Koncové zvonky elektromotorů
Obsah
Úvod - Kritická role koncových zvonků elektromotorů v moderních aplikacích
Elektromotory jsou neopěvovanými hrdiny pohánějícími širokou škálu moderních technologií, od sofistikované robotiky v letecké a kosmické výrobě až po každodenní pohodlí automobilových systémů a kritických strojů v průmyslových závodech. Srdcem těchto motorů jsou zdánlivě jednoduché, ale klíčové součásti a mezi nimi i koncový zvon elektromotoru je důležitým strukturálním prvkem. Tyto koncové zvony jsou více než jen kryty; poskytují nezbytnou oporu ložiskům, chrání vnitřní součásti před vlivy prostředí, jako je prach a vlhkost, a přispívají k celkové integritě a výkonu motoru. Vzhledem k tomu, že průmyslová odvětví vyžadují stále účinnější, lehčí a na míru šitá řešení motorů, vyvíjejí se i výrobní metody těchto kritických dílů. Zde se projevuje transformační potenciál kov 3D tisk, známá také jako aditivní výroba kovů, se dostává do popředí zájmu a nabízí nebývalou svobodu designu a všestrannost materiálů. Společnosti jako např Metal3DP, přední poskytovatel řešení pro aditivní výrobu se sídlem v čínském městě Čching-tao, stojí v čele této revoluce a nabízí pokročilé zařízení pro 3D tisk a vysoce výkonné kovové prášky, které nově definují způsob, jakým jsou koncipovány a vyráběny součásti elektromotorů, včetně koncových zvonů.
Co jsou koncové zvonky elektromotorů a jejich klíčové funkce?
Koncové zvony elektromotorů jsou obvykle umístěny na obou koncích skříně motoru a hrají několik nepostradatelných rolí v provozu a životnosti motoru. Pochopení jejich funkcí je zásadní pro pochopení přínosu používání pokročilých výrobních technik, jako je 3D tisk z kovu.
Klíčové funkce koncových zvonků elektromotorů:
- Podpora ložisek: Jednou z hlavních funkcí koncového zvonu je umístit a přesně podepřít ložiska motoru. Tato ložiska umožňují plynulé otáčení hřídele rotoru s minimálním třením. Přesné vyrovnání a bezpečné upevnění v koncovém zvonu jsou rozhodující pro efektivní a spolehlivý provoz motoru.
- Ochrana vnitřních součástí: Koncové zvony fungují jako ochranné štíty a chrání citlivé vnitřní součásti motoru, jako je statorové vinutí, rotor a komutátor (u stejnosměrných motorů), před vnějšími nečistotami, jako je prach, nečistoty a vlhkost. Tato ochrana je nezbytná pro zachování výkonu motoru a prodloužení jeho životnosti, zejména v náročných průmyslových podmínkách.
- Strukturální integrita: Koncové zvony významně přispívají k celkové tuhosti konstrukce elektromotoru. Pomáhají udržovat souosost vnitřních součástí a odolávají mechanickému namáhání, které se vyskytuje během provozu, včetně vibrací a tepelné roztažnosti.
- Odvod tepla: U některých konstrukcí motorů mohou hrát roli při odvádění tepla také koncové zvony. Mohou být opatřeny prvky, jako jsou žebra, nebo vyrobeny z tepelně vodivých materiálů, které pomáhají odvádět teplo od vnitřních součástí motoru, čímž zabraňují přehřívání a zajišťují optimální výkon.
- Montážní body: Koncové zvony často obsahují prvky, které slouží jako montážní body pro samotný motor a umožňují jeho bezpečné připevnění k poháněnému stroji nebo zařízení. Konstrukce a pevnost těchto montážních prvků jsou rozhodující pro stabilitu a spolehlivost celého systému.
Koncové zvony se tradičně vyrábějí metodami, jako je tlakové lití nebo obrábění. Tyto metody jsou sice dobře zavedené, ale mohou se potýkat s omezeními, pokud jde o složitost konstrukce, výběr materiálu a efektivitu výroby zakázkových nebo malosériových dílů. Zde se jako výkonná alternativa objevuje kovový 3D tisk, který nabízí řešení mnoha z těchto problémů. Pro ty, kteří mají zájem o prozkoumání širších aplikací kovového 3D tisku, jsou k dispozici zdroje, jako jsou informace dostupné na stránkách 3D tisk z kovu může poskytnout další poznatky.
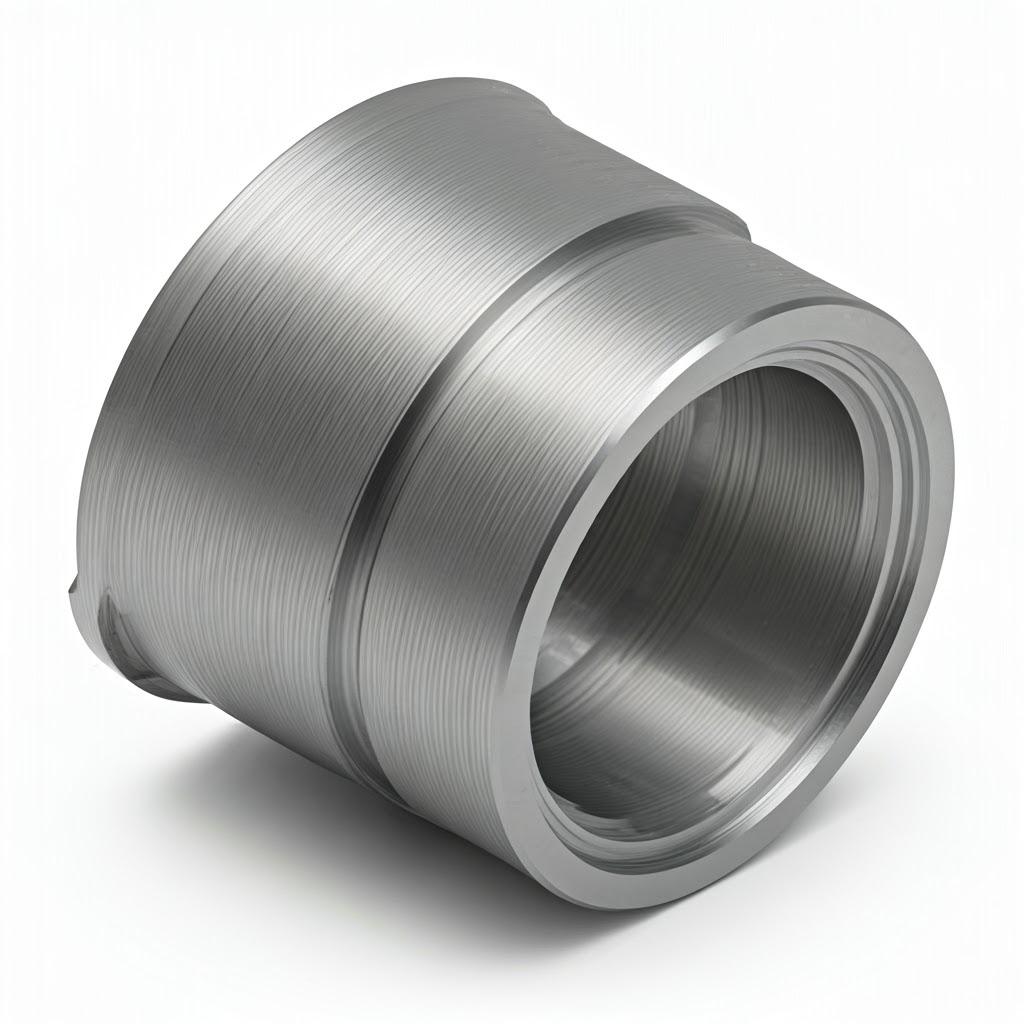
Proč zvolit 3D tisk z kovu pro výrobu koncových zvonků elektromotorů?
Využití kovového 3D tisku pro výrobu koncových zvonů elektromotorů nabízí oproti tradičním výrobním metodám řadu přesvědčivých výhod, a stává se tak stále atraktivnější volbou pro konstruktéry a manažery nákupu v různých průmyslových odvětvích.
Výhody 3D tisku kovů pro koncové zvony elektromotorů:
- Svoboda a složitost návrhu: 3D tisk z kovu umožňuje vytvářet složité geometrie a komplexní vnitřní prvky, které jsou často nemožné nebo nákladově neúnosné při použití tradičních metod, jako je odlévání nebo obrábění. Tato konstrukční svoboda umožňuje optimalizovat koncové zvony pro specifické požadavky na výkon, jako je lepší odvod tepla prostřednictvím integrovaných chladicích kanálů nebo snížení hmotnosti díky mřížkovým strukturám.
- Všestrannost materiálu: Kovový 3D tisk je kompatibilní se širokou škálou vysoce výkonných kovových prášků, včetně hliníkových slitin, jako je AlSi10Mg, a superslitin na bázi niklu, jako je IN625, které jsou doporučovány Metal3DP pro jejich vynikající mechanické vlastnosti a vhodnost pro náročné aplikace. Tato všestrannost umožňuje konstruktérům vybrat ideální materiál na základě konkrétních provozních podmínek a výkonnostních cílů elektromotoru. Metal3DP‘pokročilý systém výroby prášků zajišťuje výrobu vysoce kvalitních kovových prášků optimalizovaných pro různé metody tisku, jak je podrobně popsáno na jejich stránka produktu.
- Potenciál odlehčení: V průmyslových odvětvích, jako je letecký a automobilový průmysl, kde je snížení hmotnosti rozhodující pro účinnost paliva a výkon, umožňuje 3D tisk z kovu navrhovat koncové zvony s optimalizovanou topologií a lehkými mřížkovými strukturami. To může vést k výraznému snížení celkové hmotnosti elektromotoru, aniž by byla narušena strukturální integrita.
- Přizpůsobení a malosériová výroba: Na rozdíl od tradičních výrobních metod, které často vyžadují značné náklady na nástroje a jsou ekonomicky nejvýhodnější pro velké výrobní série, je kovový 3D tisk ideální pro výrobu přizpůsobených koncových zvonů nebo malých sérií. To je výhodné zejména pro výrobu prototypů, speciálních motorů nebo aplikací s jedinečnými požadavky.
- Rychlejší tvorba prototypů a zkrácení dodacích lhůt: 3D tisk z kovu výrazně urychluje proces výroby prototypů. Inženýři mohou rychle iterovat návrhy a vyrábět funkční prototypy koncových zvonů ve zlomku času ve srovnání s tradičními metodami. Tato rychlost uvedení na trh může být zásadní konkurenční výhodou.
- Efektivní využívání materiálů a snižování množství odpadu: Aditivní výrobní procesy vytvářejí díly vrstvu po vrstvě a používají pouze materiál potřebný pro danou součást. To vede k podstatně menšímu plýtvání materiálem ve srovnání se subtraktivními metodami, jako je obrábění, při němž se odstraňuje podstatná část surového materiálu.
- Integrace více funkcí: 3D tisk z kovu umožňuje integrovat více funkcí do jediné součásti. Například chladicí kanály, montážní prvky a konstrukční výztuhy lze navrhnout a vytisknout jako jeden jednotný koncový zvon, což snižuje potřebu montáže a zvyšuje spolehlivost.
Metal3DP‘odbornost v obou tiskárny SEBM a pokročilých kovových prášků je staví do pozice klíčového nástroje pro společnosti, které chtějí tyto výhody využít ve svých výrobních procesech elektromotorů.
Doporučené kovové prášky pro 3D tisk koncových zvonků elektromotorů: AlSi10Mg a IN625
Výběr vhodného kovového prášku má zásadní význam pro dosažení požadovaných výkonnostních charakteristik 3D tištěných koncových zvonů elektromotorů. Metal3DP doporučuje dva vysoce výkonné materiály, AlSi10Mg a IN625, z nichž každý nabízí jedinečný soubor vlastností, díky nimž jsou vhodné pro různé aplikační požadavky.
1. AlSi10Mg (slitina hliníku, křemíku a hořčíku):
AlSi10Mg je široce používaná hliníková slitina pro 3D tisk z kovu, která je známá pro svou vynikající kombinaci mechanických vlastností, tepelné vodivosti a nízké hmotnosti.
- Klíčové vlastnosti a výhody:
- Vysoký poměr pevnosti k hmotnosti: Slitiny hliníku, včetně slitiny AlSi10Mg, mají vynikající pevnost v poměru k hustotě, takže jsou ideální pro aplikace, kde je důležité snížit hmotnost, například v letectví a automobilových elektromotorech.
- Dobrá tepelná vodivost: Tato vlastnost je pro koncové zvony elektromotorů klíčová, protože usnadňuje účinný odvod tepla, pomáhá udržovat optimální provozní teploty a prodlužuje životnost motoru.
- Vynikající zpracovatelnost: AlSi10Mg vykazuje dobrou tisknutelnost pomocí technologií laserové fúze v práškovém loži (LPBF), což umožňuje vytvářet složité geometrie s vysokou přesností.
- Dobrá odolnost proti korozi: Slitina nabízí přiměřenou odolnost proti korozi v různých provozních prostředích, což zvyšuje životnost koncového zvonu.
- Nákladově efektivní: V porovnání s některými jinými vysoce výkonnými slitinami je AlSi10Mg často cenově výhodnější, což z něj činí životaschopnou volbu pro širokou škálu aplikací.
- Typické aplikace v elektromotorech:
- Koncové zvonky pro lehké elektromotory v automobilovém a leteckém průmyslu.
- Skříně motorů nebo komponenty, u nichž je tepelný management významným problémem.
- Aplikace vyžadující dobrou pevnost a tuhost při střední hmotnosti.
2. IN625 (slitina niklu, chromu a molybdenu):
IN625 je vysoce výkonná superslitina na bázi niklu, která je známá svou výjimečnou pevností, odolností proti korozi a schopností odolávat vysoké teploty.
- Klíčové vlastnosti a výhody:
- Vysoká pevnost při zvýšených teplotách: IN625 si zachovává mechanickou pevnost i při vysokých provozních teplotách, takže je vhodný pro náročné motorové aplikace, kde se očekává značná tvorba tepla.
- Vynikající odolnost proti korozi a oxidaci: Tato slitina nabízí vynikající odolnost vůči široké škále korozivních prostředí a oxidaci při vysokých teplotách, což zajišťuje dlouhodobou spolehlivost koncového zvonu v náročných podmínkách.
- Vysoká únavová pevnost: IN625 vykazuje vynikající odolnost proti únavovému poškození, což je zásadní pro součásti vystavené cyklickému zatížení a vibracím v elektromotorech.
- Dobrá svařitelnost a vyrobitelnost: Ačkoli se IN625 používá především ve formě prášku pro 3D tisk, jeho inherentní svařitelnost svědčí o jeho robustních metalurgických vlastnostech.
- Typické aplikace v elektromotorech:
- Koncové zvony pro vysoce výkonné elektromotory používané v průmyslových strojích, při zpracování chemikálií a v námořním prostředí, kde je rozhodující odolnost proti korozi a výkon při vysokých teplotách.
- Motory pracující při vysokém zatížení a značném tepelném namáhání.
- Speciální aplikace vyžadující mimořádnou odolnost a spolehlivost.
Metal3DP‘závazek poskytovat vysoce kvalitní kovové prášky vyráběné pomocí špičkových technologií plynové atomizace a PREP zajišťuje, že zákazníci mohou získat husté, vysoce výkonné kovové díly s vynikajícími mechanickými vlastnostmi, ať už se rozhodnou pro AlSi10Mg nebo IN625 pro aplikace koncových zvonů elektromotorů. Další informace o Metal3DP‘pokročilý systém výroby prášku, můžete navštívit jejich stránka o nás.
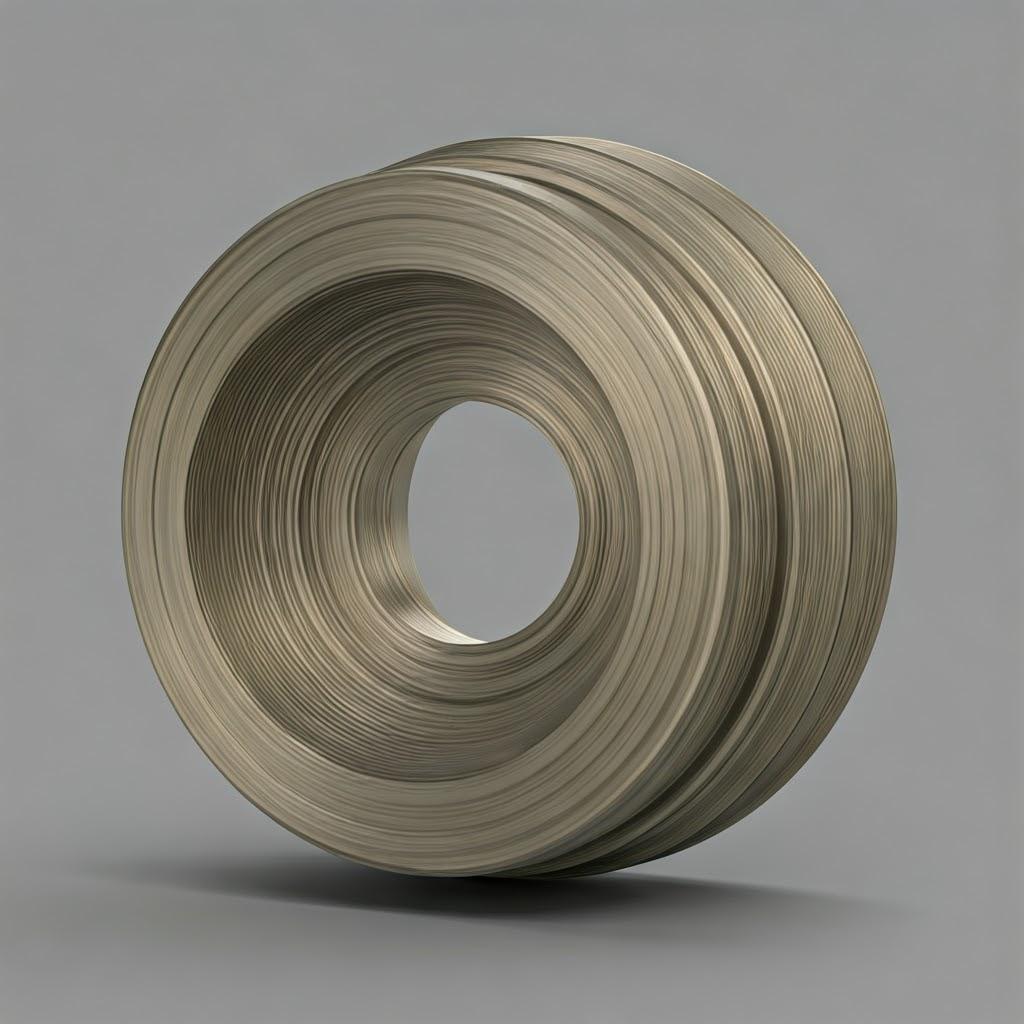
Úvahy o návrhu pro optimalizaci koncových zvonů elektromotorů tištěných na 3D tiskárně
Využití plného potenciálu kovového 3D tisku pro koncové zvony elektromotorů vyžaduje změnu v konstrukčním myšlení ve srovnání s tradiční výrobou. Zásady návrhu pro aditivní výrobu (DfAM) se stávají prvořadými pro optimalizaci funkčnosti, snížení spotřeby materiálu a zvýšení výkonu.
Klíčové aspekty návrhu 3D tištěných koncových zvonů:
- Optimalizace topologie: Tento výpočetní přístup umožňuje inženýrům definovat funkční požadavky a omezení koncového zvonu a následně algoritmy vygenerují optimalizovanou geometrii, která minimalizuje hmotnost a zároveň maximalizuje pevnost a tuhost. To může vést k organickým, neintuitivním tvarům, kterých lze dosáhnout pouze aditivní výrobou.
- Mřížové struktury: Začleněním mřížových nebo buněčných struktur do konstrukce čelního zvonu lze výrazně snížit hmotnost, aniž by byla obětována strukturální integrita. Tyto vnitřní struktury lze přizpůsobit tak, aby poskytovaly specifické charakteristiky tuhosti nebo absorpce energie v různých oblastech součásti.
- Integrované funkce: 3D tisk z kovu umožňuje integrovat více funkcí do jediného dílu. Pro koncové zvonky to může zahrnovat:
- Integrované chladicí kanály: Konstrukce vnitřních kanálů pro proudění chladicí kapaliny může zlepšit odvod tepla přímo v konstrukci koncového zvonu, čímž se zvýší účinnost a životnost motoru.
- Montážní prvky: Namísto samostatných upevňovacích prvků lze montážní šrouby, příruby nebo závity zabudovat přímo do konstrukce koncového zvonu.
- Ložisková sedadla: Přesná ložisková sedla lze navrhnout s optimálními tolerancemi a povrchovou úpravou přímo do tištěného dílu, což zajišťuje přesné vyrovnání ložisek a hladký chod.
- Tloušťka stěny a žebrování: Pečlivé zvážení tloušťky stěny a strategické umístění žeber nebo výztuh může optimalizovat poměr pevnosti a hmotnosti koncového zvonu. Pro zajištění větší pevnosti v oblastech s vysokým namáháním a minimalizaci spotřeby materiálu v méně kritických oblastech lze použít proměnnou tloušťku stěny.
- Podpůrné struktury: Podpůrné konstrukce jsou při 3D tisku z kovu často nezbytné, aby se zabránilo zhroucení nebo deformaci převislých prvků, jejich návrh a umístění je však třeba pečlivě zvážit, aby se minimalizovala spotřeba materiálu, doba tisku a náročnost následného zpracování. Přednost by měly mít konstrukční prvky, které snižují potřebu rozsáhlých podpěr, jako jsou samonosné úhelníky.
- Orientace a strategie budování: Orientace koncového zvonu na konstrukční platformě může významně ovlivnit povrchovou úpravu, požadavky na podporu a mechanické vlastnosti konečného dílu. Optimalizace orientace sestavení je klíčová pro dosažení požadované kvality a efektivity.
- Souhra výběru materiálu a designu: Volba materiálu (např. AlSi10Mg nebo IN625) ovlivní rozhodnutí o konstrukci. Například vyšší pevnost materiálu IN625 může u některých aplikací umožnit tenčí stěny nebo agresivnější strategie odlehčování ve srovnání s materiálem AlSi10Mg.
Využitím těchto principů DfAM mohou konstruktéři plně využít potenciál 3D tisku kovů a vytvářet vysoce výkonné, optimalizované koncové zvony elektromotorů přizpůsobené potřebám konkrétních aplikací.
Dosažení přesnosti: Tolerance, povrchová úprava a rozměrová přesnost u 3D tištěných koncových zvonů
V kritických aplikacích, jako jsou elektromotory, jsou tolerance, povrchová úprava a rozměrová přesnost součástí, jako jsou koncové zvony, nejdůležitější pro zajištění správného uložení, funkčnosti a dlouhodobé spolehlivosti. Technologie 3D tisku z kovu dosáhly významného pokroku v dosahování těsných tolerancí a dobré povrchové úpravy, ačkoli tyto aspekty mohou být ovlivněny různými faktory.
Faktory ovlivňující přesnost 3D tištěných kovových koncových zvonů:
- Technologie tisku: Různé procesy 3D tisku kovů, jako je například laserová fúze v práškovém loži (LPBF) a tavení elektronovým svazkem (EBM), mají své vlastní možnosti a omezení, pokud jde o dosažitelnou přesnost. LPBF obecně nabízí jemnější rozlišení prvků a přísnější tolerance ve srovnání s EBM. Metal3DP‘řada tiskáren SEBM je známá svou přesností a spolehlivostí při výrobě kritických dílů.
- Vlastnosti materiálu: Konečnou rozměrovou přesnost může ovlivnit také materiál, na který se tiskne, a to v důsledku faktorů, jako je tepelná roztažnost a smršťování během procesu tisku. Materiály s nižšími koeficienty tepelné roztažnosti mohou vykazovat lepší rozměrovou stabilitu.
- Parametry procesu: Parametry tisku, jako je výkon laseru, rychlost skenování, tloušťka vrstvy a teplota práškového lože, významně ovlivňují přesnost a kvalitu povrchu vytištěného dílu. Optimalizované sady parametrů mají zásadní význam pro dosažení požadovaných výsledků.
- Budování orientačních a podpůrných struktur: Jak již bylo zmíněno, orientace dílu na konstrukční plošině a konstrukce podpěrných konstrukcí může ovlivnit rozměrovou přesnost i kvalitu povrchu, zejména na plochách směřujících dolů, kde může odstranění podpěr zanechat stopy.
- Následné zpracování: Zatímco pro některé aplikace může být povrchová úprava ve stavu po tisku dostatečná, v případě potřeby lze použít techniky následného zpracování, jako je obrábění, leštění nebo povrchová úprava, aby se dosáhlo přísnějších tolerancí a hladšího povrchu.
Typické dosažitelné tolerance a povrchové úpravy:
Ačkoli se konkrétní hodnoty mohou lišit v závislosti na výše uvedených faktorech, lze při 3D tisku kovů obvykle dosáhnout rozměrové přesnosti v rozmezí ±0,1 až ±0,05 mm u kritických prvků. Povrchová úprava se obecně pohybuje v rozmezí 5 až 20 μmRa ve stavu po tisku. Následné zpracování může tyto hodnoty dále zlepšit.
Zajištění přesnosti pro koncové zvony elektromotorů:
- Design pro přesnost: Začlenění konstrukčních prvků, které minimalizují potřebu podpůrných konstrukcí v kritických oblastech, a orientace dílu tak, aby se snížily převisy, může zlepšit přesnost a kvalitu povrchu.
- Optimalizace procesů: Spolupráce se zkušenými poskytovateli služeb 3D tisku z kovu, jako jsou Metal3DP, kteří mají odborné znalosti v oblasti optimalizace procesních parametrů pro konkrétní materiály a geometrie, je zásadní.
- Kontrola kvality: Zavedení přísných opatření pro kontrolu kvality, včetně kontroly rozměrů pomocí souřadnicových měřicích strojů (CMM) a měření drsnosti povrchu, zajišťuje, že vytištěné koncové zvony splňují požadované specifikace.
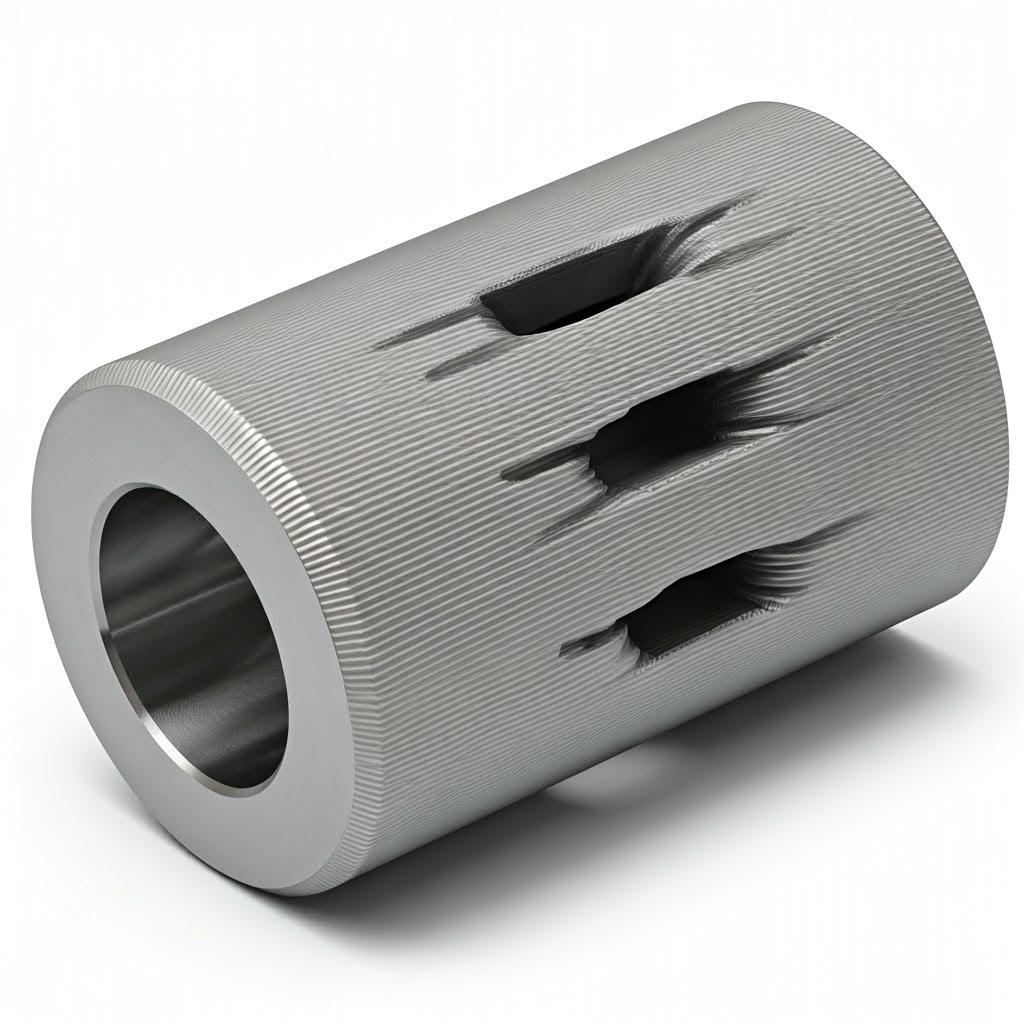
Techniky následného zpracování kovových 3D tištěných koncových zvonů elektromotorů
Přestože 3D tisk z kovu nabízí značné výhody při vytváření složitých geometrií, jsou často nutné kroky následného zpracování, aby bylo dosaženo konečných požadovaných vlastností, tolerancí a povrchové úpravy koncových zvonků elektromotorů.
Běžné požadavky na následné zpracování:
- Odstranění podpory: Podpěrné konstrukce použité při tisku je třeba opatrně odstranit. To může zahrnovat ruční lámání, řezání nebo použití specializovaných nástrojů a přípravků. Konstrukce podpěr by měla být zaměřena na minimalizaci námahy a možnosti poškození povrchu při odstraňování.
- Tepelné ošetření proti stresu: Kovové 3D tištěné díly často obsahují zbytková napětí v důsledku rychlých cyklů zahřívání a ochlazování během procesu tisku. Tepelným zpracováním se snižují tato vnitřní napětí, což může zlepšit rozměrovou stabilitu a mechanické vlastnosti.
- Izostatické lisování za tepla (HIP): HIP je proces, při kterém se na tištěný díl současně působí vysokým tlakem a teplotou. Tím lze výrazně snížit vnitřní pórovitost, zvýšit hustotu a zlepšit celkové mechanické vlastnosti materiálu, zejména u kritických aplikací.
- CNC obrábění: Pro dosažení velmi těsných tolerancí a specifických povrchových úprav kritických prvků, jako jsou ložisková sedla nebo montážní plochy, může být jako sekundární operace vyžadováno CNC obrábění. Kombinuje se tak konstrukční flexibilita 3D tisku s přesností tradičního obrábění.
- Povrchová úprava: V závislosti na požadavcích aplikace lze použít různé techniky povrchové úpravy, aby se zlepšila estetika, odolnost proti korozi nebo tribologické vlastnosti koncových zvonů. Mohou zahrnovat:
- Leštění: Mechanické nebo chemické leštění může snížit drsnost povrchu.
- Výbuch v médiích: Techniky, jako je kuličkování nebo pískování, mohou zlepšit tvrdost povrchu a únavovou životnost.
- Povrchová úprava: Použití ochranných nátěrů, jako je eloxování hliníkových slitin nebo specializované nátěry pro zvýšení odolnosti proti korozi, může zvýšit životnost koncových zvonů.
Úvahy o následném zpracování:
- Náklady a čas: Kroky následného zpracování zvyšují celkové náklady a dobu výroby 3D tištěných dílů. Výběr technik následného zpracování je třeba pečlivě zvážit na základě požadavků aplikace a rozpočtu.
- Odbornost a vybavení: Některé techniky následného zpracování, jako je HIP nebo přesné CNC obrábění, vyžadují specializované vybavení a odborné znalosti. Spolupráce s poskytovatelem komplexních služeb v oblasti 3D tisku kovů, jako je např Metal3DP, který nabízí komplexní možnosti následného zpracování, může zefektivnit výrobní proces.
Problémy při 3D tisku koncových zvonků elektromotorů a jejich řešení
3D tisk z kovu sice nabízí řadu výhod, ale existují také potenciální problémy, které je třeba řešit, aby byla zajištěna úspěšná výroba vysoce kvalitních koncových zvonů elektromotorů.
Obvyklé problémy a jak se jim vyhnout:
- Deformace a zkreslení: Tepelné namáhání během tisku může vést k deformaci nebo zkreslení dílu, zejména u velkých nebo složitých geometrií.
- Řešení: Optimalizujte orientaci stavby, používejte vhodné podpůrné konstrukce a pečlivě kontrolujte parametry procesu. Tyto problémy může zmírnit také tepelné zpracování po tisku.
- Obtíže při odstraňování podpory: Agresivně přilepené nosné konstrukce je obtížné odstranit bez poškození povrchu dílu.
- Řešení: Navrhněte pokud možno samonosné geometrie, optimalizujte konstrukci podpěrné konstrukce pro snadné odstranění a používejte vhodné nástroje a techniky pro odstranění podpěr.
- Problémy s pórovitostí a hustotou: Nedostatečné roztavení nebo ztuhnutí kovového prášku může mít za následek pórovitost tištěného dílu, což může ohrozit jeho mechanickou pevnost a únavovou životnost.
- Řešení: Optimalizujte výkon laseru nebo elektronového paprsku a strategie skenování, zajistěte vysoce kvalitní kovový prášek s dobrou tekutostí (jak je uvedeno v tabulce 1) Metal3DP) a zvažte lisování za tepla (HIP) pro zhutnění.
- Drsnost povrchu: Povrchová úprava jako při tisku nemusí být vhodná pro všechny aplikace, zejména pro kritické styčné plochy, jako jsou ložisková sedla.
- Řešení: Optimalizujte parametry tisku, zvažte orientaci sestavení a použijte vhodné techniky následného zpracování, jako je obrábění nebo leštění.
- Dosažení těsných tolerancí: Dodržení přesnosti rozměrů může být náročné, zejména u složitých geometrií a velkých dílů.
- Řešení: Navrhujte s ohledem na tolerance, optimalizujte procesní parametry, využívejte vysoce přesná zařízení pro 3D tisk (např Metal3DP‘nabídky) a zvažte sekundární obrábění kritických prvků.
- Variabilita vlastností materiálu: Mechanické vlastnosti 3D tištěných kovů se někdy mohou lišit v závislosti na orientaci konstrukce a parametrech procesu.
- Řešení: Důkladně charakterizujte vlastnosti materiálu pro konkrétní parametry tisku a orientaci sestavení a zaveďte důkladná opatření pro kontrolu procesu.
- Úvahy o ceně: Zatímco 3D tisk může být nákladově efektivní pro nízké objemy nebo vysoce přizpůsobené díly, náklady na jeden díl mohou být vyšší než u tradičních metod pro velké objemy výroby.
- Řešení: Optimalizujte konstrukce s ohledem na efektivitu materiálu, v případě potřeby prozkoumejte nákladově efektivní materiály, jako je AlSi10Mg, a pečlivě zhodnoťte celkovou nabídku hodnoty, včetně faktorů, jako je zkrácení dodacích lhůt a flexibilita konstrukce.
Pochopením těchto potenciálních problémů a zavedením vhodných řešení mohou výrobci efektivně využít 3D tisk kovů k výrobě vysoce kvalitních koncových zvonů elektromotorů, které splňují přísné požadavky na výkon.

Výběr správného poskytovatele služeb 3D tisku kovů pro potřeby vašeho koncového zvonu
Výběr správného poskytovatele služeb 3D tisku z kovu je zásadním rozhodnutím, které může významně ovlivnit kvalitu, náklady a dobu realizace vašich koncových zvonů elektromotorů. Zde jsou klíčové faktory, které je třeba vzít v úvahu při hodnocení potenciálních dodavatelů:
Klíčové aspekty výběru poskytovatele služeb 3D tisku z kovu:
- Materiálové schopnosti: Ujistěte se, že dodavatel má zkušenosti s prací s doporučenými kovovými prášky pro vaši aplikaci (např. AlSi10Mg, IN625) a může poskytnout certifikace materiálů a údaje o testování. Metal3DP nabízí širokou škálu vysoce kvalitních kovových prášků optimalizovaných pro aditivní výrobu.
- Tiskové technologie a zařízení: Porozumět typům technologií 3D tisku kovů, které poskytovatel používá (např. LPBF, EBM). Volba technologie může ovlivnit dosažitelnou přesnost, povrchovou úpravu a vlastnosti materiálu. Metal3DP se specializuje na tiskárny SEBM, které jsou známé svou přesností a spolehlivostí. Můžete se dozvědět více o různých tiskových metod na svých webových stránkách.
- Konstrukční a inženýrská podpora: Dobrý poskytovatel služeb by měl nabízet konzultace a optimalizační služby, které vám pomohou využít principy DfAM a zajistit, aby byl návrh vašeho konečného zvonu vhodný pro 3D tisk z kovu.
- Možnosti následného zpracování: Zjistěte, zda poskytovatel nabízí potřebné služby následného zpracování, jako je odstranění podpěr, tepelné zpracování, HIP, obrábění a povrchová úprava, aby splnil vaše specifické požadavky. Komplexní nabídka služeb může zefektivnit výrobní proces.
- Zajištění kvality a certifikace: Informujte se o systémech řízení kvality, kontrolních procesech a příslušných průmyslových certifikátech (např. ISO 9001, AS9100 pro letecký průmysl). Tím zajistíte, že vyrobené díly splňují přísné normy kvality.
- Zkušenosti a odbornost: Hledejte poskytovatele s prokazatelnými výsledky v oblasti 3D tisku z kovu, ideálně se zkušenostmi s výrobou komponentů pro podobná odvětví nebo aplikace. Jejich odborné znalosti mohou pomoci předvídat a překonat potenciální problémy.
- Výrobní kapacita a škálovatelnost: Posuďte, zda je poskytovatel schopen zvládnout vaše současné a budoucí objemy výroby. Ujistěte se, že má k dispozici vybavení a zdroje, které splňují vaše požadavky na dobu realizace.
- Komunikace a zákaznická podpora: Pro hladkou a úspěšnou spolupráci je nezbytná efektivní komunikace a pohotová zákaznická podpora.
- Struktura nákladů a cen: Zjistěte, jaký je cenový model poskytovatele, včetně nákladů na materiál, poplatků za tisk a následné zpracování. Vyžádejte si podrobnou cenovou nabídku a porovnejte ji s jinými poskytovateli.
- Umístění a logistika: Zvažte umístění poskytovatele a jeho schopnost efektivně řešit přepravu a logistiku, zejména v případě větších výrobních sérií.
Při hodnocení potenciálních partnerů mějte na paměti, že Metal3DP je předním poskytovatelem s desítkami let společných zkušeností v oblasti aditivní výroby kovů, který nabízí komplexní řešení zahrnující tiskárny SEBM, pokročilé kovové prášky a služby vývoje aplikací. Jejich možnosti můžete dále prozkoumat na jejich webové stránky.
Pochopení nákladových faktorů a dodacích lhůt pro 3D tištěné koncové zvony elektromotorů
Náklady a doba výroby koncových zvonů elektromotorů pomocí kovového 3D tisku jsou ovlivněny několika faktory. Jejich pochopení může pomoci při sestavování rozpočtu a efektivním plánování projektů.
Klíčové nákladové faktory:
- Náklady na materiál: Významným faktorem je cena kovového prášku (např. AlSi10Mg, IN625). Vysoce výkonné slitiny, jako je IN625, mají obvykle vyšší náklady na materiál než hliníkové slitiny.
- Doba tisku: Doba sestavení závisí na velikosti a složitosti konečného zvonu, na výšce použité vrstvy a na počtu dílů, které se tisknou na sestavovací platformě současně. Delší doba tisku znamená vyšší provozní náklady stroje.
- Odpisy a provoz stroje: Poskytovatelé služeb do svých cen započítávají náklady na zařízení, údržbu a spotřebu energie.
- Předběžné zpracování a optimalizace návrhu: Pokud od poskytovatele požadujete optimalizaci návrhu nebo služby předběžného zpracování, zvýší se tím celkové náklady.
- Náklady na následné zpracování: Rozsah požadovaného následného zpracování (např. odstranění podpory, tepelné zpracování, obrábění, povrchová úprava) významně ovlivní konečné náklady. Složité pracovní postupy následného zpracování budou dražší.
- Kontrola kvality a inspekce: Přísné postupy kontroly kvality a rozměrové kontroly zvyšují náklady, ale jsou nezbytné pro zajištění kvality dílů.
- Objem a měřítko: 3D tisk je sice výhodný pro nízké až střední objemy a přizpůsobení, ale náklady na jeden díl nemusí být tak konkurenceschopné jako u tradičních metod pro velmi vysoké objemy výroby bez ohledu na design pro hromadnou výrobu.
Typické dodací lhůty:
Dodací lhůty pro kovové 3D tištěné koncové zvony se mohou lišit v závislosti na faktorech, jako jsou:
- Složitost a velikost části: Složitější nebo větší díly obvykle vyžadují delší dobu tisku.
- Dostupnost materiálu: Dostupnost vybraného kovového prášku může ovlivnit dobu dodání. Metal3DP vyrábí širokou škálu vysoce kvalitních kovových prášků, což může snížit zpoždění při shánění materiálu.
- Kapacita poskytovatele služeb: Aktuální pracovní vytížení a kapacita vybraného poskytovatele služeb ovlivní dobu zpracování.
- Požadavky na následné zpracování: Rozsáhlé kroky následného zpracování prodlužují celkovou dobu přípravy.
- Přeprava a logistika: Je třeba vzít v úvahu dobu přepravy, zejména u mezinárodních zásilek.
U prototypů nebo malých sérií se doba dodání může pohybovat od několika dnů do několika týdnů. U větších výrobních sérií jsou dodací lhůty delší a závisí na kapacitě poskytovatele a složitosti dílů. Je velmi důležité jasně prodiskutovat očekávané doby realizace s vybraným poskytovatelem služeb 3D tisku z kovu.
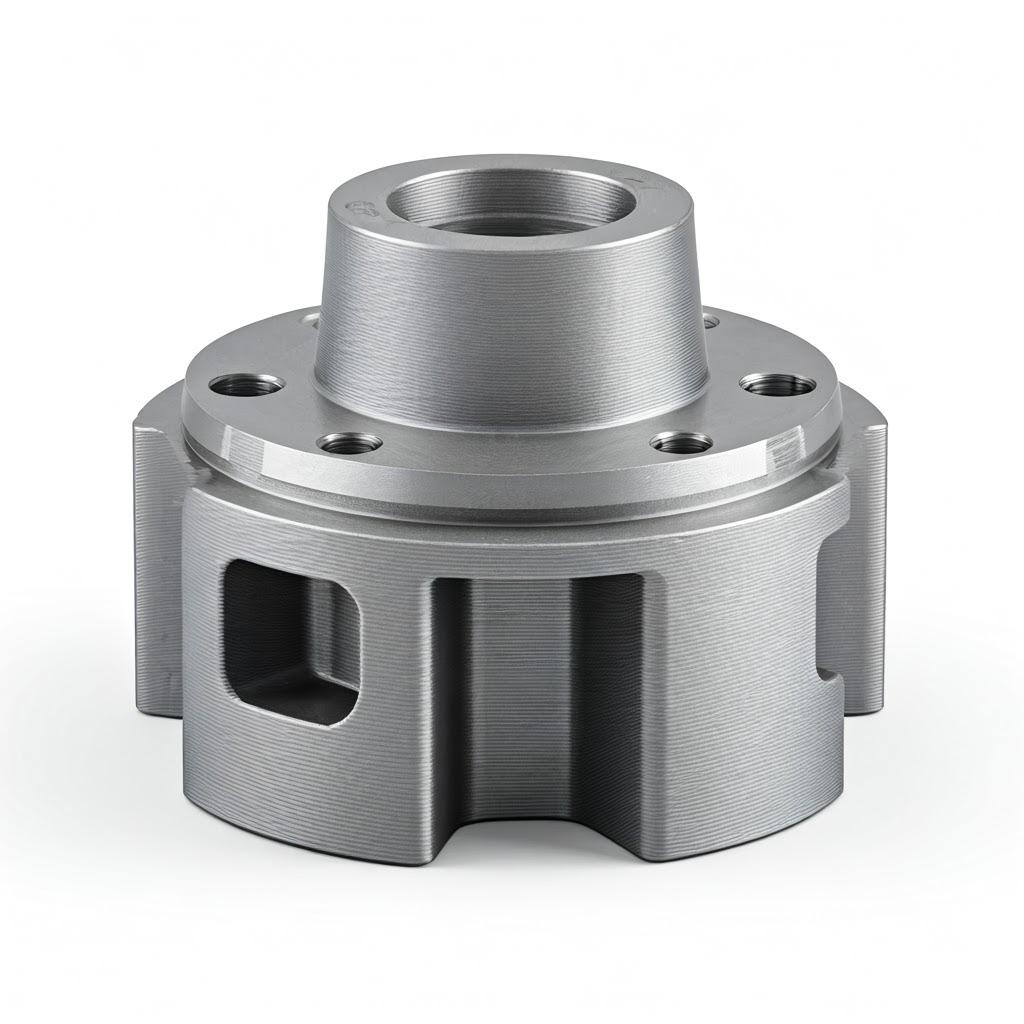
Často kladené otázky (FAQ) o 3D tisku koncových zvonů elektromotorů
Zde je několik často kladených otázek týkajících se použití kovového 3D tisku pro koncové zvony elektromotorů:
Otázka 1: Mohou kovové 3D tištěné zvony dosáhnout stejné pevnosti a odolnosti jako tradičně vyráběné zvony?
A: Ano, pokud je proces optimalizován a jsou použity správné materiály a techniky následného zpracování (například HIP pro zvýšení hustoty), mohou kovové 3D tištěné koncové zvony dosáhnout nebo dokonce překonat pevnost a trvanlivost tradičně vyráběných dílů. Materiály jako IN625 nabízejí výjimečnou pevnost při vysokých teplotách a odolnost proti korozi.
Otázka 2: Je kovový 3D tisk nákladově efektivní pro velkosériovou výrobu koncových zvonů elektromotorů?
A: Zatímco kovový 3D tisk vyniká při výrobě složitých geometrií a dílů na míru v nízkých až středních objemech, je třeba pečlivě posoudit nákladovou efektivitu pro velmi rozsáhlou výrobu. Faktory, jako jsou náklady na materiál a rychlost tisku, mohou ovlivnit celkové náklady na jeden díl ve srovnání s velkoobjemovými výrobními metodami, jako je tlakové lití. U složitých konstrukcí nebo při zvážení celkových nákladů na životní cyklus (včetně nákladů na nástroje, iterací konstrukce a potenciálu pro konsolidaci dílů) však může být 3D tisk velmi konkurenceschopný.
Otázka 3: Jaké konstrukční úpravy jsou obvykle nutné při přechodu z tradiční výroby na 3D tisk kovových zvonků?
A: Měly by být použity zásady návrhu pro aditivní výrobu (DfAM). To často zahrnuje optimalizaci geometrie pro snížení hmotnosti (např. použití mřížkových struktur), integraci více dílů do jednoho návrhu a zohlednění požadavků na podpůrnou konstrukci a její orientaci. Lze také začlenit prvky, jako jsou vnitřní chladicí kanály nebo přizpůsobená montážní řešení.
Otázka 4: Jaké materiály se běžně používají pro 3D tisk koncových zvonů elektromotorů a proč se doporučuje AlSi10Mg a IN625?
A: Mezi běžné materiály patří slitiny hliníku (např. AlSi10Mg), nerezové oceli, slitiny titanu a superslitiny na bázi niklu (např. IN625). AlSi10Mg se doporučuje pro svůj vynikající poměr pevnosti k hmotnosti a tepelnou vodivost, takže je vhodný pro lehké aplikace, kde je důležitý odvod tepla. Slitina IN625 je volena pro svou výjimečnou pevnost při vysokých teplotách a odolnost proti korozi, což je ideální pro náročné průmyslové prostředí. Metal3DP nabízí komplexní portfolio vysoce kvalitních kovových prášků, včetně těchto doporučených možností.
Otázka 5: Jaká je povrchová úprava 3D tištěného kovového zvonu ve srovnání s obráběným zvonem a lze ji zlepšit?
A: Povrch po vytištění je obvykle drsnější než povrch po obrábění. V případě kritických rozhraní, jako jsou ložisková sedla, lze však použít různé techniky následného zpracování, jako je leštění, tryskání a obrábění, aby se dosáhlo hladšího povrchu a přísnějších tolerancí.
Závěr - Využití 3D tisku kovů pro výrobu pokročilých koncových zvonů elektromotorů
Kovový 3D tisk rychle mění výrobní prostředí a nabízí výkonný soubor nástrojů pro výrobu složitých, vysoce výkonných součástí, jako jsou koncové zvony elektromotorů. Schopnost využít svobodu konstrukce, využít pokročilé materiály, jako jsou AlSi10Mg a IN625, a dokonce integrovat funkce otevírá nové možnosti optimalizace výkonu motoru, snížení hmotnosti a urychlení inovací.
Firmy jako Metal3DP stojí v čele této revoluce a poskytuje nejen špičkovou technologii tisku SEBM, ale také komplexní sortiment vysoce kvalitních kovových prášků a odborné znalosti v oblasti vývoje aplikací. Díky spolupráci se zkušenými poskytovateli a přijetí principů designu pro aditivní výrobu mohou inženýři a manažeři nákupu v letecké, automobilové, lékařské a průmyslové výrobě plně využít potenciál kovového 3D tisku k vytvoření řešení elektromotorů nové generace. Cesta k efektivnějším, přizpůsobeným a robustnějším elektromotorům je částečně poháněna transformačními schopnostmi aditivní výroby kovů. Chcete-li prozkoumat, jak Metal3DP může podpořit cíle vaší organizace’v oblasti aditivní výroby, doporučujeme vám kontaktujte nás.
Sdílet na
MET3DP Technology Co., LTD je předním poskytovatelem řešení aditivní výroby se sídlem v Qingdao v Číně. Naše společnost se specializuje na zařízení pro 3D tisk a vysoce výkonné kovové prášky pro průmyslové aplikace.
Dotaz k získání nejlepší ceny a přizpůsobeného řešení pro vaše podnikání!
Související články
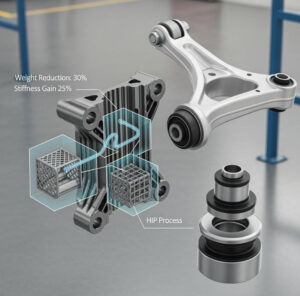
Metal 3D Printed Subframe Connection Mounts and Blocks for EV and Motorsport Chassis
Přečtěte si více "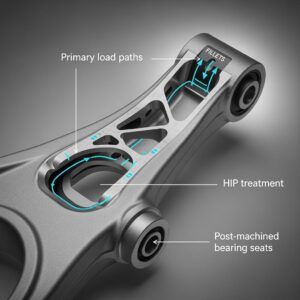
Metal 3D Printing for U.S. Automotive Lightweight Structural Brackets and Suspension Components
Přečtěte si více "O Met3DP
Nedávná aktualizace
Náš produkt
KONTAKTUJTE NÁS
Nějaké otázky? Pošlete nám zprávu hned teď! Po obdržení vaší zprávy obsloužíme vaši žádost s celým týmem.