FeCrAl pro svařování nástřikem
Obsah
Představte si, že na své komponenty nasadíte ochranný štít - štít, který odolá spalujícím teplotám, neúnavnému opotřebení a drsné oxidaci. To je kouzlo FeCrAl pro svařování nástřikem. FeCrAl však není jen univerzální řešení. Dodává se v rozmanitém týmu modelů kovových prášků, z nichž každý má své silné stránky. Připoutejte se, protože se chystáme ponořit do fascinujícího světa FeCrAl pro svařování stříkáním!
Přehled o FeCrAl pro svařování nástřikem
FeCrAl je slitina na bázi železa, která je odolná proti teplu, opotřebení a oxidaci. Při použití při svařování stříkáním vytváří hustý, dobře spojený povlak, který výrazně prodlužuje životnost a funkčnost vašich součástí. Zde je stručný přehled jejích klíčových vlastností:
- Odolnost proti vysokým teplotám: Slitiny FeCrAl odolávají teplotám přesahujícím 1400 °C, takže jsou ideální pro aplikace, jako jsou kotle, výměníky tepla a součásti pecí.
- Vynikající odolnost proti opotřebení: Představte si, že házíte písek na cihlovou zeď. Přesně tak si povlaky FeCrAl poradí s opotřebením. Vynikají v prostředí s vysokým třením a otěrem a chrání vaše díly před předčasným selháním.
- Vynikající odolnost proti oxidaci: FeCrAl vytváří stabilní oxidovou vrstvu, která působí jako bariéra proti kyslíku a dalším korozivním prvkům. To znamená vynikající ochranu v aplikacích vystavených drsnému prostředí, jako jsou chemické závody a zařízení na výrobu energie.
- Dobrá tvárnost a tvařitelnost: Představte si ohýbání kancelářské sponky, aniž by se zlomila. Povlaky FeCrAl nabízejí dobrou rovnováhu mezi pevností a pružností, což jim umožňuje přizpůsobit se mírně nepravidelným povrchům.
Ale FeCrAl není jen jeden hrdina. Je to celý tým! Různé modely prášků FeCrAl nabízejí rozdíly ve vlastnostech v závislosti na jejich specifickém složení. Pojďme tento rozmanitý tým podrobně prozkoumat.
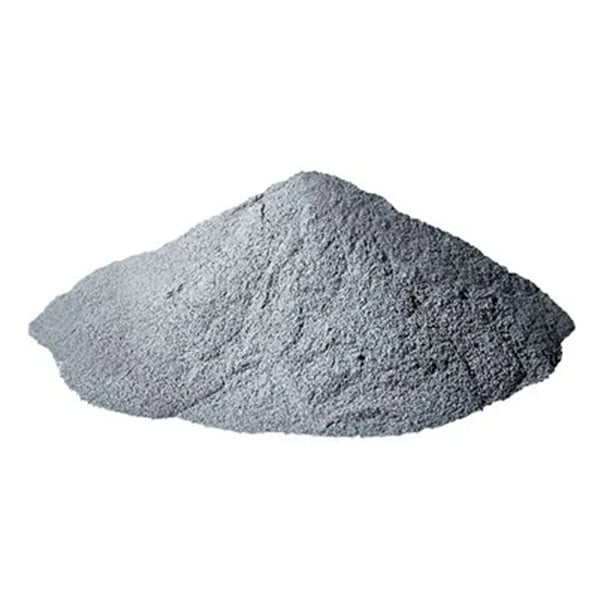
FeCrAl Kovový prášek Modely
Přinášíme vám bližší pohled na deset oblíbených modelů kovových prášků FeCrAl s důrazem na jejich silné stránky a ideální použití:
- FeCrAlY (Yttrium): Tento model obsahuje yttrium, prvek vzácných zemin, který zvyšuje jeho odolnost proti oxidaci při vysokých teplotách. Je mistrem v prostředí s extrémním teplem a drsnou atmosférou, takže je ideální pro součásti plynových turbín a vyzdívky pecí.
- FeCrAlSi (křemík): Křemík přináší zvýšenou odolnost proti oxidaci a zvýšenou smáčivost (schopnost stékat a roztírat se). Díky tomu je FeCrAlSi skvělou volbou pro aplikace zahrnující roztavené kovy nebo působení vysokoteplotní páry, jako jsou ventily a tělesa čerpadel.
- FeCrAlHf (hafnium): Hafnium, další prvek vzácných zemin, zvyšuje odolnost FeCrAlHf proti nauhličování (nežádoucí difúzi uhlíku do kovu). To z něj činí cennou výhodu pro ochranu součástí v prostředí nauhličování, jako jsou například trubky reformátorů v petrochemickém průmyslu.
- FeCrAlMo (molybden): Molybden posiluje tým tím, že zvyšuje jeho pevnost při vysokých teplotách. FeCrAlMo září v aplikacích, kde jsou součásti vystaveny vysokému namáhání a teplu současně, jako jsou například trubky přehříváků v elektrárnách.
- FeCrAl s nízkým obsahem hliníku: Tento model má nižší obsah hliníku, což vede k lepší elektrické vodivosti. Je to skvělá volba pro aplikace, kde je elektrická vodivost klíčová, jako jsou elektrody a elektrické kontakty vystavené vysokým teplotám.
- FeCrAl s vysokým obsahem hliníku: Zde se zvyšuje obsah hliníku, čímž se ještě více zvyšuje odolnost slitiny vůči oxidaci. Tento model vyniká v prostředích s extrémním teplem a silnými oxidačními problémy, jako jsou součásti pecí a výfukové potrubí.
- FeCrAlRE (vzácné zeminy): Tato široká kategorie zahrnuje různé slitiny FeCrAl s různými přídavky prvků vzácných zemin, z nichž každá nabízí jedinečné výhody. Například lanthan může zlepšit odolnost proti oxidaci, zatímco cer zvyšuje výkonnost v podmínkách cyklického zahřívání a chlazení.
- FeCrAl na bázi niklu: V tomto modelu se k nim přidává i nikl, který zvyšuje jejich odolnost vůči sulfidaci (působení sloučenin obsahujících síru). To z něj činí silného spojence v prostředí s vysokým obsahem síry, jako jsou ropné rafinerie a uhelné elektrárny.
- Metalocén FeCrAl: Tento model, vyráběný specializovanou technikou, nabízí výjimečnou čistotu prášku a velmi jemnou velikost zrn. To se promítá do vynikající kvality povlaku, hustoty a celkového výkonu.
- Vlastní slitiny FeCrAl: Nevidíte zde řešení svých konkrétních potřeb? Krása FeCrAl spočívá v jeho všestrannosti. Slitiny na zakázku lze připravit tak, aby splňovaly vaše jedinečné požadavky, a přizpůsobit jejich složení pro optimální výkon ve vaší konkrétní aplikaci.
Aplikace z FeCrAl pro svařování stříkáním
FeCrAl není jen tak ledajaký. Jeho rozmanitý tým modelů kovových prášků umožňuje širokou škálu aplikací v různých průmyslových odvětvích. Zde je pohled na to, kde FeCrAl září:
- Výroba energie: FeCrAl chrání před vysokými teplotami, oxidací a opotřebením, od trubek přehříváků a hlavic kotlů až po součásti parních turbín, a zajišťuje tak plynulou a efektivní výrobu energie.
- Petrochemický průmysl: Trubky reformerů, součásti krakování a zařízení vystavená působení vysokoteplotních uhlovodíků těží z výjimečné odolnosti FeCrAl proti nauhličování a oxidaci.
- Cementářský průmysl: Součásti rotačních pecí, jako jsou hlavy hořáků a cyklony předehřívačů, jsou vystaveny extrémnímu teplu a drsnému prostředí. Povlaky FeCrAl prodlužují jejich životnost a minimalizují prostoje.
- Ocelářský průmysl: FeCrAl chrání zařízení, jako jsou válce pecí, výměníky tepla a tundry, před oxidací, opotřebením a tepelnou únavou, což vede ke zvýšení účinnosti a doby provozu.
- Zařízení na výrobu energie z odpadu: Součásti vystavené náročné kombinaci vysokých teplot a korozivních spalin nacházejí silného spojence v povlacích FeCrAl.
- Letecký a kosmický průmysl: Výfukové potrubí, tepelné štíty a další součásti vystavené vysokému teplu v proudových motorech těží ze schopnosti FeCrAl odolávat extrémním teplotám a oxidaci.
- Automobilový průmysl: Výfukové komponenty, skříně turbodmychadel a ventilová sedla vykazují díky povlakům FeCrAl výrazné zlepšení výkonu a životnosti.
Kromě těchto hlavních aplikací se všestrannost FeCrAl rozšiřuje i na různá další průmyslová odvětví:
- Sklářský průmysl: Formy a další součásti manipulující s roztaveným sklem těží z odolnosti FeCrAl vůči teplu a opotřebení.
- Průmysl papíru a celulózy: Zařízení fermentorů a další komponenty vystavené vysokým teplotám a korozivním chemikáliím jsou chráněny povlaky FeCrAl.
- Potravinářský průmysl: FeCrAl chrání zařízení, která pracují při vysokoteplotních procesech, jako je pečení a sušení.
Tento seznam je pouze výchozím bodem. Potenciální aplikace FeCrAl jsou stejně rozmanité jako samotná průmyslová odvětví.
Výhody FeCrAl pro svařování stříkáním
FeCrAl se nevyhýbá boji. Pro svařování nástřikem nabízí řadu přesvědčivých výhod:
- Vynikající výkon při vysokých teplotách: Ať už jde o spalující žár v peci nebo intenzivní prostředí proudového motoru, FeCrAl si zachovává chladnou hlavu, a to doslova. Chrání vaše komponenty před tepelnou degradací a prodlužuje jejich životnost.
- Vynikající odolnost proti opotřebení: Představte si součást, která je neustále bombardována abrazivními částicemi. Povlaky FeCrAl fungují jako štít, minimalizují opotřebení a zabraňují předčasnému selhání.
- Vynikající odolnost proti oxidaci: Oxidace, nepřítel kovů, není pro FeCrAl žádným soupeřem. Vytváří stabilní oxidovou vrstvu, která chrání vaše součásti před korozí a zajišťuje jejich integritu.
- Dobrá tvárnost a tvařitelnost: Povlaky FeCrAl nejsou tuhé a křehké. Nabízejí dobrou rovnováhu mezi pevností a pružností, což jim umožňuje přizpůsobit se mírně nepravidelným povrchům.
- Všestrannost: Jak jsme viděli, rozmanitý tým FeCrAl uspokojuje širokou škálu aplikací a požadavků. Můžete si vybrat optimální složení slitiny, které bude dokonale odpovídat vašim specifickým potřebám.
- Kompatibilita s různými technikami svařování stříkáním: FeCrAl bez problémů spolupracuje s oblíbenými technikami svařování stříkáním, jako je vysokorychlostní svařování kyslíkovým obloukem (HVOF) a svařování plazmovým obloukem (PTA), což z něj činí flexibilní řešení pro různé aplikace.
- Efektivita nákladů: I když se počáteční náklady na prášek FeCrAl mohou zdát vyšší než u některých alternativ, dlouhodobé výhody převáží počáteční investici. Prodloužením životnosti vašich součástí a snížením nákladů na údržbu přináší FeCrAl významnou hodnotu.
Nevýhody FeCrAl pro svařování stříkáním
Každý hrdina má slabinu a FeCrAl není výjimkou. Zde je několik věcí, které je třeba vzít v úvahu:
- Omezená odolnost proti korozi: Zatímco FeCrAl vyniká odolností proti oxidaci při vysokých teplotách, jeho výkonnost proti některým korozivním prostředím může být omezená. Ve vysoce kyselém nebo zásaditém prostředí mohou být lepší volbou alternativní materiály pro svařování nástřikem.
- Křehkost při nízkých teplotách: Některé slitiny FeCrAl mohou být při velmi nízkých teplotách křehké. Pokud vaše aplikace zahrnuje extrémně nízké teploty, je nezbytné zvolit slitinu speciálně vyvinutou pro nízké teploty.
- Dovednosti potřebné pro svařování stříkáním: Efektivní aplikace povlaků FeCrAl vyžaduje odborné znalosti technik svařování stříkáním. Ujistěte se, že váš tým má potřebné dovednosti a zkušenosti k dosažení optimálních výsledků.
- Náklady na materiál: Jak již bylo zmíněno, počáteční náklady na prášek FeCrAl mohou být ve srovnání s některými jinými materiály pro svařování nástřikem vyšší. Dlouhodobé úspory nákladů díky delší životnosti součástí však často převáží tyto počáteční náklady.
Výběr správné slitiny FeCrAl
Vzhledem k tomu, že máte k dispozici rozmanitý tým modelů kovových prášků FeCrAl, je výběr toho správného pro vaši konkrétní aplikaci klíčový. Zde je rozpis klíčových faktorů, které je třeba zvážit:
- Provozní teplota: To je nejdůležitější faktor. Zvolte slitinu FeCrAl s maximální provozní teplotou, která bezpečně převyšuje vaši provozní teplotu. Například pokud vaše součást pracuje při teplotě 900 °C (1650 °F), bude dobrou volbou slitina FeCrAl s maximální provozní teplotou 1100 °C (2010 °F).
- Opotřebení: Pokud se vaše součást výrazně opotřebovává, upřednostněte modely FeCrAl s vysokou odolností proti opotřebení. Slitiny s vyšším obsahem chromu obvykle vykazují vyšší odolnost proti opotřebení.
- Oxidační prostředí: Zvažte závažnost oxidačního prostředí. Pro extrémně náročná prostředí může být nutné použít FeCrAl s vysokým obsahem hliníku nebo modely s přídavkem prvků vzácných zemin.
- Požadované vlastnosti: Potřebujete dobrou elektrickou vodivost? Řešením může být FeCrAl s nízkým obsahem hliníku. Pokud je rozhodující pevnost při vysokých teplotách, mohl by být vhodnější FeCrAlMo.
- Rozpočet: I když počáteční náklady na některé modely FeCrAl mohou být vyšší, zvažte dlouhodobé úspory, které nabízejí. Vezměte v úvahu prodlouženou životnost komponentů a zkrácené prostoje při údržbě.
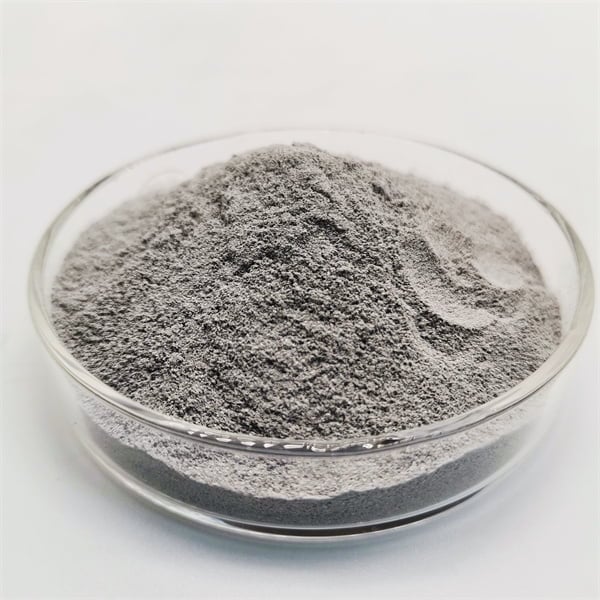
Konzultace s odborníkem na svařování stříkáním:
Výběr optimální slitiny FeCrAl může být složitým rozhodnutím. Doporučujeme spolupracovat s renomovaným odborníkem na svařování nástřikem. Ten může posoudit vaši konkrétní aplikaci, analyzovat provozní podmínky a doporučit nejvhodnější model FeCrAl pro vaše potřeby. Mohou také poskytnout cenné informace o faktorech, jako jsou např:
- Kompatibilita se stávajícím zařízením pro svařování stříkáním: Různé modely FeCrAl mohou mít různou distribuci velikosti částic, což vyžaduje úpravu parametrů svařování nástřikem.
- Požadavky na přípravu povrchu: Před nanesením povlaku FeCrAl je nutné zajistit správnou přípravu povrchu, aby byla zajištěna optimální přilnavost a výkonnost. Odborník vám poradí, jaká je nejvhodnější technika přípravy povrchu pro váš konkrétní základní materiál.
- Úvahy o tloušťce nátěru: Tloušťka povlaku FeCrAl může ovlivnit faktory, jako je odolnost proti opotřebení, přenos tepla a celkové náklady. Odborník vám pomůže určit optimální tloušťku povlaku pro vaši aplikaci.
FAQ
Zde je několik nejčastěji kladených otázek o FeCrAl pro svařování stříkáním, které jsou zodpovězeny v jasném a stručném formátu:
Otázka | Odpovědět |
---|---|
Jaká je trvanlivost prášku FeCrAl? | Při skladování v chladném a suchém prostředí mimo dosah přímého slunečního záření a vlhkosti má prášek FeCrAl obvykle trvanlivost 1-2 roky. |
Lze povlaky FeCrAl obrábět? | Do jisté míry ano. Povlaky FeCrAl lze obrábět technikami, jako je broušení a diamantové soustružení. Obrábění povlaků FeCrAl však může být vzhledem k jejich přirozené tvrdosti náročné a může vyžadovat specializované nástroje. |
Jak si FeCrAl stojí v porovnání s jinými materiály pro svařování stříkáním, jako je niklchrom (NiCr)? | FeCrAl i NiCr mají vynikající odolnost proti vysokým teplotám a opotřebení. FeCrAl však obecně vyniká odolností proti oxidaci, zatímco NiCr může nabídnout lepší výkon ve vysoce korozivním prostředí. Optimální volba závisí na konkrétních požadavcích aplikace. |
Je FeCrAl šetrný k životnímu prostředí? | Samotný FeCrAl není považován za nebezpečný materiál. Při svařování stříkáním však může vznikat prach a výpary. Pro zajištění bezpečného a ekologického provozu jsou zásadní správné systémy větrání a odlučování prachu. |
Sdílet na
MET3DP Technology Co., LTD je předním poskytovatelem řešení aditivní výroby se sídlem v Qingdao v Číně. Naše společnost se specializuje na zařízení pro 3D tisk a vysoce výkonné kovové prášky pro průmyslové aplikace.
Dotaz k získání nejlepší ceny a přizpůsobeného řešení pro vaše podnikání!
Související články
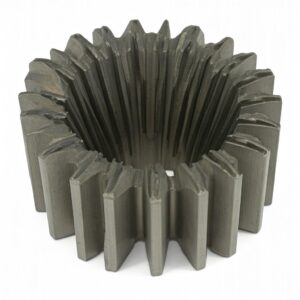
Vysoce výkonné segmenty lopatek trysek: Revoluce v účinnosti turbín díky 3D tisku z kovu
Přečtěte si více "O Met3DP
Nedávná aktualizace
Náš produkt
KONTAKTUJTE NÁS
Nějaké otázky? Pošlete nám zprávu hned teď! Po obdržení vaší zprávy obsloužíme vaši žádost s celým týmem.
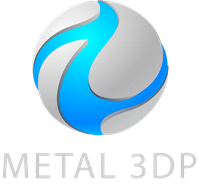
Kovové prášky pro 3D tisk a aditivní výrobu