plays a huge role here – designing supports for easier removal is key. Residual ‘nibs’ where supports were attached usually need further finishing.
4. Powder Removal (Depowdering):
- Цель: Removing all loose and partially sintered metal powder trapped within the part, especially from internal channels and complex features. Residual powder is a major contamination risk and functional impediment.
- Методы: Typically involves compressed air blow-off, manual brushing, bead blasting (which also starts the surface finishing process), vibration, and potentially ultrasonic cleaning baths with appropriate solvents or detergents. Complete powder removal from long, narrow, or tortuous internal channels can be particularly challenging and requires careful design and validated cleaning procedures. CT scanning is sometimes used to verify complete powder removal from critical internal geometries.
5. Surface Finishing:
- Цель: Achieving the required surface smoothness (low Ra value) for functionality (needle glide), cleanability, biocompatibility, and aesthetics.
- Methods (often used in combination):
- Abrasive Blasting (Bead, Sand, etc.): Creates a uniform matte finish, removes loose particles, but doesn’t dramatically lower Ra. Choice of media is important to avoid contamination.
- Tumbling / Vibratory Finishing: Parts are tumbled with abrasive media (ceramic, plastic) to smooth surfaces and round edges. Effective for batches of parts but less controlled for specific features.
- Manual Grinding/Deburring/Polishing: Skilled technicians use hand tools or power tools with abrasive pads, belts, or polishing compounds to smooth specific areas, remove support witnesses, or achieve mirror finishes. Labor-intensive.
- Electropolishing: An electrochemical process that preferentially removes material from surface peaks, resulting in a very smooth, clean, and often bright finish. Excellent for complex shapes and improving the finish of internal channels (if electrolyte can flow through). It also enhances the passive layer, improving corrosion resistance, especially for 316L. Often a preferred final finishing step for stainless steel medical devices.
6. CNC Machining (If Required):
- Цель: To achieve critical dimensions, tolerances, or surface finishes that are tighter than possible with AM and standard finishing alone.
- Процесс: Transferring the AM part to a CNC milling machine or lathe to precisely machine features like channel openings, mating interfaces, threads, or flat sealing surfaces. Requires careful fixture design to hold the potentially complex AM part accurately.
7. Cleaning and Passivation:
- Цель: Removing all residues from manufacturing and post-processing (powder, oils, machining fluids, polishing compounds, blasting media) and ensuring the surface is in the optimal state for biocompatibility and corrosion resistance.
- Процесс: Involves multiple stages of cleaning using validated detergents, solvents, ultrasonic baths, rinses with purified water (e.g., DI water), and drying. For 316L stainless steel, a пассивация step (typically using nitric or citric acid solutions according to standards like ASTM A967) is essential to fully develop the protective chromium oxide layer. Cleaning validation is a critical regulatory requirement for medical devices.
8. Inspection and Validation:
- Цель: Final verification that the needle guide meets all specifications before release.
- Методы: Dimensional inspection (CMM, scanning), surface finish measurement, visual inspection under magnification (checking for defects, residual support material, cleanliness), potentially functional testing (e.g., passing a needle through channels), and review of all processing documentation for traceability.
The extent and combination of these post-processing steps depend heavily on the specific design of the needle guide, the material used, and the functional requirements. It is crucial for medical device companies to partner with an AM supplier that possesses not only advanced printing capabilities but also comprehensive, validated, and well-documented post-processing workflows suitable for производство медицинского оборудования. Failure to properly execute any of these steps can compromise the safety and efficacy of the final surgical instrument.
Navigating Common Challenges in Metal AM for Needle Guides (and Solutions)
While metal additive manufacturing offers compelling advantages for producing complex surgical needle guides, it’s essential for engineers and procurement managers to be aware of potential challenges inherent in the technology. Successfully navigating these hurdles requires a combination of robust design practices (DfAM), tight process control, advanced post-processing techniques, and collaboration with an experienced AM partner. Here are some common challenges encountered when producing metal AM needle guides and strategies for mitigation:
1. Warping and Distortion:
- Вызов: The intense, localized heat input during PBF processes generates significant thermal gradients and residual stresses as layers fuse and cool. These stresses can cause parts to warp, curl, or distort during the build or after removal from the plate, leading to dimensional inaccuracies.
- Solutions:
- Проектирование на основе моделирования: Using process simulation software to predict thermal behavior and distortion, allowing for design modifications or compensation factors.
- Optimized Orientation: Selecting a build orientation that minimizes large flat surfaces parallel to the build plate and balances thermal stresses.
- Robust Support Strategy: Designing effective support structures to anchor the part securely and conduct heat away during the build.
- Оптимизация параметров процесса: Fine-tuning laser/beam power, scan speed, and hatch patterns to minimize stress accumulation.
- Immediate Stress Relief: Performing a proper stress relief heat treatment cycle immediately after the build, before part removal, is crucial.
2. Support Structure Removal Difficulties:
- Вызов: Removing supports, especially those inside complex internal channels or intricate external features, can be difficult, time-consuming, and risk damaging the part or leaving residual material that compromises function or cleanability.
- Solutions:
- DfAM Focus: Prioritize designing features to be self-supporting (using angles >45°, teardrop channels) whenever possible.
- Access Planning: If internal supports are unavoidable, design access ports or features that allow tools or flushing fluids to reach them. Consider designing the part in modules that are assembled after support removal if internal access is otherwise impossible.
- Optimized Support Design: Using support structures with minimal contact points or specialized geometries designed for easier break-off or dissolution (less common for these metals).
- Advanced Removal Techniques: Utilizing precise methods like micro-machining or wire EDM for delicate support removal.
3. Internal Channel Surface Finish and Cleanliness:
- Вызов: Achieving a smooth internal surface finish within narrow or tortuous channels is difficult with standard polishing methods. Furthermore, completely removing all residual metal powder from these areas is critical but challenging. Rough internal surfaces can impede needle movement, and residual powder is a serious biocompatibility risk.
- Solutions:
- DfAM for Channels: Design channels with the largest feasible diameter, smooth curves, and self-supporting shapes (teardrops) to improve as-built finish and aid powder removal/flushing.
- Advanced Finishing: Employing techniques like abrasive flow machining (AFM) or electropolishing, which can effectively smooth internal surfaces if the geometry allows sufficient flow-through.
- Rigorous Cleaning Protocols: Utilizing multi-stage ultrasonic cleaning, high-pressure flushing with validated solvents/detergents, and potentially micro-CT scanning to verify complete powder removal. Define cleanliness acceptance criteria clearly.
4. Residual Stress Management:
- Вызов: Even with stress relief heat treatment, some residual stress can remain, potentially affecting long-term dimensional stability or mechanical performance (though fatigue is less critical for guides than implants). Improper heat treatment can fail to adequately relieve stress or even negatively impact material properties.
- Solutions:
- Validated Heat Treatment Cycles: Utilizing precisely controlled, material-specific heat treatment protocols (temperature, time, atmosphere) validated for effectiveness.
- Горячее изостатическое прессование (HIP): For highly critical applications, HIP (high temperature and high-pressure inert gas) can be used after printing/stress relief. It helps close internal microporosity and further homogenize the microstructure, effectively eliminating residual stress. However, it adds cost and lead time.
5. Porosity:
- Вызов: Small voids or pores can sometimes form within the printed material due to trapped gas, incomplete fusion between layers, or powder inconsistencies. While often microscopic, excessive porosity can potentially weaken the part or act as initiation sites for cracks (less critical for static guides).
- Solutions:
- High-Quality Powder: Using powder with controlled sphericity, PSD, and low gas content (like that produced by Met3dp’s advanced atomization).
- Optimized Print Parameters: Ensuring parameters (power, speed, layer thickness, atmosphere control) are dialed in for maximum density (>99.5% is typical).
- Process Monitoring: Utilizing in-situ monitoring systems (if available) to detect potential anomalies during the build.
- HIPing: As mentioned, HIP is very effective at closing internal gas porosity.
6. Ensuring Biocompatibility After Post-Processing:
- Вызов: Every post-processing step (handling, machining, blasting, polishing) introduces a risk of surface contamination that could compromise the final part’s biocompatibility. Cleaning and passivation steps must be robust and validated.
- Solutions:
- Controlled Environment: Performing post-processing in a clean environment with proper material handling protocols.
- Validated Cleaning:* Implementing rigorous, multi-stage cleaning processes with validated detergents and rinses specifically designed for medical devices.
- Совместимость материалов: Ensuring all tools, media, and fluids used are compatible with the device material and will not leave harmful residues.
- Effective Passivation (316L): Using validated passivation processes to ensure the protective oxide layer is fully formed.
- Final Testing: Performing lot release testing or periodic biocompatibility tests (e.g., cytotoxicity testing per ISO 10993-5) on representative samples as required by regulatory standards.
7. Cost Management:
- Вызов: Metal AM can have a higher per-part cost than traditional methods for simple designs or high volumes, due to material costs, machine time, and extensive post-processing labor.
- Solutions:
- DfAM for Efficiency: Optimizing designs not just for function but also for printability (e.g., minimizing supports, reducing build height).
- Nesting: Printing multiple parts simultaneously on the build plate to maximize machine utilization.
- Автоматизация: Utilizing automation in post-processing where feasible (e.g., robotic finishing, automated cleaning lines).
- Supplier Collaboration: Working closely with the AM provider to understand cost drivers and make informed design trade-offs.
Successfully producing high-quality metal AM surgical needle guides requires acknowledging and proactively addressing these potential challenges. Partnering with a knowledgeable and experienced service provider is paramount. Companies like Met3dp provide comprehensive solutions, encompassing not just printing but also deep expertise in materials science, DfAM, process optimization, and validated post-processing, enabling them to help clients navigate these complexities and achieve reliable, high-performance surgical instruments.
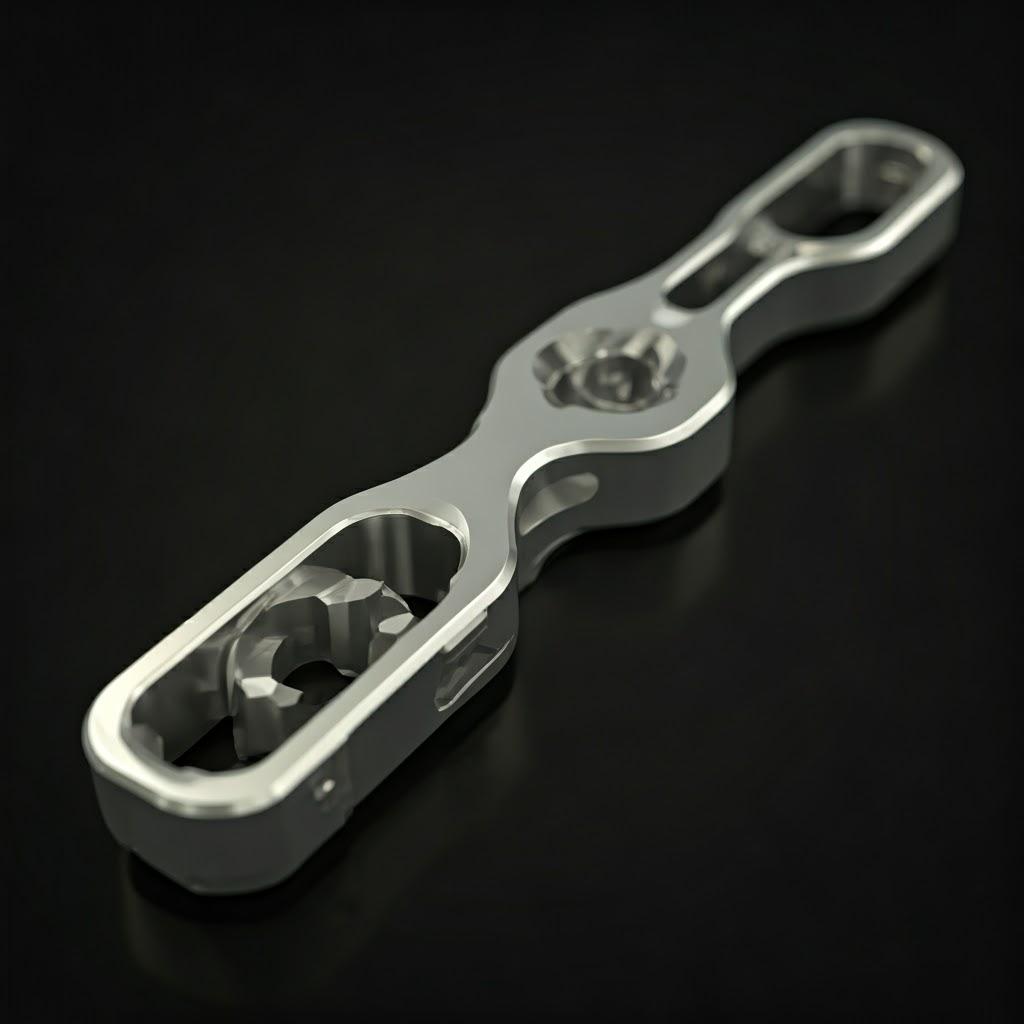
Selecting the Right Metal Additive Manufacturing Service Provider: A Buyer’s Guide
Choosing a supplier for metal additive manufacturing of critical components like surgical needle guides goes beyond simply finding a vendor with a 3D printer. It involves selecting a strategic partner with deep expertise, robust quality systems, and a proven track record in the demanding medical device sector. The right partner will collaborate with your engineering and procurement teams, provide valuable DfAM insights, and reliably deliver high-quality, compliant parts. For procurement managers and engineers vetting potential metal AM service bureaus или medical device contract manufacturers, here are essential criteria to evaluate:
1. Medical Device Expertise & Certifications:
- ISO 13485 Certification: This is non-negotiable. ISO 13485 specifies requirements for a quality management system where an organization needs to demonstrate its ability to provide 1 medical devices and related services that consistently meet customer and applicable regulatory requirements. 2 Ensure the certification scope covers the manufacturing processes involved. 1. books.google.com books.google.com 2. www.sec.gov www.sec.gov
- ISO 9001 Certification: A general standard for quality management systems, often held in conjunction with ISO 13485.
- Proven Medical Track Record: Look for demonstrated experience in manufacturing surgical instruments, implants, or other medical components subject to similar regulatory scrutiny (e.g., FDA regulations in the US, Medical Device Regulation (MDR) in Europe). Ask for case studies or references (respecting confidentiality).
- Regulatory Understanding: The supplier should understand the regulatory landscape relevant to your target markets and be able to provide the necessary documentation and traceability to support your submissions.
2. Material Capabilities & Expertise:
- Specific Material Proficiency: Confirm the supplier has extensive, documented experience printing the required alloys (316L, Ti-6Al-4V) to medical specifications (e.g., ASTM F138, ASTM F136).
- Powder Quality Control: Inquire about their powder sourcing, handling, storage, testing (e.g., chemistry, PSD, morphology), and traceability procedures. Do they recycle powder, and if so, what are their protocols for maintaining quality? Suppliers like Met3dp, who manufacture their own high-quality powders, offer an advantage in controlling this critical input.
- Сертификация материала: The ability to provide full material certifications tracing back to the original powder batch is essential.
3. Technology & Equipment:
- Appropriate AM Process: Ensure they utilize suitable PBF technology (SLM or EBM) with machines known for accuracy and reliability in the required materials.
- Machine Maintenance & Calibration: Verify they have rigorous schedules for machine maintenance and calibration to ensure consistent performance.
- Capacity & Redundancy: Do they have sufficient machine capacity to meet your prototyping and potential low-volume production needs? Is there redundancy in case of machine downtime?
4. Comprehensive Post-Processing Capabilities:
- In-House vs. Outsourced: Understand which post-processing steps (stress relief, support removal, machining, finishing, cleaning, passivation, inspection) are performed in-house versus outsourced. In-house capabilities generally offer better control and integration.
- Validated Processes: Crucially, all critical post-processing steps, especially cleaning and heat treatment, must be validated to ensure they consistently produce the desired results without compromising the part’s integrity or biocompatibility. Request evidence of process validation.
- Экспертиза: Do they possess the necessary equipment and skilled personnel for all required steps, particularly challenging ones like intricate support removal, achieving fine surface finishes, and medical-grade cleaning?
5. Robust Quality Management System (QMS):
- Beyond Certification: Look deeper than the certificate. Assess their QMS documentation, procedures for process control, change management, handling of non-conformances, corrective and preventive actions (CAPA), risk management, and operator training records.
- Traceability: Ensure complete lot traceability from raw powder through all manufacturing and post-processing steps to the final shipped part.
6. Technical Support & Collaboration:
- DfAM Expertise: Does the supplier offer DfAM consultation to help optimize your design for printability, cost-effectiveness, and performance?
- Engineering Support: Are knowledgeable engineers available to discuss technical requirements, material properties, tolerance capabilities, and potential challenges?
- Communication & Project Management: Evaluate their responsiveness, communication clarity, and project management approach. A true partner collaborates proactively.
7. Validation & Inspection Capabilities:
- Metrology Equipment: Do they possess the necessary metrology tools (CMM, 3D scanners, surface profilometers, potentially CT scanners) calibrated to traceable standards?
- Inspection Protocols: Can they accommodate your required inspection plans and provide detailed inspection reports?
- Validation Support: Can they assist with providing data or documentation needed for your device validation efforts?
8. Lead Times, Capacity & Reliability:
- Realistic Estimates: Obtain clear and realistic lead time estimates for prototypes and production runs. Understand factors that influence lead times (queue time, post-processing complexity).
- On-Time Delivery Record: Inquire about their track record for meeting delivery commitments.
- Масштабируемость: Can they support your needs if volumes increase?
9. Cost vs. Value:
- Transparent Pricing: Seek a clear breakdown of costs (material, machine time, labor, NRE).
- Focus on Value: While cost is always a factor, prioritize quality, reliability, expertise, and support. Choosing the cheapest supplier can lead to costly failures, delays, and regulatory issues in the medical field. Consider the total cost of ownership.
Finding a supplier that excels across these criteria is crucial for successfully implementing metal AM for surgical needle guides. Companies like Met3dp, with their foundation in producing both high-performance metal powders and advanced SEBM printing systems, combined with decades of collective expertise in metal additive manufacturing, position themselves as strong partners. They offer comprehensive solutions tailored for demanding industrial applications, including aerospace and medical. Their integrated approach, from material science to application development, provides the reliability and technical support needed for critical medical components. We encourage you to Contact Metal3DP to explore how its capabilities can power your organization’s additive manufacturing goals.
Understanding Cost Drivers and Lead Times for AM Needle Guides
Successfully integrating metal additive manufacturing into your supply chain for surgical needle guides requires a clear understanding of the factors that influence cost and lead times. While AM offers unique benefits, its cost structure and production timeline differ significantly from traditional high-volume methods like injection molding or even standard CNC machining runs. Communicating effectively with your AM service provider and optimizing designs with these factors in mind can help manage expectations and budgets.
Key Cost Drivers:
- Стоимость материала:
- Powder Type: Titanium alloys (Ti-6Al-4V) are inherently more expensive than stainless steels (316L).
- Powder Consumption: The total volume of the part, including any required support structures, directly impacts the amount of powder consumed. While unused powder can often be recycled, there are associated costs with sieving, testing, and qualification of recycled powder.
- Machine Time (Build Time):
- Primary Cost Driver: This is often the most significant cost component. It’s determined by:
- Part Height: The taller the part (in the build orientation), the more layers need to be processed, directly increasing time.
- Volume/Area per Layer: The total volume or cross-sectional area that needs to be scanned by the laser or electron beam on each layer affects the time per layer.
- Параметры машины: Layer thickness (thinner layers improve detail but increase time), scan speed, etc.
- Nesting: Printing multiple parts simultaneously in a single build (build nesting) spreads the constant setup and cooldown times over more parts, significantly reducing the per-part machine time cost. Efficiently packing the build volume is key.
- Primary Cost Driver: This is often the most significant cost component. It’s determined by:
- Сложность дизайна:
- While AM excels at complexity, highly intricate designs might require more extensive support structures, potentially longer print times (if density requires slower scanning), and significantly more effort in post-processing (support removal, finishing).
- Расходы на оплату труда:
- Setup: File preparation (including support generation), machine setup, powder loading, and build monitoring.
- Постобработка: This is often a major labor cost component. Manual support removal, machining operations, surface finishing (especially manual polishing), cleaning, inspection, and documentation all require skilled labor time. The more complex the part and the stricter the requirements, the higher the post-processing labor cost.
- Поддерживающие структуры:
- Beyond the material they consume, supports add cost through the labor required for their careful removal and the subsequent finishing needed on the surfaces where they were attached.
- Quality Assurance & Inspection:
- The level of inspection required (e.g., 100% dimensional inspection vs. sampling, need for CT scanning for internal features, extensive documentation packages) directly impacts cost through specialized equipment usage and quality personnel time.
- Размер партии:
- While AM is well-suited for low volumes and customization, some economies of scale exist. Larger batches allow for fully nested build plates (optimizing machine time per part) and more efficient batch post-processing and quality checks, potentially leading to volume discounts from suppliers. However, the cost reduction per part is generally less dramatic than in mass production techniques.
Typical Lead Time Factors:
Lead time in AM is the total time from order placement to part shipment and is influenced by several sequential stages:
- Pre-Processing: Order review, DfAM consultation (if needed), build file preparation, quoting, and scheduling (typically 1-5 business days).
- Queue Time: Waiting for an appropriate machine to become available. This can vary significantly depending on the supplier’s workload and capacity (can range from days to weeks).
- Print Time: The actual duration of the AM build process (can range from several hours for small, single parts to multiple days for large, complex builds or fully nested plates).
- Постобработка: Often the longest and most variable stage. Includes cooldown, stress relief, part removal, support removal, machining, various finishing steps, cleaning, passivation, and inspection. This can easily take 1-3 weeks or more, depending on the complexity and required steps.
- Перевозки: Transit time to your facility.
Typical Timelines (Estimates):
- Prototypes (1-10 units): Often 1 to 3 weeks, depending heavily on queue time and post-processing complexity.
- Low Volume Production (10-100 units): Typically 3 to 6 weeks, allowing for optimized nesting and batch processing, but still subject to queue times and post-processing demands.
It’s crucial to discuss lead time expectations early with your supplier and understand the breakdown of time for each stage. Factors like requiring specific heat treatments, complex machining setups, or extensive validation testing will add to the overall timeline. Providing complete design information and clear requirements upfront helps streamline the quoting and production process.
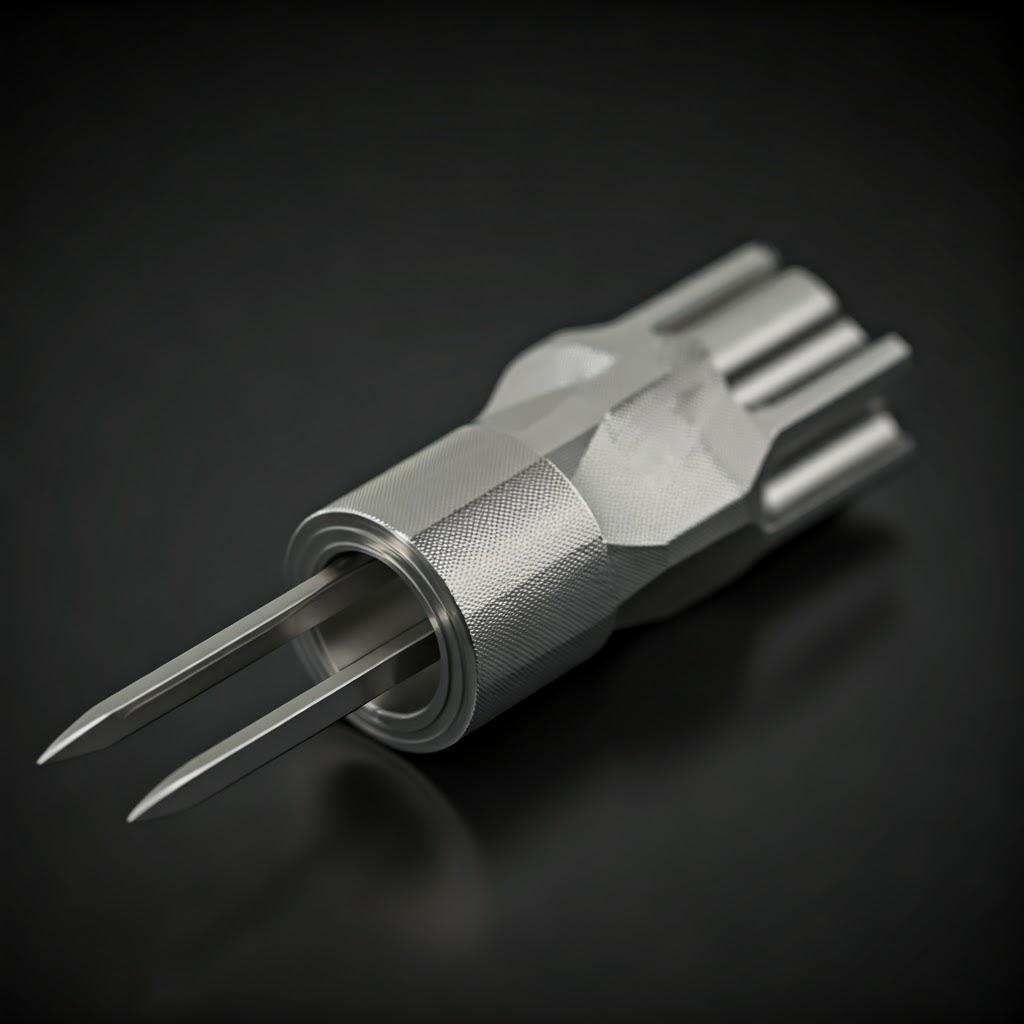
Frequently Asked Questions (FAQ) about Metal AM Surgical Needle Guides
Here are answers to some common questions engineers and procurement managers have about using metal additive manufacturing for surgical needle guides:
Q1: How does the accuracy of AM needle guides compare to machined ones?
A: As-built, metal AM processes typically achieve tolerances around ±0.1 mm to ±0.2 mm, which is generally looser than standard CNC machining capabilities (which can easily reach ±0.01-0.05 mm). However, the primary advantage of AM for needle guides often lies in its ability to create highly complex geometries or patient-specific designs that are difficult or impossible to machine economically. For critical features requiring tighter tolerances (like precise channel diameters, entry/exit points, or mating interfaces), AM parts are routinely post-machined. By combining AM for the overall complex shape with targeted CNC machining for critical features, the final guide can achieve accuracy comparable to fully machined parts where it matters most.
Q2: Are 3D printed metal needle guides reusable and sterilizable?
A: Absolutely. When produced from established medical-grade materials like 316L stainless steel or Ti-6Al-4V titanium alloy using validated AM processes and undergoing appropriate post-processing (including thorough cleaning, surface finishing, and passivation for 316L), these guides are fully compatible with standard hospital sterilization methods like steam autoclaving, ethylene oxide (EtO), or gamma radiation. Reusability depends on the specific design’s robustness, the material’s durability over multiple cycles, and the institution’s protocols for instrument inspection and lifecycle management. Rigorous cleaning between uses according to validated instructions is essential for any reusable surgical instrument.
Q3: What is the typical cost difference between a custom AM guide and a standard machined guide?
A: Comparing a custom, patient-specific AM guide to a стандарт, mass-produced machined guide, the AM guide will generally have a higher per-unit cost. This is due to the individualized nature of the process (batch size of one), potentially longer machine time per part, and often more involved post-processing compared to simplified, high-volume machining. However, the more relevant comparison is often between a custom AM guide and a custom guide produced via traditional methods (e.g., complex 5-axis CNC machining). In this scenario, especially for guides with intricate geometries, metal AM can be cost-competitive or even more economical because it avoids the need for complex programming, specialized fixtures, and potentially multiple setups associated with machining a unique, complex part. The clinical value derived from the customization (improved accuracy, potentially better outcomes) often justifies the cost for specific applications.
Q4: What information is needed to get an accurate quote for an AM needle guide?
A: To provide an accurate quote and assess manufacturability, an AM service provider typically needs:
- A 3D CAD model in a standard format (e.g., STEP, STL – though STEP is preferred for manufacturing).
- Clear specification of the desired material (e.g., 316L per ASTM F138, Ti-6Al-4V per ASTM F136).
- A 2D drawing or annotated model indicating critical dimensions, required tolerances (geometric dimensioning and tolerancing – GD&T is ideal), and necessary surface finish values (Ra) for specific features, especially internal channels and external surfaces.
- The required quantity (for prototypes or production runs).
- Details on any specific post-processing requirements (e.g., electropolishing, specific markings, passivation).
- Any required certifications (e.g., material certification, certificate of conformance).
- The desired lead time or delivery date.
- (Optional but helpful) Information about the intended use or functional requirements, which can help the supplier provide DfAM feedback.
Q5: Can complex internal channels be reliably printed and cleaned?
A: Yes, this is one of the key strengths of AM, but it requires careful design and process control. Reliability depends on:
- DfAM: Designing channels with adequate diameter (typically >0.5-1.0 mm), smooth curves, and self-supporting shapes (like teardrops) significantly improves printability and cleanability.
- Процесс печати: Using optimized parameters and high-quality powder on well-maintained machines minimizes defects. Met3dp’s printing methods are geared towards achieving high density and resolution.
- Постобработка: Implementing validated, multi-stage cleaning processes involving ultrasonics, flushing, and appropriate solvents is critical for complete powder removal. Techniques like abrasive flow machining or electropolishing can further smooth internal channel surfaces if required.
- Verification: Utilizing inspection methods like borescopic visual inspection or micro-CT scanning can verify channel clearance and integrity. Close collaboration between the designer and the AM provider is essential to ensure complex internal channels meet functional and cleanliness requirements.
Conclusion: The Future of Surgery Guided by Metal Additive Manufacturing
The landscape of surgical intervention is continually pushing towards greater precision, less invasive procedures, and more personalized patient care. In this evolution, metal additive manufacturing has firmly established itself not just as a prototyping tool, but as a powerful manufacturing solution for creating next-generation surgical instruments like precision needle guides.
As we’ve explored, metal AM delivers a unique combination of benefits directly applicable to the challenges of surgical guidance:
- Беспрецедентная свобода дизайна: Enabling the creation of complex internal channels, anatomically contoured shapes, and integrated features previously unattainable.
- Массовая кастомизация: Cost-effectively producing patient-specific guides derived from medical imaging, tailoring the instrument to the individual for enhanced accuracy and fit.
- Высокопроизводительные материалы: Utilizing proven biocompatible metals like 316L stainless steel and Ti-6Al-4V titanium alloy, ensuring strength, durability, and safety.
- Accelerated Innovation: Facilitating rapid design iteration and prototyping, speeding the development of novel surgical tools and techniques.
The value proposition extends across the healthcare ecosystem. For surgeons, metal AM guides offer enhanced confidence in targeting accuracy, potentially leading to improved procedural outcomes and reduced complications, especially in complex cases. For компании по производству медицинского оборудования, AM provides a pathway to innovate beyond the constraints of traditional manufacturing, offering differentiated products and enabling patient-specific solutions. For hospitals and patients, it translates to the potential for safer, less invasive procedures, faster recovery times, and access to more personalized treatments.
The successful adoption of metal AM for surgical guides hinges on overcoming challenges related to design optimization (DfAM), process control, rigorous post-processing, and stringent quality assurance. This underscores the critical importance of selecting the right manufacturing partner – one with not only advanced technology but also deep expertise in medical device requirements, materials science, and validated processes.
Такие компании, как Met3dp represent the forefront of this field, offering comprehensive metal AM solutions that span from the production of high-quality, specialized metal powders to the deployment of industry-leading printing systems and application development services. Their integrated approach and commitment to quality provide the foundation needed to reliably produce mission-critical components for the medical industry.
The future of surgery will undoubtedly involve increasingly sophisticated tools designed for specific anatomies and complex procedures. Metal additive manufacturing is no longer a futuristic concept but a present-day reality, playing a vital role in shaping that future. By embracing this technology and collaborating with expert partners, the medical community can continue to advance the boundaries of surgical precision, ultimately benefiting patient care worldwide.
Поделиться
MET3DP Technology Co., LTD - ведущий поставщик решений для аддитивного производства со штаб-квартирой в Циндао, Китай. Наша компания специализируется на производстве оборудования для 3D-печати и высокопроизводительных металлических порошков для промышленного применения.
Сделайте запрос, чтобы получить лучшую цену и индивидуальное решение для вашего бизнеса!
Похожие статьи
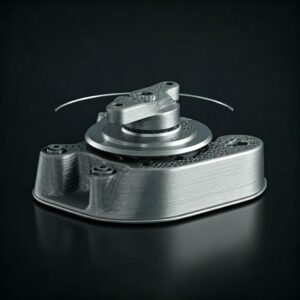
3D-печатные крепления для автомобильных радарных датчиков: Точность и производительность
Читать далее "О компании Met3DP
Последние обновления
Наш продукт
CONTACT US
Есть вопросы? Отправьте нам сообщение прямо сейчас! После получения Вашего сообщения мы всей командой выполним Ваш запрос.
Получите информацию о Metal3DP
Брошюра о продукции
Получить последние продукты и прайс-лист
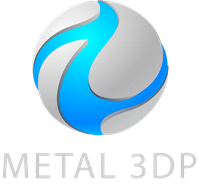
Металлические порошки для 3D-печати и аддитивного производства