výhody a nevýhody různých výrobních procesů prášku pro 3D tisk
Obsah
Představte si, jak vrstvu po vrstvě stavíte složité kovové předměty s bezkonkurenční svobodou designu a minimálním odpadem. To je kouzlo 3D tištěné kovové prášky. Ale než se z těchto drobných kovových zrn stanou stavební kameny průlomových výtvorů, je třeba je vyrobit s pečlivou péčí.
Existuje několik výrobních procesů kovových prášků, z nichž každý má své vlastní výhody a nevýhody. Volba správného procesu závisí na specifických potřebách vašeho 3D tištěného projektu. Tato komplexní příručka se ponoří do fascinujícího světa výroby kovových prášků a vybaví vás znalostmi, abyste mohli činit informovaná rozhodnutí pro své 3D tištěné projekty.
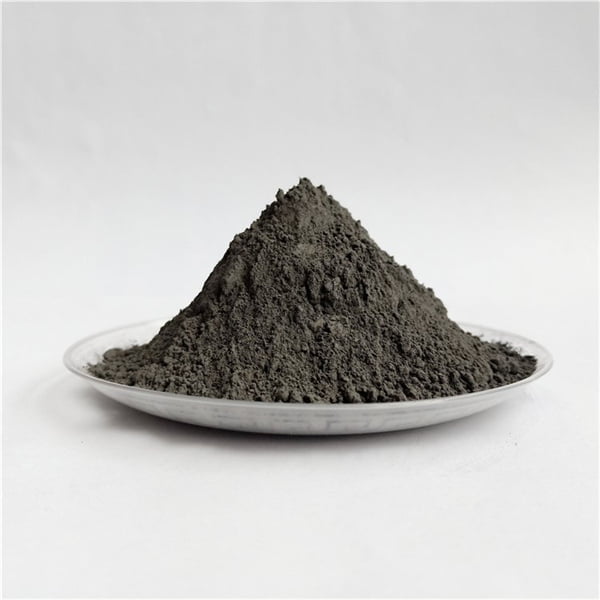
3D tištěné kovové prášky
Kovové prášky jsou neopěvovanými hrdiny 3D tisku. Tyto jemné, volně tekoucí kovové částice o velikosti od 10 do 150 mikrometrů slouží jako surovina pro různé techniky aditivní výroby (AM) kovů, jako je laserové spékání práškového lože (LPBF) a spojování prášku.
Kvalita a vlastnosti kovového prášku významně ovlivňují vlastnosti výsledného tištěného dílu, včetně jeho pevnosti, povrchové úpravy a celkového výkonu. Proto je výběr optimálního výrobního procesu kovového prášku zásadní pro dosažení požadovaných výsledků v 3D tisku.
Zkoumání metod výroby kovových prášků
Výroba kovových prášků využívá různé techniky k rozložení objemového kovu na požadovanou velikost a morfologii částic. Pojďme se hlouběji ponořit do čtyř významných metod, z nichž každá má svou vlastní jedinečnou prodejní nabídku a sadu úvah:
1. Atomizační metody: Rozklad objemového kovu s přesností
Atomizační metody jsou pracovními koňmi v aréně výroby kovových prášků. Zahrnují přeměnu roztaveného kovu na jemnou mlhu částic pomocí různých technik:
- Výhody a nevýhody metody plazmové atomizace: Plazmová atomizace využívá vysokoteplotní plazmový hořák k roztavení kovové vsázky. Roztavený kov je poté vypuzen do vysokorychlostního proudu plynu, což způsobí jeho rozpad na jemné částice. Tato metoda nabízí vynikající kontrolu nad velikostí a morfologií částic, díky čemuž je vhodná pro výrobu vysoce kvalitních prášků pro náročné aplikace, jako je letecký průmysl a lékařské implantáty. Vysoká spotřeba energie a složité nastavení zařízení z něj však mohou učinit dražší variantu.
- Výhody a nevýhody metody atomizace rotující elektrodou (REA): REA používá rychle rotující elektrodu ponořenou do lázně roztaveného kovu. Odstředivá síla generovaná rotací odhazuje drobné kovové kapky, které tuhnou na sférické částice, když se ochlazují v proudu plynu. Tato metoda se může pochlubit vysokou výrobní rychlostí a dobrou kontrolou tvaru částic, díky čemuž je ideální pro širokou škálu kovových prášků. Proces však může zavést určité vnitřní napětí v částicích, což může ovlivnit vlastnosti výsledného tištěného dílu.
- Výhody a nevýhody metody atomizace vodou: Atomizace vodou má jednodušší přístup. Roztavený kov se nalije do vysokotlakého vodního paprsku, což způsobí jeho rozpad na jemné částice. Tato metoda je nákladově efektivní a nabízí vysoké výrobní rychlosti, díky čemuž je vhodná pro hromadné aplikace. Výsledné částice však mohou mít nepravidelný tvar a vyšší povrchové oxidy, což může ovlivnit jejich tekutost a tisknutelnost.
Výběr správné atomizační metody:
Optimální atomizační metoda závisí na faktorech, jako je požadovaná velikost a morfologie částic, typ materiálu a požadavky na aplikaci.
Pokud například potřebujete vysoce přesné sférické částice pro kritické letecké díly, může být preferovanou volbou plazmová atomizace. Naproti tomu pro cenově citlivé aplikace, kde je tvar částic méně kritický, může být atomizace vodou životaschopnou možností.
2. Mechanické mletí: Broušení kovu do dokonalosti prášku
Mechanické mletí má fyzikálnější přístup. Objemový kov se drtí a mele na jemné částice pomocí vysokorychlostních mlýnů, jako jsou kulové mlýny a mlýny s attritorem.
- Výhody a nevýhody mechanického mletí: Tato metoda nabízí dobrou kontrolu nad distribucí velikosti částic a dokáže zpracovat širokou škálu materiálů, včetně křehkých kovů. Mechanické mletí však může zavést vnitřní napětí a kontaminaci do prášku v důsledku procesu mletí. Kromě toho může být dosažení velmi jemné velikosti částic náročné.
3. Metody chemické redukce: Transformující přístup
Metody chemické redukce se spoléhají na chemické reakce k přeměně oxidů kovů nebo jiných sloučenin na kovové prášky.
- Výhody a nevýhody metod chemické redukce: Tyto metody nabízejí vysokou čistotu a mohou produkovat prášky s jedinečnou morfologií. Mohou být však složité, časově náročné a generovat nebezpečné vedlejší produkty. Kromě toho může být řízení velikosti a morfologie částic náročné.
4. Elektrolýza: Tvorba kovových částic pomocí elektřiny
Elektrolýza využívá sílu elektřiny k výrobě kovových prášků. Elektrický proud prochází roztokem kovové soli, což způsobuje, že se kovové ionty usazují na katodě jako drobné částice.
- Výhody a nevýhody elektrolýzy: Elektrolýza nabízí vysokou čistotu a dobrou kontrolu nad velikostí a morfologií částic. Proces však může být pomalý a energeticky náročný, což omezuje jeho použití pro velkovýrobu. Kromě toho je často omezen na specifické kovy, které lze snadno uložit z elektrolytů.
Niche aplikace pro 3D tisk:
Elektrolýza nachází omezené uplatnění v 3D tisku kvůli své pomalé výrobní rychlosti a vhodnosti pro užší rozsah kovů ve srovnání s jinými metodami.
Výběr výrobního procesu kovového prášku
Výběr ideálního výrobního procesu kovového prášku přesahuje jen samotnou techniku. Důležitou roli hraje několik dalších faktorů:
- Materiálová kompatibilita: Ne všechny metody jsou vhodné pro všechny typy kovů. Některé metody nemusí být schopny zvládnout bod tání nebo křehkost konkrétního materiálu.
- Požadovaná velikost a morfologie částic: Velikost a tvar kovových částic významně ovlivňují jejich tekutost, tisknutelnost a vlastnosti výsledného dílu. Techniky, jako je plazmová atomizace, nabízejí větší kontrolu nad těmito aspekty.
- Čistota prášku: Přítomnost nečistot, jako jsou oxidy nebo jiné kontaminanty, může ovlivnit tisknutelnost a mechanické vlastnosti výsledného dílu. Procesy, jako jsou metody chemické redukce, mohou nabízet prášky s vysokou čistotou.
- Náklady: Výrobní náklady se liší v závislosti na složitosti metody, spotřebě energie a požadavcích na manipulaci s materiálem. Atomizace vodou je obecně nákladově efektivnější variantou, zatímco plazmová atomizace může být dražší.
- Zásah do životního prostředí: Určité metody, jako jsou ty, které zahrnují nebezpečné vedlejší produkty, mohou mít vyšší dopad na životní prostředí. Udržitelné postupy a odpovědné nakládání s odpady jsou zásadními úvahami.
Nalezení dokonalé shody:
Pečlivým vyhodnocením těchto faktorů a jejich sladěním se specifickými požadavky vašeho projektu se můžete informovaně rozhodnout o nejvhodnějším výrobním procesu kovového prášku pro vaše potřeby 3D tisku.
Další úvahy pro úspěch
Zatímco výrobní proces kovového prášku hraje zásadní roli, dosažení optimálních výsledků v 3D tisku přesahuje jen samotný prášek. Zde jsou některé další úvahy:
- Manipulace s práškem a jeho skladování: Správná manipulace a skladování jsou nezbytné pro zachování kvality prášku a zabránění absorpci vlhkosti nebo kontaminaci. To může zahrnovat použití prostředí inertního plynu nebo skladování s řízenou vlhkostí v závislosti na materiálu.
- Dodatečné zpracování prášků: Určité procesy mohou vyžadovat další kroky, jako je prosévání nebo sušení, aby se dosáhlo požadované distribuce velikosti částic nebo obsahu vlhkosti pro optimální tisknutelnost.
- Kompatibilita se stroji: Zvolený kovový prášek musí být kompatibilní s technologií a parametry sestavení vaší konkrétní 3D tiskárny.
Zvážením těchto aspektů spolu s procesem výroby kovového prášku si můžete zajistit hladký a úspěšný zážitek z 3D tisku, který dláždí cestu pro vytváření průlomových kovových předmětů.
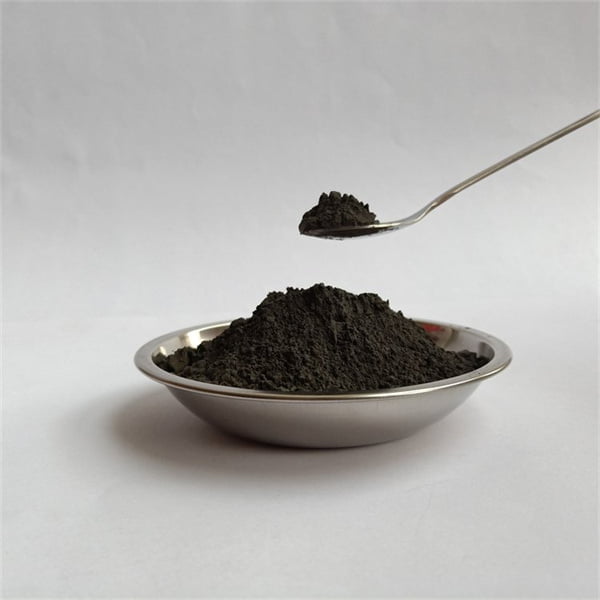
FAQ
Otázka: Jaká je nejběžnější metoda výroby kovových prášků pro 3D tisk?
Odpověď: Atomizační metody, zejména techniky atomizace plynem, jako je plazmová atomizace a atomizace rotující elektrodou, jsou nejpoužívanějšími metodami pro výrobu kovových prášků pro 3D tisk díky jejich schopnosti dosáhnout dobré kontroly nad velikostí a morfologií částic.
Otázka: Jaké faktory bych měl zvážit při výběru výrobního procesu kovového prášku?
Odpověď: Důležitou roli hraje několik faktorů, včetně typu materiálu, požadované velikosti a morfologie částic, požadavků na čistotu prášku, nákladových úvah a dopadu na životní prostředí.
Otázka: Existuje jediná „nejlepší“ metoda výroby kovového prášku?
Odpověď: Žádná jediná metoda nevládne svrchovaně. Optimální volba závisí na specifických požadavcích vašeho projektu a vlastnostech, které hledáte ve výsledném tištěném dílu.
Otázka: Jaké jsou některé z problémů spojených s výrobou kovových prášků?
Odpověď: Udržování konzistentní velikosti a morfologie částic, dosažení vysoké úrovně čistoty a vyvážení nákladové efektivity s požadovanými vlastnostmi prášku jsou některé z probíhajících problémů při výrobě kovových prášků.
Otázka: Jak se bude výroba kovových prášků vyvíjet v budoucnu?
Odpověď: Budoucnost výroby kovových prášků pravděpodobně zaznamená pokroky v technologii, což povede k efektivnějším a udržitelnějším procesům. Kromě toho probíhá výzkum nových technik výroby prášků přizpůsobených specifickým materiálům a aplikacím.
Pochopením složitosti procesů výroby kovových prášků a jejich dopadu na výsledky 3D tisku se můžete s větší jistotou a kontrolou pustit do vytváření inovativních a funkčních kovových předmětů.
Sdílet na
MET3DP Technology Co., LTD je předním poskytovatelem řešení aditivní výroby se sídlem v Qingdao v Číně. Naše společnost se specializuje na zařízení pro 3D tisk a vysoce výkonné kovové prášky pro průmyslové aplikace.
Dotaz k získání nejlepší ceny a přizpůsobeného řešení pro vaše podnikání!
Související články
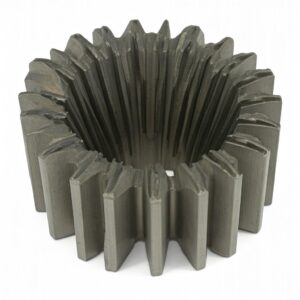
Vysoce výkonné segmenty lopatek trysek: Revoluce v účinnosti turbín díky 3D tisku z kovu
Přečtěte si více "O Met3DP
Nedávná aktualizace
Náš produkt
KONTAKTUJTE NÁS
Nějaké otázky? Pošlete nám zprávu hned teď! Po obdržení vaší zprávy obsloužíme vaši žádost s celým týmem.
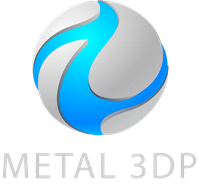
Kovové prášky pro 3D tisk a aditivní výrobu