Precision Frames for Space Telescopes via Metal AM
Innehållsförteckning
Introduction: The Critical Role of Precision Frames in Modern Space Telescopes
Space telescopes represent the pinnacle of observational astronomy, providing humanity with unprecedented views of the cosmos, unhindered by Earth’s atmospheric distortion. From the iconic Hubble Space Telescope to the revolutionary James Webb Space Telescope (JWST), these complex instruments rely on an intricate interplay of optics, sensors, and structural components working in perfect harmony. Central to their function are the precision frames that form the backbone of the telescope’s structure. These are not mere skeletal supports; they are highly engineered components responsible for maintaining the critical alignment of mirrors, lenses, detectors, and other sensitive instruments under the extreme conditions of space.
The demands placed upon these space telescope structures are immense. They must:
- Maintain Extreme Stability: Even microscopic misalignments, measured in nanometers or micrometers, can drastically degrade image quality. The frame must possess exceptional dimensional stability, resisting deformation caused by thermal fluctuations, mechanical vibrations during launch and operation, and the inherent settling of materials over mission lifetimes spanning years or decades.
- Withstand Harsh Launch Conditions: The journey to orbit is violent. Frames must endure extreme g-forces, acoustic loads, and vibrations without compromising their structural integrity or post-deployment alignment.
- Operate in a Vacuum and Extreme Temperatures: Space is a vacuum with temperatures swinging hundreds of degrees Celsius between direct sunlight and shadow. Materials must not outgas (which could contaminate sensitive optics) and must perform predictably across this vast thermal range. Low or controlled thermal expansion is often paramount.
- Be Lightweight: Every kilogram launched into orbit comes at a significant cost. Minimizing the mass of structural components like frames is crucial for mission feasibility and cost-effectiveness, freeing up mass budget for scientific instruments or propellant.
Traditionally, manufacturing these precisionskomponenter involved subtractive methods, machining complex shapes from large billets of specialized materials, or assembling numerous smaller, precisely machined parts. While effective, these methods often lead to significant material waste, long lead times, design limitations (especially for complex internal geometries), and potential points of failure at joints.
Skriva in Metal Additive Manufacturing (Metal AM), often referred to as metal 3D-utskrifter. This transformative technology offers a paradigm shift in how we design and produce critical aerospace manufacturing components, including telescope frames. By building parts layer by layer directly from metal powder, AM enables the creation of highly complex, lightweight, and integrated structures that were previously impossible or prohibitively expensive to manufacture. Companies at the forefront of this revolution, like Met3dp, provide comprehensive additiv tillverkningslösningar, leveraging advanced printing technologies and high-performance materials to meet the stringent requirements of space applications. Met3dp’s focus on industry-leading print volume, accuracy, and reliability makes them a key partner for organizations pushing the boundaries of space exploration. The ability to consolidate multiple parts into a single printed component, optimize structures using topology optimization, and utilize advanced materials with tailored properties positions metal AM as a vital tool for developing the next generation of space telescopes. This blog post will delve into the specifics of using metal AM for producing precision telescope component frames, exploring the applications, benefits, materials, design considerations, and how to partner with expert leverantörer av additiv tillverkning.
Applications and Functions: Where are Metal AM Telescope Frames Deployed?
Metal Additive Manufacturing is not just a theoretical possibility for space hardware; it is increasingly being adopted for critical structural applications where its unique benefits offer tangible advantages. Precision frames, manufactured using AM, serve diverse and vital functions within a space telescope’s architecture. Understanding these specific applications highlights why the capabilities of metal AM are so well-suited to the demands of the aerospace structural parts market.
Key Applications and Functions:
- Optical Bench Structures:
- Function: The optical bench is the primary structure that holds the telescope’s main optical elements (mirrors, lenses) in precise alignment relative to each other and to the focal plane instruments. It is arguably the most stability-critical structure.
- AM Advantage: Metal AM allows for the creation of highly complex, topologically optimized optical bench structures. These designs can achieve exceptional stiffness-to-weight ratios, minimizing mass while maximizing stability. Integrated features like mounting points, kinematic mounts, and internal baffling can be built directly into the structure, reducing part count and assembly complexity. Materials like Invar, with its near-zero coefficient of thermal expansion (CTE), are ideal candidates, and AM enables their use in complex geometries that are difficult to machine. Procurement managers seeking satellite component suppliers capable of delivering highly stable, lightweight optical benches are increasingly turning to AM specialists.
- Mirror Support Systems:
- Function: Large primary, secondary, or tertiary mirrors require sophisticated support systems. These frames must hold the mirror securely without inducing surface distortions (print-through) under gravitational release (going from 1g on Earth to 0g in space) and thermal changes. They often incorporate actuators for fine alignment.
- AM Advantage: AM enables the fabrication of intricate mirror support systems, including lightweight backplanes and whiffle tree structures, often incorporating complex lattice or cellular designs. This minimizes mass behind the mirror while providing uniform support. For segmented mirrors, like those on JWST, AM can produce the complex frame structures needed to mount and align each segment precisely. The ability to print in high-strength, lightweight alloys like Ti-6Al-4V is particularly beneficial here.
- Instrument Housing and Mounts:
- Function: Scientific instruments (cameras, spectrographs, sensors) need to be securely mounted to the telescope structure and often require environmentally controlled housings. These housings must provide structural support, thermal isolation or control, radiation shielding, and precise interfacing with the optical path.
- AM Advantage: Metal AM facilitates the creation of bespoke instrument housing manufacturing solutions. Complex internal channels for thermal management fluids, integrated shielding structures, and precise mounting interfaces can be designed and printed as a single piece. This integration reduces potential leak paths, simplifies assembly, and allows for highly conformal designs that optimize volume and mass. Companies requiring custom space mission hardware find AM offers unparalleled design freedom.
- Struts, Trusses, and Booms:
- Function: These elements often form the connections between major subsystems, such as connecting a secondary mirror assembly to the primary structure or deploying sunshields or antennas. They require high stiffness, low mass, and often specific thermal expansion properties.
- AM Advantage: AM allows for the production of highly optimized struts and truss elements. Topology optimization can be used to place material only where structurally needed, resulting in ultra-lightweight components. Functionally graded materials or lattice structures can be incorporated to tailor stiffness and vibration damping characteristics. This capability is critical for suppliers of aerospace structural parts looking to minimize launch mass.
- Kinematic Mounts and Alignment Mechanisms:
- Function: Ensuring and maintaining alignment often requires specialized mounts that allow for precise, repeatable positioning and adjustment while isolating components from structural stresses.
- AM Advantage: Metal AM can produce complex kinematic mounts with integrated flexures, hard-stops, and interfacing features. The design freedom allows for compact, highly functional mechanisms that would be difficult or impossible to create through traditional assembly of multiple machined parts.
Industry Demand:
The demand for these components comes from major aerospace prime contractors, government space agencies (like NASA, ESA, JAXA), and increasingly, commercial space companies involved in Earth observation, communications, and space exploration. Procurement managers and engineers in these organizations are actively seeking satellite component suppliers who can deliver components meeting stringent performance, quality (e.g., AS9100 certification), and reliability standards. Metal AM providers like Met3dp, with expertise in relevant materials and processes, are positioned to meet this growing demand for advanced space mission hardware. The ability to rapidly iterate designs and produce flight-qualified hardware makes AM an attractive option for accelerating mission timelines.
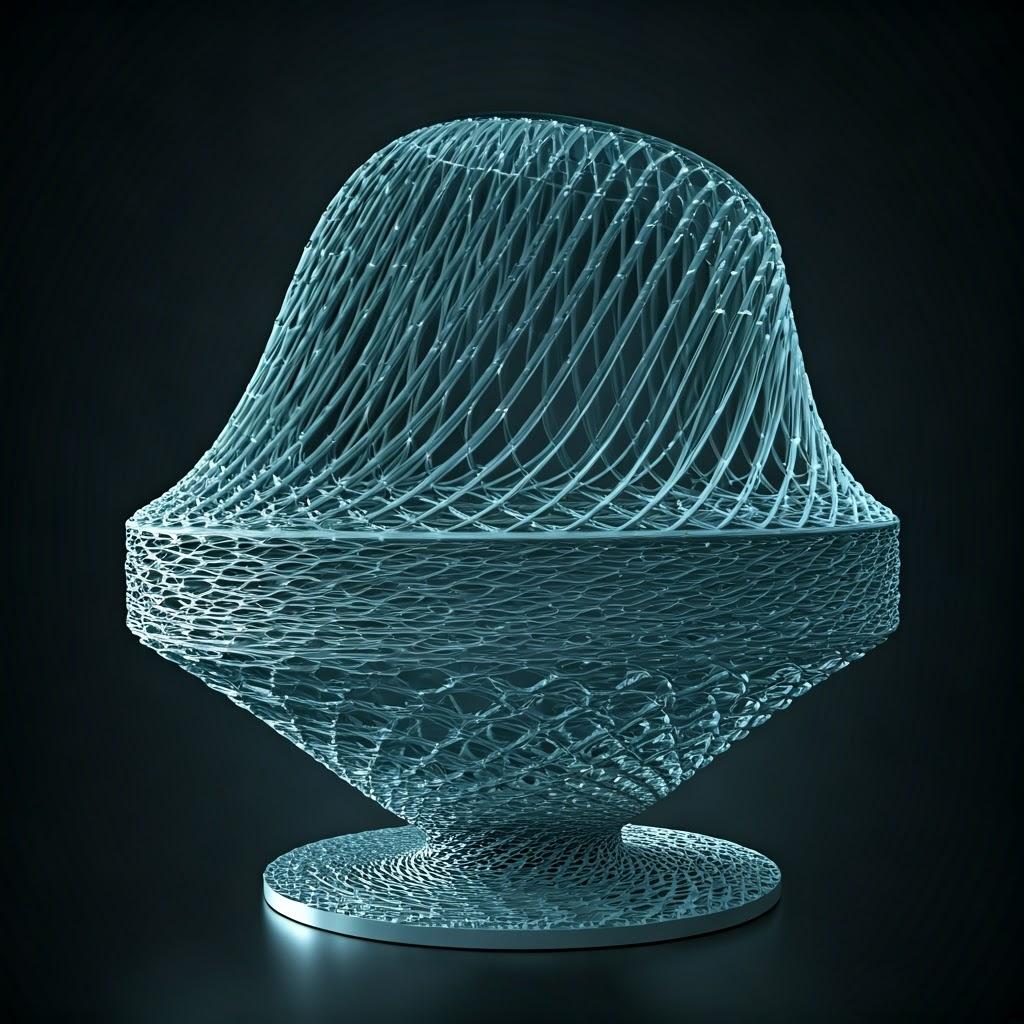
Why Choose Metal Additive Manufacturing for Telescope Component Frames?
While traditional manufacturing methods like CNC machining, casting, and fabrication have served the aerospace industry for decades, Metal Additive Manufacturing (AM) presents compelling advantages specifically tailored to the unique challenges of producing precision frames for space telescopes. Choosing AM is not merely about adopting a new technology; it’s about unlocking performance, efficiency, and design possibilities previously unattainable. Let’s compare AM with traditional methods and highlight the key benefits for aerospace structural parts.
Comparison: Metal AM vs. Traditional Manufacturing for Telescope Frames
Funktion | Metal Additive Manufacturing (e.g., PBF-LB/M, PBF-EB/M) | Traditional Manufacturing (CNC Machining, Casting, Fabrication) | Key Implications for Telescope Frames |
---|---|---|---|
Designens komplexitet | High (complex geometries, internal channels, lattices) | Moderate to Low (limited by tool access, mold constraints) | AM enables highly optimized, lightweight designs (topology optimization). |
Konsolidering av delar | Excellent (multiple parts integrated into one print) | Limited (requires assembly of multiple components) | Reduced part count, weight, assembly time, and potential failure points. |
Utnyttjande av material | High (minimal waste, powder is mostly recyclable) | Low to Moderate (significant waste in machining, gating in casting) | Lower “buy-to-fly” ratio, more sustainable, cost-effective for expensive materials. |
Lättvikt | Superior (topology optimization, lattice structures) | Good (pocketing, thin walls) but often less optimal | Crucial for reducing launch costs and maximizing payload capacity. |
Lead Time (Prototype) | Snabb (direkt digital tillverkning) | Slow (tooling, fixture setup, programming) | Rapid design iteration and validation possible with AM. |
Lead Time (Production) | Can be longer per part, but faster for complex parts | Faster per part for simple geometries, slower for complex | AM excels for low-to-mid volume production of highly complex components. |
Materialalternativ | Growing range of specialized alloys (Invar, Ti64, etc.) | Wide range, well-established properties | AM offers key aerospace materials like those provided by Met3dp. |
Initial verktygskostnad | Low to None (digital process) | High (molds, dies, fixtures) | AM is cost-effective for custom or low-volume parts. |
Achievable Tolerances | Good (as-printed), Excellent (with post-machining) | Excellent (inherent to high-precision machining) | AM often requires post-machining for critical interfaces. |
Export to Sheets
Key Advantages of Metal AM for Telescope Frames:
- Unprecedented Lightweighting: This is perhaps the most significant advantage for space applications. Metal AM, combined with topologioptimering software, allows engineers to design frames where material is placed only where stress requires it. This results in organic-looking, highly efficient structures that maintain stiffness and strength while drastically reducing mass compared to traditionally designed and machined parts. The ability to incorporate internal lattice structures further enhances lightweighting potential, offering tailored mechanical properties. For procurement managers evaluating buy vs build space components, the weight savings offered by AM can fundamentally change mission economics.
- Complex Geometry Fabrication: Space telescope frames often require intricate shapes to accommodate optical paths, mounting interfaces, cable routing, and thermal control features. AM builds parts layer by layer, removing many of the constraints imposed by machining access or casting mold design. This enables the creation of complex geometry fabrication that integrates multiple functions into a single component. Internal cooling channels, complex manifolds, or convoluted structural supports become feasible.
- Part Count Reduction: By redesigning assemblies for AM, multiple individual components can often be consolidated into a single, monolithic printed part. This significantly reduces the need for fasteners, welds, or brazing, which are potential sources of failure, add weight, and increase assembly time and complexity. Fewer parts mean simpler logistics, reduced inspection requirements, and inherently greater structural integrity for aerospace structural parts.
- Reduced Lead Times for Complex Prototypes and Parts: While the printing process itself can take hours or days, AM eliminates the need for traditional tooling (molds, dies, fixtures), which can take weeks or months to produce. For complex prototypes or low-volume production runs, the total time from design finalization to finished part can be significantly shorter with AM. This lead time reduction manufacturing capability accelerates development cycles and allows engineers to test physical hardware faster.
- Materialeffektivitet: Subtractive manufacturing, especially CNC machining, can start with a large billet of expensive aerospace-grade material (like Invar or Ti-6Al-4V) and remove up to 80-90% of it as chips. AM uses only the material needed for the part and supports, with unused powder typically being recyclable. This high material utilization is particularly advantageous when working with costly or difficult-to-machine alloys.
- Customization and Rapid Iteration: AM is ideal for producing bespoke components tailored to specific mission requirements. Design modifications can be implemented quickly in the CAD model and sent directly to the printer, facilitating rapid iteration and design optimization without the cost penalties associated with modifying traditional tooling.
Met3dp, utilizing advanced powder bed fusion technologies (like Selective Electron Beam Melting – SEBM, and Laser Powder Bed Fusion – L-PBF/SLM available through their 3D-utskrift av metall services), empowers aerospace companies to leverage these benefits fully. Their expertise in process control and materials science ensures that the manufactured frames meet the demanding performance and quality standards required for spaceflight.
Material Deep Dive: Invar and Ti-6Al-4V for Optimal Performance
The choice of material is absolutely critical for space telescope frames, directly impacting stability, weight, and overall mission success. Metal Additive Manufacturing offers the capability to work with advanced alloys specifically chosen for their properties in the harsh environment of space. Among the most important are Invar (specifically Invar 36) and Ti-6Al-4V (Grade 5 Titanium). Understanding their properties and why they are suited for AM telescope frames is essential for engineers and wholesale metal powder purchasers.
Invar 36 (FeNi36 / Alloy 36 / 1.3912): The Stability Champion
- What it is: Invar is an iron-nickel alloy containing approximately 36% nickel. Its name comes from the word “invariable,” referring to its uniquely low coefficient of thermal expansion (CTE) at room temperatures and moderately cryogenic temperatures.
- Why it Matters for Telescopes: The primary challenge for telescope optics is maintaining focus and alignment as temperatures fluctuate in orbit. Materials expand and contract with temperature changes, causing focal shifts and misalignments. Invar’s extremely low CTE (about 1.2 x 10⁻⁶ /°C near room temperature, roughly 1/10th that of steel) minimizes these thermally induced dimensional changes. This makes it the gold standard for:
- Optical benches
- Mirror metering structures (rods or frames connecting primary and secondary mirrors)
- Mounts for sensitive optical elements
- Laser optical resonators
- AM Considerations: Invar can be challenging to machine traditionally due to its gummy nature. Metal AM offers a viable pathway to create complex Invar components. However, printing Invar requires careful control of process parameters to manage residual stresses (due to the thermal gradients in AM) and achieve the desired low CTE properties in the final part. Post-print heat treatment (annealing) is typically essential to relieve stress and optimize dimensional stability. Leading metal powder for additive manufacturing suppliers, like Met3dp, utilize advanced atomization techniques (gas atomization, PREP) to produce high-quality, spherical Invar powder optimized for AM processes, ensuring good flowability and consistent melt behavior. Met3dp’s commitment to high-quality metallpulver ensures reliable performance.
- B2B Relevance: Aerospace contractors require reliable low CTE metal powder suppliers who can provide Invar 36 powder with consistent quality, appropriate particle size distribution (PSD), and proven performance in AM systems.
Ti-6Al-4V (Grade 5 Titanium): The Lightweight Strength
- What it is: Ti-6Al-4V (often called Ti64) is the workhorse alpha-beta titanium alloy, known for its excellent combination of high strength, low density, stiffness, and good corrosion resistance.
- Why it Matters for Telescopes: While its CTE is higher than Invar’s (around 8.6 x 10⁻⁶ /°C), Ti-6Al-4V’s key advantage is its exceptional strength-to-weight ratio. It is roughly 40% lighter than steel but offers comparable or higher strength. This makes it ideal for:
- Primary structural frames where overall mass reduction is paramount
- Support trusses and struts
- Instrument housings
- Brackets and mounting hardware
- Components where high specific stiffness (stiffness per unit weight) is critical
- AM Considerations: Ti-6Al-4V is one of the most mature materials for metal AM processes like L-PBF and EBM. It generally prints well, producing parts with mechanical properties often meeting or exceeding those of wrought counterparts, especially after appropriate heat treatments (like stress relief annealing or Hot Isostatic Pressing – HIP). HIP is particularly effective at closing any residual internal porosity, achieving near 100% density, which is critical for fatigue life and fracture toughness in demanding aerospace applications. Met3dp produces high-sphericity Ti-6Al-4V powders optimized for both laser and electron beam AM systems, catering to the needs of high-strength titanium alloy wholesale buyers.
- B2B Relevance: The aerospace industry is a major consumer of Ti-6Al-4V. AM providers and part manufacturers need consistent, high-purity Ti-6Al-4V powder meeting stringent aerospace specifications (e.g., AMS standards).
Material Property Comparison (Typical Values):
Fastighet | Enhet | Invar 36 (Annealed) | Ti-6Al-4V (Annealed) | Significance for Telescope Frames |
---|---|---|---|---|
Täthet | g/cm3 (lb/in3) | 8.1 (0.29) | 4.43 (0.16) | Ti64 offers significant weight savings (~45% lighter). |
Coefficient of Thermal Expansion (CTE) (at 20°C) | 10−6/°C (10−6/°F) | 1.2 (0.7) | 8.6 (4.8) | Invar provides vastly superior dimensional stability against temperature changes. |
Tensile Strength (Ultimate) | MPa (ksi) | 480 (70) | 950 (138) | Ti64 is much stronger, suitable for high-load bearing structures. |
Utbyteshållfasthet | MPa (ksi) | 275 (40) | 880 (128) | Ti64 has significantly higher yield strength. |
Young’s Modulus (Stiffness) | GPa (Msi) | 145 (21) | 114 (16.5) | Invar is inherently stiffer, but Ti64 has better specific stiffness. |
Termisk konduktivitet | W/(m·K) | 10 | 6.7 | Both are relatively poor conductors; thermal management is needed. |
Export to Sheets
Met3dp’s Role in Advanced Powders:
A successful AM outcome heavily relies on the quality of the input material. Met3dp addresses this critical need by employing industry-leading powder production technologies:
- Gas Atomization (GA): Utilizes high-pressure inert gas jets to break up a stream of molten metal into fine droplets that solidify into spherical powder particles. Met3dp’s unique nozzle and gas flow designs enhance sphericity and flowability, crucial for uniform powder bed spreading in AM machines.
- Process med roterande elektrod och plasma (PREP): A rotating electrode of the desired alloy is melted by a plasma torch, flinging off molten droplets that solidify in flight into highly spherical powders with very few trapped gas pores (satellites). This process is known for producing exceptionally clean and spherical powders, ideal for demanding applications.
By controlling the powder manufacturing process, Met3dp ensures its avancerade metallpulver, including Nickel-based alloys like Invar and Titanium alloys like Ti-6Al-4V and specialized Titanium Aluminides (TiAl) or shape memory alloys (TiNi), meet the high purity, sphericity, flowability, and particle size distribution requirements for producing dense, high-quality metal AM parts with superior mechanical properties. Their extensive portfolio caters to the specific needs of aerospace manufacturing challenges, providing the foundation for reliable and high-performance telescope component frames. Partnering with a knowledgeable material supplier like Met3dp is a crucial step for any organization looking to leverage AM for space applications.
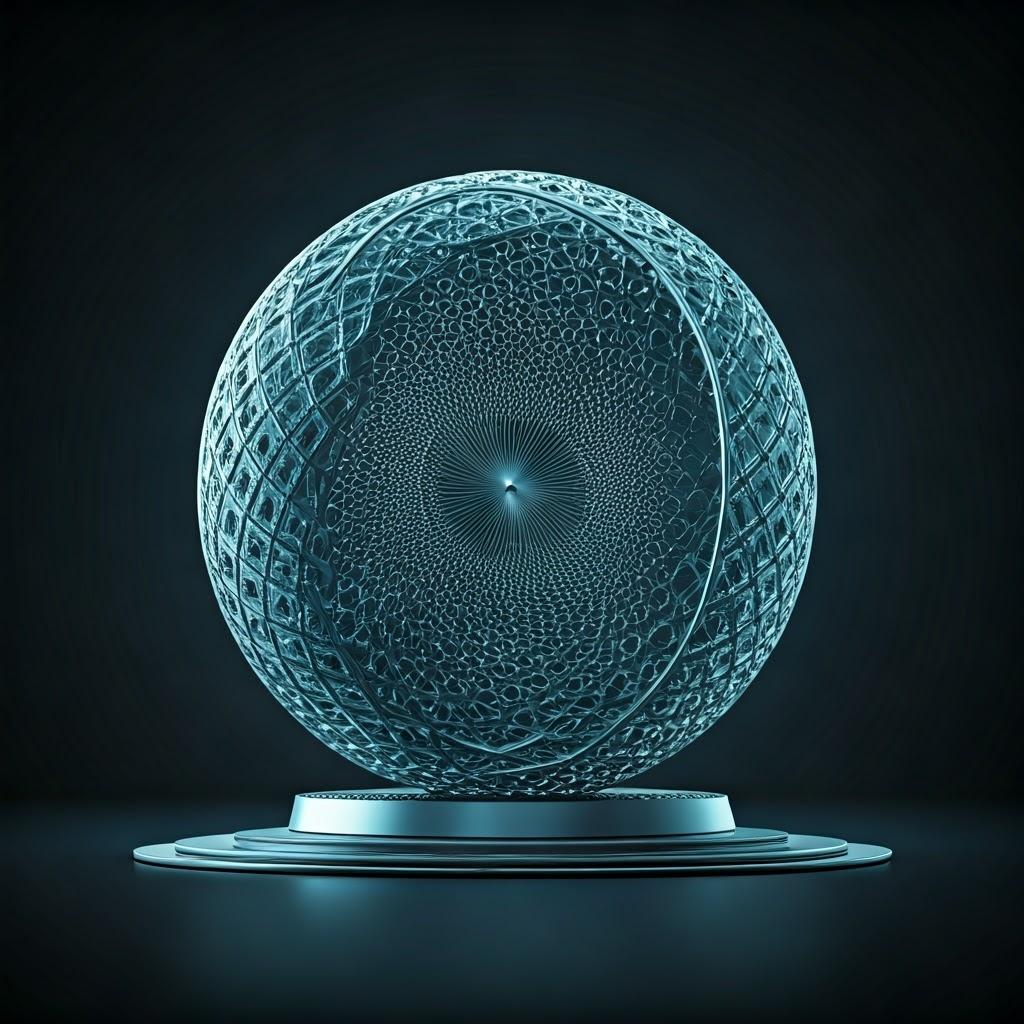
Design Optimization Strategies for AM Telescope Frames (DfAM)
Successfully leveraging Metal Additive Manufacturing (AM) for high-performance components like space telescope frames requires more than simply converting an existing design file to an AM-compatible format. It demands a fundamental shift in design thinking, known as Design för additiv tillverkning (DfAM). DfAM is a methodology that integrates manufacturing process constraints and capabilities directly into the design phase, enabling the creation of parts optimized for performance, weight, cost, and producibility via AM. For engineers designing critical aerospace structures, mastering DfAM principles is key to unlocking the full potential of metal 3D printing.
Implementing DfAM involves several key strategies specifically relevant to telescope frames:
- Topology Optimization:
- Concept: This computational technique uses Finite Element Analysis (FEA) to determine the most efficient material distribution within a defined design space, subject to specific load cases (e.g., launch vibrations, operational stresses, thermal loads) and performance objectives (e.g., maximizing stiffness, minimizing mass).
- Process: Engineers define the component boundaries, connection points, keep-out zones, applied loads, and target goals. The software iteratively removes material from low-stress areas, resulting in highly optimized, often organic-looking shapes that place material precisely where it’s needed for structural integrity.
- Benefit for Telescope Frames: This is paramount for achieving significant lightweighting while maintaining or even increasing structural stiffness, crucial for reducing launch costs and ensuring stability. Topology optimization services, often offered by AM providers or specialized engineering firms, can yield frames that are 30-60% lighter than their traditionally designed counterparts, without compromising performance. This allows for larger apertures or more instrumentation within a given mass budget.
- Lattice and Cellular Structures:
- Concept: Instead of solid material, DfAM allows for the incorporation of internal lattice or cellular structures (e.g., strut-based lattices, gyroids, Schwarz P structures based on Triply Periodic Minimal Surfaces – TPMS).
- Benefit for Telescope Frames:
- Enhanced Lightweighting: Lattices offer exceptional stiffness-to-weight and strength-to-weight ratios compared to solid material.
- Skräddarsydda egenskaper: Different lattice types and densities can fine-tune mechanical properties like vibration damping, energy absorption (useful during launch), and even thermal conductivity.
- Multi-functional Design: Lattices can create internal channels for fluid flow (thermal management) or wiring conduits, integrated directly into the structure.
- Ansökan: Lattice structure design metal AM can be used to infill large volumes within a frame, create optimized strut elements, or design specific impact-absorbing zones. Careful analysis is needed to ensure manufacturability and inspectability.
- Del Konsolidering:
- Concept: Re-evaluating assemblies traditionally made from multiple fastened or welded parts and redesigning them as a single, monolithic AM component.
- Benefit for Telescope Frames: Reduces part count, eliminates fasteners (weight, potential failure points), simplifies assembly, shortens supply chains, and can improve overall structural integrity by removing joints. Integrating brackets, mounting interfaces, and kinematic features directly into the main frame structure is a common DfAM strategy for generative design space components.
- Support Structure Strategy and Minimization:
- Concept: Powder bed fusion processes require support structures for overhangs (typically features angled less than 45 degrees from the horizontal build plane) and to anchor the part to the build plate, managing thermal stresses. However, supports consume material, add print time, require removal (a significant post-processing step), and can mar the part surface.
- DfAM Approach:
- Orientation: Choosing the optimal build orientation optimization can significantly reduce the need for supports.
- Self-Supporting Angles: Designing features with angles greater than 45 degrees wherever possible.
- Feature Modification: Modifying geometries slightly (e.g., changing a horizontal hole to a teardrop shape) to make them self-supporting.
- Designing for Removal: Ensuring support structures are accessible for easy removal without damaging delicate features.
- Utilizing Lattices as Support: In some cases, internal lattices can serve dual purposes as structural elements and self-supporting features.
- Feature Design Considerations:
- Minsta funktionsstorlek: Adhering to the minimum wall thickness, hole diameter, and feature resolution achievable by the specific AM process and machine (e.g., typically 0.4-1.0 mm for PBF-LB/M).
- Hole Orientation: Printing holes vertically often yields better circularity and surface finish than horizontal holes, which may require internal supports.
- Stress Concentrations: Incorporating fillets and smooth transitions at corners and junctions to reduce stress risers, improving fatigue life.
- Machining Allowances: Intentionally adding extra material (e.g., 0.5-2 mm) to surfaces that require high precision or specific finishes achieved through post-machining. These are key metal printing design guidelines.
Met3dp understands that effective DfAM is crucial for project success. While they offer advanced Tryckmetoder and materials, their team also provides engineering support additive manufacturing expertise, collaborating with clients to optimize designs, ensure manufacturability, and maximize the benefits of AM for demanding applications like space telescope frames. This collaborative approach ensures that the final design is not only innovative but also practical and cost-effective to produce.
Achieving Unparalleled Precision: Tolerance, Surface Finish, and Accuracy in AM Frames
For space telescopes, precision is not just a goal; it’s a fundamental requirement. The ability of a telescope frame, manufactured via Metal AM, to meet stringent specifications for tolerance, surface finish, and dimensional accuracy directly impacts optical alignment, instrument interfacing, and overall mission performance. Understanding what is achievable and the factors influencing precision is crucial for engineers designing and procurement managers sourcing these critical components.
Defining the Terms:
- Tolerance: The permissible limit or limits of variation in a physical dimension. For AM parts, this refers to how closely the final part’s dimensions match the nominal dimensions specified in the CAD model (e.g., ±0.1 mm).
- Surface Finish (Roughness): A measure of the texture of a surface, typically quantified by parameters like Ra (average roughness) or Rz (peak-to-valley roughness). It affects friction, wear, sealing, and how well coatings adhere.
- Dimensionell noggrannhet: A measure of the overall conformity of the manufactured part to its intended design geometry. It encompasses not just linear dimensions but also form features like flatness, circularity, and parallelism.
Achievable Precision with Metal AM:
Metal AM processes, particularly Laser Powder Bed Fusion (L-PBF / SLM) and Electron Beam Melting (EBM), offer good precision directly from the machine, but typically cannot match the ultra-high precision of dedicated CNC machining without secondary operations.
- As-Printed Tolerances:
- Generally, typical tolerances for L-PBF fall in the range of ±0.1 mm to ±0.2 mm (or ±0.1% to ±0.2% for larger dimensions).
- EBM, operating at higher temperatures, often has slightly looser tolerances, perhaps ±0.2 mm to ±0.4 mm, but benefits from lower residual stress.
- These values are highly dependent on the material, machine calibration, part size, geometry, and process parameters used.
- As-Printed Surface Finish (Ra):
- Top Surfaces: Usually the smoothest, often Ra 5-15 µm.
- Vertical Walls: Typically Ra 8-20 µm, influenced by layer thickness and powder characteristics.
- Upward-Facing Surfaces: Similar to vertical walls.
- Downward-Facing (Support) Surfaces: Tend to be roughest after support removal, potentially Ra 15-50 µm or more, often requiring further finishing.
- Post-Machined Precision: For critical interfaces – such as mounting points for mirrors or instruments, bearing surfaces, or precise mating surfaces – post-print CNC machining is almost always necessary. Machining can achieve:
- Tolerances: Down to ±0.01 mm or even tighter, depending on the operation and material.
- Surface Finish (Ra): Below 1 µm is readily achievable, with polishing potentially reaching nanometer-level smoothness if required.
Factors Influencing Precision:
Achieving the best possible dimensional accuracy metal printing standards depends on meticulous control throughout the AM ecosystem:
- Machine Calibration: Regular calibration of the laser/electron beam system, scanner/deflection system, and powder recoating mechanism is vital.
- Process Parameters: Laser/beam power, scan speed, layer thickness, hatch spacing, and focus significantly impact melt pool stability, shrinkage, and surface quality. Met3dp’s expertise in process optimization is key here.
- Materialegenskaper: Powder characteristics (particle size distribution, morphology, flowability) influence powder bed density and melt behavior. The material’s thermal properties dictate shrinkage and stress build-up. Met3dp’s high-quality powders contribute to consistency.
- Termisk hantering: Temperature gradients during the build cause residual stresses, which can lead to distortion (warpage). Build plate heating (common in L-PBF), higher chamber temperatures (inherent to EBM), and optimized scan strategies help mitigate this.
- Part Geometry and Orientation: Large flat surfaces are prone to warpage. Tall, thin features can be challenging to build accurately. Orientation affects support needs, which impacts surface finish.
- Stödstrukturer: Supports anchor the part and conduct heat but influence the finish of supported surfaces and can contribute to stress if not designed correctly.
- Efterbearbetning: Stress relief heat treatments are crucial for dimensional stability before final machining. Improper clamping during machining can distort the part.
Metrology and Quality Control:
Verifying the precision of complex AM telescope frames requires advanced metrology:
- Coordinate Measuring Machines (CMM): Provide high-accuracy point measurements for verifying critical dimensions, datums, and geometric tolerances (GD&T).
- 3D Laser Scanning / Structured Light Scanning: Capture millions of points to compare the full part geometry against the original CAD model, generating color maps to visualize deviations. This is invaluable for complex, freeform shapes produced by topology optimization. 3D scanning metrology is essential for comprehensive quality control metal AM.
Summary Table: Typical Precision Levels
Parameter | Process | As-Printed Typical Range | Post-Machined Typical Range | Anteckningar |
---|---|---|---|---|
Tolerans | L-PBF | ±0.1 to ±0.2 mm / % | < ±0.01 to ±0.05 mm | Depends heavily on feature size & complexity |
EBM | ±0.2 to ±0.4 mm / % | < ±0.01 to ±0.05 mm | EBM parts often require more machining | |
Surface Finish Ra | L-PBF (Vertical) | 8 – 20 µm | < 0.8 µm (machined) | Polishing can achieve << 0.1 µm |
EBM (Vertical) | 20 – 40 µm | < 0.8 µm (machined) | EBM surfaces are generally rougher |
Export to Sheets
Engineers designing telescope frames must specify tolerances and surface finishes realistically based on functional requirements, understanding that achieving the tightest specifications typically requires post-machining. Partnering with a high-precision manufacturing services provider like Met3dp, which emphasizes process control and utilizes high-accuracy equipment, helps ensure that parts meet the demanding precision requirements of space applications.
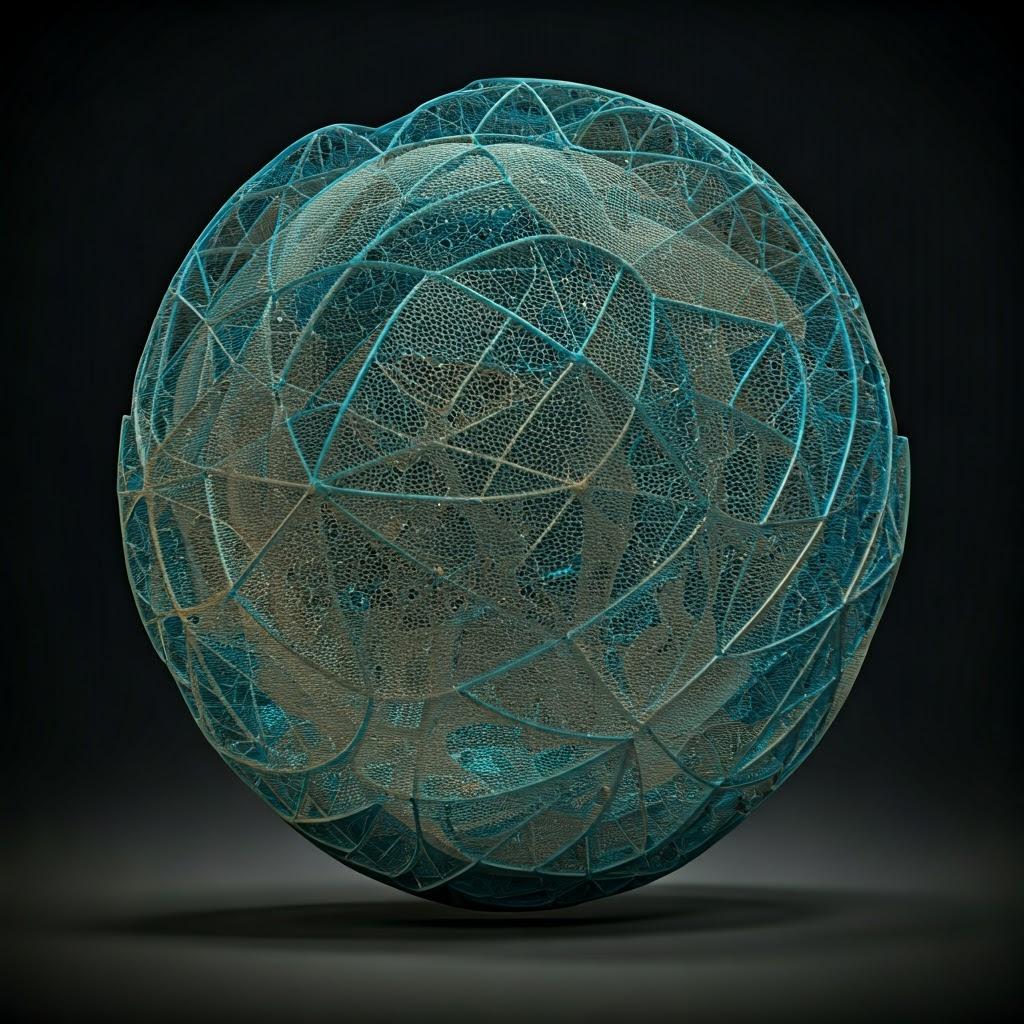
Essential Post-Processing Steps for Space-Ready Telescope Frames
Manufacturing a telescope frame using Metal AM doesn’t end when the printer stops. A series of critical efterbearbetning steps are required to transform the as-printed component into flight-ready hardware meeting the stringent demands of space applications. These steps are not optional extras but integral parts of the manufacturing workflow, ensuring the frame possesses the required dimensional accuracy, mechanical properties, surface characteristics, and overall integrity. The specific sequence and intensity of these steps depend on the chosen material (Invar or Ti-6Al-4V), the complexity of the design, and the specific functional requirements of the frame.
Key post-processing stages typically include:
- Powder Removal:
- Goal: Remove all unfused metal powder trapped within the part (especially in internal channels or lattice structures) and surrounding it on the build plate.
- Metoder: Manual brushing, compressed air blow-off, vacuuming, ultrasonic cleaning baths (sometimes with specific solvents). Complete powder removal is critical to avoid contamination, ensure accurate weight, and allow effective subsequent heat treatment. For complex internal geometries, specialized equipment and procedures may be needed.
- Stress Relief / Heat Treatment:
- Goal: Reduce the internal residual stresses built up during the rapid heating and cooling cycles inherent in the AM process. These stresses can cause distortion, cracking, and negatively impact dimensional stability and mechanical properties.
- Metoder: Performed in a controlled atmosphere (vacuum or inert gas) furnace. Specific temperature cycles (heating rate, soak temperature, soak time, cooling rate) are crucial and depend heavily on the alloy:
- Invar 36: Typically requires annealing cycles designed to minimize residual stress and stabilize the microstructure to achieve the lowest possible CTE and long-term dimensional stability.
- Ti-6Al-4V: Standard stress relief involves heating below the beta transus temperature (e.g., 600-800°C). Other treatments like annealing or solution treatment and aging (STA) can be used to tailor microstructure and mechanical properties (strength, ductility, fatigue life).
- Importance: This is arguably the most critical heat treatment metal AM parts aerospace step for ensuring dimensional stability and preventing distortion during subsequent machining or operational use. It must typically be performed before removing the part from the build plate to prevent warpage.
- Part Removal from Build Plate:
- Goal: Separate the printed frame(s) from the build plate they were fused to during printing.
- Metoder: Typically done using Wire Electrical Discharge Machining (Wire EDM) or a bandsaw. Care must be taken to avoid damaging the part.
- Borttagning av stödstruktur:
- Goal: Remove the temporary support structures required during the build process.
- Metoder: Can range from simple manual breaking for easily accessible supports to more involved methods like CNC machining, grinding, or specialized tools for complex or internal supports. This can be a labor-intensive process, highlighting the importance of DfAM in minimizing supports. Support removal additive manufacturing requires skill to avoid damaging the part surface.
- Surface Impact: Areas where supports were attached will typically have a rougher surface finish requiring subsequent treatment.
- Het isostatisk pressning (HIP):
- Goal: Eliminate internal porosity (microscopic voids) that can remain after the AM process, achieving full density (typically >99.9%). This significantly improves mechanical properties like fatigue strength, ductility, and fracture toughness.
- Method: The part is subjected to high temperature (below melting point) and high isostatic pressure (using an inert gas like Argon) in a specialized HIP vessel.
- Ansökan: Often considered mandatory for critical aerospace structural parts, especially fatigue-sensitive components made from Ti-6Al-4V. It adds cost and time but provides significant property improvements and consistency.
- CNC Machining:
- Goal: Achieve final dimensional accuracy, tight tolerances (micrometer level), and smooth surface finishes on critical features and interfaces (mating surfaces, optical mounts, datum features, threaded holes).
- Method: Utilizes traditional CNC milling, turning, or grinding operations. Requires careful fixture design to hold the often complex AM part securely without distortion. CNC machining 3D printed components bridges the gap between AM’s design freedom and traditional manufacturing’s precision.
- Ytbehandling:
- Goal: Improve the overall surface texture, remove residual support marks, prepare for coatings, or meet specific optical or thermal requirements.
- Metoder: Wide range available depending on need:
- Abrasive Blasting (Sand/Bead Blasting): Creates a uniform matte finish, removes loose particles.
- Tumbling/Vibratory Finishing: Smoothes surfaces and edges using media in a rotating or vibrating drum.
- Polering: Mechanical or electrochemical methods to achieve very smooth, reflective surfaces (required for some optical interfaces).
- Coating Preparation: Specific surface textures might be required for optimal adhesion of thermal control coatings or optical coatings.
- Aerospace surface finishing techniques must be carefully selected to avoid contamination or altering critical dimensions.
- Cleaning and Inspection:
- Goal: Ensure the part is completely free of contaminants (powder, machining fluids, debris – crucial Foreign Object Debris/FOD control for space) and meets all specifications.
- Metoder: Multi-stage precision cleaning processes. Inspection involves visual checks, dimensional verification (CMM, 3D scanning), and Non-Destructive Testing (NDT) like X-ray Computed Tomography (CT) to verify internal integrity and check for defects like porosity or cracks, ensuring post-processing quality assurance.
Met3dp understands the criticality of these post-processing steps and works closely with clients and qualified partners to ensure that each step is performed correctly, adhering to aerospace standards and delivering telescope frames ready for integration and flight.
Navigating Potential Challenges in AM Frame Production and Mitigation Strategies
While Metal Additive Manufacturing offers transformative capabilities for producing complex telescope frames, it’s essential to acknowledge and address potential challenges inherent in the technology. Proactive planning, robust process control, and deep expertise are required to navigate these hurdles and ensure the delivery of high-quality, reliable components. Understanding these challenges and their mitigation strategies is vital for engineers and procurement managers evaluating AM solutions.
- Residual Stress and Warpage/Distortion:
- Utmaning: The rapid, localized heating and cooling cycles during layer-by-layer fusion create significant thermal gradients, leading to internal stresses within the part. These stresses can cause warpage (deviation from intended shape), distortion (especially after removal from the build plate), or even cracking. This is a major concern for large, relatively thin structures like frames.
- Mitigation Strategies:
- Process Simulation: Using software to predict thermal behavior and stress accumulation before printing, allowing for optimization of build orientation and support structures.
- Optimized Scan Strategies: Using specific laser/beam scanning patterns (e.g., island scanning, checkerboard patterns) to distribute heat more evenly.
- Robust Support Structures: Designing supports not just for overhangs but also to anchor the part securely and conduct heat away effectively.
- Build Plate Heating: Maintaining an elevated temperature of the build plate (common in L-PBF) reduces thermal gradients. EBM inherently operates at higher temperatures, reducing stress.
- Mandatory Stress Relief: Performing appropriate residual stress metal AM mitigation heat treatment cycles before removing the part from the build plate is crucial for dimensional stability.
- Porositet:
- Utmaning: Small voids or pores can form within the printed material due to trapped gas (from powder or shielding gas) or incomplete fusion between layers/scan tracks (lack-of-fusion porosity). Porosity degrades mechanical properties, particularly fatigue strength and fracture toughness.
- Mitigation Strategies:
- High-Quality Powder: Using powder with low internal porosity, controlled particle size distribution, good flowability, and low moisture content (like those produced by Met3dp using advanced atomization). Proper powder handling and storage are essential.
- Optimized Process Parameters: Precisely controlling laser/beam power, scan speed, layer thickness, and shielding gas flow to ensure complete melting and fusion. Met3dp’s metal AM process control expertise is critical here.
- Het isostatisk pressning (HIP): As mentioned, HIP is highly effective at closing internal pores and achieving full density, often specified for critical aerospace AM delar.
- Support Removal Difficulties:
- Utmaning: Complex internal channels, lattice structures, or intricate geometries designed using topology optimization can make support structures very difficult or impossible to remove completely using conventional methods. Incomplete removal adds weight, can obstruct fluid flow, and acts as potential FOD.
- Mitigation Strategies:
- DfAM Focus: Designing for support minimization and accessibility from the outset (see DfAM section). Avoiding enclosed hollow sections unless absolutely necessary and designable for powder removal.
- Optimized Support Types: Using support structures (e.g., tree supports, block supports with specific hatching) designed for easier removal with minimal surface scarring.
- Advanced Removal Techniques: Employing methods like chemical etching (for specific materials), abrasive flow machining, or focused electrochemical machining for hard-to-reach areas, though these add complexity and cost. Addressing support removal challenges AM complex parts requires careful planning.
- Cracking:
- Utmaning: Some alloys, particularly those prone to solidification cracking or with high thermal expansion coefficients combined with high strength, can be susceptible to cracking during the build process or subsequent heat treatment due to high residual stresses.
- Mitigation Strategies:
- Materialval: Choosing alloys known to have good weldability/printability where possible.
- Parameter Optimization: Fine-tuning process parameters to minimize thermal gradients and stresses.
- Pre-heating: Utilizing build plate or chamber pre-heating to reduce thermal shock.
- Specific Heat Treatments: Designing stress relief cycles carefully to avoid temperatures that might induce embrittlement or cracking.
- Achieving and Verifying Material Properties:
- Utmaning: Ensuring that the mechanical properties (strength, ductility, fatigue life, CTE for Invar) of the final AM part consistently meet the stringent specifications required for spaceflight, and proving it. AM properties can be influenced by build orientation and location within the build chamber.
- Mitigation Strategies:
- Rigorous Process Control: Maintaining tight control over all process variables (machine, material, parameters).
- Material Characterization: Extensive testing of powders and printed materials to develop a robust property database.
- Witness Coupons: Printing standardized test specimens (tensile bars, fatigue coupons, CTE samples) alongside the actual parts in the same build for destructive testing to verify properties for that specific build run.
- Comprehensive NDT: Utilizing techniques like CT scanning for internal defect detection and dimensional verification.
- Robust Quality Management System (QMS): Implementing and adhering to stringent quality standards (e.g., AS9100 for aerospace) covering the entire workflow from powder procurement to final inspection, ensuring full traceability and quality assurance aerospace AM.
By acknowledging these potential challenges and implementing robust mitigation strategies grounded in deep materials science and process expertise, providers like Met3dp can reliably produce complex, high-performance metal AM telescope frames that meet the demanding requirements of the space industry. Partnering with an experienced supplier who understands these nuances is key to project success.
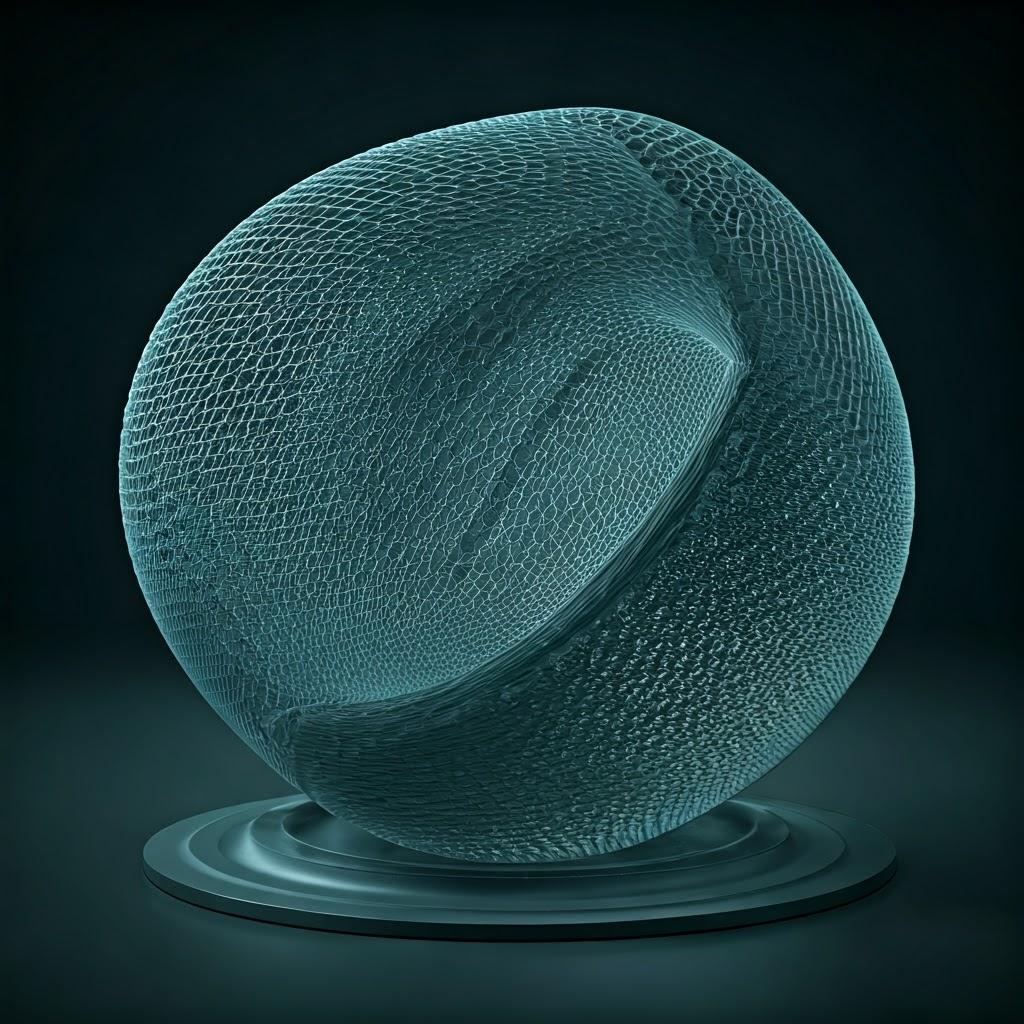
Selecting Your Ideal Metal AM Partner for Aerospace Components
Choosing the right manufacturing partner for producing critical components like space telescope frames via Metal Additive Manufacturing is as crucial as the design and material selection itself. The unique demands of the aerospace industry – stringent quality requirements, extreme performance needs, and mission-critical reliability – necessitate partnering with a supplier possessing specialized expertise, robust processes, and a proven track record. Making the wrong choice can lead to project delays, cost overruns, subpar component quality, and potentially mission failure. Therefore, a thorough aerospace additive manufacturing supplier evaluation process is essential.
Here are key criteria to consider when selecting your Metal AM partner:
- Aerospace Expertise and Certifications:
- Track Record: Does the provider have documented experience manufacturing components for space or aerospace applications? Can they demonstrate an understanding of the specific challenges and requirements (e.g., thermal stability, vibration resistance, outgassing)?
- Quality Management System (QMS): AS9100 certification is the gold standard for aerospace manufacturing. It demonstrates a rigorous QMS encompassing process control, traceability, risk management, and continuous improvement, tailored to the demands of the aerospace industry. Verify their certification status and scope.
- Compliance: Depending on the project’s nature and location, ensure the provider meets relevant regulatory requirements, such as ITAR (International Traffic in Arms Regulations) if applicable for defense-related space projects.
- Material Capabilities and Expertise:
- Specific Alloy Experience: Simply listing a material isn’t enough. Probe their proven experience in successfully printing and post-processing the specific alloys required, such as Invar 36 and Ti-6Al-4V. Ask about their internal R&D, parameter development, and material characterization data for these alloys.
- Powder Quality Control: Understand their process for sourcing, testing, handling, and recycling metal powders. Do they have stringent controls to prevent contamination and ensure powder consistency batch-to-batch? Partners like Met3dp, who manufacture their own high-quality powders using advanced techniques like PREP and Gas Atomization, offer significant advantages in material consistency and traceability. When choosing AM material suppliers, vertical integration can be a key benefit.
- Equipment, Technology, and Capacity:
- Appropriate Technology: Do they operate the right type of AM machines (e.g., L-PBF for fine features, EBM for lower stress Ti-6Al-4V parts) for your specific application?
- Byggvolym: Can their machines accommodate the size of your telescope frame components? Met3dp prides itself on offering industry-leading print volumes.
- Machine Condition and Calibration: Are their machines well-maintained and regularly calibrated to ensure accuracy and repeatability?
- Capacity and Redundancy: Do they have sufficient machine capacity to meet your lead time requirements? Do they have multiple machines to provide redundancy in case of downtime?
- Engineering and DfAM Support:
- Collaborative Approach: Look for a partner willing to work collaboratively during the design phase. Do they offer expert engineering support additive manufacturing services to help optimize the design for AM (DfAM), simulate the build process, and ensure manufacturability? This collaboration is crucial for leveraging AM’s full potential.
- Post-Processing and Inspection Capabilities:
- Integrated Services: Does the provider offer necessary post-processing steps (stress relief, heat treatment, HIP, precision machining, surface finishing) in-house, or do they manage these through a network of qualified partners? An integrated approach often streamlines the workflow and ensures accountability.
- Metrology and NDT: Evaluate their inspection capabilities. Do they have calibrated CMMs, 3D scanners, and NDT equipment (e.g., CT scanning) suitable for verifying complex aerospace components? Robust quality control metal AM relies on advanced metrology.
- Track Record, Case Studies, and References:
- Proven Success: Ask for examples of similar projects they have completed successfully. Case studies or references (within the bounds of confidentiality agreements) can provide confidence in their capabilities.
- Communication and Project Management:
- Transparency and Responsiveness: Effective communication and transparent project management are vital throughout the complex process of producing flight hardware. Evaluate their responsiveness during the quoting process and their project management methodology.
Selecting a partner like Met3dp, which offers an integrated solution encompassing advanced printers, högpresterande metallpulver, and expert application development services, can significantly de-risk the process. Their foundation, detailed on their Om oss page, showcases a deep commitment to the technology and its application in demanding industries. A thorough evaluation based on these criteria will help ensure you select a capable and reliable partner for your critical space telescope frame manufacturing needs.
Understanding Cost Drivers and Lead Times for AM Telescope Frames
While Metal Additive Manufacturing offers significant performance advantages for space telescope frames, engineers and procurement managers must have a realistic understanding of the associated costs and lead times. These factors are influenced by numerous variables specific to AM and the high-stakes nature of aerospace components. A clear grasp of these drivers enables better budget planning AM projects and schedule management.
Key Cost Drivers:
- Material Cost:
- Alloy Type: Specialized aerospace alloys like Invar 36 and Ti-6Al-4V are inherently more expensive than common engineering metals. Invar, with its high Nickel content, is particularly costly.
- Pulverkvalitet: High-purity, highly spherical powders optimized for AM command a premium but are essential for quality.
- Volym: The sheer amount of material required for the part directly impacts cost. AM’s high material utilization (low waste compared to machining) helps offset powder cost, improving the buy-to-fly ratio AM, but the base material cost remains significant.
- Recycling: While unused powder is often recyclable, the recycling process itself adds some cost, and regulations may limit the number of reuse cycles for critical applications.
- Part Design (Volume & Complexity):
- Size/Volume: Larger parts consume more material and require longer print times.
- Komplexitet: Intricate features, thin walls, complex lattice structures, and extensive overhangs increase print time, necessitate more support material, and complicate post-processing. Topology-optimized designs, while lightweight, can be complex to print and inspect.
- Machine Time (Build Time):
- Calculation: Primarily driven by the height of the part (number of layers) and the volume/surface area to be scanned per layer. Machine operating costs (power, gas, maintenance, depreciation) are factored in per hour.
- Nesting: Printing multiple parts simultaneously in one build can improve machine utilization and reduce cost per part, relevant for wholesale metal printing services or batch production.
- Stödstrukturer:
- Material Usage: Supports consume powder and add to print time.
- Removal Labor: Removing supports, especially from complex geometries, can be time-consuming and require skilled labor, significantly impacting cost.
- Post-Processing Intensity:
- Mandatory Steps: Stress relief/heat treatment is nearly always required and adds furnace time and cost.
- Optional but Recommended Steps: HIP adds significant cost but is often necessary for fatigue properties.
- Precision Requirements: The extent of CNC machining required to meet tolerance and surface finish specifications is often a major cost driver. More features requiring machining equal higher costs.
- Ytbehandling: Specific finishing requirements (polishing, coating prep) add cost.
- Quality Assurance and Inspection:
- NDT: Non-Destructive Testing like CT scanning provides invaluable internal inspection but requires specialized equipment and expertise, adding cost.
- Metrology: Dimensional verification using CMMs or 3D scanners requires time and skilled technicians.
- Documentation: The extensive documentation and certification required for aerospace components add overhead.
- Engineering & Setup:
- DfAM & Simulation: Initial non-recurring engineering (NRE) costs for design optimization and build simulation.
- Build Preparation: Labor involved in setting up the build file, preparing the machine, and loading powder.
Typical Lead Time Components:
The total time from order placement to receiving a finished, flight-ready AM telescope frame involves multiple stages:
- Quoting & Engineering Review (Days to Weeks): Initial design assessment, manufacturability check (DfAM review), build simulation, support strategy development, formal quote generation.
- Print Queue & Scheduling (Days to Weeks): Depends on machine availability and existing backlog.
- Printing Time (Hours to Many Days): Directly dependent on part height, volume, and complexity. Large frames can take several days or even over a week to print.
- Post-Processing (Weeks): Often the longest phase. Includes furnace cycles for stress relief/heat treatment/HIP (can take days per cycle including ramp up/down), machining setup and run time, support removal, finishing, and cleaning. Multiple steps are performed sequentially.
- Inspection & Shipping (Days): Final quality checks, documentation packaging, and logistics.
Overall Lead Time: While AM can significantly accelerate prototyptillverkning by eliminating tooling, the additive manufacturing lead time analysis for producing fully qualified, post-processed komponenter för flyg- och rymdindustrin like telescope frames often ranges from several weeks to a few months, depending heavily on the factors above. It’s crucial to engage with potential suppliers early to get realistic estimates for specific projects. While potentially longer than machining a simple part, AM is often competitive or faster for parts with high complexity that would otherwise require intricate machining setups or complex assembly of multiple pieces.
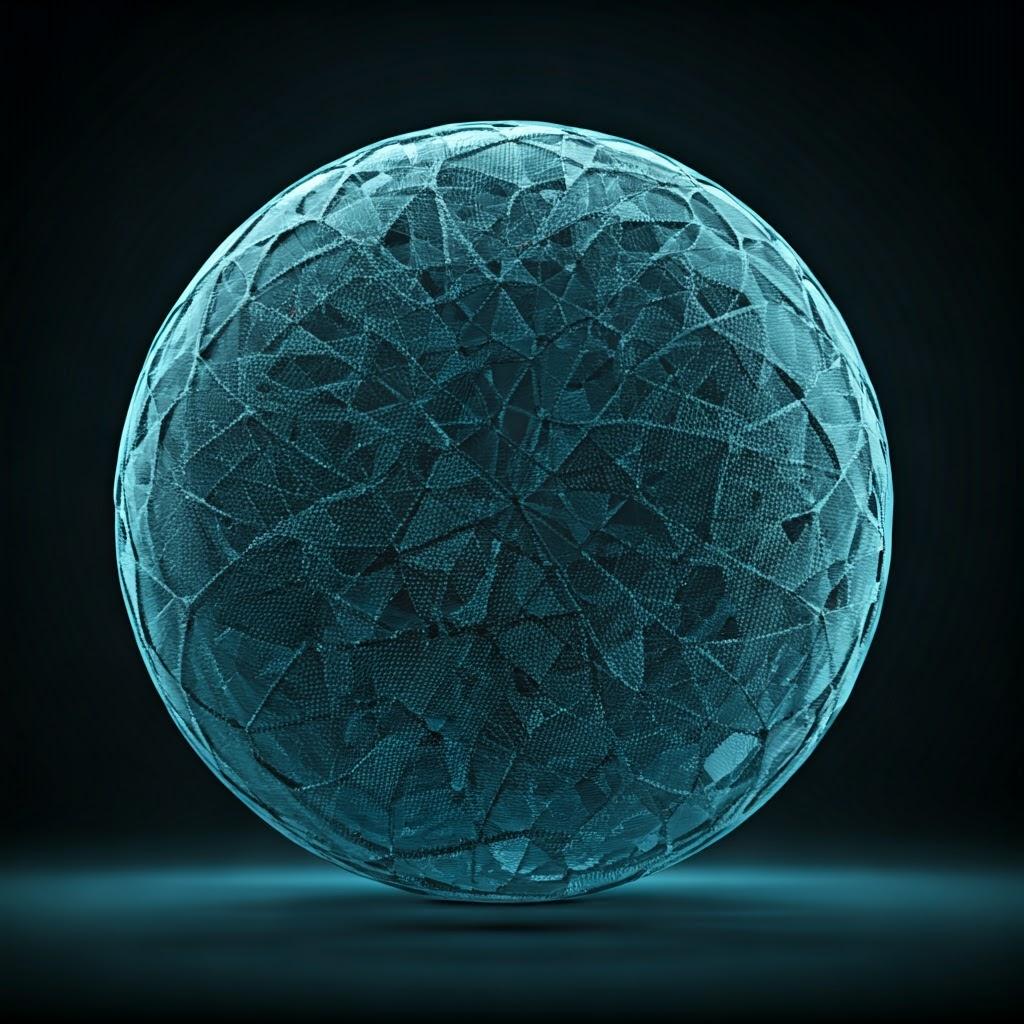
Frequently Asked Questions (FAQ) about Metal AM for Telescope Frames
Here are answers to some common questions regarding the use of Metal Additive Manufacturing for space telescope component frames:
1. What are the largest telescope frame components Met3dp can produce using metal AM?
Met3dp utilizes printers designed to offer industry-leading build volumes, suitable for a wide range of aerospace components. The maximum size depends on the specific printer model used (L-PBF or SEBM) and the chosen material. For very large structures exceeding the build volume of a single machine, components can often be designed in segments that are printed separately and then joined using established aerospace techniques (e.g., precision bolting, welding – though minimizing joints is preferred). We recommend contacting Met3dp directly with your specific component dimensions and requirements to discuss feasibility and explore options using our large-format printing capabilities.
2. How do the mechanical properties of AM Invar and Ti-6Al-4V compare to traditional wrought or cast materials?
This is a critical question for metal AM space applications. When processed correctly (including appropriate heat treatment and potentially HIP), Metal AM Ti-6Al-4V can achieve mechanical properties (tensile strength, yield strength, fatigue life) that meet or even exceed those of traditional wrought Ti-6Al-4V. The microstructure might differ slightly (e.g., finer grain structure), which can sometimes enhance certain properties. For Invar 36, achieving the extremely low CTE requires careful control over the AM process and specific post-print annealing cycles to stabilize the microstructure. While AM Invar can meet the low-CTE requirements, rigorous testing and characterization, often via witness coupons printed alongside the part, are essential to verify performance against specifications. Met3dp leverages its deep materials science expertise to optimize processes for achieving desired properties in both Invar 3D printing och Ti-6Al-4V AM.
3. What specific quality control measures and documentation are provided for aerospace telescope frames produced by Met3dp?
Quality assurance is paramount for aerospace components. Met3dp operates under a robust Quality Management System (potentially aligned with AS9100 principles, though specific certification status should always be verified for project requirements). Our process includes:
- Powder Control: Incoming powder inspection, batch traceability, controlled storage, and handling.
- Process Monitoring: Real-time monitoring of key build parameters (laser/beam power, temperature, atmosphere).
- Witness Coupons: Printing and testing of material samples alongside the main part to verify mechanical properties for each build.
- NDT: Non-Destructive Testing capabilities (e.g., CT scanning partnerships) to inspect internal integrity.
- Dimensional Metrology: Use of calibrated CMMs and 3D scanners for verifying dimensional accuracy against CAD models and drawings.
- Documentation Package: Providing comprehensive documentation including material certifications, build logs, post-processing records, dimensional inspection reports, and certificates of conformity, ensuring full traceability.
4. Besides primary structures, can Metal AM be used for other telescope hardware or even repairs?
Absolutely. Beyond main frames, Metal AM is highly suitable for producing brackets, complex instrument housings, heat exchangers or thermal straps with intricate internal channels, mirror mounts, kinematic components, and lightweight optical baffles. The technology is also being explored for in-space manufacturing and repair, although terrestrial AM focuses on producing the initial hardware. For terrestrial repair applications, techniques like Direct Energy Deposition (DED) are sometimes used to add material back to worn or damaged high-value components, though Powder Bed Fusion (Met3dp’s focus) is primarily for creating new parts.
5. What information is typically needed to get an accurate quote and lead time estimate for an AM telescope frame?
To provide the most accurate quote and realistic lead time, we typically require the following information:
- 3D CAD-modell: In a standard format (e.g., STEP, IGES).
- 2D Drawings: Specifying critical dimensions, tolerances (GD&T), surface finish requirements, and material specifications.
- Material Choice: Invar 36, Ti-6Al-4V, or other specified alloy.
- Kvantitet: Number of units required.
- Krav på efterbearbetning: Details on necessary heat treatments (stress relief, HIP, annealing), machining needs, surface finishes, and NDT/inspection requirements.
- Quality Standards: Any specific aerospace standards (e.g., AS9100 compliance) or customer specifications that must be met.
- Desired Delivery Date: To understand project urgency.
Conclusion: Elevating Space Exploration with Additively Manufactured Telescope Frames
The quest to unravel the universe’s mysteries demands increasingly sophisticated tools, and space telescopes are at the forefront of this exploration. The precision frames that form their structural heart require an extraordinary combination of stability, strength, and low mass – attributes that push the boundaries of traditional manufacturing. As we’ve explored, Additiv tillverkning av metall (AM) has emerged as a transformative technology uniquely capable of meeting these challenges, enabling the future of space manufacturing.
By leveraging AM, engineers can design and produce telescope frames with unprecedented levels of optimization. The ability to create komplexa geometrier, integrate lattice structures, and achieve significant lättviktande genom topologioptimering directly translates into enhanced telescope performance and reduced launch costs. Part consolidation simplifies assemblies and improves reliability. Furthermore, AM unlocks the potential of specialized aerospace materials like low-expansion Invar 36 for stability-critical components and high-strength-to-weight Ti-6Al-4V for structural efficiency, fabricating them into shapes previously unachievable.
However, harnessing these benefits of metal AM aerospace applications requires more than just access to a printer. It demands a holistic approach encompassing rigorous Design for Additive Manufacturing (DfAM) principles, meticulous process control, essential post-processing steps like heat treatment and precision machining, and robust quality assurance. Navigating potential challenges like residual stress and porosity requires deep expertise in materials science and AM process physics.
The success of employing AM for advanced telescope technology hinges critically on selecting the right manufacturing partner. Look for providers like Met3dp who demonstrate not only technological capability with industry-leading printers and advanced material production but also a profound understanding of aerospace requirements, a commitment to quality (evidenced by certifications like AS9100), and the engineering expertise to support projects from concept to flight-ready hardware.
Metal AM is no longer a niche prototyping technology; it is a vital tool enabling aerospace innovation. For engineers and procurement managers striving to build the next generation of space telescopes, embracing metal AM offers a pathway to components that are lighter, stronger, more stable, and built faster than ever before.
Ready to explore how Metal AM can elevate your next space mission?
Partner with Met3dp, a leader in metal AM equipment and materials. We provide comprehensive solutions spanning advanced printers, high-quality metal powders, and expert application development services. Visit our website at https://met3dp.com/ eller contact Met3dp today to discuss your specific requirements for precision telescope components and discover how our capabilities can power your organization’s additive manufacturing goals. Let’s build the future of space exploration, together.
Dela på
MET3DP Technology Co, LTD är en ledande leverantör av lösningar för additiv tillverkning med huvudkontor i Qingdao, Kina. Vårt företag är specialiserat på 3D-utskriftsutrustning och högpresterande metallpulver för industriella tillämpningar.
Förfrågan för att få bästa pris och anpassad lösning för ditt företag!
Relaterade artiklar
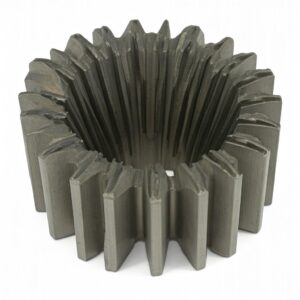
Högpresterande segment för munstycksvingar: Revolutionerande turbineffektivitet med 3D-utskrift i metall
Läs mer "Om Met3DP
Senaste uppdateringen
Vår produkt
KONTAKTA OSS
Har du några frågor? Skicka oss meddelande nu! Vi kommer att betjäna din begäran med ett helt team efter att ha fått ditt meddelande.
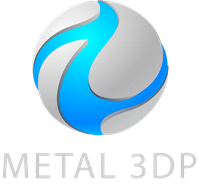
Metallpulver för 3D-printing och additiv tillverkning
FÖRETAG
PRODUKT
cONTACT INFO
- Qingdao City, Shandong, Kina
- [email protected]
- [email protected]
- +86 19116340731