Aluminiumpulver för 3D-skrivare
Innehållsförteckning
3d-skrivare aluminiumpulver är en viktig metallråvara för additiv tillverkning med pulverbäddsfusion inom flyg- och rymdindustrin, fordonsindustrin och den allmänna industrin. Den här guiden går igenom aluminiumkvaliteter, pulverspecifikationer, tryckprocesser, sintringsmetoder, mekaniska egenskaper, efterbearbetning, tillämpliga komponenter och mycket mer när det gäller att använda aluminiumpulver i 3D-utskrifter med laserpulverbädd.
Aluminiumpulver för 3D-skrivare Översikt
Aluminiums höga förhållande mellan styrka och vikt, korrosionsbeständighet, termiska egenskaper och mekaniska egenskaper gör det till ett mycket efterfrågat konstruktionsmaterial. Genom att konvertera göt till pulverform möjliggörs additiv tillverkning, vilket frigör..:
- Lättvikt - Minskad komponentmassa för bränslebesparingar i fordon och flygplan
- Konsolidering av delar - Tryckta multifunktionella enheter som kombinerar samverkande komponenter
- Anpassade legeringar - Anpassa kemi som selektivt förstärker tryckta områden efter plats
- Massanpassning - Digitala lager och automatisering av tryckerier möjliggör hög produktmix
Genom att välja lämpliga aluminiumlegeringar och ställa in respektive parametrar för lasertryckningsprocessen kan man utnyttja fördelarna med additiv tillverkning och samtidigt minska bearbetningsdefekterna med hjälp av pulverråvaror av hög kvalitet.
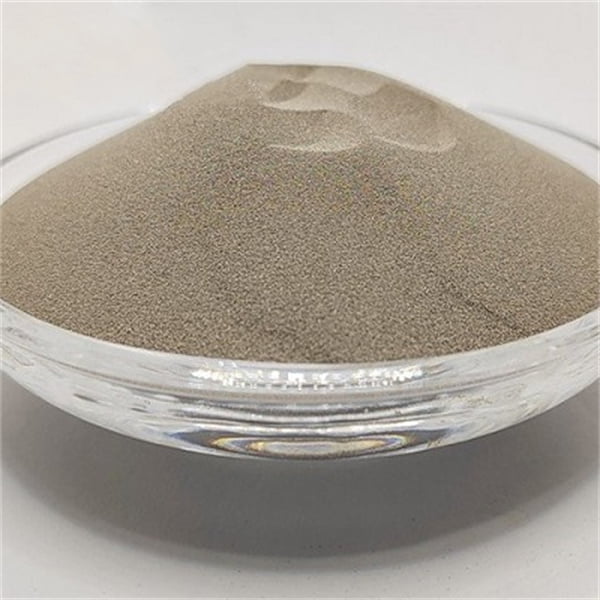
Aluminiumpulver för 3d-skrivare Typer och sammansättningar
Legering | Beskrivning | Fördelar med 3D-utskrifter | Typiska tillämpningar |
---|---|---|---|
AlSi10Mg (aluminium, kisel, magnesium) | Detta är en av de mest använda aluminiumlegeringarna för 3D-utskrifter. Den innehåller kisel (Si) som det primära legeringselementet (cirka 9-11%), tillsammans med magnesium (Mg) för ytterligare förstärkning (0,25-0,45%). | Utmärkt gjutbarhet, som lämpar sig väl för 3D-utskriftsprocessen. Bra balans mellan styrka, duktilitet och korrosionsbeständighet. Erbjuder relativt god svetsbarhet för efterbearbetning eller integrering med traditionellt tillverkade komponenter. | Fordonskomponenter (fästen, motorkomponenter) Marina komponenter (pumphjul, höljen) Delar för allmänna ändamål som kräver en balans mellan bearbetbarhet, styrka och korrosionsbeständighet. |
AlSi7Mg (aluminium, kisel, magnesium) | Mycket lik AlSi10Mg men med något lägre kiselhalt (ca 7%). | Ger en bra balans mellan egenskaper som liknar AlSi10Mg. Kan vara att föredra för applikationer där viktminimering är en prioritet på grund av den något lägre kiselhalten. | Komponenter för flyg- och rymdindustrin (lättviktsstrukturer) Funktionella prototyper som kräver ett bra förhållande mellan styrka och vikt. |
Al-5%Si (Aluminium 5% Kisel) | Denna aluminiumlegering innehåller en lägre kiselhalt (cirka 5%) jämfört med AlSi10Mg och AlSi7Mg. | Ger förbättrad duktilitet och maskinbearbetbarhet jämfört med legeringar med högre kiselhalt. Kan vara lämplig för applikationer som kräver mer formbarhet eller efterbearbetning. | Samlingsskenor och elektriska komponenter Kylflänsar som kräver god värmeledningsförmåga. |
AlSiCuMg (aluminium, kisel, koppar, magnesium) | Denna legering innehåller koppar (Cu) tillsammans med kisel och magnesium för ytterligare förstärkning. | Ger högre hållfasthet jämfört med standardlegeringar av AlSi. Kan vara lämplig för applikationer som kräver goda mekaniska egenskaper vid förhöjda temperaturer. | Strukturella komponenter Delar till flyg- och rymdindustrin (komponenter till landningsställ). |
AlMnSi (aluminium-mangan-kisel) | Denna legering använder mangan (Mn) som det primära förstärkande elementet vid sidan av kisel. | Ger god hållfasthet och slitstyrka. Kan vara lämplig för applikationer som kräver hög slitstyrka eller abrasiva miljöer. | Kugghjul, kedjehjul och slitplåtar. |
Aluminium-zirkoniumlegeringar (Al-Zr) | Dessa legeringar innehåller zirkonium (Zr) för förbättrad prestanda vid höga temperaturer. | Ger utmärkt hållfasthet och krypmotstånd vid förhöjda temperaturer. Lämplig för applikationer som kräver höga driftstemperaturer. | Motorkomponenter (kolvar, topplock) Värmeväxlare |
Metoder och egenskaper för produktion av aluminiumpulver
Metod | Beskrivning | Påverkan på aluminiumpulvers egenskaper |
---|---|---|
Atomisering | Detta är den mest använda metoden för att producera aluminiumpulver för 3D-utskrifter. Smält aluminium sönderdelas i fina droppar med hjälp av en högtrycksström av gas (inert gas som argon) eller vätska (vatten). Dropparna stelnar snabbt till sfäriska partiklar när de utsätts för finfördelningsmediet. | Partikelstorlek och distribution: Atomisering ger god kontroll över partikelstorlek och -fördelning, vilket är avgörande för tryckbarhet och slutliga detaljegenskaper. Finare pulver förbättrar i allmänhet packningsdensiteten men kan leda till problem med flytbarheten. |
Atomisering av gas: | En variant av finfördelning där inert gas (vanligtvis argon) används för att bryta upp den smälta metallströmmen. Ger en renare och mer kontrollerad miljö jämfört med vattenatomisering. | Pulver Renhet: Gasatomisering minimerar kontamineringsriskerna i samband med användning av vatten i atomiseringsprocessen, vilket potentiellt kan leda till högre pulverrenhet. |
Atomisering av vatten: | En kostnadseffektiv metod där en högtrycksvattenstråle stör den smälta aluminiumströmmen. | Partikelmorfologi: Vattenatomisering kan resultera i något mindre sfäriska partiklar jämfört med gasatomisering på grund av stelningsprocessen under interaktion med vatten. |
Snabb stelning | Nya tekniker som Melt Spinning och Rapid Solidification innebär snabb kylning av smält aluminium för att skapa en fin, amorf (icke-kristallin) metallstruktur. Detta material krossas sedan till pulver. | Unik mikrostruktur: Snabb stelning kan skapa pulver med unika mikrostrukturer, vilket potentiellt kan leda till förbättrade mekaniska egenskaper i den slutliga tryckta detaljen. Tryckbarhetsegenskaperna hos sådana pulver kan dock kräva ytterligare utveckling. |
Pulveregenskaper | Beskrivning | Betydelsen av 3D-utskrift |
---|---|---|
Partikelstorlek och distribution | Som tidigare nämnts har partikelstorlek och -fördelning stor betydelse för både tryckbarheten och de slutliga egenskaperna hos den 3D-utskrivna delen. Finare pulver ger bättre packningsdensitet men kan leda till problem med flytbarheten under utskriften. En smal partikelstorleksfördelning säkerställer konsekvent packning och minimerar tomrum i den tryckta delen. | Utskriftsmöjlighet: Pulverets flytbarhet och packningstäthet är avgörande för att få fram tryckta detaljer av god kvalitet. Mekaniska egenskaper: Partikelstorlek och -fördelning kan påverka den slutliga densiteten och styrkan hos den 3D-utskrivna komponenten. |
Partikelmorfologi | Helst bör aluminiumpulver för 3D-utskrift ha en sfärisk eller nästan sfärisk morfologi. Sfäriska partiklar flyter lättare, vilket förbättrar packningstätheten och minimerar tomrum i den tryckta delen. Oregelbundet formade partiklar kan hindra flödesförmågan och potentiellt leda till defekter. | Flytbarhet: God flytbarhet är avgörande för en jämn pulverfördelning under 3D-utskriftsprocessen. |
Skenbar densitet och tappdensitet | Dessa egenskaper representerar pulvrets bulkdensitet under olika förhållanden. Skenbar densitet: Detta avser pulvrets densitet i vila, med hänsyn tagen till mellanrummen mellan partiklarna. Tap Density: Detta återspeglar ett tätare tillstånd som uppnåtts genom en standardiserad tappningsprocess. | Materialanvändning: Högre täthet är i allmänhet önskvärt för effektivt materialutnyttjande och god måttnoggrannhet i den slutliga 3D-utskrivna delen. |
Flytbarhet | Med detta menas hur lätt pulvret flyter under inverkan av tyngdkraften eller andra krafter. God flytbarhet är avgörande för en jämn fördelning av pulvret under 3D-utskriftsprocessen. Pulver med dålig flytbarhet kan leda till inkonsekvenser i packningstätheten och potentiella defekter i den slutliga delen. | Utskriftskvalitet: En jämn flytbarhet säkerställer en jämn pulverdeponering under tryckningen, vilket minimerar risken för problem med skiktadhesion eller inkonsekvenser. |
Specifikationsstandarder för tryckpulver av aluminium
Standard kropp | Standard | Beskrivning | Betydelsen av aluminiumpulver för tryckning |
---|---|---|---|
ASTM International (ASTM) | ASTM B299 - Standard testmetod för mätning av partikelstorlek hos metaller och relaterade material genom elektronisk räkning | Denna standard beskriver en metod för att mäta partikelstorleksfördelningen hos metallpulver med hjälp av elektronisk räkningsteknik. | Ger ett standardiserat tillvägagångssätt för att karakterisera partikelstorleksfördelningen hos aluminiumpulver, en kritisk faktor för tryckbarhet och slutliga delegenskaper. |
ASTM B822 - Standardspecifikation för gasatomiserade smidesaluminiumpulver för additiv tillverkning | Denna standard definierar specifika krav på kemisk sammansättning, partikelstorleksfördelning, flytbarhet och skenbar densitet hos gasatomiserade aluminiumpulver som används vid additiv tillverkning. | Säkerställer en basnivå för kvalitet och prestanda för gasatomiserade aluminiumpulver som ofta används vid 3D-utskrifter. Konsekventa egenskaper bidrar till förutsägbart beteende under utskrift och tillförlitlig delkvalitet. | |
ASTM F3054 - Standardspecifikation för råmaterial för additiv tillverkning av metall | Denna bredare standard ger ett ramverk för att specificera krav för metallpulver som används vid additiv tillverkning, inklusive aluminium. Den omfattar aspekter som kemisk sammansättning, partikelstorleksfördelning, flytbarhet och föroreningsnivåer. | Erbjuder ett heltäckande tillvägagångssätt för att specificera aluminiumpulvers egenskaper som är relevanta för additiv tillverkning. Standardiserar kommunikationen mellan pulvertillverkare, leverantörer av 3D-utskriftsutrustning och slutanvändare. | |
Internationella standardiseringsorganisationen (ISO) | ISO 14644 - Renrum och tillhörande kontrollerade miljöer | Även om denna ISO-standard inte är exklusiv för aluminiumpulver, fastställer den riktlinjer för renrumsmiljöer som används vid produktion och hantering av pulver. | Minimerar kontamineringsriskerna i samband med aluminiumpulver, som kan påverka tryckbarheten och slutdelens kvalitet. Renrumsrutiner är avgörande för att bibehålla pulverets renhet. |
ISO 3262-1 - Kallvalsade obelagda band - Del 1: Definitioner av termer, leveransvillkor, toleranser | Denna standard, som är inriktad på aluminiumband, ger definitioner för relevanta egenskaper som skenbar densitet och tappdensitet, som också är tillämpliga på aluminiumpulver. | Fastställer en gemensam terminologi för pulverdensitetsegenskaper, vilket underlättar kommunikation och datautbyte inom aluminiumtryckindustrin. |
3D-utskriftsprocesser för aluminiumpulver
Faktor | Beskrivning | Betydelse |
---|---|---|
Tekniker för pulverbäddfusion (PBF) | Även om olika 3D-utskriftstekniker kan använda aluminiumpulver är Laser Powder Bed Fusion (LPBF) och Electron Beam Melting (EBM) de vanligaste PBF-teknikerna för aluminiumutskrift. LPBF: Använder en högeffektiv laser för att selektivt smälta och sammanfoga aluminiumpulverpartiklar lager för lager för att skapa den önskade 3D-delen. EBM: Använder en fokuserad elektronstråle för att smälta aluminiumpulvret. EBM erbjuder djupare smältpenetration jämfört med LPBF. | Valet av PBF-teknik (LPBF eller EBM) kan påverka faktorer som uppnåelig detaljstorlek, ytfinish och mekaniska egenskaper på grund av skillnader i energikälla och uppvärmningsmekanismer. |
Parametrar för laser- och elektronstrålar | Laserns (eller elektronstrålens) effekt, skanningshastighet och fokus i PBF har stor betydelse för aluminiumpulverets smältbeteende och de slutliga detaljegenskaperna. | Optimering av dessa parametrar är avgörande för att uppnå korrekt smältning, tillräcklig skiktbindning och minimering av restspänningar i den tryckta delen. |
Förvärmning | Förvärmning av aluminiumpulverbädden före tryckning kan förbättra pulverets flytbarhet och minska risken för sprickbildning i den slutliga delen. | Förvärmning kan vara särskilt fördelaktigt för tjockare sektioner eller delar med höga bildförhållanden, eftersom det främjar en jämnare värmefördelning under tryckningen. |
Stödstrukturer | Aluminiumdelar som trycks med PBF-teknik kräver ofta stödstrukturer för att förhindra att de vrider sig eller sjunker ihop under tryckprocessen på grund av de höga temperaturerna. Dessa stöd tillverkas vanligtvis av samma aluminiumpulver och avlägsnas senare genom efterbearbetningssteg. | Noggrann utformning och placering av stödstrukturer är avgörande för att säkerställa att detaljen förblir intakt under tryckningen och för att minimera utmaningarna vid borttagning av stöd. |
Efterbearbetning | Aluminiumdelar som tryckts med PBF kan genomgå olika efterbehandlingssteg, t.ex: Het isostatisk pressning (HIP): En behandling med högt tryck och hög temperatur som hjälper till att eliminera inre porositet i den tryckta delen, vilket förbättrar de mekaniska egenskaperna. Värmebehandling: Kontrollerade värmecykler kan användas för att ytterligare förbättra specifika mekaniska egenskaper som hållfasthet eller duktilitet. Maskinbearbetning: För att uppnå exakta dimensionstoleranser eller ytfinish. | Efterbehandlingsbehandlingar kan avsevärt påverka den 3D-tryckta aluminiumdelens slutliga prestanda och estetik. |
Aluminiumpulver Tryck Mekaniska egenskaper
Fastighet | Beskrivning | Påverkan på funktionaliteten | Vanliga legeringar |
---|---|---|---|
Draghållfasthet (MPa) | Den maximala spänning som en tryckt del kan motstå innan den dras isär. | Bestämmer detaljens lastbärande kapacitet. Högre draghållfasthet möjliggör användning i applikationer med större påfrestningar. | AlSi10Mg (410-460 MPa), 6061 (200-310 MPa), 7075 (460-570 MPa) |
Sträckgräns (MPa) | Den spänning vid vilken en tryckt del börjar deformeras plastiskt. | Anger den punkt där detaljen permanent böjer sig under belastning. Högre sträckgräns möjliggör elastiskt beteende under påfrestning. | AlSi10Mg (245-270 MPa), 6061 (130-200 MPa), 7075 (320-450 MPa) |
Töjning vid brott (%) | Hur mycket en tryckt del töjer sig innan den spricker. | Påverkar detaljens duktilitet och förmåga att absorbera energi innan den går sönder. Högre töjning indikerar större flexibilitet. | AlSi10Mg (5-9%), 6061 (12-35%), 7075 (6-14%) |
Utmattningshållfasthet (MPa) | Den maximala påfrestning som en tryckt komponent kan motstå under ett visst antal belastningscykler. | Avgörande för delar som utsätts för upprepade påfrestningar. Högre utmattningshållfasthet ger längre livslängd. | Begränsad data tillgänglig, vanligtvis lägre än motsvarande bulkprodukter |
Densitet (g/cm³) | Den tryckta delens massa per volymenhet. | Påverkar vikten och påverkar användningsområdena. Aluminium erbjuder inneboende lättviktsegenskaper. | AlSi10Mg (2,67), 6061 (2,70), 7075 (2,81) |
Elasticitetsmodul (GPa) | Det tryckta materialets styvhet, som anger hur mycket det deformeras under belastning. | Bestämmer detaljens styvhet och dess förmåga att motstå böjning. Högre modul indikerar ett styvare material. | AlSi10Mg (70-75), 6061 (68-70), 7075 (71-78) |
Hårdhet (HV) | Det tryckta materialets motståndskraft mot intryckning av ytan. | Påverkar slitstyrka och repkänslighet. Högre hårdhet indikerar bättre slitstyrka. | AlSi10Mg (100-130), 6061 (90-130), 7075 (150-180) |
Porositet (%) | Mängden tomt utrymme inom den tryckta delen. | Kan påverka mekanisk hållfasthet och utmattningsprestanda. Lägre porositet är i allmänhet önskvärt. | Varierar beroende på tryckprocess och parametrar, vanligtvis 0,1-5% |
Anisotropi | Variationen av mekaniska egenskaper beroende på tryckriktningen. | Kan uppstå på grund av tryckprocessens lager-för-lager-karaktär. Noggrann design och efterbearbetning kan minimera anisotropi. | Mer framträdande i vissa legeringar och tryckprocesser |
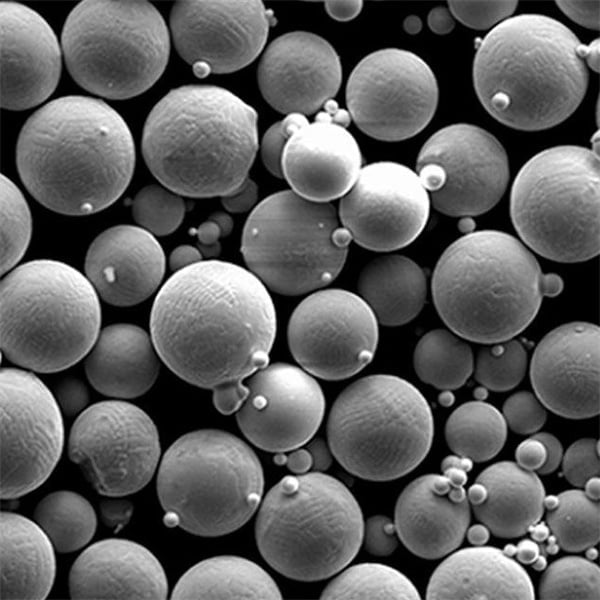
Metoder för efterbearbetning av tryckta aluminiumdelar
Process | Beskrivning | Fördelar | Nackdelar | Tillämpningar |
---|---|---|---|---|
Borttagning av stöd | Detta första steg eliminerar tillfälliga strukturer som höll delen uppe under tryckningen. Beroende på aluminiumtryckprocessen inkluderar metoderna: Wire EDM (Electrical Discharge Machining): En tunn tråd skär med precision av stöd med hjälp av elektriska gnistor, vilket minimerar termisk distorsion. Bandsågning: Ett snabbt och kostnadseffektivt alternativ för enkla geometrier, men kan lämna ojämna kanter. Manuell borttagning: För ömtåliga delar eller små stöd används tänger eller avbitartänger för försiktig borttagning. | Minimerar skador på detaljen. Säkerställer åtkomst till interna funktioner. | Trådgnistning kan vara långsamt för komplexa detaljer. Bandsågning kan kräva ytterligare efterbehandling. Manuell borttagning är tidskrävande för invecklade stöd. | Alla tryckprocesser i aluminium Detta är särskilt viktigt för detaljer med invändiga kanaler eller komplexa geometrier. |
Ytbehandling | Aluminiumdelar kan ha en grov textur på grund av tryckningens lager-för-lager-karaktär. Olika tekniker uppnår olika estetiska och funktionella mål: Slipning/blästring: Slipande partiklar slätar ut ytan och kornstorleken avgör hur slät ytan blir. Vibrerande efterbehandling: Delarna tumlas i en mediabädd med vattenblandning, vilket ger en jämn matt yta. Polering: Med hjälp av polerskivor och polermedel skapas en högglansig, reflekterande yta. Kemisk fräsning: Ett kontrollerat kemiskt bad avlägsnar material för en jämn finish och exakt dimensionskontroll. | Förbättrar estetik och passform. Förbättrar korrosionsbeständigheten. Kan exponera inre porositet för vissa metoder. | Slipning/blästring kan vara arbetsintensivt för stora delar. Mediablästring kan föra med sig ytföroreningar. Polering kräver skickliga operatörer. Kemisk fräsning kan kräva ytterligare efterbearbetning för en slät yta. | Alla tryckprocesser i aluminium Slipning/blästring för lätt utjämning eller förbehandling för andra metoder. Vibrerande ytbehandling för en jämn, matt yta på komplexa detaljer. Polering för högblank finish på synliga komponenter. Kemisk fräsning för högprecisionsdetaljer eller detaljer som kräver viktreduktion. |
Värmebehandling | Kontrollerade värme- och kylcykler ändrar aluminiumets mikrostruktur och förbättrar dess mekaniska egenskaper: Lösningsglödgning: Uppvärmning av detaljen för att lösa upp förstärkande utfällningar, följt av snabb kylning för ett mjukt, segt tillstånd. Åldershärdning: Lösningsglödgning följt av kontrollerad åldring vid förhöjd temperatur, vilket skapar en stark och hård mikrostruktur. | Förbättrar hållfasthet, hårdhet och utmattningshållfasthet. Skräddarsyr egenskaper för specifika tillämpningar. | Kan förvränga delar om de inte kontrolleras på rätt sätt. Kan kräva ytterligare maskinbearbetning efter värmebehandling. | Alla aluminiumlegeringar är inte värmebehandlingsbara. Används för detaljer som kräver hög hållfasthet i förhållande till vikt eller förbättrad utmattningshållfasthet. |
Het isostatisk pressning (HIP) | Denna högtrycks- och högtemperaturbehandling eliminerar inre porositet i den tryckta delen: Delen utsätts för ett tryck av inert gas vid förhöjd temperatur, vilket tvingar hålrummen att kollapsa. | Förbättrar detaljernas densitet och mekaniska egenskaper. Minskar initiering av utmattningssprickor. | Dyr process med specialutrustning. Kan orsaka dimensionella förändringar. | Avgörande för delar i applikationer med höga påfrestningar eller som kräver läckagetäthet. Används ofta för säkerhetskritiska komponenter. |
Maskinbearbetning | Konventionella bearbetningstekniker som CNC-fräsning och -borrning kan användas för att uppnå exakta toleranser och egenskaper: Kan skapa hål, gängor och andra funktioner som inte är lätta att åstadkomma med tryckning. Förbättrar dimensionell noggrannhet. | Ökar bearbetningstiden och kostnaden. Kan avlägsna material och blottlägga inre porositet. | För detaljer som kräver snäva toleranser eller specifika egenskaper som inte kan tryckas. Används ofta i kombination med andra efterbehandlingsmetoder. |
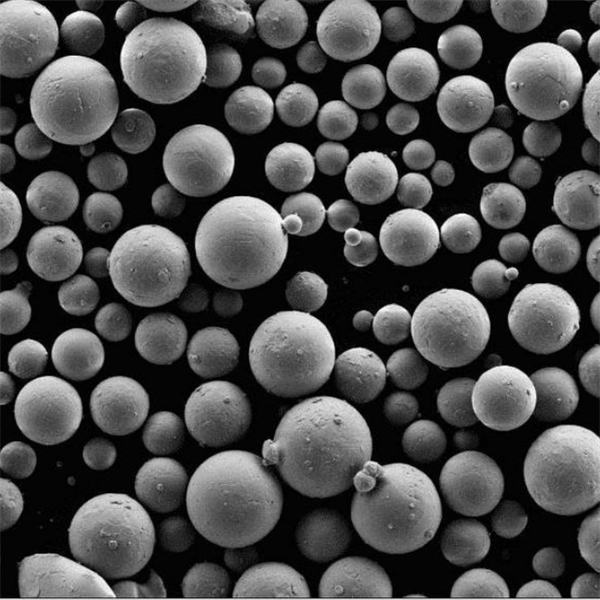
Tillämpningar av aluminiumpulver för 3D-skrivare
Tillämpning | Fastigheter med hävstångseffekt | Fördelar | Exempel |
---|---|---|---|
Komponenter för flyg- och rymdindustrin | Högt förhållande mellan styrka och vikt, utmärkt utmattningshållfasthet | Lättviktsstrukturer med exceptionell mekanisk prestanda för optimerad flygeffektivitet och bränsleekonomi | - Flygplansvingar och flygplanskroppar - Motorkomponenter - Landningsställskomponenter |
Bildelar | God maskinbearbetbarhet, svetsbarhet och gjutbarhet | Komplexa lättviktskomponenter som bidrar till ökad bränsleeffektivitet och prestanda | - Anpassade konsoler och fästen - Strukturella komponenter - Värmeväxlare |
Robotik och automation | Skräddarsydda mekaniska egenskaper för specifika behov | Lätta robotarmar och gripdon med hög hållfasthet och styvhet för exakt manipulation | - Endeffektorer - Kopplingar - Strukturella komponenter i robotar |
Medicinska implantat | Biokompatibla legeringar, skräddarsydda ytegenskaper | Anpassningsbara implantat med god biokompatibilitet och osseointegration (beninväxt) för förbättrade patientresultat | - Knä- och höftproteser - Kranioplastimplantat - Tandimplantat |
Konsumentvaror | Estetik, korrosionsbeständighet | Högkvalitativa, lätta slutprodukter med ett unikt metalliskt utseende och lång hållbarhet | - Cykelramar - Komponenter till sportartiklar - Komponenter till lyxklockor |
Prototypframställning och lågvolymproduktion | Designfrihet, snabb iteration | Funktionella prototyper och lågvolymsproduktion av komplexa aluminiumdelar utan behov av traditionella verktyg | - Konceptmodeller för validering av design - Funktionella prototyper för testning - Begränsad upplaga eller kundanpassade produkter |
Värmeväxlare | Hög värmeledningsförmåga | Effektiva värmeväxlare med låg vikt för värmehantering i olika applikationer | - Radiatorer och intercoolers för fordon - Kylkomponenter för elektronik - Kylflänsar för kraftelektronik |
Gjutformar och verktyg | Konforma kylkanaler | Konforma kylkanaler för snabb stelning och kortare cykeltider vid formsprutning | - Insatsverktyg för formsprutning - Gjutformar - Verktyg för additiv tillverkning |
Leverantörer som erbjuder tryckpulver av aluminium
Leverantörens namn | Produktbeskrivning | Ytterligare information | Webbplats |
---|---|---|---|
MSE-leveranser LLC | Erbjuder ett sortiment av aluminiumbaserade metallpulver för additiv tillverkning (3D-printing) i olika kvaliteter och partikelstorlekar. Populära alternativ inkluderar: MSE PRO 6061: Pulver av aluminiumlegering för allmänt bruk med goda mekaniska egenskaper och svetsbarhet. MSE PRO AlSi10Mg: Höghållfast aluminiumlegeringspulver med god gjutbarhet, idealiskt för flyg- och fordonstillämpningar. MSE PRO 2024: Aluminiumlegeringspulver som är känt för sitt höga förhållande mellan styrka och vikt och sin utmattningshållfasthet, lämpligt för flygplanskomponenter. | Minsta orderkvantitet kan förekomma. Erbjuder anpassning av partikelstorlek på begäran. Innehåller tekniska datablad för varje pulver. | https://www.msesupplies.com/ |
Atlantic Equipment Engineers (AEE) | En ledande leverantör av aluminiumpulver med hög renhet, bl.a: Atomiserade aluminiumpulver: Finns i olika partikelmorfologier med god flytbarhet och packningstäthet. Aluminiumflingor och -granulat: Ger unika ytegenskaper för specifika tillämpningar. | Erbjuder ett brett utbud av partikelstorlekar för att passa olika tryckprocesser. Kan tillhandahålla anpassade lösningar för specifika behov av aluminiumpulver. Omfattande branscherfarenhet och certifieringar. | https://micronmetals.com/product-category/high-purity-metal-powders-compounds/ |
Praxair Surface Technologies (genom Astro Alloys Inc.) | Distributör av TruForm metallpulver, inklusive aluminiumpulver som är särskilt utformade för tillämpningar inom additiv tillverkning. Erbjuder pulver med sfärisk morfologi för optimalt flöde och deponering. Finns i olika aluminiumlegeringar av flyg- och rymdkvalitet. | Bred produktportfölj med möjlighet till kundanpassning. Konstruerade pulver för olika AM-processer som DMLS och SLM. Etablerat rykte inom metallpulverindustrin. | https://www.astroalloys.com/ |
Eplus3D | Specialiserat på aluminiumpulver för 3D-utskrift, med fokus på högpresterande aluminiumlegeringar: AlSi7Mg och AlSi10Mg: Populära val för flyg- och fordonsindustrin på grund av deras goda hållfasthet och gjutbarhet. | Erbjuder applikationsspecifika pulver för optimala resultat. Effektiviserat produktsortiment för enklare urval. Fokus på forskning och utveckling av avancerade tryckpulver i aluminium. | https://www.eplus3d.com/products/aluminum-3d-printing-material/ |
Andra potentiella leverantörer | Flera andra företag distribuerar tryckpulver i aluminium, med varierande produktlinjer och specialiteter. Exempel på sådana är: SLM-lösningar Höganäs AB APEX Additiv tillverkning | Undersök enskilda leverantörer för specifika pulveregenskaper och målapplikationer. Tänk på faktorer som prissättning, minsta orderkvantitet och teknisk support. |
Överväganden om prissättning av aluminiumpulver
Parameter | Prispåverkan |
---|---|
Distribution Storlek | Tätare distributioner pressar avkastningen och driver kostnaderna |
Kvalitetsstandarder | Flyg- och rymdkvaliteter som kräver rigorösa defektkontrolltester |
Ordervolym | Prototypprojekt med små serier ger premier |
Kundspecifikationer | Eventuella unika olje-/fuktmål, förpackningar påverkar prissättningen |
Legeringstillägg | Elementblandningar med högre renhet överför laddningar |
Tabell 7. Faktorer i leveranskanalen som påverkar prissättningen av aluminiumpulver upp till 5-10 gånger spotpriset för basal aluminiumråvara
Att förutse volymkraven 12-18 månader före stora tryckprojekt ger störst möjlighet att minimera kostnaderna för batch- och kvalificeringstester.
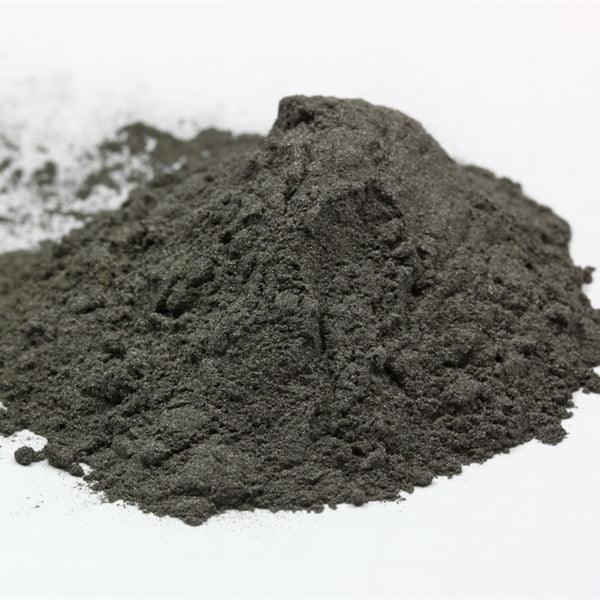
Vanliga frågor och svar
F: Behåller återanvändning av aluminiumpulver sina egenskaper?
S: Ja, pulver återprocessas väl med endast blygsam syre- och fuktupptagning som behöver övervakas innan återanvändningsblandningar blir skadliga.
F: Vad orsakar problem med porositet i tryckdelar av aluminium?
A: Instängda gasporer som härrör från dålig förvaring och hantering av pulver eller brist på avluftning under smältning smälter samman till defekter som försämrar hållfastheten.
F: Är värmebehandling bra för tryckta aluminiumkomponenter?
S: Ja, korrekt utformad termisk bearbetning reproducerar temperaturer som ökar duktiliteten och maximerar ambulerande mekaniska egenskaper som är unika för kontrollerade stelningsvägar för tryck.
F: Vilken aluminiumlegering är bäst lämpad för laserpulverbäddsfusionstillsats?
S: Scalmalloy-pulver - en legering av aluminium, skandium och zirkonium som patenterats av APWorks - ger en oöverträffad kombination av styrka och temperaturbeständighet när den är helt efterbehandlad.
Dela på
MET3DP Technology Co, LTD är en ledande leverantör av lösningar för additiv tillverkning med huvudkontor i Qingdao, Kina. Vårt företag är specialiserat på 3D-utskriftsutrustning och högpresterande metallpulver för industriella tillämpningar.
Förfrågan för att få bästa pris och anpassad lösning för ditt företag!
Relaterade artiklar
Om Met3DP
Senaste uppdateringen
Vår produkt
KONTAKTA OSS
Har du några frågor? Skicka oss meddelande nu! Vi kommer att betjäna din begäran med ett helt team efter att ha fått ditt meddelande.
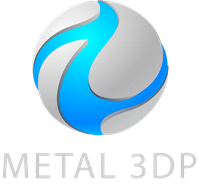
Metallpulver för 3D-printing och additiv tillverkning