Complex Positioner Housings for Valves
Innehållsförteckning
Introduction to Metal 3D Printing of Industrial Valve Positioner Housings
In the intricate dance of industrial control systems, precision and reliability are paramount. Valves, the workhorses of these systems, regulate the flow of liquids, gases, and slurries across diverse sectors, from the demanding environments of aerospace and automotive to the critical operations within medical and industrial manufacturing. At the heart of many advanced valve systems lies the valve positioner, a sophisticated device that ensures the valve stem and its control element accurately reach the position dictated by the control system. The housing of this positioner acts as a crucial protective and functional component, safeguarding internal mechanisms while providing the necessary structural integrity for seamless operation.
Traditionally, these housings have been manufactured using conventional methods such as casting or machining. While these techniques have served industry well, they often come with limitations in terms of design complexity, material waste, and lead times, particularly for intricate geometries or specialized material requirements. Enter metal 3D-utskrifter, also known as metal additive manufacturing (AM). This groundbreaking technology is rapidly transforming the landscape of industrial part production, offering unprecedented design freedom, the ability to tailor material properties, and the potential for significant efficiency gains. For complex positioner housings for valves, metal 3D printing presents a compelling alternative, enabling engineers and procurement managers to rethink design constraints and optimize performance for demanding applications. As a leader in this transformative field, Metall3DP is at the forefront, providing cutting-edge solutions in metal 3D printing equipment and high-performance metal powders, empowering industries to realize the full potential of additive manufacturing for mission-critical components like valve positioner housings.
Understanding the Functionality and Requirements of Valve Positioner Housings
The valve positioner housing is more than just an enclosure; it is an integral part of the overall valve control system. Its primary function is to protect the delicate internal components of the positioner from harsh external environments, including exposure to dust, moisture, chemicals, and extreme temperatures. Depending on the application, these housings may also need to withstand significant pressure fluctuations and mechanical vibrations.
Beyond environmental protection, the housing must provide a stable and precise platform for the internal mechanisms, ensuring accurate and reliable valve stem positioning. This often involves intricate internal features, mounting points for sensors and actuators, and precise interfaces with the valve body itself. Dimensional accuracy is therefore critical to guarantee proper assembly and functionality of the entire valve system.
The materials used for valve positioner housings must also meet stringent requirements. Depending on the industry and the specific media being controlled by the valve, the housing may need to exhibit excellent corrosion resistance to prevent degradation and ensure long-term reliability. In applications within the aerospace or chemical processing industries, for instance, resistance to aggressive chemicals and high temperatures is paramount. Mechanical strength and durability are also essential to withstand operational stresses and ensure the longevity of the valve assembly. These demanding functional and material requirements underscore the need for advanced manufacturing techniques capable of producing complex geometries with high-performance materials, a capability that metal 3D printing excels at.
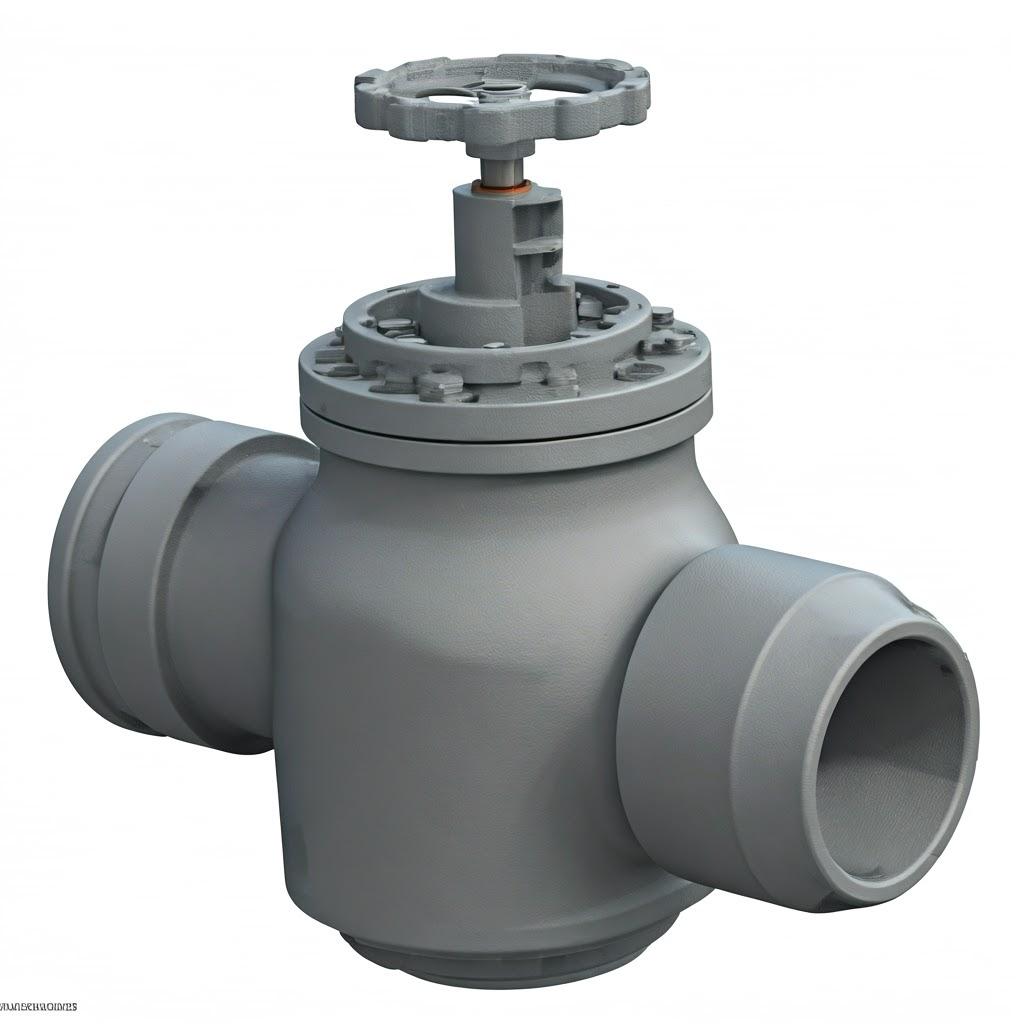
Advantages of Using Metal 3D Printing for Positioner Housing Manufacturing
The adoption of metal 3D printing for the manufacturing of industrial valve positioner housings offers a multitude of advantages over traditional manufacturing methods:
- Enhanced Design Flexibility: Metal 3D printing liberates engineers from the design constraints imposed by casting or machining. Complex internal channels for cooling or wiring, intricate lattice structures for weight reduction without compromising strength, and customized mounting features can be readily incorporated into the design. This allows for the optimization of the housing for specific application requirements, potentially leading to improved performance and reduced overall system complexity. Metal 3D printing services offered by companies like Metal3DP leverage this design freedom to create innovative solutions.
- Material Efficiency and Reduced Waste: Traditional subtractive manufacturing processes often involve significant material waste as material is removed to create the final part. Metal 3D printing, on the other hand, builds parts layer by layer, using only the necessary material. This near-net-shape manufacturing significantly reduces material waste, leading to cost savings, especially when working with expensive specialty alloys. Metal3DP’s advanced powder making system ensures that the powders used in these processes are of the highest quality, maximizing material utilization and part integrity.
- Del Konsolidering: Complex assemblies that traditionally require multiple parts and joining processes can often be consolidated into a single 3D printed component. For valve positioner housings, this could mean integrating features like mounting brackets, sensor housings, or internal flow channels directly into the main body. Part consolidation reduces assembly time, minimizes potential failure points associated with joints and fasteners, and can lead to a more robust and reliable final product.
- Rapid Prototyping and Iteration: Metal 3D printing significantly accelerates the prototyping process. Design changes can be implemented quickly, and new iterations can be produced in a fraction of the time compared to traditional tooling-dependent methods. This agility allows engineers to test and refine designs more efficiently, leading to faster product development cycles and optimized final designs.
- Kundanpassning och tillverkning på begäran: Additive manufacturing is ideally suited for producing customized parts or low-volume production runs. For specialized industrial applications requiring unique valve positioner housings, 3D printing offers a cost-effective solution without the need for expensive tooling. This enables on-demand manufacturing, reducing the need for large inventories and streamlining the supply chain.
- Tailored Material Properties: Depending on the 3D printing process and the metal powder used, it is possible to achieve specific microstructures and tailored mechanical properties within the printed part. This level of control can be crucial for meeting the demanding performance requirements of industrial valve positioner housings. Metal3DP’s range of metallpulver av hög kvalitet is specifically engineered to enable the production of dense, high-performance metal parts with superior mechanical properties.
Recommended Metal Powders for High-Performance Valve Positioner Housings: 316L and IN625
The selection of the appropriate metal powder is paramount to achieving the desired performance characteristics in a 3D printed valve positioner housing. For demanding industrial applications, two materials stand out for their exceptional properties: 316L stainless steel and Inconel 625.
316L rostfritt stål:
- Sammansättning: 316L is an austenitic stainless steel alloy primarily composed of iron, chromium (16-18%), nickel (10-14%), and molybdenum (2-3%). The “L” designation indicates a low carbon content (maximum 0.03%), which enhances resistance to sensitization (chromium carbide precipitation at grain boundaries) during welding or high-temperature exposure, thus improving corrosion resistance.
- Key Properties and Benefits for Valve Positioner Housings:
- Utmärkt korrosionsbeständighet: The high chromium and molybdenum content provides superior resistance to a wide range of corrosive environments, including acids, chlorides, and marine atmospheres. This is crucial for ensuring the long-term reliability of valve positioners operating in harsh industrial settings.
- Good Mechanical Properties: 316L exhibits good tensile strength, yield strength, and ductility, providing the necessary structural integrity to withstand operational stresses.
- Svetsbarhet: The low carbon content enhances weldability, which can be important for certain assembly processes or for adding features to the 3D printed housing.
- Biokompatibilitet: While perhaps less critical for general industrial valves, the biocompatibility of 316L makes it a potential candidate for applications in the medical or pharmaceutical industries where valves may come into contact with bodily fluids or sterile environments.
- Kostnadseffektivitet: Compared to some other high-performance alloys, 316L offers a good balance of properties at a relatively lower cost, making it an attractive option for a wide range of applications.
Inconel 625:
- Sammansättning: Inconel 625 is a nickel-chromium-molybdenum superalloy known for its exceptional strength and corrosion resistance at elevated temperatures. Its typical composition includes nickel (minimum 58%), chromium (20-23%), molybdenum (8-10%), niobium (3.15-4.15%), and small amounts of other elements.
- Key Properties and Benefits for Valve Positioner Housings:
- Superior High-Temperature Strength: IN625 retains its high strength and creep resistance at elevated temperatures, making it ideal for applications where the valve positioner may be exposed to hot process fluids or high ambient temperatures.
- Exceptionellt motståndskraftig mot korrosion: This alloy exhibits outstanding resistance to a wide variety of corrosive media, including strong acids, oxidizing and reducing environments, and chloride-induced pitting and crevice corrosion. This ensures long-term performance and reliability in the most aggressive industrial environments.
- High Mechanical Strength: IN625 possesses very high tensile strength, yield strength, and toughness, providing exceptional structural integrity and resistance to mechanical stresses.
- Excellent Fatigue Resistance: The alloy’s high fatigue strength makes it suitable for applications involving cyclic loading or vibrations.
- Mångsidighet: IN625 is used across a wide range of demanding industries, including aerospace, chemical processing, and marine engineering, attesting to its exceptional performance characteristics.
Metal3DP offers both 316L and IN625 metallpulver av hög kvalitet, meticulously produced using advanced gas atomization and PREP technologies to ensure high sphericity and flowability, critical for achieving dense, defect-free 3D printed parts with superior mechanical properties. Choosing between 316L and IN625 will depend on the specific performance requirements of the valve positioner housing, with IN625 offering superior performance in extreme temperature and highly corrosive environments, while 316L provides a cost-effective solution with excellent general corrosion resistance and good mechanical properties.
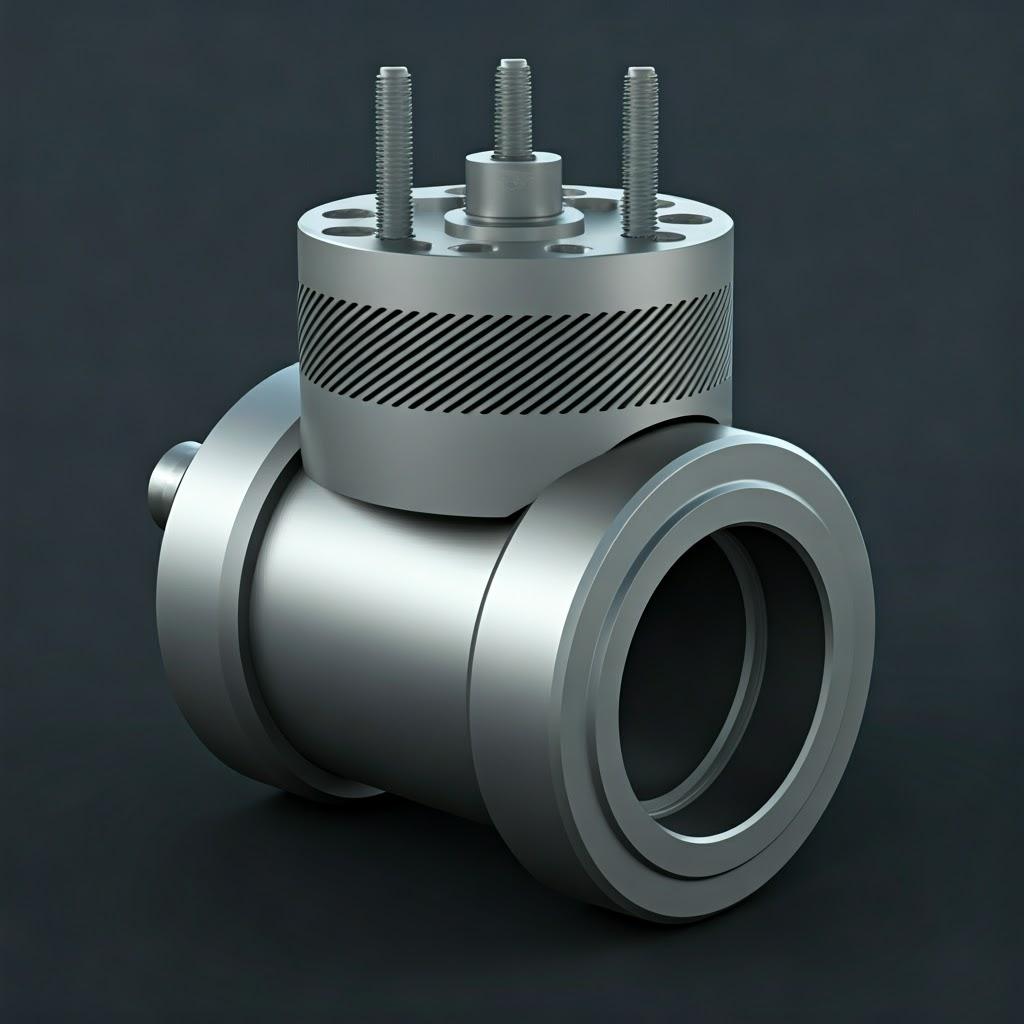
Design Considerations and Optimization for Metal 3D Printed Housings
Designing parts for additive manufacturing (DfAM) differs significantly from designing for traditional subtractive methods. To fully leverage the capabilities of metal 3D printing and achieve optimal performance for valve positioner housings, several key design considerations must be taken into account:
- Topology Optimization: This computational technique can be employed to identify and remove material from non-critical areas of the design while maintaining structural integrity. By optimizing the material distribution based on applied loads and constraints, it’s possible to create lightweight yet robust housings, reducing material usage and potentially improving performance.
- Lattice Structures: Incorporating lattice structures within the housing design can provide significant weight reduction without sacrificing stiffness or strength. These intricate, repeating cellular structures can be tailored to specific load-bearing requirements and can also enhance heat dissipation or provide damping properties.
- Consolidation of Multiple Parts: As mentioned earlier, metal 3D printing allows for the integration of multiple components into a single printed part. When designing a valve positioner housing, consider opportunities to incorporate features like mounting bosses, sensor integration points, or internal flow channels directly into the main housing structure. This reduces the need for separate parts, fasteners, and assembly steps, leading to a more streamlined and potentially more reliable final product.
- Minimizing Support Structures: Support structures are often necessary in metal 3D printing to prevent overhangs and complex geometries from collapsing during the build process. However, these supports need to be removed post-printing, which can add time and cost. Designing with self-supporting angles (typically around 45 degrees) and strategically orienting the part in the build chamber can minimize the need for extensive support structures.
- Wall Thickness and Ribbing: Careful consideration of wall thickness is crucial for achieving the required strength and stiffness while minimizing material usage and print time. Incorporating ribs or gussets can provide additional reinforcement to thinner walls in critical areas without significantly increasing weight.
- Surface Finish Considerations: The as-printed surface finish in metal 3D printing can vary depending on the process and material. If a smooth surface finish is required for sealing or aesthetic reasons, this needs to be factored into the design and post-processing plan. Designing features with easily accessible surfaces for post-processing can be beneficial.
- Termisk hantering: In some applications, valve positioner housings may need to dissipate heat generated by internal electronic components. Designing integrated cooling channels or fins using the design freedom offered by 3D printing can be an effective way to manage thermal performance.
By embracing these design principles, engineers can create metal 3D printed valve positioner housings that are not only functional and robust but also optimized for weight, material efficiency, and manufacturing cost. Metal 3D printing services from Metal3DP provide the expertise and technology to help customers realize these optimized designs.
Achieving Precision: Tolerance, Surface Finish, and Dimensional Accuracy in 3D Printed Housings
In industrial applications, particularly for critical components like valve positioner housings, achieving precise tolerances, appropriate surface finishes, and high dimensional accuracy is paramount for ensuring proper fit, functionality, and long-term reliability. Metal 3D printing technologies have made significant strides in delivering on these requirements.
- Tolerance Capabilities: The achievable tolerances in metal 3D printing depend on the specific printing technology (e.g., Selective Laser Melting (SLM), Direct Metal Laser Sintering (DMLS), Electron Beam Melting (EBM)), the material being used, and the design of the part. Generally, tolerances in the range of ±0.1 to ±0.05 mm (or even tighter in some cases with optimized parameters and post-processing) can be achieved for critical dimensions. Factors influencing tolerance include thermal shrinkage during solidification, laser spot size, and powder particle size distribution. Metal3DP’s printers are engineered to deliver industry-leading accuracy for mission-critical parts.
- Ytfinish: The as-printed surface finish in metal 3D printing typically has a certain degree of roughness due to the layer-by-layer build process and the partially sintered powder particles on the surface. The surface roughness (Ra) can range from 5 to 20 µm or higher depending on the printing parameters and material. For applications requiring smoother surfaces for sealing or reduced friction, post-processing techniques like media blasting, polishing, or machining can be employed to achieve the desired finish.
- Dimensionell noggrannhet: Dimensional accuracy refers to how closely the printed part matches the intended CAD model. Factors affecting dimensional accuracy include material shrinkage, thermal gradients during printing, and calibration of the printing equipment. With careful process control and optimized parameters, high levels of dimensional accuracy can be achieved. It’s crucial to consider potential shrinkage during the design phase and compensate for it in the CAD model.
To ensure the required precision for valve positioner housings, it’s essential to:
- Optimize Part Orientation: The orientation of the part in the build chamber can influence both tolerance and surface finish on different surfaces. Critical dimensions should be oriented in a way that minimizes the impact of layer lines and thermal gradients.
- Utilize Support Structures Strategically: While minimizing supports is generally desirable, strategically placed supports can help maintain dimensional accuracy, especially for complex geometries.
- Employ High-Quality Metal Powders: The quality and consistency of the metal powder significantly impact the final part’s density, surface finish, and dimensional accuracy. Metal3DP’s advanced powder making system ensures the production of high-quality spherical powders with excellent flowability, contributing to improved print quality and accuracy.
- Implement Robust Process Control: Maintaining strict control over printing parameters such as laser power, scan speed, layer thickness, and build chamber temperature is crucial for achieving consistent and accurate results.
- Consider Post-Processing: For applications requiring tight tolerances or smooth surface finishes, incorporating appropriate post-processing steps into the manufacturing workflow is essential.
By carefully considering these factors and partnering with a knowledgeable metal 3D printing service provider like Metal3DP, engineers can achieve the precision required for demanding industrial valve positioner housing applications.
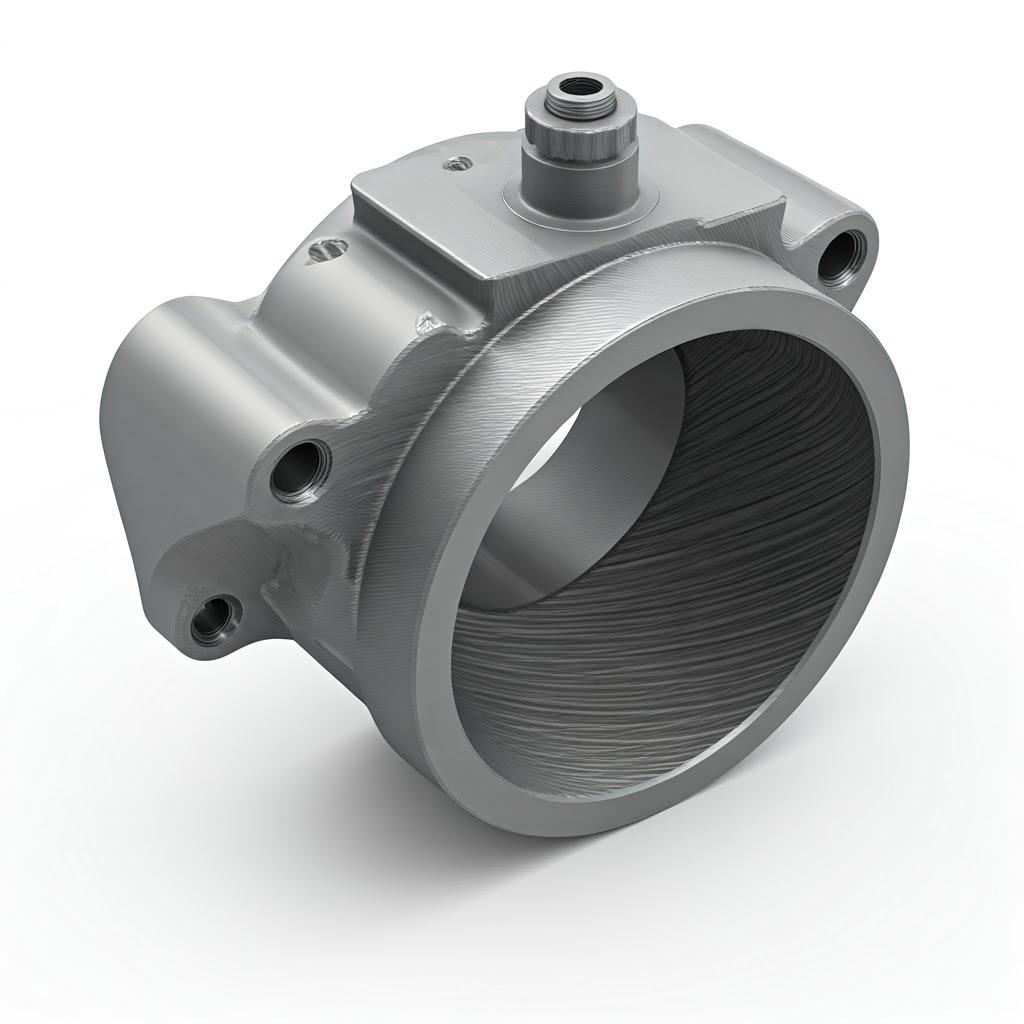
Post-Processing Techniques for Enhanced Performance of 3D Printed Housings
While metal 3D printing offers significant advantages in creating complex geometries, post-processing steps are often necessary to achieve the final desired properties, surface finish, and dimensional accuracy for industrial valve positioner housings. Common post-processing requirements include:
- Stöd för borttagning: As mentioned earlier, support structures are often used during the printing process to support overhangs and prevent deformation. These supports need to be carefully removed after printing, typically through mechanical means like cutting, grinding, or machining. The design of the part should aim to minimize the need for extensive supports and ensure that they can be easily accessed and removed without damaging the functional surfaces of the housing.
- Stress Relief Heat Treatment: Metal 3D printed parts can contain residual stresses due to the rapid heating and cooling cycles during the printing process. Stress relief heat treatment involves heating the part to a specific temperature and holding it for a certain period to reduce these internal stresses, which can improve dimensional stability and prevent warping or cracking in service.
- Het isostatisk pressning (HIP): HIP is a process that involves subjecting the printed part to high pressure and temperature in an inert gas environment. This process helps to close any internal porosity, increasing the density of the material and significantly improving its mechanical properties, such as fatigue strength and ductility. For critical valve positioner housings operating under high pressure or cyclic loading, HIP can be a crucial post-processing step.
- Ytbehandling: Depending on the application requirements, various surface finishing techniques can be employed to improve the surface roughness of the 3D printed housings. These can include:
- Media Blasting: Using abrasive media to remove partially sintered powder particles and create a more uniform surface texture.
- Polering: Mechanical or chemical polishing can be used to achieve smoother surface finishes for improved sealing or aesthetic purposes.
- Maskinbearbetning: For critical interfaces or dimensions requiring very tight tolerances, CNC machining can be used to achieve the final precise dimensions and surface finish.
- Beläggning: In some applications, the valve positioner housing may require specific coatings to enhance corrosion resistance, wear resistance, or other surface properties. These coatings can be applied using various methods such as electroplating, painting, or thermal spraying.
The specific post-processing steps required will depend on the material used, the printing process, and the performance requirements of the final valve positioner housing. It is crucial to consider these post-processing needs during the design phase to ensure that the part is designed in a way that facilitates efficient and effective post-processing. Metal3DP offers comprehensive solutions, including expertise in post-processing requirements for various metal alloys and applications.
Common Challenges and How to Avoid Them in Metal 3D Printing of Housings
While metal 3D printing offers numerous advantages, there are also potential challenges that need to be addressed to ensure the successful production of high-quality valve positioner housings:
- Warping and Distortion: Thermal stresses during the printing process can lead to warping or distortion of the part, especially for large or complex geometries. To mitigate this:
- Optimize Part Orientation: Orienting the part strategically can minimize the build-up of thermal stresses in critical areas.
- Utilize Support Structures Effectively: Properly designed and placed support structures can help anchor the part and prevent distortion.
- Control Build Chamber Temperature: Maintaining a consistent and controlled build chamber temperature can reduce thermal gradients.
- Implement Stress Relief Heat Treatment: Post-printing heat treatment can relieve internal stresses and improve dimensional stability.
- Porositet: Internal voids or porosity can compromise the mechanical strength and fatigue resistance of the printed part. To minimize porosity:
- Optimize Printing Parameters: Carefully tuning laser power, scan speed, and layer thickness can improve the density of the printed material.
- Use High-Quality Metal Powders: Powders with high sphericity and controlled particle size distribution, like those offered by Metal3DP, promote better packing density and reduce porosity.
- Consider Hot Isostatic Pressing (HIP): As mentioned earlier, HIP is an effective post-processing method for eliminating internal porosity.
- Support Removal Damage: Removing support structures can sometimes leave surface blemishes or damage the part, especially for delicate features. To avoid this:
- Design for Minimal Supports: Optimize part geometry and orientation to reduce the need for extensive supports.
- Use Optimized Support Structures: Employ support designs that are easier to remove without causing damage.
- Implement Careful Removal Techniques: Use appropriate tools and techniques for support removal.
- Residual Stresses: As discussed earlier, residual stresses can lead to warping and cracking. Implementing stress relief heat treatment is crucial for mitigating this issue.
- Surface Finish Issues: Achieving a smooth surface finish directly from the printing process can be challenging. Planning for appropriate post-processing techniques like media blasting or machining is essential when smooth surfaces are required.
- Material Property Variability: Inconsistent printing parameters or powder quality can lead to variations in the mechanical properties of the printed parts. To ensure consistency:
- Maintain Strict Process Control: Implement and adhere to well-defined printing procedures and parameters.
- Use Consistent, High-Quality Materials: Partner with reputable powder suppliers like Metal3DP that provide well-characterized and consistent metal powders.
By understanding these potential challenges and implementing appropriate design strategies, process controls, and post-processing techniques, manufacturers can successfully leverage metal 3D printing to produce high-quality and reliable valve positioner housings for demanding industrial applications.
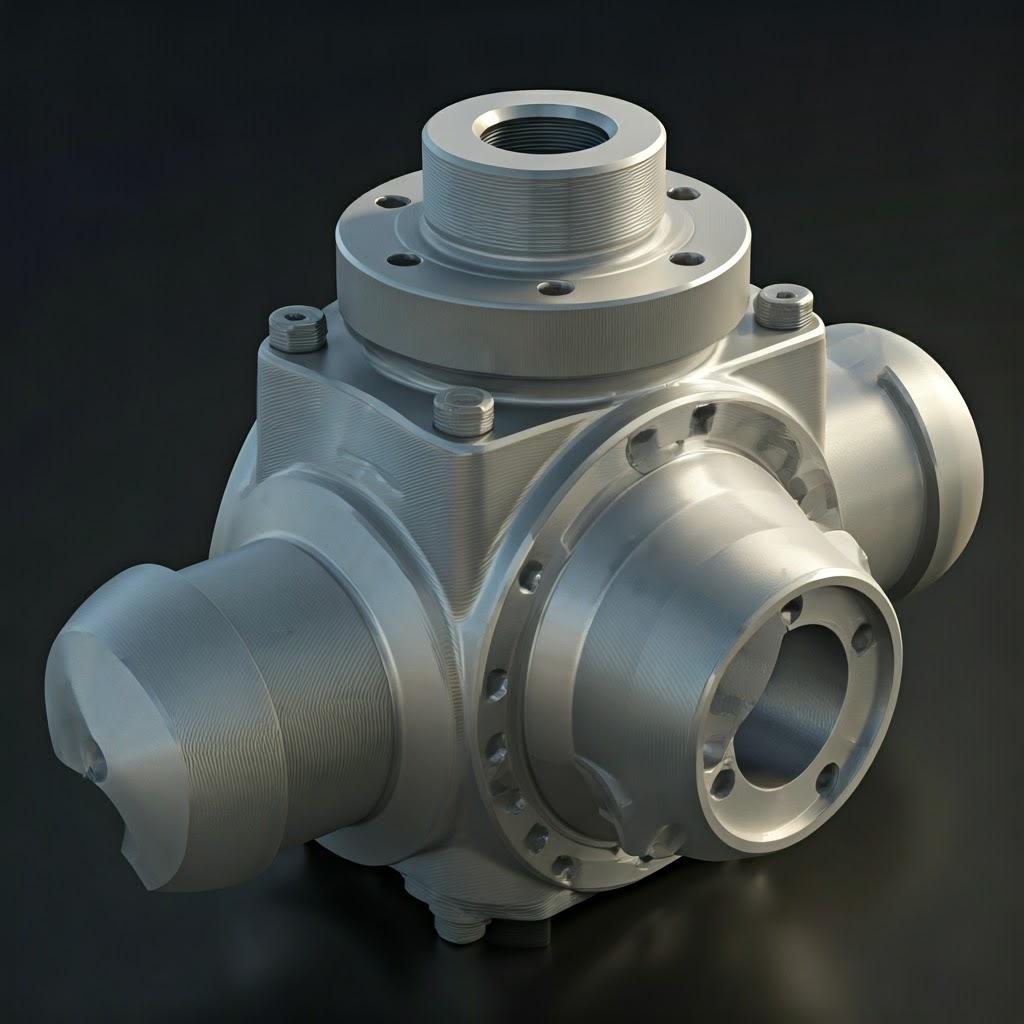
How to Choose the Right Metal 3D Printing Service Provider for Industrial Components
Selecting the right metal 3D printing service provider is a critical decision that can significantly impact the success of your project. For industrial components like valve positioner housings, which often require high performance and reliability, it’s essential to choose a partner with the expertise, capabilities, and quality standards to meet your specific needs. Here are key factors to consider when evaluating potential metal 3D printing service providers:
- Material Expertise and Range: Ensure the provider has experience working with the specific metal alloys required for your application, such as 316L or IN625. They should possess a deep understanding of the material properties, processing parameters, and post-processing requirements for these alloys. A provider like Metall3DP that also manufactures its own metallpulver av hög kvalitet often has a superior understanding of the entire material lifecycle.
- Printing Technology and Equipment: Different metal 3D printing technologies (e.g., SLM, DMLS, EBM) have varying strengths and limitations in terms of achievable accuracy, surface finish, and material compatibility. Understand the technologies the provider utilizes and ensure they are suitable for the size, complexity, and performance requirements of your valve positioner housings. Metal3DP prides itself on its industry-leading print volume, accuracy, and reliability.
- Quality Control and Certifications: Robust quality control procedures are paramount for industrial applications. Inquire about the provider’s quality management system, certifications (e.g., ISO 9001, AS9100 for aerospace), and inspection processes. They should have the capabilities to perform dimensional inspections, material testing, and non-destructive testing (NDT) as needed.
- Design for Additive Manufacturing (DfAM) Support: A knowledgeable service provider should offer expertise in DfAM principles and be able to provide guidance on optimizing your designs for metal 3D printing. This can include advice on topology optimization, part consolidation, and minimizing support structures.
- Post-Processing Capabilities: Understand the provider’s in-house post-processing capabilities, such as support removal, heat treatment, surface finishing, and coating. A provider offering a comprehensive range of post-processing services can streamline the manufacturing process and ensure the final parts meet your specifications.
- Experience with Industrial Applications: Look for a provider with a proven track record of producing metal 3D printed parts for demanding industries such as aerospace, automotive, medical, or industrial manufacturing. Their experience in these sectors will indicate their understanding of the stringent requirements and quality standards often involved.
- Lead Times and Production Capacity: Discuss lead times for prototyping and production runs, as well as the provider’s capacity to handle your anticipated volumes. Ensure their timelines align with your project schedule.
- Communication and Customer Support: Effective communication and responsive customer support are essential for a smooth and successful partnership. Evaluate the provider’s responsiveness, technical support capabilities, and willingness to collaborate.
By carefully evaluating potential metal 3D printing service providers based on these criteria, you can choose a partner that will deliver high-quality valve positioner housings that meet your specific industrial requirements.
Cost Factors and Lead Time Considerations for 3D Printed Valve Positioner Housings
Understanding the cost drivers and typical lead times associated with metal 3D printing is crucial for budgeting and project planning. Here’s a breakdown of the key factors:
Kostnadsfaktorer:
- Kostnader för material: The cost of the metal powder is a significant factor. Specialty alloys like Inconel 625 are typically more expensive than stainless steels like 316L. The quantity of material used for each part will also directly impact the cost. Design optimization to reduce material usage can help mitigate this.
- Printing Time: The build time is influenced by the part’s volume, complexity, layer height, and the number of parts being printed simultaneously in the build chamber. Longer print times translate to higher machine operation costs.
- Machine Operation and Maintenance: These costs include energy consumption, consumables (e.g., inert gases, filters), and regular machine maintenance.
- Pre-Processing Costs: This can include design optimization for additive manufacturing, build preparation, and generating support structures.
- Kostnader för efterbearbetning: As discussed earlier, post-processing steps like support removal, heat treatment, surface finishing, and machining add to the overall cost. The complexity and extent of these processes will influence the final price.
- Kostnader för arbetskraft: This includes the expertise required for design, printing, post-processing, quality control, and project management.
- Tooling Costs (Minimized but not entirely eliminated): While metal 3D printing largely eliminates the need for traditional hard tooling, there might be costs associated with specialized fixtures for post-processing or inspection.
Lead Time Considerations:
- Prototyping: Metal 3D printing significantly reduces prototyping lead times compared to traditional methods that require tooling. Prototypes can often be produced in a matter of days or weeks, depending on complexity and material availability.
- Produktion: Production lead times depend on factors such as part complexity, build volume, material availability, and the service provider’s capacity. Smaller production runs can often be completed relatively quickly. For larger volumes, lead times will be influenced by the number of printers available and the build time per part.
- Efterbearbetning: The time required for post-processing steps can also impact the overall lead time. Complex heat treatments or extensive surface finishing will add to the total manufacturing time.
It’s important to obtain detailed quotes from potential service providers that break down these cost and lead time factors for your specific valve positioner housing requirements. Discussing design optimizations and material choices with the provider can sometimes lead to cost reductions and shorter lead times.
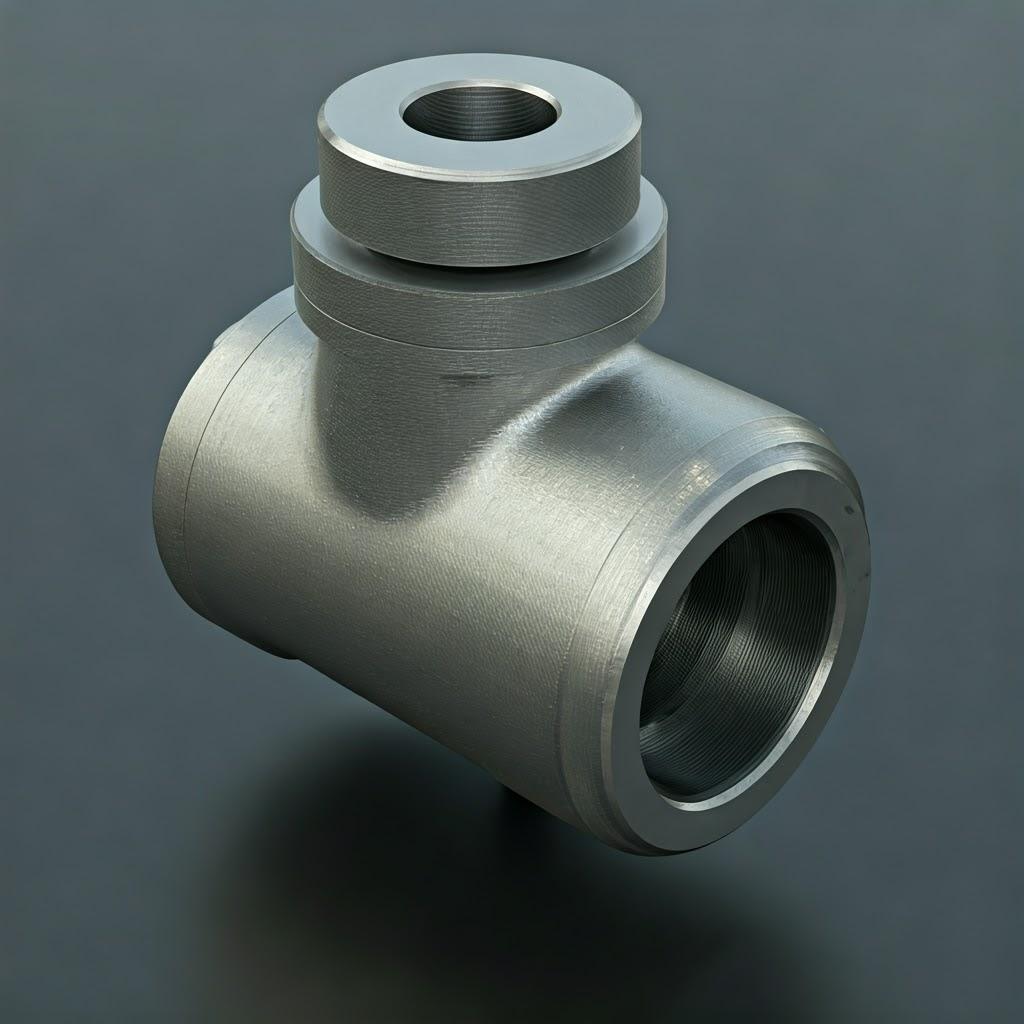
Frequently Asked Questions (FAQ) about 3D Printing Valve Positioner Housings
- Is metal 3D printing strong enough for industrial valve positioner housings?
- Yes, absolutely. When the right metal powder is used (like 316L or IN625), and the printing process is optimized with appropriate post-processing (like HIP), metal 3D printed parts can achieve mechanical properties comparable to or even exceeding those of traditionally manufactured components. The layer-by-layer build process, when properly controlled, results in dense, strong parts suitable for demanding industrial applications.
- Can metal 3D printing handle the tight tolerances required for valve positioner components?
- Yes, metal 3D printing technologies are capable of achieving tight tolerances, typically in the range of ±0.1 to ±0.05 mm. With careful design considerations, optimized build parameters, and the potential for post-processing like precision machining for critical interfaces, the dimensional accuracy required for valve positioner housings can be met. Metal3DP’s commitment to accuracy ensures reliable results.
- Is metal 3D printing cost-effective for producing valve positioner housings?
- The cost-effectiveness of metal 3D printing depends on several factors, including the complexity of the design, the material used, production volume, and the need for tooling in traditional methods. For complex geometries, low to medium production volumes, and customized parts, metal 3D printing can be very cost-competitive. It eliminates the upfront costs and lead times associated with traditional tooling and allows for design optimizations that can reduce material usage and assembly costs.
Conclusion: The Future of Industrial Valve Positioner Housings with Metal 3D Printing
Metal 3D printing is rapidly evolving into a powerful manufacturing solution for industrial components, and valve positioner housings are no exception. The ability to create complex geometries, optimize designs for performance and weight, utilize high-performance materials like 316L and IN625, and potentially consolidate multiple parts into a single component offers significant advantages over traditional manufacturing methods.
While challenges such as achieving tight tolerances and managing surface finish require careful consideration and the application of appropriate post-processing techniques, the benefits of design flexibility, material efficiency, and rapid prototyping make metal 3D printing an increasingly attractive option for engineers and procurement managers across aerospace, automotive, medical, and industrial manufacturing sectors.
As technology advances and material costs potentially decrease, we can expect to see even wider adoption of metal 3D printing for critical industrial components like valve positioner housings. Companies like Metal3DP Technology Co., LTD, with their focus on avancerade metallpulver och reliable 3D printing equipment, are at the forefront of this revolution, empowering industries to unlock new possibilities in design, performance, and manufacturing efficiency. By embracing the potential of metal additive manufacturing, companies can enhance their innovation, streamline their supply chains, and ultimately gain a competitive edge in the demanding landscape of industrial component production.
Dela på
MET3DP Technology Co, LTD är en ledande leverantör av lösningar för additiv tillverkning med huvudkontor i Qingdao, Kina. Vårt företag är specialiserat på 3D-utskriftsutrustning och högpresterande metallpulver för industriella tillämpningar.
Förfrågan för att få bästa pris och anpassad lösning för ditt företag!
Relaterade artiklar
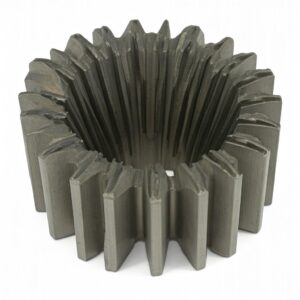
Högpresterande segment för munstycksvingar: Revolutionerande turbineffektivitet med 3D-utskrift i metall
Läs mer "Om Met3DP
Senaste uppdateringen
Vår produkt
KONTAKTA OSS
Har du några frågor? Skicka oss meddelande nu! Vi kommer att betjäna din begäran med ett helt team efter att ha fått ditt meddelande.
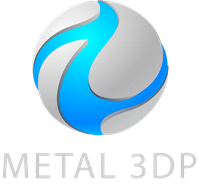
Metallpulver för 3D-printing och additiv tillverkning
FÖRETAG
PRODUKT
cONTACT INFO
- Qingdao City, Shandong, Kina
- [email protected]
- [email protected]
- +86 19116340731