Detaljerad analys av EBM:s processflöde
Innehållsförteckning
Smältning med elektronstråle (EBM) är en revolutionerande 3D-utskriftsteknik som snabbt håller på att förändra tillverkningslandskapet. Tänk dig att bygga komplexa metalldelar lager för lager med hjälp av en fokuserad elektronstråle - det är själva kärnan i EBM! Men har du någonsin undrat vad som händer bakom kulisserna i denna högteknologiska process? Spänn fast dig, för nu ska vi göra en detaljerad analys av EBM-processens flöde och dissekera varje steg för att avslöja dess magi.
Förberedande arbete för EBM Processflöde
Innan elektronstrålen börjar sin dans måste en del viktigt grundarbete läggas. Här’är vad som sätter scenen:
- CAD-design: Allt börjar med en digital ritning. Din 3D-modell, som är noggrant utformad med CAD-programvara, fungerar som en ritning som EBM-maskinen följer.
- Val av metallpulver: Hjärtat i EBM ligger i det metallpulver som används. Dessa fina metallpartiklar (vanligtvis mellan 20 och 100 mikrometer) finns i olika varianter, var och en med unika egenskaper. Vi ska strax gå djupare in i metallpulvrets fascinerande värld.
- Maskininställning och kalibrering: EBM-maskinen i sig är ett tekniskt underverk. Den innehåller en högeffektiv elektronkanon, en vakuumkammare för att upprätthålla en ren miljö och en byggplattform som sänks noggrant för varje lager. Kalibreringen säkerställer att elektronstrålen träffar pulverbädden med exakt precision, vilket är ett avgörande steg för att uppnå dimensionell precision.
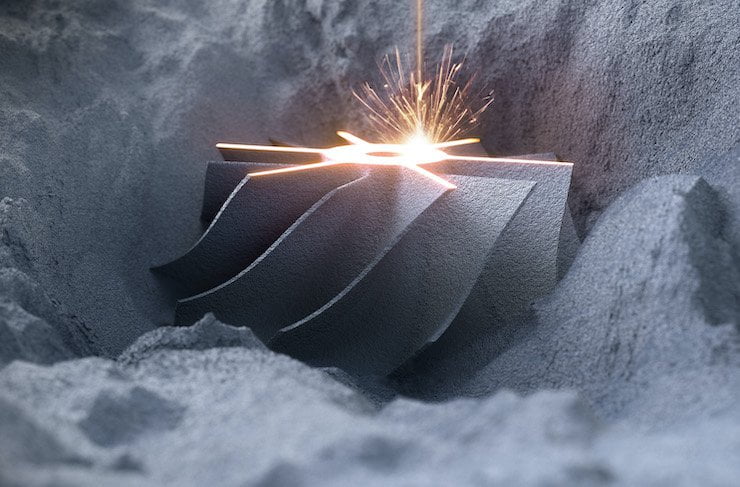
Val av metallpulver: Ett kraftverk för pulver
Som tidigare nämnts är metallpulver själva livsnerven i EBM. Här’r en närmare titt på några av de mest populära alternativen, tillsammans med deras viktigaste egenskaper:
Metallpulver | Sammansättning | Fastigheter | Tillämpningar |
---|---|---|---|
Ti-6Al-4V (titanlegering) | 6% aluminium, 4% vanadin, titan Balans | Högt förhållande mellan styrka och vikt, utmärkt biokompatibilitet | Komponenter för flyg- och rymdindustrin, biomedicinska implantat, proteser |
Rostfritt stål 316L | Krom, nickel, molybden, järn Balans | Korrosionsbeständighet, goda mekaniska egenskaper | Medicinska apparater, kemisk bearbetningsutrustning, marina komponenter |
Inconel 625 (superlegering) | Nickel, krom, molybden, columbium, järn Balans | Hållfasthet vid höga temperaturer, oxidationsbeständighet | Komponenter till gasturbiner, delar till raketmotorer, värmeväxlare |
CoCrMo (legering av kobolt-krom-molybden) | Kobolt, krom, molybden | Biokompatibel, slitstark | Ledproteser, tandimplantat |
Aluminiumlegeringar (AlSi10Mg, etc.) | Aluminium med kisel, magnesium | Lätt vikt, god hållfasthet | Bilkomponenter, romfartsstrukturer, varmesluk |
Koppar | Ren koppar | Hög värmeledningsförmåga, bra elektrisk ledningsförmåga | Värmeväxlare, elektriska komponenter, vågledare |
Volfram | Ren volfram | Hög smältpunkt, hög densitet | Gjutverktyg, elektroder, ballistiska tillämpningar |
Maråldrat stål | Nickel, molybden, titan, järn Balans | Hög hållfasthet, bra duktilitet | Komponenter för flyg- och rymdindustrin, delar till skjutvapen, verktyg |
Superlegeringar av nickel (Inconel 718 etc.) | Komplexa sammansättningar med nickel, krom, molybden | Exceptionell prestanda vid höga temperaturer | Turbinblad, delar till raketmotorer, värmeväxlare |
Titanlegeringar (CP Ti, etc.) | Kommersiellt ren titan | Utmärkt biokompatibilitet, god korrosionsbeständighet | Medicinska implantat, dentaltillämpningar, utrustning för kemisk bearbetning |
Den här listan är bara en liten inblick i det stora utbudet av metallpulver som finns tillgängliga för EBM. Valet av pulver beror på de önskade egenskaperna hos den slutliga delen, t.ex. styrka, vikt, korrosionsbeständighet, biokompatibilitet och värmeledningsförmåga.
Elektronstrålescanning av EBM Processflöde
Nu kommer det magiska! Elektronkanonen i EBM-maskinen brummar till liv och genererar en mycket fokuserad elektronstråle. Denna stråle fungerar som en virtuell pensel och smälter selektivt metallpulvret enligt den förprogrammerade CAD-designen. Här’s en uppdelning av skanningsprocessen:
- Avböjningssystem: Elektronstrålen är’inte en stel linje. Ett sofistikerat avböjningssystem styr dess rörelse och riktar den över pulverbädden för att exakt definiera det önskade mönstret för varje lager.
- Skanna strategier: Det finns olika skanningsstrategier som används i EBM, var och en med sina fördelar. Vanliga strategier är rasterscanning, vektorscanning och ö-scanning. Valet av strategi beror på faktorer som detaljgeometri, krav på ytfinhet och värmehantering.
- Kontroll av strålens effekt: Elektronstrålens effekt spelar en avgörande roll. Högre effekt resulterar i djupare smältning och potentiellt snabbare byggtider. Det krävs dock noggrann kontroll för att förhindra överhettning och distorsion av detaljen. Föreställ dig att du balanserar en glödhet pensel på en bädd av metallpulver - det är EBM:s känsliga dans!
-
Ti45Nb-pulver för additiv tillverkning
-
Pulver av TiNb-legering
-
Pulver av TiNbZrSn-legering
-
Ti6Al4V Pulver Titanbaserat metallpulver för additiv tillverkning
-
CPTi Pulver
-
TC18 Pulver : Frigör kraften hos titankarbid
-
TC11 Pulver : En omfattande guide
-
TC4 ELI Pulver
-
Bästa Ti-6Al-4V-pulver (TC4-pulver) för additiv tillverkning
Lager för lager-tillverkning av EBM Processflöde
EBM bygger delar på ett verkligt additivt sätt, ett lager i taget. Här’är hur denna lager-för-lager-magi utvecklas:
- Recoat Blade: Efter att varje lager har skannats av elektronstrålen sprider en recoat-klinga noggrant ut ett nytt lager metallpulver över byggplattformen. Detta säkerställer en kontinuerlig tillförsel av material för nästa lager som ska smältas.
- Termisk hantering: EBM innebär lokaliserad smältning, men värmen är inte begränsad. Maskinen använder olika tekniker, som förvärmning av byggplattformen och användning av stödstrukturer, för att hantera termiska gradienter och förhindra skevhet eller sprickbildning i detaljen.
- Skiktets tjocklek: Tjockleken på varje skikt i EBM kan variera beroende på önskad upplösning och byggtid. Typiska skikttjocklekar varierar från 30 till 100 mikrometer, vilket ger en balans mellan detaljrikedom och effektivitet.
Föreställ dig att du bygger en komplex struktur tegelsten för tegelsten, men istället för tegelstenar använder du lager av smält metall - det är kärnan i EBM:s tillverkningsprocess lager för lager. Detta tillvägagångssätt gör det möjligt att skapa intrikata geometrier och interna funktioner som skulle vara omöjliga med traditionella subtraktiva tekniker som maskinbearbetning.
Efterbehandling av EBM Processflöde
Resan tar inte slut efter att det sista lagret har smält. Här’är vad som följer:
- Stressavlastning: EBM-detaljer kan uppleva restspänningar på grund av de termiska cykler som ingår i processen. Avspänningsglödgning hjälper till att minska dessa spänningar, vilket förbättrar detaljens dimensionsstabilitet och mekaniska egenskaper.
- Borttagning av stödstruktur: På samma sätt som man tar bort byggnadsställningar från en byggnad måste stödstrukturer som används under EBM-processen tas bort. Detta kan göras med olika metoder, t.ex. trådgnistning eller mekanisk kapning.
- Ytbehandling: EBM-ytor kan vara något grova på grund av processens natur. Efterbearbetningstekniker som maskinbearbetning, polering eller blästring kan användas för att uppnå önskad ytfinish.
Tänk på efterbearbetning som den sista handen på ditt mästerverk. Dessa steg säkerställer att EBM-delen uppfyller kraven på måttnoggrannhet, mekaniska egenskaper och ytestetik.
Fördelar och begränsningar med EBM
EBM har flera övertygande fördelar:
- Designfrihet: EBM är utmärkt för att skapa komplexa geometrier, inklusive interna funktioner och gitterstrukturer, som är svåra eller omöjliga med traditionella metoder.
- Högpresterande material: Processen är kompatibel med ett brett utbud av högpresterande metallpulver, vilket gör det möjligt att skapa delar med exceptionell styrka, värmebeständighet och biokompatibilitet.
- Tillverkning i nära-nätform: EBM minimerar materialspillet jämfört med subtraktiva tekniker, vilket ger en mer hållbar och kostnadseffektiv metod för vissa applikationer.
EBM har dock också begränsningar som måste beaktas:
- Byggtid: EBM kan vara en långsammare process jämfört med vissa andra 3D-utskriftsmetoder, särskilt för större delar.
- Ytjämnhet: EBM-ytorna kan vara något skrovliga, vilket kräver ytterligare efterbearbetning för vissa applikationer.
- Kostnad: EBM-maskiner och metallpulver kan vara dyra, vilket gör processen mer lämplig för högvärdiga delar eller applikationer där dess unika egenskaper är avgörande.
EBM är ett kraftfullt verktyg, men som alla verktyg är det bäst lämpat för specifika jobb. Genom att förstå dess styrkor och svagheter kan du fatta välgrundade beslut om dess lämplighet för ditt projekt.
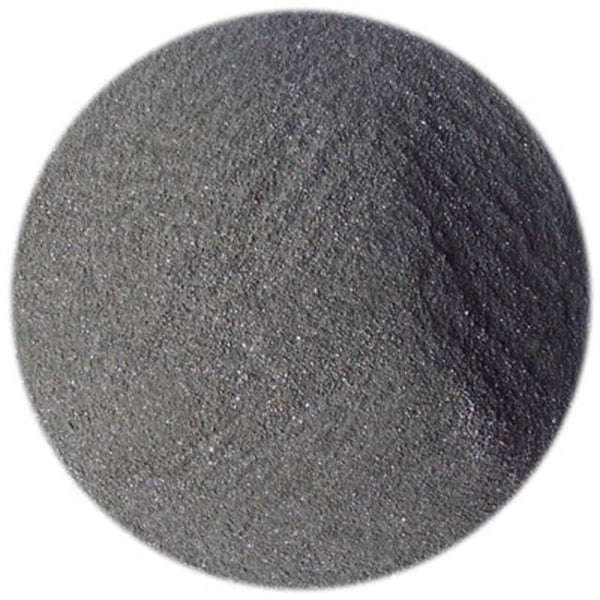
VANLIGA FRÅGOR
Här följer några vanliga frågor om EBM processflöde, besvaras i ett klart och koncist format:
Fråga | Svar |
---|---|
Vilka är fördelarna med EBM jämfört med andra 3D-utskriftsmetoder? | EBM ger överlägsen designfrihet, möjliggör användning av högpresterande metallpulver och minimerar materialspillet jämfört med vissa subtraktiva tekniker. |
Vilka är några av begränsningarna med EBM? | EBM kan vara långsammare än andra metoder, kan kräva efterbearbetning för ytfinish och kan vara dyrare på grund av maskin- och materialkostnader. |
Vilka typer av metallpulver kan användas i EBM? | Ett brett spektrum av metallpulver kan användas, inklusive titanlegeringar, rostfritt stål, superlegeringar, kobolt-krom, aluminiumlegeringar med mera. |
Vilka är några tillämpningar av EBM? | EBM används i olika branscher, bland annat inom flyg- och rymdindustrin, biomedicin, fordonsindustrin och energisektorn, för att skapa högpresterande metalldelar. |
Hur skannar elektronstrålen pulverbädden? | Ett sofistikerat avböjningssystem styr elektronstrålen och riktar den över pulverbädden för att definiera det önskade mönstret för varje skikt. |
Slutsats
Electron Beam Melting (EBM) är mer än bara en 3D-utskriftsteknik; det är en port till en värld av möjligheter. Genom att noggrant smälta metallpulver lager för lager gör EBM det möjligt att skapa komplexa, högpresterande delar som man tidigare trodde var omöjliga. Från invecklade flygkomponenter till livräddande biomedicinska implantat - EBM flyttar fram gränserna för design och tillverkning.
Som med all komplex teknik är det avgörande att förstå EBM-processflödet. Vi har fördjupat oss i varje steg, från det minutiösa förberedelsearbetet till den magiska processen lager för lager och efterbearbetningens sista detaljer. Med den här kunskapen kan du fatta välgrundade beslut om huruvida EBM är rätt verktyg för ditt projekt.
Dela på
MET3DP Technology Co, LTD är en ledande leverantör av lösningar för additiv tillverkning med huvudkontor i Qingdao, Kina. Vårt företag är specialiserat på 3D-utskriftsutrustning och högpresterande metallpulver för industriella tillämpningar.
Förfrågan för att få bästa pris och anpassad lösning för ditt företag!
Relaterade artiklar
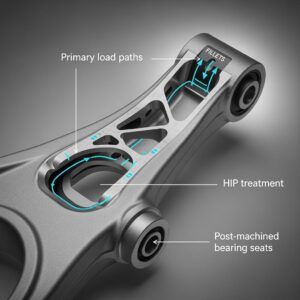
Metal 3D Printing for U.S. Automotive Lightweight Structural Brackets and Suspension Components
Läs mer "Om Met3DP
Senaste uppdateringen
Vår produkt
KONTAKTA OSS
Har du några frågor? Skicka oss meddelande nu! Vi kommer att betjäna din begäran med ett helt team efter att ha fått ditt meddelande.