3D tisk regulačních ventilů průtoku: Revoluce v letectví a kosmonautice
Obsah
Regulační ventily průtoku jsou kritickými součástmi v mnoha průmyslových odvětvích, a to nejen v leteckém průmyslu. V tomto náročném odvětví tyto ventily regulují průtok kapalin a plynů v důležitých systémech a ovlivňují vše od dodávky paliva a hydraulického ovládání až po kontrolu životního prostředí. Ventily pro regulaci průtoku, které se tradičně vyráběly subtraktivními metodami, jsou nyní nově vytvářeny díky síle kovu 3D tisk, známé také jako aditivní výroba. Tento inovativní přístup nabízí bezkonkurenční volnost při navrhování, efektivitu využití materiálů a optimalizaci výkonu, což z něj činí stále atraktivnější řešení pro letecké inženýry a manažery veřejných zakázek, kteří hledají špičková řešení. Na adrese Metal3DP, stojíme v čele této revoluce a poskytujeme pokročilé technologie 3D tisku kovů a vysoce výkonné kovové prášky, které umožňují plně využít potenciál konstrukce a výroby regulačních ventilů průtoku.
K čemu se používají 3D tištěné regulační ventily průtoku?
Kovové 3D tištěné ventily pro regulaci průtoku slouží k různým kritickým funkcím v různých průmyslových odvětvích, v čele s leteckým průmyslem. Díky své schopnosti přesně řídit průtok kapalin a plynů jsou nepostradatelné v mnoha aplikacích.
Aplikace v letectví a kosmonautice:
- Palivové systémy: Řízení toku paliva do motorů, které zajišťuje efektivní a spolehlivý provoz.
- Hydraulické systémy: Regulace hydraulické kapaliny pro ovládání podvozku, řídicích ploch a brzdových systémů.
- Systémy kontroly prostředí (ECS): Řízení proudění a tlaku vzduchu v kabině a v prostoru pro avioniku pro pohodlí a bezpečnost cestujících a vybavení.
- Chladicí systémy: Směrování průtoku chladicí kapaliny ke kritickým elektronickým součástem a dílům motoru, aby se zabránilo přehřátí.
- Pohonné systémy: V některých pokročilých aplikacích je řízení toku pohonných hmot.
Za hranice letectví a kosmonautiky:
Zatímco letecký průmysl zůstává klíčovým uživatelem, výhody 3D tištěných ventilů pro regulaci průtoku se rozšiřují i do dalších odvětví:
- Automobilový průmysl: Řízení průtoku chladicí kapaliny, brzdové kapaliny a dodávky paliva u vysoce výkonných vozidel a specializovaných aplikací.
- Lékařský: Řízení průtoku kapalin a plynů ve zdravotnických zařízeních, jako jsou systémy pro podávání léků a dýchací přístroje.
- Průmyslová výroba: Regulace průtoku různých kapalin v chemickém průmyslu, při zpracování ropy a zemního plynu a v energetice.
- Robotika: Umožňuje přesné řízení hydraulických nebo pneumatických pohonů.
Všestrannost kovového 3D tisku umožňuje vytvářet vysoce přizpůsobené ventily pro regulaci průtoku, které jsou přizpůsobeny specifickým požadavkům každé aplikace a optimalizují výkon a účinnost.
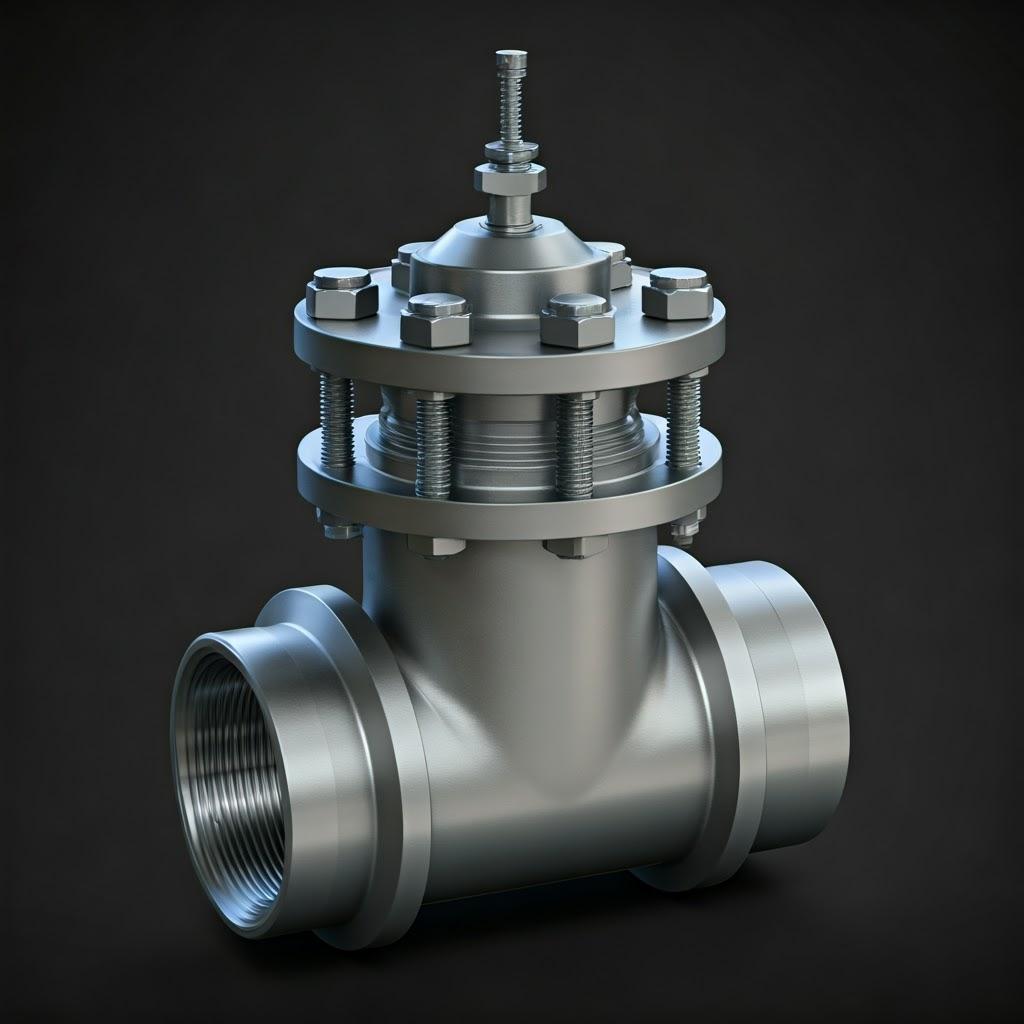
Proč používat 3D tisk z kovu pro regulační ventily průtoku?
Využití kovového 3D tisku pro výrobu ventilů pro regulaci průtoku nabízí oproti tradičním výrobním metodám řadu přesvědčivých výhod, zejména pro náročné požadavky leteckého průmyslu.
- Svoboda a složitost návrhu: Aditivní výroba umožňuje vytvářet složité vnitřní geometrie a komplexní průtokové cesty, které jsou běžnými technikami, jako je obrábění nebo odlévání, jednoduše nedosažitelné. To umožňuje:
- Optimalizovaná dynamika proudění: Návrh vnitřních kanálů pro minimalizaci tlakových ztrát, snížení turbulence a zlepšení celkové účinnosti.
- Integrace funkcí: Zahrnutí více komponent do jednoho tištěného dílu, což zkracuje dobu montáže a snižuje počet potenciálních netěsných míst.
- Odlehčení: Vytváření složitých mřížkových struktur a tenkých stěn pro snížení celkové hmotnosti ventilu, což je v letectví a kosmonautice rozhodující faktor pro efektivní využití paliva a výkon.
- Účinnost materiálu: Na rozdíl od subtraktivních metod, při kterých se materiál odebírá a vytváří se tak konečný díl, se při 3D tisku používá pouze materiál potřebný pro danou součást. Tím se výrazně snižuje plýtvání materiálem, což vede k úsporám nákladů, zejména při práci s drahými slitinami, jako je IN625.
- Rychlé prototypování a iterace: 3D tisk z kovu umožňuje rychlou výrobu prototypů, což inženýrům umožňuje rychle testovat a zdokonalovat návrhy. To urychluje vývojový cyklus a usnadňuje vytváření optimalizovaných řešení. Naše služby 3D tisku z kovu jsou navrženy tak, aby podporovaly tento agilní přístup.
- Přizpůsobení a výroba na vyžádání: Každý regulační ventil lze přizpůsobit specifickým požadavkům aplikace bez nutnosti nákladných změn nástrojů. To je výhodné zejména pro malosériovou výrobu nebo specializované aplikace v letectví a kosmonautice.
- Vylepšený výkon: Optimalizací vnitřních průtokových cest a použitím vysoce výkonných materiálů mohou 3D tištěné ventily pro regulaci průtoku nabídnout lepší účinnost, nižší tlakové ztráty a vyšší odolnost ve srovnání s konvenčně vyráběnými díly.
- Výhody dodavatelského řetězce: Aditivní výroba může umožnit lokalizovanou výrobu, což snižuje závislost na složitých globálních dodavatelských řetězcích a potenciálně zkracuje dodací lhůty.
Doporučené materiály a jejich význam
Výběr vhodného kovového prášku má zásadní význam pro dosažení požadovaných výkonnostních charakteristik 3D tištěných ventilů pro regulaci průtoku, zejména v kritických aplikacích v letectví a kosmonautice. Metal3DP vyrábí širokou škálu vysoce kvalitních kovových prášků optimalizované pro náročná prostředí. U ventilů pro řízení průtoku v letectví a kosmonautice vynikají dva výjimečné materiály: Inconel 625 (IN625) a nerezová ocel 316L.
Inconel 625 (IN625):
- Složení: Nikl-chromová superslitina s významnými přídavky molybdenu a niobu.
- Klíčové vlastnosti a výhody:
- Výjimečná odolnost při vysokých teplotách: Zachovává si vynikající mechanické vlastnosti i při zvýšených teplotách, což je důležité pro letecké motory a výfukové systémy.
- Vynikající odolnost proti korozi: Vysoce odolné vůči široké škále korozivních prostředí, včetně oxidace a vodní koroze, což je nezbytné pro dlouhodobou spolehlivost v leteckých aplikacích.
- Vysoká pevnost v tahu a trhlině: Odolává dlouhodobému vystavení vysokému namáhání a teplotě bez výrazné deformace nebo poruchy.
- Vynikající svařitelnost: Ačkoli je IN625 vytištěn 3D tiskem, jeho přirozená svařitelnost je výhodou pro případné následné zpracování nebo integraci s jinými součástmi.
- Vysoká pevnost a odolnost: Poskytuje vynikající strukturální integritu a odolnost proti nárazu.
Nerezová ocel 316L:
- Složení: Austenitická nerezová ocel obsahující chrom, nikl a molybden s nízkým obsahem uhlíku (označení “L”).
- Klíčové vlastnosti a výhody:
- Vynikající odolnost proti korozi: Nabízí vynikající odolnost proti korozi v různých prostředích, takže je vhodný pro hydraulické a jiné kapalinové systémy.
- Dobrá pevnost a tažnost: Poskytuje dobrou rovnováhu mezi pevností a tvarovatelností.
- Vynikající svařitelnost: Podobně jako u IN625 je jeho svařitelnost výhodná pro integraci.
- Biokompatibilita: V některých aplikacích v letectví a kosmonautice, které zahrnují interakci s lidmi, nebo v potenciálních vedlejších lékařských aplikacích je biokompatibilita materiálu 316L výhodou.
- Nákladově efektivní: Obecně je cenově výhodnější než superslitiny na bázi niklu, jako je IN625, takže je vhodnou volbou pro aplikace při méně extrémních teplotách, kde je odolnost proti korozi stále kritická.
Volba mezi IN625 a 316L závisí na specifických požadavcích na výkonnost regulačního ventilu. Pro aplikace vyžadující pevnost při vysokých teplotách a výjimečnou odolnost proti korozi je vhodnější volbou IN625. Pro aplikace, kde je vyžadována odolnost proti korozi a dobré mechanické vlastnosti při mírných teplotách, nabízí 316L cenově výhodné a spolehlivé řešení. Na adrese Metal3DP, náš pokročilý systém výroby prášku zajišťuje výrobu vysoce kvalitních sférických prášků IN625 i 316L s vynikající tekutostí, která je klíčová pro konzistentní a vysoce husté 3D tištěné díly. Zdroje a související obsah
Konstrukční hlediska pro aditivní výrobu regulačních ventilů průtoku
Navrhování pro 3D tisk z kovu vyžaduje jiné myšlení než tradiční výroba. Pro plné využití možností aditivní výroby a výrobu vysoce výkonných ventilů pro regulaci průtoku je třeba vzít v úvahu několik klíčových konstrukčních aspektů:
- Optimalizace topologie: Tento výpočetní přístup dokáže určit nejefektivnější rozložení materiálu pro danou sadu zatížení a omezení. U ventilů pro regulaci průtoku může optimalizace topologie vést k lehkým konstrukcím s optimalizovanou konstrukční integritou, což snižuje spotřebu materiálu a zlepšuje výkon.
- Mřížové struktury: Začleněním mřížkových struktur do těla ventilu lze výrazně snížit hmotnost, aniž by byla ohrožena pevnost. Tyto složité, vzájemně propojené sítě vzpěr a uzlů nabízejí vysoký poměr tuhosti a hmotnosti a lze je přizpůsobit konkrétním požadavkům na zatížení.
- Design vnitřního kanálu: 3D tisk umožňuje vytvářet složité vnitřní průtokové cesty, které lze optimalizovat pro laminární proudění, snížení tlakové ztráty a lepší míchání (pokud je vyžadováno). Zvažte použití hladkých, zakřivených přechodů namísto ostrých úhlů, abyste minimalizovali turbulence.
- Tloušťka stěny: Pečlivě zvažte minimální tloušťku stěny dosažitelnou při použití zvoleného kovového prášku a procesu tisku. Tenčí stěny mohou snížit hmotnost a spotřebu materiálu, ale musí být dostatečně odolné vůči provozním tlakům a zatížením.
- Podpůrné struktury: Převislé prvky a složité geometrie často vyžadují během tisku podpůrné konstrukce, aby nedošlo k jejich zborcení nebo deformaci. Navrhujte díly se samonosnými úhly, kdykoli je to možné, abyste minimalizovali potřebu podpěr, které je nutné odstranit po zpracování.
- Orientace: Orientace dílu na konstrukční plošině může významně ovlivnit kvalitu povrchu, rozměrovou přesnost a potřebu podpůrných konstrukcí. Optimalizujte orientaci tak, abyste minimalizovali požadavky na podporu kritických povrchů a vyrovnali vysoce namáhané oblasti se směrem sestavování pro dosažení optimálních mechanických vlastností.
- Velikost a rozlišení prvků: Dbejte na minimální velikost prvků a rozlišení, které lze dosáhnout pomocí zvolené tiskové technologie. Malé otvory, složité detaily a jemné závity mohou vyžadovat specifické parametry procesu a techniky následného zpracování.
- Integrace sestavy: Navrhněte více komponent jako jednu tištěnou sestavu, abyste snížili počet dílů, spojovacích prvků a montážních kroků. To může zvýšit spolehlivost a snížit výrobní náklady.
- Úvahy o povrchové úpravě: Povrchová úprava v podobě, v jaké byla vytištěna, nemusí být vhodná pro všechny aplikace. Zvažte začlenění prvků, které usnadňují následné zpracování, jako jsou přídavky na obrábění kritických těsnicích ploch.
Promyšleným řešením těchto konstrukčních otázek mohou konstruktéři využít jedinečné možnosti 3D tisku z kovu a vytvořit ventily pro regulaci průtoku s vyšším výkonem, nižší hmotností a lepší funkčností. Naše služby vývoje aplikací ve společnosti Metal3DP může poskytnout odborné poradenství v oblasti navrhování pro aditivní výrobu.
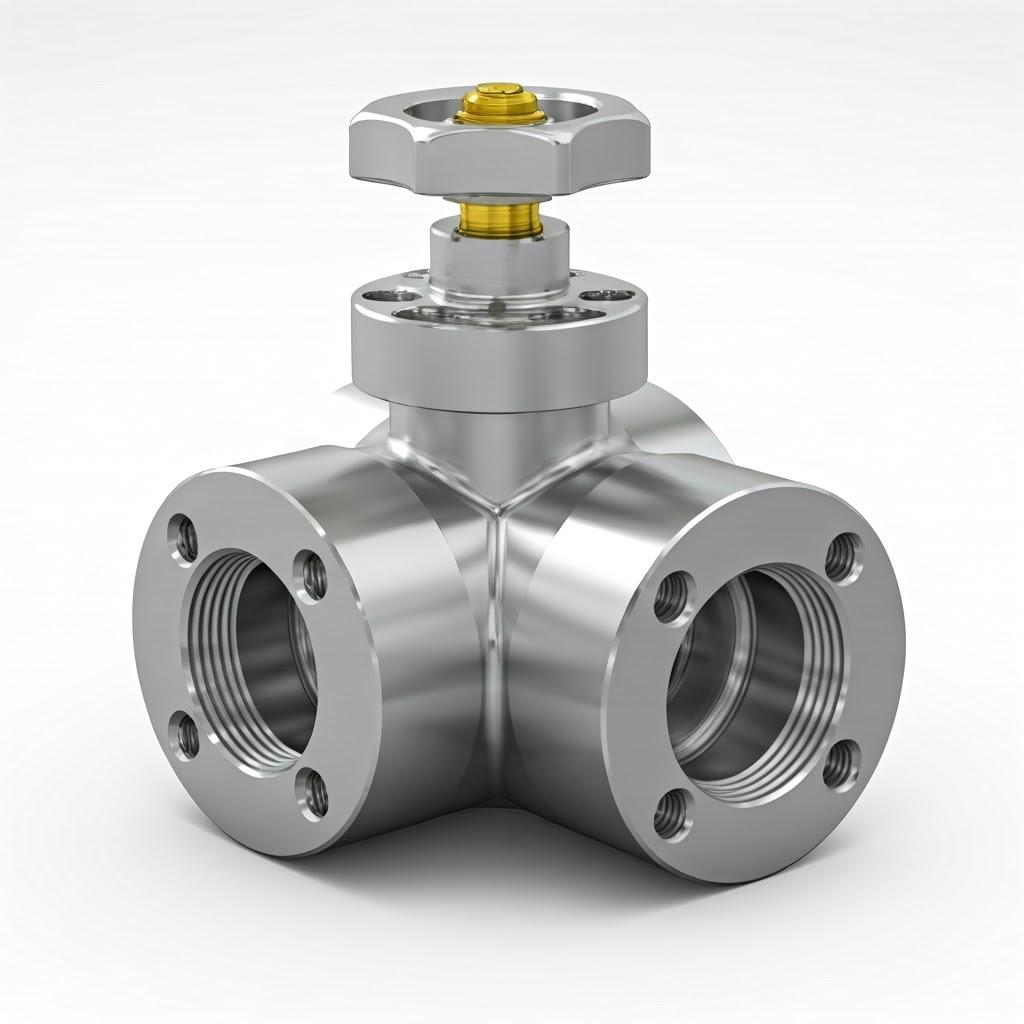
Tolerance, povrchová úprava a rozměrová přesnost 3D tištěných regulačních ventilů průtoku
Dosažení požadované tolerance, kvality povrchu a rozměrové přesnosti má zásadní význam pro funkčnost a spolehlivost regulačních ventilů, zejména v náročných aplikacích v letectví a kosmonautice. Technologie 3D tisku kovů v těchto oblastech významně pokročily, ale je nezbytné porozumět možnostem a omezením různých procesů.
- Tolerance: Dosažitelná tolerance při 3D tisku z kovu závisí na konkrétní technologii tisku (např. selektivní laserové tavení (SLM), tavení elektronovým svazkem (EBM)), použitém materiálu a geometrii dílu. Obecně lze u kritických rozměrů dosáhnout tolerance v rozmezí ±0,1 až ±0,05 mm. Přísnější tolerance mohou vyžadovat následné zpracování, například CNC obrábění. Tiskárny Metal3DP’poskytují špičkovou přesnost v oboru, což zajišťuje vysoce přesné součásti.
- Povrchová úprava: Povrchová úprava po vytištění při 3D tisku z kovu je obvykle hrubší než povrchová úprava dosažená tradičními metodami obrábění. Drsnost povrchu (Ra) se může pohybovat od 5 do 20 μm v závislosti na procesu a materiálu. U těsnicích povrchů nebo oblastí vyžadujících hladký tok jsou často nutné techniky následného zpracování, jako je leštění, kuličkování nebo obrábění, aby bylo dosaženo požadované povrchové úpravy.
- Rozměrová přesnost: Rozměrová přesnost se týká schopnosti procesu 3D tisku vyrábět díly, které přesně odpovídají zamýšlenému modelu CAD. Mezi faktory ovlivňující rozměrovou přesnost patří:
- Tepelné zkreslení: Zbytková napětí a tepelné gradienty během tisku mohou vést k deformaci nebo smrštění. Pečlivá optimalizace parametrů procesu a návrh podpůrné konstrukce mohou tyto účinky zmírnit.
- Smrštění materiálu: Některé materiály vykazují během tuhnutí předvídatelné smršťování. S tím se obvykle počítá při návrhu a tisku.
- Kalibrace a údržba: Pravidelná kalibrace a údržba 3D tiskárny jsou zásadní pro zachování přesnosti rozměrů.
- Orientace na část: Jak již bylo zmíněno, orientace dílu na konstrukční platformě může ovlivnit rozměrovou přesnost v důsledku anizotropních vlastností materiálu a interakce s nosnou konstrukcí.
Dosažitelné úrovně přesnosti:
Vlastnosti | Typická tolerance (podle tisku) | Typická drsnost povrchu (Ra) | Poznámky |
---|---|---|---|
Lineární rozměry | ±0,1-0,05 mm | 5 – 20 μm | Záleží na velikosti, materiálu a tiskárně. |
Průměr otvoru | ±0,15-0,1 mm | Vyšší než rovinné povrchy | Může vyžadovat vrtání nebo vystružování v případě těsných tolerancí. |
Plochost | 0.1 – 0,2 mm/100 mm | N/A | Může být ovlivněn deformací. |
Profil povrchu | Různé | 5 – 20 μm | Závisí na výšce vrstvy a velikosti částic prášku. |
Vnitřní kanály | ±0,2-0,1 mm | Vyšší než vnější povrchy | Optimalizace konstrukce má zásadní význam pro efektivitu průtoku. |
Export do archů
Pochopení těchto dosažitelných úrovní přesnosti a plánování nezbytných kroků následného zpracování jsou zásadní pro úspěšnou implementaci 3D tištěných ventilů pro regulaci průtoku v náročných aplikacích.
Požadavky na následné zpracování 3D tištěných regulačních ventilů průtoku
Přestože 3D tisk z kovu nabízí značné výhody, je často nutné následné zpracování, aby bylo dosaženo konečných požadovaných vlastností, povrchové úpravy a rozměrové přesnosti ventilů pro regulaci průtoku. Mezi běžné kroky následného zpracování patří:
- Odstranění podpory: Podpěrné konstrukce, které jsou nezbytné pro tisk složitých geometrií, je třeba pečlivě odstranit. To lze provést ručně pomocí nástrojů nebo automatizovanými procesy, jako je obrábění nebo chemické rozpouštění, v závislosti na podpůrném materiálu a geometrii dílu.
- Tepelné zpracování: Žíhání na uvolnění napětí se často provádí za účelem snížení zbytkových napětí vzniklých během procesu tisku, což zlepšuje mechanické vlastnosti a rozměrovou stabilitu ventilu. Konkrétní cykly tepelného zpracování se řídí požadavky na materiál a aplikaci.
- Povrchová úprava: K dosažení hladšího povrchu pro lepší těsnění nebo snížení odporu proti proudění lze použít různé techniky povrchové úpravy:
- Výbuch v médiích: Používá se k odstranění částečně roztavených částic prášku a ke zlepšení celkové povrchové úpravy.
- Leštění: Mechanickým nebo chemickým leštěním lze dosáhnout velmi hladkých povrchů v kritických těsnicích oblastech.
- Vibrační dokončovací práce: Nákladově efektivní metoda pro zlepšení kvality povrchu na složitých geometriích.
- CNC obrábění: U kritických rozměrů a těsných tolerancí lze použít CNC obrábění k dosažení konečné požadované přesnosti, zejména u těsnicích ploch, závitů a montážních prvků.
- Povrchová úprava: V závislosti na prostředí použití lze povlaky aplikovat za účelem zvýšení odolnosti proti korozi, odolnosti proti opotřebení nebo jiných specifických vlastností. Příklady zahrnují galvanické pokovování, chemické napařování (CVD) nebo fyzikální napařování (PVD).
- Kontrola a řízení kvality: K zajištění integrity a kvality tištěných ventilů, zejména u kritických aplikací v letectví a kosmonautice, lze použít nedestruktivní metody zkoušení, jako je kontrola penetrací barviva, kontrola magnetickými částicemi nebo ultrazvukové zkoušení. Přesnost rozměrů se ověřuje pomocí souřadnicových měřicích strojů (CMM).
- Montáž: Pokud se regulační ventil skládá z více 3D tištěných součástí, bude nutné provést konečnou montáž, například svařování, pájení nebo mechanické upevnění.
Konkrétní kroky následného zpracování závisí na aplikaci, použitém materiálu, požadovaných výkonnostních charakteristikách a možnostech zvoleného poskytovatele služeb 3D tisku. Na adrese Metal3DP, nabízíme komplexní služby následného zpracování, abychom zajistili, že vaše 3D tištěné ventily pro regulaci průtoku splňují nejpřísnější požadavky.
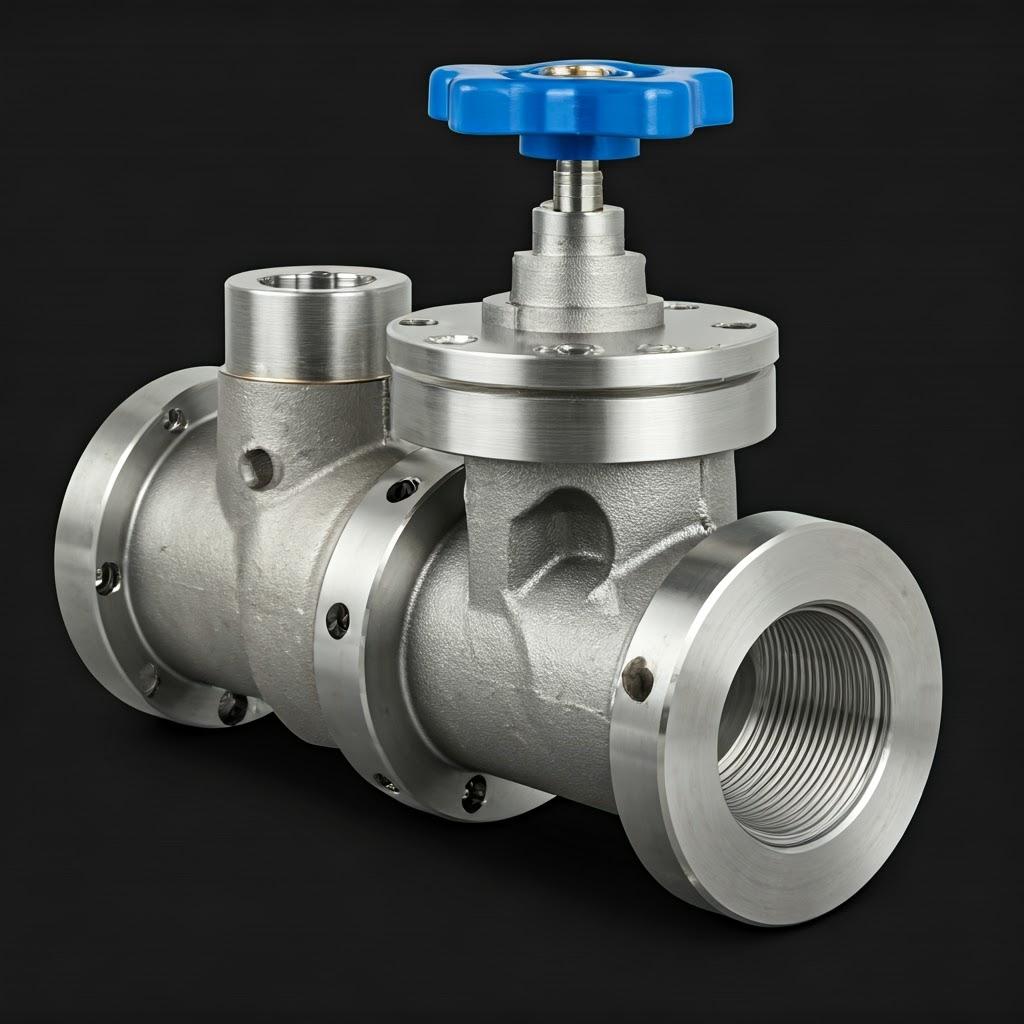
Běžné problémy a jak se jim vyhnout při 3D tisku regulačních ventilů průtoku
3D tisk z kovu nabízí řadu výhod, ale během procesu může vzniknout několik problémů. Pochopení těchto potenciálních problémů a zavedení preventivních opatření je zásadní pro úspěšnou výrobu vysoce kvalitních ventilů pro regulaci průtoku.
- Deformace a zkreslení: Tepelné namáhání během tisku může vést k deformaci nebo zkreslení dílu, zejména u velkých nebo složitých geometrií.
- Jak se tomu vyhnout: Optimalizujte orientaci dílů, používejte vhodné podpůrné struktury, pečlivě kontrolujte parametry procesu (výkon laseru, rychlost skenování, teplotu stavební desky) a zvažte tepelné zpracování po tisku.
- Obtíže při odstraňování podpory: Odstranění složitě navržených podpůrných konstrukcí může být náročné a zdlouhavé, což může vést k poškození choulostivých prvků.
- Jak se tomu vyhnout: Navrhujte díly se samonosnými úhly, kdykoli je to možné, optimalizujte konstrukci podpůrné konstrukce pro snadnou demontáž a zvažte použití rozpustných podpůrných materiálů, pokud je to možné.
- Pórovitost: Vnitřní dutiny nebo póry uvnitř tištěného dílu mohou ohrozit jeho mechanickou pevnost a těsnost, což je u ventilů pro regulaci průtoku velmi důležité.
- Jak se tomu vyhnout: Optimalizujte parametry tisku (výkon laseru, rychlost skenování, tloušťka vrstvy prášku), zajistěte vysoce kvalitní kovový prášek s dobrou tekutostí (Pokročilý systém výroby prášku Metal3DP’s ) a při tisku používejte vhodnou atmosféru inertního plynu. Jako následný krok zpracování lze použít izostatické lisování za tepla (HIP) ke snížení pórovitosti.
- Drsnost povrchu: Povrchová úprava po vytištění může být příliš drsná pro těsnicí aplikace nebo pro minimalizaci odporu proti proudění.
- Jak se tomu vyhnout: Optimalizujte parametry tisku (výška vrstvy, strategie skenování), vhodně orientujte kritické povrchy během tisku a plánujte nezbytné kroky následného zpracování, jako je leštění nebo obrábění.
- Rozměrová nepřesnost: K odchylkám od zamýšlených rozměrů může dojít v důsledku tepelného smrštění, problémů s kalibrací nebo nesprávných procesních parametrů.
- Jak se tomu vyhnout: Pravidelně kalibrujte 3D tiskárnu, optimalizujte orientaci dílů, kompenzujte smrštění materiálu ve fázi návrhu a používejte přesné strategie skenování. Metrologie a obrábění po zpracování mohou zajistit konečnou rozměrovou přesnost.
- Změny vlastností materiálu: Kvůli odchylkám v tiskovém procesu mohou vzniknout nekonzistentní vlastnosti materiálu v celém tištěném dílu.
- Jak se tomu vyhnout: Využijte renomovaného poskytovatele služeb 3D tisku s dobře řízenými procesy, zajistěte konzistentní kvalitu prášku a optimalizujte parametry procesu pro rovnoměrný příkon energie.
Aktivním řešením těchto potenciálních problémů prostřednictvím pečlivého návrhu, optimalizovaných procesních parametrů a vhodného následného zpracování mohou výrobci spolehlivě vyrábět vysoce výkonné kovové 3D tištěné ventily pro regulaci průtoku pro náročné aplikace.
Jak vybrat správného poskytovatele služeb 3D tisku kovů pro regulační ventily průtoku
Výběr správného poskytovatele služeb 3D tisku z kovu je zásadní rozhodnutí, které může významně ovlivnit kvalitu, náklady a dobu realizace vašich ventilů pro regulaci průtoku. Zde jsou klíčové faktory, které je třeba zvážit při hodnocení potenciálních dodavatelů:
- Materiálové schopnosti: Ujistěte se, že dodavatel má zkušenosti s prací s konkrétními kovovými prášky, které jsou pro vaši aplikaci potřebné, například IN625 a 316L. Ověřte si, že používá vysoce kvalitní prášky a má optimalizované parametry tisku pro tyto materiály. Metal3DP vyrábí širokou škálu vysoce kvalitních kovových prášků a má rozsáhlé zkušenosti s jejich zpracováním.
- Technologie tisku: Různé technologie 3D tisku kovů (např. SLM, DMLS, EBM) nabízejí různé úrovně přesnosti, povrchové úpravy a objemu. Vyberte si poskytovatele, jehož technologie odpovídá specifickým požadavkům na konstrukci vašeho regulačního ventilu průtoku a objemu výroby. Naše společnost se specializuje na tiskárny SEBM, známé svou přesností a spolehlivostí.
- Řízení kvality a certifikace: Pro kritické aplikace v letectví a kosmonautice je nezbytné vybrat poskytovatele s robustním systémem řízení kvality a příslušnými certifikacemi (např. AS9100 pro letectví a kosmonautiku). Informujte se o jeho kontrolních postupech, sledovatelnosti materiálu a procesech kontroly kvality.
- Odborné znalosti v oblasti návrhu pro aditivní výrobu (DfAM): Znalý poskytovatel služeb vám může nabídnout cenné rady ohledně optimalizace konstrukce regulačního ventilu pro 3D tisk, což může vést ke zlepšení výkonu, snížení hmotnosti a snížení výrobních nákladů. Hledejte poskytovatele se zkušenými inženýry, kteří rozumí nuancím DfAM. Metal3DP poskytuje komplexní řešení zahrnující služby vývoje aplikací.
- Možnosti následného zpracování: Zjistěte, zda poskytovatel nabízí potřebné služby následného zpracování, které splňují vaše požadavky, jako je odstranění podpěr, tepelné zpracování, povrchová úprava a CNC obrábění. Vlastní nebo dobře zavedená síť kapacit následného zpracování může zefektivnit výrobní proces.
- Vytváření objemu a kapacity: Ujistěte se, že poskytovatel má dostatečný objem výroby a výrobní kapacitu, aby zvládl požadavky vašeho projektu, a to jak pro výrobu prototypů, tak pro případnou sériovou výrobu.
- Doba dodání: Diskutujte o dodacích lhůtách pro výrobu prototypů i sériovou výrobu. Pochopte jejich plánovací a dodací procesy, abyste se ujistili, že jsou v souladu s časovým plánem vašeho projektu.
- Struktura nákladů: Získejte jasný a podrobný rozpis nákladů, včetně nákladů na tisk, materiály, následné zpracování a případné poplatky za návrh nebo inženýrské práce. Porovnejte nabídky od více poskytovatelů, abyste zajistili konkurenceschopné ceny.
- Komunikace a podpora: Zhodnoťte rychlost reakce poskytovatele, srozumitelnost komunikace a technickou podporu. Silné partnerství vyžaduje efektivní komunikaci a ochotu spolupracovat.
- Důvěrnost a ochrana duševního vlastnictví: Ujistěte se, že poskytovatel má zavedeny spolehlivé zásady a dohody na ochranu vašeho duševního vlastnictví a zachování důvěrnosti.
Pečlivým zvážením těchto faktorů si můžete vybrat poskytovatele služeb 3D tisku z kovu, který je dobře vybaven pro dodávku vysoce kvalitních regulačních ventilů průtoku, které splňují vaše specifické potřeby a náročné požadavky leteckého průmyslu.
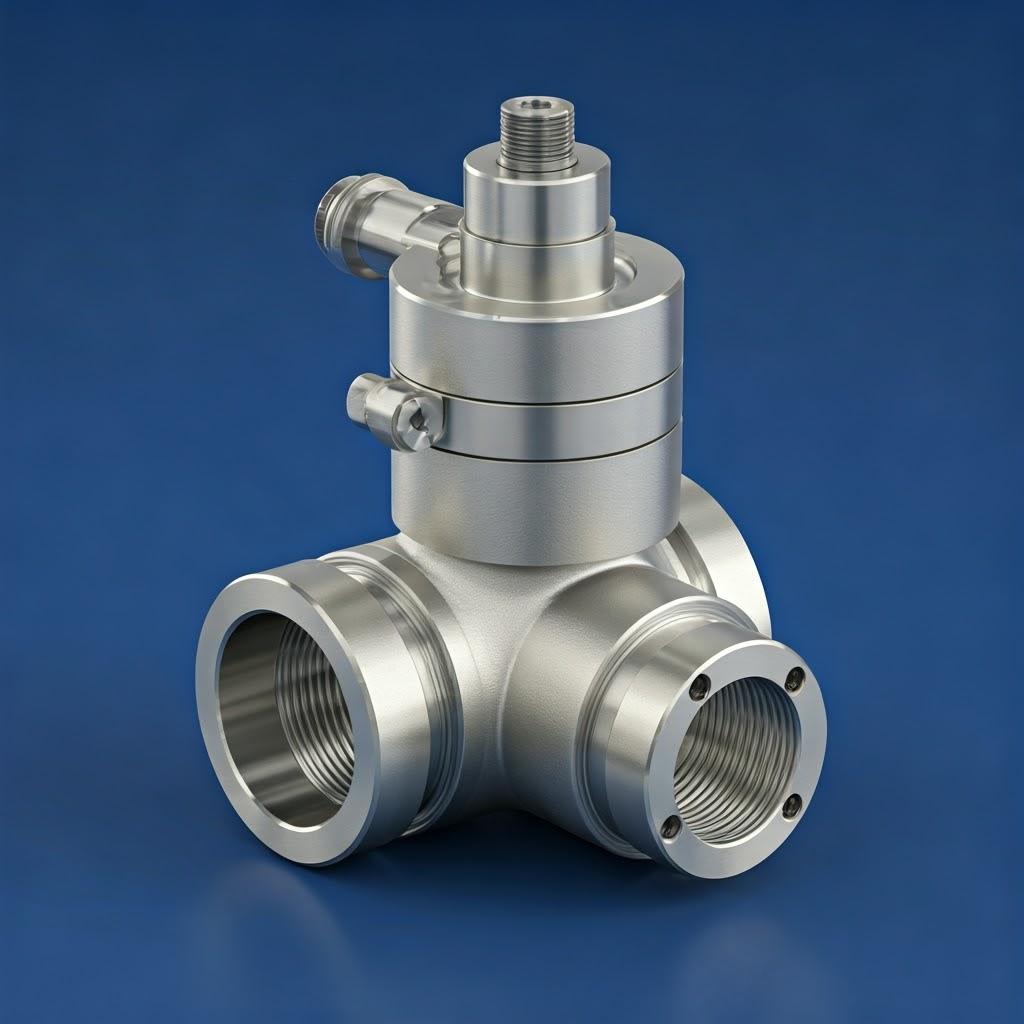
Nákladové faktory a doba realizace 3D tištěných ventilů pro regulaci průtoku
Pochopení faktorů, které ovlivňují náklady a dobu realizace 3D tištěných regulačních ventilů průtoku, je zásadní pro efektivní plánování projektu a sestavení rozpočtu.
Nákladové faktory:
- Náklady na materiál: Významným faktorem je cena kovového prášku. Slitiny jako IN625 jsou obecně dražší než nerezové oceli jako 316L. K celkovým materiálovým nákladům přispívá také materiálový odpad, který je sice nižší než při subtraktivní výrobě.
- Doba výstavby: Doba trvání tiskového procesu přímo ovlivňuje náklady na strojní čas. Mezi faktory ovlivňující dobu sestavení patří velikost dílu, složitost, využití objemu sestavení a výška vrstvy.
- Náklady na následné zpracování: Rozsah nutného následného zpracování (odstranění podpory, tepelné zpracování, povrchová úprava, obrábění atd.) významně ovlivňuje konečné náklady. Složité geometrie často vyžadují rozsáhlejší a nákladnější následné zpracování.
- Náklady na pracovní sílu: Pro optimalizaci návrhu, nastavení tisku, obsluhu stroje a následné zpracování jsou zapotřebí kvalifikovaní technici a inženýři. Náklady na pracovní sílu jsou zahrnuty v celkové ceně.
- Odpisy a údržba strojů: Náklady na zařízení pro 3D tisk a jeho údržbu jsou nedílnou součástí cenového modelu poskytovatelů služeb.
- Množství a objem: Zatímco 3D tisk vyniká v nízkých až středních objemech výroby a přizpůsobení, u vyšších objemů lze využít úspor z rozsahu. Na rozdíl od tradiční výroby však s 3D tiskem obvykle nejsou spojeny žádné náklady na nástroje.
- Složitost návrhu: Složité konstrukce, které vyžadují rozsáhlé podpůrné konstrukce nebo specializované parametry tisku, mohou vyžadovat vyšší náklady.
Faktory doby realizace:
- Design a inženýrství: Doba potřebná pro optimalizaci návrhu pro aditivní výrobu se může lišit v závislosti na složitosti dílu.
- Doba tisku: Jak již bylo zmíněno dříve, klíčovou složkou doby realizace je doba sestavení.
- Doba následného zpracování: Doba potřebná k odstranění podpěr, tepelnému zpracování, povrchové úpravě a dalším krokům následného zpracování může významně ovlivnit celkovou dobu výroby.
- Dostupnost a plánování strojů: Čas zahájení projektu ovlivní aktuální vytížení poskytovatele služeb a dostupnost strojů.
- Kontrola kvality a inspekce: Důkladné kontrolní procesy mohou prodloužit dobu přípravy, ale jsou nezbytné pro zajištění kvality, zejména v kritických aplikacích.
- Přeprava a logistika: V úvahu je třeba vzít také dobu potřebnou k přepravě hotových dílů na místo určení.
Obecné odhady:
Je obtížné poskytnout přesné odhady nákladů a doby realizace bez konkrétních údajů o dílu. Nicméně pro středně složitý letecký regulační ventil:
- Vytváření prototypů: Dodací lhůty se mohou pohybovat od několika dnů do několika týdnů a náklady se pohybují od několika set do několika tisíc dolarů v závislosti na velikosti, materiálu a následném zpracování.
- Nízkosériová výroba: Dodací lhůty se mohou pohybovat od několika týdnů do několika měsíců, přičemž náklady na jeden díl se mohou snižovat s většími velikostmi šarží, ale stále jsou ovlivněny výše uvedenými faktory.
Je velmi důležité prodiskutovat své konkrétní požadavky s potenciálními poskytovateli služeb 3D tisku z kovu, jako jsou např Metal3DP a získat přesné odhady nákladů a doby realizace vašeho projektu regulačního ventilu.
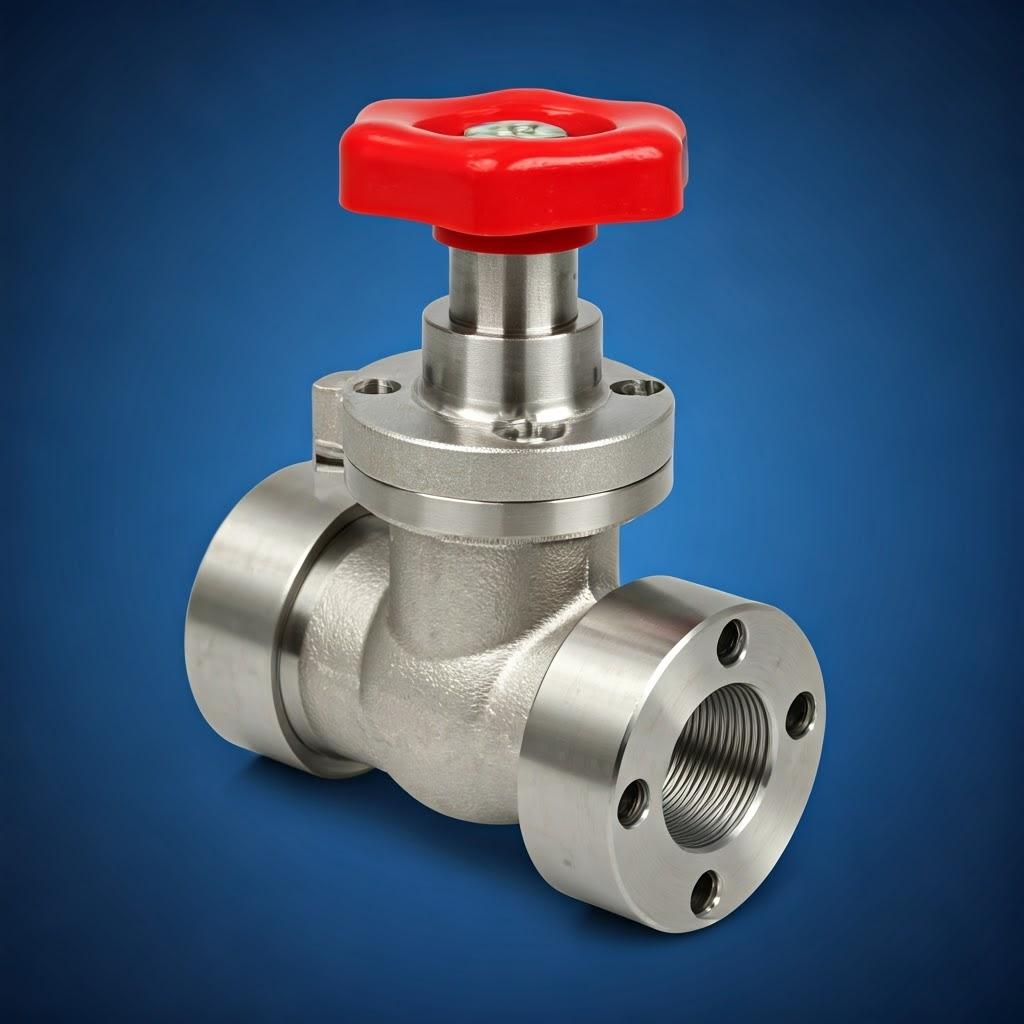
Často kladené otázky (FAQ)
- Jaké jsou typické tolerance dosažitelné u 3D tištěných kovových regulačních ventilů průtoku?
- Typické tolerance po vytištění se pohybují od ±0,1 do ±0,05 mm. Větších tolerancí lze dosáhnout následným zpracováním, například CNC obráběním. Naše tiskárny Metal3DP poskytují špičkovou přesnost v oboru.
- Je 3D tisk z kovu nákladově efektivní pro výrobu regulačních ventilů průtoku ve velkých objemech?
- Kovový 3D tisk je obecně nejvýhodnější pro nízko až středně velkou sériovou výrobu a vysoce přizpůsobené díly díky absenci nákladů na nástroje a schopnosti vytvářet složité geometrie. Pro velmi vysoké objemy mohou být ekonomičtější tradiční výrobní metody. Výhody svobody návrhu a optimalizace výkonu však často převažují nad úvahami o nákladech, zejména v leteckém průmyslu.
- Jaké jsou běžné kovové slitiny používané pro 3D tisk regulačních ventilů průtoku?
- Mezi běžné slitiny patří nerezové oceli (např. 316L), superslitiny na bázi niklu (např. IN625, Inconel 718), slitiny titanu (např. Ti-6Al-4V) a slitiny hliníku. Výběr materiálu závisí na konkrétních požadavcích na použití, jako je teplota, tlak a odolnost proti korozi. Metal3DP nabízí komplexní portfolio vysoce kvalitních kovových prášků.
Závěr
3D tisk z kovu přináší revoluci v konstrukci a výrobě regulačních ventilů, zejména pro náročný letecký průmysl. Schopnost vytvářet složité vnitřní geometrie, optimalizovat konstrukce pro odlehčení a výkon a využívat vysoce výkonné materiály, jako jsou IN625 a 316L, nabízí významné výhody oproti tradičním výrobním metodám. Přestože pečlivé zvážení návrhu pro aditivní výrobu, požadavků na následné zpracování a výběr správného poskytovatele služeb jsou klíčové, výhody vylepšené funkčnosti, snížené hmotnosti a rychlé výroby prototypů činí z kovového 3D tisku stále přesvědčivější řešení pro inženýry a manažery nákupu, kteří hledají špičkové technologie pro regulaci průtoku. Kontaktujte Metal3DP ještě dnes a zjistěte, jak mohou naše pokročilá řešení 3D tisku z kovů podpořit cíle vaší organizace v oblasti aditivní výroby a podpořit inovace ve vašem odvětví.
Sdílet na
MET3DP Technology Co., LTD je předním poskytovatelem řešení aditivní výroby se sídlem v Qingdao v Číně. Naše společnost se specializuje na zařízení pro 3D tisk a vysoce výkonné kovové prášky pro průmyslové aplikace.
Dotaz k získání nejlepší ceny a přizpůsobeného řešení pro vaše podnikání!
Související články
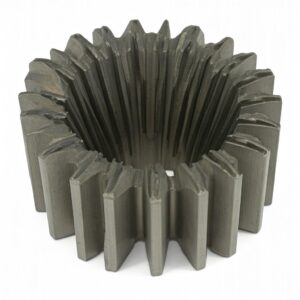
Vysoce výkonné segmenty lopatek trysek: Revoluce v účinnosti turbín díky 3D tisku z kovu
Přečtěte si více "O Met3DP
Nedávná aktualizace
Náš produkt
KONTAKTUJTE NÁS
Nějaké otázky? Pošlete nám zprávu hned teď! Po obdržení vaší zprávy obsloužíme vaši žádost s celým týmem.