3D Printed Connectors for Electric Vehicles
Innehållsförteckning
Introduction – The Growing Importance of Efficient EV Battery Connectors and Metal Additive Manufacturing
The electric vehicle (EV) revolution is rapidly transforming the automotive landscape, driven by increasing environmental concerns and the pursuit of sustainable transportation. At the heart of every EV lies its battery system, a complex assembly of cells, modules, and crucial components like battery connectors. These seemingly small parts play a vital role in ensuring the safe and efficient transfer of power, directly impacting the vehicle’s performance, range, and reliability. As the demand for EVs surges, so does the need for innovative manufacturing solutions that can deliver high-performance, lightweight, and cost-effective components. This is where metal additive manufacturing, also known as metal 3D-utskrifter, emerges as a game-changing technology, offering unprecedented design freedom and material versatility for the production of advanced EV battery connectors. Metal3DP Technology Co., LTD, headquartered in Qingdao, China, stands at the forefront of this innovation, providing industry-leading metal 3D printing equipment and high-performance metal powders tailored for demanding applications in the automotive sector and beyond. Their commitment to accuracy and reliability makes them a trusted partner for companies looking to push the boundaries of EV technology. Explore Metal3DP’s expertise in 3D-utskrift av metall to understand how this technology is shaping the future of electric mobility.
What are 3D Printed EV Battery Connectors Used For? – Applications Across Electric Vehicle Systems
3D printed EV battery connectors are integral components within the intricate electrical architecture of electric vehicles. Their primary function is to establish reliable and efficient electrical connections between various elements of the battery system and the wider vehicle powertrain. These connectors facilitate the flow of high currents necessary for powering the electric motor and enabling essential vehicle functions. The versatility of metal 3D printing allows for the creation of connectors with complex geometries optimized for specific applications within the EV. Here’s a breakdown of key use cases:
- Cell-to-Module Connections: Within battery modules, connectors link individual battery cells, ensuring seamless power transfer and enabling efficient energy management. The ability to customize the shape and size of these connectors through 3D printing allows for optimized packing density and thermal management within the module.
- Module-to-Module Connections: Multiple battery modules are often combined to form the complete battery pack. 3D printed connectors facilitate the robust and reliable electrical connection between these modules, handling significant voltage and current loads.
- Battery Pack to Inverter/Motor Connections: High-power connectors are required to transfer energy from the main battery pack to the inverter, which then supplies power to the electric motor. These connectors must be highly conductive and durable to withstand demanding operating conditions.
- Charging System Connections: 3D printed connectors are also used in the vehicle’s charging system, enabling the safe and efficient transfer of power from external charging sources to the battery pack. This includes both AC and DC fast charging applications.
- Sensor and Monitoring System Connections: Modern EV battery systems incorporate numerous sensors for monitoring temperature, voltage, and current. 3D printed connectors can be designed to integrate seamlessly with these sensors, ensuring accurate data transmission for battery management systems.
By leveraging the design flexibility offered by metal 3D printing, manufacturers can create EV battery connectors tailored to the specific requirements of each application, optimizing for factors such as current carrying capacity, vibration resistance, and space constraints. Metal3DP’s advanced Utrustning för 3D-utskrift can produce these complex connectors with high precision and material integrity.
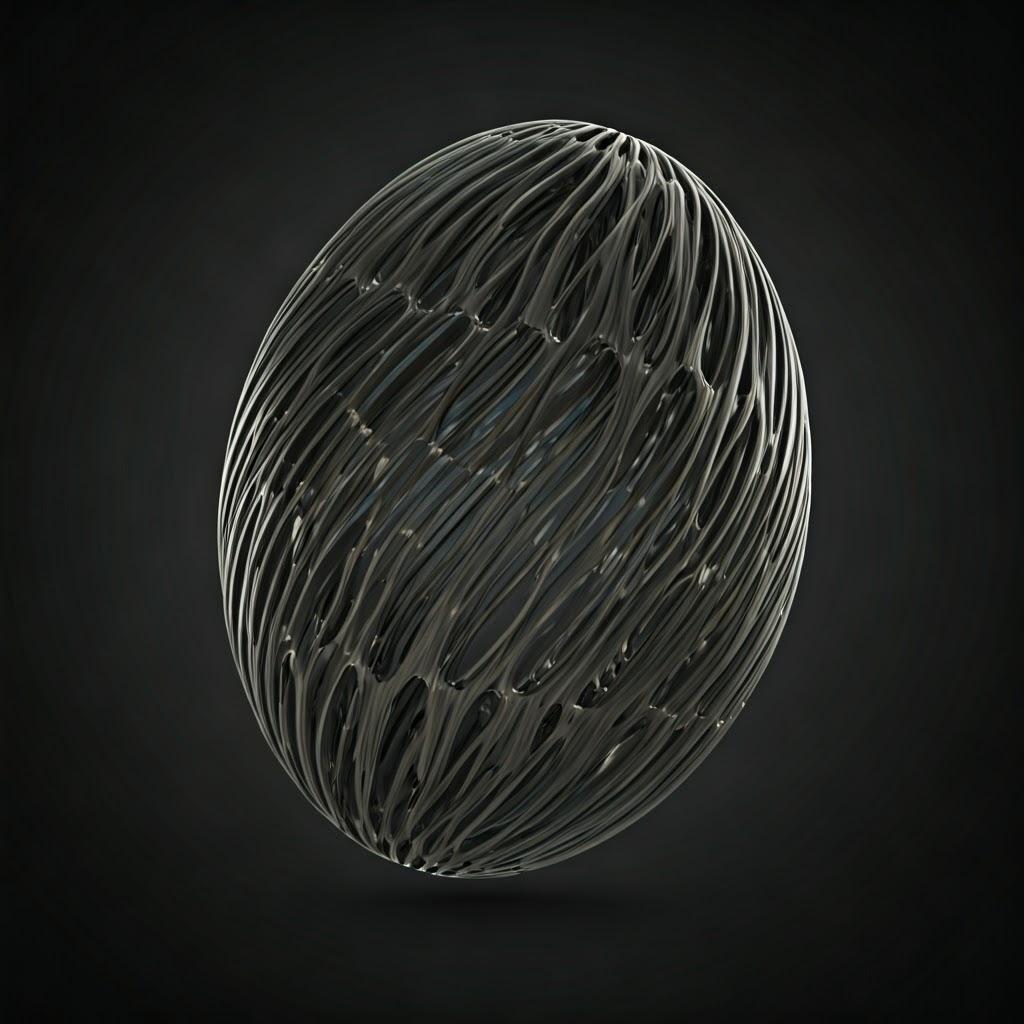
Why Use Metal 3D Printing for EV Battery Connectors? – Advantages Over Traditional Manufacturing
Traditional manufacturing methods for battery connectors, such as stamping, machining, and casting, often come with limitations in terms of design complexity, material utilization, and production flexibility. Metal 3D printing offers a compelling alternative, providing several key advantages for the production of EV battery connectors:
- Designfrihet och komplexitet: Additive manufacturing allows for the creation of intricate connector geometries that are difficult or impossible to achieve with traditional methods. This enables engineers to optimize designs for weight reduction, improved thermal management through internal cooling channels, and enhanced electrical performance.
- Lättvikt: In the automotive industry, reducing weight is crucial for improving energy efficiency and extending vehicle range. Metal 3D printing facilitates the creation of lightweight connector designs with optimized material distribution, contributing to overall vehicle weight reduction.
- Materialeffektivitet: Unlike subtractive manufacturing processes that remove material, 3D printing builds parts layer by layer, significantly reducing material waste. This is particularly important when working with expensive and specialized metals.
- Snabb prototypframtagning och iteration: Metal 3D printing enables the rapid creation of prototypes, allowing for faster design iterations and testing. This accelerates the development cycle for new EV models and battery systems.
- Customization and Low-Volume Production: Additive manufacturing is well-suited for producing customized connectors for specific battery configurations or for low-volume production runs, without the need for expensive tooling.
- Integration of Features: 3D printing allows for the integration of multiple functionalities into a single part. For example, cooling channels or mounting features can be directly incorporated into the connector design, reducing the number of assembly steps and improving reliability.
- Högpresterande material: Metal 3D printing is compatible with a wide range of high-performance metal powders, including aluminum alloys like AlSi10Mg and copper alloys like CuCrZr, which offer excellent electrical conductivity, thermal properties, and mechanical strength required for demanding EV applications. Metal3DP’s metallpulver av hög kvalitet are specifically engineered for additive manufacturing, ensuring optimal part density and performance.
By embracing metal 3D printing, EV manufacturers can overcome the limitations of traditional methods, leading to the development of more efficient, lighter, and cost-effective battery systems.
Recommended Materials and Why They Matter – Exploring AlSi10Mg and CuCrZr for High-Performance Connectors
The choice of material is paramount for the performance and reliability of EV battery connectors, as they must exhibit excellent electrical conductivity, thermal management properties, and mechanical strength to withstand the demanding operating conditions within an electric vehicle. Metal 3D printing offers the flexibility to utilize advanced metal powders tailored to these requirements. For EV battery connector applications, two particularly promising materials are AlSi10Mg and CuCrZr, both available in Metal3DP’s extensive portfolio of avancerade metallpulver.
AlSi10Mg (Aluminum-Silicon-Magnesium Alloy):
- Viktiga egenskaper:
- Lättviktare: Aluminum alloys are significantly lighter than copper alloys, contributing to overall vehicle weight reduction and improved energy efficiency.
- Good Thermal Conductivity: AlSi10Mg offers excellent heat dissipation, which is crucial for managing the thermal loads generated by high-current flow in battery connectors.
- Good Mechanical Strength: This alloy exhibits a good balance of strength and ductility, ensuring the structural integrity of the connector under mechanical stress and vibration.
- Excellent Processability: AlSi10Mg is well-suited for laser powder bed fusion (LPBF), a common metal 3D printing technique, resulting in dense and high-quality parts.
- Why it Matters for EV Battery Connectors: The lightweight nature of AlSi10Mg is a significant advantage in EVs, contributing to increased range and efficiency. Its good thermal conductivity helps to prevent overheating, ensuring the long-term reliability of the battery system.
CuCrZr (Copper-Chromium-Zirconium Alloy):
- Viktiga egenskaper:
- Hög elektrisk ledningsförmåga: Copper alloys are renowned for their exceptional electrical conductivity, minimizing energy loss during power transfer.
- Good Thermal Conductivity: CuCrZr also offers excellent thermal dissipation capabilities.
- Hög hållfasthet och hårdhet: The addition of chromium and zirconium enhances the strength and hardness of copper, making it suitable for demanding mechanical applications.
- God korrosionsbeständighet: This alloy exhibits good resistance to corrosion, ensuring long-term performance in the challenging environment of an EV battery system.
- Why it Matters for EV Battery Connectors: The high electrical conductivity of CuCrZr is critical for minimizing resistive losses and maximizing the efficiency of power transfer within the battery system. Its enhanced strength and hardness ensure the connector can withstand mechanical stresses and vibrations encountered in vehicle operation.
The selection between AlSi10Mg and CuCrZr will depend on the specific requirements of the EV battery connector application, considering factors such as weight sensitivity, current carrying capacity, and operating environment. Metal3DP’s expertise in metal additive manufacturing and their range of high-quality powders enable manufacturers to choose the optimal material for their specific needs, ensuring the production of high-performance and reliable EV battery connectors.
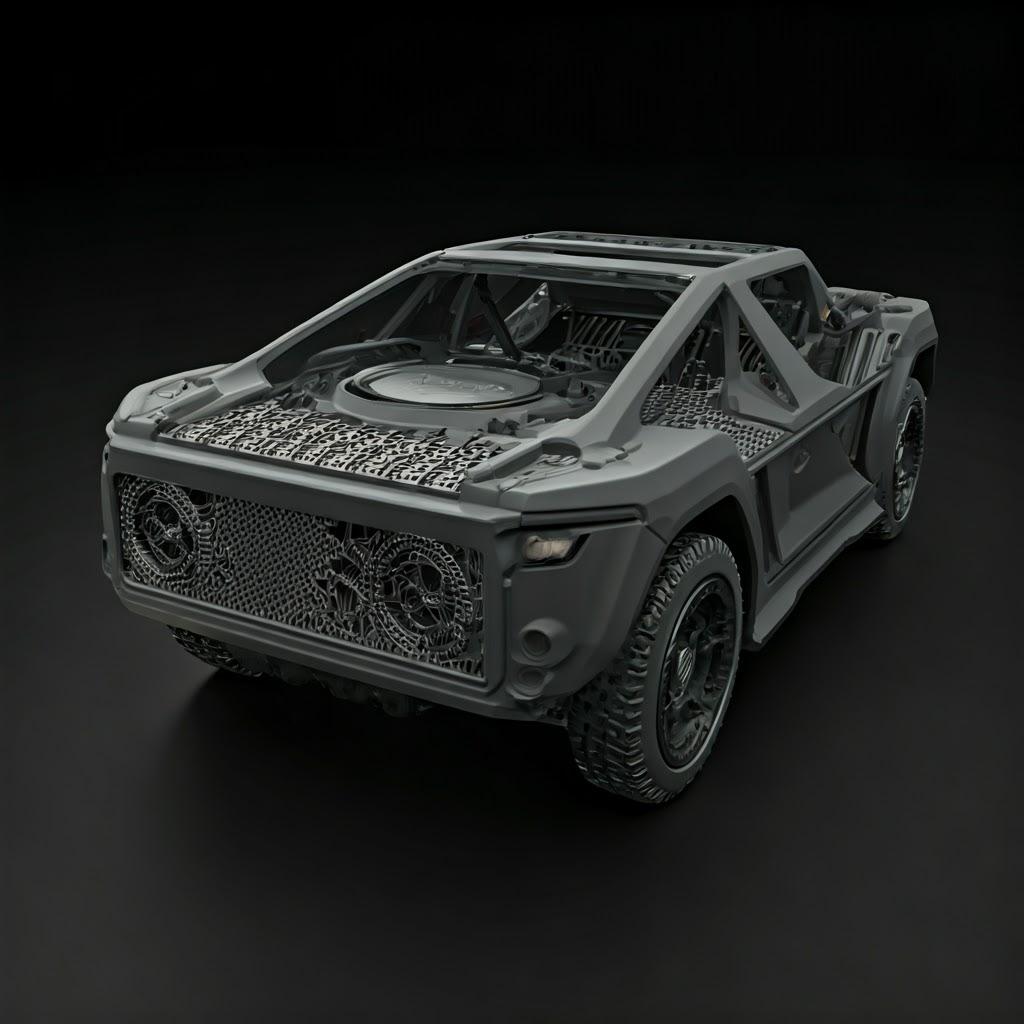
Design Considerations for Additive Manufacturing of EV Connectors – Optimizing Geometry and Performance
Designing EV battery connectors for metal 3D printing requires a different approach compared to traditional manufacturing methods. The layer-by-layer build process opens up opportunities for geometric complexity and performance optimization that were previously unattainable. Here are some key design considerations:
- Topology Optimization: Leveraging specialized software, engineers can perform topology optimization to identify the most efficient material distribution for a given load and boundary conditions. This results in lightweight connectors with maximized strength and stiffness, reducing material usage and improving overall vehicle efficiency.
- Internal Cooling Channels: High current flow in battery connectors generates heat. Additive manufacturing allows for the integration of intricate internal cooling channels within the connector design. These channels enable efficient heat dissipation through liquid or air cooling, preventing overheating and ensuring optimal performance and longevity of the battery system.
- Gitterstrukturer: For non-critical structural areas, infill patterns like lattice structures can be employed to reduce weight while maintaining sufficient mechanical integrity. Various lattice geometries, such as gyroid or cubic, can be tailored to specific strength and stiffness requirements.
- Sammanslagning av delar: 3D printing allows for the consolidation of multiple components into a single, complex part. This reduces the number of assembly steps, minimizes potential failure points, and improves overall reliability. For example, a connector and its mounting features can be designed as a single unit.
- Surface Texture Optimization: The surface texture of the connector can be tailored to enhance electrical contact and minimize contact resistance. Specific surface roughness can be designed directly into the 3D model, eliminating the need for secondary surface treatments in some cases.
- Integration of Sensors: Additive manufacturing facilitates the integration of sensor housings or channels directly into the connector design. This allows for the seamless incorporation of temperature, voltage, or current sensors for real-time monitoring of the battery system’s performance and safety.
- Consideration of Support Structures: During the metal 3D printing process, support structures are often required to prevent overhangs and ensure dimensional accuracy. Designers must strategically plan the orientation of the part and the placement of support structures to minimize material usage and simplify post-processing removal. Metal3DP’s application engineers can provide valuable insights into optimizing designs for their tryckmetoder, ensuring efficient and high-quality production.
By carefully considering these design principles, engineers can fully exploit the capabilities of metal 3D printing to create innovative EV battery connectors with enhanced performance, reduced weight, and improved functionality.
Tolerance, Surface Finish, and Dimensional Accuracy of 3D Printed EV Connectors
Achieving the required tolerance, surface finish, and dimensional accuracy is crucial for the proper functioning and reliability of EV battery connectors. Metal 3D printing technologies have made significant advancements in these areas, but understanding the capabilities and limitations is essential for successful implementation.
- Dimensionell noggrannhet: The dimensional accuracy achievable with metal 3D printing depends on several factors, including the printing technology (e.g., Laser Powder Bed Fusion (LPBF), Electron Beam Melting (EBM)), the material being used, the size and geometry of the part, and the process parameters. Generally, tolerances in the range of ±0.1 to ±0.05 mm can be achieved for critical features. Metal3DP’s industry-leading print volume, accuracy and reliability ensure that complex EV connectors can be produced within tight specifications.
- Ytfinish: The as-built surface finish of metal 3D printed parts is typically rougher compared to machined surfaces due to the layer-by-layer manufacturing process and the partially melted powder particles on the surface. The surface roughness (Ra) can range from 5 to 20 µm depending on the printing parameters and material. For applications requiring smoother surfaces, post-processing steps like polishing or machining are often employed.
- Factors Affecting Accuracy and Finish:
- Skiktets tjocklek: Thinner layers generally result in better surface finish and higher accuracy but increase build time.
- Pulverpartikelstorlek och -fördelning: Consistent and fine powder particles contribute to a smoother surface and higher resolution. Metal3DP’s advanced powder making system ensures high sphericity and good flowability, leading to improved part quality.
- Bygg orientering: The orientation of the part on the build platform can significantly impact dimensional accuracy and surface finish of specific features.
- Stödstrukturer: The attachment points of support structures can leave surface marks that require post-processing.
- Thermal Management During Printing: Controlling temperature gradients during the build process is crucial for minimizing warping and ensuring dimensional accuracy.
To achieve the desired tolerance and surface finish for EV battery connectors, it’s important to consider these factors during the design and printing process and to plan for appropriate post-processing steps if necessary. Collaboration with an experienced metal 3D printing service provider like Metal3DP, which possesses expertise in process optimization and post-processing techniques, is crucial for meeting stringent requirements.
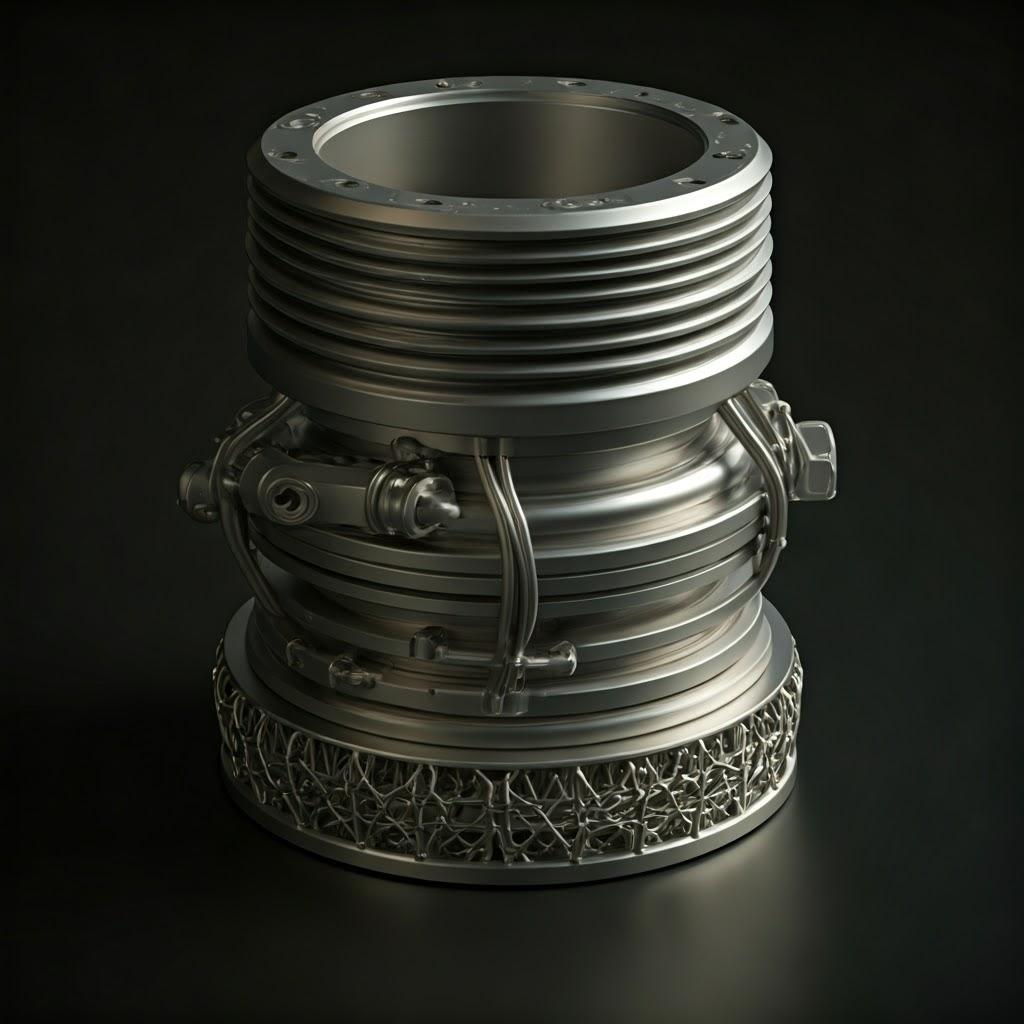
Post-Processing Requirements for Metal 3D Printed EV Battery Connectors
While metal 3D printing offers significant advantages, post-processing is often required to achieve the final desired properties, surface finish, and dimensional accuracy of EV battery connectors. Common post-processing steps include:
- Powder Removal: After the printing process, loose and partially sintered powder needs to be removed from the build chamber and internal channels of the part. This is typically done using brushes, compressed air, or vacuum systems.
- Borttagning av stödstruktur: Support structures, which are necessary for printing complex geometries, need to be carefully removed. This can be done manually using cutting tools, or through automated methods like machining or chemical dissolution, depending on the material and support type.
- Stress Relief Heat Treatment: Metal 3D printed parts can have residual stresses due to the rapid heating and cooling cycles during the printing process. Stress relief heat treatment is often performed to reduce these stresses, improving the mechanical properties and dimensional stability of the connectors.
- Ytbehandling: To achieve smoother surfaces and improve electrical contact, various surface finishing techniques can be employed, including:
- Media Blasting: Using abrasive media to remove surface imperfections and improve surface roughness.
- Polering: Mechanical or chemical polishing to achieve a smooth and lustrous finish.
- Machining (CNC): Precision machining can be used to achieve tight tolerances on critical dimensions and improve surface finish on specific features.
- Coating and Plating: Depending on the application requirements, coatings or platings may be applied to enhance corrosion resistance, improve electrical conductivity, or provide specific surface properties. For example, silver or gold plating can be used to improve contact conductivity.
- Inspection and Quality Control: Thorough inspection using techniques like coordinate measuring machines (CMM), optical scanners, and non-destructive testing (NDT) methods is essential to ensure that the printed connectors meet the required dimensional accuracy, material integrity, and performance specifications. Metal3DP adheres to stringent quality control procedures to ensure the reliability of their 3D printed components.
The specific post-processing steps required for EV battery connectors will depend on the material, the printing process used, and the final application requirements. It’s crucial to consider these requirements during the design phase and to partner with a metal 3D printing service provider that has the necessary expertise and equipment for comprehensive post-processing.
Common Challenges and How to Avoid Them in 3D Printing EV Connectors
While metal 3D printing offers numerous benefits for manufacturing EV battery connectors, there are also potential challenges that need to be addressed to ensure successful outcomes:
- Warping and Distortion: Thermal stresses during the printing process can lead to warping or distortion of the part, especially for large or complex geometries.
- How to Avoid: Optimize part orientation on the build platform, use appropriate support structures, carefully control process parameters, and consider stress relief heat treatment post-printing.
- Porositet: Internal voids or pores within the printed part can compromise its mechanical strength and electrical conductivity.
- How to Avoid: Optimize printing parameters such as laser power, scan speed, and powder layer thickness. Ensure high-quality metal powders with good flowability, such as those offered by Metal3DP, are used. Employ appropriate shielding gas to prevent oxidation during printing.
- Support Structure Removal Issues: Removing support structures can sometimes be challenging, especially for intricate designs, and can leave surface marks.
- How to Avoid: Design parts with self-supporting features where possible, optimize support structure placement and geometry, and utilize appropriate support removal techniques.
- Ytjämnhet: The as-built surface finish may not meet the requirements for electrical contact or sealing.
- How to Avoid: Consider the build orientation to minimize roughness on critical surfaces and plan for appropriate post-processing steps like media blasting, polishing, or machining.
- Material Property Consistency: Achieving consistent material properties throughout the printed part is crucial for reliability.
- How to Avoid: Work with experienced metal 3D printing service providers like Metal3DP that have robust process control and quality assurance procedures. Ensure the use of high-quality and well-characterized metal powders.
- Överväganden om kostnader: While 3D printing can be cost-effective for low to medium volumes and complex designs, the cost per part can be higher than traditional methods for very high volumes or simple geometries.
- How to Avoid: Carefully evaluate the production volume and design complexity to determine if 3D printing is the most cost-effective solution. Optimize designs for efficient printing and material usage.
By understanding these potential challenges and implementing appropriate design strategies and process controls, manufacturers can effectively leverage metal 3D printing to produce high-quality and reliable EV battery connectors.
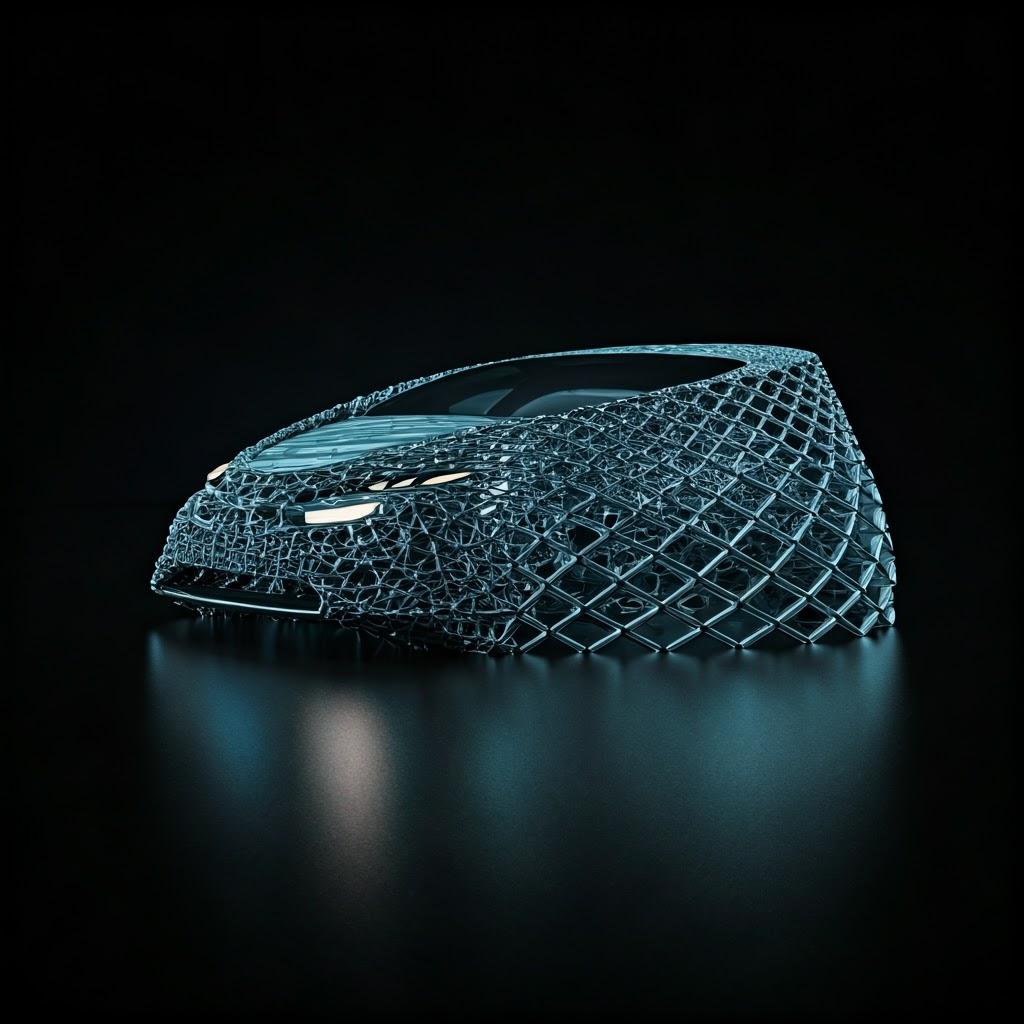
How to Choose the Right Metal 3D Printing Service Provider for EV Components
Selecting the right metal 3D printing service provider is a critical decision that can significantly impact the quality, cost, and lead time of your EV battery connectors. Here are some key factors to consider when evaluating potential suppliers:
- Material Capabilities: Ensure the provider has experience working with the specific metal powders required for your application, such as AlSi10Mg and CuCrZr. Verify their expertise in processing these materials to achieve the desired mechanical and electrical properties. Metal3DP boasts a wide range of metallpulver av hög kvalitet optimized for various applications.
- Printing Technologies: Different metal 3D printing technologies (e.g., LPBF, EBM) have varying strengths and limitations in terms of accuracy, surface finish, and build volume. Choose a provider whose technology aligns with the requirements of your EV battery connectors.
- Quality Assurance and Certifications: Look for providers with robust quality management systems and relevant certifications (e.g., ISO 9001, AS9100 for aerospace). This ensures that their processes are well-controlled and that the parts meet stringent quality standards.
- Design and Engineering Support: An experienced service provider should offer design consultation and engineering support to optimize your connector designs for additive manufacturing, ensuring manufacturability and performance. Metal3DP provides comprehensive solutions spanning equipment, powders, and application development services.
- Post-Processing Capabilities: Verify that the provider has the necessary in-house or partnered capabilities for essential post-processing steps such as powder removal, support removal, heat treatment, surface finishing, and inspection.
- Industry Experience: Prior experience in serving the automotive, aerospace, medical, or industrial manufacturing sectors is a strong indicator of the provider’s understanding of the demanding requirements of these industries.
- Lead Times and Production Capacity: Discuss lead times for prototyping and production, and assess the provider’s capacity to handle your anticipated volumes.
- Cost Structure and Transparency: Obtain a clear breakdown of the costs involved, including printing, materials, post-processing, and any additional services. Understand their pricing model and ensure transparency.
- Communication and Customer Support: Effective communication and responsive customer support are essential for a smooth and successful partnership.
- Confidentiality and Intellectual Property Protection: Ensure the provider has robust policies and agreements in place to protect your intellectual property and maintain confidentiality.
By carefully evaluating potential metal 3D printing service providers based on these criteria, you can select a partner that can reliably deliver high-quality EV battery connectors that meet your specific requirements.
Cost Factors and Lead Time for 3D Printed EV Battery Connector Manufacturing
The cost and lead time for manufacturing EV battery connectors using metal 3D printing are influenced by several factors:
- Kostnader för material: The type and quantity of metal powder used are significant cost drivers. Specialized alloys like CuCrZr can be more expensive than standard aluminum alloys like AlSi10Mg. Efficient design and topology optimization can help minimize material usage.
- Utskriftstid: The build time depends on the size and complexity of the connectors, the layer thickness, and the number of parts being printed simultaneously. Longer build times translate to higher machine operating costs.
- Kostnader för efterbearbetning: The extent of post-processing required (e.g., support removal, heat treatment, machining, polishing, coating) significantly impacts the overall cost. Complex post-processing steps increase both cost and lead time.
- Machine and Labor Costs: The cost of operating the metal 3D printer and the labor involved in design, setup, printing, and post-processing are factored into the final price.
- Produktionsvolym: While 3D printing can be cost-effective for low to medium volumes and complex geometries, the cost per part may not scale as favorably for very high volumes compared to traditional manufacturing methods. However, factors like tooling costs and design flexibility can still make it competitive.
- Designkomplexitet: Intricate designs that require extensive support structures or complex printing parameters may result in higher costs and longer lead times. Design optimization for additive manufacturing can help mitigate these factors.
Ledtid:
Lead times for 3D printed EV battery connectors can vary depending on the complexity of the part, the material availability, the printing technology used, the post-processing requirements, and the service provider’s workload. Prototyping lead times can range from a few days to a couple of weeks, while production lead times can vary from several weeks to months, depending on the volume and complexity.
It’s crucial to discuss cost and lead time expectations with your chosen metal 3D printing service provider early in the project. Obtaining detailed quotes and understanding the factors influencing them will help you make informed decisions and plan your production accordingly. Metal3DP is committed to providing transparent cost structures and efficient lead times for their additive manufacturing services.
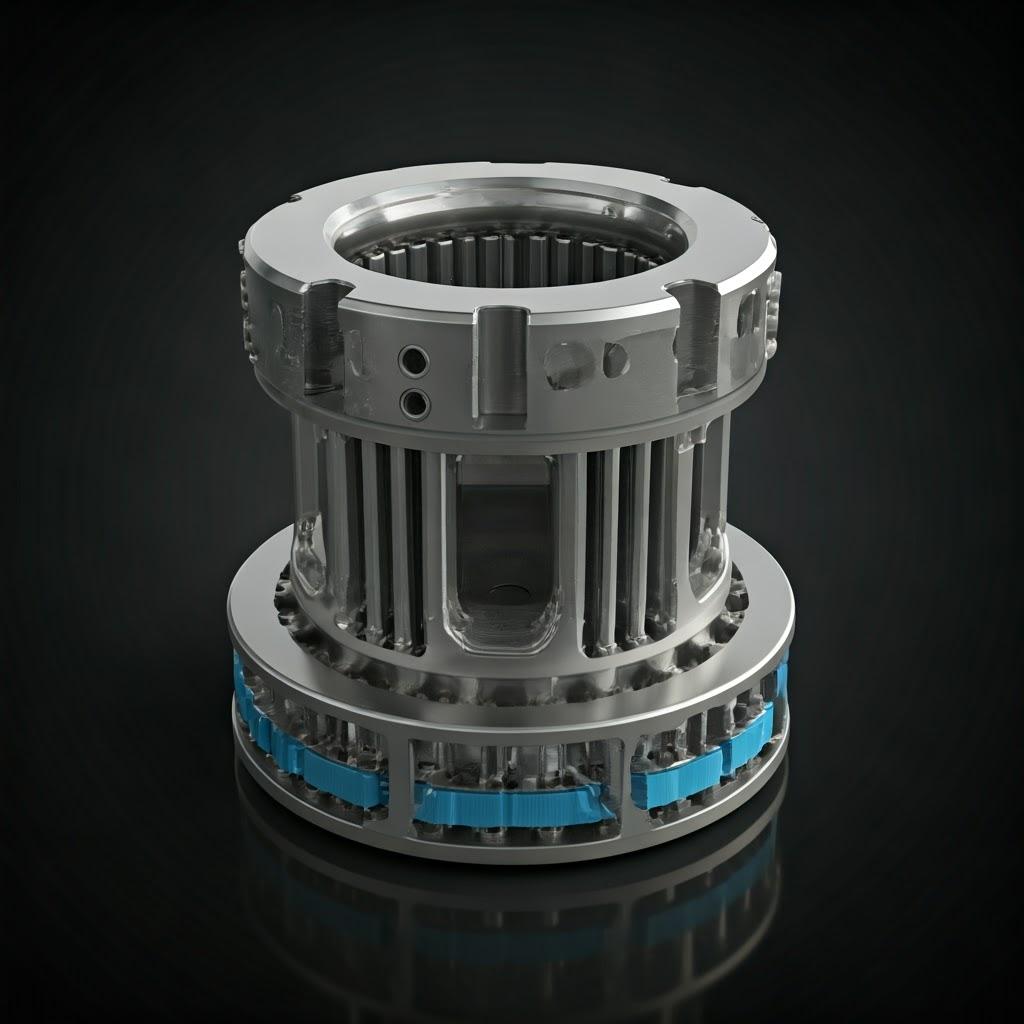
Frequently Asked Questions (FAQ) About 3D Printed EV Battery Connectors
- Q: Can metal 3D printed connectors meet the electrical conductivity requirements for EV batteries?
- A: Yes, with the appropriate material selection, such as copper alloys like CuCrZr, metal 3D printed connectors can achieve high electrical conductivity suitable for EV battery applications. Design optimization to maximize cross-sectional area and minimize contact resistance is also crucial.
- Q: Are 3D printed metal connectors strong enough for the vibrations and mechanical stresses in electric vehicles?
- A: Absolutely. Materials like AlSi10Mg and CuCrZr offer good mechanical strength and durability. Furthermore, design optimization for additive manufacturing, including features like lattice structures and optimized wall thicknesses, can enhance the structural integrity of the connectors. Proper post-processing, such as stress relief heat treatment, also contributes to improved mechanical properties.
- Q: What is the typical lifespan of a 3D printed metal battery connector in an EV?
- A: The lifespan of a 3D printed metal battery connector depends on factors such as the material used, the operating conditions (temperature, current, vibration), and the quality of the design and manufacturing process. With proper material selection, design for durability, and adherence to quality control standards, 3D printed metal connectors can achieve a lifespan comparable to traditionally manufactured components in EVs.
- Q: Can Metal3DP handle large-scale production of EV battery connectors?
- A: Metal3DP possesses industry-leading print volume and is equipped to handle both prototyping and serial production of metal 3D printed parts. Our advanced manufacturing capabilities and expertise in process optimization enable us to meet the demands of various production volumes for the automotive industry. Contact us to discuss your specific production requirements.
Conclusion – The Future of EV Connectors with Metal Additive Manufacturing
Metal additive manufacturing is revolutionizing the design and production of EV battery connectors, offering unparalleled opportunities for performance enhancement, weight reduction, and design innovation. The ability to utilize high-performance materials like AlSi10Mg and CuCrZr, coupled with the design freedom afforded by 3D printing, enables the creation of lighter, more efficient, and highly customized connectors. Companies like Metal3DP Technology Co., LTD are at the forefront of this technological shift, providing the expertise, equipment, and high-quality metal powders necessary to drive the future of electric mobility. As the demand for EVs continues to grow, metal 3D printing will play an increasingly vital role in enabling the development and manufacturing of advanced battery systems, paving the way for a more sustainable transportation future. Contact Metal3DP today to explore how our cutting-edge systems and materials can power your organization’s additive manufacturing goals.
Dela på
MET3DP Technology Co, LTD är en ledande leverantör av lösningar för additiv tillverkning med huvudkontor i Qingdao, Kina. Vårt företag är specialiserat på 3D-utskriftsutrustning och högpresterande metallpulver för industriella tillämpningar.
Förfrågan för att få bästa pris och anpassad lösning för ditt företag!
Relaterade artiklar
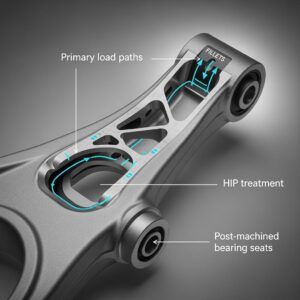
Metal 3D Printing for U.S. Automotive Lightweight Structural Brackets and Suspension Components
Läs mer "Om Met3DP
Senaste uppdateringen
Vår produkt
KONTAKTA OSS
Har du några frågor? Skicka oss meddelande nu! Vi kommer att betjäna din begäran med ett helt team efter att ha fått ditt meddelande.