3D Printed Air Scoops for Performance Vehicles
Innehållsförteckning
Introduction: Optimizing Performance with 3D Printed Metal Air Intake Scoops
In the relentless pursuit of performance, engineers in the automotive, motorsports, and performance aftermarket sectors are constantly seeking innovative ways to enhance vehicle efficiency, power, and responsiveness. One critical component influencing engine performance is the air intake system. Custom air intake scoops, designed to channel cool, dense air directly into the engine’s intake manifold or turbocharger, play a pivotal role in optimizing combustion and maximizing power output. Traditionally, manufacturing these complex, often bespoke components involved limitations in design freedom, lengthy tooling processes, and compromises in weight or material properties. However, the advent of metalltillsatstillverkning (AM), or metal 3D-utskrifter, has revolutionized the approach to creating high-performance custom air intake scoops.
Metal 3D printing allows for the creation of intricate geometries, optimized airflow pathways, and lightweight structures previously impossible or prohibitively expensive to produce. This technology empowers Fordonsteknik teams to design and manufacture scoops tailored precisely to specific vehicle architectures and performance goals. By leveraging advanced metal powders and sophisticated printing processes like Selective Laser Melting (SLM) or Electron Beam Melting (EBM), manufacturers can now produce durable, high-temperature resistant, and highly customized air intake components on demand.
At Met3DP, headquartered in Qingdao, China, we are at the forefront of this technological shift. As a leading provider of 3D-utskrift av metall solutions, specializing in both advanced printing equipment and high-performance metal powders, we empower industries to harness the full potential of additive manufacturing. Our commitment to industry-leading print volume, accuracy, and reliability ensures that the components we help produce, including custom air intake scoops, meet the rigorous demands of performance vehicles and other critical applications. This post delves into the specifics of using metal AM for air intake scoops, exploring the applications, benefits, materials, and considerations for engineers and procurement managers seeking a competitive edge.
What Are Custom Air Intake Scoops Used For?: Functionality and Applications
A custom air intake scoop, often referred to as a hood scoop, bonnet scoop, or cold air intake duct, serves a primary, critical function: to capture and direct a high volume of ambient air, preferably cool and dense, towards the engine’s air intake system. The underlying principle is simple thermodynamics and engine operation:
- Increased Air Density: Cooler air is denser than warmer air. Denser air contains more oxygen molecules per unit volume.
- Improved Combustion: More oxygen allows for a more complete and potent combustion of fuel within the engine cylinders.
- Enhanced Power Output: Efficient combustion translates directly into increased horsepower and torque.
- Reduced Intake Air Temperature (IAT): By drawing air from outside the hot engine bay (often from a high-pressure zone like the base of the windshield or front grille area), scoops help lower IAT, preventing heat soak and maintaining consistent performance, especially under demanding conditions.
Key Functionalities:
- Forced Air Induction: At speed, scoops can create a ram-air effect, slightly pressurizing the air entering the intake tract, further boosting volumetric efficiency.
- Targeted Cooling: Some scoop designs specifically target airflow towards critical components like turbochargers or intercoolers, aiding in thermal management.
- Engine Bay Ventilation: While primarily for intake, some scoop designs can also contribute to venting hot air from the engine compartment.
Primary Applications:
The use of custom air intake scoops is prevalent across various demanding sectors:
- Motorsport: Formula 1, IndyCar, Le Mans Prototypes, Drag Racing, Rallying, Touring Cars – virtually all forms of competitive racing utilize precisely engineered scoops for maximum engine performance parts optimization. Weight, aerodynamic efficiency, and thermal resistance are paramount.
- Performance Aftermarket: Tuners and enthusiasts modifying street cars (sports cars, muscle cars, hot hatches) often install aftermarket scoops to boost power, improve throttle response, and achieve a more aggressive aesthetic. Cold air intake systems are a popular modification.
- Custom Vehicle Builds: One-off custom cars, kit cars, and specialty vehicles often require bespoke intake solutions where standard parts won’t fit or meet performance targets.
- Heavy-Duty & Industrial Vehicles: In some specialized applications, scoops might be used on heavy machinery or power generation equipment where optimized air intake improves efficiency or cooling in harsh environments.
- Aerospace (Niche): While different in form, the principles of directing airflow for cooling or intake are applied in certain aerospace applications, sometimes benefiting from AM’s design freedom.
The ability to customize the shape, size, internal ducting, and mounting points makes metal 3D printing an ideal solution for creating scoops that perfectly integrate with specific turbocharger intake systems or naturally aspirated engine configurations, delivering measurable performance gains. Procurement managers sourcing these components for racing teams or performance brands value the ability to order low volumes of highly specialized designs, a key strength of additive manufacturing suppliers like Met3DP.
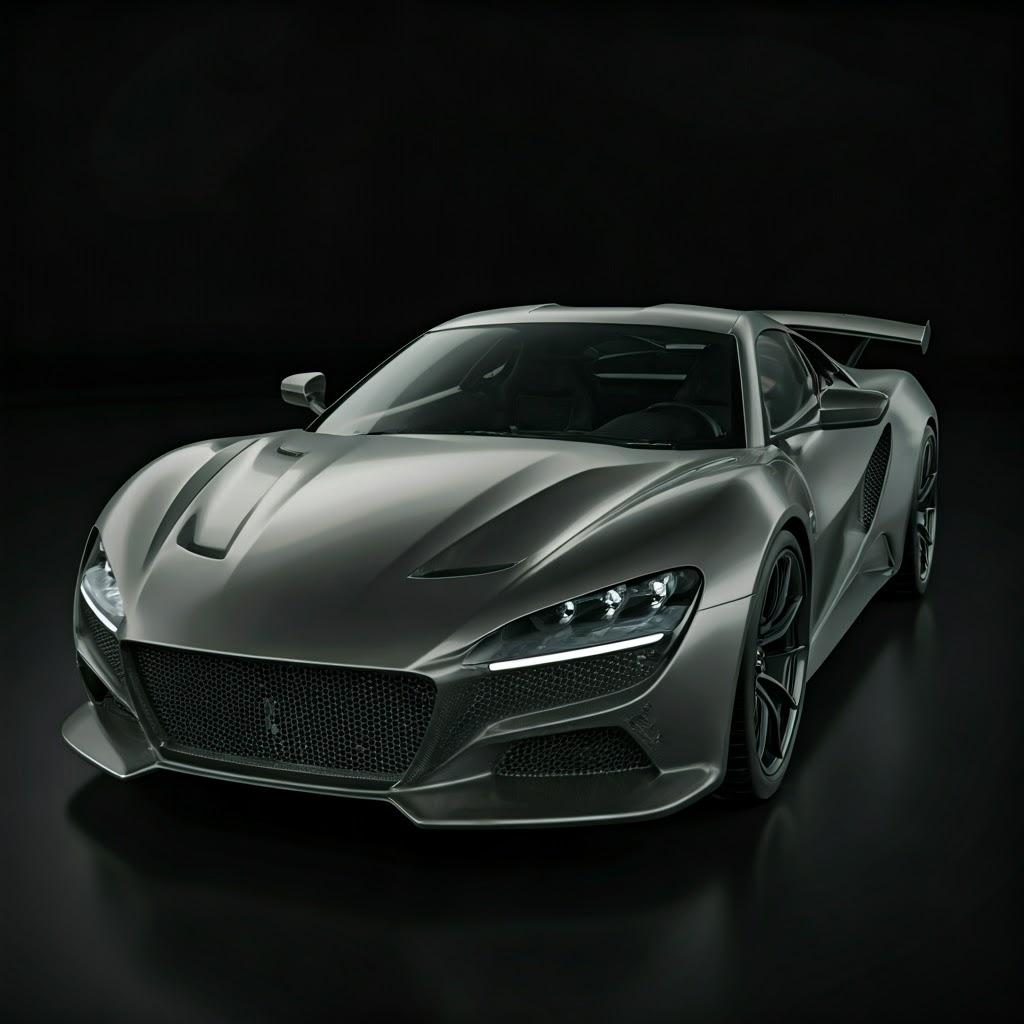
Why Use Metal 3D Printing for Air Intake Scoops?: The Additive Advantage
While air intake scoops can be manufactured using traditional methods like fiberglass molding, carbon fiber layup, plastic injection molding, sheet metal fabrication, or CNC machining from billet, additiv tillverkning av metall offers a compelling set of advantages, particularly for high-performance, low-to-mid volume, or highly customized applications. The limitations of traditional methods often involve expensive tooling (molds, dies), design constraints (undercuts, complex internal passages), longer lead times for prototypes, and potential compromises in strength-to-weight ratio or thermal resistance.
Metal 3D printing overcomes many of these hurdles:
Comparison: Metal AM vs. Traditional Manufacturing for Air Scoops
Funktion | Metal Additive Manufacturing (e.g., SLM/EBM) | Traditional Methods (Fiberglass, Carbon, CNC, Fab) |
---|---|---|
Designfrihet | Very High: Complex internal channels, organic shapes, thin walls, integrated features easily achievable. Supports topologioptimering. | Moderate to Low: Limited by mold constraints, machining access, fabrication techniques. Undercuts are difficult/costly. |
Verktyg | None: Direct digital manufacturing from CAD data. | Required: Molds, dies, jigs, fixtures often necessary, adding cost and lead time. |
Prototyping Speed | Fast: Prototypes can be printed in days, enabling rapid iteration and design validation. Ideal for snabba prototyptjänster. | Slower: Tooling creation or complex fabrication/machining setup extends prototyping timelines. |
Anpassning | High: Economical for producing unique or low-volume custom designs per vehicle/application. | Costly: Customization often requires new tooling or significant setup changes. |
Materialalternativ | Wide Range: Aluminum alloys, titanium alloys, nickel superalloys, stainless steels offer diverse properties (strength, temp resistance). | Varies: Limited by process (e.g., specific resins for molding, machinable metals for CNC). Metal options can be heavy if not optimized. |
Lättvikt | Excellent Potential: Allows for complex internal lattice structures and topology optimization to minimize mass while maintaining strength. Creates lätta fordonsdelar. | Possible but Challenged: Achieving optimal lightweighting with complex shapes can be difficult or labor-intensive (e.g., complex carbon layup). |
Konsolidering av delar | Possible: Multiple components (e.g., scoop body, mounting flanges, internal vanes) can potentially be printed as a single piece. | Often Requires Assembly: Separate parts typically need bonding, welding, or fasteners. |
Lead Time (Production) | Fast for Low Volume: Ideal for <1000 parts/year. Minimal setup time once design is finalized. | Faster for High Volume: Once tooling is made, unit production time can be very fast (e.g., injection molding). |
Initial investering | Lower (for low vol): No tooling costs amortized over parts. | Higher (for tooling): Tooling costs must be recouped, making low volumes expensive. |
Export to Sheets
Key Benefits Summarized:
- Unmatched Design Complexity: Create aerodynamically superior internal passages and mounting solutions impossible with other methods.
- Rapid Iteration & Development: Quickly test multiple design variations on a dyno or track without waiting weeks for tooling.
- Massanpassning: Produce unique scoops for different vehicle models or specific customer requirements cost-effectively.
- Optimized Material Performance: Utilize high-strength, lightweight, or high-temperature metal alloys (like AlSi10Mg or IN625) perfectly suited to the demanding under-hood environment.
- Reduced Part Count: Integrate features and consolidate assemblies, reducing weight, potential leak paths, and assembly labor.
- On-Demand-produktion: Manufacture parts as needed, minimizing inventory holding costs – ideal for procurement managers managing specialized part supply chains.
Met3DP leverages its advanced SEBM (Selective Electron Beam Melting) and other Powder Bed Fusion printers, coupled with deep materials science expertise, to fully realize these metal AM benefits. Our systems deliver the accuracy and reliability needed for mission-critical performance vehicle components like air intake scoops.
Recommended Materials for 3D Printed Air Scoops: AlSi10Mg vs. IN625
Choosing the right material is crucial for the performance and durability of a 3D printed metal air intake scoop. The operating environment (temperature, vibration, potential impacts) and performance goals (weight saving, maximum strength) dictate the best choice. Two commonly recommended metal powders, both available from specialist suppliers like Met3DP, are AlSi10Mg (an aluminum alloy) and IN625 (a nickel superalloy).
Met3DP utilizes industry-leading gas atomization and Plasma Rotating Electrode Process (PREP) technologies to produce high-sphericity, excellent flowability metal powders optimized for additive manufacturing. While our portfolio includes innovative alloys like TiNi, TiTa, TiAl, CoCrMo, and various steels, AlSi10Mg and IN625 are often the go-to choices for air intake applications. Explore our range on the Met3DP products page.
AlSi10Mg (Aluminum-Silicon-Magnesium Alloy)
AlSi10Mg is one of the most widely used aluminum alloys in metal AM. It’s essentially a casting alloy adapted for powder bed fusion processes.
- Key Characteristics & Benefits for Air Scoops:
- Lättviktare: Aluminum alloys have a low density (approx. 2.67 g/cm³), crucial for performance applications where minimizing weight is essential.
- Bra förhållande mellan styrka och vikt: Offers respectable mechanical properties after appropriate heat treatment (e.g., T6).
- Utmärkt värmeledningsförmåga: Helps dissipate heat, although less critical for the scoop itself than for components like heat exchangers.
- God korrosionsbeständighet: Suitable for typical automotive under-hood environments.
- Svetsbarhet: Can be welded if post-print modifications are needed.
- Kostnadseffektivt: Generally less expensive than titanium or nickel superalloys.
- Utskriftsmöjlighet: Well-understood processing parameters lead to reliable printing results.
- Begränsningar:
- Lower high-temperature strength compared to steel or nickel alloys. May soften significantly above 150-200°C, limiting use very close to exhaust manifolds or turbochargers without heat shielding.
IN625 (Inconel 625 – Nickel-Chromium Superalloy)
IN625 is a high-performance nickel-based superalloy known for its exceptional properties at extreme temperatures.
- Key Characteristics & Benefits for Air Scoops:
- Outstanding High-Temperature Strength: Maintains excellent mechanical properties at temperatures exceeding 650°C (up to ~980°C for short excursions), making it ideal for scoops located near hot engine components like turbochargers or exhaust systems.
- Excellent Corrosion and Oxidation Resistance: Highly resistant to a wide range of corrosive environments, including exhaust gases and road salts.
- High Tensile, Creep, and Rupture Strength: Extremely durable and resistant to fatigue, vital in high-vibration environments.
- Superb Weldability & Fabricability: Can be readily welded and formed (though less relevant for AM).
- Begränsningar:
- Higher Density: Significantly denser than aluminum (approx. 8.44 g/cm³), resulting in a heavier part unless designs are aggressively optimized for lightweighting (e.g., thin walls, topology optimization).
- Högre kostnad: Nickel superalloy powders are considerably more expensive than aluminum alloys.
- Lower Thermal Conductivity: Doesn’t dissipate heat as readily as aluminum.
- More Challenging Printability: Requires careful parameter control to manage residual stresses and ensure part quality.
Material Selection Guide:
Parameter | AlSi10Mg | IN625 | Consideration for Air Scoop |
---|---|---|---|
Primary Goal | Lightweight, Cost-Effective | High-Temp Resistance, Durability | Choose based on proximity to heat sources and budget. |
Max Operating Temp. | ~150-200°C (Continuous) | >650°C (Continuous) | Critical if scoop is near turbo/exhaust. |
Täthet | Low (~2.67 g/cm³) | High (~8.44 g/cm³) | Impacts overall vehicle weight. IN625 requires more design optimization to save weight. |
Kostnad | Lägre | Högre | Significant factor for procurement and overall project budget. |
Strength (Ambient Temp) | Good (Post-Heat Treat) | Utmärkt | Both are generally sufficient, but IN625 offers higher ultimate strength and fatigue life. |
Motståndskraft mot korrosion | Bra | Utmärkt | IN625 superior in very harsh or coastal environments. |
Supplier Availability | Mycket tillgänglig | Mycket tillgänglig | Met3DP offers high-quality versions of both as a premier metal powder supplier. |
Export to Sheets
Why Material Properties Matter for Procurement & Engineering:
- Prestanda: Directly impacts engine power potential (airflow) and vehicle dynamics (weight).
- Hållbarhet: Ensures the scoop survives the harsh under-hood environment (heat, vibration, debris).
- Kostnad: Influences the bill of materials (BOM) and overall project feasibility.
- Ledtid: Material choice can sometimes influence print time and post-processing requirements.
Engineers must carefully evaluate the specific operating conditions and performance targets to select the optimal material. Procurement managers need to understand these trade-offs to source the most cost-effective solution that meets the technical requirements. Partnering with an experienced automotive material selection expert and AM provider like Met3DP, who manufactures high-quality powders and understands their application, ensures the best outcome for your 3D printed air intake scoop project.
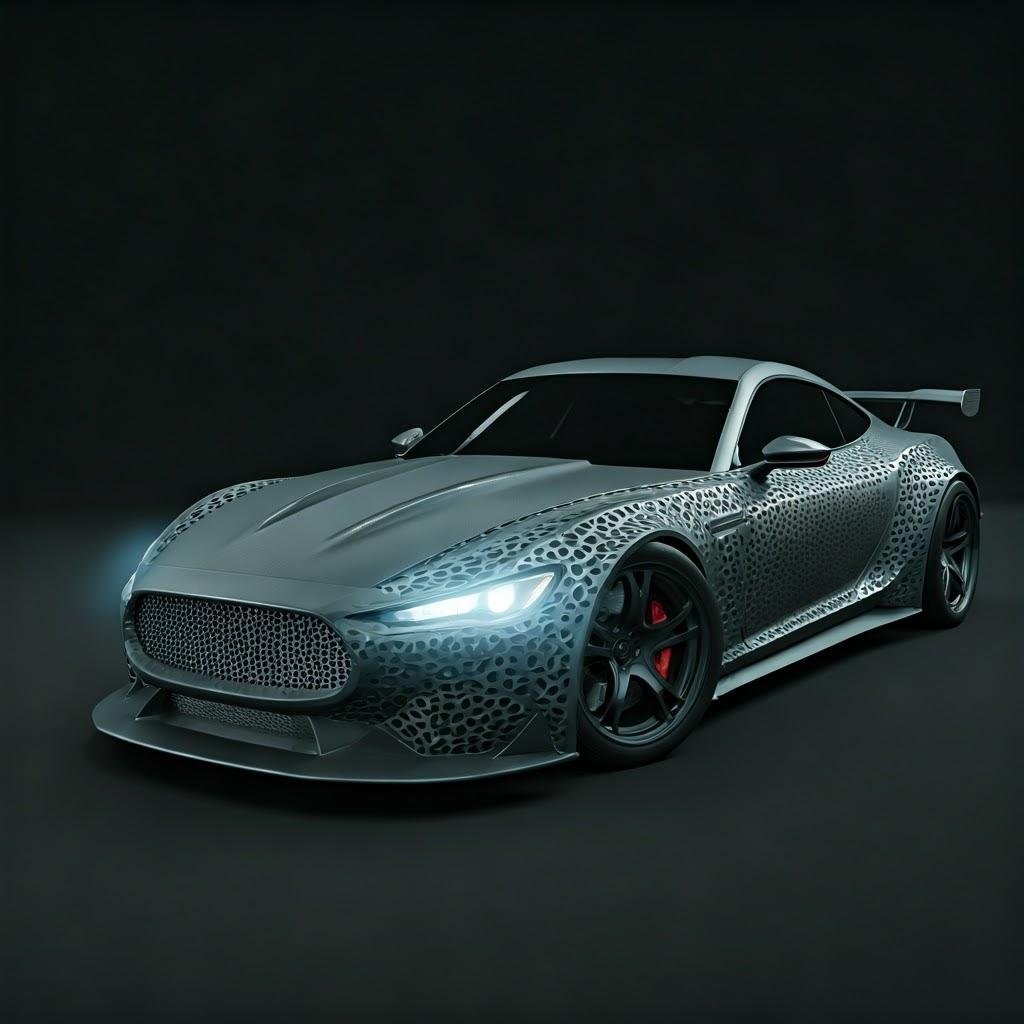
Design Considerations for Additive Manufacturing: Engineering Superior Airflow
Simply replicating a traditionally designed air intake scoop using metal 3D printing often fails to leverage the technology’s true potential. To unlock significant performance gains, weight reduction, and cost efficiencies, engineers must embrace Design för additiv tillverkning (DfAM) principles. DfAM involves rethinking the design process to suit the capabilities and nuances of layer-by-layer construction. For custom air intake scoops, this means focusing on optimizing airflow, minimizing weight, reducing post-processing, and integrating functionality. Partnering with AM experts, like the team at Met3DP, during the design phase can significantly enhance the final product.
Key DfAM Principles for Air Intake Scoops:
- Flow Path Optimization:
- Smooth Internal Channels: Utilize Computational Fluid Dynamics (CFD) airflow simulation data to guide the design of internal passages. Metal AM allows for complex, organic curves and variable cross-sections that minimize turbulence and pressure drop, maximizing air delivery efficiency to the engine or turbo inlet. Avoid sharp corners or abrupt transitions common in fabricated parts.
- Bell Mouth Entrances: Design smooth, radiused inlets (bell mouths) to reduce air entry losses and promote laminar flow.
- Internal Vanes/Structures: Incorporate complex internal vanes or flow straighteners directly into the print to manage airflow direction or velocity profiles, something extremely difficult or impossible with traditional methods.
- Support Structure Minimization:
- Self-Supporting Angles: Design overhangs and internal channels with angles typically greater than 45 degrees relative to the build plate. This significantly reduces the need for sacrificial support structures, saving material, print time, and extensive post-processing effort, especially for hard-to-reach internal areas.
- Orientation Strategy: Consider the optimal build orientation early in the design phase. Orienting the part to minimize steep overhangs and critical features facing downwards is key.
- Designing for Support Removal: If supports are unavoidable (e.g., inside complex plenums), design access ports or breakaway features to facilitate their removal without damaging the part.
- Wall Thickness and Lightweighting:
- Minimum Viable Thickness: Metal AM can achieve thin walls (down to 0.4-0.8 mm, depending on material and geometry), but consider structural integrity, handling, and vibration resistance. Aim for the minimum thickness that meets performance requirements.
- Topology Optimization: Employ topology optimization automotive software to remove material from non-critical areas while maintaining stiffness and strength. This algorithm-driven process creates organic, load-path-optimized shapes ideal for AM, resulting in significant weight savings – crucial for performance vehicles.
- Gitterstrukturer: Incorporate internal lattice or gyroid structures within thicker sections to reduce mass and material consumption without sacrificing structural integrity. These complex structures are unique to AM.
- Part Consolidation and Feature Integration:
- Reduce Assembly: Combine multiple components (e.g., scoop body, mounting flanges, sensor bosses, brackets) into a single, monolithic print. This eliminates assembly steps, fasteners, potential leak paths, and tolerance stack-up issues.
- Integrated Mounting Features: Design screw threads, bosses, snap-fits, or complex mating interfaces directly into the part, simplifying installation and improving integration with the vehicle chassis or engine components.
- Surface Texture:
- Consider the as-printed surface roughness. While often smoothed in post-processing, a slightly rougher internal surface might, in some cases, help maintain boundary layer attachment at specific flow rates. Conversely, very smooth surfaces might be desired for purely laminar flow conditions. Design intent should guide surface finish requirements.
DfAM Summary Table:
DfAM Technique | Benefit for Air Scoop | How AM Enables It |
---|---|---|
CFD-Driven Shapes | Optimized airflow, reduced pressure drop, increased power. | Layer-by-layer building allows complex internal curves. |
Self-Supporting Angles | Reduced supports, faster print, less post-processing. | Design freedom to orient features optimally. |
Topology Optimization | Maximum stiffness/strength for minimum weight. | Creates complex, organic shapes impossible otherwise. |
Konsolidering av delar | Reduced assembly, weight, leak points, cost. | Ability to print complex, multi-feature components. |
Integrated Features | Simplified installation, improved integration. | Precise feature creation during the printing process. |
Thin Walls/Lattices | Significant weight reduction, material savings. | Control over fine features and internal structures. |
Export to Sheets
By applying these DfAM principles, engineers and procurement managers can ensure they are sourcing not just a replacement part, but a truly optimized component that delivers superior performance and value, fully exploiting the additive advantage.
Tolerance, Surface Finish, and Dimensional Accuracy in Metal AM Scoops
A common question from engineers and procurement specialists evaluating metal 3D printing concerns the precision achievable. Understanding the typical metal 3D printing tolerances, surface characteristics, and dimensional accuracy is crucial for managing expectations and ensuring the final air intake scoop meets functional requirements, particularly for mating surfaces and aerodynamic performance. Met3DP’s commitment to industry-leading accuracy and reliability, backed by rigorous quality control, ensures parts consistently meet demanding specifications.
Dimensionell noggrannhet:
- General Tolerances: For metal Powder Bed Fusion (PBF) processes like SLM and EBM, typical achievable dimensional tolerances often fall within the range of +/- 0.1mm to +/- 0.2mm for smaller features (e.g., < 100mm), and potentially +/- 0.1% to +/- 0.2% of the nominal dimension for larger features. Some providers may reference standards like ISO 2768 (medium ‘m’ or fine ‘f’ classes) as a general guideline, but specific capabilities should always be confirmed.
- Factors Influencing Accuracy:
- Machine Calibration: Regular, precise calibration is fundamental.
- Materialegenskaper: Different metals exhibit varying shrinkage and thermal behavior.
- Part Geometry & Size: Large, complex parts are more prone to minor deviations.
- Bygg orientering: Affects thermal stresses and support needs.
- Thermal Stress & Warpage: Must be managed through parameters and potentially stress relief.
- Efterbearbetning: Machining operations can achieve much tighter tolerances on specific features.
Surface Finish (Roughness):
- As-Printed Surface: The nature of layer-by-layer fusion results in a characteristic surface finish.
- Ra Value: Vanligtvis varierar intervallet från 8 to 25 micrometers (µm) Ra (Roughness Average), depending on the material, parameters, orientation (upward vs. downward facing surfaces), and layer thickness used.
- Texture: Surfaces often have a slightly grainy or matte texture, showing faint layer lines, especially on angled surfaces. Powder particles may be loosely sintered to downward-facing surfaces.
- Internal Channels: Achieving a smooth finish inside long, narrow, or complex internal channels can be challenging without specialized post-processing.
- Post-Processed Surface: Various finishing steps can significantly improve the surface smoothness.
- Bead Blasting: Creates a uniform matte finish, typically Ra 5-15 µm.
- Tumbling/Vibratory Finishing: Can smooth surfaces and edges, achieving Ra values potentially down to 1-5 µm, depending on media and time.
- Maskinbearbetning: Creates smooth, precise surfaces with Ra < 1 µm possible.
- Polering: Can achieve mirror-like finishes (Ra < 0.5 µm) on accessible surfaces.
- Impact on Performance:
- Aerodynamics: While debated, the as-printed roughness inside a scoop might slightly increase turbulence compared to a polished surface, potentially affecting flow efficiency at the margins. However, the overall geometric design usually has a much larger impact.
- Mating Surfaces: Interfaces connecting to throttle bodies, turbochargers, or airboxes often require a smoother finish and tighter tolerances (achieved via machining) to ensure proper sealing.
Comparison: As-Printed vs. Post-Processed
Funktion | As-Printed Metal AM Part | Post-Processed Metal AM Part (Typical) |
---|---|---|
Tolerans | +/- 0.1 to 0.5 mm (General) | Tighter on machined features (< +/- 0.05 mm possible) |
Ytfinish | Ra 8-25 µm, Matte/Layered Texture | Ra < 1 µm (Machined) to Ra 5-15 µm (Blasted) |
Utseende | Matte, potentially visible layers | Smoother, uniform, potentially polished |
Kostnad | Lower (Print cost only) | Higher (Adds labor & machine time) |
Ledtid | Snabbare | Längre |
Export to Sheets
Quality Control & Specification:
It’s vital to clearly define critical dimensions, tolerances, and surface finish requirements on engineering drawings. Specify which features require tighter controls (e.g., machined interfaces) versus those where as-printed characteristics are acceptable. Utilize Geometric Dimensioning and Tolerancing (GD&T) for complex requirements. Robust Quality Control AM processes, including CMM inspection and surface profilometry, ensure parts meet specifications before shipping. Procurement managers should ensure potential suppliers, like Met3DP, have robust quality management systems (e.g., ISO 9001 certification) in place.
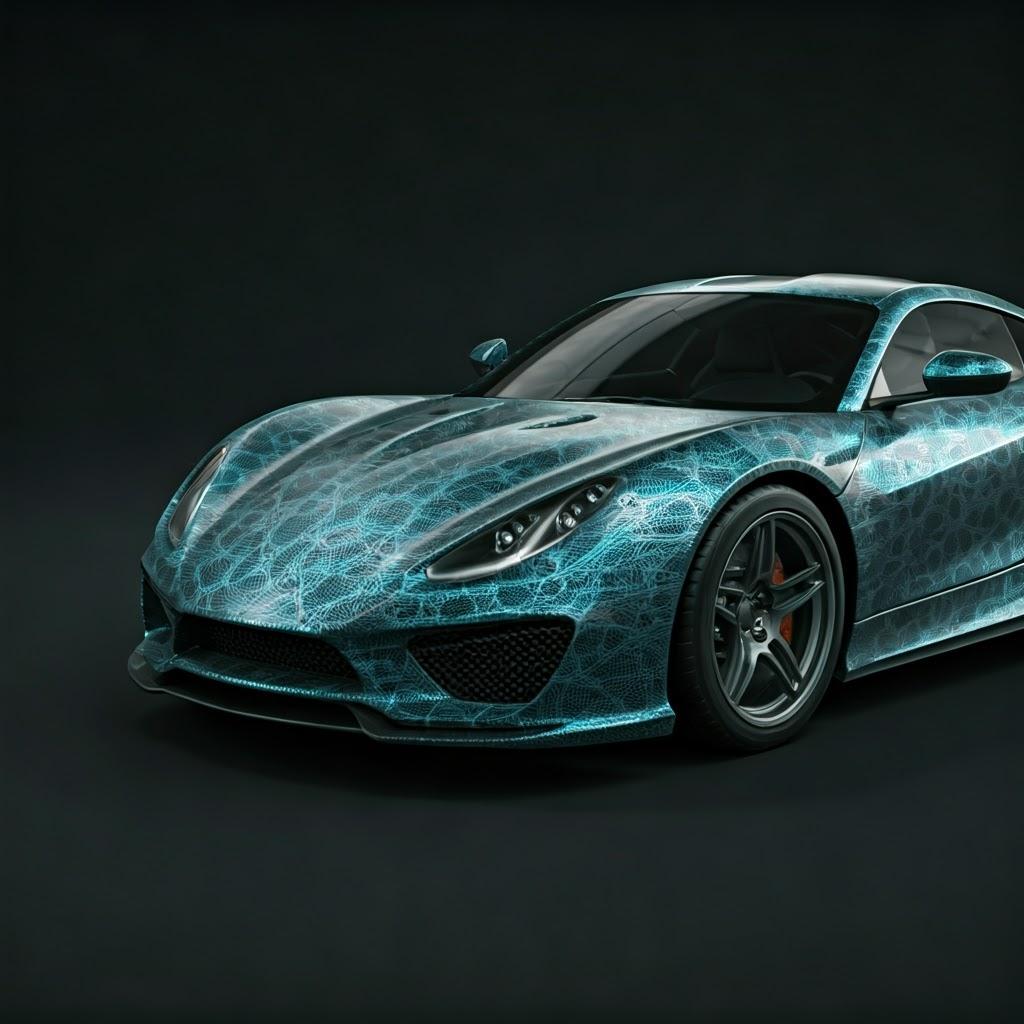
Post-Processing Requirements for Functional Air Intake Scoops
A metal 3D printed air intake scoop rarely comes off the build plate ready for immediate installation. Several crucial efterbearbetning steps are typically required to transform the raw print into a functional, durable, and dimensionally accurate performance component. Understanding these steps is essential for engineers designing the part and procurement managers planning project timelines and budgets. Leading AM service providers like Met3DP offer comprehensive post-processing capabilities, providing turnkey solutions.
Common Post-Processing Steps:
- Part Removal & Cleaning:
- The part must be carefully removed from the build plate, often requiring cutting or wire EDM, especially if printed directly onto the plate.
- Excess metal powder must be removed, particularly from internal channels and intricate features. This typically involves compressed air, brushing, and sometimes specialized powder removal stations. Thorough cleaning is vital to prevent loose powder from entering the engine.
- Stress Relief / Heat Treatment:
- Syfte: The rapid heating and cooling inherent in PBF processes create internal stresses within the printed part. Heat treatment is critical to relieve these stresses, preventing potential warping or cracking later, and to achieve the desired final mechanical properties (strength, ductility, hardness) of the alloy.
- Process:
- AlSi10Mg: Typically requires a stress relief cycle followed by a T6 solution heat treatment and artificial aging (Heat Treatment Aluminum Alloys) to reach optimal strength. Precise temperature control and furnace atmosphere are critical.
- IN625: Usually requires an annealing or solutionizing treatment at high temperatures, followed by potential aging depending on the specific strength requirements. This homogenizes the microstructure and relieves stress.
- Importance: Skipping or improperly performing heat treatment can lead to premature component failure.
- Support Structure Removal (Support Removal Metal AM):
- Syfte: Sacrificial support structures prevent overhangs from collapsing during the build. These must be removed carefully.
- Metoder: Depending on the support design and location, removal can involve:
- Manual breaking (for easily accessible, light supports).
- Hand tools (pliers, grinders).
- Machining (milling or turning away support interfaces).
- Wire EDM (for precise cutting near the part surface).
- Utmaningar: Removing supports from deep internal channels or complex geometries without damaging the part requires skill and careful planning (ideally considered during the DfAM phase).
- Machining (CNC Machining 3D Prints):
- Syfte: To achieve tighter tolerances, specific surface finishes, and precise geometric features unobtainable in the as-printed state.
- Applications for Scoops:
- Mating Flanges: Ensuring flatness and precise location for connection to throttle bodies, turbo inlets, or air filter housings.
- Sensor Ports: Creating accurately threaded or bored holes for MAP, IAT, or other sensors.
- Critical Diameters: Ensuring precise internal diameters for hose connections or airflow metering sections.
- Aesthetic Surfaces: Achieving a high-quality machined look on visible areas if desired.
- Överväganden: Requires accurate fixturing of the potentially complex AM part. Sufficient material must be left (‘machining stock’) in the design phase on surfaces intended for machining.
- Surface Finishing Techniques:
- Syfte: To improve surface smoothness, aesthetics, cleanability, or provide additional protection.
- Common Methods:
- Bead Blasting / Sand Blasting: Provides a uniform, non-directional matte finish. Cleans the surface and can remove minor imperfections. Most common general finish.
- Tumbling / Vibratory Finishing: Uses abrasive media in a vibrating bowl or tumbler to smooth surfaces and round edges. Good for deburring and achieving a consistent finish on batches of parts.
- Polering: Manual or automated polishing for highly reflective, smooth surfaces on accessible areas (mainly external).
- Anodizing (AlSi10Mg): Electrochemical process that creates a hard, corrosion-resistant oxide layer. Can also be dyed various colors.
- Painting / Powder Coating: For specific colors or enhanced environmental protection. Requires proper surface preparation.
- Ceramic Coating: Application of thermal barrier coatings, especially if the scoop is very close to extreme heat sources.
- Inspection and Quality Control:
- Verifiering av dimensioner: Using CMMs, 3D scanners, calipers, and gauges to confirm critical dimensions are within tolerance.
- Surface Finish Measurement: Using profilometers to verify Ra values meet specifications.
- Leak Testing: If sealing is critical.
- Icke-förstörande testning (NDT): Dye penetrant testing or CT scanning may be used in critical applications to check for surface defects or internal porosity, although less common for typical scoops unless specified.
Effective performance part finishing relies on a combination of these processes, tailored to the specific requirements of the air intake scoop. Engaging with a full-service provider ensures seamless integration of printing and post-processing for optimal results.
Common Challenges in 3D Printing Air Scoops and How to Avoid Them
While metal additive manufacturing offers tremendous advantages for creating custom air intake scoops, it’s not without potential challenges. Awareness of these common issues allows engineers and manufacturers to implement mitigation strategies during design, printing, and post-processing, ensuring a successful outcome. Partnering with an experienced AM provider like Met3DP, who understands additive manufacturing troubleshooting, is key to navigating these complexities.
Challenge 1: Warping and Distortion
- Cause: Significant thermal gradients during the PBF process lead to the build-up of residual stress. As the part cools, or when removed from the build plate, these stresses can cause it to warp or distort, deviating from the intended geometry. This is particularly prevalent in large, flat sections or asymmetric designs.
- Mitigation Strategies:
- Optimized Build Orientation: Position the part on the build plate to minimize large flat areas parallel to the plate and distribute thermal mass evenly.
- Robust Support Structures: Use well-designed supports to anchor the part firmly to the build plate, resisting stress-induced movement during the build.
- Processparameteroptimering: Fine-tuning laser/electron beam power, scan speed, and layer thickness can help manage thermal input. Use of pre-heating the build plate (common in EBM and some SLM systems) significantly reduces thermal gradients.
- Appropriate Heat Treatment: A proper residual stress management protocol (stress relief heat treatment) performed before removing the part from the build plate (if possible) or immediately after is crucial.
- Design Modifications: Incorporating ribs or altering geometry to increase stiffness can help resist warping.
Challenge 2: Difficult Support Removal
- Cause: Complex internal channels, deeply recessed features, or poorly designed support structures can make removal extremely difficult, time-consuming, and risk damaging the part. Supports made from the same high-strength material (AlSi10Mg, IN625) can be tough to break or cut away cleanly.
- Mitigation Strategies:
- DfAM Focus: Prioritize self-supporting angles (>45°) wherever possible during the design phase.
- Support Optimization Software: Utilize advanced software to generate supports that are strong where needed but designed for easier removal (e.g., perforated, smaller contact points).
- Design for Access: Intentionally include access ports or openings (which might be plugged or welded shut later if needed) specifically for reaching and removing internal supports.
- Consider Orientation: Orient the part so complex internal features are self-supporting or easily accessible after printing.
- Specialized Tools / Techniques: Plan for the use of specific hand tools, wire EDM, or machining for support removal during the post-processing planning stage.
Challenge 3: Achieving Desired Internal Surface Finish
- Cause: The as-printed surface roughness inside long, narrow, or convoluted internal airflow passages is difficult and costly to improve significantly using traditional polishing or blasting methods due to limited access.
- Mitigation Strategies:
- DfAM for Smoothness: Design internal channels with smooth, gradual curves and avoid sharp turns that exacerbate roughness effects and make post-processing harder. Optimize orientation for best internal surface quality.
- Specialized Post-Processing: Techniques like Abrasive Flow Machining (AFM), where a putty-like abrasive media is forced through the internal channels, can effectively polish internal surfaces but add cost and complexity.
- Accept As-Printed Finish: Often, the as-printed internal finish (Ra 8-25 µm) is perfectly acceptable from an airflow perspective, as the geometric design has a far greater impact on performance than minor surface roughness variations. Verify if ultra-smooth internal surfaces are truly necessary for the application.
- Parameter Optimization: Fine-tuning print parameters can sometimes yield slightly better internal surface finishes.
Challenge 4: Porosity Control
- Cause: Small voids or pores can form within the printed material due to trapped gas (from powder or atmosphere) or incomplete fusion between layers (Lack of Fusion – LoF). Excessive porosity can compromise mechanical properties and fatigue life.
- Mitigation Strategies:
- High-Quality Powder: Use metal powders with controlled particle size distribution, high sphericity, good flowability, and low internal gas content, such as those produced using Met3DP’s advanced gas atomization and PREP systems. Proper powder handling and storage are also vital.
- Optimized Process Parameters: Ensure correct energy density (laser/beam power, speed, hatch spacing) to achieve full melting and fusion between layers. Parameters must be tailored to the specific material and machine.
- Inert Atmosphere Control: Maintain a high-purity inert gas environment (Argon or Nitrogen) in the build chamber to minimize oxidation and gas pickup.
- Het isostatisk pressning (HIP): For critical applications requiring maximum density and fatigue strength, HIP post-processing uses high temperature and pressure to close internal pores. This adds significant cost but guarantees near 100% density.
Challenge 5: Dimensional Accuracy
- Cause: Cumulative effects of minor layer inconsistencies, thermal shrinkage, slight warping, or inaccurate machine calibration can lead to deviations from the target dimensions.
- Mitigation Strategies:
- Rigorous Machine Calibration: Ensure the 3D printer is regularly and accurately calibrated.
- Material Shrinkage Compensation: Apply appropriate scaling factors in the slicing software to account for material shrinkage during cooling.
- Robust Quality Control: Implement thorough dimensional inspection using calibrated tools (CMM, scanners) to verify compliance.
- Iterative Process Refinement: For challenging parts, initial prints may require adjustments to parameters or supports based on inspection feedback.
Successfully navigating these challenges requires a combination of good design practices, meticulous process control, appropriate post-processing, and often, the deep expertise of a dedicated metal AM supplier. Addressing these potential issues proactively minimizes delays, reduces costs, and ensures the final 3D printed air intake scoop performs as intended.
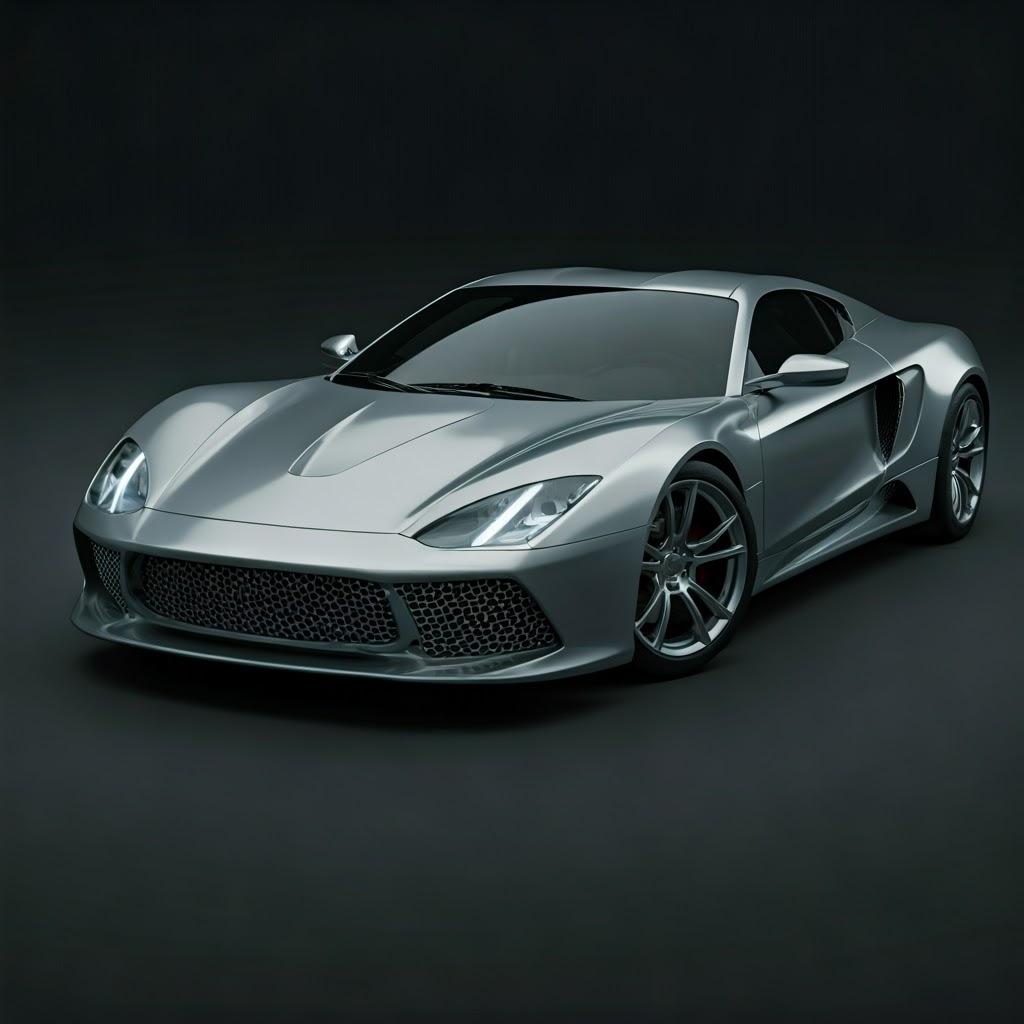
How to Choose the Right Metal 3D Printing Service Provider for Automotive Parts
Selecting the right manufacturing partner is as critical as the design and material selection for your custom air intake scoop project. The quality, performance, cost, and delivery time of your final components hinge on the capabilities and reliability of your chosen metal AM supplier. For demanding applications like performance automotive parts, thorough supplier qualification is essential. Engineers and procurement managers should evaluate potential providers based on a range of technical and operational criteria.
Here’s a checklist to guide your selection process:
- ✅ Technical Expertise & Application Experience:
- Does the provider have demonstrable experience printing with your chosen materials (e.g., AlSi10Mg, IN625)?
- Have they successfully produced similar components, such as automotive 3D printing services for ducting, manifolds, or other high-performance parts? Ask for relevant case studies or examples.
- Do they understand the specific challenges and requirements of the automotive/motorsports industry?
- ✅ Material Capabilities & Quality:
- Do they offer a suitable range of qualified metal powders? Can they provide material datasheets and certifications?
- What are their powder sourcing and quality control procedures? Companies like Met3DP, which manufacture their own high-quality powders using advanced techniques like gas atomization and PREP, offer greater control over material expertise and consistency.
- Is there traceability for powder batches used in your parts?
- ✅ Technology & Equipment:
- Do they operate the appropriate PBF technology (SLM, EBM) for your material and application? Met3DP, for instance, specializes in state-of-the-art systems, including SEBM printers known for excellent material properties.
- Is their equipment well-maintained and calibrated?
- Do they have sufficient build volume capacity for the size of your air scoop? Met3DP prides itself on industry-leading print volume capabilities.
- ✅ Quality Management System (QMS):
- Is the provider ISO 9001 Certified AM? This is a baseline requirement for industrial applications, indicating robust quality processes. AS9100 certification is a significant advantage for aerospace-grade quality.
- What are their standard inspection procedures? Can they accommodate specific NDT or advanced CMM requirements?
- ✅ Post-Processing Capabilities:
- Can they provide all necessary post-processing steps in-house (heat treatment, support removal, CNC machining, surface finishing)? Offering Turnkey Additive Manufacturing Solutions simplifies the supply chain and ensures accountability.
- Do they have expertise in the specific post-processing required for your chosen material and application?
- ✅ Engineering & DfAM Support:
- Does the provider offer design consultation or DfAM (Design for Additive Manufacturing) support to help optimize your part for printing? This collaboration can significantly improve outcomes. Met3DP offers comprehensive application development services.
- ✅ Capacity & Lead Time:
- Can they commit to realistic lead times for both prototypes and potential low-volume production runs?
- Are they transparent about their current capacity and potential bottlenecks?
- ✅ Cost Structure & Transparency:
- Is their quoting process clear, detailed, and easy to understand? Do they explain the key cost drivers?
- ✅ Customer Service & Communication:
- Are they responsive and communicative? Is there a dedicated point of contact for your project?
- ✅ Location & Logistics:
- Consider shipping costs and times. Met3DP, located in Qingdao, China, serves a global clientele with efficient logistics solutions.
By carefully evaluating potential partners against these criteria, you can select a provider like Met3DP that possesses the necessary expertise, technology, quality systems, and comprehensive capabilities to deliver high-performance 3D printed metal air intake scoops that meet your exact specifications.
Cost Factors and Lead Time for 3D Printed Metal Air Scoops
Understanding the factors that influence the cost and lead time of 3D printed metal parts is crucial for budgeting, project planning, and effective procurement. While metal AM offers significant advantages for custom and complex components like air intake scoops, it involves different cost structures and time considerations compared to traditional manufacturing. A thorough Metal 3D Printing Cost Analysis requires looking beyond just the material cost.
Key Cost Drivers:
- Material Type & Consumption:
- Kostnad för pulver: The price per kilogram varies significantly between alloys (e.g., IN625 is much more expensive than AlSi10Mg).
- Part Volume: The amount of material directly used in the part.
- Support Structure Volume: Material used for supports, which is later removed (waste or recycled at lower value). Efficient DfAM minimizes support needs.
- Maskintid:
- Print Duration: Primarily driven by the height of the part (number of layers) and the surface area scanned per layer. Taller parts take longer. Complex internal features can increase scan time per layer.
- Machine Operating Cost: High-value equipment has significant hourly operating rates (depreciation, energy, maintenance, inert gas).
- Build Preparation & Setup:
- File Preparation: Slicing the CAD model, defining orientation, generating supports.
- Machine Setup: Loading powder, preparing the build plate, initiating the print job. Setup costs are amortized over all parts in a single build – printing multiple parts simultaneously reduces the Price Per Part AM.
- Efterbearbetning:
- Labor & Machine Time: Each step (cleaning, support removal, heat treatment, machining, finishing) adds cost based on the time and resources required. Complex support removal or extensive CNC machining 3D Prints can significantly increase costs.
- Consumables: Abrasive media, cutting tools, furnace energy, etc.
- Arbete:
- Skilled labor is required for setup, operation, unpacking, powder handling, quality inspection, and manual post-processing tasks.
- Kvalitetssäkring:
- Basic inspection is standard, but more rigorous QA (e.g., CMM reports, NDT) adds cost.
- Quantity (Volume Production AM):
- While still suited for lower volumes, printing multiple copies in one build reduces the per-part cost by amortizing setup. Minor discounts might be available for larger batch orders, but economies of scale are less dramatic than in processes like injection molding.
Factors Influencing Lead Time:
- Print Time: As described above, primarily height-driven (can range from hours to several days for large/complex parts).
- Machine Availability: The service provider’s current job queue and machine capacity. Expedited options may be available at a premium.
- Post-Processing Complexity & Duration: Heat treatment cycles take hours (sometimes days including ramp-up/cool-down). Machining setup and runtime depend on complexity. Finishing steps add further time. Post-processing often defines the overall lead time.
- Kvantitet: Printing and processing larger batches naturally takes longer.
- Engineering Review & Iteration: If design adjustments are needed.
- Quality Control Steps: Time required for inspection and reporting.
- Frakt: Transit time from the provider’s facility (e.g., from Met3DP in Qingdao) to your location.
Typical Additive Manufacturing Lead Times:
While highly variable, typical timelines might look like this:
- Simple Prototypes (Minimal Post-Processing): 5-10 business days.
- Complex Parts (Extensive Post-Processing/Machining): 10-20+ business days.
- Low-Volume Production Batches: Weeks, depending on quantity and complexity.
Always obtain a specific quote with estimated lead times from your chosen provider based on your final design and requirements. Understanding these cost and time factors enables effective procurement AM parts strategies and realistic project planning. The various tryckmetoder and post-processing steps each contribute uniquely to the final schedule and budget.
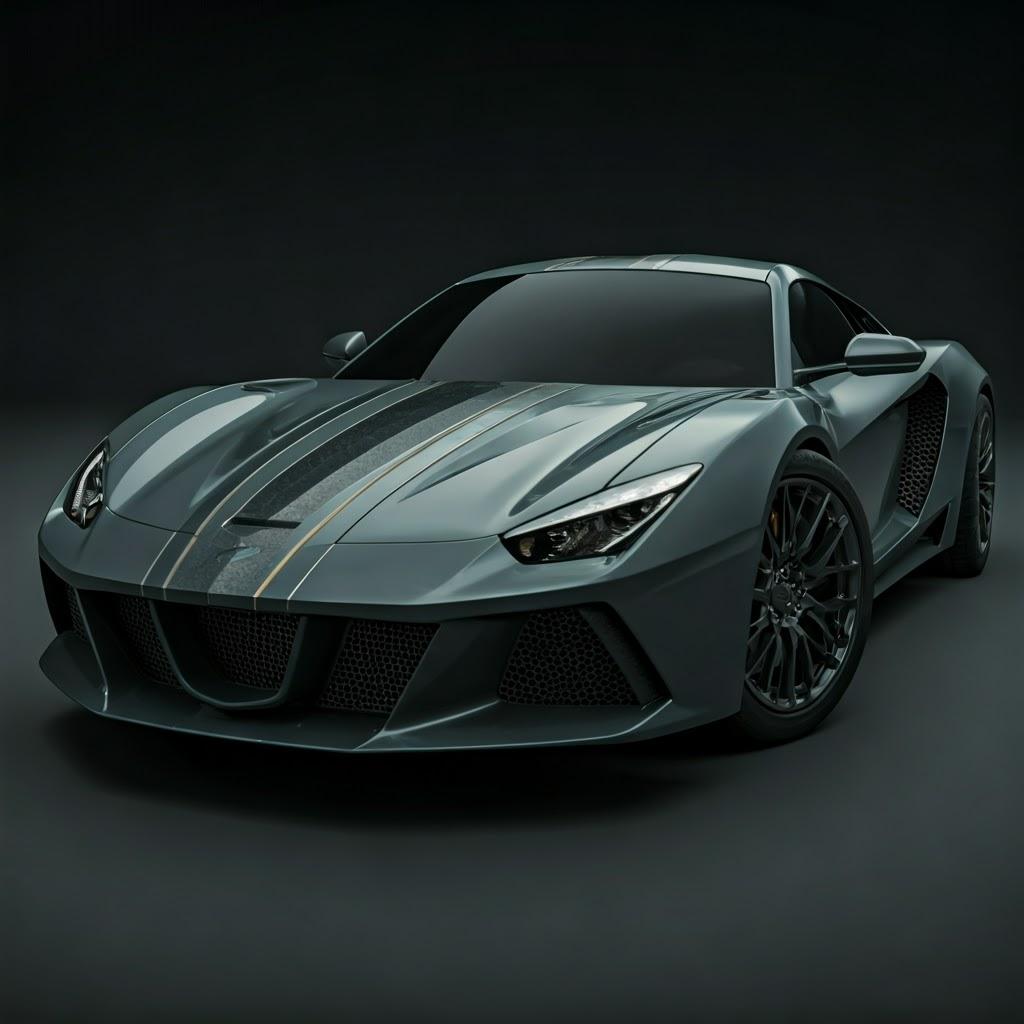
Frequently Asked Questions (FAQ) about 3D Printed Air Scoops
Here are answers to some common questions engineers and procurement managers have about using metal additive manufacturing for custom air intake scoops:
Q1: How does the strength of a 3D printed metal air scoop compare to one made traditionally (e.g., fiberglass or CNC aluminum)?
A: When designed correctly and manufactured using appropriate parameters and post-processing (especially heat treatment), the Metal Air Scoop Strength produced via AM using alloys like AlSi10Mg or IN625 can be excellent. Mechanical properties are often comparable to, and sometimes exceed, those of cast aluminum parts. Compared to CNC machined billet aluminum, the properties might be slightly different (e.g., potentially lower ductility depending on print orientation), but generally offer high strength suitable for demanding applications. Metal AM parts offer significantly higher AM Part Durability, impact resistance, and temperature tolerance compared to typical fiberglass or polymer-based scoops. IN625, in particular, offers exceptional strength even at very high temperatures.
Q2: What is the maximum size air scoop Met3DP can print?
A: Met3DP operates a range of industrial metal 3D printers, including systems with industry-leading build volumes designed for large-format components. The specific Maximum Print Size capability depends on the machine selected and the material being used. Generally, we can accommodate parts spanning several hundred millimeters in the X, Y, and Z dimensions (e.g., potentially up to 400mm x 400mm x 400mm or larger on certain platforms). We recommend contacting our technical team with your specific part dimensions and requirements so we can confirm feasibility on our available equipment.
Q3: Can you incorporate features like sensor mounts, internal dividers, or textured surfaces directly into the 3D printed scoop?
A: Absolutely. This capability is one of the primary advantages of using metal additive manufacturing. We can readily integrate complex Custom 3D Print Features directly into the scoop’s design, eliminating the need for secondary assembly or modification. This includes: * Threaded bosses or precisely located bores for MAP, IAT, or other sensors. * Complex internal vanes, dividers, or flow straighteners to manage airflow. * Integrated mounting flanges, brackets, or locating features. * Optimized surface textures (within the limits of the process) on internal or external faces if required for aerodynamic or aesthetic purposes. Designing these features into the initial CAD model allows for a more robust, lightweight, and functionally integrated final part.
Conclusion: Driving Performance Innovation with Met3DP’s Additive Manufacturing
The journey through the world of 3D printed metal air intake scoops reveals a powerful intersection of advanced materials science, sophisticated manufacturing technology, and innovative engineering design. Metal additive manufacturing has unequivocally moved beyond rapid prototyping to become a viable and often superior solution for producing Custom Performance Parts that drive tangible gains in automotive efficiency, power, and responsiveness. The ability to create complex geometries, optimize airflow with unprecedented freedom, lightweight components without sacrificing strength, and utilize high-performance alloys like AlSi10Mg and IN625 positions metal AM at the forefront of the Future of Automotive Manufacturing.
From initial concept optimization using DfAM principles to selecting the ideal high-performance metal powder, and navigating the intricacies of printing and post-processing, creating a successful metal AM air scoop requires expertise and precision at every stage. Addressing challenges like residual stress, support removal, and achieving critical tolerances demands capable technology and deep process knowledge.
Att välja rätt Metal AM Partnership is paramount. Met3DP stands as a leader in this field, offering comprehensive Met3DP Solutions that span the entire additive manufacturing value chain. Our strengths include:
- Advanced Equipment: Utilizing industry-leading printers, including specialized SEBM technology, for superior part quality and material properties.
- High-Quality Materials: In-house manufacturing of premium spherical metal powders (AlSi10Mg, IN625, Ti Alloys, CoCrMo, Stainless Steels, and more) using cutting-edge Gas Atomization and PREP systems. Learn more om oss.
- End-to-End Services: From DfAM consultation and application development to printing, rigorous quality control, and extensive post-processing capabilities.
- Decades of Expertise: A team with deep collective knowledge in metal additive manufacturing, ready to tackle complex challenges in aerospace, medical, automotive, and industrial sectors.
We partner with organizations globally to implement 3D printing effectively, accelerate their digital manufacturing transformations, and achieve next-generation performance. Whether you are developing a cutting-edge intake system for a race car, tuning a performance vehicle, or seeking innovative solutions for complex airflow management, Met3DP has the technology, materials, and expertise to bring your vision to life.
Ready to optimize your vehicle’s performance with a custom 3D printed metal air intake scoop?
Contact Met3DP today to discuss your project requirements, request a quote, or explore how our additive manufacturing capabilities can power your organization’s innovation goals.
Dela på
MET3DP Technology Co, LTD är en ledande leverantör av lösningar för additiv tillverkning med huvudkontor i Qingdao, Kina. Vårt företag är specialiserat på 3D-utskriftsutrustning och högpresterande metallpulver för industriella tillämpningar.
Förfrågan för att få bästa pris och anpassad lösning för ditt företag!
Relaterade artiklar
Om Met3DP
Senaste uppdateringen
Vår produkt
KONTAKTA OSS
Har du några frågor? Skicka oss meddelande nu! Vi kommer att betjäna din begäran med ett helt team efter att ha fått ditt meddelande.
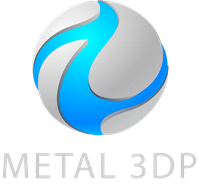
Metallpulver för 3D-printing och additiv tillverkning