Použití 3D tištěných sil z nerezové oceli ve zdravotnických prostředcích
Obsah
Lidské tělo je zázrak složité konstrukce, a když se něco pokazí, potřebují lékaři stejně pozoruhodné nástroje. Představte si svět, ve kterém lze implantáty vyrobit na míru, aby dokonale odpovídaly jedinečné anatomii pacienta, nebo chirurgické nástroje s bezkonkurenční mírou flexibility a přesnosti. To není sci-fi - je to realita. 3D tištěné síly z nerezové oceli v odvětví zdravotnických prostředků.
Výhody 3D tištěná nerezová ocel Powers
Nerezová ocel je již dlouho oblíbeným materiálem v lékařství díky své výjimečné pevnosti, odolnosti proti korozi a biokompatibilitě (což znamená, že se dobře snáší s lidským tělem). Tradiční výrobní postupy však mohou být omezující. Vstupte do 3D tisku, revoluční technologie, která umožňuje vytvářet složité trojrozměrné objekty z digitálních návrhů.
Zde se dozvíte, proč 3D tisk z nerezové oceli mění pravidla hry:
- Bezkonkurenční volnost designu: Na rozdíl od tradičních metod, které se spoléhají na subtraktivní výrobu (představte si vyřezání sochy z kamenného bloku), 3D tisk vytváří objekty vrstvu po vrstvě. To otevírá dveře složitým mřížkovým strukturám a pórovitým konstrukcím, které napodobují kosti nebo podporují růst tkání, s čímž mají běžné techniky potíže.
- Přizpůsobení je důležité: Každý pacient je jedinečný a díky 3D tisku lze implantáty a chirurgické nástroje přizpůsobit konkrétním potřebám pacienta. Představte si na míru navrženou náhradu kolenního kloubu, která dokonale odpovídá struktuře kostí pacienta, což může vést k rychlejšímu zotavení a lepší dlouhodobé funkčnosti.
- Lehká pevnost: 3D tisk umožňuje vytvářet lehké a přitom neuvěřitelně pevné konstrukce. To má zásadní význam pro implantáty, u nichž je minimalizace hmotnosti zásadní pro pohodlí a mobilitu pacienta. Představte si to jako stavbu mostu - chcete, aby byl dostatečně pevný, ale ne tak těžký, aby se zřítil pod vlastní vahou.
- Snížení množství odpadu: Při tradiční výrobě často vzniká velké množství odpadu. Při 3D tisku se používá pouze nezbytný prášek, čímž se minimalizuje množství odpadu a proces je šetrnější k životnímu prostředí. Ve světě, který se stále více zaměřuje na udržitelnost, je to vítaná výhoda.
3D prášek z nerezové oceli lze použít k výrobě chirurgických nástrojů
Výhody 3D tištěná nerezová ocel sahají daleko za implantáty. Představte si chirurga s kleštěmi, které byly vytištěny na 3D tiskárně se složitými úchopovými plochami, což umožňuje jemnější a přesnější uchopení choulostivých tkání. Nebo uvažujte o chirurgických nástrojích s vnitřními kanály, které mohou být přesně navrženy tak, aby dodávaly léky nebo chladicí tekutiny přímo do místa operace. 3D tisk otevírá dveře do nové éry konstrukce chirurgických nástrojů, což může vést k méně invazivním zákrokům, lepším výsledkům u pacientů a kratší době rekonvalescence.
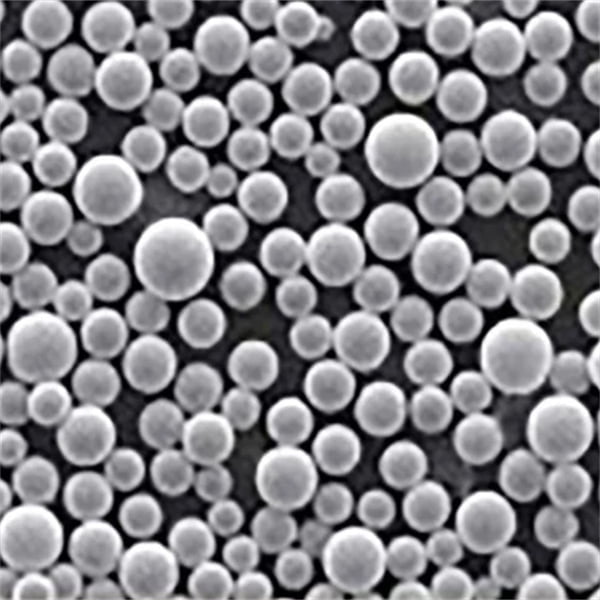
Výhody 3D tištěných implantátů z nerezové oceli
Po desetiletí se chirurgové spoléhali na hotové implantáty, které nemusely dokonale odpovídat anatomii pacienta. To může vést k problémům, jako je uvolnění implantátu, bolest a snížená funkčnost. 3D tištěné implantáty z nerezové oceli nabízejí revoluční alternativu:
- Přesné přizpůsobení: Pomocí lékařských skenů mohou chirurgové vytvářet digitální modely anatomie pacienta. Na základě těchto modelů se pak navrhují implantáty na míru, které dokonale odpovídají struktuře kosti pacienta. Představte si to jako boty na míru oproti univerzálním implantátům, které se hodí pro všechny. Přizpůsobení na míru vede k lepší stabilitě, což potenciálně snižuje riziko komplikací a zlepšuje dlouhodobou úspěšnost implantátů.
- Porézní konstrukce pro růst kostí: Tradiční implantáty mají často hladký povrch, který může ztěžovat růst kosti a její integraci s implantátem. 3D tisk umožňuje vytvářet implantáty s porézní strukturou, která napodobuje přirozenou architekturu kosti. To podporuje prorůstání kosti, což vede k pevnějšímu a stabilnějšímu rozhraní mezi implantátem a kostí.
- Snížené riziko infekce: Hladký povrch tradičních implantátů může být zdrojem bakterií, což zvyšuje riziko infekce. 3D tištěné implantáty s texturovaným povrchem mohou pomoci toto riziko snížit, protože ztěžují ulpívání bakterií.
Výhody 3D tisku zdravotnického vybavení z nerezové oceli
3D tisk není určen jen pro implantáty a nástroje. Používá se také k vytváření široké škály lékařského vybavení, jako je např:
- Protézy na míru: Představte si protézu, která nejen dobře funguje, ale také vypadá a působí přirozeně. 3D tisk umožňuje vytvářet lehké, na míru navržené protézy, které odpovídají specifickým potřebám a estetice pacienta. To může mít zásadní vliv na kvalitu života pacienta a jeho sebevědomí.
- Modely školení pro konkrétní pacienty: Složité operace často vyžadují pečlivé plánování. 3D tisk lze využít k vytvoření modelů kostí, orgánů nebo nádorů, které jsou specifické pro pacienta. Tyto modely umožňují chirurgům nacvičit si zákrok předem, což může vést ke zkrácení doby operace a zlepšení výsledků.
- Bioprinting pro regeneraci tkání: Jednou z nejzajímavějších oblastí medicínských technologií je bioprinting. Tento proces využívá techniky 3D tisku k vytváření funkčních tkání a orgánů z biokompatibilních materiálů, včetně živých buněk. Ačkoli je bioprinting s pomocí 3D tištěných nerezových scaffoldů stále v rané fázi, je obrovským příslibem pro budoucnost medicíny.
Představte si svět, kde lze poškozené tkáně, jako je kůže po popálení, regenerovat pomocí bioprintů. Nebo si představte možnost bioprintu náhradních orgánů pro pacienty, kteří potřebují transplantaci. 3D tištěné nerezové lešení může poskytnout strukturální podporu, kterou tyto bioprintované tkáně potřebují k růstu a funkci.
Výzvy a úvahy
Přestože 3D tisk z nerezové oceli nabízí pro zdravotnické prostředky řadu výhod, stále existují problémy, které je třeba překonat:
- Náklady: Technologie 3D tisku se stále vyvíjí a náklady na 3D tištěné zdravotnické prostředky mohou být vyšší než na tradičně vyráběné. Očekává se však, že s rozšířením této technologie se náklady sníží.
- Nařízení: Regulační orgány musí stanovit jasné pokyny pro vývoj a používání 3D tištěných zdravotnických prostředků. Tím se zajistí bezpečnost pacientů a účinnost těchto inovativních technologií.
- Standardizace: Vzhledem k tomu, že se 3D tisk ve zdravotnictví stále více prosazuje, je potřeba standardizovaných protokolů a materiálů, aby byla zajištěna konzistentní kvalita a výkonnost 3D tištěných zdravotnických prostředků.
Budoucnost 3D tisk z nerezové oceli v oblasti zdravotnických prostředků
Budoucnost 3D tištěné nerezové oceli ve zdravotnických prostředcích je jasná. S dalším vývojem technologie a snižováním nákladů lze očekávat, že se objeví ještě více inovativních aplikací. To by mohlo způsobit revoluci v léčbě široké škály zdravotních stavů a potenciálně vést k:
- Zlepšení výsledků pacientů: Díky implantátům a nástrojům navrženým na míru mohou chirurgové provádět přesnější a méně invazivní zákroky, což vede k rychlejšímu zotavení a snížení počtu komplikací.
- Personalizovaná medicína: 3D tisk umožňuje vytvářet zdravotnické prostředky, které jsou přizpůsobeny konkrétním potřebám pacienta. Tento personalizovaný přístup k medicíně má potenciál výrazně zlepšit péči o pacienty.
- Snížení nákladů na zdravotní péči: Počáteční náklady na 3D tištěné zdravotnické prostředky mohou být sice vyšší, ale potenciál lepších výsledků u pacientů a snížení komplikací by mohl v dlouhodobém horizontu vést ke snížení celkových nákladů na zdravotní péči.
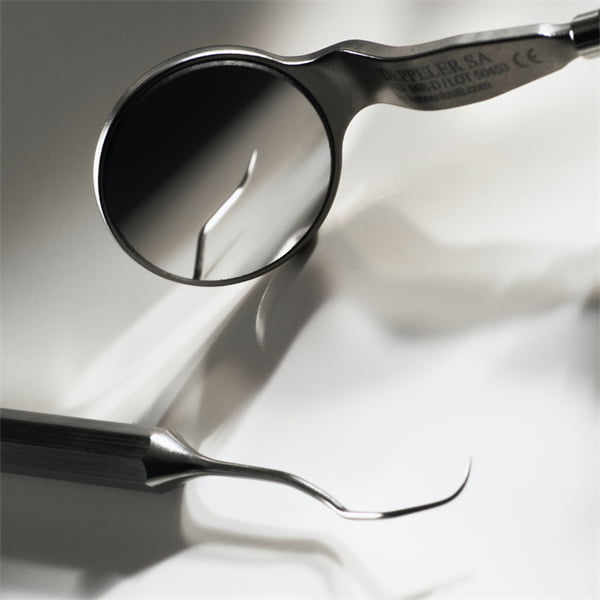
FAQ
Zde je několik často kladených otázek týkajících se 3D tisku z nerezové oceli ve zdravotnických prostředcích:
Otázka | Odpovědět |
---|---|
Jaké jsou výhody 3D tištěných zdravotnických prostředků z nerezové oceli? | 3D tištěné zdravotnické prostředky z nerezové oceli nabízejí několik výhod, včetně bezkonkurenční svobody designu, přizpůsobení, nízké hmotnosti a snížení množství odpadu. |
Lze 3D tisk nerezové oceli použít pro chirurgické nástroje? | Ano, 3D tisk z nerezové oceli lze použít k vytvoření chirurgických nástrojů se složitými prvky, což může vést k přesnějším a jemnějším zákrokům. |
Jaký přínos mají 3D tištěné implantáty z nerezové oceli pro pacienty? | 3D tištěné implantáty z nerezové oceli mohou zajistit přesnější uchycení, podpořit srůstání kosti a snížit riziko infekce, což může vést k lepším výsledkům u pacientů. |
Jaké jsou některé problémy spojené s 3D tištěnými zdravotnickými prostředky z nerezové oceli? | Mezi výzvy patří náklady na technologii, potřeba jasných předpisů a standardizace protokolů a materiálů. |
Jaká je budoucnost 3D tištěné nerezové oceli ve zdravotnických prostředcích? | Budoucnost je jasná, s potenciálem pro lepší výsledky pacientů, personalizovanou medicínu a snížení nákladů na zdravotní péči. |
Závěr
3D tisk z nerezové oceli přináší revoluci do odvětví zdravotnických přístrojů. Tato inovativní technologie nabízí řadu výhod pro pacienty, chirurgy i celý systém zdravotní péče. S dalším rozvojem 3D tisku můžeme očekávat, že se objeví ještě více převratných aplikací, které budou utvářet budoucnost medicíny a zlepšovat životy nespočtu pacientů.
Sdílet na
MET3DP Technology Co., LTD je předním poskytovatelem řešení aditivní výroby se sídlem v Qingdao v Číně. Naše společnost se specializuje na zařízení pro 3D tisk a vysoce výkonné kovové prášky pro průmyslové aplikace.
Dotaz k získání nejlepší ceny a přizpůsobeného řešení pro vaše podnikání!
Související články
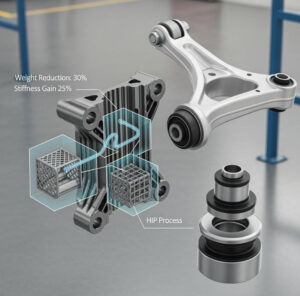
Metal 3D Printed Subframe Connection Mounts and Blocks for EV and Motorsport Chassis
Přečtěte si více "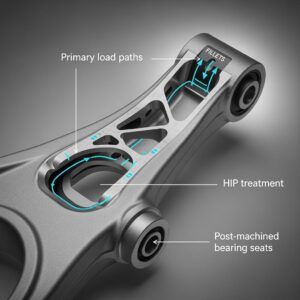
Metal 3D Printing for U.S. Automotive Lightweight Structural Brackets and Suspension Components
Přečtěte si více "O Met3DP
Nedávná aktualizace
Náš produkt
KONTAKTUJTE NÁS
Nějaké otázky? Pošlete nám zprávu hned teď! Po obdržení vaší zprávy obsloužíme vaši žádost s celým týmem.