Skillnaden mellan EBM-teknik och DMLS-teknik
Innehållsförteckning
Tänk dig att bygga komplexa metallföremål lager för lager, där varje lager omsorgsfullt smälts samman för att skapa ett färdigt tredimensionellt mästerverk. Det här är inte science fiction; det är magin med additiv tillverkning av metall, även känd som 3D-printing. Men inom denna skapelsevärld finns två titaner: Elektronstrålesmältning (EBM) och direkt metallsintering (DMLS). Båda använder metallpulver för att ge liv åt digital design, men de skiljer sig åt i sitt tillvägagångssätt, ungefär som två skickliga konstnärer som använder olika verktyg. Låt oss dyka in i den invecklade dansen med dessa tekniker, utforska deras nyanser och identifiera det perfekta valet för ditt nästa projekt.
Olika energikällor
EBM utnyttjar kraften i en fokuserad elektronstråle, som fungerar som en partikelaccelerator i miniatyr. Denna högenergistråle smälter metallpulverpartiklar i en högvakuumkammare och skapar en smält pool som smälter samman med omgivande lager. Tänk på det som en liten, superladdad pensel som noggrant smälter metallpulver för att bygga din design.
Å andra sidan.., DMLS använder en kraftfull fiberlaser som värmekälla. Laserstrålen sveper över metallpulverbädden och smälter partiklarna selektivt så att de får önskad geometri. Tänk dig att du använder en laserskärare på en plåt med metallpulver, men med otrolig precision och bygger upp objektet lager för lager.
Här är en tabell som sammanfattar de viktigaste skillnaderna i energikällor:
Funktion | Smältning med elektronstråle (EBM) | Direkt metallsintring med laser (DMLS) |
---|---|---|
Energikälla | Elektronstråle | Högpresterande fiberlaser |
Miljö | Högvakuumkammare | Atmosfär med inert gas |
Vad innebär denna skillnad? Högvakuummiljön i EBM minimerar oxidationen, vilket gör den idealisk för reaktiva metaller som titan och tantal. Omvänt använder DMLS en atmosfär med inert gas, vilket ger ett bredare utbud av metallpulverkompatibilitet.
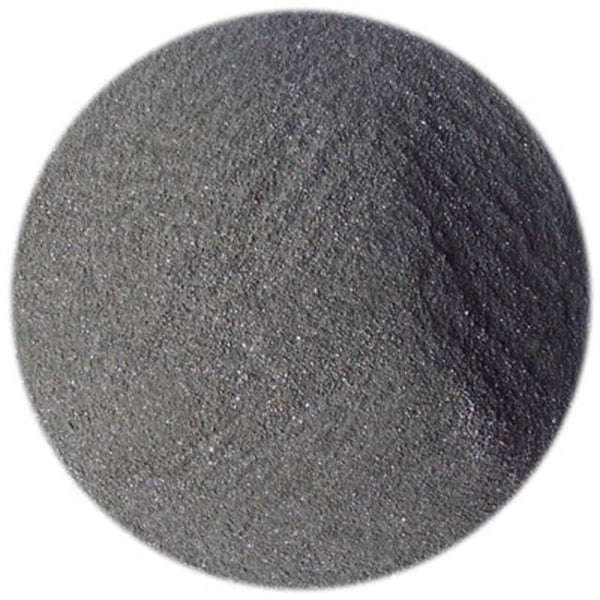
Två produkter har olika formningshastighet
EBM har imponerande formningshastigheter tack vare den högfokuserade och kraftfulla elektronstrålen. Detta innebär snabbare byggtider, särskilt för större komponenter. Föreställ dig en skicklig konstnär som arbetar snabbt med ett kraftfullt verktyg och färdigställer konstverket på kortare tid.
DMLSär visserligen långsammare än EBM, men erbjuder mer exakt kontroll över laserstrålen. Detta gör det möjligt att skapa invecklade funktioner och finare detaljer. Tänk dig en tålmodig konstnär som noggrant ristar ut invecklade detaljer med ett laserskarpt verktyg.
Här är en tabell som sammanfattar de viktigaste skillnaderna i formningshastighet:
Funktion | Smältning med elektronstråle (EBM) | Direkt metallsintring med laser (DMLS) |
---|---|---|
Formningshastighet | Snabbare | Långsammare |
Detalj Noggrannhet | Lägre | Högre |
Vad kan man ta med sig? Om hastighet är din prioritet, EBM kan vara det bättre valet. Men om invecklade detaljer och hög precision är av yttersta vikt kan DMLS vara rätt väg att gå.
Formningsnoggrannheten är annorlunda
Som nämnts tidigare, DMLS utmärker sig i formningsnoggrannhet tack vare den exakta kontrollen över laserstrålen. Detta gör det möjligt att skapa delar med finare funktioner och snävare toleranser. Tänk dig en mästerlig juvelerare som minutiöst tillverkar ett känsligt smycke med exakt precision.
EBMkan, även om den inte är lika exakt som DMLS, fortfarande producera detaljer med god måttnoggrannhet. På grund av elektronstrålesmältningsprocessens natur tenderar dock skikttjockleken att vara något tjockare jämfört med DMLS. Tänk på en skicklig skulptör som arbetar med något större verktyg, vilket resulterar i en något mindre exakt slutprodukt jämfört med en känslig juvelerare.
Här är en tabell som sammanfattar de viktigaste skillnaderna i formningsnoggrannhet:
Funktion | Smältning med elektronstråle (EBM) | Direkt metallsintring med laser (DMLS) |
---|---|---|
Formningsnoggrannhet | Bra | Utmärkt |
Skiktets tjocklek | Något tjockare | Tunnare |
Slutsatsen? Om måttnoggrannhet och invecklade detaljer är avgörande sticker DMLS ut. EBM erbjuder dock tillräcklig noggrannhet för många applikationer, särskilt de som prioriterar hastighet framför extrem precision.
Material som används av EBM Och DMLS är annorlunda
Båda teknikerna använder metallpulver, men de specifika material som är kompatibla med respektive system skiljer sig något åt.
EBM utmärker sig vid bearbetning av reaktiva metaller som:
- Titan (Ti): En lätt och stark metall som ofta används inom flyg- och rymdindustrin, medicinska implantat och högpresterande komponenter.
- Tantalum (Ta): En biokompatibel och korrosionsbeständig metall som används i medicinska implantat och utrustning för kemisk bearbetning.
- Zirkonium (Zr): En korrosionsbeständig metall som används i kärnreaktorer och utrustning för kemisk bearbetning.
DMLS erbjuder ett bredare utbud av kompatibla material, inklusive:
Specifikationer, storlekar, kvaliteter och standarder
Vi övergår från en samtalston till ett mer professionellt tillvägagångssätt och fördjupar oss i den kritiska världen av metallpulver som används i både EBM och DMLS. Dessa finkorniga material fungerar som byggstenar för 3D-printade metallkomponenter, och deras egenskaper påverkar i hög grad detaljens slutliga egenskaper. Till skillnad från dess roll vid bakning av en kaka, där mindre variationer i mjöl kan påverka texturen, kan även små inkonsekvenser i metallpulver dramatiskt påverka styrkan, ytfinishen och den övergripande kvaliteten på det utskrivna objektet. Här är en omfattande tabell som beskriver viktiga specifikationer, storlekar, kvaliteter och standarder för metallpulver som används vid additiv tillverkning:
Funktion | Beskrivning |
---|---|
Fördelning av partikelstorlek | Metallpulver tillverkas noggrant för att uppnå specifika partikelstorleksfördelningar, vanligtvis i intervallet 15-100 mikrometer. Tänk dig en exakt kalibrerad sikt; den valda partikelstorleken korrelerar direkt med den uppnåeliga ytfinishen på den tryckta delen. Finare pulver, som liknar siktat mjöl, ger jämnare ytor. Det finns dock en viktig avvägning. Pulver som är alltför fina kan ha sämre flytbarhet, vilket hindrar en jämn fördelning under tryckprocessen. Detta kan leda till inkonsekvenser och defekter i slutprodukten. Omvänt kan grövre pulver flyta lättare, men kan resultera i en grövre ytfinish och potentiell porositet (små luftspalter) i den tryckta komponenten. För att välja den optimala partikelstorleksfördelningen måste man noga överväga den specifika applikationen och det önskade resultatet. |
Partikelmorfologi | Pulverpartiklarnas form spelar en avgörande roll för packningstäthet och flytbarhet. Sfäriska partiklar, som liknar mikroskopiska kullager, är generellt att föredra för optimal tryckprestanda. De har överlägsna flödesegenskaper, packas tätt och minimerar hålrummen i pulverbädden. Detta leder till bättre måttnoggrannhet, förbättrade mekaniska egenskaper och en jämnare ytfinish på den tryckta detaljen. Att producera perfekt sfäriska metallpulver kan dock vara utmanande och dyrt. Liksidiga partiklar, även om de inte är perfekta sfärer, ger en bra balans mellan flytbarhet och packningsdensitet. Oregelbundet formade partiklar kan vara problematiska. De kan flöda dåligt, skapa luckor i pulverbädden och ha en negativ inverkan på slutproduktens strukturella integritet. |
Pulverkemi | Den exakta sammansättningen av pulvret, inklusive spårämnen och legeringstillsatser, påverkar avsevärt de slutliga egenskaperna hos den tryckta delen. Precis som de exakta ingredienserna i en läkemedelsformulering avgör dess effekt, bestämmer metallpulvrets kemiska sammansättning den tryckta komponentens egenskaper. Till exempel kan titanpulver för flyg- och rymdtillämpningar ha något annorlunda nivåer av syre och kväve jämfört med titanpulver av medicinsk kvalitet för implantat. Dessa till synes små variationer kan påverka faktorer som styrka, korrosionsbeständighet, biokompatibilitet och den tryckta delens övergripande prestanda. Tillverkare av metallpulver använder rigorösa kvalitetskontrollåtgärder för att säkerställa att deras pulver uppfyller specifika branschstandarder och applikationskrav. |
Flödesförmåga för pulver | Pulvrets förmåga att flöda fritt är avgörande för en jämn fördelning under tryckprocessen. Tänk dig att du häller sand i ett timglas; det ska flyta jämnt och konsekvent. God flytbarhet gör det möjligt att bilda en enhetlig pulverbädd, ett kritiskt steg i både EBM och DMLS. Pulver med dålig flödesförmåga kan orsaka ojämn deponering, vilket leder till inkonsekvenser och defekter i den slutliga tryckta delen. Tillverkarna mäter flödesförmågan med hjälp av standardiserade tester för att säkerställa att deras pulver uppfyller de specifika kraven för varje tryckteknik. |
Pulverets renhet | Metallpulvrets renhet påverkar direkt de mekaniska egenskaperna och prestandan hos den tryckta delen. Föroreningar som syre, kväve och andra element kan hindra bindningsprocessen mellan metallpartiklarna under tryckningen. Detta kan resultera i svagare delar med ökad känslighet för sprickor och frakturer. Tillverkare av metallpulver använder strikta kvalitetskontrollåtgärder för att minimera föroreningar och se till att deras pulver uppfyller de renhetsstandarder som krävs för olika applikationer. |
Branschstandarder för metallpulver i additiv tillverkning:
Flera etablerade industristandarder styr specifikationerna och kvaliteten på metallpulver för additiv tillverkning:
- ASTM International (ASTM): En globalt erkänd organisation som utvecklar och publicerar tekniska standarder för ett brett spektrum av material, inklusive metallpulver för AM. ASTM-standarderna definierar krav på partikelstorleksfördelning, kemisk sammansättning, flytbarhet och andra kritiska parametrar.
- American Society for Materials and Testing (AMSTM): En USA-baserad förening som arbetar för att främja testning, materialvetenskap och teknik som additiv tillverkning. AMSTM utvecklar specifikationer och standarder för metallpulver som används i AM-processer.
- EOS GmbH: En ledande tillverkare av 3D-utskriftssystem för metall. EOS publicerar också applikationsspecifika materialdatablad för olika metallpulver, som beskriver deras egenskaper och rekommenderade utskriftsparametrar.
- Materialtillverkare: Välrenommerade leverantörer av metallpulver tillhandahåller ofta detaljerade datablad för sina produkter, inklusive partikelstorleksfördelning, kemisk sammansättning, flytbarhet och andra relevanta specifikationer.
En värld av metallpulver: Avslöjande av specifika exempel
Nu när vi har utforskat de viktigaste egenskaperna hos metallpulver för additiv tillverkning, låt oss fördjupa oss i några specifika exempel som vanligtvis används i både EBM och DMLS. Detta kommer att ge ett praktiskt perspektiv på de tillgängliga alternativen och deras lämplighet för olika applikationer.
Metallpulver för EBM:
På grund av högvakuummiljön i EBM-kammaren måste de valda metallpulvren uppvisa exceptionella avgasningsegenskaper. Med avgasning menas att gaser som fångats upp i pulverpartiklarna frigörs under smältprocessen. Överdriven avgasning kan störa vakuummiljön och negativt påverka kvaliteten på den tryckta delen. Här är några vanligt förekommande metallpulver för EBM:
- Gasatomerat titanpulver (Ti-6Al-4V): Detta arbetshästmaterial är en titanlegering som innehåller 6% aluminium och 4% vanadin. Den erbjuder en utmärkt kombination av styrka, viktbesparing och korrosionsbeständighet. Används ofta inom flygindustrin, medicinska implantat och högpresterande bilkomponenter tack vare sin biokompatibilitet och gynnsamma mekaniska egenskaper när det bearbetas via EBM.
- Gasatomerad Inconel 718: Denna nickel-krombaserade superlegering har exceptionell hållfasthet vid höga temperaturer och motståndskraft mot tuffa miljöer. Dess förmåga att motstå extrema temperaturer gör den idealisk för applikationer i gasturbinmotorer, värmeväxlare och andra komponenter som utsätts för höga värmebelastningar. EBM-bearbetning ger minimal risk för kontaminering och bevarar de önskvärda egenskaperna hos Inconel 718.
- Gasatomerad koppar (Cu): Rent kopparpulver används i applikationer som kräver hög termisk och elektrisk ledningsförmåga. EBM gör det möjligt att skapa komplicerade kylflänsar och elektriska komponenter med minimal oxidation på grund av vakuummiljön.
Metallpulver för DMLS:
DMLS erbjuder en bredare materialkompatibilitet jämfört med EBM på grund av atmosfären med inert gas. Här är några vanligt förekommande metallpulver för DMLS:
- Gasatomerat rostfritt stål 316L: Denna mångsidiga rostfria stålsort erbjuder utmärkt korrosionsbeständighet och biokompatibilitet. Används ofta i medicinska implantat, kemisk processutrustning och applikationer som kräver motståndskraft mot tuffa miljöer. DMLS-bearbetning gör det möjligt att skapa komplicerade geometrier med goda mekaniska egenskaper.
- Gasatomerade aluminiumlegeringar (AlSi10Mg, etc.): Aluminiumlegeringar erbjuder en bra balans mellan styrka, viktbesparing och prisvärdhet. Tillsats av kisel (Si) och magnesium (Mg) förbättrar gjutningsegenskaperna och de mekaniska egenskaperna. Används ofta inom flyg-, fordons- och konsumentelektroniktillämpningar på grund av sin lätta vikt. DMLS-bearbetning gör det möjligt att skapa komplexa, lätta komponenter med bra ytfinish.
- Gasatomerat verktygsstål (H13, etc.): Verktygsstål är kända för sin exceptionella slitstyrka och hårdhet. H13 är ett populärt val för formar och matriser på grund av sin förmåga att motstå höga temperaturer och mekaniska påfrestningar. DMLS-bearbetning gör det möjligt att skapa komplexa verktygsinsatser med god måttnoggrannhet.
Här är en tabell som sammanfattar några viktiga egenskaper hos dessa metallpulver:
Metallpulver | Typiska tillämpningar (EBM) | Typiska tillämpningar (DMLS) | Viktiga överväganden |
---|---|---|---|
Gasatomerad Ti-6Al-4V | Flyg- och rymdindustrin, medicinska implantat | Flyg- och rymdindustrin, medicinska implantat | Utmärkt förhållande mellan styrka och vikt, biokompatibel |
Gasatomerad Inconel 718 | Gasturbinmotorer, värmeväxlare | Gasturbinmotorer, värmeväxlare | Hållfasthet vid höga temperaturer, motståndskraft mot tuffa miljöer |
Gasatomerad koppar (Cu) | Kylflänsar, elektriska komponenter | Kylflänsar, elektriska komponenter | Hög termisk och elektrisk ledningsförmåga |
Gasatomerat rostfritt stål 316L | Medicinska implantat, kemisk bearbetning | Medicinska implantat, kemisk bearbetning | Korrosionsbeständighet, biokompatibel |
Gasatomerade aluminiumlegeringar (AlSi10Mg) | Flyg- och rymdindustrin, fordonsindustrin, konsumentelektronik | Flyg- och rymdindustrin, fordonsindustrin, konsumentelektronik | Lättvikt, bra förhållande mellan styrka och vikt |
Gasatomerat verktygsstål (H13) | Gjutformar och matriser | Gjutformar och matriser | Exceptionell slitstyrka, hårdhet |
Kom ihåg att detta inte är en uttömmande lista. Tillverkarna erbjuder ett stort urval av metallpulver för additiv tillverkning, vart och ett med unika egenskaper och certifieringar. Att rådgöra med välrenommerade leverantörer av metallpulver och förstå dina specifika applikationskrav är avgörande för att välja det lämpligaste materialet för ditt 3D-utskriftsprojekt.
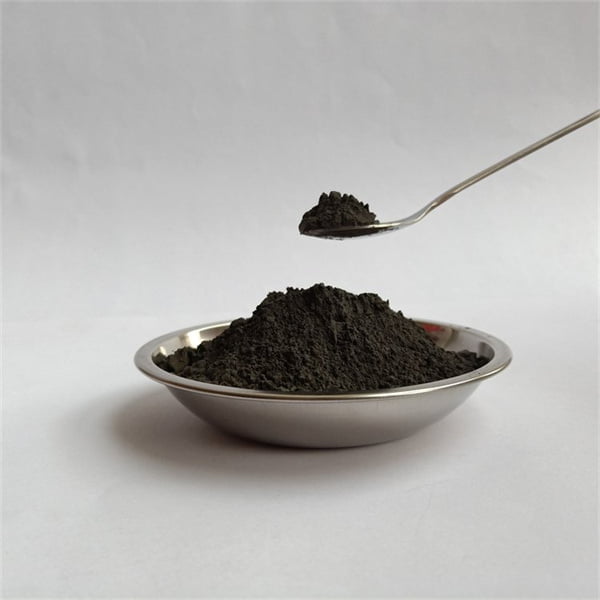
En jämförelse mellan EBM och DMLS
Efter att ha utforskat svårigheterna med både EBM- och DMLS-teknik, tillsammans med den värld av metallpulver som används i varje process, är det dags att direkt jämföra dessa två titaner inom 3D-utskrift. Detta kommer att hjälpa dig att fatta ett välgrundat beslut baserat på dina specifika projektbehov.
Här är en tabell som sammanfattar de viktigaste skillnaderna mellan EBM och DMLS:
Funktion | Smältning med elektronstråle (EBM) | Direkt metallsintring med laser (DMLS) |
---|---|---|
Energikälla | Elektronstråle | Högpresterande fiberlaser |
Miljö | Högvakuumkammare | Atmosfär med inert gas |
Formningshastighet | Snabbare | Långsammare |
Formningsnoggrannhet | Bra | Utmärkt |
Materialkompatibilitet | Limited (Reaktiva metaller) | Bredare utbud av material |
Ytfinish | Något grövre | Smidigare |
Porositet | Lägre | Potentiellt högre |
Proffs | Snabbare byggtider, bra för reaktiva metaller, minimal oxidation | Högre precision, bredare materialkompatibilitet, bra ytfinish |
Nackdelar | Lägre noggrannhet, begränsade materialalternativ, högre energiförbrukning | Långsammare byggtider, potential för högre porositet, kan kräva efterbearbetning för vissa material |
Låt oss gå djupare in på dessa viktiga skillnader för att förstå vilken teknik som kan passa bäst för ditt projekt:
- Bygghastighet: Om snabbhet är en kritisk faktor kan EBM vara det bättre valet. Den högeffektiva elektronstrålen möjliggör snabbare smältning och kortare byggtider, särskilt för större komponenter. Men om invecklade detaljer och måttnoggrannhet är av största vikt kan DMLS vara ett bättre alternativ, även om det tar något längre tid att skriva ut.
- Materialkompatibilitet: EBM är utmärkt för bearbetning av reaktiva metaller som titan och tantal tack vare högvakuummiljön som minimerar oxidation. DMLS, å andra sidan, erbjuder ett bredare utbud av materialkompatibilitet, inklusive rostfritt stål, aluminiumlegeringar och verktygsstål. Detta bredare urval möjliggör större designflexibilitet i DMLS.
- Detaljnoggrannhet och ytfinhet: DMLS är suveränt när det gäller formningsnoggrannhet och ytfinish. Den exakta kontrollen över laserstrålen gör det möjligt att skapa mycket detaljerade detaljer med en slät ytfinish. EBM erbjuder god noggrannhet, men elektronstrålesmältningsprocessens natur kan resultera i en något grövre ytfinish jämfört med DMLS.
- Porositet: Porositet avser små luftspalter i den tryckta metallen. EBM producerar i allmänhet delar med lägre porositet på grund av högvakuummiljön, som minimerar förekomsten av instängda gaser. DMLS, som ger en god övergripande kvalitet, kan ha en något högre risk för porositet, särskilt när man använder vissa material eller utskriftsparametrar. I vissa fall kan DMLS-delar kräva efterbearbetningstekniker som varm isostatisk pressning (HIP) för att eliminera eventuella inre hålrum.
- Överväganden om kostnader: Kostnaden för att 3D-printa en metalldel med antingen EBM eller DMLS beror på flera faktorer, bland annat det valda materialet, delens komplexitet och den efterbearbetning som krävs. I allmänhet kan dock EBM ha högre energiförbrukning på grund av behovet av en högvakuummiljö. DMLS kan vara ett mer kostnadseffektivt alternativ för vissa applikationer, särskilt med tanke på det potentiella behovet av efterbearbetning med EBM.
Att välja rätt vapen: EBM vs. DMLS - den slutliga domen
Det finns ingen enskild "vinnare" i kampen mellan EBM och DMLS. Vilken teknik som är bäst beror på de specifika behoven i ditt projekt. Här är några avslutande tankar som kan vägleda dig i ditt beslut:
- För projekt som kräver höghastighetstryck av reaktiva metaller som titan, och där en något grövre ytfinish kan accepteras, kan EBM vara ett bra val.
- För projekt som kräver invecklade detaljer, exceptionell måttnoggrannhet, ett bredare utbud av materialalternativ och en jämn ytfinish kan DMLS vara det bättre alternativet, även om det tar något längre tid att skriva ut.
- Överväg noga kostnadseffekterna av varje teknik, inklusive materialkostnad, energiförbrukning och eventuella behov av efterbearbetning.
Det är alltid tillrådligt att rådgöra med erfarna 3D-utskriftsexperter för att diskutera dina specifika projektkrav och avgöra vilken teknik som ska användas, EBM eller DMLS, skulle vara det lämpligaste valet för optimala resultat.
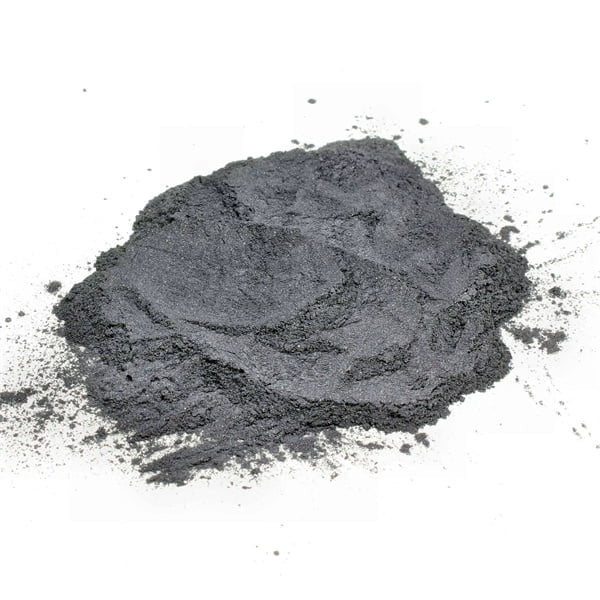
VANLIGA FRÅGOR
Q: Vilken teknik är starkast, EBM eller DMLS?
A: Både EBM och DMLS kan producera metalldelar med hög hållfasthet. Den faktiska styrkan beror på det valda metallpulvret och de specifika tryckparametrar som används. På grund av miljön med högt vakuum och potentiellt lägre porositet kan dock EBM-tryckta delar uppvisa något högre hållfasthet för vissa reaktiva metaller som titan.
Q: Kan jag använda EBM eller DMLS för att skriva ut färgade metalldelar?
S: Även om både EBM och DMLS främst fokuserar på att skapa funktionella metalldelar finns det vissa begränsade efterbearbetningstekniker som kan ge färg till ytan. Dessa tekniker innebär vanligtvis att man applicerar ett tunt lager färgad beläggning eller infiltration med en färgad harts. Det kan dock vara svårt att uppnå levande eller konsekventa färger och den långsiktiga hållbarheten hos sådana färgapplikationer kan vara begränsad. Om färg är ett kritiskt krav kan andra 3D-utskriftstekniker som bindemedelsstråle eller Multi Jet Fusion vara mer lämpliga, eftersom de erbjuder ett bredare utbud av färgalternativ direkt i utskriftsprocessen.
F: Är EBM- eller DMLS-tryckta delar miljövänliga?
S: Miljöpåverkan från EBM och DMLS beror på flera faktorer, bland annat det valda metallpulvret, energiförbrukningen under tryckprocessen och eventuella nödvändiga efterbearbetningssteg. Själva produktionen av metallpulver kan vara energiintensiv. EBM kan, på grund av sin högvakuummiljö, ha ett något högre energifotavtryck jämfört med DMLS. Båda teknikerna erbjuder dock betydande fördelar när det gäller detaljkomplexitet och materialanvändning jämfört med traditionella subtraktiva tillverkningstekniker som maskinbearbetning. Detta kan leda till mindre materialspill och potentiellt en mer hållbar tillverkningsmetod för vissa applikationer.
Q: Vilka framtida framsteg förväntas inom EBM- och DMLS-teknikerna?
S: Området EBM och DMLS är under ständig utveckling. Här är några spännande möjligheter i horisonten:
- Snabbare utskriftshastigheter: Forskare utvecklar tekniker för att öka hastigheten för både EBM och DMLS utan att kompromissa med detaljkvaliteten. Detta kan innebära framsteg inom energikälla eller förbättrade mekanismer för pulverhantering.
- Utökad materialkompatibilitet: Utbudet av metaller som lämpar sig för EBM- och DMLS-utskrifter förväntas öka. Detta skulle ge konstruktörerna ännu större flexibilitet när det gäller att välja det optimala materialet för sina specifika behov.
- Tryckning av flera material: Tekniker utforskas för att göra det möjligt att skriva ut delar med olika metaller eller till och med kombinationer av metall och andra material i en och samma konstruktion. Detta skulle kunna öppna dörrar för skapandet av mycket funktionella och komplexa komponenter.
- Förbättrad ytfinish: Framsteg inom laser- och elektronstrålstyrningsteknik kan leda till ännu jämnare ytfinish för DMLS-printa detaljer, vilket kan minska behovet av efterbearbetning i vissa applikationer.
I takt med att dessa innovativa tekniker fortsätter att utvecklas kommer EBM och DMLS att spela en allt viktigare roll när det gäller att revolutionera det sätt på vilket vi konstruerar och tillverkar metalldelar inom olika branscher.
Slutsats
Den intrikata dansen mellan EBM- och DMLS-teknikerna erbjuder en kraftfull verktygslåda för att skapa komplexa och funktionella metallobjekt. Genom att förstå styrkorna och svagheterna med varje metod, tillsammans med den stora värld av metallpulver som används som byggstenar, kan du fatta välgrundade beslut för dina 3D-utskriftsprojekt. Oavsett om du prioriterar snabbhet för reaktiva metaller med EBM eller söker exceptionella detaljer och ett bredare materialval med DMLS, flyttar båda teknikerna fram gränserna för vad som är möjligt inom metalltillverkning. Eftersom dessa tekniker fortsätter att utvecklas har framtiden en enorm potential för ännu större designfrihet, materialinnovation och ett mer hållbart tillvägagångssätt för skapande av metalldelar.
Dela på
MET3DP Technology Co, LTD är en ledande leverantör av lösningar för additiv tillverkning med huvudkontor i Qingdao, Kina. Vårt företag är specialiserat på 3D-utskriftsutrustning och högpresterande metallpulver för industriella tillämpningar.
Förfrågan för att få bästa pris och anpassad lösning för ditt företag!
Relaterade artiklar
Om Met3DP
Senaste uppdateringen
Vår produkt
KONTAKTA OSS
Har du några frågor? Skicka oss meddelande nu! Vi kommer att betjäna din begäran med ett helt team efter att ha fått ditt meddelande.
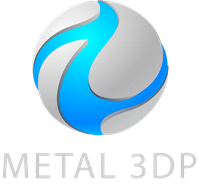
Metallpulver för 3D-printing och additiv tillverkning