Tillämpning av Binder Jetting inom flyg- och rymdindustrin
Innehållsförteckning
Föreställ dig att du tillverkar invecklade flygplanskomponenter med precisionen hos en 3D-skrivare, men med den styrka och hållbarhet som krävs av en oförlåtande himmel. Detta är verkligheten för Binder Jettingbinder Jetting är en additiv tillverkningsteknik som revolutionerar flyg- och rymdindustrin. Genom att strategiskt deponera ett flytande bindemedel på en bädd av metallpulver, lager för lager, bygger Binder Jetting komplexa, lätta strukturer som flyttar fram gränserna för vad som är möjligt inom flygplansdesign.
Enkel förståelse av Binder Jetting
Binder Jetting fungerar på samma sätt som en vanlig bläckstråleskrivare, men istället för bläck används ett bindemedel för att fästa metallpartiklar vid varandra. Processen börjar med en digital 3D-modell av den önskade komponenten. Modellen skärs sedan i tunna skikt som fungerar som en ritning för tryckprocessen. I Binder Jetting-maskinen lägger ett skrivhuvud selektivt bindemedlet på en bädd av fint metallpulver, och partiklarna fäster endast på bestämda områden baserat på den digitala skissen. När ett lager är färdigt sprids ett nytt lager pulver ut och bindningsprocessen upprepas. Detta fortsätter tills hela komponenten är byggd, lager för lager, från grunden.
Efter utskriftssteget avlägsnas det obundna pulvret och kvar blir den “gröna” delen. Denna del genomgår sedan en sintringsprocess, där den utsätts för höga temperaturer, vilket får metallpartiklarna att smälta samman, vilket resulterar i en robust och funktionell metallkomponent.
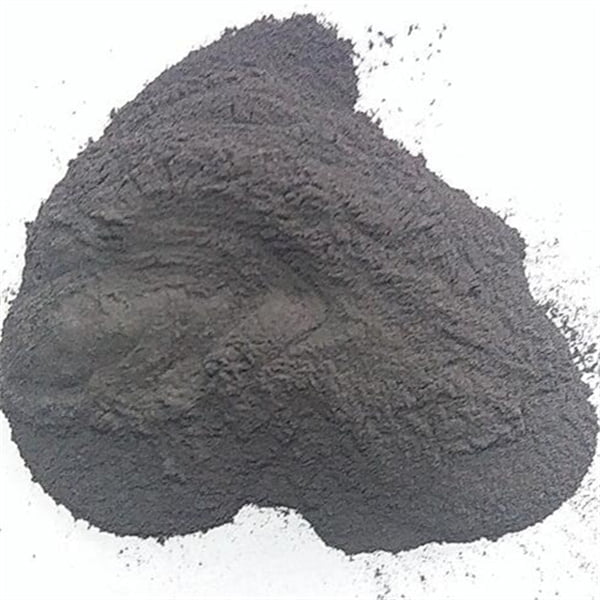
Binder Jetings 10 viktigaste metallpulver
Mångsidigheten hos Binder Jetting kommer till sin rätt genom dess kompatibilitet med ett brett utbud av metallpulver. Varje pulver har unika egenskaper som passar specifika flyg- och rymdtillämpningar. Här’r en närmare titt på 10 framstående metallpulver som flyger med Binder Jetting:
1. Rostfritt stål 316L: Rostfritt stål 316L är känt för sin utmärkta korrosionsbeständighet och goda mekaniska styrka och är ett populärt val för applikationer som interna flygplanskomponenter, kanaler och höljen som kräver motståndskraft mot tuffa miljöer.
2. Inconel 625: Denna högpresterande nickel-krom-superlegering har exceptionell hållfasthet vid förhöjda temperaturer, vilket gör den idealisk för komponenter i jetmotorers heta sektioner, t.ex. brännkammarfodringar och turbinblad. Inconel 625 kan motstå enorm värme och tryck, vilket säkerställer en smidig drift av motorn.
3. Titan 6Al-4V (Ti-6Al-4V): Ti-6Al-4V är en mästare på styrka/vikt-förhållande och erbjuder imponerande mekaniska egenskaper samtidigt som det är lätt. Denna kombination gör det perfekt för flyg- och rymdtillämpningar där viktreduktion är av största vikt, t.ex. komponenter till flygplansskrov, landningsställ och motorfästen.
4. Aluminiumlegeringar (AlSi10Mg, AlSi7Mg0,3): Aluminiumlegeringar som AlSi10Mg och AlSi7Mg0.3 erbjuder en blandning av prisvärdhet, god bearbetbarhet och anständig hållfasthet och är lämpliga för icke-kritiska flyg- och rymdtillämpningar där viktreduktion fortfarande är en prioritet. Dessa legeringar kan användas i höljen, konsoler och andra icke-bärande komponenter.
5. Nickellegering 718: Denna mångsidiga nickel-kromlegering har hög hållfasthet, god korrosionsbeständighet och utmärkt bearbetbarhet. Dessa egenskaper gör den till ett värdefullt material för olika delar inom flyg- och rymdindustrin, inklusive strukturella komponenter, komponenter till landningsställ och hydrauliska högtrycksslangar.
6. Koppar: Med sin enastående termiska och elektriska ledningsförmåga används koppar i värmeväxlare, radiatorer och elektriska komponenter i flygplan. Binder Jetting gör det möjligt att skapa intrikata kopparstrukturer som optimerar värmeöverföringsprestandan.
7. Kovar: Denna järn-nickel-koboltlegering har en värmeutvidgningskoefficient som ligger nära glasets. Denna unika egenskap gör Kovar idealisk för applikationer där tillförlitlig tätning mellan metall- och glaskomponenter är avgörande, t.ex. inom flygelektronik och instrumentdisplayer.
8. Invar 36: Invar 36 är känt för sin exceptionellt låga värmeutvidgningskoefficient och används i precisionskomponenter inom flyg- och rymdindustrin som kräver dimensionsstabilitet vid varierande temperaturer. Detta material är särskilt värdefullt för applikationer i optiska system och styrinstrument.
9. Tungstenskarbid: Volframkarbid är känd för sin exceptionella hårdhet och slitstyrka och är idealisk för komponenter som utsätts för hög friktion och nötning. Den kan användas i slitkuddar för landningsställ, skärverktyg och andra komponenter som kräver överlägsen slitstyrka.
10. Maråldrat stål: Maråldrat stål kombinerar hög hållfasthet med utmärkt seghet och är ett värdefullt material för flyg- och rymdtillämpningar som kräver exceptionella mekaniska egenskaper. Stålet kan användas i komponenter som utsätts för höga påfrestningar, t.ex. landningsställsfästen och kritiska strukturelement.
Binder Jetting‘s tillämpningar inom flyg- och rymdindustrin
Binder Jetting’:s förmåga att skapa komplexa geometrier med minimalt materialspill gör den till en "game-changer" för flygindustrin. Här’r en djupdykning i hur Binder Jetting förändrar olika aspekter av flygplansdesign och tillverkning:
Binder Jetting kan tillverka turbinblad:
Turbinblad, hjärtat i en jetmotor, tillverkas traditionellt med stor noggrannhet genom komplexa gjutnings- eller bearbetningsprocesser. Binder Jetting erbjuder ett smidigare och mer kostnadseffektivt alternativ. Tänk dig att skriva ut komplicerade kylkanaler direkt i bladdesignen, en bedrift som är utmanande med konventionella metoder. Detta möjliggör effektivare värmehantering, en kritisk faktor för att maximera motorns prestanda och bränsleeffektivitet.
Inconel 625, den superlegering som vanligtvis används för turbinblad, kan dock vara svår att bearbeta med Binder Jetting på grund av sin höga smältpunkt. Pågående forskning fokuserar på att utveckla förbättrade bindemedel och sintringstekniker för att frigöra den fulla potentialen hos Binder Jetting för denna krävande applikation.
Binder Jetting kan tillverka flygplansskrov:
Flygplanskroppen, som är huvuddelen av ett flygplan, handlar om att uppnå lättviktskonstruktion för optimal bränsleeffektivitet. Binder Jetting gör det möjligt att skapa lätta men ändå starka flygkroppsskal med intrikata gitterstrukturer. Dessa interna stödstrukturer efterliknar styrkan hos bikakestrukturer, vilket ger exceptionell styvhet utan att lägga till överdriven vikt. Dessutom kan Binder Jetting integrera interna kanaler i skrovet för kabeldragning och andra viktiga komponenter, vilket förenklar monteringen och minskar antalet delar som behövs.
Binder Jetting kan tillverka komponenter till landningsställ:
Landningsställen utsätts för enorma påfrestningar under start och landning. Binder Jetting ger möjlighet att tillverka komplexa landningsställskomponenter med hjälp av höghållfasta metallpulver som titan 6Al-4V eller nickellegering 718. Detta möjliggör viktreduktion samtidigt som den nödvändiga styrkan och hållbarheten bibehålls för att klara den tuffa driftsmiljön. Dessutom kan Binder Jetting skapa intrikata interna kanaler i landningsställskomponenter för att minska vikten ytterligare och optimera vätskeflödet för hydraulsystem.
Bortom exemplen: En bredare påverkan
Effekten av Binder Jetting inom flyg- och rymdindustrin sträcker sig bortom dessa specifika tillämpningar. Här’s en glimt av dess bredare inflytande:
- Snabb prototypframtagning och design-iteration: Binder Jetting möjliggör snabb prototyptillverkning av nya flygplanskomponenter. Detta möjliggör snabbare konstruktionscykler, vilket gör att ingenjörerna kan testa och förfina koncepten snabbt och effektivt.
- Kortare ledtider för tillverkning: Jämfört med traditionella tekniker ger Binder Jetting möjlighet till snabbare produktion av vissa komponenter. Detta kan avsevärt minska ledtiderna och effektivisera monteringsprocesserna för flygplan.
- Tillverkning på begäran: Binder Jetting’:s inneboende flexibilitet gör den lämplig för tillverkning av reservdelar på begäran. Detta kan vara särskilt fördelaktigt på avlägsna platser eller i situationer där det är opraktiskt att hålla ett stort lager av reservdelar.
- Viktminskning: Som tidigare nämnts är Binder Jetting utmärkt för att skapa lättviktsstrukturer. Detta innebär betydande bränslebesparingar för flygbolagen under ett flygplans livslängd, vilket bidrar till en mer hållbar framtid för flygresor.
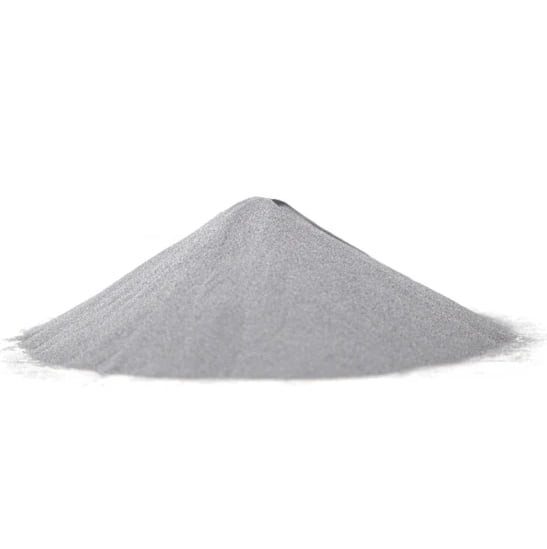
Utmaningar och överväganden
Medan Binder Jetting erbjuder en enorm potential för flygindustrin, men det är inte utan utmaningar. Här är några viktiga överväganden:
- Materialegenskaper: Medan Binder Jetting kan producera detaljer med goda mekaniska egenskaper, men de kan inte alltid mäta sig med komponenter som tillverkas med traditionella metoder som gjutning eller smide. Pågående forskning och utveckling förbättrar kontinuerligt egenskaperna hos Binder Jetted-detaljer, men det är fortfarande en ständig strävan att nå samma nivå som med traditionella metoder.
- Efterbearbetning: Binder Jetted-detaljer kräver ofta ytterligare efterbearbetningssteg som sintring, vilket kan öka den totala produktionstiden och -kostnaden.
- Ytfinish: Ytfinishen på Binder Jetted-detaljer kanske inte är lika jämn som på detaljer som tillverkas med traditionella metoder. Detta kan kräva ytterligare bearbetnings- eller efterbehandlingssteg, beroende på den specifika applikationen.
- Kvalitetskontroll: Att utveckla robusta rutiner för kvalitetskontroll är avgörande för att säkerställa konsekvent prestanda och tillförlitlighet hos Binder Jetted-komponenter i kritiska flyg- och rymdtillämpningar.
VANLIGA FRÅGOR
Fråga | Svar |
---|---|
Vilka metallpulver används vanligtvis med Binder Jetting inom flyg- och rymdindustrin? | En mängd olika metallpulver används, bland annat rostfritt stål 316L, Inconel 625, titan 6Al-4V, aluminiumlegeringar (AlSi10Mg, AlSi7Mg0,3), nickellegering 718, koppar, Kovar, Invar 36, volframkarbid och Maraging Steel. Varje pulver har unika egenskaper som lämpar sig för specifika applikationer. |
Är Binder Jetting ett bra alternativ till traditionella tillverkningsmetoder för alla komponenter inom flyg- och rymdindustrin? | Inte nödvändigtvis i det här skedet. Binder Jetting är utmärkt för att skapa komplexa lättviktsstrukturer och snabba prototyper. För komponenter som kräver de absolut högsta mekaniska egenskaperna eller mycket jämn ytfinish kan dock traditionella metoder som smide eller maskinbearbetning fortfarande vara att föredra. |
Hur kan flygindustrin säkerställa kvaliteten och tillförlitligheten hos Binder Jetted-komponenter? | Det är viktigt att införa robusta rutiner för kvalitetskontroll genom hela processen. Detta omfattar stränga kontroller av metallpulvrets kvalitet, övervakning av tryckparametrar och noggranna inspektioner efter bearbetningen. |
Vilka är några av de pågående framstegen inom Binder Jetting-tekniken som kan påverka flyg- och rymdindustrin? | Forskning pågår för att utveckla förbättrade bindemedel och sintringstekniker. Dessa framsteg kan göra det möjligt för Binder Jetting att uppnå ännu högre materialegenskaper och potentiellt ta itu med några av de nuvarande begränsningarna, vilket gör det lämpligt för ett bredare spektrum av kritiska flyg- och rymdtillämpningar. |
Hur kan Binder Jetting jämföras med andra 3D-utskriftstekniker som används inom flygindustrin, t.ex. Selective Laser Melting (SLM)? | Både Binder Jetting och SLM är additiva tillverkningstekniker, men de skiljer sig åt i sitt tillvägagångssätt. SLM använder en laser för att smälta metallpulver lager för lager, vilket resulterar i delar med mycket höga mekaniska egenskaper. SLM kan dock vara långsammare och dyrare jämfört med Binder Jetting. Binder Jetting, å andra sidan, erbjuder snabbare bygghastigheter och potentiellt lägre kostnader, men de mekaniska egenskaperna kanske inte alltid matchar SLM-delarnas. Valet mellan dessa tekniker beror på de specifika applikationskraven. |
Dela på
MET3DP Technology Co, LTD är en ledande leverantör av lösningar för additiv tillverkning med huvudkontor i Qingdao, Kina. Vårt företag är specialiserat på 3D-utskriftsutrustning och högpresterande metallpulver för industriella tillämpningar.
Förfrågan för att få bästa pris och anpassad lösning för ditt företag!
Relaterade artiklar
Om Met3DP
Senaste uppdateringen
Vår produkt
KONTAKTA OSS
Har du några frågor? Skicka oss meddelande nu! Vi kommer att betjäna din begäran med ett helt team efter att ha fått ditt meddelande.
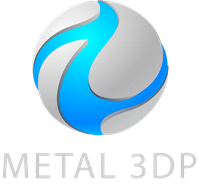
Metallpulver för 3D-printing och additiv tillverkning