Rozdíl mezi technologií EBM a technologií DED
Obsah
Svět 3D tisku z kovu je fascinující krajinou, která překypuje možnostmi vytváření složitých a robustních součástí. V této oblasti však vynikají dva titáni: Tavení elektronovým paprskem (EBM) a usměrněné energetické depozice (DED). Obě tyto technologie využívají cílený zdroj tepla k vytváření dílů vrstvu po vrstvě, jejich základní procesy a výsledné produkty se však výrazně liší. Pokud se tedy vydáváte na cestu 3D tisku z kovu, výběr správné technologie se stává prvořadým. Připoutejte se, protože se chystáme proniknout do složitých detailů EBM a DED a vybavit vás tak, abyste mohli učinit informované rozhodnutí.
Rozdíl v materiálech mezi těmito dvěma technologiemi 3D tisku kovů
Představte si spíž šéfkuchaře. EBM je jako pečlivě uspořádaná skříňka plná předem odměřených kovových prášků vysoké čistoty. Tyto prášky, které mají obvykle kulovitý tvar a velikost od 10 do 100 mikronů, zajišťují konzistentní chování při tavení během procesu tisku. Mezi nejčastěji používané kovové prášky v EBM patří:
- Slitiny titanu (Ti-6Al-4V, Gr23): Tyto slitiny jsou proslulé svým výjimečným poměrem pevnosti a hmotnosti, biokompatibilitou a odolností proti korozi a jsou ideální pro použití v letectví, lékařských implantátech a chemickém průmyslu.
- Nerezová ocel (316L): Nerezová ocel 316L je univerzální volbou, která nabízí dobrou rovnováhu mezi pevností, odolností proti korozi a cenovou dostupností. Najde uplatnění ve všech oblastech, od automobilových součástek až po lodní vybavení.
- Inconel (IN625): Tato vysoce výkonná slitina se může pochlubit vynikající pevností při zvýšených teplotách, což z ní činí ideální volbu pro součásti proudových motorů, výměníky tepla a další aplikace vyžadující tepelnou odolnost.
- Kobalt-chrom (CoCr): Díky kombinaci biokompatibility a odolnosti proti opotřebení je CoCr oblíbenou volbou pro ortopedické implantáty a další zdravotnické prostředky.
- Slitiny niklu (Inconel 718): Tyto slitiny vykazují výjimečnou pevnost, odolnost proti tečení a odolnost vůči vysokým teplotám, díky čemuž jsou cenné v aplikacích, jako jsou lopatky turbín a plynovody.
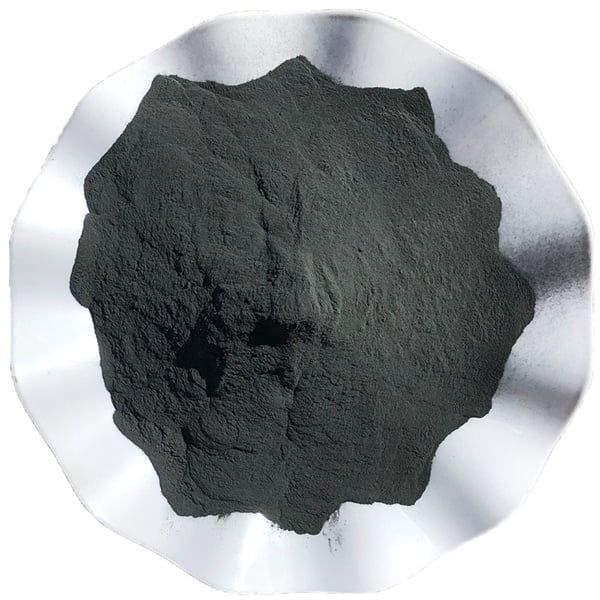
Na druhou stranu DED funguje spíše jako volně přístupná kuchyně. Využívá kovové vstupní suroviny ve formě drátů nebo tyčí, což nabízí širší spektrum kompatibility materiálů. Zde jsou některé běžně používané možnosti:
- Ocelové slitiny (nízkouhlíková ocel, AISI 4130, maraging ocel): Společnost DED vyniká zpracováním široké škály ocelových slitin, které jsou určeny pro aplikace vyžadující vysokou pevnost a cenovou dostupnost, jako jsou konstrukční součásti a nástroje.
- Slitiny niklu (Inconel 625, Inconel 718): Podobně jako EBM může DED zpracovávat vysoce výkonné slitiny niklu a díky vstupnímu materiálu v podobě drátu/tyče poskytuje větší flexibilitu, pokud jde o geometrii konstrukce.
- Slitiny hliníku (AA 6061, AA 7075): DED otevírá dveře k použití lehkých a svařitelných hliníkových slitin pro aplikace, kde je snížení hmotnosti klíčové, jako jsou letecké komponenty a automobilové díly.
- Slitiny mědi (C18000): Díky své schopnosti zpracovávat slitiny mědi je DED vhodný pro aplikace vyžadující vysokou tepelnou a elektrickou vodivost, jako jsou chladiče a elektrické přípojnice.
- Slitiny titanu (Ti-6Al-4V): Ačkoli DED může zpracovávat titanové slitiny, dosažení stejné úrovně vlastností materiálu jako u EBM může být náročné kvůli možné kontaminaci kyslíkem.
Klíčový závěr: Společnost EBM nabízí kontrolované prostředí s předem legovanými prášky, které je ideální pro vysoce výkonné díly vyžadující specifické vlastnosti materiálu. DED naproti tomu poskytuje větší materiálovou flexibilitu s drátěnými/tyčovými vstupními surovinami, takže je vhodná pro širší škálu aplikací.
Rozdíl v rychlosti tisku mezi těmito dvěma technologiemi 3D tisku kovů
Představte si závodní auto a robustní traktor. EBM, má díky pečlivému procesu tavení práškového lože nižší rychlost tisku ve srovnání s DED. Typické sestavení EBM může trvat hodiny nebo dokonce dny, v závislosti na složitosti a velikosti dílu. Technologie DED se díky kontinuálnímu nanášení drátů a tyčí může pochlubit výrazně vyšší rychlostí tisku, takže sestava může být hotová během několika minut nebo hodin.
Proč je rozdíl v rychlosti? EBM zahrnuje předehřev celého lože prášku, aby se zajistilo konzistentní chování při tavení. Každá vrstva navíc vyžaduje pečlivé skenování elektronovým paprskem. Naproti tomu DED se zaměřuje pouze na konkrétní deponovanou oblast, čímž odpadá nutnost předehřívání celé konstrukční komory.
Volba správné rychlosti: Pokud je vaší prioritou rychlá výroba prototypů nebo rychlá výroba velkých kovových dílů, může být DED lepší volbou. Pokud však požadujete vysoce přesné součásti s výjimečnými vlastnostmi materiálu, pomalejší rychlost EBM znamená větší kontrolu a přesnost.
Přesnost těchto dvou technologií 3D tisku kovů se liší
Představte si jemné švýcarské hodinky a robustní dědečkovy hodiny. EBM vyniká ve výrobě vysoce přesných dílů s výjimečnou povrchovou úpravou. To je dáno přesným tavením předem legovaných prášků a kontrolovaným prostředím v komoře EBM. Tloušťka vrstvy v EBM může být až 30 mikronů, což umožňuje vytvářet složité prvky a hladké povrchy.
DED naproti tomu upřednostňuje rychlost a ukládání materiálu před absolutní přesností. Přestože je DED stále schopen vyrábět funkční díly, mohou mít o něco hrubší povrch a potenciálně i rozměrové tolerance, které nejsou tak přísné jako u EBM. Tloušťka vrstvy při DED se obvykle pohybuje v rozmezí 100 mikronů nebo více.
Faktory ovlivňující přesnost:
- Zdroj tepla: Fokusovaný elektronový paprsek EBM nabízí přesnější kontrolu nad tavením ve srovnání s širším laserovým paprskem nebo obloukovým svařováním DED.
- Materiálová surovina: Předlegované prášky v EBM nabízejí jednotnější materiál v porovnání s potenciálními odchylkami ve vstupních surovinách z drátů a tyčí používaných v DED.
- Podpůrné struktury: Obě technologie vyžadují podpůrné konstrukce, které zabraňují deformaci a zkreslení během tisku. Podpůrné struktury EBM však mohou být složitější díky menší tloušťce vrstvy, což může vést ke snadnějšímu odstranění a čistšímu finálnímu dílu.
Volba správné přesnosti: Pokud vaše aplikace vyžaduje díly s přísnými tolerancemi, složitými detaily a hladkým povrchem, je EBM jasným vítězem. Pokud je však rozměrová přesnost méně kritická a je požadována rychlejší doba realizace, může být vhodnou volbou DED.
Vybavení pro tyto dvě technologie 3D tisku kovů se liší
Představte si špičkovou laboratoř a dílnu pro náročné práce. Stroje EBM jsou sofistikovaná zařízení, která pracují ve vakuové komoře, aby se zabránilo oxidaci kovových prášků. Využívají výkonné dělo s elektronovým paprskem a vyžadují kontrolované prostředí, aby byla zachována stálá kvalita tisku. Náklady na stroje EBM jsou ve srovnání se systémy DED obvykle vyšší.
Tiskárny DED se podobají spíše průmyslovým robotům. Pracují v otevřeném prostředí nebo v prostředí s inertním plynem a k tavení kovových surovin používají laser nebo obloukové svařování. Stroje DED bývají robustnější a mají větší stavební objem, takže jsou vhodné pro výrobu větších kovových dílů. Počáteční náklady na stroje DED jsou obecně nižší než u systémů EBM.
Další úvahy:
- Údržba: Stroje EBM vyžadují specializovanou údržbu vzhledem ke složité vakuové komoře a technologii elektronového svazku. Systémy DED jsou obecně jednodušší na údržbu.
- Bezpečnost: Jak EBM, tak DED využívají vysoce výkonné zdroje energie a vyžadují náležitá bezpečnostní opatření během provozu.
Výběr správného vybavení: Pokud potřebujete vyrábět složité díly s vysokou hodnotou v kontrolovaném prostředí, může být EBM lepší volbou i přes vyšší počáteční náklady. Pokud jsou však prioritou cenová dostupnost, větší objem výroby a rychlejší výrobní časy, nabízí DED přesvědčivou alternativu.
Další krok: Další článek: Hloubkový ponor do aplikací, výhod a omezení EBM a DED
Prozkoumali jsme základní rozdíly mezi EBM a DED z hlediska materiálů, rychlosti tisku a přesnosti. Nyní se ponoříme hlouběji do konkrétních aplikací, kde každá z technologií vyniká, spolu s jejich jedinečnými výhodami a omezeními. Tyto znalosti vám umožní učinit informované rozhodnutí při výběru správné technologie 3D tisku kovů pro váš projekt.
Aplikace, výhody a omezení systému EBM a DED Metal 3D Printing
Nyní, když jsme se seznámili se základními funkcemi EBM a DED, je čas prozkoumat bojiště, kde se tyto technologie skutečně střetávají: jejich aplikace, silné a slabé stránky. Pochopením těchto aspektů budete dobře vybaveni pro výběr šampiona pro vaše konkrétní potřeby 3D tisku z kovu.
Aplikace
EBM:
- Letectví: Schopnost EBM vyrábět vysoce pevné a lehké součásti s výjimečnými vlastnostmi materiálu je ideální pro aplikace v leteckém průmyslu, jako jsou lopatky turbín, kryty motorů a konstrukční součásti.
- Lékařské implantáty: Biokompatibilita a vysoká přesnost EBM otevírají cestu k vytváření implantátů na míru, jako jsou kyčelní jamky, kolenní náhrady a zubní protézy.
- Vysoce výkonné díly: EBM vyniká při výrobě dílů, které vyžadují výjimečný poměr pevnosti a hmotnosti, odolnost vůči vysokým teplotám a korozi, takže je cenný pro aplikace, jako jsou výměníky tepla, zařízení pro zpracování chemikálií a díly pro průzkum ložisek ropy a zemního plynu.
DED:
- Rychlé prototypování: Díky vysoké rychlosti tisku je DED cenným nástrojem pro rychlé vytváření funkčních prototypů, což umožňuje iterační cykly návrhu a testování.
- Velkoplošné kovové díly: Schopnost společnosti DED zvládat velké objemy výroby je výhodná pro výrobu konstrukčních součástí, nástrojů a zápustek a přípravků.
- Opravy a restaurování: Díky schopnosti svařovat různorodé kovy je DED vhodný pro opravy poškozených kovových dílů nebo přidávání prvků na stávající součásti.
- Konstrukce: Technologie DED má potenciál způsobit revoluci ve stavebnictví tím, že umožňuje tisk kovových komponent pro budovy a infrastrukturu přímo na místě.
Výhody EBM
- Výjimečné vlastnosti materiálu: Díky řízenému prostředí a předem legovaným práškům vyrábí EBM díly s vynikajícími mechanickými vlastnostmi, vysokou hustotou a minimální pórovitostí.
- Vysoká přesnost a preciznost: EBM umožňuje vytvářet složité prvky a hladké povrchy s přísnými tolerancemi.
- Biokompatibilita: Některé materiály EBM, například titan a kobalt-chrom, jsou biokompatibilní, takže jsou vhodné pro lékařské implantáty.
Omezení EBM
- Nižší rychlost tisku: V porovnání s DED je rychlost tisku EBM nižší kvůli procesu tavení po vrstvách a požadavkům na předehřívání.
- Omezený výběr materiálů: EBM sice nabízí řadu vysoce výkonných materiálů, ale jejich výběr není tak široký jako kompatibilita DED s různými vstupními surovinami pro dráty a tyče.
- Vyšší náklady: Stroje a materiály EBM bývají ve srovnání se systémy DED dražší.
Výhody DED
- Rychlejší tisk: DED se může pochlubit výrazně vyšší rychlostí tisku, takže je ideální pro rychlou výrobu prototypů a velkých dílů.
- Širší kompatibilita materiálů: DED může zpracovávat širší škálu kovových slitin a dokonce i různorodé kovy díky použití drátěných/tyčových vstupních materiálů.
- Nižší náklady: Stroje a materiály pro DED jsou ve srovnání s EBM obecně cenově dostupnější.
- Větší objem sestavy: Systémy DED mají často větší objem, což umožňuje výrobu větších kovových dílů.
Omezení DED
- Nižší přesnost: Díly DED mohou mít mírně drsnější povrch a volnější rozměrové tolerance ve srovnání s díly EBM.
- Potenciál pro oxidaci: DED pracuje v prostředí otevřeného nebo inertního plynu, což může u některých materiálů představovat mírné riziko kontaminace kyslíkem.
- Omezená složitost dílů: Vzhledem k většímu objemu taveniny může mít DED ve srovnání s EBM problémy s vytvářením velmi složitých prvků.
Výběr správné technologie:
Volba mezi EBM a DED nakonec závisí na konkrétních požadavcích projektu. Zde je stručný přehled, který vám pomůže při rozhodování:
- Upřednostňovat vysoce přesné, složité díly s výjimečnými vlastnostmi materiálu? Vyberte si EBM.
- Potřebujete rychlou dobu realizace, velký objem výroby a cenovou dostupnost? DED by mohl být vhodnější.
- Nejste si jisti? Zvažte faktory, jako jsou možnosti materiálu, složitost dílů a rozpočtová omezení, abyste mohli učinit informované rozhodnutí.
Závěr
Přestože obě technologie, EBM a DED, využívají sílu 3D tisku z kovu, uspokojují odlišné potřeby. EBM se stává šampionem pro vysoce hodnotné, složité díly vyžadující výjimečnou přesnost a vlastnosti materiálu. DED naproti tomu kraluje v oblasti rychlé výroby prototypů, velkých kovových součástí a nákladové efektivity. Pochopíte-li jejich silné stránky a omezení, můžete si bez obav vybrat technologii, která vám umožní uvést do života váš další kovový výtvor.
Sdílet na
MET3DP Technology Co., LTD je předním poskytovatelem řešení aditivní výroby se sídlem v Qingdao v Číně. Naše společnost se specializuje na zařízení pro 3D tisk a vysoce výkonné kovové prášky pro průmyslové aplikace.
Dotaz k získání nejlepší ceny a přizpůsobeného řešení pro vaše podnikání!
Související články
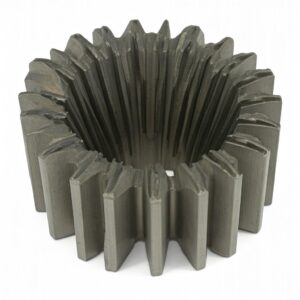
Vysoce výkonné segmenty lopatek trysek: Revoluce v účinnosti turbín díky 3D tisku z kovu
Přečtěte si více "O Met3DP
Nedávná aktualizace
Náš produkt
KONTAKTUJTE NÁS
Nějaké otázky? Pošlete nám zprávu hned teď! Po obdržení vaší zprávy obsloužíme vaši žádost s celým týmem.
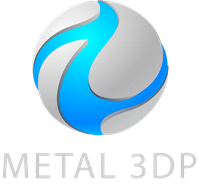
Kovové prášky pro 3D tisk a aditivní výrobu