Process med roterande elektrod i plasma
Innehållsförteckning
Den plasma roterande elektrodprocess (PREP) är en avancerad materialbearbetningsteknik som använder plasmabågar och centrifugalkrafter för att producera högpresterande material. Denna innovativa metod kombinerar fördelarna med plasmabågsmältning och centrifugalgjutning, vilket möjliggör produktion av material med överlägsna egenskaper jämfört med konventionella processvägar.
Översikt över processen med roterande plasmaelektroder
Den plasmaroterande elektrodprocessen använder en roterande grafitelektrod som är omgiven av en plasmabåge. När elektroden roterar smälts råmaterialmaterialet kontinuerligt av plasmabågen och slungas bort från spetsen av elektroden på grund av centrifugalkrafter. Det smälta materialet stelnar och samlas upp, vilket ger en färdig del eller göt.
Några av de viktigaste fördelarna med PREP-teknik inkluderar:
- Snabba smält- och stelningshastigheter, vilket möjliggör raffinerade mikrostrukturer
- Tillverkning av legeringar svår eller omöjlig att göra med konventionella metoder
- Förmåga att bearbeta reaktiva material utan kontaminering
- In-situ legering och kontroll av mikrostruktur
- Möjlighet till nästan nätform, vilket minimerar bearbetning
Jämfört med andra plasmasmältningsmetoder ger den roterande elektroden ytterligare kontroll över de termiska förhållandena under bearbetningen. Detta möjliggör skräddarsydda stelningsförhållanden för att optimera det färdiga materialets mikrostruktur och egenskaper.
Plasmakällan ger extremt höga temperaturer som överstiger 10 000°C, vilket möjliggör smältning av vilket material som helst. Genom att justera plasmaeffekten och andra parametrar kan de termiska förhållandena kontrolleras exakt. Detta möjliggör flexibilitet vid utformning av legeringar och bearbetningsförhållanden.
plasma rotating electrode process (PREP)-teknik för 3D-utskriftsapplikationer:
- Ti-6Al-4V, Ti-6Al-7Nb – Utmärkt styrka-till-vikt-förhållande och biokompatibilitet
- Mycket fina pulver med kontrollerad partikelstorleksfördelning
- AlSi10Mg, AlSi12 – Låg densitet med god hållfasthet och korrosionsbeständighet
- Sfärisk morfologi med hög pulverflytbarhet
- Inconel 718, Inconel 625 – Enastående högtemperaturegenskaper
- Täta 3D-utskrivna delar med fin mikrostruktur
Verktygsstål
- H13, P20, 420 rostfritt – Hög hårdhet, slitage och korrosionsbeständighet
- Kan ha komplexa geometrier för form- och formkomponenter
- Volfram, tantal, molybden – Extremt höga smältpunkter
- Högdensitetspulver lämpliga för strålskydd
Kopparlegeringar
- CuCrZr, CuNi2SiCr – Utmärkt termisk och elektrisk ledningsförmåga
- Används för värmehanteringsapplikationer
Kobolt-krom-legeringar
- CoCrMo, CoCrW – Biokompatibilitet och hög hållfasthet
- Låg inre porositet med optimerade parametrar
De sfäriska pulvren som produceras via PREP möjliggör högdensitet 3D-utskrivna delar med utmärkta mekaniska egenskaper lämpliga för krävande applikationer inom rymd, medicin, verktyg och mer.
Legeringssystem | Exempel legeringar | Viktiga egenskaper | Tillämpningar |
---|---|---|---|
Titanlegeringar | Ti-6Al-4V, Ti-6Al-7Nb | Högt förhållande mellan styrka och vikt, biokompatibilitet | Flyg- och rymdindustrin, medicinteknik |
Aluminiumlegeringar | AlSi10Mg, AlSi12 | Låg densitet, bra hållfasthet och korrosionsbeständighet | Fordon, konsumentprodukter |
Superlegeringar av nickel | Inconel 718, Inconel 625 | Utmärkta egenskaper vid höga temperaturer | Turbinblad, munstycken till raketer |
Verktygsstål | H13, P20, 420 rostfritt | Hög hårdhet, slitstyrka och korrosionsbeständighet | Formsprutningsverktyg, matriser |
Eldfasta legeringar | Volfram, tantal, molybden | Extremt höga smältpunkter | Strålningsavskärmning, högtemp ugnsdelar |
Kopparlegeringar | CuCrZr, CuNi2SiCr | Hög termisk och elektrisk ledningsförmåga | Elektronik kyla, kontakter |
Kobolt-krom-legeringar | CoCrMo, CoCrW | Biokompatibilitet, hög hållfasthet | Medicinska implantat, tandkronor |
-
Ti45Nb-pulver för additiv tillverkning
-
Pulver av TiNb-legering
-
Pulver av TiNbZrSn-legering
-
Ti6Al4V Pulver Titanbaserat metallpulver för additiv tillverkning
-
CPTi Pulver
-
TC18 Pulver : Frigör kraften hos titankarbid
-
TC11 Pulver : En omfattande guide
-
TC4 ELI Pulver
-
Bästa Ti-6Al-4V-pulver (TC4-pulver) för additiv tillverkning
Utrustning som används vid bearbetning av roterande elektroder i plasma
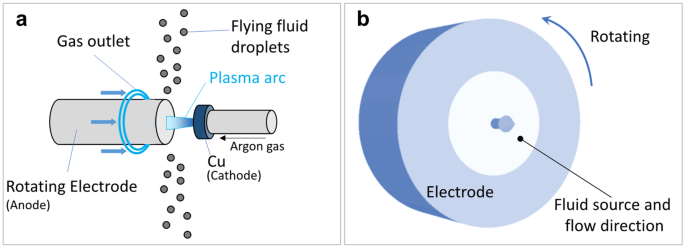
Huvudkomponenterna som används i plasmaroterande elektrodprocessen inkluderar:
Plasma facklor
- Typiskt överförda bågbrännare som levererar 10-100 kW effekt
- Tillhandahåller högtemperaturplasmabågen för att smälta matarmaterialet
- Olika plasmagaser kan användas - argon, kväve, väte, helium
Roterande elektrod
- Vanligtvis gjord av grafit för höga temperaturer
- Diameter och längd beror på delens storlek
- Roterar med hastigheter upp till 3000 rpm
- Vattenkyld för att klara hög termisk belastning
Forma
- Grafit- eller kopparform för att forma avsättningsmaterialet
- Vattenkyld för att snabbt stelna det smälta materialet
- Centrifugalkrafter projicerar materialet till formväggarna
Strömförsörjning
- DC-strömförsörjning för att driva plasmabrännaren
- Kan användas i varm eller kall katodläge
- Strömmar från 100-1000 A beroende på plasmabrännare
Vakuumkammare
- Ger kontrollerad atmosfär för plasmabåge
- Vakuum eller inert gasmiljö
Styrsystem
- Datoriserad kontroll av plasmaparametrar
- Rotationshastighet
- Materialmatningshastighet
- Automatiserad produktion
Hur den roterande plasmaelektroden fungerar
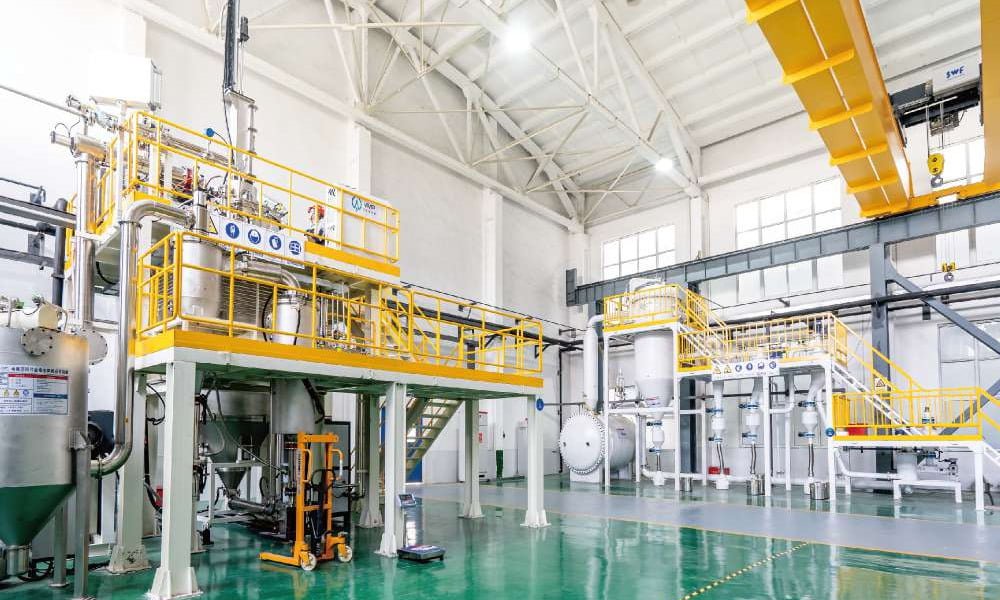
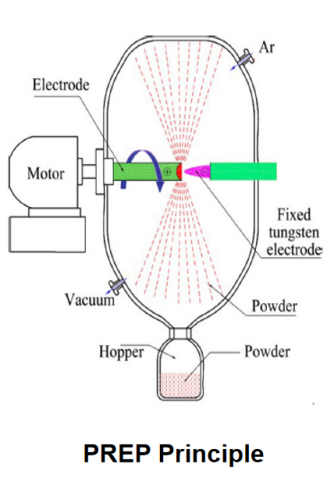
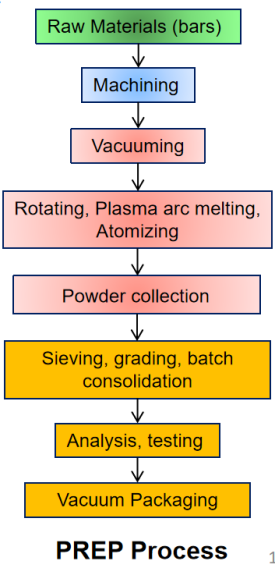
Den plasmaroterande elektrodprocessen kombinerar centrifugalgjutning och plasmabågsmältning till ett integrerat system. Här är en översikt över hur PREP fungerar:
- Införande av råmaterial – Elektroden roteras med hög hastighet upp till 3000 rpm. Råmaterial, såsom legeringspulver, injiceras i den smälta poolen på den roterande elektrodspetsen.
- Smältande – Plasmabågen från den eller de omgivande plasmabrännarna smälter det införda råmaterialet och områdena på den roterande elektrodytan. Temperaturer överstiger 10 000°C vilket säkerställer snabb smältning.
- Utstötning av smält material – Centrifugalkrafterna som genereras av den snabba rotationen gör att det smälta materialet slungas bort från elektrodspetsen. Detta bildar droppar som vandrar utåt.
- Insättningsbildning – Det utsprutade smälta materialet slår mot den vattenkylda kopparformen som placeras runt elektroden. Dropparna stelnar snabbt för att gradvis bilda en avlagring.
- Skräddarsydd stelning – Den höga värmeöverföringshastigheten från formen möjliggör kontrollerad riktningsstelning. Detta gör det möjligt att optimera insättningsstrukturen.
- Insamling av pant – När den är helt formad avlägsnas den gjutna avlagringen från kammaren. Detta kan vara ett göt, nästan nätformad del eller annan produktmorfologi.
- Automatiserad drift – PREP-systemet är helautomatiserat med datorstyrning. Det kan köras obevakat för att bygga upp betydande mängder material.
- Parameterflexibilitet – Variabler som plasmaeffekt, elektrodrotationshastighet och materialmatningshastighet kan justeras för att skräddarsy avsättningsegenskaperna.
Unika möjligheter för bearbetning av roterande elektroder i plasma
Den plasmaroterande elektrodprocessen ger några unika möjligheter som skiljer den från andra materialbearbetningsmetoder:
Snabba stelningshastigheter
- Stelningshastigheter som överstiger 100 000°C/s är möjliga
- Möjliggör bildning av icke-jämviktsfaser och metastabila strukturer
- Förfinar kornstorlekar ner till nanoskala
Tillverkning av nätform
- Avlagringar kan gjutas till nästan nettoform, vilket reducerar bearbetning
- Komplexa detaljgeometrier kan produceras direkt
- Eliminerar ytterligare bearbetningssteg
Reaktiv materialbearbetning
- Plasmabågsinneslutningen gör att reaktiva material kan bearbetas utan kontaminering
- Högreaktiva legeringar som titanaluminider kan tillverkas
Termisk kontroll
- Den roterande elektroden ger ytterligare kontroll över de termiska förhållandena
- Möjliggör skräddarsydda icke-jämvikts kylhastigheter för kontroll av mikrostruktur
In-Situ legering
- Legeringstillsatser kan matas in i den smälta poolen under bearbetningen
- Möjliggör flexibilitet vid design och tillverkning av nya legeringar
Ren bearbetningsmiljö
- Vakuumkammare ger kontrollerad atmosfär
- Inga deglar behövs för att minska potentiell kontaminering
Legeringssystem bearbetade med PREP
Legeringssystem | Beskrivning |
---|---|
Titanaluminider | Intermetalliska legeringar baserade på Ti och Al med högtemperaturegenskaper |
Bulk metalliska glasögon | Amorfa legeringar med hög hållfasthet och hårdhet |
Metallmatriskompositer | Förstärkt med partiklar för hög hållfasthet och styvhet |
Superlegeringar | Ni-, Fe- eller Co-baserade legeringar med utmärkt krypmotstånd |
Verktygsstål | Järnbaserade legeringar med hög hårdhet och slitstyrka |
Eldfasta metaller | Metaller med ultrahög smältpunkt som W, Mo, Nb, Ta |
Den plasmaroterande elektrodprocessen kan producera ett brett utbud av legeringssystem inklusive:
Titanaluminider
- Intermetalliska legeringar baserade på Ti och Al
- Utmärkta högtemperaturegenskaper med låg densitet
- Används för flyg- och biltillämpningar
Bulk metalliska glasögon
- Amorfa legeringar med överlägsen styrka och hårdhet
- Höga kylningshastigheter möjliggör bildning av metalliskt glas
- Utmärkta tekniska material och beläggningar
Metal Matrix Composites
- Förstärkt med karbider, oxider eller andra partiklar
- Utmärkt specifik styrka och styvhet
- Används för flyg-, bil- och halvledardelar
Superlegeringar
- Nickel-, järn- eller koboltbaserade legeringar med enastående krypmotstånd
- Används för högtemperaturstrukturer i turbiner och motorer
Verktygsstål
- Järnbaserade legeringar med hög hårdhet och slitstyrka
- Används för skärverktyg, formar, stansar och andra applikationer
Eldfasta metaller
- Metaller med ultrahög smältpunkt som volfram, molybden, niob, tantal
- Används för högtemperaturapplikationer på grund av bibehållande av styrka
Mikrostruktur och fastighetsförbättring
En av de främsta fördelarna med PREP är förmågan att skapa avancerade mikrostrukturer som ger förbättrade egenskaper. Några exempel inkluderar:
Kornförfining
- Extremt fina korn i nanoskala kan produceras
- Resulterar i ökad styrka enligt Hall-Petch-relationen
Förlängd fast löslighet
- Infångning av lösta ämnen via snabb stelning utökar fast löslighet
- Ändrar legeringsbeteendet och tillåter nya kompositioner
Icke-jämviktsfaser
- Metastabila faser kan bibehållas vid rumstemperatur
- Ger nederbördsstärkande och förändrar egenskaper
Partikelförstärkning
- In-situ bildning av fällningar och partiklar i nanoskala
- Utmärkta förstärkare och förfinare av kornstorlek
Eliminering av segregation
- Ingen kemisk segregation på grund av snabb stelning
- Förbättrar legeringens homogenitet och eliminerar defekter
Förbättrade gränssnitt
- Snabb stelning möjliggör gränssnitt fria från föroreningar
- Stärker korngränser och interfasgränssnitt
Fördelar med bearbetning av roterande elektroder i plasma
Några av de stora fördelarna med PREP-teknik inkluderar:
- Mångsidighet – Kan bearbeta praktiskt taget alla legeringssystem
- Överlägsna mikrostrukturer – Uppnår betydande kornförfining och mikrolegering
- Nästan nätform – Komplexa geometrier kan tillverkas direkt
- Effektivitet – Automatisk hands-off-drift med hög produktivitet
- Kvalitet – Ger en ren processmiljö och eliminerar defekter
- Prestanda – Producerar legeringar med enastående mekaniska egenskaper
- Nya legeringar – Möjliggör utveckling av unika metastabila kompositioner
- Kostnadseffektivitet – Minskar råvaruavfall och krav på bearbetning
Jämfört med andra bearbetningsmetoder möjliggör PREP nya möjligheter för legeringsutveckling och optimerad materialprestanda.
Tillämpningar av legeringar producerade av PREP
De legeringar som tillverkats med plasmaroterande elektrodprocesser har funnits i en mängd olika krävande tillämpningar:
Komponenter för flyg- och rymdindustrin
- Turbinblad, skivor, höljen av nickel och titanlegeringar
- Kräver hög hållfasthet och krypmotstånd vid förhöjda temperaturer
Skärande verktyg
- Borrkronor, pinnfräsar, sågblad med verktygsstållegeringar
- Måste tåla slitage, stötar och värme under bearbetning
Biomedicinska implantat
- Titan eller rostfria stållegeringar för ortopediska implantat
- Utmärkt korrosionsbeständighet och biokompatibilitet
Bildelar
- Motorkomponenter, drivlina från aluminium, magnesium och titanlegeringar
- Lättvikt och prestanda under extrema förhållanden
Sportartiklar
- Golfklubbor, cyklar och avancerade redskap med avancerade legeringar
- Högt förhållande mellan styrka och vikt krävs
Elektronik
- Kylflänsar skurna av berylliumkompositer
- Kräver värmehanteringsfunktioner
Kärntekniska tillämpningar
- Förstärkta material som används i kärnreaktorer
- Måste bibehålla prestanda under strålning
Tillämpningar av legeringar producerade av PREP
Industri | Tillämpning |
---|---|
Flyg- och rymdindustrin | Turbinens komponenter |
Skärande verktyg | Borr, sågblad |
Biomedicinsk | Implantat |
Fordon | Motor och drivlina delar |
Sportartiklar | Klubbar, cyklar, redskap |
Elektronik | Kylflänsar |
Kärnkraft | Komponenter för reaktorer |
Aktuell forskning om bearbetning av roterande elektroder i plasma
Det finns ett antal forskningsområden som bedrivs för att ytterligare utveckla PREP-tekniken:
- Modellering av komplexa plasma-material interaktioner
- Införlivande av nya och återvunna material som råvara
- Multielektrodkonfigurationer för tillverkning av stora delar
- Hybrid PREP-processer kombinerat med additiv tillverkning
- Utveckling av ny mätdiagnostik
- Sammanfoga olika legeringar för att skapa metallmatriskompositer
- Utforskar förstärkning av kolnanorör
- Ekonomiska och livscykelanalyser av processen
Fortsatt forskning kommer att möjliggöra ytterligare processförbättringar, ett bredare utbud av legeringar och nya tillämpningar. Statliga myndigheter och privata företag investerar aktivt i att utveckla plasmaroterande elektroder.
Framtidsutsikter för PREP-teknik
Den plasmaroterande elektrodprocessen representerar ett innovativt steg inom materialbearbetningsteknik. Pågående utveckling och antagande av industrin kommer att möjliggöra nästa generations högpresterande legeringar.
Flera trender pekar mot en ljus framtid för PREP:
- Efterfrågan på specialiserade avancerade legeringar inom olika industrier ökar. PREP tillåter legeringskompositioner som inte kan uppnås med konventionella metoder.
- Nätform och additiv tillverkning får ett bredare utnyttjande. PREP har nästan nettoformkapacitet som överträffar andra metoder i legeringsflexibilitet och kvalitet.
- Automatiserad produktion med hög genomströmning är avgörande för konkurrenskraften. PREP uppnår hands-off automatiserad drift med hög produktivitet.
- Kvalitetskraven på kritiska komponenter blir allt hårdare. PREP erbjuder en hög precision, ren och kontrollerad processmiljö.
- Legeringar med förbättrade konstruerade mikrostrukturer har exceptionell prestanda. PREP låser upp metastabila strukturer med unika egenskaper.
Med dessa drivkrafter är PREP redo att bli en viktig teknik för nästa generations legeringsproduktion inom många sektorer. Fortsatt snabb tillväxt förväntas inom detta spännande område.
Vanliga frågor om bearbetning av roterande elektroder i plasma:
Här är några vanliga vanliga frågor om processen med plasmaroterande elektroder:
Vilka är de främsta fördelarna med PREP-teknik?
Några viktiga fördelar är snabba stelningshastigheter som möjliggör avancerade mikrostrukturer, tillverkning av nästan nettoform, flexibla legeringsmöjligheter, ren bearbetningsmiljö och automatiserad produktion.
Vilka material kan bearbetas av PREP?
Praktiskt taget alla legeringssystem kan bearbetas inklusive titan, aluminium, magnesium, nickel, kobolt, järn, verktygsstål och eldfasta legeringar. Nanokompositer och amorfa legeringar är också möjliga.
Hur jämför PREP med andra additiv tillverkningsmetoder?
PREP möjliggör högre temperaturlegeringar, finare kornstrukturer och undviker vissa problem med porositet och anisotropi. Men PREP har begränsade geometrier jämfört med pulverbäddsfusionsprocesser. De två kompletterar varandra.
Vilka industrier använder legeringar tillverkade av PREP?
Flyg-, biomedicinska, bil-, sport-, elektronik- och kärnkraftsindustrin drar fördel av legeringar från PREP. Tekniken används även för att tillverka skärande verktyg.
Vilka begränsningar har PREP-tekniken?
Storleken på tillverkade delar begränsas av elektroddiametern. Komplexiteten hos detaljgeometrin är också begränsad jämfört med vissa andra additivmetoder. Initiala systemkostnader är relativt höga.
Vilka nya framsteg görs inom PREP?
Några aktuella forskningsområden inkluderar multi-elektrodsystem, hybridprocesser med additiv tillverkning, avancerad modellering, ny in-situ diagnostik och legeringsutveckling.
Hur förbättrar PREP mikrostrukturen och egenskaperna hos legeringar?
Kornförfining, bibehållna metastabila faser, infångning av lösta ämnen, eliminering av segregation, förbättrade gränssnitt och skräddarsydda stelningsförhållanden resulterar i förbättrad legeringsprestanda.
Vilken expertis krävs för att driva ett PREP-system?
Specialutbildning rekommenderas för att lära dig hur man kör PREP-utrustning på rätt sätt. Kunskaper om metallurgi och plasmafysik är också fördelaktigt för att få ut det mesta av tekniken.
Dela på
MET3DP Technology Co, LTD är en ledande leverantör av lösningar för additiv tillverkning med huvudkontor i Qingdao, Kina. Vårt företag är specialiserat på 3D-utskriftsutrustning och högpresterande metallpulver för industriella tillämpningar.
Förfrågan för att få bästa pris och anpassad lösning för ditt företag!
Relaterade artiklar
Om Met3DP
Senaste uppdateringen
Vår produkt
KONTAKTA OSS
Har du några frågor? Skicka oss meddelande nu! Vi kommer att betjäna din begäran med ett helt team efter att ha fått ditt meddelande.
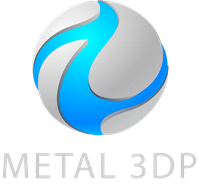
Metallpulver för 3D-printing och additiv tillverkning