Procesní kroky technologie DMLS
Obsah
Snili jste někdy o tom, že vykouzlíte ze vzduchu složité kovové předměty? S technologií Direct Metal Laser Sintering (přímého laserového spékání kovů).DMLS) se tento sen stává skutečností. DMLS, známý také jako selektivní laserové tavení (SLM), je revoluční proces 3D tisku, který využívá vysoce výkonný laser k pečlivému spojování částic kovového prášku vrstvu po vrstvě a vytváří tak složité a funkční kovové díly.
Představte si, že z digitálního souboru vyrobíte složité ozubené kolo nebo lehkou leteckou součástku s vnitřními kanály - to je síla technologie DMLS. Ale jak přesně k tomuto kouzlu dochází? Připoutejte se, protože se chystáme proniknout do fascinujícího světa DMLS krok za krokem.
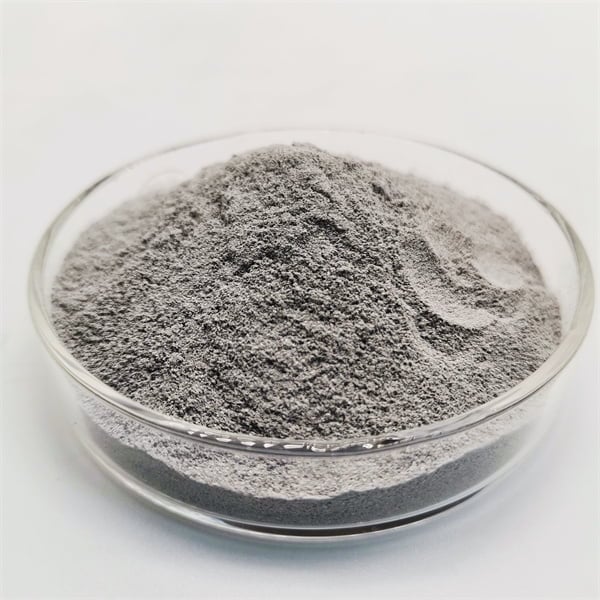
Stavební kameny: Pohled na DMLS Kovové prášky
Základem každého výtvoru DMLS je samotný kovový prášek. Tyto jemné kovové granule, jejichž velikost se obvykle pohybuje od 15 do 63 mikronů (to je neuvěřitelně málo!), se dodávají v různých variantách, z nichž každá nabízí jedinečné vlastnosti pro konkrétní aplikace. Zde je náhled na některé z nejoblíbenějších možností kovového prášku DMLS:
Kovový prášek | Složení | Vlastnosti | Aplikace |
---|---|---|---|
Nerezová ocel 316L | 16-18% Chrom, 10-14% Nikl, 2% Molybden | Vynikající odolnost proti korozi, vysoká pevnost, biokompatibilní | Lékařské implantáty, letecké a kosmické komponenty, šperky |
Titan 6Al-4V (třída 23) | 90% Titan, 6% Hliník, 4% Vanad | Vysoký poměr pevnosti k hmotnosti, dobrá biokompatibilita, vynikající odolnost proti korozi. | Letecké komponenty, lékařské implantáty, sportovní zboží |
Inconel 625 | Superslitina na bázi niklu a chromu | Výjimečná pevnost při vysokých teplotách, odolnost proti korozi | Lopatky turbín, výměníky tepla, jaderné reaktory |
Hliník AlSi10Mg | Hliníková slitina s 10% křemíku a 0,5% hořčíku | Lehká konstrukce, dobrá odolnost proti korozi, vysoká tepelná vodivost | Automobilové díly, chladiče, kryty elektroniky |
Měď | 100% Měď | Vysoká elektrická vodivost, dobrá tepelná vodivost | Výměníky tepla, elektrické komponenty, vlnovody |
Nástrojová ocel (H13) | Legovaná ocel s vysokým obsahem chromu | Vysoká odolnost proti opotřebení, dobrá tepelná stabilita | Formy, zápustky, řezné nástroje |
Nikl | 100% Nikl | Vynikající odolnost proti korozi, dobrá tažnost | Zařízení pro chemické zpracování, elektrické komponenty, výměníky tepla |
Kobaltový chrom (CoCrMo) | Slitina kobaltu a chromu s molybdenem | Vysoká pevnost, odolnost proti opotřebení, biokompatibilní | Lékařské implantáty, zubní protézy, opotřebitelné díly |
Zlato | 100% Zlatá | Vysoká tažnost, kujnost, vynikající odolnost proti korozi | Šperky, elektronika, dekorativní aplikace |
Tato tabulka poskytuje pohled do rozmanitého světa kovových prášků DMLS. Každý materiál se může pochlubit jedinečnými přednostmi, díky nimž je vhodný pro širokou škálu aplikací. Při výběru kovového prášku hrají zásadní roli faktory, jako jsou požadované mechanické vlastnosti, odolnost proti korozi, zohlednění hmotnosti a biokompatibilita (pro lékařské aplikace).
Za stolem: Hlubší ponor do vlastností kovových prášků
Je důležité si uvědomit, že tyto kovové prášky nejsou jen tak ledajaký prach. Jsou pečlivě navrženy tak, aby zajistily optimální výkon během procesu DMLS. Zde je několik klíčových vlastností, které je třeba vzít v úvahu:
- Velikost a distribuce částic: Pro plynulý tok prášku a rovnoměrné tavení laserem je zásadní konzistentní velikost a distribuce částic.
- Sféricita: Sférické částice mají lepší tekutost a hustotu balení, což vede k rovnoměrnějšímu procesu vytváření.
- Tekutost: Pro konzistentní tvorbu vrstev je zásadní schopnost prášku volně proudit ve stroji DMLS.
- Zjevná hustota: Jedná se o poměr hmotnosti prášku k jeho celkovému objemu. Vyšší zdánlivá hustota umožňuje zabalit do každé vrstvy více materiálu, což vede k hustšímu výslednému dílu.
- Absorpční schopnost laseru: Schopnost kovového prášku účinně absorbovat energii laseru určuje proces tavení a celkovou kvalitu konstrukce.
Výrobci vynakládají velké úsilí, aby zajistili, že jejich kovové prášky pro DMLS splňují tyto přísné požadavky. Pečlivou kontrolou těchto vlastností vytvářejí prášky speciálně navržené pro optimální výkon DMLS.
Od digitálních snů ke kovové realitě: Proces DMLS krok za krokem
Nyní, když jsme prozkoumali stavební kameny, se ponořme do podmanivého světa samotného DMLS. Zde je rozpis procesu krok za krokem:
1. Vyberte vhodný kovový prášek: Jak již bylo uvedeno, výběr správného kovového prášku je rozhodující pro dosažení požadovaných vlastností konečného dílu.
2. Vytvořte 3D model pomocí 3D modelovacího softwaru: Kouzlo DMLS začíná digitální reprezentací požadovaného objektu. Software pro 3D modelování, který se podobá sochařskému dlátu digitálního věku, umožňuje konstruktérům navrhovat složité geometrie, které by nebylo možné vytvořit tradičními výrobními metodami. Tyto 3D modely určují každý detail konečného dílu, od jeho celkového tvaru až po vnitřní kanály a složité prvky.
3. Připravte stavební platformu: Představte si digitální plátno, které ožívá. Konstrukční platforma stroje DMLS slouží jako základ, na kterém se vrstvu po vrstvě vytváří kovový objekt. Tato platforma se pečlivě čistí a vyrovnává, aby byl zajištěn hladký a konzistentní výchozí bod pro proces sestavování.
4. Položte kovový prášek na tiskovou plošinu: Tenká vrstva kovového prášku o tloušťce obvykle od 20 do 100 mikronů se rovnoměrně nanese na celou konstrukční platformu. Tato vrstva slouží jako první stavební prvek objektu. K dosažení rovnoměrné a konzistentní vrstvy prášku lze použít několik technik, například systém nanášení pomocí lopatek nebo válečkový mechanismus.
5. Laser roztaví kouzlo: Zde se odehrává to pravé kouzlo. Vysoce výkonný laserový paprsek, pečlivě vedený digitálním 3D modelem, skenuje kovový prášek a selektivně taví částice dohromady. Hustota výkonu laseru a dráha skenování jsou přesně řízeny, aby se vytvořila požadovaná geometrie pro každou vrstvu. Jak laser taví prášek, spojuje částice v pevnou hmotu, čímž efektivně vytváří objekt po jednotlivých vrstvách.
6. Vrstvu po vrstvě se objekt utváří: Proces DMLS probíhá v opakujícím se cyklu. Po roztavení první vrstvy se na ni nanese nová vrstva kovového prášku. Laser pak skenuje přes tuto novou vrstvu, taví prášek a spojuje jej s dříve vytvořenou vrstvou. Tento cyklus pokračuje vrstvu po vrstvě a pečlivě buduje objekt odspodu nahoru, dokud není celá konstrukce dokončena.
7. Ochlazení: Po roztavení poslední vrstvy nechá stroj DMLS zhotovený objekt pomalu vychladnout v kontrolované atmosféře. Tento řízený proces chlazení pomáhá minimalizovat zbytková napětí a deformace uvnitř dílu a zajišťuje jeho rozměrovou přesnost a strukturální integritu.
8. Odstranění podpory: Podobně jako lešení používané v tradičním stavebnictví vyžadují konstrukce DMLS často podpůrné konstrukce, aby se zabránilo zhroucení choulostivých prvků během procesu tisku. Tyto podpůrné konstrukce jsou obvykle vyrobeny ze stejného kovového prášku, ale jsou navrženy tak, aby je bylo možné po dokončení stavby snadno odstranit. K oddělení těchto podpůrných struktur lze použít techniky, jako je obrábění, řezání vodním paprskem nebo mechanické odstranění, a odhalit tak finální kovový objekt v celé jeho kráse.
9. Následné zpracování technologie DMLS: V některých případech může objekt vyrobený metodou DMLS vyžadovat další kroky následného zpracování, aby bylo dosaženo požadované povrchové úpravy nebo mechanických vlastností. Tyto kroky mohou zahrnovat tepelné zpracování pro uvolnění napětí nebo zvýšení pevnosti, pískování pro hladší povrch nebo obrábění pro vyšší rozměrovou přesnost.
Odhalení výhod a omezení DMLS
Technologie DMLS nabízí oproti tradičním výrobním metodám řadu výhod:
- Svoboda designu: DMLS umožňuje vytvářet neuvěřitelně složité geometrie, včetně vnitřních kanálků, mřížek a dalších složitých prvků, jejichž výroba tradičními technikami by byla nemožná nebo nákladná.
- Rychlé prototypování: Možnost vytvářet funkční díly přímo z 3D modelu umožňuje rychlou tvorbu prototypů, což inženýrům umožňuje rychle a efektivně vylepšovat návrhy.
- Odlehčení: Technologie DMLS umožňuje vytvářet lehké konstrukce s vysokým poměrem pevnosti a hmotnosti, takže je ideální pro aplikace v leteckém a automobilovém průmyslu.
- Přizpůsobení: Technologie DMLS snadno usnadňuje výrobu dílů na míru a výrobu malých sérií, takže je ideální pro specializované aplikace nebo jednorázové projekty.
DMLS má však také svá omezení, která je třeba vzít v úvahu:
- Náklady: Stroje a kovové prášky pro DMLS mohou být drahé, takže tento proces je méně vhodný pro velkosériovou výrobu.
- Omezení velikosti stavby: Objem výroby strojů DMLS je ve srovnání s tradičními technikami obvykle omezený.
- Povrchová úprava: Zatímco u některých dílů vyrobených metodou DMLS lze dosáhnout dobré povrchové úpravy, jiné mohou vyžadovat další dodatečné zpracování pro dosažení hladšího estetického vzhledu.
- Omezení materiálu: Nabídka materiálů pro DMLS se stále vyvíjí, i když se neustále rozšiřuje.
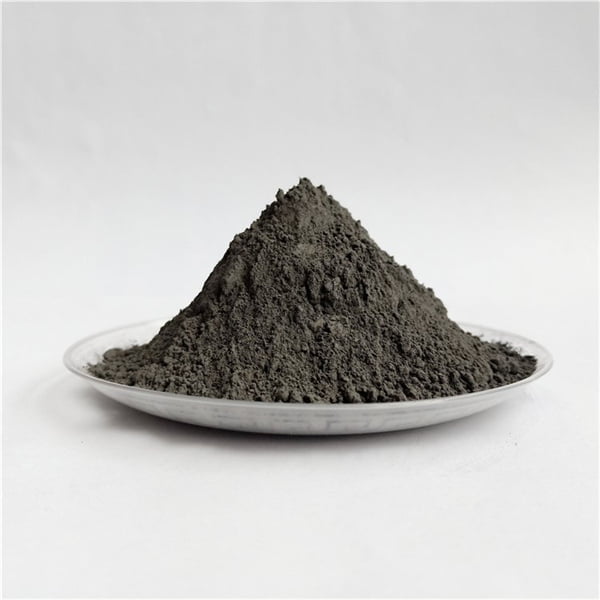
FAQ
Otázka: Jaký je rozdíl mezi DMLS a SLS?
Odpověď: DMLS i selektivní laserové slinování (SLS) jsou procesy 3D tisku, které využívají laser k vytváření objektů vrstvu po vrstvě. Klíčový rozdíl je však v materiálech, které používají. DMLS pracuje s kovovými prášky, které se taví dohromady a vytvářejí pevný objekt. Naproti tomu SLS obvykle používá plastové nebo nylonové prášky, přičemž dochází ke spékání (slučování) částic bez jejich úplného roztavení. Tento rozdíl má za následek několik klíčových rozdílů:
- Vlastnosti materiálu: Předměty vytištěné metodou DMLS jsou obvykle mnohem pevnější a odolnější než díly vytištěné metodou SLS, a to díky vlastnostem kovu ve srovnání s plastem.
- Aplikace: Technologie DMLS je vhodná pro vytváření funkčních kovových dílů pro letecký, automobilový a lékařský průmysl. SLS vyniká při výrobě prototypů a plastových dílů s dobrou estetikou.
- Náklady: DMLS je obecně dražší proces než SLS, a to kvůli vyšším nákladům na kovové prášky a složitějšímu strojnímu vybavení.
Otázka: Jak pevné jsou díly vytištěné metodou DMLS?
Odpověď: Pevnost dílů vytištěných metodou DMLS závisí na konkrétním použitém kovovém prášku a použitých technikách následného zpracování. Díly vytištěné metodou DMLS však mohou být neuvěřitelně pevné a často dosahují mechanických vlastností srovnatelných s jejich protějšky vyrobenými tradičním způsobem. Faktoren, jako je tepelné zpracování, může dále zvýšit pevnost konečného výrobku.
Otázka: Jaké jsou možnosti povrchové úpravy dílů DMLS?
Odpověď: Díly vytištěné metodou DMLS mají obvykle poněkud drsný povrch, což je způsobeno tím, že se tiskne po vrstvách. K dosažení hladšího povrchu však lze použít několik technik následného zpracování:
- Obrábění: K vytvoření hladkého a přesného povrchu lze použít tradiční obráběcí techniky, jako je frézování a soustružení.
- Pískování: Tato technika využívá proud brusných částic k vyhlazení povrchu dílu.
- Leštění: K dosažení vysoce reflexní povrchové úpravy lze použít mechanické nebo chemické leštění.
Volba povrchové úpravy závisí na požadovaném estetickém vzhledu a funkčních požadavcích konečného dílu.
Otázka: Jaké jsou environmentální aspekty DMLS?
Odpověď: Stejně jako každý výrobní proces má i DMLS určité dopady na životní prostředí. Zde je několik klíčových faktorů, které je třeba vzít v úvahu:
- Spotřeba energie: Stroje DMLS vyžadují značné množství energie na provoz vysoce výkonného laseru a udržování kontrolované atmosféry.
- Materiálový odpad: V závislosti na geometrii dílu a konstrukci nosné struktury může při procesu DMLS dojít ke ztrátě části kovového prášku. Některé stroje však nabízejí možnost recyklace prášku, která minimalizuje množství odpadu.
- Emise: Při procesu DMLS může vznikat malé množství prachu a výparů v závislosti na tištěném materiálu. Pro zmírnění těchto emisí jsou zásadní správné ventilační systémy.
Výrobci neustále usilují o zlepšení účinnosti a udržitelnosti technologie DMLS. Probíhá výzkum zaměřený na vývoj energeticky účinnějších strojů a minimalizaci vzniku odpadu.
Budoucnost DMLS: Pohled na inovace zítřka
Technologie DMLS se rychle vyvíjí a neustále posouvá hranice možností. Zde je několik zajímavých trendů, které formují budoucnost technologie DMLS:
- Vícemateriálový DMLS: Možnost tisknout objekty pomocí více kovových prášků v rámci jednoho sestavení otevírá dveře k vytváření dílů s jedinečnými kombinacemi vlastností.
- Větší stavební objemy: Ve vývoji jsou stroje DMLS s většími konstrukčními obálkami, které umožňují vytvářet ještě větší a složitější kovové předměty.
- Vyšší rychlost tisku: Pokroky v laserové technologii a mechanismech manipulace s práškem vedou ke zkrácení doby tisku, čímž se DMLS stává efektivnějším pro výrobní aplikace.
- Nové materiály: Nabídka materiálů kompatibilních s DMLS se neustále rozšiřuje, včetně nových slitin a dokonce i exotických materiálů, jako je například aluminid titanu (TiAl).
Technologie DMLS se neustále vyvíjí a má potenciál přinést revoluci do různých průmyslových odvětví, od leteckého a automobilového průmyslu až po medicínu a další. Díky své schopnosti vytvářet složité, funkční a lehké kovové díly je DMLS připravena hrát významnou roli při utváření budoucnosti výroby.
Sdílet na
MET3DP Technology Co., LTD je předním poskytovatelem řešení aditivní výroby se sídlem v Qingdao v Číně. Naše společnost se specializuje na zařízení pro 3D tisk a vysoce výkonné kovové prášky pro průmyslové aplikace.
Dotaz k získání nejlepší ceny a přizpůsobeného řešení pro vaše podnikání!
Související články
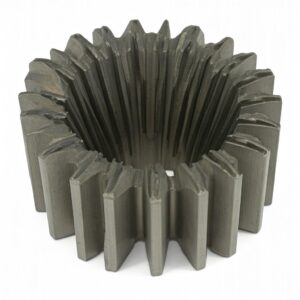
Vysoce výkonné segmenty lopatek trysek: Revoluce v účinnosti turbín díky 3D tisku z kovu
Přečtěte si více "O Met3DP
Nedávná aktualizace
Náš produkt
KONTAKTUJTE NÁS
Nějaké otázky? Pošlete nám zprávu hned teď! Po obdržení vaší zprávy obsloužíme vaši žádost s celým týmem.
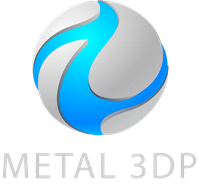
Kovové prášky pro 3D tisk a aditivní výrobu