Dodavatelé prášků pro 3D tisk
Obsah
Přehled o Dodavatelé prášků pro 3d tisk
Prášky pro 3d tisk, známá také jako aditivní výroba, využívá prášky jako surovinu pro výrobu komponent po vrstvách. Prášky se taví nebo spojují dohromady pomocí tepla, laseru nebo pojiv a vytvářejí tak trojrozměrné objekty.
Při 3D tisku se používá několik technologií, jako je selektivní laserové spékání (SLS), přímé laserové spékání kovů (DMLS), tavení elektronovým svazkem (EBM), tryskání pojiva, modelování pomocí tavené vrstvy (FDM), stereolitografie (SLA) a další. Každý proces využívá různé typy prášků se specifickými vlastnostmi a distribucí velikosti částic.
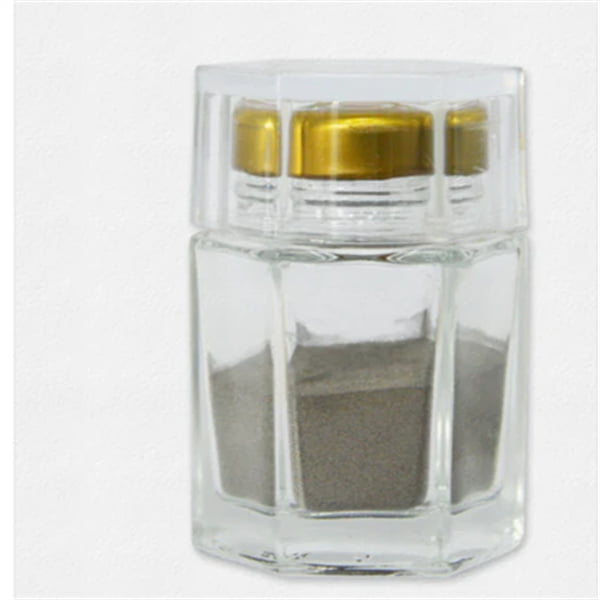
Typy 3D tiskových prášků
Typ prášku | Materiály | Charakteristika |
---|---|---|
Plasty | Nylon, ABS, TPU, PE, PP | Nejběžnější, nízké náklady, menší pevnost |
Kovy | Hliník, nerezová ocel, kobaltový chrom, titan, nástrojová ocel | Vysoká pevnost, odolnost proti teplu a korozi |
Keramika | Sklo, oxid hlinitý, zirkon | Použití při vysokých teplotách, křehké |
Písek a odlévací prášky | Křemičitý písek, zirkonový písek | Pro pískové formy a jádra |
Magnetické prášky | Železo, nikl, kobalt | Aplikace vyžadující magnetismus |
Biokompatibilní prášky | Titan, PEEK, TCP | Pro lékařské implantáty, protézy |
Vlastnosti 3D tiskových prášků
Vlastnictví | Popis | Význam v aditivní výrobě |
---|---|---|
Morfologie částic | To se týká tvaru a povrchových vlastností částic prášku. | Sférické nebo téměř sférické částice jsou ideální pro optimální tekutost, hustotu balení a tisknutelnost. Částice nepravidelného tvaru mohou bránit toku prášku a vést k nesrovnalostem ve vytištěném dílu. |
Distribuce velikosti částic | Velikost částic prášku hraje zásadní roli při určování několika aspektů výsledného tištěného dílu. | Úzká distribuce velikosti částic zajišťuje konzistentní balení a minimalizuje dutiny v tištěných vrstvách. Velikost částic ovlivňuje také povrchovou úpravu, přičemž jemnější částice obvykle vedou k hladšímu povrchu. Příliš jemné částice však mohou být náročné na manipulaci a mohou snižovat tekutost. |
Zdánlivá hustota a hustota kohoutku | Tyto vlastnosti představují objemovou hmotnost prášku za různých podmínek. | Zdánlivá hustota zohledňuje mezery mezi částicemi v klidovém stavu, zatímco hustota při poklepu odráží více zaplněný stav dosažený standardizovaným procesem poklepu. Vyšší hustota závitů je obecně žádoucí pro efektivní využití materiálu a dobrou rozměrovou přesnost tištěného dílu. |
Tekutost | To se týká snadnosti, s jakou prášek teče pod vlivem gravitace nebo jiných působících sil. | Dobrá tekutost je nezbytná pro rovnoměrné nanášení prášku během procesu aditivní výroby. Prášky se špatnou tekutostí mohou vést k nesrovnalostem v tloušťce vrstvy a potenciálním vadám tisku. |
Tepelné vlastnosti | Ty zahrnují vlastnosti, jako je bod tání, tepelná vodivost a koeficient tepelné roztažnosti. | Tepelné vlastnosti významně ovlivňují chování prášku během procesu tisku. Teplota tání určuje výkon laseru nebo zdroje energie potřebný pro tavení, zatímco tepelná vodivost ovlivňuje distribuci tepla a případné deformace tištěného dílu. Koeficient tepelné roztažnosti je třeba zohlednit, aby se minimalizovala zbytková napětí a praskání během chlazení. |
Spékavost | Tato vlastnost se týká schopnosti částic prášku spojovat se během tisku. | Spékavost má zásadní význam pro dosažení pevných a soudržných vazeb mezi vrstvami, což vede k robustnímu finálnímu dílu. Spékavost ovlivňují faktory, jako je velikost částic, chemické složení povrchu a složení materiálu. |
Chemické složení | Konkrétní prvky nebo sloučeniny obsažené v prášku určují jeho celkové vlastnosti a vhodnost pro různé aplikace. | Chemické složení přímo ovlivňuje mechanické vlastnosti, odolnost proti korozi a další výkonnostní charakteristiky konečného tištěného dílu. Například prášky z kovových slitin se specifickými prvky mohou nabídnout vysokou pevnost nebo lepší biokompatibilitu pro lékařské implantáty. |
Aplikace z Prášky pro 3D tisk
Průmysl | Aplikace |
---|---|
Aerospace | Lopatky turbín, trysky proudových motorů, konstrukční rámy |
Automobilový průmysl | Prototypování, zakázkové díly, jako jsou ozubená kola |
Lékařský | Zubní náhrady, implantáty, protetika |
Nástroje | Odlévací vzory, vstřikovací formy, přípravky a přípravky |
Architektura | Modely, dekorativní stavební prvky |
Spotřební zboží | Zakázkové návrhy, rychlé prototypování |
Specifikace 3D tiskového prášku
Práškové materiály používané v aditivní výrobě musí splňovat přísné specifikace pro distribuci velikosti částic, morfologii, tekutost a čistotu. Níže jsou uvedeny typické rozsahy velikostí, standardy a třídy:
Typ materiálu | Velikost částic (μm) | Normy | Společné známky |
---|---|---|---|
Polymerní prášky | 20-150 | ASTM D638 | PA12, PLA, ABS, PC |
Kovové prášky | 10-45 | ASTM F3049 | Ti-6Al-4V, 17-4PH, 316L |
Keramické prášky | 10-150 | ASTM F2792 | Zirkon, oxid hlinitý, TCP |
Odlévací prášky | 140-200 | ASTM B213 | Křemičitý písek, zirkonový písek |
Globální dodavatelé 3d tiskových prášků
Existují jak velcí globální dodavatelé, tak i menší výrobci prášků, kteří poskytují služby v oblasti aditivní výroby:
Velcí výrobci prášku
Společnost | Materiály |
---|---|
Sandvik | Slitiny niklu a titanu |
Prášková metalurgie GKN | Nástrojové oceli, nerezové oceli |
Höganäs | Nerezové oceli, slitiny |
Přísada pro tesaře | Kobaltový chrom, titan, další |
BASF | Ultrajemné polyamidy |
Výrobci speciálních prášků
Společnost | Materiály |
---|---|
Technologie LPW | Hliník, titan, slitiny Ni |
Praxair | titanové, niklové superslitiny |
Arcam AB | Slitiny titanu, CoCr, hliník |
3DXtech | Plasty jako ABS, nylon a další |
Analýza nákladů na kovové 3D tiskové prášky
Faktor | Popis | Dopad na náklady |
---|---|---|
Náklady na materiál | Jedná se o základní cenu za kilogram samotného prášku z kovové slitiny. | Cena prášků z kovových slitin se může výrazně lišit v závislosti na konkrétním složení slitiny. Prášky pro běžně používané materiály, jako je nerezová ocel nebo hliník, bývají cenově dostupnější ve srovnání s prášky pro vysoce výkonné slitiny, jako jsou superslitiny niklu nebo aluminid titanu. Přítomnost prvků vzácných zemin nebo složité výrobní procesy mohou navíc cenu prášku dále zvýšit. |
Objem prášku | Množství prášku z kovové slitiny potřebné pro konkrétní tiskovou úlohu přímo ovlivňuje celkové náklady na materiál. | Pečlivá optimalizace konstrukce a minimalizace podpůrných struktur může pomoci snížit celkový potřebný objem prášku, což vede k úspoře nákladů. Kromě toho může být pro velkoobjemovou výrobu výhodné využití systémů zpětného získávání prášku, které zachycují a znovu využívají nepotištěný prášek. |
Výběr dodavatele | Výběr renomovaného dodavatele kovového prášku může ovlivnit náklady. | Vyjednávání o smlouvách o hromadném nákupu nebo zkoumání alternativních dodavatelů s konkurenčními cenovými strategiemi může pomoci optimalizovat náklady na materiál. Zásadní je vyvážit cenu s faktory, jako je kvalita prášku, konzistence a technická podpora nabízená dodavatelem. |
Vlastnosti prášku | Specifické vlastnosti prášku z kovové slitiny mohou ovlivnit jeho cenu. | Jemnější prášky obecně vyžadují složitější výrobní procesy a mohou být dražší. Prášky s úzkou distribucí velikosti částic nebo se specifickou povrchovou úpravou pro lepší sypnost mohou mít navíc vyšší cenu. |
Minimální množství objednávky | Někteří dodavatelé mohou mít u prášků z kovových slitin minimální objednací množství. | To může představovat nákladové hledisko, zejména při výrobě prototypů nebo při malosériové výrobě. Prozkoumání dodavatelů s menšími minimálními objednacími množstvími nebo spolupráce s jinými uživateli za účelem sdílení hromadných nákupů může být nákladově efektivní strategií. |
Náklady na následné zpracování | Kovové díly vytištěné pomocí 3D tiskových prášků často vyžadují následné zpracování, jako je tepelné zpracování nebo izostatické lisování za tepla (HIP), aby bylo dosaženo optimálních mechanických vlastností. | Náklady na tyto kroky následného zpracování je třeba zahrnout do celkové analýzy. V některých případech může potřeba rozsáhlého následného zpracování negovat potenciální nákladové výhody 3D tisku ve srovnání s tradičními výrobními metodami. |
Výhody a nevýhody Prášky pro 3D tisk
Klady | Nevýhody |
---|---|
Flexibilita designu: Práškové 3D tisky umožňují vytvářet složité geometrie se složitými prvky, kterých je obtížné nebo nemožné dosáhnout tradičními výrobními metodami. To otevírá dveře inovativním konstrukcím a lehkým součástem v různých průmyslových odvětvích. | Omezený výběr materiálů: Ve srovnání s tradičními výrobními technikami se výběr prášků pro 3D tisk stále vyvíjí. I když je k dispozici široká škála materiálů, některé slitiny nebo speciální materiály nemusí být snadno dostupné nebo mohou vyžadovat kvalifikaci pro specifické tiskové procesy. |
Účinnost materiálu: Prášky pro 3D tisk podporují výrobu téměř čistého tvaru, což minimalizuje plýtvání materiálem ve srovnání se subtraktivními technikami, jako je obrábění. To je výhodné zejména u drahých nebo vysoce výkonných materiálů. | Vyšší náklady: Samotné prášky pro 3D tisk mohou být dražší než sypké materiály kvůli dodatečnému zpracování při jejich výrobě. Kromě toho mohou zařízení pro 3D tisk a kroky následného zpracování přispět k vyšším celkovým výrobním nákladům, zejména u malosériové výroby. |
Vlastnosti na míru: Vlastnosti prášků pro 3D tisk lze přesně řídit úpravami výrobního procesu a složení prášku. To umožňuje vytvářet materiály se specifickými vlastnostmi, jako je vysoká pevnost, lehká konstrukce nebo biokompatibilita pro lékařské aplikace. | Povrchová úprava: Povrchová úprava dílů vytištěných pomocí 3D tiskových prášků může být ve srovnání s obráběnými nebo litými součástmi hrubší. K dosažení požadované kvality povrchu mohou být nutné další techniky následného zpracování, jako je leštění nebo obrábění. |
Rychlé prototypování: Prášky pro 3D tisk jsou ideální pro rychlou výrobu prototypů složitých dílů. To umožňuje rychlejší iterace návrhu a zkrácení doby uvedení nových výrobků na trh. | Obavy o bezpečnost: Manipulace s některými prášky pro 3D tisk může představovat bezpečnostní riziko kvůli potenciální hořlavosti, riziku vdechnutí a podráždění kůže. Správné osobní ochranné pomůcky a dodržování bezpečnostních protokolů jsou nezbytné. |
Řízení zásob: 3D tisk umožňuje výrobu na vyžádání za použití snadno dostupných prášků. To snižuje potřebu rozsáhlé správy zásob předem vyrobených dílů. | Řízení procesu: Aditivní výrobní procesy zahrnující 3D tisk prášků vyžadují pečlivou kontrolu parametrů, jako je výkon laseru, rychlost skenování a tloušťka vrstvy. Nesrovnalosti v těchto parametrech mohou ovlivnit kvalitu a výkonnost finálního vytištěného dílu. |
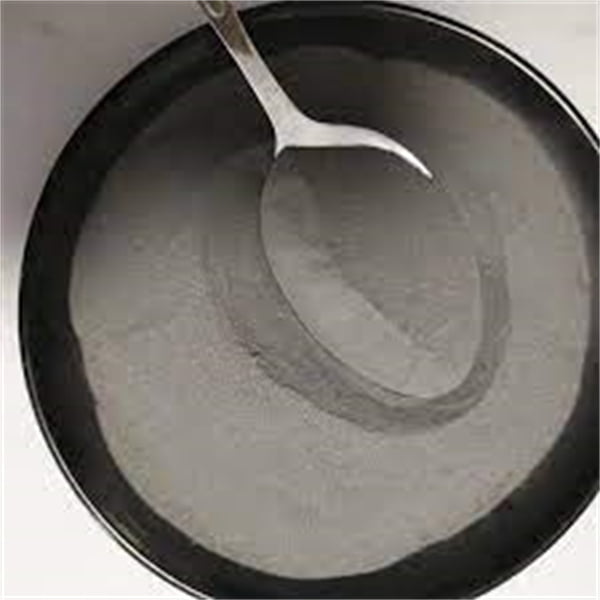
FAQ
Otázka: Jaký je nejčastěji používaný plast pro práškový 3D tisk?
Odpověď: Polyamid 12 (PA12, nylon 12) je nejoblíbenější plastový prášek s vynikajícími vlastnostmi a kompatibilitou s procesem SLS.
Otázka: Jaký je rozdíl mezi panenským a recyklovaným práškem?
Odpověď: Panenské prášky jsou čerstvé a nepoužité ve srovnání s recyklovanými prášky, které pocházejí z předchozích 3D tištěných dílů. Panenský prášek je dražší, ale nabízí vyšší a konzistentnější kvalitu.
Otázka: Jak se vyrábí kovové prášky pro aditivní výrobu?
Odpověď: Kovové prášky se vyrábějí pomocí plynové nebo vodní atomizace, při níž se z roztavených surovin pod vysokým tlakem vytvářejí jemné sférické částice slitin. Prášky mohou být podrobeny specializovaným úpravám za účelem úpravy distribuce velikosti, morfologie, toku nebo složení.
Otázka: Jaká opatření je třeba dodržovat při manipulaci s prášky?
Odpověď: Postupy při manipulaci s práškem musí být zaměřeny na minimalizaci expozice, omezení úniku a rozlití, zajištění správných masek/PPE výstroje, zajištění odpovídajícího větrání a zavedení správné praxe udržování pořádku. Některé kovové prášky mohou při neopatrné manipulaci hořet nebo explodovat.
Otázka: Jaká velikost částic prášku je optimální?
Odpověď: Nejlepších výsledků při rovnoměrném roztírání tenkých vrstev obvykle dosahují částice o velikosti od 10 mikronů do přibližně 100 mikronů. Jemnější nanočástice mohou aglomerovat, zatímco velké částice snižují rozlišovací schopnost. Zásadní je přizpůsobit velikost částic požadavkům 3D tiskárny.
Otázka: Jak ovlivňují prášky vlastnosti dílů?
Odpověď: Vlastnosti prášku přímo ovlivňují hustotu, povrchovou úpravu, přesnost, mechanické vlastnosti, mikrostrukturu a výkonnost tištěných součástí. Odstupňované vlastní slitiny a povlaky částic umožňují přizpůsobit vlastnosti materiálu při aditivní výrobě.
Sdílet na
MET3DP Technology Co., LTD je předním poskytovatelem řešení aditivní výroby se sídlem v Qingdao v Číně. Naše společnost se specializuje na zařízení pro 3D tisk a vysoce výkonné kovové prášky pro průmyslové aplikace.
Dotaz k získání nejlepší ceny a přizpůsobeného řešení pro vaše podnikání!
Související články
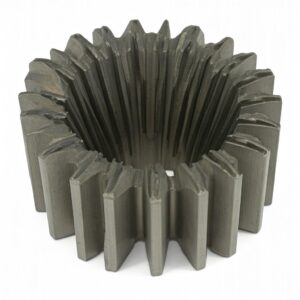
Vysoce výkonné segmenty lopatek trysek: Revoluce v účinnosti turbín díky 3D tisku z kovu
Přečtěte si více "O Met3DP
Nedávná aktualizace
Náš produkt
KONTAKTUJTE NÁS
Nějaké otázky? Pošlete nám zprávu hned teď! Po obdržení vaší zprávy obsloužíme vaši žádost s celým týmem.
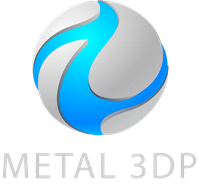
Kovové prášky pro 3D tisk a aditivní výrobu