Řešení problémů s plazmovou atomizací pro 3D tisk kovových prášků
Obsah
Plazmová atomizace, kritická fáze ve výrobě vysoce kvalitních kovových prášků pro Kovové prášky pro 3D tisk, se může někdy setkat s problémy, které ovlivňují kvalitu a tisknutelnost konečného produktu. Pokud se potýkáte s problémy s procesem plazmové atomizace, nebojte se! Tato příručka vás vybaví znalostmi a strategiemi pro odstraňování běžných problémů a optimalizaci procesu pro konzistentní úspěch.
Pochopení plazmové atomizace pro 3D tisk kovových prášků:
Plazmová atomizace, často srovnávaná s dotekem sochaře, přesahuje lidskou sféru tím, že využívá sílu intenzivního tepla a pečlivého inženýrství. Představte si proces, který přeměňuje roztavený kov, typicky prostřednictvím elektrického oblouku, na množství drobných, dokonale tvarovaných koulí. To je v podstatě podstata plazmové atomizace – technologie zásadní pro svět 3D tisku.
Zde je rozpis tohoto procesu:
- Roztavená múza: Cesta začíná přeměnou kovu do kapalného stavu působením intenzivního tepla. Tento roztavený kov se stává surovinou pro transformaci.
- Plazmová hranice: Na scénu vstupuje vysokoteplotní plazmový hořák, v podstatě proud ionizovaného plynu. Tento hořák, poháněný inertními plyny, jako je argon, generuje teploty přesahující několik tisíc stupňů Celsia.
- Od kapičky ke kouli: Jak se roztavený kov setkává s žhavou plazmou, rozpadá se na množství jemných kapiček. Tyto roztavené kapičky, na okamžik suspendované ve vzduchu, se stávají plátnem pro finální transformaci.
- Rychlé tuhnutí: Klíčem k dosažení dokonalé koule je proces rychlého chlazení. Díky své malé velikosti a vystavení okolnímu prostředí tyto kapičky téměř okamžitě ztuhnou. Toto rychlé ztuhnutí zabraňuje tvorbě nežádoucích krystalických struktur, což vede k téměř dokonalým koulím.
- Práškové potomstvo: Konečným produktem tohoto složitého tance tepla a přesnosti je sbírka sférických kovových částic – kýžený kovový prášek. Tyto prášky, známé svou vysokou čistotou, tekutostí a konzistentním tvarem, jsou zásadní ve světě 3D tisku.
Plazmová atomizace s přesnou kontrolou teploty a chlazení umožňuje vytváření vysoce kvalitních kovových prášků pro různé aplikace, nejen pro 3D tisk. Dláždí cestu pro pokrok v různých oblastech, jako je letectví, lékařské implantáty a dokonce i lehké automobilové komponenty.
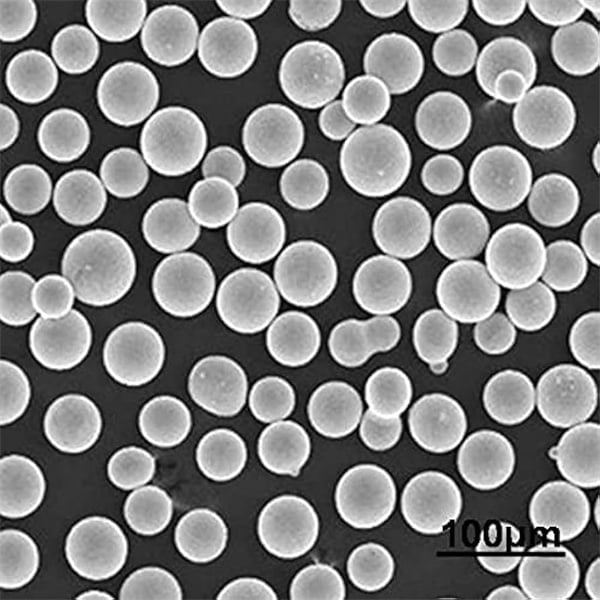
Běžné problémy s odstraňováním problémů a řešení:
- Velikost a distribuce částic:
- Problém: Práškové částice nemají jednotnou velikost, což vede k nekonzistentnímu toku, hustotě balení a tisknutelnosti.
- Řešení:
- Upravte parametry plazmového hořáku: Doladěním výkonu plazmy, průtoku plynu a průměru trysky kontrolujte velikost a distribuci kapiček.
- Optimalizujte vstupní materiál: Ujistěte se, že kovová vsázka neobsahuje nečistoty a má požadovaný bod tání a charakteristiky toku.
- Sféricita a morfologie:
- Problém: Práškové částice nejsou dokonale sférické, což ovlivňuje tekutost, hustotu balení a mechanické vlastnosti konečného produktu.
- Řešení:
- Zdokonalte proces atomizace: Experimentujte s různými typy plazmového plynu, tlakem a podmínkami chlazení, abyste podpořili sférické tuhnutí.
- Techniky následného zpracování: Zvažte zavedení metod prosévání nebo klasifikace pro oddělení požadované velikosti částic a frakcí morfologie.
- Obsah kyslíku:
- Problém: Nadměrný obsah kyslíku v prášku může vést k oxidaci během tisku, což způsobuje vady a oslabené části.
- Řešení:
- Implementujte řízenou atmosféru: Použijte prostředí inertního plynu, jako je argon nebo dusík, během atomizace, abyste minimalizovali vystavení kyslíku.
- Optimalizujte následné zpracování: Použijte vakuové odplyňovací techniky k odstranění veškerého zbývajícího kyslíku zachyceného v částicích prášku.
- Tvorba satelitů:
- Problém: Malé satelitní částice se připojují k větším, což způsobuje problémy s tekutostí a potenciálně vede k vadám v konečné tištěné části.
- Řešení:
- Zdokonalte parametry atomizace: Upravte vlastnosti plazmového hořáku a podmínky chlazení, abyste minimalizovali tvorbu satelitních kapiček.
- Následné zpracování: Použijte techniky prosévání nebo klasifikace k odstranění satelitních částic z požadované frakce prášku.
Další tipy pro hladký proces plazmové atomizace:
Stejně jako jakýkoli složitý tanec vyžaduje dosažení hladkého a úspěšného procesu plazmové atomizace kombinaci přípravy a jemného ladění. Zde je několik dalších tipů, které zajistí, že váš proces poběží jako hodinky:
1. Síla údržby: Podobně jako dobře udržovaný hudební nástroj vydává nejlepší zvuk, je pravidelná údržba zásadní pro vaše zařízení pro plazmovou atomizaci. To zahrnuje rutinní kontroly, čištění a výměnu opotřebovaných dílů. Zajištěním toho, že je vše ve špičkovém stavu, můžete výrazně snížit riziko neočekávaných poruch a zpoždění výroby.
2. Oči procesu: Stejně jako sochař studuje svou práci, aby doladil detaily, hraje analýza dat a monitorování procesů zásadní roli při optimalizaci plazmové atomizace. Využijte dostupné monitorovací systémy ke shromažďování informací z každé šarže. Analyzujte tato data, abyste identifikovali trendy a provedli úpravy parametrů procesu, jako jsou nastavení plazmového hořáku nebo rychlosti chlazení. Tato kontinuální zpětná vazba vám umožňuje dosáhnout konzistentní kvality prášku a vyhnout se nesrovnalostem v konečném produktu.
3. Hledání moudrosti zkušeností: I ten nejzkušenější sochař může občas potřebovat radu. Podobně, pokud se během procesu plazmové atomizace setkáte s přetrvávajícími problémy, neváhejte vyhledat radu zkušených odborníků. Jejich odbornost může poskytnout cenné poznatky o odstraňování problémů a optimalizaci vašeho procesu pro úspěch. Využitím jejich znalostí můžete překonat výzvy a zajistit hladký provoz vašeho systému plazmové atomizace.
Pamatujte, že dosažení konzistentních a vysoce kvalitních výsledků v plazmové atomizaci vyžaduje proaktivní přístup, který kombinuje pečlivou přípravu, analýzu založenou na datech a moudrost zkušených odborníků. Začleněním těchto dalších tipů můžete proměnit svůj proces plazmové atomizace v symfonii přesnosti a efektivity.
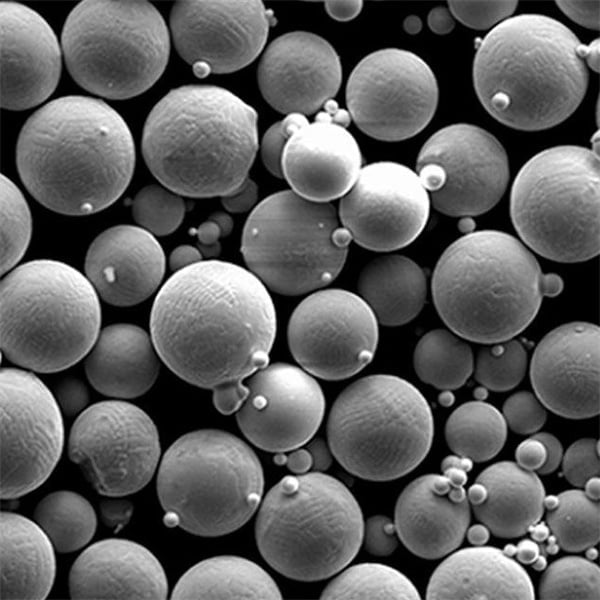
Závěr:
Pochopením potenciálních problémů a implementací těchto strategií pro odstraňování problémů můžete efektivně optimalizovat svůj proces plazmové atomizace a zajistit výrobu vysoce kvalitních kovových prášků pro úspěšné projekty 3D tisku. Pamatujte, že konzistentní monitorování, kontrola procesu a proaktivní přístup jsou klíčem k dosažení konzistentního úspěchu v plazmové atomizaci.
Často kladené otázky:
1. Jaké jsou výhody použití plazmové atomizace pro 3D tisk kovových prášků?
Plazmová atomizace nabízí několik výhod oproti jiným metodám:
- Vysoká čistota: Vysoké teploty dosažené během procesu minimalizují riziko kontaminace, což vede k čistším práškům.
- Kulovitý tvar: Rychlé tuhnutí vytváří téměř dokonalé koule, což zlepšuje tekutost a hustotu balení pro lepší výkon 3D tisku.
- Jemnější částice: Plazmová atomizace umožňuje vytváření jemnějších prášků ve srovnání s jinými metodami, což umožňuje tisk složitých detailů.
- Širší kompatibilita materiálů: Tento proces funguje se širší škálou kovů ve srovnání s některými jinými metodami, což nabízí větší všestrannost.
2. Jaká jsou omezení atomizace plazmatu?
I když je plazmová atomizace výhodná, má některá omezení:
- Vyšší náklady: Komplexní nastavení a vysoká spotřeba energie z něj činí nákladnější proces ve srovnání s některými alternativami.
- Dopad na životní prostředí: Vysoká spotřeba energie může vést k větší ekologické stopě ve srovnání s jinými metodami.
- Omezená výrobní kapacita: Ve srovnání s jinými technikami má plazmová atomizace často nižší výrobní kapacitu.
3. Jaké jsou některé běžné aplikace plazmově atomizovaných kovových prášků v 3D tisku?
Plazmově atomizované prášky se používají v různých 3D tiskových aplikacích, včetně:
- Letectví: Tisk lehkých a vysoce pevných součástí pro letadla a kosmické lodě.
- Lékařské implantáty: Vytváření vlastních protetických pomůcek a implantátů s vynikající biokompatibilitou.
- Automobilový průmysl: Tisk lehkých a složitých součástí pro automobily a další vozidla.
- Spotřební zboží: Výroba přizpůsobených a složitých kovových předmětů pro různé aplikace.
4. Jak se plazmová atomizace srovnává s jinými metodami výroby kovových prášků pro 3D tisk?
Zde je rychlé srovnání:
- Rozprašování plynu: Podobný proces s nižšími energetickými nároky, ale může mít za následek méně sférické a čisté prášky.
- Rozprašování vody: Nákladově efektivní, ale omezeno na specifické materiály a často produkuje nepravidelné tvary částic.
- Elektrodepozice: Vytváří jemné prášky, ale je to pomalejší proces a často omezeno na specifické materiály.
5. Jaké jsou budoucí trendy v plazmové atomizaci pro 3D tisk?
Budoucí trendy zahrnují:
- Vývoj v technologii plazmových hořáků: Optimalizace designu hořáku a řídicích systémů pro zlepšení účinnosti a kvality prášku.
- Zaměření na udržitelnost: Zkoumání způsobů, jak snížit spotřebu energie a dopad procesu na životní prostředí.
- Zkoumání nových materiálů: Rozšíření rozsahu kovů a slitin vhodných pro plazmovou atomizaci a 3D tisk.
Sdílet na
MET3DP Technology Co., LTD je předním poskytovatelem řešení aditivní výroby se sídlem v Qingdao v Číně. Naše společnost se specializuje na zařízení pro 3D tisk a vysoce výkonné kovové prášky pro průmyslové aplikace.
Dotaz k získání nejlepší ceny a přizpůsobeného řešení pro vaše podnikání!
Související články
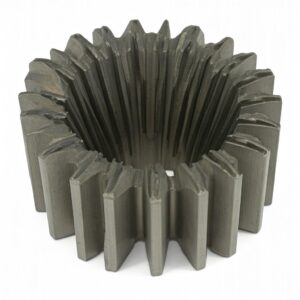
Vysoce výkonné segmenty lopatek trysek: Revoluce v účinnosti turbín díky 3D tisku z kovu
Přečtěte si více "O Met3DP
Nedávná aktualizace
Náš produkt
KONTAKTUJTE NÁS
Nějaké otázky? Pošlete nám zprávu hned teď! Po obdržení vaší zprávy obsloužíme vaši žádost s celým týmem.
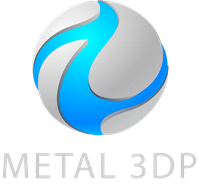
Kovové prášky pro 3D tisk a aditivní výrobu