Översikt över metallpulver
Innehållsförteckning
Metalliska pulver hänvisar till fina metallkorn som används vid tillverkning, tillverkning och andra industriella tillämpningar. De består av metallpartiklar i pulverform som uppvisar unika egenskaper jämfört med bulkmetall som gör dem lämpliga för specialiserade användningar.
Viktiga detaljer om metallpulver:
Sammansättning | Rena metaller som järn, koppar, aluminium, nickel, etc. eller metallegeringar |
Partikelstorlek | Varierar kraftigt från 10-250 mikron beroende på avsedd användning |
Produktionsprocess | Atomisering, elektrolys, karbonylprocess, malning, kondensation, etc. |
Viktiga egenskaper | Flytbarhet, skenbar densitet, tappdensitet, kompressibilitet, permeabilitet, etc. |
Huvudsakliga tillämpningar | Additiv tillverkning, formsprutning, pressning och sintring, svetsning, hårdlödning, ytbeläggning, etc. |
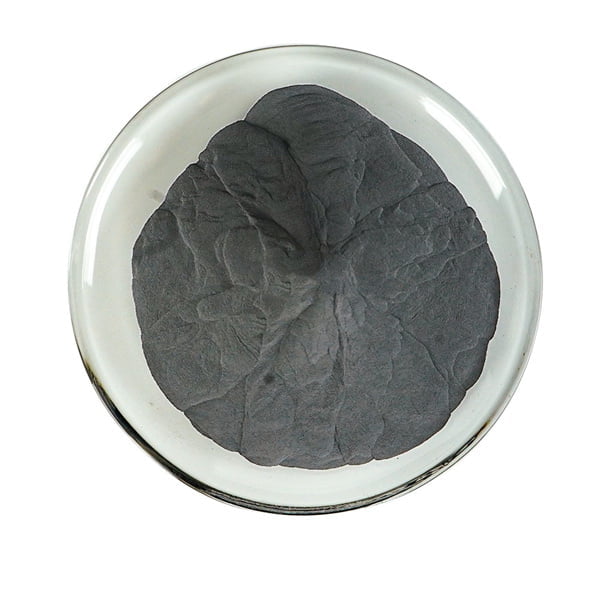
Typer av Metalliska pulver
Många rena metaller och metallegeringar finns i pulverform för industriellt bruk. Några av de viktigaste kategorierna och exemplen inkluderar:
Typ | Sammansättning |
---|---|
Ren metall | Järn, koppar, aluminium, krom, nickel, kobolt, volfram |
Järnlegeringar | Rostfritt stål, verktygsstål, legerat stål |
Icke-järnlegeringar | Mässing, brons, titanlegeringar |
Ädelmetaller | Guld, silver, platina |
Eldfasta metaller | Volfram, molybden, niob, tantal |
Den specifika metallen eller legeringen som väljs beror på faktorer som kostnad, fysiska egenskaper som krävs, kompatibilitet, estetik och applikationens prestandabehov.
Sammansättning och egenskaper
Sammansättningen och egenskaperna hos metallpulver beror på basmetallen, använda legeringselement, produktionsmetod, partikelstorleksintervall, form, porositet och ytbehandling.
Parameter | Beskrivning |
---|---|
Basmetall | Kärnelement som utgör högsta komposition. Bestämmer densitet, styrka, smältpunkt, etc. |
Legeringselement | Läggs till för att skräddarsy fysiska och mekaniska egenskaper som hårdhet, korrosionsbeständighet, konduktivitet, etc. |
Produktionsprocess | Påverkar partikelstorleksintervall, form, porositetsnivå, flödesegenskaper, skenbar densitet, etc. |
Partikelstorlek | Typiskt område är 10 – 250 μm. Underkategorier av nanopulver (<100 nm) finns också. Påverkar reaktivitet, flytbarhet, densitet. |
Partikelform | Sfärisk, strimlad, oregelbunden, flagnande. Påverkar flödeshastighet, packningsdensitet, skiktvidhäftning vid additiv tillverkning. |
Porositet | Fasta eller porösa partiklar. Porös absorberar lätt fukt. Fast material har högre densitet. |
Ytbehandling | Beläggningar (organiska, metalliska) kan förbättra flytbarheten, minska reaktiviteten med miljön. |
Att förstå hur dessa parametrar påverkar pulveregenskaperna gör det möjligt att välja lämpligt pulver för en applikation.
Tillämpningar och användningsområden
Metalliska pulver finner utbredd användning inom tillverkning, konstruktion, elektronik, fordon, flyg, medicin och andra sektorer.
Område | Tillämpningar |
---|---|
Additiv tillverkning | 3D-utskrift av metalldelar med hjälp av teknologier som DMLS, SLM, EBM, binder jetting |
Pulverformsprutning | Tillverkning av små komplexa metalldelar i nätform med bra finish |
Pulvermetallurgi | Pressa och sintra pulver komprimerar till delar; askfria smörjmedel förbättrar egenskaperna |
Svetsning & lödning | Tillsatsmetallpulver för sammanfogning av metaller; flusskärna trådar förbättrar svetsningen |
Ytbeläggning | Termisk spray metallisk beläggning för korrosions- och slitageskydd |
Elektronik | Ledande silver-, koppar- och nickelpulver i lim och bläck |
Bildelar | Pulversmidda växlar av stål och aluminium, motordelar |
Flyg- och rymdindustrin | Precisionsdelar av titan och nickellegeringar; turbin- och bladbeläggningar |
Medicin | Porösa titanimplantat tillåter beninväxt; bioresorberbara järnpulver |
Metallpulver tjänar olika tillämpningar inom många teknikområden och möjliggör specialiserade tillverkningstekniker.
Specifikationer
Metallpulver måste uppfylla en rad exakta fysiska och sammansättningsspecifikationer för att de ska fungera effektivt i tillverkningsprocesser.
Parameter | Typiska värden | Roll |
---|---|---|
Partikelstorlek | 10 - 150 μm | Bestämmer densitet/flytbarhet; mindre = mer reaktiv |
Skenbar densitet | Upp till 65% av sann densitet | Påverkar vikt, flytbarhet; lägre densitet packar bättre |
Tappdensitet | Upp till 80% av sann densitet | Indikator för flödesegenskaper under vibration/omrörning |
Hausner-kvot | <1,25 indikerar god flytbarhet | Förhållandet mellan tappdensitet och skenbar densitet |
Kompressibilitet | 20-35% | Pulvrets förmåga att minska volymen under tryck |
Angle of Repose | <40° är fritt flytande | Branthet av pulverhög; lägre = mer flytande |
Hall Flödeshastighet | <30 s/50g | Tid det tog för 50 g pulver att rinna genom en öppning |
Morfologi | Sfärisk/ oregelbunden | Partikelformen påverkar fluiditeten och packningsdensiteten |
Renhet | >99,5% | Hög renhet krävs för prestanda; avlägsnas genom gasatomisering |
Fukthalt | <0,1 vikt.% | Fukt orsakar dåligt flöde och minskad styrka |
Uppfyllande av specifikationer säkerställer batch-till-batch-konsistens och pulverkompatibilitet med produktionsprocesser.
Pulverproduktionsprocesser
Metalliska pulver framställs genom olika metoder, var och en resulterar i pulver med olika egenskaper lämpade för vissa applikationer.
Process | Metod | Typisk storlek | Morfologi | Skalbarhet | Kostnad |
---|---|---|---|---|---|
Atomisering av gas | Högtrycksgas bryter upp smält metallström | 15 – 150 μm | Mestadels sfärisk | Hög | Medium |
Atomisering av vatten | Uppbrott med höghastighetsvattenstrålar | 20 – 250 μm | Oregelbunden, porös | Hög | Låg |
Elektrolys | Elektrokemisk reaktion avsätter fina partiklar | 1 – 1000 μm | Dendritisk, porös | Låg | Hög |
Roterande elektrod | Centrifugalkrafter avlägsnar partiklar | 20 – 100 μm | Flakig, oregelbunden | Låg | Medium |
Karbonylprocessen | Termisk nedbrytning av gasformiga föreningar | 1 – 10 μm | Sfärisk | Hög | Hög |
Mekanisk fräsning | Hårda partiklar maler metallklumpar till pulver | 10 – 250 μm | Oregelbunden, porös | Hög | Låg |
- Gas- och vattenförstoftning tillåter höga produktionshastigheter av fina sfäriska pulver som är bra för additiv tillverkning
- Elektrolys ger porösa, oregelbundna pulver lämpliga för pressning/sintring
- Mekanisk fräsning är mångsidig för framställning av komposit-, legerings-, nanopulver av olika metaller
Pulverattribut kan därför skräddarsys med olika produktionsmetoder.
Betyg och standarder
Olika nationella och internationella standardorganisationer har tagit fram kvalitetsspecifikationer för vanliga metallpulver för att möjliggöra kvalitetskontroll under tillverkning och användning.
Region | Betyg specificerade | Metaller täckta | Roll |
---|---|---|---|
Förenta staterna | MPIF-standarder | Järn, stål, rostfritt stål, koppar, mässing, nickellegeringar | Säkerställer konsekventa mekaniska egenskaper |
Europa | EN, DIN och ISO standarder | Stål, rostfria stål, verktygsstål, koppar, aluminiumlegering, nickel, kobolt | Pulverkompatibilitet med industriella processer |
Japan | JIS-standarder | Pulver av järn, koppar, aluminiumlegering | Definierar exakt testmetod |
Indien | BIS-standarder | Järn, stål, kopparpulver | Skräddarsydd för indiska tillverkare och användare |
Klassbeteckningen indikerar partikelstorleksintervall, renhetsnivåer, legeringssammansättning och andra parametrar som hjälper till att matcha pulver med avsedd användning inom olika sektorer.
Prissättning
Priserna på metallpulver beror på sammansättning, sökta renhetsnivåer, använda produktionsmetod, brist på råvaror, dynamik mellan utbud och efterfrågan och köpt kvantitet.
Metallpulver | Prisintervall* |
---|---|
Järn och låglegerat stål | $1 – 3 per kg |
Verktyg och rostfritt stål | $5 – 10 per kg |
Nickellegeringar | $10 – 30 per kg |
Titan och superlegeringar | $50 – 250 per kg |
Tungsten tunga legeringar | $50 – 100 per kg |
Ädelmetaller (Au, Ag, Pt) | $3000 – 5000 per kg |
Beräknade prisintervall för bulkvantiteter som köps direkt från större producenter.
Priserna följer typisk ordning – järnmetaller < icke-järnlegeringar < högpresterande legeringar baserat på insatsmetallkostnader. Massmarknadsmetaller som järn och pulver av rostfritt stål produceras i stora volymer vilket gör dem mest ekonomiska.
Jämförelse mellan stora metalliska pulvertyper
Parameter | Rostfritt stål | Aluminiumlegering | Nickellegering | Titanlegering |
---|---|---|---|---|
Täthet | Medium (7–8 g/cc) | Låg (2,7 g/cc) | Hög (8–9 g/cc) | Medium (4,5 g/cc) |
Styrka | Medium | Låg | Hög | Medium |
Reaktivitet | Låg | Hög | Medium | Hög |
Termisk konduktivitet | Låg | Hög | Medium | Låg |
Motståndskraft mot korrosion | Hög | Medium | Hög | Hög |
Kostnad | Låg | Låg | Hög | Mycket hög |
Exempel på tillämpningar | Medicinska implantat, köksutrustning | Bildelar, flygplan | Turbinblad, marina | Flyg- och rymdindustrin, medicinteknik |
- Pulver av rostfritt stål erbjuder korrosionsbeständighet och styrka till låg kostnad lämplig för konsumentprodukter
- Lättviktspulver av aluminiumlegering som används allmänt för viktkänsliga bilkomponenter
- Nickellegeringar klarar höga temperaturer bra; användbar för motorer och gasturbiner
- Titan har styrka-till-vikt-förhållandet som önskas i flygplanets strukturdelar
Således har varje pulvertyp specifika egenskaper som gör den att föredra för nischapplikationer inom olika industrier.
För- och nackdelar med Metalliska pulver
Fördelar | Nackdelar |
---|---|
Mycket stor yta ökar reaktiviteten | Benägen för brand och dammexplosioner om pulver är suspenderat |
Nära nätformade delar från olika tekniker | Kräver skyddande atmosfär eller beläggningar på grund av hög reaktivitet |
Inget skrot eller bearbetning till skillnad från konventionella metoder | Ofta lägre hållfasthet och densitet jämfört med gjuten och smidd metall |
Konsekvent fin mikrostruktur från snabb kylning | Särskild hantering och behållare behövs för att förhindra kontaminering |
Lätt legerad till högpresterande kompositioner | Flödesegenskaperna varierar avsevärt för olika pulver |
Lägre energianvändning än utvinning från malmer | Hög kostnad för vissa specialmetallpulver |
Förenklad tillverkning av komplexa, intrikata former | Porositetsproblem under packning påverkar mekaniska egenskaper |
Proffs – metallpulver möjliggör transformativa tillverkningsmöjligheter och skräddarsydda egenskaper från breda materialval.
Nackdelar – Säkerhetsproblem finns med lagring och hantering; egenskaper är applikationsspecifika.
Med sunda tekniska kontroller uppväger de unika fördelarna med metallpulver bristerna för kritiska applikationer.
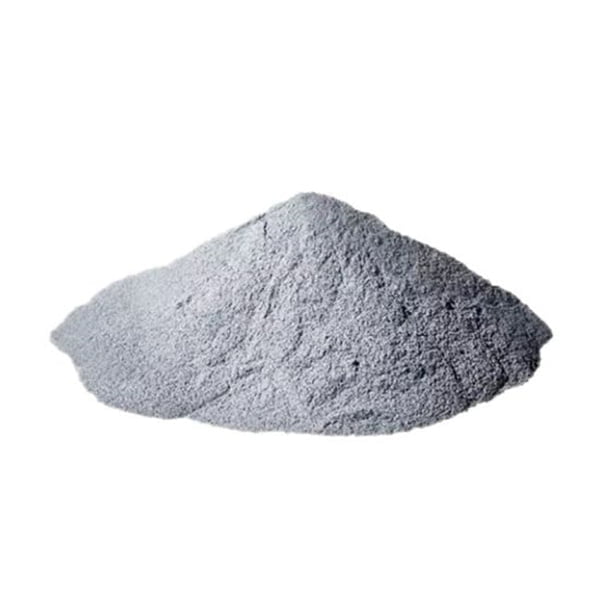
VANLIGA FRÅGOR
Varför används metallpulver istället för fasta metaller?
Metallpulver erbjuder unika fördelar jämfört med bulkmetaller vid tillverkning och andra applikationer:
- Stort förhållande mellan ytarea och volym förbättrar reaktiviteten för legering, uppvärmning, beläggning
- Fina enhetliga strukturer och kontrollerad snabb kylning från pulverprocesser
- Nära nätformtillverkningsmetoder som additiv tillverkning och pulverformsprutning
- Skräddarsydda pulverkompositioner möjliggör högpresterande legeringar
- Förenklad tillverkning av komplexa, intrikata komponenter
- Lägre energiförbrukning än utvinning och raffinering från malmer
Specifika egenskaper som endast är möjliga med pulver gör dem därför lämpliga över bulkmetaller för nischapplikationer.
Hur avgör man om ett metallpulver är av god kvalitet?
Indikatorer på att ett metallpulver uppfyller kvalitetsstandarder:
- Sammansättning – Hög renhet med specificerade legeringselement säkerställer tillförlitlig prestanda
- Partikelstorlek – Smal fördelning förbättrar densitet och flödesegenskaper
- Morfologi – Sfäriska partiklar ger bättre flyt än oregelbundna former
- Flödeshastighet – Uppmätt med hallflödesmätare eller vilovinkeltest för att uppfylla riktmärken för flytbarhet
- Skenbar densitet – Högre densitet förbättrar packningen och pulverspridbarheten
- Tappdensitet – Högre densitet indikerar bättre flytbarhet under vibrationer
- Fukthalt – Låg fuktighet säkerställer att pulver inte agglomererar under lagring och hantering
Att uppfylla specifikationerna för pulverkaraktäristik visar produktionsprocesskontroll och enhetlighet från batch-till-batch för användarna.
Vilka försiktighetsåtgärder bör vidtas vid hantering av metallpulver?
Särskilda försiktighetsåtgärder som krävs vid hantering av metallpulver:
- Explosionsrisker – I finfördelad form är pulver mycket brandfarliga, undvik antändningskällor
- Oxidationsproblem – Känsliga reaktiva pulver måste förvaras i inert gasatmosfär
- Inneslutningssystem – läckagesäkra behållare som används undviker spill; förseglade pulverhanteringssystem föredras
- Personalsäkerhet – Skyddskläder, handskar, andningsmasker obligatoriska speciellt för giftiga pulver
- Ventilation – Lokala avgassystem för att förhindra att fina partiklar suspenderas i luft som kan andas in
- Jordning – Jordad utrustning förhindrar uppbyggnad av statisk laddning som kan antända pulver
- Fuktkontroll – Fuktigheten bibehålls för att förhindra att pulver hopbakas och smutsar ner
Strikta kontroller och skyddssystem behövs för säker hantering av metallpulver på grund av brand-, hälso- och kontamineringsrisker.
Vilka är vanliga tekniska problem med 3D-utskrift med metallpulver?
Några vanliga problem med metallpulverbaserad tillsatstillverkning:
- Porositet – Gasbubblor som fångas under stelningen lämnar tomrum som minskar styrkan
- Ytfinish – Lager-för-lager uppbyggnad orsakar grovhet som behöver efterbearbetas
- Restspänning – Termiska cykler inducerar inre spänningar som leder till dels varp eller sprickor
- Anisotropa egenskaper – Riktning från bygglager orsakar variationer i materialegenskaper
- Dimensionell tolerans – Noggrannhetsgränser på grund av krympning, variationer i pulverpartikelstorlek
- Brist på fusion – Ofullständig smältning mellan lagren på grund av dålig pulverspridning påverkar styrkan
- Oönskad legering – Interaktion mellan exotiska material och bottenplatta kräver kontroll
- Långa byggtider – Komplexa geometrier som tar dagar riskerar att utrustningsfel stoppar jobb
Att förstå och mildra dessa mekanismer genom modellering, optimerade bearbetningsparametrar och kvalitetskontroll är avgörande för pålitlig tillverkning av metalltillsatser.
Slutsats
Metallpulver ger ett mångsidigt materialformat som öppnar upp för nya tillverkningsmöjligheter inom olika branscher. De möjliggör skräddarsydda kompositioner omöjliga genom konventionell bearbetning av bulkmetaller i fast form. När pulverspecifikationer och -kvaliteter standardiseras globalt kommer konsistensen och tillförlitligheten att fortsätta att förbättras för att hjälpa till att överföra specialiserade tekniker till mainstream. Framsteg inom produktionsteknik kommer också att sänka kostnaderna och mildra nuvarande begränsningar avseende brist på smältning, kvarvarande spänningar och riktningsegenskaper. Den snabba expansionen av metalltillsatstillverkning, särskilt inom flyg-, medicin- och verktygssektorerna, understryker metallpulvers transformativa potential. Med ökad användning är de redo att ta en viktig roll som kopplar högpresterande materialutveckling till nästa generations tillverkningsprocesser.
Dela på
MET3DP Technology Co, LTD är en ledande leverantör av lösningar för additiv tillverkning med huvudkontor i Qingdao, Kina. Vårt företag är specialiserat på 3D-utskriftsutrustning och högpresterande metallpulver för industriella tillämpningar.
Förfrågan för att få bästa pris och anpassad lösning för ditt företag!
Relaterade artiklar
Om Met3DP
Senaste uppdateringen
Vår produkt
KONTAKTA OSS
Har du några frågor? Skicka oss meddelande nu! Vi kommer att betjäna din begäran med ett helt team efter att ha fått ditt meddelande.
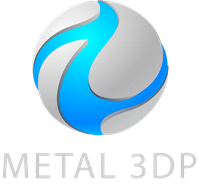
Metallpulver för 3D-printing och additiv tillverkning