Použití technologie DMLS v automobilovém průmyslu
Obsah
Představte si svět, ve kterém mohou výrobci automobilů vyrábět složité součásti motorů, lehké podvozkové díly a dokonce i interiéry na míru - to vše s bezkonkurenční přesností a volností designu. To není sci-fi, ale realita přímého laserového spékání kovů (Direct Metal Laser Sintering).DMLS), která rychle mění automobilový průmysl. Připoutejte se, milovníci převodovek, protože se chystáme proniknout do fascinujícího světa DMLS a prozkoumat, jak formuje budoucnost automobilů.
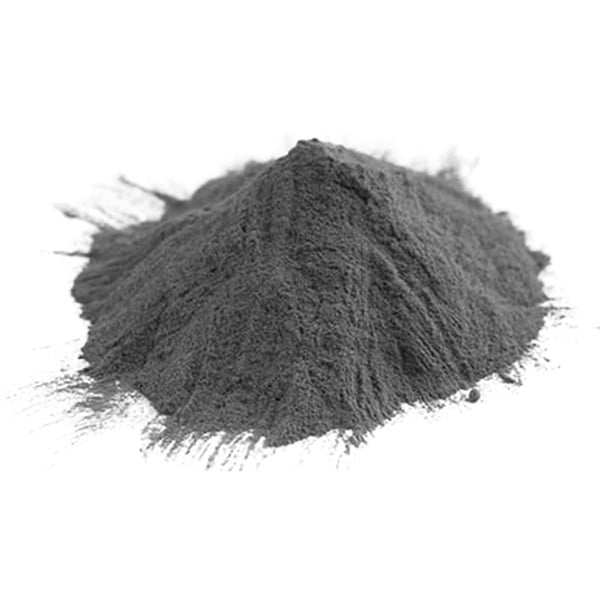
DMLS: 3D tisk pro kovové díly
DMLS, známý také jako selektivní laserové tavení (SLM), je revoluční proces aditivní výroby (AM). Na rozdíl od tradičních subtraktivních výrobních metod, jako je obrábění, které vyřezávají materiál z pevného bloku, DMLS vytváří díly vrstvu po vrstvě pomocí vysoce výkonného laserového paprsku. Tento laser roztaví jemný kovový prášek a spojí jej dohromady, čímž vznikne trojrozměrný objekt na základě digitálního návrhového souboru.
Kouzlo technologie DMLS spočívá ve schopnosti zpracovávat širokou škálu kovových prášků, z nichž každý má jedinečné vlastnosti, které vyhovují specifickým automobilovým aplikacím. Pojďme se ponořit hlouběji do fascinujícího světa těchto kovových prášků, stavebních kamenů inovací DMLS:
Kovové prášky pro DMLS v automobilovém průmyslu
Kovový prášek | Popis | Vlastnosti | Aplikace v automobilech |
---|---|---|---|
Nerezová ocel (316L, 17-4 PH) | Univerzální ocel odolná proti korozi | Vynikající pevnost, tažnost a biokompatibilita | Součásti motoru, výfukové potrubí, ozdobné díly |
Hliníkové slitiny (AlSi10Mg, AlSi7Mg0,3) | Lehké směsi hliníku s vysokou pevností | Vynikající poměr pevnosti a hmotnosti, dobrá odolnost proti korozi | Písty, hlavy válců, kola, součásti zavěšení |
Slitiny titanu (Ti6Al4V, Ti-6Al-7Nb) | Vysoce pevný titan s nízkou hmotností | Výjimečný poměr pevnosti a hmotnosti, vynikající biokompatibilita | Vysoce výkonné součásti motorů, ojnice, klikové hřídele |
Inconel (IN625, Inconel 718) | Superslitina známá svou odolností vůči vysokým teplotám | Výjimečná pevnost při zvýšených teplotách, dobrá odolnost proti korozi | Součásti turbodmychadla, výfukové systémy, výměníky tepla |
Slitiny niklu (Hastelloy C-22, Inconel 625) | Slitiny niklu a chromu odolné proti korozi | Vynikající odolnost vůči agresivním chemikáliím a vysokým teplotám. | Součásti palivového systému, skříně čerpadel, tělesa ventilů |
Nástrojové oceli (H13, AISI M2) | Oceli s vysokou tvrdostí pro nástrojové aplikace | Vynikající odolnost proti opotřebení, vynikající rozměrová stabilita | Formy na odlévání bloků motorů, převodovek, řezných nástrojů |
Slitiny mědi (CuSn4, C18150) | Vodivá měď s vylepšenými vlastnostmi | Vysoká tepelná a elektrická vodivost, dobrá obrobitelnost | Výměníky tepla, radiátory, elektrické komponenty |
Kobaltový chrom (CoCrMo) | Biokompatibilní slitina používaná v lékařských implantátech | Vysoká pevnost, odolnost proti opotřebení a korozi | Vlastní protézy pro úpravu automobilů (např. ruční ovládání) |
Slitiny hořčíku (AZ91E, AM60B) | Ultralehké hořčíkové směsi | Výjimečný poměr pevnosti a hmotnosti, dobrá rozměrová stabilita | Lehké panely karoserie, závodní komponenty, díly interiéru |
Slitiny molybdenu (Mo-0,5Ti,TZM) | Vysokoteplotní žáruvzdorné kovy | Výjimečná tepelná odolnost, dobrá mechanická pevnost | Vložky kelímků pro vysokoteplotní lití, formy pro výrobu bloků motorů |
Tato tabulka poskytuje přehled o rozmanitém prostředí kovových prášků pro DMLS v automobilovém průmyslu. Každý prášek nabízí jedinečné výhody, které se promítají do lehčích, pevnějších a účinnějších automobilových dílů, od pracovní nerezové oceli až po vysoce výkonný titan.
DMLS v akci: Transformace výroby automobilů
Nyní, když jsme prozkoumali zázraky kovových prášků, se podívejme, jak technologie DMLS mění různé aspekty výroby automobilů:
1. Součásti motoru: Představte si písty se složitými chladicími kanály nebo lehké hlavy válců s optimalizovanou vnitřní strukturou. DMLS tyto skutečnosti umožňuje. Schopnost vytvářet složité geometrie s vnitřními kanály umožňuje lepší řízení tepla a lepší výkon motoru. Použití lehkých kovových slitin, jako je hliník a titan, navíc znamená výrazné snížení hmotnosti, což vede ke zvýšení spotřeby paliva.
2. Součásti přenosového systému: Technologie DMLS se osvědčuje při vytváření složitých ozubených kol a komplexních převodových součástí s výjimečným poměrem pevnosti a hmotnosti. To umožňuje plynulejší řazení, lepší přenos výkonu a celkovou účinnost převodovky. Schopnost navrhovat a vyrábět lehká ozubená kola pomocí DMLS přispívá k lepší spotřebě paliva a snížení emisí.
3. Součásti podvozku: Technologie DMLS otevírá dveře k vytváření lehkých a zároveň robustních součástí podvozku, jako jsou ramena zavěšení a držáky. Schopnost navrhovat a vyrábět lehké a přitom robustní součásti podvozku pomocí DMLS přispívá k lepší úspoře paliva a snížení emisí. Kromě toho DMLS umožňuje vytvářet díly s optimalizovanou vnitřní strukturou, což vede ke zlepšení tuhosti a jízdních vlastností. Představte si vůz, který ostřeji projíždí zatáčkami a přináší vzrušující zážitek z jízdy - to je síla technologie DMLS.
4. Součásti automobilové karoserie: DMLS se neomezuje pouze na vnitřní komponenty. Rozvíjí se i v oblasti automobilových karoserií. Vzpomeňte si na přizpůsobené výdechy kapoty se složitým designem nebo lehké panely karoserie s výjimečnou pevností. DMLS umožňuje vytvářet složité aerodynamické součásti karoserie, které nejenže vypadají úchvatně, ale díky nižší hmotnosti přispívají i k lepší spotřebě paliva.
5. Součásti interiéru: DMLS se dostává i do interiéru vozu. Představte si upravené řadicí páky, lehké, ale pevné držáky sedadel nebo dokonce složité obložení palubní desky - to vše vyrobené pomocí DMLS. Tato technologie umožňuje vytvářet personalizované a jedinečné součásti interiéru, které zlepšují celkový vzhled a dojem z kabiny vozu.
Výhody a úvahy o DMLS
DMLS nabízí výrobcům automobilů řadu výhod, ale je důležité vzít v úvahu i jeho omezení:
Výhody DMLS:
- Svoboda designu: DMLS umožňuje vytvářet složité geometrie, které jsou při tradičních výrobních metodách nemožné. To otevírá dveře inovativním a lehkým konstrukcím automobilů.
- Snížení hmotnosti: Použití lehkých kovových prášků v DMLS vede k výrazným úsporám hmotnosti automobilových dílů, což se projevuje ve zvýšení spotřeby paliva a výkonu.
- Zvýšení výkonu: Technologie DMLS umožňuje vytvářet součásti s optimalizovanou vnitřní strukturou, což vede k lepšímu řízení tepla, pevnějším dílům a lepšímu celkovému výkonu.
- Přizpůsobení: Technologie DMLS umožňuje vyrábět díly automobilů na míru, které vyhovují specifickým potřebám a preferencím.
- Zkrácení doby realizace: V porovnání s tradičními metodami odlévání nebo obrábění může DMLS nabídnout rychlejší časy pro vývoj prototypů a výrobu malosériových dílů.
Úvahy o DMLS:
- Náklady: Stroje DMLS a kovové prášky mohou být drahé, což z nich činí nákladnější variantu ve srovnání s tradiční výrobou pro hromadnou výrobu.
- Doba výstavby: V závislosti na složitosti dílu může být doba výroby pomocí DMLS v porovnání s některými tradičními metodami delší.
- Následné zpracování: DMLS díly mohou vyžadovat další kroky následného zpracování, jako je odstranění podpěr a povrchová úprava.
- Kvalita povrchu: Ačkoli se při DMLS vyrábějí vysoce kvalitní díly, povrchová úprava nemusí být tak hladká jako u dílů, kterých se dosahuje tradičními metodami obrábění.
Budoucnost DMLS v oblasti Automobily
S dalším vývojem technologie DMLS můžeme očekávat ještě více transformačních aplikací v automobilovém průmyslu. Zde je několik zajímavých možností, na které se můžeme těšit:
- Hromadná výroba: Pokrok v technologii DMLS a snížení nákladů by mohly otevřít cestu k jejímu využití při hromadné výrobě automobilových dílů.
- Tisk z více materiálů: Možnost kombinovat různé kovové prášky v rámci jednoho procesu DMLS by mohla vést k vytváření dílů s jedinečnými vlastnostmi materiálu.
- Hybridní výroba: DMLS lze integrovat s dalšími výrobními metodami a vytvářet tak složité, vícemateriálové součásti automobilů.
- Výroba na vyžádání: Technologie DMLS by mohla přinést revoluci v logistice náhradních dílů, protože by umožnila prodejcům nebo opravnám tisknout díly na vyžádání.
Budoucnost DMLS v automobilovém průmyslu je plná možností. S tím, jak technologie dozrává a náklady se stávají konkurenceschopnějšími, můžeme očekávat, že se rozšíří škála automobilových dílů vyráběných pomocí této technologie. DMLS, což vede k lehčím, silnějším, účinnějším a dokonce i personalizovaným vozidlům.
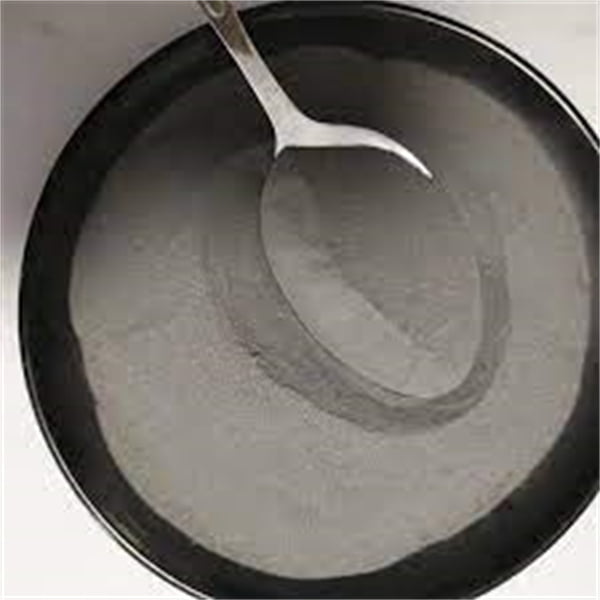
Nejčastější dotazy
Zde je několik často kladených otázek o DMLS v automobilovém průmyslu, které jsou pro snadnější orientaci uvedeny v tabulce:
Otázka | Odpovědět |
---|---|
Jaké jsou výhody použití DMLS pro automobilové díly? | DMLS nabízí volnost při navrhování, snížení hmotnosti, zvýšení výkonu, přizpůsobení a zkrácení dodacích lhůt pro vývoj prototypů. |
Jaká jsou některá omezení DMLS pro automobilové díly? | DMLS může být ve srovnání s tradičními metodami drahá, doba výroby může být delší a může být nutné následné zpracování. Povrchová úprava nemusí být tak hladká jako při tradičním obrábění. |
Používá se DMLS při hromadné výrobě automobilových dílů? | V současné době se DMLS používá především pro výrobu prototypů a malosériovou výrobu z důvodu nákladů. Technologický pokrok by však mohl v budoucnu otevřít cestu k masové výrobě. |
Jaké jsou budoucí možnosti DMLS v automobilovém průmyslu? | Můžeme očekávat pokrok v oblasti hromadné výroby, tisku z více materiálů, hybridní výroby a výroby náhradních dílů na vyžádání pomocí DMLS. |
Sdílet na
MET3DP Technology Co., LTD je předním poskytovatelem řešení aditivní výroby se sídlem v Qingdao v Číně. Naše společnost se specializuje na zařízení pro 3D tisk a vysoce výkonné kovové prášky pro průmyslové aplikace.
Dotaz k získání nejlepší ceny a přizpůsobeného řešení pro vaše podnikání!
Související články
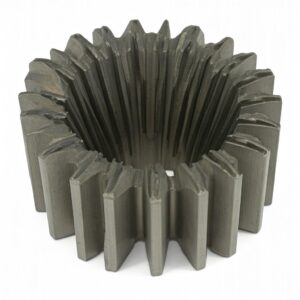
Vysoce výkonné segmenty lopatek trysek: Revoluce v účinnosti turbín díky 3D tisku z kovu
Přečtěte si více "O Met3DP
Nedávná aktualizace
Náš produkt
KONTAKTUJTE NÁS
Nějaké otázky? Pošlete nám zprávu hned teď! Po obdržení vaší zprávy obsloužíme vaši žádost s celým týmem.
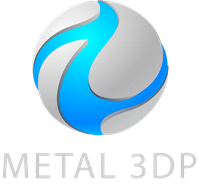
Kovové prášky pro 3D tisk a aditivní výrobu