Úvod do přímého laserového spékání kovů (DMLS)
Obsah
Kouzlo 3D tisku kovů
Představte si svět, kde se složité kovové díly materializují z lože prášku, vrstvu po vrstvě, s laserovou přesností. To není sci-fi; je to realita přímého laserového slinování kovů (DMLS), revoluční technologie 3D tisku, která transformuje způsob, jakým navrhujeme a vyrábíme kovové součásti.
DMLS, známý také jako selektivní laserové tavení (SLM) nebo fúze laserového práškového lože (LPBF), je proces aditivní výroby, který používá vysoce výkonný laser k selektivnímu tavení a spojování kovových částic dohromady a vytváří 3D objekt z digitálního návrhu. Tato technologie nabízí bezkonkurenční svobodu v designu, což umožňuje vytváření složitých geometrií a vnitřních prvků, které jsou nemožné tradičními technikami, jako je odlévání nebo obrábění.
Ale DMLS není jen o skvělých tvarech. Může se pochlubit řadou výhod, včetně:
- Výjimečná pevnost a přesnost: DMLS vyrábí díly s vynikajícími mechanickými vlastnostmi, které konkurují vlastnostem tradičně vyráběných součástí. Navíc přístup vrstva po vrstvě zajišťuje výjimečnou rozměrovou přesnost.
- Potenciál odlehčení: Zahrnutím vnitřních mřížek a dutých struktur umožňuje DMLS vytváření lehkých, ale robustních dílů, což je hlavní výhoda v odvětvích, jako je letectví a automobilový průmysl.
- Svoboda designu: Uvolněte svou kreativitu! DMLS odstraňuje omezení konvenčních metod a umožňuje výrobu složitých geometrií a vnitřních prvků, kterých by bylo jinak neuvěřitelně obtížné nebo dokonce nemožné dosáhnout.
- Rychlé prototypování: DMLS umožňuje rychlé a efektivní vytváření funkčních prototypů, což urychluje proces návrhu a vývoje.
- Hromadné přizpůsobení: DMLS umožňuje výrobu přizpůsobených dílů v malých dávkách, což je ideální pro aplikace s malým objemem nebo personalizované produkty.
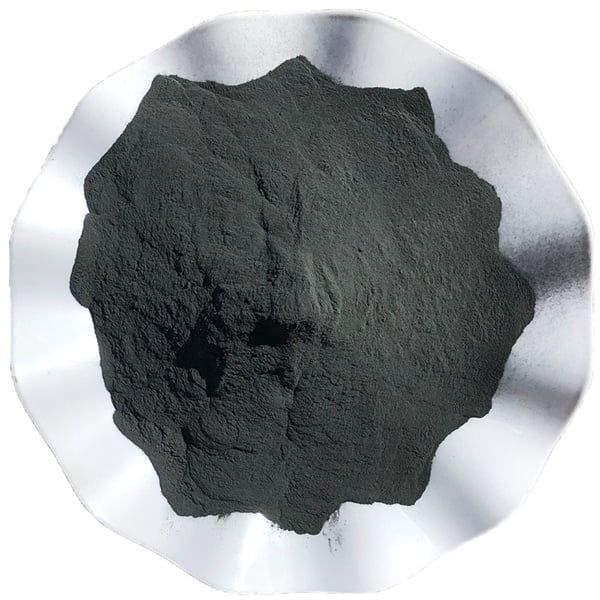
Stavební kameny DMLS
Srdcem procesu DMLS jsou použité kovové prášky. Tyto jemné kovové částice, obvykle o velikosti 20 až 40 mikrometrů, jsou pečlivě vybírány na základě požadovaných vlastností konečného dílu. Zde je bližší pohled na některé z nejběžněji používaných kovových prášků v DMLS spolu s jejich jedinečnými vlastnostmi:
Běžné kovové prášky DMLS:
Kovový prášek | Popis | Vlastnosti | Aplikace |
---|---|---|---|
Slitiny titanu (Ti-6Al-4V, Ti-6Al-4V ELI) | Pracovní kůň DMLS, který nabízí dobrou rovnováhu mezi pevností, hmotností a odolností proti korozi. | Vysoký poměr pevnosti k hmotnosti, vynikající biokompatibilita (stupeň ELI). | Letectví a kosmonautika, lékařské implantáty, sportovní zboží |
Nerezová ocel (316L, 17-4PH) | Všestranný a nákladově efektivní, s dobrými mechanickými vlastnostmi a odolností proti korozi. | Vynikající odolnost proti korozi (316L), vysoká pevnost a tvrdost (17-4PH). | Průmyslové komponenty, zařízení pro chemické zpracování, šperky |
Hliníkové slitiny (AlSi10Mg, AlSi7Mg0,3) | Lehké a nabízejí dobrou obrobitelnost pro následné zpracování. | Vynikající poměr pevnosti k hmotnosti, dobrá slévatelnost (AlSi7Mg0.3). | Automobilové díly, letecké a kosmické komponenty, výměníky tepla |
Inconel (IN625, 718) | Superslitiny proslulé svou vysokoteplotní pevností a odolností proti korozi. | Výjimečný výkon při zvýšených teplotách, dobrá odolnost proti oxidaci. | Součásti plynových turbín, raketové motory, výměníky tepla |
Kobalt-chrom (CoCr) | Biokompatibilní a odolné proti opotřebení, ideální pro lékařské implantáty. | Vynikající biokompatibilita, vysoká pevnost a odolnost proti opotřebení. | kloubní náhrady, zubní implantáty, chirurgické nástroje |
měď (Cu) | Vysoce vodivé, takže jsou ideální pro elektrické aplikace. | Vynikající tepelná a elektrická vodivost. | Chladiče, elektronické součástky, vlnovody |
nikl (Ni) | Čistý nikl nabízí kombinaci pevnosti, tažnosti a odolnosti proti korozi. | Vysoká pevnost, dobrá tažnost a odolnost proti korozi. | Elektrody, zařízení pro chemické zpracování, pájecí materiály |
Nástrojová ocel (H13, M2) | Navrženy pro vysokou odolnost proti opotřebení a houževnatost. | Vynikající odolnost proti opotřebení, vysoká tvrdost (H13), dobrá houževnatost (M2). | Řezné nástroje, formy a matrice, otěruvzdorné desky |
Drahé kovy (zlato, stříbro, platina) | Cenné pro svou estetickou přitažlivost a jedinečné vlastnosti. | Vysoká hodnota, vynikající elektrická vodivost (zlato, stříbro), vysokoteplotní stabilita (platina). | Šperky, dekorativní díly, elektrické kontakty |
Žáruvzdorné kovy (wolfram, tantal) | Nabízejí výjimečnou vysokoteplotní pevnost a odolnost vůči drsným prostředím. | Velmi vysoké body tání, vynikající odolnost proti opotřebení (wolfram |
Průběh procesu DMLS
Nyní, když jsme prozkoumali stavební kameny DMLS, pojďme se ponořit do samotného fascinujícího procesu. Zde je rozpis typického pracovního postupu při vytváření kovového dílu pomocí DMLS:
- Digitální design: Cesta začíná 3D modelem (CAD) požadovaného dílu s počítačovou podporou. Tento model definuje přesnou geometrii, rozměry a vnitřní prvky konečné součásti. Software speciálně navržený pro aditivní výrobu se často používá k zajištění toho, aby byl model optimalizován pro 3D tisk DMLS.
- Krájení dat: 3D CAD model je poté rozřezán na sérii extrémně tenkých průřezů, obvykle v tloušťce od 20 do 100 mikrometrů. Každý řez představuje jednu vrstvu, kterou bude stroj DMLS stavět. Představte si digitální stoh výkresů, z nichž každý podrobně popisuje konkrétní vrstvu dílu.
- Příprava práškového lože: Uvnitř stroje DMLS se rovnoměrně nanese vrstva jemného kovového prášku na stavební plošinu. Tato vrstva odpovídá prvnímu řezu digitálního modelu. Plošina se může přesně pohybovat nahoru a dolů, což umožňuje vytváření následných vrstev.
- Selektivní laserové tavení: Vysokoenergetický laserový paprsek, typicky vláknový laser, skenuje práškové lože podle dat z rozřezaného modelu. Laser roztaví kovové částice ve vyznačených oblastech, spojí je dohromady a vytvoří první pevnou vrstvu dílu.
- Konstrukce vrstva po vrstvě: Proces se opakuje – nanese se čerstvá vrstva prášku a laser selektivně roztaví požadované části a spojí je s předchozí vrstvou. Tento cyklus pokračuje pečlivě, buduje díl vrstvu po vrstvě, dokud není celý objekt dokončen.
- Odstranění podpory: Jakmile je proces tisku dokončen, stavební plošina se spustí a odhalí nově vytvořený kovový díl. Díl však může být obklopen podpůrnými strukturami, které byly vytištěny spolu s ním, aby se zabránilo prohýbání nebo deformaci během stavby. Tyto podpůrné struktury se pečlivě odstraňují pomocí technik, jako je obrábění nebo řezání vodním paprskem.
- Následné zpracování: V závislosti na aplikaci a požadované povrchové úpravě může díl DMLS podstoupit další kroky následného zpracování, jako je tepelné zpracování, horké izostatické lisování (HIP) nebo pískování. Tyto procesy mohou zlepšit mechanické vlastnosti, zmírnit zbytková napětí a zlepšit kvalitu povrchu konečné součásti.
Technické charakteristiky DMLS
DMLS nabízí jedinečnou sadu technických charakteristik, které z něj činí výkonný nástroj pro různé aplikace. Zde je bližší pohled na některé z klíčových aspektů, které je třeba zvážit:
- Rozlišení a přesnost: DMLS se může pochlubit výjimečným rozlišením a rozměrovou přesností, typicky s tloušťkou vrstvy v rozmezí od 20 do 100 mikrometrů. To umožňuje vytváření vysoce složitých prvků a složitých geometrií.
- Povrchová úprava: Povrchová úprava dílů DMLS se může lišit v závislosti na použitém kovovém prášku a použitých technikách následného zpracování. Vlastní povaha procesu vrstva po vrstvě však může mít za následek poněkud stupňovitou povrchovou úpravu ve srovnání s tradičními metodami obrábění.
- Vlastnosti materiálu: Díly DMLS vykazují vynikající mechanické vlastnosti, často srovnatelné s vlastnostmi konvenčně vyráběných součástí. Faktory, jako je specifický kovový prášek, parametry stavby a následné zpracování, mohou ovlivnit konečné vlastnosti dílu.
- Objem sestavení: Stavební objem stroje DMLS určuje maximální velikost dílu, který lze vytisknout v jedné stavbě. Stavební objemy se mohou pohybovat od několika krychlových centimetrů až po několik krychlových metrů, což vyhovuje široké škále aplikací.
- Rychlost sestavení: Ve srovnání s některými dalšími technologiemi aditivní výroby může být DMLS relativně pomalý proces. Doba stavby závisí na velikosti a složitosti dílu, stejně jako na tloušťce vrstvy a nastavení výkonu laseru.
- Materiálový odpad: Na rozdíl od subtraktivních výrobních technik, které generují značný odpadní materiál, nabízí DMLS minimální odpad. Nepoužitý kovový prášek lze recyklovat a znovu použít v následných stavbách, čímž se minimalizuje spotřeba materiálu.
Oblasti použití DMLS
DMLS rychle transformuje rozmanitou škálu průmyslových odvětví díky svým jedinečným schopnostem. Zde jsou některé z významných oblastí použití, kde DMLS vyniká:
- Letectví: DMLS mění hru v letectví a kosmonautice a umožňuje vytváření lehkých, ale robustních součástí pro letadla a kosmické lodě. Složité vnitřní struktury a mřížkové návrhy mohou být začleněny pro optimalizaci výkonu a snížení hmotnosti, což je zásadní faktor pro palivovou účinnost.
- Lékařské implantáty: Biokompatibilní povaha určitých kovových prášků, jako je titan a kobaltový chrom, činí DMLS ideální pro výrobu přizpůsobených lékařských implantátů. Tyto implantáty lze přesně přizpůsobit anatomii pacienta a nabídnout tak dokonalé přizpůsobení a vylepšenou funkčnost.
- Automobilový průmysl: (Pokračování) Automobilový průmysl využívá DMLS k vytváření vysoce výkonných součástí, jako jsou písty, hlavy válců a části převodovky. Schopnost navrhovat lehké a složité struktury umožňuje snížení hmotnosti a zlepšení spotřeby paliva, což je hlavní výhoda na dnešním trhu šetrném k životnímu prostředí. DMLS navíc umožňuje vytváření přizpůsobených dílů pro závodní aplikace nebo vozidla v limitované edici.
- Výroba forem a matric: DMLS přináší revoluci ve výrobě forem a matric tím, že umožňuje výrobu složitých a konformních chladicích kanálů uvnitř forem. Tyto kanály zlepšují přenos tepla během procesu vstřikování, což vede k rychlejším dobám cyklu, lepší kvalitě dílů a sníženým výrobním nákladům.
- Spotřební zboží: DMLS se dostává na trh spotřebního zboží a umožňuje vytváření jedinečných a personalizovaných produktů, jako jsou šperky, brýle a sportovní zboží. Schopnost vyrábět složité geometrie otevírá nové možnosti designu, zatímco povaha DMLS na vyžádání vyhovuje trendu přizpůsobení.
- Vytváření prototypů: DMLS je výkonný nástroj pro rychlé prototypování, který umožňuje inženýrům a designérům rychle vytvářet funkční prototypy nových produktů. Tento cyklus rychlé iterace urychluje proces návrhu a vývoje, což vede k rychlejší inovaci produktů a uvedení na trh.
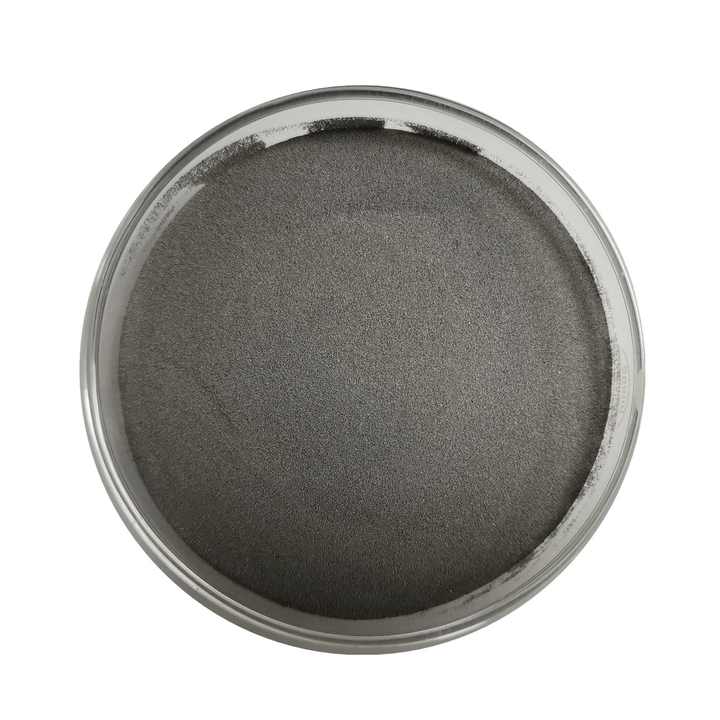
Omezení a úvahy DMLS
I když DMLS nabízí nepřeberné množství výhod, je nezbytné uznat jeho omezení a úvahy:
- Náklady: Stroje DMLS a kovové prášky mohou být drahé ve srovnání s tradičním výrobním zařízením a materiály. To může učinit DMLS méně vhodnou volbou pro velkoobjemovou výrobu jednoduchých dílů.
- Povrchová úprava: Jak již bylo zmíněno, povaha DMLS vrstva po vrstvě může mít za následek poněkud stupňovitou povrchovou úpravu. I když techniky následného zpracování mohou zlepšit kvalitu povrchu, dosažení dokonale hladké povrchové úpravy může vyžadovat další kroky obrábění, což zvyšuje náklady a složitost procesu.
- Doba výstavby: DMLS může být pomalý proces, zejména u velkých nebo složitých dílů. To je třeba zohlednit při zvažování dodacích lhůt a výrobních plánů.
- Podpůrné struktury: Požadavek na podpůrné struktury během procesu DMLS může přidat složitost a potenciálně zvýšit dobu následného zpracování. Pečlivé úvahy o návrhu mohou minimalizovat potřebu složitých podpůrných struktur.
- Kvalifikace dílů: Pro kritické aplikace v průmyslových odvětvích, jako je letectví a lékařství, mohou díly DMLS vyžadovat další testování a kvalifikační postupy, aby se zajistilo, že splňují přísné standardy výkonu a bezpečnosti.
DMLS vs. jiné technologie aditivní výroby
DMLS není jediným hráčem ve hře 3D tisku. Zde je rychlé srovnání DMLS s dalšími významnými technologiemi aditivní výroby, které vám pomohou vybrat ten správný nástroj pro danou práci:
- Stereolitografie (SLA): SLA používá laser k vytvrzování kapalné pryskyřice do pevného objektu, vrstvu po vrstvě. Ve srovnání s DMLS nabízí SLA vyšší rozlišení a hladší povrchovou úpravu, ale je omezena na menší rozsah materiálů, primárně plastů.
- Selektivní laserové slinování (SLS): SLS funguje podobně jako DMLS, ale používá laser ke slinování částic plastového prášku. SLS je obecně rychlejší a nákladově efektivnější než DMLS pro výrobu plastových dílů, ale nabízí nižší pevnost a omezené možnosti materiálů ve srovnání s DMLS pro kovové aplikace.
- Tavené depoziční modelování (FDM): FDM funguje vytlačováním roztaveného plastového vlákna pro stavbu objektu vrstvu po vrstvě. FDM je široce používaná a relativně levná technologie, ale nabízí nižší rozlišení a pevnost ve srovnání s DMLS.
- Tavení elektronovým svazkem (EBM): Podobně jako DMLS používá EBM elektronový paprsek k tavení kovového prášku. EBM vyniká při zpracování reaktivních kovů, jako je titan, ale vyžaduje vakuové prostředí, což z něj činí složitější a dražší proces ve srovnání s DMLS.
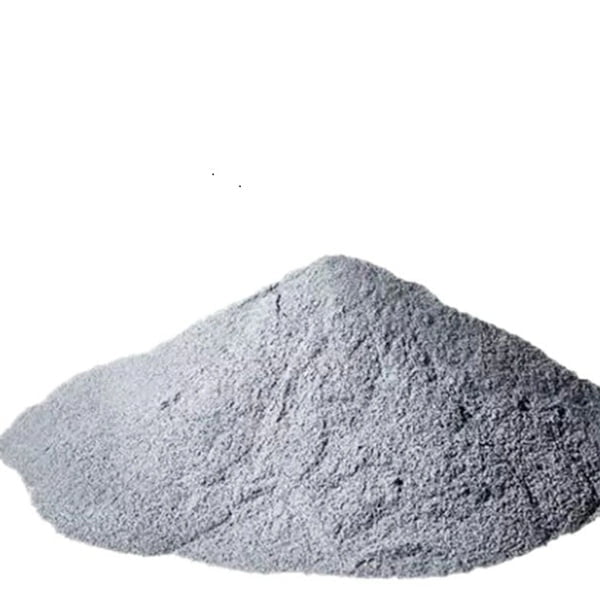
FAQ
Zde jsou některé z nejčastěji kladených otázek o DMLS:
Otázka: Jaké jsou výhody DMLS?
Odpověď: DMLS nabízí několik výhod, včetně výjimečné svobody designu, vysoké pevnosti a přesnosti dílů, potenciálu pro odlehčení, možností rychlého prototypování a minimálního odpadu materiálu.
Otázka: Jaká jsou omezení DMLS?
Odpověď: Omezení DMLS zahrnují jeho relativně vysoké náklady ve srovnání s tradiční výrobou, potenciální problémy s povrchovou úpravou, pomalejší doby stavby ve srovnání s některými dalšími technologiemi 3D tisku a potřebu dalších úvah, jako jsou podpůrné struktury a kvalifikace dílů pro určité aplikace.
Otázka: Jaké materiály lze použít s DMLS?
Odpověď: S DMLS lze použít širokou škálu kovových prášků, včetně slitin titanu, nerezové oceli, slitin hliníku, Inconelu, kobaltového chromu, mědi, niklu, nástrojové oceli, drahých kovů a žáruvzdorných kovů.
Otázka: Jaké jsou některé z aplikací DMLS? (Pokračování)
Odpověď: DMLS nachází uplatnění v různých průmyslových odvětvích, včetně letectví a kosmonautiky, lékařských implantátů, automobilového průmyslu, výroby forem a matric, spotřebního zbo
Otázka: Kolik stojí stroj DMLS?
Odpověď: Cena stroje DMLS se může značně lišit v závislosti na objemu výroby, schopnostech a značce. Ceny se mohou pohybovat od desítek tisíc dolarů u menších strojů až po miliony dolarů u špičkových průmyslových systémů.
Otázka: Mohu DMLS používat doma?
Odpověď: I když se objevují stolní 3D tiskárny pro kov, průmyslové stroje DMLS nejsou obvykle vhodné pro domácí použití kvůli jejich složitosti, nákladům, bezpečnostním hlediskům a specializovaným požadavkům na manipulaci s práškem.
Otázka: Jaká je budoucnost DMLS?
Odpověď: Budoucnost DMLS je slibná. S pokrokem technologie můžeme očekávat dostupnější stroje DMLS, širší škálu kompatibilních kovových prášků a ještě rychlejší rychlosti tisku. DMLS je připraven hrát stále důležitější roli ve výrobě a umožnit vytváření inovativních a vysoce výkonných dílů v různých průmyslových odvětvích.
Závěr
DMLS představuje revoluční skok vpřed ve výrobě, který nabízí bezkonkurenční svobodu designu a schopnost vytvářet složité kovové díly s výjimečnou pevností a přesností. Od lehkých leteckých komponentů až po zakázkové lékařské implantáty, DMLS mění způsob, jakým navrhujeme a vyrábíme širokou škálu produktů. I když je třeba zvážit omezení, jako jsou náklady a doba výroby, DMLS se neustále vyvíjí a stává se dostupnějším, což z něj činí výkonný nástroj pro inženýry, designéry a výrobce. S tím, jak technologie DMLS dospívá a její schopnosti se rozšiřují, můžeme očekávat, že se v nadcházejících letech objeví ještě více průlomových aplikací.
Sdílet na
MET3DP Technology Co., LTD je předním poskytovatelem řešení aditivní výroby se sídlem v Qingdao v Číně. Naše společnost se specializuje na zařízení pro 3D tisk a vysoce výkonné kovové prášky pro průmyslové aplikace.
Dotaz k získání nejlepší ceny a přizpůsobeného řešení pro vaše podnikání!
Související články
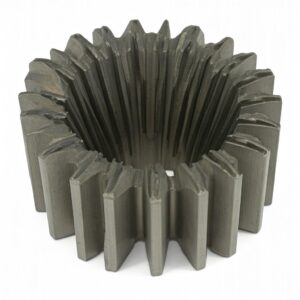
Vysoce výkonné segmenty lopatek trysek: Revoluce v účinnosti turbín díky 3D tisku z kovu
Přečtěte si více "O Met3DP
Nedávná aktualizace
Náš produkt
KONTAKTUJTE NÁS
Nějaké otázky? Pošlete nám zprávu hned teď! Po obdržení vaší zprávy obsloužíme vaši žádost s celým týmem.
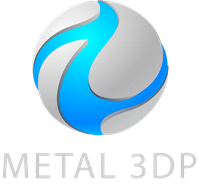
Kovové prášky pro 3D tisk a aditivní výrobu