3D Printing Metal Powder:Ensure the safety of plasma atomization
Innehållsförteckning
The world of 3D Printing Metal Powder has revolutionized manufacturing, allowing for the creation of complex, customized parts with unprecedented ease. But this innovative process relies heavily on a crucial element: 3D-utskrift av metallpulver.
This fine, metallic dust is the building block for numerous 3D printing technologies like Selective Laser Melting (SLM) and Electron Beam Melting (EBM). However, producing such metal powder requires a specific technique called Plasmaatomisering, which involves intense heat and molten metal, raising safety concerns.
This article delves deep into the world of Metallpulver för 3D-utskrift, focusing on plasma atomization. We’ll explore:
- The intricacies of plasma atomization: We’ll break down the process, highlighting its advantages and limitations.
- A diverse range of metal powders: We’ll dive into the properties and applications of 10 distinct metal powder models.
- Safety considerations during plasma atomization: We’ll discuss potential risks and essential measures to ensure a safe working environment.
- Frequently Asked Questions (FAQs): We’ll address common concerns regarding plasma atomization and metal powder safety.
By the end, you’ll gain a comprehensive understanding of plasma atomization, its role in creating metal powder for 3D printing, and the crucial steps to prioritize safety throughout the process.
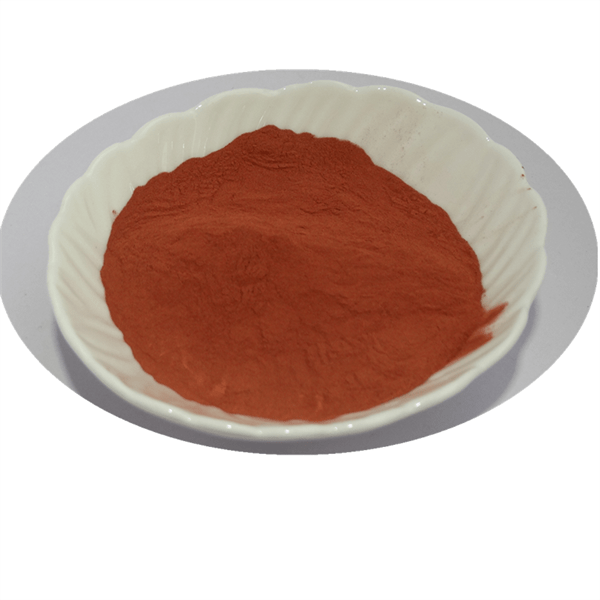
3D Printing Metal Powder:Understanding Plasma Atomization
Imagine a high-powered torch that instantly melts metal, converting it into a fine mist of tiny droplets. That’s the essence of plasma atomization. Here’s how it works:
- Feedstock Preparation: The process begins with a solid metal ingot, which is then chopped into smaller pieces.
- Plasma Generation: An inert gas, typically argon, is passed through an electric arc, creating an intense plasma stream with temperatures exceeding 10,000°C (18,000°F).
- Metal Melting and Atomization: The molten metal ingot pieces are injected into the plasma stream, causing them to melt instantly. The high-velocity plasma then breaks the molten metal into a fine spray of droplets.
- Solidification and Collection: As the droplets rapidly cool in the surrounding atmosphere, they solidify into individual metal particles. These particles are then collected and sieved to obtain the desired powder size distribution.
Advantages of Plasma Atomization:
- Hög renhet: The inert gas environment minimizes contamination, resulting in high-purity metal powders.
- Spherical Morphology: The rapid cooling promotes the formation of spherical particles, ideal for efficient 3D printing processes.
- Brett utbud av material: Plasma atomization can handle a vast array of metals, including reactive and high-melting-point materials.
Limitations of Plasma Atomization:
- Energy Intensive: The process requires significant energy to generate and maintain the high-temperature plasma stream.
- Costly Equipment: Setting up and maintaining plasma atomization equipment can be expensive.
- Säkerhetsfrågor: The high temperatures and hazardous materials involved demand strict safety measures to protect workers.
Exploring the Spectrum of Metal Powders
Now, let’s explore a diverse selection of metal powders commonly used in 3D Printing Metal Powder, each with unique properties and applications:
1. Stainless Steel 316L: This versatile, corrosion-resistant powder is widely used in aerospace, medical devices, and general engineering applications.
2. Titanium Grade 2: This lightweight, high-strength powder is ideal for biomedical implants, aerospace components, and sporting goods due to its excellent biocompatibility and strength-to-weight ratio.
3. Inconel 625: This high-temperature alloy powder offers exceptional resistance to oxidation and corrosion, making it suitable for jet engine components, chemical processing equipment, and heat exchangers.
4. Aluminum Si7Mg0.6: This readily weldable powder delivers a good balance of strength and ductility, making it popular for automotive components, consumer electronics, and architectural applications.
5. Copper: This highly conductive powder is valuable for electrical components, heat exchangers, and applications requiring high thermal conductivity.
6. Nickel: This versatile powder finds applications in electronics, batteries, and chemical processing due to its excellent corrosion resistance and catalytic properties.
7. Cobalt Chrome (CoCr): This biocompatible powder is a popular choice for orthopedic implants and dental prosthetics due to its high wear resistance and strength.
8. Tungsten: This high-density, high-melting-point powder is used in applications requiring extreme durability and heat resistance, such as armor plating and welding electrodes.
9. Niobium: This superconductor powder, often used in combination with other metals, exhibits zero electrical resistance at extremely low temperatures, making it crucial for high-performance magnets and medical imaging equipment.
Potential security risk assessment
While plasma atomization offers numerous benefits for producing high-quality metal powders, it’s crucial to acknowledge the inherent safety risks associated with the process. Here are some key areas of concern:
- High Temperatures: The intense heat generated during plasma creation (reaching over 10,000°C) poses a significant fire hazard. Accidental spills or equipment malfunctions could lead to burns or even explosions if not handled with proper safety protocols.
- Hazardous Materials: The process often involves handling potentially hazardous materials, such as heavy metals and flammable gases. Inhalation of metal dust or exposure to harmful fumes can cause respiratory problems and other health issues for workers.
- Noise Pollution: The plasma generation process creates a loud, high-pitched sound that can exceed safe noise levels and damage workers’ hearing if adequate protection isn’t employed.
- Explosion Risk: Any malfunction in the equipment or improper handling of flammable gases can lead to a potential explosion, causing severe injuries or property damage.
Providing Safety Operating Procedures and Protective Measures
To mitigate these risks and ensure a safe work environment for all personnel involved in plasma atomization, strict safety protocols must be implemented. These include:
- Engineering Controls: Utilizing enclosed systems, ventilation systems, and remote operation whenever possible can significantly reduce exposure to hazardous materials, heat, and noise.
- Personal Protective Equipment (PPE): Equipping workers with appropriate PPE, such as heat-resistant clothing, respirators, and ear protection, is crucial to minimize the risk of injuries and health issues.
- Regular Maintenance and Inspection: Regularly inspecting and maintaining equipment is essential to identify and address potential malfunctions before they occur.
- Safety Training and Education: Comprehensive training programs should be provided to all personnel involved in the process, covering safe operating procedures, emergency protocols, and hazard identification.
- Signage and Labeling: Proper signage and labeling should be used to clearly identify potential hazards and safety instructions throughout the work area.
By adhering to these safety measures and fostering a culture of safety awareness, plasma atomization facilities can minimize risks and operate responsibly, protecting both their employees and the surrounding environment.
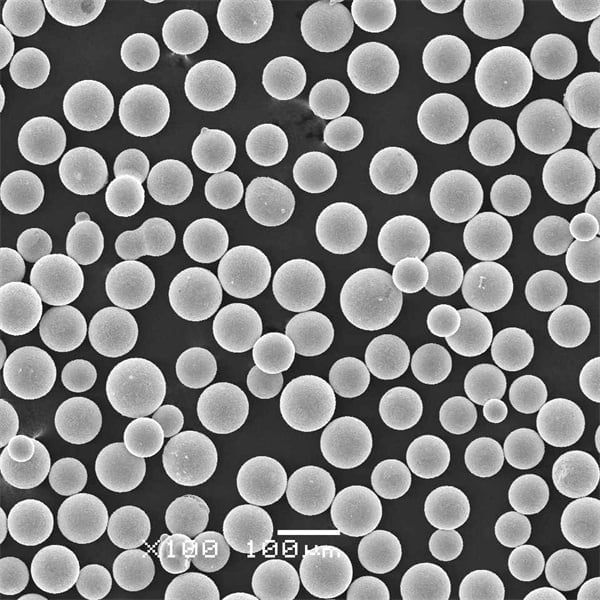
Vanliga frågor
1. Is plasma atomization environmentally friendly?
While plasma atomization offers significant advantages in terms of producing pure and high-quality metal powders, it does have an environmental impact. The process consumes significant energy, contributing to greenhouse gas emissions. Additionally, the handling of hazardous materials requires strict regulations and proper disposal practices to minimize environmental pollution.
2. How does the cost of different metal powders vary?
The cost of metal powders can vary significantly depending on several factors, including:
- The cost of the raw material: The price of the base metal plays a major role in the final cost of the powder. For example, precious metals like gold or platinum will naturally be more expensive than common metals like iron.
- The complexity of the production process: More complex processes like plasma atomization, compared to simpler methods like gas atomization, often lead to higher production costs, which are reflected in the final price of the powder.
- Market demand and supply: The demand and availability of specific metal powders can also influence their cost. If the demand is high and the supply is limited, the price will likely be higher.
3. What are the future trends in plasma atomization technology?
The future of plasma atomization technology is expected to see advancements in several areas:
- Energy efficiency: Research and development efforts are aimed at improving the energy efficiency of the process to reduce environmental impact and operating costs.
- Automation: Increased automation in plasma atomization facilities can enhance safety, consistency, and production efficiency.
- Development of new materials: As the demand for advanced materials in various industries grows, plasma atomization is expected to play a crucial role in producing customized and high-performance metal powders for these applications.
By addressing potential safety concerns, continuously improving the technology, and exploring its full potential for producing diverse metal powders, plasma atomization will remain a vital tool in the ever-evolving world of 3D printing and advanced manufacturing.
Dela på
MET3DP Technology Co, LTD är en ledande leverantör av lösningar för additiv tillverkning med huvudkontor i Qingdao, Kina. Vårt företag är specialiserat på 3D-utskriftsutrustning och högpresterande metallpulver för industriella tillämpningar.
Förfrågan för att få bästa pris och anpassad lösning för ditt företag!
Relaterade artiklar
Om Met3DP
Senaste uppdateringen
Vår produkt
KONTAKTA OSS
Har du några frågor? Skicka oss meddelande nu! Vi kommer att betjäna din begäran med ett helt team efter att ha fått ditt meddelande.
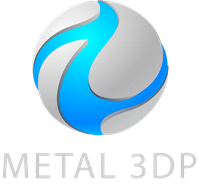
Metallpulver för 3D-printing och additiv tillverkning
FÖRETAG
PRODUKT
cONTACT INFO
- Qingdao City, Shandong, Kina
- [email protected]
- [email protected]
- +86 19116340731